DOI:
10.1039/D3PY00907F
(Paper)
Polym. Chem., 2023,
14, 4205-4215
Bifunctional diazirine reagent for covalent dyeing of Kevlar and inert polymer materials†
Received
4th August 2023
, Accepted 27th August 2023
First published on 4th September 2023
Abstract
We report a convenient bifunctional diazirine reagent that is capable of photochemically modifying inert polymers, particularly those used in fibers and textiles for ballistics and blast protective gear, such as para-aramid and ultra-high molecular weight polyethylene (UHMWPE). The reagent's structure features a trifluoromethyl diazirine group as a precursor to a carbene that binds the textile surface. On the reagent's other terminus, a benzyl bromide group acts as a site accessible for substitution reactions. As a bench-stable liquid, this bifunctional diazirine can be prepared on gram-scale quantities and rapidly activates under long-wave UV light. A series of fabrics made from Kevlar, Spectra, Dyneema, etc. were functionalized with this diazirine reagent, then subsequently dyed by binding nucleophilic dyes. The resulting coloration was found to be robust and colorfast with respect to water, organic solvent, and simulated laundering with detergent, and the strength of the fibers or fabrics was retained through the dyeing process, as shown through TGA and mechanical break testing. Overall, this carbene-based method provides a general, mild strategy for the covalent attachment of small molecules to textiles made from inert polymers, particularly para-aramids and UHMWPE, as well as nylon and fiber blends of these materials, and has potential use in next-generation protective outerwear.
Introduction
Lightweight, high-strength synthetic fibers made from polymers such as para-aramids (e.g., Kevlar® or Twaron®) or ultra-high molecular weight polyethylene (abbreviated UHMWPE, e.g., Spectra® or Dyneema®) have been implemented in a growing number of diverse applications in ropes, cables, tires, cut-resistant gloves, sportswear and athletic apparel, firefighter gear, and various types of law enforcement and military tactical gear related to ballistics and blast protection, such as vests, body armor, face masks, helmets,1 as well as camouflage-printed flame resistant (FR) uniform fabrics,2 and undergarments designed with knit and woven Kevlar components to be breathable and moisture-wicking and to protect lower extremities and soft tissues in buried blast events.3
The chemical basis of Kevlar is the para-aramid polymer poly(p-phenylene terephthalamide) (abbreviated PPTA)4 that is known to have a high melting point, high glass transition point, and superior thermal and chemical resistance properties.5 PPTA is converted to Kevlar through industrial fiber and fabric processing methods. Kevlar shows exceptional tensile strength (particularly tensile strength-to-weight ratio),6 Young's modulus,7 and stability toward thermal8 or mechanical degradation.9 Kevlar has a strong backbone of amide bonds, efficient interchain hydrogen-bonding interactions, a high degree of crystallinity, and a lack of reactive functional groups, all of which contribute to Kevlar's chemical resistance, including toward dye molecules applied with conventional methods10 and some functional coatings for use as outerwear. Traditional non-covalent dyes wash off Kevlar readily, and reactive dyes do not have sufficient electrophilic or nucleophilic sites to react and form chemical bonds.11 Additionally, due to the involvement of the amide N–H groups in the hydrogen bonding networks, Kevlar does not form strong intermolecular interactions with small-molecule adsorbents. UHMWPE is also chemically inert due to its hydrocarbon structure and shows resistance to dyeing and the application of coatings. Typically, UHMWPE is processed into fibers and other structures through gel-spinning and drawing.12 UHMWPE fibers have become ubiquitous in the fields of composite reinforcements and soft armor.13
Investigating new alternatives for dyeing Kevlar and other inert materials is important for developing next-generation protective outerwear that can be dyed/printed in multi-color patterns, typically in shades of green, brown, tan, and black, and suitable for camouflage in different operational environments.14,15 Some alternative methods for dyeing Kevlar include solution dyeing, pad dyeing, or the use of swelling agents. The drawbacks of these methods are their use of strong acids, harsh solvents, or chemical additives that raise environmental concerns for the safe treatment of effluent wastewater streams.11,16 Environmentally–friendly methods to dye Kevlar have emerged recently, as in the use of non-thermal plasma (NTP) as part of a pre-treatment regime with renewable materials (e.g., soybean oil, glycerol), and NTP was used as a pre-treatment in conjunction with ScCO2 to dye Kevlar woven fabrics with disperse or cationic dyes.17 Similarly, Shim et al. used environmentally–friendly supercritical carbon dioxide (ScCO2) to dye Kevlar knit fabrics through the sorption of disperse dyes.18 However, all of these methods produce Kevlar fabrics as solid colors in a limited number of monochromatic hues.
Several approaches reported derivatizing the surface of Kevlar or Kevlar composite fibers with chemical methods that introduce covalently-bound functionality, such as the use of acidic amide hydrolysis,19N-silylation,20 electrophilic bromination/nitration/sulfonation,21 and N-acylation.22 Yatvin et al. reported a significantly milder and more convenient method to covalently graft several polymers to Kevlar through C–H activation.23 In that approach, various alkenes were first co-polymerized with a sulfonyl azide co-monomer, then the azides were thermally activated to produce electrophilic nitrene intermediates capable of insertion into the aromatic backbone of Kevlar. Aryl and diarylcarbenes have been used as reactive intermediates to functionalize and dye Kevlar fabric and other textile-related polymers, such as cotton (fabric, fibers), nylon-610 (sheet), and UHMWPE (powders).24 These prior carbene-based methods are limited by their lengthy treatment times (>18 h) that are untenable for scale-up and manufacturing processes and by their use of toxic mercury-containing compounds that are unsafe for human health and the environment.
For decades, photo-crosslinking with diazirines as carbene equivalents has been used as a powerful technique in chemical biology for the identification of protein targets for small-molecule binders.25 More recently, diazirines, which can be easily synthesized from ketones,25a have been used in materials science for the crosslinking of unreactive polymers.26 A particularly impressive demonstration of the powerful reactivity of multivalent diazirines was described by Wulff et al. using unfunctionalized aliphatic polymers.27 Presently, we propose the use of a bifunctional, photoactivated small-molecule halogenated carbene precursor to react efficiently through covalent bond formation28 with the backbone of Kevlar to provide covalently-attached electrophilic sites for the attachment of various dyes (Fig. 1). In step 1 (carbene functionalization), the bifunctional carbene precursor molecule bearing a benzyl bromide fragment (2, 4-[3-(trifluoromethyl)-3H-diazirin-3-yl]benzyl bromide) covalently binds Kevlar through the carbene moiety at its first terminus. In step 2 (nucleophilic dyeing), the benzyl bromide group of 2 covalently binds weak nucleophilic dyes via substitution reactions.
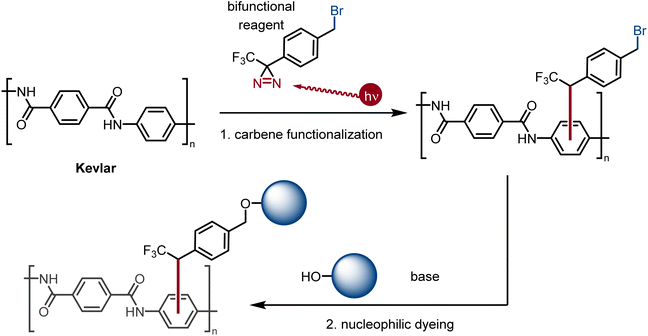 |
| Fig. 1 General scheme for bifunctional carbene-based dyeing of inert polymers. | |
The present carbene-based strategy has several potential advantages over existing technologies. Trifluoromethyl carbenes are more reactive than nitrenes, even though nitrenes have been used more widely for dyeing polymeric substrates.24c Carbenes can also insert directly into C–H bonds.28a Additionally, compared to previous carbene methods, the present method is faster (<2 h) and safer (avoids the use of hazardous mercuric compounds). Further, the present method uses a diazirine reagent that is easily prepared on gram-scale, liquid at ambient temperature and miscible with most organic solvents to facilitate convenient application to fabrics and textiles, and that is bench-stable, yet rapidly activated by long-wave UV light or heat. The diazirine carbene precursor is also more stable than a diazo precursor,28b,c and it is not prone to uncontrolled decomposition that is observed with diazo compounds that can limit their effectiveness. Additionally, the reagents used in the present method are thermally stable, whereas other methods use reagents that are temperature-sensitive and can degrade non-specifically during storage or the functionalization procedures, lowering the efficiency of the dye attachment to the polymer/fiber. Overall, this diazirine method for the chemical modification of para-aramid (Kevlar), UHMWPE (Spectra or Dyneema), nylon (Cordura), or fiber-blend fabrics uses relatively mild conditions, does not compromise the structural integrity and mechanical strength of the fibers/fabrics, and it can be used to dye or apply other finishes or functional coating technologies (e.g., anti-wrinkle,29 anti-microbial30) to these high-performance textiles.
Materials and methods
Materials
Unless otherwise noted, all chemicals were obtained from commercial sources, stored at room temperature, and used as received. Diazirine-containing alcohol (3-[4-(hydroxymethyl)phenyl]-3-(trifluoromethyl)-3H-diazirine) (1) was purchased from TCI America and stored under argon in the dark in a refrigerator. Products were purified by flash chromatography using SiliCycle SiliaFlashP60 (230–400 mesh) silica gel. The organic base 1,8-diazabicyclo[5.4.0]undec-7-ene (abbreviated DBU) was used in these experiments with dyes that include acridine yellow G, solvent yellow 7, oil red O, 1,4-diamino anthraquinone, Texas red cadaverine, napthazarin, quinizarin, pyridium dyes, and toluidine blue O. A multitude of synthetic and designed dyes can be used with this method, provided they contain a group capable of displacing the bromide leaving group on compound 2. The fabrics used to demonstrate the effectiveness of the diazirine-dyeing process and to verify the retention of breaking strength via mechanical testing consist of: Kevlar, Spectra, Dyneema, nylon Cordura, and a fiber-blend experimental fabric. A handheld UV lamp capable of producing either short-wave (254 nm) and long-wave (375 nm) light was used for the photoactivated carbene treatments.
Equipment
Nuclear magnetic resonance spectroscopy (NMR).
1H, 13C, and 19F NMR spectra were obtained with a Bruker Avance-600 MHz or 500 MHz spectrometer. 1H and 13C spectra were calibrated using residual solvent as an internal reference (CHCl3: δ 7.26 ppm and δ 77.36 ppm, respectively; DMSO: 2.50 ppm and 39.52 ppm, respectively). Broadband 1H decoupling was used during the collection of 13C and 19F NMR spectra. The following abbreviations were used to denote multiplicities: s = singlet, bs = broad singlet, d = doublet, t = triplet, q = quartet, p = pentet, and m = multiplet.
X-ray photoelectron spectroscopy (XPS).
XPS measurements were performed using a Thermo Scientific K-Alpha+ X-ray photoelectron spectrometer with a hemispherical energy analyzer and a monochromated X-ray source (Al K-alpha). Survey and high-resolution scans were collected with an X-ray spot size of 400 μm and a pass energy of 200 and 50 eV, respectively. XPS spectra were processed with the Avantage software.
Fourier-transform infrared spectroscopy (FT-IR).
All of the FT-IR spectra of the diazirine-dyed fabric samples were obtained on a Thermo Scientific Nicolet iS5 spectrometer (iD5 ATR, diamond).
Optical spectroscopy.
Ultraviolet–visible (UV-Vis) absorption spectrometry was carried out with an Agilent Cary 5000 instrument. Total diffuse reflection measurements were performed using a PerkinElmer Lambda 1050 UV/Vis/NIR Spectrophotometer with Universal Reflectance Accessory. Photoluminescence measurements were carried out using a HORIBA Jobin Yvon Fluorolog-3 spectrofluorometer (model FL-321).
Thermogravimetric analysis (TGA).
TGA measurements were carried out under nitrogen atmosphere (AirGas, ultra-high purity grade) using a TGA 550 from TA Instruments. The ramp speed was 10 °C min−1, and isotherms were performed from room temperature to 900 °C. The degradation temperature (Td) of a polymer is the temperature at which the polymer loses 10% of its initial mass.
Breaking strength testing.
An Instron (Model 5666) was used to determine the breaking strength and elongation properties of Kevlar, UHMWPE (Spectra or Dyneema), and the fiber-blend fabrics before or after the treatment in General procedure A. Testing was done in accordance with the international test standard ASTM D5034 titled “Breaking Strength and Elongation of Textile Fabrics (Grab Test)”. A Universal Testing System (Instron Model 5500R) was used to determine the tensile strength of a Kevlar filament yarn in accordance with the international test standard ASTM D7269 (“Standard Test Methods for Tensile Testing Aramid Yarns”).
4-[3-(Trifluoromethyl)-3H-diazirin-3-yl]benzyl bromide (2)
Benzyl bromide 2 was synthesized by Appel bromination of the commercially available alcohol 1.31 Specifically, in a 50 mL round-bottomed flask previously dried in an oven and cooled under dry nitrogen, carbon tetrabromide (1.68 g, 5.06 mmol, 1.1 equiv.) and dry dichloromethane (abbreviated DCM, 10 mL) were combined. A magnetic stir bar was added, and the flask was capped with a rubber septum. Using a needle connected to a vacuum manifold, the flask was quickly evacuated and refilled with nitrogen. This procedure was repeated a total of three times. While the solution was stirring rapidly, a solution of triphenylphosphine (1.33 g, 5.06 mmol, 1.1 equiv.) in DCM (10 mL) was added dropwise by syringe. After 30 min, alcohol 1 (1.0 g, 4.6 mmol, 1 equiv.) was added in one portion, and the reaction mixture was left to stir at rt for 12 h. At this point, the septum was removed, and the solvent was distilled away with the aid of a rotary evaporator. The crude residue was subjected to flash column chromatography using a gradient of hexanes to 1
:
5 ethyl acetate/hexanes as eluent. The title product was obtained as a colorless oil (1.19 g, 93% yield), which was stored in the dark in a conventional refrigerator. Spectroscopic data closely matched those reported in the literature.31
Functionalizing fabrics
General procedure A.
The sample, a piece of fabric roughly 2 cm × 2 cm in size, was cleaned thoroughly by rinsing with water, acetone, and DCM, followed by drying in a 50 °C oven for 20 min. The sample was then placed into a glass Petri dish inside a well-ventilated chemical fume hood, and a solution of the diazirine reagent 2 (10 mg mL−1 in DCM) was added dropwise to saturate the fabric sample. After about 1 mL of the solution had been added, the fabric was turned over and the procedure was repeated, and the Petri dish and fabric was placed inside a 50 °C oven for 5 min to evaporate excess DCM. The fabric was removed and irradiated for 30 min on each side with a handheld long-wave UV lamp (375 nm) held at a distance of about 5 cm. The sample was placed in a 20 mL scintillation vial, which was then filled with DCM and submerged in an ultrasonication bath for about 30 seconds. The solvent was decanted away. This washing procedure was repeated a total of 4 times, followed by an additional wash with acetone. In some instances, after completing General procedure A, the sample was air-dried, then analyzed with XPS to assess incorporation of the diazirine-derived fragments. In other instances, after completing General procedure A, the sample was treated with a nucleophilic dye.
Nucleophilic substitution reactivity of Kevlar-attached benzyl bromide groups
Thioacetate.
In a 20 mL scintillation vial, potassium thioacetate (1.14 g, 10 mmol) was suspended in acetonitrile (10 mL), and the mixture was stirred at rt using a magnetic stir bar for 10 min. A sample of 2 attached to Kevlar (Kevlar-BnBr) prepared according to General procedure A was submerged into the solution, then stirred for 30 min. At this point, the fabric was removed and placed in a 20 mL scintillation vial, which was then filled with acetonitrile and submerged in an ultrasonication bath for about 30 seconds. The solvent was decanted away, and this washing procedure was repeated a total of 5 times. After drying in air, the functionalized sample (Kevlar-BnSAc) was analyzed by IR absorbance spectroscopy.
Thioester hydrolysis.
In a 20 mL scintillation vial, 5 mL of a 1 M aqueous NaOH solution, 5 mL of acetone, and the functionalized fabric sample Kevlar-BnSAc were combined and stirred rapidly at 60 °C for 1 h. After cooling to rt, the fabric was removed and placed in a 20 mL scintillation vial, which was then filled with acetone and submerged in an ultrasonication bath for about 30 seconds. The solvent was decanted away, and this washing procedure was repeated a total of 5 times. After drying in air, the hydrolyzed sample (Kevlar-BnSH) was analyzed by IR absorbance spectroscopy.
Dye application and dye scope studies
Fluorophore attachment.
A sample of Kevlar, treated according to General procedure A, was placed into a 20 mL scintillation vial. DCM (15 mL), 1-pyrenemethylamine hydrochloride (25 mg) and anhydrous potassium carbonate (50 mg) were added, and the mixture was stirred vigorously for 10 min. The vial was then capped and immersed in an ultrasonication bath for 30 min at rt. The sample was then removed and placed in pure DCM in a 20 mL scintillation vial for removal of excess, unreacted dye. After thoroughly rinsing the sample with acetone and drying in air, fluorescence of the sample under UV irradiation was evaluated.
Dyeing with nucleophilic dyes.
Fabric samples (Kevlar, UHMWPE, nylon, or fiber-blend) treated according to General procedure A were air-dried, immediately placed in a dry Petri dish, and dyed as follows:
General procedure B.
A solution of dye (5.0 mg) and minimal DCM, acetone, or acetonitrile (1.0 mL or less) was combined in a 20 mL scintillation vial. DBU (0.050 mL) was added, and the mixture was stirred or subjected to sonication until fully homogeneous. This dye mixture was then added dropwise to the fabric sample, allowing for several minutes of evaporation in a well-ventilated fume hood in between applications. The Petri dish containing the fabric was then placed into a pre-heated oven at 120 °C for 10 min. After cooling to rt, the sample was placed in a 20 mL scintillation vial, which was then filled with DCM and submerged in an ultrasonication bath for about 30 seconds. The solvent was decanted away, and this washing procedure was repeated with acetone, methanol, and water. After drying in air, photographs and total diffuse reflectance spectra were obtained.
Colorfastness of dyed Kevlar.
The colorfastness of Kevlar dyed with quinizarin according to General procedure B was determined using a procedure adapted from ISO standard 105-C10:2006 (“Textiles – tests for colorfastness – Part C10: Colorfastness to washing with soap or soap and soda”, Test procedure A). Specifically, the quinizarin-dyed Kevlar sample was placed in an aqueous detergent solution (500 mg of ECOS hypoallergenic laundry detergent with stain-fighting enzymes in 100 mL water) at 40 °C (oil bath heating) and agitated with mechanical stirring for 30 min. The sample was removed from the detergent solution, rinsed thoroughly with warm tap water (pH = 6), dried between two pieces of paper towel, and placed in a 150 °C oven for 2 min. After drying, photographs and total diffuse reflectance spectra before and after laundering were obtained.
Results and discussion
Presently, benzyl bromide (2) was synthesized by Appel bromination of the commercially available alcohol 1.31 Routes have also been reported from acid 3,32p-tolyl diazirine 4,33 and phenyl diazirine 5 (Scheme 1).
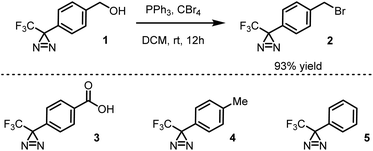 |
| Scheme 1 Synthesis of diazirine reagent. | |
Compound 2 was isolated as a clear liquid on multi-gram scale,34 and 2 can be stored in a dark vial under ambient conditions for at least several months without noticeable decomposition. Compound 2 exhibits a broad absorbance feature in the long-wave UV range (λmax = 352 nm, ε = 270 M−1 cm−1), which decreases in intensity over 70 s of irradiation with a handheld UV lamp (375 nm), indicating photo-activation of the diazirine (see ESI, Fig. 1†). To coordinate this reagent to Kevlar (Scheme 2), this reagent was dissolved in DCM solution (10 mg mL−1 concentration), deposited onto a swatch of Kevlar by soaking, then air-evaporated in a chemical fume hood. Following the evaporation of the solvent, the sample was irradiated with a handheld UV lamp for 30 min. After completion of the UV treatment, the material was extensively rinsed with DCM and acetone to remove any physisorbed organics.
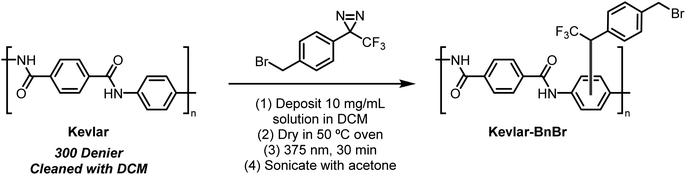 |
| Scheme 2 Coordination of brominated diazirine reagent (2) to Kevlar. | |
X-ray photoelectron spectroscopy (XPS) was carried out to examine the elemental composition of the Kevlar surface. XPS revealed that fluorine and bromine had been incorporated in a ratio of 3
:
1, consistent with the addition of CF3 and Br in a stoichiometric proportion (Fig. 2). For further details, see ESI, Section 2,† as a control experiment, Kevlar was treated with the same chemical procedure, except without UV irradiation. In this case, only trace fluorine and bromine were detected, showing that unactivated compound 1 does not bond or adsorb strongly to the Kevlar surface. Additionally, to assess whether the covalent bonds formed with Kevlar were stable, the first, light-treated sample was subjected to Soxhlet extraction with acetone for 24 h. Although a substantial amount of the fluorine content remained, a decrease in the bromine content was observed. The covalent bond of the brominated diazirine reagent 2 to the polymer appears to be fairly robust, while the benzyl bromide group may be prone to hydrolysis during prolonged exposure to solvent. Thus, in the following experiments, any subsequent functionalization was carried out within a few hours after the initial diazirine treatment.
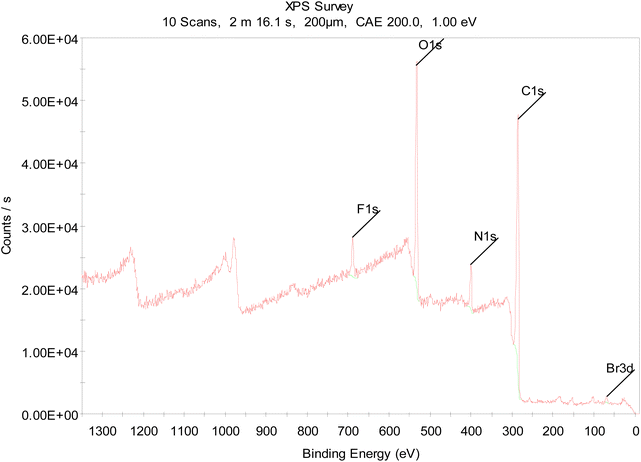 |
| Fig. 2 XPS spectrum of Kevlar functionalized with compound 2 (see Scheme 2). | |
After confirming covalent attachment of the benzyl–bromide diazirine reagent 2 to Kevlar with XPS and the solvent extraction methods, the reactivity of the bromine-containing group toward nucleophiles was tested with the diazirine coordinated to Kevlar. Specifically, a benzyl–bromide-modified Kevlar sample was prepared according to General procedure A, then treated with a potassium thioacetate (–SAc) in acetonitrile solution. FT-IR spectroscopy (Fig. 3) showed the appearance of a small new signal around 1700 cm−1, consistent with the carbonyl stretch of a thioester group,35 in addition to the presence of the intense –C
O stretching peak of Kevlar17,36 occurring at ca. 1650 cm−1. Upon subsequent treatment of the sample with sodium hydroxide, the thioester was hydrolyzed quantitatively, and the corresponding IR resonance at 1700 cm−1 disappeared (Fig. 3). This procedure verified the reactivity of the benzyl bromide group on the second terminus of the diazirine reagent to nucleophiles, without interfering with the bonding of the first terminus of the diazirine with the Kevlar surface.
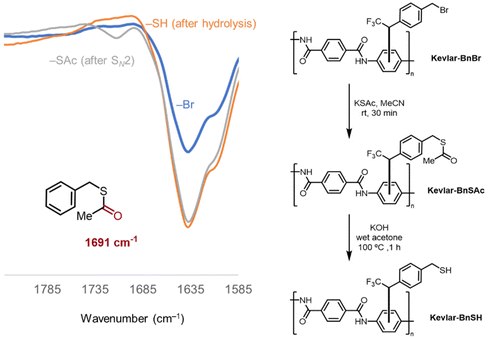 |
| Fig. 3 IR transmission spectrum of Kevlar sample after benzyl–bromide diazirine attachment (blue), thioacetate treatment (grey), and base hydrolysis of the thioester group (orange). | |
This carbene method was also used to modify Kevlar with organic fluorophores through nucleophilic substitution. The photochemical treatment of General procedure A was used to attach benzyl bromide functional groups to Kevlar. A sample of functionalized Kevlar was placed in an acetonitrile solution containing 1-pyrenemethylamine and DBU. After washing the surface with various organic solvents and drying, the material exhibited bright blue fluorescence characteristic of the presence of pyrene groups, in contrast to the inherent green-yellow emission of Kevlar (Fig. 4). Photoluminescence spectra were obtained on this pyrene-modified sample, as well as control samples of plain Kevlar and Kevlar exposed to 1-pyrenemethylamine without the diazirine treatment, and the results confirmed the change in fluorescence caused by covalent attachment of the dye.
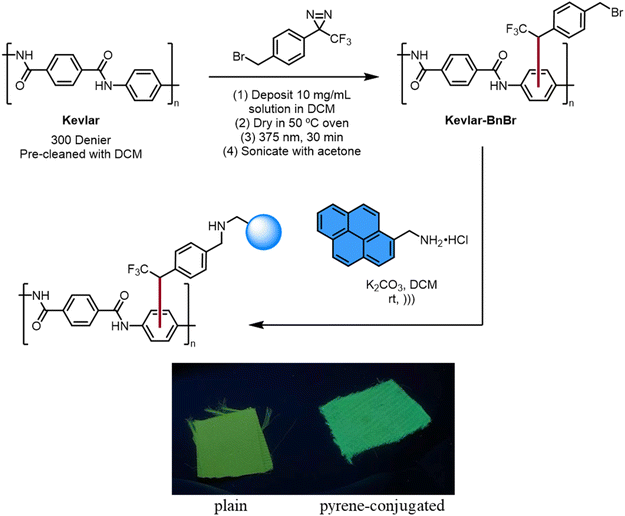 |
| Fig. 4 Attachment of a fluorescent dye to Kevlar. | |
The diazirine method was used to attach various dye molecules to functionalized Kevlar. After attaching the diazirine to Kevlar through General procedure A, the Kevlar swatches functionalized with the benzyl–bromide diazirine reagent were soaked in a concentrated solution of dye in DCM or acetone solvent, with several percent of the soluble organic base DBU added to it. The sample was removed from solution, then immediately placed in a 120 °C oven for 10 min. To remove excess, unreacted dye and other residual compounds, the samples were rinsed thoroughly with DCM and water, then subjected to ultrasonication in various organic solvents. The resultant samples showed visual indications of dyeing. Photographs of the dyed fabric samples, the chemical structures of the eight (8) dyes, and the total reflectance spectra of the dyed samples (and undyed Kevlar control) are provided in Fig. 5A–C.
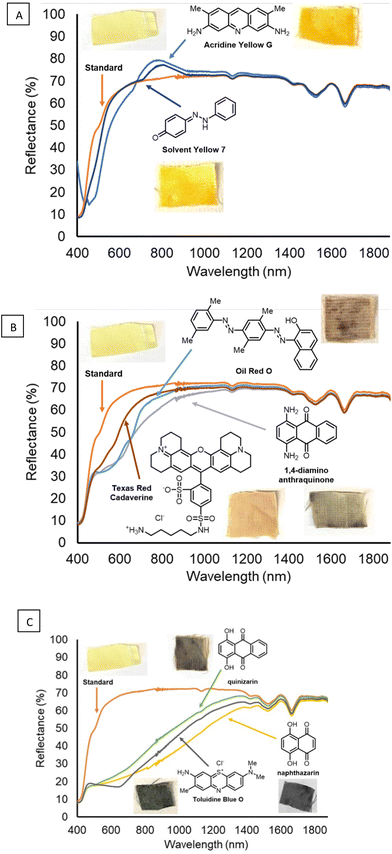 |
| Fig. 5 (A–C) Reflectance spectra and photographs of dyed Kevlar samples, and the corresponding dye structures for each sample. | |
In addition to the fabric made of Kevlar mentioned above (Fig. 5A–C), a range of other ballistics-related fabrics were stained successfully through the diazirine functionalization method, followed by thermal treatment with quinizarin and DBU. Additionally, fabrics comprising UHMWPE (Spectra), nylon (Cordura), and a fiber blend experimental fabric were successfully stained a dark brown color (Fig. 6) similar to that of quinizarin-dyed Kevlar (Fig. 5C).
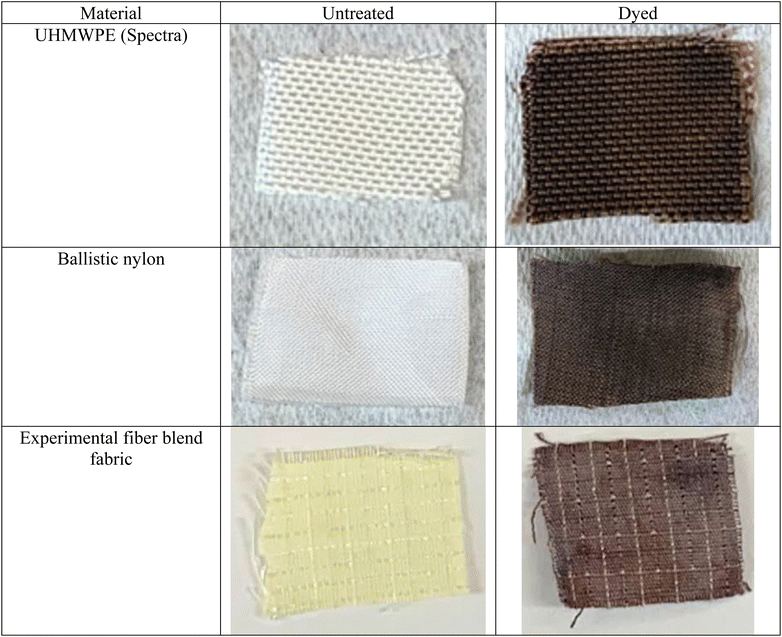 |
| Fig. 6 UHMWPE, nylon, and fiber-blend fabrics dyed with the diazirine-based method. | |
Colorfastness is a common measure of the ability of dyed textiles to retain color without fading or running, including during laundering. To assess the robustness of the dye attachment with the present diazirine method, the colorfastness of a representative sample of dyed Kevlar was evaluated using a simulated laundering procedure based on an international standard procedure.37 The dyed Kevlar sample was subjected to an aqueous detergent mixture at elevated temperature (40 °C) with agitation (vigorous mechanical stirring), followed by rinsing with water and drying. After the simulated laundering cycle, a faint yellow color developed in the liquid phase of the wash cycle, although no noticeable fading was observed visually in the washed versus the unwashed fabric sample. To measure colorfastness, the total diffuse reflectance of the sample was measured before and after laundering, and the values remained virtually unchanged at 5% and 6% (at 450 nm), respectively (Fig. 7).
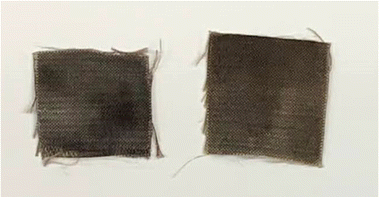 |
| Fig. 7 Stained Kevlar sample before (left) and after (right) simulated laundering. | |
Most applications of para-aramids depend on the high tensile strength, modulus, and similar mechanical properties of the fibers. The effects of the present carbene-based dyeing method on the integrity of the fabrics or its constituent fibers was investigated using TGA measurements and mechanical break tests. The diazirine compound 2 and UV irradiation treatment were applied to Kevlar, UHMWPE, and the fiber blend experimental fabric according to General procedure A, without carrying out the subsequent dyeing step. The effect of this diazirine functionalization procedure on the thermal stability of the Kevlar fibers was evaluated using TGA, which showed (Fig. 8) that treated and untreated fabric samples decomposed at a similar temperature. This trend was observed consistently for fabrics comprising para-aramid (Kevlar), UHMWPE, or the fiber blend (Fig. 8).
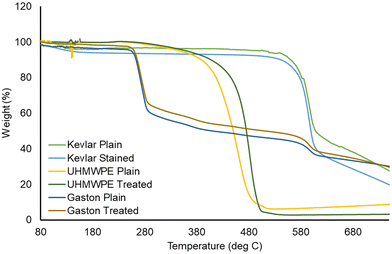 |
| Fig. 8 Thermogravimetric analysis of three fabrics before and after carbene-based dyeing, using quinizarin as the dye component. | |
Similarly, the breaking strength and elongation were determined for the para-aramid (Kevlar), UHMWPE, and fiber blend fabrics after diazirine treatment using standard test methods (in the warp and fill directions for woven fabrics, in the Wales direction for knit fabrics – see Table 1). In all cases, the stretching force tolerated by the processed samples was similar to that of the untreated textile, with some noticeable differences based on the material and the construct of the fabric being tested. Specifically, woven Kevlar, UHMWPE (Spectra), or fiber blend fabrics showed no significant change in breaking strength in either the warp or fill directions (fill direction only for the fiber blend fabric) after diazirine treatment, although Kevlar and UHMWPE (Spectra) showed significantly higher values in maximum load and per cent elongation compared to the fiber blend fabric. Similarly, the UHMWPE (Dyneema) knit fabric showed no loss in mechanical strength resulting from the diazirine treatment, but had a substantially higher per cent elongation prior to breaking than the woven fabrics. Testing individual yarns represents a worst-case for exposure to a chemical treatment than might be expected for a fabric. A Kevlar yarn showed no significant change in breaking strength after the diazirine treatment (Table 1). Taken together with the TGA results, these results indicate there is no significant chemical or physical damage of these fibers/fabrics occurring from the diazirine treatment. Therefore, this carbene-based method can dye high performance textiles without compromising the mechanical properties of the fibers/fabrics and rendering these textiles unsuitable for their intended application(s).
Table 1 Summary of tensile testing results
Sample |
Diazirine treatmenta |
Direction |
Max load (lbf) |
Elongation (%) |
Samples marked “Yes” for treatment were subjected to diazirine application according to General procedure A in the Materials and Methods.
|
Kevlar yarn |
|
N/A |
127 (T = 21.6 gf den−1) |
N/A |
Kevlar yarn |
Yes |
N/A |
126 (T = 21.4 gf den−1) |
N/A |
Kevlar woven |
|
Warp |
571 |
18.0 |
Kevlar woven |
Yes |
Warp |
560 |
18.0 |
Kevlar woven |
|
Filling |
846 |
7.9 |
Kevlar woven |
Yes |
Filling |
855 |
7.8 |
Fiber blend woven |
|
Filling |
125 |
7.9 |
Fiber blend woven |
Yes |
Filling |
127 |
7.9 |
UHMWPE woven (Spectra) |
|
Warp |
669 |
16.3 |
UHMWPE woven (Spectra) |
Yes |
Warp |
737 |
16.0 |
UHMWPE woven (Spectra) |
|
Fill |
742 |
26.1 |
UHMWPE woven (Spectra) |
Yes |
Fill |
740 |
23.9 |
UHMWPE knit (Dyneema) |
|
Wales |
298 |
184 |
UHMWPE knit (Dyneema) |
Yes |
Wales |
293 |
191 |
Conclusions
In summary, we have developed an approach using a bifunctional diazirine intermediate for the surface modification of ballistics textiles made from high performance fibers that are generally considered difficult to dye with conventional methods. Specifically, fabrics made of para-aramid (Kevlar), UHMWPE (Spectra or Dyneema), nylon (Cordura), or fiber blends were functionalized to have accessible benzyl bromide groups through a relatively mild procedure that uses a bench-stable bifunctional diazirine reagent that is efficiently activated under UV irradiation. With the diazirine's first terminus covalently bonded to the fabric surface, electrophilic sites on the diazirine's second terminus are accessible to attach visible-color dyes in a robust manner. The dyed fabrics were colorfast with respect to simulated laundering, thermally stable, and retained their mechanical properties, such that the diazirine and UV treatment did not compromise the structural integrity of the fabrics or their constituent fibers. We expect that further development of bifunctional carbene reagents such as 2 will provide a convenient and general method for the incorporation of diverse functional groups on inert polymer surfaces, particularly applying finishes or functional coating technologies to high performance textiles used in ballistics protection.
Conflicts of interest
The authors are preparing to file a patent application based on the described method.
Acknowledgements
This research is funded in part by US Army Combat Capabilities Development Command Soldier Center (CCDC SC) in Natick, MA.
References
-
(a)
H. Mera and T. Takata, High–Performance Fibers, in Ullmann's Encyclopedia of Industrial Chemistry, Wiley-VCH Verlag, 2000 Search PubMed
;
(b) J. A. Reglero Ruiz, M. Trigo-López, F. C. García and J. M. García, Polymers, 2017, 9, 414 CrossRef PubMed
.
-
R. Gavin, The Boston Globe, “A standout in camo. Army's new combat uniforms showcase Bay State textile firm's technological savvy”, 2010, (Jul 11, 2010) – available at https://archive.boston.com/business/technology/articles/2010/07/11/a_standout_in_camo/.
-
C. T. Lopez, US Army ‘Kevlar underpants’ protect pelvic region, 2012, (Feb. 23, 2012) – available at https://www.army.mil/article/74306/kevlar_underpants_protect_pelvic_region#.
- P. W. Morgan and S. L. Kwolek, Macromolecules, 1975, 8, 104 CrossRef CAS
.
-
S. Ozawa, Y. Nakagawa, K. Matsuda, T. Nishihara and H. Yunoki, Novel Aromatic Copolyamides prepared from 3,4′-diphenylene type diamines, and shaped articles therefrom, USPTO4075172, 1978 Search PubMed
.
-
(a) J. Quintanilla, Polym. Eng. Sci., 1990, 39, 559 CrossRef
;
(b) D. Zhu, B. Mobasher and S. Rajan, J. Mater. Civ. Eng., 2011, 23, 230 CrossRef CAS
.
-
(a)
S. L. Kwolek, P. W. Morgan and W. R. Sorenson, Process of making wholly aromatic polyamides, USPTO3063966, 1962 Search PubMed
;
(b)
T. Kiriyama and T. Santa, Fiber of wholly aromatic copolyimide from 2,6-Naphthalene Dicarboxylic acid and 3,4′-Diaminodiphenylether, USPTO5177175, 1993 Search PubMed
;
(c)
R. S. Irwin, Drawable high tensile strength aramids, USTPO5310861, 1994 Search PubMed
;
(d)
R. S. Irwin, Drawable high tensile strength aramids, USPTO5459231, 1995 Search PubMed
;
(e)
R. S. Irwin, Drawable High tensile strength aramids, USPTO5691443, 1997 Search PubMed
.
-
(a) X.-G. Li and M.-R. Huang, J. Appl. Polym. Sci., 1999, 71, 565 CrossRef CAS
;
(b) J. Brown and B. Ennis, Text. Res. J., 1977, 47, 62 CrossRef CAS
.
- R. Pinto, D. Carr, M. Helliker, L. Girvan and N. Gridley, Text. Res. J., 2012, 82, 1157 CrossRef CAS
.
- E. A. Manyukok, S. F. Sadova, N. N. Baeva and V. A. Platonov, Study of dyeing of thermostable para/meta-aramid fibre, Fibre Chem., 2005, 37(1), 54–58 CrossRef
.
-
A. K. R. Choudhury, Dyeing of Synthetic Fibres, in Handbook of Textile and Industrial Dyeing, Elsevier, 2011 Search PubMed
.
-
(a)
T. Y.-T. Tam, C. B. Tan, C. R. Arnett and Q. Zhou, Drawn gel-spun polyethylene yarns and process for drawing, USPTO6969553, 2005 Search PubMed
;
(b)
J. A. P. M. Simmelink and R. Marissen, Process for spinning UHMWPE, USPTO9194059, 2015 Search PubMed
;
(c)
J. A. P. M. Simmelink, J. J. Mencke, M. J. N. Jacobs and R. Marissen, High-performance polyethylene multifilament yarn, USPO11505879, 2022 Search PubMed
.
- K. E. Strawhecker, E. J. Sandoz-Rosado, T. A. Stockdale and E. D. Laird, Interior morphology of high-performance polyethylene fibers revealed by modulus mapping, Polymer, 2016, 103, 224–232 CrossRef CAS
.
- S. M. Burkinshaw, G. Hallas and A. D. Towns, Infrared camouflage, Rev. Prog. Color. Relat. Top., 1996, 26(1), 47–53 CAS
.
- K. K. Gupta, A. Nishkam and N. Kasturiya, Camouflage in the non-visible region, J. Ind. Text., 2001, 31(1), 27–42 CrossRef CAS
.
-
A. Gürses, K. Günes and E. Sahin, Removal of dyes and pigments from industrial effluents, in Green Chemistry and Water Remediation: Research and Applications, Elsevier Inc., 2021, ch. 5, pp. 135–187. DOI:10.1016/B978-0-12-817742-6.00005-0
.
-
(a) M. Morris, X. P. Ye and C. J. Doona, J. Am. Oil Chem. Soc., 2021, 98, 463 CrossRef CAS
;
(b) M. Morris, X. P. Ye and C. J. Doona, Polymers, 2021, 13, 1492 CrossRef CAS PubMed
;
(c) C. Metzcar, X. P. Ye, T. Wang and C. J. Doona, J. Am. Oil Chem. Soc., 2022, 99, 1175 CrossRef CAS
;
(d) C. Metzcar, X. P. Ye, T. Wang and C. J. Doona, Polymers, 2022, 14, 628 CrossRef CAS PubMed
.
-
J.-J. Shim, J.-H. Choi, J.-H. Ju, B.-K. Son, J.-M. Ahn, B. H. Kim and K.-S. Kim, Dyeing of Polyester, Aramid, and Polypropylene Fibers in Supercritical CO2, The 6th ISSF, Versailles, France, 2003, Apr. 28–30 Search PubMed
.
- G. Li, C. Zhang, Y. Wang, P. Li, Y. Yu, X. Jia, H. Liu, X. Yang, Z. Xue and S. Ryu, Compos. Sci. Technol., 2008, 68, 3208 CrossRef CAS
.
- T. Ai, R. Wang and W. Zhou, Polym. Compos., 2007, 28, 412 CrossRef CAS
.
-
(a) Y. Wu and G. C. Tesoro, J. Appl. Polym. Sci., 1986, 31, 1041 CrossRef CAS
;
(b) R. Benrashid and G. C. Tesoro, Text. Res. J., 1990, 60, 334 CrossRef CAS
.
- W. Chen, X.-M. Qian, X.-Q. He, Z.-Y. Liu and J.-P. Liu, J. Appl. Polym. Sci., 2012, 123, 1983 CrossRef CAS
.
- J. Yatvin, S. A. Sherman, S. F. Filacamo and J. Locklin, Polym. Chem., 2015, 6, 3090 RSC
.
-
(a)
M. Moloney and J.-P. Griffiths, Surface functionalisation using arylcarbene reactive intermediates, USPTO7939581, 2011 Search PubMed
;
(b)
M. G. Moloney, W. Ebenezer and K. Awenat, Process for surface functionalization of polymeric substrates using diaryl carbenes as reactive intermediates, USPTO7034129, 2006 Search PubMed
;
(c)
M. G. Moloney, W. Ebenezer and K. Awenat, Process for surface functionalization of polymeric substrates using diaryl carbenes as reactive intermediates, USPTO Patent6699527, 2004 Search PubMed
;
(d) C. L. Bagwell, D. M. L. Leonard, J.-P. Griffiths, M. G. Moloney, N. J. Stratton and D. P. Travers, Macromol. React. Eng., 2014, 8, 170 CrossRef CAS
.
-
(a) J. R. Hill and A. A. B. Robertson, J. Med. Chem., 2018, 61, 6945 CrossRef CAS PubMed
;
(b) L. Dubinsky, B. P. Krom and M. M. Meijler, Bioorg. Med. Chem., 2012, 20, 554 CrossRef CAS PubMed
;
(c) J. Brunner, H. Senn and F. M. Richards, J. Biol. Chem., 1980, 255, 3313 CrossRef CAS PubMed
.
-
(a)
H. Burgoon, C. D. Cyruns and L. F. Rhodes, U.S. PatentWO2016049123, 2016 Search PubMed
;
(b) A. Welle, F. Billard and J. Marchand-Brynaert, Synthesis, 2012, 44, 2249 CrossRef CAS
;
(c) A. Blencowe, C. Blencowe, K. Cosstick and W. Hayes, React. Funct. Polym., 2008, 68, 868 CrossRef CAS
.
- M. L. Lepage, C. Simhadri, C. Liu, M. Takaffoli, L. Bi, B. Crawford, A. S. Milani and J. E. Wulff, Science, 2019, 366, 875 CrossRef CAS PubMed
.
-
(a) D. Bourissou, O. Guerret, F. P. Gabbaï and G. Bertrand, Chem. Rev., 2000, 100, 39 CrossRef CAS PubMed
;
(b) S. Iqbal, Y. Lui, J. G. Moloney, E. M. Parker, M. Suh, J. S. Foord and M. G. Moloney, Appl. Surf. Sci., 2019, 465, 754 CrossRef CAS
;
(c) P. Yang and M. G. Moloney, RSC Adv., 2016, 6, 111276 RSC
.
- C. M. Welch, Text. Res. J., 1988, 58, 480 CrossRef CAS
.
-
(a) M. J. Saif, K. M. Zia, F.-U. Rehman, M. N. Ahmad, S. Kiran and T. Gulzar, J. Text. Inst., 2015, 106, 907 CrossRef CAS
;
(b) V. P. Dhende, S. Samanta, D. M. Jones, I. R. Hardin and J. Locklin, ACS Appl. Mater. Interfaces, 2011, 3, 2830 CrossRef CAS PubMed
;
(c) Y. H. Kim, C. W. Nam, J. W. Choi and J. Jang, J. Appl. Polym. Sci., 2003, 88, 1567 CrossRef CAS
.
- H. Nishiyama, M. Hashimoto, Y. Sadakane, T. Tomohiro and Y. Hatanaka, J. Am. Chem. Soc., 2006, 128, 15092 CrossRef PubMed
.
- B. Latli, H. Morimoto, P. G. Williams and J. E. Casida, J. Labelled Compd. Radiopharm., 1998, 41, 191 CrossRef CAS
.
- M. Nassal, J. Am. Chem. Soc., 1984, 106, 7540 CrossRef CAS
.
- The compound is a crystalline solid at temperatures below about −30 °C.
- Benzyl thioacetate was found to have a C
O stretching frequency of 1691 cm−1.
- M. Mukherjee, S. Kumar, S. Bose, C. K. Das and A. P. Kharitonov, Study on the Mechanical, Rheological, and Morphological Properties of Short Kevlar™ Fiber/s-PS Composites, Polym.-Plast. Technol. Eng., 2008, 47(6), 623–629 CrossRef CAS
.
- Our procedure was developed based on Test A in ISO standard 105-C10:2006.
|
This journal is © The Royal Society of Chemistry 2023 |
Click here to see how this site uses Cookies. View our privacy policy here.