DOI:
10.1039/D3SC06758K
(Perspective)
Chem. Sci., 2024,
15, 5802-5813
Revisiting poly(vinyl chloride) reactivity in the context of chemical recycling
Received
16th December 2023
, Accepted 28th February 2024
First published on 20th March 2024
Abstract
Poly(vinyl chloride) (PVC) is one of the highest production volume polymers due to its many applications, and it is one of the least recycled due to its chemical structure and frequent formulation with additives. Developing efficient PVC recycling techniques would enable PVC waste to be reused or repurposed in other processes. Within this context, the literature on PVC modification offers considerable insight into versatile reaction pathways, potentially inspiring new approaches for repurposing PVC waste into value-added products. This perspective provides an overview of PVC functionalization through a lens of chemical recycling, discussing various PVC reactivity trends and their applications with a critical assessment and future outlook of their recycling implications.
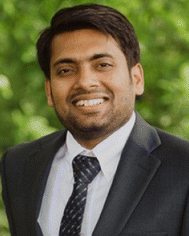 Rahul Kant Jha | Rahul Kant Jha is currently a PhD candidate working under the supervision of Prof. Anne J. McNeil in the Department of Chemistry at the University of Michigan. He obtained his B.S. in Chemistry from Birla Institute of Technology and his M.S. in Chemistry from IISER Bhopal, India. Prior to coming to Michigan, he worked on developing organic redoxmers for nonaqueous redox flow batteries at the University of Kentucky under the supervision of Prof. Susan Odom. His current research focuses on developing electrochemical approaches to poly(vinyl chloride) recycling. |
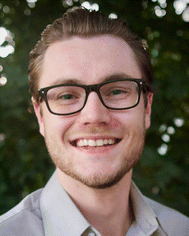 Bertrand J. Neyhouse | Dr Bertrand Neyhouse is a postdoctoral research associate at the University of Michigan working under the supervision of Prof. Anne McNeil. He received his PhD in chemical engineering from the Massachusetts Institute of Technology, working with Prof. Fikile Brushett to develop design strategies for redox flow batteries. His research centers on developing electrochemical technologies to address modern sustainability challenges. |
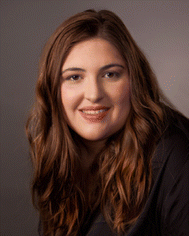 Morgan S. Young | Morgan Young received her B.S. Chemistry at the University of Michigan in 2021. She was an undergraduate research student with Prof. Anne J. McNeil, where she worked on catalyst transfer polymerization and chemical recycling of PVC. Now, Morgan is a PhD candidate at Cornell University working on catalytic methods to synthesize biodegradable polymers under the supervision of Prof. Geoffrey W. Coates. |
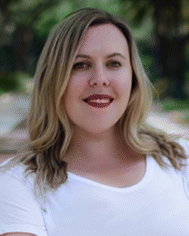 Danielle E. Fagnani | Dr Danielle Fagnani is currently a research chemist at Ashland developing sustainability-conscious ingredients for market applications. Prior to this role, she completed her post-doctoral appointment at the University of Michigan with Prof. Anne McNeil, where she developed innovative methods to recycle plastic waste. She earned her doctorate from the University of Florida, Department of Chemistry in 2018. |
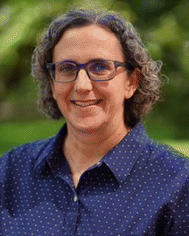 Anne J. McNeil | Prof. Anne McNeil is the Carol A. Fierke Professor of Chemistry at the University of Michigan, where she is also a member of the Macromolecular Science and Engineering Program and the Program in the Environment. Her research is focused on sustainable materials, with interests in the chemical recycling of waste plastics, renewable energy storage in redox flow batteries, as well as measuring and removing microplastics in the environment. She is also an HHMI Professor, and has developed innovative approaches towards educating the next generation. |
Introduction
Plastics are integrated into all facets of modern society, and their ubiquity has led to waste accumulation that threatens both environmental and ecological systems.1,2 The United States (U.S.) generates 44 million tons of plastic waste each year—the majority of which is comprised of polyethylene (PE, 52%), polypropylene (PP, 19%), polyethylene terephthalate (PET, 14%), polystyrene (PS, 7%), and poly(vinyl chloride) (PVC, 2%).3 Each year, 86% (38 million tons) of this plastic waste is disposed in landfills, prompting efforts to expand plastic reuse and recycling through technology, policy, and humanitarian efforts.
For some plastics (e.g., PET), closed-loop recycling can be achieved by chemically deconstructing the polymer into its constituent monomers and repolymerizing them to generate pristine material.4 For others, such as those with all-carbon backbones (e.g., PE, PP, PS, PVC), the polymers are more thermodynamically and kinetically stable, making depolymerization more difficult.5 In most cases, mechanical recycling—where plastics are separated by their chemical identity and melt reprocessed—is used.6 However, the efficacy is limited and the resultant recycled plastics typically exhibit poorer material properties. An alternative is open-loop chemical recycling—where polymers are converted into alternative products through chemical reactions.7 While this approach is feasible for most polyolefins, PVC presents additional challenges to existing recycling methods due to facile cleavage of the C–Cl bond and extensive use of additives.8,9 Consequently, only ca. 18
000 tons (3% of total municipal PVC waste) is recycled in the U.S. per year, presumably via mechanical recycling methods.3
PVC is a uniquely versatile polymer, owing to its variability in material strength, durability, chemical stability, flexibility, and processability when compatibilized with various plasticizers, stabilizers, and lubricants. These qualities enable its use in wide-ranging applications, including construction materials, fluid piping, cable insulation, floor and wall coverings, and healthcare devices, some of which have product lifetimes of 30–50 years.8,10 However, the diverse applications and long lifetimes make it difficult to recycle, as the additives frustrate a one-size-fits-all approach while corrosive chlorine byproducts present hazardous conditions for thermochemical recycling processes.11
Despite the challenges associated with PVC recycling, several efforts by industrial and governmental groups have demonstrated promising results.12 For instance, the European PVC industry has worked for over 20 years to minimize the environmental impact of PVC production and manufacturing through voluntary commitments (Vinyl 2010, VinylPlus, and VinylPlus 2023).13 Using primarily mechanical recycling methods, they have recycled 8.9 million tons of PVC since 2000, including 896
000 tons in 2022 (ca. 27% of total PVC waste generated in Europe).14 Meanwhile, VinylLoop—a recycling project developed by Solvay that used solvent-based separation—ceased operation at its Ferrara plant in 2018 following European Union regulations on phthalates, which stymied market demand for their recycled PVC containing phthalate plasticizers.15 In the U.S., the Vinyl Institute recently launched the Vinyl Sustainability Council, an industry-wide initiative that aims to drive sustainable economic development in the PVC industry, citing 550
000 tons of PVC recycled in 2020, 13% of which is post-consumer materials.16 Indeed, there are certainly promising directions within post-industrial PVC recycling, yet the challenges of post-consumer PVC waste remain. Mechanical methods are particularly effective and economical for recycling within production facilities and clean waste streams. However, the diversity of post-consumer PVC waste—featuring varying amounts and classes of additives—requires chemical processing which can tolerate or separate these complex mixtures. To this end, significant opportunities remain to develop sustainable and economical chemical recycling routes for PVC.
An ideal chemical recycling process would enable complete utilization of the carbon, chlorine, and hydrogen content of PVC without negative environmental impacts (e.g., emissions, process waste) and prohibitive costs. While this ideal has yet to be fully achieved, numerous research groups have proposed potential routes for recycling waste PVC. Conventional approaches apply thermochemical methods (e.g., combustion, pyrolysis, gasification) to deconstruct PVC, and these developments have been previously reviewed.8,10,17 Broadly, these processes dechlorinate PVC and subsequently deconstruct the resulting hydrocarbon to generate fuels and small molecules or recover energy. However, the evolution of gaseous hydrogen chloride—among other reactive species—requires specialized process equipment (e.g., scrubbers) to capture or neutralize these products. Synthetic methods offer a compelling alternative, wherein PVC may be dechlorinated or converted directly to alternative products within less harsh reaction environments. As such, these targeted transformations may require fewer unit operations and cheaper reactor equipment than existing thermochemical routes and may provide facile pathways for chlorine utilization rather than disposal.
Here we aim to focus on more direct chemical transformations that circumvent deconstruction to monomeric and oligomeric constituents. There is an enormous body of existing research on PVC reactivity, which has largely been conducted outside the scope of recycling. We believe that many of these studies could be leveraged to develop new chemical recycling methods for PVC waste. This perspective highlights select papers from an extensive literature search of over 3000 PVC papers published since 2010.† We then consider possible extensions of this prior research in the context of recycling and emphasize studies which specifically target post-consumer PVC materials. Ultimately, we aim to invigorate the chemical science community to identify and evaluate potentially sustainable recycling routes which can facilitate complete PVC utilization.
Structure and reactivity
The repeat unit structure informs how PVC plastics can be recycled or repurposed. Three reaction types are most often utilized based on the C–Cl bond reactivity (Scheme 1): (1) heterolytic dechlorination (i.e., nucleophilic substitution), (2) homolytic dechlorination, and (3) dehydrochlorination (i.e., elimination). The resulting products can be used directly or leveraged in further transformations as discussed throughout this perspective. Before delving into the specific reactions, we start by providing some general structure and reactivity principles gleaned from the literature.
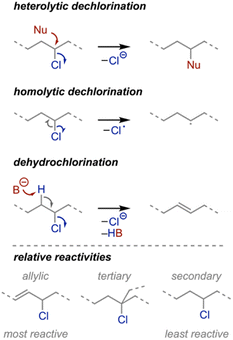 |
| Scheme 1 Common reaction modalities for PVC and relative reactivities of different C–Cl bonds within PVC. | |
Chlorine is a modest leaving group and can take part in substitution and elimination reactions under many conditions. Competition between these processes can diminish product selectivity, presenting a challenge for chemical recycling strategies, which require high purity and/or control for practical applications. Various factors influence the propensity for substitution or elimination, including polymer structure and reaction environment. For instance, isotactic sequences preferentially undergo substitution over elimination as compared to atactic and syndiotactic polymers.18,19 Within the context of reaction conditions, aprotic polar solvents such as dimethylformamide favor substitution over elimination as compared to protic polar solvent like ethylene glycol;20,21 higher temperatures favor elimination over substitution;22,23 higher nucleophile concentrations improve dechlorination efficiency with increased substitution and elimination;24 and less basic nucleophiles favor substitution over elimination as compared to more basic ones.25
In addition, structural defects, which stem from uncontrolled free radical polymerization, can impact reactivity.26 Specifically, tertiary and allylic chlorine-substituted carbons that result from backbiting and subsequent rearrangements, hydride shifts, and β-scission reactions are often the most reactive sites in PVC. The concentration of defects varies with polymerization conditions,27 but on average, free radical polymerization results in 3–5 tertiary defects per 1000 repeat units28 and 1 allylic defect (either internal or terminal) per polymer chain.29 Although sparse, these defects are responsible for initiating autocatalytic thermal dehydrochlorination because of their weaker C–Cl bond strengths.30 Though efforts to reduce the defect sites31,32 and autocatalysis33 are underway, some researchers have taken advantage of these more labile chlorine atoms in reactions (vide infra).
Heterolytic dechlorination
Chlorine substitution by nucleophiles can convert PVC into alternative polymeric materials that may be useful in specialty applications. Nevertheless, these studies rarely leverage waste PVC as their starting materials. We discuss herein potential extensions of these reaction pathways, highlighting particularly interesting or promising research across synthetic routes and end-use applications. Throughout, we generally organize the discussion by reaction pathway.
As noted above, PVC readily undergoes substitution reactions with nucleophiles. Previous work with PVC has primarily utilized S-, N- and O-based nucleophiles to generate materials for targeted applications such as catalysis,34–41 separations,42–47 metal-complexation,48–55 biodegradable polymers,56,57 thermally stable and photostable polymers,58,59 and antimicrobial polymers.59,60 In their 2010 and 2015 reviews, Moulay outlines many transformations that occur via a heterolytic, SN2 mechanism.61,62
As an example, Reinecke and coworkers developed a method to attach phthalate- and isophthalate-based plasticizers to PVC via thiol substitution, which would reduce plasticizer contamination in other waste streams during recycling (Scheme 2A).63 When compared to commercial plasticized PVC, the covalently linked plasticizer completely reduced plasticizer migration, albeit at the expense of flexibility. Further optimizing these strategies by evaluating the reaction efficiency with other molar masses could lead to competitive, flexible PVC products (e.g., packaging) without plasticizer migration. In a different report, Yagci and coworkers utilized elemental sulfur and sodium sulfide nonahydrate to form polysulfide, which was used to vulcanize commercial PVC at room temperature.64 The resulting PVC-polysulfide network exhibited self-healing behavior and could be reprocessed after use due to the dynamic S–S linkages.
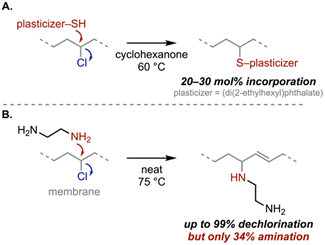 |
| Scheme 2 Nucleophilic substitution reactions on PVC. (A) Covalent incorporation of plasticizer via substitution.63 (B) Competing substitution and elimination observed when PVC is reacted with ethylenediamine.65 | |
While these are promising examples, nucleophilic substitution pathways are limited in practice due to incomplete dechlorination and competition with elimination, which lead to residual chlorine atoms and alkenes, respectively. These structural “impurities” will likely alter the polymer properties and potentially limit their utility. Nevertheless, these synthetic challenges represent opportunities for innovation. For instance, Hwang and coworkers achieved up to 99% dechlorination of PVC membranes using ethylenediamine; however, only 34% amination (substitution) was observed (Scheme 2B).65 Another example, introduced by Fieser and coworkers, uses (xantphos)Rh catalysts and hydrogen donors (i.e., sodium hydride, sodium formate, triethylsilane) to enable selective hydrodechlorination to polyethylene-like materials with 63% substitution efficiency.66 Optimizing dechlorination efficiency and selectivity simultaneously, while challenging, could be instrumental in yielding versatile recycling approaches. Previous studies have shown that choosing appropriate reaction conditions, including nucleophile identity, temperature, concentration, and solvent polarity (summarized in the Structure and reactivity section), could lead to reactions with higher substitution efficiency.
Other, less common routes to substitute PVC include Friedel–Crafts alkylation,67,68 cross-coupling,69 and the Barbier reaction.70 For example, Arslan and coworkers utilized magnesium-mediated activation of the C–Cl bonds to generate a nucleophile that subsequently reacted with electrophilic aldehydes and epoxide derivatives.70 An impressively high functionalization efficiency (up to 90%) was achieved by optimizing the ratio of magnesium to chlorine. Such methods could enable polymers with higher degrees of functionalization; however, there are few examples, likely due to the low reactivity of alkyl chlorides in organometallic reactions. One exciting approach is to directly convert PVC into an existing high-value polymer by substituting chlorine for other functionalities (e.g., a phenyl moiety to form PS). For example, Fieser and coworkers recently reported a method for converting PVC to poly(ethylene-co-styrene) via tandem hydrodechlorination/Friedel–Crafts alkylation.71
An alternative approach to direct chlorine substitution is to install a more versatile reactive moiety that enables subsequent functionalization. While the need for and cost associated with additional processing steps could stifle the practical efficacy of this approach, these secondary reactions provide access to a wider array of functionality. As an example, an azide can be installed onto the polymer backbone using conventional SN2 chemistry and then subsequently reacted with an alkyne to yield a triazole linkage in a “click” reaction. This strategy has been used to affix different moieties onto PVC for wide-ranging applications, including covalently linked plasticizers,72–77 electrochemical systems,78–83 metal detection,84 energy storage,85 photochemistry,86,87 and anti-bactericides.88,89 One potential limitation is the lower degree of azide incorporation (<15%) due to both incomplete substitution and competing elimination pathways.
Click reactions have also been employed to modify PVC surfaces. For example, Finn and coworkers utilized the Cu-catalyzed azide–alkyne reaction to add ammonium, pyridyl, ether, and fluorinated amides to the surface of commercial, plasticized PVC tubing (Scheme 3A).90 In complementary work, Chen and coworkers reported a one-pot photoreaction and sulfur-fluoride exchange (SuFEx) reaction to functionalize PVC films (Scheme 3B).91 SuFEx reactions are appealing due to their mild conditions and lack of metal catalyst. It would be interesting to extend this chemistry to conditions that favor PVC dissolution and evaluate the functionalization efficiencies under homogeneous reaction conditions.
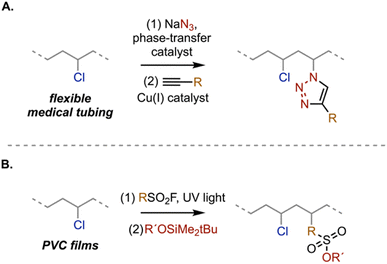 |
| Scheme 3 Click reaction pathways for a two-step PVC functionalization, including an (A) azide–alkyne cycloaddition90 and (B) SuFEx reactions.91 | |
Beyond click chemistry, other researchers have performed multi-step reactions on PVC via secondary steps such as acylation57 or epoxidation.92 For example, Jaymand and coworkers used allylic alcohol-based substitution followed by epoxidation to generate epoxy-resin nanocomposites consisting of epoxidized novolac (a phenol-formaldehyde resin), epoxidized poly(vinyl chloride), and modified silica nanoparticles.92 The resin nanocomposite showed improved thermal stability compared to the neat epoxidized novolac; however, it was not compared to commercially available epoxy resins. Similar to other studies, a competing elimination reaction generates alkenes that can also undergo epoxidation, complicating structural control.
Homolytic dechlorination
Homolytic C–Cl bond cleavage generates reactive carbon-centered radicals, which have been used to generate graft copolymers from PVC. For example, atom transfer radical polymerization (ATRP) is the most common approach, leveraging tertiary alkyl and allylic chlorides in PVC as macroinitiator sites (Scheme 4A). Previous work has utilized numerous monomers—methyl methacrylate, styrene, acrylonitrile, glycidyl methacrylate—for various applications such as hydrogen-bonded macromolecules,93,94 dye-sensitized solar cells,95–97 membranes,98–102 covalent plasticizers,103 and polymeric sorbents.104 In particular, photoinitiated ATRP has gained attention due to its spatial and temporal control. For example, Yagci and coworkers reported a visible-light-mediated ATRP using dimanganese decacarbonyl as a light-absorbing component and parts per million levels of Cu-catalyst to synthesize graft poly(methyl methacrylate) copolymers from PVC.105 In a separate report, Huang and coworkers developed an Ir-catalyzed visible-light-mediated ATRP to graft poly(methyl methacrylate), poly(pentafluorophenyl methacrylate), and poly(oligo(ethylene glycol) methyl ether methacrylate) onto PVC (Scheme 4B).106 Although ATRP is quite versatile in functionalizing PVC, the reaction proceeds predominantly at the sparse structural defect sites (i.e., allylic and tertiary chlorides), limiting grafting density and dechlorination efficiency.
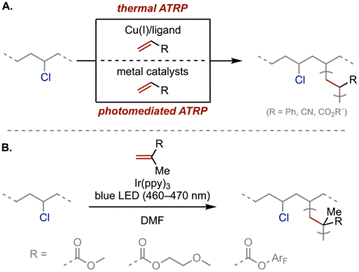 |
| Scheme 4 (A) Thermal and photomediated ATRP for PVC functionalization. (B) An Ir-catalyzed example for generating graft copolymers.106 | |
Other graft copolymerization techniques have also been applied for PVC modification; however, their use is limited to only a few studies (e.g., reversible addition fragmentation chain transfer,107 emulsion polymerization,108 as well as other radical-generating strategies including plasma,109–111 gamma rays,112 and UV light113). Although these graft copolymers, along with those synthesized by ATRP, could potentially make cheaper end products by leveraging waste PVC feedstocks, the present market demand for such specialty copolymers is limited.
Beyond polymer grafting, others have used radical chemistry to install maleic anhydride substituents using benzoyl peroxide114,115 and fullerene substituents using azobisisobutyronitrile as initiators.116 Additionally, sodium trisulfide has been applied to crosslink PVC via monosulfide bridges.117 Our group recently introduced an electrochemical approach that combines homolytic C–Cl reduction with oxidative arene electrochlorination, allowing waste PVC to serve as a chlorine feedstock for organic syntheses at room temperature.118
Nevertheless, radical pathways are likely more limited on what functional groups can be installed when compared with nucleophilic substitution. While the generation of carbon-centered radicals presents unique opportunities to install new functionalities, their potent reactivity can result in undesired coupling reactions (e.g., crosslinking). In controlled radical polymerizations like ATRP, crosslinking may not be prominent because of the low concentration of defect sites. However, generating higher radical concentrations could facilitate reactions with solvent and adventitious contaminants, including O2 and H2O.119 Additionally, the PVC macroradical may undergo chain-scission to form low molar-mass fragments that can limit applications.120 Consideration and control of these multifaceted reaction pathways will be essential to enable such methods for broader applications in chemical recycling.
Dehydrochlorination
Dehydrochlorination involves the base-mediated elimination of hydrogen and chloride to generate an alkene. For example, aqueous alkaline solutions (e.g., NaOH, K2CO3, NH3) can be used to dechlorinate PVC (Scheme 5A), forming polyolefins and inorganic chlorides (e.g., NaCl, KCl, NH4Cl). To this end, Osada and Yana performed deplasticization and dechlorination in a single pot by varying the temperature—dioctyl phthalate hydrolysis at 150 °C and up to 100% dechlorination at 235 °C—via microwave heating in an 8 M NaOH solution.121 Using a more conventional heating source required higher temperatures and base concentrations. One advantage of this approach is that chlorine-containing products (e.g., NaCl) have existing markets. However, the resulting polyene has limited applications, owing to insolubility. In addition, further reaction optimization is required to reduce NaOH concentrations for chemical recycling given its high energy requirements for production.122 In other reports, NaOH was combined with diols (ethylene glycol, diethylene glycol, tetraethylene glycol)123 and then ball milled124,125 to achieve up to 99% dechlorination for waste PVC at lower alkaline concentrations. However, competing substitution reactions led to mixed products. In related work, Pang and coworkers evaluated KOH-assisted dehalogenation of waste PVC via ballmilling to generate KCl and chlorine-free carbonaceous materials, which were thermally annealed to form porous carbon electrodes for supercapacitor applications.126
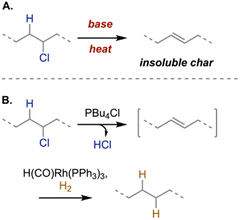 |
| Scheme 5 (A) Dehydrochlorination of PVC via elimination leading to insoluble char. (B) Tandem ionic liquid-mediated PVC dehydrochlorination with Rh-catalyzed hydrogenation to form highly saturated but non-linear soluble polymers.132 | |
Ionic liquids have been explored as both a solvent and base for dehydrochlorination reactions, owing to their high basicity, thermal stability, and low vapor pressure.127 For example, De Vos and coworkers reported 98% dehydrochlorination of PVC in a PBu4Cl ionic liquid after heating at 180 °C for 1 h.128 Building on this work, Oster and coworkers evaluated similar phosphonium-based ionic liquids to separate the components of a multilayer blisterpack (containing PVC, aluminium, and oriented polyamide), with up to 99% dehydrochlorination.129
Though often touted as “green” solvents, ionic liquids are made through energy- and material-intensive processes.130,131 As such, developing approaches to reuse ionic liquids after the reaction could facilitate its large-scale usability. However, this approach has yet to be explored in PVC chemistry beyond a few reuses. In addition, the costs of recycling ionic liquids must be considered. A separate concern relates to how to dispose of ionic liquids after use, as they can be classified as persistent pollutants due to their chemical and thermal stability. Concerns about their ecological toxicity have already been well documented.131
One remaining challenge is what to do with the polyene products formed after dehydrochlorination. De Vos and coworkers developed an elegant tandem dehydrochlorination–hydrogenation process to convert PVC into saturated but nonlinear, soluble polymers with approximately 80% dechlorination (Scheme 5B).132 While the use of rhodium catalysts could prohibit large-scale demonstrations, cheaper hydrogenation catalysts could be explored.133 For example, Goulas and coworkers reported a tandem dehydrochlorination–hydrogenation–hydrogenolysis to generate polyethylene waxes suitable for hot melt adhesive applications.134 Using an organic amine base, a Pt/C heterogeneous catalyst, high pressures of H2, and high temperatures, they obtained >70% yields of wax products with high conversions for both Cl elimination and alkene hydrogenation. To further improve this approach, lower catalyst loadings or recyclable catalysts will be needed, as well as milder reaction conditions.
The future of chemical PVC recycling
While there is a wealth of literature aimed at chemically modifying PVC, few of these studies utilize waste plastic as a feedstock. As such, further research will be required to understand how these methods would work with commercial PVC products, which often contain plasticizers, stabilizers, lubricants, and other plastic and non-plastic components. However, there are several emergent approaches demonstrating promising chemical recycling methods applied directly to post-consumer PVC materials.
One approach is to leverage waste PVC as a chlorine feedstock by using dechlorination to extract chlorine on-demand for direct use as a synthetic reagent. Work by our group used plasticized PVC tubing as a chlorine source for an oxidative arene electrochlorination (Scheme 6A).118 A preliminary life cycle assessment showed a 68% reduction in greenhouse gas emissions when using waste PVC as the chlorine source compared to hydrochloric acid. More work is needed, however, to optimize the electrodechlorination because the mixed, partially dechlorinated polymer has low market value.
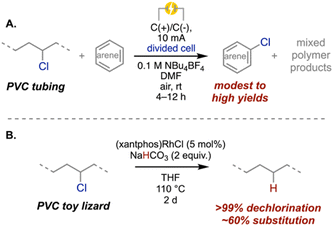 |
| Scheme 6 (A) PVC as a chlorine source for organic synthesis using electrochemistry.118 (B) Reductive hydrodechlorination using a metal catalyst and a hydride source.66 | |
One route aimed at recycling the carbon content focuses on dechlorinating PVC to form polyethylene-like materials that could be used directly or further recycled alongside waste PE using conventional thermochemical recycling methods. The previously described study by Fieser and coworkers (Scheme 6B), which leverages hydride donors, offers a pathway for simultaneously recycling the carbon content of the polymer and generating potentially valuable Cl-containing byproducts (e.g., chlorotriethylsilane when Et3SiH is used).66 However, the required catalysts and hydrogen sources are expensive, potentially challenging economic viability. Additionally, a more selective substitution would help limit dehydrochlorination side reactions, adding value to the resulting polyethylene-like materials.
While numerous potential approaches have achieved partial utilization of carbon, chlorine, and hydrogen content, we know of few such non-thermochemical processes capable of fully dechlorinating PVC and reconstituting its substituents into new, useful products. Nevertheless, some of these chemical recycling pathways discussed above and throughout this perspective appear promising, and we posit that these methodologies could yield commercially viable PVC recycling technologies in the future with further optimization.
Conclusions
By evaluating recent literature on chemical modification to PVC, we have outlined promising future routes for waste recycling and highlighted potential challenges and limitations for such processes. These trends suggest that a given class of reaction may be more desirable depending on the end-goal of a particular recycling operation. For instance, nucleophilic substitution offers direct access to diverse polymer products, but these reactions display relatively low substitution efficiency and high competition with elimination. Future chemical modification schemes should look to improve reaction efficacy and product purity. Alternatively, reactions to form polyenes could be a more facile approach to achieve high dechlorination efficiencies, as elimination reactions can be conducted with higher selectivity and conversion. However, subsequent processing is typically needed to generate useful polymeric or chemical products from the dechlorinated PVC. New methods in this area should look to conduct reactions under more mild conditions (e.g., lower NaOH concentrations) while considering the practical scalability of such pathways (e.g., ionic liquid cost). In addition, finding applications for the char produced or identifying more mild hydrogenation conditions to instead generate polyethylene are needed. Finally, homolytic pathways forming graft copolymers may also feature a diverse range of unique product structures, but the limited large-scale demand for such products currently frustrates the viability of these pathways for chemical recycling. Other homolytic pathways, including electrodechlorination, are promising but need more optimization to increase dechlorination efficiency and product selectivity.
Beyond the chemical processes themselves, the field would benefit greatly from complementary analyses of waste PVC products and their broader impacts. For instance, the chemical composition of PVC waste streams is not thoroughly characterized, making investigations in representative conditions more challenging at the lab-scale and preventing more detailed understanding of reactions that utilize post-consumer products. Life-cycle assessments, especially done in tandem with chemical recycling studies, could provide necessary context for the overall sustainability of PVC recycling methods. Those approaches that address challenges in plastic waste yet generate other environmental hazards (e.g., CO2 emissions) limit the overall benefits of such processes.
Taken together, there are numerous promising approaches for chemically recycling PVC waste beyond traditional thermochemical processes. Considering the breadth of opportunities within chemical discovery, reaction engineering, and auxiliary analyses, there exists considerable space for new entrants to impact the chemical recycling field.
Author contributions
The manuscript was written through contributions of all authors. RKJ was involved with conceptualization, data curation, formal analysis, methodology, validation, visualization, and writing – original draft, reviewing, and editing. BJN was involved with formal analysis, methodology, validation, visualization, and writing – original draft, reviewing, and editing. MSY and DEF were involved with early conceptualization and writing – reviewing and editing. AJM was involved with conceptualization, funding acquisition, project administration, resources, supervision, visualization, and writing – original draft, review, and editing.
Conflicts of interest
There are no conflicts to declare.
Acknowledgements
This work was supported through a subcontract from the Ames Laboratory with funding from the U.S. Department of Energy (DOE), Office of Science, Office of Basic Energy Sciences, under Contract No. DE-AC02-07CH11358 as part of the Energy Frontier Research Center titled the Institute for Cooperative Upcycling of Plastics (iCOUP).
Notes and references
- R. Geyer, J. R. Jambeck and K. L. Law, Production, use, and fate of all plastics ever made, Sci. Adv., 2017, 3, e1700782 CrossRef PubMed.
- A. L. Andrady and M. A. Neal, Applications and societal benefits of plastics, Philos. Trans. R. Soc., B, 2009, 364, 1977–1984 CrossRef CAS PubMed.
- A. Milbrandt, K. Coney, A. Badgett and G. T. Beckham, Quantification and evaluation of plastic waste in the United States, Resour., Conserv. Recycl., 2022, 183, 106363 CrossRef.
- A. Rahimi and J. M. García, Chemical recycling of waste plastics for new materials production, Nat. Rev. Chem., 2017, 1, 0046 CrossRef.
- G. W. Coates and Y. D. Y. L. Getzler, Chemical recycling to monomer for an ideal, circular polymer economy, Nat. Rev. Mater., 2020, 5, 501–516 CrossRef CAS.
- Z. O. G. Schyns and M. P. Shaver, Mechanical recycling of packaging plastics: A review, Macromol. Rapid Commun., 2020, 42, 2000415 CrossRef PubMed.
- L. T. J. Korley, T. H. Epps, B. A. Helms and A. J. Ryan, Toward polymer upcycling—adding value and tackling circularity, Science, 2021, 373, 66–69 CrossRef CAS.
- K. Lewandowski and K. Skórczewska, A brief review of poly(vinyl chloride) (PVC) recycling, Polymers, 2022, 14, 3035 CrossRef CAS PubMed.
- K. Pivenko, M. K. Eriksen, J. A. Martín-Fernández, E. Eriksson and T. F. Astrup, Recycling of plastic waste: Presence of phthalates in plastics from households and industry, Waste Manage., 2016, 54, 44–52 CrossRef.
- M. Sadat-Shojai and G.-R. Bakhshandeh, Recycling of PVC wastes, Polym. Degrad. Stab., 2011, 96, 404–415 CrossRef CAS.
- J. C. Worch and A. P. Dove, 100th anniversary of macromolecular science viewpoint: Toward catalytic chemical recycling of waste (and future) plastics, ACS Macro Lett., 2020, 9, 1494–1506 CrossRef CAS.
- S. Seki, F. Osakada and T. Yoshioka, Developments in an industry-led R&D program for recycling PVC products in Japan, J. Mater. Cycles Waste Manage., 2014, 16, 385–397 CrossRef CAS.
- A. Buekens and A. Sevenster, Vinyl 2010 – nearing the target date, J. Mater. Cycles Waste Manage., 2010, 12, 184–192 CrossRef CAS.
-
VinylPlus, Progress report, 2023, https://www.vinylplus.eu/our-achievements/progress-report-2023/ Search PubMed.
- B. A. Helms, Electrifying the upcycling of plastics, Nat. Synth., 2022, 1, 919–920 CrossRef.
-
VantageVinyl, Progress report, 2021, https://vantagevinyl.com/download/progress-report-2021/ Search PubMed.
- M. A. Keane, Catalytic conversion of waste plastics: focus on waste PVC, J. Chem. Technol. Biotechnol., 2007, 82, 787–795 CrossRef CAS.
- J. Millan, G. Martinez and C. Mijangos, Chemical modification of poly(vinyl chloride): a conclusive study of the influence of tacticity, J. Polym. Sci., Part A: Polym. Chem., 1985, 23, 1077–1087 CAS.
- N. Guarrotxena, G. Martinez, J. M. Gomez-Elvira and J. L. Millan, Effect of some tacticity-depending local chain conformations on the behaviour of poly(vinyl chloride). Changes of glass transition temperature through stereoselective substitution in solution, Macromol. Rapid Commun., 1994, 15, 189–196 CrossRef CAS.
- G. Martinez, N. Guarrotxena, J. M. Gomez-Elvira and J. Millan, Specific polymer-solvent interaction and stereospecificity of nucleophilic substitution reaction of PVC, Polym. Bull., 1992, 28, 427–433 CrossRef CAS.
- T. Kameda, M. Ono, G. Grause, T. Mizoguchi and T. Yoshioka, Chemical modification of poly(vinyl chloride) by nucleophilic substitution, Polym. Degrad. Stab., 2009, 94, 107–112 CrossRef CAS.
- S. Moulay and Z. Zeffouni, Application of the Conant-Finkelstein reaction to the modification of PVC: iodinated PVC, J. Polym. Res., 2006, 13, 267–275 CrossRef CAS.
- N. S. Shaglaeva, V. V. Bayandin, R. G. Sultangareev, T. I. Vakul'skaya, S. S. Khutsishvili, E. A. Orkhokova and G. F. Prozorova, Copolymers of vinyl chloride obtained by polymer-analogous reactions of polyvinyl chloride with sodium salts of heteroaromatic H-N acids, Russ. J. Appl. Chem., 2013, 86, 1576–1580 CrossRef CAS.
- C. Mijangos, J. M. Gomez-Elvira, G. Martinez and J. Millan, Chemical modification on PVC during the melt: some fundamental features, Makromol. Chem., Macromol. Symp., 1989, 25, 209–217 CrossRef CAS.
- A. Asadinezhad, M. Lehocky, P. Saha and M. Mozetic, Recent progress in surface modification of polyvinyl chloride, Materials, 2012, 5, 1937–2959 CrossRef.
- W. H. Starnes Jr, Structure defects in poly(vinyl chloride), J. Polym. Sci., Part A: Polym. Chem., 2005, 43, 2451–2467 CrossRef.
- W. H. Starnes Jr, Structural and mechanistic aspects of the thermal degradation of poly(vinyl chloride), Prog. Polym. Sci., 2002, 27, 2133–2170 CrossRef.
- K. Van Cauter, B. J. Van Den Bossche, V. Van Speybroeck and M. Waroquier,
Ab initio study of free-radical polymerization: defect structures in poly(vinyl chloride), Macromolecules, 2007, 40, 1321–1331 CrossRef CAS.
- W. H. Starnes Jr, H. Chung, B. J. Wojciechowski, D. E. Skillicorn and G. M. Benedikt, Auxiliary mechanism for transfer to monomer during vinyl chloride polymerization, Adv. Chem. Ser., 1996, 249, 3–18 CrossRef.
-
G. Wypych, Chapter 4: Principles of thermal degradation, in PVC Degradation and Stabilization, 3rd edn, 2015, pp. 79–165 Search PubMed.
- V. Percec, A. V. Popov, E. Ramirez-Castillo, J. F. J. Coelho and L. A. Hinojosa-Falcon, Non-transition metal-catalyzed living radical polymerization of vinyl chloride initiated with iodoform in water at 25 °C, J. Polym. Sci., Part A: Polym. Chem., 2004, 42, 6267–6282 CrossRef CAS.
- V. Percec, A. V. Popov, E. Ramirez-Castillo and O. Weichold, Living radical polymerization of vinyl chloride initiated with iodoform and catalyzed by nascent Cu0/tris(2-aminoethyl)amine or polyethyleneimine in water at 25 °C proceeds by a new competing pathways mechanism, J. Polym. Sci., Part A: Polym. Chem., 2003, 41, 3283–3299 CrossRef CAS.
- W. H. Starnes Jr and I. M. Plitz, Chemical stabilization of poly(vinyl chloride) by prior reaction with di(n-butyl)tin bis(n-dodecyl mercaptide), Macromolecules, 1976, 9, 633–640 CrossRef.
- L. Shao, C. Qi and X.-M. Zhang, Aminated chlorinated polyvinylchloride nanofiber mat-supported palladium heterogeneous catalysts: preparation, characterization and applications, RSC Adv., 2014, 4, 53105 RSC.
- L. Zhang, M. Xue and Y. Cui, Catalytic performance of PVC-triethylene-tetramine supported Palladium complex for Heck reaction, J. Appl. Polym. Sci., 2010, 115, 2523–2527 CrossRef CAS.
- B. Zhou and Y.-Q. Li, Palladium nanoparticles immobilized on poly(vinyl chloride)-supported pyridinium as an efficient and recyclable catalyst for Suzuki-Miyaura cross-coupling reaction, E-J. Chem., 2011, 8, 1490–1497 CrossRef CAS.
- G. R. Krishnan, K. S. Niveditha and K. Sreekumar, Aminated poly(vinyl chloride): an efficient green catalyst for Knoevenagel condensation reactions, Indian J. Chem., Sect. B: Org. Chem. Incl. Med. Chem., 2013, 52, 428–431 Search PubMed.
- J. Li, G. Yang and Y. Cui, Recyclable polyvinyl chloride-supported pyrrolidine-thiourea as a bifunctional organocatalyst for direct asymmetric aldol reaction in aqueous medium, J. Appl. Polym. Sci., 2011, 121, 1506–1511 CrossRef CAS.
- M. Bakherad, A. Keivanloo, B. Bahramian and M. Siavoshi, Copper- and solvent-free Sonogashira reaction catalyzed by polyvinyl chloride-supported palladium(II) triazole complex, Lett. Org. Chem., 2013, 10, 758–763 CrossRef CAS.
- M. Bakherad, A. Keivanloo, A. Hadi and M. Siavoshi, Copper-free Sonogashira coupling reaction catalyzed by PVC-supported triazine palladium(II) complex under aerobic conditions, Asian J. Org. Chem., 2014, 3, 1189–1192 CrossRef CAS.
- M. Bakherad, A. Keivanloo and S. Samangooei, Poly(vinyl chloride)-supported Pd(II) complex as an efficient catalyst for Heck and Cu-free Sonogashira reactions under aerobic conditions, Chin. J. Catal., 2014, 35, 324–328 CrossRef CAS.
- J. Zhu, Y. Su, X. Zhao, Y. Li, J. Zhao, X. Fan and Z. Jiang, Improved antifouling properties of poly(vinyl chloride) ultrafiltration membranes via surface zwitterionicalization, Ind. Eng. Chem. Res., 2014, 53, 14046–14055 CrossRef CAS.
- A. Oztuna, H. Nazir and M. Baysallar, Simultaneous Bacillus anthracis spores detection via aminated-poly(vinyl chloride) coated piezoelectric crystal immunosensor, J. Coat., 2014, 2014, 256168 Search PubMed.
- Y. Shu, X.-W. Chen and J.-H. Wang, Ionic liquid-polyvinyl chloride ionomer for highly selective isolation of basic proteins, Talanta, 2010, 81, 637–642 CrossRef CAS.
- A. Siekierka, J. Wolska, W. Kujawski and M. Bryjak, Modification of poly(vinyl chloride) films by aliphatic amines to prepare anion-exchange membranes for Cr (VI) removal, Sep. Sci. Technol., 2018, 53, 1191–1197 CrossRef CAS.
- K. Bierbrauer, M. Lopez-Gonzalez, E. Riande and C. Mijangos, Gas transport in fluorothiophenyl modified PVC membranes, J. Membr. Sci., 2010, 362, 164–171 CrossRef CAS.
- N. S. Shaglaeva, V. V. Bayandin, P. V. Multuev, K. A. Abzaeva and M. G. Voronkov, Polyvinyl chloride modification with sodium salt of 2-thiobenzimidazole, Russ. J. Gen. Chem., 2014, 84, 1799–1802 CrossRef CAS.
- F. Ammari and F. Meganem, Poly(vinyl chloride) functionalization by aliphatic and aromatic amines: application to the extraction of some metal cations, Turk. J. Chem., 2014, 38, 638–649 CrossRef CAS.
- M. S. Abdallh, Synthesis and optical properties of some metal complexes of poly(vinyl chloride)-pyridine-4-carbohydrazide, Journal of Al-Nahrain University Science, 2013, 16, 24–29 CrossRef.
- A. Singh, M. S. M. Rawat and C. S. Pande, Chemical modification and characterization of poly(vinyl chloride) by crosslinking of multifunctional amines, J. Appl. Polym. Sci., 2010, 118, 876–880 CrossRef CAS.
- F. Ammari, M. Dardouri and F. Meganem, A poly(vinyl chloride) functionalized by diethylenetriamine, 2,6-bis-(chloromethyl) pyridine and a crowded aromatic amine. Inductively coupled plasma study of the extraction of La(III) and Bi(III) by modified PVC polymers, Desalin. Water Treat., 2016, 57(41), 19488–19494 CrossRef CAS.
- M. Lamanna and N. D'Accorso, New copolymers with heterocyclic pendant groups obtained from PVC using microwave-assisted process, J. Appl. Polym. Sci., 2011, 121, 951–956 CrossRef CAS.
- E. Yousif and D. S. Ahmed, Poly(vinyl chloride) reinforced Schiff base as an eco-friendly alternative to conventional PVC, SN Appl. Sci., 2019, 1, 955 CrossRef CAS.
- M. Abdallh, M. Bufaroosha, A. Ahmed, D. S. Ahmed and E. Yousif, Modification of poly(vinyl chloride) substrates via Schiff's base for photochemical application, J. Vinyl Addit. Technol., 2020, 26, 475–480 CrossRef CAS.
- A. Ouerghui, F. Ammari and C. Girard, The use of chemically modified PVC waste to remove ions from wastewater, Polimery, 2020, 65, 801–806 CrossRef CAS.
- A. S. Abdel-Naby and A. A. Al-Ghamdi, Poly(vinyl chloride) blend with biodegradable cellulose acetate in presence of N-(phenyl amino) maleimides, Int. J. Biol. Macromol., 2014, 70, 124–130 CrossRef CAS PubMed.
- B. Massoumi, M. Eskandani and M. Jaymand, Novel strategy for anhydride-functionalization of poly(vinyl chloride): synthesis and characterization, Polym.-Plast. Technol. Eng., 2016, 55, 1357–1364 CrossRef CAS.
- A. M. Elsharif, A. A. Al-Ghamdi and A. S. Abdel-Naby, Modification of poly(vinyl chloride) by N-phenyl itaconimides for the improvement of its thermal stability, J. Chem., 2019, 2019, 4782745 Search PubMed.
- M. M. T. El-Saidi, A. A. El-Sayed, D. A. Ali, N. Y. Khaireldin and S. T. Rabie, Chemical modification of poly(vinyl chloride) using some aminopyrimidine derivatives for photo, thermal, mechanical, and antimicrobial evaluation, Egypt. J. Chem., 2020, 63, 3117–3128 Search PubMed.
- D. A. Ali, N. Y. Khaireldin, M. A. El-Hashash, M. M. T. El-Saidi, A. A. El-Sayed, N. A. M. Abdelwahed and S. T. Rabie, Synthesis, characterization and in vitro antimicrobial evaluation of thermally and photostable Schiff base-modified PVC/nanocomposites, Egypt. J. Chem., 2020, 63, 4833–4849 Search PubMed.
- S. Moulay, Covalent functionalization of poly(vinyl chloride) in tune with applications: an update, J. Res. Updates Polym. Sci., 2015, 4, 79–122 CrossRef CAS.
- S. Moulay, Chemical modification of poly(vinyl chloride)–Still on the run, Prog. Polym. Sci., 2010, 35, 303–331 CrossRef CAS.
- R. Navarro, M. P. Perrino, M. G. Tardajos and H. Reinecke, Phthalate plasticizers covalently bound to PVC: plasticization with suppressed migration, Macromolecules, 2010, 43, 2377–2381 CrossRef CAS.
- Z. Deliballi, R. Demir-Cakan, B. Kiskan and Y. Yagci, Self-healable and recyclable sulfur rich poly(vinyl chloride) by S–S dynamic bonding, Macromol. Chem. Phys., 2023, 224, 2100423 CrossRef CAS.
- E. J. Park, B. C. Park, Y. J. Kim, A. Canlier and T. S. Hwang, Elimination and substitution compete during amination of poly(vinyl chloride) with ethylenediamine: XPS analysis and approach of active site index, Macromol. Res., 2018, 26, 913–923 CrossRef CAS.
- N. G. Bush, M. K. Assefa, S. Bac, S. M. Sharada and M. E. Fieser, Controlling selectivity for dechlorination of poly(vinyl chloride) with (xantphos)RhCl, Mater. Horiz., 2023, 10, 2047–2052 RSC.
- X. L. Wu and P. Liu, Poly(vinyl chloride)-grafted multi-walled carbon nanotubes via Friedel-Crafts alkylation, eXPRESS Polym. Lett., 2010, 4, 723–728 CrossRef CAS.
- H. Song, J. Gao, X. Chen, J. He and C. Li, Removal of thiophenic sulfur compounds from oil using chlorinated polymers and Lewis acid mixture via adsorption and Friedel-Crafts alkylation reaction, Chin. J. Chem. Eng., 2014, 22, 713–720 CrossRef CAS.
- B. Massoumi, A. Farnoudian-Habibi and M. Jaymand, Chemical and electrochemical grafting of polythiophene onto poly(vinyl chloride): synthesis, characterization, and materials properties, J. Solid State Electrochem., 2016, 20, 489–497 CrossRef CAS.
- R. Arslan, M. A. Tasdelen and M. Arslan, Covalent modification of poly(vinyl chloride) via organometallic Barbier reaction, Eur. Polym. J., 2022, 177, 111475 CrossRef CAS.
- M. K. Assefa and M. E. Fieser, Divergent silylium catalysis enables facile poly(vinyl chloride) upcycling to poly(ethylene-co-styrene) derivatives, J. Mater. Chem. A., 2023, 11, 2128 RSC.
- A. Earla and R. Braslau, Covalently linked plasticizers: triazole analogues of phthalate plasticizers prepared by mild copper-free “click” reactions with azide-functionalized PVC, Macromol. Rapid Commun., 2014, 35, 666–671 CrossRef CAS.
-
R. Braslau, Polymer plasticizing agents that produce polymers that do not release endocrine disrupting compounds, US Pat., WO2014/071347A1, 2014 Search PubMed.
- P. Yang, J. Yan, H. Sun, H. Fan, Y. Chen, F. Wang and B. Shi, Novel environmentally sustainable cardanol-based plasticizer covalently bound to PVC via click chemistry: synthesis and properties, RSC Adv., 2015, 5, 16980–16985 RSC.
- K. W. Lee, J. W. Chung and S.-Y. Kwak, Structurally enhanced self-plasticization of poly(vinyl chloride) via click grafting of hyperbranched polyglycerol, Macromol. Rapid Commun., 2016, 37, 2045–2051 CrossRef CAS PubMed.
- P. Jia, L. Hu, G. Feng, C. Bo, M. Zhang and Y. Zhou, PVC materials without migration obtained by chemical modification of azide-functionalized PVC and triethyl citrate plasticizer, Mater. Chem. Phys., 2017, 190, 25–30 CrossRef CAS.
- G. Demirci and M. A. Tasdelen, Synthesis and characterization of graft copolymers by photoinduced CuAAC click chemistry, Eur. Polym. J., 2015, 66, 282–289 CrossRef CAS.
- M. Pawlak, E. Grygolowicz-Pawlak and E. Bakker, Ferrocene bound poly(vinyl chloride) as ion to electron transducer in electrochemical ion sensors, Anal. Chem., 2010, 82, 6887–6894 CrossRef CAS PubMed.
- Z. Jarolimova, G. A. Crespo, M. G. Afshar, M. Pawlak and E. Bakker, All solid state chronopotentiometric ion-selective electrodes based on ferrocene functionalized PVC, J. Electroanal. Chem., 2013, 709, 118–125 CrossRef CAS.
- M. Sohail, R. De Marco, M. T. Alam, M. Pawlak and E. Bakker, Transport and accumulation of ferrocene tagged poly(vinyl chloride) at the buried interfaces of plasticized membrane electrodes, Analyst, 2013, 138, 4266–4269 RSC.
- M. Pawlak, G. Mistlberger and E. Bakker, In situ surface functionalization of plasticized poly(vinyl chloride) membranes by ‘click chemistry, J. Mater. Chem., 2012, 22, 12796–12801 RSC.
- M. Pawlak, E. Grygolowicz-Pawlak, G. A. Crespo, G. Mistlberger and E. Bakker, PVC-based ion-selective electrodes with enhanced biocompatibility by surface modification with “click” chemistry, Electroanalysis, 2013, 25, 1840–1846 CrossRef CAS.
- M. Pawlak, G. Mistlberger and E. Bakker, Concanavalin A electrochemical sensor based on the surface blocking principle at an ion-selective polymeric membrane, Microchim. Acta, 2015, 182, 129–137 CrossRef CAS.
- Y. Liu, Y. Xue, H. Tang, M. Wang and Y. Qin, Click-immobilized K+-selective ionophore for potentiometric and optical sensors, Sens. Actuators, B, 2012, 171–172, 556–562 CrossRef CAS.
- B. Oktay, Poly(ethylene glycol)/polyvinyl chloride composite form-stable phase-change materials by the azide-alkyne click reaction, ChemistrySelect, 2018, 3, 11737–11743 CrossRef CAS.
- Z. Huang, A. Ding, H. Guo, G. Lu and X. Huang, Construction of nontoxic polymeric UV-absorber with great resistance to UV-photoaging, Sci. Rep., 2016, 6, 25508 CrossRef PubMed.
- H. Akat and M. Ozkan, Synthesis and characterization of poly(vinylchloride) type macrophotoinitiator comprising side-chain thioxanthone via click chemistry, eXPRESS Polym. Lett., 2011, 5, 318–326 CrossRef CAS.
- J. Lafarge, N. Kebir, D. Schapman and F. Burel, Design of self-disinfecting PVC surfaces using the click chemistry, React. Funct. Polym., 2013, 73, 1464–1472 CrossRef CAS.
- S. Bigot, G. Louarn, N. Kebir and F. Burel, Facile grafting of bioactive cellulose derivatives onto PVC surfaces, Appl. Surf. Sci., 2013, 283, 411–416 CrossRef CAS.
- J. M. Beveridge, H. M. Chenot, A. Crich, A. Jacob and M. G. Finn, Covalent functionalization of flexible polyvinyl chloride tubing, Langmuir, 2018, 34, 10407–10412 CrossRef CAS PubMed.
- W. Liu, Y. Dong, S. Zhang, Z. Wu and H. Chen, A rapid one-step surface functionalization of polyvinyl chloride by combining click sulfur(VI)-fluoride exchange with benzophenone photochemistry, Chem. Commun., 2019, 55, 858 RSC.
- M. Abbasian, B. Massoumi, R. Mohammad-Rezaei and M. Jaymand, A novel epoxy-based resin nanocomposite: co-curing of epoxidized novolac and epoxidized poly(vinyl chloride) using amine-functionalized silica nanoparticles, Mater. Res. Express, 2019, 6, 085346 CrossRef CAS.
- M. Patel, R. Patel, W. S. Chi, J. H. Kim and J.-S. Sung, Antibacterial behavior of quaternized poly(vinyl chloride)-g-poly(4-vinyl pyridine) graft copolymers, Chin. J. Polym. Sci., 2015, 33, 265–274 CrossRef CAS.
- J. H. Koh, S. J. Byun, W. S. Chi and J. H. Kim, Preparation of nanoporous films from self-assembled poly(vinyl chloride-g-methyl methacrylate) graft copolymer, Korean J. Chem. Eng., 2012, 29, 959–963 CrossRef CAS.
- R. Patel, S. H. Ahn, J. A. Seo, S. J. Kim and J. H. Kim, Poly(vinyl chloride)-g-poly(2-(dimethylamino)ethyl methacrylate) graft copolymers templated synthesis of mesoporous TiO2 thin films for dye-sensitized solar cells, J. Nanopart. Res., 2012, 14, 211–222 Search PubMed.
- S. H. Yeon, R. Patel, J. K. Koh, S. H. Ahn and J. H. Kim, Preparation of porous TiO2 thin films by poly(vinyl chloride)-graft-poly(N-vinyl pyrrolidone) and their applications to dye-sensitized solar cells, J. Korean Electrochem. Soc., 2011, 14, 83–91 CrossRef CAS.
- D. K. Roh, J. T. Park, S. H. Ahn, H. Ahn, D. Y. Ryu and J. H. Kim, Amphiphilic poly(vinyl chloride)-g-poly(oxyethylene methacrylate) graft polymer electrolytes: interaction, nanostructures and applications to dye-sensitized solar cells, Electrochim. Acta, 2010, 55, 4976–4981 CrossRef CAS.
- S. H. Yeon, S. H. Ahn, J. H. Kim, K. B. Lee, Y. Jeong and S. U. Hong, Synthesis and gas permeation properties of poly(vinyl chloride)-graft-poly(vinyl pyrrolidone) membranes, Polym. Adv. Technol., 2012, 23, 516–521 CrossRef CAS.
- R. Patel, M. Patel, S. H. Ahn, Y. K. Sung, H.-K. Lee, J. H. Kim and J.-S. Sung, Bioinert membranes prepared from amphiphilic poly(vinyl chloride)-g-poly(oxyethylene methacrylate) graft copolymers, Mater. Sci. Eng. Carbon, 2013, 33, 1662–1670 CrossRef CAS PubMed.
- X.-S. Shao, J.-H. Li, Q. Zhou, J. Miao and Q.-Q. Zhang, Amphiphilic poly(vinyl chloride)-g-poly[poly(ethylene glycol) methylether methacrylate] copolymer for the surface hydrophilicity modification of poly(vinylidene fluoride) membrane, J. Appl. Polym. Sci., 2013, 129, 2472–2478 CrossRef CAS.
- L.-F. Fang, N.-C. Wang, M.-Y. Zhou, B.-K. Zhu, L.-P. Zhu and A. E. John, Poly(N,N-dimethylaminoethyl methacrylate) grafted poly(vinyl chloride)s synthesized via ATRP process and their membranes for dye separation, Chin. J. Polym. Sci., 2015, 33, 1491–1502 CrossRef CAS.
- L.-F. Fang, H. Matsuyama, B.-K. Zhu and S. Zhao, Development of antifouling poly(vinyl chloride) blend membranes by atom transfer radical polymerization, J. Appl. Polym. Sci., 2018, 135, 45832 CrossRef.
- L. Li, Y. Schneider, A. B. Hoeglund and R. Braslau, Advances in internal plasticization of PVC: copper-mediated atom-transfer radical polymerization from PVC defect sited to form acrylate graft copolymers, Synlett, 2021, 32, 497–501 CAS.
- E. Yavuz, Y. Gursel and B. F. Senkal, Modification of poly(glycidyl methacrylate) grafted onto crosslinked PVC with iminopropylene glycol group and use for removing boron from water, Desalination, 2015, 310, 145–150 CrossRef.
- M. Ciftci, M. A. Tasdelen and Y. Yagci, Sunlight induced atom transfer radical polymerization by using dimanganese decacarbonyl, Polym. Chem., 2014, 5, 600–606 RSC.
- Z. Huang, C. Feng, H. Guo and X. Huang, Direct functionalization of poly(vinyl chloride) by photo-mediated ATRP without a deoxygenation procedure, Polym. Chem., 2016, 7, 3034 RSC.
- T. Ozturk, M. Gojtas, B. Savas, M. Isiklar, M. N. Atalar and B. Hazer, Synthesis and characterization of poly(vinyl chloride-graft-2-vinylpyridine) graft copolymers using a novel macroinitiator by reversible addition-fragmentation chain transfer polymerization, e-Polymers, 2014, 14, 27–34 CAS.
- Y. Chang, M. Pan, J. Yuan, Y. Liu, X. Wang, P. Jiang, Y. Wang, G.-J. Zhong and Z.-M. Li, Morphology and film performance of phthalate-free plasticized poly(vinyl chloride) composite particles via the graft copolymerization of acrylate swelling flower-like latex particles, RSC Adv., 2015, 5, 40076–40087 RSC.
- J. Hu, C. Zhang, J. Cong, H. Toyoda, M. Nagatsu and Y. Meng, Plasma-grafted alkaline anion-exchange membranes based on polyvinyl chloride for potential application in direct alcohol fuel cell, J. Power Sources, 2011, 196, 4483–4490 CrossRef CAS.
- A. Asadinezhad, I. Novak, M. Lehocky, V. Sedlarik, A. Vesel, I. Junkar, P. Saha and I. Chodak, A physicochemical approach to render antibacterial surfaces on plasma-treated medical-grade PVC: Irgasan coating, Plasma Processes Polym., 2010, 7, 504–514 CrossRef CAS.
- A. Asadinezhad, I. Novak, M. Lehocky, F. Bilek, A. Vesel, I. Junkar, P. Saha and A. Popelka, Polysaccharides coatings on medical-grade PVC: a probe into surface characteristics and the extent of bacterial adhesion, Molecules, 2010, 15, 1007–1027 CrossRef CAS PubMed.
- L. Islas, C. Alvarez-Lorenzo, B. Magarinos, A. Concheiro, L. F. D. Castillo and G. Burillo, Singly and binary grafted poly(vinyl chloride) urinary catheters that elute ciprofloxacin and prevent bacteria adhesion, Int. J. Pharm., 2015, 488, 20–28 CrossRef CAS PubMed.
- E. Arenas, F. F. Castillon and M. H. Farias, EDC and sulfo-NHS functionalized on PVC-g-PEGMA for streptokinase immobilization, Des. Monomers Polym., 2012, 15, 369–378 CrossRef CAS.
- D. Hammiche, A. Boukerrou, H. Djidjelli and A. Djerrada, Effects of some PVC-grafted maleic anhydrides (PVC-g-MAs) on the morphology, and the mechanical and thermal properties of (alfa fiber)-reinforced PVC composites, J. Vinyl Addit. Technol., 2013, 19, 225–232 CrossRef CAS.
- D. Hammiche, A. Boukerrou, H. Djidjelli, M. Beztout and S. Krim, Synthesis of a new compatibilisant agent PVC-g-MA and its use in the PVC/Alfa composites, J. Appl. Polym. Sci., 2012, 124, 4352–4361 CrossRef CAS.
- N. Seeponkai, J. Wootthikanokkhan and C. Thanachayanont, Synthesis and characterization of fullerene functionalized poly(vinyl chloride) (PVC) and dehydrochlorinated PVC using atom transfer radical addition and AIBN based fullerenation, J. Appl. Polym. Sci., 2013, 130, 2401–2421 CrossRef.
- T. Kameda, M. Yoshihara, G. Grause and T. Yoshioka, Chemical modification of poly(vinyl chloride) using sodium trisulfide, J. Polym. Res., 2015, 22, 88 CrossRef.
- D. E. Fagnani, D. Kim, S. I. Camarero, J. F. Alfaro and A. J. McNeil, Using waste poly(vinyl chloride) to synthesize chloroarenes by plasticizer-mediated electro(de)chlorination, Nat. Chem., 2023, 15, 222–229 CrossRef CAS PubMed.
- C. Decker, Oxidative degradation of poly(vinyl chloride), J. Appl. Polym. Sci., 1976, 20, 3321–3336 CrossRef CAS.
- C. Decker, Degradation of poly(vinyl chloride) by u.v. radiation––II, Eur. Polym. J., 1984, 20, 149–155 CrossRef CAS.
- F. Osada and J. Yana, Deplasticization and dechlorination of flexible polyvinyl chloride in NaOH solution by microwave heating, J. Mater. Cycles Waste Manag., 2010, 12, 245–253 CrossRef CAS.
- A. Kumar, F. Du and J. H. Lienhard V, Caustic soda production, energy efficiency, and electrolyzers, ACS Energy Lett., 2021, 6, 3563–3566 CrossRef CAS.
- F. H. Jabrail, H. M. Awad and A. A. Matlob, Dechlorination of landfill poly(vinyl chloride) waste and estimation of recovered chlorine, Polym. Polym. Compos., 2021, 29, 1273–1281 CAS.
- J. Lu, S. Borjigin, S. Kumagai, T. Kameda, Y. Saito and T. Yoshioka, Practical dechlorination of polyvinyl chloride wastes in NaOH/ethylene glycol using an up-scale ball mill reactor and validation by discrete element method simulations, Waste Manage., 2019, 99, 31–41 CrossRef CAS PubMed.
- J. Lu, S. Borjigin, S. Kumagai, T. Kameda, Y. Saito and T. Yoshioka, Machine learning-based discrete element reaction model for predicting the dechlorination of poly(vinyl chloride) in NaOH/ethylene glycol solvent with ball milling, Chem. Eng. J. Adv., 2020, 3, 100025 CrossRef CAS.
- Y. Chang, Y. Pang, Q. Dang, A. Kumar, G. Zhang, Z. Chang and X. Sun, Converting polyvinyl chloride plastic wastes to carbonaceous materials via room-temperature dehalogenation for high-performance supercapacitor, ACS Appl. Energy Mater., 2018, 1, 5685–5693 CAS.
- T. Zhao, Q. Zhou, X.-L. He, S.-D. Wei, L. Wang, J. M. N. van Kasteren and Y.-Z. Wang, A highly efficient approach for dehydrochlorinating polyvinyl chloride: catalysis by 1-butyl-3-methylimidazolium chloride, Green Chem., 2010, 12, 1062–1065 RSC.
- D. Glas, J. Hulsbosch, P. Dubois, K. Binnemans and D. E. De Vos, End-of-life treatment of poly(vinyl chloride) and chlorinated polyethylene by dehydrochlorination in ionic liquids, ChemSusChem, 2014, 7, 610–617 CrossRef CAS PubMed.
- K. Oster, A. Tedstone, A. J. Greer, N. Budgen, A. Garforth and C. Hardacre, Dehydrochlorination of PVC in multi-layered blisterpacks using ionic liquids, Green Chem., 2020, 22, 5132–5142 RSC.
- P. G. Jessop, Searching for green solvents, Green Chem., 2011, 13, 1391–1398 RSC.
- C. J. Clarke, W.-C. Tu, O. Levers, A. Brohl and J. P. Hallett, Green and sustainable solvents in chemical processes, Chem. Rev., 2018, 118, 747–800 CrossRef CAS PubMed.
- G. O'Rourke, T. Hennebel, M. Stalpaert, A. Skorynina, A. Bugaev, K. Janssens, L. V. Emelen, V. Lemmens, R. D. O. Silva, C. Colemonts, P. Gabriels, D. Sakellariou and D. De Vos, Catalytic tandem dehydrochlorination-hydrogenation of PVC towards valorisation of chlorinated plastic waste, Chem. Sci., 2023, 14, 4401–4412 RSC.
- L. Zhang, M. Zhou, A. Wang and T. Zhang, Selective hydrogenation over supported metal catalysts: From nanoparticles to single atoms, Chem. Rev., 2020, 120, 683–733 CrossRef CAS PubMed.
- S. Svadlenak, S. Wojcik, O. Ogunlalu, M. Vu, M. Dor, B. W. Boudouris, D. Wildenschild and K. A. Goulas, Upcycling of polyvinyl chloride to hydrocarbon waxes via dechlorination and catalytic hydrogenation, Appl. Catal., B, 2023, 338, 123065 CrossRef CAS.
Footnote |
† Papers indexed in Clarivate's Web of Science were searched using the following criteria: using the “all fields” search with multiple rows, the keywords “PVC”, “polyvinyl chloride”, “poly(vinyl chloride)”, and “polyvinylchloride” were entered with the “or” option, which returned 47 845 documents. This list was narrowed down by selecting specific “citation topics”, including “polymer sciences”, “polymers and macromolecules”, “electrochemistry”, “sustainability science”, and “manufacturing”, yielding 11 350 papers. Next, “years published” was narrowed to only include papers published in 2010–2023, which gave 4224 papers. These papers were further filtered by document type, including “articles”, “reviews”, “book chapters”, “early access”, “letters”, and “books”, to give 3866 papers. Next, papers on the following topics were removed to generate 2600 papers: “lithium–sulfur batteries”, “flame retardancy”, “protein adsorption”, “lithium-ion batteries”, “climbing robot”, “proton conductivity”, “thermal comfort”, and “gene delivery”. Next, the title, abstract, and conclusion of these papers were read and non-relevant ones (e.g., construction applications) were removed from the list, bringing the total to 214 papers. Focusing further on the chemical modification of PVC, and omitting the papers related to pyrolysis, gasification, hydrothermal, plasticizer stability, etc., provided 112 papers (85 articles and 27 review papers), which are cited herein. Additional papers were discovered and added during the writing of this work. |
|
This journal is © The Royal Society of Chemistry 2024 |