DOI:
10.1039/D3MA00968H
(Paper)
Mater. Adv., 2024,
5, 2368-2376
Top-down surfactant-free electrosynthesis of magnéli phase Ti9O17 nanowires†
Received
5th November 2023
, Accepted 26th January 2024
First published on 27th January 2024
Abstract
TiO2 nanowires have proven their importance as a versatile material in numerous fields of technology due to their unique properties attributable to their high aspect ratio and large surface area. However, synthesis is an enormous challenge since state-of-the-art techniques rely on complex, multi-stage procedures with expensive, specialized equipment, employing high-temperature steps and potentially toxic precursor materials and surfactants. Hence, we elucidate a simple and facile top-down methodology for the synthesis of nanowires with non-stoichiometric Magnéli phase Ti9O17. This methodology relies on the electrochemical erosion of bulk Ti wires immersed in an aqueous electrolyte, circumventing the use of environmentally harmful precursors or surfactants, eliminating the need for high temperatures, and reducing synthesis complexity and time. Using multiple techniques, including transmission electron microscopy, X-ray photoelectron spectroscopy, and X-ray diffraction, we provide evidence of the successful synthesis of ultrathin nanowires with the crystal structure of non-stoichiometric Ti9O17 Magnéli phase. The nanowire width of ∼5 nm and the Brunauer–Emmett–Teller surface area of ∼215 m2 g−1 make the nanowires presented in this work comparable to those synthesized by state-of-the-art bottom-up techniques.
Introduction
Titanium dioxide (TiO2) is a widely used class of transition metal oxide materials with many different fields of application. These reach from energy storage systems, such as batteries1 and supercapacitors,2 over a variety of sensor systems,3 to photocatalysis,4 which has gained ever-growing research interest since Fujishima and Honda discovered photocatalytic water splitting on TiO2 using ultraviolet light in 1972.5 Besides photoelectrochemical water splitting, composites of CeO2/TiO2 showed remarkable photocatalytic activity for the degradation and mineralization of tetracycline at room temperature.6 Furthermore, Ti-based materials have gathered increasing interest as micro- or nanoporous layers in electrolyzers for efficient hydrogen production due to their unique properties of minimizing interfacial resistance between the catalyst and gas diffusion layer.7 Besides this, nanostructured TiO2 holds great potential in other branches of heterogeneous catalysis, either directly as a catalyst8 or, most importantly, as a catalyst support material.9 For the former, Ni/TiO2 catalyst systems, as an example, revealed high catalytic activity and stability for undiluted methane decomposition under high-temperature conditions.10 The latter functions as a framework to which catalysts can attach. As a result, the catalyst support material can contribute to the total catalyst stability and activity by preventing agglomeration and maximizing the accessible number of the catalyst's active surface sites. Therefore, support materials must exhibit a large surface-to-volume ratio; hence nanostructured morphologies are indispensable.
Various classes of support materials exist to date, of which mesoporous materials,11 conductive polymers,12 carbon-based materials,13 and metal oxides14 are the most important ones. Metal oxides, such as tungsten oxide (WO3), cerium oxide (CeO2), and TiO2, offer significant advantages compared to the other support materials classes. Apart from excellent mechanical, thermal, and chemical stability, they profit from the strong metal–support interaction (SMSI), which stabilizes the active metal catalyst and improves the catalytic activity.15 TiO2 nanowires meet these requirements and thus belong to the state-of-the-art support materials in the class of metal oxides due to their excellent chemical stability under catalytic conditions, resistance to corrosion and oxidation, mechanical strength, and large surface area.16 Moreover, Ti is one of the most abundant, non-toxic, and environmentally friendly materials, making TiO2 nanowires an ideal candidate for a sustainable catalyst support material.17 However, the toxicity of nanomaterials, such as nanoparticles or nanowires, has been shown in various studies and should be addressed.18 Nevertheless, nanomaterials have become indispensable in modern technologies. Obeying standard health and safety protocols for handling nanomaterials allows the synthesis, handling, and application of novel nanomaterials, such as the Ti9O17 nanowires presented in our study. Besides TiO2, non-stoichiometric titanium oxides with the general formula TixO2x−1 (4 ≤ x ≤ 10) have been reported to show distinctive properties, such as great stability until almost 2000 K, and superior corrosion stability in acidic and alkaline environments.19 Their unique structure, consisting of rutile layers separated by shear planes, leads to a high electronic conductivity compared to TiO2.20 Due to the superior properties of non-stoichiometric TiOx, these so-called Magnéli phases are a promising class of materials for application in the field of electronics or energy systems, i.e., as catalyst support material in (electro) catalysis, compared to classical TiO2.21 Magnéli-phase TixO2x−1 revealed significant durability as a support material for palladium catalysts in alkaline direct ethanol fuel cells22 and platinum catalysts in formic acid electrooxidation.23 In addition, the Magnéli phase proved to be an excellent candidate for thermoelectric applications.19,24
However, the production of nanostructured titanium oxides (TiOx) poses a severe challenge despite the diverse variety of synthesis methods available to date. The most common approaches include, among others, sol–gel, hydrothermal, solvothermal, microwave-assisted, surfactant-assisted, and sonochemical methods, as well as chemical and physical vapor deposition.25 Nonetheless, the synthesis of TiO2-like nanowires usually relies on complicated multi-step approaches at elevated temperatures or pressures utilizing additives, such as surfactants, which can be harmful to the environment. For example, in physical and chemical vapor deposition, Ti vapor condenses at the surface of a substrate and forms a solid-phase nanostructure. However, raw Ti first needs to be brought to its vapor phase requiring high temperatures in the range of 500–700 °C, making it an environmentally unfavorable technique. The sol–gel method is a common bottom-up approach to producing inorganic ceramic and glass materials but usually requires a mixture of precursor solutions with subsequent stirring, drying, and heating at high temperatures of up to several 100 °C for several hours to obtain the final TiOx nanowires. As another standard bottom-up synthesis technique for TiOx nanostructures, the hydrothermal method covers the heterogeneous reactions of Ti precursor mixtures in aqueous solutions.16 Unfortunately, several synthesis steps at elevated temperatures and pressures, usually for several hours or days, are necessary to form the desired nanostructures. In contrast to hydrothermal, solvothermal approaches use organic solvents instead of aqueous ones. This utilization of organic solvents results in temperatures and pressures even higher than for the hydrothermal method, which enables better control of the TiOx size and morphology. Still, it also requires more energy during the synthesis process.
The addition of surfactants demonstrates a standard procedure to control the growth of nanostructured TiOx synthesized by the bottom-up approaches mentioned before.26 However, the addition of surfactants during the synthesis constitutes several concerns. Primary and secondary toxicity, biodegradability, eco-friendliness, and environmental pollution remain immense problems.27 In addition, surfactant residues at the surface of the nanomaterial after synthesis are detrimental to its performance as they can block the nanomaterial's surface and, therefore, impair its unique properties. Consequently, we present a novel, alternative, top-down approach to synthesizing Magnéli phase Ti9O17 nanowires without needing elevated temperatures or using environmentally harmful substances, such as surfactants, called electrochemical erosion. Even though reported by Bredig and Haber as early as the end of the 19th century,28 this approach only gained increasing interest in recent years as the groups of Li and Koper employed it to successfully fabricate various metal nanostructures including Bi, Pt, Rh, Au, Cu, Ag, Ni, and Si, among others.29 In previous studies, our group explored the synthesis of platinum-lanthanide nanoparticles and the influence of the synthesis parameters on Pt nanoparticles.30
Experimental
Synthesis
To fabricate ultrathin non-stoichiometric Ti9O17 nanowires with a high surface area, two Ti bulk wires (Ø 0.25 mm, 99.6%, MaTecK, Germany) were immersed in a saturated KOH solution (85%, Grüssing, Germany) and subjected to an alternating current (AC) signal to initiate electrochemical erosion using a VSP 300 potentiostat (Bio-Logic, France). The influence of the AC signal frequency and solution composition on the nanostructure size, morphology, and composition is further elucidated in the ESI.† Using a sinusoidal voltage signal with an amplitude of 25 V and a frequency of 200 Hz, we eroded the bulk Ti wires into ultrathin Ti9O17 nanowires. The formation of Ti9O17 nanowires occurred immediately during the synthesis process in the saturated KOH electrolyte through oxidation, indicated by a change in the color of the eroded Ti from dark grey (Ti) to white (Ti9O17 nanowires). Subsequently, the saturated KOH electrolyte containing the Ti9O17 nanowires was diluted, filtered, washed with ultrapure water (18.2 MΩ cm, Merck Millipore, USA) and ethanol (EMSURE® ACS, ISO, Reag. Ph Eur, Sigma Aldrich®, USA), and dried in a furnace (Heraeus, Germany) at 60 °C in air to obtain Ti9O17 nanowires. More detailed information on the synthesis procedure and materials can be found in the ESI.† Here, we highlight the simplicity of our approach, which can be carried out in one pot within one step with subsequent filtering, washing, and drying at low temperatures. No surfactants, precursor solution mixtures, complicated multi-stage synthesis protocols, or elevated temperatures are needed compared to other state-of-the-art approaches mentioned before.
Characterization methods
Adsorption measurements.
Adsorption measurements with N2 at −196.15 °C were carried out on a 3Flex Physisorption from Micromeritics Instrument Corp., which uses a manometric method to determine the amount adsorbed under equilibrated gas pressure. Adsorption data were processed using the 3Flex Software Version 5.01 by Micromeritics Instrument Corp. and plotted in OriginPro 2021b by OriginLab Corp. Samples were transferred into pre-weighed sample tubes and capped with Micromeritics CheckSeals. Samples were subsequently activated again at room temperature for 12 h under a dynamic vacuum of ∼10−3 mbar using a SmartVac Prep by Micromeritics Instrument Corp. to ensure the absence of unwanted adsorbates and identical pre-measurement states of all samples. The mass of the adsorbent was then recorded, generally in the range of 25–100 mg. A liquid nitrogen bath is used for the measurements at −196.15 °C. The surface area of the materials was derived using the Brunauer–Emmett–Teller (BET) model, hence given as the ‘BET surface’ and based on N2-isotherms measured at −196.15 °C. To determine the apparent BET area – or more precisely: BET capacity – for microporous materials, care was taken to adhere to the Rouquerol criteria.
Transmission electron microscopy (TEM).
The morphology, structure, and chemical composition of the TiOx nanowire network was studied in nanoscale with a Cs image-corrected transmission electron microscope TITAN Themis 60–300 Cubed (Thermo Fisher Scientific, USA). The high-resolution imaging with sub-Angstrom resolution, selected area electron diffraction (SAED) acquisition, and scanning TEM- energy dispersive X-ray spectroscopy (STEM-EDX) elemental mapping was conducted with an acceleration voltage of 300 kV. STEM- electron energy loss spectroscopy (STEM-EELS) elemental mapping was conducted with 120 kV and an electron beam current of ∼100 pA to mitigate electron beam damage during the probing of single nanowires. Additional TEM images were taken using a JEOL 2010 microscope bearing a LaB6 filament and operated at 200 kV (resolution 0.19 nm). EDX spectroscopy was performed with a Super-X detector and elemental maps and chemical composition measurements in atomic percentage (at%) were acquired and processed in the software Velox utilizing a standard Cliff–Lorimer (K-factor) quantification method. EELS was performed with Gatan GIF Quantum ERS spectrometer and EEL spectrum images and elemental maps were acquired and processed with the software GMS3 utilizing a model-based quantification.31 A sample for TEM analysis was prepared from a dispersed solution made of TiOx powder and pure ethanol, which was drop-casted onto a copper TEM grid coated with a carbon holey membrane.
X-Ray photoelectron spectroscopy (XPS).
The surface chemical composition and electronic state of the TiOx nanostructures were determined by XPS (ESCA2SR, Scienta-Omicron) using a monochromatic Al Kα (1486.7 eV) X-ray source operated at 250 W. The samples were fixed in the sample holders with carbon conductive adhesive tape. The measurements were carried out in the analysis chamber with a pressure of around 1 × 10−9 mbar. The surface charge compensation of the samples was controlled with a charge neutralizer (CN 10). The binding energy (BE) scale of the spectra was corrected taking the adventitious carbon at 284.8 eV as a reference. The data analysis was performed with the CasaXPS software (Casa software Ltd) using the elemental sensitivity factors provided by the manufacturer. For the fitting procedure, a Shirley baseline was used together with the Gaussian–Lorentzian function (70–30).
Structural studies.
A series of structural studies applying synchrotron radiation were performed at ambient temperature using the beamline (P02.1) at PETRA III, DESY. Fixed photon energy of 60 keV (λ = 0.20723 Å) was used.32 Diffraction patterns were collected using a VAREX area detector at two distinct sample-to-detector distances of 350 mm and 2200 mm, corresponding to the pair distribution function (PDF) and high-resolution diffraction (XRD) modes, accordingly. Exposure times for each diffraction pattern were 20 min and 1 min in PDF and XRD modes, respectively. Azimuthal data integration was carried out using pyFAI applying LaB6 (NIST, SRM660c) as a reference.33 Powder samples were contained in sealed glass capillaries with 0.7 mm diameter, where diffraction data collection was performed under constant capillary spinning. Analysis of obtained XRD patterns was performed by the full profile analysis\decomposition using FullProf program package.34 To model the peak profile shape, the pseudo-Voigt function in Thompson–Cox–Hastings setting was chosen. Background contribution was determined using a linear interpolation between selected data points in non-overlapping regions and subtracted from the dataset. Total scattering data were reduced using PDFGetX3 software.35 The accessible range of momentum transfer was Q = 31.8 Å−1, whilst due to obtained signal-to-noise and instrumental geometry the meaningful Qmax-inst and Qmax limits were set to 20 Å−1 and 16 Å−1, accordingly.
Scanning electron microscopy (SEM).
The morphology of the prepared samples was examined by SEM (JEOL JSM 7500F, Japan) with a field-emission cathode. The samples were observed without any conductive coating.
Results and discussion
Nanowire morphology and BET surface analysis
The ultrathin nanowires synthesized in saturated KOH are characterized via TEM in Fig. 1. The TEM images were used to estimate the width of the nanowires, which corresponded to approximately (5.0 ± 0.6) nm. Furthermore, the nanowires showed high isotropy, forming a complex nano-structural network. The length of the nanowires is estimated to be in the range of micrometers. We determined the surface area of the ultrathin nanowires to be (215 ± 15) m2 g−1 from adsorption and desorption isotherms via BET measurements, as shown in Fig. 2. The isotherms resulting from the BET analysis of various other nanostructures synthesized with different parameters are illustrated in Fig. S2a and b (ESI†). The determined BET surface area competes with reported values for TiO2 nanowires synthesized via more traditional methods, such as anodic oxidation, electrospinning, hydrothermal, and one-pot solvothermal, for which the BET surface areas correspond to (12–89) m2 g−1, (68–95) m2 g−1, (112–232) m2 g−1, and 67.2 m2 g−1, respectively.36 Obtaining state-of-the-art BET surface areas with this simple and facile electrochemical erosion approach is advantageous, as it does not use environmentally harmful substances, like organic additives. Furthermore, the inset in Fig. 2 displays the pore size distribution of the nanowires revealing micropores in the sub-nanometer regime, indicated by the peak at ∼0.8 nm pore width. In addition, we observed bigger pores with sizes in the range of ∼3 nm to ∼40 nm. The rather continuous behavior of the pore size distribution in this region arises most likely due to the mesoporous character of the highly isotropic nano-structure network of the Ti9O17 nanowires, contributing to the high BET surface area.
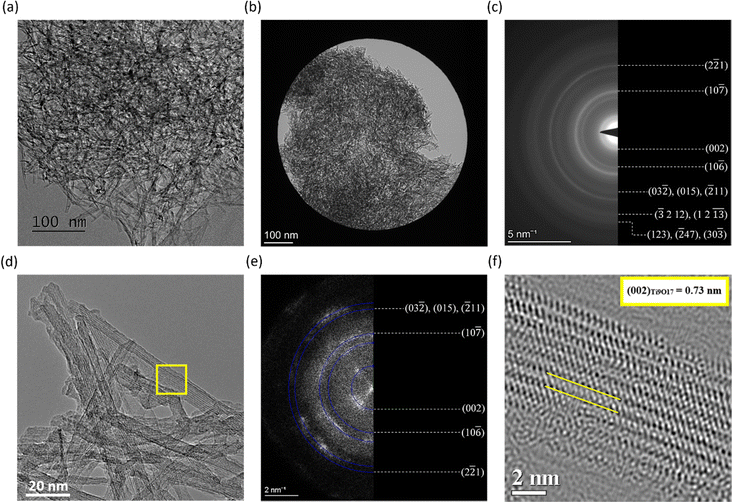 |
| Fig. 1 A set of TEM characterizations of nanowires synthesized in saturated KOH. (a) Overview image of a nanowire network. (b) TEM image showing an encircled volume of a SAED aperture for diffraction analysis and (c) a resulting electron diffraction pattern with rings corresponding to lattice planes of the Ti9O17 crystal phase. (d) HR-TEM image of a nanowire network with atomic resolution and (e) an FFT pattern of nanowires observed in HR-TEM revealing spots from lattice planes of the Ti9O17 phase. (f) HR-TEM image showing in detail the atomic structure of a single nanowire marked in (d) and revealing the (002) lattice plane stacking with a d-spacing of 0.73 nm. | |
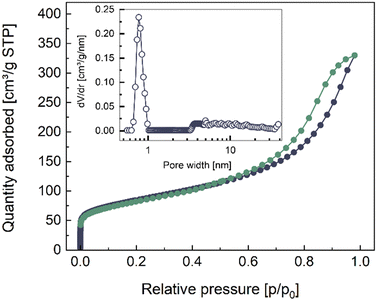 |
| Fig. 2 N2 adsorption (black) and desorption (green) isotherms of the Ti9O17 nanowires synthesized in saturated KOH via electrochemical erosion. The inset shows the pore size distribution with a strong peak around ∼0.8 nm. | |
Structural TEM characterization of Ti9O17 nanowires
A SAED analysis of a broader region containing a large number of nanowires, as shown in Fig. 1b and c, gives insights into the lattice structure of the nanowires. An evaluation of lattice spacings and ring intensities from the SAED pattern and a comparison of obtained results with crystallographic standards for Ti (hcp) and various TiOx titanates indicated that the nanowires synthesized by electrochemical erosion have the structure of a non-stoichiometric Ti9O17 with triclinic P
lattice, a so-called Magnéli phase of TiO2.37 The presence of any other crystal phases can be excluded based on the SAED analysis. The same results are confirmed by HR-TEM, and fast Fourier transformation (FFT) characterization of the nanorod network imaged with atomic resolution, shown in Fig. 1d and e, where FFT patterns also reveal d-spacings in good agreement with the Ti9O17 lattice planes. In addition, HR-TEM imaging reveals the presence of crystal lattice plane stacking along the length of nanowires. This lattice stacking is characteristic of the synthesized nanowires, which is demonstrated in Fig. 1f at a detail of a nanowire marked by a yellow rectangle in Fig. 1d. The measured value of ∼0.73 nm matches with (002) lattice planes of the Ti9O17 crystal structure. Interestingly, minor differences in lattice plane d-spacings were revealed occasionally, for example, between the (002) planes when measurements of either SAED or FFT patterns showed a d-spacing of ∼0.76 nm, which is slightly larger than the standard value. It suggests a presence of strain in the lattice, possibly resulting from the electrochemical synthesis of the nanowires.
In the following part, we discuss the results obtained by multiple techniques, including XPS, EDX, high-resolution XRD (HR-XRD), PDF, and EELS to confirm the findings made by the HR-TEM imaging with SAED and FFT characterization.
XPS examination of Ti9O17 nanowires
The XPS results, depicted in Fig. 3a and b, display the 2p1/2 and 2p3/2 doublet peaks for titanium (Ti 2p) and oxygen (O 1s), respectively. From region quantification, we assess the atomic concentration ratio of potassium, oxygen, and titanium to correspond to ∼1
:
6
:
2. This ratio indicates traces of potassium within the investigated sample, likely a residue component of the saturated KOH synthesis electrolyte during electrochemical erosion. Furthermore, the significant oxygen concentration implies that the nanowires are not composed of elemental titanium but rather consist of its oxidized form. Further analysis confirms the presence of various oxidation states of Ti within the material, primarily including Ti3+, Ti4+, and a neglectable amount of non-stoichiometric Tiδ+. For the Ti3+ and Ti4+ oxidation states of titanium, we quantified the respective ratio Ti3+
:
Ti4+ to 1
:
16. From XPS results, we assume that our fabricated nanowires consist largely of titanium in a Ti4+ oxidation state, i.e., a TiO2-like composition, which is close to the non-stoichiometric Ti9O17 compound determined by the TEM characterization.
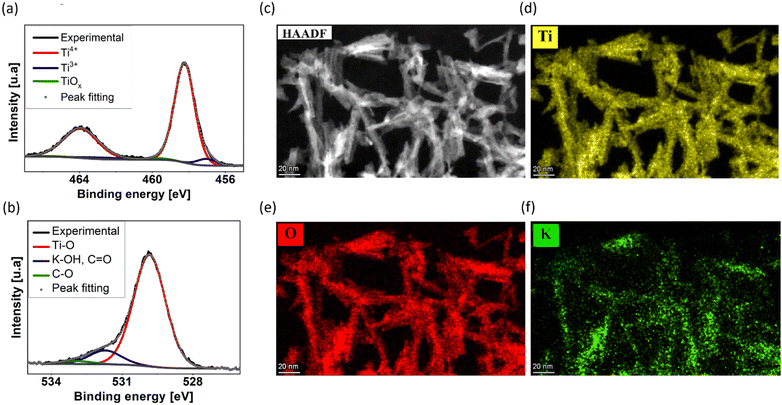 |
| Fig. 3 (a) And (b) XPS spectra of the synthesized nanowires with the 2p1/2 and 2p3/2 doublet peaks for Ti 2p and O 1s, respectively. The peaks indicate the presence of Ti with different oxidation states. (c) STEM-HAADF image of a nanowire network. (d), (e) and (f) corresponding STEM-EDX elemental maps of nanowires for Ti–K, O–K, and K–K, respectively. | |
Elemental composition of Ti9O17 nanowires
In agreement with the XPS results, STEM imaging with a high-angle annular dark-field detector (STEM-HAADF) complemented with EDX elemental mapping identified titanium, oxygen, and potassium, as displayed in Fig. 3c–f. Quantification of the EDX spectra, summarized in Fig. S4 (ESI†), reveals a Ti
:
O ratio of 1
:
2, supporting the presence of a TiO2-like structure of the nanowire network, i.e., the oxidation state Ti4+, as well as a small amount of potassium of about 3–5 at%. From XPS and EDX evaluation, we hypothesize the synthesis of ultrathin TiO2-like nanowires by our simple, facile, and environmentally friendly methodology without any surfactants or additives, employing electrochemical erosion.
Diffraction experiments of Ti9O17 nanowires
To gain more precise information about the structure of the nanowires, diffraction experiments in HR-XRD and PDF mode were performed, shown in Fig. 4a and b, respectively. The HR-XRD pattern can be modeled using a superposition of contributions from the non-stoichiometric compound Ti9O17 and two side phases, namely KTiO2(OH) and metallic (hcp) titanium.31,38 Both side phases have been found to exhibit coherent scattering lengths comparable with the resolution limit of the diffractometer (∼100 nm), while an average crystallite size of 74 Å was determined for Ti9O17. This suggests a rather large crystal structure of the two side phases, which does not coincide with the ultrathin nanowires with a diameter of ∼5 nm examined by the TEM characterization. Therefore, we assume metallic (hcp) titanium and KTiO2(OH) to be side products in the synthesized sample in low amounts, which could not be entirely avoided, despite extensive washing procedures after the synthesis. Fig. 4b displays the pair distribution function G(r) obtained from the PDF mode for the synthesized nanowires. The damping of G(r) at increased correlation distances r is primarily caused by the low momentum transfers Qmax-inst and Qmax limits set, making the correlation length above the effective detection limit. The dashed vertical lines showcase the maximum peaks, and the small tickmarks illustrate the interatomic distances in the parent titanium oxides rutile, anatase, and TiO. From this, it is evident that Ti2+ cannot be found in the bulk, and the maximum peaks align rather well with the tickmarks of the parent anatase form of TiO2. This confirms the presence of a TiO2-like phase of our nanowires, or more accurately, a non-stoichiometric Magnéli phase Ti9O17 structure according to HR-XRD, FFT, and SAED. Fig. S6 (ESI†) shows the difference in the crystal structure between rutile, anatase, and Ti9O17, which serves as the basis for the model used to describe the Ti9O17 structure via HR-XRD. In addition, the small tail observed at ∼2.85 Å can be identified as Ti–Ti or K–O distances most likely arising from KTiO2(OH) and metallic (hcp) titanium phases, in agreement with the conducted HR-XRD mode. Besides this, a weak correlation at r ∼ 1.45 Å can indicate weak carbon contamination (C–C bond), which is always present when working under atmospheric conditions.
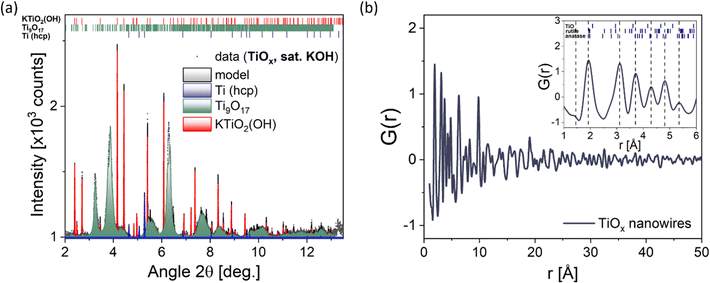 |
| Fig. 4 (a) Background-subtracted, high-resolution XRD pattern of ultrathin nanowires synthesized in saturated KOH solution via the electrochemical top-down approach with modeling results. Contributions from different phases are displayed by color, and vertical tickmarks correspond to the calculated Bragg reflection positions. (b) Pair distribution function G(r) determined from diffraction data in PDF mode. Dashed vertical lines correspond to the maximum peaks for the Ti9O17 nanowires, and small tickmarks illustrate interatomic distances in parent TiO2 rutile, anatase, and TiO. | |
Elemental mapping of single Ti9O17 nanowires
The results obtained from XRD and PDF average the structural information over many nanowires due to the large probing area. Nevertheless, in addition to the STEM-EDX, chemical analysis within the volume of single nanowires can be performed by using STEM-EELS measurements with higher sensitivity than the previously used EDX technique. Fig. 4a shows a single nanowire with the respective line-scan position where the chemical composition profile was measured. Furthermore, Fig. 5a illustrates elemental maps of potassium, oxygen, and titanium of the probed nanowire. Quantification of EEL spectra then provided percent composition (at%) profiles in Fig. 4b of the three elements across the nanowire shown in Fig. 4a. Remarkably, the atomic concentration profile indicates that the core of the nanowire contains ∼3–4 at% of potassium, which is in agreement with STEM-EDX. Following the discussion of the XRD results, the sharp peaks in Fig. 4a correspond to relatively large KTiO2(OH) crystallites as only a small amount of potassium was detected via EELS in the core of the nanowires within dimensions of a few nm. Therefore, we exclude KTiO2(OH), found via XRD, as a potential candidate for the crystal structure of the nanowires and hypothesize the presence of Ti9O17 nanowires. From the line-scan profile in Fig. 5b, we calculated an averaged Ti
:
O ratio of 0.63 ± 0.08, which approximates the expected Ti
:
O ratio of Ti9O17 and thus confirms the presence of nanowires with Ti9O17 crystal structure. Another interesting finding from EELS mapping is that potassium is present only in the core of the nanowires. It can indicate the beneficial role of synthesis in saturated KOH. K+ dissolved in the saturated electrolyte could serve as a scaffold or seed for the growth of the nanowires. However, a more fundamental examination of the synthesis procedure needs to be conducted to prove these assumptions and reveal the origin of the formation of nanowires via electrochemical erosion.
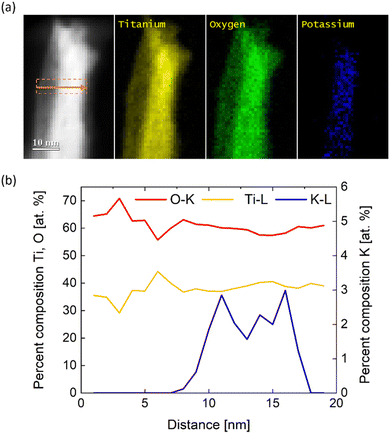 |
| Fig. 5 STEM-EELS analysis of the chemical composition of single nanowires synthesized in saturated KOH. (a) HAADF-STEM image of a probed single nanowire and corresponding STEM-EELS elemental maps calculated from intensities of Ti–L, O–K, and K–L edges. (b) Chemical composition profile of the elements after quantification to atomic concentrations. The position of the profile is marked by the orange arrow in (a). The orange rectangle depicts the used integration width for each profile to denoise the data output. | |
Conclusions
In this work, we presented a novel top-down approach, called electrochemical erosion, to synthesize Magnéli phase Ti9O17 nanowires as a versatile material with promising potential for future advancements in electronics and energy technologies. This simple and facile one-pot technique yields ultrathin nanowires with a diameter of ∼5 nm and a large BET surface area of ∼215 m2 g−1, comparable to state-of-the-art TiO2 nanowires. Comparative measurements, including a range of analytical TEM techniques in combination with XPS and state-of-the-art HR-XRD and PDF characterizations, provided deep insights into the structure, morphology, and composition of ultrathin, isotropic nanowires with a non-stoichiometric crystal structure close to TiO2, namely Ti9O17. These Magnéli phase nanowires could provide a promising opportunity to boost catalyst performance in (electro) catalysis as a stable, conductive, and high-surface area support material, which needs further investigation for particular applications. Furthermore, STEM-EELS measurements revealed not only a TiO2-like chemical composition of single nanowires but also revealed that the core of nanowires seems to contain a small amount of potassium. This could stem from the electrolyte used during the synthesis and could be crucial for the formation of nanowires. However, further in-depth investigation is necessary to determine the role of potassium in the synthesis of Ti9O17 nanowires. We want to highlight the great advantage of our synthesis approach, i.e., we can prevent environmental and health concerns by avoiding harmful precursor solutions or surfactants and eliminating complex, multi-step synthesis routes containing high-temperature profiles compared to conventional synthesis techniques. It is important to note again that standard health and safety precautions have to be obeyed when handling nanostructured materials, such as Ti9O17 nanowires, due to their nano-size-related toxicity in order to guarantee the fabrication and application of these novel materials.
Conflicts of interest
There are no conflicts to declare.
Acknowledgements
We want to thank Siegfried Schreier, Kathrin L. Kollmannsberger, Shujin Hou for their help with the conducted SEM and BET experiments, respectively. P. M. S. and A. S. B. are thankful for the funding via the Excellence Strategy of the Federal Government and the Länder in the context of the ARTEMIS Innovation Network and DFG project BA 5795/6-1. The authors are grateful for the funding support by the DFG Cluster of Excellence “e-conversion”. The authors acknowledge support from the Ministry of Education, Youth and Sports of the Czech Republic for supporting Large Research Infrastructures CEMNAT (LM2023037) and CzechNanoLab (LM2023051) for providing SEM, XRD, XPS and TEM accesses, respectively.
References
- S. Liang, X. Wang, R. Qi, Y.-J. Cheng, Y. Xia, P. Müller-Buschbaum and X. Hu, Adv. Funct. Mater., 2022, 32, 2201675 CrossRef CAS; H. Shi, C. Shi, Z. Jia, L. Zhang, H. Wang and J. Chen, RSC Adv., 2022, 12, 33641 RSC; S. Liang, X. Wang, Y. J. Cheng, Y. Xia and P. Müller-Buschbaum, Energy Storage Mater., 2022, 45, 201–264 CrossRef.
- Q. Wang, Z. H. Wen and J. H. Li, Adv. Funct. Mater., 2006, 16, 2141–2146 CrossRef CAS; X. Lu, M. Yu, G. Wang, T. Zhai, S. Xie, Y. Ling, Y. Tong and Y. Li, Adv. Mater., 2013, 25, 267–272 CrossRef PubMed; S. Yang, Y. Lin, X. Song, P. Zhang and L. Gao, ACS Appl. Mater. Interfaces, 2015, 7, 17884–17892 CrossRef PubMed; P. Pazhamalai, K. Krishnamoorthy, V. K. Mariappan and S.-J. Kim, J. Colloid Interface Sci., 2019, 536, 2–70 CrossRef PubMed; W. Zhong, H. Sun, J. Pan, Y. Zhang, X. Yan, Y. Guan, W. Shen and X. Cheng, Mater. Sci. Semicond. Process., 2021, 127, 105715 CrossRef.
- J. Bai and B. Zhou, Chem. Rev., 2014, 114, 10131–10176 CrossRef CAS PubMed; X. Tian, X. Cui, T. Lai, J. Ren, Z. Yang, M. Xiao, B. Wang, X. Xiao and Y. Wang, Nano Mater. Sci., 2021, 3, 390–403 CrossRef; B. B. Azer, A. Gulsaran, J. R. Pennings, R. Saritas, S. Kocer, J. L. Bennett, Y. D. Abhang, M. A. Pope, E. Abdel-Rahman and M. Yavuz, J. Electroanal. Chem., 2022, 918, 116466 CrossRef; L. Bertel, D. A. Miranda and J. M. García-Martín, Sensors, 2021, 21, 6167 CrossRef PubMed; S. Jafari, B. Mahyad, H. Hashemzadeh, S. Janfaza, T. Gholikhani and L. Tayebi, Int. J. Nanomed., 2020, 15, 3447–3470 CrossRef PubMed.
- A. Fujishima, T. N. Rao and D. A. Tryk, J. Photochem. Photobiol., C, 2000, 1, 1–21 CrossRef CAS; M. Ni, M. K. H. Leung, D. Y. C. Leung and K. Sumathy, Renewable Sustainable Energy Rev., 2007, 11, 401–425 CrossRef; M. Pelaez, N. T. Nolan, S. C. Pillai, M. K. Seery, P. Falaras, A. G. Kontos, P. S. M. Dunlop, J. W. J. Hamilton, J. A. Byrne, K. O’Shea, M. H. Entezari and D. D. Dionysiou, Appl. Catal., B, 2012, 125, 331–349 CrossRef; X. Kang, S. Liu, Z. Dai, Y. He, X. Song and Z. Tan, Catalysts, 2019, 9, 191 CrossRef; M. Ijaz and M. Zafar, Int. J. Energy Res., 2021, 45, 3569–3589 CrossRef.
- A. Fujishima and K. Honda, Nature, 1972, 238, 37–38 CrossRef CAS PubMed.
- M. Pudukudy, Q. Jia, J. Yuan, S. Megala, R. Rajendran and S. Shan, Mater. Sci. Semicond. Process., 2020, 108, 104891 CrossRef CAS; J. Yuan, M. Pudukudy, T. Hu, Y. Liu, X. Luo, Y. Zhi, H. Su, L. Jiang and S. Shan, Appl. Surf. Sci., 2021, 557, 149829 CrossRef.
- Z. Kang, G. Yang, J. Mo, S. Yu, D. A. Cullen, S. T. Retterer, T. J. Toops, M. P. Brady, G. Bender, B. S. Pivovar, J. B. Green Jr. and F.-Y. Zhang, Int. J. Hydrogen Energy, 2018, 43, 14618–14628 CrossRef CAS; M. F. Ernst, V. Meier, M. Kornherr and H. A. Gasteiger, Meet. Abstr., 2022, MA2022-01 1750 Search PubMed.
- L. K. Noda, R. M. de Almeida, L. F. D. Probst and N. S. Gonçalves, J. Mol. Catal. A: Chem., 2005, 225, 39–46 CrossRef CAS; H. Zhao, P. Jiang, Y. Dong, M. Huang and B. Liu, New J. Chem., 2014, 38, 4541–4548 RSC; J. Gardy, A. Hassanpour, X. Lai and M. H. Ahmed, Appl. Catal., A, 2016, 527, 81–95 CrossRef.
- S. D. Lin, M. Bollinger and M. A. Vannice, Catal. Lett., 1993, 17, 245–262 CrossRef CAS; V. Idakiev, Z.-Y. Yuan, T. Tabakova and B.-L. Su, Appl. Catal., A, 2005, 281, 149–155 CrossRef; K.-W. Park and K.-S. Seol, Electrochem. Commun., 2007, 9, 2256–2260 CrossRef; B. Dong, B.-L. He, J. Huang, G.-Y. Gao, Z. Yang and H.-L. Li, J. Power Sources, 2008, 175, 266–271 CrossRef; M. Méndez-Cruz, J. Ramírez-Solís and R. Zanella, Catal. Today, 2011, 166, 172–179 CrossRef; R. Palcheva, L. Dimitrov, G. Tyuliev, A. Spojakina and K. Jiratova, Appl. Surf. Sci., 2013, 165, 309–316 CrossRef; X.-L. Sui, Z.-B. Wang, M. Yang, L. Huo, D.-M. Gu and G.-P. Yin, J. Power Sources, 2014, 255, 43–51 CrossRef; A.-R. Rautio, P. Mäki-Arvela, A. Aho, K. Eränen and K. Kordas, Catal. Today, 2015, 241, 170–178 CrossRef; S. K. S. Hossain, J. Saleem, S. Rahman, S. M. J. Zaidi, G. McKay and C. K. Cheng, Catalysts, 2019, 9, 298 CrossRef; H. A. Lara-García, J. A. Mendoza-Nieto, H. Pfeiffer and L. Torrente-Murciano, Int. J. Hydrogen Energy, 2019, 44, 30062–30074 CrossRef; S. Hoang, Y. Guo, A. J. Binder, W. Tang, S. Wang, J. Liu, H. Tran, X. Lu, Y. Wang, Y. Ding, E. A. Kyriakidou, J. Yang, T. J. Toops, T. R. Pauly, R. Ramprasad and P.-X. Gao, Nat. Commun., 2020, 11, 1062 CrossRef PubMed; T. Fröschl, U. Hörmann, P. Kubiak, G. Ku
erová, M. Pfanzelt, C. K. Weiss, R. J. Behm, N. Hüsing, U. Kaiser, K. Landfester and M. Wohlfahrt-Mehrens, Chem. Soc. Rev., 2012, 41, 5313–5360 RSC; S. Bagheri, N. M. Julkapli and S. B. A. Hamid, Sci. World J., 2014, 727496 Search PubMed.
- M. Pudukudy, Z. Yaakob, A. Kadier, M. S. Takriff and N. S. M. Hassan, Int. J. Hydrogen Energy, 2017, 42, 16495–16513 CrossRef CAS.
- A. Walcarius, Chem. Soc. Rev., 2013, 42, 4098–4140 RSC.
- S. Ghosh, T. Maiyalagan and R. N. Basu, Nanoscale, 2016, 8, 6921–6947 RSC.
- E. Auer, A. Freund, J. Pietsch and T. Tacke, Appl. Catal., A, 1998, 173, 259–271 CrossRef CAS.
- Z. Zhang, J. Liu, J. Gu, L. Su and L. Cheng, Energy Environ. Sci., 2014, 7, 2535–2558 RSC.
- S. J. Tauster, S. C. Fung, R. T. K. Baker and J. A. Horsley, Science, 1981, 211, 1121–1125 CrossRef CAS PubMed; X. Du, Y. Huang, X. Pan, B. Han, Y. Su, Q. Jiang, M. Li, H. Tang, G. Li and B. Qiao, Nat. Commun., 2020, 11, 5811 CrossRef PubMed.
- L. Dai, C. H. Sow, C. T. Lim, W. C. D. Cheong and V. B. C. Tan, Nano Lett., 2009, 9, 576–582 CrossRef CAS PubMed; P. Roy, S. Berger and P. Schmuki, Angew. Chem., Int. Ed., 2011, 50, 2904–2939 CrossRef PubMed; Y. Takabatake, Z. Noda, S. M. Lyth, A. Hayashi and K. Sasaki, Int. J. Hydrogen Energy, 2014, 39, 5074–5082 CrossRef.
- J. Thakare and J. Masud, Energies, 2022, 15, 4437 CrossRef CAS.
- S. Sharifi, S. Behzadi, S. Laurent, M. L. Forrest, P. Stroeve and M. Mahmoudi, Chem. Soc. Rev., 2012, 41, 2323–2343 RSC; P. Ganguly, A. Breen and S. C. Pillai, ACS Biomater. Sci. Eng., 2018, 4, 2237–2275 CrossRef CAS PubMed; M. Allegri, M. G. Bianchi, M. Chiu, J. Varet, A. L. Costa, S. Ortelli, M. Blosi, O. Bussolati, C. A. Poland and E. Bergamaschi, PLoS One, 2016, 11, e0151365 CrossRef PubMed.
- A. F. Arif, R. Balgis, T. Ogi, F. Iskandar, A. Kinoshita, K. Nakamura and K. Okuyama, Sci. Rep., 2017, 7, 3646 CrossRef CAS PubMed; Y. Fan, X. Feng, W. Zhou, S. Murakami, K. Kikuchi, N. Nomura, L. Wang, W. Jiang and A. Kawasaki, J. Eur. Ceram. Soc., 2018, 38, 507–513 CrossRef.
- A. A. Gusev, E. G. Avvakumov, A. Zh. Medvedev and A. I. Masily, Sci. Sintering, 2007, 39, 51–57 CrossRef CAS.
- W.-Q. Han and X.-L. Wang, Appl. Phys. Lett., 2010, 97, 243104 CrossRef CAS; X. Li, A. L. Zhu, W. Qu, H. Wang, R. Hui, L. Zhang and J. Zhang, Electrochim. Acta, 2010, 55, 5891–5898 CrossRef; H. Zhao, Y. Wang, Q. Tang, L. Wang, H. Zhang, C. Quan and T. Qi, Int. J. Hydrogen Energy, 2014, 39, 9621–9627 CrossRef.
- S. T. Nguyen, J.-M. Lee, Y. Yang and X. Wang, Ind. Eng. Chem. Res., 2012, 51, 9966–9972 CrossRef CAS.
- H. Zhao, Y. Wang, Q. Tang, L. Wang, H. Zhang, C. Quan and T. Qi, Int. J. Hydrogen Energy, 2014, 39, 9621–9627 CrossRef CAS.
- Q. He, Q. Hao, G. Chen, B. Poudel, X. Wang, D. Wang and Z. Ren, Appl. Phys. Lett., 2007, 91, 052505 CrossRef CAS; M. Backhaus-Ricoult, J. R. Rustad, D. Vargheese, I. Dutta and K. Work, J. Electron. Mater., 2012, 41, 1636–1647 CrossRef; Y. Fan, X. Feng,W. Zhou, S. Murakami, K. Kikuchi, N. Nomura, L. Wang, W. Jiang and A. Kawasaki, J. Eur. Ceram. Soc., 2018, 38, 507–513 CrossRef.
- X. Chen and S. S. Mao, Chem. Rev., 2007, 107, 2891–2959 CrossRef CAS PubMed; X. Wang, Z. Li, J. Shi and Y. Yu, Chem. Rev., 2014, 114, 9346–9384 CrossRef PubMed; Y. Wang, Y. He, Q. Lai and M. Fan, J. Environ. Sci., 2014, 26, 2139–2177 CrossRef PubMed; X. Chen and S. S. Mao, J. Nanosci. Nanotechnol., 2006, 6, 906–925 CrossRef PubMed; S. Reghunat, D. Pinherio and S. D. Kr, Appl. Surf. Sci. Adv., 2021, 3, 100063 CrossRef; M. Ge, C. Cao, J. Huang, S. Li, Z. Chen, K.-Q. Zhang, S. S. Al-Deyab and Y. Lai, J. Mater. Chem. A, 2016, 4, 6772–6801 RSC; B. Xu, H. Y. Sohn, Y. Mohassab and Y. Lan, RSC Adv., 2016, 6, 79706–79722 RSC; X. Zhang, Y. Lin, X. Zhong, L. Wang, W. Liu, A. Singh and Q. Zhao, J. Mater. Sci: Mater. Electron., 2016, 27, 4861–4865 CrossRef; S. Qian and J. Mao, J. Mater. Sci: Mater. Electron., 2015, 26, 5166–5169 CrossRef.
- J. Joo, S. G. Kwon, T. Yu, M. Cho, J. Lee, J. Yoon and T. Hyeon, J. Phys Chem. B, 2005, 109, 15297–15302 CrossRef CAS PubMed; P. D. Cozzoli, A. Kornowski and H. Weller, J. Am. Chem. Soc., 2003, 125, 14539–14548 CrossRef PubMed; Y.-W. Jun, M. F. Casula, J.-H. Sim, S. Y. Kim, J. Cheon and A. P. Alivisatos, J. Am. Chem. Soc., 2003, 125, 15981–15985 CrossRef PubMed; X.-L. Li, Q. Peng, J.-X. Yi, X. Wang and Y. Li, Chem. – Eur. J., 2006, 12, 2383–2391 CrossRef PubMed; J. Hu, H. Li, S. Muhammad, Q. Wu, Y. Zaho and Q. Jiao, J. Solid State Chem., 2017, 253, 113–120 CrossRef.
- S. O. Badmus, H. K. Amusa, T. A. Oyehan and T. A. Saleh, Environ. Sci. Pollut. Res., 2021, 28, 62085–62104 CrossRef CAS PubMed; S. Rebello, A. K. Asok, S. Mundayoor and M. S. Jisha, Environ. Chem. Lett., 2014, 12, 275–287 CrossRef; M. Lechuga, M. Fernández-Serrano, E. Jurado, J. Núñez-Olea and F. Ríos, Ecotoxicol. Environ. Saf., 2016, 125, 1–8 CrossRef PubMed.
- G. Bredig and F. Haber, Ber. Dtsch. Chem. Ges., 1898, 31, 2741–2752 CrossRef CAS.
- X. Chen, S. Chen, W. Huang, J. Zheng and Z. Li, Electrochim. Acta, 2009, 54, 7370–7373 CrossRef CAS; W. Huang, S. Chen, J. Zheng and Z. Li, Electrochem. Commun., 2009, 11, 469–472 CrossRef; J. Liu, W. Huang, S. Chen, S. Hu, F. Liu and Z. Li, Int. J. Electrochem. Sci., 2009, 4, 1302–1308 CrossRef; A. I. Yanson, P. Rodriguez, N. Garcia-Araez, R. V. Mom, F. D. Tichelaar and M. T. M. Koper, Angew. Chem., 2011, 123, 6470–6474 CrossRef; T. J. P. Hersbach, I. T. McCrum, D. Anastasiadou, R. Wever, F. Calle-Vallejo and M. T. M. Koper, ACS Appl. Mater. Interfaces, 2018, 10, 39363–39379 CrossRef PubMed; A. I. Yanson, P. V. Antonov, P. Rodriguez and M. T. M. Koper, Electrochim. Acta, 2013, 112, 913–918 CrossRef; P. Rodriguez, F. D. Tichelaar, M. T. M. Koper and A. I. Yanson, J. Am. Chem. Soc., 2011, 133, 17626–17629 CrossRef PubMed.
- J. Fichtner, B. Garlyyev, S. Watzele, H. A. El-Sayed, J. N. Schwämmlein, W.-J. Li, F. Maillard, L. Dubau, J. Michali
ka, J. M. Macak, A. Holleitner and A. S. Bandarenka, ACS Appl. Mater. Interfaces, 2019, 11, 5129–5135 CrossRef CAS PubMed; B. Garlyyev, S. Watzele, J. Fichtner, J. Michali
ka, A. Schökel, A. Senyshyn, A. Perego, D. Pan, H. A. El-Sayed, J. M. Macak, P. Atanassov, I. V. Zenyuk and A. S. Bandarenka, Nano Res., 2021, 14, 2762–2769 CrossRef.
- P. J. Thomas and R. D. Twesten, Microsc. Microanal., 2012, 18, 968–969 CrossRef.
- A.-C. Dippel, H.-P. Liermann, J. T. Delitz, P. Walter, H. Schulte-Schrepping, O. H. Seeck and H. Franz, J. Synchrotron Radiat., 2015, 22, 675–687 CrossRef CAS PubMed.
- A. P. Hammersley, S. O. Svensson, M. Hanfland, A. N. Fitch and D. Hausermann, High Press. Res., 1996, 14, 235–248 CrossRef.
- J. Rodríguez-Carvajal, Commission on Powder Diffraction (IUCr), Newsletter, 2001, 26, 12–19 Search PubMed.
- P. Juhás, T. Davis, C. L. Farrow and S. J. L. Billinge, J. Appl. Cryst., 2013, 46, 560–566 CrossRef.
- S. Çetinkaya, G. Khamidov, L. Özcan, L. Palmisano and S. Yurdakal, Front. Chem., 2022, 10 Search PubMed; J.-S. Lee, Y.-I. Lee, H. Song, D.-H. Jang and Y.-H. Choa, Curr. Appl. Phys., 2011, 11, S210–S214 CrossRef CAS; Y. Meng, D. Wang, Y. Zhao, R. Lian, Y. Wei, X. Bian, Y. Gao, F. Du, B. Liu and G. Chen, Nanoscale, 2017, 9, 12934–12940 RSC; Z. P. Tshabalala, T. P. Mokoena, M. Jozela, J. Tshilongo, T. K. Hillie, H. C. Swart and D. E. Motaung, ACS Appl. Nano Mater., 2021, 4, 702–716 CrossRef; H. B. Wu, H. H. Hng and X. W. Lou, Adv. Mater., 2012, 24, 2567–2571 CrossRef PubMed.
- S. Andersson and L. Jahnberg, Mater. Sci., 1963, 21, 413–426 Search PubMed.
- N. Masaki, S. Uchida, H. Yamane and T. Sato, Chem. Mater., 2002, 14, 419–424 CrossRef CAS.
Footnotes |
† Electronic supplementary information (ESI) available. See DOI: https://doi.org/10.1039/d3ma00968h |
‡ P. M. Schneider and C. M. Schott contributed equally to this work. |
|
This journal is © The Royal Society of Chemistry 2024 |