DOI:
10.1039/C5QI00194C
(Research Article)
Inorg. Chem. Front., 2016,
3, 111-116
A surfactant-thermal method to prepare crystalline thioantimonate for high-performance lithium-ion batteries†
Received
8th October 2015
, Accepted 2nd November 2015
First published on 3rd November 2015
Abstract
Rechargeable lithium-ion batteries (LIBs) have attracted great attention in various applications. However, high energy density is still a challenge for next-generation lithium ion batteries. Therefore, searching for novel electrode materials to address this issue is highly desirable. In this report, we employed a surfactant-thermal method to prepare a novel 1D crystalline thioantimonate [NH(CH3)2][Sb4S5(S3)]. After grinding for 10 min using a mortar, [NH(CH3)2][Sb4S5(S3)] presented an ultrathin nanosheet morphology (around 20 nm in thickness and several micrometers in lateral dimension). Employed as an anode material for lithium ion batteries, the nano-sized crystalline thioantimonate shows a high reversible specific capacity of 568 mA h g−1 over 50 cycles at a current density of 0.1 A g−1 and an excellent rate capability of 301 mA h g−1 at a current density of 5 A g−1. Our research suggests that crystalline thioantimonate could have great potential applications in high performance Li-ion batteries.
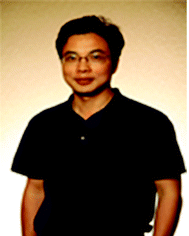 Qichun Zhang | Dr Qichun Zhang obtained his B.S. at Nanjing University in China in 1992, MS in physical organic chemistry (organic solid lab) at the Institute of Chemistry, Chinese Academy of Sciences (Prof. Peiji Wu/Daoben Zhu's group, ICCAS, Beijing) in 1998, MS in organic chemistry (Prof. Fred Wudl's group) at the University of California, Los Angeles (USA), and completed his Ph.D. in inorganic chemistry at the University of California Riverside (Prof. Pingyun Feng's group, USA) in 2007. Then, he joined Prof. Kanatzidis’ group at Northwestern University as a Postdoctoral Fellow (Oct. 2007–Dec. 2008). Since Jan. 2009, he joined the School of Materials Science and Engineering at Nanyang Technological University (NTU, Singapore) as an Assistant Professor. On Mar. 1st, 2014, he was promoted as an Associate Professor with tenure and on Dec. 1st, 2014, he became an adjunct Associate Professor at the Division of Chemistry and Biological Chemistry, School of Physical and Mathematical Sciences, Nanyang Technological University. Besides these, he also has three-year working experience in the Research Institute of Nanjing Chemical Industry Co. (Aug. 1992–Aug. 1995) and two-year research experience in ICCAS (Aug. 1998–Jun. 2000). He received TCT fellowship in 2013 and lectureship from National Taiwan University in 2014. Currently, he is an associate editor of J. Solid State Chem. He has published >190 papers and 4 patents (H-index: 37). |
Introduction
Lithium ion batteries (LIBs) have been dominating the energy market for more than 20 years. However, it still cannot meet the increasing technical demands from portable electronics, hybrid electric vehicles and electric vehicles.1,2 To achieve high performance LIBs with low cost, high energy density and long cycling performance, intensive research efforts have been made to develop novel anode materials for LIBs.3–5 Recently, various transition metal oxides have been investigated as potential alternatives to commercial graphite (372 mA h g−1) for LIBs due to their high theoretical capacity.6–8 However, the low electrical conductivity is a bottleneck for further improvement,9–11 which leads to an inferior rate capability.
Alternatively, metal sulfides have attracted much attention as anode materials for LIBs due to their metallic character, rich redox chemistry and good thermal stability.12–14 Among such materials, alloy-based SbSx have been studied as promising anode materials for LIBs,15–18 because they can undergo both the conversion reaction between Li and SbSx and the alloying reaction between Sb and Li, which can result in high charge and discharge capacities. However, large volume expansion often occurs during the lithiation/delithiation process, which leads to the fracture of the as-fabricated structures and the contact loss with the current collector. Therefore, how to minimize the volume change as well as the enhancement of the cycling performance during the lithiation/delithiation process becomes the current main focus.19,20
Recently, materials with an ultrathin 2D morphology are of great interest for lithium ion battery applications21–23 since their ultrathin thickness provides much shorter paths for fast lithium ion diffusion and their large surface area offers increased active sites. Thus, a novel crystalline thioantimonate with an ultrathin 2D morphology might be a promising candidate for high-performance Li-ion batteries. In this article, we successfully synthesized a new crystalline thioantimonate [NH(CH3)2][Sb4S5(S3)]. After grinding for 10 min and mixed with carbon black and binder, the as-obtained [NH(CH3)2][Sb4S5(S3)] shows excellent performance in LIBs as an anode material. Specifically, it delivers a high specific capacity of 568 mA h g−1 over 50 cycles at a current density of 0.1 A g−1 and a very good rate capability of 301 mA h g−1 at a current density of 5 A g−1.
Experimental section
All chemicals in this study were commercially available and used without further purification. The scanning electron microscopy (SEM) and elemental analyses of Sb and S were performed on an EDX-equipped JEOL/JSM-6360A SEM. The transmission electron microscopy (TEM) images were taken with a JEOL 2100F at 200 kV. Atomic force microscopy (AFM) (Digital Instruments) was used to determine the thickness of the nanosheets. Powder X-ray diffraction data were recorded on a Bruker D8 Advance diffractometer with a graphite-monochromatized Cu Kα radiation. The data were collected with 2θ in a range of 5°–65°. The solid-state UV-Vis diffuse-reflectance spectrum was recorded at room temperature on powder samples with a Model UV-2501 PC. A BaSO4 plate was used as a standard (100% reflectance). The absorption data were calculated from the reflectance spectrum using the Kubelka–Munk function: α/S = (1 − R)2/2R, where α is the absorption coefficient, S is the scattering coefficient and R is the reflectance. The thermal stability study was carried out on a TGA Q500 instrument under flowing N2 with a heating rate of 10 °C min−1 up to 400 °C.
Synthesis of [NH(CH3)2][Sb4S5(S3)] (1)
A mixture of Sb2S3 powder (0.40 mmol, 136 mg), S (3.00 mmol, 96 mg), N,N-dimethylformamide (DMF, HPLC grade, 2.0 ml), hydrazine monohydrate (98%, 0.5 ml) and octylamine (99%, 1.5 ml) was sealed into an autoclave equipped with a Teflon liner (20 ml) and heated at 160 °C for 6 days. After cooling to room temperature, the mixture was washed with ethanol and red plate crystals of 1 were obtained by filtration and the pure phase was selected by hand (yield: 72% based on Sb).
Single crystal X-ray crystallography
Single crystal X-ray diffraction data collection was performed on a SuperNova CCD diffractometer with a graphite-monochromatized Mo-Kα radiation source (λ = 0.71073 Å) at room temperature. The structure was solved by direct methods and refined by full-matrix least-squares cycles in SHELX-97.24 The relevant crystallographic data and structure refinement details are listed in Table S1.† CCDC number: 1430117.
Electrochemical measurements
The as-prepared products [NH(CH3)2][Sb4S5(S3)] were ground for about 10 min before use. The working electrode was prepared by mixing compound 1 with carbon black and polyvinylidene fluoride (PVdF) as the binder in a weight ratio of 7
:
2
:
1 in the N-methylpyrrolidone (NMP) solvent. The slurry was coated on a copper foil and dried in a vacuum oven at 60 °C overnight. The electrochemical measurements were carried out using two-electrode coin cells (X2 Labwares, Singapore) with pure lithium foil as both the counter and reference electrodes at room temperature. A Celgard 2400 membrane was used as the separator, and the electrolyte was 1 M LiPF6 in ethylene carbonate (EC)/diethyl carbonate (DEC) (1
:
1 in volume). Cell assembly was carried out in an Ar-filled glovebox with the concentrations of both moisture and oxygen below 1.0 ppm. The mass loading for each battery is about 0.8 mg cm−2.
Results and discussion
Although there are several methods such as high-temperature solid-state reaction, solvo(hydro)-thermal method, or low-temperature diffusion (or evolution) to prepare crystalline chalcogenides, the surfactant-thermal process is more promising.25–33 In this research, red plate crystals of compound 1 were surfactant-thermally prepared by the reaction of Sb2S3, S, N,N-dimethylformamide and hydrazine monohydrate in the surfactant media (octylamine). Parallel experiments indicated that the presence of octylamine was crucial for the successful preparation of compound 1. It is noteworthy that no crystals were observed if octylamine was replaced with sodium dodecyl sulfate (SDS) or nonanoic acid. Only small crystallites with poor quality were obtained when octylamine was removed or replaced with PEG-400 and suberic acid. The purity and stability of 1 have been examined by PXRD (Fig. 1a) and TGA, which is provided in the ESI.†
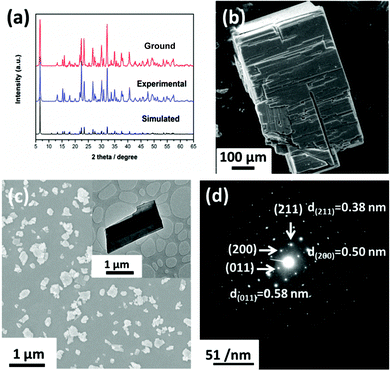 |
| Fig. 1 Characterization of compound 1. (a) XRD pattern; (b) SEM image of the as-obtained crystalline product; (c) SEM image of the grinding product (the inset is a typical TEM image); (d) SAED pattern. | |
The morphologies of the as-ground compound 1 were studied by scanning electron microscopy (SEM) and transmission electron microscopy (TEM), respectively. The SEM image (Fig. 1b) of 1 shows the original morphology of the as-obtained crystalline product. After grinding the as-obtained samples for about ten minutes, the products are mainly present in the 2D morphology, as shown in Fig. 1c. The TEM image (the inset of Fig. 1c) shows a typical piece of nanosheet obtained after grinding. The selected-area electron diffraction (SAED) pattern (Fig. 1d) reveals a high degree of crystallinity of the product. The marked pattern can be attributed to the planes of (200), (011) and (211), respectively. To further confirm the thickness of the nanosheets, atomic force microscopy (AFM) measurements were also conducted, as shown in Fig. 2a. Cross-sectional profiling (Fig. 2b) shows that the thickness of one typical nanosheet is about 20 nm, which indicates the ultrathin property of compound 1.
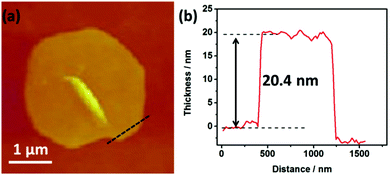 |
| Fig. 2 (a) AFM scans of [NH(CH3)2][Sb4S5(S3)] nanosheets; (b) the corresponding cross-sectional thickness. | |
Structure of [NH(CH3)2][Sb4S5(S3)]
Single crystal X-ray diffraction (XRD) analysis reveals that compound 1 belongs to the orthorhombic space group Ama2. Structural analysis indicates that compound 1 is constructed by 1-D [Sb4S5(S3)] neutral ribbons and dimethylamine molecules. The asymmetric unit (Fig. 3a) consists of one and two halves of Sb3+ ions, two and four halves of S2− ions and a half dimethylamine molecule, respectively. In the inorganic [Sb4S5(S3)] chain of 1, all the crystallographically independent Sb atoms (Sb1, Sb2 and Sb3) are coordinated to three S atoms to form [SbIIIS3]3− trigonal-pyramidal geometries with Sb–S distances ranging from 2.391(7) to 2.487(5) Å, which is similar to the previously reported values in thioantimonate compounds.29,33–36 Two Sb1 and one Sb2 connect to each other via corner-sharing S1 and S2 atoms to construct a six-membered [Sb3S3] ring while Sb3 and S3 that is composed of two S5 and one S4 form a four-membered [Sb(S3)] ring. The bond length of S4–S5 is 2.418(7) Å that is a little longer than the reported values.37,38 Both kinds of rings [Sb3S3] and [Sb(S3)], as shown in Fig. 3b, are alternatingly arranged through the connection of Sb1–S5 to form an infinite [Sb4S5(S3)]n chain along the a-axis (Fig. 3c). The dimethylamine molecules are located in the inter-chain spaces and form N–H⋯S and C–H⋯S hydrogen bonds with the S atoms to result in a pseudo-2D network (Fig. S1†).
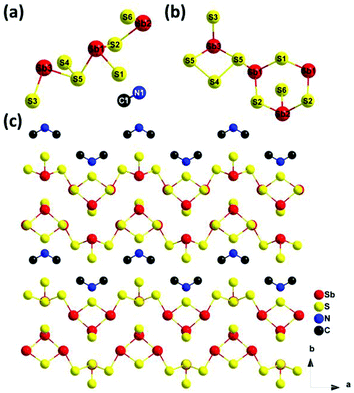 |
| Fig. 3 (a) Asymmetric unit of compound 1; (b) alternatingly arranged two rings, [Sb3S3] and [Sb(S3)]; (c) view of the infinite [Sb4S5(S3)]n chains and dimethylamine molecules along the a-axis. | |
Electrochemical lithium storage
The electrochemical performance of compound 1 was evaluated with 20% carbon black and 10% PVdF as the binder in the EC/EDC electrolyte. To investigate the redox behavior of compound 1, the cyclic voltammetry (CV) measurement was carried out in the voltage window of 0.01–3.0 V at a scan rate of 0.1 mV s−1 at room temperature. As shown in Fig. 4a, during the first cathodic scan, three main peaks centered at 1.7 V, 1.3 V and 0.75 V appear. The two peaks at around 1.7 V and 1.3 V are related to the conversion reaction of [NH(CH3)2][Sb4S5(S3)] to Sb and Li2S. The lower peak at 0.75 V is due to the alloying between Sb and Li. For the first anodic scan, two peaks at 1.1 V and 1.8 V are observed, which correspond to the delithiation process of LixSb and the continuous oxidation of Sb, respectively. It is similar to the previously reported results, indicating that the mechanism for the redox reaction process of 1 is similar to the reported ones.15,16,19 During subsequent cycles, the shape of CV curves can almost be retained, indicating the good stability of the electrochemical process. The constant current charge–discharge profiles of 1st, 2nd and 3rd cycles are shown in Fig. 4b. As can be seen, the initial discharge capacity of 1385 mA h g−1 and a charge capacity of 813 mA h g−1 can be obtained, indicating a large reversible capacity. Furthermore, the potential plateaus are in good agreement with the redox peaks in the CV curves. For the following 2nd and 3rd charge and discharge curves, they almost overlapped, which also demonstrates the good stability of compound 1 as the anode materials of LIBs.
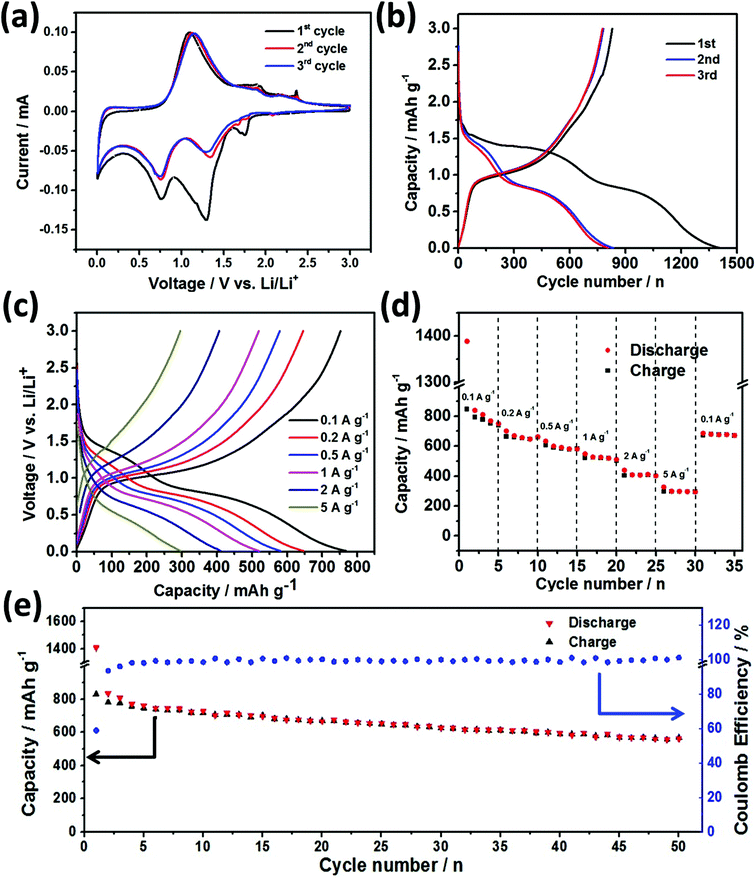 |
| Fig. 4 Electrochemical characterization of the [NH(CH3)2][Sb4S5(S3)] anode. (a) Cyclic voltammograms between 0.01 and 3.0 V measured at a scan rate of 0.1 mV s−1; (b) the charge and discharge curves at a current density of 0.1 A g−1; (c) the charge–discharge curves at different current densities; (d) rate performance at different rates; (e) capacity as a function of cycle numbers at a current density of 0.1 A g−1. | |
The rate performance of the [NH(CH3)2][Sb4S5(S3)] electrode at room temperature was further investigated by cycling the half-cell at different current densities (0.1–5 A g−1). Fig. 4c shows the galvanostatic profiles (5th cycle of each current density) of compound 1 in the half-cell. It is found that the observed curves show a similar sloped behavior. The charge–discharge specific capacities at different current densities are shown in Fig. 4d. Reversible capacities of about 720 mA h g−1 at a current density of 0.1 A g−1, 620 mA h g−1 at 0.2 Ag−1, 585 mA h g−1 at 0.5 A g−1, 521 mA h g−1 at 1 A g−1, 405 mA h g−1 at 2 A g−1, and 310 mA h g−1 at 5 A g−1 are achieved. It should be noted that a specific capacity of 678 mA h g−1 can still be obtained after intensive cycles.
Good cycling performance is a critical factor in practical application of next-generation LIBs. Therefore the long-term cycling properties of compound 1 are performed at a current density of 0.1 A g−1, as shown in Fig. 4e. During 2nd to 50th cycles, it is found that 78.2% of the capacity can be retained. In addition, coulombic efficiency during the cycles can almost remain at 100%, which indicates the good cycling properties of compound 1 as an anode material of LIBs.
The mechanism of the oxidation and reduction reactions is similar to the previously reported one:15,16,19 during the discharging process, Sb3+ first undergoes a conversion reaction corresponding to the peaks of 1.7 and 1.4 V, as shown in the CV curves. After that, a metal alloying reaction with lithium ions happens, corresponding to the peak of 0.75 V. The equations are as follows:
Conversion reaction: [SbIIISII] + 3e− + 3Li+ → Sb + Li2S |
Alloying reaction: Sb + Li+ + 3e− → Li3Sb |
During the charging process, the peaks of 1.1 V and 1.8 V are attributed to the delithiation process of LixSb → Sb and the oxidation of Sb → [SbIIISII], respectively.
Conclusion
In summary, crystalline thioantimonate [NH(CH3)2][Sb4S5(S3)] (1) has been successfully synthesized via the surfactant-thermal strategy. After grinding, the resulting compound 1 presented as ultrathin nanosheets that can offer fast ion diffusion and increased active sites as well as a good accommodation ability for volume expansion, which are favourable properties for LIBs. Employed as an anode material of LIBs, the as-ground compound 1 exhibits a high reversible specific capacity of 568 mA h g−1 over 50 cycles at a current density of 0.1 A g−1 and an excellent rate capability of 301 mA h g−1 at a current density of 5 A g−1. Our research indicates that crystalline chalcogenides could be a promising candidate as an anode material for next-generation LIBs.
Conflict of interest
The authors declare no competing financial interest.
Acknowledgements
Q.Z. acknowledges financial support from AcRF Tier 1 (RG 13/15 and RG133/14) and Tier 2 (ARC 20/12 and ARC 2/13) from MOE, and the CREATE program (Nanomaterials for Energy and Water Management) from NRF, Singapore. Q.Z. also thanks the support from Open Project of State Key Laboratory of Supramolecular Structure and Materials (Grant number: sklssm2015027), Jilin University, China.
References
- V. Etacheri, R. Marom, R. Elazari, G. Salitra and D. Aurbach, Energy Environ. Sci., 2011, 4, 3243–3262 CAS.
- B. Scrosati, J. Hassoun and Y.-K. Sun, Energy Environ. Sci., 2011, 4, 3287–3295 CAS.
- Z. S. Wu, W. C. Ren, L. Xu, F. Li and H. M. Cheng, ACS Nano, 2011, 5, 5463–5471 CrossRef CAS PubMed.
- X. Zhou, L. J. Wan and Y. G. Guo, Adv. Mater., 2013, 25, 2152–2157 CrossRef CAS PubMed.
-
(a) J. Wu, X. Rui, G. Long, W. Chen, Q. Yan and Q. Zhang, Angew. Chem., Int. Ed., 2015, 54, 7354–7358 CrossRef CAS PubMed;
(b) J. Wu, X. Rui, C. Wang, W.-B. Pei, R. Lau, Q. Yan and Q. Zhang, Adv. Energy Mater., 2015, 5, 1402189 Search PubMed.
-
(a) A. A. Mikhaylov, A. G. Medvedev, C. W. Mason, A. Nagasubramanian, S. Madhavi, S. K. Batabyal, Q. Zhang, J. Gun, P. V. Prikhodchenko and O. Lev, J. Mater. Chem. A, 2015, 3, 20681–20689 RSC;
(b) R. Cai, Y. Du, W. Zhang, H. Tan, T. Zeng, X. Huang, H. Yang, C. Chen, H. Liu, J. Zhu, S. Peng, J. Chen, Y. Zhao, H. Wu, Y. Huang, R. Xu, T. M. Lim, Q. Zhang, H. Zhang and Q. Yan, Chem. – Eur. J., 2013, 19, 1568–1572 CrossRef CAS PubMed;
(c) X. Huang, H. Yu, H. Tan, J. Zhu, W. Zhang, C. Wang, J. Zhang, Y. Wang, Y. Lv, Z. Zeng, D. Liu, J. Ding, Q. Zhang, M. Srinivasan, P. M. Ajayan, H. H. Hng and Q. Yan, Adv. Funct. Mater., 2014, 41, 6516–6523 CrossRef.
- J. Wang, N. Yang, H. Tang, Z. Dong, Q. Jin, M. Yang, D. Kisailus, H. Zhao, Z. Tang and D. Wang, Angew. Chem., Int. Ed., 2013, 52, 6417–6420 CrossRef CAS PubMed.
- B. Koo, H. Xiong, M. D. Slater, V. B. Prakapenka, M. Balasubramanian, P. Podsiadlo, C. S. Johnson, T. Rajh and E. V. Shevchenko, Nano Lett., 2012, 12, 2429–2435 CrossRef CAS PubMed.
- X. Zhu, Y. Zhu, S. Murali, M. D. Stoller and R. S. Ruoff, ACS Nano, 2011, 5, 3333–3338 CrossRef CAS PubMed.
- Y. Sun, X. Hu, W. Luo, F. Xia and Y. Huang, Adv. Funct. Mater., 2013, 23, 2436–2444 CrossRef CAS.
- J. Lin, Z. Peng, C. Xiang, G. Ruan, Z. Yan, D. Natelson and J. M. Tour, ACS Nano, 2013, 7, 6001–6006 CrossRef CAS PubMed.
- X. Xu, W. Liu, Y. Kim and J. Cho, Nano Today, 2014, 9, 604–630 CrossRef CAS.
- J. Yang, Y. Zhang, C. Sun, G. Guo, W. Sun, W. Huang, Q. Yan and X. Dong, J. Mater. Chem. A, 2015, 3, 11462–11470 CAS.
- Y. Zhang, W. Sun, X. Rui, B. Li, H. T. Tan, G. Guo, S. Madhavi, Y. Zong and Q. Yan, Small, 2015, 11, 3694–3702 CrossRef CAS PubMed.
- D. Y. Yu, P. V. Prikhodchenko, C. W. Mason, S. K. Batabyal, J. Gun, S. Sladkevich, A. G. Medvedev and O. Lev, Nat. Commun., 2013, 4, 2922 Search PubMed.
- D. Y. Yu, H. E. Hoster and S. K. Batabyal, Sci. Rep., 2014, 4, 4562 Search PubMed.
- C.-H. Lai, M.-Y. Lu and L.-J. Chen, J. Mater. Chem., 2012, 22, 19–30 RSC.
- H. Yang, X. Su and A. Tang, Mater. Res. Bull., 2007, 42, 1357–1363 CrossRef CAS.
- P. V. Prikhodchenko, J. Gun, S. Sladkevich, A. A. Mikhaylov, O. Lev, Y. Y. Tay, S. K. Batabyal and D. Y. W. Yu, Chem. Mater., 2012, 24, 4750–4757 CrossRef CAS.
- H. Hou, M. Jing, Y. Yang, Y. Zhu, L. Fang, W. Song, C. Pan, X. Yang and X. Ji, ACS Appl. Mater. Interfaces, 2014, 6, 16189–16196 CAS.
- M. Naguib, J. Halim, J. Lu, K. M. Cook, L. Hultman, Y. Gogotsi and M. W. Barsoum, J. Am. Chem. Soc., 2013, 135, 15966–15969 CrossRef CAS PubMed.
- J.-w. Seo, J.-t. Jang, S.-w. Park, C. Kim, B. Park and J. Cheon, Adv. Mater., 2008, 20, 4269–4273 CrossRef CAS.
- W. Sun, X. Rui, J. Zhu, L. Yu, Y. Zhang, Z. Xu, S. Madhavi and Q. Yan, J. Power Sources, 2015, 274, 755–761 CrossRef CAS.
-
G. M. Sheldrick, SHELXS97 and SHELXL97, University of Göttingen, Germany, 1997 Search PubMed.
-
(a) Q. Zhang, X. Bu, J. Zhan, T. Wu and P. Feng, J. Am. Chem. Soc., 2007, 129, 8412–8413 CrossRef CAS PubMed;
(b) Q. Zhang, X. Bu, L. Han and P. Feng, Inorg. Chem., 2006, 45, 6684–6687 CrossRef CAS PubMed;
(c) Q. Zhang, X. Bu, Z. Lin, M. Biasini, W. Beyermann and P. Feng, Inorg. Chem., 2007, 46, 7262–7264 CrossRef CAS PubMed;
(d) Q. Zhang, T. Wu;, X. Bu, T. Tran and P. Feng, Chem. Mater., 2008, 20, 4170–1472 CrossRef CAS;
(e) Q. Zhang, Y. Liu, X. Bu, T. Wu and P. Feng, Angew. Chem., Int. Ed., 2008, 47, 113–116 CrossRef CAS PubMed.
-
(a) K. Biswas, Q. Zhang, I. Chung, J.-H. Song, J. Androulakis, A. Freeman and M. G. Kanatzidis, J. Am. Chem. Soc., 2010, 132, 14760–14762 CrossRef CAS PubMed;
(b) Q. Zhang, I. Chung, J. I. Jang, J. B. Ketterson and M. G. Kanatzidis, Chem. Mater., 2009, 21, 12–14 CrossRef CAS;
(c) Q. Zhang, C. D. Malliakas; and M. G. Kanatzidis, Inorg. Chem., 2009, 48, 10910–10912 CrossRef CAS PubMed;
(d) Q. Zhang, G. Armatas and M. G. Kanatzidis, Inorg. Chem., 2009, 48, 8665–8667 CrossRef CAS PubMed.
-
(a) W. W. Xiong, G. D. Zhang and Q. C. Zhang, Inorg. Chem. Front., 2014, 1, 292–301 RSC;
(b) W. W. Xiong, P. Z. Li, T. H. Zhou, A. L. Y. Tok, R. Xu, Y. L. Zhao and Q. C. Zhang, Inorg. Chem., 2013, 52, 4148–4150 CrossRef CAS PubMed.
-
(a) W. W. Xiong, E. U. Athresh, Y. T. Ng, J. F. Ding, T. Wu and Q. C. Zhang, J. Am. Chem. Soc., 2013, 135, 1256–1259 CrossRef CAS PubMed;
(b) W. W. Xiong, J. W. Miao, K. Q. Ye, Y. Wang, B. Liu and Q. C. Zhang, Angew. Chem., Int. Ed., 2015, 54, 546–550 CAS.
- L. N. Nie, W. W. Xiong, P. Z. Li, J. Y. Han, G. D. Zhang, S. M. Yin, Y. L. Zhao, R. Xu and Q. C. Zhang, J. Solid State Chem., 2014, 220, 118–123 CrossRef CAS.
- W.-W. Xiong and Q. Zhang, Angew. Chem., Int. Ed., 2015, 54, 11616–11623 CrossRef CAS PubMed.
- L. Nie, Y. Zhang, K. Ye, J. Han, Y. Wang, G. Rakesh, Y. Li, R. Xu, Q. Yan and Q. Zhang, J. Mater. Chem. A, 2015, 3, 19410–19416 CAS.
- G. D. Zhang, P. Z. Li, J. F. Ding, Y. Liu, W. W. Xiong, L. N. Nie, T. Wu, Y. L. Zhao, A. I. Y. Tok and Q. C. Zhang, Inorg. Chem., 2014, 53, 10248–10256 CrossRef CAS PubMed.
- J. K. Gao, Q. L. Tay, P. Z. Li, W. W. Xiong, Y. L. Zhao, Z. Chen and Q. C. Zhang, Chem. – Asian J., 2014, 9, 131–134 CrossRef CAS PubMed.
- M.-L. Feng, W.-W. Xiong, D. Ye, J.-R. Li and X.-Y. Huang, Chem. – Asian J., 2010, 5, 1817–1823 CrossRef CAS PubMed.
- N. Ding and M. G. Kanatzidis, Chem. Mater., 2007, 19, 3867–3869 CrossRef CAS.
- C. Y. Yue, X. W. Lei, Y. X. Ma, N. Sheng, Y. D. Yang, G. D. Liu and X. R. Zhai, Cryst. Growth Des., 2014, 14, 101–109 CAS.
- T. S. Cameron, A. Decken, I. Dionne, M. Fang, I. Krossing and J. Passmore, Chem. – Eur. J., 2002, 8, 3386–3401 CrossRef CAS.
- M. D. Meienberger, K. Hegetschweiler, H. Ruegger and V. Gramlich, Inorg. Chim. Acta, 1993, 213, 157–169 CrossRef CAS.
Footnotes |
† Electronic supplementary information (ESI) available. CCDC 1430117. For ESI and crystallographic data in CIF or other electronic format see DOI: 10.1039/c5qi00194c |
‡ These authors contributed equally to this work. |
|
This journal is © the Partner Organisations 2016 |
Click here to see how this site uses Cookies. View our privacy policy here.