DOI:
10.1039/D3QM00487B
(Review Article)
Mater. Chem. Front., 2023,
7, 5140-5170
MOFs meet membrane: application in water treatment and separation
Received
29th April 2023
, Accepted 3rd July 2023
First published on 7th July 2023
Abstract
Metal–organic frameworks (MOFs) are a class of solid crystalline materials formed by the self-assembly of organic ligands and metal ions or clusters through coordination bonds. Owing to their intrinsic rich chemical composition, large specific surface area, diverse topology, tunable pore channels and good thermal stability, MOFs are favored in many applications. In particular, MOFs are considered to be viable membrane-based separation materials based on their unique advantages in the adsorption of specific chemicals. Research into MOF-based membrane-preparation methods and separation applications is flourishing, and MOF-based membranes have achieved marvellous achievements in the field of gas separation and liquid separation. This review first introduces the general criteria for selecting MOFs for separation applications. Then, we specifically describe how to prepare MOF-based membranes as well as the specific classification of MOF hybrid membranes, and finally describe the application of MOF-based membranes in water treatment. Most of all, the opportunities and challenges of MOF membranes in industrial applications are outlined.
1. Introduction
Separation is widely used and plays a significant role in our daily life and industrial applications. However, traditional separation techniques such as distillation, filtration, etc., are not easy to operate and are expensive when completing separation operations, hindering their practical application.1 Recently, membrane technology has been proved to be an excellent alternative to traditional separation technologies in applications due to its high separation efficiency, low secondary pollution, and environmental friendliness. Selective separation at the molecular level can be achieved when mixtures of molecules of different particle sizes pass through a semi-permeable membrane.2 However, the efficiency of membrane separation technologies is often affected by the interplay between the membrane permeability and selectivity. To the best of our knowledge, rubbery polymers have been demonstrated to be more permeable, whereas glassy polymers exhibit better selectivity.3 In order to achieve simultaneously high permeability and selectivity in membrane separation, it is particularly important to develop new types of separation membrane. In most cases, good separation cannot be achieved due to harsh operating conditions. Inorganic membranes have attracted a lot of attention as ideal membrane separation materials that have stable chemical properties and an excellent separation performance. Currently, materials processed into inorganic membranes include metals, ceramics, silicon, carbon, zeolites, metal–organic frameworks (MOFs), etc. In various separation applications, various kinds of inorganic membrane have been utilized, depending on the properties of the materials. Among them, MOFs are of great interest because of their large surface area, rich chemical functionality, tunable pore system, and good thermal stability.4
Metal–organic frameworks (MOFs), a class of materials containing pores made of metal ions or ionic clusters bonded to organic ligands, are also known as porous coordination polymers (PCPs).5,6 Unlike other materials, MOFs are preferred because of their rich chemical composition, large specific surface area, diverse topology, adjustable pore channels, and thermal stability.7 Based on these advantages, MOF scaffolds have been applied to enhance the adsorption of specific chemicals for precise and rapid separation.8,9 MOFs are considered to be viable membrane-based separation materials and are typically grown on substrates to construct continuous membranes or are used as fillers to form mixed matrix membranes (MMMs). The organic nature of the MOF framework can enable interactions with polymers, resulting in good compatibility.10 Combining the benefits of MOF materials and polymeric fillers, such produced MOF-based membranes demonstrate increased permeability and perhaps selectivity compared with virgin membranes.
In past studies, MOF-based membranes have displayed extraordinary possibilities in many applications, particularly in gas separation and purification. In gas separation, advances in MOF membrane applications have been summarized in many articles. In contrast, few review articles are available on the synthesis and application of MOF membranes in liquid separation, particularly in water treatment. Herein, the preparation standards and methods of MOF-based membranes, as well as the classification of the various types of MOF hybrid membrane, are systematically reviewed in this paper. Then, MOF-based membranes are highlighted for the treatment of heavy metal ions, organic pollutants, and radionuclides in wastewater as well as oil–water separation and seawater desalination. Finally, the prospects of MOF-based membranes in industrial applications are discussed, and possible opportunities and challenges in the fabrication and application of MOF-based membranes are outlined in the hope of facilitating the realization of these membranes in practical applications.
2. Design criteria for MOF-based membranes
2.1 Selection criteria for MOFs
As a porous crystalline material, MOFs, with their flexible structure, high specific surface area and abundant adsorption sites, largely determine the separation ability of MOF-based membranes.11 And in recent years, polymeric materials have become popular in the field of membrane separation because of their advantageous mechanical strength, plasticity and high elasticity.12 In order to prepare MOF membranes with an excellent performance, researchers considered combining MOF and polymeric materials to combine the tunable pore structure and high specific surface area of the MOF with the strong mechanical strength of the polymeric material to achieve a more stable and efficient membrane separation performance. Combining MOFs and polymers, while retaining the advantages of the MOF material with its high specific surface area, can also avoid the excessive agglomeration of MOF crystals, making them more evenly dispersed in the polymer, which can better exploit their advantages. As for the polymer, the addition of MOFs makes it more flexible and improves the separation performance of polymer material in membrane separation. Therefore, combining the two would be a good choice for membrane separation. How to prepare MOF-based membranes that show an excellent performance will be the key consideration. High-efficiency MOF-based membranes should have excellent separation capabilities, high recyclability and stability, and be environmentally friendly. According to these criteria, MOFs should be homogeneously dispersed in the polymer, providing strong hydrothermal stability, hydrophilicity,13 suitable pore sizes, and small particle sizes.14
Uniform dispersion.
Interfacial defects are largely influenced by the dispersion of MOFs in the polymer, and an inhomogeneous dispersion of MOFs leads to the inability to form a complete laminar structure and defect-free membranes, thus degrading the performance of the MMMs. The successful preparation of MOF-based membranes with an excellent separation efficiency requires both a maximum loading and a uniform dispersion of the MOFs. Researchers have proposed several strategies to homogeneously disperse MOFs in hybrid membranes. (i) Pre-dispersion: MOFs will be poorly distributed if they are dispersed directly in the polymer during preparation; thus, as a typical example, zeolitic imidazolate framework (ZIF) particles (ZIF-8) were dispersed in isooctane, followed by treatment in an ice bath and heating to room temperature, and then the isooctane solution of ZIF-8 was mixed with the rest of the mixture to produce a homogeneously dispersed mixture.15 In addition, it has been shown that in the preparation of chitosan (CS)/ZIF-8 MMMs, 10% of the desired CS was first added to the ZIF-8 suspension to achieve a uniform dispersion and maintain good adhesion, after which the remaining CS was added to obtain the desired concentration of CS solution.16 (ii) Surface modification of MOFs: a general modification method is to enhance the dispersion properties of MOFs by introducing other functional groups. For example, Ma et al. prepared MOF/chitosan nanofiltration (NF) membranes via the amino modification of a Matériaux de l′Institut Lavoisier (MIL) framework (MIL-101) which was then combined with chitosan. MOF particles were evenly distributed in the chitosan polymeric matrix, significantly enhancing the flux and repulsion of the NF membrane cations.17 (iii) Self-assembly technology: MOF particles are grown within the polymer in situ, while metal ions coordinate simultaneously with both MOF ligands and the functionalized organic polymer. As a result, the membrane is highly compatible and the MOFs are uniformly distributed. Adopting this method, an ultrathin ZIF-8/poly(sodium 4-styrene-sulfonate) (PSS) membrane that can effectively separate dyes was prepared.18 Shahid and co-workers19 optimized the MOF–polymer interactions using self-assembly and the controlled fusion of MOF and polymer particles to obtain well-dispersed ZIF-8.
Strong water stability.
Considering the instability of the ligand–metal bonds of MOFs, they are extremely sensitive to water and are not suitable for use in aqueous environments. Only MOFs with strongly coordinated bonds or notable steric hindrance in the structure show good water stability.20 In 2015, Liu et al. prepared the first highly water-stable UiO-66 membrane.21 This study demonstrated that the UiO-66 MOF material can be a good choice as a membrane material for water treatment. According to the current studies, water-stable MOFs (such as MIL-100, MIL-101, ZIF-8 and UiO-66) are mainly metal carboxylate frameworks that consist of high-valence metal ions, metal azole frameworks that contain nitrogen donor ligands, and MOFs functionalized with hydrophobic pore surfaces or with clogged metal ions.22–25 Composite membranes prepared from water-stable MOFs have a relatively high separation performance. Considering that some MOFs with poor water stability still exist, some post-synthesis modifications such as ligand modification,26 metal and ligand exchange27 have also been designed to improve the hydrothermal stability of MOFs.
Rational choice of hydrophilicity/hydrophobicity.
Ligands and the availability of unoccupied metal sites in MOFs determine their hydrophilicity/hydrophobicity. When applying MOFs to water pollution remediation, appropriate MOF materials must be selected for target compounds with different properties. Hydrophobic MOFs usually have a remarkable ability to adsorb organic matter in water during full evaporation, for example ZIF-71, which can selectively adsorb alcohol in alcohol–water mixtures.28 In contrast, hydrophilic MOFs show a better ability when treating dyes with MOF-based membranes. To enhance the hydrophilicity of MOFs, Zhu et al. fabricated thin film nanocomposite (TFN) membranes containing poly(sodium 4-styrenesulfonate) (PSS)-modified ZIF-8 in a polyamide (PA) layer using the interfacial polymerization (IP) technique.29 Such ZIF-8 TFN membranes have a much higher hydrophilicity and water flux, and can remove >99.0% of dyes.
Suitable pore size.
MOFs are preferred for membrane separation applications due to their adaptability and designability. A crucial factor determined membrane separation technology is the pore size of the MOFs. By increasing the chain length, introducing functional groups, and using the right linkers, the pore size can be changed. For example, ZIF-8 possesses a pore aperture diameter of 3.4 Å and a gate-opening diameter of 4.2 Å, and is able to separate water with a kinetic radius of 2.6 Å from ethanol with a kinetic radius of 4.5 Å.30 Therefore, the selection of MOF materials with suitable pore diameters when performing separations can well achieve the screening of different pore size separation materials for separation purposes.
2.2 Impact factors related to polymer membrane performance
MOF polymer hybrid membranes are the most widely used class of MOF-based membranes. Combining organic and inorganic materials creates a membrane with the properties of both and a performance that is superior to that of the two phases alone. The primary requirements when choosing polymer substrates include strong chemical stability, excellent separation properties, and excellent mechanical strength. In addition, the swelling properties, solubility, and processability of the polymer should not be neglected. The molecular weight, glass transition temperature, melting point, crystallinity, and polarity are the main factors that affect the performance of polymer membranes.31 The molecular weight is a true reflection of the degree of polymerization of organic matter and determines the viscosity, mechanical strength, and chemical stability of the polymer. Typically, the polymer viscosity, mechanical strength, and chemical stability increase with the molecular weight. In addition, the temperature affects the properties of the polymer and how it changes physically. When heated, an amorphous nucleated thermoplastic polymer transitions from a glassy state to a rubbery or pliable plastic state at a temperature known as the “glass transition temperature” (Tg). The Tg value can reflect the rigidity and flexibility of polymer chains,32 where a low Tg increases the chain flexibility and activity. During the heat treatment of crystalline polymers, crystalline polymers’s upper temperature-melting point should be considered. For rubber-based polymers, the operating temperature should be sited between the glass transition temperature and the melting point. Another significant factor in determining the performance of polymer membrane separations is the degree of crystallinity. High crystalline polymer levels reduce the permeability of the guest molecule and inhibit the membrane-separation performance.33 An uneven charge distribution in polymers can lead to polarity. The charge density, dipole moment, and hydrogen bonding of the functional groups contained in the polymer cause the polymer to be polarized. A greater polymer polarity requires more hydrogen bonds to absorb electrons. According to the principle of “like dissolves like”, polymers with polar solubility exhibit a stronger adsorption-solubilization effect on polar compounds and can achieve improved separation. Therefore, when selecting a polymer, it is necessary to consider not only its mechanical strength and water stability but also the nature of the object to be treated.34 Polymers with a low Tg are more flexible and mobile, forming continuous dynamic channels inside the polymer molecules, and a higher permeability to liquid molecules; polymers with a high hydrophobicity are more suitable for organic separation, and the higher the Tg, the more rigid and chemically stable they are.35,36 Many polymers have been used to be laminated with MOFs to form membranes, but not all are suitable, and the choice of polymer type should be made wisely. As for the synthesis of polymers, since MOF polymer hybrids are prepared using already synthesized polymer materials, there are no special requirements for the synthesis conditions, which will not be described in detail herein.
3. Synthesis of MOF-based membranes
Manufacturing completely continuous, complete and defect-free membranes is key to creating MOF-based membranes. Through the tireless efforts of researchers, significant advances have been made in the development of a variety of membrane fabrication techniques over the past decade (Table 1). Next, we will detail the more commonly used synthesis methods (Fig. 1).
Table 1 Summary of the characteristics of common synthetic methods for MOF membranes
Method |
Brief description |
Advantages |
Disadvantages |
Ref. |
In situ growth |
Substrate directly immersed in growth solution, isotropic diffusion |
Simple manipulation, easy to operate |
MOF membranes are not tightly bound to each other, and thickness cannot be adjusted |
38 and 41–45
|
Low manufacturing cost |
Wide range of applications |
Secondary growth |
Seed crystals need to be grown on the substrate, and then placed in the MOF reaction solution for secondary growth |
High crystallinity |
Complex operation |
52–54
|
Wide range of applications |
Higher requirements for seed crystals |
Good control of the thickness and direction of membrane growth |
|
More stability |
|
Layer-by-layer (LBL) growth/liquid-phase epitaxy (LPE) |
The substrate is immersed in metal-only and ligand-only solutions for repeated crystal growth |
Mild preparation conditions |
Time-consuming |
57 and 108
|
Suitable for large-scale production |
High cost |
Precise control of membrane thickness |
Cannot produce a defect-free membrane layer |
Electrochemical deposition (ECD) |
MOFs are grown only on the conducting part of the substrate, and the membrane thickness can be controlled by tuning the voltage and electrolyte |
Adjustable external conditions |
N2 environment required |
69
|
Mild reaction conditions |
Slow membrane formation speed |
Low solvent consumption |
Generation of by-products |
Chemical vapor deposition (CVD) |
Consists of two steps: adsorption and reaction |
High crystallinity, no chemical contamination and corrosion |
High operating temperature |
74
|
Product transfer difficulties |
Atomic layer deposition (ALD) |
Different gas-phase precursors are alternately passed through the reactor to complete the corresponding physical and chemical reactions to produce the MOF membranes |
No solvent consumption possible |
High cost |
80 and 81
|
Self-terminating, the thickness can be controlled down to the subnanometer level |
Slow deposition rate |
Blending |
MOF particles and polymers are mixed directly without any modification to form a stable solution and then coated on the substrate surface |
Without the limitation of the substrate |
Poor compatibility of MOFs with organic polymers, membrane-formation difficulties |
83 and 84
|
Easy to use |
Substrate independent |
Wide range of MOFs to choose from |
Post-modification polymerization |
Interfacial polymerization (IP) |
Membrane formation via reverse diffusion after the polymerization of two incompatible solvents at the intersecting interface |
Simple preparation process |
Small application range |
89 and 90
|
Does not alter the mechanical flexibility of the membranes, excellent scalability |
Post-synthetic polymerization (PSP) |
Covalent linking of MOFs crystals via flexible polymer chains |
Improved MOF particle agglomeration and compatibility |
Complicated operation |
95 and 96
|
Electrospinning |
Microfibers of micron and submicron diameters are used to synthesize polymer films via certain methods |
Large porosity and specific surface area |
Easy to aggregate |
103–107
|
Good structural and chemical adjustability |
Difficult to operate |
Avoids corrosion or oxidation |
|
Mild reaction conditions |
|
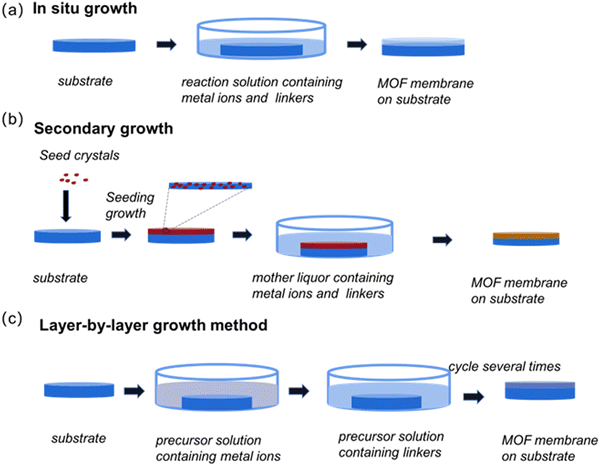 |
| Fig. 1 Schematic illustration of three commonly used MOF-based membrane preparation routes. | |
3.1
In situ growth method
As a classical MOF membrane synthesis method, the in situ growth method has been used extensively (Fig. 2). The substrate is submerged directly in the reaction solution containing the metal solution and the linker, allowing them to diffuse in the same direction, thus enabling the MOF membranes to grow through the crystallization reaction. In this process, two steps, which include ion adsorption and crystal nucleation, must be completed. Remarkably, a wide variety of MOF membranes can be obtained through in situ growth. According to the nature of the substrate, three approaches – direct synthesis, modified substrate synthesis, and the “same metal source” method – have been developed to prepare continuous MOF membranes.37
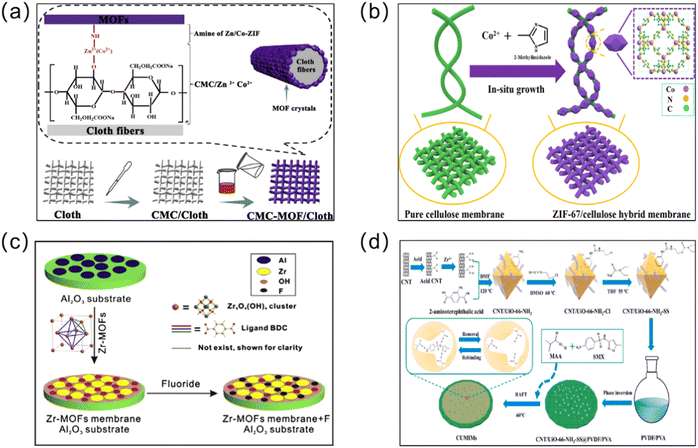 |
| Fig. 2 Schematic diagrams of in situ synthesized MOF membranes. (a) Rapid in situ synthesis of CMC/cloth and CMC-MOF/cloth composite membranes. Reprinted with permission from ref. 46. Copyright 2018 Elsevier. (b) In situ synthesis of a ZIF-67/cellulose hybrid membrane. Reprinted with permission from ref. 47. Copyright 2021 Springer. (c) Preparation of a Zr-MOF membrane using the in situ solvent thermal method. Reprinted with permission from ref. 48. Copyright 2016 Elsevier. (d) In situ synthesis of CNT/UiO-66-NH2-based molecularly imprinted nanocomposite membranes. Reprinted with permission from ref. 49. Copyright 2022 Elsevier. | |
The direct synthesis method is defined herein as the direct in situ formation of membranes on substrates without modification. In 2009, Liu et al. successfully prepared the first continuous and well-intergrown MOF-5 membrane via an in situ solvothermal method using α-Al2O3 as a porous scaffold.38 The resulting membrane had a thickness of about 25 μm, was free of defects, and had a high specific surface area. Meanwhile, the membrane was strongly bonded to the carrier and could withstand high temperatures, with the MOF-5 structure remaining stable up to 400 °C. Although this method is easy to operate, the surface of the unmodified substrate fails to offer adequate nucleation sites. In addition, MOFs tend to nucleate and grow in solution under normal operating conditions, resulting in uneven membrane formation and easy detachment from the substrate, which cannot be widely applied. According to the reported studies, this synthesis method was more often used for the synthesis of ZIF-type MOF membranes, such as ZIF-8 membranes39 and ZIF-69 membranes.40
An excellent way to improve the problem of poor substrate bonding is via chemical modification of the support. Following this idea, modified substrate synthesis was proposed. First, the substrate was modified with organic compounds (such as polydopamine) or inorganic compounds (such as hydroxide and metal oxide/sulfide, etc.). Then the modified substrate is self-grown into a membrane in the precursor reaction solution. For example, Hermes and co-workers selected COOH/CF3 groups to modify Au(111) substrates to achieve the selective nucleation and growth of MOF-5 membranes.41 The resulting membranes represented the creation of a new organic–inorganic, hierarchical nanocomposite functional material, where the MOF-5 membranes not only reached a thickness of 500 nm but also adhered well to the surface of the substrate. Inspired by this research concept, Huang et al. developed a range of continuously grown ZIF membranes (such as ZIF-22, ZIF-8 and ZIF-7 membranes) using 3-aminopropyltriethoxysilane (APTES) as a covalent linker to modify porous ceramic supports (such as TiO2, Al2O3).42 Similarly, under mild conditions, stainless-steel-nets (SSNs) were functionalized with polydopamine, and then added to the precursor solution. Covalent bonds of Zn–N and Zn–O were formed between the growing ZIF-8 layer and the carrier, which contributed to the nucleation and growth of the ZIF-8 membrane (Fig. 3).43 Not only did this method synthesize dense and continuous ZIF-8 membranes, which had an excellent membrane performance, it also had a low manufacturing cost, making it suitable for mass production.
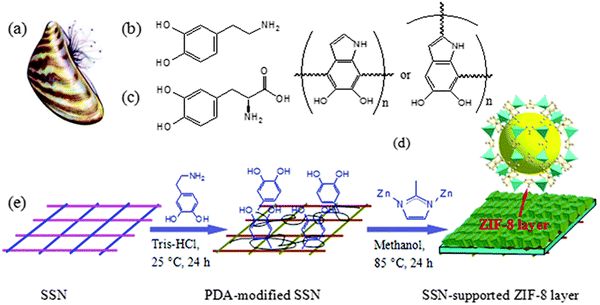 |
| Fig. 3 Mussel with byssus threads (a); chemical structures of DPA (b), DOPA (c), and PDA (d); and schematic of the preparation of a ZIF-8 molecular sieve membrane on a PDA-functionalized SSN (e). Reprinted with permission from ref. 43. Copyright 2014 Royal Society of Chemistry. | |
In both of these methods, the substrate plays only a supporting role. Unlike the above two methods, in the “same metal source” synthesis method, the substrate contains the same metal as the grown MOFs, enabling the reaction process to proceed without the addition of additional metal ions, while enhancing the bonding between the membrane layer and the substrate. Initially, the “twin copper source” method was proposed by Guo et al.44 The copper mesh that generated green copper oxide on the surface after heat treatment was mixed with a solution containing copper nitrate and trimeric acid for a specific period of time, and the HKUST-1 ([Cu3(BTC)2]) membrane was generated on the surface of the copper mesh. In this reaction, the metal source for crystal growth is Cu2+ on both the copper net and in the reaction solution, which provided the crystal with a sufficient metal source to form uniform nucleation sites for continuous membrane growth. Unlike other MOF membranes based on Al2O3 and ceramics, this MOF membrane contained a larger void volume and a higher permeability. In view of the advantages of the bimetallic source synthesis method, Neelakanda et al. used the double-zinc-source method to prepare ZIF-8 membranes.45 ZIF-8 membranes were prepared using the in situ method. First, a thin ZnO layer was deposited on a polyacrylonitrile (PAN) support membrane via magnetron sputtering, followed by nucleation and crystal growth to form a continuous ZIF-8 membrane. The main advantages of the double-zinc-source method are the rapid synthesis speed and the simple synthesis conditions.
3.2 Secondary growth method
The secondary growth method (or seeded-assisted growth method) also has wide applicability, and achieves the generation of MOF membranes by first attaching the seed crystals to the substrate and then subjecting them to solvent heat treatment by immersing them in the mother liquor.50 Unlike in situ growth, which usually results in an unsatisfactory membrane thickness, secondary growth enables easier control over the membrane thickness and direction. An important component of the secondary growth method is the seed layer. The seed size, seed layer thickness, and the bond between the seed layer and substrate all affect the separation efficiency of the resulting MOF membranes. Currently, rub-coating, dip-coating, the wiping method, spin-coating, thermal seeding and step-by-step seeding methods have been used to prepare seed layers.51 The secondary growth method is a relatively mature method for preparing MOF membranes. For instance, Yuan et al. obtained a ZIF-300 membrane via the secondary growth method.52 Firstly, they added ZIF-300 seeds on an α-Al2O3 substrate and then immersed them in a mixed solution for the solvothermal preparation of a pure ZIF-300 membrane (Fig. 4). From this, a ZIF-300 membrane about 10 μm thick was formed, which can remove 99.21% of heavy metal ions, showing good water stability and high-water permeability.
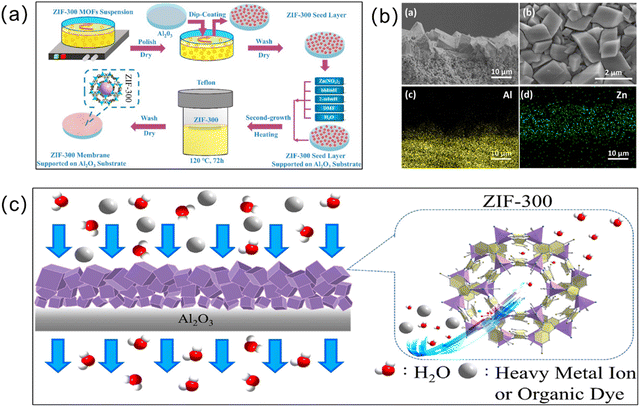 |
| Fig. 4 (a) Preparation of a ZIF-300 membrane using the secondary growth method. (b) SEM images (a, cross-section; b, surface) and EDXS mapping images (for Al (c, yellow) and Zn (d, green), corresponding to a) of the defect-free ZIF-300 membrane supported on the Al2O3 substrate (120 °C, 72 h). (c) Schematic of the process of removing heavy metal ions from water on the basis of the size-exclusion mechanism for a novel asymmetric ZIF-300 membrane. Reprinted with permission from ref. 52. Copyright 2019 Elsevier. | |
For the secondary growth method, the preparation of the seed layer is crucial, and both spin coating and dip coating are the most commonly used methods for preparing the seed layer. Gascon et al. coated a Cu3(BTC)2 seed solution on an α-Al2O3 membrane using the spin-coating method, and a Cu3(BTC)2 membrane of about 2 μm thick was prepared via secondary growth.53 Fang et al. prepared UiO-66 and UiO-66-NH2 membranes with thicknesses of 1.6 μm and 1.3 μm, respectively, by dip-coating UiO-66 NPs and UiO-66-NH2 NPs onto α-Al2O3 tubular scaffolds.54 Both the UiO-66 and UiO-66-NH2 membranes exhibited a high rhodamine B (RB) removal rate (>80%), and exhibited high permeability, good dye selectivity and reusability. Secondary growth can not only achieve uniform nucleation and control over the growth thickness of the membrane, but can also be used to obtain the ideal thickness of the membrane materials. One major issue that hinders the further development and large-scale application of this approach is that the operating conditions are complicated.
3.3 Layer-by-layer (LBL) growth method
The layer-by-layer (LBL) growth method, also known as liquid-phase epitaxy (LPE), begins with the repeated immersion of the substrate into respective solutions containing metal ions and organic ligands, where the layer is deposited continuously over several cycles after rinsing off the excess precursor solution, forming a continuous MOF layer55 (Fig. 5). The most important feature of the LBL method is the ability to form a continuous MOF layer of precisely controlled thickness under mild conditions, and due to the unique advantages of LBL technology, an important class of MOF membranes, i.e., surface-attached metal–organic frameworks (SURMOFs) can be produced.56 Three types of SURMOF, namely HUKST-1, laminated MOF and hybrid MOF (MOF-on-MOF), have been reported so far, all of which have shown great potential and wide applications in water treatment. Taking inspiration from the LBL method, Shekhah et al. constructed the first ZIF-8 membranes via LBL deposition on an α-Al2O3 support.57 After 150 cycles, extremely thin (0.5–1 μm) and uninterrupted ZIF-8 membranes were obtained for the separation of H2–CO2, H2–N2, H2–CH4 and C2H4–C2H6 in gas mixtures (Fig. 5c). Gao et al. also applied the LBL method to prepare UiO-66-NH2 separation membranes with good hydrophobicity and lipophilicity.58 On a polymer substrate pretreated with high-energy γ-irradiation, the metal and organic ligand layers were incubated separately in progressive layers. Nanothickness MOF coatings (NTMCs) of ∼44 nm thick were achieved through constant repetition. Using this method, chemical bonds formed between the substrate and NTMCs and between the MOF layers, enhancing adhesion with the substrate. As a typical MOF membrane synthesis route, the LBL approach enables the use of automated machines to complete the entire membrane growth process under mild preparation conditions. Although the LBL method enables height control over the thickness, the process is cycled several times and consumes large amounts of organic solvents, which undoubtedly increases the cost of membrane production and the manufacturing time to some extent. In addition, Wang et al. carefully selected ceramic substrates with exceptional resistance to high temperatures, mechanical strength, and good antiswelling properties.59 They then used an in situ LBL technique to create hybrid membranes made of ZIF-8 and poly(sodium 4-styrenesulfonate) (PSS). The in situ LBL method resulted in a greatly enhanced dispersion of the ZIF-8 particles and compatibility with PSS. The ZIF-8/PSS composite membrane was used for the nanofiltration removal of the methyl blue (MB) dye from water. On the one hand, because the pore size of the ZIF-8 particles is smaller than that of the MB molecules but larger than that of water molecules, both can be sieved. On the other hand, the anionic polyelectrolyte PSS can repel the MB anionic dye with the same charge through the charge repulsion effect. Therefore, the composite membrane can remove 98.6% MB in water. And the stability of the membrane was improved because of the good compatibility, and the dye removal rate and flux of the membrane remained at a constant level under 20 h of continuous operation. Due to their excellent mechanical properties, ceramic substrates show great potential for MOF-based membrane preparation.
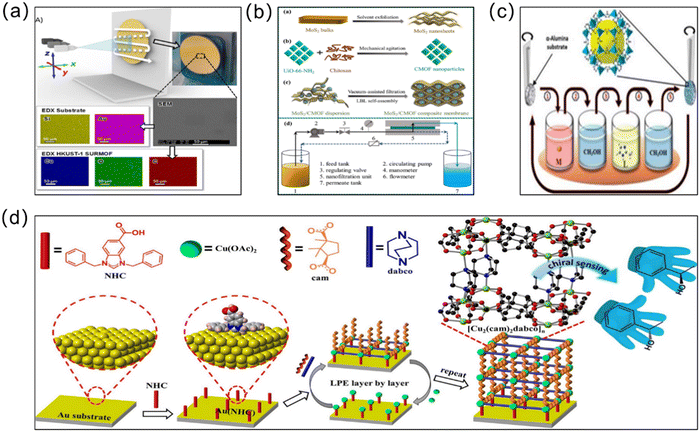 |
| Fig. 5 (a) Synthesis of HKUST-1-based membranes using a stepwise spray method. Reprinted with permission from ref. 60. Copyright 2017 Wiley-VCH Verlag GmbH & Co. KGaA, Weinheim. (b) Electrostatic LBL self-assembly strategy for constructing the MoS2/CMOF composite membrane. Reprinted with permission from ref. 61. Copyright 2022 Elsevier. (c) Schematic representation of the LBL method used for growth of the ZIF-8 membrane. Reprinted with permission from ref. 57. Copyright 2014 Royal Society of Chemistry. (d) Preparation of [Cu2(cam)2dabco]n thin films via the liquid phase epitaxial LBL method. Reprinted with permission from ref. 62. Copyright 2020 American Chemical Society. | |
3.4 Deposition
Deposition refers to the continuous settling of solid particles suspended in a liquid. The settled material forms layers without natural accumulation. MOF membrane preparation methods derived via deposition are relatively widely used. Three deposition methods for preparing MOF membranes are summarized as follows: electrochemical deposition (ECD), chemical vapor deposition (CVD), and atomic layer deposition (ALD).63
In order to shorten the synthesis time and reduce the thickness of the MOF membranes, another strategy, known as the ECD method, has been developed to fabricate MOF membranes (Fig. 6). To obtain MOF membranes with the desired thickness, the voltage and electrolyte can be regulated so that the growth of MOF crystals, which occurs only on the conductive portion of the substrate, is automatically stopped. After four stages, which include initial nucleation, island growth, mutual growth and detachment, a continuous MOF membrane is ultimately formed via ECD. In addition, the metal source in ECD originates from oxidation of the anode, so there is no interference of anions (e.g., nitrate, sulfate, chloride, or chloride) with the metal source without the addition of metal salts.64 Depending on the deposition method, three types of ECD, i.e., anodic electrode deposition (AED), cathodic electro deposition (CED), and electrophoretic deposition (EPD), have been reported.65
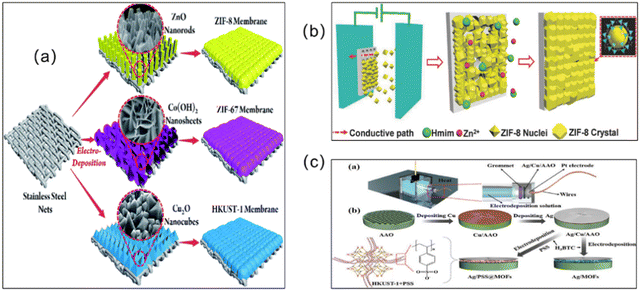 |
| Fig. 6 (a) Schematic illustration of the in situ growth of three different MOF membranes on supports modified via electrodeposition. Reprinted with permission from ref. 70. Copyright 2017 Royal Society of Chemistry. (b) Synthesis of MOF films on various substrates via electrophoretic deposition. Reprinted with permission from ref. 71. Copyright 2018 Wiley-VCH Verlag GmbH & Co. KGaA, Weinheim. (c) Electrochemical deposition to form an Ag/MOF membrane and the Ag/PSS@MOF composite membrane. Reprinted with permission from ref. 72. Copyright 2023 Wiley-VCH GmbH. | |
During the AED synthesis process, the metal anode undergoes an electrochemical reaction and gradually dissolves under high positive voltage conditions. Subsequently, the metallic ions in solution combine with organic ligands to create membranes. The crystal size and thickness of the MOF membranes synthesized via the AED method are determined by the applied voltage.66 The AED synthesis process is relatively flexible, and it is more often combined with other methods to jointly prepare MOF membranes with a better performance. During AED, the temperature has no effect on the solubility of the linker, the conductivity of the electrolyte, the kinetics of MOF formation and the resulting morphology.67
CED occurs through the deprotonation of organic ligands, enabling the membrane to be formed via cathodic precipitation. When an electrochemical reaction is performed, hydroxide ions are generated in the alkaline region near the cathode, and the OH− react with the linker to induce deprotonation of the linker, and the deprotonated linker reacts with the metal precursor solution to produce a MOF membrane on the cathode surface. Compared with AED where the MOF layer and substrate are firmly bonded, CED also has the advantage of a flexible substrate.68 The application potential, deposition time, supporting electrolyte, substrate and additives all influence the synthesis of MOF membranes. In particular, the deposition time controls the thickness and mass loading of the MOF membranes.
Unlike the first two methods where MOFs are deposited in situ on the substrate, MOFs deposited using EPD are grown in reverse order to create a membrane. By applying an external electric field to two conductive electrodes immersed in a solution containing MOFs, the MOF particles move towards the electrode with the opposite charge to deposit the membrane. ECD is used widely because of its simple operation, short time consumption and the ability to the control membrane thickness. For example, Hod et al. selected four representative MOFs (NU-1000, UiO-66, HKUST-1, and MIL-53) to test the broad applicability of preparing MOF membranes using the EPD method.69 Their experimental results indicated that these four MOFs can be successfully deposited into membranes. This is further evidence that ECD is applicable to a wide range of MOF components.
As a basic technology for micro component manufacturing, CVD has a wide range of applications. CVD is carried out by evaporating the substances involved in the reaction to the gaseous state, followed by a two-step chemical reaction of adsorption and reaction, which results in a uniform and high-quality membrane after deposition.73 A significant advantage of CVD is that because the organic linker is vaporized into gaseous form, the substrate is not contaminated and corroded by the solution. Stassen and co-workers74 demonstrated a MOF-CVD method, which prepared ZIF-8 membranes with homogeneous and high quality properties (Fig. 7b). First, the precursor solution was vapor processed and deposited onto the substrate using atomic layer deposition to form a dense metal oxide layer. Subsequently, a continuous vapour–solid reaction was carried out. After a two-step reaction, a 500-nm-thick continuous ZIF-8 membrane was successfully prepared. Considering that CVD can achieve the solvent-free synthesis of MOF membranes, it has great potential for the preparation of green and pollution-free MOF membranes.75
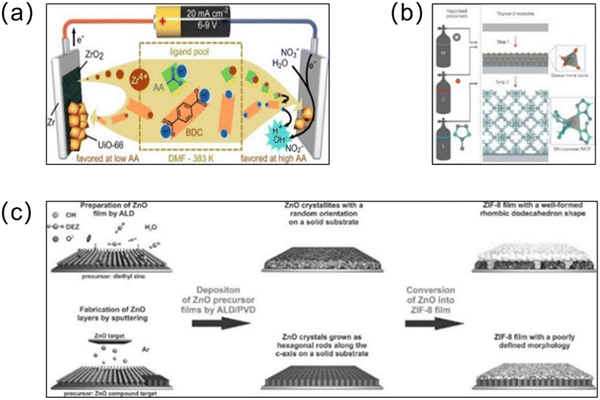 |
| Fig. 7 (a) Schematic illustration of the anodic and cathodic electrochemical deposition mechanisms for UiO-66 membranes. Reprinted with permission from ref. 82. Copyright 2015 American Chemical Society. (b) Chemical vapor deposition of ZIF-8 thin films. Atom colors: zinc (grey) oxygen (red), nitrogen (light blue) and carbon (dark blue); hydrogen atoms are omitted for clarity. Reprinted with permission from ref. 74. Copyright 2016 Nature Materials. (c) Schematic illustration of the synthesis of ZIF-8 membranes from ZnO precursor films deposited on solid substrates. Reprinted with permission from ref. 80. Copyright 2014 Wiley-VCH Verlag GmbH & Co. KGaA, Weinheim. | |
ALD (or molecular layer deposition (MLD)) is a special CVD technique.76 Similar to CVD, ALD can also achieve the solvent-free formation of uniform membranes,77 and a unique advantage of ALD is that the “self-limiting” surface reactions can achieve nanometer-thick membranes.78 Gas phase precursors are deposited on the substrate via adsorption or surface reactions to form atomic layers, where the thickness of the generated MOF membrane can be controlled precisely through continuous cycles.79 In recent years, ALD has become the preferred deposition method for depositing high-quality thin membranes. Khaletskaya and co-workers used ALD to produce ZnO precursor membranes that could be used for nucleation and growth of ZIF-8 membranes, marking the first known instance of such a methodology (Fig. 7c).80 Subsequently, to improve the problem of the poor conformation that results when MOF crystals are integrated onto fibers, Al2O3 substrates were obtained after 50 ALD cycles on polymeric fiber substrates, and then the HKUST-1 MOF was grown on the resulting core@shell (fiber@Al2O3) substrate layer by layer.81 The addition of ALD-Al2O3 enhanced the wettability of the hydrophobic polymer while providing more sites to promote the MOF growth. Furthermore, the successful preparation of HKUST-1 MOF membranes demonstrated the potential applicability of this method for combining other polymer materials and MOFs.
3.5 Blending methods
3.5.1 Direct blending.
Mixing MOF crystals and other materials to form a membrane can solve the problems encountered with a single inorganic membrane, such as low elasticity, low stretchability and high preparation costs. The blending method is a relatively simple method for preparing MOF hybrid membranes. Two methods, direct blending and post-modification polymerization, have been developed. The direct mixing method coats the substrate surface with a suspension formed by mixing the original MOFs and other materials to form a membrane. After a period of curing and drying, a complete MOF membrane can be obtained. Interestingly, based on this strategy, Fan et al. reported a spray self-assembly technique to prepare MOF membranes.83 A ZIF-8-polydimethylsiloxane (PDMS) suspension and a solution of the tetraethyl orthosilicate (TEOS) cross-linking agent and the dibutyltin dilaurate (DBTDL) catalyst were poured into two self-stirring pressure drums, respectively. Then, they were simultaneously sprayed onto the polysulfone (PS) substrate. Using the mechanical atomization method, the ZIF-8 nanoparticles were uniformly dispersed on the PS surface, and an ultrathin uniform ZIF-8 membrane with high loading was achieved. In addition, the direct mixing method allows the MOF membrane to be separated from the substrate, making it more convenient to use. For example, the aromatic poly(m-phenylene isophthalamide) (PMIA) polymer substrate solution and MIL-53(Al) particles were mixed and stirred continuously to obtain a homogeneous polymer solution, and, after removing the air bubbles, the polymer solution was cast onto a clean glass plate and then underwent an inverse rotation to prepare substrate-free MIL-53(Al) membranes.84 In mixed Na2SO4/dye solutions, the membrane was able to achieve over 80% removal of the nitroso-R salt, xylenol orange, and ponceau S, showing a broad application in dye desalination.
3.5.2 Post-modification polymerization.
Direct mixing between MOF crystals and polymers to form membranes can lead to the agglomeration of MOF particles during the synthesis process due to the difference in quality and interfacial compatibility between them, resulting in a large number of void defects after membrane formation, further reducing the membrane separation performance. Therefore, researchers have used the post-modification polymerization method to address the incompatibility of MOFs and polymers. First, the surface modification of MOF particles is carried out, and then they are combined with the polymer to form membranes. This strategy is mainly achieved via the chemical modification of MOFs after synthesis, such as through cation exchange, linker exchange, and post-synthesis metallization. Considering the high efficiency applications of MOF-based membranes, derived from the post-modification polymerization design concept, many MOF membrane preparation strategies have been generated.
Interfacial polymerization.
Unlike simple physical blending methods, interfacial polymerization (IP) synthesis is based on the reverse diffusion of two insoluble solvent molecules on the substrate (Fig. 8).85 In this method, an interfacial reaction occurs between the aqueous and organic phases, and the MOFs crystallize at the interface to form a membrane. A large portion of MOF-based membranes are thin-film nanocomposite (TFN) membranes supported by polymers, where most TFN membranes are synthesized via IP methods.86 Therefore, IP dominates in the synthesis of MOF-based membranes.87 Zirehpour et al. prepared a thin PA layer on a polyethersulfone (PES) substrate via the IP method and then inserted MOF nanosheets into it for the first time.88 Organic linkers in the MOF provide better compatibility between the MOF and organic polymers through covalent or non-covalent bonding. The resulting thin film composite (TFC) forward osmosis (FO) membranes have improved permeability to pure water and show great potential for desalination applications. In recent years, MOF-based TFN membranes have been widely prepared. For example, on a porous poly(phenylsulfone) (PPSU) substrate, Shukla et al. prepared highly permeable and salt-resistant TFN membranes via the IP reaction of porous Zn-MOF and polyamide.89 Adding Zn-MOF with its intrinsic nanopore structure gives the membrane more water channels, increases the surface hydrophilicity, and improves the water permeability. Moreover, the combination of the spatial repulsion effect and the electrostatic repulsion effect produces the Donnan effect, which enabled up to 99% removal of Na2SO4 by the MOF TFN membrane. The IP method enabled the coordination of hydrogen and amide bonds between the Zn-MOF and polyamide, which enhanced the binding of the filler and polyamide layers, providing the Zn-MOF TFN membranes with long-term water resistance and stability. However, the chlorine concentration can affect conventional TFC membranes and reduce the membrane selectivity. The chlorine resistance of MOF TFN membranes was also investigated in this experiment. Due to the protective amide bonds produced by Zn-MOFs during IP and the good hydrogen bonding and hydrophilicity between the MOF material and the polyamide, damage to the composite membrane by chlorine was avoided. After 264 hours of chlorine immersion and 72 hours of filtration, the MOF TFN membrane performance remained stable. In addition, Liu et al. treated UiO-66-NH2 nanoparticles with palmitoyl chloride to prevent agglomeration by introducing long alkyl chains. Then the modified UiO-66-NH2 nanoparticles and a TMC/cyclohexane organic solution were subjected to the IP reaction to prepare TFN membranes.90 Dispersing the palmitoyl chloride-modified UiO-66-NH2 nanoparticles in organic solvents, on the one hand, reduced the agglomeration of MOF particles, and, on the other hand, the –COOH generated by the ionization in the organic phase adsorbs the positively charged amine monomer, making the substrate more hydrophilic. Besides, ZIF-8/GO TFN membranes with effective antibacterial and desalination properties91 and Ag@HKUST-1/PA TFN membranes, which have antibacterial properties and the ability to degrade pesticides,92 were also synthesized via the IP method. Although IP technology is currently widely used for the fabrication of PA layers in many commercial TFC membranes and for the preparation of MOF TFN or TFC membranes in laboratory-scale studies, it is not perfect. It is still a challenge to prepare extremely thin PA layers and requires more organic solvents to be consumed, which are more expensive and difficult for large-scale generation.93 It is hoped that the existing IP technology can be modified in the future so that these disadvantages can be overcome and it can be better applied to the preparation of MOF membranes.
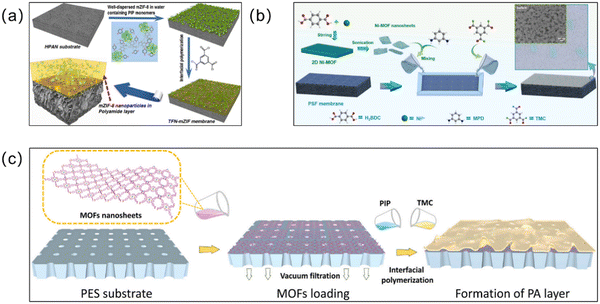 |
| Fig. 8 (a) Preparation process of a TFN containing PSS-modified ZIF-8 nanoparticles via IP. Reprinted with permission from ref. 29. Copyright 2016 American Chemical Society. (b) Schematic illustration for the fabrication of a 2D-MOF-modified TFN membrane via the IP reaction. Reprinted with permission from ref. 97. Copyright 2022 Elsevier. (c) Fabrication process for the MOF-interlayered TFN membrane. Reprinted with permission from ref. 98. Copyright 2022 Elsevier. | |
Post-synthetic polymerization.
Inspired by IP, a new post-synthetic modification method for post-synthetic polymerization (PSP) has been proposed.94 In this method, MOF crystals are covalently linked by flexible polymer chains in an orderly manner, achieving the copolymerization of MOFs with polymerizable functional groups and organic monomers to improve the separation performance. Yao et al. used the PSP method to polymerize UiO-66-NH2 nanoparticles and polyurethane low polyester oligomers for the preparation of membranes that can selectively adsorb hydrophilic dyes (e.g., eosin Y (EY), RB, malachite green (MG), and methylene blue (MB)).95 The resulting membranes were substrate-independent, defect-free, and stable, enabling the separation of individual dyes (EY and RB) and mixed dyes in aqueous solutions. In another study, Min et al. used PSP to realize a luminescent membrane comprised of a MOF, polymers and lanthanide ions.96 Specifically, through copolymerization of the MOF and ethyl methacrylate doped with lanthanide ions (Eu3+ or Tb3+), a uniform MOF membrane with a good structure and excellent luminescence properties was successfully prepared.
Electrospinning.
Another effective strategy for improving the efficiency of MOF membrane separation is electrospinning (Fig. 9). As a relatively new technology, it is widely used to polymerize microfiber materials of micron and submicron diameters. Electrospun fiber membranes have been widely used as ideal carriers for MOFs due to their large porosity, specific surface area and adjustable structure.102 Recently, combining functional nanoparticles with electrostatic spinning fibers has become a hot topic in the current research field. More scholars are also working on the preparation of MOF/polymer hybrid membranes via electrospinning. Wang et al. prepared nanocomposite membranes by introducing ZIF-8 into green biodegradable poly(lactic acid) using the electrospinning method.103 To enhance the nanofiber substrate adhesion, Yang et al. used the “solvent basing” method to pretreat the poly(vinylidene fluoride) substrate, and then performed electrospinning with the MOF materials.104 Using this method, the water contact angle of the membrane was increased and the NaCl removal rate was 99.99% with a high cycling stability. MOF membranes produced via electrospinning are effective in removing heavy metal ions from solution. For example, Liu et al. synthesized polyurethane (PU)/UiO-66-NH2 and PAN/UiO-66-NH2 fiber membranes using electrospinning.105 The composite membrane can adsorb precious metal Pd(II) and Pt(IV) from strongly acidic solutions with a good regeneration performance. Efome et al. selected the PAN nanofiber with hydrophilic properties and Zr-based MOF-808 materials to prepare composite PAN membranes via electrospinning.106 The loading of the MOF on the composite membrane was up to 20%, which can adsorb and separate Cd2+ and Zn2+ effectively. Guo et al. prepared UiO-66 membranes via electrospinning using PAN as the substrate and uniformly mixing it with the Zr-based MOF (UiO-66).107 This Zr-based MOF composite membrane maintains the original adsorption performance of the MOF for As(III) and As(V), and exhibits a stable performance and easy recovery. As introduced above, MOF membranes prepared via electrospinning can achieve “zero loss of material”, which is beneficial for environmental safety.
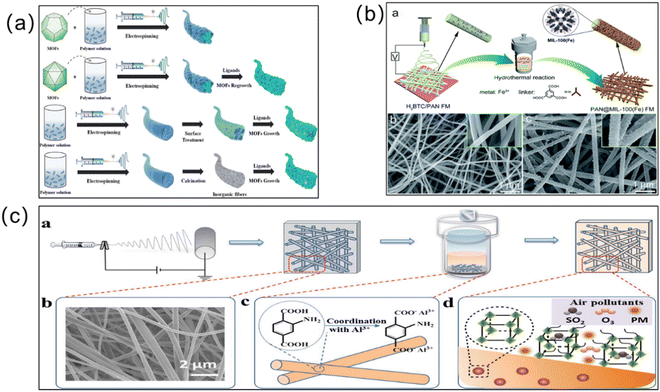 |
| Fig. 9 (a) Schematic diagram of electrospinning for the manufacture of MOF nanofibers (NFs). Reprinted with permission from ref. 99. Copyright 2022 Elsevier. (b) Preparation of the PAN@MIL-100(Fe) fiber membrane via electrospinning. Reprinted with permission from ref. 100. Copyright 2019 Royal Society of Chemistry. (c) Preparation and adsorption process of a MOF-based fiber membrane prepared via electrospinning. Reprinted with permission from ref. 101. Copyright 2019 Royal Society of Chemistry. | |
In addition to the methods mentioned above, there are many methods for the synthesis of MOF membranes. Several innovative strategies have been shown to be useful in the production of MOF membranes, such as pressure-assisted self-assembly (PASA) filtration technology, the contra-diffusion method, and so on (Table 2). To further enhance the membrane separation efficiency, researchers are developing new methods to enable MOF membranes to be more widely used.
Blending |
MIL-53(Al) |
Poly(m-phenylene isophthalamide) (PMIA) |
Water permeates above 45 L m−2 h−1 under a 1.0 MPa operating pressure, and the removal rate of paraxylene xylenol orange was about 99% |
84
|
Post-modification polymerization |
Interfacial polymerization (IP) |
MOF nanocrystals, consisting of silver(I) and 1,3,5-benzenetricarboxylic acid (3HBTC) |
14 wt% polyethersulfone (PES) and 1 wt% polyvinylpyrrolidone (PVP) |
Water flux was 82 L m−2 h−1, seawater fluxes of above 34 L m−2 h−1 |
88
|
Zn-MOFs |
Poly(phenylsulfone) (PPSU) |
Water permeability of 2.46 ± 0.12 LMH bar−1, removal of NaCl (>90%) and Na2SO4 (>95%), showed excellent water stability during 72 h of filtration and showed resistance to chlorine after 264 h of a chlorine immersion test |
89
|
UiO-66-NH2 |
Polyacrylonitrile (PAN) |
When the UiO-66-NH2-PC loading amount was within 0.10% w/v, the MgSO4 removal was about 100% and NaCl removal was above 30% |
90
|
ZIF-8 |
Poly(ether sulfone) (PES) |
Water permeability was 40.63 L m−2 h−1 MPa−1, Na2SO4 and MgSO4 removal rates were 100% and 77%, respectively; antimicrobial activity was 84.3% |
91
|
Ag@HKUST-1 |
Ultra-filtration (UF) poly(sulfone) supporting membranes |
Complete degradation of 2,4-dichlorophenoxyacetic acid (2,4-D) within 17 min, high salt removal values of up to 90%, and the water flux was 27 kg m−2 h−1 |
92
|
Post-synthetic polymerization (PSP) |
UiO-66-NH2 |
Free-standing membrane |
Thickness of about 100 μm, effective removal of aqueous solutions of eosin Y (EY), and RB |
95
|
Electrospinning |
MOF (iron 1,3,5-benzenetricarboxylate) |
Non-woven substrate |
Water vapor flux was 2.87 kg m−2 h−1, the removal rate of NaCl at 35 g L−1 was 99.99%, no Fe2+ ion leaching |
104
|
UiO-66 and UiO-66-NH2 |
Aluminum foil, Teflon paper, or filtration paper |
Adsorption of precious metals Pd(II) and Pt(IV) from strongly acidic solutions |
105
|
MOF-808 |
Poly(vinylidene difluoride) (PVDF) |
The maximum adsorption capacities were 225.05 and 287.06 mg g−1 for Cd2+ and Zn2+, respectively |
106
|
UiO-66 |
Polyacrylonitrile (PAN) |
The maximal adsorption capacities of the hybrid membrane for As(V) and As(III) were 42.17 mg g−1 and 32.90 mg g−1, respectively |
107
|
Table 2 Comparison of the performance of MOF membranes synthesized using different methods
Method |
Membrane type |
Membrane performance |
Ref. |
MOF |
Support |
In situ growth |
MOF-5 |
α-Al2O3 |
Langmuir surface area of 2259 m g−1; membrane thickness is around 25 μm, can withstand 400 °C high temperatures |
38
|
ZIF-8 |
Polydopamine (PDA)-modified stainless steel nets |
High selectivity and high permeability |
43
|
UiO-66-NH2 |
Polyvinylidene fluoride (PVDF)/polyvinyl alcohol (PVA) |
The adsorption capacity of SMX was 2.11 mg g−1, and after 8 cycles, the adsorption capacity of CUMIMs for SMX remained relatively stable, still reaching 87.1% of the maximum adsorption capacity |
49
|
UiO-66-NH2 |
Polyvinyl alcohol (PVA) |
The water permeability was 130.9 ± 2.9 L m−2 h−1 MPa−1 with significant removal of Congo red, methyl blue, active black 5 and direct red 23 (99.89–100%) |
109
|
Secondary growth |
ZIF-300 |
α-Al2O3 |
Thickness of 10 μm; high water permeance (39.2 L m−2 h−1 bar−1); the removal rate of dyes (RhB, MB, MO) was higher than 98% and the removal rate of heavy metal ions was 99.21% |
52
|
UiO-66 and UiO-66-NH2 |
α-Al2O3 |
Thicknesses of 1.6 μm and 1.3 μm, respectively, and the removal efficiency of RB was greater than 80% |
54
|
Layer-by-layer (LBL) growth/liquid-phase epitaxy (LPE) |
UiO-66-NH2 |
PP films |
Thickness of 44 nm, good hydrophobicity and lipophilicity, can be used for oil–water separation |
58
|
ZIF-8 |
Poly(sodium 4-styrenesulfonate) (PSS) |
Water flux was 210 L m−2 h−1 bar−1, with a 98.6% nanofiltration removal toward MB from water |
59
|
UiO-66-NH2 |
PVDF |
Water permeance was 78.98 ± 1.45 L m−2 h−1 bar−1, with superior antibiotic removal (98.01 ± 1.12% for ciprofloxacin and 94.31 ± 0.68% for ofloxacin) |
61
|
Electrochemical deposition (ECD) |
HKUST-1 |
Anodic aluminum oxide (AAO) membrane |
Excellent ion selectivity and ultrahigh permeability, showed an ultra-high energy conversion efficiency of 48.76% at a 100-fold salinity gradient |
72
|
Chemical vapor deposition (CVD) |
ZIF-8 |
Titanium-based layers |
Thickness of 500 nm, green and pollution-free |
74
|
Atomic layer deposition (ALD) |
HKUST-1 |
Non-woven polypropylene (PP), polyethylene terephthalate (PET), cotton fiber mats |
Good uniformity and high fiber coverage of MOF membranes with a specific surface area of ∼535 m2 gMOF−1 |
81
|
4. Types of MOF hybrid membrane
In order to achieve excellent separation performance, more scholars have combined MOFs with other functional membranes to form MOF hybrid membranes (Fig. 10). MOF hybrid membranes can simultaneously combine the molecular transport channels of two or even more materials with special morphological microstructures, and integrate the excellent properties of multiple materials. MOF–carbon based hybrid membranes, MOF–LDH hybrid membranes, MOF–zeolite molecular sieve hybrid membranes, MOF-other skeletal material hybrid membranes (such as MOF–MOF and MOF–COF hybrid membranes), MOF–ionic liquid hybrid membranes, and MOF–organic polymer hybrid membranes are the main types of MOF hybrid membrane at present.110 Next, we will introduce these different types of MOF hybrid membrane in detail.
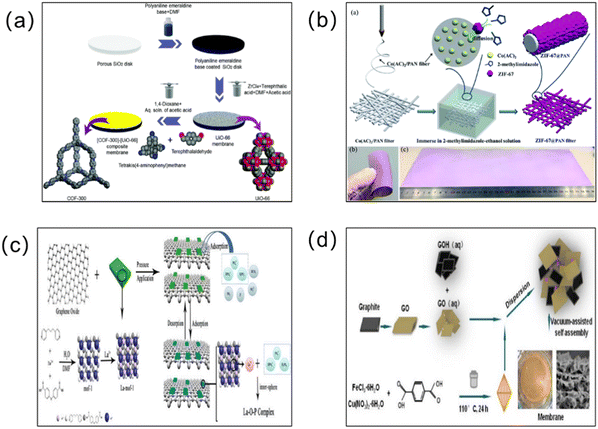 |
| Fig. 10 (a) Strategy for the fabrication of the [COF-300]–[UiO-66] composite membrane. Zirconium, carbon, nitrogen, and oxygen atoms are shown as cyan, gray, blue, and red, respectively. Hydrogen atoms are omitted for clarity. Reprinted with permission from ref. 111. Copyright 2018 Royal Society of Chemistry. (b) Schematic representation of the fabrication procedure for ZIF-67@PAN filters. Reprinted with permission from ref. 112. Copyright 2018 Royal Society of Chemistry. (c) Schematic diagram of the construction of the lanthanum-modified MOF–graphene oxide composite membrane. Reprinted with permission from ref. 113. Copyright 2020 Elsevier. (d) Preparation of the GO/GOH/FeCuBDC ternary blend membrane. Reprinted with permission from ref. 114. Copyright 2022 Elsevier. | |
4.1 MOF–carbon-based hybrid membranes
In order to achieve a better separation effect, researchers have chosen to combine carbon-based materials and MOFs to form MOF–carbon-based material hybrid membranes. As typical carbon nanomaterials, graphene oxide (GO) and carbon nanotubes (CNTs) have promising applications in the fields of energy storage, catalysis, separation, and sensing.115–117 At present, MOF–carbon-based hybrid membranes mainly include MOF–GO hybrid membranes and MOF–CNT hybrid membranes. GO is an important type of graphene derivative. It is a two-dimensional (2D) carbon material with a single atomic layer. In contrast to graphene, GO is considered to be a more economically viable option118 due to the oxygen-containing functional groups on the thin GO layers,119 which enable GO to exhibit good hydrophilicity and be easily dispersed in water. When GO is dispersed in water, the carboxyl groups are hydrolyzed into negatively charged carboxylic acid and hydrogen ions, thus a stable water-dispersible solution is formed. Subsequently, a separation membrane made of single-layer GO sheets stacked in parallel can be prepared via spraying, spin coating and vacuum filtration. Due to the excellent properties of GO, researchers have considered hybridizing and combining it with MOF materials to form a membrane. Li et al. proposed a novel environmentally friendly one-step etching-assisted cross-linking strategy to synthesize hollow MOF/GO composite membranes with good antifouling and desalination properties.120 Due to the inclusion of ZIF-8 in the hollow structure, the interlayer spacing of the GO nanosheets was expanded, providing more water channels. Meanwhile, ZIF-8 crystals modified with tannic acid cross-linked with the adjacent GO nanosheets through π–π interfacial interactions and the abundant –OH groups on their surfaces increased the permeability of the membranes, resulting in a more stable structure and a much higher antifouling performance of the composite membrane. The modified MOF/GO composite membrane with its stable 3D/2D structure can achieve a higher than 99% removal of Congo red (CR) and an 86.3% removal of Na2SO4 using an optimal MOF loading. Qu et al. embedded 3D ZIF-8 into graphene oxide membranes to prepare ZIF-8/GO membranes with a high water permeability.121 By adding positively charged ZIF-8 to neutralize the negative charge in GO, the defects presented in the single-layer GO could be masked, further enhancing the electrostatic stability of the GO membrane (GOM) and improving the structure of the separation membrane.122 Compared with the pure GOM, the composite nanofiltration membrane showed a 6-fold higher water permeability and removed more than 99% of MB and RB. Meanwhile, dopamine-modified prGO@cHKUST-1 composite membranes were prepared.122 GO was partially reduced by the addition of polydopamine (PDA), and the interlayer spacing of GO was increased by the insertion of cubic HKUST-1. These changes to the stacking pattern of GO were beneficial to form more active sites on the membrane surface. The prGO@cHKUST-1 membrane permeability was significantly increased, demonstrating an admirable separation capability in oil–water emulsions.
Recently, nanostructured carbon materials have become increasingly popular because of their unique atomic structure and excellent physical and mechanical properties. CNTs, as a typical one-dimensional nanomaterial, are seamless tubular structures curled around the central axis of 2D graphene sheets. Considering the high specific surface area and special mechanical properties, separation membranes constructed from CNTs with a high permeability are ideal materials for separation and filtration.123 For example, researchers seeded ZIF-8 nanocrystals on CNT bucky-paper supports and synthesized ZIF-8/CNT membranes via the secondary growth method. Carbon nanotubes were fully embedded within the ZIF-8 matrix, resulting in a novel CNT–ZIF-8 hybrid membrane boasting excellent selectivity and hydrothermal stability.124 The new CNT–ZIF-8 hybrid membranes were also an ideal material for the separation of complex gases and liquids. An alternative preparation strategy is that carbon nanotubes covered with MOF particles were successfully prepared using NH2-MIL-101(Al) for in situ growth on carbon nanotubes.125 Subsequently, the synthesized composites were applied to the preparation of polyimide-based MMMs. These synthesized MMMs showed much improved permeability and gas selectivity, which also provided a more efficient way to modify the MOFs on the filler.
4.2 MOF–LDHs hybrid membranes
Layered double hydroxides (LDHs), consisting of interlayer anions and positively charged laminates stacked on top of each other, are a typical representative of ionic layered compounds, and include hydrotalcite and hydrotalcite-like compounds (HTlcs). Their general formula is [M1−x2+Mx3+(OH)2](An−)x/n·zH2O (where M2+ and M3+ represent di- and tri-valent metal ions, respectively, and An− denotes inorganic or organic anions).126 As an important class of inorganic separation membrane materials, LDHs consisting of positively charged layers and charge-balanced anions exhibit highly tunable interlayer voids, making them attractive for the separation of gas or liquid mixtures.127 A characteristic feature of LDHs is their very uniform gallery height that can be adjusted by inserting different anions. However, the LDH membranes often include a large number of water molecules between the layers, which will prevent the diffusion and transmission of other gases and liquids molecules. So, LDH membranes need to be activated by heating to remove the interlayer water molecules.128 Using this strategy, Liu et al. successfully synthesized ZIF-8–ZnAl-NO3 LDH composite membranes through the partial self-conversion of MOFs by laminated membranes. Firstly, ZnAl-NO3 LDH membranes were grown in situ on a γ-Al2O3 substrate, which can provide a zinc source for ZIF-8 growth. Then, the LDH membranes were partially dissolved via the solvothermal method in methanol solution, leading to the synthesis of the ZIF-8–ZnAl-NO3 LDH membranes.129 Due to the specific affinity of LDHs for CO2 and the partial dissolution of the ZnAl-NO3 LDH membrane, the diffusion barrier was lowered and the membrane thickness was reduced. Moreover, the addition of ZIF-8 achieved charge compensation for the LDH interlayer channel, further enhancing the separation performance of the membrane.
4.3 MOF–zeolite molecular sieve hybrid membranes
Zeolite molecular sieves are microporous crystalline materials formed by crystalline alum inosilicate metal salts. Common zeolite molecular sieves are NaA (LTA-type structure), ZSM-5 (MFI-type structure), X or Y (FAU-type structure), AIPO-5 (AFI-type structure) molecular sieves and so on.130 MOF–zeolite molecular sieve hybrid membranes are formed mainly via the distributed assembly method. Currently, the hybrid membranes prepared are assembled mainly from ZIF-8 with an LTA-type or T-type molecular sieve distribution. For instance, Zhang et al. first introduced the NaA zeolite membrane as a modified layer via the secondary growth of microchannels. Then, a catalyst layer consisting of a ZIF-8 membrane was grown on top of the NaA zeolite layer using a ZnO-induced synthesis method, resulting in the successful synthesis of the stable ZIF-8/NaA composite membrane.131 Furthermore, Yeo et al. synthesized the ZIF-8–zeolite-T hybrid membrane with high CO2/CH4 selectivity.132 Firstly, the ZIF-8 continuous layer was prepared through novel vacuum thermal seeding with α-Al2O3 as the carrier, and then zeolite T was deposited in the crystal interstices of the ZIF-8 layer, supplemented by secondary growth to obtain the ZIF-8–zeolite-T hybrid membrane. After the double screening of ZIF-8 and zeolite T, the separation performance of the hybrid membrane was significantly improved and showed both good stability and high activity after 50 h. By adding ZIF-8, the zeolite T hybrid membrane achieved a good balance of permeability and selectivity.
4.4 MOF–MOF/MOF–COF hybrid membranes
MMMs can be constructed using MOFs because of their excellent physicochemical properties.133 Combining two or even more MOFs to prepare hybrid membranes has been reported. For example, to avoid the issue of difficulty in controlling the operation during the solvent heat reaction, Knebel et al. prepared 180 nm ZIF-8 membranes through layer-by-layer growth on ZIF-67 membranes via the self-assembly method.134 These ZIF-8-on-ZIF-67 membranes were defect-free and showed a stronger adsorption effect, thus improving their selectivity. Xiao et al. prepared a novel MOF-on-MOF membrane, i.e., constructed from double-layered UiO-66-based (–(COOH)2 and –NH2) membranes via a seed-assisted in situ growth method.135 The experimental results showed that, compared with the double-layered UiO-66-NH2 membrane, the UiO-66-based membranes with –COOH were more selective for monovalent ions (Li+) than divalent ions (Mg2+) because the monovalent ions were more easily trapped or attracted by the negatively charged –(COOH)2 under electric-field-driven conditions. In addition to the composite of structurally similar MOF materials, some composite membranes of MOF materials with completely different structures have been prepared.136 Inspired by this, Xu et al. designed a heterogeneous layered UiO-66-NH2@ZIF-8 membrane137 using a simple layer-by-layer assembly method. The UiO-66-NH2@ZIF-8 membrane retained the large pores of the UiO-66-NH2 material and the molecular-sieving pores of ZIF-8, which promoted the transport of water and intercepted the dye with a >97% dye removal rate. Through such simple preparation method, the advantages of the respective MOF materials were well preserved, which will undoubtedly be a good alternative for designing other advanced methods.
Covalent-organic frameworks (COFs) are a new class of porous skeletal materials in which light elements (such as C, B, N, O, Si, etc.) are connected by reversible strong covalent bonds.138 Similar to MOFs, COF materials have a tunable pore size, a large specific surface area, and high crystallinity. The pure organic component in COF materials makes them less dense and well compatible with other materials.139 Combining the excellent properties both materials, Fu et al. firstly reported the generation of COF–MOF composite membranes in 2016, which were assembled from COF-300 and ZIF-8 in a distributed manner.140 The preparation method is relatively simple, and the chemicals used are inexpensive, and easy to mass produce. COF crystals form chemical bonds through the interaction of imine groups with the polyaniline layer, while HN-Zn-imidazole bonds close the interface between the COF and ZIF materials to form an amorphous MOF layer. This amorphous MOF layer is beneficial for membrane selectivity, and this unique preparation method also means that the COF–MOF composite membrane has a better separation performance. Very recently, COF–MOF hybrid membranes have also received increasing attention.141,142 Thanks to the synergistic effect of hybrid membranes, Das et al. prepared UiO-66/COF-300 composite membranes via the continuous and uniform growth of COF-300 on UiO-66 membranes. The synergistic effect of COF-300 and UiO-66 led to a significant improvement in the permeability and selectivity.111 Inspired by the alloying effect of the aluminum alloy, Liu et al. demonstrated the formation of MOF–COF “alloy” membranes (AMs).143 By adding quaternary ammonium salt (QA)-functionalized COFs to the ZIF-8 matrix and adjusting the loading of the COFs, composite membranes with a specific rigidity were obtained through a one-step electro-driven co-deposition method. The addition of different amounts of QA enabled good control over the molecular screening ability of the AMs, whereas the addition of COFs promoted the epitaxial growth of ZIF-8 and reduced the thickness of the membranes, resulting in a better separation performance of the composite membrane. In the future, MOF membranes laminated with COF materials will also be a good choice for the mass production of high-quality MOF membranes.
4.5 MOF–ionic liquid hybrid membranes
Ionic liquids (ILs) are type of ionic compound with a melting point below 100 °C.144 ILs are green solvents for chemical synthesis with strong solubility, non-combustibility, high thermal and chemical stability.145 As a new type of membrane separation material, ILs can form ionic liquid membranes (ILMs) with various forms and structures. Over the past few years, important gas-purification and wastewater-treatment developments of composite membranes that combine the advantages of ILs and MOFs have been accomplished.146 The most applied are supported ionic liquid membranes (SILMs).147 Compared with conventional ionic liquid adsorbents, SILMs have a larger contact area between the gas and liquid phases, and show a higher adjustability, separation efficiency and stability.148 For example, Tzialla et al. prepared ZIF-69 membranes on porous α-Al2O3 substrates using the secondary growth method.149 Then, ZIF-69-functionalized membranes with tricyanomethanide anion/alkylmethylimidazolium cation-based ionic liquid were used to synthesize the ZIF-69–IL hybrid membranes. After the functionalization of ZIF-69 by the ionic liquid, the intergranular boundaries and defects of the ZIF crystals were repaired, and the gaps between the ZIF crystals were plugged, allowing the framework pores to open. This composite material exhibited a higher selectivity and permeability, and can be used widely for membrane separation. To further enhance the separation efficiency of the hybrid membrane, Hao et al. prepared a MOF–polymerized ionic liquid–ionic liquid three-phase hybrid membrane.150 First, they prepared ZIF-8, a polymerizable room temperature ionic liquid (poly(RTIL), i.e., 1-vinyl-3-butylimidazolium-bis(trifluoromethylsulfonyl)imidate ([vbim][NTf2]),) and a “free” room temperature ionic liquid (RTIL), which was (i) 1-ethyl-3-methylimidazolium tetrafluoroborate ([emim][BF4]), (ii) 1-ethyl-3-methylimidazolium bis(trifluoromethanesulfonyl)imide ([emim][NTf2]) or (iii) 1-ethyl-3-methylimidazolium tetracyanoborate ([emim][B(CN)4]), and then synthesized the poly(RTIL)/RTIL/ZIF-8 membranes via UV polymerization. In the three-phase hybrid membrane, the ZIF-8 particles were homogeneously dispersed. The combined advantages of each component meant that the permeability of the hybrid membrane was significantly improved and showed good separation. More studies have reported the use of ILs to functionalize MOF materials and then combining them with polymers to prepare MMMs.151,152 Strong electrostatic interactions between the ionic polymers and the MOFs can enhance their compatibility and enable the preparation of defect-free MMMs without additional treatment.
4.6 MOF–organic polymer hybrid membranes
MOF–organic polymer hybrid membranes are formed by hybridizing MOF grains with organic polymers. According to the binding pathway between the MOF and the polymer, these hybrid membranes can be classified into three types: surface-grown, organic phase-filled and mixed-matrix membranes. Among these, MMMs are a kind of bi-directional hybrid membrane formed using an organic polymer as the matrix in which the MOF grains are embedded. MMMs are the most common and widely used type of MOF–organic polymer hybrid membrane.12,153 In MMMs, polymer materials are commonly used as separation membranes, and include polysulfone (PSF), polyaniline (PA), polyarylate (PAR), polycarbonate (PC), polyimide (PI), polyetherimide (PEI), and so on.154 For instance, Liu et al. synthesized ZIF-8–PMPS composite membranes that can selectively adsorb furfural molecules by filling the silicone rubber matrix with ZIF-8 particles.155 A hierarchically ordered stainless steel mesh (HOSSM) was used as the skeleton matrix. Then, the holes in the top layer of the HOSSM were plugged with ZIF-8 nanoparticles. Finally, the space between the nanoparticles and the mesh filaments was filled with polymethylphenylsiloxane (PMPS) silicone rubber. Influenced by the unique adsorption selectivity of ZIF-8 on furfural molecules and the space restriction and physical cross-linking of the HOSSM, the ZIF-8–PMPS composite membrane demonstrated a superior permeation performance in comparison with the other membranes reported, and still maintained good stability after 120 h of operation at 80 °C. Li et al. prepared MMMs of amine-functionalized MOFs combined with PI.156 Compared with the pure PI membrane, the amine-functionalized MOFs showed enhanced hydrogen bonding with PI, improved MOF dispersion in PI solution, and a 1.5-fold increased permeability of the composite membrane. A novel MOF hybrid membrane with excellent antifouling properties was prepared using zwitterionic MOF polymerized PA.157 Featuring superior thermal properties, an exceptional resistance to harsh chemicals, and an outstanding mechanical strength, polyvinylidene fluoride (PVDF) has emerged as a highly popular choice for porous polymer membranes.158 For instance, Tan et al. prepared MOF–polymer hybrid membranes by incorporating functionalized NH2-MIL-101 (Cr) into porous PVDF using a co-blending method.159 The –NH2 groups in the CR dye and NH2-MIL-101 (Cr) undergo chemisorption through hydrogen bonding. Incorporating the MOF particles improves the membrane's hydrophilicity and porosity, achieving good adsorption separation of dye wastewater. Other than that, a series of MOF–PVDF hybrid membranes were also prepared, such as PVDF/NH2-MIL-88B(Fe) membranes,160 and MIL-101/PVDF membranes.161 Experimental results showed that the MOF–PVDF hybrid membranes will provide a new route for the design of antifouling membranes. Benefitting from the promotion of 2D materials for the fabrication of a thin separation layer and better compatibility with polymers, Shu et al. chose PEI, which has good solubility in water/ethanol, as the polymer substrate and combined it with a new 2D MOF material, BUT-203, to prepare the BUT-203/PEI-HPAN(x) composite membrane (where x represents the MOF nanosheet loading).162 The best performance was shown by the BUT-203/PEI-HPAN(73) membrane, which had a thickness of 70 nm and a MOF loading of 73%. The removal rate of anionic dyes with a molecular weight greater than 461 was 97.9%, and the water permeability of 870 L m−2 h−1 MPa−1 was one order of magnitude higher than that of commercial filtration membranes. In addition, the membrane showed a good desalination performance for dye solutions within 30 h, as well as a good antifouling performance for bovine serum albumin (BSA) and humic acid (HA). This is due mainly to the higher electrostatic repulsion and anti-scaling properties of the negatively charged BUT-203 nanosheets against anionic dyes.
5. Applications in water separation and treatment
Water pollution is escalating as a significant ecological concern, presenting a critical danger to the well-being of humanity, animals, and plants.163 In order to achieve effective treatment of the water environment, MOF materials have been applied to the treatment of water pollution due to their adjustable structure and excellent performance. In particular, MOF membranes, with notable benefits in separation and adsorption, have been used increasingly in wastewater treatment, seawater desalination, and oil–water separation in recent years (Fig. 11).
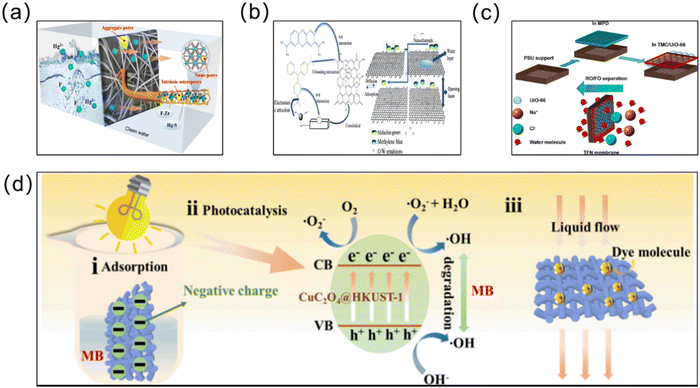 |
| Fig. 11 (a) Schematic of the Zr-based MOFs@PIM nanofiber membrane containing multi-stage pores for the effective removal of Hg(II) ions from water. Reprinted with permission from ref. 164. Copyright 2023 Elsevier. (b) Schematic of the PDA/RGO/MOFs&SiO2-COOH membrane separation of dyes. Reprinted with permission from ref. 165. Copyright 2022 Elsevier. (c) Schematic of thin film nanocomposite (TFN) membrane desalination combined with the super-hydrophilic metal–organic framework (MOF) UiO-66. Reprinted with permission from ref. 166. Copyright 2017 American Chemical Society. (d) Schematic of the rational mechanism and complex emulsion separation of CM@CuC2O4@HKUST-1 for dye removal via adsorption and photocatalysis. Reprinted with permission from ref. 167 Copyright 2022 Elsevier. | |
5.1 Removal of heavy metal ions
Heavy metal ions that are not biodegraded are enriched through the food chain and gradually increase in concentration, eventually entering the organism and causing chronic toxicity,168 even at trace levels.169,170
In recent years, to further improve the treatment efficiency, more researchers have chosen MOF–organic polymer hybrid membranes to treat heavy metal ions in wastewater.171–173 For example, Efome and co-workers prepared Zr-based MOF-808–PAN electrospun nanofiber composite membranes through electrospinning.106 After “hydractivation”, the composite membrane maintained the original hydrophilic nature of PAN. During hydractivation, the pore space was occupied by water, the lattice was stretched, and the MOF structure was deformed, resulting in expansion of the pores, resulting in enhanced adsorption capacity. Compared with the conventional vacuum-activated composite, the PAN/MOF-808 hydractivated composite membrane showed an enhanced ability to treat Cd with maximum adsorption capacities of 225.05 and 287.06 mg g−1 for Cd2+ and Zn2+, respectively. In another example, Li et al. prepared hybrid membranes with highly loaded MOFs via electrostatic spinning on an electrospun-silk-nanofiber (ESF) membrane substrate.174 The ESF@MOF (ZIF-8 or ZIF-67) showed the highest loading content among other common polymer membranes and reported analogs, with both ZIF-8 and ZIF-67 being above a 30% loading. This enabled the ESF@MOF composite membrane to have a homogeneous dispersion of MOFs and obtain the maximum number of active adsorption sites. The acid–base sites of the hydrogen and amino groups formed on the surface of the ZIF-8 crystals tightly bonded with the As(V) ions, while Cr(VI) was adsorbed by the activated site Co2+ on the surface of ZIF-67 through electrostatic interactions. Nearly 100% of Cr(VI) and As(V) ions can be removed by the hybrid membrane. Furthermore, Wang et al. prepared a range of MOFs@PIM-W membranes to remove Hg(II) from water by hybridizing UiO-66 functionalized with porous nanofiber membranes.164 Due to the hydrophobic group in UiO-66-SH (Ui-S), in which S2− will coordinate well with Hg(II), the Ui-S@PIM-W nanofiber membrane can effectively remove Hg(II) from water in a wide pH range (pH = 2–10) with a 99% removal efficiency, and no significant loss of adsorption capacity after 3 cycles.
To further improve the separation capacity of MOF membranes, bimetallic MOF membranes are also being gradually applied for heavy metal ion removal. Sharma et al. first incorporated bimetallic MOFs into a TFN to synthesize hydro-stable TFN membranes.175 Thanks to the π–π interaction between the Co–Zn mixed MOFs (mMOFs) and the 2-MIM ligand in the m-phenylenediamine (MPD) monomer, the nanoparticles were more uniformly dispersed in the membrane. The incorporation of the two metal centers provided more effective adsorption sites for arsenic. Due to the favorable compatibility between the MOF monomer and organic ligands, the formed PA layer was defect-free in the MOF-modified TFN membranes synthesized via IP. Therefore, the permeability of the modified TFN was 2.5 times higher than that of the unmodified TFN, thus showing great potential for arsenic removal, with a 94% removal efficiency for As5+. Inspired by the bimetallic MOF membranes, Yang and co-workers demonstrated the rapid in situ method of synthesizing Zn/Co-ZIF crystals to form uniform and robust MOF membranes on readily available cloth.46 Due to its highly hydrophilic, flexible, biocompatible, large-surface-area, and low-cost features, it was beneficial to select cloth as the substrate. By introducing sodium carboxymethyl cellulose (CMC), the chemical surface adhesion of MOF crystals was enhanced, while the agglomeration of crystals in the liquid phase was hindered. The CMC-MOF(Zn/Co-ZIF)/cloth membrane showed remarkable selectivity and an excellent adsorption capacity (862.44 mg g−1) for Pb(II). After 5 cycles, the adsorption capacity of the CMC-MOF/cloth composite membrane decreased insignificantly, and the removal rate of Pb(II) still reached 79.12%, which showed potential for water purification and remediation.
5.2 Removal of organic contaminants
With the current economic and industrial development, organic pollution has become the most important source of water pollution.176,177 The direct disposal of synthetic industrial dyes and the misuse of antibiotics and pesticides pose a huge challenge for water pollution management. Membrane materials with a microporous structure and a good adsorption capacity are ideal for the continuous removal of organic contaminants. To enable effective wastewater treatment, many researchers have also applied MOF membranes to separate organic pollutants from contaminated water bodies.
5.2.1 Dyes.
Dyes are carcinogenic, teratogenic and mutagenic, and are difficult to degrade, and thus they are a threat to animal and human health.109 Compared with traditional adsorption technology, MOF membrane separation technology enables the adsorption of dyes with different properties and easy recovery.180–182 Taking the GO–MOF membrane as an example, Xiao et al. used a vacuum filtration self-assembly device to prepare composite membranes of MOFs that can efficiently remove dyes from wastewater.178 The strong π–π conjugation between PTCDA and GO in the GO@PTCDA-UiO-66-NH2 membrane (PTCDA = perylene-3,4,9,10-tetracarboxylic acid dianhydride) made the modified UiO-66-NH2 bind strongly to GO. At the same time, in addition to the spherical structure formed for dye adsorption, PTCDA-UiO-66-NH2 also achieved the secondary lateral adsorption of the dye, and the whole membrane formed a unique vertical screening and horizontal adsorption filtration structure (Fig. 12a). The π–π stacking, hydrogen bonding, and electrostatic effects work together to achieve the complete removal of the dyes. As a result, the GO@PTCDA-UiO-66-NH2 membrane achieved nearly 100% degradation of MB, CR, crystalline violet (CV) and dispersion black 9 (DB9). What is even more surprising is that the membrane maintains a good filtration performance at a high salt concentration (9 w/v%) and under extreme pH conditions. This was due to the improved viscosity and membrane resistance of the dye at high salt concentrations, which makes it easier for the dye molecules to agglomerate and thus increases the removal rate. After the addition of PTCDA, the compatibility between PTCDA-UiO-66-NH2 and the GO sheet increased due to the binding effect between PTCDA and GO, and the composite membrane became more compact and less susceptible to damage, which contributed to extending the membrane life. The dye removal rate remained the same after 6 cycles in the pH range of 2–8. By contrast, the ternary GO/GOH/MOF hybrid membrane constructed from GO, hydroxylated graphene (GOH) and FeCuBDC using vacuum filtration exhibited a high RB separation efficiency (99.98%).114 The horizontal structure formed by GO, GOH and FeCuBDC, and the vertical sieve structure of the GO layer formed a laminar structure with many nanochannels. In addition, the insertion of the bimetallic MOF swelled the GO nanosheets and increased the interlayer spacing of the composite membrane, which greatly improved the membrane flux, and the water flux of the composite membrane was 9.5 times higher than that of the GO membrane. By contrast, the removal of dyes depended on the electrostatic attraction, hydrogen bonding, and size sieving between GO and FeCuBDC. Most importantly, the inclusion of GO and GOH in the ternary blend membrane accelerated the electron transfer rate during the catalytic process of the bimetallic MOF FeCuBDC, which not only brought about an efficient removal efficiency but also enhanced the self-cleaning effect of the membrane. Another membrane, i.e., g-C3N4/NH2-MIL-88B(Fe)/CD@GO (called M2), which was prepared by embedding a Z-type heterojunction composite photocatalyst (g-C3N4) into GO nanosheets, still showed a removal rate of more than 95% for CR and MB after 6 cycles at pH = 1–3 and a salt concentration of 10%.183 Surprisingly, due to the g-C3N4/NH2-MIL-88B(Fe)/CD embedded in the GO layer, the roughness of the composite membrane and the GO interlayer spacing increased, and the membrane permeation was improved, where the pure water permeation of M2 (253.26 L m−2 h−1 bar−1) was 13 times higher than that of pristine GO (18.83 L m−2 h−1 bar−1). Due to the strong size-sieving effect, π–π conjugation and electrostatic effects, M2 maintained a good separation efficiency and permeability even after 10 cycles. In the composite membrane, on the one hand, the tightly arranged structure formed by GO and the role of the capillaries and the photocatalytic process prevented catalyst agglomeration, provided transfer channels for electron transfer, avoided electron–hole pair recombination, and improved the degradation performance of the composite membrane. On the other hand, the addition of the photocatalyst not only oxidized and reduced some dye molecules, but also reduced some other pollutants, which effectively alleviated the problem of membrane pollution. Therefore, the emergence of this composite membrane provided an effective and feasible direction for the development of new environmentally friendly water-treatment membranes using MOFs.
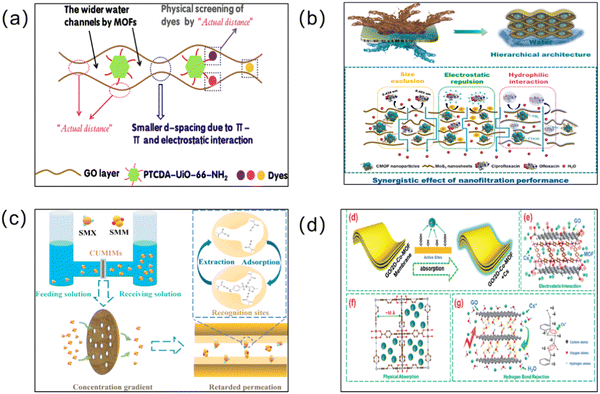 |
| Fig. 12 (a) Adsorption schematic of the GO@PTCDA-UiO-66-NH2 membrane. Reprinted with permission from ref. 178. Copyright 2022 Elsevier. (b) Separation mechanisms across the MoS2/CMOF composite membrane with the synergistic effect of the molecular sieving effect (size exclusion), electrostatic repulsion, and hydrophobic–hydrophilic interactions for the removal of ciprofloxacin and ofloxacin. Reprinted with permission from ref. 61. Copyright 2022 Elsevier. (c) Schematic illustration of the selective separation mechanism in CUMIMs. Reprinted with permission from ref. 49. Copyright 2022 Elsevier. (d) Schematic diagram of the adsorption mechanism of Cs+ by the GO/Co-MOF membrane. Reprinted with permission from ref. 179. Copyright 2018 Royal Society of Chemistry. | |
Considering that not just a single dye is usually present in the wastewater but a mixture of binary, ternary, or even multiple dyes more often exists, Li and co-workers loaded Zr-MOFs onto polyurethane foam (PUF) and evaluated the performance of Zr-MOF–PUF membranes in binary or ternary systems for the removal of different dyes.184 RB (neutral dye), MB (cationic dye), and CR (anionic dye) were chosen as the model contaminants to study the membrane filtration performance. The cationic form of RB, the positively charged form of MB, and CR with protonated amino/azo groups were easily attracted by the negatively charged Zr-MOF–PUF membrane through electrostatic interactions, coupled with the fact that SO3− in the CR molecule will interact with zirconium ions through Lewis acid–base interactions. Taken together, the composite membrane can simultaneously remove RB, MB, and CR due to electrostatic interactions, hydrogen bonding, and Lewis acid–base interactions between the membrane and the dye molecules. This makes the Zr-MOF–PUF membrane more valuable for practical applications.
5.2.2 Antibiotics.
Misuse of antibiotics in homes, hospitals, livestock and agriculture is another major source of contaminants in water.185 Since antibiotics are not fully absorbed by humans and animals when used, a large proportion of the antibiotics is discharged into wastewater as metabolites. Although few studies on the treatment of antibiotics using MOF-based membrane separation technology have been reported, the potential of these membrane materials in such a field has been presented in the limited literature.186,187 For instance, Fang et al. prepared loosely layered composite membranes by inserting the UiO-66-NH2 MOF (CMOF) in MoS2 using an electrostatic layer-by-layer self-assembly method.61 Due to the synergistic mechanism between the molecular sieving effect (size repulsion), electrostatic repulsion and hydrophilic–hydrophobic interactions, the membrane surface formed abundant specific active sites. The inserted CMOF nanoparticles provided layered nanopores to enhance the solute inhibition and the hydrophilicity of the membrane (Fig. 12b). The shape-selective function, the molecular sieving effect and the electrostatic interactions of the MoS2/CMOF composite membrane enable the membrane to exhibit a higher removal capacity of ciprofloxacin (98.01 ± 1.12%) and ofloxacin (94.31 ± 0.68%) compared with the two monolithic membranes. Because of the addition of UiO-66-NH2 MOFs with a rigid 3D pore structure and the hydroxy-methylation reaction of the formed polysaccharide chitosan in NaOH solution, the composite membrane can continuously maintain a good separation under alkaline and acidic environments for 72 h. In addition, Li et al. modified glass fibers with PVDF solutions containing hydrophilic GO hybrid NH2-MIL-101 (Fe) particles, and successfully prepared glass fiber (FG) assisted PVDF hybrid membranes with a strong mechanical strength.188 Due to the semiconducting nature of NH2-MIL-101 (Fe) and its strong oxidation in the valence band, it formed a direct Z-type photocatalyst after being combined with GO, which inhibited electron–hole recombination and improved separation efficiency. The composite membrane not only degraded tetracycline (TC) up to about 93% within 90 min in the emulsion, but could also be reused dozens of times without cracking, with the degradation rate remaining higher than 90%. There is rarely just one type of antibiotic present in water, so their selective removal is relatively difficult. Recently, using the specific recognition role of molecular imprinting technology, Wang et al. prepared molecularly imprinted nanocomposites (CUMIMs) based on CNT/UiO-66-NH2 that are capable of the selective removal of sulfamethoxazole (SMX) by combining molecular imprinting technology and membrane separation technology.49 In the process of preparing the CUMIMs, an SMX imprinted layer was formed on its surface in the first step, which enables the formation of SMX selective recognition sites, followed by the removal of SMX on the surface. Through the SMX selective recognition sites on the imprinted layer, the CUMIMs in wastewater could selectively adsorb SMX (2.11 mg g−1) (Fig. 12c) and remain relatively stable after eight cycles, still reaching 87.1% of their maximum adsorption capacity. This showed that the prepared CUMIMs had good stability and reusability, which is beneficial for practical applications and opened up a new pathway for the synthesis of MOF membranes.
5.2.3 Other organic contaminants.
MOF-based membranes can not only achieve good removal of dyes and antibiotics from wastewater but are also applicable for some other organic pollutants (Fig. 13).189–193 In order to continuously and effectively remove micro-pollutants from water, Xu et al. prepared horseradish peroxidase (HRP)@ZIF-8 membranes that can be combined with enzyme catalysis.194 Owing to the synergistic effect between the adsorption of the MOFs, catalytic oxidation by enzymes and membrane retention, this biocatalytic composite membrane can remove 98% of Bisphenol A (BPA) via continuous operation, and exhibits greater stability and reusability, even in the presence of proteolysis. As for hydrocarbons and their chlorinated substitutes, Wu et al. prepared a ceramic hollow fiber NF membrane containing UiO-66 through the IP of UiO-66 and PA on a ceramic support,195 achieving a greater than 96% removal of trichloroethylene (TCE) and trichlorobenzene (TCB). Benefitting from the stability of the ceramic substrate and the defect-free PA separation layer, the diffusion coefficient of water in the pores of UiO-66 is about 1.5 times higher than in PA. Among the tested membrane formulations, the membrane with 0.02% UiO-66 in the organic phase showed the best performance with a pure water flux of 30.4 L m−2 h−1 bar−1. At present, there are relatively limited types of MOF-based membranes used in water treatment separations, and it is hoped that more types of MOF membrane will be used in water treatment applications in the future.
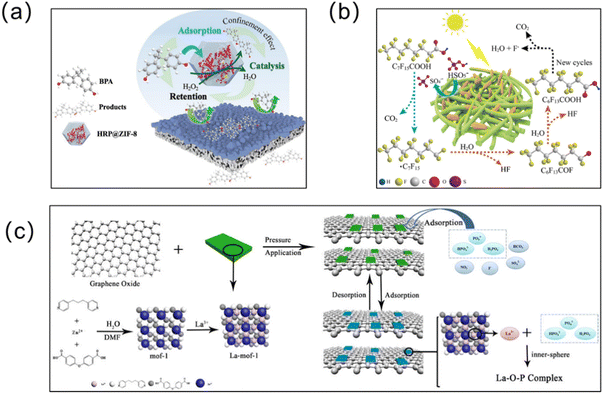 |
| Fig. 13 MOF membranes remove other organic contaminants from water. (a) HRP@ZIF-8 on a PDA/PEI membrane for BPA removal. Reprinted with permission from ref. 194. Copyright 2021 Elsevier. (b) Degradation of perfluorooctanoic acid (PFOA) by the lignin/polyvinyl alcohol/Co/Fe MOF (lignin/PVA/bi-MOF) composite membrane. Reprinted with permission from ref. 191. Copyright 2021 Elsevier. (c) Highly selective phosphorus recovery from lanthanum-modified MOF–graphene oxide composite membranes. Reprinted with permission from ref. 113. Copyright 2020 Elsevier. | |
5.3 Removal of radioactive pollutants
Due to the gradual shortage of fossil fuels, nuclear energy has attracted intensive attention as a clean energy source. However, the rapid development of nuclear power plants has brought about many safety and environmental problems. Removing and recovering radionuclides from wastewater has become a major challenge in water treatment.196 In order to solve the problems of low cost and high energy consumption for the removal of radionuclides using conventional treatment technologies, researchers have also applied MOF-based membrane technology for the removal of radionuclides from wastewater.197 Back in 2018, Cheng et al. achieved the adsorption and removal of Cs+ using a 2D GO/Co-MOF membrane.179 Using vacuum filtration devices, negatively charged GO and positively charged Co-MOF were assembled into a composite GO/Co-MOF membrane with mechanical flexibility. Two groups, C–O and C
O, were generated in the 2D GO/Co-MOF composites, providing sufficient sites for bonding with Cs+ during the reaction. In GO/Co-MOF membranes, hydrogen bonds on the GO surface are easily eliminated by the interface between Co-MOF and GO, resulting in the facilitated permeation and adsorption of Cs with oxygen-containing groups in GO. Interfacial or surface complexation and electrostatic interactions between the membrane materials promoted the chemisorption of Cs+ by the membrane (Fig. 12d). The 2D GO/Co-MOF membrane could adsorb up to 88.4% of Cs+, and still showed a good separation performance in strong acid/base solutions. For strontium (Sr), as one of the most dangerous radiological contaminants that threaten the environment and human beings, its separation and recovery from wastewater is a very urgent issue. In another study, GO/Ni-MOF membranes were prepared using a simple filtration method, where the oxygen-containing functional groups in GO nanosheets were combined with Sr2+ through electrostatic interactions.198 As with the GO/Co-MOF composite membrane, the interface formed between Ni-MOF and GO in the GO/Ni-MOF membrane effectively eliminated hydrogen bonding on the GO surface and promoted a portion of Sr2+ uptake. Secondly, the electrostatic interaction between Sr2+ and O–C
O and C
O in the GO nanosheets, the physical adsorption of porous MOFs, and the substitution of Sr2+ for Ni2+ in the structure of MOFs synergistically promoted the removal of Sr2+. Thus, the maximum effective adsorption of Sr2+ in a 100 mg L−1 Sr2+ aqueous solution of 32.99% could be achieved with only 2 mg of the composite membrane. For other radionuclides, Liu et al. prepared a composite membrane with high mechanical strength by inserting a prepared 1,3,5-benzenetricarboxylic acid (BTC)-MOF into the interlayer of GO using the intercalation method.199 The interlayer distance within the GO membrane increased after MOF insertion. By changing the separation factor, both the prepared Cu-BTC-MOF/GO and Zn-BTC-MOF/GO membranes achieved the highly selective separation of Th4+ and UO22+. More importantly, the Cu-BTC-MOFs/GO membrane can remove 100% of Ce3+. In view of these above examples, GO–MOF hybrid membranes may become an ideal material for the effective treatment of radionuclide wastewater in the future.
5.4 Oil–water separation
Oil-containing wastewater from industry and daily life has seriously polluted the environment and affected all aspects of people's lives.167 Traditional oil–water separation technology has a low separation efficiency and thus a high cost. Considering these problems, the preparation of membranes with superhydrophilic and underwater superoleophobic properties to separate oily wastewater would be a better choice.200 In recent years, researchers have also begun to apply MOF-based membranes to the separation of oily wastewater.165,201 For example, Cao and co-workers combined electrostatic spinning with MOF materials and prepared PVP–UiO-66-NH2 membranes that can effectively separate oil-containing wastewater.202 By grafting PVP chains onto UiO-66-NH2, the pore volume and pore size of the nanoparticles were increased, enhancing the hydrophilicity of the particles. Before contact with oil, the formation of a microsphere/fine fiber structure via a continuous electrostatic sputtering electrospray method may form a functional layer/water biphasic distribution interface, blocking the adhesion of oil to the electrostatic sputtering nanofiber membrane (NFM) fibers. Then, on the NFM surface, the oil phase of the emulsion undergoes rolling and coalescing, increasing the diameter of the oil droplets. After reaching a certain value, the oil droplets will detach and float up into a continuous phase to achieve oil–water separation. These NFMs achieved a 99.2% oil–water separation efficiency and have a stable antifouling performance. Similarly, Samari et al. prepared MOF–PES composite membranes by combining modified UiO-66-NH2 with PES via the phase inversion method.203 UiO-66-NH2, when modified with melamine, introduces more amino groups onto the surface to provide hydrogen bonds, increasing the hydrophilicity of the membrane. As the addition of MOFs improved the membrane porosity and reduced the surface roughness, the modified hybrid membrane demonstrated a higher hydrophilicity and antifouling ability, and a 99% oil–water separation efficiency. In addition to one-dimensional structured MOF membranes, 2D MOF-based membranes with ultrafast oil–water separation capabilities were prepared by He et al.204 Cu-CAT-1@CM membranes with micro/nanostructures can be synthesized in just 20 min at room temperature. The MOF was grown directly on the copper mesh (CM), and the resulting layered structure will combine with polar nanocavities in the MOF crystals to endow the copper mesh membrane with superior superhydrophilic and submerged superoleophobic properties. In addition, the separated crude oil flux under gravity conditions exceeded 329 kL m−2 h−1 and the residual oil was as low as 24.6 mg L−1. Most pleasingly, the flux was still maintained above 200 kL m−2 h−1 after 20 cycles, and the residual oil content was lower than 7.4 mg L−1. This enables the composite membrane to operate consistently under challenging conditions.
5.5 Desalination
Although water covers 70.8% of the Earth's surface, freshwater accounts for only 2.5% of it. About one-third of the world's population faces the problem of insufficient drinking water. In order to cope with the shortage of water, seawater desalination has become the main response. Desalination includes two main processes: distillation desalination and membrane desalination.205 Recently, membrane desalination technology has gained widespread adoption owing to its higher processing efficiency and lower cost.98 However, the poor anti-fouling properties and short service life hinder the further development of polymer membranes.206 Polymeric membranes combined with high-quality MOFs can improve the compatibility between the filler and the matrix, effectively reducing any resulting non-selective defects in the membrane. As a result, the composite membrane displays excellent physical and chemical properties.207,208 Therefore, Hu et al. proposed a new synergistically driven in situ self-assembly method to prepare ZIF-8–PA TFN membranes.209 In seawater, the different molecules and ions present have different sizes, and the intrinsic pores of ZIF-8 crystals enable the separation of water molecules with small pore sizes from Na+ and Cl−. Notably, the in situ grown ZIF-8 crystals made them more favorable for the separation of NaCl from water. This method resulted in the uniform doping of the ZIF-8 material into the membranes without agglomeration and defect generation. ZIF-8 TFN membranes show a 5-fold higher water flux than conventional TFN membranes and inhibit 99.03% of NaCl. As another example, Kachhadiya et al. successfully synthesized GO@CUBTC integrated PVDF membranes with high stability, selectivity and reusability.210 By doping GO@CuBTC into the PVDF membrane, the GO@CuBTC was uniformly dispersed, which increased the porosity and hydrophilicity of the membrane, and the separation performance and stability of the membrane were enhanced. Experimental data showed that the membrane can run continuously for 260 h with a desalination rate of 99.68%. Similar to MOF membranes applied for oil–water separation, 2D MOF membranes also can be applied in seawater desalination. Liu et al. prepared a high-performance reverse osmosis (RO) TFN membrane by embedding a 2D nickel-based MOF into a polysulfone substrate selective layer.97 The additional pore space of the 2D-MOF and its H-bonding with free water molecule ligands accelerated the transport of water molecules. Because the pore size of the MOFs is smaller than Na+ and Cl−, water molecules pass through the membrane while salt molecules are rejected. Thus, both the salt rejection and the water permeability were maintained by the modified TFN membrane (99.3% NaCl rejection). Moreover, the higher surface hydrophilicity and roughness enable the 2D-MOF membrane to maintain good antifouling properties even under a high humic acid concentration. Thus, 2D MOFs will potentially become ideal membrane separation materials in water treatment.
6. Perspective on the industrial scale up of MOF-based membranes
To sum up, MOF-based membranes are widely applied in water treatment, achieving good separation abilities for organic and inorganic compounds in water. Nonetheless, studies are still in the laboratory stage, and the industrial scale up of MOF-based membranes has not yet been realized. The biggest challenges in applying MOF-based membranes to industrial applications are hydrothermal stability and large-scale production.
First of all, the high hydrothermal stability can extend the environmental applicability of MOF membranes in industrial applications, especially at certain high temperatures and acidic/alkaline environments. As mentioned in Section 2, we can select MOF materials with water stability, such as MIL-100, MIL-101, ZIF-8 and UiO-66, for preparation of the membrane; secondly, we can also choose to modify the synthesized MOF materials to enhance their water stability, mainly through ligand modification and metal–ligand exchange to enhance the stability of the ligand–metal bonds.
Some industrial assembly line operations can achieve more complex operational processes. Indeed, large-scale production requires a relatively simple and easy preparation route, which facilitates the formation of an assembly line operation. Currently, the more commonly used methods for preparing MOF membranes can be hindered due to more complex operations, high preparation costs and the time-consuming nature of the method, so most existing methods are unable to achieve the large-scale manufacture of MOF membranes. Fortunately, as research on MOF membranes continues, innovative preparation methods have made it possible to fabricate MOF membranes on a large scale. And with more and more hydrothermally stable MOF materials being discovered, it is likely that both large-scale and high-performance MOF membranes will be produced in the future. In addition, many MOF materials currently have the problem of low yield, and only by solving the problem of low yield can mass-produced high-performance MOF materials better serve the industry. First, MOF particles in a single MOF membrane tend to agglomerate, thus affecting the membrane performance, so MOFs and functional membrane materials are combined to form hybrid membranes. Due to the limited compatibility between MOFs and other materials, MOFs are first modified and then combined to form hybrid membranes. By homogeneously dispersing MOF particles in MOF hybrid membranes through functionalization, the inherent advantages of both the MOFs and the polymers are retained, which results in high stability of the hybrid membranes. Secondly, synergistic strategies are used to engineer different synthetic pathways in the growth of MOFs and membrane preparation considering the shortcomings of a single MOF membrane preparation method. Studies have been conducted, showing the potential of MOF-based membranes for industrial applications. The modification of MOF materials or combining them with other functional materials greatly improves the hydrothermal stability of MOF membranes. And the combination of two or more synthesis methods not only reduces the preparation cost, but also enables preparation within a short time. Both ideas offer good potential for industrial-scale applications based on MOF-based membranes.
7. Conclusion and outlook
Recently, MOF-based membranes have shown great potential for practical separation applications. MOF membranes prepared from water-stabilized MOFs have been used in gas separation, adsorption, catalysis and liquid separation. This review has summarized the key factors for the preparation of MOF-based membranes, such as uniform dispersion, high water stability, and suitable hydrophobicity, which lay the foundation for the preparation of high-performance membranes. Then, the article focused on the common methods of MOF-based membrane preparation and the classification of MOF hybrid membranes. In addition, the latest advances in MOF-based membranes for water treatment were discussed in depth, which show their high superiority in the removal of heavy metal ions, dyes, antibiotics, and radionuclides from wastewater, as well as in desalination and oil–water separation, and we concluded with the prospects for industrial applications of MOF-based membranes and the challenges that may be encountered during their future development. Highly water-resistant MOFs will undoubtedly be an ideal choice for wastewater treatment, and further exploration for the effective separation of MOF-based membranes will soon emerge. However, there are still several challenges regarding the development of MOF-based membranes.
First of all, in terms of the MOF membrane materials themselves, not all reported MOF-based membranes reported so far have a high separation performance. Thus, the selection of MOFs with both chemical stability and high efficiency is crucial for expanding their application in membrane separation. (1) Most of the MOF-based membrane materials reported so far are monometallic-centered MOFs, which have good water stability. Their separation efficiency, however, needs to be improved. Firstly, given the synergistic effect between different metals, the selection of suitable bimetallic-centric MOFs would be an effective strategy. Meanwhile, three-dimensional MOF-based membrane materials with more active sites can be constructed to achieve more efficient separation, since the widely applied one-dimensional structured MOFs membranes and few two-dimensional structured MOFs membranes. In addition, it is also necessary to focus on the performance of the supported membranes. Choosing membrane materials with better compatibility or improving the membrane performance through membrane modification will greatly increase the success rate of preparing MOF membranes with a high separation efficiency. (2) The chemical stability of the membrane is a key factor in determining its separation efficiency. Current research is usually conducted under relatively mild conditions, and further research is needed to enhance the stability of MOF-based membranes in strong acid/base, high temperature, and complex composition environments. (3) Several types of MOF hybridized membranes have been prepared, but the membranes more commonly used in water treatment applications are those that are hybrids of MOFs and organic polymers. Some other types of hybrid membrane have not worked in the field of water treatment, and efforts to develop different types of hybrid membrane for water treatment may be a new way to expand the application of MOFs for membrane separation.
In addition to this, the current characterization and mechanistic analysis of membrane materials does not enable a comprehensive analysis of the possible chemical mechanisms in the system. Due to the complexity of the structure and surface chemistry of MOF membranes, more efforts should be devoted to investigating the fabrication of model MOF-based membranes, or even establishing correlations between their structures and separating abilities, with both a single contaminant type and for more complex situations. Future research needs to use more advanced characterization tools and theories to characterize materials at a smaller level and analyze the adsorption separation mechanisms in depth. A combined experimental and theoretical approach, especially one that combines advanced machine learning, will be essential to understand these structure–function relationships thoroughly and to identify the structure, mechanism, and kinetics of water separation or treatment.
From a wider perspective, the demand for the development of environmentally friendly and resource-efficient processing equipment is giving momentum to MOF-based membranes, and may contribute to their large-scale applications for liquid separation and purification. For existing membrane separation technologies, the membrane surface is easily contaminated and needs to be cleaned. In order to achieve potential large-scale applications, attempts can be made to develop MOF membrane materials that can perform self-cleaning with good water stability and solvent resistance. It is also hoped that MOF membrane materials with a wider range of applications can be developed for the removal of conventional contaminants in industrial effluents and municipal sewage, and even for the removal of nanoscale contaminants, such as microplastics, from atmospheric and aqueous environments.
All the limitations and prospects mentioned above contribute to the fact that a more economical, environmentally friendly, safe and efficient application of MOF membranes can be achieved in the future. Overall, MOF-based membranes are expected to provide an alternative for the efficient and scalable separation and treatment of water.
Conflicts of interest
The authors declare that they have no known competing financial interests or personal relationships that could have appeared to influence the work reported in this paper. There are no conflicts to declare.
Acknowledgements
This work was supported by the Program for the National Natural Science Foundation of China (52070077), the Natural Science Foundation of Hunan Province, China (2021JJ40098, 2022JJ20013), and the Science and Technology Innovation Program of Hunan Province (2022RC1121), and the Fundamental Research Funds for the Central Universities (531118010226).
References
-
W. Qingbo and C. Qiuling, Application of membrane separation technology in water treatment process, IOP Conference Series Earth and Environmental Science, 2020, 508.
- R. W. Baker, Future Directions of Membrane Gas Separation Technology, Ind. Eng. Chem. Res., 2002, 41, 1393–1411 CrossRef CAS
.
- X. Yan, S. Anguille, M. Bendahan and P. Moulin, Ionic liquids combined with membrane separation processes: A review, Sep. Purif. Technol., 2019, 222, 230–253 CrossRef CAS
.
- Q.-L. Zhu and Q. Xu, Metal–organic framework composites, Chem. Soc. Rev., 2014, 43, 5468–5512 RSC
.
- J. R. Li, R. J. Kuppler and H. C. Zhou, Selective gas adsorption and separation in metal–organic frameworks, Chem. Soc. Rev., 2009, 38, 1477–1504 RSC
.
- Z. Wang, H. Wang, Z. Zeng, G. Zeng, P. Xu, R. Xiao, D. Huang, X. Chen, L. He, C. Zhou, Y. Yang, Z. Wang, W. Wang and W. Xiong, Metal–organic frameworks derived Bi2O2CO3/porous carbon nitride: A nanosized Z-scheme systems with enhanced photocatalytic activity, Appl. Catal., B, 2020, 267, 118700, DOI:10.1016/j.apcatb.2020.118700
.
- Y. He, Z. Wang, H. Wang, Z. Wang, G. Zeng, P. Xu, D. Huang, M. Chen, B. Song, H. Qin and Y. Zhao, Metal–organic framework-derived nanomaterials in environment related fields: Fundamentals, properties and applications, Coord. Chem. Rev., 2021, 429, 213618, DOI:10.1016/j.ccr.2020.213618
.
- Y. He, Z. Wang, H. Wang, E. Almatrafi, H. Qin, D. Huang, Y. Zhu, C. Zhou, Q. Tian, P. Xu and G. Zeng, Confinement of ZIF-derived copper-cobalt-zinc oxides in carbon framework for degradation of organic pollutants, J. Hazard. Mater., 2022, 440, 129811, DOI:10.1016/j.jhazmat.2022.129811
.
- Y. He, Z. Yin, Z. Wang, H. Wang, W. Xiong, B. Song, H. Qin, P. Xu and G. Zeng, Recent progress on mixed transition metal nanomaterials based on metal–organic frameworks for energy-related applications, J. Mater. Chem. A, 2022, 10, 9788–9820 RSC
.
- O. Shekhah, J. Liu, R. A. Fischer and C. Woll, MOF thin films: existing and future applications, Chem. Soc. Rev., 2011, 40, 1081–1106 RSC
.
- M. Kadhom and B. Deng, Metal–organic frameworks (MOFs) in water filtration membranes for desalination and other applications, Appl. Mater. Today, 2018, 11, 219–230 CrossRef
.
- B. Liang, B. Li, Z. Li and B. Chen, Progress in Multifunctional Metal–Organic Frameworks/Polymer Hybrid Membranes, Chemistry, 2021, 27, 12940–12952 CrossRef CAS PubMed
.
- X. Li, Y. Liu, J. Wang, J. Gascon, J. Li and B. Van der Bruggen, Metal–organic frameworks based membranes for liquid separation, Chem. Soc. Rev., 2017, 46, 7124–7144 RSC
.
- J. Kujawa, S. Al-Gharabli, T. M. Muzioł, K. Knozowska, G. Li, L. F. Dumée and W. Kujawski, Crystalline porous frameworks as nano-enhancers for membrane liquid separation – Recent developments, Coord. Chem. Rev., 2021, 440, 213969, DOI:10.1016/j.ccr.2021.213969
.
- X. L. Liu, Y. S. Li, G. Q. Zhu, Y. J. Ban, L. Y. Xu and W. S. Yang, An organophilic pervaporation membrane derived from metal–organic framework nanoparticles for efficient recovery of bio-alcohols, Angew. Chem., Int. Ed., 2011, 50, 10636–10639 CrossRef CAS PubMed
.
- S. Fazlifard, T. Mohammadi and O. Bakhtiari, Chitosan/ZIF-8 Mixed-Matrix Membranes for Pervaporation Dehydration of Isopropanol, Chem. Eng. Technol., 2017, 40, 648–655 CrossRef CAS
.
- X.-H. Ma, Z. Yang, Z.-K. Yao, Z.-L. Xu and C. Y. Tang, A facile preparation of novel positively charged MOF/chitosan nanofiltration membranes, J. Membr. Sci., 2017, 525, 269–276 CrossRef CAS
.
- R. Zhang, S. Ji, N. Wang, L. Wang, G. Zhang and J. R. Li, Coordination-driven in situ self-assembly strategy for the preparation of metal–organic framework hybrid membranes, Angew. Chem., Int. Ed., 2014, 53, 9775–9779 CrossRef CAS PubMed
.
- S. Shahid, K. Nijmeijer, S. Nehache, I. Vankelecom, A. Deratani and D. Quemener, MOF-mixed matrix membranes: Precise dispersion of MOF particles with better compatibility via a particle fusion approach for enhanced gas separation properties, J. Membr. Sci., 2015, 492, 21–31 CrossRef CAS
.
- N. C. Burtch, H. Jasuja and K. S. Walton, Water stability and adsorption in metal–organic frameworks, Chem. Rev., 2014, 114, 10575–10612 CrossRef CAS PubMed
.
- X. Liu, N. K. Demir, Z. Wu and K. Li, Highly Water-Stable Zirconium Metal–Organic Framework UiO-66 Membranes Supported on Alumina Hollow Fibers for Desalination, J. Am. Chem. Soc., 2015, 137, 6999–7002 CrossRef CAS PubMed
.
- C. Wang, X. Liu, N. Keser Demir, J. P. Chen and K. Li, Applications of water stable metal-organic frameworks, Chem. Soc. Rev., 2016, 45, 5107–5134 RSC
.
- X. Zhang, B. Wang, A. Alsalme, S. Xiang, Z. Zhang and B. Chen, Design and applications of water-stable metal-organic frameworks: status and challenges, Coord. Chem. Rev., 2020, 423, 213507, DOI:10.1016/j.ccr.2020.213507
.
- T. Rasheed, Water stable MOFs as emerging class of porous materials for potential environmental applications, Chemosphere, 2023, 313, 137607 CrossRef CAS PubMed
.
- S. Zhang, J. Wang, Y. Zhang, J. Ma, L. Huang, S. Yu, L. Chen, G. Song, M. Qiu and X. Wang, Applications of water-stable metal-organic frameworks in the removal of water pollutants: A review, Environ. Pollut., 2021, 291, 118076 CrossRef CAS PubMed
.
- B. Yuan, X. Q. Yin, X. Q. Liu, X. Y. Li and L. B. Sun, Enhanced Hydrothermal Stability and Catalytic Performance of HKUST-1 by Incorporating Carboxyl-Functionalized Attapulgite, ACS Appl. Mater. Interfaces, 2016, 8, 16457–16464 CrossRef CAS PubMed
.
- B. Liu, K. Vikrant, K.-H. Kim, V. Kumar and S. K. Kailasa, Critical role of water stability in metal–organic frameworks and advanced modification strategies for the extension of their applicability, Environ. Sci.: Nano, 2020, 7, 1319–1347 RSC
.
- X. Dong and Y. S. Lin, Synthesis of an organophilic ZIF-71 membrane for pervaporation solvent separation, Chem. Commun., 2013, 49, 1196–1198 RSC
.
- J. Zhu, L. Qin, A. Uliana, J. Hou, J. Wang, Y. Zhang, X. Li, S. Yuan, J. Li, M. Tian, J. Lin and B. Van der Bruggen, Elevated Performance of Thin Film Nanocomposite Membranes Enabled by Modified Hydrophilic MOFs for Nanofiltration, ACS Appl. Mater. Interfaces, 2017, 9, 1975–1986 CrossRef CAS PubMed
.
- X. Cheng, Z. Jiang, X. Cheng, H. Yang, L. Tang, G. Liu, M. Wang, H. Wu, F. Pan and X. Cao, Water-selective permeation in hybrid membrane incorporating multi-functional hollow ZIF-8 nanospheres, J. Membr. Sci., 2018, 555, 146–156 CrossRef CAS
.
- L. Wang, Y. Wang, L. Wu and G. Wei, Fabrication, Properties, Performances, and Separation Application of Polymeric Pervaporation Membranes: A Review, Polymers, 2020, 12(7), 1466, DOI:10.3390/polym12071466
.
- J. Yin and J. A. Forrest, Film Thickness Dependent
Stability and Glass Transition Temperature of Polymer Films Produced by Physical Vapor Deposition, Phys. Rev. Lett., 2023, 130, 168101, DOI:10.1103/PhysRevLett.130.168101
.
- K. Janus, D. Chlebosz, A. Janke, W. Goldeman and A. Kiersnowski, Contributions of Polymer Chain Length, Aggregation and Crystallinity Degrees in a Model of Charge Carrier Transport in Ultrathin Polymer Films, Macromolecules, 2023, 56, 964–973 CrossRef CAS
.
- M. Kalaj, K. C. Bentz, S. Ayala, Jr., J. M. Palomba, K. S. Barcus, Y. Katayama and S. M. Cohen, MOF-Polymer Hybrid Materials: From Simple Composites to Tailored Architectures, Chem. Rev., 2020, 120, 8267–8302 CrossRef CAS PubMed
.
- S. C. Hess, R. N. Grass and W. J. Stark, MOF Channels within Porous Polymer Film: Flexible, Self-Supporting ZIF-8 Poly(ether sulfone) Composite Membrane, Chem. Mater., 2016, 28, 7638–7644 CrossRef CAS
.
- T. Kitao, Y. Zhang, S. Kitagawa, B. Wang and T. Uemura, Hybridization of MOFs and polymers, Chem. Soc. Rev., 2017, 46, 3108–3133 RSC
.
- Y. Deng, Y. Wu, G. Chen, X. Zheng, M. Dai and C. Peng, Metal-organic framework membranes: Recent development in the synthesis strategies and their application in oil–water separation, Chem. Eng. J., 2021, 405, 127004, DOI:10.1016/j.cej.2020.127004
.
- Y. Liu, Z. Ng, E. A. Khan, H.-K. Jeong, C.-B. Ching and Z. Lai, Synthesis of continuous MOF-5 membranes on porous α-alumina substrates, Microporous Mesoporous Mater., 2009, 118, 296–301 CrossRef CAS
.
- M. C. McCarthy, V. Varela-Guerrero, G. V. Barnett and H. K. Jeong, Synthesis of zeolitic imidazolate framework films and membranes with controlled microstructures, Langmuir, 2010, 26, 14636–14641 CrossRef CAS PubMed
.
- Y. Liu, E. Hu, E. A. Khan and Z. Lai, Synthesis and characterization of ZIF-69 membranes and separation for CO2/CO mixture, J. Membr. Sci., 2010, 353, 36–40 CrossRef CAS
.
- S. Hermes, Selective Nucleation and Growth of Metal-Organic Open Framework Thin Films on Patterned COOH/CF3-Terminated Self-Assembled Monolayers on Au(111), J. Am. Chem. Soc., 2005, 127, 13744–13745, DOI:10.1021/ja053523l
.
- A. Huang, H. Bux, F. Steinbach and J. Caro, Molecular-sieve membrane with hydrogen permselectivity: ZIF-22 in LTA topology prepared with 3-aminopropyltriethoxysilane as covalent linker, Angew. Chem., Int. Ed., 2010, 49, 4958–4961 CrossRef CAS PubMed
.
- A. Huang, Q. Liu, N. Wang and J. Caro, Highly hydrogen permselective ZIF-8 membranes supported on polydopamine functionalized macroporous stainless-steel-nets, J. Mater. Chem. A, 2014, 2, 8246–8251 RSC
.
- G. Z. H. Guo, I. J. Hewitt and S. Qiu, “Twin Copper Source” Growth of Metal−Organic Framework Membrane: Cu3(BTC)2 with High Permeability and Selectivity for Recycling H2, J. Am. Chem. Soc., 2009, 131, 1646–1647, DOI:10.1021/ja8074874
.
- P. Neelakanda, E. Barankova and K.-V. Peinemann, Polymer supported ZIF-8 membranes by conversion of sputtered zinc oxide layers, Microporous Mesoporous Mater., 2016, 220, 215–219 CrossRef CAS
.
- W. Yang, J. Wang, Q. Yang, H. Pei, N. Hu, Y. Suo, Z. Li, D. Zhang and J. Wang, Facile fabrication of robust MOF membranes on cloth via a CMC macromolecule bridge for highly efficient Pb(II) removal, Chem. Eng. J., 2018, 339, 230–239 CrossRef CAS
.
- S. Zhang, M. Zhao, H. Li, C. Hou and M. Du, Facile in situ synthesis of ZIF-67/cellulose hybrid membrane for activating peroxymonosulfate to degrade organic contaminants, Cellulose, 2021, 28, 3585–3598 CrossRef CAS
.
- J. He, X. Cai, K. Chen, Y. Li, K. Zhang, Z. Jin, F. Meng, N. Liu, X. Wang, L. Kong, X. Huang and J. Liu, Performance of a novelly-defined zirconium metal-organic frameworks adsorption membrane in fluoride removal, J. Colloid Interface Sci., 2016, 484, 162–172 CrossRef CAS PubMed
.
- C. Wang, W. Xing, Y. Wu, Y. Li, Y. Yan and J. Zhu,
In situ synthesis of CNT/UiO-66-NH2-based molecularly imprinted nanocomposite membranes for selective recognition and separation of sulfamethoxazole: A synergistic promotion system, Surf. Interfaces, 2022, 31, 101986, DOI:10.1016/j.surfin.2022.101986
.
- Y. Yoo, Z. Lai and H.-K. Jeong, Fabrication of MOF-5 membranes using microwave-induced rapid seeding and solvothermal secondary growth, Microporous Mesoporous Mater., 2009, 123, 100–106 CrossRef CAS
.
- S. Qiu, M. Xue and G. Zhu, Metal-organic framework membranes: from synthesis to separation application, Chem. Soc. Rev., 2014, 43, 6116–6140 RSC
.
- J. Yuan, W.-S. Hung, H. Zhu, K. Guan, Y. Ji, Y. Mao, G. Liu, K.-R. Lee and W. Jin, Fabrication of ZIF-300 membrane and its application for efficient removal of heavy metal ions from wastewater, J. Membr. Sci., 2019, 572, 20–27 CrossRef CAS
.
- J. Gascon, S. Aguado and F. Kapteijn, Manufacture of dense coatings of Cu3(BTC)2 (HKUST-1) on α-alumina, Microporous Mesoporous Mater., 2008, 113, 132–138 CrossRef CAS
.
- M. Fang, M. Drobek, D. Cot, C. Montoro and M. Semsarilar, A Straightforward Method to Prepare MOF-Based Membranes via Direct Seeding of MOF-Polymer Hybrid Nanoparticles, Membranes, 2023, 13, 65, DOI:10.3390/membranes13010065
.
- M. Gao, G. Liu, Y. Gao, G. Chen, X. Huang, X. Xu, J. Wang, X. Yang and D. Xu, Recent advances in metal-organic frameworks/membranes for adsorption and removal of metal ions, TrAC, Trends Anal. Chem., 2021, 137, 116226, DOI:10.1016/j.trac.2021.116226
.
- B. Liu and R. A. Fischer, Liquid-phase epitaxy of metal organic framework thin films, Sci. China: Chem., 2011, 54, 1851–1866 CrossRef CAS
.
- O. Shekhah, R. Swaidan, Y. Belmabkhout, M. du Plessis, T. Jacobs, L. J. Barbour, I. Pinnau and M. Eddaoudi, The liquid phase epitaxy approach for the successful construction of ultra-thin and defect-free ZIF-8 membranes: pure and mixed gas transport study, Chem. Commun., 2014, 50, 2089–2092 RSC
.
- J. Gao, W. Wei, Y. Yin, M. Liu, C. Zheng, Y. Zhang and P. Deng, Continuous ultrathin UiO-66-NH(2) coatings on a polymeric substrate synthesized by a layer-by-layer method: a kind of promising membrane for oil–water separation, Nanoscale, 2020, 12, 6658–6663 RSC
.
- N. Wang, T. Liu, H. Shen, S. Ji, J.-R. Li and R. Zhang, Ceramic tubular MOF hybrid membrane fabricated through in situ layer-by-layer self-assembly for nanofiltration, AIChE J., 2016, 62, 538–546 CrossRef CAS
.
- S. Hurrle, S. Friebe, J. Wohlgemuth, C. Woll, J. Caro and L. Heinke, Sprayable, Large-Area Metal-Organic Framework Films and Membranes of Varying Thickness, Chemistry, 2017, 23, 2294–2298 CrossRef CAS PubMed
.
- S.-Y. Fang, J.-L. Gong, L. Tang, W.-C. Cao, J. Li, Z.-K. Tan, Q.-Y. Niu and Z.-P. Chen, Construction the hierarchical architecture of molybdenum disulfide/MOF composite membrane via electrostatic self-assembly strategy for efficient molecular separation, Chem. Eng. J., 2022, 449, 137808, DOI:10.1016/j.cej.2022.137808
.
- L. M. Chang, Y. Y. An, Q. H. Li, Z. G. Gu, Y. F. Han and J. Zhang, N-Heterocyclic Carbene as a Surface Platform for Assembly of Homochiral Metal-Organic Framework Thin Films in Chiral Sensing, ACS Appl. Mater. Interfaces, 2020, 12, 38357–38364 CrossRef CAS PubMed
.
- S. Jia, D. Ji, L. Wang, X. Qin and S. Ramakrishna, Metal–Organic Framework Membranes: Advances, Fabrication, and Applications, Small Structures, 2022, 3, 2100222, DOI:10.1002/sstr.202100222
.
- X. Liu, T. Yue, K. Qi, Y. Qiu, B. Y. Xia and X. Guo, Metal-organic framework membranes: From synthesis to electrocatalytic applications, Chin. Chem. Lett., 2020, 31, 2189–2201 CrossRef CAS
.
- X. Zhang, K. Wan, P. Subramanian, M. Xu, J. Luo and J. Fransaer, Electrochemical deposition of metal–organic framework films and their applications, J. Mater. Chem. A, 2020, 8, 7569–7587 RSC
.
- R. Ameloot, L. Stappers, J. Fransaer, L. Alaerts, B. F. Sels and D. E. De Vos, Patterned Growth of Metal-Organic Framework Coatings by Electrochemical Synthesis, Chem. Mater., 2009, 21, 2580–2582 CrossRef CAS
.
- A. Martinez Joaristi, J. Juan-Alcañiz, P. Serra-Crespo, F. Kapteijn and J. Gascon, Electrochemical Synthesis of Some Archetypical Zn2 +, Cu2 +, and Al3+ Metal Organic Frameworks, Cryst. Growth Des., 2012, 12, 3489–3498 CrossRef CAS
.
- X. Liu, Metal-organic framework UiO-66 membranes, Front. Chem. Sci. Eng., 2019, 14, 216–232 CrossRef
.
- I. Hod, W. Bury, D. M. Karlin, P. Deria, C.-W. Kung, M. J. Katz, M. So, B. Klahr, D. Jin, Y.-W. Chung, T. W. Odom, O. K. Farha and J. T. Hupp, Directed Growth of Electroactive Metal-Organic Framework Thin Films Using Electrophoretic Deposition, Adv. Mater., 2014, 26, 6295–6300 CrossRef CAS PubMed
.
- S. Zhou, Y. Wei, L. Zhuang, L.-X. Ding and H. Wang, Introduction of metal precursors by electrodeposition for the in situ growth of metal–organic framework membranes on porous metal substrates, J. Mater. Chem. A, 2017, 5, 1948–1951 RSC
.
- G. He, M. Dakhchoune, J. Zhao, S. Huang and K. V. Agrawal, Electrophoretic Nuclei Assembly for Crystallization of High-Performance Membranes on Unmodified Supports, Adv. Funct. Mater., 2018, 28, 1707427, DOI:10.1002/adfm.201707427
.
- B. Yao, S. Hussain, Z. Ye and X. Peng, Electrodeposited MOFs Membrane with In Situ Incorporation of Charged Molecules for Osmotic Energy Harvesting, Small, 2023, e2207559, DOI:10.1002/smll.202207559
.
- M. Choe, J. Y. Koo, I. Park, H. Ohtsu, J. H. Shim, H. C. Choi and S. S. Park, Chemical Vapor Deposition of Edge-on Oriented 2D Conductive Metal-Organic Framework Thin Films, J. Am. Chem. Soc., 2022, 144, 16726–16731 CrossRef CAS PubMed
.
- I. Stassen, M. Styles, G. Grenci, H. V. Gorp, W. Vanderlinden, S. D. Feyter, P. Falcaro, D. D. Vos, P. Vereecken and R. Ameloot, Chemical vapour deposition of zeolitic imidazolate framework thin films, Nat. Mater., 2016, 15, 304–310 CrossRef CAS PubMed
.
- T. Stassin, I. Stassen, J. Marreiros, A. J. Cruz, R. Verbeke, M. Tu, H. Reinsch, M. Dickmann, W. Egger, I. F. J. Vankelecom, D. E. De Vos and R. Ameloot, Solvent-Free Powder Synthesis and MOF-CVD Thin Films of the Large-Pore Metal–Organic Framework MAF-6, Chem. Mater., 2020, 32, 1784–1793 CrossRef CAS
.
- K. B. Lausund, V. Petrovic and O. Nilsen, All-gas-phase synthesis of amino-functionalized UiO-66 thin films, Dalton Trans., 2017, 46, 16983–16992 RSC
.
- C. Crivello, S. Sevim, O. Graniel, C. Franco, S. Pane, J. Puigmarti-Luis and D. Munoz-Rojas, Advanced technologies for the fabrication of MOF thin films, Mater. Horiz., 2021, 8, 168–178 RSC
.
- M. Weber, A. Julbe, S. S. Kim and M. Bechelany, Atomic layer deposition (ALD) on inorganic or polymeric membranes, J. Appl. Phys., 2019, 126, 041101, DOI:10.1063/1.5103212
.
- J. Ren and T.-C. Jen, Atomic layer deposition (ALD) assisting the visibility of metal-organic frameworks (MOFs) technologies, Coord. Chem. Rev., 2021, 430, 213734, DOI:10.1016/j.ccr.2020.213734
.
- K. Khaletskaya, S. Turner, M. Tu, S. Wannapaiboon, A. Schneemann, R. Meyer, A. Ludwig, G. Van Tendeloo and R. A. Fischer, Self-Directed Localization of ZIF-8 Thin Film Formation by Conversion of ZnO Nanolayers, Adv. Funct. Mater., 2014, 24, 4804–4811 CrossRef CAS
.
- J. Zhao, B. Gong, W. T. Nunn, P. C. Lemaire, E. C. Stevens, F. I. Sidi, P. S. Williams, C. J. Oldham, H. J. Walls, S. D. Shepherd, M. A. Browe, G. W. Peterson, M. D. Losego and G. N. Parsons, Conformal and highly adsorptive metal–organic framework thin films via layer-by-layer growth on ALD-coated fiber mats, J. Mater. Chem. A, 2015, 3, 1458–1464 RSC
.
- I. Stassen, M. Styles, T. Van Assche, N. Campagnol, J. Fransaer, J. Denayer, J.-C. Tan, P. Falcaro, D. De Vos and R. Ameloot, Electrochemical Film Deposition of the Zirconium Metal–Organic Framework UiO-66 and Application in a Miniaturized Sorbent Trap, Chem. Mater., 2015, 27, 1801–1807 CrossRef CAS
.
- H. Fan, Q. Shi, H. Yan, S. Ji, J. Dong and G. Zhang, Simultaneous spray self-assembly of highly loaded ZIF-8-PDMS nanohybrid membranes exhibiting exceptionally high biobutanol-permselective pervaporation, Angew. Chem., Int. Ed., 2014, 53, 5578–5582 CrossRef CAS PubMed
.
- H. Ruan, C. Guo, H. Yu, J. Shen, C. Gao, A. Sotto and B. Van, der Bruggen, Fabrication of a MIL-53(Al) Nanocomposite Membrane and Potential Application in Desalination of Dye Solutions, Ind. Eng. Chem. Res., 2016, 55, 12099–12110 CrossRef CAS
.
- Q. Yuan and G. Zhu, A review on metal organic frameworks (MOFs) modified membrane for remediation of water pollution, Environ. Eng. Res., 2020, 26, 190435, DOI:10.4491/eer.2019.435
.
- T. Devic and C. Serre, High valence 3p and transition metal based MOFs, Chem. Soc. Rev., 2014, 43, 6097–6115 RSC
.
- S. Yuan, X. Li, J. Zhu, G. Zhang, P. Van Puyvelde and B. Van der Bruggen, Covalent organic frameworks for membrane separation, Chem. Soc. Rev., 2019, 48, 2665–2681 RSC
.
- A. Zirehpour, A. Rahimpour and M. Ulbricht, Nano-sized metal organic framework to improve the structural properties and desalination performance of thin film composite forward osmosis membrane, J. Membr. Sci., 2017, 531, 59–67 CrossRef CAS
.
- A. K. Shukla, J. Alam, M. S. Alhoshan, F. A. A. Ali, U. Mishra and A. A. Hamid, Thin-Film Nanocomposite Membrane Incorporated with Porous Zn-Based Metal-Organic Frameworks: Toward Enhancement of Desalination Performance and Chlorine Resistance, ACS Appl. Mater. Interfaces, 2021, 13, 28818–28831 CrossRef CAS PubMed
.
- H. Liu, M. Zhang, H. Zhao, Y. Jiang, G. Liu and J. Gao, Enhanced dispersibility of metal-organic frameworks (MOFs) in the organic phase via surface modification for TFN nanofiltration membrane preparation, RSC Adv., 2020, 10, 4045–4057 RSC
.
- J. Wang, Y. Wang, Y. Zhang, A. Uliana, J. Zhu, J. Liu and B. Van der Bruggen, Zeolitic Imidazolate Framework/Graphene Oxide Hybrid Nanosheets Functionalized Thin Film Nanocomposite Membrane for Enhanced Antimicrobial Performance, ACS Appl. Mater. Interfaces, 2016, 8, 25508–25519 CrossRef CAS PubMed
.
- L. F. Dumée, J. W. Maina, A. Merenda, R. Reis, L. He and L. Kong, Hybrid thin film nano-composite membrane reactors for simultaneous separation and degradation of pesticides, J. Membr. Sci., 2017, 528, 217–224 CrossRef
.
- M. Q. Seah, W. J. Lau, P. S. Goh, H. H. Tseng, R. A. Wahab and A. F. Ismail, Progress of Interfacial Polymerization Techniques for Polyamide Thin Film (Nano)Composite Membrane Fabrication: A Comprehensive Review, Polymers, 2020, 12, 2817, DOI:10.3390/polym12122817
.
- Y. Zhang, X. Feng, H. Li, Y. Chen, J. Zhao, S. Wang, L. Wang and B. Wang, Photoinduced postsynthetic polymerization of a metal-organic framework toward a flexible stand-alone membrane, Angew. Chem., Int. Ed., 2015, 54, 4259–4263 CrossRef CAS PubMed
.
- B. J. Yao, W. L. Jiang, Y. Dong, Z. X. Liu and Y. B. Dong, Post-Synthetic Polymerization of UiO-66-NH2 Nanoparticles and Polyurethane Oligomer toward Stand-Alone Membranes for Dye Removal and Separation, Chemistry, 2016, 22, 10565–10571 CrossRef CAS PubMed
.
- J. Min, H. Lu and B. Yan, Eu(3+) functionalized robust membranes based on the post-synthetic copolymerization of a metal-organic framework and ethyl methacrylate, Dalton Trans., 2021, 50, 7597–7603 RSC
.
- Y. Liu, X.-P. Wang, Z.-A. Zong, R. Lin, X.-Y. Zhang, F.-S. Chen, W.-D. Ding, L.-L. Zhang, X.-M. Meng and J. Hou, Thin film nanocomposite membrane incorporated with 2D-MOF nanosheets for highly efficient reverse osmosis desalination, J. Membr. Sci., 2022, 653, 120520, DOI:10.1016/j.memsci.2022.120520
.
- P. Cheng, Y. Liu, X. Wang, K. Fan, P. Li and S. Xia, Regulating interfacial polymerization via constructed 2D metal-organic framework interlayers for fabricating nanofiltration membranes with enhanced performance, Desalination, 2022, 544, 116134, DOI:10.1016/j.desal.2022.116134
.
- Y. Liu, H. Lv, Y. Liu, Y. Gao, H. Y. Kim, Y. Ouyang and D.-G. Yu, Progresses on electrospun metal–organic frameworks nanofibers and their wastewater treatment applications, Mater. Today Chem., 2022, 25, 100974, DOI:10.1016/j.mtchem.2022.100974
.
- R. Zhao, Y. Tian, S. Li, T. Ma, H. Lei and G. Zhu, An electrospun fiber based metal–organic framework composite membrane for fast, continuous, and simultaneous removal of insoluble and soluble contaminants from water, J. Mater. Chem. A, 2019, 7, 22559–22570 RSC
.
- X. Wang, W. Xu, J. Gu, X. Yan, Y. Chen, M. Guo, G. Zhou, S. Tong, M. Ge, Y. Liu and C. Chen, MOF-based fibrous membranes adsorb PM efficiently and capture toxic gases selectively, Nanoscale, 2019, 11, 17782–17790 RSC
.
- J. Li, H. Wang, X. Yuan, J. Zhang and J. W. Chew, Metal-organic framework membranes for wastewater treatment and water regeneration, Coord. Chem. Rev., 2020, 404, 213116, DOI:10.1016/j.ccr.2019.213116
.
- Y. Wang, X. Dai, X. Li and X. Wang, The PM2.5 capture of poly (lactic acid)/nano MOFs eletrospinning membrane with hydrophilic surface, Mater. Res. Express, 2018, 5, 036416, DOI:10.1088/2053-1591/aab7b5
.
- F. Yang, J. E. Efome, D. Rana, T. Matsuura and C. Lan, Metal-Organic Frameworks Supported on Nanofiber for Desalination by Direct Contact Membrane Distillation, ACS Appl. Mater. Interfaces, 2018, 10, 11251–11260 CrossRef CAS PubMed
.
- Y. Liu, S. Lin, Y. Liu, A. K. Sarkar, J. K. Bediako, H. Y. Kim and Y. S. Yun, Super-Stable, Highly Efficient, and Recyclable Fibrous Metal-Organic Framework Membranes for Precious Metal Recovery from Strong Acidic Solutions, Small, 2019, 15, e1805242 CrossRef PubMed
.
- J. E. Efome, D. Rana, T. Matsuura and C. Q. Lan, Insight Studies on Metal-Organic Framework Nanofibrous Membrane Adsorption and Activation for Heavy Metal Ions Removal from Aqueous Solution, ACS Appl. Mater. Interfaces, 2018, 10, 18619–18629 CrossRef CAS PubMed
.
- Q. Guo, Y. Li, X. Y. Wei, L. W. Zheng, Z. Q. Li, K. G. Zhang and C. G. Yuan, Electrospun metal-organic frameworks hybrid nanofiber membrane for efficient removal of As(III) and As(V) from water, Ecotoxicol. Environ. Saf., 2021, 228, 112990 CrossRef CAS PubMed
.
- Y. Xiao, W. Zhang, Y. Jiao, Y. Xu and H. Lin, Metal-phenolic network as precursor for fabrication of metal-organic framework (MOF) nanofiltration membrane for efficient desalination, J. Membr. Sci., 2021, 624, 119101, DOI:10.1016/j.memsci.2021.119101
.
- P. Zhao, R. Li, W. Wu, J. Wang, J. Liu and Y. Zhang,
In situ growth of polyvinylpyrrolidone modified Zr-MOFs thin-film nanocomposite (TFN) for efficient dyes removal, Composites, Part B, 2019, 176, 107208, DOI:10.1016/j.compositesb.2019.107208
.
- W. Li, Metal–organic framework membranes: Production, modification, and applications, Prog. Mater. Sci., 2019, 100, 21–63 CrossRef
.
- S. Das and T. Ben, A [COF-300]-[UiO-66] composite membrane with remarkably high permeability and H2/CO2 separation selectivity, Dalton Trans., 2018, 47, 7206–7212 RSC
.
- Y. Bian, R. Wang, S. Wang, C. Yao, W. Ren, C. Chen and L. Zhang, Metal–organic framework-based nanofiber filters for effective indoor air quality control, J. Mater. Chem. A, 2018, 6, 15807–15814 RSC
.
- N. Wei, X. Zheng, Q. Li, C. Gong, H. Ou and Z. Li, Construction of lanthanum modified MOFs graphene oxide composite membrane for high selective phosphorus recovery and water purification, J. Colloid Interface Sci., 2020, 565, 337–344 CrossRef CAS PubMed
.
- J. Jiang, D. Wu, N. Tian, M. Wang, J. Huang, R. Li, M. Wu, H. Ni and P. Ye, Preparation of GO/GOH/MOFs ternary blend membrane and its application for enhanced dye wastewater purification, J. Solid State Chem., 2022, 310, 123028, DOI:10.1016/j.jssc.2022.123028
.
- K. Yang, F. Zhang, Y. Chen, H. Zhang, B. Xiong and H. Chen, Recent progress on carbon-based composites in multidimensional applications, Composites, Part A, 2022, 157, 106906, DOI:10.1016/j.compositesa.2022.106906
.
- P. Baraneedharan and S. Vadivel, A. A. C, S. B. Mohamed and S. Rajendran, Advances in preparation, mechanism and applications of various carbon materials in environmental applications: A review, Chemosphere, 2022, 300, 134596 CrossRef CAS PubMed
.
- J. S. Babu, H. B. N. Prasanna, J. S. Babu, Y. N. Rao and S. M. Beyan, and L. R, Environmental Applications of Sorbents, High-Flux Membranes of Carbon-Based Nanomaterials, Adsorpt. Sci. Technol., 2022, 2022, 1–13 CrossRef
.
- D. R. Dreyer, A. D. Todd and C. W. Bielawski, Harnessing the chemistry of graphene oxide, Chem. Soc. Rev., 2014, 43, 5288–5301 RSC
.
- W. Yu, L. Sisi, Y. Haiyan and L. Jie, Progress in the functional modification of graphene/graphene oxide: a review, RSC Adv., 2020, 10, 15328–15345 RSC
.
- Y. Li, X. Zhang, A. Yang, C. Jiang, G. Zhang, J. Mao and Q. Meng, Polyphenol etched ZIF-8 modified graphene oxide nanofiltration membrane for efficient removal of salts and organic molecules, J. Membr. Sci., 2021, 635, 119521, DOI:10.1016/j.memsci.2021.119521
.
- H. Qu, X. Xiao, Z. Han, M. Hu, S. Shen, L. Yang, F. Jia, T. Wang, Z. Ye, W. Sun, Y. Wang, L. Huang, Z. Zhu, P. Servati, J. Tang and J. Chen, Graphene Oxide
Nanofiltration Membrane Based on Three-Dimensional Size-Controllable Metal–Organic Frameworks for Water Treatment, ACS Appl. Nano Mater., 2022, 5, 5196–5207 CrossRef CAS
.
- M. Zhu, Y. Liu, M. Chen, D. Gan, M. Wang, H. Zeng, M. Liao, J. Chen, W. Tu and W. Niu, Ultrahigh flux of graphene oxide membrane modified with orientated growth of MOFs for rejection of dyes and oil-water separation, Chin. Chem. Lett., 2020, 31, 2683–2688 CrossRef CAS
.
- S. F. Nitodas, M. Das and R. Shah, Applications of Polymeric Membranes with Carbon Nanotubes: A Review, Membranes, 2022, 12, 454, DOI:10.3390/membranes12050454
.
- L. Dumée, L. He, M. Hill, B. Zhu, M. Duke, J. Schütz, F. She, H. Wang, S. Gray, P. Hodgson and L. Kong, Seeded growth of ZIF-8 on the surface of carbon nanotubes towards self-supporting gas separation membranes, J. Mater. Chem. A, 2013, 1, 9208, 10.1039/c3ta11483j
.
- R. Lin, L. Ge, S. Liu, V. Rudolph and Z. Zhu, Mixed-Matrix Membranes with Metal-Organic Framework-Decorated CNT Fillers for Efficient CO2 Separation, ACS Appl. Mater. Interfaces, 2015, 7, 14750–14757 CrossRef CAS PubMed
.
- Q. Wang and D. O'Hare, Recent advances in the synthesis and application of layered double hydroxide (LDH) nanosheets, Chem. Rev., 2012, 112, 4124–4155 CrossRef CAS PubMed
.
- Y. Liu, N. Wang, Z. Cao and J. Caro, Molecular sieving through interlayer galleries, J. Mater. Chem. A, 2014, 2, 1235–1238 RSC
.
- Y. Liu, N. Wang and J. Caro, In situ formation of LDH membranes of different microstructures with molecular sieve gas selectivity, J. Mater. Chem. A, 2014, 2, 5716–5723 RSC
.
- Y. Liu, J. H. Pan, N. Wang, F. Steinbach, X. Liu and J. Caro, Remarkably enhanced gas separation by partial self-conversion of a laminated membrane to metal-organic frameworks, Angew. Chem., Int. Ed., 2015, 54, 3028–3032 CrossRef CAS PubMed
.
- J. L. Casci, Zeolite molecular sieves: preparation and scale-up, Microporous Mesoporous Mater., 2005, 82, 217–226 CrossRef CAS
.
- G. Zhang, T. Zhang, X. Zhang and K. L. Yeung, Continuous flow ZIF-8/NaA composite membrane microreactor for efficient Knoevenagel condensation, Catal. Commun., 2015, 68, 93–96 CrossRef CAS
.
- Z. Y. Yeo, P. W. Zhu, A. R. Mohamed and S.-P. Chai, An enhanced hybrid membrane of ZIF-8 and zeolite T for CO2/CH4 separation, CrystEngComm, 2014, 16, 3072–3075 RSC
.
- N. Liu, J. Cheng, W. Hou, X. Yang and J. Zhou, Pebax-based mixed matrix membranes loaded with graphene oxide/core shell ZIF-8@ZIF -67 nanocomposites improved CO2 permeability and selectivity, J. Appl. Polym. Sci., 2021, 138, 50553, DOI:10.1002/app.50553
.
- A. Knebel, P. Wulfert-Holzmann, S. Friebe, J. Pavel, I. Strauss, A. Mundstock, F. Steinbach and J. Caro, Hierarchical Nanostructures of Metal-Organic Frameworks Applied in Gas Separating ZIF-8-on-ZIF-67 Membranes, Chemistry, 2018, 24, 5728–5733 CrossRef CAS PubMed
.
- H. Xiao, M. Chai, M. Abdollahzadeh, H. Ahmadi, V. Chen, D. B. Gore, M. Asadnia and A. Razmjou, A lithium ion selective membrane synthesized from a double layered Zrbased metalorganic framework (MOF-on-MOF) thin film, Desalination, 2022, 532, 115733, DOI:10.1016/j.desal.2022.115733
.
- H. Tang, M. Jia and W. Li, Gel-to-crystal route towards MOF-mixed MOF-matrix membranes, Mater. Today Chem., 2022, 24, 100867, DOI:10.1016/j.mtchem.2022.100867
.
- Y. Xu, X. Zhao, R. Chang, H. Qu, J. Xu and J. Ma, Designing heterogeneous MOF-on-MOF membrane with hierarchical pores for effective water treatment, J. Membr. Sci., 2022, 658, 120737, DOI:10.1016/j.memsci.2022.120737
.
- M. Fang, C. Montoro and M. Semsarilar, Metal and Covalent Organic Frameworks for Membrane Applications, Membranes, 2020, 10, 107, DOI:10.3390/membranes10050107
.
- Y. Cheng, Y. Ying, L. Zhai, G. Liu, J. Dong, Y. Wang, M. P. Christopher, S. Long, Y. Wang and D. Zhao, Mixed matrix membranes containing MOF@COF hybrid fillers for efficient CO2/CH4 separation, J. Membr. Sci., 2019, 573, 97–106 CrossRef CAS
.
- J. Fu, S. Das, G. Xing, T. Ben, V. Valtchev and S. Qiu, Fabrication of COF-MOF Composite Membranes and Their Highly Selective Separation of H2/CO2, J. Am. Chem. Soc., 2016, 138, 7673–7680 CrossRef CAS PubMed
.
- Y. Deng, Y. Wang, X. Xiao, B. J. Saucedo, Z. Zhu, M. Xie, X. Xu, K. Yao, Y. Zhai, Z. Zhang and J. Chen, Progress in Hybridization of Covalent Organic Frameworks and Metal-Organic Frameworks, Small, 2022, 18, e2202928 CrossRef PubMed
.
- R. Xue, H. Guo, W. Yang, S.-L. Huang and G.-Y. Yang, Cooperation between covalent organic frameworks (COFs) and metal organic frameworks (MOFs): application of COFs–MOFs hybrids, Adv. Compos. Hybrid Mater., 2022, 5, 1595–1611 CrossRef CAS
.
- Y. Liu, H. Wu, R. Li, J. Wang, Y. Kong, Z. Guo, H. Jiang, Y. Ren, Y. Pu, X. Liang, F. Pan, Y. Cao, S. Song, G. He and Z. Jiang, MOF–COF “Alloy” Membranes for Efficient Propylene/Propane Separation, Adv. Mater., 2022, 34, e2201423 CrossRef PubMed
.
- K. Friess, P. Izak, M. Karaszova, M. Pasichnyk, M. Lanc, D. Nikolaeva, P. Luis and J. C. Jansen, A Review on Ionic Liquid Gas Separation Membranes, Membranes, 2021, 11, 97, DOI:10.3390/membranes11020097
.
- D. Zheng, D. Hua, Y. Hong, A.-R. Ibrahim, A. Yao, J. Pan and G. Zhan, Functions of Ionic Liquids in Preparing Membranes for Liquid Separations: A Review, Membranes, 2020, 10, 395, DOI:10.3390/membranes10120395
.
- B. Sasikumar, G. Arthanareeswaran and A. F. Ismail, Recent progress in ionic liquid membranes for gas separation, J. Mol. Liq., 2018, 266, 330–341 CrossRef CAS
.
- R. D. Noble and D. L. Gin, Perspective on ionic liquids and ionic liquid membranes, J. Membr. Sci., 2011, 369, 1–4 CrossRef CAS
.
- M. Hasib-ur-Rahman, M. Siaj and F. Larachi, Ionic liquids for CO2 capture—Development and progress, Chem. Eng. Process., 2010, 49, 313–322 CrossRef CAS
.
- O. Tzialla, C. Veziri, X. Papatryfon, K. G. Beltsios, A. Labropoulos, B. Iliev, G. Adamova, T. J. S. Schubert, M. C. Kroon, M. Francisco, L. F. Zubeir, G. E. Romanos and G. N. Karanikolos, Zeolite Imidazolate Framework–Ionic Liquid Hybrid Membranes for Highly Selective CO2 Separation, J. Phys. Chem. C, 2013, 117, 18434–18440 CrossRef CAS
.
- L. Hao, P. Li, T. Yang and T.-S. Chung, Room temperature ionic liquid/ZIF-8 mixed-matrix membranes for natural gas sweetening and post-combustion CO2 capture, J. Membr. Sci., 2013, 436, 221–231 CrossRef CAS
.
- S. Qian, L. Xia, L. Yang, X. Wang, X. Suo, X. Cui and H. Xing, Defect-free mixed-matrix membranes consisting of anion-pillared metal-organic frameworks and poly(ionic liquid)s for separation of acetylene from ethylene, J. Membr. Sci., 2020, 611, 118329, DOI:10.1016/j.memsci.2020.118329
.
- C. Geng, Y. Sun, Z. Zhang, Z. Qiao and C. Zhong, Mixed matrix metal–organic framework membranes for efficient CO2/N2 separation under humid conditions, AIChE J., 2023, 69(5), e18025, DOI:10.1002/aic.18025
.
- M. Ulbricht, Advanced functional polymer membranes, Polymer, 2006, 47, 2217–2262 CrossRef CAS
.
- C. E. Powell and G. G. Qiao, Polymeric CO2/N2 gas separation membranes for the capture of carbon dioxide from power plant flue gases, J. Membr. Sci., 2006, 279, 1–49 CrossRef CAS
.
- X. Liu, H. Jin, Y. Li, H. Bux, Z. Hu, Y. Ban and W. Yang, Metal–organic framework ZIF-8 nanocomposite membrane for efficient recovery of furfural via pervaporation and vapor permeation, J. Membr. Sci., 2013, 428, 498–506 CrossRef CAS
.
- X. Li, T. Gao, Z. Zhou, J. Jiang, J. Feng and L. Chen, Facile Synthesis of Amine-functionalized MOFs Incorporated Polyimide MMMs with Enhanced CO2 Permselectivity, ChemistrySelect, 2019, 4, 2368–2373 CrossRef CAS
.
- C. Wang, H. Wang, Y. Li, Y. Feng, Z. Q. Liu, T. S. Zhao and L. Cao, Zwitterionic metal-organic frameworks modified polyamide membranes with enhanced water flux and antifouling capacity, Chemosphere, 2022, 309, 136684 CrossRef CAS PubMed
.
- L. Cheng, Z. Zhou, L. Li, P. Xiao, Y. Ma, F. Liu and J. Li, PVDF/MOFs mixed matrix ultrafiltration membrane for efficient water treatment, Front. Chem., 2022, 10 DOI:10.3389/fchem.2022.985750
.
- Y. Tan, Z. Sun, H. Meng, Y. Han, J. Wu, J. Xu, Y. Xu and X. Zhang, Aminated metal-organic framework (NH2-MIL-101(Cr)) incorporated polyvinylidene (PVDF) hybrid membranes: Synthesis and application in efficient removal of Congo red from aqueous solution, Appl. Organomet. Chem., 2019, 34(1), e5281, DOI:10.1002/aoc.5281
.
- A. Xie, J. Cui, J. Yang, Y. Chen, J. Lang, C. Li, Y. Yan and J. Dai, Photo-Fenton self-cleaning PVDF/NH2-MIL-88B(Fe) membranes towards highly-efficient oil/water emulsion separation, J. Membr. Sci., 2020, 595, 117499, DOI:10.1016/j.memsci.2019.117499
.
- H. C. H. Wang, Y. Zeng, G. R. Chen and M. B. Cui, Hydrophilic modification and anti-fouling properties of PVDF ultrafiltration membrane via blending of nano-particle MIL-101 MOFs, Dig. J. Nanomater. Bios., 2021, 16, 515–526 CrossRef
.
- L. Shu, L.-H. Xie, Y. Meng, T. Liu, C. Zhao and J.-R. Li, A thin and high loading two-dimensional MOF nanosheet based mixed-matrix membrane for high permeance nanofiltration, J. Membr. Sci., 2020, 603, 118049, DOI:10.1016/j.memsci.2020.118049
.
- H. Qin, Y. He, P. Xu, D. Huang, Z. Wang, H. Wang, Z. Wang, Y. Zhao, Q. Tian and C. Wang, Spinel ferrites (MFe(2)O(4)): Synthesis, improvement and catalytic application in environment and energy field, Adv. Colloid Interface Sci., 2021, 294, 102486 CrossRef CAS PubMed
.
- Z. Wang, Y. Chen, L. Wang, J. Zheng, Y. Fan and S. Zhang, Rapid and efficient removal of toxic ions from water using Zr-based MOFs@PIM hierarchical porous nanofibre membranes, Chem. Eng. J., 2023, 452, 139198, DOI:10.1016/j.cej.2022.139198
.
- Y. Liu, Z. Huang, W. He, M. Chen, W. Tu, M. Zhu, D. Gan and S. Liu, Multifunctional stable PDA/RGO/MOFs&SiO2-COOH membrane with excellent flux and anti-fouling performance for the separation of organic dye and oil/water, Surf. Interfaces, 2022, 33, 102183, DOI:10.1016/j.surfin.2022.102183
.
- D. Ma, S. B. Peh, G. Han and S. B. Chen, Thin-Film Nanocomposite (TFN) Membranes Incorporated with Super-Hydrophilic Metal-Organic Framework (MOF) UiO-66: Toward Enhancement of Water Flux and Salt Rejection, ACS Appl. Mater. Interfaces, 2017, 9, 7523–7534 CrossRef CAS PubMed
.
- H. He, Y. Liu, Y. Zhu, T. C. Zhang and S. Yuan, Underoil superhydrophilic CuC2O4@Cu-MOFs core-shell nanosheets-coated copper mesh membrane for on-demand emulsion separation and simultaneous removal of soluble dye, Sep. Purif. Technol., 2022, 293, 121089, DOI:10.1016/j.seppur.2022.121089
.
- X. Liu, Y. Shan, S. Zhang, Q. Kong and H. Pang, Application of metal organic framework in wastewater treatment, Green Energy Environ., 2022, 8(3), 698–721, DOI:10.1016/j.gee.2022.03.005
.
- P. Xu, M. Chen, G. Zeng, D. Huang, C. Lai, Z. Wang, M. Yan, Z. Huang, X. Gong, B. Song, T. Li and A. Duan, Effects of multi-walled carbon nanotubes on metal transformation and natural organic matters in riverine sediment, J. Hazard. Mater., 2019, 374, 459–468 CrossRef CAS PubMed
.
- P. Xu, G. M. Zeng, D. L. Huang, M. Yan, M. Chen, C. Lai, H. Jiang, H. P. Wu, G. M. Chen and J. Wan, Fabrication of reduced glutathione functionalized iron oxide nanoparticles for magnetic removal of Pb(II) from wastewater, J. Taiwan Inst. Chem. Eng., 2017, 71, 165–173 CrossRef CAS
.
- N. Yin, K. Wang, L. Wang and Z. Li, Amino-functionalized MOFs combining ceramic membrane ultrafiltration for Pb (II) removal, Chem. Eng. J., 2016, 306, 619–628 CrossRef CAS
.
- S. Miao, J. Guo, Z. Deng, J. Yu and Y. Dai, Adsorption and reduction of Cr(VI) in water by iron-based metal-organic frameworks (Fe-MOFs) composite electrospun nanofibrous membranes, J. Cleaner Prod., 2022, 370, 133566, DOI:10.1016/j.jclepro.2022.133566
.
- B. Forouzesh Rad, H. Mahdavi, M. Forouzesh Rad and M. Baghdadi, Using Design-Expert to Optimize the Properties of a Polyethersulfone Ultrafiltration Membrane Through the Incorporation of NH2-MIL-53(Fe) and PVP for Maximum Cr(VI) Removal and Flux, J. Polym. Environ., 2022, 30, 3875–3889 CrossRef CAS
.
- Z. Li, G. Zhou, H. Dai, M. Yang, Y. Fu, Y. Ying and Y. Li, Biomineralization-mimetic preparation of hybrid membranes with ultra-high loading of pristine metal–organic frameworks grown on silk nanofibers for hazard collection in water, J. Mater. Chem. A, 2018, 6, 3402–3413 RSC
.
- U. Sharma, R. Pandey, S. Basu and P. Saravanan, Facile monomer interlayered MOF based thin film nanocomposite for efficient arsenic separation, Chemosphere, 2022, 309, 136634 CrossRef CAS PubMed
.
- P. Xu, M. Chen, C. Lai, G. Zeng, D. Huang, H. Wang, X. Gong, L. Qin, Y. Liu, D. Mo, X. Wen, C. Zhou and R. Wang, Effects of typical engineered nanomaterials on 4-nonylphenol degradation in river sediment: based on bacterial community and function analysis, Environ. Sci.: Nano, 2019, 6, 2171–2184 RSC
.
- H. Qin, Y. He, P. Xu, Y. Zhu, H. Wang, Z. Wang, Y. Zhao, H. Xie, Q. Tian, C. Wang, Y. Zeng and Y. Li, Carbon-doped CuFe2O4 with C--O--M channels for enhanced Fenton-like degradation of tetracycline hydrochloride: From construction to mechanism, Green Energy Environ., 2022 DOI:10.1016/j.gee.2022.09.006
.
- F. Xiao, M. Cao, R. Chu, X. Hu, W. Shi and Y. Chen, Novel Perylene-3, 4, 9, 10-tetracarboxylic dianhydride modified Zr-MOFs/Graphene oxide membrane for dye wastewater treatment, J. Colloid Interface Sci., 2022, 610, 671–686 CrossRef CAS PubMed
.
- J. Cheng, J. Liang, L. Dong, J. Chai, N. Zhao, S. Ullah, H. Wang, D. Zhang, S. Imtiaz, G. Shan and G. Zheng, Self-assembly of 2D-metal-organic framework/graphene oxide membranes as highly efficient adsorbents for the removal of Cs(+) from aqueous solutions, RSC Adv., 2018, 8, 40813–40822 RSC
.
- Z. Shi, C. Xu, F. Chen, Y. Wang, L. Li, Q. Meng and R. Zhang, Renewable metal–organic-frameworks-coated 3D printing film for removal of malachite green, RSC Adv., 2017, 7, 49947–49952 RSC
.
- X. Yu, W. Fan, V. Wee, D. Shi, H. Yuan, Y. Ying, Y. D. Yuan, Z. Yang, Y. Feng, D. Sun and D. Zhao, Polycrystalline Iron(III) metal-organic framework membranes for organic solvent nanofiltration with high permeance, J. Membr. Sci., 2022, 644, 120130, DOI:10.1016/j.memsci.2021.120130
.
- L. Sarango, L. Paseta, M. Navarro, B. Zornoza and J. Coronas, Controlled deposition of MOFs by dip-coating in thin film nanocomposite membranes for organic solvent nanofiltration, J. Ind. Eng. Chem., 2018, 59, 8–16 CrossRef CAS
.
- Q. Xiang, Z. Yu, X. Li, P. Wang, N. He, Y. Pang, Q. Wang and Y. Liu, Construction of a highly stable g-C3N4/NH2-MIL-88B(Fe)/CD@graphene oxide self-cleaning membrane for dye wastewater separation and degradation, New J. Chem., 2022, 46, 17438–17455 RSC
.
- J. Li, J. L. Gong, G. M. Zeng, P. Zhang, B. Song, W. C. Cao, H. Y. Liu and S. Y. Huan, Zirconium-based metal organic frameworks loaded on polyurethane foam membrane for simultaneous removal of dyes with different charges, J. Colloid Interface Sci., 2018, 527, 267–279 CrossRef CAS PubMed
.
- L. Zhou, N. Li, G. Owens and Z. Chen, Simultaneous removal of mixed contaminants, copper and norfloxacin, from aqueous solution by ZIF-8, Chem. Eng. J., 2019, 362, 628–637 CrossRef CAS
.
- K. Li, J. J. Li, N. Zhao, Y. Ma and B. Di, Removal of Tetracycline in Sewage and Dairy Products with High-Stable MOF, Molecules, 2020, 25(6), 1312, DOI:10.3390/molecules25061312
.
- Alamgir, K. Talha, B. Wang, J.-H. Liu, R. Ullah, F. Feng, J. Yu, S. Chen and J.-R. Li, Effective adsorption of metronidazole antibiotic from water with a stable Zr(IV)-MOFs: Insights from DFT, kinetics and thermodynamics studies, J. Environ. Chem. Eng., 2020, 8(1), 103642, DOI:10.1016/j.jece.2019.103642
.
- H. Li, X. Xu, J. Wang, X. Han and Z. Xu, A Robust PVDF-Assisted Composite Membrane for Tetracycline Degradation in Emulsion and Oil-Water Separation, Nanomaterials, 2021, 11(12), 3201, DOI:10.3390/nano11123201
.
- Q. Wu, J. Fan, X. Chen, Z. Zhu, J. Luo and Y. Wan, Sandwich structured membrane adsorber with metal organic frameworks for aflatoxin B1 removal, Sep. Purif. Technol., 2020, 246, 116907, DOI:10.1016/j.seppur.2020.116907
.
- C. Hu, C. Yang, X. Wang, X. Wang, S. Zhen, L. Zhan, C. Huang and Y. Li, Rapid and facile synthesis of Au nanoparticle-decorated porous MOFs for the efficient reduction of 4-nitrophenol, Sep. Purif. Technol., 2022, 300, 121801, DOI:10.1016/j.seppur.2022.121801
.
- C. Hou, W. Chen, L. Fu, S. Zhang, C. Liang and Y. Wang, Efficient degradation of perfluorooctanoic acid by electrospun lignin-based bimetallic MOFs nanofibers composite membranes with peroxymonosulfate under solar light irradiation, Int. J. Biol. Macromol., 2021, 174, 319–329 CrossRef CAS PubMed
.
- C. Yang, J. Wang, W. Yan and Y. Xia, Facile synthesis disposable MOF membrane filter: Growth of NH2-MIL-125 (Ti) on filter paper for fast removal of organophosphorus pesticides
in aqueous solution and vegetables, Food Chem., 2022, 389, 133056, DOI:10.1016/j.foodchem.2022.133056
.
- P. Huang, X. Wang, J. Zhao, Z. Zhang, X. Du and X. Lu, Hollow Co-MOF-74 incorporated electrospun nanofiber membranes with hierarchical structures for enhanced removal of polycyclic aromatic hydrocarbons by drain-type adsorption, Chem. Eng. J., 2022, 449, 137759, DOI:10.1016/j.cej.2022.137759
.
- S. Xu, J. Liang, M. I. B. Mohammad, D. Lv, Y. Cao, J. Qi, K. Liang and J. Ma, Biocatalytic metal–organic framework membrane towards efficient aquatic micropollutants removal, Chem. Eng. J., 2021, 426, 131861, DOI:10.1016/j.cej.2021.131861
.
- Y.-Z. Wu, H.-X. Li, Z.-L. Xu, P. Li, Z.-M. Zhan, P.-P. Li and S.-J. Xu, Ceramic hollow fiber NF membrane incorporating UiO-66 for the chlorinated hydrocarbons removal, Chem. Eng. J., 2022, 435, 134789, DOI:10.1016/j.cej.2022.134789
.
- M. Feng, P. Zhang, H. C. Zhou and V. K. Sharma, Water-stable metal-organic frameworks for aqueous removal of heavy metals and radionuclides: A review, Chemosphere, 2018, 209, 783–800 CrossRef CAS PubMed
.
- B. F. Parker, Z. Zhang, L. Rao and J. Arnold, An overview and recent progress in the chemistry of uranium extraction from seawater, Dalton Trans., 2018, 47, 639–644 RSC
.
- J. Cheng, K. Liu, X. Li, L. Huang, J. Liang, G. Zheng and G. Shan, Nickel-metal-organic framework nanobelt based composite membranes for efficient Sr(2 +) removal from aqueous solution, Environ. Sci. Ecotechnology, 2020, 3, 100035 CrossRef PubMed
.
- T. Liu, Z. Li, X. Zhang, H. Tan, Z. Chen, J. Wu, J. Chen and H. Qiu, Metal-Organic Framework-Intercalated Graphene Oxide Membranes for Selective Separation of Uranium, Anal. Chem., 2021, 93, 16175–16183 CrossRef CAS PubMed
.
- J. Zhanga, X. Pan, Q. Xue, D. He, L. Zhu and Q. Guo, Antifouling hydrolyzed polyacrylonitrile/graphene oxide membrane with spindle-knotted structure for highly effective separation of oil-water emulsion, J. Membr. Sci., 2017, 532, 38–46 CrossRef
.
- J. Cao, Y. Su, Y. Liu, J. Guan, M. He, R. Zhang and Z. Jiang, Self-assembled MOF membranes with underwater superoleophobicity for oil/water separation, J. Membr. Sci., 2018, 566, 268–277 CrossRef CAS
.
- M. Cao, F. Xiao, Z. Yang, Y. Chen and L. Lin, Purification of oil-containing emulsified wastewater via PAN nanofiber membrane loading PVP-UiO-66-NH2, Sep. Purif. Technol., 2022, 297, 121514, DOI:10.1016/j.seppur.2022.121514
.
- M. Samari, S. Zinadini, A. A. Zinatizadeh, M. Jafarzadeh and F. Gholami, A new antifouling metal-organic framework based UF membrane for oil-water separation: A comparative study on the effect of MOF (UiO-66-NH2) ligand modification, Korean J. Chem. Eng., 2022, 39, 3092–3101, DOI:10.1007/s11814-022-1177-1
.
- X.-T. He, B.-Y. Li, J.-X. Liu, W.-Q. Tao and Z. Li, Facile fabrication of 2D MOF-Based membrane with hierarchical structures for ultrafast Oil-Water separation, Sep. Purif. Technol., 2022, 297, 121488, DOI:10.1016/j.seppur.2022.121488
.
- N. Abdullah, N. Yusof, A. F. Ismail and W. J. Lau, Insights into metal-organic frameworks-integrated membranes for desalination process: A review, Desalination, 2021, 500, 114867, DOI:10.1016/j.desal.2020.114867
.
- M. Alhoshan, A. K. Shukla, T. H. Mana, F. A. A. Ali and J. Alam, An Evolving MOF Thin-Film Nanocomposite Tubular Ceramic Membrane for Desalination Pretreatment, J. Inorg. Organomet. Polym. Mater., 2022, 33, 337–352, DOI:10.1007/s10904-022-02501-y
.
- Y. Lin, Y. Chen and R. Wang, Thin
film nanocomposite hollow fiber membranes incorporated with surface functionalized HKUST-1 for highly-efficient reverses osmosis desalination process, J. Membr. Sci., 2019, 589, 117249, DOI:10.1016/j.memsci.2019.117249
.
- B. Yin, L. Sun, S. Tang and H. Zhou, Preparation of Metal–Organic Framework/Polyvinylidene Fluoride Mixed Matrix Membranes for Water Treatment, Ind. Eng. Chem. Res., 2020, 59, 19689–19697 CrossRef CAS
.
- P. Hu, B. Yuan, Q. Jason Niu, N. Wang, S. Zhao, J. Cui and J. Jiang, In situ assembled zeolite imidazolate framework nanocrystals hybrid thin film nanocomposite membranes for brackish water desalination, Sep. Purif. Technol., 2022, 293, 121134, DOI:10.1016/j.seppur.2022.121134
.
- D. D. Kachhadiya and Z. V. P. Murthy, Graphene oxide modified CuBTC incorporated PVDF membranes for saltwater desalination via pervaporation, Sep. Purif. Technol., 2022, 290, 120888, DOI:10.1016/j.seppur.2022.120888
.
|
This journal is © the Partner Organisations 2023 |