Continuous synthesis of block copolymer nanoparticles via telescoped RAFT solution and dispersion polymerisation in a miniature CSTR cascade†
Received
7th November 2022
, Accepted 9th December 2022
First published on 12th December 2022
Abstract
Miniaturised continuous-flow reactors offer a safe, economical, and scalable route to explore the synthesis of high-value chemical products. In the context of polymer synthesis, precisely defined and tuneable products can be prepared via reversible de-activation radical polymerisation (RDRP) techniques such as reversible addition-fragmentation chain-transfer (RAFT), for which tubular reactors are commonly reported. Herein, we present a miniature continuous stirred-tank reactor (CSTR) cascade for continuous-flow RAFT polymerisation with active mixing throughout, which is found to perform close to a theoretical CSTR cascade for the polymerisations considered in this study. The performance of the reactor is evaluated for both the aqueous solution RAFT polymerisation of N,N-dimethylacrylamide (DMAm) and the RAFT dispersion polymerisation of diacetone acrylamide using a poly(DMAm) macromolecular chain transfer agent (macro-CTA). It was determined that the residence time distribution (RTD) is important for informing the properties of the resulting polymers, with more CSTRs resulting in a narrower molar mass distribution. For particle synthesis by polymerisation-induced self-assembly (PISA), a series of block copolymers were prepared in separate batch and flow experiments for which the particles obtained were found to vary despite comparable molecular weights. Towards the development of a high throughput screening platform, a multi-stage, telescoped tubular-CSTR cascade reactor configuration was applied for inline macro-CTA synthesis and subsequent block extension. Differences in product properties between the processing methods used supports the idea that polymers are so-called ‘products-by-process’; indeed different polymer products can be accessed from the same chemistry through the application of alternative synthesis approaches.
1. Introduction
Reversible addition-fragmentation chain transfer (RAFT) polymerisation is a reversible de-activation radical polymerisation (RDRP) technique that affords access to more complex polymer architectures than free radical polymerisation. RAFT polymerisation in flow-reactors is well established,1–6 and is typically conducted in tubular systems. CSTRs and CSTR cascades are relatively unexplored in their application to RAFT polymerisation,7 with only few examples in the literature applied primarily to miniemulsion polymerisation.8,9 This is likely as a result of the inherently broad RTD of the CSTR which is known to broaden the molecular weight distribution of polymers prepared by RAFT.10 Despite this drawback, there are a number of benefits to the use of CSTRs – and especially CSTR cascades – which make their application to continuous-flow RAFT polymerisation worth exploring. Firstly, active mixing provided by an agitator is known to enhance mass transfer, which is particularly important in multiphasic systems. Secondly, using multiple CSTRs in series yields a narrower RTD, resulting in a more precisely defined product. In addition, higher conversion can be achieved with a smaller total reactor volume, and in the case of first order kinetics – such as for ideal RAFT polymerisations – the optimum design is conveniently that of equally sized CSTRs.11 Finally, CSTRs are a favourable choice for larger scale continuous processes, however engineering challenges associated with scale-up can make the transfer from the laboratory to manufacturing scale difficult. Adopting CSTRs at the discovery stage could therefore lead to more facile scale-up operations.
Until recently, lab-scale CSTRs have operated on the scale of litres, limiting their application in high-value product development where material is scarce or costly. The advent of new miniature CSTR cascades has facilitated the exploration of a variety of organic and inorganic chemical systems on the scale of millilitres where active mixing allowed for efficient handling of multiphasic chemical processes.12–19 A further benefit of continuous-flow operation is the potential to combine multiple synthesis stages into a single experiment using telescoped reactor configurations where sequential operations can be performed inline. Whilst the different stages of a CSTR cascade can be used to introduce components,9 alternative reactors that may be more suited to a particular reaction can just as easily be placed up- or down-stream.17,20 The convenience of performing multiple reaction steps consecutively is accompanied by an additional element of safety, reducing the chemical handling between reactions. These developments open the door to efficient multi-stage synthetic processes on the laboratory scale.
In the context of polymer synthesis where solids fractions are high and products often viscous, it is important to gain an understanding of the capabilities of these miniature CSTR cascade reactor systems. Herein we report the first example of such miniature CSTR cascades used for continuous-flow polymer synthesis. Their performance is evaluated for continuous-flow RAFT synthesis of polyacrylamides both in solution and in systems that are known to undergo polymerisation induced self-assembly (PISA).21 In principle, conducting a well-controlled RAFT polymerisation in the mini-CSTR cascade presents an opportunity to understand the importance of reactor characteristics on the performance of polymers synthesised in multiphasic systems. Finally, we apply a telescoped tubular-CSTR cascade system of reactors to perform both stages of the block copolymerisation in a single continuous-flow experiment.
2. Experimental
2.1. Materials
Monomers N,N-dimethylacrylamide (DMAm) (Merck, 99%, 500 ppm MEHQ) and diacetone acrylamide (DAAm) (Alfa Aesar, 99%) were used as received without further purification. 3-((((1-Carboxyethyl)thio)carbonothioyl)thio)propanoic acid (CCTP) (Boron Molecular) was used as chain transfer agent (CTA) and 4,4′-azobis(4-cyanovaleric acid) (ACVA) (Sigma Aldrich, ≥98%) as initiator. For dispersion polymerisations, the product of the solution polymerisation of DMAm and CCTP was used as a macromolecular chain transfer agent (macro-CTA) after dilution with HCl solution to a pH of 2.5. During telescoped reactions, DMAm solutions were prepared using pH 2.5 water so that inline adjustment was not required.
2.2. Reactor platform
The fReactor is a commercially available, modular, miniature scale (<10 mL) CSTR cascade comprising five actively mixed reaction cells heated and stirred by means of a standard stirrer hot-plate. A bespoke stirring device was constructed based on the design of Niño22 to offer more uniform mixing of each cell (see ESI†), and heating was provided directly to the heating block of the CSTR cascade with a pair of inset cartridge heaters. Temperature was controlled using a Eurotherm temperature controller and a K-type thermocouple inserted directly into the aluminium heating block. Back-pressurisation of the reactor was achieved using a custom compressed air system (see ESI† for details) to avoid the issue of clogging which is prevalent where standard back-pressure regulators are used for particle synthesis.
A ReaXus 6010R reciprocating pump (Teledyne ISCO) was used to deliver reagents from a single flask to the CSTR cascade via 1/16′′ stainless steel tubing. 8 cm lengths of 1/8′′ PFA tubing connected the five CSTRs. A 3-way valve between the reactor and pressurised (1.5 bar) waste container was used to manually extract samples for analysis. Each reactor was fitted with a K-type thermocouple in one of the spare 1/4-28 flat-bottomed ports to directly monitor the fluid temperature in real time. A schematic of the reactor platform is shown in Fig. 1.
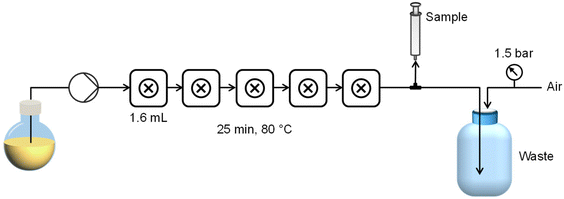 |
| Fig. 1 Reactor platform for polymer synthesis in a miniature five-CSTR cascade. All five reactors are heated from the same temperature-controlled heating block, with stirring provided by five pairs of neodymium magnets glued to 5 V DC computer fans located underneath the heating block. | |
2.3. Residence time distribution measurements
To measure the residence time distribution (RTD) of the system, a manual switching valve with a 10 μL sample loop was placed between a Teledyne ReaXus 6010R reciprocating HPLC pump and the reactor inlet. A flow cell was connected at the outlet to a Cary 60 UV-visible absorbance spectrophotometer via fibre optic cables. The reactor was filled with purified water and at least three additional reactor volumes of water were passed through the system to remove any residual material.
The flow-rate was then set at 0.35 mL min−1 and the spectrophotometer ‘zeroed’. Meanwhile, the sample loop was set to the ‘load’ position and filled with eosin Y tracer solution using a syringe. The dye was introduced to the system by moving the selector to ‘inject’, and the absorbance measurement simultaneously commenced. Recording of the absorption at the outlet started for a period of at least five reactor volumes. The same procedure was repeated when operating one, two, three, four, and five CSTRs separately. Eosin Y concentrations were adjusted such that peak absorbance did not exceed a value of 1.
RTDs were also measured for mixtures of glycerol and water used to represent the rheology of a series of polymer solutions. Poly(dimethylacrylamide) (PDMAm) homopolymers were synthesised in batch targeting degrees of polymerisation (DP) of 50, 100, 200, and 400, and their viscosity measured at shear rates ranging from 0.1 to 500 s−1 using an Anton Paar MCR 301 rheometer with a concentric cylinder spindle. Mixtures of glycerol and water were prepared and their viscosity measured to define a composition that would give equivalent rheological properties for subsequent RTD measurements (see ESI†). These glycerol/water mixtures were used according to the procedure above to conveniently obtain RTDs for one and five CSTRs at increased viscosities.
2.4. Macro-CTA synthesis by aqueous solution RAFT polymerisation of dimethylacrylamide (DMAm)
A typical procedure for batch synthesis of PDMAm macro-CTA (Scheme 1) with a target degree of polymerisation (DP) of 40 involves adding DMAm (17.16 g, 0.174 mol, 40 eq.), CCTP (1.10 g, 4.4 mmol, 1 eq.), and ACVA (0.12 g, 0.44 mmol, 0.1 eq.) to a round-bottom flask. Water (43.0 g) was added to make a 30% w/w solution. A magnetic stirrer bar was added before the flask was sealed and the reaction solution sparged with nitrogen for at least 30 minutes. The flask was lowered into a temperature-controlled oil bath at 80 °C for 25 minutes before being quenched by cooling and exposing to air. The product was used without purification for subsequent syntheses.
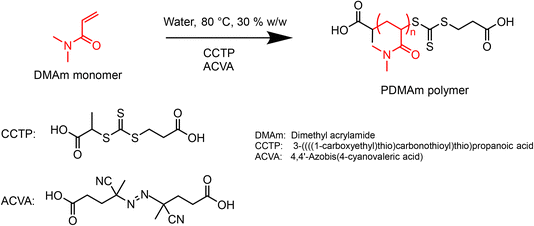 |
| Scheme 1 RAFT aqueous solution polymerisation of dimethylacrylamide (DMAm) at 30% w/w in the presence of a CCTP CTA using ACVA as initiator ([CTA] : [initiator] = 10 : 1) to produce a poly(dimethylacrylamide) (PDMAm)n macromolecular chain transfer agent. | |
For the equivalent continuous-flow reaction, a reaction mixture of the same composition was prepared in a sealed flask and sparged with nitrogen for at least 30 minutes. The reactor was prepared by filling with purified water and feeding through any trapped air bubbles at an arbitrary high flow rate. The downstream pressure was increased to 1.5 bar by opening the air inlet to the waste container, before the reactor was heated to the required set temperature. To target a residence time of 25 minutes, the flow rate of purified water was set to 0.35 mL min−1, requiring a set temperature of 92 °C to give a mean fluid temperature of 80 °C. The temperature was allowed to stabilise before the pump was switched from water to the reaction solution. After 3.5 residence times (87.5 min) the three-way valve downstream of the reactor was switched to the sample position and a sample manually extracted.
2.5. Aqueous dispersion RAFT polymerisation of diacetone acrylamide (DAAm) using PDMAm macro-CTA
A typical procedure for the batch synthesis of PDMAmn-b-PDAAmm (Scheme 2) for n = 100, m = 400 involves adding DAAm (7.00 g, 41.4 mmol, 400 eq.), the pre-prepared 30% w/w macro-CTA solution (3.50 g total, 1.05 g macro-CTA, 0.10 mmol, 1 eq.), ACVA (2.9 mg, 0.01 mmol, 0.1 eq.) to a round-bottom flask. Water (29.76 g) was added to make a 20% w/w solution. A magnetic stirrer bar was added before the flask was sealed and the reaction solution sparged with nitrogen for at least 30 minutes. The flask was lowered into a temperature-controlled oil bath at 70 °C for 50 minutes before being quenched by cooling and exposing to air.
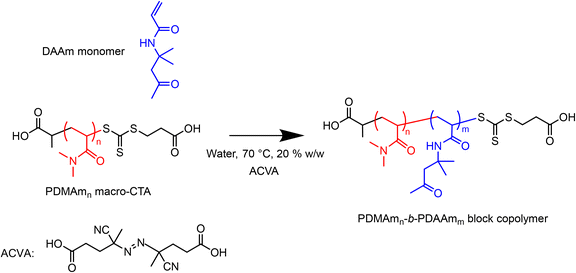 |
| Scheme 2 Poly(dimethylacrylamide)n-b-poly(diacetone acrylamide)m (PDMAmn-b-PDAAmm) nanoparticle synthesis via RAFT aqueous dispersion polymerisation of DAAm at 30% w/w in the presence of a PDMAmn macro-CTA using ACVA as initiator ([mCTA] : [initiator] = 10 : 1). | |
The equivalent flow reaction was performed by preparing a reaction solution of the same composition which was sealed and sparged with nitrogen for at least 30 minutes. The reactor was prepared by filling with purified water and feeding through any trapped air bubbles at an arbitrary high flow rate. The downstream pressure was increased to 1.5 bar by opening the air inlet to the waste container, before the reactor was heated to the required set temperature. To target a residence time of 50 minutes, the flow rate of purified water was set to 0.17 mL min−1, requiring a set temperature of 80.5 °C to give a fluid temperature of 70 °C. The temperature was allowed to stabilise before the pump was switched from water to the reaction solution. After 3.5 residence times (175 min) the three-way valve downstream of the reactor was switched to the sample position and a sample manually extracted.
2.6. Synthesis of poly(dimethylacrylamide)n-b-poly(diacetone acrylamide)m (PDMAmn-b-PDAAmm) nanoparticles via telescoped macro-CTA and RAFT dispersion polymerisation
With the aim of optimising a platform for continuous-flow synthesis of copolymer systems which undergo PISA, a stainless-steel tubular reactor (1 mL total volume, 1/16′′ OD, ID = 0.762 mm) was installed upstream of the CSTR cascade for inline macro-CTA synthesis and subsequent block extension (Fig. 2). The temperature of the tubular reactor was set by submerging it in a temperature-controlled oil bath, and the outlet fed into the first CSTR of the miniature CSTR cascade via a packed bed mixer. A typical procedure for performing the telescoped synthesis of PDMAm40-b-PDAAm400 is as follows. DMAm (0.989 g, 10.00 mmol, 40 eq.), CCTP (63 mg, 0.25 mmol, 1 eq.), and ACVA (7 mg, 0.03 mmol, 0.1 eq.) were added to a round-bottom flask (flask A). Water (12.02 g adjusted to pH 2.50) was added to make an 8.1% w/w solution. DAAm (17.60 g, 0.10 mol) and ACVA (7 mg, 0.03 mmol) were added to a second round-bottom flask (flask B). Water (62.40 g) was added to make a 22.0% w/w solution. Both flasks were sealed and sparged with nitrogen for at least 30 minutes. A gas-tight stainless-steel syringe was degassed by filling and emptying with three volumes of nitrogen before being filled with the contents of flask A and attached to a syringe pump (Chemyx Nexus 6000). The reactor was pressurised to 1.5 bar by opening the compressed air inlet to the waste container, and the pump started at a flow rate of 0.025 mL min−1 to target a residence time of 40 minutes. During the time taken for the tubular reactor to reach steady state (3 residence times, 120 minutes), purified water was pumped into the second inlet of the packed bed mixer prior to the first CSTR of the miniature CSTR cascade at a flow rate of 0.15 mL min−1 to target a second stage residence time of 50 minutes. Once the tubular reactor reached steady state, the second inlet was switched from water to the solution in flask B. The CSTR cascade was allowed to reach steady state (3.5 residence times, 175 minutes), before the outlet valve was switched to the sample position and a sample manually extracted. To control the DP of the copolymer whilst maintaining the same residence times and product weight fraction, the concentrations of monomer solutions in flasks A and B were adjusted according to a set of material balances (see ESI†).
 |
| Fig. 2 Telescoped tubular-CSTR cascade configuration for sequential RAFT solution polymerisation of DMAm and RAFT dispersion polymerisation of DAAm. The inlet to the tubular reactor contains a 30% w/w solution of DMAm, CCTP, and ACVA (40 : 1 : 0.1) and was heated in a temperature-controlled oil bath at 80 °C. Both the outlet of the tubular reactor and a second monomer inlet containing a solution of DAAm and ACVA (see ESI† for composition details) were fed through a packed bed mixer to the first CSTR of the cascade which was temperature-controlled to give a fluid temperature of 70 °C. | |
2.7. Material characterisation
2.7.1. Dynamic light scattering.
Particle size distributions were obtained using a Zetasizer Ultra (Malvern Panalytical). To avoid multiple scattering, samples were diluted with purified water to give a 0.1% w/w polymer dispersion, and sonicated for at least 2 minutes. Three analysis runs were performed for each sample at 25 °C with a detector angle of 173°.
2.7.2. Gel permeation chromatography.
An Agilent 1260 Infinity was used with a refractive index (RI) detector at 60 °C to measure the elution volume of samples dissolved in dimethylformamide (0.1% w/w LiBr) eluent at 1 mL min−1. Columns were calibrated using a set of poly(methyl methacrylate) standards with Mp values ranging from 800 to 2
200
000 g mol−1 to determine molar mass and dispersities of the polymer samples.
2.7.3. Nuclear magnetic resonance spectroscopy.
Monomer conversion was obtained from 1H NMR spectra measured using a 60 Hz benchtop NMR spectrometer (Magritek). PDMAm homopolymers were diluted with water and copolymer particles dissolved in CD3OD before analysis.
3. Results and discussion
3.1. Reactor development and characterisation
Several adaptations were made to the commercially available miniature CSTR cascade to enhance its performance for the synthesis of polymeric nanoparticles.
3.1.1. Mixing.
The mini-CSTR cascade is designed such that a single magnetic stirrer plate induces rotation of magnetic stirrers in each CSTR. When this was employed for systems with minor increases in viscosity, it was observed that stirrer bars would often become immobilised during the course of a polymerisation as particle concentrations and viscosity increased. A custom stirrer was instead designed based on that reported by Niño22 which successfully enabled more uniform stirring, and therefore resulted in reliable mixing within each of the five reactors across all viscosities and polymerisation solutions reported in this work.
3.1.2. Temperature.
Without a hotplate, it was also necessary to regulate temperature within the system by inserting two cartridge heaters into the aluminium block. Thermocouples were inserted into each reactor for direct measurement of the fluid temperature at different stages of the polymerisation. To ensure a full understanding of the conditions, the difference between the set temperature and solution temperature was recorded across a range of flow-rates. At a set temperature of 80 °C, the measured fluid temperatures were significantly lower due to the poor thermal conductivity of the PEEK reactor body. As a result, it was important to establish the required set temperature of the heating block to reach the target fluid temperature for each flow rate. At higher flow rates, a larger temperature gradient was observed across the five reactors, with the first being the coldest and the fifth being the hottest (Fig. S1†). For the fastest flow rate used in this work, the temperature difference is 10 °C at its largest between reactors one and two, and increases by less than 1 °C in each reactor thereafter. Before each reaction, the set temperature was adjusted so that the reaction temperature was reached by reactor three at the flow rate used. During polymer synthesis the temperatures were more variable as a result of the reaction exotherm evidenced by a notable temperature increase, however this was quickly dissipated to give a lower temperature in the proceeding CSTRs (Fig. S2†).
3.1.3. Residence time distribution.
Measurements of residence time distributions indicated fair agreement with theoretical distributions based on the tanks-in-series model (eqn (1)) for N well-mixed tanks albeit with some slight narrowing (Fig. S3†). We anticipate this can be attributed to the small lengths of tubing prior to the CSTR cascade (approximately 20 cm) and between each reactor (8 cm), which would provide additional volume to the reactor operating closer to plug flow. | 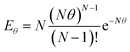 | (1) |
Eθ is the RTD function in dimensionless time (θ = t/τ, where t is time and τ is the residence time of the CSTR cascade). N is the number of tanks used in the cascade.
RTDs which are known to influence polymer characteristics10 can therefore be manipulated by changing the number of reactors in the cascade. During polymerisation, the reaction mixture is likely to increase in viscosity, which can have implications for the mixing performance and hence the RTD of the reactor. To assess the mixing performance four batches of PDMAm with target DPs of 50, 100, 200, and 400 were synthesised separately (in batch) to give 30% w/w solutions of homopolymer with increasing molecular weights and different macroscopic properties. These polymers were found to be Newtonian at shear rates between 0.1 to 500 s−1 and had viscosities ranging from 0.025 to 0.191 Pa s (Fig. S5†). To conveniently measure the RTD of the miniature CSTRs at viscosities corresponding to these polymers, four glycerol and water mixtures with increasing weight fractions of glycerol were identified which reflected the rheology of the four homopolymers (72% w/w for PDMAm50, 77% w/w for PDMAm100, 83% w/w for PDMAm200, and 90% w/w for PDMAm400). RTD measurements for these mixtures revealed that the mixing performance was largely unaffected by the increasing viscosity of the polymerisation, with only slight broadening of the RTD when a 90% w/w mixture of glycerol and water is used versus pure water (Fig. 3). Despite this, it is important to note that attempts to evaluate viscosities much higher than those shown here introduced challenges with stirrer bars decoupling from the driving magnets.
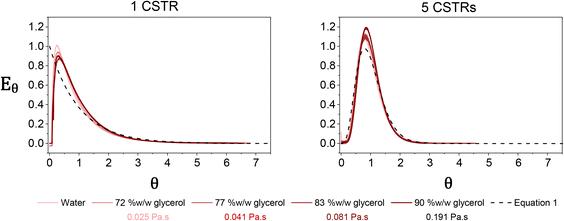 |
| Fig. 3 Residence time distributions measured in one (left) and five (right) miniature CSTRs using mixtures of glycerol and water to represent the rheology of different PDMAm polymers. Traces were obtained by monitoring the UV absorption at the reactor outlet after injecting 10 μL of tracer. Dashed lines represent the theoretical distributions based on eqn (1). | |
3.2. Aqueous solution RAFT polymerisation using a miniature CSTR cascade
The four batch polymers were prepared in equivalent continuous-flow reactions using the miniature CSTR cascade, with high conversion and comparable Mn values achieved (Table 1). During polymer synthesis the temperature increased much more rapidly due to the exotherm inherent to the polymerisation. Indeed, the exotherm could typically be observed at residence times of 5 minutes and above, which helped to qualitatively identify the reactor in which most of the polymerisation occurred (Fig. S2†).
Table 1 Summary of polymer properties for 30% w/w solution PDMAm prepared in batch and flow using the miniature CSTR cascade for target DPs of 50, 100, 200, and 400. Average reaction/residence time = 25 minutes. [CTA]
:
[initiator] = 10
:
1
Polymer |
Conversion (%) |
M
n (g mol−1) |
Đ
|
Batch |
Flow |
Batch |
Flow |
Batch |
Flow |
PDMAm50 |
98 |
96 |
2900 |
5200 |
1.25 |
1.59 |
PDMAm100 |
99 |
97 |
10 500 |
10 700 |
1.19 |
1.44 |
PDMAm200 |
97 |
92 |
25 400 |
24 700 |
1.09 |
1.38 |
PDMAm400 |
99 |
92 |
47 900 |
48 100 |
1.10 |
1.34 |
Importantly, the MWDs of the polymers prepared in flow are much broader as a direct result of the RTD within the reactor (Fig. 4), even when using five CSTRs in series. In batch where there is no RTD, the dispersity reduces for larger DP values to a minimum of approximately 1.10. This reduction due to the chemistry is also apparent across the four samples prepared in flow, but the overall molar mass dispersities are higher, ranging from 1.59 for PDMAm50 to 1.34 for PDMAm400. Hence there is a clear influence of the RTD on the dispersity of the products, however this does not overshadow the potential to observe trends associated with the chemistry. This is important, since the RTD is easily measured, meaning the effects on the polymer are predictable and so may be disregarded where the benefits in productivity of flow are more important than the final molar mass distribution. In principle, the method also offers a simplified opportunity to tune the shape of the MWD if desired without having to manipulate the chemistry.23
 |
| Fig. 4 Comparison of aqueous solution RAFT PDMAm polymers prepared in batch versus continuous-flow in a miniature CSTR cascade. All polymers were prepared at 30% w/w, 80 °C, 25 minutes. | |
To further investigate the effect of RTD on polymerisation, the aqueous solution polymerisation of DMAm was attempted (target DP = 100) with different numbers of CSTRs to manipulate the RTD. As expected, a narrowing in MWD is observed as the number of CSTRs is increased (Fig. 5), reaching a minimum of 1.44 (Table 2). Interestingly, when a single CSTR is used, a significant shoulder is observed, suggesting the presence of a second population of higher molecular weight material. This is a direct consequence of the RTD acting on the chemistry, where within one CSTR, the RTD measurements (Fig. S3†) show that some of the material recirculates well beyond the mean residence time. The monomers chosen (acrylamides) tend to terminate by recombination at long reaction times, where the probability of terminative events is much higher. This method of termination thus likely results in the large MW shoulder as a result of two polymer chains combining to give a single chain with double the molecular weight.
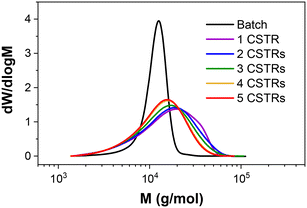 |
| Fig. 5 MWDs for different CSTR cascade configurations versus the batch MWD for the aqueous solution RAFT polymerisation of 30% w/w PDMAm100 at 80 °C. Average reaction/residence time = 25 minutes. [CTA] : [initiator] = 10 : 1. | |
Table 2 Summary of polymer properties for 30% w/w PDMAm prepared via solution RAFT polymerisation using different numbers of reactors in the CSTR cascade versus batch. Average reaction/residence time = 25 minutes. [CTA]
:
[initiator] = 10
:
1
Sample |
Conversion (%) |
M
n (g mol−1) |
Đ
|
Batch |
97 |
10 700 |
1.11 |
1 reactor |
83 |
11 700 |
1.60 |
2 reactors |
96 |
11 800 |
1.58 |
3 reactors |
97 |
11 200 |
1.53 |
4 reactors |
97 |
10 700 |
1.45 |
5 reactors |
97 |
10 700 |
1.44 |
A further experiment to investigate this phenomenon was conducted whereby samples were collected from a similar synthetic formulation at different time points after feeding had started at a set flow-rate. Where one CSTR was used, the formation of this second higher MW population is clearly observed (Fig. 6). For three CSTRs (Fig. S6†) the irregular MWDs over the course of the experiment suggest the persistence of the second population, which makes obtaining steady state difficult on a reasonable timescale. The narrower RTD of the five CSTR configuration reduces the significance of such terminative events, and the reactor can quickly achieve steady state (Fig. 6). In addition, reaching a stable steady state in under three residence times (75 min) confirms this as an appropriate equilibration time, and suggests that continuous manufacture is feasible.
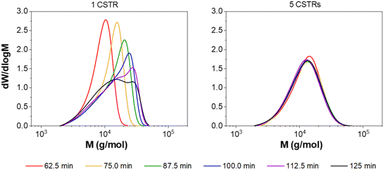 |
| Fig. 6 MWDs obtained at different time points for the aqueous solution RAFT polymerisation of DMAm at 80 °C in either one (left) or five (right) CSTRs. Average residence time of 25 minutes, [CTA] : [initiator] = 10 : 1. | |
3.3. Synthesis of PDMAm-b-PDAAm via RAFT dispersion polymerisation
Since the molecular weight dispersity obtained in the CSTR cascade is typically broad on account of its RTD, it might be more appropriate to use a traditional tubular reactor for continuous synthesis when minimising dispersity is more important. However, the lack of agitation afforded by tubular reactors can lead to gradual foulding,4 which makes the CSTR cascade a valuable tool for polymerisations involving multiple phases, where mass transfer and phase stability are important. One such heterogeneous system is the aqueous RAFT dispersion polymerisation of diacetone acrylamide (DAAm) in the presence of a PDMAm macro-CTA which forms nanoparticles as a result of polymerisation-induced self-assembly (PISA).21 Using a PDMAm40 macro-CTA prepared in batch, a series of dispersion polymers were synthesised in equivalent batch and flow reactions using the miniature CSTR cascade to compare their performance where different morphologies might be obtained.21 For each polymer, simultaneous batch and flow reactions were performed from the same reaction solution to target the following block copolymers: PDMAm40-b-PDAAm100, PDMAm40-b-PDAAm200, PDMAm40-b-PDAAm300, and PDMAm40-b-PDAAm400. Table 3 summarises the properties of the resulting products. Molecular weight measurements of each product again revealed a larger molar mass dispersity from the CSTR cascade likely as a consequence of the same RTD effects observed in the homopolymer synthesis, however values of Mn were broadly comparable for each (Fig. 7). As the target DP increased, the reaction conversion achieved in batch reduced, accounting for the lower value of Mn for the batch PDMAm40-b-PDAAm400 where conversion was only 84% compared to 94% in flow. This may be attributed to the enhanced heat and mass transfer achieved in continuous-flow which becomes more important at lower initiator concentrations.
Table 3 Characterisation of block copolymers prepared via RAFT dispersion polymerisation using three synthetic approaches. Macro-CTA is prepared either in batch, or inline using a tubular reactor. Block copolymerisation is performed either in batch or using the mini-CSTR cascade. [CTA]
:
[initiator] = 10
:
1. Particle sizes reported based on number-average values. Multimodal particle size distributions are indicated by the multiple values given
Polymer |
Synthesis method |
Conversion (%) |
M
n (g mol−1) |
Đ
|
Particle size (nm) |
Macro-CTA |
Copolymerisation |
PDMAm40-b-PDAA100 |
Batch |
Batch |
100 |
21 400 |
1.18 |
47/92/235 |
Batch |
CSTR cascade |
98 |
17 300 |
1.36 |
16/38 |
Tube |
CSTR cascade |
98 |
18 600 |
1.39 |
12/33 |
PDMAm40-b-PDAA200 |
Batch |
Batch |
98 |
38 300 |
1.19 |
82/307 |
Batch |
CSTR cascade |
97 |
39 200 |
1.37 |
65 |
Tube |
CSTR cascade |
96 |
33 500 |
1.66 |
164/342 |
PDMAm40-b-PDAA300 |
Batch |
Batch |
93 |
53 600 |
1.18 |
236 |
Batch |
CSTR cascade |
97 |
51 100 |
1.57 |
97 |
Tube |
CSTR cascade |
97 |
43 100 |
1.48 |
104 |
PDMAm40-b-PDAA400 |
Batch |
Batch |
84 |
58 000 |
1.22 |
280 |
Batch |
CSTR cascade |
94 |
65 700 |
1.57 |
124 |
Tube |
CSTR cascade |
96 |
63 100 |
1.63 |
300/1623 |
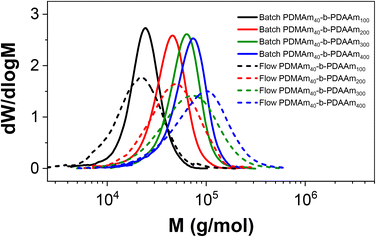 |
| Fig. 7 Molecular weight distributions of PDMAm40-b-PDAAmm copolymers prepared simultaneously in batch and a miniature CSTR cascade for a reaction time of 50 minutes at 70 °C. The same batch synthesised PDMAm40 macro-CTA was used in each case. [CTA] : [initiator] = 10 : 1. | |
Although the Mn values and monomer conversion of the resulting batch and flow polymers are similar, there are large differences in properties of the corresponding particles obtained. According to DLS measurements (Fig. 8), the particles obtained in flow for these systems are smaller than those prepared in a batch process, indicating that the particle self-assembly is influenced by the hydrodynamics of the reactor. Number-average distributions are used to demonstrate the major particle populations obtained, however intensity-average distributions (Fig. S7†) indicated the presence of larger particles (visible in the long ‘tails’ of the size distributions). These minor populations contribute to broadening of the particle size distributions and are likely a further consequence of the reactor RTD. As a result of the inherent RTD, each CSTR will contain material at many different stages of the reaction. Since these particles are known to undergo morphological transitions during growth, it is likely that the CSTRs provide a unique environment in which particles with a broad range of shapes and sizes coexist, particularly in the first few reactors. On this basis, it becomes challenging to suggest a precise explanation for the observed differences in particle structure in the absence of a detailed mechanistic understanding, which is beyond the scope of this work.
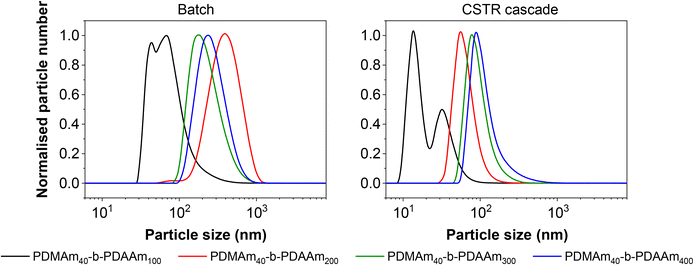 |
| Fig. 8 Particle size distributions of PDMAm40-b-PDAAmm copolymers prepared simultaneously in batch (left) and a miniature CSTR cascade (right) for a reaction time of 50 minutes at 70 °C. The same batch synthesised PDMAm40 macro-CTA was used in each case. [CTA] : [initiator] = 10 : 1. | |
3.4. Telescoped RAFT synthesis of PDMAm macro-CTA and copolymerisation in a tubular-CSTR cascade configuration
Since the self-assembly behaviour of a given polymer system is complex and difficult to predict, we suggest an experimental approach that utilises the benefits of continuous-flow chemistry to enable high-throughput screening of the polymer dispersions obtained from these various systems. Towards this end, the above acrylamide block copolymers were sequentially synthesised in a telescoped reactor system comprising a 1 mL tubular coil followed by the five-stage CSTR cascade to perform both parts of the block copolymerisation in a single experiment. Four products were targeted with varying copolymer block lengths from the same target macro-CTA. In each case, the tubular reactor was used to prepare a PDMAm40 macro-CTA via solution RAFT polymerisation, to which a solution of DAAm was added in the first stage of the mini-CSTR cascade for chain extension with a second block. For the macro-CTA syntheses at 30% w/w above, a residence time of 25 minutes was sufficient to reach >95% conversion, and so initially the residence time in the tubular reactor was set to 25 minutes. To maintain the same residence time and final concentration for each reaction, the copolymer block length was manipulated by adjusting the concentration (% w/w) of the reaction solutions. For PDMAm40-b-PDAAm400 the required macro-CTA concentration was therefore 5.1% w/w, whilst for PDMAm40-b-PDAAm100 the required macro-CTA concentration was 17.2% w/w. The polymer dispersions collected appeared very viscous and gel-like, particularly for the higher molecular weight copolymers. Surprisingly, this did not cause any significant operational challenges within the reactor. This is likely due to the shear thinning behaviour observed in gel-like copolymer dispersions synthesised by traditional24 or RAFT aqueous dispersion polymerisation.25 Analysis of the particle characteristics indicated the formation of large nano-scale and even micro-scale structures (Fig. S8†). This often indicates the presence of non-spherical nano-objects during RAFT dispersion polymerisation,21,26 but may also indicate insufficient conversion in preparing the macro-CTA or insufficient mixing of the second monomer with the macro-CTA solution. Both of these issues may allow uncontrolled free-radical polymerisation to proceed. To ensure differences in product properties were not a consequence of this uncontrolled radical polymerisation a longer 40 minute residence time was used for the PDMAm40 macro-CTA synthesis to guarantee high DMAm conversion (as determined by 1H NMR to be >90%) and a pre-mixer was included before the first CSTR to ensure the PDMAm and DAAm solutions were well mixed.
Once the optimised set up was used for these experiments, the resulting polymers were similar to those prepared using a batch macro-CTA (see Table 3 and Fig. 9). However, there were clear differences in the properties of the self-assembled polymer nano-objects (Fig. 10), and a small population of micro-scale objects persisted for the telescoped synthesis of PDMAm40-b-PDAAm400.
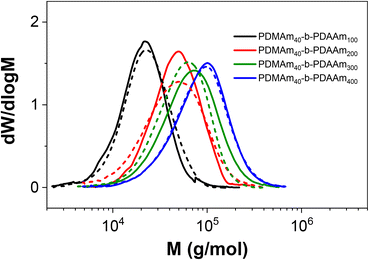 |
| Fig. 9 Molecular weight distributions of PDMAm40-b-PDAAmm copolymers prepared in a miniature CSTR cascade using a batch macro-CTA (solid lines) versus a telescoped configuration with macro-CTA prepared inline using a tubular reactor (dashed lines). PDMAm40 macro-CTA was prepared at 80 °C for 40 minutes, with copolymerisation at 70 °C for 50 minutes. [CTA] : [initiator] = 10 : 1. | |
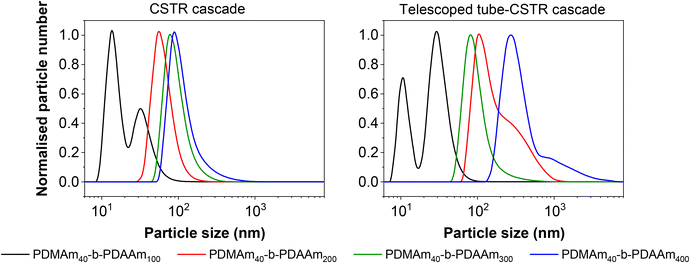 |
| Fig. 10 Particle size distributions of PDMAm40-b-PDAAmm copolymers prepared via RAFT dispersion polymerisation in a miniature CSTR cascade using a batch macro-CTA (left) versus in a miniature CSTR cascade with a macro-CTA prepared upstream in a telescoped tubular reactor (right). PDMAm40 macro-CTA was prepared at 80 °C for 40 minutes, with copolymerisation at 70 °C for 50 minutes. [CTA] : [initiator] = 10 : 1. | |
4. Conclusions
Alongside the growing demand for new functional materials comes a growing cost of the materials required to develop them. Continuous-flow chemistry offers an avenue to explore the synthesis of valuable chemical products which is economical, safe, and scalable. We have demonstrated the first instance of a reversible de-activation radical polymerisation polymerisation performed in CSTRs on a miniature scale for both single phase systems and indeed for more complex multi-phasic polymerisations.
The miniaturised reactor had characteristics which agreed well with the established theory of CSTR cascades, and reliably handled the preparation of block copolymers via both RAFT solution and dispersion polymerisation. Clear differences in molar mass dispersity between equivalent products prepared in batch were attributed to the broad residence time distribution of the flow reactor for both solution and dispersion systems. During PDMAmn-b-PDAAmm particle synthesis, the complex dynamics of particle nucleation and growth within a mixed flow reactor resulted in particle characteristics which were different to those obtained in batch despite relatively similar molar mass values. For a telescoped process, the integration of an inline tubular reactor for macro-CTA synthesis (via solution RAFT) produced polymers with very similar molar mass characteristics to those prepared from a stock batch of macro-CTA. Despite the similarity of the polymer properties, the sensitivity of the particle characteristics to the synthetic method was indicated by the differences in the particle size distributions. These results indicate the potential for products with different macroscopic behaviour to be prepared from the same chemical inputs, and implies that new functional materials may be obtained by taking alternative synthetic approaches. The technology developed here offers a unique approach to the high-throughput exploration of multiphasic polymerisations. The prevalence of CSTRs as a manufacturing tool means that the developed system also presents an opportunity to gather early insights for scale-up operations. We anticipate several challenges for this, which we intend to explore in future studies.
Author contributions
PMP – data curation, investigation, methodology, writing-original draft, writing-review and editing; GG – investigation; STK – investigation, data curation, writing-review and editing; OJC – supervision, writing-review and editing; NK – conceptualisation, supervision, writing – review and editing; NJW – conceptualisation, funding acquisition, supervision, project administration, writing – review and editing.
Conflicts of interest
There are no conflicts to declare.
Acknowledgements
The EPSRC are thanked for providing a studentship for PMP. The EPSRC are also thanked for supporting STK and NJW (EP/V055089/1); and OJC (EP/V027646/1).
References
- C. Diehl, P. Laurino, N. Azzouz and P. H. Seeberger, Macromolecules, 2010, 43, 10311–10314 CrossRef CAS.
- C. H. Hornung, X. Nguyen, G. Dumsday and S. Saubern, Macromol. React. Eng., 2012, 6, 458–466 CrossRef CAS.
- J. Peng, C. Tian, L. Zhang, Z. Cheng and X. Zhu, Polym. Chem., 2017, 8, 1495–1506 RSC.
- S. Parkinson, N. S. Hondow, J. S. Conteh, R. A. Bourne and N. J. Warren, React. Chem. Eng., 2019, 4, 852 RSC.
- M. Rubens, J. H. Vrijsen, J. Laun and T. Junkers, Angew. Chem., Int. Ed., 2019, 58, 3183–3187 CrossRef CAS PubMed.
- S. T. Knox, S. J. Parkinson, C. Y. P. Wilding, R. A. Bourne and N. J. Warren, Polym. Chem., 2022, 13, 1576–1585 RSC.
- X. Li, E. Mastan, W. Wang, B. Li and S. Zhu, React. Chem. Eng., 2016, 1, 23–59 RSC.
- W. W. Smulders, C. W. Jones and F. J. Schork, Macromolecules, 2004, 37, 9345–9354 CrossRef CAS.
- W. W. Smulders, C. W. Jones and F. J. Schork, AIChE J., 2005, 51, 1009–1021 CrossRef CAS.
- M. H. Reis, T. P. Varner and F. A. Leibfarth, Macromolecules, 2019, 52, 3551–3557 CrossRef CAS.
- K. G. Denbigh, Chem. Eng. Sci., 1961, 14, 25–35 CrossRef CAS.
- D. L. Browne, B. J. Deadman, R. Ashe, I. R. Baxendale and S. V. Ley, Org. Process Res. Dev., 2011, 15, 693–697 CrossRef CAS.
- Y. Mo and K. F. Jensen, React. Chem. Eng., 2016, 1, 501–507 RSC.
- I. Lignos, H. Ow, J. P. Lopez, D. McCollum, H. Zhang, J. Imbrogno, Y. Shen, S. Chang, W. Wang and K. F. Jensen, ACS Appl. Mater. Interfaces, 2020, 12, 6699–6706 CrossRef CAS.
- I. Lignos, Y. Mo, L. Carayannopoulos, M. Ginterseder, M. G. Bawendi and K. F. Jensen, React. Chem. Eng., 2021, 6, 459–464 RSC.
- M. R. Chapman, M. H. T. Kwan, G. King, K. E. Jolley, M. Hussain, S. Hussain, I. E. Salama, C. G. Niño, L. A. Thompson, M. E. Bayana, A. D. Clayton, B. N. Nguyen, N. J. Turner, N. Kapur and A. J. Blacker, Org. Process Res. Dev., 2017, 21, 1294–1301 CrossRef CAS.
- J. Morvan, T. McBride, I. Curbet, S. Colombel-Rouen, T. Roisnel, C. Crévisy, D. L. Browne and M. Mauduit, Angew. Chem., Int. Ed., 2021, 60, 19685–19690 CrossRef CAS.
- K. Y. Nandiwale, T. Hart, A. F. Zhart, A. M. K. Namibar, P. T. Mahesh, Y. Mo, M. J. Nieves-Remacha, M. D. Johnson, P. García-Losada, C. Mateos, J. A. Rincón and K. F. Jensen, React. Chem. Eng., 2022, 7, 1315–1327 RSC.
- D. Francis, A. J. Blacker, N. Kapur and S. P. Marsden, Org. Process Res. Dev., 2022, 26, 215–221 CrossRef CAS.
- W. Li, M. Jiang, M. Liu, X. Ling, Y. Xia, L. Wan and F. Chen, Chem. – Eur. J., 2022, 28, e202200700 CAS.
- S. J. Byard, M. Williams, B. E. McKenzie, A. Blanazs and S. P. Armes, Macromolecules, 2017, 50, 1482–1493 CrossRef CAS.
-
C. G. Niño, Optimisation of flow chemistry: tools and algorithms, PhD thesis, University of Leeds, 2020 Search PubMed.
- R. Whitfield, N. P. Truong, D. Messmer, K. Parkatzidis, M. Rolland and A. Anastasaki, Chem. Sci., 2019, 10, 8724–8734 RSC.
- G. Wang, H. Fan, G. Jiang, W. Li, Y. Ye, J. Liu, X. Kong, Z. Zhong and F. Qian, Mater. Express, 2020, 10, 657–662 CrossRef CAS.
- R. Verber, A. Blanazs and S. P. Armes, Soft Matter, 2012, 38, 9915–9922 RSC.
- S. Parkinson, S. T. Knox, R. A. Bourne and N. J. Warren, Polym. Chem., 2020, 11, 3465–3474 RSC.
|
This journal is © The Royal Society of Chemistry 2023 |