DOI:
10.1039/D3YA00470H
(Perspective)
Energy Adv., 2024,
3, 108-122
Interfacial engineering of lithium metal anodes: what is left to uncover?
Received
21st September 2023
, Accepted 11th November 2023
First published on 14th November 2023
Abstract
Lithium metal batteries possess remarkable energy storage capabilities, but their commercial realization is hindered by challenges in controlling the reactivity of lithium. Interfacial engineering has emerged as a promising strategy for addressing lithium reactivity. In this article, we discuss several key interfacial engineering approaches used to stabilize lithium metal at lithium–electrolyte and lithium–current collector interfaces. We examine these commonly employed interfacial engineering methods and highlight unresolved questions crucial for advancing the understanding of lithium reactivity. Our discussion highlights the potential of interfacial engineering tools to enhance our understanding of and overcome the challenges associated with lithium reactivity.
Introduction
Society's accelerating shift towards renewable and intermittent energy technologies necessitates the use of dependable energy storage systems. While lithium-ion batteries (LIBs) are often used for this purpose, the search for alternative energy storage technologies with higher capacity is becoming increasingly crucial as we approach their theoretical capacity limit.1,2 The lithium metal anode, with a high gravimetric capacity of 3860 mA h g−1, presents opportunities for significant capacity enhancements over LIBs. However, the deployment of lithium metal batteries (LMBs) is hindered by the instabilities associated with lithium metal.3,4 Specifically, the strong reducing ability of lithium causes its reaction with battery electrolytes, resulting in poor capacity retention over extended battery cycles. Additionally, the poor control of lithium growth on the copper current collector used in LMBs promotes inhomogeneous Li microstructures commonly known as dendrites, which pose safety hazards.
Numerous strategies have been employed to address the instabilities of lithium metal batteries, and some of the most successful ones are based on interfacial engineering.5–7 Interfacial engineering schemes stabilize the Li–electrolyte and Li–copper interfaces by decreasing lithium metal reaction during battery cycling. These interfacial engineering approaches include the molecular engineering of liquid electrolytes, the design of artificial solid electrolyte interphases (a-SEIs), and the modification of the copper current collector upon which lithium grows. Each of these strategies addresses the interfacial instability of lithium metal in a specific way. First, in molecular engineering of electrolytes, the electrolyte is designed to react with Li and form species that prevent further Li–electrolyte reactions. The species that form from electrolyte decomposition and remain at the Li–electrolyte interface are referred to as the solid electrolyte interphase (SEI).8,9 In the second strategy, a-SEIs are formed before battery assembly to serve as protective layers that isolate Li from the electrolyte.10,11 In the third strategy, copper modification is carried out using materials that control the growth of Li microstructures and reduce the extent of Li reaction with the electrolyte.12,13 Copper modification is a relatively new approach to interfacial engineering, possibly due to its indirect role in regulating lithium reactivity. While each of these interfacial strategies has significantly contributed to the improvement of lithium metal batteries, questions about their working mechanisms, failure processes, and design principles still need to be addressed for the lithium metal anode to achieve commercial efficacy.
In this perspective article, we present some concepts required for advancing interfacial engineering of lithium metal anodes along each of the three strategies – SEI manipulation through molecular engineering of electrolytes, the design of a-SEIs, and the modification of the copper current collector. Under each interfacial engineering strategy, we discuss the underlying fundamental principles, highlight some of the major discoveries within the approach, and present some unresolved questions that are crucial for further advancement. We pose several unanswered questions and provide discussion from a surface science perspective, enabling readers to understand these systems and formulate additional questions. Finally, we conclude with an outlook on interfacial engineering for lithium metal anodes by discussing opportunities for synergies across the common interfacial engineering thrusts, the importance of understanding interface evolution, and the need for a fundamental understanding of the mechanistic underpinnings of existing strategies. While other promising methods for stabilizing alkali metal batteries have been discussed in excellent perspective and review articles,14–17 our focus in this article is on interfacial engineering. This choice stems from the intriguing and yet unresolved scientific questions that interfacial engineering presents.
The Li–electrolyte interface
Controlling the Li–electrolyte interface is essential for stable battery operation due to the (electro)chemical instability of Li. Li is a potent reducing agent, which means it quickly reacts with most liquid electrolytes.9 This reaction leads to the loss of active Li and electrolyte, and if left uncontrolled, could result in battery failure caused by the complete consumption of active Li or electrolyte. To prevent these undesirable reactions at the Li–electrolyte interface, two methods aimed at creating a stabilizing interface between the Li and the electrolyte are commonly employed: SEI design through molecular engineering of electrolytes, and the design of a-SEIs.
SEI design through molecular engineering of electrolytes
Conceptual framework.
The reaction of Li with liquid electrolytes forms an SEI, a solid barrier layer that resides at the Li–electrolyte interface.9 The SEI controls the extent of Li–electrolyte reactions and dictates the transport of Li ions towards the cathode and anode during battery cycling. To ensure that the Li–electrolyte reaction is self-limiting, the SEI should ideally be electrically resistive to prevent the transport of electrons from Li towards the electrolyte, non-porous to prevent infiltration of electrolyte towards Li metal, and mechanically robust to prevent cracks that could expose Li metal to the electrolyte. In addition to these characteristics, the SEI should be ionically conductive to ensure that Li ions shuttle across battery electrodes easily during cycling, and homogenous to ensure that the transport of Li occurs uniformly across all its domains (Fig. 1a). These SEI properties are usually achieved by tuning electrolyte salts and solvents and introducing additives into electrolytes (Fig. 1b). Here, we will highlight the key trends and findings in SEI design by electrolyte engineering. Rather than offering an exhaustive list of all electrolyte engineering efforts, we refer the reader to excellent reviews for a more extensive discussion on this subject.8,18,19
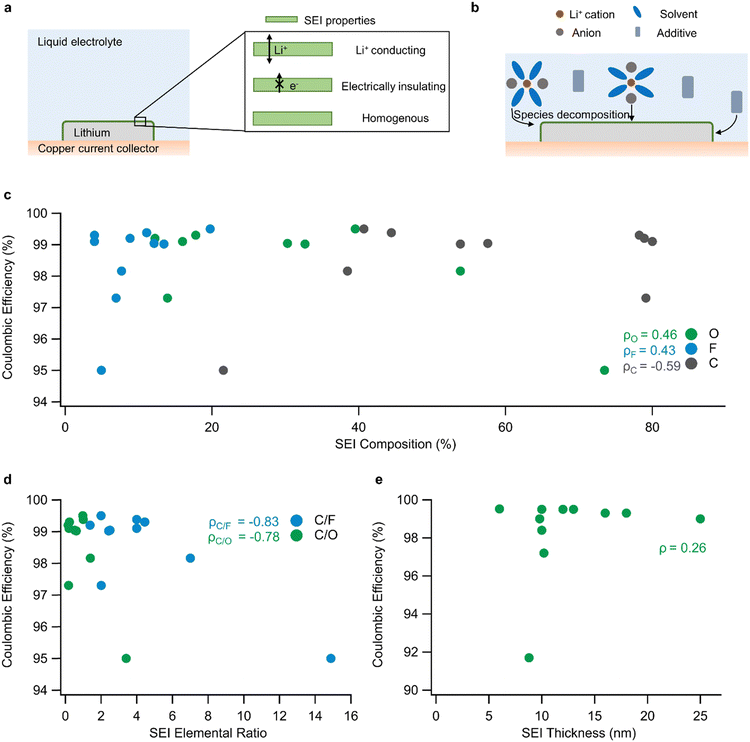 |
| Fig. 1 SEI design through electrolyte engineering: (a) SEI location and ideal properties in a lithium metal battery. (b) Depiction of SEI formation from the decomposition of electrolyte components. (c) Correlation between SEI composition (expressed as % composition of O, F, or C) and CE in a sample of electrolytes (linear correlation for each component is calculated and denoted as ρ). The data in (c) are from Table 1. (d) Correlation between SEI elemental ratio and CE in a sample of electrolytes. (e) Weak correlation between SEI thickness and CE in a sample of electrolytes (data from Table 2). | |
Key approaches to date.
First, the use of additives for SEI design involves the preferential decomposition of additives into favorable SEI species. This preferential decomposition occurs due to changes in electrolyte species distribution or their corresponding decomposition voltage. Some of the common additives are fluoroethylene carbonate (FEC)20–22 and lithium nitrate (LiNO3).23–26 FEC changes the solvation structure of Li ions in electrolytes due to the electron-withdrawing property of fluorine (F). Due to this behavior of F, FEC has been shown to preferentially decompose into LiF, an SEI component that is mechanically stable, electrically resistive, and ionically conductive.27–29 Several reports have shown that the incorporation of FEC into electrolytes improves the long-term cycling stability of the lithium metal anode.20–22 More importantly, the extent of reversibility of lithium deposition, referred to as Coulombic efficiency (CE), increases in the presence of FEC, suggesting that it reduces the extent of parasitic reactions between Li and the electrolyte. A similar strategy is employed with LiNO3 as an additive. LiNO3 has a high decomposition potential,30 indicating its tendency to decompose at potentials higher than the Li/Li+ redox potential. More importantly, LiNO3 decomposes into species like Li2O and Li3N, which are considered beneficial for the SEI because of their mechanical robustness and high ionic conductivity.31,32 As a result, LiNO3 is used as an additive for the formation of stable SEIs in many electrolyte mixtures, the most common of which is the 1 M lithium bis(trifluoromethanesulfonyl)imide (LiTFSI) in 1
:
1 v
:
v 1,3 dioxolane and 1,2 dimethoxyethane mixture.
Another strategy for controlling the SEI involves changing salt chemistry and concentration. This approach aims to promote Li+-anion coordination and induce the formation of favorable SEI species, such as LiF, Li3N, and Li2O at the Li–electrolyte interface while preserving bulk electrolyte transport properties. Over the years, there has been a systematic shift from salts like lithium hexafluorophosphate (LiPF6) and lithium hexafluoroarsenate(V) (LiAsF6) to salts like lithium bis(fluoromethanesulfonyl)imide (LiFSI) and LiTFSI, which decompose into LiF, Li3N, and Li2O.19,33 Other salts that have been used with some success include lithium difluoro(oxalato)borate (LiDFOB) and lithium tetrafluoroborate (LiBF4) because they also decompose into species that are associated with improvements in lithium metal performance.34,35 However, the benefits of changing salts are often hindered by the presence of organic solvents that react with lithium to form unfavorable SEI compounds.36 To circumvent this challenge and preserve the benefits of modifying salt chemistry, salt concentration is usually increased to raise the likelihood of salt/solvent decomposition.37,38 Essentially, by populating the electrolyte with more salt species, the immediate solvation environment of Li+ is predominantly occupied by anions, resulting in the decomposition of those anions into favorable SEI species after lithium deposition. Furthermore, combinations of salts in high and low concentrations are also employed to obtain synergistic Li-passivation benefits.34,35
Finally, electrolyte solvents have also been molecularly tuned for improving the passivation of lithium. Solvents are usually modified to improve SEI chemistry via two routes, namely: the addition of elements like fluorine that react with Li to form favorable SEI species such as LiF, and by molecular changes that impact the solvation of Li+ ions. Some of the notable efforts have involved the introduction of new fluorinated ethers that coordinate weakly with Li+, resulting in Li+ coordination environments that are rich in anions, yielding preferential decomposition of anions, and ensuing formation of favorable SEI species.33,39 Similar changes in Li+ solvation and SEI chemistry have also been achieved using non-fluorinated ethers like diethoxyethane and tert-butyl ether, which also coordinate weakly with Li+.40,41 Another strategy for promoting favorable SEI species is to use solvents that promote clusters of highly concentrated cation–anion pairs. The working principle behind these solvents is that they dilute electrolytes without participating in Li+ solvation, resulting in electrolytes that are referred to as localized high concentration electrolytes (LHCEs).42,43 Because LHCEs accentuate Li+-anion coordination, they promote anion decomposition even at low salt concentrations. Some of the commonly used solvents in LHCEs are 1,1,2,2-tetrafluoroethyl-2,2,3,3-tetrafluoropropyl ether and bis(2,2,2-trifluoroethyl) ether.
Unresolved questions to date.
One of the most pressing issues in SEI design is understanding the connection between the presence of LiF in an SEI, improved lithium passivation, and the subsequent increase in CE. An examination of literature reports of 10 electrolytes used in lithium metal batteries reveals that LiF was identified in the SEI of each one, i.e., across each electrolyte and across differing performances that ranged from 95% CE to 99.5% CE (Table 1). This finding is not surprising since most of the salts used in LMBs contain fluorine and decompose into LiF when in contact with Li metal. Yet, beyond the consistent presence of LiF across the electrolytes, there is no strong linear correlation (ρF = 0.43) between CE and the quantity of fluorine in the SEI (of which the majority can be attributed to LiF as indicated by the X-ray photoelectron spectroscopy (XPS) data in the analyzed literature reports) (Fig. 1c). Hence, this observation suggests that the mere presence of fluorine or LiF in the SEI does not imply passivation of Li metal. A more useful metric for assessing SEI stability may be the ratio of F to other elements that constitute less beneficial components of the SEI, such as C. To explore whether such a relationship exists, the C/F and C/O ratios for the data presented in Fig. 1c are calculated and correlated with CE as shown in Fig. 1d. The analysis shows that C/F and C/O correlate strongly with CE, with linear correlation values of −0.83 and −0.78, suggesting that an increase in carbonaceous species relative to F and O species in the SEI results in lower CE. We speculate that C/F correlates more strongly with CE than C/O because C/F is a more direct comparison between undesired solvent-derived species and desired anion-derived species. Essentially, the electrolytes analyzed in Table 1 contain fluorine-free solvents and carbon-free salts while all the solvents contain O, making the C/F ratio a stronger indicator of solvent/anion incorporation in the SEI than C/O. A few studies have shown that such ratios are useful indicators for anion/solvent decomposition in the SEI, consistent with the strong correlation identified here.44,45 Measurements of SEI species ratios like these can serve as valuable guides for electrolyte selection and design. In particular, the atomic ratio of electrolytes can be combined with simulated distributions of salts and solvents at the lithium-reducing interface to predict the ratio of species within the SEI. These predicted ratios, when combined with insights into the correlation between CE and measured SEI ratios, can inform the design of new electrolytes.
Table 1 SEI composition for different electrolytes with varying CEs. All SEIs listed here contain LiF
Index |
Electrolyte CE |
SEI F%a |
SEI C%a |
SEI O%a |
Ref. |
SEI composition, obtained using XPS, was normalized to include only its major component elements, namely F, C, and O. All CEs were obtained with Li|Cu cells tested using the modified Aurbach method48 or long term cycling CE averages, at 0.5 mA cm−2.
|
1 |
97.3 |
6.94 |
13.94 |
79.12 |
46
|
2 |
99.2 |
8.85 |
12.24 |
78.91 |
46
|
3 |
99.1 |
4 |
16 |
80 |
42
|
4 |
99.3 |
4 |
17.8 |
78.22 |
42
|
5 |
98.16 |
7.69 |
53.85 |
38.46 |
40
|
6 |
99.04 |
12.12 |
30.3 |
57.58 |
40
|
7 |
99.02 |
13.46 |
32.69 |
53.85 |
40
|
8 |
99.38 |
11.11 |
44.44 |
44.44 |
40
|
9 |
95 |
4.94 |
73.49 |
21.57 |
47
|
10 |
99.5 |
19.77 |
39.53 |
40.7 |
47
|
Additionally, it could be helpful to quantify the spatial distribution of elements in the SEI to assess its homogeneity. SEI homogeneity is valuable for evaluating the likelihood of SEI breakdown because it provides information regarding the existence of local regions with high ionic conductivity or low mechanical strength, which could be more susceptible to fracture during battery cycling. The chemical quantification of SEI homogeneity can be carried out by using XPS to characterize multiple spots atop the surface of lithium metal.44
Another question surrounding any approach to influence the SEI design is its structural characterization. Typically, the structural properties of an SEI are determined by evaluating its thickness and uniformity, which are measured using cryogenic-transmission electron microscopy (cryo-TEM). The common understanding has been that thinner and structurally uniform SEIs are beneficial for ion transport and indicative of reduced lithium–electrolyte reactions. However, a comparison of literature reports on SEI thickness reveals only a weak correlation between SEI thickness and CE (Fig. 1e and Table 2, ρ = 0.26). This observation suggests that SEI thickness should not be assessed in isolation but rather must be combined with the measurement of other SEI properties. One of these properties is the chemical identity of the SEI, as discussed earlier, because it could provide insights into the ideal chemistry-thickness combination required for stable SEIs. Another common characterization employed for the SEI is the classification of its microstructure into amorphous or crystalline domains and the subsequent association of Li-ion transport with the properties of those bulk domains. However, Li-ion transport is more complex. Beyond its microstructure, the chemistry and arrangement of local regions of the SEI could significantly impact Li-ion transport. For instance, a computational study showed that Li-ion transport at the interface of LiF and Li2CO3 can be accelerated by interfacial defects.49 Furthermore, it is reasonable to infer that Li-ion transport can be modified by changing the grain size and volume fraction of constituent SEI materials. Therefore, it is important to use nanoscale TEM images in combination with micron-scale SEI chemical information to understand the local and global distribution of components in the SEI. Finally, metrics related to SEI thickness, such as the swelling ratio recently identified by Cui and coworkers,50 can provide information regarding the likelihood of electrolyte infiltration into the SEI, equipping us to better understand lithium passivation.
Table 2 SEI thickness for different electrolytes with varying CEs
Index |
Electrolyte CE (%) |
SEI thickness (nm) |
Ref. |
1 |
98.4 |
10 |
33
|
2 |
99.52 |
6 |
33
|
3 |
99 |
25 |
39
|
4 |
99.3 |
18 |
39
|
5 |
99.3 |
16 |
39
|
6 |
99.5 |
13 |
39
|
7 |
99.5 |
12 |
39
|
8 |
99.5 |
10 |
51
|
9 |
91.7 |
8.8 |
50
|
10 |
97.2 |
10.2 |
50
|
11 |
99 |
9.8 |
50
|
SEI analysis is often performed on freshly deposited lithium. While fresh deposits improve the ease of characterization, they do not provide much information about SEI evolution in subsequent battery cycles. For instance, similar SEIs could form across different electrolytes in the first cycle but evolve differently due to differences in reactivities of solvents and salts present across such systems. The evolution of the SEI in those cases would influence changes in battery performance in subsequent cycles. As such, late-stage cycling analysis of the SEI should be combined with the analysis of freshly formed SEIs to provide a more robust understanding of lithium's interfacial evolution. This analysis could be carried out using spectroscopic techniques like XPS and Fourier transform infrared (FTIR) spectroscopy that can resolve chemical information even after repeated cycles, or methods like electrochemical impedance spectroscopy (EIS) that can be used to characterize SEI growth.
Optimizing the anode's SEI through electrolyte engineering should not occur in isolation from the considerations required for a stable cathode. When addressing the stability challenges of lithium metal, the electrolyte is likely to be paired with numerous cathode materials, spanning from high-voltage transition metal oxides to sulfur and oxygen cathodes. These cathodes introduce additional constraints on the electrolyte,52–54 requiring them to resist oxidation at high voltage, promote facile cathode reaction kinetics, and prevent active cathode disintegration. Consequently, the design of lithium metal electrolytes should encompass both lithium passivation and cathode stabilization.
Finally, there is very little emphasis on the measurement of concrete descriptors for the SEI using metrics such as electrical resistance, mechanical strength, and ionic conductivity. These descriptors are useful because they provide quantitative ways of assessing the requirements for lithium metal passivation. Electrical resistance captures the likelihood of electron transport towards electrolyte decomposition, mechanical strength captures the likelihood of SEI fracture especially under high Li-ion flux, and ionic conductivity captures the energy barrier associated with transporting lithium ions across the SEI. Electrical resistance can be measured using electron spectroscopy, mechanical strength can be measured using atomic force microscopy (AFM), and ionic conductivity can be measured using EIS techniques. These descriptors provide a more holistic view of SEI stability and passivation, and they should be correlated with the more widely used metrics like SEI composition and thickness. By connecting these descriptors with the chemistry, structure, and evolution of the SEI during battery cycling, the battery community will have a more accurate picture of ideal SEI properties.
Artificial SEI design
Conceptual framework.
Due to the high reactivity of lithium metal, a-SEIs are situated at the lithium–electrolyte interface to isolate lithium from the electrolyte and preserve its capacity over the course of battery cycling. However, for an a-SEI to adequately prevent lithium capacity loss without adversely impacting the battery, it must possess several properties, similar to those of “natural” SEIs. First, it must have reasonable ionic conductivity to ensure effective lithium-ion transport. Second, it must be mechanically stable enough to withstand the large stress changes associated with the deposition and dissolution of lithium metal. Third, it must be electrically insulating to prevent electrolyte decomposition caused by electron transport. Finally, it must be chemically inert when placed in contact with lithium to prevent capacity loss. To obtain a-SEIs with all these beneficial properties, many material chemistries and synthesis methods have been explored. Again, excellent review papers55–57 are available that contain detailed discussions of a-SEIs; here we focus only on a few approaches to highlight the fundamental concepts shared among different classes of a-SEIs.
Key approaches to date.
The earliest demonstrations of a-SEIs involved inorganic materials such as metal oxides like Al2O3 and TiO2, which were deposited on top of lithium to isolate its reactive surface from the electrolyte.58–61 One of the main benefits of using inorganic materials is that they have a high Young's modulus, which allows them to retain their mechanical integrity under battery cycling conditions. In addition, when placed in contact with lithium, these inorganic materials can be reduced to form lithium-containing compounds such as LixAl2O3 and LixTiO2, which are conductive to lithium ions. Alternatively, inorganic materials that contain Li, such as Li3PO4, LiF, Li3PS4, and Li3N, have also been used because they are intrinsically conductive to lithium.28,32,62–64 These Li-containing a-SEIs are also expected to be more chemically stable when in contact with Li, thereby reducing parasitic lithium loss in batteries. Inorganic a-SEIs are synthesized using a variety of methods, including atomic layer deposition (ALD), which offers precise control over the thickness and conformality of thin films, enabling nanoscale control over a-SEI properties. Other methods include sputtering, drop-casting, dip-coating of lithium in reactive liquid media, and lithium reaction with gas phase precursors.
Polymers represent another class of a-SEIs. One of the reasons for using polymers as a-SEIs is that their flexibility enables them to adapt to the rapid changes in mechanical stress and surface roughness when lithium metal is deposited and dissolved. Some of the early demonstrations of polymeric a-SEIs were polyethylene oxide,65,66 polyacrylic acid,67 poly (vinylidene difluoride),65,68,69 polyurea,70 and polydimethylsiloxane,65,71 and they showed reasonable stability by extending the cycle life of lithium metal under practical testing conditions. These polymers are often infused with electrolyte mixtures, modified with chemical moieties, and modified structurally to enhance their ionic conductivity. In addition to improved ion transport, polymers can be designed to react minimally with lithium and decompose marginally at the reduction potential of lithium.72 Even though the aforementioned polymers are flexible, they are still likely to fracture under the high stress of practical current densities. As a result, significant efforts have been focused on the design of self-healing polymers which quickly regain their original structure after fracture.65,73 This design is useful because it prevents electrolyte infiltration after polymer fracture, resulting in high-capacity retention of lithium metal batteries. Some notable efforts by Bao and coworkers have fueled the development of self-healing polymer a-SEIs which are cross-linked with hydrogen bonds of different types.65,73 Polymer a-SEIs are often synthesized using traditional polymer chemistry routes65,66 or techniques like molecular layer deposition,70 before being coated onto the lithium anode or battery current collector.
The use of hybrid materials that combine some of the benefits of inorganic materials with those of polymers is another strategy for designing a-SEIs. One notable effort by Sun and coworkers involved using a-SEIs made up of alternating layers of Al2O3 and alucone (a flexible polymeric film with Al–O and glycol moieties), providing the combined benefits of Al2O3's high Young's modulus with alucone's flexibility.74 Other hybrid methods have involved embedding inorganic particles, such as Cu3N, Li3PS4, and LiF, into polymers such as styrene butadiene rubber,75 polydimethylsiloxane,76 and poly vinylidene difluoride,68 respectively, to obtain the strength-flexibility synergy of hybrid a-SEIs. Recently, new synthetic routes have emerged for designing single-ion conducting polymers that contain metal-oxide segments, thereby augmenting the flexible polymer backbone with high mechanical strength. Some of these hybrid SEIs have perfluoro-alkane-diol polymer backbones with Si–O, Al–O, or B–O cross-linked segments.77 Hybrid SEIs are often synthesized using thin-film deposition methods or solution-phase chemistry.
Unresolved questions to date.
One of the key unresolved questions about a-SEIs is how they fail in batteries. In principle, if a-SEIs retain their integrity under repeated battery cycling conditions, lithium metal batteries will not fail. However, in practice, lithium metal batteries do fail even in the presence of a-SEIs, and it is unclear how they do so. First, it is important to distinguish between the possible ways in which a-SEIs can fail. Based on the stresses associated with deposition and dissolution of lithium,78 a-SEIs could fail by delamination. Alternatively, based on the reducing conditions of lithium deposition and the reactivity of common battery electrolytes, a-SEIs could fail due to chemical corrosion (Fig. 2a). By understanding exactly how a-SEIs fail, we will be able to design appropriate mitigation strategies. If physical delamination is identified as the dominant mechanism, more design emphasis can be placed on the mechanical and structural integrity of the a-SEIs. Whereas, if chemical corrosion is the dominant mechanism, emphasis should be placed on designing less reactive electrolytes or designing a-SEIs that are more resistant to chemical degradation. This question regarding the failure mode of a-SEIs in batteries can be addressed by systematically characterizing a-SEIs, electrolytes, and counter electrodes after extended cycling. By identifying and mapping the chemical species atop Li after prolonged battery cycling, it will be possible to ascertain if a-SEIs retain their physical integrity. Additionally, by quantifying the chemistry of species in liquid electrolytes and characterizing the surface of counter electrodes after extended battery cycling, we can determine whether corrosion and dissolution of a-SEIs occur.
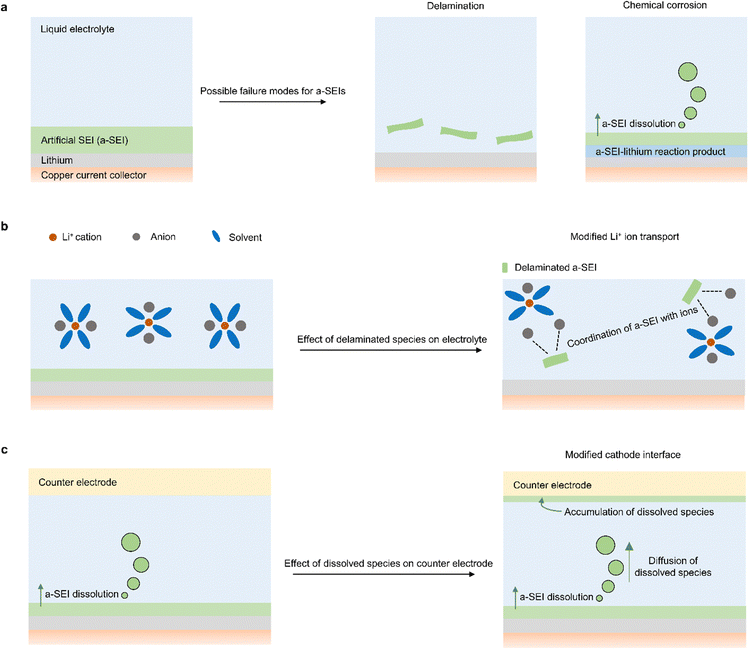 |
| Fig. 2 Design considerations for artificial SEIs: (a) illustration of possible failure modes of a-SEIs in lithium metal batteries. (b) Illustration of delaminated a-SEIs and their effects on ion transport. (c) Illustration of dissolved a-SEIs and their effects on counter electrodes. | |
In addition to identifying the failure modes of a-SEIs, it is important to understand the implications of their failure on other aspects of the battery. One important phenomenon to consider if a-SEI delamination occurs is how it changes electrolyte properties (Fig. 2b). Foreign species in liquid electrolytes can modify the transport of Li-ions and alter the solvation thermodynamics of the electrolyte. In fact, there are two classes of electrolytes called soggy-sand electrolytes79,80 and suspension electrolytes81,82 in which solid species with unique chemical properties are intentionally introduced into liquid electrolytes to modify properties that influence battery performance. Therefore, it is important to understand how a-SEIs that become unintentionally incorporated in the electrolyte affect battery performance. To tackle this challenge, one could first understand the rate at which delamination occurs, identify the regions of the electrolyte that delaminated a-SEIs access, and then design electrolytes that contain the chemical constituents of a-SEIs to understand how they impact lithium metal battery cyclability.
Another important phenomenon to consider during a-SEI failure is how chemically corroded species affect the counter electrode (Fig. 2c). If an a-SEI reacts and forms new species close to the Li electrode, those species will diffuse under a concentration gradient towards the counter electrode. This dissolution phenomenon and its deleterious effects have been observed from the native SEI formed on lithium metal.83 As a result, it is important to identify how the interfacial and electrochemical properties of the counter electrode change in the presence of the a-SEI species that have diffused. The accumulation of foreign non-conductive species could impede the transport of Li-ions at the counter electrode and prove detrimental to battery performance.84,85 To clarify these issues associated with a-SEI dissolution and diffusion, one could use spectroscopy and electrochemistry methods to examine counter electrode materials after long-term battery cycling in the presence and absence of a-SEIs. By using characterization tools, the differences in species adhered to the counter electrode surface can be identified and used to quantify the extent of a-SEI diffusion. Additionally, by pairing cycled counter electrodes with uncycled (fresh) lithium electrodes, one could identify how changes in counter electrode interfaces affect charge transfer at the counter electrode. It is noteworthy that corroded species could also modify transport properties in the electrolyte, similar to delaminated a-SEI species. Likewise, delaminated SEIs could also migrate to the counter electrode interface and affect battery cycling, similar to corroded species.
One other relatively unexplored question is the effect of a-SEIs on molecular properties such as the interfacial solvation of liquid electrolytes. Since a-SEIs typically consist of materials that differ from the species present in electrolytes, they are likely to change the distribution of electrolyte species at the a-SEI–electrolyte interface. These changes in electrolyte distribution can impact Li ion transport and the chemistry of new SEIs formed at those interfaces. Because a high Li ion transport number is deemed to reduce the likelihood of dendrite formation,86 and certain SEI chemistries improve the efficiency of Li cycling,27,33 it is possible that a-SEIs provide these added benefits to Li cyclability. Furthermore, because a-SEIs could be porous, the local changes in electrolyte distribution at the a-SEI–electrolyte interface could influence the species that reach the surface of Li. Species that reach the surface of Li react with Li to form SEIs, and these SEIs could impact battery failure. For instance, a-SEIs that promote the local enrichment of anions will drive preferential transport of anions towards the surface of Li. These anions will react with Li to form anion-rich SEIs, which are reportedly beneficial for improving battery performance.33,45,49,50 To understand how a-SEIs impact interfacial electrolyte properties, there is an opportunity to use molecular simulations to quantify the distribution of electrolyte species on top of corresponding a-SEI materials.87 By performing those simulations under bias, one could also understand how the distribution of electrolyte species at the a-SEI interface changes under battery cycling conditions.
The Li–current collector interface
Modification of the copper current collector
Conceptual framework.
The growth of lithium on Cu incurs a large energy barrier because of the high cost of forming lithium deposits at the Li–Cu interface. As a result, lithium particles tend to prefer growth away from the surface of Cu. This poor wetting of Li at the surface of Cu leads to poor coalescence of lithium and the formation of lithium particles with high surface area. These high surface area particles can then react severely with the electrolyte, resulting in poor cyclability of lithium. To resolve these cyclability problems, Cu modification strategies have been introduced to ensure that uniform, low-surface area lithium deposits form during battery charging. In addition to controlling lithium growth morphology, these strategies must avoid compromising other important battery metrics such as electrical conductivity and energy density. Numerous modification methods have been reported; here we highlight only a few approaches that illustrate thematic threads. For a more exhaustive exploration of copper modification strategies, the reader should refer to excellent review articles.88,89
Key approaches to date.
The most commonly employed copper modification strategy is the design of porous, three-dimensional Cu templates with controlled pore size and distribution (Fig. 3a). Owing to their design, template structures control the homogeneity of lithium-ion flux from the electrolyte to the substrate and enable uniform growth of lithium particles. Moreover, because these 3D structures have a higher surface area than planar Cu, they reduce the effective local current density of lithium ions, resulting in lower overpotentials for lithium growth. Lower overpotentials for lithium growth have been shown to suppress the likelihood of forming high surface area Li particles,90 resulting in reduced Li–electrolyte reactions. In addition, the improved homogeneity in lithium-ion flux which can be attained by tuning the spacing and size of 3D structures, reduces the likelihood of local depletion of lithium ions at the electrode which could lead to the formation of dendrites.91 These benefits make 3D structures advantageous for ensuring that lithium metal batteries operate without losing capacity due to dendrite formation and Li–electrolyte reactions. Many ways have been explored to make 3D Cu structures, including selective etching and dealloying of Cu alloys,92–94 and co-reduction of H+ with Cu2+.95
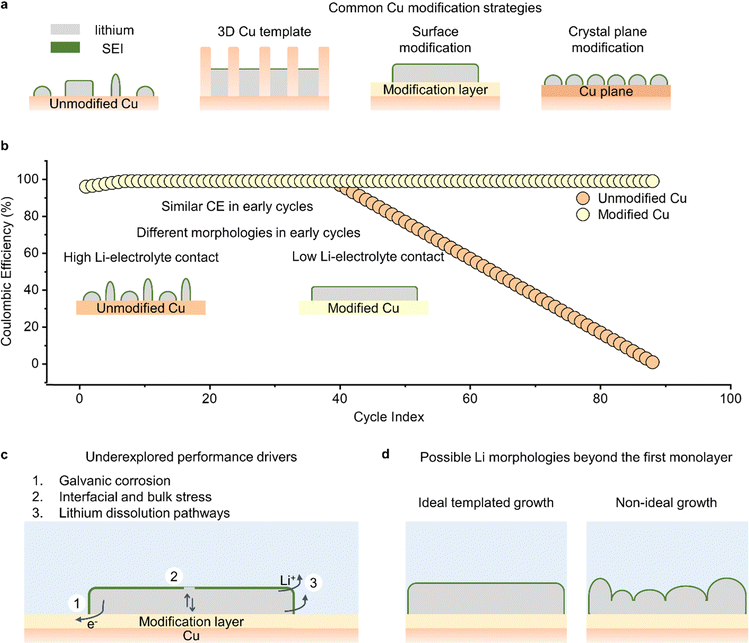 |
| Fig. 3 Design considerations for the Li–Cu interface: (a) illustration of common Cu modification strategies, including 3D Cu templates, surface modification layers, and Cu crystallographic modification. (b) Typical performance trends of modified and unmodified Cu current collectors. The inset figure illustrates expected lithium morphology on unmodified versus modified Cu for early cycles (c) illustration of underexplored performance drivers in Cu modification studies. (d) Illustration of possible Li morphologies beyond the first monolayer on modified Cu. | |
Surface modification of Cu is also commonly used to change the growth structure of lithium (Fig. 3a). Surface modification strategies are centered on selecting materials that alter the energy barrier for nucleating and/or growing (coalescing) lithium particles. These modified materials enable the formation of large lithium nuclei, which subsequently coalesce to form larger lithium particles. Large lithium particles usually have a smaller contact area with the electrolyte, resulting in reduced Li–electrolyte reactions. Some of the materials used for modifying Cu and in turn improving lithium growth include zinc,96 tin,12,97 gold and silver,98,99 and oxides.13,100–102 In most cases, the materials used for modification layers are selected because they react with lithium and form lithium alloys or lithium-containing compounds. When these alloys are formed prior to lithium deposition, they serve as the template for improved lithium growth, as they have lower lithium nucleation barriers than the surface of Cu. In one demonstration of this concept, our group used ALD to modify the surface of Cu with thin films of TiO2.102 These TiO2 films reacted with Li+ prior to lithium metal deposition to form a lithium-containing compound that promoted the growth and coalescence of large lithium particles. In another demonstration of the benefits of surface modification, our group showed that electrically resistive films of ALD-grown Al2O3 can restrict the nucleation of lithium particles to small defect sites, promote the lateral growth of lithium particles, and foster large clusters of lithium on the current collector.103 One notable finding from that work was that, contrary to conventional wisdom which suggests that low nucleation overpotentials (nucleation energy barriers) are required to form large lithium grains, we showed that high nucleation overpotential surfaces like Al2O3 can promote large lithium particles. This lithium growth on Al2O3 followed a radial diffusion-assisted route that is different from common modes of lithium nucleation and growth.
The crystallographic orientation of the Cu current collector is another approach for controlling the growth of lithium. The copper substrate commonly used in batteries is polycrystalline with exposed [100], [110], and [111] planes.103 However, these planes have different surface energies and thus different energy barriers for lithium nucleation and growth. Consequently, lithium grows on these heterogeneous planes in different morphologies thereby consuming varying, and often significant amounts of, electrolyte. This heterogeneity has motivated studies of single crystal Cu substrates to determine the relationship between surface plane and the growth of lithium. There have been a few reports on single crystal Cu substrates: one study reports that Cu[100] has the lowest energy barrier for nucleating lithium, resulting in non-dendritic lithium particles,104 while other groups have reported that Cu[111] also yields non-dendritic lithium particles.105,106 One possible explanation for the difference in conclusions regarding the superior Cu plane is that different lithium growth mechanisms may be dominating on the two planes. In any case, it is clear that more understanding is needed on the role that crystallographic orientation plays in Li deposition morphology.
Unresolved questions to date.
The mechanism behind the performance improvements in modified Cu current collectors has not been fully elucidated. Fig. 3b displays a representative performance trend for both modified and unmodified Cu current collectors, showing CE as a function of cycle index. In the illustration, the unmodified Cu exhibits a drastic decline in CE after 40 cycles, while the modified Cu maintains a high CE beyond 40 cycles. This improved performance of the modified Cu is often attributed to a decrease in the contact area between Li and the electrolyte (Fig. 3b inset). The rationale is that a higher Li–electrolyte contact area in the unmodified Cu results in quicker consumption of the electrolyte and a faster buildup of resistive SEI species, leading to a rapid decline in CE after 40 cycles. However, this contact area rationale alone does not explain the similarities in CE during the early battery cycles (index 1–39). In principle, differences in Li–electrolyte contact area should impact the quantity of Li lost in early cycles, resulting in differences in CE. The fact that similar CEs are displayed in the early cycles suggests that other factors are at play on modified Cu. It is possible that Cu modifications introduce alternative pathways for lithium consumption that offset the lithium preserved from the reduction in Li–electrolyte contact area. To gain a deeper understanding, experiments should be designed to investigate the effects of Cu modifications on the deposition and dissolution of lithium during cycling and calendar aging conditions. By characterizing the battery under both conditions, one could discern if the similar CEs observed in early cycles can be attributed to additional pathways for lithium consumption or electrical isolation. For example, by using titration gas chromatography to quantify the amount of metallic lithium that is unrecovered after stripping on both modified and unmodified Cu,107 one could identify how much lithium is lost to electrical isolation in the early cycles. Also, by using coulometry to quantify the amount of lithium that is recoverable after open circuit calendar aging on both modified and unmodified Cu,108 we could measure differences in corrosion rates. This comprehensive analysis will provide valuable insights into the mechanisms underlying the performance improvements of modified Cu current collectors.
Another unresolved question in current collector design is whether the advantages provided by modification of the copper are solely due to changes in the extent of Li–electrolyte reactions. Current collector modification strategies often involve both structural and chemical changes at the Li–substrate interface, so it is reasonable to assume that these changes can also affect other parameters, such as the rate of lithium galvanic corrosion, the strain within lithium, and the dissolution pathway of lithium (Fig. 3c). Unfortunately, although these factors can strongly influence the reversible cycling of lithium metal, they are not commonly investigated in studies employing current collector modifications. For instance, galvanic corrosion is characterized by the transfer of electrons at the Li–current collector interface due to differences in electrochemical potential between Li and the current collector. Therefore, changes in the structure and chemistry of the current collector could directly impact the surface area available for corrosion, the kinetics of corrosion, and the electrical resistance to corrosion. Similarly, the extent of stress within the bulk and surface of lithium could vary with the underlying substrate, resulting in different implications for the stability of the SEI and rate of consumption of lithium particles. Finally, the dissolution of lithium constitutes the second half of lithium cycling, and its preferred pathway could be altered by changing the current collector. Even though studies of Li dissolution have typically lagged those on Li deposition in lithium metal batteries, it is still important to understand how current collectors change the dissolution rate at the region of contact between Li and the underlying substrate. All these factors can be investigated using carefully designed experiments such as measuring currents when the voltage on Cu is fixed at 0 V vs. Li+/Li to understand how galvanic corrosion varies, measuring CE after lithium deposition at different charge capacities to understand how stress-related SEI fracture varies, and using in operando microscopy to identify lithium dissolution mechanisms.
One concern with current collector modifications is that the modifications are “buried” at the lithium–substrate interface, which raises questions about their effectiveness when lithium deposits grow beyond the monolayer level. Changes in the energy barrier associated with nucleating and coalescing lithium particles at the lithium–current collector interface can affect the way lithium grows, but it is uncertain to what extent these changes propagate through the lithium films as they become thicker (Fig. 3d). This question has implications for the mechanism of lithium deposition. By using scanning electron microscopy to visualize the diameter and thickness of lithium as it grows away from the current collector, we could understand how lithium growth structures at the monolayer level affect deposition beyond the monolayer level. This could provide insights into structural templates that are beneficial for depositing lithium particles with improved reversibility during battery cycling.
Outlook and conclusions
Interfacial engineering strategies have advanced the development of lithium metal batteries. These strategies include molecular engineering of liquid electrolytes for improved SEIs, designing a-SEIs, and modifying copper current collectors. Our discussion demonstrates the versatility of these strategies, as each can effectively preserve lithium capacity by minimizing lithium–electrolyte contact and reactions. Yet, a few important points need to be addressed for the strategies to be used to their full advantage (Fig. 4).
 |
| Fig. 4 Summary of avenues for further investigation in the interfacial engineering of lithium metal anodes. | |
First, we suggest conducting more thorough mechanistic studies to understand how interfacial engineering strategies work. This includes the need for more concrete descriptors of SEI properties that can inform fundamental principles of lithium passivation and guide the design of improved SEI layers. Additionally, mechanistic studies should be utilized to unravel the molecular impact of a-SEIs on Li-ion transport and solvation in the battery. Furthermore, mechanistic work can help reveal new performance drivers at the Li–Cu interface when Cu modification strategies are employed for stabilizing lithium metal anodes.
Second, we propose characterizing battery interfaces over long timescales to shed light on the evolution of interfacial engineering strategies. At different timescales, characterization methods like X-ray photoelectron spectroscopy and infrared spectroscopy can reveal the chemical state of battery interfaces, nuclear magnetic resonance can reveal the species in the electrolyte, Raman spectroscopy can reveal the solvation of electrolyte components, and electrochemical impedance spectroscopy can reveal the resistance and capacitance of battery interfaces. These approaches will reveal the implications of SEI evolution during battery cycling and unravel the failure mechanisms of a-SEIs. Understanding these changes over time will provide valuable insights into the stability and effectiveness of interfacial engineering strategies.
Finally, we emphasize the importance of combining interfacial engineering strategies to understand the compatibility of materials designed for specific interfacial engineering purposes. Developing a foundational understanding of combined approaches is crucial because most interfacial engineering strategies are developed in isolation from each other. For instance, it is unclear if the best performing electrolytes are compatible with the best performing artificial SEIs. As some of these strategies address unique aspects of the lithium reactivity problem, it is essential to ensure their compatibility when combined in a battery. This will promote the retention of their individual ensuing benefits and enhance the overall battery performance.
Interfacial engineering encompasses vast unexplored regions that hold immense potential for comprehending and regulating the reactivity of lithium metal, and ultimately enabling the development of advanced LMBs.
Author contributions
S. T. O. and S. F. B. conceived the idea and wrote the paper.
Conflicts of interest
There are no conflicts to declare.
Acknowledgements
S. T. O. acknowledges support from the TomKat Center Fellowship for Translational Research at Stanford University and the Knight-Hennessy scholarship for graduate studies at Stanford University. S. F. B. acknowledges support from the Stanford StorageX initiative seed grant award.
References
- M. Li, J. Lu, Z. Chen and K. Amine, 30 Years of Lithium-Ion Batteries, Adv. Mater., 2018, 30, 1800561, DOI:10.1002/adma.201800561.
- B. Scrosati, J. Hassoun and Y. K. Sun, Lithium-Ion Batteries. A Look into the Future, Energy Environ. Sci., 2011, 4(9), 3287–3295, 10.1039/c1ee01388b.
- D. Lin, Y. Liu and Y. Cui, Reviving the Lithium Metal Anode for High-Energy Batteries, Nat. Nanotechnol., 2017, 12(3), 194–206, DOI:10.1038/nnano.2017.16.
- J. Liu, Z. Bao, Y. Cui, E. J. Dufek, J. B. Goodenough, P. Khalifah, Q. Li, B. Y. Liaw, P. Liu, A. Manthiram, Y. S. Meng, V. R. Subramanian, M. F. Toney, V. V. Viswanathan, M. S. Whittingham, J. Xiao, W. Xu, J. Yang, X.-Q. Q. Yang and J.-G. G. Zhang, Pathways for Practical High-Energy Long-Cycling Lithium Metal Batteries, Nat. Energy, 2019, 4(3), 180–186, DOI:10.1038/s41560-019-0338-x.
- H. Wang, Y. Liu, Y. Li and Y. Cui, Lithium Metal Anode Materials Design: Interphase and Host, Electrochem. Energy Rev., 2019, 2(4), 509–517, DOI:10.1007/s41918-019-00054-2.
- Q. Yan, G. Whang, Z. Wei, S. T. Ko, P. Sautet, S. H. Tolbert, B. S. Dunn and J. Luo, A Perspective on Interfacial Engineering of Lithium Metal Anodes and Beyond, Appl. Phys. Lett., 2020, 117(8), 80504, DOI:10.1063/5.0018417.
- P. Zhai, L. Liu, X. Gu, T. Wang and Y. Gong, Interface Engineering for Lithium Metal Anodes in Liquid Electrolyte, Adv. Energy Mater., 2020, 10(34), 2001257, DOI:10.1002/aenm.202001257.
- H. Wang, Z. Yu, X. Kong, S. C. Kim, D. T. Boyle, J. Qin, Z. Bao and Y. Cui, Liquid Electrolyte: The Nexus of Practical Lithium Metal Batteries, Joule, 2022, 6(3), 588–616, DOI:10.1016/j.joule.2021.12.018.
- E. Peled and S. Menkin, Review—SEI: Past, Present and Future, J. Electrochem. Soc., 2017, 164(7), A1703–A1719, DOI:10.1149/2.1441707jes.
- Z. Huang, S. Choudhury, N. Paul, J. H. Thienenkamp, P. Lennartz, H. Gong, P. Müller-Buschbaum, G. Brunklaus, R. Gilles and Z. Bao, Effects of Polymer Coating Mechanics at Solid-Electrolyte Interphase for Stabilizing Lithium Metal Anodes, Adv. Energy Mater., 2022, 12(5), 2103187, DOI:10.1002/aenm.202103187.
- L. Fan, H. L. Zhuang, L. Gao, Y. Lu and L. A. Archer, Regulating Li Deposition at Artificial Solid Electrolyte Interphases, J. Mater. Chem. A, 2017, 5(7), 3483–3492, 10.1039/c6ta10204b.
- J. Luan, Q. Zhang, H. Yuan, Z. Peng, Y. Tang, S. Wu and H. Wang, Sn Layer Decorated Copper Mesh with Superior Lithiophilicity for Stable Lithium Metal Anode, Chem. Eng. J., 2020, 395, 124922, DOI:10.1016/j.cej.2020.124922.
- K. H. Chen, A. J. Sanchez, E. Kazyak, A. L. Davis and N. P. Dasgupta, Synergistic Effect of 3D Current Collectors and ALD Surface Modification for High Coulombic Efficiency Lithium Metal Anodes, Adv. Energy Mater., 2019, 9(4), 1802534, DOI:10.1002/aenm.201802534.
- M. T. McDowell, S. W. Lee, W. D. Nix and Y. Cui, 25th Anniversary Article: Understanding the Lithiation of Silicon and Other Alloying Anodes for Lithium-Ion Batteries, Adv. Mater., 2013, 25(36), 4966–4985, DOI:10.1002/adma.201301795.
- S. Liu, L. Kang and S. C. Jun, Challenges and Strategies toward Cathode Materials for Rechargeable Potassium-Ion Batteries, Adv. Mater., 2021, 33(47), 1–40, DOI:10.1002/adma.202004689.
- S. Liu, L. Kang, J. Henzie, J. Zhang, J. Ha, M. A. Amin, M. S. A. Hossain, S. C. Jun and Y. Yamauchi, Recent Advances and Perspectives of Battery-Type Anode Materials for Potassium Ion Storage, ACS Nano, 2021, 15(12), 18931–18973, DOI:10.1021/acsnano.1c08428.
- M. N. Obrovac and V. L. Chevrier, Alloy Negative Electrodes for Li-Ion Batteries, Chem. Rev., 2014, 114(23), 11444–11502, DOI:10.1021/cr500207g.
- X. Q. Zhang, X. B. Cheng and Q. Zhang, Advances in Interfaces between Li Metal Anode and Electrolyte, Adv. Mater. Interfaces, 2018, 5(2), 1701097, DOI:10.1002/ADMI.201701097.
- G. M. Hobold, J. Lopez, R. Guo, N. Minafra, A. Banerjee, Y. Shirley Meng, Y. Shao-Horn and B. M. Gallant, Moving beyond 99.9% Coulombic Efficiency for Lithium Anodes in Liquid Electrolytes, Nat. Energy, 2021, 6(10), 951–960, DOI:10.1038/s41560-021-00910-w.
- X. Q. X. X.-Q. Zhang, X.-B. B. X. Cheng, X. Chen, C. Yan, Q. Zhang, X. Q. X. X.-Q. Zhang, X.-B. B. X. Cheng, X. Chen, C. Yan and Q. Zhang, Fluoroethylene Carbonate Additives to Render Uniform Li Deposits in Lithium Metal Batteries, Adv. Funct. Mater., 2017, 27(10), 1605989, DOI:10.1002/adfm.201605989.
- K. Huang, S. Bi, B. Kurt, C. Xu, L. Wu, Z. Li, G. Feng and X. Zhang, Regulation of SEI Formation by Anion Receptors to Achieve Ultra-Stable Lithium-Metal Batteries, Angew. Chem., Int. Ed., 2021, 60(35), 19232–19240, DOI:10.1002/anie.202104671.
- X. Ren, Y. Zhang, M. H. Engelhard, Q. Li, J. G. Zhang and W. Xu, Guided Lithium Metal Deposition and Improved Lithium Coulombic Efficiency through Synergistic Effects of LiAsF6 and Cyclic Carbonate Additives, ACS Energy Lett., 2018, 3(1), 14–19, DOI:10.1021/acsenergylett.7b00982.
- H. Chu, J. Jung, H. Noh, S. Yuk, J. Lee, J. H. Lee, J. Baek, Y. Roh, H. Kwon, D. W. Choi, K. Sohn, Y. K. Kim and H. T. Kim, Unraveling the Dual Functionality of High-Donor-Number Anion in Lean-Electrolyte Lithium-Sulfur Batteries, Adv. Energy Mater., 2020, 10(21), 2000493, DOI:10.1002/aenm.202000493.
- X. Q. Zhang, X. Chen, L. P. Hou, B. Q. Li, X. B. Cheng, J. Q. Huang and Q. Zhang, Regulating Anions in the Solvation Sheath of Lithium Ions for Stable Lithium Metal Batteries, ACS Energy Lett., 2019, 4(2), 411–416, DOI:10.1021/acsenergylett.8b02376.
- L. Zhang, M. Ling, J. Feng, L. Mai, G. Liu and J. Guo, The Synergetic Interaction between LiNO3 and Lithium Polysulfides for Suppressing Shuttle Effect of Lithium–Sulfur Batteries, Energy Storage Mater., 2018, 11, 24–29, DOI:10.1016/j.ensm.2017.09.001.
- J. Guo, Z. Wen, M. Wu, J. Jin and Y. Liu, Vinylene Carbonate-LiNO3: A Hybrid Additive in Carbonic Ester Electrolytes for SEI Modification on Li Metal Anode, Electrochem. Commun., 2015, 51, 59–63, DOI:10.1016/j.elecom.2014.12.008.
- C. Cui, C. Yang, N. Eidson, J. Chen, F. Han, L. Chen, C. Luo, P. F. Wang, X. Fan and C. Wang, A Highly Reversible, Dendrite-Free Lithium Metal Anode Enabled by a Lithium-Fluoride-Enriched Interphase, Adv. Mater., 2020, 32(12), 1906427, DOI:10.1002/ADMA.201906427.
- J. Lang, Y. Long, J. Qu, X. Luo, H. Wei, K. Huang, H. Zhang, L. Qi, Q. Zhang, Z. Li and H. Wu, One-Pot Solution Coating of High Quality LiF Layer to Stabilize Li Metal Anode, Energy Storage Mater., 2019, 16, 85–90, DOI:10.1016/J.ENSM.2018.04.024.
- Y. X. Lin, Z. Liu, K. Leung, L. Q. Chen, P. Lu and Y. Qi, Connecting the Irreversible Capacity Loss in Li-Ion Batteries with the Electronic Insulating Properties of Solid Electrolyte Interphase (SEI) Components, J. Power Sources, 2016, 309, 221–230, DOI:10.1016/j.jpowsour.2016.01.078.
- S. S. Zhang, Role of LiNO3 in Rechargeable Lithium/Sulfur Battery, Electrochim. Acta, 2012, 70, 344–348, DOI:10.1016/j.electacta.2012.03.081.
- R. Guo and B. M. Gallant, Li2O Solid Electrolyte Interphase: Probing Transport Properties at the Chemical Potential of Lithium, Chem. Mater., 2020, 32(13), 5525–5533, DOI:10.1021/acs.chemmater.0c00333.
- M. Wu, Z. Wen, Y. Liu, X. Wang and L. Huang, Electrochemical Behaviors of a Li3N Modified Li Metal Electrode in Secondary Lithium Batteries, J. Power Sources, 2011, 196(19), 8091–8097, DOI:10.1016/j.jpowsour.2011.05.035.
- Z. Yu, H. Wang, X. Kong, W. W. Huang, Y. Tsao, D. G. Mackanic, K. Wang, X. Wang, W. W. Huang, S. Choudhury, Y. Zheng, C. V. Amanchukwu, S. T. Hung, Y. Ma, E. G. Lomeli, J. Qin, Y. Cui and Z. Bao, Molecular Design for Electrolyte Solvents Enabling Energy-Dense and Long-Cycling Lithium Metal Batteries, Nat. Energy, 2020, 5(7), 526–533, DOI:10.1038/s41560-020-0634-5.
- A. J. Louli, A. Eldesoky, R. Weber, M. Genovese, M. Coon, J. Degooyer, Z. Deng, R. T. White, J. Lee, T. Rodgers, R. Petibon, S. Hy, S. J. H. Cheng and J. R. Dahn, Diagnosing and Correcting Anode-Free Cell Failure via Electrolyte and Morphological Analysis, Nat. Energy, 2020, 5, 693–702, DOI:10.1038/s41560-020-0668-8.
- R. Weber, M. Genovese, A. J. Louli, S. Hames, C. Martin, I. G. Hill and J. R. Dahn, Long Cycle Life and Dendrite-Free Lithium Morphology in Anode-Free Lithium Pouch Cells Enabled by a Dual-Salt Liquid Electrolyte, Nat. Energy, 2019, 4, 683–689, DOI:10.1038/s41560-019-0428-9.
- L. Wang, A. Menakath, F. Han, Y. Wang, P. Y. Zavalij, K. J. Gaskell, O. Borodin, D. Iuga, S. P. Brown, C. Wang, K. Xu and B. W. Eichhorn, Identifying the Components of the Solid–Electrolyte Interphase in Li-Ion Batteries, Nat. Chem., 2019, 11(9), 789–796, DOI:10.1038/s41557-019-0304-z.
- Z. Zeng, V. Murugesan, K. S. Han, X. Jiang, Y. Cao, L. Xiao, X. Ai, H. Yang, J. G. Zhang, M. L. Sushko and J. Liu, Non-Flammable Electrolytes with High Salt-to-Solvent Ratios for Li-Ion and Li-Metal Batteries, Nat. Energy, 2018, 3(8), 674–681, DOI:10.1038/s41560-018-0196-y.
- J. Qian, W. A. Henderson, W. Xu, P. Bhattacharya, M. Engelhard, O. Borodin and J. G. Zhang, High Rate and Stable Cycling of Lithium Metal Anode, Nat. Commun., 2015, 6(1), 1–9, DOI:10.1038/ncomms7362.
- Z. Yu, P. E. Rudnicki, Z. Zhang, Z. Huang, H. Celik, S. T. Oyakhire, Y. Chen, X. Kong, S. C. Kim, X. Xiao, H. Wang, Y. Zheng, G. A. Kamat, M. S. Kim, S. F. Bent, J. Qin, Y. Cui and Z. Bao, Rational Solvent Molecule Tuning for High-Performance Lithium Metal Battery Electrolytes, Nat. Energy, 2022, 7(1), 94–106, DOI:10.1038/s41560-021-00962-y.
- Y. Chen, Z. Yu, P. Rudnicki, H. Gong, Z. Huang, S. C. Kim, J.-C. C. Lai, X. Kong, J. Qin, Y. Cui and Z. Bao, Steric Effect Tuned Ion Solvation Enabling Stable Cycling of High-Voltage Lithium Metal Battery, J. Am. Chem. Soc., 2021, 143(44), 18703–18713, DOI:10.1021/jacs.1c09006.
- S. C. Kim, S. T. Oyakhire, C. Athanitis, J. Wang, Z. Zhang, W. Zhang, D. T. Boyle, M. S. Kim, Z. Yu, X. Gao, T. Sogade, E. Wu, J. Qin, Z. Bao, S. F. Bent and Y. Cui, Data-Driven Electrolyte Design for Lithium Metal Anodes, Proc. Natl. Acad. Sci. U. S. A., 2023, 120(10), e2214357120, DOI:10.1073/pnas.2214357120.
- X. Ren, L. Zou, X. Cao, M. H. Engelhard, W. Liu, S. D. Burton, H. Lee, C. Niu, B. E. Matthews, Z. Zhu, C. Wang, B. W. Arey, J. Xiao, J. Liu, J. G. Zhang and W. Xu, Enabling High-Voltage Lithium-Metal Batteries under Practical Conditions, Joule, 2019, 3(7), 1662–1676, DOI:10.1016/j.joule.2019.05.006.
- S. Chen, J. Zheng, D. Mei, K. S. Han, M. H. Engelhard, W. Zhao, W. Xu, J. Liu, J.-G. G. Zhang, S. Chen, J. Zheng, W. Zhao, W. Xu, J. Liu, J.-G. G. Zhang, D. Mei, K. S. Han and M. H. Engelhard, High-Voltage Lithium-Metal Batteries Enabled by Localized High-Concentration Electrolytes, Adv. Mater., 2018, 30(21), 1706102, DOI:10.1002/adma.201706102.
- S. T. Oyakhire, H. Gong, Y. Cui, Z. Bao and S. F. Bent, An X-Ray Photoelectron Spectroscopy Primer for Solid Electrolyte Interphase Characterization in Lithium Metal Anodes, ACS Energy Lett., 2022, 7(8), 2540–2546, DOI:10.1021/acsenergylett.2c01227.
- S. T. Oyakhire, W. Zhang, Z. Yu, S. E. Holmes, P. Sayavong, S. C. Kim, D. T. Boyle, M. S. Kim, Z. Zhang, Y. Cui and S. F. Bent, Correlating the Formation Protocols of Solid Electrolyte Interphases with Practical Performance Metrics in Lithium Metal Batteries, ACS Energy Lett., 2023, 8(1), 869–877, DOI:10.1021/acsenergylett.2c02137.
- S. Chen, J. Zheng, L. Yu, X. Ren, M. H. Engelhard, C. Niu, H. Lee, W. Xu, J. Xiao, J. Liu and J. G. Zhang, High-Efficiency Lithium Metal Batteries with Fire-Retardant Electrolytes, Joule, 2018, 2(8), 1548–1558, DOI:10.1016/J.JOULE.2018.05.002.
- H. Liu, J. Holoubek, H. Zhou, A. Chen, N. Chang, Z. Wu, S. Yu, Q. Yan, X. Xing, Y. Li, T. A. Pascal and P. Liu, Ultrahigh Coulombic Efficiency Electrolyte Enables Li||SPAN Batteries with Superior Cycling Performance, Mater. Today, 2021, 42, 17–28, DOI:10.1016/j.mattod.2020.09.035.
- B. D. Adams, J. Zheng, X. Ren, W. Xu and J.-G. G. Zhang, Accurate Determination of Coulombic Efficiency for Lithium Metal Anodes and Lithium Metal Batteries, Adv. Energy Mater., 2018, 8(7), 1702097, DOI:10.1002/aenm.201702097.
-
Q. Zhang, P. Lu, Z. Liu, M. W. Verbrugge, X. Xiao, J. Pan, Y. T. Cheng, B. W. Sheldon and Y. Qi, Synergetic Effects of Inorganic Components in Solid Electrolyte Interphase on High Cycle Efficiency of Lithium Ion Batteries, in Battery Congress, American Chemical Society, 2016, vol. 16, pp. 2011–2016. DOI:10.1149/ma2016-03/2/192.
- Z. Zhang, Y. Li, R. Xu, W. Zhou, Y. Li, S. T. Oyakhire, Y. Wu, J. Xu, H. Wang, Z. Yu, D. T. Boyle, W. Huang, Y. Ye, H. Chen, J. Wan, Z. Bao, W. Chiu and Y. Cui, Capturing the Swelling of Solid-Electrolyte Interphase in Lithium Metal Batteries, Science, 2022, 375(6576), 66–70, DOI:10.1126/science.abi8703.
- X. Cao, X. Ren, L. Zou, M. H. Engelhard, W. Huang, H. Wang, B. E. Matthews, H. Lee, C. Niu, B. W. Arey, Y. Cui, C. Wang, J. Xiao, J. Liu, W. Xu and J. G. Zhang, Monolithic Solid–Electrolyte Interphases Formed in Fluorinated Orthoformate-Based Electrolytes Minimize Li Depletion and Pulverization, Nat. Energy, 2019, 4(9), 796–805, DOI:10.1038/s41560-019-0464-5.
-
T. Li, X. Z. Yuan, L. Zhang, D. Song, K. Shi and C. Bock, Degradation Mechanisms and Mitigation Strategies of Nickel-Rich NMC-Based Lithium-Ion Batteries, Springer, Singapore, 2020, vol. 3. DOI:10.1007/s41918-019-00053-3.
- D. Aurbach, B. D. McCloskey, L. F. Nazar and P. G. Bruce, Advances in Understanding Mechanisms Underpinning Lithium-Air Batteries, Nat. Energy, 2016, 1(9), 1–11, DOI:10.1038/nenergy.2016.128.
- M. Zhao, B. Q. Li, X. Q. Zhang, J. Q. Huang and Q. Zhang, A Perspective toward Practical Lithium–Sulfur Batteries, ACS Cent. Sci., 2020, 6(7), 1095–1104, DOI:10.1021/acscentsci.0c00449.
- Z. Yu, Y. Cui and Z. Bao, Design Principles of Artificial Solid Electrolyte Interphases for Lithium-Metal Anodes, Cell Rep. Phys. Sci., 2020, 1, 100119, DOI:10.1016/j.xcrp.2020.100119.
- R. Xu, X. B. Cheng, C. Yan, X. Q. Zhang, Y. Xiao, C. Z. Zhao, J. Q. Huang and Q. Zhang, Artificial Interphases for Highly Stable Lithium Metal Anode, Matter, 2019, 1(2), 317–344, DOI:10.1016/J.MATT.2019.05.016.
- D. Kang, M. Xiao and J. P. Lemmon, Artificial Solid-Electrolyte Interphase for Lithium Metal Batteries, Batter. Supercaps, 2021, 4(3), 445–455, DOI:10.1002/BATT.202000225.
- E. Kazyak, K. N. Wood and N. P. Dasgupta, Improved Cycle Life and Stability of Lithium Metal Anodes through Ultrathin Atomic Layer Deposition Surface Treatments, Chem. Mater., 2015, 27(18), 6457–6462, DOI:10.1021/acs.chemmater.5b02789.
- L. Chen, J. G. Connell, A. Nie, Z. Huang, K. R. Zavadil, K. C. Klavetter, Y. Yuan, S. Sharifi-Asl, R. Shahbazian-Yassar, J. A. Libera, A. U. Mane and J. W. Elam, Lithium Metal Protected by Atomic Layer Deposition Metal Oxide for High Performance Anodes, J. Mater. Chem. A, 2017, 5(24), 12297–12309, 10.1039/C7TA03116E.
- X. Wu, S. Cui, M. Fei, S. Liu, X. Gao and G. Li, Inverse-Opal Structured TiO2 Regulating Electrodeposition Behavior to Enable Stable Lithium Metal Electrodes, Green Energy Environ., 2022, 8(6), 1664–1672, DOI:10.1016/J.GEE.2022.03.010.
- M. Wang, X. Cheng, T. Cao, J. Niu, R. Wu, X. Liu and Y. Zhang, Constructing Ultrathin TiO2 Protection Layers via Atomic Layer Deposition for Stable Lithium Metal Anode Cycling, J. Alloys Compd., 2021, 865, 158748, DOI:10.1016/j.jallcom.2021.158748.
- M. Bai, K. Xie, B. Hong, K. Yuan, Z. Li, Z. Huang, C. Shen and Y. Lai, An Artificial Li3PO4 Solid Electrolyte Interphase Layer to Achieve Petal-Shaped Deposition of Lithium, Solid State Ionics, 2019, 333, 101–104, DOI:10.1016/j.ssi.2019.01.016.
- H. Wang, L. Wu, B. Xue, F. Wang, Z. Luo, X. Zhang, L. Calvez, P. Fan and B. Fan, Improving Cycling Stability of the Lithium Anode by a Spin-Coated High-Purity Li3PS4Artificial SEI Layer, ACS Appl. Mater. Interfaces, 2022, 14(13), 15214–15224, DOI:10.1021/acsami.1c25224.
- Y. Y. Li, Y. Sun, A. Pei, K. Chen, A. Vailionis, Y. Y. Li, G. Zheng, J. Sun and Y. Cui, Robust Pinhole-Free Li3N Solid Electrolyte Grown from Molten Lithium, ACS Cent. Sci., 2018, 4(1), 97–104, DOI:10.1021/acscentsci.7b00480.
- J. Lopez, A. Pei, J. Y. Oh, G.-J. J. N. Wang, Y. Cui and Z. Bao, Effects of Polymer Coatings on Electrodeposited Lithium Metal, J. Am. Chem. Soc., 2018, 140(37), 11735–11744, DOI:10.1021/jacs.8b06047.
- G. Wang, C. Chen, Y. Chen, X. Kang, C. Yang, F. Wang, Y. Liu and X. Xiong, Self-Stabilized and Strongly Adhesive Supramolecular Polymer Protective Layer Enables Ultrahigh-Rate and Large-Capacity Lithium-Metal Anode, Angew. Chem., Int. Ed., 2020, 59(5), 2055–2060, DOI:10.1002/anie.201913351.
- N.-W. Li, Y. Shi, Y.-X. Yin, X.-X. Zeng, J.-Y. Li, C.-J. Li, L.-J. Wan, R. Wen and Y.-G. Guo, A Flexible Solid Electrolyte Interphase Layer for Long-Life Lithium Metal Anodes, Angew. Chemie, 2018, 130(6), 1521–1525, DOI:10.1002/ange.201710806.
- S. Guo, N. Piao, L. Wang, H. Xu, G. Tian, J. Li and X. He, PVDF-HFP/LiF Composite Interfacial Film to Enhance the Stability of Li-Metal Anodes, ACS Appl. Energy Mater., 2020, 3(7), 7191–7199, DOI:10.1021/acsaem.0c01232.
- J. Luo, C. C. Fang and N. L. Wu, High Polarity Poly(Vinylidene Difluoride) Thin Coating for Dendrite-Free and High-Performance Lithium Metal Anodes, Adv. Energy Mater., 2018, 8(2), 1701482, DOI:10.1002/aenm.201701482.
- Y. Sun, Y. Zhao, J. Wang, J. Liang, C. Wang, Q. Sun, X. Lin, K. R. Adair, J. Luo, D. Wang, R. Li, M. Cai, T. T.-K. K. Sham, X. Sun, Y. Sun, Y. Zhao, J. Liang, C. Wang, Q. Sun, X. Lin, K. R. Adair, J. Luo, D. Wang, R. Li, X. Sun, J. Wang, T. T.-K. K. Sham and M. Cai, A Novel Organic “Polyurea” Thin Film for Ultralong-Life Lithium-Metal Anodes via Molecular-Layer Deposition, Adv. Mater., 2019, 31(4), 1–9, DOI:10.1002/adma.201806541.
- B. Zhu, Y. Jin, X. Hu, Q. Zheng, S. Zhang, Q. Wang and J. Zhu, Poly(Dimethylsiloxane) Thin Film as a Stable Interfacial Layer for High-Performance Lithium-Metal Battery Anodes, Adv. Mater., 2017, 29(2), 1603755, DOI:10.1002/adma.201603755.
- Z. Huang, J. C. Lai, S. L. Liao, Z. Yu, Y. Chen, W. Yu, H. Gong, X. Gao, Y. Yang, J. Qin, Y. Cui and Z. Bao, A Salt-Philic, Solvent-Phobic Interfacial Coating Design for Lithium Metal Electrodes, Nat. Energy, 2023, 8, 577–585, DOI:10.1038/s41560-023-01252-5.
- Z. Huang, S. Choudhury, H. Gong, Y. Cui and Z. Bao, A Cation-Tethered Flowable Polymeric Interface for Enabling Stable Deposition of Metallic Lithium, J. Am. Chem. Soc., 2020, 142(51), 21393–21403, DOI:10.1021/jacs.0c09649.
- Y. Zhao, M. Amirmaleki, Q. Sun, C. Zhao, A. Codirenzi, L. V. Goncharova, C. Wang, K. Adair, X. Li, X. Yang, F. Zhao, R. Li, T. Filleter, M. Cai and X. Sun, Natural SEI-Inspired Dual-Protective Layers via Atomic/Molecular Layer Deposition for Long-Life Metallic Lithium Anode, Matter, 2019, 1, 1215–1231 CrossRef.
- Y. Liu, D. Lin, P. Y. Yuen, K. Liu, J. Xie, R. H. Dauskardt, Y. Cui, P. Yan Yuen, K. Liu, J. Xie, R. H. Dauskardt, Y. Cui, Y. Liu, D. Lin, K. Liu, J. Xie, R. H. Dauskardt, Y. Cui, P. Y. Yuen, K. Liu, J. Xie, R. H. Dauskardt and Y. Cui, An Artificial Solid Electrolyte Interphase with High Li-Ion Conductivity, Mechanical Strength, and Flexibility for Stable Lithium Metal Anodes, Adv. Mater., 2017, 29(10), 1605531, DOI:10.1002/adma.201605531.
- Q. Pang, L. Zhou and L. F. Nazar, Elastic and Li-Ion–Percolating Hybrid Membrane Stabilizes Li Metal Plating, Proc. Natl. Acad. Sci. U. S. A., 2018, 115(49), 12389–12394, DOI:10.1073/pnas.1809187115.
- Z. Yu, D. G. Mackanic, W. Michaels, M. Lee, A. Pei, D. Feng, Q. Zhang, Y. Tsao, C. V. Amanchukwu, X. Yan, H. Wang, S. Chen, K. Liu, J. Kang, J. Qin, Y. Cui and Z. Bao, A Dynamic, Electrolyte-Blocking, and Single-Ion-Conductive Network for Stable Lithium-Metal Anodes, Joule, 2019, 3(11), 2761–2776, DOI:10.1016/J.JOULE.2019.07.025.
- L. Qin, K. Wang, Y. Wu, S. Sun, X. Yang, P. Jiang, M. Wu and W. Wu, Residual Stress-Tailored Lithium Deposition and Dissolution Behaviors for Safe Lithium Metal Anode, J. Alloys Compd., 2022, 927, 166776, DOI:10.1016/J.JALLCOM.2022.166776.
- C. Pfaffenhuber, M. Göbel, J. Popovic and J. Maier, Soggy-Sand Electrolytes: Status and Perspectives, Phys. Chem. Chem. Phys., 2013, 9, 18318–18335, 10.1039/c3cp53124d.
- S. K. Das and A. J. Bhattacharyya, Oxide Particle Surface Chemistry and Ion Transport in “Soggy Sand” Electrolytes, J. Phys. Chem. C, 2009, 113(16), 6699–6705, DOI:10.1021/jp810761e.
- M. S. Kim, Z. Zhang, J. Wang, S. T. Oyakhire, S. C. Kim, Z. Yu, Y. Chen, D. T. Boyle, Y. Ye, Z. Huang, W. Zhang, R. Xu, P. Sayavong, S. F. Bent, J. Qin, Z. Bao and Y. Cui, Revealing the Multifunctions of Li3N in the Suspension Electrolyte for Lithium Metal Batteries, ACS Nano, 2023, 17(3), 3168–3180, DOI:10.1021/acsnano.2c12470.
- M. S. Kim, Z. Zhang, Z. Zhang, P. E. Rudnicki, Z. Yu, J. Wang, H. Wang, S. T. Oyakhire, Y. Chen, S. C. Kim, W. Zhang, D. T. Boyle, X. Kong, R. Xu, Z. Huang, W. Huang, S. F. Bent, L.-W. Wang, J. Qin, Z. Bao and Y. Cui, Suspension Electrolyte with Modified Li+ Solvation Environment for Lithium Metal Batteries, Nat. Mater., 2022, 21, 445–454, DOI:10.1038/s41563-021-01172-3.
- P. Sayavong, W. Zhang, S. T. Oyakhire, D. T. Boyle, Y. Chen, S. C. Kim, R. A. Vilá, S. E. Holmes, M. S. Kim, S. F. Bent, Z. Bao and Y. Cui, Dissolution of the Solid Electrolyte Interphase and Its Effects on Lithium Metal Anode Cyclability, J. Am. Chem. Soc., 2023, 145, 12342–12350, DOI:10.1021/jacs.3c03195.
- Q. A. Huang, Y. Shen, Y. Huang, L. Zhang and J. Zhang, Impedance Characteristics and Diagnoses of Automotive Lithium-Ion Batteries at 7.5% to 93.0% State of Charge, Electrochim. Acta, 2016, 219, 751–765, DOI:10.1016/j.electacta.2016.09.154.
- C. F. Chen, A. Mistry and P. P. Mukherjee, Probing Impedance and Microstructure Evolution in Lithium-Sulfur Battery Electrodes, J. Phys. Chem. C, 2017, 121(39), 21206–21216, DOI:10.1021/acs.jpcc.7b07245.
- P. Bai, J. Li, F. R. Brushett and M. Z. Bazant, Transition of Lithium Growth Mechanisms in Liquid Electrolytes, Energy Environ. Sci., 2016, 9(10), 3221–3229, 10.1039/c6ee01674j.
- S. T. Oyakhire, S. L. Liao, S. B. Shuchi, M. S. Kim, S. C. Kim, Z. Yu, R. A. Vilá, P. E. Rudnicki, Y. Cui and S. F. Bent, Proximity Matters: Interfacial Solvation Dictates Solid Electrolyte Interphase Composition, Nano Lett., 2023, 23(16), 7524–7531, DOI:10.1021/acs.nanolett.3c02037.
- D. Li, H. Hu, B. Chen and W. Y. Lai, Advanced Current Collector Materials for High-Performance Lithium Metal Anodes, Small, 2022, 18(24), 2200010, DOI:10.1002/SMLL.202200010.
- B. Zhou, A. Bonakdarpour, I. Stoševski, B. Fang and D. P. Wilkinson, Modification of Cu Current Collectors for Lithium Metal Batteries – A Review, Progress Mater. Sci., 2022, 1, 100996, DOI:10.1016/j.pmatsci.2022.100996.
- A. Pei, G. Zheng, F. Shi, Y. Li and Y. Cui, Nanoscale Nucleation and Growth of Electrodeposited Lithium Metal, Nano Lett., 2017, 17(2), 1132–1139, DOI:10.1021/acs.nanolett.6b04755.
- J. Xiao, How Lithium Dendrites Form in Liquid Batteries: Studies of Interfacial Reactions and Mass Transport May Allow Safe Use of Lithium Metal Anodes, Science, 2019, 426–427, DOI:10.1126/science.aay8672 . American Association for the Advancement of Science October 25.
- Y. Shi, Z. Wang, H. Gao, J. Niu, W. Ma, J. Qin, Z. Peng and Z. Zhang, A Self-Supported, Three-Dimensional Porous Copper Film as a Current Collector for Advanced Lithium Metal Batteries, J. Mater. Chem. A, 2019, 7(3), 1092–1098, 10.1039/c8ta09384a.
- D. Zhang, A. Dai, M. Wu, K. Shen, T. Xiao, G. Hou, J. Lu and Y. Tang, Lithiophilic 3D Porous CuZn Current Collector for Stable Lithium Metal Batteries, ACS Energy Lett., 2020, 5(1), 180–186, DOI:10.1021/acsenergylett.9b01987.
- W. Zhang, H. Jin, C. Xu, S. Zhao, Y. Du and J. Zhang, Diffusion Couples Cu–X (X = Sn, Zn, Al) Derived 3D Porous Current Collector for Dendrite-Free Lithium Metal Battery, J. Power Sources, 2019, 440, 227142, DOI:10.1016/j.jpowsour.2019.227142.
- B. N. Choi, J. Y. Seo, B. Kim, Y. S. Kim and C. H. Chung, Electro-Deposition of the Lithium Metal Anode on Dendritic Copper Current Collectors for Lithium Battery Application, Appl. Surf. Sci., 2020, 506, 144884, DOI:10.1016/j.apsusc.2019.144884.
- Y. X. Song, W. Y. Lu, Y. J. Chen, H. Yang, C. Wu, W. F. Wei, L. B. Chen and X. P. Ouyang, Coating Highly Lithiophilic Zn on Cu Foil for High-Performance Lithium Metal Batteries, Rare Met., 2022, 41(4), 1255–1264, DOI:10.1007/s12598-021-01811-3.
- Z. Ni, D. Yang, Y. Wang, W. Yang, B. Deng, J. Hou, Y. Zhang, X. Li and Y. Zhang, The Effect of Alloy Type of Lithophilic Cu–Sn Interface Layer on the Deposition/Stripping Behavior of Lithium Metal Anode, J. Alloys Compd., 2022, 906, 164307, DOI:10.1016/j.jallcom.2022.164307.
- K. Yan, Z. Lu, H. W. Lee, F. Xiong, P. C. Hsu, Y. Li, J. Zhao, S. Chu and Y. Cui, Selective Deposition and Stable Encapsulation of Lithium through Heterogeneous Seeded Growth, Nat. Energy, 2016, 1(3), 1–8, DOI:10.1038/NENERGY.2016.10.
- H. Wang, P. Hu, X. Liu, Y. Shen, L. Yuan, Z. Li and Y. Huang, Sowing Silver Seeds within Patterned Ditches for Dendrite-Free Lithium Metal Batteries, Adv. Sci., 2021, 8, 2100684, DOI:10.1002/advs.202100684.
- Y. Jiang, B. Wang, A. Liu, R. Song, C. Bao, Y. Ning, F. Wang, T. Ruan, D. Wang and Y. Zhou, In Situ Growth of CuO Submicro-Sheets on Optimized Cu Foam to Induce Uniform Li Deposition and Stripping for Stable Li Metal Batteries, Electrochim. Acta, 2020, 339, 135941, DOI:10.1016/j.electacta.2020.135941.
- C. Zhang, W. Lv, G. Zhou, Z. Huang, Y. Zhang, R. Lyu, H. Wu, Q. Yun, F. Kang and Q. H. Yang, Vertically Aligned Lithiophilic CuO Nanosheets on a Cu Collector to Stabilize Lithium Deposition for Lithium Metal Batteries, Adv. Energy Mater., 2018, 8(21), 1703404, DOI:10.1002/aenm.201703404.
- S. T. Oyakhire, W. Huang, H. Wang, D. T. Boyle, J. R. Schneider, C. de Paula, Y. Wu, Y. Cui and S. F. Bent, Revealing and Elucidating ALD-Derived Control of Lithium Plating Microstructure, Adv. Energy Mater., 2020, 10(44), 2002736, DOI:10.1002/aenm.202002736.
- S. T. Oyakhire, W. Zhang, A. Shin, R. Xu, D. T. Boyle, Z. Yu, Y. Ye, Y. Yang, J. A. Raiford, W. Huang, J. R. Schneider, Y. Cui and S. F. Bent, Electrical Resistance of the Current Collector Controls Lithium Morphology, Nat. Commun., 2022, 13(1), 1–12, DOI:10.1038/s41467-022-31507-w.
- Y. J. Kim, S. H. Kwon, H. Noh, S. Yuk, H. Lee, H. S. Jin, J. Lee, J. G. Zhang, S. G. Lee, H. Guim and H. T. Kim, Facet Selectivity of Cu Current Collector for Li Electrodeposition, Energy Storage Mater., 2019, 19, 154–162, DOI:10.1016/j.ensm.2019.02.011.
- S. T. Liu, H. Y. Ku, C. L. Huang and C. C. Hu, Improvements in Li Deposition and Stripping Induced by Cu (111) Nanotwinned Columnar Grains, Electrochim. Acta, 2022, 430, 141011, DOI:10.1016/j.electacta.2022.141011.
- K. Ishikawa, S. Harada, M. Tagawa and T. Ujihara, Effect of Crystal Orientation of Cu Current Collectors on Cycling Stability of Li Metal Anodes, ACS Appl. Mater. Interfaces, 2020, 12(8), 9341–9346, DOI:10.1021/acsami.9b22157.
- C. Fang, J. Li, M. Zhang, Y. Zhang, F. Yang, J. Z. Lee, M. H. Lee, J. Alvarado, M. A. Schroeder, Y. Yang, B. Lu, N. Williams, M. Ceja, L. Yang, M. Cai, J. Gu, K. Xu, X. Wang and Y. S. Meng, Quantifying Inactive Lithium in Lithium Metal Batteries, Nature, 2019, 572(7770), 511–515, DOI:10.1038/s41586-019-1481-z.
- D. T. Boyle, W. Huang, H. Wang, Y. Li, H. Chen, Z. Yu, W. Zhang, Z. Bao and Y. Cui, Corrosion of Lithium Metal Anodes during Calendar Ageing and Its Microscopic Origins, Nat. Energy, 2021, 6(5), 487–494, DOI:10.1038/s41560-021-00787-9.
|
This journal is © The Royal Society of Chemistry 2024 |