DOI:
10.1039/C5GC02183A
(Paper)
Green Chem., 2016,
18, 165-175
Selective transformation of hemicellulose (xylan) into n-pentane, pentanols or xylitol over a rhenium-modified iridium catalyst combined with acids†
Received
14th September 2015
, Accepted 29th October 2015
First published on 29th October 2015
Abstract
n-Pentane, pentanols and xylitol can be separately produced from hemicellulose (xylan) over an Ir–ReOx/SiO2 catalyst combined with acids by simply adjusting the reaction conditions. n-Pentane can be produced by using Ir–ReOx/SiO2 combined with HZSM-5 + H2SO4 in a biphasic solvent system (4 ml n-dodecane + 9.5 ml H2O) with a reaction temperature of 463 K for 24 h. Pentanols can be produced by using Ir–ReOx/SiO2 combined with H2SO4 in a biphasic solvent system (20 ml n-dodecane + 9.5 ml H2O) with a reaction temperature of 413 K for 144 h. Xylitol can be produced by using Ir–ReOx/SiO2 combined with H2SO4 in the aqueous phase with a reaction temperature of 413 K for 12 h. The highest yields of n-pentane, pentanols and xylitol could reach 70%, 32% and 79%, respectively. The reuse of the catalyst was feasible when the catalyst was regenerated by calcination at 773 K for 3 h. The calcination step is for removing the humins which were formed at the hydrolysis + hydrogenation step during conversion of xylan. The humins covered the active site of Ir–ReOx/SiO2 and HZSM-5, and they deactivated Ir–ReOx/SiO2 in C–O hydrogenolysis performance in part. The mineral ions (such as Na+ and K+) in xylan decreased the hydrogenolysis activity of Ir–ReOx/SiO2 significantly since the mineral ions can make the number of hydroxorhenium sites (Re–OH) smaller, which is the active site of Ir–ReOx/SiO2 for C–O hydrogenolysis, by ion exchange. The appropriate amount of H2SO4 addition is very crucial for the production of target products in high yield. The addition of H2SO4 not only neutralized the residual alkali of xylan after being isolated from lignocellulose to make the reaction solution acidic, but also improved the C–O hydrogenolysis activity of Ir–ReOx/SiO2 through increasing the number of hydroxorhenium sites by competitive adsorption on the Re site with mineral ions.
1. Introduction
Biomass and its derived substrates are playing a more and more important role in replacing non-renewable fossil resources in the production of transportation fuels and chemical products because of the dwindling fossil resources and global warming.1–10 Lignocellulose is the most abundant biomass resource, which comprises three different fractions: cellulose (40–50%), hemicellulose (20–30%), and lignin (20–30%). All of these fractions have high oxygen content, and the conversions to useful chemicals and fuels usually require reduction. Recently, numerous research studies have focused on reductive conversion of cellulose11–14 and lignin.15–19 On the other hand, the transformation of hemicellulose, which is mainly composed of pentoses (xylose and arabinose), usually starts with the hydrolysis to pentose20–23 or further dehydration to furfural.24–26
One-pot conversion of hemicellulose to chemicals by reduction has been less extensively studied.27–31 Conversion of xylan, which is a kind of hemicellulose abundant in hardwood, into xylitol was reported with the yield of 50–80% by using Ru/C27,28 or Pt–SnOx/Al2O3.29 Xylitol can serve as an artificial sweetener in food. While selective productions of long chain hydrocarbons,6,32–36 2-methylfuran,37,38 furan,38 tetrahydrofuran derivatives,39–41 cyclopentane derivatives,42,43 pentanediols44–47 from furfural have been extensively reported,37,38,44–47 there are few reports on production of n-pentane and pentanols from furfural.48,49 In addition, a small number of research studies on the conversion of xylitol to n-pentane and pentanols by hydrogenolysis have been reported.50–54 On the other hand, both n-pentane and pentanols can be used as organic solvents and as components of gasoline or fuel additives.55 However, the production of n-pentane or pentanols from furfural or xylitol needs the extra steps of hydrolysis + dehydration or hydrolysis + hydrogenation of xylan. Therefore, one-pot reductive transformation of xylan to xylitol, pentanols and n-pentane with a heterogeneous catalyst is more attractive and meaningful.
Both xylan and cellulose are polysaccharides. One-pot catalytic conversion of cellulose to sorbitol,11–14,56–60 hexanols61 and hexanes62–64 by hydrolysis + hydrogenation or hydrogenolysis methods has been widely reported, especially conversion to sorbitol. Sels et al.63 and Ma et al.64 reported catalytic systems for the conversion of cellulose to n-hexane using Ru/C and acid catalysts. In these systems, cyclic intermediates such as 5-hydroxymethylfurfural (HMF) and cyclic ethers were involved. On the other hand, we have very recently found that an Ir–ReOx/SiO2 catalyst combined with HZSM-5 was effective in the production of n-hexane from cellulose (∼80% yield)62 and an Ir–ReOx/SiO2 catalyst combined with H2SO4 was effective in the production of hexanols from mechanocatalytic depolymerized cellulose (∼60% yield).61 The reaction for the production of hexanes dominantly proceeds via hydrogenolysis of sorbitol step-by-step, and cyclic ethers are hardly formed. Therefore, in this work, we used the Ir–ReOx/SiO2 catalyst and different acids for the selective production of n-pentane, pentanols or xylitol from hemicellulose (xylan) (Scheme 1).
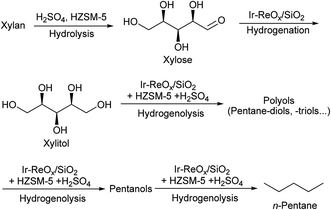 |
| Scheme 1 The reaction pathway for conversion of xylan to n-pentane over Ir–ReOx/SiO2 + HZSM-5 + H2SO4. | |
2. Experimental
2.1. Catalyst preparation
Ir–ReOx/SiO2 catalysts were prepared by the sequential impregnation method as described previously.61,62,65–74 First, Ir/SiO2 was prepared by impregnating SiO2 (Fuji Silysia G-6, calcined in air at 973 K for 1 h, BET surface area 535 m2 g−1) with an aqueous solution of H2IrCl6 (Furuya Metals Co., Ltd). After evaporating the solvent at ≤353 K and drying at 383 K for 12 h, the Ir–ReOx/SiO2 catalysts were impregnated with an aqueous solution of NH4ReO4 (Soekawa Chemical Co., Ltd). These catalysts were calcined in a crucible in air at 773 K for 3 h after drying at 383 K for 12 h. The loading amount of Ir was 4.0 wt% and the Re/Ir molar ratio was typically 2. All the catalysts were used in powdered form with a granule size of <100 mesh. HZSM-5 [JRC-Z5-90H(1), Süd-Chemie Catalysts and Catalysis Society of Japan, SiO2/Al2O3 = 90] was used as received.
2.2. Activity tests
Activity tests were performed in a 190 ml stainless steel autoclave with an inserted glass vessel. The catalyst was put into an autoclave together with a stirrer and an appropriate amount of water and heated at 473 K with 8 MPa H2 for 1 h for the reduction pretreatment. The stirring rate was 250 rpm. After the pretreatment, the autoclave was cooled down, and hydrogen was removed. 0.5 g xylan, an appropriate amount of H2SO4 aqueous solution and n-dodecane (0, 4 or 20 ml; Tokyo Chemical Industry Co. Ltd, 99%) were put into the autoclave. Three types of xylans were obtained from TCI, Wako and Sigma-Aldrich, and typically TCI-xylan was used. The elemental analysis results of these xylan samples are shown in Table S1 (ESI†). 0.06 g HZSM-5 was also added when necessary. After sealing the reactor, the air was purged by flushing three times with H2 (1 MPa, 99.99%; Nippon Peroxide Co., Ltd). The reactor was pressurized with H2 to 6.0 MPa and then heated to a set temperature (413 or 463 K). The heating took about 0.8 h. After the set temperature was reached, the temperature was maintained for an appropriate reaction time. The stirring rate was 500 rpm. After reaction, the reactor was cooled down by using an ice bath and the gases were collected in a gas bag. The reaction mixture was separated into organic and aqueous phases. The autoclave contents were transferred to a vial, and the catalyst was separated by centrifugation and filtration. The hydrogenolysis of xylitol (Wako Pure Chemical Industries, Ltd, 98%) was also tested in a similar way to that of xylan.
The detected products were xylose, sugar alcohols: xylitol, arabitol, sorbitol; mono-alcohols: 1-pentanol, 2-pentanol, 3-pentanol, 1-hexanol, 2-hexanol and 3-hexanol; cyclic ethers: 2-methyltetrahydrofuran, tetrahydropyran and 2,5-dimethyltetrahydrofuran and alkanes: n-hexane, 2-methylpentane, 3-methylpentane, n-pentane, 2-methylbutane, cyclopentane, n-butane, propane, ethane and methane; and other products that could not be identified. Sugar and sugar alcohols in the aqueous phase were analyzed by using HPLC (Shimadzu LC-10A) with a refractive index detector (RID) and an Phenomenex Rezex RPM-Monosaccharide Pb + 2 column (diameter 7.8 mm, 300 mm) and an Aminex HPX-87C column (diameter 7.8 mm, 300 mm). Mono-alcohols in the aqueous phase were analyzed by using a gas chromatograph (Shimadzu GC-2014) equipped with a TC-WAX capillary column (diameter 0.25 mm, 30 m) and FID. Alkanes, cyclic ethers and mono-alcohols in the organic phase were analyzed by a gas chromatograph (Shimadzu GC-2014) equipped with a DB-1 capillary column (diameter 0.25 mm, 30 m) and FID. A TC-WAX capillary column (diameter 0.25 mm, 30 m) and a FID were used for the separation of internal alcohols (2- and 3-pentanols) with the same carbon number. Alkanes in the gas phase were analyzed by a gas chromatograph (Shimadzu GC-2014) equipped with an Rtx-1-PONA capillary column (diameter 0.25 mm, 100 m) and FID. The distributions of products in the three phases for typical runs are shown in Tables S2 and S3 (ESI).†
The conversion of xylan and the yield of products were calculated on the basis of carbon and defined as follows:
The weight of xylan after the reaction was determined by subtracting the weight of the solid in the reaction mixture by the weight of catalysts. It should be noted that the formation of a solid product on the catalysts underestimates the conversion value. Loss of carbon balance corresponds to the amount of polyols and soluble polymers. The used catalyst was washed with excess water and dried in air and then calcined at 773 K for 3 h. A slight loss (<12% in weight) was observed during the recovery process and was compensated with a fresh catalyst in each reuse experiment. The amount of eluted metal during the reaction and the amount of mineral ions in xylan were analyzed by inductively coupled plasma atomic emission spectrometry (ICP-AES, Thermo Scientific iCAP 6500). X-ray diffraction (XRD) patterns of the used catalyst were recorded by a diffractometer (Rigaku MiniFlex 600).
3. Results and discussion
3.1 Production of n-pentane from xylan over Ir–ReOx/SiO2 + HZSM-5 + H2SO4 in a biphasic solvent system
We chose Ir–ReOx/SiO2 (Re/Ir = 2) as the catalyst for hydrogenolysis because we have found that this catalyst is very effective in C–O hydrogenolysis of various molecules including cellulose.61,62,65–72 In our previous work, Ir–ReOx/SiO2 (Re/Ir = 2) combined with HZSM-5 showed good performance in the production of n-hexane from ball-milled cellulose after 12 h reaction.62 However, when this catalyst system was applied to the conversion of xylan (TCI xylan), almost no n-pentane was formed even with a prolonged reaction time (Table 1, entry 1). Large amount of humins was formed and deposited on the stirrer and the wall of the reactor. The pH of the filtrate after the reaction was 6.94, which was almost neutral, while the filtrate of Ir–ReOx/SiO2 after reduction without xylan and even HZSM-5 had a pH value of 3.32. According to our previous work, the Ir–ReOx/SiO2 catalyst was effective in C–O hydrogenolysis under acidic conditions.69 The almost neutral condition not only decreases the activity of the Ir–ReOx/SiO2 catalyst but also makes the hydrolysis rate of xylan into xylose lower. This could be the reason for the low yield of n-pentane and other detected products. In the production of hemicellulose, extraction with alkali was the most common method. Typically used alkalis are potassium, sodium and calcium hydroxide with a concentration of 0.05–0.15 g alkali per g biomass.75 Some alkalis could be converted to irrecoverable salts or incorporated as salts into hemicellulose samples.74 Indeed, the used xylan contained small amounts of Na+ (11.66 mg g−1 xylan) and K+ (0.14 mg g−1 xylan) (Table S1, ESI†). The pH of the reaction solution and inorganic impurities could affect the activity of Ir–ReOx/SiO2.
Table 1 Conversion of xylan to n-pentane over Ir–ReOx/SiO2 + HZSM-5 catalysts with different amount of H2SO4
Entry |
H2SO4/mg |
Conversion/% |
Yield/% |
Loss of carbon balance |
pH |
n-Pentane |
Other pentanes |
n-Hexane |
Other hexanes |
Cyclic ethers |
PeOHs |
HxOHs |
C1–C4 alkanes |
Other hexanes: 2-methylpentane and 3-methylpentane, Other pentanes: 2-methylbutane and cyclopentane, HxOH: hexanol; PeOH: pentanol; cyclic ethers: 2-methyltetrahydrofuran, tetrahydropyran, 2,5-dimethyltetrahydrofuran and 2-methyltetrahydropyran; C1–C4 alkanes: methane, ethane, propane and n-butane. Sugars and sugar alcohols were not detected in all entries. Reaction conditions: TCI xylan: 0.5 g, H2O: 9.5 g, Ir–ReOx/SiO2: 0.15 g, HZSM-5: 0.06 g, n-dodecane: 4 ml, 463 K, initial H2: 6 MPa, 24 h. |
1 |
0 |
95 |
3.0 |
0.2 |
2.1 |
0.0 |
0.0 |
0.0 |
0.0 |
2.9 |
86 |
6.94 |
2 |
10 |
94 |
1.0 |
0.4 |
0.0 |
0.0 |
0.5 |
4.2 |
0.1 |
1.2 |
86 |
5.85 |
3 |
20 |
94 |
6.3 |
0.6 |
0.6 |
0.1 |
1.3 |
15 |
2.0 |
3.8 |
65 |
4.64 |
4 |
30 |
96 |
64 |
1.2 |
5.9 |
0.5 |
1.4 |
0.6 |
0.0 |
6.4 |
17 |
2.04 |
5 |
40 |
98 |
70 |
2.5 |
7.3 |
0.9 |
0.8 |
0.9 |
0.0 |
5.2 |
10 |
1.82 |
6 |
50 |
95 |
70 |
3.2 |
7.4 |
0.7 |
3.9 |
0.0 |
0.0 |
5.8 |
4.2 |
1.65 |
7 |
60 |
97 |
62 |
2.9 |
7.8 |
0.7 |
3.2 |
0.0 |
0.3 |
4.2 |
16 |
1.45 |
8 |
70 |
97 |
57 |
2.9 |
7.0 |
0.6 |
3.4 |
0.2 |
0.3 |
4.2 |
21 |
1.34 |
To decrease the pH of the reactant solution, different amounts of H2SO4 were added. The yield of n-pentane increased and the pH value decreased quickly when the amount of H2SO4 was increased to 30 mg (Table 1, entries 1–4). The “conversion” of xylan was ≥94% for all entries, and the difference from 100% was probably due to the formation of a solid product. This indicates that the C–O hydrogenolysis activity of the Ir–ReOx/SiO2 catalyst is increased by decreasing the pH from ∼7 to 2. On further increasing the amount of H2SO4, the pH of filtrate after reaction decreased slowly. The yield of n-pentane showed a volcanic type distribution when the H2SO4 amount was further increased (Table 1, entries 4–8): the highest yield of n-pentane could reach about 70% when the added H2SO4 amount was 40–50 mg and the pH of filtrate was in the range of 1.65–1.82 (Table 1, entries 5 and 6). Further decreasing the pH of the filtrate (H2SO4 amount ≥60 mg) decreased the yield of n-pentane (Table 1, entries 7 and 8). The loss of carbon balance increased, which could be explained by the formation of humins from xylan in strong acidic solution. The above results indicate that controlling the pH of the reactant solution is very important for the production of n-pentane in high yield from xylan by using the Ir–ReOx/SiO2 catalyst. It should be noted that when the reaction was conducted without xylan at 463 K for 24 h, no n-dodecane was converted. As a result, it is verified that the organic solvent is inert under the reaction conditions.
3.2 Time dependence on conversion of xylan to n-pentane
The time course of the reaction over Ir–ReOx/SiO2 + HZSM-5 with 40 mg H2SO4 is shown in Fig. 1. Almost all of the xylan was converted during the heating to 463 K. The main product just after heating was xylitol, which is the product of hydrolysis + hydrogenation of xylan. Then xylitol was further converted into n-pentane via polyols (undetected products = loss of carbon balance) and pentanols. The yield of n-pentane increased gradually with the reaction time. The yield of n-pentane reached about 70% when most of the detected oxygenates disappeared (24 h). These data support the reaction route shown in Scheme 1. First, H2SO4 and/or HZSM-5 hydrolyze xylan to xylose in hot water and then xylose is hydrogenated into xylitol over the Ir–ReOx/SiO2 catalyst at the beginning of this reaction. Too low pH facilitates the formation of humins from xylan and decreases the amount of xylitol and the hydrogenolysis products. Next, hydrogenolysis of xylitol over Ir–ReOx/SiO2 and HZSM-5 in H2SO4 solution proceeds step-by-step to the end product of n-pentane. Although the reaction pathway of production of n-pentane from xylan was similar to that of production of n-hexane from cellulose, the rate-determining step was different: in the conversion of xylan, almost of all the xylan can be converted into xylitol at the beginning of the reaction and then xylitol was converted into n-pentane gradually. However, in the conversion of cellulose even after ball-milling, the conversion of cellulose and n-hexane yield is similar and the hydrolysis of cellulose into water-soluble sugars is the rate-determining step.61 Xylan has a random, amorphous structure which is different from cellulose that has a robust crystalline structure, and xylan has lower degree of polymerization than cellulose. The addition of a small amount of H2SO4 could promote the hydrolysis rate of xylan, and the hydrolysis rate of xylan into xylose becomes faster than the hydrogenolysis rate of formed xylitol over the Ir–ReOx/SiO2 catalyst. Under this situation, xylose can be converted to furfural by acid catalyzed dehydration, and high concentration of furfural can give humins by polymerization. Therefore, the rapid hydrogenation of xylose to xylitol is important in order to suppress the formation of furfural and subsequent polymerization to humins. Fortunately, it has been reported that the Ir–ReOx/SiO2 catalyst has high activity in the hydrogenation of aldehyde,72 which can contribute to the suppression of the reaction route via furfural. On the other hand, when xylitol was used as the substrate, over 60% yield of n-pentane can be produced in the same reaction system in only 0.5 h (Table 2, entries 1–4). The conversion of xylitol was much slower when it was in situ produced from xylan (Fig. 1). To clarify the reason for this, two impacts were taken into consideration: the mineral substances in xylan and humins formed during the reaction.
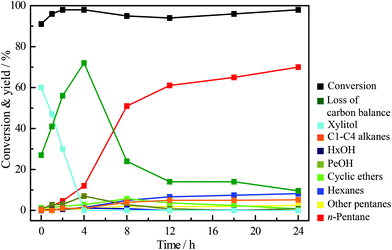 |
| Fig. 1 Time dependence of conversion of xylan to n-pentane over Ir–ReOx/SiO2 + HZSM-5 + H2SO4. Reaction conditions: TCI xylan: 0.5 g, H2O: 9.5 g, Ir–ReOx/SiO2: 0.15 g, HZSM-5: 0.06 g, H2SO4: 40 mg, n-dodecane: 4 ml, 463 K, initial H2: 6 MPa. | |
Table 2 The effect of K+, Na+ and H+ on Ir–ReOx/SiO2 + HZSM-5 catalysts for conversion of xylitol to n-pentane
Entry |
Additive/mg |
pH |
Molar ratio |
Conversion/% |
Yield/% |
Loss of carbon balance |
K+ |
Na+ |
H2SO4 |
(K+ or Na+)/Re |
H2SO4/(Na+ or K+) |
n-Pentane |
Other pentanes |
Cyclic ethers |
1-PeOH |
2- and 3-PeOH |
C1–C4 alkanes |
Other pentanes: 2-methylbutane and cyclopentane; PeOH: pentanol; cyclic ethers: 2-methyltetrahydrofuran, tetrahydropyran; C1–C4 alkanes: methane, ethane, propane and n-butane. Reaction conditions: xylitol: 0.5 g, H2O: 9.5 g, Ir–ReOx/SiO2: 0.15 g, HZSM-5: 0.06 g, additive: Na2SO4, K2SO4 and/or H2SO4, n-dodecane: 4 ml, 463 K, initial H2: 6 MPa, 0.5 h. Without HZSM-5. |
1 |
0 |
0 |
0 |
2.99 |
— |
— |
>99 |
52 |
0.6 |
8.3 |
6.6 |
1.8 |
2.3 |
28 |
2 |
0 |
0 |
10 |
1.88 |
— |
— |
>99 |
63 |
0.5 |
7.4 |
4.2 |
1.0 |
2.5 |
21 |
3 |
0 |
0 |
20 |
1.59 |
— |
— |
>99 |
68 |
0.6 |
7.4 |
2.9 |
0.9 |
2.9 |
18 |
4 |
0 |
0 |
40 |
1.30 |
— |
— |
>99 |
74 |
1.2 |
7.1 |
2.6 |
0.0 |
2.7 |
12 |
5 |
0.2 |
0 |
0 |
2.99 |
0.08 |
— |
>99 |
49 |
0.4 |
7.9 |
6.8 |
2.4 |
2.3 |
31 |
6 |
0.4 |
0 |
0 |
2.90 |
0.16 |
|
>99 |
45 |
0.3 |
8.0 |
9.4 |
2.7 |
2.2 |
33 |
7 |
0.6 |
0 |
0 |
2.93 |
0.25 |
|
>99 |
27 |
0.2 |
6.3 |
11 |
2.7 |
1.4 |
52 |
8 |
0 |
0.2 |
0 |
2.89 |
0.14 |
— |
>99 |
52 |
0.4 |
7.6 |
7.0 |
2.0 |
2.6 |
28 |
9 |
0 |
0.4 |
0 |
2.88 |
0.28 |
— |
>99 |
45 |
0.3 |
7.3 |
9.0 |
3.2 |
2.2 |
33 |
10 |
0 |
1.0 |
0 |
3.11 |
0.70 |
— |
>99 |
15 |
0.0 |
3.0 |
4.9 |
5.4 |
1.1 |
71 |
11 |
0 |
2.0 |
0 |
3.11 |
1.4 |
— |
>99 |
4.9 |
0.0 |
2.4 |
7.0 |
5.8 |
0.7 |
79 |
12 |
0 |
4.0 |
0 |
3.02 |
2.8 |
— |
83 |
2.5 |
0.0 |
0.3 |
2.1 |
3.0 |
0.5 |
75 |
13 |
0 |
6.0 |
0 |
3.02 |
4.2 |
— |
80 |
2.0 |
0.0 |
0.0 |
1.3 |
2.5 |
0.5 |
74 |
14 |
0 |
8.0 |
0 |
2.94 |
5.6 |
— |
73 |
1.1 |
0.0 |
0.0 |
0.9 |
1.8 |
0.3 |
69 |
15 |
0 |
6.0 |
5 |
2.13 |
4.2 |
0.20 |
>99 |
6.0 |
0.0 |
1.8 |
4.0 |
4.5 |
0.7 |
83 |
16 |
0 |
6.0 |
10 |
1.89 |
4.2 |
0.39 |
>99 |
12 |
0.1 |
3.1 |
6.1 |
3.5 |
0.8 |
74 |
17 |
0 |
6.0 |
20 |
1.61 |
4.2 |
0.8 |
>99 |
42 |
0.3 |
6.7 |
8.9 |
2.0 |
1.8 |
38 |
18 |
0 |
6.0 |
40 |
1.39 |
4.2 |
1.5 |
>99 |
63 |
0.8 |
7.1 |
3.3 |
0.9 |
2.4 |
23 |
19 |
0 |
6.0 |
60 |
1.24 |
4.2 |
2.4 |
>99 |
63 |
0.7 |
6.7 |
3.6 |
0.6 |
2.5 |
23 |
20 |
0.6 |
0 |
40 |
1.36 |
0.25 |
27 |
>99 |
63 |
0.7 |
8.0 |
6.4 |
2.2 |
2.2 |
17 |
21a |
0 |
0 |
40 |
1.32 |
— |
— |
>99 |
56 |
0.1 |
3.8 |
3.6 |
8.3 |
1.4 |
27 |
3.3 The effect of mineral substance
In typical reaction conditions, 0.07 mg K+ and 5.83 mg Na+ derived from xylan were present in the reaction mixture (Table S1, ESI†). Herein, to investigate the effect of K+ and Na+ on the catalytic performance, xylitol was chosen as the substrate, since xylitol is the primary intermediate in the conversion of xylan. The K+ and Na+ precursors were K2SO4 and Na2SO4, respectively. The effect of K+ and Na+ addition on the xylitol hydrogenolysis is shown in Table 2 (Table 2, entries 5–7 and 8–14, respectively). The yield of n-pentane decreased with increasing amount of Na+ or K+. The conversion of xylitol decreased below 90% when the amount of Na+ was over 4.0 mg. The amount of loss of carbon balance, probably polyols, was increased. In our previous work, we found that two different hydrogenolysis mechanisms contributed to the last step of the production of n-pentane; i.e. hydrogenolysis of mono-alcohols.50 The hydrogenolysis of 1-pentanol proceeds by direct hydrogenolysis catalyzed by Ir–ReOx/SiO2 while the hydrogenolysis of internal mono-alcohols (2- and 3-pentanol) proceeds by the dehydration + hydrogenation mechanism. The addition of HZSM-5 greatly accelerates the hydrogenolysis of internal mono-alcohols by promoting the dehydration. This can be supported by the higher yields of 2- and 3-pentanols over Ir–ReOx/SiO2 + H2SO4 without the addition of HZSM-5 (Table 2, entries 4 and 21). Here, the yield of 1-pentanol increased as the amount of Na+ or K+ increased from 0 mg to 0.6 mg. The amount of 2- and 3-pentanol remained small. These data indicate that Na+ or K+ mainly affect the direct hydrogenolysis pathway of Ir–ReOx/SiO2. Comparison between the data with a similar K+/Re or Na+/Re molar ratio showed that K+ has a stronger deactivation effect (Table 2, entry pairs 6 and 8, 7 and 9). However, the K+ content in xylan was much smaller than Na+ and thus the effect of Na+ could be much larger in xylan conversion. It was reported that the hydroxorhenium site (Re–OH) is the adsorption site of substrates which is very important for the direct C–O hydrogenolysis activity.64–71 The addition of Na+ or K+ could decrease the number of hydroxorhenium sites by ion exchange which decreases the catalytic activity (Scheme 2). Davis’ group has very recently reported that the high concentration of sodium ions (100 mM NaCl) could poison the Pt–Re/C catalyst in the hydrogenolysis of glycerol by exchange with the acidic protons,76 which could support our results. They also referred that the negative effect of Cl− on a Pt metal catalyst could also be inevitable.75 On the other hand, the number of hydroxorhenium sites can be increased by the addition of H2SO4 (Scheme 2) and the presence of hydroxo groups on the surface of the ReOx clusters has been suggested by the characterization of Ir–ReOx/SiO2 by using Re L3-edge extended X-ray absorption fine structure (EXAFS) analysis.64–71 Therefore, the effect of different amounts of H2SO4 was investigated. The amount of Na+ was fixed at 6 mg in the reaction solution which is almost the same in xylan conversion (Table 2, entries 11–18). Indeed, the yield of n-pentane increased when the amount of H2SO4 was increased, especially with the pH value lower than 1.6. Comparison with the reaction tests without Na+ (Table 2, entries 1–4) showed that the difference in n-pentane yield between runs with and without Na+ shrinked by H+ addition. This indicates that H+ and Na+ interact with the Re site competitively (Scheme 2) and the addition of large amounts of H2SO4 could increase the number of active sites (hydroxorhenium site (Re–OH)) that promoted hydrogenolysis activity of the Ir–ReOx/SiO2 catalyst. However, even at pH < 1.4 (H2SO4 amount ≥40 mg), the yield of n-pentane was still lower in the presence of Na+ or K+. As discussed in section 3.1, too much H2SO4 (pH < 1.65) promotes the formation of humins and is not favorable in xylan conversion. The conversion of xylitol shown in Fig. 1, where xylitol was in situ produced from xylan, was slowed down significantly by the presence of Na+. The amount of Na+ content in xylan substrate can much affect the results.
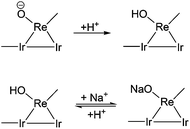 |
| Scheme 2 The formation of hydroxorhenium site and ion-exchange with Na+ or H+. | |
We tested two other xylan samples. One was purchased from Wako, and it has a similar amount of Na+. The other one was purchased from Sigma-Aldrich, and it has a slightly higher Na+ content. The reaction results are shown in Table 3. Wako xylan showed almost the same yields as TCI xylan. On the other hand, Sigma-Aldrich xylan gave lower n-pentane yield than TCI xylan. Increasing the amount of H2SO4 from 40 mg to 50 mg increased the n-pentane yield of Sigma-Aldrich xylan to a value comparable to that obtained from TCI or Wako xylan. Therefore, adjusting the amount of H2SO4 for each xylan substrate is essential in obtaining a good yield of n-pentane.
Table 3 Conversion of different xylan to n-pentane over Ir–ReOx/SiO2 + HZSM-5 catalysts with different amount of H2SO4
Entry |
Xylan |
Na+/mgNa+ g−1 xylan |
K+/mgK+ g−1xylan |
Conversion/% |
Yield/% |
Loss of carbon balance |
pH |
n-Pentane |
Other pentanes |
n-Hexane |
Other hexanes |
Cyclic ethers |
PeOHs |
HxOHs |
C4–C1 alkanes |
Other hexanes: 2-methylpentane and 3-methylpentane, Other pentanes: 2-methylbutane and cyclopentane, HxOH: hexanol; PeOH: pentanol; cyclic ethers: 2-methyltetrahydrofuran, tetrahydropyran, 2,5-dimethyltetrahydrofuran and 2-methyltetrahydropyran; C1: methane; C2: ethane; C3: propane; C4: n-butane; reaction conditions: xylan: 0.5 g, H2O: 9.5 g, Ir–ReOx/SiO2: 0.15 g, HZSM-5: 0.06 g, H2SO4: 40 mg, n-dodecane: 4 ml, 463 K, initial H2: 6 MPa, 24 h. H2SO4 50 mg. |
1 |
TCI |
11.66 |
0.14 |
98 |
70 |
2.5 |
7.3 |
0.9 |
0.8 |
0.9 |
0.0 |
5.2 |
10 |
1.82 |
2 |
Wako |
11.33 |
0.15 |
96 |
69 |
1.6 |
6.9 |
0.9 |
1.1 |
0.0 |
0.0 |
5.3 |
11 |
1.86 |
3 |
Sigma-Aldrich |
13.59 |
0.17 |
95 |
54 |
2.0 |
4.3 |
0.3 |
0.7 |
0.0 |
0.0 |
5.6 |
28 |
2.15 |
4a |
Sigma-Aldrich |
13.59 |
0.17 |
96 |
66 |
2.5 |
7.4 |
1.0 |
1.8 |
0.0 |
0.0 |
4.2 |
13 |
1.85 |
3.4 Catalyst stability
Table 4 shows the results of the activity tests of the reused Ir–ReOx/SiO2 (Re/Ir = 2) + HZSM-5 catalysts. The method of the catalyst reuse was as follows: the solid catalysts (Ir–ReOx/SiO2 and HZSM-5) were recycled by centrifugation while H2SO4 in aqueous solution was discarded. The recycled solid catalysts were washed with water and dried at 383 K for 12 h and calcined in air at 773 K for 3 h. Before the activity test, the reduction pretreatment was carried out in the same way as the case of the fresh catalyst. The yield of n-pentane slightly decreased from 70% to 66% after four consecutive runs (Table 4, entries 1–4). Inductively coupled plasma (ICP) analysis of the reaction solution after the solid catalysts had been removed by filtration showed almost no Ir (<0.01%) and slight Re (0.92 wt%) leaching. The XRD peak patterns (ESI. Fig. S1†) that were assigned to HZSM-5 were almost the same even after the fourth run while the peaks for the Ir metal became sharper. The average size of Ir metal particle increased from 2.2 nm to 2.9 nm calculated by the Scherrer equation.77 Therefore, the slight decrease of the yield of n-pentane and increase of the yields of cyclic ethers could be attributed to the aggregation of metals during the reaction and recalcination that lowered the hydrogenolysis activity of the Ir–ReOx/SiO2 catalyst. It should be noted that the step of calcination is very important for the catalyst reuse. The yield of n-pentane dropped from 70% to 23% after the 1st reuse over the catalysts without calcination (Table 4, entries 1 and 5). The result of TG-DTA analysis showed that about 4 wt% humins (1.3 wt% based on the substrate) were formed on the solid catalysts after the first time reaction (ESI, Fig. S2a†). The humins covered the active site of Ir–ReOx/SiO2 and HZSM-5 that led to the catalyst deactivation. To clarify the humins formed during the hydrolysis and hydrogenation step or the hydrogenolysis step, TG-DTA analysis was also performed by using the recovered solid catalysts after 0.5 h reaction (ESI, Fig. S2b†). The amount of humins was almost the same as that of the catalysts after 24 h reaction, indicating that the most of the humins were formed at the step of hydrolysis + hydrogenation of xylan. In addition, hydrogenolysis of xylitol over the catalysts after 0.5 h xylan reaction with calcination and without calcination was performed (ESI, Table S4†). The yield of n-pentane was much lower over the catalysts without calcination compared to that over the fresh catalysts, while the yield of n-pentane was almost maintained over the catalysts with calcination. These results indicate that the humins formed at the beginning of conversion of xylan covered the active site of Ir–ReOx/SiO2 and HZSM-5 that decreased the hydrogenolysis performance.
Table 4 Reusability of Ir–ReOx/SiO2 + HZSM-5 catalysts for conversion of xylan to n-pentane
Entry |
Usage |
Conversion/% |
Yield/% |
Loss of carbon balance |
n-Pentane |
Other pentanes |
n-Hexane |
Other hexanes |
Cyclic ethers |
PeOHs |
HxOHs |
C4–C1 alkanes |
Other hexanes: 2-methylpentane and 3-methylpentane, other pentanes: 2-methylbutane and cyclopentane, HxOH: hexanol; PeOH: pentanol; cyclic ethers: 2-methyltetrahydrofuran, tetrahydropyran, 2,5-dimethyltetrahydrofuran and 2-methyltetrahydropyran; C1–C4 alkanes: methane, ethane, propane and n-butane. Reaction conditions: TCI xylan: 0.5 g, H2O: 9.5 g, Ir–ReOx/SiO2: 0.15 g, HZSM-5: 0.06 g, H2SO4: 40 mg, n-dodecane: 4 ml, 463 K, initial H2: 6 MPa, 24 h. Without calcination before reuse. |
1 |
1 |
98 |
70 |
2.5 |
7.3 |
0.9 |
0.8 |
0.9 |
0.0 |
5.2 |
10 |
2 |
2 |
97 |
69 |
2.3 |
7.0 |
0.7 |
1.6 |
1.1 |
0.2 |
5.3 |
9.8 |
3 |
3 |
>99 |
67 |
2.7 |
6.1 |
0.4 |
4.3 |
0.0 |
0.4 |
5.2 |
14 |
4 |
4 |
97 |
66 |
2.7 |
6.0 |
0.4 |
4.6 |
0.1 |
0.3 |
4.9 |
12 |
5 |
2a |
99 |
23 |
1.3 |
1.9 |
0.0 |
5.9 |
7.3 |
0.7 |
1.3 |
57 |
3.5 Production of pentanols from xylan over Ir–ReOx/SiO2 + H2SO4 in a biphasic solvent system
In our previous work, the Ir–ReOx/SiO2 catalyst combined with H2SO4 was effective in the production of hexanols from mechanocatalytically depolymerized cellulose.59 The keys to high hexanols yield are lowering the reaction temperature, increasing cellulose reactivity (for such low reaction temperature), and a large amount of organic solvent for extraction. Here, we used Ir–ReOx/SiO2 + H2SO4 and a larger amount of n-dodecane (20 ml) for the conversion of xylan into pentanols at lower reaction temperature (413 K). The effect of H2SO4 amount was investigated and the results are shown in Table 5. The yield of pentanols showed a volcanic type distribution when the amount of H2SO4 was in the range of 30–60 mg (Table 5). The main products were 2-pentanol and 3-pentanol. A large amount of polyols still existed when the amount of H2SO4 was 30 mg (Table 5, entry 1), reflected by the low C–O hydrogenolysis activity of Ir–ReOx/SiO2 under this reaction condition. The yield of n-pentane increased as the addition of H2SO4 increased, indicating that over-hydrogenolysis proceeded at lower pH (Table 5, entries 1–4). It was reported that hydrogenolysis of 2- and 3-pentanols proceeds by the tandem dehydration and hydrogenation mechanism.50 The lower pH facilitated the dehydration of 2- and 3-pentanols thereby further hydrogenated to n-pentane over Ir–ReOx/SiO2 (ESI, Table S5†). The yield of pentanols could reach about 32% when the added H2SO4 amount was 40–50 mg (Table 5, entries 2 and 3). The time course of the reaction is shown in Table S6 (ESI†), and the highest yield of pentanols was obtained at this reaction time. The above results indicate that controlling the acidity of the reactant solution is also very important for production of pentanol in high yield from xylan by using the Ir–ReOx/SiO2 catalyst, and the optimum H2SO4 amount is similar to that in n-pentane production. The production of pentanols from the other xylans was also tested (Table 5, entries 5–7). Similarly to n-pentane production, the yield of pentanols from Wako xylan was almost the same as that from TCI xylan. The yield of pentanols from Sigma-Aldrich xylan was lower than those from TCI or Wako xylans, and it was increased to a comparable value by adjusting the H2SO4 amount.
Table 5 Conversion of xylan to pentanols over Ir–ReOx/SiO2 catalyst + H2SO4
Entry |
H2SO4/mg |
Conversion/% |
Yield/% |
Loss of carbon balance |
pH |
Sum of PeOHs |
1-PeOH |
2-PeOH |
3-PeOH |
HxOHs |
Pentanes |
Hexanes |
C1–C4 alkanes |
Cyclic ethers |
PeOH: pentanol; HxOH: hexanol; pentanes: n-pentane, 2-methylbutane and cyclopentane, hexanes: n-hexane, 2-methylpentane and 3-methylpentane, C1–C4 alkanes: methane, ethane, propane and n-butane; cyclic ethers: 2-methyltetrahydrofuran, tetrahydropyran, 2,5-dimethyltetrahydrofuran and 2-methyltetrahydropyran; reaction conditions: TCI xylan: 0.5 g, H2O: 9.5 g, Ir–ReOx/SiO2: 0.15 g, n-dodecane: 20 ml, 413 K, initial H2: 6 MPa, 144 h. Wako xylan. Sigma-Aldrich xylan. |
1 |
30 |
97 |
20 |
3.4 |
7.0 |
9.9 |
2.4 |
6.9 |
0.8 |
1.2 |
0.7 |
64 |
2.05 |
2 |
40 |
95 |
32 |
1.3 |
13 |
17 |
3.7 |
22 |
1.7 |
1.8 |
2.0 |
33 |
1.83 |
3 |
50 |
97 |
32 |
0.3 |
14 |
18 |
4.4 |
30 |
2.3 |
1.9 |
2.2 |
24 |
1.66 |
4 |
60 |
94 |
22 |
0.3 |
9 |
12 |
4.8 |
42 |
3.5 |
1.8 |
2.6 |
18 |
1.57 |
5a |
40 |
97 |
31 |
0.7 |
15 |
16 |
3.9 |
22 |
1.7 |
1.8 |
1.9 |
35 |
1.79 |
6b |
40 |
97 |
20 |
5.5 |
7.3 |
6.7 |
2.6 |
7.9 |
0.7 |
0.9 |
1.4 |
64 |
1.87 |
7b |
50 |
96 |
29 |
0.4 |
12 |
16 |
3.7 |
26 |
2.0 |
1.4 |
1.9 |
33 |
1.71 |
3.6 Production of xylitol from xylan over Ir–ReOx/SiO2 + H2SO4 in the aqueous phase
At the beginning of the reactions in production of n-pentane or pentanols from xylan, over 60% yield of xylitol was obtained, which motivated us to convert xylan to xylitol in high yield. To obtain a higher yield of xylitol, protection of the formed xylitol from hydrogenolysis into other products is the key. This can be done in two ways. The first one is by lowering the reaction temperature with a short reaction time. The other one is by decreasing the amount of H2SO4 in order to decrease the number of hydroxorhenium sites (Re–OH). In the production of xylitol, only water was used as a solvent because xylitol is soluble in water. The results are shown in Table 6. First, the effect of the amount of H2SO4 was investigated (Table 6, entries 1–4). The yield of xylitol increased quickly with the amount of H2SO4 increasing from 10 to 30 mg, indicating the importance of H2SO4 for hydrolysis of xylan. Further increase in the amount of H2SO4 slightly decreased the yield of xylitol, which can be attributed to the hydrogenolysis reaction. Next, the effect of reaction temperature was also investigated (Table 6, entries 6–9). The loss of carbon balance was higher at lower reaction temperature (Table 6, entry 6), which can be explained by the low hydrolysis rate. The yield of arabitol was higher at higher reaction temperature, indicating that the isomerization reaction proceeded. The highest yield of xylitol could reach 79% when the reaction temperature was 403 K (Table 6, entry 7). The performances of different commercial noble metals on carbon catalysts (Ru/C, Pt/C, Rh/C and Pd/C) were compared with that of Ir–ReOx/SiO2 (ESI, Table S7†). The yield of xylitol (≤61%) was lower than that over the Ir–ReOx/SiO2 catalyst (79%). In the case of Pd/C, the yield of xylitol was higher than other carbon-supported noble metal catalysts; however, it is still lower than that over Ir–ReOx/SiO2. The 13% yield of xylose on Pd/C can be explained by the lower hydrogenation activity of Pd/C than that of Ir–ReOx/SiO2, which is also supported by our previous work that Ir–ReOx/SiO2 has high activity of the hydrogenation of the formyl group in unsaturated aldehydes.73 In the case of Ru/C, a very low yield of xylose indicates that Ru/C has high hydrogenation activity of xylose, however, the side reaction of the isomerization of xylitol to arabitol proceeds and this can decrease the yield of xylitol significantly. This behavior is explained by the high ability of Ru/C in the dehydrogenation of CH–OH because the isomerization reaction proceeds in the dehydrogenation + hydrogenation route and at the same time, these tendencies indicate that Ir–ReOx/SiO2 has much lower isomerization activity, which is connected to high xylitol yield on Ir–ReOx/SiO2. The very low isomerization activity of Ir–ReOx/SiO2 and the high isomerization performance of Ru/C are also supported in the case of the hydrogenolysis of erythritol.68 In the cases of Pt/C and Rh/C, the yield of xylose was high, which means the low activity of these catalysts in the hydrogenation of xylose. As a result, it is concluded that Ir–ReOx/SiO2 is very efficient for the production of xylitol by hydrolysis + hydrogenation of xylan.
Table 6 Conversion of xylan to xylitol over Ir–ReOx/SiO2 catalyst + H2SO4
Entry |
H2SO4/mg |
T/K |
Conversion/% |
Yield/% |
Loss of carbon balance |
pH |
Xylitol |
Arabitol |
Sorbitol |
Alkanes |
Alkanes: C1–C6 alkanes. Reaction conditions: TCI xylan: 0.5 g, H2O: 9.5 g, Ir–ReOx/SiO2: 0.15 g, initial H2: 6 MPa, 12 h. |
1 |
10 |
413 |
92 |
18 |
0.6 |
0.3 |
0.1 |
72 |
4.42 |
2 |
15 |
413 |
92 |
47 |
0.9 |
0.7 |
0.2 |
43 |
4.01 |
3 |
20 |
413 |
92 |
74 |
0.8 |
1.3 |
0.4 |
16 |
3.01 |
4 |
30 |
413 |
93 |
78 |
1.0 |
2.4 |
0.5 |
11 |
2.17 |
5 |
40 |
413 |
91 |
73 |
1.0 |
3.4 |
0.6 |
13 |
1.87 |
6 |
30 |
393 |
94 |
74 |
0.6 |
1.0 |
0.1 |
18 |
2.17 |
7 |
30 |
403 |
97 |
79 |
0.8 |
2.3 |
0.1 |
15 |
2.17 |
8 |
30 |
423 |
93 |
75 |
1.3 |
2.9 |
0.3 |
13 |
2.17 |
The production of xylitol from other xylans was also tested (Table 7). In contrast to the cases of n-pentane or pentanols production, all the three xylans can be converted to xylitol in similar high yields. The active site of the hydrogenation is suggested to be the interface between the Ir metal and ReOx species,73 and the substrate is probably coordinated to the Re atom with the oxygen atom in the C
O bond. The number of hydroxorhenium sites may not affect the activity.
Table 7 Conversion of different xylan to xylitol over Ir–ReOx/SiO2 catalyst + H2SO4
Entry |
Xylan |
Conversion/% |
Yield/% |
Loss of carbon balance |
pH |
Xylitol |
Arabitol |
Sorbitol |
Alkanes |
Alkanes: C1–C6 alkanes. Reaction conditions: xylan: 0.5 g, H2O: 9.5 g, Ir–ReOx/SiO2: 0.15 g, H2SO4: 30 mg, initial H2: 6 MPa, 413 K, 12 h. |
1 |
TCI |
93 |
78 |
1.0 |
2.4 |
0.5 |
11 |
2.17 |
2 |
Wako |
92 |
77 |
0.9 |
2.4 |
0.2 |
11 |
2.26 |
3 |
Sigma-Aldrich |
93 |
78 |
0.2 |
2.1 |
0.1 |
13 |
2.36 |
4. Conclusions
Ir–ReOx/SiO2 combined with acids was very effective in the conversion of hemicellulose (xylan) into three different products, n-pentane, pentanols and xylitol, by simply adjusting the reaction temperature, amounts of organic solvents and reaction time. 70% yield of n-pentane can be produced by using Ir–ReOx/SiO2 combined with HZSM-5 + H2SO4 in a biphasic solvent system (4 ml n-dodecane + 9.5 ml H2O) at 463 K for 24 h. 32% yield of pentanols can be produced by using Ir–ReOx/SiO2 combined with H2SO4 in a biphasic solvent system (20 ml n-dodecane + 9.5 ml H2O) at 413 K for 144 h. 79% yield of xylitol can be produced by using Ir–ReOx/SiO2 combined with H2SO4 in the aqueous phase at 413 K for 12 h. Adjusting the amount of H2SO4 is also very important, and especially for n-pentane or pentanols production. The optimum amount of H2SO4 depended on the amount of mineral ions in the xylan samples.
The conversion of xylan and the yield of n-pentane were almost maintained during three repeated tests when the catalyst was calcined during the regeneration procedure. The humins, formed at the hydrolysis + hydrogenation step during xylan conversion, covered the active site of Ir–ReOx/SiO2 and HZSM-5 to decrease C–O hydrogenolysis performance of Ir–ReOx/SiO2 in part. The calcination step for removing the humins is very important for the catalyst reuse.
The mineral ions (such as Na+ and K+) in xylan also decrease C–O hydrogenolysis performance of the Ir–ReOx/SiO2 catalyst severely because the mineral ions decreased the number of active sites of Ir–ReOx/SiO2 (hydroxorhenium site (Re–OH)) by ion exchange. The addition of H2SO4 not only maintained the acidic reaction environment, which is beneficial for the Ir–ReOx/SiO2 catalyst work, by neutralizing the residual alkali of xylan after being isolated from lignocellulose, but also maintained and enhanced the C–O hydrogenolysis activity of Ir–ReOx/SiO2 through increasing the number of hydroxorhenium sites by the competitive adsorption of protons on the Re site with mineral ions. However, too much of H2SO4 decreased the yields of the target compounds by humins formation from xylan and/or over hydrogenolysis.
Acknowledgements
This work was in part supported by the JSPS KAKENHI 26249121. Sibao Liu thanks the China Scholarship Council (CSC) for the financial support.
References
- G. W. Huber, S. Iborra and A. Corma, Chem. Rev., 2006, 106, 4044–4098 CrossRef CAS PubMed.
- J. C. Serrano-Ruiz, R. Luque and A. Sepulveda-Escribano, Chem. Soc. Rev., 2011, 40, 5266–5281 RSC.
- A. Corma, S. Iborra and A. Velty, Chem. Rev., 2007, 107, 2411–2502 CrossRef CAS PubMed.
- M. Schlaf, Dalton Trans., 2006, 4645–4653 RSC.
- C.-H. Zhou, X. Xia, C.-X. Lin, D.-S. Tong and J. Beltramini, Chem. Soc. Rev., 2011, 40, 5588–5617 RSC.
- Y. Nakagawa, S. Liu, M. Tamura and K. Tomishige, ChemSusChem, 2015, 8, 1114–1132 CrossRef CAS PubMed.
- M. Besson, P. Gallezot and C. Pinel, Chem. Rev., 2014, 114, 1827–1870 CrossRef CAS PubMed.
- M. J. Climent, A. Corma and S. Iborra, Green Chem., 2014, 16, 516–547 RSC.
- H. Kobayashi and A. Fukuoka, Green Chem., 2013, 15, 1740–1763 RSC.
- Y. Nakagawa, M. Tamura and K. Tomishige, ACS Catal., 2013, 3, 2655–2668 CrossRef CAS.
- J. A. Geboers, S. V. Vyver, R. Ooms, B. O. Beeck, A. P. Jacobs and B. F. Sels, Catal. Sci. Technol., 2011, 1, 714–726 Search PubMed.
- S. V. Vyver, J. Geboers, P. A. Jacobs and B. F. Sels, ChemCatChem, 2011, 3, 82–94 CrossRef.
- H. Kobayashi, T. Komanoya, S. K. Guha, K. Hara and A. Fukuoka, Appl. Catal., A, 2011, 409–410, 13–20 CrossRef CAS.
- M. Yabushita, H. Kobayashi and A. Fukuoka, Appl. Catal., B, 2014, 145, 1–9 CrossRef CAS.
- J. Zakzeski, P. C. A. Bruijnincx, A. L. Jongerius and B. M. Weckhuysen, Chem. Rev., 2010, 110, 3552–3599 CrossRef CAS PubMed.
- C. Xu, R. A. D. Arancon, J. Labidi and R. Luque, Chem. Soc. Rev., 2014, 43, 7485–7500 RSC.
- A. J. Ragauskas, G. T. Beckham, M. J. Biddy, R. Chandra, F. Chen, M. F. Davis, B. H. Davison, R. A. Dixon, P. Gilna, M. Keller, P. Langan, A. K. Naskar, J. N. Saddler, T. J. Tschaplinski, G. A. Tuskan and C. E. Wyman, Science, 2014, 344, 709 CrossRef CAS PubMed.
- S. V. Bosch, W. Schutyser, R. Vanholme, T. Driessen, S.-F. Koelewijn, T. Renders, B. De Meester, W. J. J. Huijgen, W. Dehaen, C. M. Courtin, B. Lagrain, W. Boerjan and B. F. Sels, Energy Environ. Sci., 2015, 8, 1748–1763 Search PubMed.
- S. V. Bosch, W. Schutyser, S.-F. Koelewijn, T. Renders, C. M. Courtin and B. F. Sels, Chem. Commun., 2015, 51, 13158–13161 RSC.
- P. M. Arvela, T. Salmi, B. Holmbom, S. Willför and D. Yu. Murzin, Chem. Rev., 2011, 111, 5638–5666 CrossRef PubMed.
- G. Hilpmann, N. Becher, F.-A. Pahner, B. Kusema, P. Mäki-Arvela, R. Lange, D. Yu. Murzin and T. Salmi, Catal. Today DOI:10.1016/j.cattod.2015.04.044.
- T. Salmi, D. Yu. Murzin, P. M. Arvela, B. Kusema, B. Holmbom, S. Willför and J. Wärnå, AIChE J., 2014, 60, 1066–1077 CrossRef CAS.
- B. M. Matsagar and P. L. Dhepe, Catal. Sci. Technol., 2015, 5, 531–539 CAS.
- S. Dutta, S. De, B. Saha and M. I. Alam, Catal. Sci. Technol., 2012, 2, 2025–2036 CAS.
- R. Karinen, K. Vilonen and M. Niemela, ChemSusChem, 2011, 4, 1002–1016 CrossRef CAS PubMed.
- E. I. Gürbüz, J. M. R. Gallo, D. M. Alonso, S. G. Wettstein, W. Y. Lim and J. A. Dumesic, Angew. Chem., Int. Ed., 2013, 52, 1270–1274 CrossRef PubMed.
- G. Yi and Y. Zhang, ChemSusChem, 2012, 5, 1383–1387 CrossRef CAS PubMed.
- S. K. Guha, H. Kobayashi, K. Hara, H. Kikuchi, T. Aritsuka and A. Fukuoka, Catal. Commun., 2011, 12, 980–983 CrossRef CAS.
- A. P. Tathod and P. L. Dhepe, Green Chem., 2014, 16, 4944–4954 RSC.
- D. Yu. Murzin, E. V. Murzina, A. Tokarev, N. D. Shcherban, J. Wärnå and T. Salmi, Catal. Today DOI:10.1016/j.cattod.2014.07.019.
- D. Yu. Murzin, B. Kusema, E. V. Murzina, A. Aho, A. Tokarev, A. S. Boymirzaev, J. Wärnå, P. Y. Dapsens, C. Mondelli, P.-R. Javier and T. Salmi, J. Catal., 2015, 330, 93–105 CrossRef CAS.
- A. Bohre, S. Dutta, B. Saha and M. M. Abu-Omar, ACS Sustainable Chem. Eng., 2015, 3, 1263–1277 CrossRef CAS.
- G. Li, N. Li, S. Li, A. Wang, Y. Cong, X. Wang and T. Zhang, Chem. Commun., 2013, 49, 5727–5729 RSC.
- S. Li, N. Li, G. Li, A. Wang, Y. Cong, X. Wang and T. Zhang, Catal. Today, 2014, 234, 91–99 CrossRef CAS.
- G. Li, N. Li, Z. Wang, C. Li, A. Wang, X. Wang, Y. Cong and T. Zhang, ChemSusChem, 2012, 5, 1958–1966 CrossRef CAS PubMed.
- J. Yang, N. Li, S. Li, W. Wang, L. Li, A. Wang, X. Wang, Y. Cong and T. Zhang, Green Chem., 2014, 16, 4879–4884 RSC.
- K. Yan, J. Liao, X. Wu and X. Xie, RSC Adv., 2013, 3, 3853–3856 RSC.
- S. Bhogeswararao and D. Srinivas, J. Catal., 2015, 327, 65–77 CrossRef CAS.
- Y. Nakagawa, H. Nakazawa, H. Watanabe and K. Tomishige, ChemCatChem, 2012, 4, 1791–1797 CrossRef CAS.
- Y. Nakagawa, K. Takada, M. Tamura and K. Tomishige, ACS Catal., 2014, 4, 2718–2726 CrossRef CAS.
- Y. Nakagawa and K. Tomisihge, Catal. Commun., 2010, 12, 157–160 CrossRef.
- M. Hronec and K. Fulajtarová, Catal. Commun., 2012, 24, 100–104 CrossRef CAS.
- Y. Yang, Z. Du, Y. Huang, F. Lu, F. Wang, J. Gao and J. Xu, Green Chem., 2013, 15, 1932–1940 RSC.
- W. Xu, H. Wang, X. Liu, J. Ren, Y. Wang and G. Lu, Chem. Commun., 2011, 47, 3924–3926 RSC.
- S. Liu, Y. Amada, M. Tamura, Y. Nakagawa and K. Tomishige, Green Chem., 2014, 16, 617–626 RSC.
- S. Liu, Y. Amada, M. Tamura, Y. Nakagawa and K. Tomishige, Catal. Sci. Technol., 2014, 4, 2535–2549 CAS.
- T. Mizugaki, T. Yamakawa, Y. Nagatsu, Z. Maeno, T. Mitsudome, K. Jitsukawa and K. Kaneda, ACS Sustainable Chem. Eng., 2014, 2, 2243–2247 CrossRef CAS.
- X. Zhang, T. Wang, L. Ma and C. Wu, Fuel, 2010, 89, 2697–2702 CrossRef CAS.
- A. Lino, A. Cho, A. Takagaki, R. Kikuchi and S. T. Oyama, J. Catal., 2014, 311, 17–27 CrossRef.
- K. Chen, M. Tamura, Z. L. Yuan, Y. Nakagawa and K. Tomishige, ChemSusChem, 2013, 6, 613–621 CrossRef CAS PubMed.
- N. Li, G. A. Tompsett and G. W. Huber, ChemSusChem, 2010, 3, 1154–1157 CrossRef CAS PubMed.
- A. V. Kirilin, A. V. Tokarev, H. Manyar, C. Hardacre, T. Salmi, J.-P. Mikkola and D. Yu. Murzin, Catal. Today, 2014, 223, 97–107 CrossRef CAS.
- A. V. Kirilin, B. Hasse, A. V. Tokarev, L. M. Kustov, G. N. Baeva, G. O. Bragina, A. Yu. Stakheev, A. Rautio, D. Salmi, B. J. M. Etzold, J. Mikkola and D. Yu. Murzin, Catal. Sci. Technol., 2014, 4, 387–401 CAS.
- T. Jiang, Q. Zhang, T.-J. Wang, Q. Zhang and L.-L. Ma, Energy Convers. Manage., 2012, 59, 58–65 CrossRef CAS.
-
D. E. Resasco, S. Sitthisa, J. F. T. Prasomsri and M. P. Ruiz, Heterogeneous in biomass to Chemicals and Fuels, Research Signpost, 2012, pp. 155–188 Search PubMed.
- A. Fukuoka and P. L. Dhepe, Angew. Chem., Int. Ed., 2006, 45, 5161–5163 CrossRef CAS PubMed.
- C. Luo, S. Wang and H. C. Liu, Angew. Chem., Int. Ed., 2007, 46, 7636–7639 CrossRef CAS PubMed.
- J. Geboers, S. Van de Vyver, K. Carpentier, K. de Blochouse, P. Jacobs and B. F. Sels, Chem. Commun., 2010, 46, 3577–3579 RSC.
- R. Palkovits, K. Tajvidi, A. M. Ruppert and J. Procelewska, Chem. Commun., 2011, 47, 576–578 RSC.
- J. Geboers, S. Van de Vyver, K. Carpentier, P. Jacobs and B. F. Sels, Green Chem., 2011, 13, 2167–2174 RSC.
- S. Liu, Y. Okuyama, M. Tamuara, Y. Nakagawa, A. Imai and K. Tomishige, ChemSusChem, 2015, 8, 628–635 CrossRef CAS PubMed.
- S. Liu, M. Tamura, Y. Nakagawa and K. Tomishige, ACS Sustainable Chem. Eng., 2014, 2, 1819–1827 CrossRef CAS.
- B. O. Beeck, M. Dusselier, J. Geboers, J. Holsbeek, E. Morré, S. Oswald, L. Giebeler and B. F. Sels, Energy Environ. Sci., 2014, 8, 230–240 Search PubMed.
- Y. Liu, L. Chem, T. Wang, X. Zhang, J. Long, Q. Zhang and L. Ma, RSC Adv., 2015, 5, 11649–11657 RSC.
- Y. Nakagawa, Y. Shinmi, S. Koso and K. Tomishige, J. Catal., 2010, 272, 191–194 CrossRef CAS.
- Y. Amada, Y. Shinmi, S. Koso, T. Kubota, Y. Nakagawa and K. Tomishige, Appl. Catal., B, 2011, 105, 117–127 CrossRef CAS.
- K. Y. Chen, K. Mori, H. Watanabe, Y. Nakagawa and K. Tomishige, J. Catal., 2012, 294, 171–183 CrossRef CAS.
- Y. Amada, H. Watanabe, Y. Hirai, Y. Kajikawa, Y. Nakagawa and K. Tomishige, ChemSusChem, 2012, 5, 1991–1999 CrossRef CAS PubMed.
- Y. Nakagawa, X. Ning, Y. Amada and K. Tomishige, Appl. Catal., A, 2012, 433–434, 128–134 CrossRef CAS.
- Y. Aamada, H. Watanabe, M. Tamura, Y. Nakagawa, K. Okumura and K. Tomishige, J. Phys. Chem. C, 2012, 116, 23503–23514 Search PubMed.
- Y. Nakagawa, K. Mori, K. Chen, Y. Aamda, M. Tamura and K. Tomishige, Appl. Catal., A, 2013, 468, 418–425 CrossRef CAS.
- M. Tamura, Y. Amada, S. Liu, Z. Yuan, Y. Nakagawa and K. Tomishige, J. Mol. Catal. A: Chem., 2014, 388–389, 177–187 CrossRef CAS.
- M. Tamura, K. Tokonami, Y. Nakagawa and K. Tomishige, Chem. Commun., 2013, 49, 7034–7036 RSC.
- Y. Nakagawa, M. Tamura and K. Tomishige, J. Mater. Chem. A, 2014, 2, 6688–6702 CAS.
- F. Carvalheiro, L. C. Duarte and F. M. Girio, J. Sci. Ind. Res., 2008, 67, 849–864 CAS.
- D. D. Falcone, J. H. Hack, A. Yu. Klyushin, A. Knop-Gericke, R. Schlögl and R. J. Davis, ACS Catal., 2015, 5, 5679–5695 CrossRef CAS.
- S. R. Sashital, J. B. Cohen, R. L. Burwell Jr. and J. B. Butt, J. Catal., 1977, 50, 479–493 CrossRef CAS.
Footnote |
† Electronic supplementary information (ESI) available. See DOI: 10.1039/c5gc02183a |
|
This journal is © The Royal Society of Chemistry 2016 |
Click here to see how this site uses Cookies. View our privacy policy here.