DOI:
10.1039/D2NH00218C
(Communication)
Nanoscale Horiz., 2022,
7, 1210-1216
Thermally driven phase transition of cobalt hydroxide sheets via cobalt oxides to cobalt nanoparticles†
Received
3rd May 2022
, Accepted 25th July 2022
First published on 26th July 2022
Abstract
Transition metal oxides, which include many stoichiometric variations, are formed into various crystal structures by the atomic arrangement of cations and anions according to stoichiometric composition and are used for a wide range of applications based on this. Among them, cobalt oxide, which has wide crystal structures depending on the lattice points of the anion and the valence of the Co cation, from its hydroxide formula, is attracting a lot of attention due to its interesting catalytic properties due to its crystal structure. In this study, using the synthesized Co(OH)2 nanosheets, the real-time behavior of the phase transition that occurs when continuous heat is applied to the sample has been systematically analyzed using an aberration-corrected scanning transmission electron microscope. The layered Co(OH)2 phase passes through hexagonal CoO and cubic CoO phases to finally become Co nanoparticles, but when the temperature is dropped in the hexagonal phase, spinel Co3O4 is formed. These results suggest that various phases included in transition metal oxides can be selectively implemented according to temperature range control.
New concepts
Cobalt oxide, a representative transition metal oxide with various crystal structures, exhibits interesting catalytic properties which are useful for several applications. Two-dimensional (2D) cobalt hydroxide (Co(OH)2), cobalt oxyhydroxide (CoOOH), and cobalt oxide are more efficient catalysts for the oxygen evolution reaction than their bulk counterparts. Even though the synthesis and use of stable phases of cobalt oxides have received considerable attention in recent years, there are not many reports on the phase transformations originating from cobalt hydroxide. Hence, we analyzed the different phase transitions of Co(OH)2 nanosheets by in situ scanning transmission electron microscopy heating experiments. The phase transformation of Co(OH)2 proceeds through various intermediate phases of cobalt oxide. Hexagonal CoO is formed with a continuous increase in temperature up to 450 °C. Interestingly, spinel structured Co3O4 is formed when the temperature of hexagonal CoO is reduced to 200 °C. With further increase in temperature, a new phase transition to c-CoO occurs (instead of h-CoO), leading to the formation of Co nanoparticles. Thus, the different phases of cobalt oxide could be selectively obtained by temperature control. It is believed that this study can be extended to other transition metal oxides to understand the formation of new phases.
|
Introduction
Transition metal oxides (TMOs) are thermodynamically and chemically stable materials and exist in a variety of crystal structures. Their unique and interesting physical and chemical properties make them promising materials for numerous applications (e.g., catalysis,1–3 energy storage,4–7 sensors,8,9 nonlinear optics, and electrodes10–13). Transition metal monoxides are especially important for their various crystal structures and physicochemical properties that are useful for several potential applications.14–16
Cobalt oxides, representative TMOs, are a family of chemical compounds consisting of cobalt and oxygen atoms, which can exist in various stoichiometries.17–21 Cobalt oxide catalyzes the oxygen evolution reaction, and two-dimensional (2D) cobalt hydroxide (Co(OH)2), cobalt oxyhydroxide (CoOOH), and cobalt oxide are more efficient catalysts than their bulk counterparts.23–27 Therefore, recent research is focused on the preparation of 2D cobalt oxide nanosheets with non-layered or layered structures using methods such as hydrothermal reaction,28,29 electrodeposition,30,31 atomic layer deposition,32,33 and ionic layer epitaxy.34 The commonly investigated phases of cobalt oxide are spinel Co3O4, hexagonal CoO (h-CoO), and cubic CoO (c-CoO),17–22 all of which undergo phase transformations under certain conditions.18,20 The synthesis and use of the stable phases of the cobalt oxides have received considerable attention in recent years,35,36 and interesting studies have been reported on the thermodynamic behaviors of phase transitions.17,18,20 However, studies on phase transformations originating from cobalt hydroxide are lacking. The stoichiometric ratio of synthetic cobalt oxide (transition metal ion to oxygen ion) with a non-layered structure is 1
:
1 or 3
:
4, while that of synthesized Co(OH)2 nanosheets with a layered structure is 1
:
2. Therefore, it is important to explore the structural evolution and formation of CoOOH, CoO, and Co3O4.
Herein, we report the phase transition of Co(OH)2 nanosheets during in situ-controlled vacuum annealing at temperatures near the melting point. The reason for using Co(OH)2 as an initial material is that when Co(OH)2 having a hexagonal phase is heat-treated in a vacuum atmosphere, the Co3O4 structure with the highest oxidation number is not preferentially formed, but CoOOH, which is hydrogen desorbed from the Co(OH)2, is preferentially formed. Since it is possible to understand the process of forming different crystalline structures of a hexagonal lattice, it is possible to systematically confirm the implementation of multiple intermediate phases.20 Various phases of cobalt oxide are formed because of the structural changes induced by oxygen loss. The Co3O4 structure appears within a specific temperature range, and the continuous increase in temperature induces a final structural change leading to the formation of Co nanoparticles. Various intermediate phases with a non-layered structure are formed from the layered structure of hydroxide. The use of high angle annular dark field scanning transmission electron microscopy (HAADF-STEM) enables structural and chemical characterization of the different phases.
Results
X-ray photoelectron spectroscopy (XPS; Fig. S1, ESI†) was used to identify the phases in the synthesized Co(OH)2 nanosheets.34 Subsequently, the nanosheets were loaded onto a heating chip with temperature control up to 1100 °C. During in situ TEM heating, the Co(OH)2 nanosheets undergo phase transitions, as shown in Fig. 1 and Fig. S2 (ESI†). The initial Co(OH)2 phase changes to stable Co naoparticles via different phases of cobalt oxides (e.g., h-CoO, c-CoO, and Co3O4) depending on the heating steps (Fig. 2(a)–(f)). We focused on the different phase changes of Co(OH)2 nanosheets and analyzed the structural reconstruction with change in temperature. Fig. 2(g) shows the HAADF-STEM image of Co(OH)2 nanosheets transferred onto the heating chip (structure shown in Fig. 2(b)). We induced a phase transformation in the nanosheets by applying a heating pulse of 450 °C (Fig. 2(c)) in regions showing phase change. Then, we decreased the temperature to 200 °C to cause a phase transition to Co3O4 (Fig. 2(d)). We repeated this experiment several times using different Co(OH)2 specimens to obtain reproducible results. Fig. S3 and S4 (ESI†) show the in situ real-time imaging of an area of Co(OH)2 nanosheets transforming to Co nanoparticles during the annealing experiments. Continuous heating to higher temperatures or for longer durations causes loss of oxygen and further phase transitions. Eventually, Co nanoparticles are formed from the c-CoO phase (Fig. 2(e) and (f)). The respective simulated images of the structures of h-CoO, Co3O4, c-CoO, and Co in Fig. 2(h)–(k) correspond with the obtained HAADF-STEM images (Fig. 2(c)–(f)). The electron energy loss (EEL) spectrum of each phase indicates near-stoichiometric composition (Fig. 2(l) and (m)).43,44 The slight peak shifts of the Co-L2,3 edge depending on their phase changes (Fig. 2(m)) indicate the changes in oxidation states, which will be discussed in the next section. In addition, definite differences of O–K edge shape between Co3O4 and other phases help to distinguish their respective phases. The spinel structured Co3O4 is formed only when the temperature is decreased from 450 to 200 °C (Fig. 2(n)–(p)). Successive heating induces phase transition from Co(OH)2 to Co nanoparticles via only the CoO phases (h-CoO and c-CoO) (Fig. S4, ESI†). The real-time observation of the phase transitions in a vacuum is discussed in detail in the following sections. Meanwhile, the phase transitions that occur in air are described in Note S1 and Fig. S8 (ESI†).
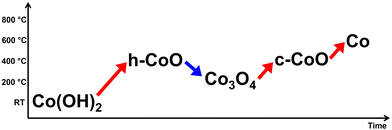 |
| Fig. 1 A simple flowchart showing the overall behaviour of phase transitions. | |
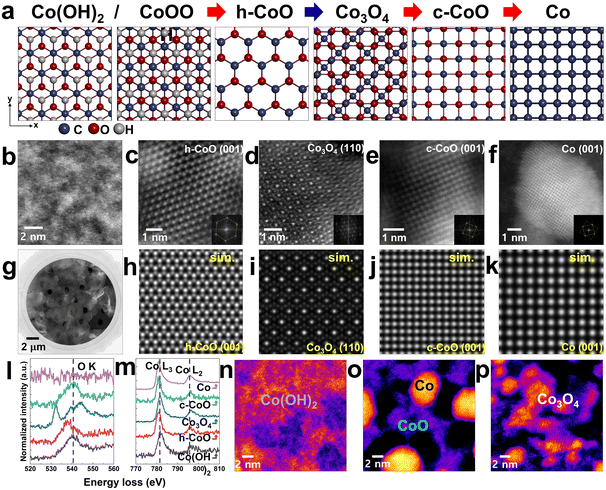 |
| Fig. 2 Phase transition from Co(OH)2 to Co depending on temperature. (a) Atomic models showing crystal structures of Co(OH)2, CoOOH, h-CoO, Co3O4, c-CoO, and Co. The red arrows indicate increase in temperature, and the blue arrow indicates decrease in temperature. (b)–(f) HAADF-STEM images showing the evolution of atomic structures from Co(OH)2 nanosheets to Co. (g) HAADF-STEM image of the Co(OH)2 sheets loaded onto the heating chip. (h)–(k) Multislice image simulations of each structure from h-CoO to Co. (l) and (m) EEL spectra of Co L2,3- and O K-edges, respectively, obtained from the different phases. (n)–(p) HAADF-STEM images showing the phase transition from Co(OH)2via CoO sheets with Co nanoparticles to Co3O4 flakes. | |
1. Co(OH)2 to h-CoO
It is known that heating of synthetic Co(OH)2 nanosheets induces the formation of h-CoO phase. The structure of Co(OH)2 is easily deformed by electron beam irradiation; however, the digital diffractogram of the field of view shows the formation of β-Co(OH)2 (inset of Fig. 3(a)). It has a hexagonal layered structure with a Co layer sandwiched between two OH layers (Fig. 3(c)).37 The elemental analysis of the formation of h-CoO phase at temperatures >300 °C is performed using the energy dispersive X-ray spectroscopy (EDS) mapping (Fig. 3(b), (e) and Fig. S7, ESI†).
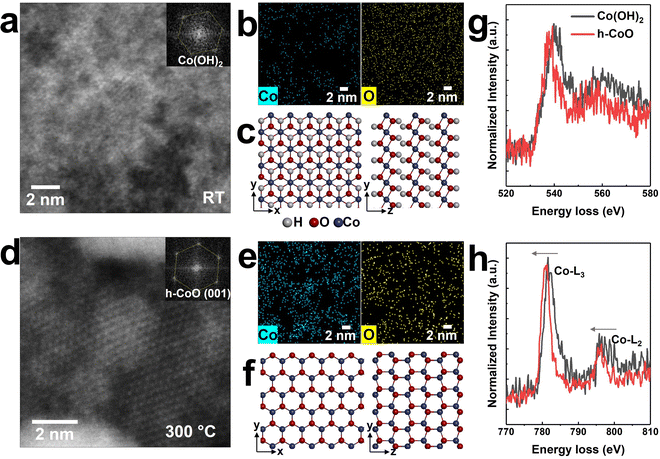 |
| Fig. 3 Phase transition of h-CoO from Co(OH)2 nanosheets. (a) HAADF-STEM image of Co(OH)2; the inset shows the digital diffractogram. (b) and (c) EDS mapping images and atomic models of the Co(OH)2 sheets. (d) HAADF-STEM image of h-CoO; the inset shows the digital diffractogram. (e) and (f) EDS mapping images and atomic models of h-CoO. (g) and (h) EEL spectra of O K- and Co L2,3-edges, respectively, obtained from Co(OH)2 and h-CoO. | |
In general, CoO exists in two crystal structures: c-CoO with cations in the octahedral site, and h-CoO with cations in the tetrahedral site. c-CoO is more thermodynamically stable than h-CoO.38,39 In the present case, the starting material is Co(OH)2 with a hexagonal lattice (Fig. 3(c)); therefore, hydrogen desorption could occur as an intermediate process.40,41 The remaining species may undergo condensation reaction to form Co–O–Co bonds,42 ultimately leading to the formation of h-CoO phase (Fig. 3(f)).
The O K-edge (Fig. 3(g)) and the Co-L2,3 edge (Fig. 3(h)) peaks shift to lower energy loss when Co(OH)2 transforms to h-CoO, as confirmed via EELS. The peak shift of the Co L2,3-edge (∼0.6 eV) to lower energy loss implies the transformation of Co to lower valence cobalt oxides.43,44 The desorption of hydrogen from Co(OH)2 upon electron beam irradiation suggests that the synthesized Co(OH)2 nanosheets consist of mixed states of Co(OH)2 (Co2+) and CoOOH (Co3+), which transform into h-CoO (Co2+) after annealing. If Co3+ is more dominant in a synthesized nanosheet, the O-K edge must look like Co3O4 spectra (Fig. 2(l)). However, the O-K edge of the synthesized nanosheet is similar to that of h-CoO (Fig. 3(h)). This indicates that the synthesized nanosheet predominantly consists of Co(OH)2 (Co2+).
2. h-CoO to spinel Co3O4
We observed that Co(OH)2 nanosheets can be directly transformed into h-CoO nanosheets without a change of its morphology by increasing the temperature. Above 300 °C, they are partially transformed into Co nanoparticles. When the temperature is decreased from 450 to 200 °C, another phase is observed. As shown in Fig. 4(a), partially transformed Co nanoparticles and h-CoO sheets remaining at the base are shown and the transition to Co3O4 is initiated. The remaining Co and O atoms around the merged particle gather and react with the Co nanoparticle to form the Co3O4 phase, a spinel structure. The atomic structure of Co3O4 (with Co2+ cations in the tetrahedral interstitial sites): (111) (Fig. 4(b)), (110) (Fig. 4(c)), and (112) (Fig. 4(d)). Each plane is well-matched with a length of interplanar spacing corresponding to the plane and its image simulation and atomic model (Fig. 4(e), (f) and (g)). This phase transition is observed in other regions also, as shown in Fig. S5 and S6 (ESI†). Oxygen-rich Co(OH)2 nanosheets transform into Co and h-CoO at 450 °C. Furthermore, imperfectly crystallized Co–O in Co and h-CoO are directly crystallized with a continuous increase in the temperature because of the decomposition of residual oxygen. The formation of Co3O4 from h-CoO may be attributed to the participation of surface adsorbed oxygen molecules (that existed as amorphous phase) in the oxidation reaction with a decrease in the temperature. EDS spectra showing the stoichiometric ratio of each phase (Fig. S7, ESI†) support our expectation. The averaged atomic ratio between Co and O (at% (O/Co)) in the Co(OH)2 nanosheets is 7.27, and it decreases to 2.12 as it transforms into h-CoO and Co with the thermal decomposition of oxygen sources. When cooling down the temperature, the Co
:
O atomic ratio reaches 3
:
3.56 via forming Co3O4 phases. When converted from Co(OH)2 to Co3O4 in this way, the Co3O4 structure exhibits better electrochemical catalytic properties than the Co(OH)2 structure as an electrocatalyst in an alkaline medium for water splitting.45,46
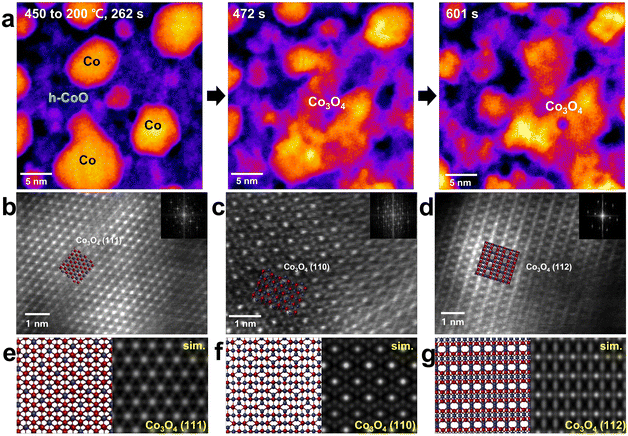 |
| Fig. 4 Formation of Co3O4 from Co particles and h-CoO. (a) Successive HAADF-STEM images showing the phase transition. (b)–(d) HAADF-STEM images showing atomic structures of spinel Co3O4 flakes depending on the (111), (110), and (112) planes with insets of digital diffractograms and atomic models. (e)–(g) Atomic arrangements and corresponding multislice image simulations of Co3O4 (111), (110) and (112), respectively. | |
3. Co3O4 to c-CoO
The Co3O4 phase gradually changes to c-CoO when the heating pulse is re-applied (Fig. 5(a)). As the c-CoO phase is formed in the region with the Co3O4 phase, the interface between the two phases is naturally exposed (Fig. 5(b)). The lattice image of the c-CoO (111) plane is well matched with a length of interplanar spacing corresponding to the (111) plane (Fig. 5(c)). The Co3O4 phase is completely transformed to the c-CoO phase when continuous heat is applied; however, small Co nanoparticles are also observed (Fig. 5(d)). In particular, since c-CoO is directly related to chemical, structural and magnetic properties, nano-sized c-CoO can be used as a material for controlling local magnetic properties and local electronic properties using nano-sized c-CoO.47
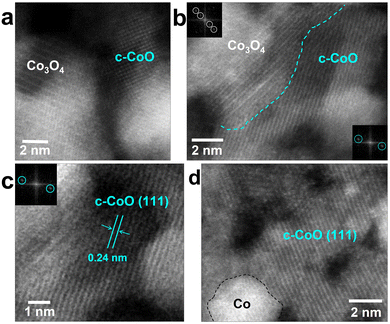 |
| Fig. 5 HAADF-STEM images showing the formation of c-CoO from Co3O4. (a) and (b) Interface between Co3O4 and c-CoO. (c) d-spacing of the c-CoO (111) plane. (d) Transformed c-CoO phase with Co nanoparticles. | |
4. Co nanoparticle formation
At a high temperature, c-CoO undergoes a reduction reaction and transforms into c-Co. The c-Co nanoparticles grow with time whereas the c-CoO particles deoxidize and disappear (Fig. 5(a)–(d)), indicating a complete transition. As the Co nanoparticles are heated, oxygen anions continuously diffuse out of the surface pores. Furthermore, electrons are transferred from the surface Co atoms to the inner Co2+ ions to form Co2+ ions on the surface. The loss of oxygen anions means that surface Co nanoparticles formed at the initiation determine the shape, which is entirely due to the loss of oxygen anions (Fig. 6).18
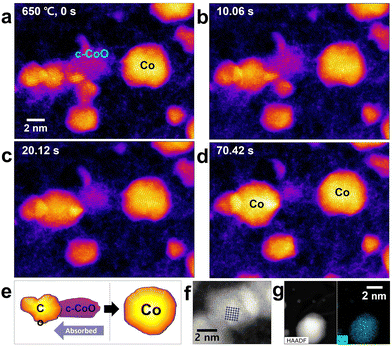 |
| Fig. 6 HAADF-STEM images showing the formation of Co nanoparticles from a c-CoO cluster. (a)–(d) Successive images and (e) schematic showing the formation process of Co. (f) Atomic resolution STEM image of Co nanoparticles with the corresponding atomic model. (g) HAADF-STEM image and corresponding EDS mapping image of a Co-only nanoparticle. | |
Conclusions
We studied the transitions of various Co–O phases originating from Co(OH)2 nanosheets by in situ TEM. The phase transition of Co(OH)2 into Co nanoparticles occurs through various intermediate phases of cobalt oxide (h-CoO, Co3O4, and c-CoO) each with a unique crystal structure. The h-CoO phase formed at approximately 450 °C transforms to spinel Co3O4 only when the temperature is decreased to 200 °C. A new phase transition to c-CoO occurs (instead of h-CoO) when the temperature is further increased, and the transition ends with the formation of Co nanoparticles. The real-time STEM heating experiments of the multi-phase Co–O system enable us to analyze changes in the crystal structure and chemical composition, thus opening a promising avenue for in-depth studies of the formation routes of new materials and their phases.
Materials and methods
Materials
To synthesize Co(OH)2 sheets, the aqueous nutrient solution containing 2 mM cobalt nitrate hexahydrate and 2 mM hexamethylenetetramine (HMTA) was gently added to a Glasslock (size: 74 × 74 × 63.5 mmH). Depending on the opening area of the Glasslock, a calculated amount of chloroform solution of sodium hexadecyl sulfate (SHS) was added to the water–air interface. After about 30 minutes, the Glasslock was capped and placed in a convection oven at 70 °C for typically 180 minutes. The synthesized Co(OH)2 sheets were scooped using an arbitrary substrate for characterization.
Characterization using XPS
The chemical properties of CoO were characterized by X-ray photoemission spectroscopy (XPS, Thermofisher K-alpha) data obtained from the nanosheets transferred onto a 50 nm-thick platinum coated-Si substrate to minimize the signal from the native oxide of the Si substrates. Peak deconvolution was carried out after background subtraction using Shirley background.
TEM observations
Specimens were analyzed using an aberration-corrected FEI Titan Cubed TEM (FEI Titan3 G2 60-300), which was operated at an 80 kV acceleration voltage with a monochromator. The microscope provided a sub-Angstrom resolution at 80 kV and −13 ± 0.5 μm of spherical aberration (Cs). The convergence angle was set to be 26.6 mrad. Typical electron beam densities were adjusted to ∼6 × 105 e− nm−2 and the images were recorded on the 1024 × 1024 scan array at a scanning rate of 4–5 μs per pix for successive HAADF-STEM images and 8 μs per pix for single HAADF-STEM images. HAADF-STEM images were obtained using a high-angle annular dark-field (HAADF) detector to collect semi-angles from 50.5 to 200 mrad with a spatial resolution of 0.65 Å. The obtained atomic resolution STEM images were filtered using a Wiener filter to reduce noise and enhance contrast. Multislice STEM image simulation was performed by commercially available software TEMPAS (Total Resolution LLC) to confirm the crystal structure. EDS analysis was performed using the four-quadrant Super-X EDS detector system (FEI). EELS were obtained using a Gatan Quantum 965 dual EELS system, and the energy resolution was 0.8 eV, as measured from the full-width-at-half-maximum of the zero-loss peak. Temperature dependent HAADF-STEM imaging up to 1100 °C was performed using a commercially available in situ heating holder from DENSSolutions (Wildfire S3). Focused ion beam (FIB) (FEI, Quanta 3D FEG) was used to cut open slits in the Si3N4 membrane to enable suspended Co(OH)2 samples for imaging. Slits were fabricated in the Si3N4 membranes using FIB milling before transferring the Co(OH)2. Heating the sample was achieved by passing a current through a platinum resistive coil embedded in the MEMS chip.
Author contributions
G. H. Ryu and Z. Lee contributed as co-corresponding authors. A. Yoon imaged the specimen and performed data analysis. G. Kim and M. Lee conducted synthesis of the sample and the experiments. G. H. Ryu wrote the manuscript with contributions from all authors.
Conflicts of interest
There are no conflicts to declare.
Acknowledgements
This work was supported by the National Research Foundation of Korea (NRF) grant funded by the Korea government (MSIT) (No. 2020R1G1A1099542 and No. 2022R1F1A1068161) and the Institute for Basic Science (IBS-R019-D1). We would like to thank Editage (http://www.editage.co.kr) for English language editing.
References
- Y. Wang, J. Li and Z. Wei, J. Mater. Chem. A, 2018, 6, 8194–8209 RSC.
- C. Goswan, K. K. Hazarika and P. Bharali, Mater. Sci. Technol., 2018, 1, 117–128 Search PubMed.
- M. Baltes, O. Collart, P. V. D. Voort and E. F. Vansant, Langmuir, 1999, 15, 5841–5845 CrossRef CAS.
- M. V. Reddy, G. V. Subba Rao and B. V. R. Chowdari, Chem. Rev., 2013, 113, 5364–5457 CrossRef CAS PubMed.
- X. Guo, G. Zhang., Q. Li, H. Xue and H. Pang, Energy Storage Mater., 2018, 15, 171–201 CrossRef.
- S. Fang, D. Bresser and S. Passerini, Adv. Funct. Mater., 2020, 10, 1902485 CAS.
- H. T. Tan, W. Sun, L. Wang. and Q. Yan, Chem. Nanostruct. Mater., 2015, 2, 562–577 Search PubMed.
- E. Lee, Y. S. Yoon and D.-J. Kim, ACS Sens., 2018, 3, 2045–2060 CrossRef CAS PubMed.
- J. Ma, Y. Li, J. Li, X. Yang, Y. Ren, A. A. Alghamdi, G. Song, K. Yuan and Y. Deng, Adv. Funct. Mater., 2022, 32, 2107439 CrossRef CAS.
- A. Moreo, S. Yunoki and E. Dagotto, Science, 1999, 283, 2034–2040 CrossRef CAS PubMed.
- Y.-W. Jun, J.-S. Choi and J. Cheon, Angew. Chem., Int. Ed., 2006, 45, 3414–3439 CrossRef CAS PubMed.
- W. S. Seo, H. H. Jo, K. Lee, B. Kim, S. J. Oh and J. T. Park, Angew. Chem., Int. Ed., 2004, 116, 1135–1137 CrossRef.
- J. Tao, T. Luttrell and M. Batzill, Nat. Chem., 2011, 3, 296–300 CrossRef CAS PubMed.
-
H. H. Kung, Selective Oxidation Reactions II, Elsevier, 1989, vol. 45, pp. 200–226 Search PubMed.
- J. Y. Park, L. R. Baker and G. A. Somorjai, Chem. Rev., 2015, 115, 2781–2817 CrossRef CAS PubMed.
- H.-J. Zhai and L.-S. Wang, Chem. Phys. Lett., 2010, 500, 185–195 CrossRef CAS.
- K.-W. Park and A. M. Kolpak, J. Catal., 2018, 365, 115–124 CrossRef CAS.
- K. M. Nam, W. S. Seo, H. Song and J. T. Park, NPG Asia Mater., 2017, 9, e364 CrossRef CAS.
- M.-J. Xiao, H. Zhang, B. Ma, Z.-Q. Zhang, X.-Y. Li, Q. Xiao, Q. Wang, Y. Peng and H.-L. Zhang, J. Mater. Chem. A, 2021, 9, 24548–24559 RSC.
- X. Chen, H. v Gog and M. A. v Huis, J. Mater. Chem. C, 2021, 9, 5662–5675 RSC.
- W. Zeng, J. Zhang, S. Zhu, X. Deng, H. Ma, J. Zhang, Q. Zhang, P. Li, D. Xue, N. J. Mellors, X. Zhang and Y. Peng, Nanoscale, 2017, 9, 7493 RSC.
- A. Ma, H. J. Park, J. H. Seo, K. Y. Jang, H. K. Lee, D. Y. Kim, J. E. Lee, K. M. Nam. and D.-S. Lee, Sens. Actuators, B, 2020, 308, 127698 CrossRef CAS.
- J. K. Norskov, T. Bligaard, J. Rossmeisl and C. H. Christensen, Nat. Chem., 2009, 1, 37–46 CrossRef CAS PubMed.
- M. W. Kanan and D. G. Nocera, Science, 2008, 321, 1072–1075 CrossRef CAS PubMed.
- J. D. Blakemore, H. B. Gray, J. R. Winkler and A. M. Müller, ACS Catal., 2013, 3, 2497–2500 CrossRef CAS.
- B. M. Hunter, H. B. Gray and A. M. Müller, Chem. Rev., 2016, 116, 14120–14136 CrossRef CAS PubMed.
- Y. Yu, Z. Zhang, X. Yin, A. Kvit, Q. Liao, Z. Kang, X. Yan, Y. Zhang and X. Wang, Nat. Energy, 2017, 2, 17045 CrossRef CAS.
- T. Adschiri, Y. Hakuta and K. Arai, Ind. Eng. Chem. Res., 2000, 39, 4901–4907 CrossRef CAS.
- M. S. Whittingham, Curr. Opin. Solid State Mater. Sci., 1996, 1, 227–232 CrossRef CAS.
- A. Camila, S. Cabezas, K. Miller, S. Heo, A. Dolocan, G. LeBlanc and D. J. Milliron, Chem. Mater., 2020, 32, 4600–4608 CrossRef.
- Z. Yan, H. Sun, X. Chen, H. Liu, Y. Zhao, H. Li, W. Xie, F. Cheng and J. Chen, Nat. Commun., 2018, 9, 2373 CrossRef PubMed.
- A. M. Jasim, S. He, T. A. White and Y. Xing, Commun. Mater., 2020, 1, 9 CrossRef.
- M. Ritala, K. Kukli, A. Rahtu, P. I. Räisänen, M. Leskelä, T. Sajavaara and J. Keinnonen, Science, 2000, 288, 319–321 CrossRef CAS PubMed.
- F. Wang, Y. Yu, X. Yin, P. Tian and X. Wang, J. Mater. Chem. A, 2017, 5, 9060–9066 RSC.
- M. Bajdich, M. García-Mota, A. Vojvodic, J. K. Nørskov and A. T. Bell, J. Am. Chem. Soc., 2013, 135, 13521–13530 CrossRef CAS PubMed.
- R. K. Nare, S. Ramesh, P. K. Basavi, V. Kakani, C. Bathula, H. M. Yadav, P. B. Dhanapal, R. K. R. Kotanka and V. R. Pasupuleti, Sci. Rep., 2022, 12, 1998 CrossRef CAS PubMed.
- Z. Liu, R. Ma, M. Osada, K. Takada and T. Sadaki, J. Am. Chem. Soc., 2005, 127, 13869–13874 CrossRef CAS PubMed.
- K. A. Marek, J. R. Raker, T. A. Holme and K. L. Murphy, J. Chem. Educ., 2018, 95, 233–237 CrossRef CAS.
- W. L. Roth, Phys. Rev., 1958, 110, 1333–1341 CrossRef CAS.
- V. Pralong, A. Delahaye-Vidal, B. Beaudoin, B. Gérand and J.-M. Tarascon, J. Mater. Chem., 1999, 9, 955–960 RSC.
- J. Yang, H. Liu, W. N. Martens and R. L. Frost, J. Phys. Chem. C, 2010, 114, 111–119 CrossRef CAS.
- N. Pinna, G. Garnweitner, M. Antonietti and M. A. Niederberger, J. Am. Chem. Soc., 2005, 127, 5608–5612 CrossRef CAS PubMed.
- H. Tan, J. Verbeeck, A. Abakumov and G. Van Tendeloo, Ultramicroscopy, 2012, 116, 24–33 CrossRef CAS.
- N. O. Peña, D. Ihiawakrim, M. Han, B. Lassalle-Kaiser, S. Carenco, C. Sanchez, C. Laberty-Robert, D. Portehault and O. Ersen, ACS Nano, 2019, 13, 11372–11381 CrossRef PubMed.
- M. Darbandi, E. Narimani, P. Y. Sefidi, H. Rasouli and M. G. Hosseini, Int. J. Hydrogen Energy, 2020, 46, 3887–3897 CrossRef.
- D. Su, S. Dou and G. Wang, Sci. Rep., 2014, 4, 2014 Search PubMed.
- R. V. Santos, G. A. Cabrera-Pasca, C. S. Costa, B. Bosch-Santos, L. Otubo, L. F. Pereira, B. S. Correa, F. B. Effenberger, A. Burimova, R. S. Freitas and A. W. Carbonari, Sci. Rep., 2021, 11, 21028 CrossRef CAS PubMed.
|
This journal is © The Royal Society of Chemistry 2022 |