DOI:
10.1039/D3SU00123G
(Tutorial Review)
RSC Sustain., 2023,
1, 1354-1368
A tutorial mini-review on nanoporous carbons from biosourced compounds: ordered hierarchical nanoarchitectures through benign methodologies
Received
22nd April 2023
, Accepted 17th July 2023
First published on 20th July 2023
Abstract
Ordered hierarchically porous carbons exhibiting micro- and mesopores are state-of-the-art porous structures with extraordinary performance in a range of applications (e.g., electrochemistry, catalysis, water treatment). Nevertheless, they are mostly prepared using petroleum-based chemicals, through resource- and energy-intensive, environmentally unfriendly processes. In this tutorial mini-review, we highlight major limitations in the methodologies, and showcase important achievements towards developing more sustainable synthetic strategies. Compared to multi-step hard-templating/nano-casting procedures, soft-templating techniques can provide more efficient, benign, and direct ways to produce these nanostructures. The original soft-templating method, using Pluronic® surfactants as structure-directing agents and phenolic resins as carbon precursors, has been substantially modified over the years in light of sustainability issues. The formaldehyde crosslinker has been replaced with more benign, less toxic alternatives (e.g., glyoxal), and catalyst-free crosslinking approaches have been developed. Furthermore, the use of biobased building-blocks for the carbon precursor, such as lignin, plant-derived polyphenols (e.g., tannins), and various saccharides (e.g., D-glucose, D-fructose), has also been explored. Novel techniques, such as the coordination-induced self-assembly, mechanosynthesis, and modified hydrothermal treatment strategies are amongst the greenest processes developed so far. We give some critical comments on ongoing research in this field and point towards important research directions.
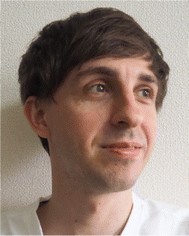 László Szabó | László Szabó received his PhD in 2016 in Chemical Sciences (Budapest University of Technology and Economics, Hungary). He was a Postdoctoral Fellow between 2017 and 2020 in Kanazawa University, and then an ICYS Research Fellow from 2020 to 2022 at the National Institute for Materials Science in Japan. He received a Marie-Curie Fellowship in 2022, and joined the group of Professor Veerle Vandeginste (KU Leuven, Belgium), resulting in this tutorial mini-review. He is now a tenured Senior Researcher at the Forestry and Forest Products Research Institute (Japan). His broad scientific interest lies in benign-by-design, environmentally more friendly materials, and processes. |
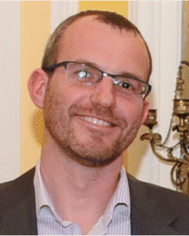 Wim Thielemans | Wim Thielemans received his PhD in Chemical Engineering from the University of Delaware (USA) in 2004. After an MSCA Fellowship at the Institut National Polytechnique de Grenoble (France), he started as a Lecturer in Chemistry and Chemical Engineering at the University of Nottingham (UK) in 2006. After being promoted to Associate Professor, Wim moved to KU Leuven in 2013 where he is now a Full Professor and leads the Sustainable Materials Lab working on renewable materials and recycling strategy developments. Wim is currently Chair of the ACS Cellulose and Renewable Materials division and sits on the KU Leuven Research Council. |
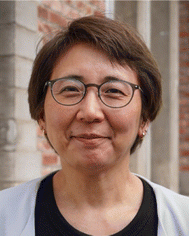 Jin Won Seo | Jin Won Seo graduated from RWTH Aachen and received her PhD in solid state physics at RWTH Aachen and Research Centre Jülich in Germany. She worked at the Electron Microscopy Center EMAT of University of Antwerp in Belgium, at the IBM Zurich Research Laboratory and at the Institute of Physics of Complex Matter IPMC at EPFL in Switzerland. Since 2007, she has been Professor at the Department of Materials Engineering (MTM) of KU Leuven in Belgium. Her research interest focuses on the synthesis, functionalization and application of nanoscale materials, mainly carbon-based nanomaterials and transition metal oxides, as well as on nanoscale characterization, especially by means of electron microscopy. |
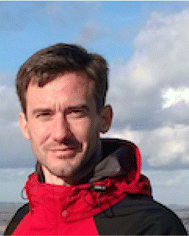 Frank Buysschaert | Frank Buysschaert obtained his PhD degree at the Faculty of Engineering and the Environment of the University of Southampton (UK) in 2015. He worked as a researcher at the Belgian Royal Military Academy and the Université Libre de Bruxelles, Belgium, performing research related to helicopters and fuel cells. In 2019, he joined KU Leuven as an Assistant Professor in the Department of Mechanical Engineering (TME division) with focus on hybrid propulsion systems for aircraft and drones. |
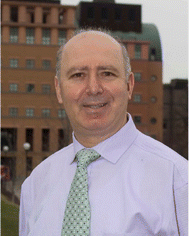 Dionysios D. Dionysiou | Dionysios D. Dionysiou is currently a Herman Schneider Professor of Environmental Engineering and Distinguished Research Professor (STEM) at the University of Cincinnati. He has served as a UNESCO co-Chair Professor on “Water Access and Sustainability”. Professor Dionysiou is leading several projects of local, state, national and international importance focused on water quality, treatment, reuse, and monitoring. His expertise and research interests include (i) physical chemical processes for water treatment and water reuse, (ii) advanced oxidation processes, including UV and solar light-based remediation processes, (iii) treatment of contaminants of emerging concern; (iv) remediation of harmful algal blooms/cyanotoxins, (v) environmental nanotechnology, environmental catalysis, and nanosensing, and (vi) water–energy–food (WEF) nexus and water sustainability. |
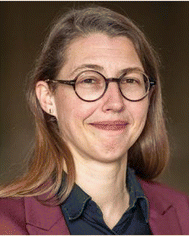 Veerle Vandeginste | Veerle Vandeginste obtained her PhD degree in Geology in 2006 at KU Leuven, Belgium. She worked as a Research Fellow at the Department of Earth Science and Engineering at Imperial College London, UK. In 2015, she was appointed as an Assistant Professor in the School of Chemistry at the University of Nottingham, UK. Since 2020, she is an Associate Professor in the Department of Materials Engineering at KU Leuven. Her research combines sustainability and functionality of materials, focusing on the physicochemical interactions at interfaces in materials for energy storage and conversion devices, advanced coatings, and medical devices. |
Sustainability spotlight
The realisation of a carbon neutral society cannot be achieved with the intense use of petroleum-derived materials. The petroleum refinery sector is one of the biggest CO2 emitters, and hazardous wastes are produced during the processing steps. Thus petroleum-derived materials have large CO2 and environmental footprint. In this tutorial mini-review, we focus on more sustainable ways to produce ordered mesoporous hierarchical nanocarbons. We look at possible ways to replace petroleum-derived components to bio-sourced building blocks, together with the use of less hazardous chemicals, and more energy- and resource-efficient processes to manufacture them. Our paper contributes to our efforts towards “Responsible Consumption and Production” (Sustainable Development Goal (SDG) 12). Furthermore, these advanced nanocarbons have various applications such as in energy storage/conversion systems, water purification, and therefore, this work aligns with several other SDGs as well (SDG7, SDG6). In fact, reducing reliance on petroleum is an important aspect of the climate action (SDG13).
|
1. Introduction
Carbon structures constitute an intriguing class of materials that play a significant role in advancing a sustainable future. For example, carbon fibres help to produce “green” lightweight fuel-efficient composites for the transportation industry that reduce CO2 emission, and graphite is a state-of-the-art carbon used in important energy storage devices (lithium-ion batteries and beyond) or in solar panels to harvest renewable solar energy. Nevertheless, despite carbon being used for green applications, many of these structures in use, or under development, are derived from non-renewable resources (e.g., carbon fibre from petroleum-based precursors, natural graphite through mining or synthetic graphite from petroleum refineries) clearly compromising our sustainability aspirations. Thus, great efforts have been devoted to prepare these relatively “simple” carbon structures using biomass-derived building blocks such as lignin and cellulose.1–3
Nanoporous carbons have a more “complex” architecture compared to common carbon structures, and consequently, it is more difficult (still challenging) to fully characterise them, and to produce well-designed materials for advanced applications. These materials gained considerable interest in charge storage devices such as supercapacitors, owing to the large amount of available surface (sometimes thousands of square meters per gram material) to store energy through electrostatic or electrochemical interactions.4,5 Supercapacitors are expected to be important devices for our sustainable future; they not only help making more efficient energy storage systems, but they are also crucial elements in renewable energy utilisation devices (solar panels, wind turbines, etc.).5,6 Furthermore, nanoporous carbon electrodes are being developed for capacitive deionisation (CDI) devices, a technique with great premises to compete with energy-intensive desalination technologies (e.g., reverse osmosis, distillation) in the future due to its low cost, as well as a reduced energy consumption and lower environmental footprint.7 The need for such systems is expected to become more prevalent in the years to come as climate change pushes us towards severe water shortage problems in every corner of the world. Nanoporous carbons showed outstanding performance and gained appreciable interest as electrodes for the oxygen reduction reaction as well.8,9 In addition, these carbon structures show promise for water purification systems on account of their fascinating photochemical activity,10 and potential for metal-free carbocatalysis.11 For these reasons, nanoporous carbons are expected to be crucial players for a sustainable water–energy nexus in the future (see Fig. 1; water and energy are interdependent resources, i.e., we need energy to produce water and vice versa, this connection is referred to as the “water–energy nexus”).12
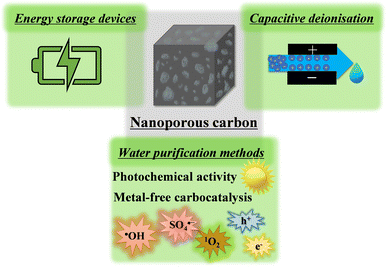 |
| Fig. 1 Some of the emerging applications of nanoporous carbons for supporting a sustainable water–energy nexus. | |
Unfortunately, methods to prepare well-designed ordered nanoporous carbons are mostly limited to environmentally unfriendly technologies with large carbon footprint, involving petroleum-derived often hazardous reactants together with energy- and resource-wasteful processes. Although some progress has been made on using biomass-derived carbon precursors, state-of-the-art ordered nanoporous carbons from biobased building blocks (through sustainable synthesis methods) are still far from being realised. In this tutorial mini-review, we shed light on major challenges in this field, in order to stimulate more research in this direction. Once basic methods are developed, there will be expanding horizons for applications (if we think about the myriad of opportunities residing in doping these nanoporous structures).
2. Tailoring the pore network in nanoporous carbons
The performance of nanoporous carbons greatly depends on the pore network that determines the diffusion of ionic species within its structure, and the accessibility to the active sites. The surface chemistry is also important, governing ionophilicity (wettability) of the pores, determining the presence/absence of faradaic pseudocapacitive or parasitic irreversible reactions in electrochemical applications.4,13 Chromophores or catalytically active moieties on the surface may be advantageous in photochemical and advanced oxidation processes (AOPs).10,11 As an example, persulfate activation, a promising AOP for wastewater treatment,14 has been studied on various carbon materials – the mechanism of activation and the nature of reactive species (e.g., radicals, singlet oxygen or reactive complexes on the surface) were strongly connected to the carbon structure.11 With respect to catalytic groups on the surface – it was shown for example that carbonyl groups play a role in peroxymonosulfate activation on an ordered mesoporous carbon (CMK-3) and on multiwalled carbon nanotubes,15 on carbon spheres,16 and on graphene oxide,17 yielding sulfate radical anions (SO4˙−). Nanoporous carbons can provide an intriguing platform for persulfate activation or for other carbocatalysis processes as well, on account of the possibility of an advantageous cooperative pollutant adsorption–degradation process.18 In addition, in photocatalysis N-, S-, and O-containing groups on nanoporous carbons may act as chromophores.10 Furthermore, the carbon nanostructure determines the electronic properties of the material, and has an influence on charge transfer processes in electrochemical devices.19,20
In general, a hierarchical pore network (Fig. 2) is often considered ideal providing fast diffusion kinetics to the micropores (dp< 2 nm) through a meso-(2 nm < dp< 50 nm)/macroporous (50 nm < dp) system.18,21–23 Hierarchical pore network structures are quite common in Nature. Such design allows efficient mass transport across multiple length scales following Murray's law observed in leaf veins, and in vascular and respiratory systems (Fig. 2A and B).24,25 Materials designed according to this law (coined as Murray materials) can provide exceptional performance in a range of applications (photocatalysis, gas sensing and electrochemical applications) on account of their advantageous mass-transfer properties.25,26 Nature achieved material design with structural control and interactions across multiple length scales through the nano–micro–macro level, leading to advanced functions and properties. Hierarchically designed bioinspired structures are at the forefront of materials science; this topic has been comprehensively addressed in a recent review.27 As a first example, a multi-step process to create a hierarchically designed porous carbon material (Fig. 2C), along with SEM and TEM images on this fabricated scaffold can be seen in Fig. 2D–F. The micrographs highlight the presence of face-centred cubic macropores (Fig. 2E; around 150 nm diameter) with window-like pores (Fig. 2E; 60–80 nm diameter), and mesopores (Fig. 2F; around 18 nm diameter).23 Micropores were created in this meso–macroporous scaffold using KOH activation (by mixing with excess KOH (twice the weight of carbon) in water, followed by thermal treatment under Ar atmosphere at 800 °C). The construction of such architecture usually cannot be achieved in one step as can be seen in Fig. 2C, although this would be certainly desired in consideration of sustainability metrics, such as the E-factor (environmental factor, defined as the mass of waste per mass of product), material- and energy-efficiency.28
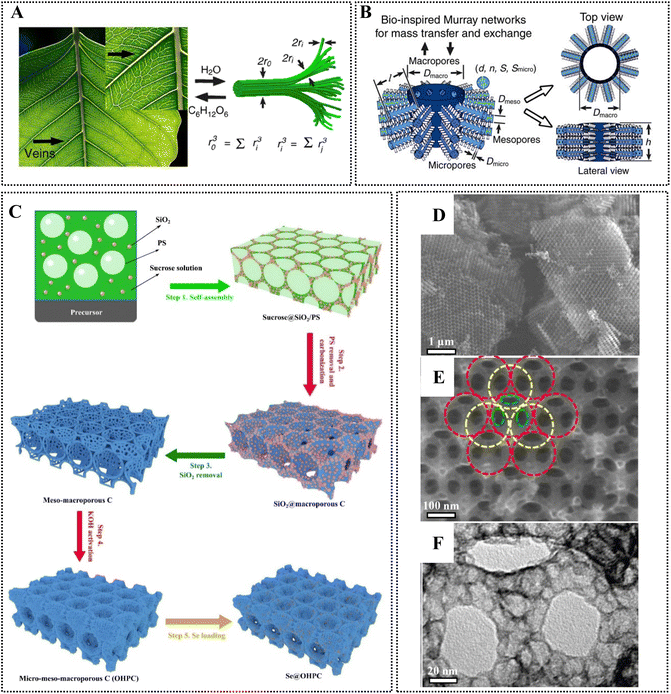 |
| Fig. 2 (A and B) Hierarchically designed pore network to achieve efficient mass transfer following Murray's law.26 (C) A method to prepare hierarchically porous Se-doped carbon as cathode for Li–Se batteries. (D and E) SEM and (F) TEM images of the prepared hierarchically porous material. Reproduced from ref. 23. Copyright 2022 Elsevier. | |
As a more common strategy, mesoporous carbons are designed using soft or hard-templating methods,29,30 and micropores are usually drilled into the wall of these mesopores using various activation methods (chemical or physical activation).31 A frequently adopted soft-templating strategy uses triblock copolymer Pluronic® surfactant micelles as structure directing agents along with the carbon precursor phloroglucinol (Fig. 3A). Micropores are then created into the wall of the mesopores using KOH activation (see the changes in porosity based on N2 adsorption experiments in Fig. 3B). For KOH activation, the mesoporous carbon was impregnated with excess amount of KOH (4 times the weight of carbon) in water first, followed by water evaporation at 100 °C, and then thermal treatment under N2 atmosphere at 700 °C.32 This and similar systems will be at the focus of our later discussions. The robust soft-templating method was originally developed by Liang and Dai in 2006, allowing the large-scale preparation of periodically ordered mesoporous carbons for the first time.33
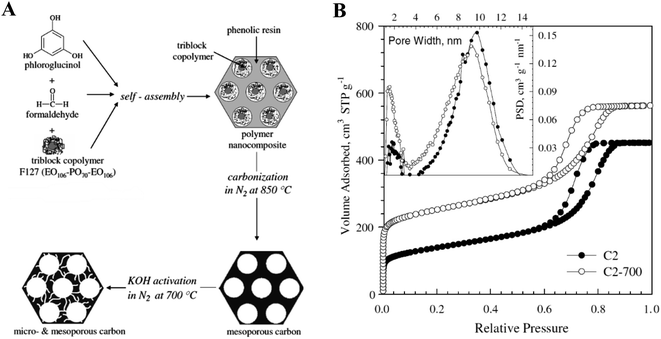 |
| Fig. 3 (A) A common soft-templating system to prepare highly ordered mesoporous carbons, and then micropores on their wall via KOH activation. (B) N2 adsorption–desorption isotherms before (C2) and after the KOH activation step (C2-700) (inset shows the pore size distribution derived from these isotherms). Reproduced from ref. 32 with slight modification. Copyright 2008 Elsevier. | |
Among the activation techniques aimed at creating micropores in various carbon structures, KOH activation has gained much popularity, as it provides one of the most efficient ways to obtain high micropore volume and surface area (can be as high as 3000 m2 g−1). During the process, carbon is mixed with KOH (usually at a weight ratio several times that of the carbon) followed by a thermal treatment under inert atmosphere in a temperature range of around 600–900 °C.34 The resulting activated carbon subsequently needs to be washed thoroughly to remove remaining chemicals. It was proposed that the following events take place during KOH activation: (a) various redox reactions between potassium species and carbon occur, such as in eqn (1)–(3) below; (b) H2O and CO2 formation during the chemical activation contributing to pore evolution processes (these are actually referred to as physical activation processes); (c) the formation of elemental K in-between graphitic layers leading to lattice expansion after removing K during the washing step, further contributing to the microporosity.34 In contrast, physical activation methods that use oxidizing gases, such as CO2, O2, and steam, require higher temperature regimes (∼600–1200 °C), longer time, and yield lower surface area and micropore volume. Nevertheless, KOH is an aggressive chemical agent that needs to be used in excess amount compared to the weight of carbon, and an additional washing step is also needed, which is not the case for physical activation.
| 6KOH + 2C → 2K + 3H2 + 2K2CO3 | (1) |
Periodically ordered mesoporous carbon systems with uniform pore shapes and sizes have gained appreciable interest due to their advantageous and unique properties for various applications. In electrochemical applications for example, it has been shown that ordered mesoporous carbons can have exceptionally high gravimetric capacitance,35 and are also superior in terms of their volumetric performance due to their compact porous structure.36 Moreover, very recent theoretical calculations further confirmed the superiority of an ordered mesoporous system with narrow pore size distribution over that of a disordered porous structure.37 The ordered mesoporous network can spatially confine the electrolyte promoting accelerated diffusion kinetics, and for the disordered porous network it appears that a significant amount of the carbon can be inaccessible for the ions on account of the tortuosity of the pore walls, thus not contributing to charge storage.
According to our present understanding, an ordered mesoporous network with uniform pore sizes that can provide access to the micropores in the walls of the mesopores (i.e., a hierarchical interconnected network), can be considered the epitome of nanoporous carbons with extraordinary performance. These features are important for a range of applications where high surface area (provided by the micropores) and facile mass transport (through a mesoporous network) to the active sites on the surface play a role. Mesopores are large enough for the easy diffusion of molecules, or ions with their hydration shell. Furthermore, ordering in the mesoporous system is beneficial as it can lead to the formation of interconnected mesoporous channels under certain conditions, further enhancing mass transport throughout the material.35,36,38 The applications of such well-designed nanoarchitectures cover a large area of research, e.g., electrochemical storage and conversion, catalysis, adsorption and separation, and biomedical research. Interested readers are directed to comprehensive reviews that detail the applications of hierarchically-structured porous carbons,21 mesoporous carbon nanoarchitectures,39,40 and in particular ordered mesoporous carbons.30,38 To design such nanoarchitectures, petroleum-based precursors and pore-forming agents are at the forefront. The aim of this tutorial mini-review is to highlight environmentally benign processes to fabricate these materials, together with the use of biosourced compounds with low environmental footprint.
3. Biobased nanoporous carbons – top-down vs. bottom-up strategies
As biosourced solutions are coming to the fore in many aspects of materials science, appreciable interest has been sparked for preparing biobased nanoporous carbons as well.21,41–50 Most of the studies in this topic focus on using the entire part of plants (e.g., nut shell),51 microorganisms (e.g., Tremella)52 or animal residues (e.g., fish scale).53 Such source materials are directly carbonised at high temperatures (under inert atmosphere [i.e., pyrolysis], usually above 400 °C by applying low heating rates <10 °C min−1 and several hours holding time at the target temperature),50 followed by an activation process. We may call these approaches “top-down” strategies (Fig. 4, left side). The biobased nanoporous carbons thus prepared can have a hierarchical pore structure with high surface area (>1000 m2 g−1) and pore volume (>0.5 cm3 g−1) thanks to the activation process creating micropores. Nevertheless, highly disordered nanoporous carbons can be achieved in this way, with little or no control on the developing nanoarchitecture, which is mostly determined by the structure of the starting material. Therefore, state-of-the-art controlled carbon nanoarchitectures (e.g., a periodically ordered interconnected meso/microporous scaffold) cannot be realised. To obtain controlled porous nanoarchitectures from biosourced building blocks, we propose “bottom-up” approaches from bio-derived molecular building blocks (Fig. 4, right side). In the following sections, we focus on introducing methods that can be grouped into the bottom-up strategies.
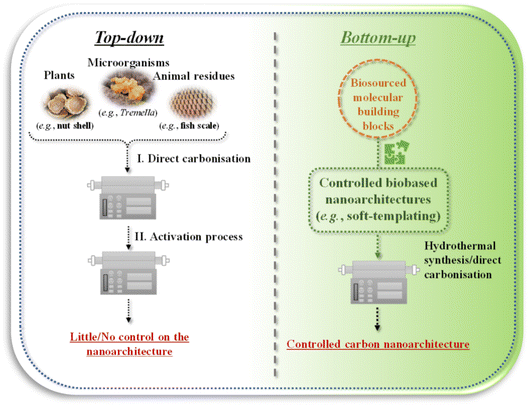 |
| Fig. 4 Different concepts of fabricating biobased nanoporous carbons through (left) “top-down” or (right) “bottom-up” strategies. | |
4. Hierarchically designed ordered mesoporous biobased carbons with micropores via templating methods – emphasis on soft-templating systems
Ordered mesoporous carbons can be fabricated via hard or soft-templating methods. For a typical hard templating method (Fig. 5), an ordered mesoporous silica template is prepared first, from silica/surfactant mesophases (a) after removing the surfactant (b). This hard template is then filled with the carbon precursor (c) and is subjected to a carbonisation process (d). The ordered mesoporous carbon is thus obtained after removing the template (e) via a chemical etching procedure, yielding the negative replica of the original template. In some places this hard-templating method is referred to as a nanocasting strategy. Various biosourced carbon precursors have been explored to successfully prepare ordered mesoporous carbons via the hard-templating method, such as sucrose, glucosamine and furfuryl alcohol.54 Moreover, it was shown that cellulose nanocrystals are able to direct the formation of surfactant/silica mesophases, enabling the room temperature synthesis of highly ordered mesoporous silicas (SBA-15).55 This indicates the possibility of preparing the silica around a carbon precursor directing the porous structure. Nevertheless, we cannot consider the multistep, time-consuming hard-templating method that generates appreciable amount of waste a sustainable approach. Furthermore, during the etching process, concentrated bases (NaOH) or dangerous toxic acids (HF) are used.
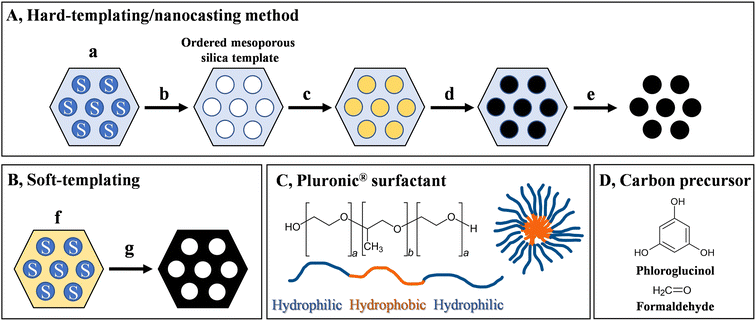 |
| Fig. 5 (A) Hard- vs. (B) soft-templating methods. (C) Pluronic® surfactant and (D) the phloroglucinol–formaldehyde resin as structure directing agent and carbon precursor, respectively, for typical soft-templating methods. | |
A more sustainable, direct way to produce ordered mesoporous carbons is provided by the soft-templating method (Fig. 5B). In this case, carbon precursor-surfactant self-assemblies (f) are directly converted to the ordered mesoporous carbon (g). Such method was first reported by Liang et al. in 2004, based on the self-assembly of polystyrene-block-poly(4-vinylpyridine) block copolymers together with resorcinol-formaldehyde resin as the carbon precursor.56 The introduction of commercially available Pluronic® F127 amphiphilic triblock copolymer (EO106PO70EO106) as micelle-forming structure-directing agent (Fig. 5C) by Tanaka et al.57 led to the widespread application of this method. Later, Liang and Dai33 in 2006 introduced the phloroglucinol–formaldehyde platform (Fig. 5D) as carbon precursor that gained much popularity due to the robustness (wide composition ranges) and mild reaction conditions. It should be noted that compared to the hard-templating methods, these systems are more difficult to realise, as several factors need to be considered to construct such self-assemblies. First of all, (1) the components of the system need to self-assemble into the precursor nanostructure: the surfactant needs to form stable micelles in the presence of the carbon precursor, which arranges around the micelles and forms important secondary interactions. In case of the typical soft-templating method, phloroglucinol forms hydrogen bonding interactions with the polyethylene oxide domains and self-assembles around the micelles, which is a critical prerequisite for the formation of the nanostructure. There are also requirements regarding the thermal properties of the components. The structure-directing agent needs to be (2) stable at the curing temperature of the carbon precursor leading to a stable polymeric scaffold, and needs to act as a (3) sacrificial agent that almost completely decomposes at the carbonisation temperature. In addition, the carbon precursor needs to convert to a (4) graphitic carbon structure at the carbonisation temperature while the sacrificial agent decomposes and the ordered nanostructure is kept (typically, compared to the precursor nanostructure, there is always a contraction observed in the resulting carbon structure at high temperature). Ordered mesoporous carbons with various symmetries can be realised, such as 2-D hexagonal p6m (see Fig. 5B), body-centred cubic Im3m, and bicontinuous cubic Ia3d geometries, by varying the ratios of the components.58,59 Furthermore, the size of the pores can be controlled by adding hydrocarbon swelling agents to the system.58
4.1. Towards more sustainable soft-templating systems
Although certainly more sustainable than hard-templating methods, the soft-templating technique is not without limitations. Several studies have demonstrated the application of more benign crosslinkers for phloroglucinol compared to the toxic formaldehyde. Mayes et al.60 showed that glyoxal can also be used as crosslinker for the soft-templating method. Glyoxal however reacts more slowly than formaldehyde. The authors noted the similarity of the phloroglucinol/glyoxal system to that of resorcinol/formaldehyde,61 as phloroglucinol reacts faster with formaldehyde than resorcinol. They observed ordered 7.5 nm pores with uniform sizes, together with larger pores up to 200 nm in diameter. Such hierarchical porosity was not observed in formaldehyde/phloroglucinol system,33 and the authors also ruled out the possibility of spinodal decomposition due to a secondary solvent. Using glyoxal, the formation of a stable intermediate probably slows down the crosslinking process. It was pointed out that glyoxal was responsible for the formation of the hierarchical structure, although the mechanism has not yet been clarified. The LD50 value of glyoxal (orally 3000 to 9000 mg kg−1 body weight for rats)62 is much higher compared to formaldehyde (orally 500 to 800 mg kg−1 body weight for rats),63 which is classified as a category 1B carcinogen and is subject to restrictions in the European Union.64 Furthermore, glyoxal can be produced from biomass-derived sugars, and is seen as a promising crosslinker to realise more sustainable formaldehyde-free wood adhesives.65,66
Another limitation of typical soft-templating systems is the use of strong acids or bases as catalysts for the crosslinking reaction of the resins. Ghimbeu et al.67 elegantly introduced glyoxylic acid with double functionality – the aldehyde group for crosslinking and the acidic functionality for catalysing the reaction – to realise a catalyst-free soft-template synthesis. By varying the precursor ratios and the manufacturing process, ordered mesoporous carbons with various architectures could be realised, such as the typical 2D hexagonal p6m and body-centred cubic Im3m mesostructures. Glyoxylic acid is a natural substance that has lower toxicity (oral LD50 ≈ 2500 mg kg−1 body weight for rats) than formaldehyde.
Furthermore, there has been interest in replacing the fossil-fuel derived phloroglucinol by biomass-based alternatives. Herou et al.68 focused on using hardwood (beech) organosolv lignin for the soft-templating method. They used glyoxal as crosslinker without catalyst, by applying the evaporation-induced self-assembly technique in acetone as solvent. The authors noted that lignins with smaller molecular weight and less branched structure could be better for the interaction with the surfactant micelles, favouring the self-assembly process due to their higher mobility. The hardwood lignin that they used had a Mw/Mn of 3834/2286 g mol−1, having a low polydispersity index (1.67). In this system, the polypropylene oxide units of Pluronic® F127 could form the core of the micelles, with the polyethylene oxide segments facing outwards, and interacting with phloroglucinol via hydrogen bonds (see Fig. 6A). The evaporation-induced self-assembly at room temperature was followed by a cross-linking process at 85 °C, and then a carbonisation step (at 900 °C) to obtain the ordered mesoporous carbon scaffold. The authors could replace about half of phloroglucinol to lignin, and still obtained the typical 2D-hexagonal pore structure (p6m) (see Fig. 6B–E). Compared to the system with phloroglucinol only, the addition of lignin gave rise to the development of smaller pores (decreased from 7 nm to 4 nm) with shorter interpore distance (decreased from 12 nm to 9.5 nm), i.e., they obtained a smaller unit cell (compare Fig. 6B and C with Fig. 6D and E). This phenomenon was explained in light of the bulkier structure of lignin, leaving less free volume for the micelles. It is interesting that the authors could not obtain ordered mesoporous carbon when only lignin was used (Fig. 6F and G), thus highlighting the importance for the presence of phloroglucinol that strongly interacts with and self-assembles around the micelles as depicted in Fig. 6A.
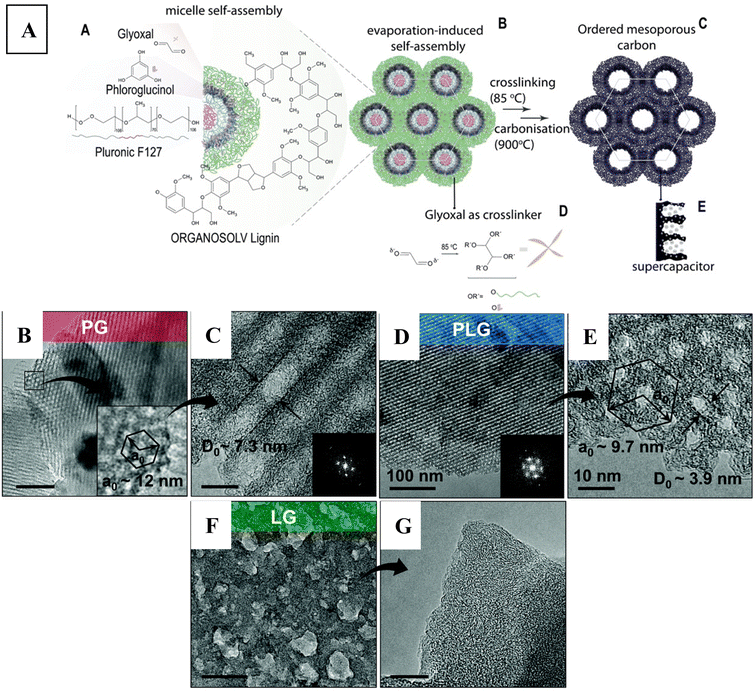 |
| Fig. 6 (A) Schematic representation of the self-assembly process together with the processing steps to obtain ordered mesoporous carbon using lignin–phloroglucinol carbon precursors. TEM images recorded on the material after the carbonisation process, obtained using (B and C) phloroglucinol only, (D and E) phloroglucinol–lignin and (F and G) only lignin precursors. Inset shows a (B) zoomed-in image with unit cell, and (C and D) FFT micrographs. The scalebar is 100 nm for (B), (D) and (F), and 10 nm for (C), (E) and (G). Reproduced from ref. 68 with permission from the Royal Society of Chemistry. | |
One of the greenest methods so far was developed by Castro-Gutiérrez et al.,69 through a mechanosynthesis technique using mimosa tannin as renewable carbon precursor and Pluronic® F127 as structure directing agent in water (see Fig. 7A). The ordered nanoporous carbon was obtained by ball-milling the reactant mixture, yielding a paste-like intermediate which gave the desired material upon carbonisation (at 900 °C). There was no need to use cross-linking agent or catalyst, the mechanosynthesis was performed within a relatively short time (60 min), and direct carbonisation was possible after the synthesis, making this method an attractive energy- and resource-efficient process. When ordered mesoporous carbon is fabricated from tannins in the conventional way, ethanol and HCl need to be added, and curing is also necessary (100 °C).70 The surfactant/tannin/water ratio appeared to be crucial to produce the 2D hexagonal mesoporous structure (see Fig. 7B). The authors noted that the mesostructure was retained even at high temperature (up to 1500 °C, see Fig. 7C), leading to an increase in the long-range ordering of the disordered carbon (i.e., higher graphitic crystallite size). CO2 activation could lead to micropores while maintaining the ordered uniformly sized mesopores (see Fig. 7D), affording a high surface area (around 1900 m2 g−1). Several ordered mesoporous carbon based heterostructures could be also realised through the mechanosynthesis method with tannins, by incorporating Ni nanoparticles,71 alkaline metal oxides,72 and Ru nanoparticles.73 In these systems, it was concluded that coordination cross-linking between the flavonoid units of tannins and the metal ions facilitated the self-assembly process.
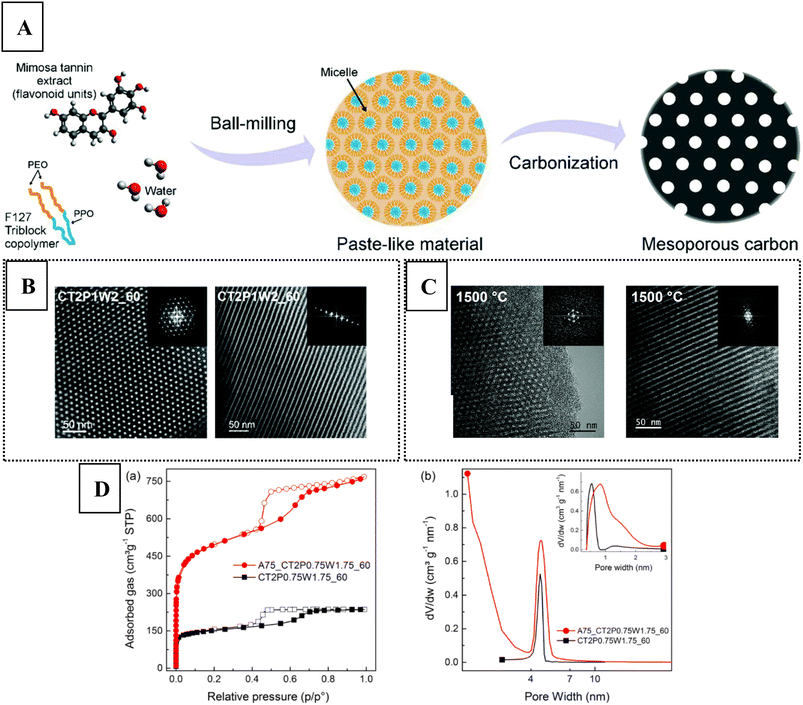 |
| Fig. 7 (A) Schematic representation of the mechanosynthesis method developed by Castro-Gutiérrez et al.69 The structure in the upper-left corner depicts robinetinidol, a flavanol building unit of condensed mimosa tannins. Bright field TEM images with transversal (left) and longitudinal (right) views on the developed ordered mesoporous carbons prepared at (B) 900 °C and at (C) 1500 °C. Inset shows the corresponding FFT micrographs. (D) (left) N2 adsorption–desorption results (right) with pore size distribution before (black squares) and after (red dots) CO2 activation. Reproduced from ref. 69 with permission from the Royal Society of Chemistry. | |
The metal-ion assisted, coordination-induced self-assembly was shown to work with organosolv lignin by Wang et al.74 They used acetone to dissolve organosolv lignin, Pluronic® F-127 and the metal salt, followed by an evaporation-induced self-assembly step. Curing at 100 °C appeared to be necessary before the carbonisation step that yielded metal nanoparticle/metal oxide doped ordered mesoporous carbons (note that this curing step is not necessary when mechanosynthesis is used, as discussed above). In a similar manner, a range of plant-derived polyphenols (ferulic acid, quercetin, caffeic acid, gallic acid, arbutin, proanthocyanidins) were converted to metal-doped ordered mesoporous carbons using ethanol as solvent.75 The authors concluded that the presence of phenolic hydroxyl group that can form coordination bond with metal ions (see Fig. 8), a good solubility in the solvent for the evaporation-induced self-assembly, and a low molecular weight (preferably less than 5 flavonoid units) were conducive to the formation of the ordered mesoporous carbon.
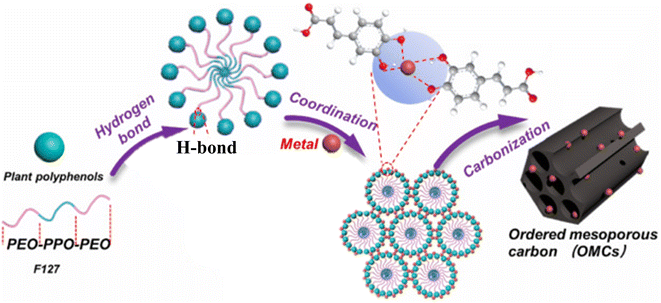 |
| Fig. 8 Schematic representation of the metal-ion assisted coordination-induced self-assembly approach yielding metal-doped ordered mesoporous carbons using plant-derived polyphenols. Reproduced from ref. 75 with some modifications. In the upper part caffeic acid is depicted as it coordinates with a metal ion. Copyright 2023 Elsevier. | |
The hydrothermal method is known to produce carbons directly from bio-derived building blocks, such as lignin as well as cellulose and its monomeric unit glucose.76 This strategy has also been explored as a modification of the original soft templating technique by adding the Pluronic® F127 to the hydrothermal reaction. Unfortunately, the micelles are not stable at the typical temperature of the hydrothermal synthesis (180–280 °C).76–78 To overcome this problem, Xiao et al.79 added tetraethyl orthosilicate to stabilise the micelles (using Pluronic® P123 surfactant: EO20PO70EO20) through formation of a silica layer, which is then removed by an etching step using HF. They used biomass-derived saccharides as carbon precursors, such as D-glucose, D-fructose, D-maltose, sucrose, D-glucosamine hydrochloride, and β-cyclodextrin. Furthermore, Xu et al.80 has shown that ordered mesoporous carbons can be obtained from pentoses (xylose, arabinose, ribose) at low temperature (140 °C) via a hydrothermal synthesis by the addition of H2SO4. A much greener way was realised by Kubo et al.,81 by using D-fructose, which can undergo a hydrothermal process at much lower temperature (130 °C), using Pluronic® F127 surfactant. The hydrothermal process yielded an ordered cubic Im3m mesostructure with a micelle diameter of about 6 nm, and a carbon wall thickness of about 10 nm. Carbonisation at 550 °C facilitated the removal of the template, leading to a microporous ordered structure that kept the Im3m symmetry. In order to shift the pore size to the mesoporous domain, the authors used trimethylbenzene swelling agent (a petroleum-derived additive). By doing so, they obtained the ordered Im3m structure with bimodal pore size distribution falling in the meso- and micropore domain.
5. Critical outlook
Lignin has high carbon content, and has already a polyaromatic structure. There has been a lot of research on developing advanced carbon structures based on lignin.2,82–87 In respect to ordered mesoporous carbons, so far, it was shown that in the typical soft-templating method, about half of phloroglucinol can be replaced by lignin,68 and even more when metal ions are added due to the coordination-assisted self-assembly.74,88 It would be interesting to explore whether other types of lignin can be a better fit to the soft-templating method, to shed light on structural requirements/benefits for facilitating the self-assembly. This has already been investigated in detail for plant-derived polyphenols, for the coordination-induced self-assembly approach.75
Application of the aggressive activating agent KOH is one of the most efficient methods to create micropores, and thus the most popular in the literature; however, this method is not the greenest way to go. There are other methods that could be explored such as the use of harmless reagents: potassium carbonates, bicarbonates, and organic salts.89 Furthermore, bio-derived pore forming agents may also be interesting to explore. Thermally label/volatile biosourced compounds, which can be compatible with our system (i.e., solubility, interactions, etc.), can be promising candidates. An interesting example was given by Ra et al.:90 they used camphor, a small natural organic molecule, as pore forming agent to prepare porous carbon nanofibers using polyacrylonitrile precursor. Camphor is a naturally occurring volatile compound with low melting point (around 180 °C). The obtained porous carbon had high micropore volume (around 90% of the total pore volume), with the presence of ultramicropores (pores with diameter below 0.7 nm; around 30% of the micropore volume). High surface area could be achieved (around 880 m2 g−1), without the necessity of additional activation steps, which is advantageous for the energy efficiency of the process. Some biopolymers can also be good sacrificial pore forming agents, as it was demonstrated recently on high amylose starch.91,92 High amylose starch has a melting point around 280 °C, and starts decomposing soon after it melts from about 300 °C.91 When blended with polyacrylonitrile for the preparation of porous carbon nanofibers, a specific surface area as high as ∼1200 m2 g−1 could be reached with micro–mesoporous hierarchical structure.92 Albeit the mentioned biosourced porogens were applied in different systems (not for templating methods), these approaches may give some inspirations to discover this research direction. Although considered less efficient, physical activation methods using e.g., steam or CO2 are also more benign strategies compared to KOH-activation.
Characterising the carbon structure and surface chemistry is very important for applications, nevertheless, this has mostly been neglected at some extent thus far amongst the studies focusing on green soft-templating strategies. Not only the porosity, but carbon structure and surface chemistry also have crucial influence on the performance and characteristics of the porous carbons. For example, in electrochemical applications, the graphitic carbon structure will determine the conductivity of the structure, and the surface chemistry will be important for wettability with the electrolyte, and will determine the presence/absence of pseudocapacitive or parasitic redox reactions. Thus, it would be important to know the surface chemistry and carbon structure of the fabricated micro- and mesoporous biobased carbons. It can be expected that the temperature, the activation process, and the nature of the biosourced precursor together with other additives and processing conditions will shape these properties.
Green methods for doping the created biobased ordered mesoporous carbon structures with heteroatoms, such as N, S, P, etc., have not been investigated in much detail so far, and it should be an interesting direction for future research.
We believe that one of the major limitations of the soft-templating method, which has not been addressed so far, is the use of Pluronic® surfactants, which are inherently petroleum-derived components in the system. As we have discussed above, the soft-templating system is very sensitive, and many requirements need to be met for the creation of the ordered nanoporous structure. Nevertheless, there may be more sustainable, bio-derived surfactants that can replace these components in the future.
6. Conclusions
Nanoarchitecturing biobased porous carbons is paramount for competing with high-performing, state-of-the-art petroleum-derived nanoporous carbons, including meso–microporous hierarchically structured architectures. In doing so, methodologies to prepare such architectures must be revisited to arrive at a safe and sustainable-by-design product. Based on our critical overview on existing methods, the soft-templating approach appears to be the greenest way developed so far. Several modifications enabled the realisation of more benign soft-templating processes (e.g., benign crosslinkers, catalyst-free synthesis), together with the application of biosourced carbon precursors. Modified soft-templating methods, including the mechanochemical synthesis, coordination-assisted self-assembly techniques, and hydrothermal approaches are major achievements in this field. Nevertheless, there is still much to be done, for example to replace the petroleum-based surfactants, one of the biggest challenges to tackle thus far. The principles of green chemistry could be more thoroughly implemented when developing carbon nanoarchitectures in the future.
Conflicts of interest
There are no conflicts to declare.
Acknowledgements
L. Szabó would like to thank the support through the Marie Skłodowska-Curie Actions (MSCA), Horizon Europe Program (Project “BioNanoCarb”, Grant agreement ID: 101062130).
References
- W. J. Sauges, J. Yang, N. Monroe, S.-D. Han, T. Vinzant and M. Yung,
et al.
, A simple method for producing bio-based anode materials for lithium-ion batteries, Green Chem., 2020, 22, 7093–7108 RSC.
- E. Frank, L. M. Steudle, D. Ingildeev, J. M. Spörl and M. R. Buchmeiser, Carbon fibers: precursor systems, processing, structure, and properties, Angew. Chem., Int. Ed., 2014, 53, 5262–5298 CrossRef CAS PubMed.
-
S. Y. Liew, W. Thielemans, S. Freunberger and S. Spirk, Polysaccharide Based Supercapacitors, Springer, Cham, 2017 Search PubMed.
- M. Salanne, B. Rotenberg, K. Naoi, K. Kaneko, P.-L. Taberna and C. P. Grey,
et al.
, Efficient storage mechanisms for building better supercapacitors, Nat. Energy, 2016, 1, 1–10 Search PubMed.
- L. Liu, P.-L. Taberna, B. Dunn and P. Simon, Future directions for electrochemical capacitors, ACS Energy Lett., 2021, 6, 4311–4316 CrossRef CAS.
- J. R. Miller and P. Simon, Electrochemical capacitors for energy management, Science, 2008, 321, 651–652 CrossRef CAS PubMed.
- Z.-H. Huang, Z. Yang, F. Kang and M. Inagaki, Carbon electrodes for capacitive deionization, J. Mater. Chem. A, 2017, 5, 470–496 RSC.
- P. Chen, L.-K. Wang, G. Wang, M.-R. Gao, J. Ge and W.-J. Yuan,
et al.
, Nitrogen-doped nanoporous carbon nanosheets derived from plant biomass: an efficient catalyst for oxygen reduction reaction, Energy Environ. Sci., 2014, 7, 4095–4103 RSC.
- D. M. Fernandes, A. S. Mestre, A. Martins, N. Nunes, A. P. Carvalho and C. Freire, Biomass-derived nanoporous carbons as electrocatalysts for oxygen reduction reaction, Catal. Today, 2020, 357, 269–278 CrossRef CAS.
- T. J. Bandosz and C. O. Ania, Origin and perspectives of the photochemical activity of nanoporous carbons, Adv. Sci., 2018, 5, 1800293 CrossRef PubMed.
- X. Duan, H. Sun and S. Wang, Metal-free carbocatalysis in advanced oxidation reactions, Acc. Chem. Res., 2018, 51, 678–687 CrossRef CAS PubMed.
- A. M. Hamiche, A. B. Stambouli and S. Flazi, A review of the water-energy nexus, Renewable Sustainable Energy Rev., 2016, 65, 319–331 CrossRef.
- L. Szabó, X. Xu, K. Uto, J. Henzie, Y. Yamauchi and I. Ichinose,
et al.
, Tailoring the structure of chitosan-based porous carbon nanofiber architectures toward efficient capacitive charge storage and capacitive deionization, ACS Appl. Mater. Interfaces, 2022, 14, 4004–4021 CrossRef PubMed.
- J. Lee, U. von Gunten and J.-H. Kim, Persulfate-based advanced oxidation: critical assessment of opportunities and roadblocks, Environ. Sci. Technol., 2020, 54, 3064–3081 CrossRef CAS PubMed.
- X. Duan, Z. Ao, L. Zhou, H. Sun, G. Wang and S. Wang, Occurrence of radical and nonradical pathways from carbocatalysts for aqueous and nonaqueous catalytic oxidation, Appl. Catal., B, 2016, 188, 98–105 CrossRef CAS.
- Y. Wang, Z. Ao, H. Sun, X. Duan and S. Wang, Activation of peroxymonosulfate by carbonaceous oxygen groups: experimental and density functional theory calculations, Appl. Catal., B, 2016, 198, 295–302 CrossRef CAS.
- X. Duan, H. Sun, Z. Ao, L. Zhou, G. Wang and S. Wang, Unveiling the active sites of graphene-catalyzed peroxymonosulfate activation, Carbon, 2016, 107, 371–378 CrossRef CAS.
- C. Chu, J. Yang, D. Huang, J. Li, A. Wang and P. J. J. Alvarez,
et al.
, Cooperative pollutant adsorption and persulfate-driven oxidation
on hierarchically ordered porous carbon, Environ. Sci. Technol., 2019, 53, 10352–10360 CrossRef CAS PubMed.
- M. Seredych, M. Koscinski, M. Sliwinska-Bartkowiak and T. J. Bandosz, Active pore space utilization in nanoporous carbon-based supercapacitors: effects of conductivity and pore accessibility, J. Power Sources, 2012, 220, 243–252 CrossRef CAS.
- J. Sánchez-González, F. Stoeckli and T. A. Centeno, The role of the electric conductivity of carbons in the electrochemical capacitor performance, J. Electroanal. Chem., 2011, 657, 176–180 CrossRef.
- S. Dutta, A. Bhaumik and K. C.-W. Wu, Hierarchically porous carbon derived from polymers and biomass: effect of interconnected pores on energy applications, Energy Environ. Sci., 2014, 7, 3574–3592 RSC.
- M. Kim, K. L. Firestein, J. F. S. Fernando, X. Xu, H. Lim and D. V. Golberg,
et al.
, Strategic design of Fe and N co-doped hierarchically porous carbon as superior ORR catalyst: from the perspective of nanoarchitectonics, Chem. Sci., 2022, 13, 10836–10845 RSC.
- H. Li, W. Dong, C. Li, T. Barakat, M. Sun and Y. Wang,
et al.
, Three-dimensional ordered hierarchically porous carbon materials for high performance Li-Se battery, J. Energy Chem., 2022, 68, 624–636 CrossRef CAS.
- L.-H. Chen, Y. Li and B.-L. Su, Hierarchy in materials for maximized efficiency, Natl. Sci. Rev., 2020, 7, 1626–1630 CrossRef CAS PubMed.
- L. Wu, Y. Li, Z. Fu and B.-L. Su, Hierarchically structured porous materials: synthesis strategy and applications in energy storage, Natl. Sci. Rev., 2020, 7, 1667–1701 CrossRef CAS PubMed.
- X. Zheng, G. Shen, C. Wang, Y. Li, D. Dunphy and T. Hasan,
et al.
, Bio-inspired Murray materials for mass transfer and activity, Nat. Commun., 2017, 8, 14921 CrossRef CAS PubMed.
- D. Nepal, S. Kang, K. M. Adstedt, K. Kanhaiya, M. R. Bockstaller and L. C. Brinson,
et al.
, Hierarchically structured bioinspired nanocomposites, Nat. Mater., 2023, 22, 18–35 CrossRef CAS PubMed.
- R. A. Sheldon, The E factor 25 years on: the rise of green chemistry and sustainability, Green Chem., 2017, 19, 18–43 RSC.
- C. Liang, Z. Li and S. Dai, Mesoporous carbon materials: synthesis and modification, Angew. Chem., Int. Ed., 2008, 47, 3696–3717 CrossRef CAS PubMed.
- T.-Y. Ma, L. Liu and Z.-Y. Yuan, Direct synthesis of ordered mesoporous carbons, Chem. Soc. Rev., 2013, 42, 3977–4003 RSC.
- Z. Heiderinejad, M. H. Dehghani, M. Heidari, G. Javedan, I. Ali and M. Sillanpää, Methods for preparation and activation of activated carbon: a review, Environ. Chem. Lett., 2020, 18, 393–415 CrossRef.
- J. Górka, A. Zawislak, J. Choma and M. Jaroniec, KOH activation of mesoporous carbon obtained by soft-templating, Carbon, 2008, 46, 1159–1174 CrossRef.
- C. Liang and S. Dai, Synthesis of mesoporous carbon materials via enhanced hydrogen-bonding interaction, J. Am. Chem. Soc., 2006, 128, 5316–5317 CrossRef CAS.
- J. Wang and S. Kaskel, KOH Activation of carbon-based materials for energy storage, J. Mater. Chem., 2012, 22, 23710–23725 RSC.
- T. Lin, I.-W. Chen, F. Liu, C. Yang, H. Bi and F. Xu,
et al.
, Nitrogen-doped mesoporous carbon of extraordinary capacitance for electrochemical energy storage, Science, 2015, 350, 1508–1513 CrossRef CAS PubMed.
- M. Xie, H. Meng, J. Chen, Y. Zhang, C. Du and L. Wan,
et al.
, High-volumetric supercapacitor performance of ordered mesoporous carbon electrodes enabled by the Faradaic-active nitrogen doping and decrease of microporosity, ACS Appl. Energy Mater., 2021, 4, 1840–1850 CrossRef CAS.
- E. H. Lahrar, P. Simon and C. Merlet, Carbon-carbon supercapacitors: beyond average pore size or how electrolyte confinement and inaccessible pores affect the capacitance, J. Chem. Phys., 2021, 155, 184703 CrossRef CAS PubMed.
- A. Eftekhari and Z. Fan, Ordered mesoporous carbon and its applications for electrochemical energy storage and conversion, Mater. Chem. Front., 2017, 1, 1001–1027 RSC.
- A. Saleem, Y. Zhang, M. Usman, M. Haris and P. Li, Tailored architectures of mesoporous carbon nanostructures: from synthesis to applications, Nano Today, 2022, 46, 101607 CrossRef CAS.
- S. Yuan, Q. Gao, C. Ke, T. Zuo and J. Hou,
et al.
, Mesoporous carbon materials for electrochemical energy storage and conversion, ChemElectroChem, 2022, 9, e202101182 CrossRef CAS.
- J. Deng, M. Li and Y. Wang, Biomass-derived carbon: synthesis and applications in energy storage and conversion, Green Chem., 2016, 18, 4824–4854 RSC.
- Z. Bi, Q. Kong, Y. Cao, G. Sun, F. Su and X. Wei,
et al.
, Biomass-derived porous carbon materials with different dimensions for supercapacitor electrodes: a review, J. Mater. Chem. A, 2019, 7, 1608–16045 Search PubMed.
- Z. Li, D. Guo, Y. Liu, H. Wang and L. Wang, Recent advances and challenges in biomass-derived porous carbon nanomaterials for supercapacitors, Chem. Eng. J., 2020, 397, 125418 CrossRef CAS.
- J. Wang, X. Zhang, Z. Li, Y. Ma and L. Ma, Recent progress of biomass-derived carbon materials for supercapacitors, J. Power Sources, 2020, 451, 227794 CrossRef CAS.
- A. Gopalakrishnan and S. Badhulika, Effect of self-doped heteroatoms on the performance of biomass-derived carbon for supercapacitor applications, J. Power Sources, 2020, 480, 228830 CrossRef CAS.
- R. Chakraborty, K. Vilya, M. Pradhan and A. K. Nayak, Recent advancement of biomass-derived porous carbon based materials for energy and environmental remediation applications, J. Mater. Chem. A, 2022, 10, 6965–7005 RSC.
- G. Zhang, X. Liu, L. Wang and H. Fu, Recent advances of biomass derived carbon-based materials for efficient electrochemical energy devices, J. Mater. Chem. A, 2022, 10, 9277–9307 RSC.
- B. M. Matsagar, R.-X. Yang, S. Dutta, Y. S. Ok and K. C.-W. Wu, Recent progress in the development of biomass-derived nitrogen-doped porous carbon, J. Mater. Chem. A, 2021, 9, 3703–3728 RSC.
- X.-L. Zhou, H. Zhang, L.-M. Shao, F. Lü and P.-J. He, Preparation and application of hierarchical porous carbon materials from waste and biomass: a review, Waste Biomass Valorization, 2021, 12, 1699–1724 CrossRef CAS.
- G. Singh, K. S. Lakhi, S. Sil, S. V. Bhosale, I. Kim and K. Albahily,
et al.
, Biomass derived porous carbon for CO2 capture, Carbon, 2019, 148, 164–186 CrossRef CAS.
- T. Shang, Y. Xu, P. Li, J. Han, Z. Wu and Y. Tao,
et al.
, A bio-derived sheet-like porous carbon with thin-layer pore walls for ultrahigh-power supercapacitors, Nano Energy, 2020, 70, 104531 CrossRef CAS.
- N. Guo, M. Li, X. Sun, F. Wang and R. Yang, Tremella derived ultrahigh specific surface area activated carbon for high performance supercapacitor, Mater. Chem. Phys., 2017, 201, 399–407 CrossRef CAS.
- N. Wu, X. Gu, S. Zhou, X. Han, H. Leng and P. Zhang,
et al.
, Hierarchical porous N, S co-doped carbon derived from fish scales for enhanced membrane capacitive deionization, Electrochim. Acta, 2022, 409, 139983 CrossRef CAS.
- E. Maruccia, M. A. O. Lourenço, T. Priamushko, M. Bartoli, S. Bocchini and F. C. Pirri,
et al.
, Nanocast nitrogen-containing ordered mesoporous carbons from glucosamine for selective CO2 capture, Mater. Today Sustain., 2022, 17, 100089 CrossRef.
- C. Lawrence, W. Thielemans and R. Mokaya, One step room temperature synthesis of ordered mesoporous silica SBA-15 mediated by cellulose nanoparticles, J. Mater. Chem., 2010, 20, 320–325 RSC.
- C. Liang, K. Hong, G. A. Guiochon, J. W. Mays and S. Dai, Synthesis of a large-scale highly ordered porous carbon film by self-assembly of block copolymers, Angew. Chem., Int. Ed., 2004, 43, 5785–5789 CrossRef CAS PubMed.
- S. Tanaka, N. Nishiyama, Y. Egashira and K. Ueyama, Synthesis of ordered mesoporous carbons with channel structure from an organic-organic nanocomposite, Chem. Commun., 2005, 2125–2127 RSC.
- F. Zhang, Y. Meng, D. Gu, Y. Yan, Z. Chen and B. Tu,
et al.
, An aqueous cooperative assembly route to synthesize ordered mesoporous carbons with controlled structures and morphology, Chem. Mater., 2006, 18, 5279–5288 CrossRef CAS.
- Y. Meng, D. Gu, F. Zhang, Y. Shi, L. Cheng and D. Feng,
et al.
, A family of highly ordered mesoporous polymer resin and carbon structures from organic-organic self-assembly, Chem. Mater., 2006, 18, 4447–4464 CrossRef CAS.
- R. T. Mayes, C. Tsouris, J. O. Kiggans Jr, S. M. Mahurin, D. W. DePaoli and S. Dai, Hierarchical ordered mesoporous carbon from phloroglucinol-glyoxal and its application in capacitive deionization of brackish water, J. Mater. Chem., 2010, 20, 8674–8678 RSC.
- X. Wang, C. Liang and S. Dai, Facile synthesis of ordered mesoporous carbons with high thermal stability by self-assembly of resorcinol-formaldehyde and block copolymers under highly acidic conditions, Langmuir, 2008, 24, 7500–7505 CrossRef CAS.
-
J. Kielhorn, C. Pohlenz-Michel, S. Schmidt and I. Mangelsdorf, Concise International Chemical Assessment Document 57. Glyoxal, World Health Organization, Geneva, 2004 Search PubMed.
- K. Tsuchiya, Y. Hayashi, M. Onodera and T. Hasegawa, Toxicity of formaldehyde in experimental animals – concentrations of the chemical in the elution from dishes of formaldehyde resin in some vegetables, Keio J. Med., 1975, 24, 19–37 CrossRef CAS.
-
European Chemicals Agency, Formaldehyde and Formaldehyde Releasers - Strategy for Future Work, https://echa.europa.eu/documents/10162/17233/formaldehyde_review_report_en.pdf/551df4a2-28c4-2fa9-98ec-c8d53e2bf0fc, last accessed on 09/01/ 2023 Search PubMed.
- I. Van Nieuwenhove, T. Renders, J. Lauwaert, T. De Roo, J. De Clercq and A. Verberckmoes, Biobased resins using lignin and glyoxal, ACS Sustainable Chem. Eng., 2020, 8, 18789–18809 CrossRef CAS.
- M. Siahkamari, S. Emmanuel, D. B. Hodge and M. Nejad, Lignin-glyoxal: a fully biobased formaldehyde-free wood adhesive for interior engineered wood products, ACS Sustainable Chem. Eng., 2022, 10, 3430–3441 CrossRef CAS.
- C. M. Ghimbeu, L. Vidal, L. Delmotte, J.-M. Le Meins and C. Vix-Guterl, Catalyst-free soft-template synthesis of ordered mesoporous carbon tailored using phloroglucinol/glyoxylic acid environmentally friendly precursor, Green Chem., 2014, 16, 3079–3088 RSC.
- S. Herou, M. C. Ribadeneyra, R. Madhu, V. Araullo-Peters, A. Jensen and P. Schlee,
et al.
, Ordered mesoporous carbons from lignin: a new class of biobased electrodes for supercapacitors, Green Chem., 2019, 21, 550–559 RSC.
- J. Castro-Gutiérrez, A. Sanchez-Sanchez, J. Ghanbaja, N. Díez, M. Sevilla and A. Celzard,
et al.
, Synthesis of perfectly ordered mesoporous carbons by water-assisted mechanochemical self-assembly of tannin, Green Chem., 2018, 20, 5123–5132 RSC.
- S. Schlienger, A.-L. Graff, A. Celzard and J. Parmentier, Direct synthesis of ordered mesoporous polymer and carbon materials by a biosourced precursor, Green Chem., 2012, 14, 313–316 RSC.
- P. Zhang, L. Wang, S. Yang, J. A. Schott, X. Liu and S. M. Mahurin,
et al.
, Solid-state synthesis of ordered mesoporous carbon catalysts via a mechanochemical assembly through coordination cross-linking, Nat. Commun., 2017, 8, 15020 CrossRef PubMed.
- W. Shan, P. Zhang, S. Yang, H. Zhu, P. Wu and H. Xing,
et al.
, Sustainable synthesis of alkaline metal oxide-mesoporous carbons via mechanochemical coordination self-assembly, J. Mater. Chem. A, 2017, 5, 23446–23452 RSC.
- L. Wang, J. Zhao, P. Zhang, S. Yang, W. Zhan and S. Dai, Mechanochemical synthesis of ruthenium cluster@ordered mesoporous carbon catalysts by synergetic dual templates, Chem.–Eur. J., 2019, 25, 8494–8498 CrossRef CAS PubMed.
- X. Wang, X. Liu, R. L. Smith, Y. Liang and X. Qi, Direct one-pot synthesis of ordered mesoporous carbons from lignin with metal coordinated self-assembly, Green Chem., 2021, 23, 8632–8642 RSC.
- X. Liu, Y. Wang, Y. Tang, R. L. Smith, Y. Xu and Y. Liang,
et al.
, Plant polyphenol-derived ordered mesoporous carbon materials via metal ion cross-linking, Carbon, 2023, 202, 90–100 CrossRef CAS.
- C. Falco, N. Baccile and M.-M. Titirici, Morphological and structural differences between glucose, cellulose and lignocellulosic biomass derived hydrothermal carbons, Green Chem., 2011, 13, 3273–3281 RSC.
- W.-D. Hergeth, P. Bloss, K. Schmutzler, S. Wartewig, K. Witkowski and L. Wolinski, Micellization of poly(oxyethylene)-poly(oxypropylene)-poly(oxyethylene) copolymers in aqueous solution, Acta Polym., 1989, 40, 416–418 CrossRef CAS.
- P.-W. Xiao, D. Guo, L. Zhao and B.-H. Han, Soft templating synthesis of nitrogen-doped porous hydrothermal carbons and their applications in carbon dioxide and hydrogen adsorption, Microporous Mesoporous Mater., 2016, 220, 129–135 CrossRef CAS.
- P.-W. Xiao, L. Zhao, Z.-Y. Sui, M.-Y. Xu and B.-H. Han, Direct synthesis of ordered mesoporous hydrothermal carbon materials via a modified soft-templating method, Microporous Mesoporous Mater., 2017, 253, 215–222 CrossRef CAS.
- F. Xu, Y. Chen, M. Tang, H. Wang, J. Deng and Y. Wang, Acid induced self-assembly strategy to synthesize ordered mesoporous carbons from biomass, ACS Sustainable Chem. Eng., 2016, 4, 4473–4479 CrossRef CAS.
- S. Kubo, R. J. White, N. Yoshizawa, M. Antonietti and M.-M. Titirici, Ordered carbohydrate-derived porous carbons, Chem. Mater., 2011, 23, 4882–4885 CrossRef CAS.
- W. Fang, S. Yang, X.-L. Wang, T.-Q. Yuan and R.-C. Sun, Manufacture and application of lignin-based carbon fibers (LCFs) and lignin-based carbon nanofibers (LCNFs), Green Chem., 2017, 19, 1794–1827 RSC.
- W. Qu, J. Yang, X. Sun, X. Bai, H. Jin and M. Zhang, Towards producing high-quality lignin-based carbon fibers: a review of crucial factors affecting lignin properties and conversion techniques, Int. J. Biol. Macromol., 2021, 189, 768–784 CrossRef CAS PubMed.
- S. Chatterjee and T. Saito, Lignin-derived advanced carbon materials, ChemSusChem, 2015, 8, 3941–3958 CrossRef CAS PubMed.
- W. Zhang, X. Qiu, C. Wang, L. Zhong and F. Fu,
et al.
, Lignin derived carbon materials: current status and future trends, C, 2022, 1, 1–39 Search PubMed.
- M. R. Snowdon, A. K. Mohanty and M. Misra, A study of carbonized lignin as an alternative to carbon black, ACS Sustainable Chem. Eng., 2014, 2, 1257–1263 CrossRef CAS.
- K. Chen, Z.-J. He, Z.-H. Liu, A. J. Ragauskas and B.-Z. Li,
et al.
, Emerging modification technologies of lignin-based activated carbon toward advanced applications, ChemSusChem, 2022, 15, 1–18 Search PubMed.
- X. Wang, M. Qiu, R. L. Smith, J. Yang, F. Shen and X. Qi, Ferromagnetic lignin-derived ordered mesoporous carbon for catalytic hydrogenation of furfural to furfuryl alcohol, ACS Sustainable Chem. Eng., 2020, 8, 18157–18166 CrossRef CAS.
- M. Sevilla, N. Díez and A. B. Fuertes, More sustainable chemical activation strategies for the production of porous carbons, ChemSusChem, 2021, 14, 94–117 CrossRef CAS PubMed.
- E. J. Ra, T. H. Kim, W. J. Yu, K. H. An and Y. H. Lee, Ultramicropore formation in PAN/camphor-based carbon nanofiber paper, Chem. Commun., 2010, 46, 1320–1322 RSC.
- H. Wang, W. Wang, H. Wang, Y. Li and X. Jin,
et al.
, Improving supercapacitance of electrospun carbon nanofibers through increasing micropores and microporous surface area, Adv. Mater. Interfaces, 2019, 6, 1801900 CrossRef.
- H. Wang, H. Wang, F. Ruan, Q. Feng and Y. Wei,
et al.
, High-porosity carbon nanofibers prepared from polyacrylonitrile blended with amylose starch for application in supercapacitors, Mater. Chem. Phys., 2023, 293, 126896 CrossRef CAS.
|
This journal is © The Royal Society of Chemistry 2023 |