DOI:
10.1039/C6GC03153F
(Paper)
Green Chem., 2017,
19, 2390-2397
Electrocatalytic upgrading of itaconic acid to methylsuccinic acid using fermentation broth as a substrate solution†
Received
15th November 2016
, Accepted 14th December 2016
First published on 6th January 2017
Abstract
Biomass presents a promising renewable feedstock allowing access to valuable platform chemicals. In particular, biotechnological processes enable a highly selective product formation but are carried out in aqueous electrolyte-containing solutions. Consequently, the separation of usually polar products poses severe challenges on product separation associated with a high energy demand of product purification. A direct further catalytic transformation within fermentation broth reduces the number of unit operations and the need for an energy intensive separation. We herein study the potential of a chemo- and electrochemical reduction of itaconic acid (IA) to methylsuccinic acid (MS) using acidic media or crude fermentation broth as a case study. Despite an efficient chemo-catalytic hydrogenation of neat IA over Ru/C or RANEY® nickel, the presence of various salts as well as glucose prohibits a direct chemo-catalytic valorisation in fermentation broth. In contrast, the electrochemical hydrogenation enabled very benign conditions. The selection of the electrode material proved to be decisive and had, together with the voltage, a strong influence on the conversion and faradaic efficiency of electrolysis facilitating 99% faradaic efficiency. The conversion of IA only slightly declined for an IA fermentation broth instead of neat IA in a diluted sulfuric acid environment reaching 60 versus 64%. Moreover, a full conversion and yield could also be achieved by simple optimizations of the reaction period and the substrate concentration. The electrocatalytic valorisation of a crude biotechnological product stream reduces not only energy demand and unit operations but presents a promising approach to introduce renewable electrical energy in biomass utilization.
Introduction
Since the beginning of the 21st century, the societal need for eco-friendly and renewable energy sources has become increasingly imperative. In this regard, biomass resources have attracted plenty of attention over the last decade as a renewable carbon source for the production of potentially CO2-neutral chemicals and fuels.1–4 Besides building blocks such as levulinic acid and 5-hydroxymethylfurfural, the US Department of Energy (DOE) named itaconic acid (IA) as one of the 12 future major platform molecules derived from biomass feedstocks.5 Since the 1960s the production of IA is in general accomplished by the fermentation of Aspergillus terreus on sugar containing media.6,7 Unsaturated di-carboxylic acid is typically used as a starting material in the manufacturing of polymers,6,7 but it is also considered to be a promising substrate for tailor made fuels, such as 3-methyltetrahydrofuran.8–11 In particular the use of IA as an alternative monomer for the production of poly(methyl methacrylate) is of recent interest and will likely promote the production of IA further.12,13 In addition, studies on the economic potential of IA estimate the projected market for IA to nearly 410
000 MT with a value of 570 million USD in 2020.14 This also shows the strong increase of the market size of IA since the year 2001.6 Methylsuccinic acid (MS) can be obtained from IA via hydrogenation of the double bond.15 The saturated product of IA can e.g. find applications as a substrate for polymerization reactions and as an additive in coating agents.16 The diethylester of methylsuccinic acid on the other hand is considered as a suitable solvent in cosmetics.17 Recently, the Wong Chang group showed that methylsuccinic monoesters have great properties as a substrate for the electrochemical coupling reaction called “Kolbe electrolysis”. The obtained product 2,5-dimethyladipic acid after release of the ester groups might possess very promising characteristics in the polymer industry.18
One of the key steps in the production of biofuels or value-added chemicals from biomass presents a suitable connection between the highly selective biotechnological transformation of biomass, e.g. cellulose, into platform chemicals such as ethanol and lactic acid or IA with subsequent processing.2,19,20 Indeed, fermentation processes delivering high-boiling and polar products in aqueous electrolyte-solutions often cause highly demanding and energy intensive separation processes.21–24 These challenges make a close integration with further transformation attractive avoiding intermediate product separation.25 However, despite promising progress in the design of efficient catalysts for a valorisation of biomass-derived platform chemicals, few examples demonstrate a direct catalytic transformation of crude fermentation broth.
Beside conventional chemo-catalysis, electrocatalysis poses an efficient methodology for the production of bio-derived chemicals.26–35 In this regard, in particular the hydrogenation (or reduction) of levulinic acid into valeric acid and γ-valerolactone reported by Nilges, Xin, Qiu and Dos Santos et al. revealed that electrochemistry represents a feasible tool for the effective and sustainable production of promising chemicals.26,28,31,33 The mentioned reaction was carried out in aqueous acidic solutions and at room temperature, using Pb electrodes for high valeric acid selectivities and glassy carbon electrodes for high γ-valerolactone selectivities.28 Among these electrochemical approaches also the mild electrosynthesis of 2,5-furandicarboxylic acid from HMF has received attention, as it does not require high temperatures and oxygen pressure.29,36 The mild process conditions fulfil the major criteria of green chemistry and open a window of opportunity to integrate renewable electrical energy into biomass valorization.
In the recent past, literature studies described the electrochemical hydrogenation (ECH) of muconic acid to different diacid monomers34 and the reduction of 5-hydroxymethylfurfural to 2,5-bis(hydroxymethyl)furan.32 A recent contribution by Matthiesen et al. also highlights the potential of an electrochemical transformation of biologically produced muconic acid.35 Regarding the electrocatalytic transformation of IA, only a few examples exist. In 1989 Smigielski et al. reported an electrocatalytic conversion of IA (83%) to methylsuccinic acid (MS) at 60 °C under strongly basic conditions using a high excess of RANEY® Ni as a catalyst and an electrode (molar ratio of Ni/IA = 1.4, Fig. 1).37 The second study describes water soluble manganese complexes such as manganese porphyrin as efficient electrocatalysts for the oxidation of different unsaturated dicarboxylic acids. However, these complexes are very pH-dependent and therefore difficult to implement for the often very acidic environments in electrochemical reactions.38
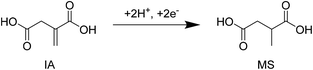 |
| Fig. 1 The proposed ECH of IA to MS. | |
Herein, we present the successful direct transformation of biotechnologically produced IA in an electrochemical process running at ambient pressure and temperature over an inexpensive full metal electrode. Prior to the electrocatalytic conversion of crude biotechnological IA solution the electrode material, which provided the highest MS yield and best faradaic efficiency, was optimized by varying the applied negative potential. This provided valuable insights into achieving high selectivity of the ECH over the competitive hydrogen evolution reaction. With the goal of assessing the impact of ECH, we have also examined the ability of Ru/C and RANEY® nickel catalysts in a conventional hydrogenation reaction (applying H2 pressure and heat) for comparison.
Experimental
Fermentation
Cultivation of Aspergillus terreus DSM 23081 was performed in a minimal medium according to Kuenz et al.39 and Hevekerl et al.40 The medium contained 180 g L−1 glucose, 0.8 g L−1 KH2PO4, 3 g L−1 NH4NO3, 1 g L−1 MgSO4·7H2O, 5 g L−1 CaCl2·2H2O, 0.00167 g L−1 FeCl3·6H2O, 0.008 g L−1 ZnSO4·7H2O and 0.015 g L−1 CuSO4·5H2O. The main substrate glucose was obtained from Carl Roth GmbH & Co. KG (Karlsruhe, Germany) as a monohydrate with a purity of ≥99.5%. The medium was completed from stock solutions, which, except for the CaCl2 and FeCl3 solutions, were adjusted to pH 3.1 with 1 M H2SO4 and were autoclaved separately. Experiments were conducted at 33 °C in unbaffled 250 mL shake flasks with a filling volume of 20 mL and an initial spore concentration of 5 × 106 spores per mL. The flasks were shaken at 300 min−1 with a shaking diameter of 50 mm. After 130 hours of cultivation without interruption of shaking, the culture broth was harvested and fungal biomass was removed via filtration.
Electrocatalysis
All electrochemical reactions were conducted in a custom designed single compartment three-electrode cell under potentiostatic or galvanostatic control using a potentiostat/galvanostat (Autolab PGSTAT 302N). The electrode reactions were undertaken using a three-electrode arrangement. In this regard, EWE stands for potential applied vs. reference electrode, for which Ag/AgCl saturated KCl electrodes (ProSense, 0.195 V vs. standard hydrogen electrode (SHE)) were used throughout the study. All electrode potentials in this study are reported vs. Ag/AgCl sat. KCl, but normalized to SHE for energetic calculations and for better comparability.
A pre-treatment procedure was applied to remove contaminants from the electrode and membrane surfaces. All metal electrodes were treated with sandpaper (400, 1500 and 2500 grits subsequently) and washed with deionized water. Glassy carbon electrodes were first treated with different intense sandpapers (400, 1500 and 2500 grits) and washed with ethanol in an ultrasonic bath. After use, the membranes were stored in a diluted sulfuric acid solution (0.5 mol L−1) and cleaned with deionized water before being used again.
Initial experiments to compare various metal electrodes and measure the impact of different EWE were performed with 16 mL solution of IA (0.208 g, 1.6 mmol or 1.187 g, 9.1 mmol) dissolved in 0.5 M sulfuric acid (16 mL) as an electrolyte. The cell was equipped with a glassy carbon (Hochtemperatur Werkstoffe GmbH) counter electrode and divided via an ion-exchange Nafion membrane (NR-324, Alfa Aesar). Testing of the fermentation broth was conducted with 16 mL IA fermentation broth with IA (1.187 g, 9.1 mmol), glucose (0.375 g, 2.1 mmol) and various minor salt amounts (MgSO4, CaCl2, FeCl3, ZnSO4, CuSO4, KH2PO4 and NH4NO3). The cell was equipped with a glassy carbon counter electrode. All reported current densities are normalized to the geometric surface area of the working electrode (surface = 8 cm2). All reported results were conducted at least 3 times in total. All utilized full-metal working electrodes had technical grade.
Chemocatalytic batch reactions
Heterogeneous catalysts were tested in a 50 mL batch reactor (stainless-steel autoclave) with a glass or Teflon inlet, which contained a stirring bar, temperature controller and pressure controller. The pressure of H2 gas could be controlled by using a barometer. The batch autoclave was charged with water (15 mL or 10 mL) containing IA (1.187 g, 9.1 mmol or 0.791 g, 6.1 mmol) or fermentation broth (15 mL or 10 mL) and Ru/C 0.5 wt% (100 mg) or RANEY® nickel (33.3 mg, 4 wt% of the substrate amount), 10 bar of hydrogen pressure were applied and the mixture was heated to 70 °C for 1 h. The stirring speed of the stirrer was set to 500 rpm. All reported results were averaged over 3 experiments.
Product analysis
1H NMR spectra were recorded at 25 °C on a Bruker Avance 400 MHz spectrometer. The samples were in the case of low concentrations of IA (0.1 mol L−1) dried at 60 °C under vacuum, reconstituted in deuterium oxide (Deutero), and subsequently analysed. In the case of high concentrations of IA and when using fermentation broth, 0.2 mL of the product mixture was diluted in deuterium oxide. Ethanol was in each case used as an internal standard during the quantitative measurements. The spectra of the reactant and product are depicted in the ESI.†
Inductively coupled plasma atomic emission spectroscopy (ICP-AES)
For the determination of the metal amount in the aqueous solutions, the samples were analysed on a spectro-flame D device. The samples were directly injected without any additional treatment.
Results and discussion
Initial screening studies with different metal electrodes
The electrochemical production of MS was up to now only investigated by one group.37 Moreover, since previous studies required additional heating the conditions need further optimization. These findings motivated us to investigate the ECH reaction of IA to MS over different electrodes in more detail. In this regard, the metals Cu, Ni, Fe, Pb and Cu–Pb (plastic bronze) have been investigated for electrochemical activity using a fixed voltage (Fig. 2).
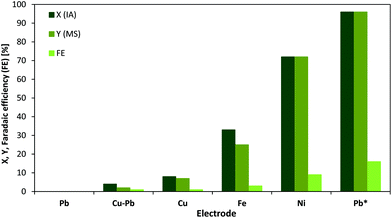 |
| Fig. 2 Screening of various metal electrodes in the ECH of IA to MS. Conditions: r.t., 1 h, counter electrode: glassy carbon, E = −1.06 V vs. standard-hydrogen-electrode (SHE), water (16 mL), H2SO4 (0.5 mol L−1), IA (0.1 mol L−1, 1.6 mmol, 0.208 g). *E = −1.41 V vs. SHE (X denotes conversion, Y means yield). | |
The ECH of IA was studied in an aqueous acidic solution (0.5 mol L−1 H2SO4). For all experiments, a potential of −1.06 V vs. SHE has been applied for a 1 h reaction period. Cu and Cu–Pb electrodes showed only a very low electrochemical performance for the hydrogenation reaction at this voltage, whereas for Pb the voltage was not high enough to achieve a current flow. The highest catalytic activity as well as faradaic efficiency was observed for Ni, while Fe still revealed a notable yield and conversion. Interestingly, when switching the applied potential from −1.06 V to −1.41 V vs. SHE Pb electrodes meet the required overpotential for hydrogenation and start to clearly stand out over the other tested electrodes in terms of substrate conversion (96%), yield of MS (96%) and faradaic efficiency (16%, calculation described in the ESI†). The obtained current value at −1.41 V is comparable to the values observed when using other electrodes at lower potentials (see cyclic voltammograms in the ESI†). As it was already stated by dos Santos et al.,28 the higher performance of Pb for ECH reactions can be often explained by the higher overpotential of water electrolysis.41 Hydrogen evolution at Cu-, Fe- and Ni-cathodes start already before −1.0 V vs. SHE in acidic media.41,42
In summary, MS can be obtained from IA using acidic aqueous solutions and Pb-cathodes with excellent selectivity and yields, while the faradaic efficiency needs to be optimized. However, the faradaic efficiency is very dependent on the initial substrate concentration and therefore, can be increased using higher substrate concentrations.
Kinetic potential dependent experiments with Pb-cathodes
Considering the results from the section before, another set of experiments was conducted in order to reveal the impact of different applied potentials on conversion, and the change of the faradaic efficiency over a 1 h reaction time in comparison with the studied electrode potentials (Fig. 3).
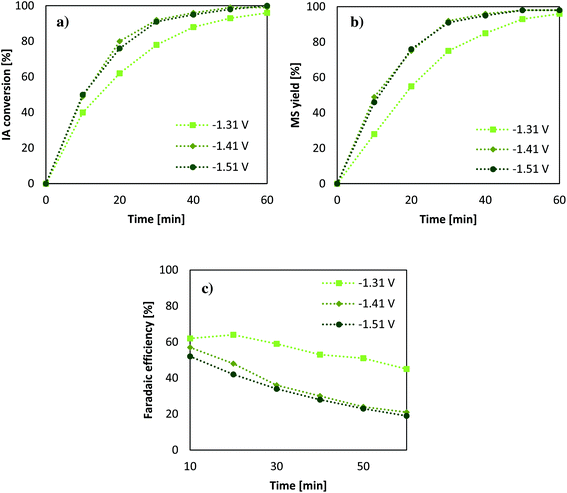 |
| Fig. 3 The effect of the applied potential on the conversion, yield and faradaic efficiency: (a) IA conversion, (b) yield of MS, and (c) faradaic efficiency. Conditions: r.t., working electrode: Pb, counter electrode: glassy carbon, water (16 mL), H2SO4 (0.5 mol L−1), IA (0.1 mol L−1, 1.6 mmol, 0.208 g). The dashed lines are added as guide to the eye. | |
Since Pb-cathodes showed the highest reaction rates and best faradaic efficiencies, they were utilised for further experiments. The effect of the voltage ranging from −1.31 to −1.51 V vs. SHE shows that the time for reduction decreases for higher voltages. However, when reaching −1.41 V vs. SHE the effect becomes negligible, which can likely be attributed to mass transfer limitations during the process. As mentioned in the literature applying a potential to a certain electrode, it is found that, upon increasing the applied voltage the current value at first increases until it reaches a saturation level, called a current plateau. It then requires clearly higher potentials to achieve higher current growth again. When this limiting is encountered, it is in most cases caused by the slowness of transport of charged or uncharged species through the solution.43 Using a stirrer or a rotational disk electrode can shift the limitation to a higher value emphasising the high impact of reactor design in such a transformation. Another important factor relates to an electrode material with a higher specific surface area; however, also there mass transfer limitations will be encountered at a certain potential.43 According to the obtained results, the highest faradaic efficiency of 62% is achieved after 10 min when applying lower potentials. The difference in higher potentials rises when it comes to longer reaction periods; however, this behaviour is probably intensified due to low IA amounts in solution after 50% conversion. This suggestion implies a better faradaic efficiency for all potentials when using higher substrate solutions and that low efficiencies are also connected to lower concentrations of IA in solution. On this account, it is expected that the faradaic efficiency can be clearly increased when using higher initial substrate concentrations or when performing the ECH of IA in a continuous setup. Nevertheless, a very mild process for the production of MS from IA has been elaborated, which does not require the addition of thermal heat as it was necessary in a previous study of Smigielski et al.37 For this reason, and especially with regard to the rules of green chemistry, the ECH of IA when using Pb-cathodes and an acidic aqueous solution presents a very sustainable system and promising setup for continuing investigations.
Comparison study of neat IA solutions and IA fermentation broth
The ECH of IA to MS was carried out in a custom designed electrolysis cell consisting of two half-cells, which were separated through an ion permeable membrane (Nafion). The only additive was H2SO4 (0.5 mol L−1) when using neat IA solution as a substrate solution. However, using almost pure IA solution requires the purification of the previous downstream extract meaning the fermented sugar containing media with significant amounts of several salts and still notable quantities of glucose. The regeneration of fermentation broth presents an additional cost factor and of course, it is economically favoured to reduce the overall amount of unit operations in a process. In this context, a comparison of the transformation of a neat IA solution and an IA fermentation broth has been conducted utilising chronopotentiometry in order to keep the current flow (0.3 A) constant and achieve better comparability.
Fig. 4 presents the conversion, yield and faradaic efficiency for neat IA solution and fermentation broth after 1 h. Noteworthily, the IA concentration in the fermentation broth is almost 6-fold higher compared to the previously shown results with neat IA solution. Therefore, concentrations for neat IA solution were adjusted to 0.57 mol L−1 to preserve comparability. Despite a 6-fold higher IA concentration, 64% conversion and 63% yield could be achieved after a 1 h reaction time. Applying the same conditions to the fermentation broth as to the neat IA solution, we could confirm that IA conversion (60%) and MS (60%) yield are only slightly lower, despite the presence of high glucose amounts and several salts (MgSO4, CaCl2, FeCl3, ZnSO4, CuSO4, KH2PO4 and NH4NO3) in the substrate solution.
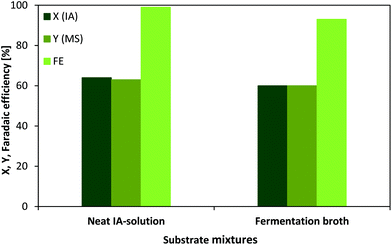 |
| Fig. 4 Comparison of neat IA-solution with fermentation broth using Pb as WE. Conditions: r.t., 1 h, counter electrode: glassy carbon, I = 0.3 A, neat IA-solution: water (16 mL), H2SO4 (0.5 mol L−1), IA (0.57 mol L−1, 9.1 mmol, 1.187 g). | |
Although, the applied potential has to be increased (approximately −1.4 to −4.4 V vs. SHE) as the resistance of the mixture is higher when using fermentation broth, this problem is easily solved when mixing the broth with a diluted sulfuric acid solution (0.5 mol L−1). According to the obtained faradaic efficiencies for both substrate mixtures, there is a slightly lower efficiency (93%) for the fermentation broth in comparison with pure IA solution (99%). The main reason for this quantity distinction might be explained by the fact that the broth still contains remarkable amounts of sugar (0.13 mol L−1) which can undergo side reactions, for example the already well known reduction of glucose into sorbitol.44 Nevertheless, the discussed differences are very small and therefore it could be proven that fermentation broth represents a very promising alternative substrate solution for a direct electrochemical further transformation.
Comparison of thermal batch reactions to ECH
In addition to the electrochemical conversion of IA, we have focused on the conventional reaction path to the target product MS, since it is usually produced by applying heat, hydrogen pressure and using a noble metal catalyst. In this regard, the mild conditions could be a major challenge considering the maximum product yield. In this work, electrochemistry has proven to be a worthwhile method for the mild and fast production of MS using only lead cathodes and no additional heat. Interestingly, it was observed that a chemo-catalytic hydrogenation of pure IA over a supported ruthenium catalyst (Ru/C) required at least 70 °C and 10 bar of hydrogen for a yield of 75%.
In order to determine the Ru/C stability in pure IA solution and fermentation broth recycling tests were conducted (Fig. 5). Between the cycles the catalyst was washed with distilled water and methanol and dried at 60 °C under vacuum. Ru/C shows excellent recyclability with only slight loss of yield and conversion under these conditions and using neat substrate solution. However, only 3% conversion and 1% yield were achieved after the first experiment when applying this catalyst to fermentation broth. These findings imply that because of high amounts of glucose, which might plug the Ru/C pores, the catalyst deactivates fast. In addition, the various salts could inhibit the performance. In order to ensure that the low activity was not only related to the properties of the Ru/C catalyst, additional tests were conducted with a conventional hydrogenation catalyst.45 RANEY® nickel (4 wt% of the substrate amount) showed similar activity compared to Ru/C in neat IA solution (43% conversion, 41% yield) and was even more active in a first run with fermentation broth (30% conversion, 30% yield) compared to Ru/C. However, upon recycling the Ni catalyst became completely inactive. This can be assigned most likely to notable leaching of the active species into the solution, which led to a green solution after the reaction. ICP-AES confirmed 0.545 mg g−1 Ni corresponding to almost 39% of the initial amount of the catalyst. It is clear that although a neat IA solution as a substrate might provide similar results in comparison with the mild electrochemical conversion it cannot be easily applied to the downstream mixture from the fermentation. In contrast, the utilized Pb electrode for the ECH was not changed throughout the whole study and we did not observe any destruction. This was additionally confirmed by the results obtained from ICP-AES showing only a very low Pb amount (0.00363 mg g−1 Pb, which relates to 0.1% of the Pb electrode). On this account, the electrode is considered as long term stable.
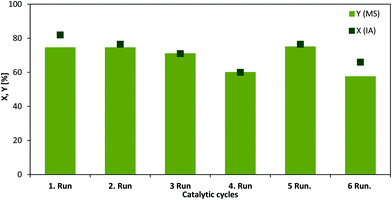 |
| Fig. 5 Chemo-catalytic batch hydrogenation of IA over a Ru/C catalyst including recycling: 100 mg Ru/C in pure IA solution (0.61 mol L−1, 9.1 mmol, 1.187 g). Reaction conditions: 1 h, 70 °C, 10 bar of H2, 15 mL water, 500 rpm stirring speed. | |
Conclusions
The direct electrocatalytic valorisation of platform chemicals without prior separation from crude fermentation broth presents a valuable approach to minimize the number of required unit operations and energy demand. Focusing on the reduction of itaconic acid (IA) as a case study, an efficient chemo-catalytic hydrogenation of neat IA over Ru/C or RANEY® nickel required at least 70 °C and 10 bar of hydrogen pressure facilitating 75% yield of methylsuccinic acid (MS). However, the presence of various salts as well as glucose prohibited a chemo-catalytic valorisation of an IA fermentation broth. In the case of RANEY® nickel a distinct catalyst leaching occurred. In contrast, we were able to transform IA into methylsuccinic acid (MS) over various electrodes at ambient temperature and pressure. Pb and Ni facilitated the highest activity in a separated single electrolysis cell. Pb showed under slightly different conditions the highest activity with a maximum yield of MS of 98% at room temperature, −1.41 V vs. SHE in an aqueous, acidic medium. The applied voltage has a distinct impact on the conversion and faradaic efficiency with an increasing faradaic efficiency at lower potentials but increasing conversion for higher potentials further rising until mass transfer limitation becomes rate limiting. Interestingly, the conversion of IA only slightly declined for an IA fermentation broth instead of neat IA in a diluted sulfuric acid environment confirming the potential of this strategy. Future studies will elaborate on further transformations and substrates. Overall, the electrocatalytic valorisation of a crude biotechnological product stream reduces not only energy demand and unit operations but presents a promising approach to introduce renewable electrical energy in biomass utilization.
Funding sources
Cluster of Excellence: DFG-EXC 236.
Acknowledgements
We acknowledge financial support by the Cluster of Excellence “Tailor-Made Fuels from Biomass” (TMFB) funded by the Excellence Initiative of the German federal and state governments to promote science and research at German universities.
References
- J. Zakzeski, P. C. A. Bruijnincx, A. L. Jongerius and B. M. Weckhuysen, The Catalytic Valorization of Lignin for the Production of Renewable Chemicals, Chem. Rev., 2010, 110(6), 3552–3599 CrossRef CAS PubMed.
- A. M. Ruppert, K. Weinberg and R. Palkovits, Hydrogenolysis Goes Bio: From Carbohydrates and Sugar Alcohols to Platform Chemicals, Angew. Chem., Int. Ed., 2012, 51(11), 2564–2601 CrossRef CAS PubMed.
- R. Luque, L. Herrero-Davila, J. M. Campelo, J. H. Clark, J. M. Hidalgo, D. Luna, J. M. Marinas and A. A. Romero, Biofuels: a technological perspective, Energy Environ. Sci., 2008, 1(5), 542–564 CAS.
- J. C. Serrano-Ruiz and J. A. Dumesic, Catalytic routes for the conversion of biomass into liquid hydrocarbon transportation fuels, Energy Environ. Sci., 2011, 4(1), 83–99 CAS.
-
T. Werpy and G. Petersen, Results of Screening for Potential Candidates from Sugars and Synthesis Gas, in Top Value Added Chemicals from Biomass, 2004, vol. I, p. 76 Search PubMed.
- T. Willke and K.-D. Vorlop, Biotechnological production of itaconic acid, Appl. Microbiol. Biotechnol., 2001, 56(3), 289–295 CrossRef CAS PubMed.
- M. Okabe, D. Lies, S. Kanamasa and E. Y. Park, Biotechnological production of itaconic acid and its biosynthesis in Aspergillus terreus, Appl. Microbiol. Biotechnol., 2009, 84(4), 597–606 CrossRef CAS PubMed.
- F. M. A. Geilen, B. Engendahl, A. Harwardt, W. Marquardt, J. Klankermayer and W. Leitner, Selective and Flexible Transformation of Biomass-Derived Platform Chemicals by a Multifunctional Catalytic System, Angew. Chem., 2010, 122(32), 5642–5646 CrossRef.
- M. Besson, P. Gallezot and C. Pinel, Conversion of Biomass into Chemicals over Metal Catalysts, Chem. Rev., 2014, 114(3), 1827–1870 CrossRef CAS PubMed.
- A. Voll and W. Marquardt, Reaction network flux analysis: Optimization-based evaluation of reaction pathways for biorenewables processing, AICHE J., 2012, 58(6), 1788–1801 CrossRef CAS.
- T. Klement and J. Büchs, Itaconic acid A biotechnological process in change, Bioresour. Technol., 2013, 135, 422–431 CrossRef CAS PubMed.
-
I. Global Market Insights, Itaconic Acid Market size to exceed $290 mn by 2024, Global Market Insights, 2016 Search PubMed.
-
I. Global Market Insights, Itaconic Acid Market Size By Application, Global Market Insights, 2016 Search PubMed.
-
S. R. O. Weastra, WP, 8.1. Determination of market potential for selected platform chemicals Itaconic acid, Succinic acid, 2,5-Furandicarboxylic acid, 2012.
- R. Luque and J. H. Clark, Water-tolerant Ru-Starbon® materials for the hydrogenation of organic acids in aqueous ethanol, Catal. Commun., 2010, 11(10), 928–931 CrossRef CAS.
-
S. Garnier, J. Heimann, D. Mijolovic and Z. J. Szarka, Powder coating useful as a coating agent, and for coating metallic- and non-metallic surfaces, comprises a binder comprising methyl succinic acid, DE102011080722A1, 2012 Search PubMed.
-
H. Richard and B. Muller, Use of a 2-methylsuccinic acid diester derivative as solvent in cosmetic compositions; cosmetic compositions containing the same, WO2012119861A2, 2012 Search PubMed.
- L. Wu, M. Mascal, T. Farmer, P. S. Cheau Arnaud and M. A. Wong Chang, 2,7-Octanedione and 2,5-Dimethyladipic Acid From the Electrochemical Coupling of Biomass-derived Carboxylic Acids: C8 Platforms for Renewable Polymers and Fuels, ChemSusChem, 2016 DOI:10.1002/cssc.201601271.
- G. Brodeur, E. Yau, K. Badal, J. Collier, K. B. Ramachandran and S. Ramakrishnan, Chemical and Physicochemical Pretreatment of Lignocellulosic Biomass: A Review, Enzyme Res., 2011, 2011, 17 Search PubMed.
-
V. Strezov and T. J. Evans, Biomass processing technologies, CRC Press, 2014 Search PubMed.
- K. Schute, C. Detoni, A. Kann, O. Jung, R. Palkovits and M. Rose, Separation in Biorefineries by Liquid Phase Adsorption: Itaconic Acid as Case Study, ACS Sustainable
Chem. Eng., 2016, 4(11), 5921–5928 CAS.
- A. A. Kiss, J.-P. Lange, B. Schuur, D. W. F. Brilman, A. G. J. van der Ham and S. R. A. Kersten, Separation technology–Making a difference in biorefineries, Biomass Bioenergy, 2016, 95, 296–309 CrossRef CAS.
- H.-J. Huang, S. Ramaswamy, U. W. Tschirner and B. V. Ramarao, A review of separation technologies in current and future biorefineries, Sep. Purif. Technol., 2008, 62(1), 1–21 CrossRef CAS.
- C. J. Davey, D. Leak and D. A. Patterson, Hybrid and mixed matrix membranes for separations from fermentations, Membranes, 2016, 6(1), 17 CrossRef PubMed.
- I. Delidovich, K. Leonhard and R. Palkovits, Cellulose and hemicellulose valorisation: an integrated challenge of catalysis and reaction engineering, Energy Environ. Sci., 2014, 7(9), 2803–2830 CAS.
- P. Nilges, T. R. dos Santos, F. Harnisch and U. Schröder, Electrochemistry for biofuel generation: Electrochemical conversion of levulinic acid to octane, Energy Environ. Sci., 2012, 5(1), 5231–5235 CAS.
- P. Nilges and U. Schröder, Electrochemistry for biofuel generation: production of furans by electrocatalytic hydrogenation of furfurals, Energy Environ. Sci., 2013, 6(10), 2925–2931 CAS.
- T. R. dos Santos, P. Nilges, W. Sauter, F. Harnisch and U. Schröder, Electrochemistry for the generation of renewable chemicals: electrochemical conversion of levulinic acid, RSC Adv., 2015, 5(34), 26634–26643 RSC.
- D. J. Chadderdon, L. Xin, J. Qi, Y. Qiu, P. Krishna, K. L. More and W. Li, Electrocatalytic oxidation of 5-hydroxymethylfurfural to 2,5-furandicarboxylic acid on supported Au and Pd bimetallic nanoparticles, Green Chem., 2014, 16(8), 3778–3786 RSC.
- S. K. Green, J. Lee, H. J. Kim, G. A. Tompsett, W. B. Kim and G. W. Huber, The electrocatalytic hydrogenation of furanic compounds in a continuous electrocatalytic membrane reactor, Green Chem., 2013, 15(7), 1869–1879 RSC.
- Y. Qiu, L. Xin, D. J. Chadderdon, J. Qi, C. Liang and W. Li, Integrated electrocatalytic processing of levulinic acid and formic acid to produce biofuel intermediate valeric acid, Green Chem., 2014, 16(3), 1305–1315 RSC.
- J. J. Roylance, T. W. Kim and K.-S. Choi, Efficient and Selective Electrochemical and Photoelectrochemical Reduction of 5-Hydroxymethylfurfural to 2,5-Bis(hydroxymethyl)furan using Water as the Hydrogen Source, ACS Catal., 2016, 6(3), 1840–1847 CrossRef CAS.
- L. Xin, Z. Zhang, J. Qi, D. J. Chadderdon, Y. Qiu, K. M. Warsko and W. Li, Electricity Storage in Biofuels: Selective Electrocatalytic Reduction of Levulinic Acid to Valeric Acid or γ-Valerolactone, ChemSusChem, 2013, 6(4), 674–686 CrossRef CAS PubMed.
- J. E. Matthiesen, J. M. Carraher, M. Vasiliu, D. A. Dixon and J.-P. Tessonnier, Electrochemical Conversion of Muconic Acid to Biobased Diacid Monomers, ACS Sustainable Chem. Eng., 2016, 4(6), 3575–3585 CrossRef CAS.
- J. E. Matthiesen, M. Suástegui, Y. Wu, M. Viswanathan, Y. Qu, M. Cao, N. Rodriguez-Quiroz, A. Okerlund, G. Kraus, D. R. Raman, Z. Shao and J.-P. Tessonnier, Electrochemical Conversion of Biologically Produced Muconic Acid: Key Considerations for Scale-Up and Corresponding Technoeconomic Analysis, ACS Sustainable Chem. Eng., 2016, 4(12), 7098–7109 CrossRef CAS.
- K. R. Vuyyuru and P. Strasser, Oxidation of biomass derived 5-hydroxymethylfurfural using heterogeneous and electrochemical catalysis, Catal. Today, 2012, 195(1), 144–154 CrossRef CAS.
- K. Smigielski, J. Gora, J. Kula, G. Mlynarczyk and D. Choma, Electrocatalytic reduction of itaconic acid to methylsuccinic acid, Chem. Stosow., 1989, 33, 107–111 CAS.
- M.-H. Liu and Y. O. Su, Selective electrocatalysis of olefins by a water-soluble manganese porphyrin in acidic solution, J. Chem. Soc., Chem. Commun., 1994,(8), 971–972 RSC.
- A. Kuenz, Y. Gallenmüller, T. Willke and K.-D. Vorlop, Microbial production of itaconic acid: developing a stable platform for high product concentrations, Appl. Microbiol. Biotechnol., 2012, 96(5), 1209–1216 CrossRef CAS PubMed.
- A. Hevekerl, A. Kuenz and K.-D. Vorlop, Filamentous fungi in microtiter plates—an easy way to optimize itaconic acid production with Aspergillus terreus, Appl. Microbiol. Biotechnol., 2014, 98(16), 6983–6989 CrossRef CAS PubMed.
- J. O. M. Bockris, Electrolytic polarisation-I. The overpotential of hydrogen on some less common metals at high current densities. Influence of current density and time, Trans. Faraday Soc., 1947, 43(0), 417–429 RSC.
- H. Ezaki, M. Morinaga and S. Watanabe, Hydrogen overpotential for transition metals and alloys, and its interpretation using an electronic model, Electrochim. Acta, 1993, 38(4), 557–564 CrossRef CAS.
-
J. R. Selman and C. W. Tobias, Mass-Transfer Measurements by the Limiting-Current Technique, in Advances in Chemical Engineering, ed. T. B. Drew, G. R. Cokelet, J. W. Hoopes and T. Vermeulen, Academic Press, 1978, vol. 10, pp. 211–318 Search PubMed.
- P. N. Pintauro, D. K. Johnson, K. Park, M. M. Baizer and K. Nobe, The paired electrochemical synthesis of sorbitol and gluconic acid in undivided flow cells. I, J. Appl. Electrochem., 1984, 14(2), 209–220 CrossRef CAS.
-
A. Bavley and C. J. Knuth, Preparation of methylsuccinic acid and metal salts thereof, US2773897A, 1956 Search PubMed.
Footnote |
† Electronic supplementary information (ESI) available: Calculations, NMR spectra and cyclic voltammograms of the different electrode materials. See DOI: 10.1039/c6gc03153f |
|
This journal is © The Royal Society of Chemistry 2017 |
Click here to see how this site uses Cookies. View our privacy policy here.