DOI:
10.1039/D4VA00058G
(Critical Review)
Environ. Sci.: Adv., 2024,
3, 983-1003
A review of current developments in graphene oxide–polysulfone derived membranes for water remediation
Received
17th February 2024
, Accepted 7th May 2024
First published on 7th May 2024
Abstract
Water pollution has become a major issue due to the presence of hazardous pollutants resulting from ever-increasing industrial growth, and researchers are actively seeking innovative solutions for water treatment. Graphene Oxide (GO)–polysulfone (PSF) membranes are widely used in water remediation due to their resistance to high pH and harsh chemicals, and their ability to remove water pollutants. These materials have unique two-dimensional structures, tailorable micropores, large surface areas, and fascinating surface properties, making them ideal for water treatment. This review article provides a comprehensive overview of the latest developments in polysulfone-derived membranes modified with graphene oxide, including their separation performance, antifouling effect, and ability to separate and degrade organic pollutants. Additionally, the review article covers membrane performance for filtration of organic dyes, metal ions, radionuclides and salts from contaminated water. The review article also highlights simulation or computational studies and concludes by discussing the challenges and prospects of GO–PSF derived membranes for water remediation.
Environmental significance
Water pollution poses a significant threat to both the environment and public health, primarily due to unregulated industrial development. Numerous individuals worldwide lack access to clean drinking water, underscoring the need for effective water treatment methods. Membrane technology, which encompasses polymeric membranes, such as polysulfone, demonstrates promise due to its cost-effective nature and mechanical properties. However, further research is essential to explore the use of nanomaterials, such as graphene oxide (GO), to enhance the performance of these membranes. The development of advanced composite membranes holds great potential for addressing water pollution and scarcity, preserving water resources, and promoting sustainable environmental management.
|
1. Introduction
The escalating population and unprecedented industrialization have imposed numerous challenges, including a hazardous environment, on our generation. The byproducts of industrial processes have permeated the air and water, contaminating water resources and depriving humans and other living organisms of clean water.1–4 The World Health Organization (WHO) reports that billions of individuals are faced with a shortage of hygienic drinking water.5 Additionally, oil spills from transportation, drilling, and storage activities further exacerbate the pollution of water resources.6,7 The need for potable water and a solution for the global water scarcity problem has led to the development of effective water treatment methods.8,9
Membrane technology is of considerable importance in the separation process. It is a highly effective method for treating wastewater, effluents, and seawater desalination due to its cost-efficiency, high productivity, exceptional removal efficiency, straightforward operation, and minimal reliance on chemical additives.10–13 A membrane serves as a physical barrier that allows for selective permeation of desired materials, while preventing the passage of unwanted materials.10,14 Membranes are classified based on various characteristics, including the material used for their fabrication, the surface properties of the membrane, and the filtration process and pore size.15 They are typically divided into polymeric and inorganic membranes, which differ in the materials used for their construction. Inorganic membranes are made from metals and ceramic materials and possess high thermal, structural, and mechanical strength. However, they have limited permeability and are therefore less commonly used.16 The issue of permeability has been addressed through the use of polymeric membranes. Membranes are typically classified based on their surface properties as either hydrophilic (polar surface) or hydrophobic (non-polar surface). Additionally, the filtration process and pore size are also used to categorize membranes into Nano-Filtration (NF), Micro-Filtration (MF), Ultra-Filtration (UF), and Reverse Osmosis (RO) membranes.17–21
MF membranes have a pore size ranging from 0.1–1 μm, making them suitable for the separation of macromolecules, colloids, and bacteria.22 UF membranes have a pore size of 0.01–0.1 μm, making them impermeable to viruses and macromolecules, yet permeable to water molecules and low molecular weight solutes.23 NF membranes have a pore size of 0.1–0.001 μm, making them more dense than MF and UF membranes, and they are capable of removing divalent ions while allowing monovalent ions to pass.24,25 RO membranes have a pore size of less than 0.001 μm, making them the densest of all membranes, and they are only used in high-pressure filtration processes to produce clean water by removing impurities and monovalent ions.26,27
Polymeric materials, such as polysulfones and polyamides, are commonly used membranes.28,29 Polysulfones are widely employed polymers in water treatment applications due to their porous structure, favorable mechanical properties, relatively low cost, and ease of operation.30,31 Additionally, they exhibit resistance to higher pH, high temperatures, and chemical inertness. However, the hydrophobic nature of PSF limits its use, as these membranes are prone to fouling.32,33
To address this issue, various nanomaterials, including zeolite, MOFs (metal–organic frameworks), metal carbides, chalcogenides, carbon-composite based nanofibers and carbonaceous materials, are suitable for enhancing the characteristics of PSF membranes.34–39 Graphene derivatives, such as graphene oxide (GO), are the most popular carbonaceous materials used to improve the separation performance of membranes. GO is a well-known graphene derivative and is commonly used for synthesizing composite membranes.40–42 The addition of GO not only decreases the membrane's hydrophobicity but also improves its mechanical properties. GO has oxygen;43,44 as a result, the GO surface is electron-rich (negatively charged) and exhibits excellent adsorption of cationic compounds.45–47 Moreover, these membranes do not swell in water and remain stable.48,49 Single layer GO nanosheets are two-dimensional and approximately 1–2 nm thick. Due to their high surface area, GO nanosheets exhibit high interaction with PSF membranes.46,49,50 These extraordinary surface and dimensional properties make GO a promising candidate for the development of PSF composite membranes. These PSF composite materials exhibit extraordinary structural properties, including increased hydrophilicity, high chemical stability, water permeation, and excellent antifouling properties.51–53
So, the objective of this review is to examine the most recent advancements made in PSF membranes that have been modified with graphene oxide, specifically their applications for water remediation. This literature review distinguishes itself from prior studies by providing a comprehensive review of graphene oxide–polysulfone based membranes, covering aspects such as performance, mechanism, properties and computational studies, all within a single review article.
2. Methods of preparation of GO and PSF
The utilization of graphene derivatives, particularly those derived from carbonaceous materials, has become increasingly popular for enhancing the performance of membranes utilized for separation purposes. Among these derivatives, graphene oxide (GO) is notably prominent and widely employed in the fabrication of composite membranes.54 Graphene oxide (GO) has the ability to not only decrease the hydrophobicity of membranes but also enhance their mechanical properties. This is due to the presence of oxygenated groups on the GO surface.55 The electron-rich (negatively charged) GO surface exhibits an exceptional ability for the adsorption of cationic compounds. This is attributed to the electrostatic repulsive force that repels negatively charged ions from passing through the surface. As illustrated in Fig. 1, the single layer GO nanosheet is two-dimensional with a one atom thickness, translating to approximately 1–2 nm. The high surface area of GO nanosheets facilitates their remarkable interaction with membranes.3,57 The remarkable surface and dimensional characteristics of GO nanosheets make them a more favourable option for the fabrication of composite membranes. These composite materials exhibit exceptional structural properties, such as elevated hydrophilicity, enhanced chemical stability, superior water permeability, and anti-fouling properties.54
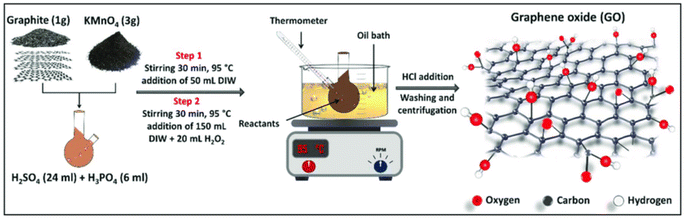 |
| Fig. 1 GO synthesis by a modified Hummer's method.57 | |
There are numerous techniques employed in the production of membranes, including stretching, track-etching, dip-coating, template-leaching, sintering, and phase inversion. Among these methods, phase inversion is the most commonly utilized procedure for generating membranes from polymers.58–62
The phase-inversion method (immersion–precipitation technique) is widely used for the generation of membranes from polysulfone like other polymers such as polycarbonates, polyoxadiazoles, polyamides, nylon 6,6, polyphenylene oxide and polyimides.63–65 This technique consists of four steps: solution preparation of PSF in a suitable solvent, film formation of PSF solution on a flat support, film immersion in a coagulation bath having polymer solvent and conditioning of the membrane.59,66,67 The schematic procedure of the phase inversion method is shown in Fig. 2.
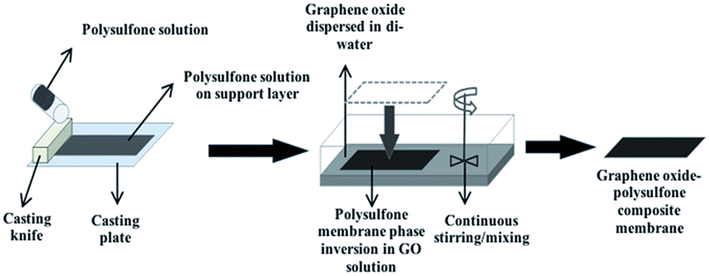 |
| Fig. 2 Phase inversion method for generation of a PSF membrane.68 | |
GO required for the fabrication of the membrane is prepared from the exfoliation of graphite oxide, which is used for cost-effective and large-scale production of GO. Different methods have been reported for the generation of graphite oxide from graphite. Foremost, Brodie prepared graphite oxide by graphite oxidation in a potassium chlorate mixture. After that, Staudenmaier et al. reported a method (Staudenmaier method) of graphite oxidation using an ice bath with a 1
:
4 volume ratio of nitric acid
:
sulphuric acid and potassium chlorate as an oxidizing agent. Then, with continuous stirring, 4.37 g/100 mL graphite was added to an ice bath. Although the evolution of toxic gases is a limitation of the Staudenmaier method, it is considered more secure than the Brodie method. In 1958, Hummer reported another method involving the oxidation of graphite in a few hours using H2SO4, NaNO3 and KMnO4 as oxidizing agents. Hummers' Method (HM) has advantages, i.e. less reaction time, safety from toxic explosives (ClO2 and KClO3) because of using KMnO4 instead of KClO3 and removal of acid fog formation using NaNO3 instead of HNO3. Therefore, HM is preferred over the others for GO preparation. Later on, in 2010, Tour et al. further improved HM to enhance the degree of oxidation and to reduce the formation of toxic gases NO2 and N2O4. In the Tour method, KMnO4 replaced sodium nitrate.69–74 Epoxy is the dominant group in graphene oxide (generated by the Hummer and Tour method). GO synthesis reported by HM has extended sheets and is effective for developing the mechanical properties of membranes. GO has lateral dimensional thickness with amphiphilic nature due to the existence of a variety of surface functionalities and chemical inertness.75,76
3. Separation mechanisms
3.1 Classical adsorption
The general adsorption process involving the transfer of materials to the surface of the solid phase, through either physical or chemical interactions, is followed during classical adsorption through membranes. The adsorption of metal ions by a membrane (Fig. 3) consists of three steps. The first step is the penetration along with the diffusion of metal ions through membrane pores and finger-like layers, the 2nd step consists of surface complexation on inner spheres, which are external to nano-sized adsorbents that are localized inside the membrane structure, the third step involves the transfer of metal ions towards the interface of the adsorbent and the last step is the equilibrium stage. The preparation, characterization and adsorptive removal of heavy metal ions from aqueous solution using GO-impregnated membranes have been reported.77,78
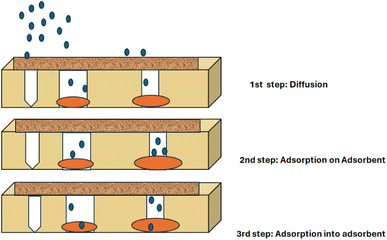 |
| Fig. 3 Mechanism of classical adsorption. | |
3.2 Sieving mechanism/size exclusion (steric hindrance)
A particle removal process that prevents particles from passing through any passage/way or pore smaller than the size of the particle itself is called sieving.79 This process is presented in Fig. 4(a). The membrane can only pass the particles that are smaller than the pore size. Salt ions having hydrated ionic diameters greater than the pore size of the membrane are rejected due to steric hindrance.80 Uncharged or neutral solutes are also separated through steric hindrance known as size exclusion. The size exclusion process controls the rejection of As(III) at pH values 4.5–8.5 because in this pH range, As(III) remains uncharged.79–81
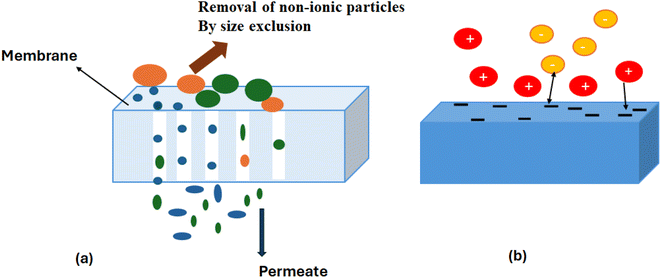 |
| Fig. 4 (a) Removal of non-ionic particles by size exclusion and (b) Donnan exclusion; attraction of positive ions by a negatively charged membrane. | |
The membrane separation mechanisms are based on various mathematical models such as Spiegler–Kedem (SK), Combined-Film-Theory-Spiegler–Kedem (CFSK) etc. The latter model is preferred over the former because the former doesn't consider the concentration polarization effect (CPE). The CPE actually causes a decrease in the performance of the system owing to the increased osmotic pressure in the opposite direction at the interface of the feed solution and membrane film.82 The above-discussed mechanisms ignore the impact of the charges on the surface of membranes; however, the same has been considered in the following mechanisms.
3.3 Donnan exclusion
For compact membranes, Donnan exclusion is a non-sieving mechanism for the rejection of unwanted particles. The mechanism operates on the repulsion produced between the charged membrane surface and ionic species. The steric hindrance also operates at the isoelectric point, where electrostatic repulsions disappear. The pH of solution less than the isoelectric point induces a negatively charged surface of the membrane, which shows greater repulsion towards negatively charged ions, whereas a pH higher than the isoelectric point (IEP) generates a positive charge on the membrane surface, which shows better rejection towards positively charged ions. This reaction occurs due to the ionization of functional groups on the membrane surface, which causes the creation of charges on the external and internal surfaces of membranes.77,83,84
3.4 Dielectric exclusion
Yaroshcuk et al. reported dielectric exclusion during the separation process by providing an in-depth analysis of this exclusion mechanism. It has been postulated that when an ion interacts with bound electrical charges produced by the ions at the boundary between two materials with different dielectric constants (solvent and membrane matrix), a dielectric exclusion process occurs. According to relative dielectric constants, it is measured that the ion polarizes the two media and forms polarized charge distribution at the discontinuous surface.84–87
4. Separation performance of modified PSF membranes
Several two-dimensional materials have been shown to be excellent building blocks for high-performance membranes in recent years. These materials include the graphene family, exfoliated dichalcogenides, zeolites, metal–organic framework (MOF) nanosheets, and dichalcogenides.88,89 However, graphene oxide–polysulfone based membranes are preferred over other 2D derived materials due to their exceptional strength and stability, resulting in increased durability and a longer lifespan.90 In addition, GO–PSF based membranes are known for their exceptional permeability and selectivity, which make them ideal for enhancing separation processes. The versatility of graphene oxide–polysulfone membranes is enhanced by their ability to function effectively in a variety of solvents and operating conditions, thereby enhancing their suitability for a broad spectrum of pollutants for water remediation applications.91–93
Hydrophilic membranes show minimum fouling by oil droplets as compared to hydrophobic membranes.94–96 The separation application is affected due to membrane fouling, which results in lowered membrane reusability. Membrane performance in terms of permeability, thermo-mechanical stability and anti-fouling properties can be increased by adding nanomaterials having an extended surface area with adjustable pore size. Modi et al. reported improvement in the efficiency of PSF membranes for oil/water separation through implanting carboxylated multiwalled CNTs/graphene oxide in the hollow region of the membranes. They prepared GO by dispersion of graphite oxide in basic solution and obtained a monomolecular layer of GO. The modified membrane showed high mechanical strength (Young's modulus), anti-biofouling properties and high negative values of zeta potential (high surface negative charge). The reported PSF composite membranes showed high oil/water separation.55 The separation tendency of hollow fiber membranes (HFMs) can be calculated by measuring antifouling properties, pure water permeability (PWP), permeate water flux through the membrane and efficiency of oil/water separation.55,97,98
4.1 Pure water permeability
Pure Water Permeability (PWP) is the flux of pure water without fouling of membranes. The determination of PWP for different samples of hollow fiber membranes (HFMs) has been reported by Modi et al. by passing water (for 2 h and at 1 bar pressure) through different samples of HFMs. The PWP can be measured using the following formula (shown in eqn (1)).99–101In the above-mentioned equation Q (mL h−1), Di (m), L (m) and ΔP (Pa) represent the flow rate, inner diameter, fiber length and transmembrane pressure (TMP), respectively.55
In a study for oil/water separation, the preparation of oil/water (O/W) emulsion was achieved by blending oil, water and a weighed amount of sodium dodecyl sulphate (SDS) and the resultant mixture was stirred and sonicated for 5 h. As a result, milky white O/W emulsion having a pH of 6.5 was generated.102,103 The separation processes were applied by feeding O/W emulsion through the HFM sample at one bar for 1 hour. Permeate from HFMs was calculated and dynamic light scattering (DLS) was used to measure the size distribution of oil droplets in permeate. The following eqn (2) was applied to compute the efficiency of each sample (HFMs) to separate O/W.
| 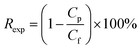 | (2) |
In the above equation,
Cp and
Cf demonstrate the oil-concentration in the permeate and feed, respectively. A UV-visible spectrophotometer was reported to perform calculations regarding oil concentration.
104,105 An increase in the PWP value by using a polysulfone membrane modified with graphene oxide has been reported by Modi
et al.55
Zhao et al. reported106 the determination of permeate water flux from a membrane. In order to determine permeate flux, different samples of membranes were submerged for 24 h in deionized water. Then at operating pressure 1–2 bar, the volume of permeate water within 50 minutes was measured by using the following eqn (3).
where
JW,
V,
A and
t represent the pure water flux (L h
−1 m
−2), permeate water volume, membrane effective surface area and time, respectively. The increase in the pure water flux with rise in the GO content in membranes has been reported by Nasseri
et al. A GO/PSF membrane with 1.0% GO has been reported to possess the highest flux of water,
i.e. 512 L h
−1 m
−2.
107
4.2 Antifouling behavior
The antifouling behavior of membranes is reduction in the deposition of salts, microorganisms, macromolecules and colloids, which cause membrane fouling (Fig. 5). The membrane fouling decreases the membrane life, permeation flux and selectivity.108,109
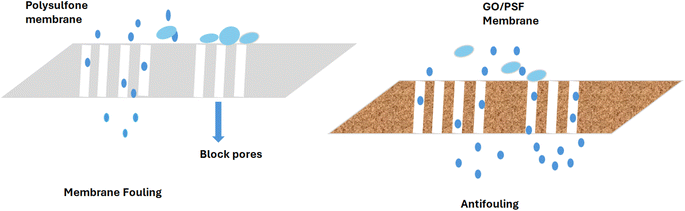 |
| Fig. 5 Fouling and antifouling behaviour of PSF and GO/PSF. | |
The calculation of the antifouling behavior of different samples of HFMs through measurement of the PWP value after a refusal of oil experiment has been reported. The pure water permeability (PWP) after fouling is called PWPf. The highest flux recovery ratio (FRR) of 90.5% was reported for CGP-(carboxylated multiwalled GO–PSF)-100 (HFMS), whereas 84.3% FRR was reported for CGP-75 (HFMs). The excellent performance of CGP-100 was attributed to high hydrophilicity and negative surface charge. The hydrophilic membranes containing negative charges allowed the penetration of water molecules and synchronously prevented oil adsorption and hence gave oil free water in permeate.55 The factors including the measurement of surface charge and electrostatic repulsion are reported for the prediction of the foul-resistance features of the membrane. Moreover, GO reduces the membrane roughness and the resulting smooth surface possesses a better tendency to resist the membrane-oil adhesion on the surface, which results in the minimum fouling of the membrane. Modi et al. concluded that among all the HFM samples, the reduction in the pure water permeability value was found to be lowest in CGP-100 (9.5%). For HFM samples, the flux recovery (FR) increased with the decrease in the CGP percentage. Thus, it can be concluded that polysulfone membranes modified with GO show enhanced separation properties and anti-fouling ability. These graphene oxide polysulfone composite membranes possess significant oil rejection efficiency and are hence used widely for O/W separation.110
4.3 Selectivity performance
The term selectivity refers to the selective use of membranes for the separation of certain substances. The changes in the hydrophilicity, contact angle, zeta potential and size of pores are the factors that affect the membrane selectivity performance.111–113 The membrane having zeta potential and a low contact angle (higher hydrophilicity) shows improved permeability and the membrane having small sized pores decreases the flux or enhances the selectivity of the membrane.93 Oil rejection experiments have been reported extensively in the literature, which reflect the selectivity of modified GO–PSF membranes for oil/water separation. An oil rejection test was also reported to separate the oil from the emulsion using dead cells by collecting three permeate samples. The measurement of total organic carbon (TOC) of feed and that of permeate was used to evaluate the oil rejection % age. The membrane having 0.1% GO showed maximum oil rejection up to 97.92%. The trade-off between permeability and oil rejection is expected, but this can be adjusted by using the optimum amount of GO. The best agreement between the separation factor and permeability factor is usually achieved through graphical comparison of permeability and selectivity. The reported data showed that membranes which are more permeable to water have less capacity for the separation of oil and water, whereas the membranes with less water permeability have higher potential for the separation of oil from water. The best rejection efficiency was reported for the membrane containing 0.1% GO with low permeability. The membrane having high permeability was modified by minimizing the separation factor.114 Since the properties of GO alter remarkably upon changing the methods of its synthesis,115 GO/PSF membranes fabricated from differently synthesized GO show different properties. Salt, oil and various dyes are rejected by using mixed matrix membranes containing GO because of having acidic functional groups, which are the source of negative charge separation on the surface of the membranes.116 Zeta potential indicates the rejection performance, which measures the charge on the surface of the membranes. The zeta potential of PSF/GO membranes is more negative as compared to PSF membranes, which means that PSF/GO membranes have a more tendency to reject negative ions. The presence of specific functional groups having oxygen which include hydroxyl, carboxyl and carbonyl on the membrane surface is the main reason for the negative values of zeta potential. Initially, rejection increases with an increase in the graphene oxide concentration until the graphene oxide concentration reaches the optimum value and a further increase in the GO content beyond the optimum value causes a decrease in the rejection. The use of GO in optimum amounts causes increases in the flux and oil rejection. This is attributed to the tailoring effect of hydrophilicity and the surface contact angle from the measurement of hydrophilic and hydrophobic properties from interfacial tensions.117
5. Characterization of modified membranes
Most of the attributes of membranes depend on the hydrophilic/hydrophobic nature of the membranes, the pore size of the membranes and the rough/smooth appearance of the membranes. The measurement of the contact angle is the best way to determine these characteristics.118–120
5.1 Hydrophilic/hydrophobic properties
The use of the water contact angle is reported for the characterization of the hydrophilicity of membranes. The water contact angle decreases with an increase in the addition of isocyanate graphene oxide (iGO) from 0.0 to 0.10%. This water contact angle reduction is a manifestation of increasing hydrophilicity of the membranes. When the iGO amount is increased to 0.15%, then the water contact angle of blended membranes is increased, indicating a decrease in the hydrophilicity of the membrane. The irregular position of iGO in the membrane structure at a concentration of 0.1% iGO causes a reduction in the water contact angle. When the content of isocyanate graphene oxide increases, then the zeta potential decreases on account of the presence of carboxylic groups on the surface layer, which appear on the surface due to hydrolysis upon immersing the membrane in water. The reported experimental results indicate an increase in water flux upon the addition of a small amount of iGO (0.025%) to the PSF membrane. This increase in the flux is due to an increase in hydrophilicity and the formation of straighter and slightly finger like microvoids. But if the iGO concentration exceeds 0.05%, then the water flux decreases. This decrease is due to the agglomeration of iGO, which enhances the viscosity of the membrane and consequently, the membrane porosity is reduced greatly. The decrease in the flux is an indication of the fouling process on the membrane.121,122
5.2 Pore size
Brunauer–Emmett–Teller (BET) analysis is used to find out the porosity as well as the surface area of micropores and mesopores in membranes. The BET method determines all the available pores for nitrogen adsorption.123 Kovtun A. used the BET formula to study the adsorption process for a GO–PSF membrane for organic-contaminant removal from water as shown in eqn (4). | Qe = (QmCBETx)/(1−x)(1 + CBETx − x) | (4) |
where Qe represents the number of molecules absorbed at equilibrium, Qm represents the number of molecules required to cover the whole surface of the adsorbent and CBET is the thermodynamic equilibrium constant.124 Recently, Lekena N. reported BET results for GO–PSF with a pore surface area of 80.5 m2 g−1, which increased in the case of the GO–APTES system up to 333.8 m2 g−1.125
5.3 Surface roughness
Van der Waals forces, hydrogen bonding and electrostatic force play a role in the fouling process.126,127 The flux recovery ratio of composite membranes is greater than that of pure PSF membranes, which reflects the enhanced anti-fouling properties of composite membranes. The increase in hydrophilicity is accountable for the blocking of protein chemisorption on the membrane surfaces.128 Atomic Force Microscopy (AFM) is used to study surface roughness and fouling. According to AFM, a decrease in surface smoothness enhances fouling.129 The antifouling properties can be increased by increasing the surface smoothness. The smoothness of the surface is increased after doping iGO (0.05%) and as a result antifouling properties are increased. When the iGO content is increased beyond (0.15%), a valley appears and foulants are absorbed in the valley of the membranes. which results in lowered antifouling properties.130
6. Types of modification in GO–PSF membranes
6.1 Modification in GO nanosheets
The synthesis of GO has been reported through the deposition of nanosheets of GO in layers. These sheets were then interconnected through 1,3,5-benzenetricarbonyl trichloride on a PSF support coated with polydopamine (PDA) as shown in Fig. 6.
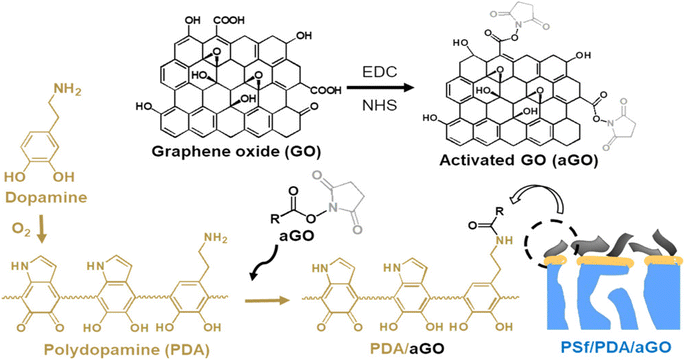 |
| Fig. 6 Modification of a graphene oxide based polydopamine coated polysulfone (GO–PDA–PSF) membrane using 1-ethyl-3-(3-dimethylaminopropyl)carbodiimide (EDC) and N-hydroxysuccinimide (NHS).131 | |
Liang et al. recently reported poly(vinylidene fluoride) modified PSF/GO–Ag nanosheets with dopamine coating. This membrane possessed a water flux of 650.52 L m−2 h−1, a contact angle of 69°, a rejection of 98%, a pore size of 21.16 nm and 81.02% porosity.132 The separation performance of the mentioned membrane is envisaged by using monovalent salt sodium chloride (NaCl) and divalent Na2SO4 salt. The membrane coated with polydopamine showed less than 10% rejection of dyes and almost no rejection of the salt. GO coating on this type of membrane increased the rejection of monovalent along with divalent salts in the range of 6–19% and 26–46%, respectively. The rejection rate varied due to a different number of GO layers deposited on the polydopamine coated PSF support. The rejection of organic dyes was also enhanced by GO coating. The rejection rate for methylene blue was 46–66%, whereas that of rhodamine-WT was 93–95%. The reasons behind the higher rejection rate of R-WT include the higher molecular weight of R-WT than that of MB dyes (size exclusion effect), and the repulsion between the negatively charged surface of the GO (due to the presence of carboxylic groups) coated membrane and anionic R-WT in comparison to MB, which is positively charged. So, the spacing between graphene oxide layers (size exclusion effect) and membrane charges (Donnan exclusion) are the prime factors that determine the rejection performance of GO membranes. The rejection also decreases when the concentration of the solution increases. Na2SO4 rejection decreases from 88% to 26% upon an increase in its concentration from 0.1 to 10 mM and a similar effect has been reported for NaCl. The aforementioned observations indicate the great contribution of the charge effect to the membrane separation mechanism. A decrease in the Debye length leads to a decrease in repulsion between the ions and charged membranes, which ultimately leads to a decrease in the rejection rate.133
6.2 PSF–GO silver nanocomposite membranes
PSF–GO silver nanocomposite membranes are synthesized by blending the solutions of PSF, GO and silver nanoparticles. These membranes have a larger Young's modulus and tensile strength than PSF membranes. The adsorption capacity of silver-decorated graphene oxide (Ag/GO) is often better than that of graphene oxide (GO). This is because GO sheet stacking is decreased and more adsorption sites are provided by the attachment of silver nanoparticles (AgNPs). This decrease in stacking effectively improves the surface area by increasing the gap between the sheets.134,135 Moreover, the PSF–GO–AG membrane possesses more finger shaped pores and channels with reduced surface-pore size, which results in an enhanced exchange rate in phase separation, increased surface roughness having a mean-surface (Ra) value of 4.40 nm and an increased flux of 66.7 L m−2 h−1.136 Suhalim et al. reported a PSF–GO–Ag nanocomposite membrane with a water flux of 141.6 L m−2 h−1, a contact angle of 54.71°, rejection of 78.5% and 78% porosity.137 GO for membrane preparation was obtained from graphite powder (raw material) by employing HM. A GO–Ag nano-hybrid was prepared in a two step process. In the first step, 20 mg GO was mixed with 60 mL PPh3 (triphenylphosphine), followed by sonication for 1 h at room temperature to disperse GO nanoparticles. 1.4 mg of AgNO3 was separately dispersed in PPh3. Then both solutions were mixed and sonicated for half an hour. Then the mixture was stirred vigorously, and the temperature was maintained at 80 °C for 24 hours. The GO–Ag nano-hybrid was thus prepared. After that ethanol washing of the nano-hybrid and then drying were performed above room temperature. The GO–Ag nano-hybrid showed higher anti-bactericidal potential due to strong adhesion through PPh3 between the sheets of GO and AgNPs. A PSF–GO–Ag nanocomposite was synthesized by a solution blending method. First PSF was dried for 24 hours at 80 °C under vacuum and then DMF as a solvent was added to polysulfone resin (PSU) to form a transparent solution. Then this solution was added to the dispersion of GO and silver nanoparticles and then stirred for 6 hours. With the use of an automatic coating machine, the solution was cast into a thin film. Then solvent molecules were evaporated at 25 °C (room temperature) to obtain PS–GO–Ag nanocomposite membranes.
The composite PSF–GO membrane containing silver nanoparticles possesses antibacterial properties against Staphylococcus aureus and Escherichia coli at a low GO–Ag loading. The antibacterial screening of the membrane was performed using Gram-negative and Gram-positive bacteria. PSU film samples were cut having a width of (50 mm) and then placed into a sterile Petri dish and then bacterial suspension of 0.4 mL was poured onto the film and the sample was covered with a polyethylene square film. Then the antibacterial rate was measured using the following eqn (5).
N0 represents the average number of viable bacteria on neat PSU and
N represents the number of viable bacteria on the PSU/GO–Ag film after antibacterial examination. The above-mentioned use is because of their bactericidal capability to prevent bacterial contamination. GO and AgNPs show antibacterial properties (inhibition of bacterial growth) against Gram-positive as well as Gram-negative bacteria. The antibacterial effect of GO–Ag membranes is due to the fact that this material functions as a conducting bridge for the electrons emitted during respiration and fermentation processes to increase the concentration of reactive oxygen species (ROS). The ROS disturbs the balance of the metabolic process of bacteria and also accounts for membrane damage. Besides causing imbalance in the metabolic process and damage to the membranes, this membrane releases Ag ions, which go into bacterial cell walls and have interaction with the biochemical material and cause damage to the nitrogenous base and hereditary material DNA and hence result in decreased cellular activity. Experimental studies indicate that the anti-bactericidal properties are very high for
E. coli (83%) and
S. aureus (58.5%) when using the PSU/GO–Ag nano-composite membrane. This difference in antibacterial properties for Gram-positive bacteria and Gram-negative bacteria may be attributed to variations in the nature of the cell membrane and the biochemical composition of each type of bacteria. This type of membrane is therefore considered an excellent candidate for medical uses because of having antibacterial properties.
138
6.3 PSF/GO zinc oxide membranes
ZnO nanoparticles (ZnO NPs) are beneficial for the membrane process in desalination because of having anti-fouling and antibacterial properties.139 Compared with other NPs, ZnO NPs are cost effective, biocompatible and considered more appropriate for the preparation of nanocomposites.140 The ZnO incorporated into the PSF/GO membrane possesses enhanced porosity (83.00 ± 1.18%) compared to neat PSF 52.20 ± 0.28%. These membranes possess a high permeate flux of 35.03 L m−2 h−1 and a reduced contact angle of 52°, showing more hydrophilic nature than that of PSF/GO.97 The rejection behaviors of PSF–ZnO–GO (ZG3), PSF polymer and PSF–ZnO (Z2) have been compared by applying humic acid as an organic foulant in solution form. The PSF membrane shows a humic acid rejection of 52% and the ZG3 membrane shows 99% rejection of humic acid. ZG3 showed high permeability and excellent rejection capability. This is because the anti-fouling properties of the membrane are modified due to the hydrophilic character of GO and ZnO–GO NPs. Consequently, the hydrophilic nature decreases the adsorption of organic pollutants within the membranes.141,142 This increased hydrophilicity is due to the high polarity of ZnO NPs and the presence of epoxy, hydroxyl and carbonyl functional groups on GO nanosheets, which increase antifouling properties or minimize humic acid adsorption on membrane surfaces. These more hydrophilic membranes showed a higher affinity of nanoparticles towards water instead of organic matter, thus causing a minimum hydraulic resistance.143 The antifoulant behaviour is dependent on the hydrophilicity of the membrane and this hydrophilicity can be changed due to the presence of oxygenated groups in the ZnO–GO nano-hybrid.144,145 ZnO nano-particles act as an antimicrobial agent in many applications because they are bio-safe materials.146 ZnO NPs show antibacterial properties against Bacillus subtilis and Escherichia coli 45, which inhibit bacterial growth and propagation. ZnO NPs disturb the bacterial cell integrity by direct interaction. This also causes the generation of the ROS, which releases superoxide anions and hydrogen peroxide, and hydrophilic membrane surfaces cause less adhesion of E. coli. PSF–ZnO–GO shows antibacterial properties due to the increased transfer of electrons to contribute to more ROS generation and hence destroys the bacterial cell.147,148
6.4 PSF/GO-bovine serum albumin membranes
Bovine Serum Albumin (BSA) is a protein of serum (derived from a cow) with wide biochemical application143 and routinely employed as a concentration standard for proteins. BSA can interact with different carbon nanomaterials.149 Huang et al. reported a PSF/GO membrane with a flux of 641.7 L m−2 h−1 that is 3 times the flux of pristine PSF membranes (229.2 L m−2 h−1) under 0.1 MPa pressure. This membrane possessed 98.22% rejection for protein, 47.75 nm pore size, 78.07% porosity and excellent hydrophilic character.150 Chemically modified BSA has also been used as glue with GO to bind enzymes without any loss in enzyme activity.151 A dye rejection study is done with the composite (GO–PSF) using intermediate BSA. Its mechanical strength, pore size and contact angle are altered by adding GO to the PSF membrane, which generates a center for binding of BSA. The molecular structure as well as the properties of BSA help it to interact with GO and textile dye (reactive orange), making it possible for the filtration of dye. The pH has a major effect on the dye sorption and filtration mechanism. Experiments have been reported with three PSF membranes different from each other and having different concentrations of GO (2, 4 and 8%) at different pH. It has been proven that addition of 2% GO at pH 7 is the optimal condition for the binding of BSA. The carboxyl group of graphene binds to the amine group of BSA through covalent linkages. Membranes having 2% GO at pH 10 showed maximum dye rejection capability. Besides pH, contact time also affect the filtration mechanism. Higher the contact time between dye and protein molecules, the higher will be the rejection capacity.141,152
6.5 PSF/GO matrix membranes
Polysulfone graphene oxide mixed matrix composite membranes (MMMs) have been synthesized by the process of phase inversion.153 Abdalla et al. reported PSF/GO–NH2 with properties including 68.9% porosity, 65° contact angle, 95.6% oil rejection, 2071 LMH bar−1 permeability and maximum hydrophilic character for 0.2 wt% GO–NH2.154 Required amounts of graphene oxide (0, 0.05, 0.1, 0.2, and 0.4) and 0.8 wt% relative to PSF are dispersed, which is carried out by sonication in dimethylacetamide (DMAc) for five minutes. A solution of 80% N-DMAc/GO, 15% PSF and 5% PVP is prepared by overnight stirring. After this nano-composite solution is degassed in a sonication bath for 10 minutes and then this solution is cast on a glass plate by using a membrane casting machine. Then after half a minute the glass plate is dipped in a deionized water containing coagulation bath for five minutes and then the coagulating film is stored in deionized water (UP, ultra-pure water) for three days.153
This composite membrane shows better mechanical and thermal performance as compared to PSF. The reported result is that the tensile modulus and tensile strength are also increased by the incorporation of GO from 153 MPa to 330 MPa and from 3.5 MPa to 5.6 MPa, respectively.155
Interfacial polymerization is also a technique used to prepare thin film composite membranes with or without graphene oxide on the top surface of polysulfone membranes. Hosseini et al. reported this process including washing (with deionized water), spreading of metaphenylene diamine (MPD) having additives (sodium lauryl sulfate and camphor sulfonic acid) on a polysulfone substrate, initiation of interfacial polymerization by trimesoylchloride solution (in hexane), and removal of excess organic solution, followed by heat treatment of the PSF membrane at 65 °C for the thin film composite membrane. After this washing is done with water and then these membranes are stored in water. For the preparation of a graphene oxide incorporated thin film/layer composite membrane, the same process is followed and the only difference is the use of MPD/GO aqueous solution (Table 1).156
Table 1 Comparison of the properties of various types of modified GO–PSF membranes
Types of membranes |
Pore size (nm) |
Porosity (%) |
Rejection |
Contact angle |
Permeate flux L m−2 h−1 |
Operating conditions |
Pollutants |
Ref. |
GO–PDA–PSF nanosheets |
21.16 |
81.02 |
98% |
69° |
650.52 |
37 °C, 0.1 MPa |
BSA |
131
|
PSF/GO–Ag nanocomposite membrane |
2.1–2.4 |
78% |
78.5% |
54.71° |
141.6 |
37 °C, 7 bar, stirring at 300 rpm |
Fe2+ |
132
|
PSF/GO–ZnO membranes |
41.40 |
83 |
99% |
52° |
35.03 |
5 bar sheet thickness 4 cm |
Organic pollutant |
97
|
PSF/GO BSA membranes |
47.75 |
78.07 |
98.22% |
57° |
641.7 |
0.1 MPa |
BSA |
150
|
PSF/GO matrix membranes |
2.44 |
68.5 |
95.6% |
65° |
207.1 |
1–7 bar |
Oil |
154
|
7. Applications of GO–PSF membranes
7.1 Removal of organic pollutants
Bisphenol A (BPA) is generally used for the synthesis of plastics and found as a pollutant in small amounts in water due to its low solubility. BPA is a hazardous pollutant of water bodies.107 This pollutant disturbs the endocrine function. It can cause liver damage, (THD) and cancer.157 Traditional methods are not good for the removal of BPA. For the removal of this pollutant, membrane physiochemical separation techniques are feasible.158
Nano-composite membranes show better performance when regarding BPA removal and permeate flux. This permeated flux has linear relationships with the GO content of the membranes, meaning that permeated flux increases when the graphene oxide content increases. The BPA rejection efficiency is highest for the nanocomposite-membrane having 0.4% GO. There are various factors that affect the BPA removal efficiency. The BPA rejection efficiency is enhanced by lowering the operating pressure and enhancing the BPA concentration. When the BPA concentration is high, then less time is required for the removal of BPA because of enhanced electrostatic repulsion of negative charge with the membrane negative charges. pH also affects the rejection efficiency of BPA. Increased pH results in increased electrostatic repulsion and hence leads to higher BPA rejection and also reduced operating time.107
Methylene Blue (MB) is a cationic dye and hazardous because its exposure results in jaundice and an increased heart rate. Hence, removal of dye from water is essential to avoid its health risks.159 PSF exhibits low adsorption of dye. An increase in the adsorption of MB dye has been reported upon using a PSF/GO nanocomposite (generated by a phase inversion method). The adsorption efficiency increased approximately 20% for PSF/GO composite membranes in comparison to PSF membranes. This increase is attributed to the negatively charged groups of GO on the polysulfone membrane surface. The observed ease in the absorption of methylene blue was due to electrostatic interactions between positively charged MB and the negatively charged membrane surface.90
PSF modified with GO (1% weight) exhibits organic removal up to 70%. The doping of GO in PSF gives additional properties to the membranes.160 Ion adsorption and Gibbs Donnan exclusion are operative mechanisms in the rejection performance of membranes. GO imparts negative charges to the membrane on account of deprotonated carboxyl groups. The negatively charged surface repels anionic species and facilitates the adsorption of positively charged metal cations. Higher the quantity of GO in the membrane, easier will be the adsorption of dissolved ions (having position charge) and hence lower the total dissolved salt concentration (TDS) in water.161 Ammonia exists in the form of ammonium ions in water bearing positive charge. The pH of natural rubber wastewater was 6.6. This phenomenon shows that equilibrium shifts towards the ionized form (ammonium ions) having a positive zeta potential effect on the separation properties of membranes particularly for charges to be separated. These positively charged ions are adsorbed on the negatively charged membrane surface (Table 2).162
Table 2 GO–PSF derived materials for the removal of organicsa
Adsorbent |
Adsorbate |
Adsorption capacity (mg g−1) |
Parameters |
Ref. |
NA: data not available.
|
Alg/GO |
Methylene blue |
12.64 |
25 °C, pH = 7.78 |
163
|
GO–PAMAM |
Oil |
120 |
4 recycles |
164
|
PSF–TiO2/GO |
TDS (from rubber) |
NA |
pH = 8–8.5, C 335 mg L−1 |
160
|
(P(Aam-IA)/GO–PEI) |
Azo dyes (cationic (crystal violet)) |
390.6–774.46 |
0.2% GO wt |
165
|
SA/GO@Fe3O4/CS |
Methylene blue |
21.325 |
5 recycles |
166
|
Neutral red |
44.654 |
Safranine T |
44.313 |
CS/AAm/IA/GO |
Methylene blue |
247.47 |
C
0 5 mg L−1, pH = 8 |
167
|
rGO/MMT/XDV |
Rhodamine |
482 |
5 adsorption/desorption cycle |
168
|
rGO/XDV |
Toluene |
500 |
β-CD/GO |
Organic dyes (methylene blue) |
76.4 |
70 °C, 60 min, adsorbent C = 0.04 g L−1 |
169
|
SA–GO |
Tartrazine |
420.36 |
Aqueous medium |
170
|
MOF-525/GO |
Tetracycline |
436 |
303 K, pH = 3 |
171
|
SA–HEC/GO |
Crystal violet |
312.72 |
pH = 5 |
172
|
GO rGO |
Methylene blue |
33 333 |
25 °C |
173
|
Methylene blue |
2000 |
Fe3O4@GO@AHSA |
Methylene blue |
286 |
37 °C |
174
|
PSF/GO/poly(MMA-co-GMA) |
Oil |
NA |
C 50–1000 mg L−1 |
104
|
BSA |
PSF–MMMs–GO |
Oil |
NA |
C 0.05–0.8 wt% |
114
|
GO–CuO@CA–PES |
Methylene blue |
37.1 |
273 K, C = 1 × 10−5 M & pH 9 |
175
|
Rhodamine blue |
30.05 |
Congo red |
20.20 |
Methyl orange |
6.79 |
RGO–PEG–ZnO |
2,4-Dichlorophenol (2,4-DCP) |
570.641 |
25 °C, pH = 7 |
176
|
Phenol |
531.804 |
2-CP |
511.248 |
Bisphenol-A (BPA) |
485.756 |
7.2 Removal of salts
Desalination is an important method for fresh water augmentation by removal of salts and minerals from saline water.177 Membranes used for the desalination process require modification in terms of antifouling properties, water flux and salt rejection. The development of nano-fields leads to addition of nano-materials in polymeric membranes for desalination techniques. Advanced membrane materials have an influence on desalination processes, including reverse-osmosis, membrane distillation, forward-osmosis, pervaporation, and electrodialysis.178
Desalination membranes require hydrophilicity. For increasing hydrophilicity and salt rejection, PSF membranes are modified with GO. MGO has amphiphilic nature, and water molecules are adsorbed first at terminal hydroxide (hydrophilic nature) and then rapidly diffused in the carbon core (hydrophobic and hence a creating water channel), which enhances the permeation flux. This thin carbon sheet when incorporated in PSF increases the properties of PSF at low concentration. Besides increasing the salt rejection, water uptake also increases the water uptake with increase in GO in the membranes. This relationship is due to the presence of hydrophilic sites in GO, which result in increase in the uptake of the solvent. Three factors affect the water uptake potential of the membranes and are the membrane morphology, number of hydrophilic sites in the membranes and pH. GO doping also increases macro-voids in the PSF sub-layer. This increase in macro-voids results in increase of the uptake capacity of the membranes. Solvent uptake increases with increase in pH in GO/PSF membranes. Through ion dipole forces, negative charges (on GO) interact with molecules of water, resulting in more water uptake. When pH increases, hydrogen ion concentration decreases and hence equilibrium reactions shift toward the right, producing more negative ions.179
For salt rejection PSF/GO nano-composite membranes can also be used. A salt rejection study has been performed through finding rejection in 1000 ppm Na2SO4 and NaCl solution at various operating pressures. The solute rejection is directly proportional to GO content in composite membranes. Membranes having 2000 ppm GO content show an optimum rejection of 72% for Na2SO4 at an operating pressure of 4 bar. The low pH of feed solution induces low rejection. This low rejection is because of small dissociation of ionizable species and reaction shift toward the left, which produces less negative charge or fewer cation exchange groups. This also indicates that the membrane has negative charge on the surface. The functional group dissociation is also a cause of the appearance of negative charges found on graphene oxide. At higher applied pressure, the rejection efficiency of PSF/GO is decreased as compared to that at low pressure. The pristine PSF membrane shows poor rejection efficiency as compared to PSF/GO nano-composite membranes. The rejection efficiency is highest when 2000 ppm GO is doped into PSF membranes. PSF/GO membranes show higher rejection of Na2SO4 as compared to NaCl. This increased rejection of Na2SO4 is because of negative charges on the membranes, which strongly repel SO42− in contrast to chloride ions due to smaller hydrated ionic size.180 Hence, the low rejection of NaCl by the membranes is attributed to the small effect of Donnan and size exclusion. GO nanosheets are incorporated in polysulfone to get a polysulfone graphene oxide composite membrane support layer. After this polyamide layers are generated on polysulfone GO through interfacial polymerization for a thin film composite for forward osmosis (TFC-FO membranes). The membrane permeability for water molecules is increased by a suitable amount of GO in PSF.112 The problem of water storage arises due to economic development and population growth. To overcome this water shortage, one solution is sea water desalination for substituted resources of water. The technology of forward osmosis (FO) membranes is implemented for desalination181 and wastewater treatment.182,183 The FO membrane is semi-permeable and across it a gradient of osmotic pressure induces the transport of water. TFC membranes show high permeability for water molecules and low reverse permeability for solute molecules. The FO membrane containing a thin film composite has a slim active layer, which is formed from polyamide with a permeable structure. This polyamide layer (PA) is liable for large salt rejection and promotes the transport of water molecules. GO is an excellent material to modify TFC-FO membranes because of possessing various oxygen containing functional groups.184 GO with a high surface area to volume ratio facilitates effective interaction with the matrix of polymer. The addition of GO also reduces the contact angle that corresponds to higher hydrophilicity and this increased hydrophilicity results in increased water permeability for composite membranes. The addition of GO beyond 1% causes the reduction of favorable structural properties, which affects layer preparation for PA rejection and water permeability. This reduction in permeability and rejection for higher contents of GO is because of unequal GO dispersion in the PSF and leads to membrane formation having smaller pore size, resulting in an adverse effect on membrane salt rejection.185,186
7.2.1 Regression error.
Regression models are applied to study the statistical effects of various parameters on the desalination performance of membranes. The given relationship determines how the empirical equation is employed to approximate the experimental data regarding the independent process variables.
where Xi and Xj are the dimensionless coded variables, Y is the expected response, b0 indicates the constant, bi, bii, and bij are the linear, quadratic, and interaction regression coefficients, and n is the number of design variables.187 A determination coefficient (R2) is also used to elucidate the model data derived from experimental data and it also determines the removal efficiency of the membrane. The ratio of the model's sum square to the sum square of y was defined as R2.188
7.3 Removal of metal ions
The biochemical process within the human body involves some heavy metals like Zn, Cu and Mn. Unfortunately, excessive exposure to these metals causes an adverse effect and some heavy metals including cadmium, mercury and lead are toxic because these metals are non-biodegradable and hence can store in the human body. These metals should therefore be removed from water.189
Commercial GO based nano-filtration membranes are available for heavy metal rejection. These commercial membranes have been used successfully for the treatment of copper, cadmium, manganese, and lead under a pressure of 4 bar for 1000 mg L−1 initial concentration of heavy metal. Metal salts are successfully rejected according to Donnan exclusion theory. There is a significant role of Donnan repulsion as well as the adsorption mechanism in rejection. This composite membrane shows greater adsorption (Table 3) due to the existence of reactive functional groups, including the carboxylic group on the membrane's surface and due to porous additives in the membrane's structure.77 Arsenate rejection up to 83% occurs at basic pH. The predominant mechanism in arsenate rejection is Donnan repulsion.190 Lead is a heavy metal and exists in divalent form. Lead damages the kidney, brain and reproductive system in humans. Uncoupling of ionic species through nano-filtration membranes is dependent on membrane charges and the membrane pore radius. A porous membrane possessing smaller pores has potential for the retention of charged species, and highly charged membranes have more potential for the exclusion of co-ions (similarly charged ions to membranes). A lead rejection experiment has been reported at various pressures 1, 2, and 3 bar at solution pH 6. After 30 minutes, the permeate sample is collected and quantitative analysis is performed by measuring rejection for lead ions. At 1 bar pressure, 1% GO content membranes are reported to show high rejection. PSF/GO nano-composite membranes exhibit lower flux for lead nitrate solution as compared to pure water. The flux decreased but it was still higher than the flux when only PSF membranes were used. When only the PSF membrane was used, the flux for lead nitrate was higher than the pure water flux. This increase is due to pore opening and the absence of graphene oxide that can retain the lead ions. Membrane rejection efficiency decreased with increase in pressure. A higher pressure results in increased permeability for water molecules, which causes lead ions to pass through membranous pores by convection. GO addition develops negative charges on the membrane, which cause the adsorption of lead ions (positively charged).191
Table 3 GO–PSF derived materials for the removal of inorganicsa
Adsorbent |
Adsorbate |
Adsorption capacity (mg g−1) |
Parameters |
Ref. |
NA: data not available.
|
GO–Ch |
Cu cation |
58.5 |
20 ± 2 °C, pH = 7, 20 g L−1 |
196
|
GO–Fe3O4/PSf |
NaCl |
NA |
27.79 g mL−1 |
197
|
rGO@CDs |
As(V) |
87.6 |
100 μg L−1, 40 bar |
198
|
PSF–GO/Pt |
Nitrate |
NA |
50 mg L−1, 3 bar |
199
|
PSF–PVA–SA–GO |
As(III) |
NA |
5 mg L−1 |
200
|
PSF–MMt–GO |
Hg(II) |
144.89 |
150 mg L−1, pH = 2 |
201
|
PSF–ZnO |
Cu(II) |
84 |
pH = 7 |
202
|
GO–Fe3O4 |
Cu(II) |
18.1 |
Basic conditions |
203
|
Sr–GO–MMT–PSF |
Cu(III) |
101.83 |
pH = 6 |
204
|
GO–EDA–Al2O3 |
Na+, Mg2+, SO42− |
NA |
pH = 7–11 |
205
|
Lignin–PNMA–rGO |
Pb(II) |
753.5 |
pH = 5.1 |
206
|
GO–EDTA–CS |
Hg(II) |
324 |
pH = 5.10–8.30 |
207
|
Cu(II) |
130 |
GO/PEI |
Cu(II) |
150.9 |
pH = 5.5 |
208
|
MXene/GO |
U(VI) |
1003.5 |
pH = 6.0, 298 K |
209
|
CS–GO–DO/ZnO |
Uranium |
561.09 |
— |
210
|
Lignin/GO–PSF |
Pb(II) |
71.32 |
pH = 7.0, 300 rpm |
211
|
Donnan exclusion (charge–charge repulsion) in arsenic removal occurs from water when using nano-filtration membranes having negative charges. As (5) and As (3) have different rejection capacities by the membranes when the concentration of arsenic feed water solution is changed. By enhancing the concentration of arsenic feed, the rejection efficiency of As(V) is also expanded from 60% to 90% by increasing the concentration of arsenic feed from 10 to 316 μg L−1. The rejection efficiency of As(III) is decreased by increasing the arsenate feed water concentration. The arsenate rejection efficiency is decreased to 5% from 28% by increasing the arsenic feed concentration from 10 to 316 mg L−1. The rejection efficiency of As(V) decreases by decreasing the pH. However, the As(III) rejection efficiency is affected by the pH. This information is obtained on the basis of membrane pore size and charge. Donnan exclusion mechanisms are the reason for high rejection efficiency instead of relatively large membrane pore size. The separation results show that for highly charged species As(V) rejection the employed mechanism is Donnan exclusion. The reported arsenic rejection survey determines that the main factors affecting the separation (As(V) and As(III)) are the pH and concentration of bulk solution. The separation of As(V) was found to be within 60–90% for the feed concentration of arsenic of 10 and 315 mg L−1. The rejection was decreased to 5% by adding 10 mM NaCl. There, rejection is due to electrostatic repulsion that exists between the co-ion HAsO42− and the negatively charged membranes. The decrease of rejection efficiency by adding salt is because of charge exclusion decrease due to increasing salt concentration in the test solution, therefore lowering the separation of As(V) oxyanions. According to Hodgson, the ionic separation of different species can be enhanced using solutions of various solutes due to the presence of more permeable ions of the same charges.192 Hence the rejection of As(V) can be increased by the addition of bicarbonate ions that are more permeable than As(V). When feed arsenate concentration increases, As(III) separation decreases. This decrease is because when feed arsenate As(V) and As(III) concentrations increase, the diffusion and convection of uncharged species increase. This increase in the diffusion and convection of As(III) results in a decrease in its rejection. At low pH, As(V) rejection is also low and rejection of As(III) is independent of the pH. There are multiple factors that contribute to the decrease in the rejection of As(V) at low pH. In other words, the negative charges on the membranes are less at low pH, thus decreasing the Donnan exclusion for oxyanions of As(V). The As(III) rejection is independent of pH in the range of 4.5 to 8.5. This is because it remains unchanged in this range. The As(III) removal is due to steric exclusion, which is small and therefore its rejection is not affected by the change in the membrane properties.193
Dhara et al. reported a lignin/GO–PSF membrane (synthesized by phase inversion) for the removal of Pb(II) from water. Filtration operations were performed using an aqueous solution of Pb and Eosin Y dye. The electrostatic interaction between Pb2+ ions and negatively charged Eosin Y molecules created a bigger Eosin–Pb complex. According to the best-model-fit, the adsorption process may entail multilayer physisorption.194
The separation performance of a ZnO–Al2O3–PSF mixed matrix membrane has been checked in terms of permeation fluctuation and removal of ions (heavy metal), including As(V) and Pb(II). The improved hydrophilicity, surface charge, and porosity of the synthesized membranes allowed the removal of As and Pb with efficiencies of 87% and 98%, respectively. Filtration experiments have been reported at different pressures. Increasing the number of nanoparticles (Zn and Al2O3) gradually increases the rejection of heavy metals and permeation flux; however increasing the number of nanoparticles beyond an optimum number results in decrease in the rejection efficiency of the membranes and this is because excess nanoparticles lead to larger porosity. Steric and Donnan exclusion is the operating mechanism for the rejection of ions. As(V) is an oxyanion and it exists in the hydrogen arsenate form (HAsO42−) and dihydrogen arsenate (H2AsO4) near neutral pH and removal of As(V) is in the combined form. As negative charge causes electrostatic repulsion by anionic species on the membrane surface and Pb2+ cations cause electrostatic attraction with the negatively charged membrane surface. Dielectric exclusion also contributes significantly to ion rejection, and it also explains the high rejection that is observed in the nano-filtration membrane in ionic solution having divalent counter ions. As(V) exists in the monovalent state H2AsO4− and hence it is affected slightly compared to Pb2+.195
7.4 Removal of radionuclides
Graphene oxide has high potential for radionuclide sorption. GO synthesized by Hummers' method (HGO) exhibits a high sorption capacity of radionuclides as compared to GO generated by the Brodie method (BGO). BGO shows fewer defects and contains a high relative concentration of hydroxyl groups and even functional group distribution over the surface.212Fig. 7 presents an illustration of the formation of HGO defects and sorption sites. HGO exhibits a larger number of carboxyl and carbonyl groups possessing numerous holes and increased sorption capacity of HGO towards radionuclides due to interactions with the carboxylic group on GO flakes.213 HGO is used to produce reduced graphene oxide (rGO), which is then oxidized by HM, resulting in the formation of defective graphene oxide (dGO). This dGO exhibits enhanced sorption of radionuclides due to a larger number of defects and doubly bonded oxygen. This rGO is generated by thermal standard HGO molting.214 This reduced graphene oxide undergoes further oxidation, which results in the multiplication of defects. The gas pressure inside the interlayer is developed due to the high rate of generation of carbon oxides and explosion.215 The strong explosion and heating result in the maximum surface area and maximum number of defects.216–218 The carboxylic group which is present inside the hole of dGO is the sorption site for the elimination of radioactive waste from aqueous solution.
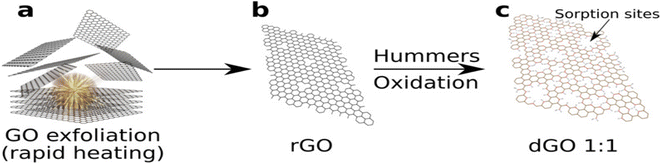 |
| Fig. 7 Scheme for the preparation of defective GO: (a) explosive thermal-exfoliation of GO, (b) Hummer's oxidation of defective rGO and (c) dGO with sorption sites.219 | |
The sorption of U(VI), Am(III), and Eu(III) has been reported for the examination of graphene oxide defects and the HGO standard. U(VI) is present in the form of a cation that is the uranyl cation UO22+ possessing +2 total charge and +3.2 effective charge. Am(III) has +3 charge. dGO has great sorption potential for both U and Am over a wide range of pH. dGO shows higher sorption because of higher carboxyl group concentration than HGO. Hence the sorption isotherm for radionuclides has been applied to find functional group contents. The sorption capacity of dGO is 15 times more for U(VI) and 2 times for Am(III) as compared to pristine HGO. Radionuclides bind to various GO types, and carboxylic acid present on the boundaries of small holes is the reason for the sorption of cations including uranyl cations. dGO exhibits 15 times more sorption for U(VI) and 2 times for Am(III). This huge increase in the sorption of uranyl is due to even uranyl distribution over the dGO flakes. This uranyl cation is bound to the carboxylic group. This carboxyl group is found inside of small holes in dGO. dGO shows higher sorption capacity due to this increase in the defect and hence can be used in the treatment of radioactive waste.214
Graphene is considered an excellent adsorbent because of its high surface to volume ratio.220 But graphene has one disadvantage; it causes aggregation and hence promotes the precipitation of aqueous solution that hinders its application. The dispersion properties can be increased by graphene oxide for which graphene is the precursor, and it can be applied as an adsorbent for radionuclides. Adsorption is a surface phenomenon and is regulated by surface functionalities. Graphene is modified with functional groups to enhance the adsorption potential for pollutants by increasing dispersion in solution and decreasing the self-aggregation.221 Amidoxime is grafted on graphene oxide. Amidoxime has hydroxyl and amino groups that are used for improving the performance of adsorbent adsorption for aqueous solution containing heavy metal ions.222 pH also affects the adsorption of radionuclides on poly amidoxime reduced graphene oxide (PAO–rGO). The adsorption of Sr(II) on the PAO–rGO composite increased from 7–73% in the pH range 2–11. The pH change can increase or decrease the metal ion adsorption by changing Sr(II) distribution in the solution and charges on the adsorbent surface through dissociation of the functional group.223 When pH is low, the functional group on the adsorbent surface is less dissociated. As a result, less Sr(II) is adsorbed and increasing pH causes negative charges on the adsorbent surface and increases the adsorption potential.224 The zeta potential at different pH is examined to study the pH effect on radionuclide removal. The membrane or adsorbent surface is positively charged at pH less than 4.2 due to protonation of the PAO group. However, when pH is more than 4.2 the composite membrane gains a negative charge, which causes an increase in the binding of positive radionuclide ions. Hence, the trivalent ions having a positive charge on Eu possess a higher binding than positively charged divalent ions Co. From the above-mentioned information, it can be concluded that the adsorption of radionuclides is due to the interaction of ions having opposite charges.223 Sr is a radionuclide, and it enters the body and replaces calcium and it damages the organs of the body and is hence responsible for causing diseases.225 Hence it is very important to remove strontium from wastewater. The interlamellar spacing of GO using polyvinyl alcohol increases, which enhances the exposure of the active site and increases the adsorption capacity of GO towards strontium. The PVA/GO aerogel possesses monolithic morphology. This unique morphological feature endows the aerogel with a unique feature of convenient separation. The reported result indicates that the adsorption of strontium does not depend on temperature. PVA/GO at pH 7 exhibits a high removal efficiency of up to 79.13. Under a low pH or acidic environment, the carboxyl group of GO is protonated and the Sr(II) adsorption is decreased because of electrostatic repulsion.226 Under a higher pH or basic environment, the deprotonation of the carboxyl group of GO occurs, and the presence of the hydroxyl group therefore destroys the H bond and as a result, aggregation of GO leading to reduced active sites has been observed. The selectivity of PVA/GO can be checked in the presence of various competitors like Na1+, K1+, Ca2+, and Mg2+. The competitive effect depends on the nature of Sr(II) ions, and this ability follows the decreasing trend Mg2+ > K1+ > Na1+. This competitive ion decreases the adsorption performance of Sr when the ratio is set as 40/1. Moreover, the hydrated ionic radius of divalent ions is comparable to that of strontium, and thus they also have a much greater inhibition effect on the immobilization of Sr2+. The adsorption mechanism of Sr includes two aspects: interaction developed between the pi electron domain of GO sheets and Sr(II) and strong complexation between Sr(II) and COOH/OH groups. Both of the above aspects decrease the interlamellar spacing among GO layers and hence cause deformation along GO planes.225
8. Simulation studies of PSF membranes
Simulation studies give information related to the microstructure of nanocomposite polymer membranes. In addition, these studies give fast and computationally inexpensive information about calculated properties, which include end to end distance, d spacing of microstructural plates and free volume of the polymer chain with high accuracy compared to experimental data.227
Force gives a statistically consistent set of system configurations along with a complete description of quantum mechanics.228,229 Within a statistical framework, discrete and random samples are used in the Monte Carlo (MC) simulation approach. It is frequently used in thermodynamic systems, especially when examining atomic migration and related phenomena. Defects in layered 2D nanomaterial membranes were studied using Monte Carlo simulations in order to understand how their layered structure forms and how this affects molecular transport, namely permeability and selectivity.230,231 Independent pathways have different probabilities of permeability because molecules prefer paths with a lower barrier. The effective path length was given by eqn (6)
| 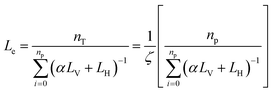 | (6) |
where
nT and
nP are the total number of probes and the number of probes passing through the membrane;
ζ is the ratio of
nT and
nP,
α is the weighting factor, and
LV and
LH are the vertical and horizontal path length, respectively. Since the path length that water molecules take through the laminate determines the water permeability, which is inversely proportional, the average permeability
P is therefore determined using the harmonic mean as the function that is followed.
where
rH represents the horizontal-resistance per unit-length. The salt-rejection was given as
eqn (7)232 | 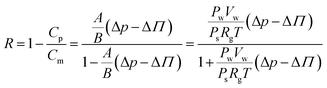 | (7) |
The atomic-scale investigation of mass transport theory in graphene-based membranes is greatly aided by molecular mechanics-based MD simulation.233,234
Recently, Khajouei et al. performed the simulation investigation (Fig. 8) of a GO–Pt/PSF membrane for nitrate removal using simulating software OPEN-MX. The results showed that 0.75 wt% GO/Pt nanoparticles have the highest stability in the membrane.
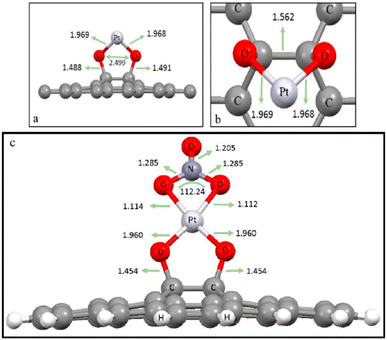 |
| Fig. 8 (a and b) Side view and top view of the optimized position of Pt-nanoparticles on the surface of GO, and (c) optimized nitrate-interaction with the GO/Pt surface and bond lengths (Å).199 | |
Yang et al. reported a simulation examination of a single layer nanoporous GO membrane (NPG) for the desalination and removal of small organic pollutant molecules from water. Seven organic molecules including methanol, phenol, 2-propanol, pyrrole, n-nitrosodimethylamine and urea were considered to recognize the molecular factors that promote organic removal. The reported results demonstrated that water-organic permselectivity for small pores having hydroxyl functionalities is higher. The pore-size sieving mechanism was observed for the separation of organic molecules. Fig. 9 shows that transport through the NPG membrane decreases with an increase in molecular size.229,235
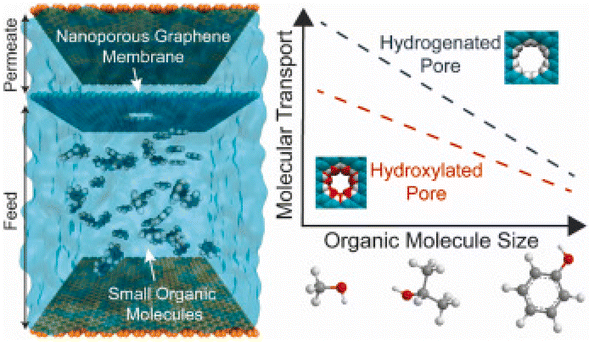 |
| Fig. 9 Illustration of the performance of the NPG membrane for the removal of organic molecules.229 | |
9. Challenges and future prospects
The performance of PSF–GO derived membranes in removing pollutants from contaminated water has been impressive. However, there are several challenges associated with scaling up their applications. Firstly, research has demonstrated that the issue of GO aggregation within polymeric networks can be addressed through the functionalization of graphene oxide. This functionalization prevents agglomeration in polymer systems, particularly in the presence of sulfuric acid. Furthermore, sulfonated graphene oxide can be readily produced from graphene oxide and features negatively charged clusters that enhance hydrophilicity and dispersion and prevent fouling.236 Secondly, limited adhesion between the GO layer and the substrate, since GO films are commonly produced using the drop-casting method, poses a challenge for the composite structure. Nevertheless, studies have demonstrated that the weak attachment can be improved by applying surface modification techniques.237
In recent times, a new nano-architecture has been introduced that utilizes GO-assembled 2D channels with a specific interlayer height of a few nanometers. This design is intended to facilitate rapid transport and enable specific gas sieving through the use of carefully crafted external forces.238 In order to enhance the hydrophilicity of a film, various techniques have been employed, including surface coating, interfacial polymerization, and layer-by-layer assembly, each presenting specific challenges. While surface coating effectively reduces the number of surface pores on the membrane, it does not affect the membrane's internal pores. However, the intricate procedures involved in polymerization techniques, including interfacial polymerization, increase the yield of the film. An alternative approach is to improve the antifouling performance by increasing the hydrophilicity of the film by incorporating hydrophilic nanofillers into the bulk polymer network to produce a hybrid ultrafiltration membrane.239
The majority of existing research has focused on the individual performance of each pollutant. However, it is extremely difficult to adsorb both organic and inorganic pollutants simultaneously with high adsorption. In the near future, it is crucial to direct research efforts towards making specialized modifications to these membranes, to achieve improved performance in the removal of multiple contaminants while maintaining their durability.
10. Summary
Graphene oxide–polysulfone membranes have demonstrated great potential for water purification. These membranes exhibit exceptional adsorption capacities for organic and metal ions. Recent research has enabled them to overcome their resistance to high pH and harsh chemical conditions. The fabrication of these membranes results in a superior porous structure, high compressibility, and cost-effective operation when compared to other membrane systems. Additionally, various methods have been employed to generate GO–PSF membranes, and their separation performance was tested for the removal of organic pollutants, such as methylene blue, rhodamine blue, congo red, methyl orange, tetracycline, tartrazine, rhodamine, toluene, and safranine T, as well as inorganics, including Cu(II), U(VI), Na+, Mg2+, SO42−, As(III), Hg(II), NaCl and nitrates. The incorporation of GO into/onto PSF membranes provides a variety of pore sizes and thermal stability and enhances hydrophilicity, contributing to the adsorption capacities of the membranes. Studies have also shown that Donnan exclusion is the primary separation mechanism for GO–PSF membranes. Overall, the availability of PSF–GO derived membranes on a commercial scale is rather limited. Therefore, it is imperative that current research initiatives focus on enhancing and optimizing graphene oxide–polysulfone membranes for water purification at the industrial level.
Conflicts of interest
There are no conflicts to declare.
References
-
J. Ahmed, A. Thakur and A. Goyal, Biological treatment of industrial wastewater, ed. M. P. Shah, Royal Society of Chemistry, 2021 Search PubMed.
- C. Zamora-Ledezma, D. Negrete-Bolagay, F. Figueroa, E. Zamora-Ledezma, M. Ni, F. Alexis and V. H. Guerrero, Environ. Technol. Innovation, 2021, 22, 101504 CrossRef CAS.
- M. Zubair, M. S. Roopesh and A. Ullah, Chemosphere, 2022, 308, 136339 CrossRef CAS PubMed.
- M. Zubair, I. Zahara, M. Roopesh and A. Ullah, Int. J. Biol. Macromol., 2023, 124446 CrossRef CAS PubMed.
-
UN-Water, Summary progress update 2021: SDG 6 – water and sanitation for all, 2021, https://www.unwater.org/sites/default/files/app/uploads/2021/12/SDG-6-Summary Progress-Update-<?pdb_no 2021?>2021<?pdb END?>_Version-July-2021a.pdf Search PubMed.
- P. Keramea, K. Spanoudaki, G. Zodiatis, G. Gikas and G. Sylaios, J. Mar. Sci. Eng., 2021, 9, 181 CrossRef.
- N. A. Nahyoon, M. Mehdi, K. H. Thebo, N. Mahar, A. A. Memon, N. Memon and N. Hussain, Opt. Mater., 2023, 135, 113260 CrossRef.
- M. M. Pendergast and E. M. Hoek, Energy Environ. Sci., 2011, 4, 1946–1971 RSC.
- T. H. Banglani, I. Chandio, A. Ali, A. A. Memon, J. Yang, M. Kazi and K. H. Thebo, Environ. Sci.: Water Res. Technol., 2024, 10, 1061–1096 RSC.
- A. Yusuf, A. Sodiq, A. Giwa, J. Eke, O. Pikuda, G. De Luca, J. L. Di Salvo and S. Chakraborty, J. Cleaner Prod., 2020, 266, 121867 CrossRef CAS.
- D. Li, Y. Yan and H. Wang, Prog. Polym. Sci., 2016, 61, 104–155 CrossRef CAS.
- J. Luo, W. Cao, L. Ding, Z. Zhu, Y. Wan and M. Y. Jaffrin, Sep. Purif. Technol., 2012, 96, 194–203 CrossRef CAS.
- T. Mezher, H. Fath, Z. Abbas and A. Khaled, Desalination, 2011, 266, 263–273 CrossRef CAS.
- A. Ali, F. Rehman, M. Ali Khan, F. H. Memon, F. Soomro, M. Iqbal, J. Yang and K. H. Thebo, ACS Omega, 2022, 7, 32410–32417 CrossRef CAS PubMed.
- S. P. Nunes, P. Z. Culfaz-Emecen, G. Z. Ramon, T. Visser, G. H. Koops, W. Jin and M. Ulbricht, J. Membr. Sci., 2020, 598, 117761 CrossRef CAS.
- P. Goh and A. Ismail, Desalination, 2018, 434, 60–80 CrossRef CAS.
- M. Amirilargani, M. Sadrzadeh, E. Sudhölter and L. De Smet, Chem. Eng. J., 2016, 289, 562–582 CrossRef CAS.
- Y. Wen, J. Yuan, X. Ma, S. Wang and Y. Liu, Environ. Chem. Lett., 2019, 17, 1539–1551 CrossRef CAS.
- S. Bandehali, H. Sanaeepur, A. E. Amooghin, S. Shirazian and S. Ramakrishna, Sep. Purif. Technol., 2021, 269, 118731 CrossRef CAS.
- F. Abuhantash, Y. H. Abuhasheesh, H. M. Hegab, I. H. Aljundi, F. Al Marzooqi and S. W. Hasan, J. Water Proc. Eng., 2023, 56, 104310 CrossRef.
- S. Karki, G. Hazarika, D. Yadav and P. G. Ingole, Desalination, 2023, 117200 Search PubMed.
- R. Majumdar, U. Mishra and B. Bhunia, Adv. Funct. Membr. Mater. Appl, 2022, 120, 43–71 CAS.
- Q. Yang, N. Adrus, F. Tomicki and M. Ulbricht, J. Mater. Chem., 2011, 21, 2783–2811 RSC.
- M. Jiang, C. Jing, C. Lei, X. Han, Y. Wu, S. Ling, Y. Zhang, Q. Li, H. Yu and S. Liu, Nat Sustainability, 2024, 1–11 CAS.
- T. M. Joseph, H. E. Al-Hazmi, B. Śniatała, A. Esmaeili and S. Habibzadeh, Environ. Res., 2023, 117114 CrossRef CAS PubMed.
-
M. T. Simiyu, Investigation of the Point-of-use Water Purification Efficacy of Fabricated Diatomaceous Earth-based Filter Membranes With Static Magnetic Field, Doctoral dissertation, University of Nairobi, 2022 Search PubMed.
- I. Ali, S. Z. Hasan, H. Garcia, M. K. Danquah and G. Imanova, Chem. Eng. J., 2024, 149108 CrossRef CAS.
- M. Paul and S. D. Jons, Polymer, 2016, 103, 417–456 CrossRef CAS.
- A. K. Ghosh and E. M. Hoek, J. Membr. Sci., 2009, 336, 140–148 CrossRef CAS.
- S. C. Mamah, P. S. Goh, A. F. Ismail, N. D. Suzaimi, L. T. Yogarathinam, Y. O. Raji and T. H. El-badawy, J. Water Proc. Eng., 2021, 40, 101835 CrossRef.
- O. Dumbrava, A. Filimon and L. Marin, Eur. Polym. J., 2023, 112316 CrossRef CAS.
- S. Kheirieh, M. Asghari and M. Afsari, Rev. Chem. Eng., 2018, 34, 657–693 CAS.
- A. Khan, T. A. Sherazi, Y. Khan, S. Li, S. A. R. Naqvi and Z. Cui, J. Membr. Sci., 2018, 554, 71–82 CrossRef CAS.
- V. Kumari, P. P. Singh and S. Kaushal, Polyhedron, 2022, 214, 115645 CrossRef CAS.
- S. A. E. Naser, K. O. Badmus and L. Khotseng, Coatings, 2023, 13, 1456 CrossRef CAS.
- I. Mahar, F. H. Memon, J.-W. Lee, K. H. Kim, R. Ahmed, F. Soomro, F. Rehman, A. A. Memon, K. H. Thebo and K. H. Choi, Membranes, 2021, 11, 869 CrossRef CAS PubMed.
- M. K. Shahzad, F. H. Memon, F. Soomro, M. Iqbal, A. Ibrar, A. A. Memon, J. H. Lim, K. H. Choi and K. H. Thebo, J. Environ. Chem. Eng., 2023, 11, 109329 CrossRef CAS.
- F. Rehman, F. Hussain Memon, S. Ullah, M. A. Jafar Mazumder, A. Al-Ahmed, F. Khan and K. Hussain Thebo, Chem. Rec., 2022, 22, e202200107 CrossRef CAS PubMed.
- I. Mahar, F. K. Mahar, N. Mahar, A. A. Memon, A. A. A. Pirzado, Z. Khatri, K. H. Thebo and A. Ali, Chem. Eng. Res. Des., 2023, 191, 462–471 CrossRef CAS.
- U. Kamran, K. Y. Rhee, S.-Y. Lee and S.-J. Park, Chemosphere, 2022, 135590 CrossRef CAS PubMed.
- F. Rehman, F. H. Memon, Z. Bhatti, M. Iqbal, F. Soomro, A. Ali and K. H. Thebo, Rev. Inorg. Chem., 2022, 42, 327–336 CrossRef CAS.
- A. H. Jatoi, K. H. Kim, M. A. Khan, F. H. Memon, M. Iqbal, D. Janwery, S. N. Phulpoto, A. Samantasinghar, K. H. Choi and K. H. Thebo, RSC Adv., 2023, 13, 12695–12702 RSC.
- J. Zhou, K. Li, Z. Chen, X. Su, H. Xie, L. Yao, Y. Wu, X. Zhang, L. Chen and X. Wu, J. Environ. Chem. Eng., 2023, 11, 109840 CrossRef CAS.
- J. M. Luque-Alled, S. Leaper, A. Abdel-Karim, C. Skuse and P. Gorgojo, J. Environ. Chem. Eng., 2023, 11, 109898 CrossRef CAS.
- G. Zhao and H. Zhu, Adv. Mater., 2020, 32, 1905756 CrossRef CAS PubMed.
- W. Czepa, D. Pakulski, S. Witomska, V. Patroniak, A. Ciesielski and P. Samori, Carbon, 2020, 158, 193–201 CrossRef CAS.
- K. H. Thebo, X. Qian, Q. Wei, Q. Zhang, H.-M. Cheng and W. Ren, J. Mater. Sci. Technol., 2018, 34, 1481–1486 CrossRef CAS.
- A. H. Jatoi, A. Ali, A. Nadeem, S. N. Phulpoto, M. Iqbal, A. A. Memon, J. Yang and K. H. Thebo, New J. Chem., 2024, 48, 1715–1723 RSC.
- M.-U.-N. Khilji, A. A. Otho, R. Memon, A. Khalid, M. Kazi, A. Hyder, D. Janwery, N. A. Nahyoon, A. A. Memon and N. Memon, Anal. Lett., 2023, 1–18 CrossRef.
- T. Lee and B.-S. Kim, ACS Appl. Mater. Interfaces, 2020, 12, 13116–13126 CrossRef CAS PubMed.
- M. Fathizadeh, W. L. Xu, F. Zhou, Y. Yoon and M. Yu, Adv. Mater. Interfaces, 2017, 4, 1600918 CrossRef.
- J. Zhu, J. Hou, A. Uliana, Y. Zhang, M. Tian and B. Van der Bruggen, J. Mater. Chem. A, 2018, 6, 3773–3792 RSC.
- F. A. Janjhi, D. Janwery, I. Chandio, S. Ullah, F. Rehman, A. A. Memon, J. Hakami, F. Khan, G. Boczkaj and K. H. Thebo, ChemBioEng Rev., 2022, 9, 574–590 CrossRef CAS.
- Z. Xu, J. Zhang, M. Shan, Y. Li, B. Li, J. Niu, B. Zhou and X. Qian, J. Membr. Sci., 2014, 458, 1–13 CrossRef CAS.
- A. Modi and J. Bellare, J. Environ. Chem. Eng., 2019, 7, 102944 CrossRef.
- S. S. Rahman, M. Arshad, M. Zubair, M. Ghasri-Khouzani, A. Qureshi and A. Ullah, Mater. Today Commun., 2020, 25, 101633 CrossRef CAS.
- A. Alkhouzaam, H. Qiblawey and M. Khraisheh, Membranes, 2021, 11, 86 CrossRef CAS PubMed.
- A. S. Lashkenari, M. T. H. Mosavian, M. Peyravi and M. Jahanshahi, Prog. Org. Coat., 2019, 129, 147–158 CrossRef.
- C. Bărdacă Urducea, A. C. Nechifor, I. A. Dimulescu, O. Oprea, G. Nechifor, E. E. Totu, I. Isildak, P. C. Albu and S. G. Bungău, Nanomaterials, 2020, 10, 2349 CrossRef PubMed.
- N. D. Suzaimi, P. S. Goh, K. C. Wong, N. A. N. N. Malek, A. F. Ismail and J. W. Lim, J. Membr. Sci., 2022, 657, 120706 CrossRef CAS.
- L. Yu, M. Kanezashi, H. Nagasawa and T. Tsuru, J. Membr. Sci., 2020, 595, 117477 CrossRef CAS.
- M. Rezakazemi, M. Sadrzadeh and T. Matsuura, Prog. Energy Combust. Sci., 2018, 66, 1–41 CrossRef.
- J.-J. Qin, S. Chen, M. H. Oo, K. A. Kekre, E. R. Cornelissen and C. J. Ruiken, Water Sci. Technol., 2010, 61, 2897–2904 CrossRef CAS PubMed.
- C. Barth, M. Goncalves, A. Pires, J. Roeder and B. Wolf, J. Membr. Sci., 2000, 169, 287–299 CrossRef CAS.
- L.-P. Cheng, D.-J. Lin and K.-C. Yang, J. Membr. Sci., 2000, 172, 157–166 CrossRef CAS.
- L. Martínez-Izquierdo, M. Malankowska, C. Téllez and J. Coronas, J. Environ. Chem. Eng., 2021, 9, 105624 CrossRef.
- I. V. Maggay, M.-L. Yu, D.-M. Wang, C.-H. Chiang, Y. Chang and A. Venault, J. Membr. Sci., 2022, 655, 120597 CrossRef CAS.
- V. Mokkapati, D. Y. Koseoglu-Imer, N. Yilmaz-Deveci, I. Mijakovic and I. Koyuncu, RSC Adv., 2017, 7, 4378–4386 RSC.
- A. Moosa and M. Abed, Turk. J. Chem., 2021, 45, 493–519 CrossRef CAS PubMed.
- B. C. Brodie, Philos. Trans. R. Soc. London, 1859, 249–259 Search PubMed.
- L. Staudenmaier, Ber. Dtsch. Chem. Ges., 1898, 31, 1481–1487 CrossRef CAS.
- U. Hoffmann and E. Koenig, Z. Anorg. Allg. Chem., 1937, 234, 311–336 CrossRef.
- S. William, J. Hummers and R. E. Offeman, J. Am. Chem. Soc., 1958, 80, 1339 CrossRef.
- K. Bansal, J. Singh and A. Dhaliwal, IOP Conf. Ser.: Mater. Sci. Eng., 2022, 1225, 012050 Search PubMed.
- D. C. Marcano, D. V. Kosynkin, J. M. Berlin, A. Sinitskii, Z. Sun, A. Slesarev, L. B. Alemany, W. Lu and J. M. Tour, ACS Nano, 2010, 4, 4806–4814 CrossRef CAS PubMed.
- Z. Benzait, P. Chen and L. Trabzon, Nanoscale Adv., 2021, 3, 223–230 RSC.
- R. Mukherjee, P. Bhunia and S. De, Chem. Eng. J., 2016, 292, 284–297 CrossRef CAS.
- A. M. Nasir, P. S. Goh, M. S. Abdullah, B. C. Ng and A. F. Ismail, Chemosphere, 2019, 232, 96–112 CrossRef CAS PubMed.
-
T. Sandle, Sterility, Sterilisation and Sterility Assurance for Pharmaceuticals, 2013, pp. 143–155 Search PubMed.
- R. Zhang, J. Tian, S. Gao and B. Van der Bruggen, J. Mater. Chem. A, 2020, 8, 8831–8847 RSC.
- A. Seidel, J. J. Waypa and M. Elimelech, Environ. Eng. Sci., 2001, 18, 105–113 CrossRef CAS.
- A. Suárez and F. A. Riera, Desalin. Water Treat., 2016, 57, 24176–24186 CrossRef.
- S. Yadav, I. Ibrar, A. K. Samal, A. Altaee, S. Déon, J. Zhou and N. Ghaffour, J. Hazard. Mater., 2022, 421, 126744 CrossRef CAS PubMed.
- A. R. Nadig, N. S. Naik, M. Padaki, R. K. Pai and S. Déon, J. Water Proc. Eng., 2021, 41, 102026 CrossRef.
- A. E. Yaroshchuk, Adv. Colloid Interface Sci., 2000, 85, 193–230 CrossRef CAS PubMed.
- M. Fernández de Labastida and A. Yaroshchuk, Membranes, 2021, 11, 272 CrossRef PubMed.
- M. Kotobuki, Q. Gu, L. Zhang and J. Wang, Molecules, 2021, 26, 3331 CrossRef CAS PubMed.
- G. Liu, W. Jin and N. Xu, Angew. Chem., Int. Ed., 2016, 55, 13384–13397 CrossRef CAS PubMed.
- A. Bakshi, H. Bustamante, X. Sui and R. Joshi, Ind. Eng. Chem. Res., 2021, 60, 10917–10959 CrossRef CAS.
- L. Badrinezhad, S. Ghasemi, Y. Azizian-Kalandaragh and A. Nematollahzadeh, Polym. Bull., 2018, 75, 469–484 CrossRef CAS.
- N. A. Elessawy, J. Exley, D. S. El-Sayed, A. Toghan, S. A. Al-Hussain, M. Elzokm, A. H. Konsowa and M. Tillotson, J. Environ. Chem. Eng., 2024, 12, 112489 CrossRef CAS.
- Y. Jiang, Q. Zeng, P. Biswas and J. D. Fortner, J. Membr. Sci., 2019, 581, 453–461 CrossRef CAS.
- S. Sali, H. R. Mackey and A. A. Abdala, Nanomaterials, 2019, 9, 769 CrossRef PubMed.
- J. Prince, S. Bhuvana, V. Anbharasi, N. Ayyanar, K. Boodhoo and G. Singh, Water Res., 2016, 103, 311–318 CrossRef CAS PubMed.
- Y. Liu, F. Zhang, W. Zhu, D. Su, Z. Sang, X. Yan, S. Li, J. Liang and S. X. Dou, Carbon, 2020, 160, 88–97 CrossRef CAS.
- A. Alammar, S.-H. Park, C. J. Williams, B. Derby and G. Szekely, J. Membr. Sci., 2020, 603, 118007 CrossRef CAS.
- T. D. Kusworo, F. Dalanta, N. Aryanti and N. H. Othman, J. Water Proc. Eng., 2021, 41, 102030 CrossRef.
- A. Alkhouzaam and H. Qiblawey, J. Membr. Sci., 2021, 620, 118900 CrossRef CAS.
- A. Modi, S. K. Verma and J. Bellare, Mater. Sci. Eng., C, 2018, 91, 524–540 CrossRef CAS PubMed.
- F. Chen, X. Shi, X. Chen and W. Chen, J. Membr. Sci., 2018, 552, 295–304 CrossRef CAS.
- A. Modi, S. K. Verma and J. Bellare, Colloids Surf., B, 2018, 167, 457–467 CrossRef CAS PubMed.
- Y. Cai, D. Chen, N. Li, Q. Xu, H. Li, J. He and J. Lu, J. Membr. Sci., 2017, 543, 10–17 CrossRef CAS.
- B. Chakrabarty, A. Ghoshal and M. Purkait, J. Membr. Sci., 2008, 325, 427–437 CrossRef CAS.
- R. Vaghasia, B. Saini and A. Dey, J. Mol. Liq., 2022, 359, 119346 CrossRef CAS.
- Y. Wu, R. Yao, X. Zhang, B. Zhang and T. Wang, J. Environ. Chem. Eng., 2021, 9, 105164 CrossRef CAS.
- S. Zhao, Z. Wang, J. Wang and S. Wang, J. Membr. Sci., 2014, 469, 316–325 CrossRef CAS.
- S. Nasseri, S. Ebrahimi, M. Abtahi and R. Saeedi, J. Environ. Manage., 2018, 205, 174–182 CrossRef CAS PubMed.
- V. Kochkodan and N. Hilal, Desalination, 2015, 356, 187–207 CrossRef CAS.
- M. Rezakazemi, A. Dashti, H. Riasat Harami and N. Hajilari, Environ. Chem. Lett., 2018, 16, 715–763 CrossRef CAS.
- Z. Wang, J. Jin, D. Hou and S. Lin, J. Membr. Sci., 2016, 516, 113–122 CrossRef CAS.
- V. Vatanpour, A. Shockravi, H. Zarrabi, Z. Nikjavan and A. Javadi, J. Ind. Eng. Chem., 2015, 30, 342–352 CrossRef CAS.
- M. J. Park, S. Phuntsho, T. He, G. M. Nisola, L. D. Tijing, X.-M. Li, G. Chen, W.-J. Chung and H. K. Shon, J. Membr. Sci., 2015, 493, 496–507 CrossRef CAS.
- M. Shaban, H. AbdAllah, L. Said, H. S. Hamdy and A. A. Khalek, Chem. Eng. Res. Des., 2015, 95, 307–316 CrossRef CAS.
- O. Abdalla, M. A. Wahab and A. Abdala, J. Environ. Chem. Eng., 2020, 8, 104269 CrossRef CAS.
- A. Romero, M. Lavin-Lopez, L. Sanchez-Silva, J. Valverde and A. Paton-Carrero, Mater. Chem. Phys., 2018, 203, 284–292 CrossRef CAS.
- S. Zinadini, A. A. Zinatizadeh, M. Rahimi, V. Vatanpour and H. Zangeneh, J. Membr. Sci., 2014, 453, 292–301 CrossRef CAS.
- M. L. Pedersen, T. R. Jensen, S. V. Kucheryavskiy and M. E. Simonsen, J. Photochem. Photobiol., A, 2018, 366, 162–170 CrossRef CAS.
- S. Kim, D. E. Heath and S. E. Kentish, Desalination, 2023, 548, 116277 CrossRef CAS.
- L. Mérai, Á. Deák, I. Dékány and L. Janovák, Adv. Colloid Interface Sci., 2022, 303, 102657 CrossRef PubMed.
- P. G. Torres-Valenzuela, J. Álvarez-Sánchez, G. E. Dévora-Isiordia, M. M. Armendáriz-Ontiveros, M. del Rosario Martínez-Macias, S. Pérez-Sicairos, R. G. Sánchez-Duarte and G. A. Fimbres Weihs, Polym. Bull., 2023, 80, 6285–6306 CrossRef CAS.
- L. Song, J. Membr. Sci., 1998, 139, 183–200 CrossRef CAS.
- M. S. Ramasamy, A. Rahaman and B. Kim, Ceram. Int., 2021, 47, 11010–11021 CrossRef.
- T. Virtanen, G. Rudolph, A. Lopatina, B. Al-Rudainy, H. Schagerlöf, L. Puro, M. Kallioinen and F. Lipnizki, Sci. Rep., 2020, 10, 3427 CrossRef CAS PubMed.
- A. Kovtun, M. Zambianchi, C. Bettini, A. Liscio, M. Gazzano, F. Corticelli, E. Treossi, M. L. Navacchia, V. Palermo and M. Melucci, Nanoscale, 2019, 11, 22780–22787 RSC.
- N. Lekena, T. A. Makhetha and R. M. Moutloali, J. Environ. Chem. Eng., 2023, 11(5), 110883 CrossRef CAS.
- Q. Gao, L. Duan, Y. Jia, H. Zhang, J. Liu and W. Yang, Membranes, 2023, 13, 837 CrossRef CAS PubMed.
- L. Jaber, I. W. Almanassra, A. AbuShawish, A. Chatla, I. Ihsanullah, M. M. Ali, Y. Manawi, A. Shanableh and M. A. Atieh, J. Membr. Sci., 2024, 691, 122259 CrossRef CAS.
- V. Vatanpour, S. S. Madaeni, R. Moradian, S. Zinadini and B. Astinchap, J. Membr. Sci., 2011, 375, 284–294 CrossRef CAS.
- D. Rana and T. Matsuura, Chem. Rev., 2010, 110, 2448–2471 CrossRef CAS PubMed.
- A. Razmjou, J. Mansouri and V. Chen, J. Membr. Sci., 2011, 378, 73–84 CrossRef CAS.
- X. Chen, E. Deng, D. Park, B. A. Pfeifer, N. Dai and H. Lin, ACS Appl. Mater. Interfaces, 2020, 12, 48179–48187 CrossRef CAS PubMed.
- J. Liang, Y. Tan, Y. Yu, Y. Hu and C. Liao, Polym. Adv. Technol., 2023, 34, 1575–1584 CrossRef CAS.
- M. Hu and B. Mi, Environ. Sci. Technol., 2013, 47, 3715–3723 CrossRef CAS PubMed.
- A. Rossi, M. Zannotti, M. Cuccioloni, M. Minicucci, L. Petetta, M. Angeletti and R. Giovannetti, Nanomaterials, 2021, 11, 1733 CrossRef CAS PubMed.
- X. Cao, C. Ma, J. Zhao, H. Guo, Y. Dai, Z. Wang and B. Xing, Sci. Total Environ., 2019, 679, 270–278 CrossRef CAS PubMed.
- F. A. A. Ali, J. Alam, A. K. Shukla, M. Alhoshan, M. A. Ansari, W. A. Al-Masry, S. Rehman and M. Alam, React. Funct. Polym., 2019, 140, 136–147 CrossRef CAS.
- N. S. Suhalim, N. Kasim, E. Mahmoudi, I. J. Shamsudin, N. L.-A. Jamari and F. Mohamed Zuki, Membranes, 2023, 13, 602 CrossRef CAS PubMed.
- L. Yu, W. Zhou, Y. Li, Q. Zhou, H. Xu, B. Gao and Z. Wang, ACS Sustain. Chem. Eng., 2019, 7, 8724–8734 CrossRef CAS.
- Y. T. Chung, E. Mahmoudi, A. W. Mohammad, A. Benamor, D. Johnson and N. Hilal, Desalination, 2017, 402, 123–132 CrossRef CAS.
- R. Huang, S. Zhang, W. Zhang and X. Yang, IET Collaborative Intelligent Manufacturing, 2021, 3, 281–289 CrossRef.
- S. Balta, A. Sotto, P. Luis, L. Benea, B. Van der Bruggen and J. Kim, J. Membr. Sci., 2012, 389, 155–161 CrossRef CAS.
- R. Rajakumaran, M. Kumar and R. Chetty, Desalination, 2020, 495, 114673 CrossRef CAS.
- V. Mokkapati, D. Y. K. Imer, N. Yilmaz, V. Ozguz and I. Koyuncu, RSC Adv., 2015, 5, 71011–71021 RSC.
- M. Safarpour, A. Khataee and V. Vatanpour, Ind. Eng. Chem. Res., 2014, 53, 13370–13382 CrossRef CAS.
- Y. T. Chung, L. Y. Ng and A. W. Mohammad, J. Ind. Eng. Chem., 2014, 20, 1549–1557 CrossRef CAS.
- M. J. Hajipour, K. M. Fromm, A. A. Ashkarran, D. J. de Aberasturi, I. R. de Larramendi, T. Rojo, V. Serpooshan, W. J. Parak and M. Mahmoudi, Trends Biotechnol., 2012, 30, 499–511 CrossRef CAS PubMed.
- A. Sirelkhatim, S. Mahmud, A. Seeni, N. H. M. Kaus, L. C. Ann, S. K. M. Bakhori, H. Hasan and D. Mohamad, Nano-Micro Lett., 2015, 7, 219–242 CrossRef CAS PubMed.
- A. Akbar, M. B. Sadiq, I. Ali, N. Muhammad, Z. Rehman, M. N. Khan, J. Muhammad, S. A. Khan, F. U. Rehman and A. K. Anal, Biocatal. Agric. Biotechnol., 2019, 17, 36–42 CrossRef.
- G. Fan, J. Ge, H.-Y. Kim, B. Ding, S. S. Al-Deyab, M. El-Newehy and J. Yu, RSC Adv., 2015, 5, 64318–64325 RSC.
- Q. Huang, Z. Ding, H. Lu, M. Geng, J. Liu, M. Meng, Z. Liu, Y. Liu and J. Pan, Sep. Purif. Technol., 2023, 325, 124694 CrossRef CAS.
- A. Pattammattel, M. Puglia, S. Chakraborty, I. K. Deshapriya, P. K. Dutta and C. V. Kumar, Langmuir, 2013, 29, 15643–15654 CrossRef CAS PubMed.
- G. S. Prihandana, T. Sriani, A. D. Muthi’ah, A. Machmudah, M. Mahardika and N. Miki, Nanomaterials, 2022, 12, 388 CrossRef CAS PubMed.
- S. S. Hosseini, E. Bringas, N. R. Tan, I. Ortiz, M. Ghahramani and M. A. A. Shahmirzadi, J. Water Proc. Eng., 2016, 9, 78–110 CrossRef.
- O. Abdalla, A. Rehman, A. Nabeeh, M. A. Wahab, A. Abdel-Wahab and A. Abdala, Membranes, 2023, 13, 678 CrossRef CAS PubMed.
- V. K. Thakur and S. I. Voicu, Carbohydr. Polym., 2016, 146, 148–165 CrossRef CAS PubMed.
- J. Liu, C. Zhao, Z. Zhang, J. Liao, Y. Liu, X. Cao, J. Yang, Y. Yang and N. Liu, Chem. Eng. J., 2016, 288, 505–515 CrossRef CAS.
- L. Ghasemi-Mobarakeh, M. P. Prabhakaran, L. Tian, E. Shamirzaei-Jeshvaghani, L. Dehghani and S. Ramakrishna, World J. Stem Cell., 2015, 7, 728 CrossRef PubMed.
- K. I. John, M. O. Omorogie, A. A. Bayode, A. T. Adeleye and B. Helmreich, Chem. Pap., 2023, 77, 657–676 CrossRef CAS.
- M. Kasbaji, M. Mennani, A. Boussetta, N. Grimi, F. J. Barba, M. Mbarki and A. Moubarik, Sep. Sci. Technol., 2023, 58, 221–240 CrossRef CAS.
- T. D. Kusworo, H. Susanto, N. Aryanti, N. Rokhati, I. N. Widiasa, H. Al-Aziz, D. P. Utomo, D. Masithoh and A. C. Kumoro, J. Environ. Chem. Eng., 2021, 9, 105066 CrossRef CAS.
- R. Hu, G. Zhao, Y. He and H. Zhu, Desalination, 2020, 477, 114271 CrossRef CAS.
- X. Luo, Q. Yan, C. Wang, C. Luo, N. Zhou and C. Jian, Int. J. Environ. Res. Public Health, 2015, 12, 11975–11987 CrossRef CAS PubMed.
- S. J. Ajeel, A. A. Beddai and A. M. N. Almohaisen, Mater. Today: Proc., 2022, 51, 289–297 CAS.
- A. T. Yasir, A. Benamor, M. Ba-Abbad and A. H. Hawari, J. Water Proc. Eng., 2024, 60, 105095 CrossRef.
- Y. Tamer, M. D. Özeren and H. Berber, J. Polym. Environ., 2021, 29, 4000–4016 CrossRef CAS.
- J. Ma, M. Zhang, M. Ji, L. Zhang, Z. Qin, Y. Zhang, L. Gao and T. Jiao, Int. J. Biol. Macromol., 2021, 193, 2221–2231 CrossRef CAS PubMed.
- Y. Tamer, A. Koşucu and H. Berber, Int. J. Biol. Macromol., 2022, 219, 273–289 CrossRef CAS PubMed.
- R. Castaldo, R. Avolio, M. Cocca, M. E. Errico, M. Lavorgna, J. Šalplachta, C. Santillo and G. Gentile, Chem. Eng. J., 2022, 430, 133162 CrossRef CAS.
- Z. Yang, X. Liu, X. Liu, J. Wu, X. Zhu, Z. Bai and Z. Yu, Colloids Surf., B, 2021, 200, 111605 CrossRef CAS PubMed.
- L. Lentz, D. A. Mayer, M. Dogenski and S. R. S. Ferreira, Mater. Chem. Phys., 2022, 283, 125981 CrossRef CAS.
- B. Chen, Y. Li, M. Li, M. Cui, W. Xu, L. Li, Y. Sun, M. Wang, Y. Zhang and K. Chen, Microporous Mesoporous Mater., 2021, 328, 111457 CrossRef CAS.
- Y. Tamer and H. Berber, J. Macromol. Sci., Part A: Pure Appl.Chem., 2022, 1–14 Search PubMed.
- N. Jahan, H. Roy, A. H. Reaz, S. Arshi, E. Rahman, S. H. Firoz and M. S. Islam, Case Stud. Chem. Environ. Eng., 2022, 6, 100239 CrossRef CAS.
- I. H. Alsohaimi, M. S. Alhumaimess, A. A. Alqadami, G. T. Alshammari, R. F. Al-Olaimi, A. A. Abdeltawab, M. Y. El-Sayed and H. M. Hassan, Inorg. Chem. Commun., 2023, 147, 110261 CrossRef.
- G. Natesan and K. Rajappan, Environ. Sci. Pollut. Res., 2023, 30, 42658–42678 CrossRef CAS PubMed.
- D. R. Rout and H. M. Jena, Environ. Res., 2022, 214, 114044 CrossRef CAS PubMed.
- S. J. Kim, S. H. Ko, K. H. Kang and J. Han, Nat. Nanotechnol., 2010, 5, 297–301 CrossRef CAS PubMed.
- C. Shivalingam, L. Mohan, D. Ganapathy, R. Shanmugam, S. Pitchiah, R. Ramadoss and A. K. Sundramoorthy, Curr. Anal. Chem., 2022, 18, 989–998 CrossRef CAS.
- H. Wang, W. Wang, L. Wang, B. Zhao, Z. Zhang, X. Xia, H. Yang, Y. Xue and N. Chang, Chem. Eng. J., 2018, 334, 2068–2078 CrossRef CAS.
- K. Y. Wang and T. S. Chung, AIChE J., 2006, 52, 1363–1377 CrossRef CAS.
- T.-S. Chung, X. Li, R. C. Ong, Q. Ge, H. Wang and G. Han, Curr. Opin. Chem. Eng., 2012, 1, 246–257 CrossRef CAS.
- T. Y. Cath, S. Gormly, E. G. Beaudry, M. T. Flynn, V. D. Adams and A. E. Childress, J. Membr. Sci., 2005, 257, 85–98 CrossRef CAS.
- R. W. Holloway, A. E. Childress, K. E. Dennett and T. Y. Cath, Water Res., 2007, 41, 4005–4014 CrossRef CAS PubMed.
- H. Salehi, A. Shakeri and S. R. Razavi, ACS ES&T Water, 2022, 2, 508–517 Search PubMed.
- L. Chekli, S. Phuntsho, H. K. Shon, S. Vigneswaran, J. Kandasamy and A. Chanan, Desalin. Water Treat., 2012, 43, 167–184 CrossRef CAS.
- S. Phuntsho, H. K. Shon, T. Majeed, I. El Saliby, S. Vigneswaran, J. Kandasamy, S. Hong and S. Lee, Environ. Sci. Technol., 2012, 46, 4567–4575 CrossRef CAS PubMed.
- M. Ganj, M. Asadollahi, S. A. Mousavi, D. Bastani and F. Aghaeifard, J. Polym. Res., 2019, 26, 1–19 CrossRef.
- M. R. S. Emami, M. K. Amiri and S. P. G. Zaferani, Korean J. Chem. Eng., 2021, 38, 316–325 CrossRef CAS.
- P. Babuji, S. Thirumalaisamy, K. Duraisamy and G. Periyasamy, Water, 2023, 15, 2532 CrossRef CAS.
- K. Tulugan, P. Tian, X. Li, W. Zhao, X. Zhang and Y. Zhao, J. Eng. Res., 2024 DOI:10.1016/j.jer.2024.01.001.
- S. Poolachira and S. Velmurugan, Environ. Res., 2022, 210, 112924 CrossRef CAS PubMed.
- F. Zhu, L. Kong, M. He, D. Fang, X. Hu and X. Peng, Water Res., 2023, 243, 120355 CrossRef CAS PubMed.
- A. Maher, M. Sadeghi and A. Moheb, Desalination, 2014, 352, 166–173 CrossRef CAS.
- S. Dhara, A. Sontakke, N. Samanta, M. K. Purkait and R. V. Uppaluri, Sep. Purif. Technol., 2024, 341, 126894 CrossRef CAS.
- P. Sherugar, N. S. Naik, M. Padaki, V. Nayak, A. Gangadharan, A. R. Nadig and S. Déon, Chemosphere, 2021, 275, 130024 CrossRef CAS PubMed.
- N. Politaeva, A. Yakovlev, E. Yakovleva, V. Chelysheva, K. Tarantseva, S. Efremova, L. Mukhametova and S. Ilyashenko, Water, 2022, 14, 1430 CrossRef CAS.
- M. Nasir, Y. Purnama Utami, N. Faaizatunnisa, L. Rohmawati, E. Suebah, A. Taufiq and E. S. Sazali, J. Water Environ. Nanotechnol., 2023, 8, 241–253 CAS.
- I. Akin and E. Zor, J. Environ. Chem. Eng., 2024, 111976 CrossRef CAS.
- M. Khajouei, M. Najafi, S. A. Jafari and M. Latifi, Micromachines, 2023, 14, 128 CrossRef PubMed.
- S. Amiri, V. Vatanpour and T. He, Chemosphere, 2023, 322, 138159 CrossRef CAS PubMed.
- A. M. Alosaimi, Polymers, 2021, 13, 2792 CrossRef CAS PubMed.
- R. Mondal and S. De, Environ. Technol. Innovation, 2022, 26, 102300 CrossRef CAS.
- Y. Liu, Ceram. Int., 2018, 44, 18571–18577 CrossRef CAS.
- X. Hao, S. Yang, E. Tao and Y. Li, J. Hazard. Mater., 2022, 424, 127680 CrossRef CAS PubMed.
- C. Ding and H. Qi, Membranes, 2023, 13, 536 CrossRef CAS PubMed.
- S. Velusamy, A. Roy, S. Sundaram and T. Kumar Mallick, Chem. Rec., 2021, 21, 1570–1610 CrossRef CAS PubMed.
- M. Verma, I. Lee, J. Oh, V. Kumar and H. Kim, Chemosphere, 2022, 287, 132385 CrossRef CAS PubMed.
- Y. Kuang, Z. Zhang and D. Wu, Sci. Total Environ., 2022, 806, 151258 CrossRef CAS PubMed.
- K. Li, T. Xiong, J. Liao, Y. Lei, Y. Zhang and W. Zhu, Chem. Eng. J., 2022, 433, 134449 CrossRef CAS.
- N. Liu, H. Liang, W. Tian, C. Li, Q. Gao, N. Wang, R. Guo and Z. Mo, Colloids Surf., A, 2022, 649, 129367 CrossRef CAS.
- S. Dhara, A. D. Sontakke, N. S. Samanta, R. V. S. Uppaluri and M. K. Purkait, Sep. Purif. Technol., 2024, 126894 CrossRef CAS.
- A. V. Talyzin, G. Mercier, A. Klechikov, M. Hedenström, D. Johnels, D. Wei, D. Cotton, A. Opitz and E. Moons, Carbon, 2017, 115, 430–440 CrossRef CAS.
- A. S. Kuzenkova, A. Y. Romanchuk, A. L. Trigub, K. I. Maslakov, A. V. Egorov, L. Amidani, C. Kittrell, K. O. Kvashnina, J. M. Tour and A. V. Talyzin, Carbon, 2020, 158, 291–302 CrossRef CAS.
- K. Erickson, R. Erni, Z. Lee, N. Alem, W. Gannett and A. Zettl, Adv. Mater., 2010, 22, 4467–4472 CrossRef CAS PubMed.
-
H.-P. Boehm, A. Clauss, G. Fischer and U. Hofmann, Proceedings of the Fifth Conference on Carbon, 1962 Search PubMed.
- A. G. Klechikov, G. Mercier, P. Merino, S. Blanco, C. Merino and A. V. Talyzin, Microporous Mesoporous Mater., 2015, 210, 46–51 CrossRef CAS.
- A. V. Talyzin, T. Szabó, I. Dékány, F. Langenhorst, P. S. Sokolov and V. L. Solozhenko, J. Phys. Chem. C, 2009, 113, 11279–11284 CrossRef CAS.
- A. Klechikov, J. Sun, G. Hu, M. Zheng, T. Wågberg and A. V. Talyzin, Microporous Mesoporous Mater., 2017, 250, 27–34 CrossRef CAS.
- N. Boulanger, A. S. Kuzenkova, A. Iakunkov, A. Y. Romanchuk, A. L. Trigub, A. V. Egorov, S. Bauters, L. Amidani, M. Retegan and K. O. Kvashnina, ACS Appl. Mater. Interfaces, 2020, 12, 45122–45135 CrossRef CAS PubMed.
- K. S. Kim, Y. Zhao, H. Jang, S. Y. Lee, J. M. Kim, K. S. Kim, J.-H. Ahn, P. Kim, J.-Y. Choi and B. H. Hong, Nature, 2009, 457, 706–710 CrossRef CAS PubMed.
- Y. Huang, L. Taylor, X. Chen and N. Ayres, J. Polym. Sci., Part A: Polym. Chem., 2013, 51, 5230–5238 CrossRef CAS.
- Y. Zhao, J. Li, L. Zhao, S. Zhang, Y. Huang, X. Wu and X. Wang, Chem. Eng. J., 2014, 235, 275–283 CrossRef CAS.
- S. Yang, J. Hu, C. Chen, D. Shao and X. Wang, Environ. Sci. Technol., 2011, 45, 3621–3627 CrossRef CAS PubMed.
- H. Chen, D. Shao, J. Li and X. Wang, Chem. Eng. J., 2014, 254, 623–634 CrossRef CAS.
- J.-b. Huo, G. Yu and J. Wang, Chemosphere, 2021, 278, 130492 CrossRef CAS PubMed.
- C. Ursino, R. Castro-Muñoz, E. Drioli, L. Gzara, M. H. Albeirutty and A. Figoli, Membranes, 2018, 8, 18 CrossRef PubMed.
- K. Golzar, S. Amjad-Iranagh, M. Amani and H. Modarress, J. Membr. Sci., 2014, 451, 117–134 CrossRef CAS.
- O. Hölck, M. Böhning, M. Heuchel, M. R. Siegert and D. Hofmann, J. Membr. Sci., 2013, 428, 523–532 CrossRef.
- J. Yang, Z. Shen, J. He and Y. Li, J. Membr. Sci., 2021, 630, 119331 CrossRef CAS.
- C. L. Ritt, J. R. Werber, A. Deshmukh and M. Elimelech, Environ. Sci. Technol., 2019, 53, 6214–6224 CrossRef CAS PubMed.
- Z. Zhang, L. Huang, Y. Wang, K. Yang, Y. Du, Y. Wang, M. J. Kipper, L. A. Belfiore and J. Tang, Phys. Chem. Chem. Phys., 2020, 22, 6032–6057 RSC.
- J. Muscatello, F. Jaeger, O. K. Matar and E. A. Müller, ACS Appl. Mater. Interfaces, 2016, 8, 12330–12336 CrossRef CAS PubMed.
- B. Chen, H. Jiang, X. Liu and X. Hu, J. Phys. Chem. C, 2017, 121, 1321–1328 CrossRef CAS.
- H. Dai, Z. Xu and X. Yang, J. Phys. Chem. C, 2016, 120, 22585–22596 CrossRef CAS.
- H. Zhang, B. Liu, H. T. Kieu, M. S. Wu, K. Zhou and A. W.-K. Law, J. Membr. Sci., 2018, 558, 34–44 CrossRef CAS.
- Y. Kang, M. Obaid, J. Jang, M.-H. Ham and I. S. Kim, Chemosphere, 2018, 207, 581–589 CrossRef CAS PubMed.
- Y. Lou, G. Liu, S. Liu, J. Shen and W. Jin, Appl. Surf. Sci., 2014, 307, 631–637 CrossRef CAS.
- J. Shen, G. Liu, K. Huang, Z. Chu, W. Jin and N. Xu, ACS Nano, 2016, 10, 3398–3409 CrossRef CAS PubMed.
- M. Kumar, N. Sreedhar, N. Thomas, M. Mavukkandy, R. A. Ismail, T. M. Aminabhavi and H. A. Arafat, Chem. Eng. J., 2022, 433, 133526 CrossRef CAS.
|
This journal is © The Royal Society of Chemistry 2024 |