DOI:
10.1039/D4RA03565H
(Review Article)
RSC Adv., 2024,
14, 20765-20779
Back to the future with emerging iron technologies
Received
15th May 2024
, Accepted 23rd June 2024
First published on 1st July 2024
Abstract
Here is a comprehensive overview of iron's potential in low-carbon energy technologies, exploring applications like metal fuel combustion, iron-based batteries, and energy-carrier cycles, as well as sustainable approaches for production and recycling with a focus on reducing environmental impact. Iron, with its abundance, safety, and electrochemical characteristics, is a promising material to contribute to a decarbonized future. This paper discusses the advancements and challenges in iron-based energy storage technologies and sustainable iron production methods. Various innovative approaches are explored as energy storage solutions based on iron, like advancements in thermochemical Fe–Cl cycles highlight the potential of iron chloride electrochemical cycles for long-term high-capacity energy storage technology. Additionally, the utilization of iron as a circular fuel in industrial processes demonstrates its potential in large-scale thermal energy generation. Sustainable iron production methods, such as electrolysis of iron chloride or oxide and deep eutectic solvent extraction, are investigated to reduce the carbon footprint in the iron and steel industry. These findings also show the importance of policy and technology improvements that are vital for the widespread use and recycling of iron-based tech, stressing the need for collaboration toward a sustainable future.
1 Iron as a solution in emerging technologies for a decarbonized energy future
The concept of energy resilience is now becoming an increasingly important topic of discussion at many levels (e.g., social, economic, technical, and political), highlighting the need for concrete solutions. The shift towards producing energy from renewable and low-carbon energy sources instead of fossil fuels has been agreed upon at the government and industry levels as the way forward for sustainable societal development. The development of environmentally friendly energy technologies and systems has become a global urgent task. The adoption of this concept will lead to an increase in the production of environmentally friendly or green applications, including energy-efficient buildings, electric vehicles, and technologies for generating and storing renewable energy. Due to the increasing inclusion of intermittent renewable energy sources in the grid energy mix, there is an inevitable need for energy storage solutions to support these developments. On the production side, more cost-effective and efficient photovoltaic panels and wind turbines, fabricated for more accessible end-of-life materials recycling, and an advanced power management system will be required to support this shift. The flip side of clean and renewable technologies is the high and constant demand for minerals and metals.1 The depletion of metal and mineral resources is a potential concern that could impact the future production of clean and renewable technologies.2 To date, iron and steel are the most recycled materials (i.e. steel has a recycling ratio close to 95%).3 The end-of-life recovery rate varies among metals, e.g. it is over 50% for zinc, aluminum, gold, cobalt, copper, and manganese,4 while it is less than 1% for indium and gallium and less than 5% for Li-ion batteries.5
Iron is the most commonly used metal, widely available compared to others, and has been an essential part of social development for more than 5000 years. Due to its abundance and relatively low cost, it is an attractive material for various industries. New technologies and applications will further increase the demand for iron. However, the major drawback of using iron is its current carbon-intensive production technology, which has negative impacts on the environment. This highlights the need for improved methods of iron production. Data show that the iron and steel industry is responsible for one-third of global industrial CO2 emissions, with increasing trends in all countries.6 The transition to a low-carbon energy future includes the iron and steel industry and requires radical innovation to address the current fossil fuel mode of production. This may include implementing new technologies and processes that are not only risky and expensive but also complex, requiring systemic development.3 For instance, one intensively studied promising option is the reduction of iron ore with hydrogen. Although it is not an established industrial process yet, there are some breakthrough projects ongoing in this direction.7–19
Iron has great potential for use in emerging grid energy storage technologies. As research and development efforts continue to improve the storage of available renewable energy, the use of iron in these applications is likely to increase. Lately, the iron-based electrochemical energy storage (EES) options have drawn a lot of attention for several reasons; they are economically affordable, recyclable, less toxic, rich in valent states, and redox behavior with good energy density and unique electrochemical characteristics. Even more, iron-based aqueous EES are highly mechanically robust and resilient.20
Iron can play a significant role in a low-carbon intensity energy future, particularly in the production of green hydrogen. Green hydrogen is considered a perspective energy carrier that can contribute to the reduction of CO2 emissions and other environmental impacts. Hydrogen global demand is estimated to increase by 4–5% per year,21 and for the European scenario, hydrogen has the potential to meet 5–20% of industrial energy needs.22 In addition, the production of green hydrogen is a necessity not only for environmental reasons but also for economic and energy security and diversification. Among promising green hydrogen production approaches, that use iron as an energy carrier, are chemical cycles,23,24 alkaline electrolysis cells,25 and thermochemical water splitting.26 Therefore, the iron and steel industry can play a vital role in the development of the hydrogen economy.
Metallic iron has great potential as a fuel or energy carrier, although research in this area is still in its early stages. Iron fuel has several advantages over conventional fossil fuels, including its high energy density, ease of transport and storage, and low cost. Additionally, iron fuel can be produced from existing iron resources (iron ore) and can be reused through recycling (scrap iron). In a future with an abundance of renewable and low-carbon energy, metal fuels, including iron, are important for their potential applications such as fuel additives in propellants,27 energetic materials,28 fuels in batteries, and recyclable electro-fuels.29 Additionally, metal propellants such as iron powder have the prospect of being used for in situ resource utilization in future space missions.30 However, there are currently limitations to its application in a clean energy distribution network because of the lack of efficient technologies for transferring chemical energy from metal fuels into electricity or mechanical energy for end-users. It is important to recognize that the implementation of clean energy technologies involves complex considerations, including environmental and social risks. Policy support plays a vital role in ensuring the widespread adoption and safe recycling of these technologies. By considering the environmental impact, promoting the circular economy, and implementing supportive policies, iron-based technologies can play a significant role in the transition towards a sustainable energy landscape.
In this paper, a selection of innovative applications of iron in emerging low-carbon energy technologies is discussed. The paper also reviews current approaches for low-carbon-intensive iron production and recycling. Finally, it presents perspectives on the management of evolving iron technologies and current trends in the research and application of iron-based technologies in academia and industry. The paper aims to provide a comprehensive overview of the current state and future potential use of iron for energy technologies.
2 Applications of iron in emerging energy low-carbon technologies
Iron is abundant, safe, and possesses impressive electrochemical characteristics as detailed in Table 1. It is significantly cheaper than nickel, lithium, zinc, and aluminum, and its abundance is greater than both lithium and nickel. Compared to other metals, iron's specific capacity surpasses zinc and nickel, although it is lower than aluminum and lithium. Its volumetric capacity is superior to zinc and magnesium, matches copper, and is just slightly below nickel and aluminum. Aqueous solutions of iron, zinc, nickel, and copper salts (chlorides, sulfates, nitrates, phosphates), can undergo electroreduction via cold electrolysis. In contrast, aluminum cannot be electroplated from aqueous solutions. Environmentally, iron excels with low toxicity and a high recycling rate, outperforming aluminum and zinc in these aspects.35,36 These properties position it as a highly promising material for energy storage technologies, particularly for large-scale applications. However, the application of iron for metal anodes for aqueous rechargeable batteries in practice is still limited by passivation, parasitic hydrogen evolution reaction, and low energy efficiency.37 Nevertheless, innovation in energy storage devices and the advancement of battery technology are exponentially increasing. A few relevant examples of iron-based chemical cycles as energy storage devices and recent developments in the EES field are discussed below and summarized in Table 4.
Table 1 Comparative properties of iron and other elements for energy low carbon technologies (EU Comission 2023 (ref. 31); Kania and Saternus;32 EU Comission 2018 (ref. 33); Li et al.34)
Element (electrons transferred) |
Price per specific capacity ($ per mA h) |
Planetary element abundance (%) |
Price ($ per kg) |
Specific capacity (mA h g−1) |
Volumetric capacity (mA h cm−3) |
Redox potential (V) |
E-o-L recycling rate |
Toxicity |
Fe (2) |
0.125 |
5.3 |
0.12 |
960 |
7557 |
−0.45 |
62% |
Low |
Fe (3) |
0.08 |
1439 |
11 328 |
Al (3) |
0.92 |
8.2 |
2.73 |
2980 |
8046 |
−1.66 |
51% |
Low |
Li (1) |
3.77 |
0.002 |
14.56 |
3861 |
2062 |
−3.04 |
<5% |
Moderate |
Zn (2) |
3.81 |
0.004 |
3.12 |
820 |
5845 |
−0.76 |
45% |
Medium |
Mg (2) |
8.87 |
2 |
19.56 |
2205 |
3833 |
−2.37 |
13% |
Very low |
Cu (2) |
12.71 |
0.007 |
10.71 |
843 |
7558 |
+0.34 |
55% |
High |
Ni (2) |
22.52 |
0.009 |
20.56 |
913 |
8136 |
−0.26 |
16% |
High |
Co (2) |
29.87 |
0.003 |
27.15 |
909 |
8092 |
−0.28 |
22% |
High |
2.1. Fe–Cl2 chemical cycles for hydrogen production
The Fe–Cl (thermo- and electro-) chemical cycles have several advantages, such as low cost, known chemistry, and availability of materials. However, they also have some disadvantages, including low energy efficiency which is affected by either a low yield of reverse Deacon's reaction for chlorine conversion to HCl38 or the energy-consuming reduction of iron oxides. A recent example of both thermo- and electro-chemical cycles is a materially closed technological loop that employs the hydrogen evolution reaction between iron powder and HCl acid.39,40 Under room temperature conditions, the metallic iron is oxidized with HCl acid. The reaction releases hydrogen from HCl molecules while producing FeCl2 as a byproduct.
2.1.1. Thermo-electrochemical cycles. Thermo-electrochemical cycles for grid energy storage and examples of thermo–electrochemical cycles based on the reduction of Fe2+ ions in the ferrous chloride aqueous solution were patented40 and presented by Luin and Valant.41 In the reductive segment of this cycle, the grid energy is used to electrolyze concentrated FeCl2 solution and deposit the metallic Fe on the cathode. The iron metal becomes the energy carrier and can be easily stored. Chlorine gas is evolved at the anode and directed to a reactor, where within the reverse Deacon process the hydrochloric acid is regenerated, ready for re-use in the oxidative segment. In the oxidative segment, which comes into play when energy demand outstrips supply, the metallic energy carrier is reacted with hydrochloric acid to produce hydrogen on demand. A mol of H2 is formed per a mol of Fe. Without any need for storage, the hydrogen can be directly supplied to the fuel cell for conversion back to electrical energy (or for combustion). The remaining saturated metal chloride solution can then be stored, making it readily available for re-use in the reductive segment for electrolysis.The metal energy density can be calculated from the stoichiometry of the chemical processes described above and the crystallographic properties of the Fe crystal cell. The calculated energy density for Fe is 11.3 kW h L−1, which by far exceeds any other energy carrier used in the current energy storage technologies even liquid fossil fuels (see Table 2). The energy efficiency of the cycle can be as much as 80% and the AC-to-AC efficiency 38% (taking into account the 50%-efficiency of fuel cells).
Table 2 Comparison of specific energy and energy density of the energy carriers used in the proposed storage technology with currently used technologies and gasoline
|
Energy density [kW h L−1] |
Specific energy [kW h kg−1] |
Elemental Fe (calculated based on Atkins and de Paula 2010 (ref. 42)) |
11.3 (Fe oxidation with HCl yielding H2) |
1.4 (Fe oxidation with HCl yielding H2) |
16.1 (burning Fe powder to Fe2O3) |
2.1 (burning Fe powder to Fe2O3) |
Gasoline (Mazloomi et al. 2012 (ref. 43)) |
9.5 |
12.9 |
Hydrogen gas (atmospheric pressure) |
∼0.003 (Lanz et al.44) |
33.3 (LHV) |
Compressed hydrogen gas (700 bar) |
1.3 (Hirscher & Hirose 2010 (ref. 45)) |
39.4 (HHV) |
Liquid hydrogen (T =< −253 °C) |
2.2 (Hirscher & Hirose 2010 (ref. 45)) |
(Lanz et al.44) |
Hydrogen in hydrides (Abe et al. 2019,46 Klopčič et al. 2023 (ref. 47)) |
1.6–6.2 |
0.4–6.2 |
Commercially available Li-batteries (Li-ion, Li-polymer) (Choi and Aurbach 2016,48 Hamerr and van Niekerk 2015 (ref. 49)) |
0.2–0.7 |
0.1–0.3 |
Emerging battery technologies (Li–S, Li–air, Mg–air) (Hagen et al. 2015,50 Kim et al. 2019 (ref. 51)) |
0.4–1 |
0.35–1.5 |
Flywheels (Ibrahim et al. 2008 (ref. 52)) |
∼0.02 |
Compressed air energy storage (Hameer and van Niekerk 2015 (ref. 49)) |
∼0.01 |
Pumped hydropower energy storage (Ibrahim et al. 2008 (ref. 52)) |
∼0.001 |
By using the Fe solid-state energy carrier, it is possible to avoid the expensive hydrogen compression or refrigeration and its storage in tanks. It can resolve the fundamental problems of current EES technologies because it exhibits a combination of unique characteristics such as high energy density, a small land footprint for the new storage stations, no geographical constraints for the storage plants, no emission or waste due to a closed working cycle and no self-discharge during long-term storage (Fig. 1). In addition, the storage and conversion segments of the technology can be decoupled. The electrical energy storage can be realized at a suitable location near the power generation, while the conversion back to electricity can take place at one or multiple locations elsewhere. This offers the possibility for a very long-distance energy supply without losses (e.g., over deserts, over the sea to remote islands, etc.).
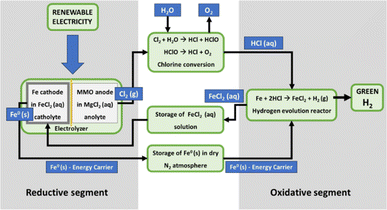 |
| Fig. 1 Schematic material-flow diagram of the Fe-based power-to-solid EES technology. | |
The importance of energy storage is undeniable, e.g. storing excess energy and thus reducing electricity production, reducing carbon emissions, and managing grid stability.53 The required characteristics such as long lifetime, low cost, high density, and efficiency are not yet all met simultaneously in energy storage technologies, so caution should be taken when selecting them for a particular application. Although the outlook for the future is very promising, the challenges of these systems remain technological and economic. Technologically, they struggle with achieving high energy density, long lifetimes, and high efficiency.54 Issues such as thermal management and material limitations also persist.55 Economically, high initial costs, maintenance expenses, market and policy uncertainties, and difficulties in securing financing still stay in the way of widespread adoption.56
2.1.2. Thermochemical Fe–Cl cycle. Recently, thermochemical methods have gained attention mainly because of their low environmental impact and cost-effectiveness. By using clean or waste energy sources they can be integrated into sustainable energy systems.57 These methods involve a closed material cycle, in which oxygen and hydrogen are produced from water within a sequence of reduction–oxidation reactions driven by thermal energy. These processes typically operate at high temperatures (500–2000 °C) using a combination of exothermic chemical reactions at low temperatures and endothermic reactions at high temperatures.38 The thermochemical methods can either use only thermal energy or can be hybrid, utilizing both thermal energy and an additional energy source such as electricity.58 The thermal energy required for these processes can be obtained through various means, such as concentrating sunlight, utilizing waste industrial heat, or electric heating. An example of reduction–oxidation reactions in the thermochemical cycles that produce hydrogen is the Fe2+ to Fe3+ back-and-forth conversions. One example of the chemical reactions involved in such cycles is shown in Table 3. Within these cycles, all materials are repurposed. In a modeling study of this cycle using Aspen Plus,59 it was shown that the pressure has a negligible effect on reaction production rates, but increasing temperature favors oxygen and magnetite production while decreasing hydrogen production. Increasing the steam-to-chlorine ratio increases hydrogen, oxygen, and hydrochloric acid production.59 Other types of the Fe–Cl cycles involve the oxidation–reduction reactions that occur between metallic iron and different iron species such as FeCl2 FeCl3, or different iron oxides.26,61,62
Table 3 The reactions of an iron–chloride thermochemical four-step cycle for hydrogen production from Safari and Dincer59 and Castro Oliveira et al.60
Steps |
Reactions |
Thermal decomposition |
2FeCl3 → 2FeCl2 + Cl2, ΔH0 = −160.5 kJ mol−1 |
(1) |
Reverse Deacon reaction |
Cl2 + H2O → 2HCl + 1/2O2, ΔH0 = +59.4 kJ mol−1 |
(2) |
Hydrolysis |
3FeCl2 + 4H2O → Fe3O4 + 6HCl + H2, ΔH0 = +156 kJ mol−1 |
(3) |
Chlorination |
Fe3O4 + 8HCl → FeCl2 + 2FeCl3 + 4H2O, ΔH0 = −244 kJ mol−1 |
(4) |
Table 4 Considerations for the essential role of iron in emerging energy technologies
Technology |
Maximum energy eff% |
Key advantages |
Key disadvantages |
Redox flow batteries (RBFs) |
VRBF |
87 |
High cycling stability |
Species crossover, high costs, temperature sensitivity, electrolyte management, infrastructure requirements |
High theoretical voltage, cost-effective |
ORBF |
82 |
High energy density, environmentally friendly |
Chemical instability, low solubility, degradation over time |
Zn–Br RFB |
85 |
High energy density, long cycle life |
Bromine toxicity, potential for zinc dendrites |
Zn–Ce RFB |
71 |
High cell voltage (∼2.4 V), lower cost compared to other RFBs |
Limited stability, limited large-scale application, lowest energy efficiency |
![[thin space (1/6-em)]](https://www.rsc.org/images/entities/char_2009.gif) |
Iron redox flow batteries |
Fe RFBs |
87 |
Scalability, longer cycle lives, non-toxic |
Internal short circuits risk |
Fe–Cl RFB |
83 |
Eco-friendly, low cost |
Low stability |
![[thin space (1/6-em)]](https://www.rsc.org/images/entities/char_2009.gif) |
Iron batteries |
Fe-air |
94 after 1000 cycles |
High energy density, cost-effective, environmentally friendly |
Dendrite growth, longevity, anode passivation |
![[thin space (1/6-em)]](https://www.rsc.org/images/entities/char_2009.gif) |
Emerging iron batteries |
RCII |
<80 |
Competitive reactivity, dynamics, energy density |
Dissolution in acidic electrolytes, sluggish redox reaction |
IHE |
93 |
Stable lifetime (>20 000 cycles), cost-effective |
Limited implementation |
Battolyser |
90 |
Dual-function (battery and electrolyzer) |
Still under research and development |
In the regeneration segment, FeCl2 is thermally decomposed to yield HCl acid and iron oxide that is utilizing metallurgical processes reduced back to iron. The required low-temperature thermal energy for the decomposition processes can be obtained from industrial waste heat or concentrated sunlight as a renewable energy source.62 This makes the process highly sustainable and ready to be integrated into clean energy systems. We conducted a life cycle assessment analysis (LCA) on this hydrogen production process, focusing on the operation phase. The detailed results will be presented in a forthcoming study. The operation phase included the use of water, heat, and electricity. Results comparing two scenarios (photovoltaic vs. grid electricity) show that the scenario using grid electricity has a significantly higher environmental impact than photovoltaic. This is evident in terms of abiotic depletion of elements and marine aquatic ecotoxicity potential (3 times higher), eutrophication potential, and ecotoxicity potential (2 times higher). Acidification potential and freshwater aquatic ecotoxicity show similar impacts in both scenarios. The analyzed process is sustainable and operates on a closed-loop principle, regenerating materials (iron and HCl) and requiring no additional raw materials. It can utilize intermittent renewable energy sources and act as a heat recovery system, producing a significant amount of green hydrogen. We refer to the preliminary studies conducted by Knoche et al.63 and the comprehensive experimental studies conducted by Canavesio et al.,61 which revealed that the Fe–Cl thermochemical cycle achieved a maximum energy efficiency of 37%, lower than the alternative cycles such as the Cu–Cl cycle with an efficiency of around 55%. The breakthrough in the implementation of Fe–Cl cycles might be achieved if the reverse Deacon's reaction could be replaced with a low-temperature catalytic process. In addition to the energy efficiency gains, the implementation of low-temperature catalytic processes would offer significant economic benefits. The reduced energy demand directly translates into lower operational costs. Moreover, the capital expenditure (capex) required for establishing and maintaining the Fe–Cl cycle system would also decrease, contributing to enhanced economic viability. The development of low-temperature catalytic processes would not only optimize Fe–Cl cycles but would also have important implications for industrial HCl production. Currently, vast amounts of hydrogen are consumed in the synthesis of HCl. By utilizing low-temperature catalytic processes, the hydrogen as a reactant would be substituted with hydrogen from water molecules, resulting in significant savings and making HCl production more cost-effective.
Challenges also involve chlorine management and corrosion prevention,64 alongside the effective handling of reaction heat, FeCl3 thermal decomposition kinetics, and hydrolysis of FeCl2.58 Due to the complexity of thermochemical cycles, studies on their simulation and performance at an industrial scale are limited.65 Concerning environmental and safety risks, it is important to understand that very sophisticated and safe chlorine technology measures have already been developed and are required to be implemented in technology systems and processes involving chlorine or HCl.66 The chlorine technologies must comply with the so-called Best Available Techniques (BAT) documents for chlorine management67,68 and, if so, the environmental and safety risks are well under control. However, it is a fact that these measures make chlorine technology more expensive.
2.1.3. Electrochemical Fe–Cl cycle. The iron chloride electrochemical cycle is based on the electrolysis of FeCl2 aqueous solution. Energy is stored in the reductive–oxidative potential change Fe2+/Fe by electro-reduction of iron cations from a concentrated FeCl2 aqueous electrolyte, yielding metallic iron deposits on the cathode. Simultaneously, the evolved chlorine gas on the anode enters conversion to HCl acid through a reversed Deacon process.69 Energy is released as hydrogen gas on demand through a spontaneous reaction between iron and HCl acid. Iron and HCl acid can be stored stably for months, without self-discharge of stored energy. This makes the FeCl2 electrochemical cycle. Suitable for long-term high-capacity energy storage technology.40,41 Integrating iron chemical cycles within the iron industry and renewable energy storage systems for supporting the grid, as presented in Fig. 2, the potential of iron as a sustainable fuel source is highlighted.
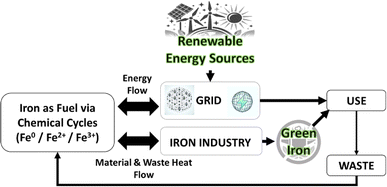 |
| Fig. 2 Integration of iron chemical cycles into the iron industry and grid energy storage. | |
2.2. Electrochemical energy storage using iron
Electrochemical energy storage (EES) systems play an important role in the utilization of renewable energy sources to balance the grid during energy fluctuations.70 They can be implemented in stationary, portable, or transport applications. Aqueous rechargeable batteries using water-based electrolytes are promising alternatives due to their safety and potential to reduce production costs.71
2.2.1. Redox flow batteries (RFB). RFBs represent such an option for large-scale energy storage. RFBs have a range of unique chemistries, each with its distinctive features and challenges. Despite the numerous advantages, their widespread use is limited due to various obstacles. The hydrogen–bromine RFB (HBr RFB) chemistry, despite its potential as is the high-power density, struggles with corrosion issues. The corrosive nature of bromine can cause severe damage to the components, potentially limiting the longevity and efficiency of the system.72 While the vanadium RFB excels in cycling stability, it poses significant environmental concerns due to its extensive use of vanadium electrolytes and the potential for leakage into groundwaters. Despite their advantages, high production and maintenance costs hinder the widespread adoption of vanadium RFBs, which must be addressed for large-scale energy storage viability.73,74 China is leading with recent installations of 200 MW/800 MW h and 100 MW/500 MW h vanadium RFBs in Dalian and Hubei provinces.75 In a related development, a vanadium–chromium RFB (V/Cr RFB) has been developed, combining the benefits of all-vanadium and iron–chromium systems. This system features a high theoretical voltage of 1.41 V and cost-effective chromium use, achieving a peak power density of over 900 mW cm−2 at 50 °C and stable performance over 50 cycles with over 87% energy efficiency, making it a promising candidate for large-scale energy storage.76 Zinc–bromine RFB (Zn–Br RFB) uses a zinc bromide salt solution, and they are known for their high energy density and long cycle life.77,78The organic RFB uses organic compounds as active redox species instead of metal ions. Their appeal comes from the wide range of potential organic molecules that could be used, which might provide higher energy density or more environmentally friendly options.34 Aqueous hybrid organic–inorganic RFBs based on AQDS-ferrocyanide active materials have been used to highlight the main characteristics of ORFBs.79 Research interest is growing in non-aqueous systems to pursue higher voltage output from RFBs, as conventional aqueous RFBs have a limit of the cell voltage window of 1.24 V. Non-aqueous organic RFBs exhibit other advantages, such as higher energy density, wider operating temperature range, faster reaction kinetics, and more combinations of organic redox couples.80 However, organic solvents used in non-aqueous systems are known to have disadvantages such as volatility and toxicity.81 The active organic species themselves can suffer from issues such as chemical instability, crossover through the membrane, low solubility, and degradation over time, which can negatively impact the performance and lifespan of the batteries.82,83
Zinc–cerium (Zn–Ce) batteries are a type of redox flow battery that uses cerium(III)/cerium(IV) and zinc for the redox couple. The Ce(III)/Ce(IV) and Zn(II)/Zn redox reactions take place at the positive and negative electrodes, respectively. Zinc–cerium batteries are known for their high cell voltage, high energy density, and lower cost compared to other redox flow batteries. Zinc–cerium RFBs are capable of providing one of the highest cell voltages (∼2.4 V) among flow batteries and a large theoretical energy density.84 Another RFB chemistry is based on iron chloride (FeCl RFB). This type is well-regarded for its eco-friendliness and low cost. However, the most significant challenge for FeCl RFB is stability, which hinders its broader application in energy storage systems.
2.2.2. Iron redox flow batteries (Fe RFBs). In contrast, iron redox flow batteries (Fe RFBs) employ a distinct design with separate tanks for catholyte and anolyte. The energy storage capacity in Fe RFBs is determined by the volume of these tanks, making them highly scalable and ideal for utility-scale storage solutions. They typically exhibit longer cycle lives due to reduced degradation mechanisms. Moreover, while all-iron batteries are generally safe, they might face risks like internal short circuits. Fe RFBs, on the other hand, present a lower risk profile because of their aqueous solutions and the use of non-toxic iron-based electrolytes.Fe RFBs are one of the key technologies for increasing the integration of renewable energy into the grid due to the abundance of Fe, environmental-friendliness, flexibility, and scalability.85 The principle of a flow battery system consists of a power generation unit and an energy storage unit with ionic solutions used as electrolytes and stored in separate storage tanks. The electrolytes are circulated between the two units through flow channels and directed to the surface of the electrodes where the reaction takes place. The electrodes are inert and serve as catalyst supports. After the reaction is complete, the electrolytes are returned to the storage tanks where they are regenerated later during charging. Their efficiency was estimated to be around 70–80%, which is higher than fuel cells.86 The electrochemical reactions of iron flow batteries were first proposed by Hruska and Savinell:87
All-iron flow batteries utilize iron-based redox couples in the electrolyte solution. In this system, both electrolytes (anolyte and catholyte) are highly concentrated iron (ferrous and ferric) chloride aqueous solutions in two separate tanks, one with a reduced form of iron (Fe/Fe2+) and the other with an oxidized form (Fe2+/Fe3+). Electrolytes are pumped into a cell stack separated by a selective anion exchange membrane. During charging, electrochemical redox reactions occur at both electrodes, converting electrical energy into chemical potential by changing the oxidation state of the iron ions. During discharge, the reactions reverse, releasing the stored energy as electrical power. The iron-based electrolytes offer advantages over other chemistry variants in terms of abundance, cost-effectiveness, and environmental safety. The energy storage capacity of an iron flow battery is determined by the total volume of electrolytes, while the power output is determined by the size and design of the cell stack.88,89
A comparative LCA study was conducted to evaluate iron-flow batteries and lithium-ion systems in industrial production the study revealed that the iron-flow batteries outperform lithium-ion systems in terms of selected materials and production parameters (e.g., iron-based electrolytes and carbon-based cell stacks).90 Additionally, the iron flow batteries offer several application advantages such as extended cycle life and the ability to independently manage power and energy operations. To further mitigate environmental impact, it is recommended to replace polymer resins with alternative materials that have lower ecotoxicity. In recent years, efforts have been made to develop a new generation of low-cost iron flow batteries for long-term energy storage systems, and among these, liquid flow batteries and hybrid flow batteries are interesting options.91 A promising low-cost alkaline whole-iron flow battery was developed by coupling ferric/ferrous-gluconate complexes with [Fe(CN)6]3−/[Fe(CN)6]4− system.92 This new all-iron flow battery system exhibited a coulombic efficiency of over 99% and an energy efficiency of ∼83% at a current density of 80 mA cm−2 and can operate continuously for more than 950 cycles. Another potentially inexpensive approach to storing large amounts of energy is through the use of a redox concentration flow cell battery that uses aqueous iron chloride as a reacting solution on carbon electrodes.93 This method is promising in terms of cycling and power density of the cell but still needs more work on cycling and chemical stabilization of the iron-based electrolytes, which could be achieved with the addition of organic acids like citric or ascorbic acid.
2.2.3. Iron batteries. Iron batteries are solid-state devices where the electrodes and electrolytes have direct contact, yielding a fixed energy capacity determined by the battery's physical size. They are best suited for applications requiring a fixed capacity, such as residential power backups. However, they may encounter longevity challenges, such as dendrite growth.Iron-batteries have a theoretical specific energy density of 1200 W h kg−1 which is way better than commercially available lithium-ion batteries (100–265 W h kg−1).94 They consist of a negative iron electrode, a positive air electrode, and an alkaline electrolyte. In this system, in the negative electrode half-cell, the iron oxidation from elementary through Fe(II) to Fe(III) occurs, while in the positive electrode half-cell, the reduction of oxygen occurs yielding iron oxides and resulting in a voltage of about 1.28 V.95 The iron–air batteries are considered advanced secondary batteries due to the low solubility of the electrolytically deposited iron, which is a disadvantage for primary batteries. One example is an iron–air battery-microbial electrolysis cell system that was used to treat swine wastewater and produce hydrogen in a self-powered mode.96 In this system, the iron–air battery produced coagulants necessary for pollutant removals such as carbon oxygen demand (COD) and electricity, while the microbial fuel cell powered by the iron–air battery generated hydrogen. Powered by a battery with an electrolyte concentration of 35 g L−1 NaCl, the COD removal rate of the microbial fuel cell with the coagulation process reached 98%, and hydrogen generation reached cca. 6 L per m3 per day using raw swine wastewater and 57 L per m3 per day using coagulated swine wastewater. The commercialization of Fe–air batteries is limited by certain drawbacks, including potential hydrogen leaks and anode passivation due to the formation of iron oxide films. These factors contribute to the low cycling stability of Fe–air batteries and lead to battery capacity deterioration.97 Recently, among the various strategies to improve the efficiency of iron–air batteries, the use of ionic liquids (ILS) was proposed.98 In this study, 1-ethyl-3-methylimidazolium L-(+)-lactate was used for the first time as an electrolyte additive to suppress hydrogen release and anode passivation for iron–air batteries. This method resulted in a capacity retention of more than 94% after 1000 cycles with a nominal capacity of 0.416 A h g−1 at a charging or discharging rate equivalent to one-fifth of the battery's capacity.
2.2.4. Emerging iron batteries.
Rocking-chair iron-ion battery. Rocking-chair iron-ion batteries are new rechargeable aqueous metal-ion batteries without adverse electrolyte modifications that are more competitive than acidic all-Fe cells or zinc metal batteries, in terms of reactivity/dynamics, performance, and energy density.99 In this system, Fe2+ ions circulate between an iron supplier anode and a host cathode. Wu et al. demonstrated the viability of Fe metals as anodes using a reversible Fe plating/stripping process in a FeSO4 salt solution at a pH of ∼3–5 and reversible Fe2+ topotactic insertion into a Fe-based Prussian blue analog or LiFePO4 cathodes at 1000 cycles.36 Despite the advances, iron anodes are still plagued with side effects such as dissolution in acidic aqueous electrolytes, low coulombic efficiency (<80%), and sluggish redox reaction kinetics.20
Iron–hydrogen battery. Iron–hydrogen battery is a novel rechargeable aqueous battery system for large-scale energy storage,100 designed as a static cell without using electrolyte pumping or circulation systems, which reduces manufacturing costs. It is based on the [Fe(CN)6]3−/[Fe(CN)6]4− redox couple cathode and hydrogen gas anode in an alkaline solution. This battery operates at a current range of 10–60 mA, with an output voltage of 1.29 V, an energy efficiency of 93%, and an ultra-stable lifetime of over 20
000 cycles.
Battolyser. The battolyser combines two energy storage approaches electricity stored in a nickel–iron battery and as a water-splitting device that outputs hydrogen gas as the energy carrier.101 The study conducted by Barton et al.,102 showed that it can be used for both short- and long-term energy storage. The short-term is done by DC electricity storage as a Ni–Fe battery, while the long-term is through hydrogen gas, which evolves on the same Ni and Fe electrodes when the battery electricity storage capacity is fully charged or reached. In essence, the battolyser could serve as both an electrolyzer for power-to-X energy conversion and an electrochemical Ni–Fe battery.
3 Iron as circular fuel
In recent years, metal-fuel cycles have been proposed for large-scale thermal energy generation because their use avoids harmful emissions, is advantageous for storage and transportation, and has high energy density.29 Aluminum, iron, magnesium, silicon, and titanium have been identified as feasible metal fuels that can be recycled and reused an unlimited number of times.103
Iron as a clean metal fuel is gaining importance. Still, a better understanding of the fundamental properties of iron combustion is required for the development of new iron fuel technologies. Detailed characteristics of iron combustion such as flame propagation,104 flame temperatures of iron aerosols,105 and the behavior of a single laser-ignited iron particle106 have only recently become available.
A recent study conducted by Goroshin et al.107 investigated the structure and velocity of laminar iron dust flames under controlled laboratory and microgravity conditions. The selected conditions eliminated factors such as particle sedimentation and bulk instability of dense dust clouds. Consequently, the study allowed observation of the flame at low velocities in suspensions containing large particles and slow-burning, non-volatile fuels. The study not only explored the potential applications of these findings in combustion systems but also shed light on the challenges and the promising prospects of solid fuels for propulsion and power generation purposes. To fully understand the implications of laminar flame experiments, it is crucial to combine the obtained results with numerical modeling and simulations that consider the underlying physics of the systems where these findings may find practical application. For this reason, various numerical models have been developed focusing either on the effect of slip, Stefan flow, evaporation, or the ignition phase.108,109 More recently, the study by Thijs et al.110 improved a 0D Lagrangian particle model for the first stage of diffusion-limited iron particle combustion (heat and mass transfer) using a boundary layer-resolved model.
The flame temperature of iron/air suspensions is 1500–1900 °C,111 which is comparable to that of hydrocarbon fuels, but without CO2 emissions. The solid iron oxides produced during combustion are easily recycled. Because of these fuel properties, the use of iron as metal fuel has been proposed for retrofitting coal-fired power plants.112 Theoretically, replacing coal with iron in power plants could reduce CO2 emissions by an estimated 10 million t per year.113 A multi-stage feasibility assessment based on forecast data on iron, hydrogen, and renewable energy production, showed that a retrofit plan is feasible in reality. The proposed model combined existing technologies. Carbon-free carriers, such as iron, are used in a redox cycle. The oxidation of elementary iron by burning in oxygen releases heat and results in solid Fe2O3. The heat generates steam that drives the turbines which turn the generator as in a classic steam-compression cycle. There are no greenhouse gas emissions and the ‘ash’ in such a system are solid iron oxides that can be easily stored, transported, and recycled to elementary Fe and oxygen gas at the reduction facilities. Ideally, the iron oxides are reduced electrochemically using renewable sources or using green hydrogen for the thermochemical processes. This model is an example of a circular energy economy.112 The phasing out of coal will need a long transition, predicted to be difficult for many countries. Some countries, such as Germany, plan to reach this goal by 2030.114 Another example of here is the usage of iron powder as a circular fuel, which has been implemented in an industrial process in a beer brewing plant at Bavaria Brewery in Lieshout, near Eindhoven.115
3.1. Trends and challenges for sustainable iron production and recycling
The iron and steel industry, accounting for one-third of global CO2 emissions, has received limited attention in terms of sustainable transition.14,116 Despite the pressure to adopt more sustainable production methods, transitioning to low-carbon processes is a time-consuming and complex endeavor that involves radical innovations and thorough testing.117,118 The industry is often seen as slow and resistant to large-scale transitions, but it is currently on the brink of a new technological shift driven by not only productivity and profitability but also the imperative of environmental sustainability. This urgency is primarily influenced by climate change mitigation policies aiming to reduce CO2 emissions.119 It was estimated that without taking appropriate measures, the emissions from industry could reach 2.7 Gt CO2 per year by 2050, which is 7% higher than today.120 To ensure a decarbonized energy future, it is essential to adopt planning technologies that prioritize reuse, redistribution, and remanufacturing, while placing significant emphasis on longevity and regenerative materials. In this context, the potential for sustainable iron production becomes a crucial topic of discussion. Specifically, we explore the possibilities of reducing iron using hydrogen as well as producing iron through electrolysis. By focusing on these approaches, we can pave the way forward toward a more sustainable and environmentally friendly iron production process.
3.2. Reduction of iron with hydrogen
To reduce the carbon footprint of the iron and steel industry, hydrogen metallurgy, namely the use of hydrogen as a reducing agent, is of great interest. Direct reduction of iron (DRI) in shaft furnaces or fluidized bed reactors,121 hydrogen plasma-based reduction,122 and direct injection of hydrogen into existing blast furnaces, in addition to coke123 are three approaches considered to have high feasibility for future industrial applications. The direct reduction of iron with hydrogen, which adapts an already mature technology, is considered a promising method for achieving carbon neutrality in the iron and steel industry. This process was reported to be mainly carried out at high temperatures of 700–1000 °C, but also at lower temperatures (500 °C) for the production and separation of metallic iron from sandy and silty tailings.124 Examples of projects that will commercialize large-scale hydrogen DRI plants in the future include the Hybrit project (already in operation) in Sweden with an expected increase in iron production of 1 million tons per year by 2025 (ref. 125) and projects by ThyssenKrupp ArcelorMittal planned for 2024 and 2030, respectively.
3.3. Hydrogen plasma iron reduction
Hydrogen plasma represents a promising carbon-neutral solution for iron production.126–128 During hydrogen plasma reduction, a plasma arc zone forms between an electrode and the input iron ore (e.g., hematite). In this zone, the ore is both melted and reduced by hydrogen, which exists in molecular and plasma states. The plasma state consists of ionized (H+, H2+, and H3+), excited (H*), and atomized (H) species formed through hydrogen particle collisions with electrons.129 Hydrogen plasma reduction offers simultaneous ore reduction and melting, enabling the inclusion of scrap in the same process. However, hydrogen plasma reduction is still in the exploratory stage despite its thermodynamic efficiency. Souza Filho et al.130 proposed a hybrid approach between hydrogen-based direct reduction and hydrogen plasma reduction to improve hydrogen and energy consumption of iron ore reduction. The results showed that this hybrid process consumes six times less hydrogen than laboratory-scale direct reduction at 700 °C. A hybrid approach allows the exploitation and maximization of specific technology characteristics and kinetically favorable regimes leading to reduced energy and hydrogen consumption, enhanced production stability, and an extended lifespan of the furnace. Moreover, it eliminates the need for unnecessary H2 recirculation and enables cost-competitive production of pure iron.
The green hydrogen production required for iron ore reduction is expected to remain a challenge for the next two decades. Factors such as high recycling costs, inefficient conversion, energy-intensive production and storage of green hydrogen,131 and the very high annual production demand of approximately 100 million tons130 contribute to this challenge. However, studies have shown that CO2 emissions in the iron and steel industry can be reduced by 78–95% if carbon is replaced by hydrogen from renewable sources.132 Currently, the hydrogen supply side is still dominated by low-cost steam methane reforming and coal gasification. Water electrolysis powered with surplus hydro, wind, and photovoltaic power currently appears to be the only viable option to supply the required quantities of green hydrogen at an acceptable price.133
3.4. Iron production through electrolysis of iron oxide
Electrolysis is a promising solution for both iron recycling and production from iron oxide ore, due to minimal direct CO2 emissions. However, the implementation of iron ore electrolysis has faced challenges such as low energy efficiency and the absence of a suitable anode material capable of withstanding high temperatures and corrosion.134 Nevertheless, recent advancements in electrowinning135 and molten oxide electrolysis136 are prominent approaches in this field.
Electrowinning or electroextraction (a subset of electrolysis, specifically used to recover metals from aqueous solutions of their salts, the metal ions in solution are reduced at the cathode to form a metal deposit) is a promising technology that has already been demonstrated on a small scale.135 In this process, the electrolyte is iron ore (iron oxide particles) suspended in an alkaline sodium hydroxide solution at an elevated temperature of 100–110 °C. The metallic iron is deposited on the cathode through the electro-reduction of iron(III) cations (Fe3+), while the hydroxide anions are oxidized to oxygen gas at the anode. The obtained iron purity is high (∼99.98%), and the reported energy consumption is up to 3 kW h kg−1 Fe, for a setup with an iron production capacity of 5 kg per day.137 Another example reported in the literature by Wang et al.138 is the electro-reduction of Fe2O3 to produce metallic Fe at an even lower temperature of 110 °C in an alkaline solution.138 In this study, an electrical-ionic conductive colloidal electrode containing electrochemically active Fe2O3 particles, NaOH solution, and a percolating electrical conductor (C-network) was applied.138 The drawbacks currently preventing a practical application of low-temperature electrolysis include the issue of Fe2O3 particle adherence to the electrode surface, a low reaction rate, and low energy efficiency of Fe2O3 electro-reduction.139
Molten oxide electrolysis requires very high temperatures between 1550 and 1700 °C. Various electrolytes have been studied for this process, such as molten salts,140 molten oxide, molten carbonates,141 and a low-temperature approach by using aqueous solutions.142 To make iron production more sustainable, reducing the working temperature of electrolysis has gained attention. In a study by Choi et al.,143 the B2O3–Na2O oxide system was shown to act as a supporting electrolyte for the electrochemical reduction of Fe2O3 to Fe at a lower temperature than any other molten oxide electrolysis method. In this case, the average energy consumption was 5.27 kW h kg−1 of Fe for electrolysis at 1000 °C which is low for an oxide melt. However, a challenge is ensuring a stable anode. Progress has been made in addressing the problem of anode oxidation by utilizing an electrically conductive solid solution of chromium and aluminum oxides with a corundum structure.144 Another challenge is technological readiness, which currently is less than five on a scale of nine, and industrial development may not occur until 2045 or even 2050.145
Deep Eutectic Solvents (DESs) are formed by mixing two or more compounds at a certain molar ratio, where the melting point of the mixture is lower than that of each component. DESs exhibit great potential as functional electrolytes involved in electrochemical devices and energy storage systems, as well as for other various fields, due to their low toxicity, biodegradability, ability to dissolve a wide range of materials, environmental friendliness, and cost-effectiveness.146–148 Moreover, their attractive features for ES technologies include low flammability, minimal volatility, high ionic conductivity, and excellent chemical stability. Several reviews have examined the utilization of DESs for metal extraction, recycling, and recovery.149,150 Alongside their various applications, DESs also serve as flexible platforms for high-performance electrocatalysts, particularly for metal digestion and recovery, as metal oxides have significant solubility in DESs.151 The literature on novel eutectics in electrochemistry focuses on binary eutectics of choline chloride and hydrogen-bond donors (e.g., ethylene glycol, glycerol, oxalic acid, and urea).152 Their extended applications are ternary or quaternary eutectics with a mixture of hydrogen-bond donors.153 One example is calcium chloride hexahydrate eutectics with ethylene glycol, which provide a cheaper and more environmentally friendly liquid formation for metal recovery compared to other DESs. These have been successfully used in the electrodeposition of Fe, Co, and Ni at ambient temperature without additives.154 In Table 5, selected iron and steelmaking technologies are summarized as environmentally friendly alternatives to the conventional blast furnace technology.
Table 5 Comparison of CO2 emission reduction potential and various characteristics from selected iron and steelmaking technologies (CO2 emissions reduction are compared with traditional blast furnace–basic oxygen furnace (BF-BOF) ironmaking)
Production method |
CO2 emissions reduction potential |
Advantages |
Disadvantages/issues |
DRI (coal-based) |
38% (Ling et al. 2024 (ref. 155)) |
Large production; mature technology for industrial application |
High-temperature operation (700–1000 °C); high hydrogen demand; cost of green hydrogen production; low iron oxide pellet quality |
H2DRI |
6% (Ling et al., 2024 (ref. 155)) |
|
|
CH4DRI |
97% (Ling et al., 2024 (ref. 155)) |
|
|
DRI-EAF |
Depends on the % of DRI used with scrap, 50% (35% scrap and 65% DRI) (Hornby and Brooks, 2021 (ref. 156)) |
|
|
Hydrogen plasma smelting reduction |
95% (Draxler, 2021 (ref. 157)) |
Thermodynamic efficiency; ability to include scrap in the process |
Still in exploratory stage; high energy consumption; high temperature operation (1500–1700 °C) |
Electrowinning |
87–95% |
High iron purity (up to 99.9%); low decomposition voltage, reduced oxygen evolution potential and minimal hydrogen evolution side reactions (Wang et al., 2023 (ref. 158)) |
Low energy efficiency; anode materials; high operational temperatures (100–110 °C) |
Molten oxide electrolysis |
96% (Draxler et al., 2021 (ref. 157)) |
Minimal direct CO2 emissions; high iron purity (up to 99.9%) |
Low energy efficiency; suitable anode materials; high operational temperatures (1550–1700 °C molten) |
Deep eutectic solvent extraction |
Depend on the lifecycle analysis, including DES component production and energy sources used (Zaib et al., 2022 (ref. 159)) |
Low toxicity; biodegradability; cost-effective |
Limited industrial scale application; need for optimization of solvents and processes |
4 Conclusions
This paper highlights the transformative potential of iron in a decarbonized energy future, emphasizing its role as an energy carrier, particularly in the production of green hydrogen and grid energy storage. Innovations such as iron redox flow batteries (Fe RFBs) and iron–hydrogen batteries offer scalable, efficient, and non-toxic solutions for utility-scale storage. The battolyser system, which combines a nickel–iron battery with the production of hydrogen, is a versatile energy storage option. Iron-based chemical cycles, such as the FeCl2 cycle for hydrogen production, and thermo–electrochemical cycles, where iron is oxidized with HCl acid, show the potential for sustainable closed-loop hydrogen production technologies. Innovative approaches such as hydrogen metallurgy and the electrolysis of iron oxide ore, promise to minimize CO2 emissions and reduce the carbon footprint of iron and steel production. Despite challenges such as low energy efficiency and suitable anode materials, progress in electrowinning and molten oxide electrolysis is promising. Policy measures and technological advances are crucial for the uptake and recycling of iron-based technologies and emphasize the need for collaborative efforts to create a sustainable energy ecosystem.
Research into novel iron-based energy storage technologies that go beyond batteries, such as supercapacitors or hybrid systems that combine different storage mechanisms, also includes research into advanced materials and manufacturing processes to improve the performance and efficiency of these solutions. The integration of artificial intelligence and machine learning algorithms is crucial for optimizing the operation and management of iron-based energy storage systems. Interdisciplinary approaches for sustainable iron production and energy storage applications are utilized through collaboration with other industries and research areas. The focus is on the scalability and economic viability of iron-based technologies to facilitate their widespread adoption in the energy sector.
The future of iron-based energy technologies looks promising with advances in materials, production methods, and applications. Nanostructured iron materials offer higher efficiency, while hybrid systems combining iron batteries with supercapacitors offer high energy efficiency and fast-charging capability. Sustainable production methods, such as the integration of green hydrogen production with iron production, can significantly reduce CO2 emissions. In addition, advanced electrochemical reduction techniques provide energy-efficient and environmentally friendly alternatives to conventional processes.
The transition to a circular economy concept further maximizes resource efficiency. By integrating sustainable practices into the entire life cycle of iron-based energy technologies, such as recycling and reusing materials, we can minimize waste and reduce environmental impact. LCA studies are critical to guiding sustainable practices by assessing the environmental impact of iron-based energy technologies, enabling informed decision-making, and promoting sustainable development.
Emerging applications of iron include its potential as a fuel or as a material for space exploration, as it is abundant and recyclable. The integration of iron-based energy storage into smart grids can improve grid stability and support renewable energy sources.
Data availability
No primary research results, software or code have been included and no new data were generated or analysed as part of this review.
Author contributions
Conceptualization: M. V. and A. O. M.; investigation: A. O. M. and U. L.; writing – original draft: A. O. M., U. L. and M. V.; writing – review & editing: A. O. M. and U. L.; visualization: U. L.; funding acquisition: M. V.
Conflicts of interest
There are no conflicts to declare.
Acknowledgements
We acknowledge funding from the Slovenian Research Agency (grant number P2-0412).
Notes and references
- K. Hund, D. La Porta, T. P. Fabregas, T. Laing and J. Drexhage, Minerals for Climate Action: the Mineral Intensity of the Clean Energy Transition, World Bank, 2023 Search PubMed.
- T. Watari, K. Nansai and K. Nakajima, Resour., Conserv. Recycl., 2021, 164, 105107 CrossRef CAS.
- J. Kim, B. K. Sovacool, M. Bazilian, S. Griffiths, J. Lee, M. Yang and J. Lee, Energy Res. Soc. Sci., 2022, 89, 102565 CrossRef.
- M. L. C. M. Henckens and E. Worrell, J. Cleaner Prod., 2020, 264, 121460 CrossRef CAS.
- EU Commission JRC, E. Garbarino, F. Ardente, D. Blagoeva, F. Bouraoui, G. Blengini, C. Pavel, C. Torres De Matos, F. Mathieux, T. Hámor, S. Solar, P. Nuss, D. Wittmer, E. Tzimas, B. Gawlik, P. Alves Dias, G. Orveillon, H. Saveyn, D. Huygens and S. Bobba, Critical Raw Materials and the Circular Economy ? Background Report, Publications Office of the European Union, Luxembourg (Luxembourg), 2017 Search PubMed.
- X. Lu, W. Tian, H. Li, X. Li, K. Quan and H. Bai, Int. J. Miner., Metall. Mater., 2023, 30, 388–400 CrossRef.
- C. Wulf, J. Linßen and P. Zapp, Energy Procedia, 2018, 155, 367–378 CrossRef.
- M. Abdul Quader, S. Ahmed, S. Z. Dawal and Y. Nukman, Renewable Sustainable Energy Rev., 2016, 55, 537–549 CrossRef CAS.
- Paul Wurth - Direct Reduction Technology, https://www.paulwurth.com/en/technology/direct-reduction/, accessed December 15, 2023.
- ArcelorMittal, Climate Action Report, https://constructalia.arcelormittal.com/files/Climate_Action_Report_2_July_2021--94aa5d83ef86cd03ec059ef8d1728966.pdf, accessed December 15, 2023.
- Primetals Technologies, Primetals Technologies develops break-through technology for carbon-free, hydrogen-based direct reduction for iron ore fines, https://www.primetals.com/fileadmin/user_upload/press-releases/2019/20190626/PR2019061901en.pdf, accessed December 15, 2023.
- A. Hasanbeigi, L. K. Price and M. Arens, Emerging Energy-Efficiency and Carbon Dioxide Emissions-Reduction Technologies for the Iron and Steel Industry, Berkeley, 2013 Search PubMed.
- K. Nishioka, Y. Ujisawa, S. Tonomura, N. Ishiwata and P. Sikstrom, J. Sustain. Met., 2016, 2, 200–208 CrossRef.
- E. Karakaya, C. Nuur and L. Assbring, J. Cleaner Prod., 2018, 195, 651–663 CrossRef.
- T. Kaiser, A. Rathgeb, C. Gertig, A. Bardow, K. Leonhard and A. Jupke, Chem. Ing. Tech., 2018, 90, 1497–1503 CrossRef CAS.
- J. Zhao, H. Zuo, Y. Wang, J. Wang and Q. Xue, Ironmaking Steelmaking, 2020, 47, 296–306 CrossRef CAS.
- First Hydrogen-Based DRI Plant - Tenova China, https://tenova.com/newsroom/press-releases/first-hydrogen-based-energiron-dri-plant-tenova-china, accessed December 15, 2023.
- GFG Alliance, https://www.gfgalliance.com/media-release/gfg-alliance-signs-mou-with-romanian-government-to-create-a-european-greensteel-flagship-at-liberty-galati/, accessed December 15, 2023.
- H2 Green Steel Newsroom, https://www.h2greensteel.com/newsroom/h2greensteel, accessed December 15, 2023.
- J. Jiang and J. Liu, Interdiscip. Mater., 2022, 1, 116–139 CrossRef.
- N. Sazali, Int. J. Hydrogen Energy, 2020, 45, 18753–18771 CrossRef CAS.
- M. Genovese, A. Schlüter, E. Scionti, F. Piraino, O. Corigliano and P. Fragiacomo, Int. J. Hydrogen Energy, 2023, 48, 16545–16568 CrossRef CAS.
- M. Luo, Y. Yi, S. Wang, Z. Wang, M. Du, J. Pan and Q. Wang, Renewable Sustainable Energy Rev., 2018, 81, 3186–3214 CrossRef CAS.
- R. Ramezani, L. Di Felice and F. Gallucci, JPhys Energy, 2023, 5, 24010 CrossRef.
- S. Song, L. Yu, X. Xiao, Z. Qin, W. Zhang, D. Wang, J. Bao, H. Zhou, Q. Zhang, S. Chen and Z. Ren, Mater. Today Phys., 2020, 13, 100216 CrossRef.
- F. Safari and I. Dincer, Energy Convers. Manage., 2020, 205, 112182 CrossRef CAS.
- A. G. Korotkikh, O. G. Glotov, V. A. Arkhipov, V. E. Zarko and A. B. Kiskin, Combust. Flame, 2017, 178, 195–204 CrossRef CAS.
- E. L. Dreizin, Prog. Energy Combust. Sci., 2009, 35, 141–167 CrossRef CAS.
- J. M. Bergthorson, Prog. Energy Combust. Sci., 2018, 68, 169–196 CrossRef.
- J. Palecka, S. Goroshin, A. J. Higgins, Y. L. Shoshyn, P. de Goey, J. R. Angilella, H. Oltmann, A. Stein, B. Schmitz, A. Verga, S. Vincent-Bonnieu, W. Sillekens and J. M. Bergthorson, Acta Astronaut., 2020, 177, 639–651 CrossRef CAS.
- E. Commission, I. Directorate-General for Internal Market Entrepreneurship and SMEs, M. Grohol and C. Veeh, Study on the Critical Raw Materials for the EU 2023 – Final Report, Publications Office of the European Union, 2023 Search PubMed.
- H. Kania and M. Saternus, Appl. Sci., 2023, 13(3), 2003 CrossRef CAS.
- E. Commission, J. R. Centre, L. Talens Peiró, G. Blengini, F. Mathieux and P. Nuss, Towards Recycling Indicators Based on EU Flows and Raw Materials System Analysis Data – Supporting the EU-28 Raw Materials and Circular Economy Policies through RMIS, Publications Office, 2018 Search PubMed.
- Z. Li, T. Jiang, M. Ali, C. Wu and W. Chen, Energy Storage Mater., 2022, 50, 105–138 CrossRef.
- Y. Fang, Z. Chen, L. Xiao, X. Ai, Y. Cao and H. Yang, Small, 2018, 14, 1703116 CrossRef PubMed.
- X. Wu, A. Markir, Y. Xu, C. Zhang, D. P. Leonard, W. Shin and X. Ji, Adv. Funct. Mater., 2019, 29, 1900911 CrossRef.
- Z. He, F. Xiong, S. Tan, X. Yao, C. Zhang and Q. An, Mater. Today Adv., 2021, 11, 100156 CrossRef CAS.
- M. Mehrpooya and R. Habibi, J. Cleaner Prod., 2020, 275, 123836 CrossRef CAS.
- Slovenian Agency for Intellectual Property, National patent, SI26105A, 2022 Search PubMed.
- United States Patent and Trademark Office, Patent No. US20200308715, 2021.
- U. Luin and M. Valant, J. Solid State Electrochem., 2022, 26, 929–938 CrossRef CAS.
- P. Atkins and J. de Paula, Atkins' Physical Chemistry, Oxford University Press, Oxford, 9th edn, 2010 Search PubMed.
- K. Mazloomi and C. Gomes, Renewable Sustainable Energy Rev., 2012, 16, 3024–3033 CrossRef CAS.
- A. Lanz, J. Heffel and C. Messer, Hydrogen Fuel Cell Engines and Related Technologies, United States. Department of Transportation, Federal Transit Administration, 2001 Search PubMed.
- M. Hirscher and K. T. A. Hirose, Handbook of Hydrogen Storage : New Materials for Future Energy Storage, 2010 Search PubMed.
- J. O. Abe, A. P. I. Popoola, E. Ajenifuja and O. M. Popoola, Int. J. Hydrogen Energy, 2019, 44, 15072–15086 CrossRef CAS.
- N. Klopčič, I. Grimmer, F. Winkler, M. Sartory and A. Trattner, J Energy Storage, 2023, 72, 108456 CrossRef.
- J. W. Choi and D. Aurbach, Nat. Rev. Mater., 2016, 1, 16013 CrossRef CAS.
- S. Hameer and J. L. van Niekerk, Int. J. Energy Res., 2015, 39, 1179–1195 CrossRef.
- M. Hagen, D. Hanselmann, K. Ahlbrecht, R. Maça, D. Gerber and J. Tübke, Adv. Energy Mater., 2015, 5, 1401986 CrossRef.
- T. Kim, W. Song, D.-Y. Son, L. K. Ono and Y. Qi, J. Mater. Chem. A, 2019, 7, 2942–2964 RSC.
- H. Ibrahim, A. Ilinca and J. Perron, Renewable Sustainable Energy Rev., 2008, 12, 1221–1250 CrossRef CAS.
- A. G. Olabi, C. Onumaegbu, T. Wilberforce, M. Ramadan, M. A. Abdelkareem and A. H. Al-Alami, Energy, 2021, 214, 118987 CrossRef CAS.
- A. A. Ahmed, A. Alsharif and N. Yasser, Int. J. Electr. Eng. and Sustain., 2023, 1, 9–17 Search PubMed.
- M. Khaleel, Z. Yusupov, Y. Nassar, H. J. El-khozondar, A. Ahmed and A. Alsharif, e-Prime - Advances in Electrical Engineering, Electronics and Energy, 2023, 5, 100223 CrossRef.
- M. Amir, R. G. Deshmukh, H. M. Khalid, Z. Said, A. Raza, S. M. Muyeen, A. S. Nizami, R. M. Elavarasan, R. Saidur and K. Sopian, J Energy Storage, 2023, 72, 108694 CrossRef.
- F. Sorgulu and I. Dincer, Energy, 2023, 269, 126834 CrossRef CAS.
- O. Oruc and I. Dincer, Fuel, 2021, 286, 119325 CrossRef CAS.
- F. Safari and I. Dincer, Int. J. Hydrogen Energy, 2020, 45, 18867–18875 CrossRef CAS.
- M. Castro Oliveira, M. Iten and H. A. Matos, Sustainability, 2022, 14(12), 7506 CrossRef CAS.
- C. Canavesio, H. E. Nassini and A. E. Bohé, Int. J. Hydrogen Energy, 2015, 40, 8620–8632 CrossRef CAS.
- M. Valant and U. Luin, J. Cleaner Prod., 2024, 438, 140681 CrossRef CAS.
- K. F. Knoche, P. Schuster and T. Ritterbex, Int. J. Hydrogen Energy, 1984, 9, 473–482 CrossRef CAS.
- B. Ghorbani, S. Zendehboudi, Y. Zhang, H. Zarrin and I. Chatzis, Energy Convers. Manage., 2023, 297, 117599 CrossRef CAS.
- M. A. Miller, J. Petrasch, K. Randhir, N. Rahmatian and J. Klausner, Therm. Mech. Hybrid Chem. Energy Storage Syst., 2021, 249–292 Search PubMed.
- Thyssenkrupp, HCl Electrolysis, Thyssenkrupp, 2018.
- T. Brinkmann, G. Giner Santonja, F. Schorcht, S. Roudier and L. Delgado Sancho, Best Available Techniques Reference Document for the Production of Chlor-Alkali, 2014 Search PubMed.
- EU Commission, Best Available Techniques (BAT) Reference Document for the Production of Chlor-alkali, Industrial Emissions Directive 20210/75/EU,http://eippcb.jrc.ec.europa.eu/reference/BREF/CAK_Adopted_072014.pdf.
- D. L. Ulrichson and Y. S. Yeh, Thermochemical water splitting: The reverse Deacon reaction and alternatives, NASA STI/Recon Technical Report, 1975 Search PubMed.
- P. Wei, M. Abid, H. Adun, D. Kemena Awoh, D. Cai, J. H. Zaini and O. Bamisile, Appl. Sci., 2023, 13, 5626 CrossRef CAS.
- L. Li, Q. Zhang, B. He, R. Pan, Z. Wang, M. Chen, Z. Wang, K. Yin, Y. Yao, L. Wei and L. Sun, Adv. Mater., 2022, 34, 2104327 CrossRef CAS PubMed.
- M. Küttinger, J. K. Wlodarczyk, D. Daubner, P. Fischer and J. Tübke, RSC Adv., 2021, 11, 5218–5229 RSC.
- K. Lourenssen, J. Williams, F. Ahmadpour, R. Clemmer and S. Tasnim, J Energy Storage, 2019, 25, 100844 CrossRef.
- C. Ding, Z. Shen, Y. Zhu and Y. Cheng, Materials, 2023, 16, 3811 CrossRef CAS PubMed.
- J. F. Weaver, World's largest battery: 200MW/800MW h vanadium flow battery—site work ongoing, https://electrek.co/2017/12/21/worlds-largest-battery-200mw-800mwh-vanadium-flow-battery-rongke-power/, accessed June 10, 2024.
- X. Huo, X. Shi, Y. Bai, Y. Zeng and L. An, Cell Rep. Phys. Sci., 2024, 5, 101782 CrossRef CAS.
- K. W. Knehr, R. Buline, T. Baldwin, E. Guzman, H. Huynh, R. E. Ciez and D. A. Steingart, J. Electrochem. Soc., 2018, 165, A4041 CrossRef CAS.
- U. Jiménez-Blasco, E. Moreno, M. Cólera, P. Díaz-Carrasco, J. C. Arrebola, A. Caballero, J. Morales and Ó. A. Vargas, Int. J. Mol. Sci., 2021, 22(17), 9288 CrossRef PubMed.
- J. Asenjo-Pascual, I. Salmeron-Sanchez, J. R. Avilés-Moreno, P. Mauleón, P. Mazur and P. Ocón, Batteries, 2022, 8(10), 193 CrossRef CAS.
- A. Kurilovich, M. Pugach, G. Gonzalez, P. Peljo and K. J. Stevenson, ECS Meet. Abstr., 2022, MA2022-01, 2020 Search PubMed.
- F. Zhong, M. Yang, M. Ding and C. Jia, Front. Chem., 2020, 8, 1–14 CrossRef PubMed.
- M. Mitra, S. Kundu, M. Layek, S. Mondal, U. Mandal and B. Saha, in Advanced Redox Flow Technology, 2024, pp. 51–82 Search PubMed.
- A. G. Olabi, M. A. Allam, M. A. Abdelkareem, T. D. Deepa, A. H. Alami, Q. Abbas, A. Alkhalidi and E. T. Sayed, Batteries, 2023, 9(8), 409 CrossRef CAS.
- K. Amini and M. Pritzker, ECS Meet. Abstr., 2020, MA2020-02, 3732 Search PubMed.
- E. Sánchez-Díez, E. Ventosa, M. Guarnieri, A. Trovò, C. Flox, R. Marcilla, F. Soavi, P. Mazur, E. Aranzabe and R. Ferret, J. Power Sources, 2021, 481, 228804 CrossRef.
- D. E. Eapen, R. Suresh, S. Patil and R. Rengaswamy, Renewable Sustainable Energy Rev., 2021, 147, 111165 CrossRef CAS.
- L. W. Hruska and R. F. Savinell, J. Electrochem. Soc., 1981, 128, 18 CrossRef CAS.
- K. L. Hawthorne, J. S. Wainright and R. F. Savinell, J. Electrochem. Soc., 2014, 161, A1662 CrossRef CAS.
- M. C. Tucker, A. Phillips and A. Z. Weber, ChemSusChem, 2015, 8, 3996–4004 CrossRef CAS PubMed.
- H. He, S. Tian, B. Tarroja, O. A. Ogunseitan, S. Samuelsen and J. M. Schoenung, J. Cleaner Prod., 2020, 269, 121740 CrossRef CAS.
- O. J. Guerra, Nat. Energy, 2021, 6, 460–461 CrossRef.
- X. Liu, T. Li, Z. Yuan and X. Li, J. Energy Chem., 2022, 73, 445–451 CrossRef CAS.
- R. Bock, B. Kleinsteinberg, B. Selnes-Volseth and O. Stokke Burheim, Energies, 2021, 14(4), 1109 CrossRef CAS.
- B. Tian, J. Światowska, V. Maurice, S. Zanna, A. Seyeux and P. Marcus, Electrochim. Acta, 2018, 259, 196–203 CrossRef CAS.
- M. Egashira, in Encyclopedia of Electrochemical Power Sources, Elsevier, 2009, pp. 372–375 Search PubMed.
- X. Han, Y. Qu, D. Li, Y. Dong, D. Chen, Y. Yu, N. Ren and Y. Feng, Process Biochem., 2021, 101, 104–110 CrossRef CAS.
- H. Weinrich, Y. E. Durmus, H. Tempel, H. Kungl and R.-A. Eichel, Materials, 2019, 12(13), 2134 CrossRef CAS PubMed.
- M. A. Deyab and Q. Mohsen, Renewable Sustainable Energy Rev., 2021, 139, 110729 CrossRef CAS.
- C. Bai, H.-Y. Jin, Z. Gong, X. Liu and Z. Yuan, Energy Storage Mater., 2020, 28, 247–254 CrossRef.
- Z. Zhu, Y. Meng, M. Wang, Y. Yin and W. Chen, Mater. Today Energy, 2021, 19, 100603 CrossRef CAS.
- F. M. Mulder, B. M. H. Weninger, J. Middelkoop, F. G. B. Ooms and H. Schreuders, Energy Environ. Sci., 2017, 10, 756–764 RSC.
- J. P. Barton, R. J. L. Gammon and A. Rahil, Front. Energy Res., 2020, 8 DOI:10.3389/fenrg.2020.509052.
- P. Julien and J. M. Bergthorson, Sustainable Energy Fuels, 2017, 1, 615–625 RSC.
- M. McRae, P. Julien, S. Salvo, S. Goroshin, D. L. Frost and J. M. Bergthorson, Proc. Combust. Inst., 2019, 37, 3185–3191 CrossRef CAS.
- J. Palečka, J. Sniatowsky, S. Goroshin, A. J. Higgins and J. M. Bergthorson, Combust. Flame, 2019, 209, 180–186 CrossRef.
- D. Ning, Y. Shoshin, J. A. van Oijen, G. Finotello and L. P. H. de Goey, Combust. Flame, 2021, 230, 111424 CrossRef CAS.
- S. Goroshin, J. Palečka and J. M. Bergthorson, Prog. Energy Combust. Sci., 2022, 91, 100994 CrossRef.
- M. Schiemann, S. Wirtz, V. Scherer and F. Bärhold, Powder Technol., 2013, 245, 70–79 CrossRef CAS.
- X. C. Mi, A. Fujinawa and J. M. Bergthorson, Combust. Flame, 2022, 240, 112011 CrossRef CAS.
- L. C. Thijs, C. E. A. G. van Gool, W. J. S. Ramaekers, J. G. M. Kuerten, J. A. van Oijen and L. P. H. de Goey, Combust. Sci. Technol., 2022, 196(4), 572–588 CrossRef.
- D. Ning, Y. Shoshin, M. van Stiphout, J. van Oijen, G. Finotello and P. de Goey, Combust. Flame, 2022, 236, 111801 CrossRef CAS.
- P. Debiagi, R. C. Rocha, A. Scholtissek, J. Janicka and C. Hasse, Renewable Sustainable Energy Rev., 2022, 165, 112579 CrossRef CAS.
- IEA, International Energy Agency – Electricity generation by source 2022, https://www.iea.org/, accessed September 10, 2023.
- F. F. Adedoyin, N. Erum, D. Taşkin and D. Chebab, Energy Rep., 2023, 9, 4749–4762 CrossRef.
- TU/e, TU/e demonstrates iron fuel at brewery Bavaria: a new circular and CO2-free fuel for the industry, Eindhoven University of Technology (TU/e), 2020.
- Y. Chang, F. Wan, X. Yao, J. Wang, Y. Han and H. Li, Energy Rep., 2023, 9, 3057–3071 CrossRef.
- J. H. Wesseling, S. Lechtenböhmer, M. Åhman, L. J. Nilsson, E. Worrell and L. Coenen, Renewable Sustainable Energy Rev., 2017, 79, 1303–1313 CrossRef CAS.
- B. Kazmi, S. A. A. Taqvi and D. Juchelková, Fuel, 2023, 347, 128459 CrossRef CAS.
- W. Li, S. Zhang and C. Lu, J. Cleaner Prod., 2022, 361, 132237 CrossRef CAS.
- IEA, International Energy Agency – Energy Storage: Tracking progress 2020, https://www.iea.org/fuels-and-technologies/energy-storage, accessed November 4, 2023.
- S. Li, H. Zhang, J. Nie, R. Dewil, J. Baeyens and Y. Deng, Sustainability, 2021, 13, 8866 CrossRef CAS.
- I. R. Souza Filho, Y. Ma, M. Kulse, D. Ponge, B. Gault, H. Springer and D. Raabe, Acta Mater., 2021, 213, 116971 CrossRef CAS.
- T. Okosun, S. Nielson and C. Zhou, JOM, 2022, 74, 1521–1532 CrossRef CAS.
- P. Pinto, L. Milagre, L. Moreira, H. Junior, A. Salviano, J. Ardisson, F. Parreira, A. Teixeira and R. Lago, J. Braz. Chem. Soc., 2022, 33, 969–977 CAS.
- M. Pei, M. Petäjäniemi, A. Regnell and O. Wijk, Metals, 2020, 10, 972 CrossRef.
- R. Béchara, H. Hamadeh, O. Mirgaux and F. Patisson, Materials, 2018, 11, 1094 CrossRef PubMed.
- D. Ernst, U. Manzoor, I. R. Souza Filho, M. A. Zarl and J. Schenk, Metals, 2023, 13, 558 CrossRef CAS.
- K. C. Sabat, J. Phys.: Conf. Ser., 2019, 1172, 12043 CrossRef CAS.
- M. Naseri Seftejani, J. Schenk and M. A. Zarl, Materials, 2019, 12, 1608 CrossRef PubMed.
- I. Souza Filho, H. Springer, Y. Ma, A. Mahajan, C. Silva, M. Kulse and D. Raabe, J. Cleaner Prod., 2022, 130805 CrossRef CAS.
- Y. Chen and H. Zuo, Ironmaking Steelmaking, 2021, 48, 749–768 CrossRef CAS.
- A. Otto, M. Robinius, T. Grube, S. Schiebahn, A. Praktiknjo and D. Stolten, Energies, 2017, 10, 451 CrossRef.
- S. F. Ahmed, M. Mofijur, S. Nuzhat, N. Rafa, A. Musharrat, S. S. Lam and A. Boretti, Int. J. Hydrogen Energy, 2022, 47, 37227–37255 CrossRef CAS.
- K. Daehn, R. Basuhi, J. Gregory, M. Berlinger, V. Somjit and E. A. Olivetti, Nat. Rev. Mater., 2022, 7, 275–294 CrossRef CAS.
- N. McPherson, Ironmaking Steelmaking, 2019, 46, 943 CrossRef CAS.
- X. Zhang, K. Jiao, J. Zhang and Z. Guo, J. Cleaner Prod., 2021, 306, 127259 CrossRef CAS.
- Y. Junjie, Int. J. Miner. Process. Extr. Metall., 2018, 3, 15–22 Search PubMed.
- Q. Wang, Y. Zhu, Q. Wu, E. Gratz and Y. Wang, RSC Adv., 2015, 5, 5501–5507 RSC.
- A. Allanore, J. Feng, H. Lavelaine and K. Ogle, J. Electrochem. Soc., 2010, 157, E24 CrossRef CAS.
- G. Z. Chen, D. J. Fray and T. W. Farthing, Nature, 2000, 407, 361–364 CrossRef CAS PubMed.
- A. Kulkarni and S. Giddey, J. Solid State Electrochem., 2012, 16, 3123–3146 CrossRef CAS.
- A. Allanore, H. Lavelaine, G. Valentin, J. P. Birat and F. Lapicque, J. Electrochem. Soc., 2008, 155, E125 CrossRef CAS.
- H.-G. Choi, S. Choi, M.-K. Kim, J. Jang, K. T. Nam, I.-H. Jung and K.-W. Yi, Ironmaking Steelmaking, 2021, 48, 1030–1037 CrossRef CAS.
- A. Allanore, L. Yin and D. R. Sadoway, Nature, 2013, 497, 353–356 CrossRef CAS PubMed.
- M. Shahabuddin, M. A. Rhamdhani and G. Brooks, Mater. Aust. Mag., 2022, 55, 30–31 Search PubMed.
- A. M. Navarro-Suárez and P. Johansson, J. Electrochem. Soc., 2020, 167, 70511 CrossRef.
- S. Azmi, M. F. Koudahi and E. Frackowiak, Energy Environ. Sci., 2022, 15, 1156–1171 RSC.
- A. Sharma, R. Sharma, R. C. Thakur and L. Singh, J. Energy Chem., 2023, 82, 592–626 CrossRef CAS.
- G. Zante and M. Boltoeva, Sustainable Chem., 2020, 1, 238–255 CrossRef.
- K. S. Ryder, A. D. Ballantyne, E. L. Smith, E. J. R. Palin and A. P. Abbott, in Electronic Waste Management, ed. G. H. Eduljee and R. M. Harrison, The Royal Society of Chemistry, 2019, pp. 278–312 Search PubMed.
- A. P. Abbott, R. C. Harris, F. Holyoak, G. Frisch, J. Hartley and G. R. T. Jenkin, Green Chem., 2015, 17, 2172–2179 RSC.
- S. Anggara, F. Bevan, R. C. Harris, J. M. Hartley, G. Frisch, G. R. T. Jenkin and A. P. Abbott, Green Chem., 2019, 21, 6502–6512 RSC.
- A. P. Abbott, Curr. Opin. Green Sustainable Chem., 2022, 36, 100649 CrossRef CAS.
- J. M. Hartley, J. Allen, J. Meierl, A. Schmidt, I. Krossing and A. P. Abbott, Electrochim. Acta, 2022, 402, 139560 CrossRef CAS.
- J. Ling, H. Yang, G. Tian, J. Cheng, X. Wang and X. Yu, J. Cleaner Prod., 2024, 441, 140933 CrossRef CAS.
- S. Hornby and G. Brooks, Impact of Hydrogen DRI on EAF Steelmaking, https://www.midrex.com/tech-article/impact-of-hydrogen-dri-on-eaf-steelmaking/, accessed June 12, 2024.
- M. Draxler, A. Sormann, T. Kempken, T. Hauck, J. C. Pierret, J. Borlee, A. Di Donato, M. De Santis and C. Wang, Technology Assessment and Roadmapping, 2021, vol. 1 Search PubMed.
- X. Wang, H. Yang, X. Yu, J. Hu, J. Cheng and H. Jing, J. Appl. Electrochem., 2023, 53, 1521–1536 CrossRef CAS.
- Q. Zaib, M. J. Eckelman, Y. Yang and D. Kyung, Green Chem., 2022, 24, 7924–7930 RSC.
|
This journal is © The Royal Society of Chemistry 2024 |
Click here to see how this site uses Cookies. View our privacy policy here.