Designing polyurethane-based microcapsules with tailored swelling behaviours for enhanced oil recovery†
Received
29th August 2023
, Accepted 2nd November 2023
First published on 2nd November 2023
Abstract
Polyurethane (PU) materials have been widely used for developing microcapsules due to their excellent polymerization, encapsulation, and controlled release properties. These unique properties endow PU-based microcapsules with desired functions for enhanced oil recovery (EOR). However, there are some special requirements for PU-based microcapsules in their application of the EOR process, such as they are expected to exhibit good stability at room temperature but thermo-responsive swelling-release properties in the oil reservoir. To enhance the functionality of PU-based microcapsules for EOR, after validating the swelling-release behaviors of PU-based microcapsules, we employed all-atom molecular dynamics (MD) simulations to study the effects of molecular structure of PU-based polymers on thermo-responsivity of microcapsules. The simulation results demonstrate that the diisocyanate segments have significant influence on swelling behaviors of PUs. The different diisocyanate segments, including isophorone diisocyanate (IPDI), toluene diisocyanate (TDI), 4,4′-diphenylmethane diisocyanate (MDI), and hexamethylene diisocyanate (HDI), have different impacts on the flexibility of the polymer, which further influence the network structure of the polymer matrix. The different swelling behaviors of PU-based polymers were further analyzed from energetic and kinetic perspectives, and it is demonstrated that TDI–PU can combine stability and thermo-responsivity together. In addition, the introduction of anionic functional groups can further facilitate the swelling process. The findings in this study serve as a foundation for future studies toward the development of polymer flooding technology and provide valuable molecular insights into the swelling mechanism of PU-based polymers.
Design, System, Application
Polyurethane (PU) materials have gained widespread utilization in microcapsule development due to their distinctive properties. Nevertheless, when PU-based microcapsules are applied in enhanced oil recovery (EOR) processes, achieving tailored thermo-responsive swelling-release behaviours becomes imperative. To enhance the efficacy of PU-based microcapsules for EOR applications, it is highly desirable to understand the relationship between molecular structure and swelling behaviours of PU-based molecules. In view of this, we designed PU-based polymers with different diisocyanate monomers, and studied the influence of molecular structures on the thermo-responsive characteristics of the PU-based microcapsules at different temperatures. By delving into the energetic and kinetic properties of these PU-based polymers, the roles of different segments in swelling behaviours are systematically elucidated. This study not only serves as a foundation for future studies toward the enhancement of EOR efficiency, but also highlights the importance of molecular design in tailoring PU-based microcapsules for specific applications.
|
1. Introduction
Polymer flooding has gained significant attention in recent years as a widely employed technique for enhanced oil recovery (EOR).1 The high viscosity and molecular weight of polymers can enhance the viscosity of the aqueous phase, thereby reducing the emulsification between water and oil, resulting in a significant improvement in displacement efficiency and a decrease in residual oil saturation.2 Partially hydrolyzed polyacrylamide (HPAM) is a commonly used material for polymer flooding in the context of enhanced oil recovery. It demonstrates excellent performance in improving oil displacement efficiency.3 However, HPAM is susceptible to degradation in the EOR process. The extreme conditions of the reservoir, such as high temperature and high salinity, can result in viscosity loss and subsequent failure of polymer flooding.4 To address these challenges effectively, various derivatives of polyacrylamide have been explored,5–7 These derivatives aim to enhance viscosity, improve shear resistance, and enhance temperature/salt tolerance. But due to the intrinsic properties of HPAM, the achieved performance improvements are limited. In addition to molecular modification, microcapsule technology has also been increasingly utilized,8 and polyurethane (PU) is one of the most used materials for encapsulating HPAM. By taking advantage of PU, microcapsules are able to protect HPAM during the injection process. Thus, in practical application, PU-based microcapsules are expected to exhibit stability at room temperature for storage and transportation, while gradually releasing HPAM at elevated temperatures to achieve controlled release and viscosity enhancement.9–11 However, their sustained-release performance has yet to be improved. In order to further optimize the practicality of microcapsule-based polymer flooding technology, the key is to conduct delicate molecular design of a PU-based microcapsule shell.12,13
To enhance the performance of PU-based polymers as microcapsule shells, researchers in different areas have devoted themselves to designing and optimizing the molecular structures of PU-based polymers. For instance, Wang et al. prepared monosultap-polyurethane microcapsules by adopting interfacial polymerization. They demonstrated that the obtained microcapsules exhibit superior thermal stability. Besides the good thermal stability and encapsulation efficiency (81.9%), these microcapsules also displayed sustained-release properties in various pH environments. The incorporation of isophorone diisocyanate (IPDI) and pentaerythritol in the synthesis of PU microcapsules, which encased water-soluble core materials, has expanded the potential applications of PU microcapsules.14 Bai et al. prepared thermo-expandable microcapsules by using PU as the shell material and n-hexane as the foaming agent. Their research focused on optimizing the encapsulation efficiency by varying the NCO/OH ratio, revealing that a ratio of 3 yielded the highest efficiency. Additionally, the introduction of diethylenetriamine (DMPA) as a polyamine chain extender can lead to a remarkable enhancement in the synthesis efficiency of the PU shell.15 In addition, researchers have synthesized IPDI, toluene diisocyanate (TDI), and 4,4′-diphenylmethane diisocyanate (MDI) with different diamines or diols, and it was found that the combination of IPDI with triethylenetetramine exhibited the best performance in encapsulating ionic liquids.16 Alizadegan et al. synthesized bulky-IPDI-filled PU microcapsules using a TDI-based pre-polymer to investigate the effect of various nanoclay contents on the self-healing behavior of three different defect types (intact, scratched, and healed). They concluded the optimal ratio.17 Previous studies have richly validated that, when PUs are used as the shell of microcapsules, the practicality of microcapsules is closely related to the molecular structure of PUs. Hence, the molecular design of PUs is of significance for development of PU-based microcapsules.
Considering the versatility of PU microcapsules, they have been widely used in various fields such as biology and drug delivery.18,19 Besides that, PU microcapsules have gained gradual attention in the petroleum industry in recent years. For instance, by using IPDI and polyethylene glycol (PEG) as reaction monomers, Gong et al. employed emulsion reversed-phase polymerization to synthesize PU-shell microcapsules for enhancing polymer flooding. Through screening various shell-to-core ratios, it was observed that microcapsules with a shell-to-core ratio of 0.25 exhibited superior performance. These microcapsules demonstrated a more uniform particle size distribution (297.8–531.8 nm), a more spherical morphology, and a high thermal degradation temperature of up to 221.6 °C. These characteristics contributed to the PU microcapsules' excellent encapsulation efficiency and stability.20 To understand the temperature-induced release process, they adopted atomic force microscopy, and demonstrated that the shells undergo three distinct stages: shell hydration, shell swelling, and shell rupture. Experimentally, it is well-established that water permeation plays a pivotal role in the swelling and release process of microcapsules. In order to further enhance the performance of the microcapsule-based EOR process (Fig. 1a), it is necessary to gain deeper insights into the interactions of polymer–water and polymer–polymer.
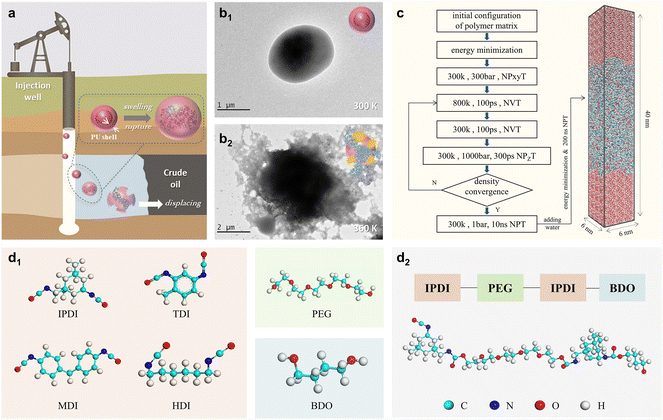 |
| Fig. 1 (a) Illustration of the microcapsule-based EOR process. TEM images of PU microcapsules at (b1) 300 K and (b2) 360 K. (c) Flowchart of simulation procedures. (d1) Molecular structures of four diisocyanate monomers and other blocks for constructing PU-based polymers. (d2) Molecular structure of the block polymer (taking IPDI–PU as an example). | |
With the development of computational methods, molecular dynamics (MD) simulations have emerged as a powerful tool for investigating the microscopic mechanisms of polymer-based materials.21 For example, researchers conducted MD simulations for clarifying the mechanical and interfacial properties of microencapsulated-based self-healing composites under uniaxial stretching.22 In addition, by means of MD simulations, the osmotic pressure and swelling behaviour of ionic microcapsules have been elucidated.23 It is worth pointing out that, besides MD simulations, some mesoscale simulation methods (such as Monte Carlo and dissipative particle dynamics) also provide valuable insights into the swelling behaviours of the polymer matrix. For instance, Song et al. demonstrated that spatial heterogeneity and changes in the swelling state not only alter the swelling modes but also have a significant impact on interfacial properties.24 With the deepening of simulation studies, the influence of temperature on the microscopical properties of the polymer matrix has also been investigated.25–27 However, simulation studies on temperature-responsive slow release mechanisms of PU-based microcapsules are sparse, and further research on this topic is of importance to the application of PU-based microcapsules in EOR.
In this work, the swelling behaviours of PU-based microcapsules were studied by combining all-atom MD simulations and experiments. Firstly, transmission electron microscopy (TEM) was adopted to observe the swelling and rupture of PU microcapsules. It is demonstrated that PU microcapsules possess good stability at room temperature, and underwent swelling and rupture at high temperatures. Furthermore, by employing MD simulations, the effect of polymer structure on the swelling behaviour of the microcapsule shell was systematically studied. The structural and energetic analyses demonstrate that the diisocyanate segments of the PU-based polymer have significant impact on the flexibility of the polymer, as well as the interaction strength between water and polymer. Meanwhile, the introduction of anionic functional groups can further facilitate the water permeation and swelling process. This work is expected to provide valuable insights for future optimization of thermo-responsive PU-based microcapsules.
2. Methodology
2.1 Experimental observation of microcapsules
In order to investigate the temperature-controlled swelling and rupture of PU microcapsules, we prepared PU microcapsules based on IPDI–PU. The synthesis methods were reported in a previous study.20 The aging period is 48 hours. TEM (HT-7700, Hitachi) was adopted to observe the morphologies of microcapsules. The samples were placed on microgrids and tested after infrared drying, with an exposure time of 500 ms.
2.2 Molecular structures and procedures of MD simulations
The various molecular structures of PU are constructed by combining four different diisocyanates, PEG, and a chain extender 1,4-butanediol (BDO), as shown in Fig. 1d1. Taking IPDI–PU as an example, the polymer structure is reported in Fig. 1d2. To obtain the reasonable conformation of the polymer matrix, 100 PU polymers were randomly put into a cubic simulation box by using Packmol.28 After energy optimization, a seven-step compression relaxation method was employed, and this method was proposed and validated by Jiang et al.29,30 After 15 rounds of compression–relaxation, all the systems reach reasonable density (Fig. S1†), and the PUs are in the melt state (Fig. S2†). In each system, the polymer matrix (6 nm × 6 nm × 20 nm) was selected to construct the polymer–water interaction model. After obtaining the interaction model (6 nm × 6 nm × 40 nm), energy minimization and 200 ns NPT simulation were conducted at different temperatures (300 K, 353 K, and 433 K). The root mean square deviation (RMSD) (Fig. S3†) and mean squared displacement (MSD) (Fig. S4†) profiles of PUs demonstrate that the systems reach equilibrium state after 200 ns of simulation. The density profiles of water molecules demonstrate that the water molecules are uniformly dispersed in the polymer matrix at equilibrium state (Fig. S5a†), and the membrane–water interface was determined for the following statistical analysis. Besides that, it is found that the adsorption peak of water molecules on the polymer is at approximately 2 Å (Fig. S5b†). In all simulations, the three-dimensional periodic boundary condition with a truncation radius of 1.2 nm was applied. Restrained electrostatic potential (RESP) charges were calculated and assigned to atoms for MD simulations. Optimization of molecules was performed using the Gaussian 09 program at the level of B3LYP/6-31G*, and the RESP charges were calculated using the Multiwfn software.31 The SPC/E model was used for the water force field. The CHARMM force field was adopted to describe the intermolecular interactions,32 while the field list updated every 10 steps. All simulations were performed using GROMACS (version 2019.6).33 The trajectories were visualized using VMD.34
3. Results and discussion
3.1 Temperature response characteristic
To evaluate the encapsulation and swell-release properties of PU microcapsules, IPDI–PU microcapsules were prepared, and their morphologies at different temperatures were investigated by TEM. At 300 K, the microcapsule is stable and exhibits minimal release (Fig. 1b1). In contrast, the shell is swelled and ruptured at 360 K (Fig. 1b2), resulting in the release of the encapsulated material. Additionally, the microcapsule size increased from approximately 1.5 μm to 2–3 μm. The experimental results demonstrate the thermo-responsive swelling-release properties of IPDI–PU microcapsules. However, the effects of molecular structure of PU-based polymers on their swelling behaviors are less studied. Hence, we designed different PU-based polymers and examined their properties by means of MD simulations. Fig. 2 displays the representative snapshots of the four types of PU membranes at three different temperatures. The simulation results indicate that it is difficult for the water molecules at the polymer–water interface to penetrate into the polymer matrix at 300 K. As a result, the swelling behaviors of PU membranes are not observed. However, at 353 K and 433 K, the water molecules penetrate into the polymer matrix, leading to the swelling of the four types of membranes. Compared to the other types of PU membranes, there is a greater amount of water molecules entering into the HDI–PU and TDI–PU matrices, leading to more pronounced swelling (Fig. S6†), while the number of water molecules in MDI–PU is the least. Overall, it can be concluded that the membrane swelling is greatly influenced by the temperature, as well as the molecular structure of PUs. To further understand the underlying mechanisms, the swelling behaviours were further quantitatively analysed.
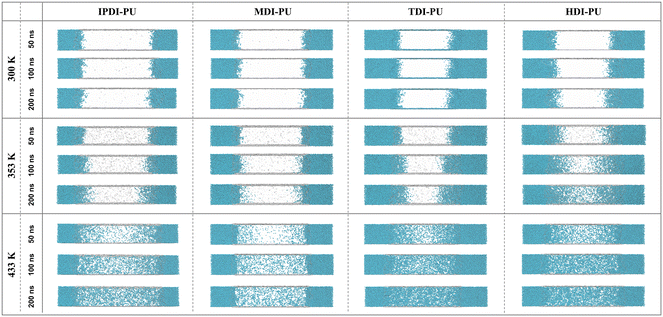 |
| Fig. 2 Simulation snapshots of four water–PU interaction systems at different temperatures (300 K, 353 K, 433 K). Color code: cyan for water molecules, transparent color for PUs. | |
3.2 Swelling behaviours of the membrane
Fig. 3a presents the swelling volume ratios of the four types of PUs at different temperatures. It can be observed that the swelling volume changes of IPDI–PU and MDI–PU are relatively weak at 353 K. At 433 K, IPDI–PU (9.7%) is slightly higher than MDI–PU (5.4%), while the swelling of TDI–PU and HDI–PU is more notable. More specifically, TDI–PU exhibits the largest change at 433 K (19.8%), whereas HDI–PU shows the greatest change at 353 K (8.34%). The dynamic swelling process of PUs at 433 K and 353 K was further analysed, as shown in Fig. 3b and S7.† The density profiles of PUs in the Z-direction demonstrate that the swelling of IPDI–PU and MDI–PU is relatively limited. In contrast, in the TDI–PU and HDI–PU systems, as the simulation progresses, the membrane density gradually decreases, and the PU membrane extends in the Z-direction. By comparing the results from 0 to 50 ns, we observed a rapidly decreasing membrane density of HDI–PU, which confirms its higher sensitivity to temperature.
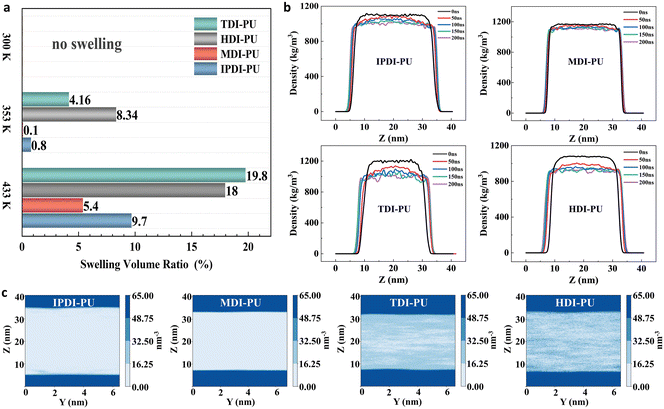 |
| Fig. 3 (a) Swelling volume ratios of the four PUs at three different temperatures. (b) Density profiles of different PUs in the Z-direction at various simulation times. (c) Two-dimensional density distributions (YZ plane) of water molecules within the PU matrix at equilibrium state. | |
The two-dimensional density distributions of water molecules demonstrate that the water molecules are uniformly dispersed within the PU matrix at equilibrium state (433 K), as shown in Fig. 3c. The uniform distribution of water molecules within the membrane once again proves that the system is in equilibrium. In addition, a distinct membrane–water interface was observed, with more water molecules located at the interface. Fig 3c illustrate that the order of water permeability in the different systems is as follows: HDI–PU > TDI–PU > IPDI–PU > MDI–PU. This result is consistent with the swelling volume ratios (Fig. 3a). The above analyses demonstrate the temperature-responsive swelling behaviours of PUs. More importantly, PUs with different molecular structures have different degrees of resistance to water permeation. The MDI–PU membrane has the strongest resistance, while HDI–PU and TDI–PU membranes have the weakest resistance. Furthermore, the swelling rate of HDI–PU is significantly superior to the other types of PUs.
3.3 Structural and energetic analysis of swelling behaviours
To better understand the differences in swelling performance among IPDI–PU, MDI–PU, TDI–PU, and HDI–PU, the swelling behaviours were further analysed from structural and energetic perspectives. Fig. 4a illustrates the conformational variation of the polymer in the swelling process. At the initial stage, the four kinds of polymer chains possess varied conformations due to their different flexibilities, but with the permeation of water molecules, all four kinds of polymer chains show a progression from aggregation to extension. Among them, MDI–PU chains are relatively extended at the initial structure, and the HDI–PU polymer possesses the most noticeable conformational variation. To quantitatively investigate the conformational variation, RMSD and MSD were calculated, as shown in Fig. S3 and S4.† The gradual stabilization of RMSD and MSD values indicates that the water has reached the diffusive regime in the bulk of the polymer after 50 ns. In addition, by analysing the RMSD of PUs at different temperatures, it is found that, due to the enhanced thermal motion, the conformational changes of the polymer chains become more pronounced with increasing temperature (Fig. S3†), and the RMSD of HDI–PU is the highest (Fig. 4b). We further calculated the mean-square radius of gyration (Rg) of PUs to probe the dynamic process of conformational variation (Fig. 4c). At 300 K, it is difficult for the water molecules to permeate into the polymer matrix, thus the Rg of PUs remains relatively stable at this situation. In the systems of 433 K, a large number of water molecules permeate into the membrane, leading to conformational variation of PUs. Meanwhile, the order of Rg value is changed due to the diverse flexibility of polymers. Obviously, the Rg gradually increases with the transition of polymer chains from aggregation to extension. Among them, HDI–PU exhibits the largest change in Rg, while MDI–PU shows the smallest change, and the conformational variation of IPDI–PU and TDI–PU is moderate. These results indicate that the flexibility of different types of PUs is a significant factor influencing water permeation and membrane swelling. The molecular structure of MDI contains two benzene ring structures, which endow MDI–PU with rigidity, and the self-aggregation of MDI–PU is therefore hindered. As a result, it is difficult for water molecules to penetrate into the rigid MDI–PU polymer membrane. In contrast, IPDI and TDI contain only one six-membered ring structure, thus the flexibility of IPDI–PU and TDI–PU is moderate. Additionally, there are few hydrogen atoms present in TDI. The relatively weak steric effect leads to the water molecules easily penetrating into TDI–PU as compared with IPDI–PU. Different with the above cases, HDI–PU exhibits enhanced flexibility due to the absence of ring structure. The alkane segment of HDI–PU endows the polymer with good flexibility, and provides a diffusion channel for water molecules. As a result, the swelling behaviours of HDI–PU are the most significant.
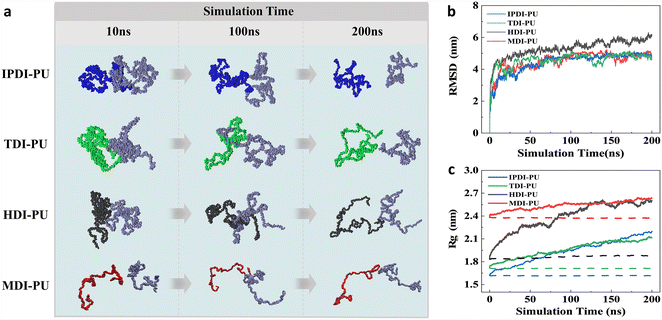 |
| Fig. 4 (a) Conformational variation of PUs during the swelling process. (b) RMSD profiles of PUs during the swelling process. (c) Rg of Pus during the swelling process, solid lines correspond to systems at 433 K, dashed lines correspond to systems at 300 K. | |
The different performance of PUs cannot only be understood from the structural perspective. Specifically, the Rg of IPDI–PU and TDI–PU is close to each other, however, as mentioned above, they are different with each other in terms of swelling behaviours. In view of this, the swelling processes were further analysed from dynamical and energetic perspectives. To evaluate the diffusivity of water molecules in different systems, the diffusion coefficient (D) of water molecules in the system was calculated based on mean squared displacements, as shown in Fig. 5a. The higher diffusion coefficients indicate stronger diffusivity of water molecules, and they easily permeate into the membrane. At different temperatures, the D of water in the HDI–PU system is the highest, followed by TDI–PU, IPDI–PU, and MDI–PU systems. The diffusion of water further influences the RMSD of Pus, as shown in Fig. S8.† MSDs of PUs are rapidly increased at the initial stage, which correspond to the penetration process of water molecules. After the water inside membrane reaches a saturated state, MSDs reach a plateau and steadily increase with simulation time. Overall, the MSD of HDI–PU is the highest. This result further demonstrates that the water molecules exhibit stronger diffusion capabilities when they are interacting with PUs with enhanced flexibility.
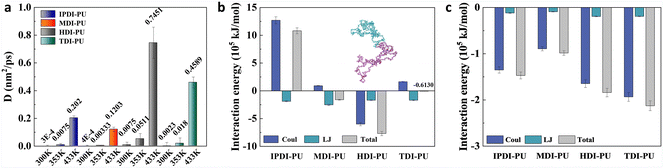 |
| Fig. 5 (a) Diffusion coefficients of water molecules at three different temperatures. (b) Interaction energies between PUs and PUs at 433 K. (c) Interaction energies between PUs and water at 433 K. | |
The interaction energies of PUs–PUs and PUs–water were calculated and reported in Fig. 5b and c. Based on the variation of density profiles of water molecules (Fig. S9†), it was determined that the water inside membrane reached a saturated state after 150 ns. Therefore, interaction energies were calculated using the last 50 ns of the simulation, and a more negative value of interaction energy indicates stronger interaction strength between components. The comparison shows that these PUs, except IPDI–PU, exhibit attractive interactions between polymers. The interaction strength between HDI–PU is the strongest, followed by MDI–PU and TDI–PU. According to previous studies,29 this difference is mainly caused by the different numbers of tetrahedral carbons and different types of hexagonal rings in the diisocyanate structure of PUs. IPDI–PU, with one cycloaliphatic ring and three tetrahedral carbons, exhibits a strong repulsion effect between polymers. In contrast, π–π interaction contributes to the interactions between TDI–PU with an aromatic ring. MDI–PU, with two benzene rings, shows stronger attraction than TDI–PU. HDI–PU with no hexagonal rings or tetrahedral carbons demonstrates the strongest polymer–polymer interaction strength due to its variable and flexible conformations.
The interaction energy between PU and water is dominated by Coulomb interaction. Among four interaction systems, TDI–PU exhibits the strongest interaction with water, followed by HDI–PU, IPDI–PU and MDI–PU. Generally, the interaction energies between PU and water correspond to the diffusivity of water molecules and the swelling behaviours of PUs. As mentioned above, MDI–PU with two benzene rings is able to form a rigid and stable structure to resist water permeation. Thus, the interaction between water and MDI–PU is limited. During the swelling process, the conformation of IPDI–PU is relatively less changed, thus the interaction strength between water and IPDI–PU is moderate. In contrast, TDI–PU and HDI–PU exhibit stronger interaction with water molecules, as TDI–PU and HDI–PU with variable molecular conformations can effectively interact with water molecules. These results indicate that the swelling behaviours of PUs should be understood from both thermodynamic and kinetic perspectives.
3.4 Influence of different segments and further optimization
To understand the effects of different segments on water permeation and membrane swelling, the role of different segments in the swelling process was further analysed. Fig. 6a1–4 illustrate the number of water molecules around each PU segment (within a 2 Å range) during a 200 ns swelling process at 433 K. The results show that, due to the presence of terminal diisocyanate blocks, these segments come into contact with water initially. As the simulation progresses, the number of water molecules steadily increases until reaching a stable state. Overall, the water adsorption capacity of PEG and BDO segments is weaker as compared to diisocyanate blocks. These results indicate that the diisocyanate blocks not only influence the flexibility of the PU chains but also affect the water adsorption capacity of PUs. Additionally, the comparison of different types of diisocyanate blocks demonstrates that they endow PUs with different water adsorption capacities. These results highlight the role of diisocyanate monomer types in regulating the water permeation and swelling properties of PUs. Fig. 6b presents the number of water molecules inside the whole membrane during simulations. The statistical result is consistent with previous analysis such as swelling volume ratios. Moreover, the numbers of hydrogen bonds of different systems during the swelling process were further examined, as shown in Fig. 6c. It is demonstrated that the polymer swelling process is accompanied by the reconfiguration of hydrogen bonding networks. With water permeation and membrane swelling, the number of hydrogen bonds between PUs gradually decreases, while the number of hydrogen bonds between PUs and water molecules steadily increases and eventually stabilizes. Among the four types of PUs, TDI–PU and HDI–PU can form a higher number of hydrogen bonds with water molecules, while IPDI–PU and MDI–PU can form fewer hydrogen bonds with water.
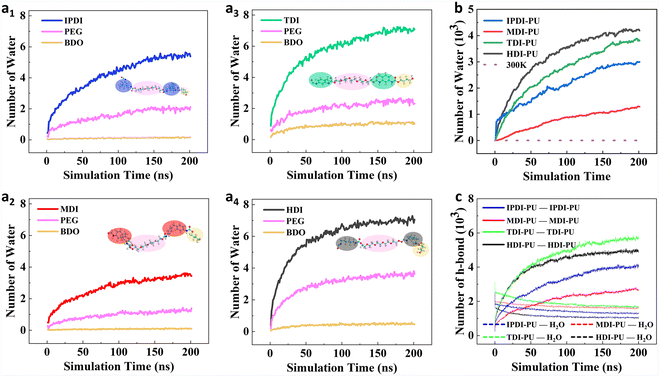 |
| Fig. 6 (a) Number of water molecules within a 2 Å radius around different segments of PUs as a function of time. Subfigure (a1) corresponds to the IPDI–PU system, (a2) to the MDI–PU system, (a3) to the TDI–PU system, and (a4) to the HDI–PU system. (b) Number of water molecules within PU membranes as a function of time at 433 K (solid lines) and at 300 K (dashed lines). (c) Number of hydrogen bonds formed between PU–PU (dashed lines) and PU–water (solid lines) at 433 K. | |
Our previous analysis highlights the effects of different diisocyanate monomers on the flexibility and water adsorption capacity of PUs. Besides the control of diisocyanate segments, how can one further manipulate the swelling behaviours of PUs? This question arouses our interest. Our previous results demonstrate that MDI–PU exhibits the most insignificant swelling performance. Thus, it has been selected as the control group to further evaluate the role of the chain extender in the swelling behaviours of PUs. An anionic chain extender, DMPA, was introduced into MDI–PU to examine its effect on the swelling process (Fig. 7a). Experimentally, DMPA is a common anionic chain extender and it is widely used in the synthesis of waterborne polyurethanes.35,36Fig. 7b illustrates the final snapshots of simulations at different temperatures, indicating that the introduction of DMPA obviously facilitates the water permeation. Details regarding the dynamics process and density analysis are reported in Fig. S10.†
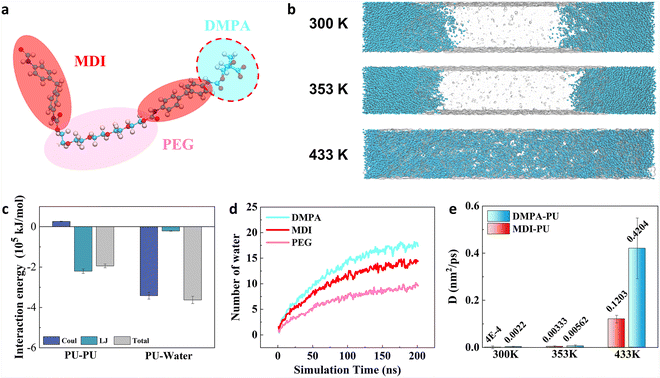 |
| Fig. 7 (a) Molecular structure of the PUs after introducing DMPA. (b) Simulation snapshots of the DMPA–PU system at equilibrium state at different temperatures. (c) Interaction energies between PU–PU and PU–water after introducing DMPA into the molecular structure. (d) Number of water molecules within a 2 Å radius around different segments. (e) Diffusion coefficients of water molecules at varying temperatures. | |
To further evaluate the effectiveness of this strategy, interaction energies were calculated, as shown in Fig. 7c. The results reveal that there is no significant change in the interaction energy between PUs, indicating that the interactions between blocks are independent of the chain extender type. However, there is a noticeable change in the interaction energy between PUs and water. These results indicate the variation of swelling behaviours is mainly caused by thermodynamics. Fig. 7d shows the number of water molecules around different segments. Most notably, the number of water molecules around DMPA is the largest as compared with other segments. As a result, the number of water molecules inside the membrane is greatly enhanced. This variation is caused by DMPA exhibiting strong water adsorption capacity due to its stronger hydrophilic group (COO−). Accordingly, the diffusion coefficient of water is significantly improved, as shown in Fig. 7e. Taken together, the simulation results demonstrate that the swelling of the membrane can be facilitated by introducing DMPA as a chain extender. In addition, it is important to note that some other environmental factors, such as salinity and shear forces, can also influence the performance of PU-based microcapsules. In view of this, to further enhance the performance of PU-based microcapsules in the EOR process, more comprehensive design optimization of PU-based molecules is still an important topic that needs to be studied.
Conclusions
In this study, TEM experiments confirm the thermo-responsive swelling-release properties of PU microcapsules. After validating the practicality of PU microcapsules, all-atom MD simulations were adopted to rationally design and optimize the PU-based polymers. The analysis from energetic and structural perspectives demonstrates that the type of diisocyanate segment significantly influences the flexibility of PUs, as well as the PU–water interactions. Overall, the characteristics of HDI–PU endow it with noticeable swelling performance. In contrast, the rigidity of MDI–PU is unfavourable for the penetration process of water molecules, while the swelling process of IPDI–PU and TDI–PU is also limited due to their undesired molecular confirmations and interaction process with water. Further investigation on the PU–water interaction configurations and process demonstrates that the water penetration process is dominated by the diisocyanate segments of PU-based block polymers, and the swelling process is accompanied by the reconfiguration of hydrogen bonding networks within the membrane. Moreover, besides the control of diisocyanate segments, the introduction of hydrophilic DMPA as a chain extender can also promote the swelling process significantly, and this effect is mainly caused by thermodynamics (enhanced interaction between water and the chain extender). Taken together, this study provides valuable insights into the molecular design of PU-based microcapsules with desired swelling behaviours, and the findings in the structure–activity relationship study can facilitate the potential application of PU-based microcapsules in many areas including EOR.
Author contributions
Tongyi Wang: investigation, visualization, formal analysis, data curation, writing – original draft. Yongsheng Liu: investigation, data curation. Jiawei Li: methodology, validation, writing – review & editing. Jun Zhang: funding acquisition, resources, supervision. Jian Hou: funding acquisition, resources, supervision. Youguo Yan: funding acquisition, project administration. Xiao Wang: funding acquisition, writing – review & editing.
Conflicts of interest
The authors declare that they have no known competing financial interests or personal relationships that could have appeared to influence the work reported in this paper.
Acknowledgements
This work is financially supported by the National Natural Science Foundation of China (Grant No. U21B2070, 52104059), Shandong Provincial Natural Science Foundation, China (ZR2021QE003), and Fundamental Research Funds for the Central Universities (21CX06010A).
References
- M. S. Kamal, I. A. Hussein and A. S. Sultan, Energy Fuels, 2017, 31, 7701–7720 CrossRef CAS.
- H. Liao, H. Yu, G. Xu, P. Liu, Y. He and Y. Zhou, ACS Omega, 2022, 7, 4595–4605 CrossRef CAS PubMed.
- B. Wei, L. Romero-Zerón and D. Rodrigue, J. Pet. Explor. Prod. Technol., 2014, 4, 113–121 CrossRef CAS.
- A. L. Viken, T. Skauge, P. E. Svendsen, P. A. Time and K. Spildo, Energy Fuels, 2018, 32, 10421–10427 CrossRef CAS.
- A. Sabhapondit, A. Borthakur and I. Haque, J. Appl. Polym. Sci., 2003, 87, 1869–1878 CrossRef CAS.
- S. Wang, Z. Tang, J. Qu, T. Wu, Y. Liu, J. Wang, X. Liu, Y. Ju and F. Liu, RSC Adv., 2021, 11, 5763–5772 RSC.
- D. A. Z. Wever, F. Picchioni and A. A. Broekhuis, Eur. Polym. J., 2013, 49, 3289–3301 CrossRef CAS.
- X. Zhou, W. Li, L. Zhu, H. Ye and H. Liu, RSC Adv., 2019, 9, 1782–1791 RSC.
-
F. M. de Souza, P. K. Kahol and R. K. Gupta, in Polyurethane Chemistry: Renewable Polyols and Isocyanates, American Chemical Society, 2021, ch. 1, vol. 1380, pp. 1–24 Search PubMed.
- P. Kardar, Prog. Org. Coat., 2015, 89, 271–276 CrossRef CAS.
- E. Koh, N.-K. Kim, J. Shin and Y.-W. Kim, RSC Adv., 2014, 4, 16214–16223 RSC.
- R. He, J. Wang, X. Wang, W. Li and X. Zhang, Colloids Surf., A, 2018, 550, 138–144 CrossRef CAS.
- A. Özsevinç and C. Alkan, Ind. Crops Prod., 2023, 192, 116131 CrossRef.
- R. Wang and Y. Xiao, J. Appl. Polym. Sci., 2020, 137, 48594 CrossRef CAS.
- X. Bai, J. Li, C. Wang and Q. Ren, J. Polym. Res., 2020, 27, 185 CrossRef CAS.
- Y. Ma, Z. Li, H. Wang and H. Li, J. Colloid Interface Sci., 2019, 534, 469–479 CrossRef CAS PubMed.
- F. Alizadegan, S. M. Mirabedini, S. Pazokifard, S. Goharshenas Moghadam and R. Farnood, Prog. Org. Coat., 2018, 123, 350–361 CrossRef CAS.
- J. Xie, S. Tian, H. Zhang, C. Feng, Y. Han, H. Dai and L. Yan, Biomacromolecules, 2023, 24, 2225–2236 CrossRef CAS PubMed.
- K. M. Zia, F. Zia, M. Zuber, S. Rehman and M. N. Ahmad, Int. J. Biol. Macromol., 2015, 79, 377–387 CrossRef CAS PubMed.
- J. Gong, Y. Wang, X. Cao, F. Yuan and Y. Ji, J. Mol. Liq., 2022, 360, 119394 CrossRef CAS.
- L. Lv, M. Yang, Y. Long and J. Chen, Appl. Surf. Sci., 2021, 557, 149823 CrossRef CAS.
- X. Wang, W. Xie, L. Li, J. Zhu and F. Xing, Polymers, 2022, 14, 611 CrossRef CAS.
- M. O. Alziyadi and A. R. Denton, J. Chem. Phys., 2021, 155, 214904 CrossRef CAS.
- X. Song, S. Wang, X. Duan, H. Liu, S. Chen, T. Long, X. Xu, J. Tang, T. Li, S. Zhao and H. Liu, Appl. Surf. Sci., 2022, 605, 154639 CrossRef CAS.
- S. Nikolov, A. Fernandez-Nieves and A. Alexeev, J. Appl. Math. Mech., 2017, 39, 47–62 CrossRef.
- A. A. Rudov, I. V. Portnov, A. R. Bogdanova and I. I. Potemkin, J. Colloid Interface Sci., 2023, 640, 1015–1028 CrossRef CAS.
- A. J. Schmid, J. Dubbert, A. A. Rudov, J. S. Pedersen, P. Lindner, M. Karg, I. I. Potemkin and W. J. S. R. Richtering, Sci. Rep., 2016, 6, 1–13 CrossRef.
- L. Martínez, R. Andrade, E. G. Birgin and J. M. Martínez, J. Comput. Chem., 2009, 30, 2157–2164 CrossRef.
- J. Liu, Q. Xu and J. Jiang, J. Membr. Sci., 2019, 573, 639–646 CrossRef CAS.
- Q. Xu and J. Jiang, Curr. Opin. Chem. Eng., 2020, 28, 66–74 CrossRef.
- T. Lu and F. Chen, J. Comput. Chem., 2012, 33, 580–592 CrossRef CAS.
- A. D. MacKerell, Jr., D. Bashford, M. Bellott, R. L. Dunbrack, Jr., J. D. Evanseck, M. J. Field, S. Fischer, J. Gao, H. Guo, S. Ha, D. Joseph-McCarthy, L. Kuchnir, K. Kuczera, F. T. K. Lau, C. Mattos, S. Michnick, T. Ngo, D. T. Nguyen, B. Prodhom, W. E. Reiher, B. Roux, M. Schlenkrich, J. C. Smith, R. Stote, J. Straub, M. Watanabe, J. Wiórkiewicz-Kuczera, D. Yin and M. Karplus, J. Phys. Chem. B, 1998, 102, 3586–3616 CrossRef.
- M. J. Abraham, T. Murtola, R. Schulz, S. Páll, J. C. Smith, B. Hess and E. Lindahl, SoftwareX, 2015, 1-2, 19–25 CrossRef.
- W. Humphrey, A. Dalke and K. Schulten, J. Mol. Graphics, 1996, 14(33–38), 27–38 Search PubMed.
- H. Lijie, D. Yongtao, Z. Zhiliang, S. Zhongsheng and S. Zhihua, Colloids Surf., A, 2015, 467, 46–56 CrossRef.
- I. Jiménez-Pardo, P. Sun, R. A. T. M. van Benthem and A. C. C. Esteves, Eur. Polym. J., 2018, 101, 324–331 CrossRef.
|
This journal is © The Royal Society of Chemistry 2024 |