DOI:
10.1039/D3PY00183K
(Paper)
Polym. Chem., 2023,
14, 2803-2819
Exploring SiliaCat Pd-DPP as a recyclable heterogeneous catalyst for the multi-batch direct heteroarylation polymerization for P(NDI2OD-T2)†
Received
18th February 2023
, Accepted 12th May 2023
First published on 16th May 2023
Abstract
Donor–acceptor (D–A) conjugated polymers like P(NDI2OD-T2) are important constituents of the active layer of energy conversion devices like all-polymer solar cells. A cost-effective and environmentally amiable pathway for the synthesis of this and similar D–A polymers is highly desirable for the large-scale production of these materials. In this report we have combined two cost-effective approaches, namely, direct heteroarylation polymerization (DHAP) and a recyclable heterogeneous catalyst (SiliaCat Pd-DPP), for the multi-batch synthesis of P(NDI2OD-T2). The general applicability of the approach was first established with a series of conjugated small molecules based on naphthalene diimide and bithiophene derivatives (N1 to N6). The Meitlis hot filtration test and inductively coupled plasma-optical emission spectroscopy (ICP-OES) were conducted to estimate the quantity of leached palladium in the final reaction product. Catalyst recyclability up to five cycles was demonstrated for N1 with <2 ppm leached palladium impurity. A comparison was made with the homogeneous catalyst Pd2dba3 which indicated the presence of much higher levels of palladium impurity in the final product. The polymerization of P(NDI2OD-T2) was demonstrated using the regular monomers (NDIOD-Br2 and bithiophene) and also using a modified monomer with activated bithiophene (naphthalene diimide substituted bithiophene) under DHAP conditions employing SiliaCat Pd-DPP as the recyclable heterogeneous catalyst. The modified monomer proved to be amenable to DHAP polymerization using SiliaCat Pd-DPP as the heterogeneous catalyst, which could be consecutively reused four times with reproducible molecular weights in the range of Mn/Mw: 27.1/49.0 to 33.5/61.3.
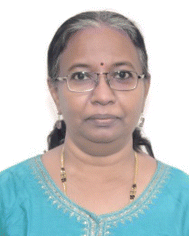 Asha S. K. | Asha Syamakumari is a scientist and chair of the Polymer Science & Engineering Division at CSIR National Chemical Laboratory (CSIR-NCL), Pune, India. She did her PhD from the Indian Institute of Science, Bangalore with Professor S. Ramakrishnan during 1994–2000. Subsequently, she worked as a postdoctoral Research Associate in the group of Professor E. W. Meijer at the Eindhoven University of Technology, The Netherlands. Upon returning to India, she worked as a polymer scientist at JFWTC-GE, Bangalore for a year. She began her research career as a scientist at CSIR-NIIST, Trivandrum, Kerala in 2004. In 2008 she moved to CSIR-NCL, Pune, where she established her research group and for the last 15 years has been working on the development of polymer-based materials with potential applications in the opto-electronic industry, as biosensors, for additive manufacturing, etc. She has published more than 65 papers in reputed international journals. She has served on the Editorial Advisory Board of Macromolecules (2018–2020) and is currently serving as a member of the Editorial Advisory Board, Journal of Macromolecular Science, Part A: Pure and Applied Chemistry (Taylor & Francis Group Journal). |
Introduction
Organic conjugated polymers and oligomers have been extensively explored in electronic applications like organic solar cells, organic field effect transistors, supercapacitors, light-emitting diodes, etc.1–9 Naphthalene diimide based polymers and conjugated oligomers have been widely used as non-fullerene acceptors in electronic devices.10–16 The commercialization potential of these organic conjugated materials depends on the ability to synthesize and scale them up using a cost-effective and sustainable approach. The conventional C–C bond forming reactions like the Stille, Suzuki, and Negishi coupling reactions, which are traditionally used for the synthesis of organic conjugated polymers, are associated with significant drawbacks like the multistep synthesis (pre-functionalization) of the monomer and its purification.17 In this regard, Toshio Itahara et al. developed a novel synthetic strategy for C–C bond formation using aromatic C–H bonds with an aromatic halide.18 This synthetic strategy was extended further for synthesizing organic conjugated polymers via the direct heteroarylation polymerization (DHAP) method. DHAP is a promising method for the synthesis of organic conjugated polymers as it does not require pre-functionalization of the monomer, thereby reducing the number of steps required.19–23 The by-products produced (e.g. HCl, HBr and HI) in the DHAP method are more atom economically favourable and easy to remove compared to the side products produced in Stille polycondensation (trialkyltin halide).24 These advantages of DHAP make it a cost-effective, eco-friendly and attractive method with minimum environmental impact.25
One of the most critical drawbacks of conventional and DHAP synthetic approaches is the use of rare and expensive Pd metal catalysts.26 The Pd-based homogeneous catalysts have some inherent drawbacks such as limited reusability, high cost and also rather high levels of palladium contamination in the reaction product caused by leaching. The presence of the residual Pd catalyst as a contaminant in the conjugated polymer reduces the performance of electronic devices made using them.27–29 As an alternative to the expensive palladium based catalysts, low-cost and sustainable metal catalysts like those based on copper have also been explored for direct heteroarylation polymerization, notably by the research group of Barry Thompson.30–32 Intense research efforts to develop efficient heterogeneous palladium catalysts for application as reusable solid catalysts have been ongoing for quite some time.33–37 For instance, Hong-Zheng Chen et al. used a ligand-free Pd/C heterogeneous catalyst to synthesize organic conjugated polymers via Suzuki, Heck and Stille coupling polymerization processes. They observed that by Suzuki and Heck polymerization, the polymers synthesized using a heterogeneous catalyst exhibited higher molecular weights and better yields along with lower contamination by residual Pd compared to the same polymers synthesized by the homogeneous catalyst Pd(PPh3)4.35 However, recycling the used Pd/C proved to be challenging. Toshio Koizumi et al. reported the successful application of Pd/C for the direct arylation polycondensation of various classes of PEDOTF8 and P3HT polymers with a considerable molar mass of the polymers.38,39 Reuse of Pd/C was not reported in these examples.
When it comes to the reuse of a heterogeneous catalyst, a new catalyst (SiliaCat Pd-DPP) was developed by SiliCycle Incorporation and used in several fundamental transformations in organic chemistry (aryl halide to boronic acid pinacol esters, selective hydrogenation and O-debenzylation).40–42 This catalyst is air-stable and does not require laborious handling under a carefully controlled atmosphere like that of a glove box, making it very feasible for handling industrial-scale reactions.43 The SiliaCat Pd-DPP catalyst (structure shown in Fig. 1) consists of a diphenylphosphine based Pd(II) species covalently bound to an organosilica matrix and has successfully demonstrated C–C bond formation of conjugated small molecules and organic conjugated polymers via Suzuki, Sonogashira, Heck, and Stille polymerizations.43–45 The first report of the application of the SiliaCat Pd-DPP catalyst for the synthesis of a conjugated polymer (based on diketopyrrolopyrrole) by the direct heteroarylation route appeared in 2018.37 It reported an Mn value of 10
900 g mol−1 upon using 10 mol% of the supported SiliaCat Pd-DPP catalyst, which was comparable to the Mn afforded by using a homogeneous catalyst for the synthesis of the same polymer. This was followed by a report from the research group of Barry Thompson in 2022 who synthesized the conjugated polymer PEDOTF based on 3,4-ethylenedioxythiophene and 9,9′-dioctylfluorene via the DHAP method using the SiliaCat Pd-DPP catalyst and disclosing for the first time the recyclability of the catalyst up to five cycles.46
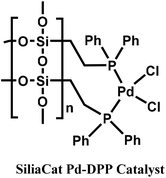 |
| Fig. 1 Structure of the SiliaCat Pd-DPP catalyst. | |
In this context, our research group has been engaged in the development of versatile acceptor polymers based on naphthalene diimide, by conventional and DHAP methods in the presence of Pd-based homogeneous catalysts (Pd2dba3 and Pd(PPh3)2Cl2).47–51 We had reported a new A–B–A monomer design for the synthesis of the commercially important naphthalene diimide-based polymer poly{[N,N′-bis(2-octyldodecyl)-naphthalene-1,4,5,8-bis(dicarboximide)-2,6-diyl]-alt-5,5′-(2,2′-bithiophene)} or P(NDI2OD-T2) also known as Polyera ActivInk N2200 following the atom economical DHAP route by using tris-(dibenzylideneacetone)dipalladium(0) (Pd2dba3) as the homogeneous catalyst.51
In our ongoing pursuit for more sustainable development of important conjugated polymers, we have focused on synthesizing the P(NDI2OD-T2) polymer by DHAP using SiliaCat Pd-DPP as a heterogeneous catalyst in this report. The optimization of the DHAP reaction conditions for catalyst recyclability was conducted with naphthalene diimide-based conjugated small molecules (N1 to N6) and further extended to the P(NDI2OD-T2) polymer via two different monomer routes. Fig. 2 summarizes the synthetic scheme for the synthesis of P(NDI2OD-T2) polymers using our A–B–A monomer design as well as the regular monomer based on 2,2′-bithiophene. To the best of our knowledge, this is the first report where the P(NDI2OD-T2) polymer has been developed by the DHAP route using a heterogeneous (SiliaCat Pd-DPP) catalyst and the reusability of the catalyst up to five consecutive cycles was demonstrated. The quantitative estimation of Pd leaching was carried out using inductively coupled plasma-optical emission spectroscopy (ICP-OES) analysis. An in-depth analysis of the P(NDI2OD-T2) polymer synthesized using the reused SiliaCat Pd-DPP catalyst in consecutive cycles was conducted by gel permeation chromatography, 1H NMR spectroscopy, thermogravimetric analysis and differential scanning calorimetry. The presented work is a green and sustainable approach towards synthesizing organic conjugated polymers with minimal contamination of the Pd metal after reusing the catalyst in a number of consecutive cycles.
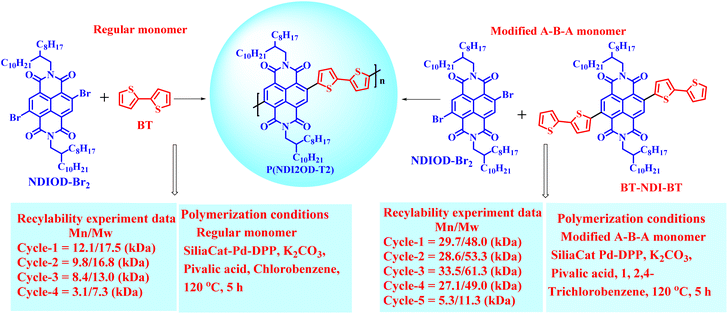 |
| Fig. 2 Schematic representation summarizing the synthesis of the P(NDI2ODT2) polymer by different monomers demonstrating the reusability of the SiliaCat Pd-DPP heterogeneous catalyst. | |
Results and discussion
Naphthalene diimide based conjugated small molecules (N1 to N6)
The feasibility of the application of the commercial SiliaCat Pd-DPP heterogeneous catalyst for synthesizing donor–acceptor (D–A) conjugated polymers was verified with preliminary studies using conjugated small molecules based on naphthalene diimide. A series of conjugated molecules N1 to N6 were designed with various substituted thiophene-based donor molecules (A1 to A6) to react with NDIOD-Br2via the direct heteroarylation route. Scheme 1 shows the synthetic scheme for the reaction of NDIOD-Br2 with various thiophene molecules. Evidence from the literature suggests that it is difficult to predict the extent of C–H activation on thiophene due to the presence of either electron-donating or electron-withdrawing substituents.52 This is because nucleophilic substituents have a more favorable interaction energy and a higher distortion energy, whereas electron-withdrawing substituents have a small interaction energy and a lower distortion energy.52 The details of optimization reactions performed with different solvents and bases are tabulated in Table S1.†Scheme 1 summarizes the optimized conditions that were finalized for the synthesis of the conjugated small molecules N1 to N6. In brief, the optimized conditions involved reacting 1 eq. of NDIOD-Br2 with 2 eq. of A1 (A1 to A6), 1 eq. of pivalic acid, and 5 mol% of the SiliaCat Pd-catalyst. The highest yield was obtained using K2CO3 as the base and chlorobenzene as the solvent; the observed yields are based on one reaction per sample. The detailed synthetic procedure and characterization for naphthalene diimide-based conjugated small molecules (N1 to N6) are outlined in the ESI (S1–S11 and Fig. S1–S28†).
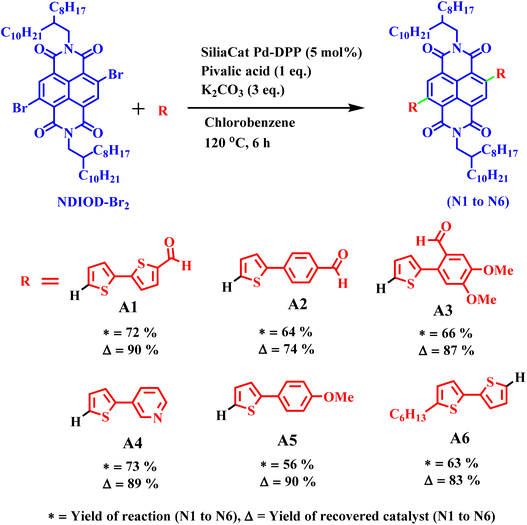 |
| Scheme 1 Synthesis of naphthalene diimide conjugated small molecules (N1 to N6) by the direct heteroarylation method using the SiliaCat Pd-DPP catalyst. | |
From Scheme 1, based on the best yields for both the product and the recovered catalyst, N1 was chosen for further studies involving catalyst recyclability. Scheme 2 summarizes the optimized reaction conditions for the synthesis of N1 for six consecutive cycles along with the yields of the precipitated product and the recovered catalyst. The catalyst was recovered from the reaction mixture by the filtration process and used for further reaction. Product and catalyst recovery yields greater than 90% were observed for the first and second consecutive cycles; thereafter a steady drop in yields was observed for both the product and the recovered catalyst. Still, more than 60% product yield and 89% catalyst recovery were achieved for the fifth cycle. Beyond the fifth cycle, the product yield reduced to 35% and only about 75% catalyst could be recovered.
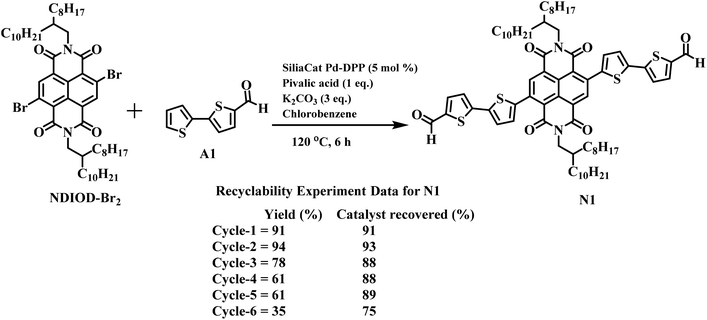 |
| Scheme 2 The SiliaCat Pd-DPP catalyst recyclability studies setup using N1 as an example for six consecutive cycles. | |
Some insight into the loss of the product yield beyond five consecutive catalyst recovery cycles could be gained by analysing the 1H and 13C NMR spectra of the recovered products from each cycle. Fig. 3 compares the expanded aromatic region in the proton NMR spectra of N1 from cycle 1 to cycle 6. The NMR spectra were identical and confirmed the predicted structure of the product for cycles 1 through 5. However, the proton NMR spectrum of N1 from cycle 6 exhibited additional peaks, which was indicative of the mono-coupled product. The mono-coupling could also be confirmed from MALDI-TOF data which show the presence of a mixture of single-side and both-sides coupled products. A comparison of the MALDI-TOF spectra of the samples from cycle 1 and cycle 6 is provided in ESI Fig. S29.† The detailed synthesis and the full proton and 13C NMR spectra are given in the ESI S12 and Fig. S30–S41.† These recyclability studies firmly established the applicability of the SiliaCat Pd-DPP catalyst for the DHAP method due to its reusability and air and temperature stability.43–46,53
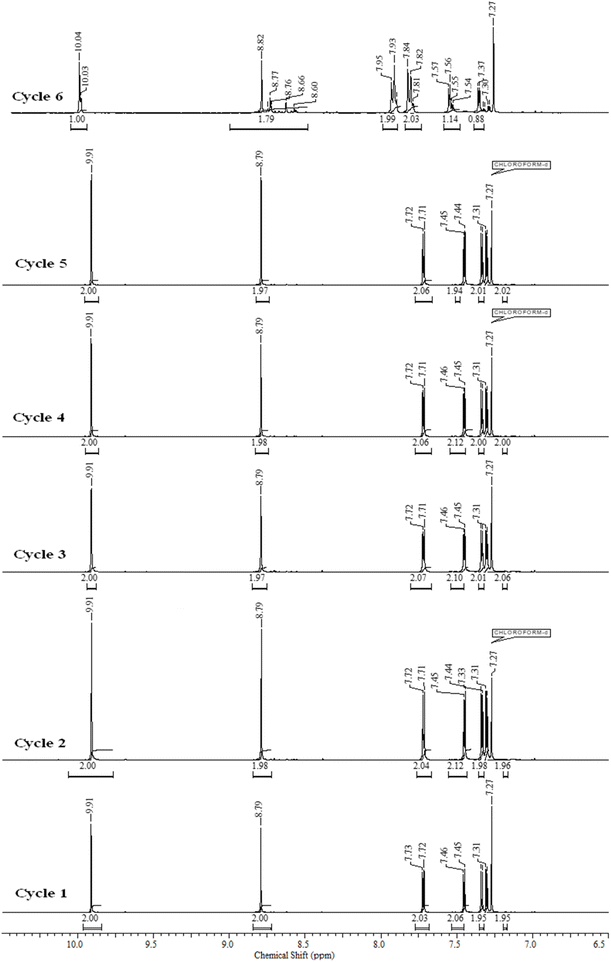 |
| Fig. 3 Expanded aromatic region in the 1H NMR spectra from six consecutive catalyst recovery cycles for N1. | |
The probable reasons for the continued reduction in the product yield over consecutive catalyst recycling cycles are the leaching of dissolved Pd species from the heterogeneous catalyst, and catalyst decomposition upon reuse. ICP-OES chemical analysis of the filtrate is usually carried out for detecting the presence of leached Pd. A quick qualitative assessment of the presence of leached palladium catalysing the reaction is the Meitlis hot filtration test, which involves the comparison of the catalytic activity before and after hot filtration of the heterogeneous catalyst solution. Fig. 4 shows the experimental procedure for carrying out the Meitlis hot filtration test. Briefly, two identical reactions were set up – one proceeded via route A where one equivalent of NDIOD-Br2 reacted with two equivalents of A1 for one hour in the presence of 5 mol% of the SiliaCat Pd-DPP catalyst along with added K2CO3 and pivalic acid. The reaction was stopped after one hour and the reaction mixture was worked up and precipitated into methanol followed by drying. The yield of the product N1 from route A was obtained at around 51%. In route B, the same reaction was conducted under identical conditions and at the end of 1 hour, the reaction was stopped and the hot reaction mixture was filtered at 70 °C using a PVDF filter (0.45 μm) to remove the catalyst. The remaining clear blue-coloured filtrate was introduced into another Schlenk tube and the reaction was allowed to continue at 120 °C for 24 h along with added K2CO3 as the base. The yield of the precipitated product from route B was 72%. The enhancement of the yield from 51% at 1 hour in the presence of the catalyst to 72% in the absence of the added catalyst indicated the presence of dissolved palladium in the reaction medium, which continued to catalyse the reaction. The chemical structure of the products isolated from route A and route B was confirmed to be identical by 1H NMR spectroscopy as shown in Fig. 5.
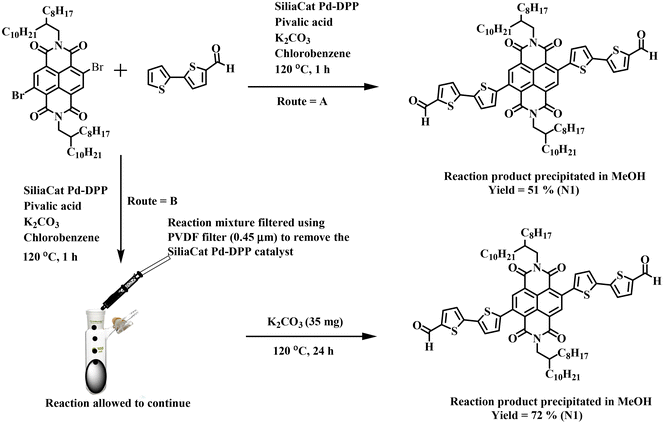 |
| Fig. 4 Schematic diagram for the Meitlis hot filtration test performed for the reaction of NDIOD-Br2 with A1. | |
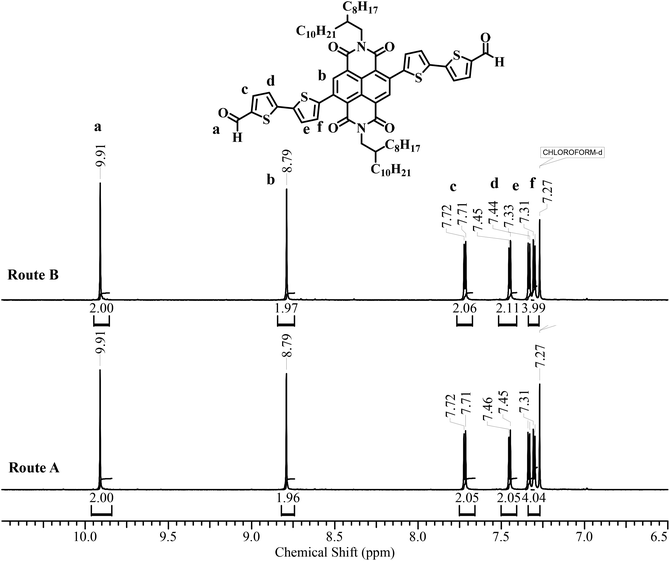 |
| Fig. 5 The expanded aromatic region in the 1H NMR spectra for N1 formed via route A and route B. | |
With evidence of the probable presence of leached palladium in the reaction medium, a quantitative estimation of palladium in the reaction mixture in catalyst recycling experiments was performed using ICP-OES analysis. The details of the sample preparation for the ICP analysis are given in the Experimental section. A fresh catalyst recycling experiment was conducted for the reaction of NDIOD-Br2 with A1. After filtration of the catalyst in each cycle, the reaction mixture (after following the analysis protocol) was characterized by the ICP-OS technique to identify the presence of Pd impurities in the reaction product. The recovered catalyst was used for setting up the next catalyst recycling experiment.
As a reference, the fresh SiliaCat-Pd-DPP catalyst was also subjected to ICP-OES analysis. An estimated amount of 0.294 mmol L−1 was obtained for Pd loading in fresh SiliaCat-Pd-DPP, which was taken to be 100%. Table 1 lists the values of the amount of leached Pd in the five consecutive catalyst recycling experiments. Compared to the Pd loading in the fresh catalyst, the leached Pd in each consecutive cycle was estimated to be about 6%, which is less than 2 ppm. This is an acceptable quantity of Pd, which could be expected to be present in the dissolved form in the solution through the ‘catch and release mechanism’ by which the dissolved Pd is redeposited on the support at the end of the reaction.54 It has been debated in the literature that even in heterogeneous catalysed reactions palladium leaches out into the solution as a consequence of the oxidative addition of the aryl halide to the surface of the catalyst, which is later redeposited after the reaction. The presence of this dissolved palladium even in <2 ppm is sufficient to catalyse the reaction further from about 51 to 72% (in the Meitlis hot filtration test; Fig. 4). In contrast to the heterogeneous catalysis, the presence of palladium impurity in homogeneous catalysis reaction products is normally on the higher side. For the quantification of the Pd impurity in heterogeneous vs. homogeneous catalysis reaction, the synthesis of N1 was performed using Pd2dba3 (homogeneous catalyst) (details of the synthesis and characterization are given in the ESI S13 and Fig. S42, S43†). The ICP-OES analysis indicated 0.107 mmol L−1 (six times higher) Pd impurity in the reaction product compared to N1 synthesized using the SiliaCat Pd-DPP catalyst.
Table 1 ICP-OS data for the reaction product N1 from five consecutive catalyst recycling experiments
Sr. no. |
Reaction cycles |
Leaching of Pd (mmol L−1) |
Leaching of Pd (%) (@0.294 mmol L−1 for 100% Pd loading) |
The catalyst leaching in homogeneously synthesised N1 using the homogeneous catalyst Pd2dba3 was 6 times higher compared to that using the heterogeneous SiliaCat Pd-DPP catalyst.
|
1 |
Cycle-1 |
0.018 |
6.1 |
2 |
Cycle-2 |
0.017 |
6.08 |
3 |
Cycle-3 |
0.017 |
5.9 |
4 |
Cycle-4 |
0.017 |
6.1 |
5 |
Cycle-5 |
0.017 |
6.03 |
6 |
Homogeneous catalysed reaction using Pd2dba3 |
0.107a |
|
The morphological characterization studies of the recycled catalyst for the five consecutive cycles were performed using FE-SEM and TEM techniques. The morphology of the fresh SiliaCat-Pd-DPP catalyst was also recorded for comparison. From the FE-SEM images presented in Fig. 6, it can be seen that the overall spherical particle shape is more or less well preserved for all the cycles, although some surface roughness becomes more apparent with reuse. The corresponding TEM images (Fig. 7) seemed to suggest some extent of aggregation for cycles 4 and 5 compared to the first 3 cycles. Taking the observation from the Pd leaching experiments and the imaging studies, the catalyst modification by particle aggregation seems to be a more probable reason for the observed deterioration in the catalyst performance efficiency with repeated cycling.
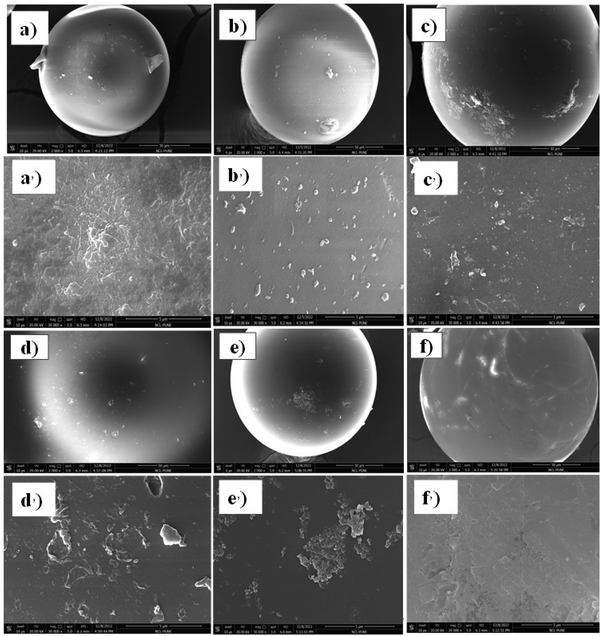 |
| Fig. 6 FE-SEM images for the fresh SiliaCat-Pd-DPP catalyst (a and a′) and the catalyst recovered from five consecutive cycles (b and b′), cycle-1, (c and c′) cycle-2, (d and d′) cycle-3, (e and e′) cycle-4, (f and f′) and cycle-5. a, b, c, d, e and f shows the images collected at a lower magnification. a′, b′, c′, d′, e′ and f′ shows the images collected at a higher magnification. | |
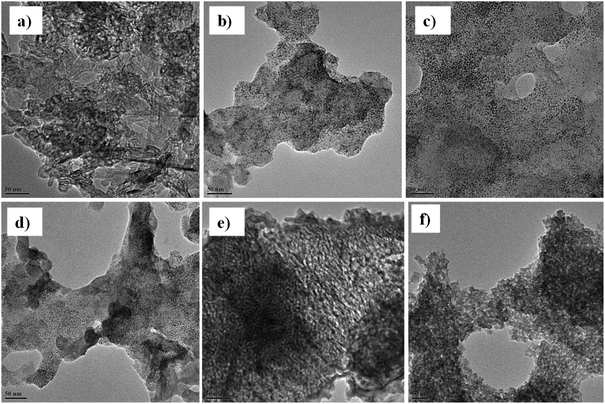 |
| Fig. 7 TEM images for (a) the fresh SiliaCat-Pd-DPP catalyst and the catalyst recovered from five consecutive cycles, (b) cycle-1, (c) cycle-2, (d) cycle-3, (e) cycle-4, and (f) cycle-5. | |
Synthesis of P(NDI2OD-T2) using SiliaCat Pd-DPP via the DHAP method employing NDIOD-Br2 and bithiophene as the starting monomers
After optimizing the direct heteroarylation process and the catalyst recyclability for the naphthalene diimide-based small molecules, the application of SiliaCat Pd-DPP was explored as a heterogeneous DHAP catalyst for the polymerization of P(NDI2OD-T2). The scheme for the polymerization involving NDIOD-Br2 and bithiophene is shown in Scheme 3.
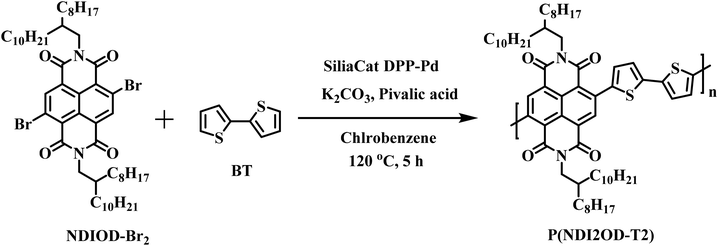 |
| Scheme 3 The synthesis of P(NDI2OD-T2) by the reaction of NDIOD-Br2 and bithiophene using SiliaCat Pd-DPP as the heterogeneous catalyst for direct heteroarylation polymerization. | |
The polymerization conditions were optimized by exploring solvents like 1,2,4-trichlorobenzene, chlorobenzene etc. Better molecular weights were obtained with chlorobenzene as the solvent medium; details of which are given in the ESI S14 and Fig. S44.†Table 2 summarizes the optimization experiments for various durations of polymerization time in chlorobenzene as the solvent. Only a moderate molecular weight build-up could be achieved even after a prolonged polymerization time. Reasonable molecular weights of Mn 23.3 and ĐM 2.0 could be obtained for 15 h of polymerization although extending beyond 15 h did not result in a molecular weight build-up. Catalyst recyclability studies were taken up for a polymerization timescale of 5 hours at 120 °C under identical reaction conditions. Table 3 lists the molecular weights achieved and the yields of the polymers as well as the recovered catalyst. The detailed synthetic procedure and the GPC chromatogram are shown in ESI S15 and Fig. S45,† respectively.
Table 2 Synthesis of P(NDI2OD-T2) using the SiliaCat Pd-DPP catalyst for different experimental durations at 120 °C using chlorobenzene as the solvent
Sr. no |
Timea (h) |
Concentrationb (M) |
M
n/Mw (kDa) |
Đ
M
|
Yieldd (%) |
Catalyst recoverede (%) |
Polymerization at different times.
The NDIOD-Br2 monomer concentration in the reaction mixture.
Dispersity index.
Yield calculated after the Soxhlet extraction.
Catalyst recovered after polymerization.
|
1 |
5 |
0.14 |
12.1/17.5 |
1.4 |
77 |
91 |
2 |
10 |
0.14 |
8.1/12.8 |
1.5 |
68 |
94 |
3 |
15 |
0.14 |
23.3/46.8 |
2.0 |
77 |
89 |
4 |
20 |
0.14 |
12.7/28.1 |
2.2 |
82 |
89 |
5 |
25 |
0.14 |
17.1/35.2 |
2.0 |
81 |
90 |
Table 3 Synthesis of P(NDI2OD-T2) at 120 °C in chlorobenzene as the solvent using NDIOD-Br2 and bithiophene as monomers and recycling the SiliaCat Pd-DPP catalyst
Sr. no. |
Number of cyclea |
Time (h) |
Concentrationb (M) |
M
n/Mw (kDa) |
Đ
M
|
Yieldd (%) |
Catalyst recyclede (%) |
New polymerization using the recovered catalyst from the previous cycle.
The NDIOD-Br2 monomer concentration in the reaction mixture.
Dispersity index.
Yield calculated after Soxhlet extraction.
Catalyst recovered after polymerization and used for the next cycle.
|
1 |
Cycle 1 |
5 |
0.14 |
12.1/17.5 |
1.4 |
77 |
91 |
2 |
Cycle 2 |
5 |
0.14 |
9.8/16.8 |
1.7 |
71 |
92 |
3 |
Cycle 3 |
5 |
0.14 |
8.4/13.0 |
1.5 |
85 |
90 |
4 |
Cycle 4 |
5 |
0.14 |
3.1/7.3 |
2.3 |
79 |
69 |
In the recyclability experiments, the recovered catalyst was reused for four consecutive cycles. As can be seen from Table 3, the molar masses of the polymers obtained from the recovered catalyst were not identical. In fact, there was a continuous drop in the molecular weight of the polymer in the consecutive cycles. The observation from Tables 2 and 3 seems to suggest that the SiliaCat Pd-DPP catalyst did not serve as a good catalyst for the synthesis of P(NDI2OD-T2) employing NDIOD-Br2 and bithiophene as the starting monomers.
Synthesis of P(NDI2OD-T2) using SiliaCat Pd-DPP via the DHAP method with the modified monomer
In our previously reported work, we had demonstrated an alternate synthetic route for P(NDI2OD-T2) by enhancing the C–H activation of the bithiophene monomer by designing a new monomer 2,2-bithiophene substituted with naphthalene diimide.51Scheme 4 shows the new polymerization scheme, where DFT calculations had shown that the abstraction of a proton from 2,2-bithiophene substituted with naphthalene diimide was 2.6 kcal mol−1 (ΔΔG) more favorable than that from 2,2-bithiophene (regular monomer). The failure of the SiliaCat Pd-DPP catalyst to produce high molecular weight P(NDI2OD-T2) using regular monomers, prompted us to explore the applicability of the heterogeneous catalyst to our newly designed monomer system. Using SiliaCat Pd-DPP as the catalyst, and chlorobenzene as the solvent medium, P(NDI2OD-T2) could be obtained with 30.0/51.7 (Mn/Mw) kDa and 98% yield in 5 h of polymerization time. The optimization reactions with both chlorobenzene and 1,2,4-trichlorobenzene as the solvent medium is given in ESI Table S2.† A more or less similar range of molecular weights could be obtained using either of the solvents. Recyclability experiments were carried out with the new monomer design in the TCB solvent and for 5 hours of polymerization time. In Table 4 the molecular weights, and yields of polymers and the recovered catalyst yields for five consecutive catalyst recovery cycles are compared. It is obvious from the table that high molecular weight polymers could be reproducibly obtained until four consecutive catalyst recovery cycles in reasonably good yields. A drastic drop in the molecular weight was observed during the fifth catalyst recovery cycle. The synthetic procedure and the GPC chromatogram are given in S16 and Fig. S46.†
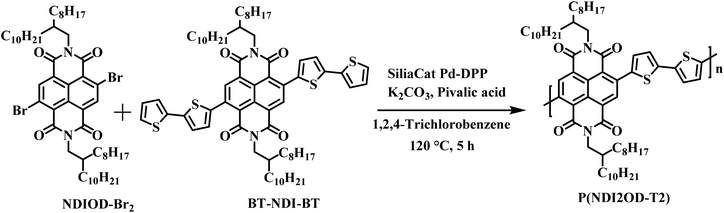 |
| Scheme 4 The synthesis of P(NDI2OD-T2) via the DHAP method using SiliaCat Pd-DPP with the new monomer. | |
Table 4 Synthesis of P(NDI2OD-T2) method using SiliaCat Pd-DPP with the modified monomer
Sr. no. |
Number of cyclea |
Time (h) |
M
n/Mw (kDa) |
Đ
M
|
Yieldc (%) |
Catalyst recycledd (%) |
T
d (10%)
(°C) |
T
m
(°C) |
ΔHmg (J g−1) |
New polymerization after recovering the catalyst from the previous cycle.
Dispersity index.
Yield calculated after the Soxhlet extraction.
Catalyst recovered after polymerization and used for the next cycle.
T
d10 value of polymers determined by thermogravimetric analysis.
Melting point of the polymer determined by differential scanning calorimetry.
Melting enthalpy of the polymer determined by differential scanning calorimetry.
|
1 |
Cycle 1 |
5 |
29.7/48.0 |
1.6 |
93 |
94 |
451 |
294 |
3.70 |
2 |
Cycle-2 |
5 |
28.6/53.3 |
1.9 |
91 |
86 |
445 |
300 |
3.33 |
3 |
Cycle-3 |
5 |
33.5/61.3 |
1.8 |
85 |
87 |
445 |
302 |
5.19 |
4 |
Cycle-4 |
5 |
27.1/49.0 |
1.8 |
84 |
73 |
452 |
296 |
3.68 |
5 |
Cycle-5 |
5 |
5.3/11.3 |
2.1 |
62 |
52 |
443 |
255 |
1.30 |
Structural characterization
In Fig. 8 the expanded region in the proton NMR spectra of the polymers collected from the above catalyst recycling experiments cycle 1 to cycle 5 are compared and their full spectra are provided in ESI Fig. S47–S51.† The NMR spectra were recorded in deuterated 1,1,2,2-tetrachloroethane (TCE-d2) at 90 °C. The proton ratio of the naphthalene diimide unit to that of the bithiophene ring was 2
:
4 as reported in the literature, which confirmed the expected structure because a deviation from this ratio would indicate the presence of homocoupling. Additionally, peaks corresponding to homocoupling defects were not observed as explained in detail in our earlier work.51 Small peaks observed at 7.15, 7.33, and 7.39 ppm (7.15 to 7.39 ppm region) is attributed to bithiophene end groups and that at 8.81 and 8.85 ppm is attributed to the Br-NDI end group.51,55 As can be seen from the figure, this end group peak is very prominent for the sample from cycle 5 since this sample has the lowest molecular weight.55
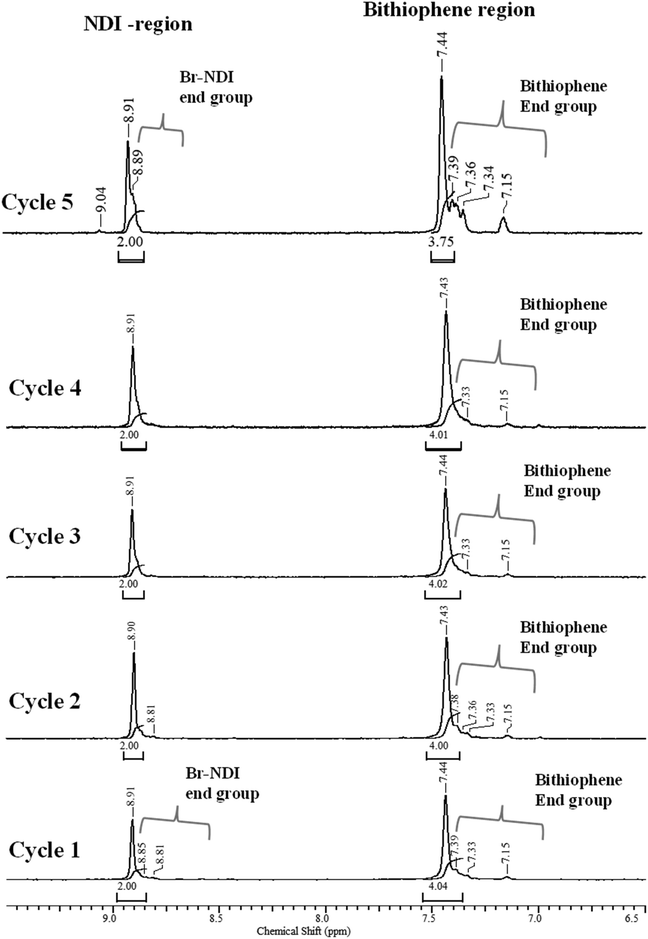 |
| Fig. 8 The expanded aromatic region in the 1H NMR spectra for five cycles of P(NDI2OD-T2), synthesized using the recycled SiliaCat Pd-DPP catalyst. 1H NMR spectra recorded in TCE-d2 solvent at a temperature of 90 °C. | |
The polymers obtained from the five consecutive catalyst recycling experiments were subjected to thermal analysis using thermogravimetric analysis (TGA) and differential scanning calorimetry (DSC). Fig. 9 and Table 4 summarizes the DSC graphs and data respectively. All polymers were thermally stable upto 440 °C as seen from the TGA graph shown in Fig. S52.† P(NDI2OD-T2) is a semicrystalline polymer and its melting transition and enthalpy of melting (ΔHm) values were obtained from DSC experiments. The polymer obtained from cycle 3 exhibited the highest molecular weight and it also had the highest melting temperature (302 °C) and high enthalpy of melting, confirming its highly crystalline nature. The polymers from all other cycles except the fifth one exhibited a more or less similar extent of crystallinity based on the enthalpy of melting. The polymer from the fifth cycle which was mostly an oligomer, had the lowest enthalpy (1.30 J g−1). These structure–property evaluations clearly established the feasibility of using SiliaCat Pd-DPP as a recyclable heterogeneous catalyst for the synthesis of P(NDI2OD-T2), using the modified monomer design.
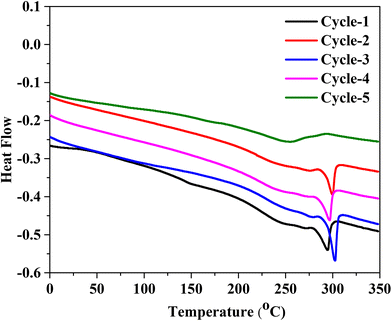 |
| Fig. 9 DSC data for five cycles of P(NDI2OD-T2), synthesized using recycled SiliaCat Pd-DPP as the heterogeneous catalyst. | |
Reaction scope
Encouraged by the success of SiliaCat Pd-DPP as a recyclable heterogeneous catalyst for the synthesis of a high molecular weight polymer based on naphthalene diimide, a couple of more D–A polymers based on naphthalene diimide were designed for polymerization. Scheme 5 shows the structure of the monomers and polymers that were synthesized using SiliaCat Pd-DPP as the heterogeneous catalyst and adopting the direct heteroarylation route for the synthesis. The details of the synthesis of the two starting materials C1 and C2 are given in ESI S17, S18 and Fig. S53–S56.† The polymers P(NDI-TVT) and P(NDI-TVTCN) were obtained with molecular weights of 13.0/29.8 and 29.6/82.5 (Mn/Mw) respectively. The structures of the polymers were confirmed by 1H NMR spectroscopy (Fig. 10) using TCE-d2 as the solvent at room temperature. The detailed synthesis of the P(NDI-TVT) and P(NDI-TVTCN) polymer, the entire range of the proton NMR spectra and the GPC chromatogram are provided in the ESI (S19, S20 and Fig. S57–S59†).
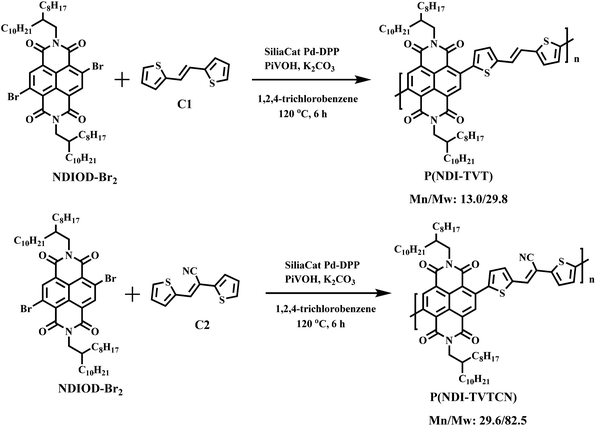 |
| Scheme 5 Synthesis of P(NDI-TVT) and P(NDI-TVTCN) polymers via the direct heteroarylation method using the SiliaCat Pd-DPP catalyst. | |
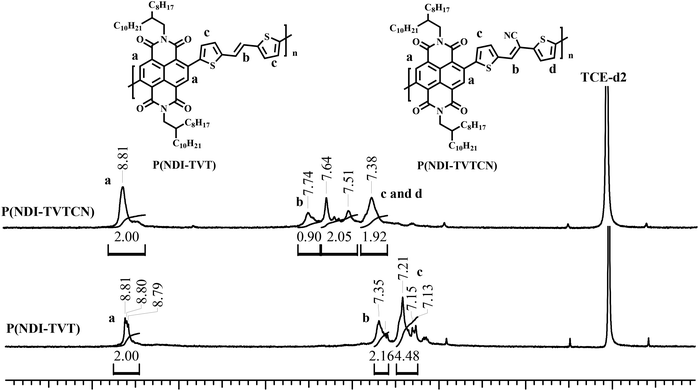 |
| Fig. 10 The expanded aromatic region in the 1H NMR spectra for P(NDI-TVT) and P(NDI-TVTCN) polymers synthesized using the SiliaCat Pd-DPP catalyst. 1H NMR spectra recorded in TCE-d2 solvent at room temperature. | |
Under optimized conditions, a higher molecular weight was observed for P(NDI-TVTCN) compared to P(NDI-TVT). A catalyst recyclability experiment was conducted for the P(NDI-TVTCN) polymer. P(NDI-TVTCN) was synthesized using the SiliaCat Pd-DPP catalyst for up to five consecutive cycles, as described in Scheme 6. As can be seen from the scheme, a continuous decrease in the molecular weight and yield was observed with each catalyst recycling experiment. The molecular weight decreased from 28.1/67.5 kDa in the first cycle to 17.9/30.0 and 15.9/28.5 in the second and third cycles and thereafter only very low molecular weight oligomers (9.1/17.3 kDa) were formed for cycle four. Similarly, a continuous reduction in the polymer yield also was observed, while the recovered catalyst yield remained more or less similar.
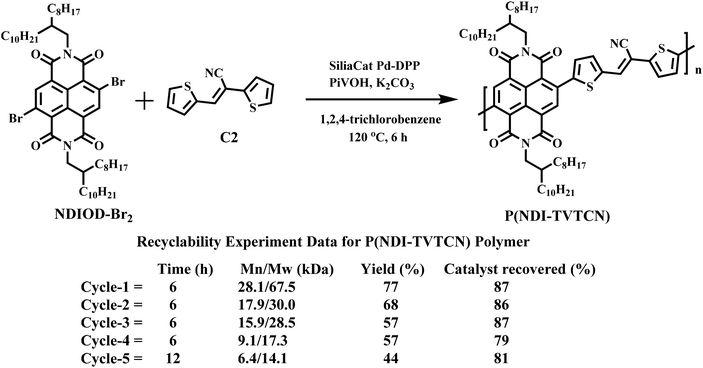 |
| Scheme 6 The SiliaCat Pd-DPP catalyst recyclability studies setup for the synthesis of P(NDI-TVTCN) for five consecutive cycles. | |
Therefore, after the fourth cycle, the polymerization was allowed to proceed for a longer time (12 h instead of 6 h). However, no significant improvement was observed either in the molecular weight of the polymer or its yield compared to cycle-1 to cycle-3. This reduction in the molecular weight may be attributed to the aggregation of the catalyst or the reduced catalyst reactivity after multiple reuses.
Fig. 11 shows the expanded aromatic region in the proton NMR spectra of the P(NDI-TVTCN) polymer obtained from the catalyst recycling experiment cycles-1 to cycle-5, along with their full spectra and GPC graph in ESI Fig. S60–S65.† The NMR spectra were recorded at room temperature in deuterated 1,1,2,2-tetrachloroethane (TCE-d2). The proton ratio of the naphthalene diimide unit to the (E)-2,3-di(thiophen-2-yl) acrylonitrile ring was 2
:
5, which was consistent with the chemical structure of the P(NDI-TVTCN) polymer.
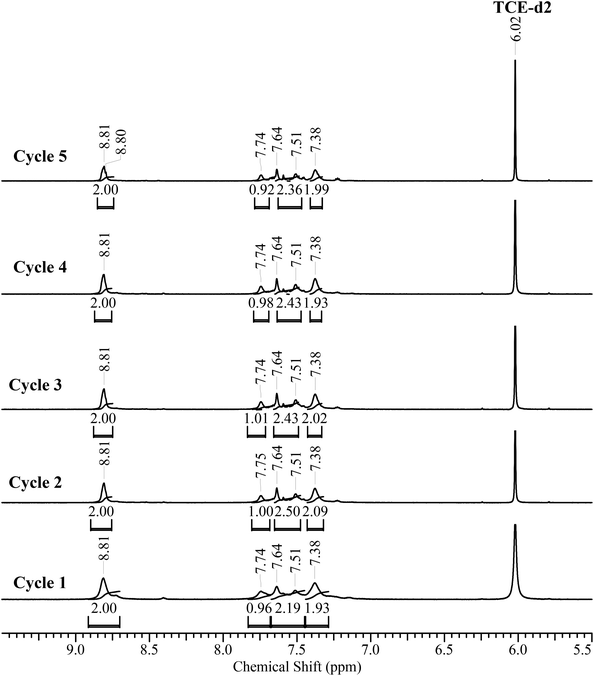 |
| Fig. 11 The expanded aromatic region 1H NMR spectra for five cycles of P(NDI-TVTCN), synthesized using recycled SiliaCat Pd-DPP catalyst. 1H NMR spectra recorded in TCE-d2 solvent at a room temperature. | |
Conclusion
A sustainable multi-batch synthesis of P(NDI2OD-T2) was demonstrated adopting the direct heteroarylation polymerization route using SiliaCat Pd-DPP as a heterogeneous catalyst. High molecular weight P(NDI2OD-T2) with good crystallinity and thermal stability could be obtained using a modified monomer designed by enhancing the C–H activation of the bithiophene monomer by substitution with naphthalene diimide. The SiliaCat Pd-DPP catalyst could be reused for four consecutive cycles to obtain a polymer of similar molecular weight and desirable properties. Elaborate catalyst recyclability studies conducted using naphthalene diimide and thiophene-based small conjugated molecules (N1) indicated a very low extent of palladium leaching (<2 ppm) while using SiliaCat Pd-DPP as the heterogeneous catalyst. But it was ∼11 ppm when Pd2dba3 was used as a homogeneous catalyst for the synthesis of N1, highlighting the advantage of a heterogeneous catalyst over a homogeneous catalyst for improved purity of the product. In addition to this advantage, SiliaCat Pd-DPP could be recycled for up to four cycles with reproducible properties of the final polymer. Beyond four catalyst cycles, although there were no noticeable changes in the amounts of leached palladium in the product, morphological changes like particle aggregation were observed for the SiliaCat Pd-DPP catalyst which could be the reason for the deterioration in the catalyst efficiency with repeated cycling. Combining DHAP, which is an atom economical synthesis process, together with a recyclable air-stable catalyst makes this a potential approach for the industrial scaling of D–A conjugated polymers like P(NDI2OD-T2) and other naphthalene diimide based polymers.
Experimental section
Materials
Bithiophene, tributylstannyl thiophene, Pd(PPh3)2Cl2, Pd2dba3, 4-bromobenzaldehyde, 2-phenyl thiophene, 2-bromo-4,5-dimethoxy benzaldehyde, 3-bromo pyridine, 5-hexyl-2-2-bithiophene, dimethyl formamide (DMF), dichloroethane (DCE) and phosphorus oxychloride (POCl3), were purchased from Sigma Aldrich. 1,4,5,8-Naphhalenetetracarboxylic dianhydride (NTCDA), 2-octyldodecanol, triphenylphosphine, potassium phthalimide, molecular bromine (Br2), hydrazine hydrate, oleum and iodine (I2) were purchased from TCI and used without further purification. The SiliaCat Pd-DPP heterogeneous catalyst was a kind gift from SiliCycle Incorporation as a research sample and it was used as received. The catalyst has an orange colour and contains 0.2 to 0.3 mmol g−1 (2.2 to 3.2%) of the Pd metal. Its tap density typically ranges from 0.300 to 0.400 g mL−1. This catalyst can be used with both aqueous and organic solvents and should be stored under dry conditions. Sodium acetate (NaOAc), sodium sulfate (Na2SO4), and potassium carbonate (K2CO3) were purchased from Loba Chemie Pvt Ltd. Dichloromethane (DCM), chlorobenzene (CB), 1,2,4-trichlorobenzene (TCB), methanol (MeOH) and acetone HPLC grade were purchased from Merck.
Measurement and method
Structural characterization of conjugated small molecules and monomers was conducted by recording 1H and 13C NMR spectra at 25 °C using a Bruker-AVENS 400 or 500 MHz NMR instrument. Deuterated chloroform (CDCl3) was used as a solvent with a trace amount of TMS as an internal reference. Chemical shifts of the NMR peaks were reported in ppm at 25 °C. The mass of the monomer was determined using an Applied Bio system 4800 PLUS matrix-assisted laser desorption/ionization (MALDI) TOF/TOF analyzer. 2 mg of the sample was dissolved in 3 mL of chloroform and sonicated for 1 h. 2,5-Dihydroxybenzoic acid (DHB) in 50
:
50 water/acetonitrile with 0.1% TFA was used as the matrix. The monomer samples were characterized using a reflection detector in the positive analysis mode. (Attempts at recording the MALDI-TOF in negative ionization mode to avoid fragmentation as per reviewer's suggestion did not yield any data) The polymer structural characterisation was conducted by 1H NMR spectroscopy at 80 °C using deuterated 1,1,2,2-tetrachloroethane (TCE-d2) as the solvent using Bruker-AVENS 400 MHz NMR instruments. Number-average (Mn) and weight-average (Mw) molecular weights were determined by size exclusion chromatography (SEC) using a high-temperature Agilent PL-GPC 220 system equipped with an RI detector. The column consisted of Agilent PLgel 10 μm MIXED-B, 300 × 7.5 mm (part no PL1110-6100) columns. The flow rate was fixed at 1 mL min−1 using 1,2,4-trichlorobenzene (TCB) as the eluent and the temperature was set at 140 °C. The samples (2 mg) were dissolved in 2 ml of TCB in a chromatography vial and heated at 100 °C for 1 h for complete dissolution. Afterwards, the samples were filtered using a 0.45 μm PVDF filter. Polystyrene narrow standard Easi-Vials PS-M from Varian Polymer Laboratories dissolved in TCB were used for the calibration. TGA (thermogravimetric analysis) was performed on a PerkinElmer STA (simultaneous thermal analyzer) 6000 thermogravimetric analyzer. The heating rate was set at 10 °C min−1 and the samples were heated from 40 to 900 °C under a nitrogen atmosphere. The DSC (differential scanning calorimetry) was performed using a TA discover 250 seconds generation instrument. Samples were run at a heating rate of 10 °C min−1 from −10 to 330 °C under a nitrogen (N2) atmosphere. Inductively coupled plasma-optical emission spectroscopy (ICP-OES) SPECTRO ARCOS model FHS-12 (Germany) was used for the analysis of leached Pd from the catalyst. The morphological characterization studies of the SiliaCat Pd-DPP catalyst was performed using field emission scanning electron microscopy (FE-SEM) using an FEI Nova Nano SEM 450 instrument. The pristine and recovered catalyst was directly stuck on carbon tape and mounted on the top of the grooved edge of the aluminum SEM specimen stub. Before conducting morphological studies, the samples were coated with a 5 nm thick gold film using the sputtering method. Transmission electron microscopy (TEM) data was acquired using an FEI-Tecnai-F20 electron microscope operating at 200 kV. The pristine and recovered catalyst was added to ethanol and sonicated for 4 hours. The uniformly dispersed sample was dropcast on a carbon-coated copper grid with 400 mesh size and dried overnight at 50 °C in a fume hood.
Sample preparation for ICP analysis
NDIOD-Br2 (100 mg, 0.101 mmol), 2,2-bithiophene-5-carbaldehyde (39.44 mg, 0.203 mmol), pivalic acid (10.36 mg, 0.101 mmol), K2CO3 (42 mg, 0.304 mmol) and SiliaCat Pd-DPP (16.92 mg, 5 mol%) were taken in a 10 ml oven-dry Schlenk tube equipped with a stirring bar. The Schlenk tube was evacuated three times and purged by nitrogen gas. Degassed chlorobenzene (1 ml) was added to the Schlenk tube using a syringe and purged for 15 minutes. The reaction mixture was stirred for 6 h at 120 °C and warmed to room temperature. After the completion of the reaction, the reaction mixture was transferred to a 20 mL beaker, and the solvent was evaporated. 40 mg of the dried sample was mixed with aqua regia solution (6 mL) and heated to complete the digestion of the reaction product. The concentrated reaction mixture was diluted in 40 mL of DI water. The sample was filtered through a syringe micro filter and used for ICP analysis.
Procedure for catalyst recovery from the reaction mixture
After the reaction or polymerization was completed, the reaction mixture was diluted with chloroform (CHCl3) (30 mL) and filtered using Whatman 41 filter paper to collect the SiliaCat Pd-DPP catalyst. The residue (catalyst) was further washed with ∼20 mL of CHCl3 until the disappearance of the blue colour, followed by washing with methanol and acetone. The catalyst was dried in a vacuum oven at 70 °C for 12 h and used for the next reaction cycle.
Conflicts of interest
The authors declare no competing financial interest.
Acknowledgements
This work has been financially supported by the SERB project SPF/2021/000135 and the Centre of Excellence (CoE) (F.No. 25014/2/2015-PC-II (FTS: 14428) supported by the Ministry of Chemical and Fertilizers, Department of Chemicals and Petrochemicals, Government of India and Facility Creation Project (FCP; No. 34/FCP/NCL/2019-RPPBDD) supported by the Council of Scientific and Industrial Research, Project Planning & Business Development Directorate, New Delhi. Navnath R. Kakde thanks CSIR for the senior research fellowship (SRF). The authors would like to thank Professor M Jayakannan, IISER Pune for fruitful discussions throughout the execution of this project. The authors acknowledge Dr Sapna Ravindranathan from CSIR NCL Pune for facilitating high temperature NMR studies. We would also like to place on record our sincere thanks to Dr N. Rajasekar and SiliCycle Incorporation for providing the research sample of the SiliaCat Pd-DPP catalyst.
References
- X. Zhang, C. Xiao, A. Zhang, F. Yang, H. Dong, Z. Wang, X. Zhan, W. Li and W. Hu, Polym. Chem., 2015, 6, 4775–4783 RSC.
- A. Yin, D. Zhang, S. H. Cheung, S. K. So, Z. Fu, L. Ying, F. Huang, H. Zhou and Y. Zhang, J. Mater. Chem. C, 2018, 6, 7855–7863 RSC.
- Y. M. Kim, E. Lim, I. N. Kang, B. J. Jung, J. Lee, B. W. Koo, L. M. Do and H. K. Shim, Macromolecules, 2006, 39, 4081–4085 CrossRef CAS.
- S. Vegiraju, X. L. Luo, L. H. Li, S. N. Afraj, C. Lee, D. Zheng, H. C. Hsieh, C. C. Lin, S. H. Hong, H. C. Tsai, G. H. Lee, S. H. Tung, C. L. Liu, M. C. Chen and A. Facchetti, Chem. Mater., 2020, 32, 1422–1429 CrossRef CAS.
- J. Dhar, U. Salzner and S. Patil, J. Mater. Chem. C, 2017, 5, 7404–7430 RSC.
- R. Gracia and D. Mecerreyes, Polym. Chem., 2013, 4, 2206–2214 RSC.
- M. Sun, G. Wang, C. Yang, H. Jiang and C. Li, J. Mater. Chem. A, 2015, 3, 3880–3890 RSC.
- J. T. Chen and C. S. Hsu, Polym. Chem., 2011, 2, 2707–2722 RSC.
- S. J. Uke, S. P. Mardikar, A. Kumar, Y. Kumar, M. Gupta and Y. Kumar, R. Soc. Open Sci., 2021, 8, 210567 CrossRef CAS PubMed.
- M. Sommer, J. Mater. Chem. C, 2014, 2, 3088–3098 RSC.
- M. M. Durban, P. D. Kazarinoff and C. K. Luscombe, Macromolecules, 2010, 43, 6348–6352 CrossRef CAS.
- W. Wang, R. Chen, Y. Hu, H. Lu, L. Qiu, Y. Ding, D. Sun and G. Zhang, J. Mater. Chem. C, 2019, 7, 8450–8456 RSC.
- J. Royakkers, K. Guo, D. T. W. Toolan, L. W. Feng, A. Minotto, D. G. Congrave, M. Danowska, W. Zeng, A. D. Bond, M. Hashimi, T. J. Marks, A. Facchetti, F. Cacialli and H. Bronstein, Angew. Chem., Int. Ed., 2021, 60, 25005–25012 CrossRef CAS PubMed.
- S. Griggs, A. Marks, H. Bristow and I. McCulloch, J. Mater. Chem. C, 2021, 9, 8099–8128 RSC.
- F. De Araújo Silva, R. S. Cicolani, G. Lima, F. Huguenin and G. Jean-François Demets, RSC Adv., 2018, 8, 24029–24035 RSC.
- S. V. Bhosale, M. Al Kobaisi, R. W. Jadhav, P. P. Morajkar, L. A. Jones and S. George, Chem. Soc. Rev., 2021, 50, 9845–9998 RSC.
- L. Ye and B. C. Thompson, J. Polym. Sci., 2022, 60, 393–428 CrossRef CAS.
- T. Itahara, J. Org. Chem., 1985, 50, 5272–5275 CrossRef CAS.
- R. Matsidik, H. Komber and M. Sommer, ACS Macro Lett., 2015, 4, 1346–1350 CrossRef CAS PubMed.
- S. Yu, F. Liu, J. Yu, S. Zhang, C. Cabanetos, Y. Gao and W. Huang, J. Mater. Chem. C, 2017, 5, 29–40 RSC.
- C. Guo, J. Quinn, B. Sun and Y. Li, Polym. Chem., 2016, 7, 4515–4524 RSC.
- J. R. Pouliot, B. Sun, M. Leduc, A. Najari, Y. Li and M. Leclerc, Polym. Chem., 2015, 6, 278–282 RSC.
- G. Marzano, F. Carulli, F. Babudri, A. Pellegrino, R. Po, S. Luzzati and G. M. Farinola, J. Mater. Chem. A, 2016, 4, 17163–17170 RSC.
- A. D. Hendsbee and Y. Li, Molecules, 2018, 23, 1255 CrossRef PubMed.
- D. J. Burke and D. J. Lipomi, Energy Environ. Sci., 2013, 6, 2053–2066 RSC.
- K. S. Egorova and V. P. Ananikov, Angew. Chem., Int. Ed., 2016, 55, 12150–12162 CrossRef CAS PubMed.
- M. P. Nikiforov, B. Lai, W. Chen, S. Chen, R. D. Schaller, J. Strzalka, J. Maser and S. B. Darling, Energy Environ. Sci., 2013, 6, 1513–1520 RSC.
- F. C. Krebs, R. B. Nyberg and M. Jørgensen, Chem. Mater., 2004, 16, 1313–1318 CrossRef CAS.
- S. Griggs, A. Marks, D. Meli, G. Rebetez, O. Bardagot, B. D. Paulsen, H. Chen, K. Weaver, M. I. Nugraha, E. A. Schafer, J. Tropp, C. M. Aitchison, T. D. Anthopoulos, N. Banerji, J. Rivnay and I. McCulloch, Nat. Commun., 2022, 13, 1–11 Search PubMed.
- L. Ye, R. M. Pankow, A. Schmitt and B. C. Thompson, Polym. Chem., 2019, 10, 6545–6550 RSC.
- L. Ye, A. Schmitt, R. M. Pankow and B. C. Thompson, ACS Macro Lett., 2020, 9, 1446–1451 CrossRef CAS PubMed.
- R. M. Pankow, L. Ye and B. C. Thompson, Polym. Chem., 2018, 9, 4120–4124 RSC.
- P. A. Troshin, D. K. Susarova, Y. L. Moskvin, I. E. Kuznetsov, S. A. Ponomarenko, E. N. Myshkovskaya, K. A. Zakharcheva, A. A. Balakai, S. D. Babenko and V. F. Razumov, Adv. Funct. Mater., 2010, 20, 4351–4357 CrossRef CAS.
- J. Kettle, M. Horie, L. A. Majewski, B. R. Saunders, S. Tuladhar, J. Nelson and M. L. Turner, Sol. Energy Mater. Sol. Cells, 2011, 95, 2186–2193 CrossRef CAS.
- S. Y. Liu, H. Y. Li, M. M. Shi, H. Jiang, X. L. Hu, W. Q. Li, L. Fu and H. Z. Chen, Macromolecules, 2012, 45, 9004–9009 CrossRef CAS.
- L. Yin and J. Liebscher, Chem. Rev., 2007, 107, 133–173 CrossRef CAS PubMed.
- P. Josse, S. Dayneko, Y. Zhang, S. Dabos-Seignon, S. Zhang, P. Blanchard, G. C. Welch and C. Cabanetos, Molecules, 2018, 23, 962 CrossRef PubMed.
- Y. Kojima, S. Hayashi and T. Koizumi, J. Polym. Sci., Part A: Polym. Chem., 2017, 55, 1183–1188 CrossRef CAS.
- S. Hayashi, Y. Kojima and T. Koizumi, Polym. Chem., 2015, 6, 881–885 RSC.
- V. Pandarus, G. Gingras, F. Béland, R. Ciriminna and M. Pagliaro, Beilstein J. Org. Chem., 2014, 10, 897–901 CrossRef PubMed.
- V. Pandarus, G. Gingras, F. Béland, R. Ciriminna and M. Pagliaro, Org. Process Res. Dev., 2012, 16, 1307–1311 CrossRef CAS.
- A. Mai and W. De Borggraeve, J. Flow Chem., 2015, 5, 6–10 CrossRef CAS.
- S. M. McAfee, J. S. J. McCahill, C. M. MacAulay, A. D. Hendsbee and G. C. Welch, RSC Adv., 2015, 5, 26097–26106 RSC.
- R. Ciriminna, V. Pandarus, G. Gingras, F. Béland, P. D. Carà and M. Pagliaro, ACS Sustainable Chem. Eng., 2013, 1, 57–61 CrossRef CAS.
- V. Pandarus, D. Desplantier-Giscard, G. Gingras, F. Béland, R. Ciriminna and M. Pagliaro, Org. Process Res. Dev., 2013, 17, 1492–1497 CrossRef CAS.
- Key reference: L. Ye, T. Hooshmand and B. C. Thompson, ACS Macro Lett., 2022, 11, 78–83 CrossRef CAS PubMed.
- S. Sharma, N. B. Kolhe, V. Gupta, V. Bharti, A. Sharma, R. Datt, S. Chand and S. K. Asha, Macromolecules, 2016, 49, 8113–8125 CrossRef CAS.
- S. Sharma, R. Soni, S. Kurungot and S. K. Asha, Macromolecules, 2018, 51, 954–965 CrossRef CAS.
- S. Sharma, R. Soni, S. Kurungot and S. K. Asha, J. Phys. Chem. C, 2019, 123, 2084–2093 CrossRef CAS.
- B. A. Wavhal, M. Ghosh, S. Sharma, S. Kurungot and A. Sk, Nanoscale, 2021, 13, 12314–12326 RSC.
- N. R. Kakde, H. J. Bharathkumar, B. A. Wavhal, A. Nikam, S. Patil, S. R. Dash, K. Vanka, K. Krishnamoorthy, A. Kulkarni and S. K. Asha, J. Mater. Chem. C, 2022, 10, 13025–13039 RSC.
- J. T. Blaskovits, P. A. Johnson and M. Leclerc, Macromolecules, 2018, 51, 8100–8113 CrossRef CAS.
- A. Bourouina, V. Meille and C. de Bellefon, Catalysts, 2019, 9, 1–27 CrossRef.
- G. Albano, S. Interlandi, C. Evangelisti and L. A. Aronica, Catal. Lett., 2020, 150, 652–659 CrossRef CAS.
- R. Matsidik, H. Komber, A. Luzio, M. Caironi and M. Sommer, J. Am. Chem. Soc., 2015, 137, 6705–6711 CrossRef CAS PubMed.
Footnote |
† Electronic supplementary information (ESI) available: The procedure for the synthesis of the small molecules A1 to A6 and N1 to N6 and their structural characterization using 1H NMR, 13C NMR and MALDI-TOF spectroscopy. The synthesis of the polymer using different monomers, optimization table, and characterization of the polymers using 1H NMR spectroscopy and gel permeation chromatography. See DOI: https://doi.org/10.1039/d3py00183k |
|
This journal is © The Royal Society of Chemistry 2023 |