DOI:
10.1039/C7RA12835E
(Review Article)
RSC Adv., 2018,
8, 10040-10056
A review on organic–inorganic hybrid nanocomposite membranes: a versatile tool to overcome the barriers of forward osmosis
Received
27th November 2017
, Accepted 26th February 2018
First published on 12th March 2018
Abstract
Forward osmosis (FO) processes have recently attracted increasing attention and show great potential as a low-energy separation technology for water regeneration and seawater desalination. However, a number of challenges, such as internal concentration polarization, membrane fouling, and the trade-off effect, limit the scaleup and industrial practicality of FO. Hence, a versatile method is needed to address these problems and fabricate ideal FO membranes. Among the many methods, incorporating polymeric FO membranes with inorganic nanomaterials is widely used and effective and is reviewed in this paper. The properties of FO membranes can be improved and meet the demands of various applications with the incorporation of nanomaterials. This review presents the actualities and advantages of organic–inorganic hybrid nanocomposite FO membranes. Nanomaterials applied in the FO field, such as carbon nanotubes, graphene oxide, halloysite nanotubes, silica and Ag nanoparticles, are classified and compared in this review. The effects of modification methods on the performance of nanocomposite FO membranes, including blending, in situ interfacial polymerization, surface grafting and layer-by-layer assembly, are also reviewed. The outlook section discusses the prospects of organic–inorganic hybrid nanocomposite FO membranes and advanced nanotechnologies available for FO processes. This discussion may provide new opportunities for developing novel FO membranes with high performance.
1. Introduction
Forward osmosis (FO) is a promising membrane separation technology with recently expanded focus as a low energy process.1,2 It is a spontaneously occurring osmotic process that separates water effectively from a dissolved solute via a semi-permeable membrane. Unlike conventional pressure-driven membrane processes, FO is driven by osmotic pressure between the feed solution and draw solution.3 Without external pressure, the FO process has several unique benefits, including low energy consumption, low operating cost, efficient separation and a wide range of feed solutions.4–6 Therefore, FO is deemed to be potentially useful in various industries, such as desalination, waste water treatment,7 food processing, medicine, and biological processes.8,9 A desirable FO membrane must possess high water flux and solute rejection, low concentration polarization, adequate mechanical and antifouling properties and good stability. However, some drawbacks still limit the application of FO in large scale processes. The most severe of these include: (1) internal concentration polarization (ICP); (2) membrane fouling; (3) the trade-off effect. To address these limitations, many efforts have been made to improve conventional FO membranes, among which organic–inorganic hybrid nanocomposite FO membranes are a candidate to mitigate these problems.
ICP is one of the most serious problems in FO processes; it dramatically reduces the osmotic driving force. Hence, the water flux declines and negatively affects the FO process. In order to minimize ICP, FO membranes should have low structural parameters. Hydrophilicity and wettability modifications of the FO support layers are the main methods of ICP mitigation. It is assumed that a hydrophilic support layer not only promotes the transport of water and solute molecules, but also enhances the wettability of the support layer. Hence, hydrophilization of the FO support layer is an active area of membrane research. Many studies have found that the incorporation of nanomaterials can significantly enhance the hydrophilicity of FO membranes. Also, incorporation of nanomaterials into the support layer of FO membranes promotes decrease of the structural parameter, which implies a lower ICP. Ma et al.10 incorporated zeolite into the polysulfone support layer of an FO membrane to obtain a lower ICP. The resulting membrane had a decreased structure parameter from 0.96 mm to 0.34 mm and increased water flux. This result was attributed to the higher porosity, enhanced hydrophilicity and additional water channels supplied by the addition of porous zeolite. This was the first study to exhibit the feasibility of employing an organic–inorganic hybrid nanocomposite FO membrane to limit ICP in the FO process. Subsequently, researchers have used multi-walled carbon nanotubes (MWCNTs)11–13 and TiO2 (ref. 4, 14 and 15) to control ICP in the support layers of FO membranes. The resulting nanomaterials all demonstrated decreased structure parameters. Furthermore, the support layers also showed enhanced strength and other desirable properties for FO applications.
Membrane fouling is a complex procedure which has a strong impact on the performance of membranes, especially their filtration efficiencies and service life. Among fouling factors and mechanisms, some are universal in pressure-driven membrane processes, such as hydrodynamic conditions, membrane materials, feed solution constituents and concentration polarization. Other factors are specific to FO, such as the draw solution constituents, operating orientation of the membranes, and reverse diffusion. Although the membrane fouling of FO is reversible,16 it is still considered to be a limitation that reduces the FO filtration efficiency, particularly for wastewater purification applications without pretreatment.17 Many researchers have indicated that introducing nanomaterials into the active layer of a FO membrane will provide a smoother and more hydrophilic surface so that membrane fouling can be effectively prevented. It was discovered that with the incorporation of hydrophilic mesoporous carbons into their active layers,18 FO membranes demonstrated increased surface hydrophilicity. A similar phenomenon was also observed by Zhao et al.19 when they employed a hybrid nanocomposite FO membrane incorporated with MWCNTs.
The trade-off effect between permeability and selectivity is a barrier to the development of membranes. It is common knowledge that for conventional polymeric membranes, water flux and solute rejection cannot be increased simultaneously. To overcome the permeability/selectivity trade-off effect, permeability must be enhanced without sacrificing solute rejection. According to the published literature, higher rejection involves a combination of steric and Donnan exclusion.20 Also, certain elements will disrupt this effect, such as reducing polymer cross-linking, increasing the surface charge density and providing adequate nanovoids and channels. For example, zeolite molecular sieves and silica nanoparticles can provide water pathways and enhance charge density. Hence, incorporating nanomaterials will affect polymer cross-linking and also provide adequate pathways to water rather than solutes, thus overcoming the trade-off effect.
As discussed above, incorporation of inorganic nanomaterials is a versatile method to modify FO membranes which can address the main problems that restrict the development of FO. Currently, with the development of membranes in water treatment and other fields, the requirements of membrane function, such as permeability, selectivity, anti-pollution, and chemical and thermal stability, are becoming more strict. It is difficult for traditional membrane materials to meet application requirements. Therefore, researchers have begun to turn their focus to developing novel composite membranes or membrane materials with suitable properties. The treatment and purification of water will benefit from improving the separation efficiency of membranes, and the water supply will be enhanced with safer water sources. Since Ma et al.21 incorporated NaY zeolite nanoparticles into a polyamide active layer in 2012, recent advances in nanotechnology have offered opportunities for the development of FO technology. Fig. 1 shows the growing trend of published papers on organic–inorganic hybrid nanocomposite FO membranes.
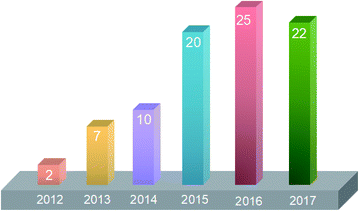 |
| Fig. 1 Annual number of publications on organic–inorganic hybrid nanocomposite FO membranes since 2012. The data were obtained from Web of Science on 18th November 2017. | |
In this work, we review the development of organic–inorganic hybrid nanocomposite FO membranes. We discuss the available nanomaterials, properties, advantages and modification methods used in the application of nanotechnology to the FO process. Diagrams of frequently used nanomaterials in the FO membrane field are summarized and presented in Table 1. In the last section, we list the limitations of this technique for commercialization and provide an overview of the trends in the development of nanocomposite FO membranes. By discussing these advanced technologies and the physicochemical properties of nanomaterials, this review outlines the opportunities and limitations to further capitalize on the unique properties of FO technology.
Table 1 Diagrams of the nanomaterials
Nanomaterial shape |
Diagram |
Nanomaterials |
Tubular |
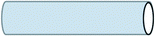 |
CNTs, HNTs |
Ball |
 |
Ag, TiO2, SiO2 |
Flake |
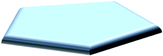 |
GO, zeolite |
Massive |
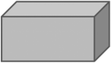 |
Boehmite, CaCO3 |
Linear |
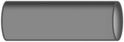 |
CNFs |
2. Effects of nanomodifiers on FO membrane performance
Currently, with the development of nanotechnology, many novel functional nanomaterials are being explored to enhance the performance of membranes. Employing inorganic nanomaterials with FO membranes can result in enhanced separation performance and the development of new functions, such as antisepsis and photocatalysis, that are endowed by the nanomaterials. Researchers have indicated that organic–inorganic hybrid nanocomposite membranes have significantly higher water flux, mechanical strength, selectivity, stability and hydrophilicity compared with conventional polymeric FO membranes.22–24 The main objectives of incorporating inorganic nanomaterials into FO membranes are obtaining ideal structures to mitigate ICP, reducing membrane fouling and overcoming the trade-off effect. The interactions between nanomaterials and polymer molecular linkers and the functional groups of nanomaterials are the major cause of enhanced performance.25–28 Hence, organic–inorganic hybrid nanocomposite FO membranes with comprehensive performance can replace conventional polymeric FO membranes to meet the requirements of specific application areas. Table 2 summarizes nanomaterials composited with FO membranes and the filtration performance of the FO membranes.
Table 2 Summary of organic–inorganic hybrid nanocomposite FO membranes
|
Nanomodifier |
Polymer |
Component loading |
Test temperature |
FS |
DS |
Operating orientation |
Water flux |
Solute flux |
Reference |
Low-dimensioal carbon based nanomaterials |
CNTs |
Polysulfone |
0.01, 0.05 and 0.1 wt% |
— |
10 mM |
2 M |
FO |
37 L m−2 h−1 |
2.7 g m−2 h−1 |
8 |
PRO |
95.7 L m−2 h−1 |
5.2 g m−2 h−1 |
Polyethyleneimine–poly(amide–imide) |
0.31, 0.62, 1.25 and 2.49 mg L−1 |
— |
Deionized (DI) water |
0.5 M MgCl2 |
FO |
11.4 L m−2 h−1 |
— |
3 |
PRO |
12.5 L m−2 h−1 |
Polysulfone |
0.01, 0.05 and 0.1 wt% |
— |
DI water |
2 mol L−1 MgCl2 |
FO |
8 L m−2 h−1 |
2 g m−2 h−1 |
29 |
Polyethersulfone |
0.5, 1, 1.5, 2 and 2.5 wt% |
— |
DI water |
1000 ppm NaCl |
PRO |
11.5 L m−2 h−1 |
— |
30 |
GO |
Poly L-lysine |
0.08 mg cm−2 |
— |
Milli-Q water |
2 M NaCl |
FO |
11 L m−2 h−1 |
1.3 g m−2 h−1 |
31 |
Polydopamine |
0.6 mg cm−2 |
— |
Milli-Q water |
2 M NaCl |
FO |
13.63 L m−2 h−1 |
0.68 mg min−1 |
32 |
Polysulfone |
0.1, 0.25, 0.5 and 1.0 wt% |
25 °C |
DI water |
0.5 M NaCl |
FO |
19.77 L m−2 h−1 |
3.2 g m−2 h−1 |
33 |
PRO |
41 L m−2 h−1 |
6.3 g m−2 h−1 |
Polyamide |
0.1, 0.25, 0.5 and 1.0 wt% |
25 ± 0.5 °C |
DI water |
2 M NaCl |
FO |
35.4 L m−2 h−1 |
12.5 g m−2 h−1 |
34 |
PRO |
56.6 L m−2 h−1 |
14.5 g m−2 h−1 |
Polyethersulfone |
0.2, 0.5, 0.8 and 1.0 wt% |
— |
DI water |
2 M NaCl |
FO |
41.4 L m−2 h−1 |
170 mM m−2 h−1 |
35 |
Sulfonated polyethersulfone |
0.1% |
25 ± 1 °C |
DI water |
1 M Na2SO4 |
FO |
25 L m−2 h−1 |
1.5 g m−2 h−1 |
36 |
PRO |
30 L m−2 h−1 |
3 g m−2 h−1 |
CNFs |
Cellulose acetate/cellulose triacetate |
0.25, 0.5 and 1 wt% |
25 °C |
10 mM NaCl |
Seawater |
FO |
15.6 L m−2 h−1 |
0.4 g m−2 h−1 |
37 |
Nano mineral materials |
HNTs |
Polysulfone |
0.01, 0.05, 0.1 wt% |
Room temperature |
10 mM NaCl |
2 M NaCl |
FO |
20.1 L m−2 h−1 |
6.5 g m−2 h−1 |
38 |
PRO |
34 L m−2 h−1 |
8 g m−2 h−1 |
Polysulfone |
0.25, 0.5 and 1 wt% |
25 °C |
10 mM NaCl |
2 M NaCl |
FO |
27.71 L m−2 h−1 |
14.62 g m−2 h−1 |
39 |
PRO |
43.25 L m−2 h−1 |
27.52 g m−2 h−1 |
Boehmite |
Cellulose acetate/cellulose triacetate |
0.25, 0.5 and 1 wt% |
— |
10 mM NaCl |
|
FO |
23 L m−2 h−1 |
6.5 g m−2 h−1 |
1 |
PRO |
38.5 L m−2 h−1 |
14.5 g m−2 h−1 |
CaCO3 |
Polysulfone |
5, 7.5 and 10 wt% |
Room temperature |
DI water |
2 M NaCl |
FO |
17 L m−2 h−1 |
45 g m−2 h−1 |
40 |
PRO |
27.6 L m−2 h−1 |
50 g m−2 h−1 |
Polyethersulfone |
3,5 and 10 wt% |
Room temperature |
DI water |
2 M NaCl |
FO |
52 L m−2 h−1 |
16.8 g m−2 h−1 |
41 |
PRO |
62 L m−2 h−1 |
21.6 g m−2 h−1 |
Silica |
Polyacrylonitrile |
0, 5, 10 and 15 wt/wt% |
20 °C to 25 °C |
DI water |
1 M |
FO |
56 L m−2 h−1 |
8 g m−2 h−1 |
42 |
PRO |
74 L m−2 h−1 |
11.8 g m−2 h−1 |
Polysulfone |
1, 3 and 5 wt% |
25 ± 1 °C |
DI water |
2 M NaCl |
FO |
22.3 L m−2 h−1 |
12 g m−2 h−1 |
43 |
PRO |
41.9 L m−2 h−1 |
19 g m−2 h−1 |
Polysulfone |
0.01, 0.05 and 0.1 wt% |
30 °C |
10 mM NaCl |
2 M |
FO |
22 L m−2 h−1 |
1.2 g m−2 h−1 |
44 |
PRO |
36 L m−2 h−1 |
1.5 g m−2 h−1 |
Poly(vinylidene fluoride) |
0.5, 1, 2 and 5 wt% |
Room temperature |
DI water |
1 M |
FO |
52 L m−2 h−1 |
34.84 g m−2 h−1 |
45 |
Zeolite |
Polysulfone |
0.02, 0.05, 0.1, 0.2 and 0.4 w/v% |
20 ± 0.5 °C |
10 mM |
1 M |
FO |
14 L m−2 h−1 |
3 g m−2 h−1 |
21 |
PRO |
30.7 L m−2 h−1 |
7 g m−2 h−1 |
Polysulfone |
0.5 and 1 wt% |
20 ± 0.5 °C |
DI water |
2 M |
FO |
40 L m−2 h−1 |
29 g m−2 h−1 |
10 |
PRO |
86 L m−2 h−1 |
58 g m−2 h−1 |
Metal/metal-oxide nanoparticles |
Ag |
Polydopamine |
0.22, 1.04, and 1.19% |
Room temperature |
Milli-Q water |
0.5 M MgCl2 |
FO |
18 L m−2 h−1 |
3.2 g m−2 h−1 |
46 |
PRO |
42 L m−2 h−1 |
3.4 g m−2 h−1 |
Polydopamine |
— |
25.0 ± 0.5 °C |
DI water |
1 M NaCl |
PRO |
13.31 L m−2 h−1 |
22.39 g m−2 h−1 |
47 |
TiO2 |
Polysulfone |
0.01, 0.05 and 0.1 w/v% |
Room temperature |
10 mM NaCl |
2.0 M NaCl |
FO |
25.5 L m−2 h−1 |
5 g m−2 h−1 |
25 |
PRO |
40.8 L m−2 h−1 |
7.5 g m−2 h−1 |
Polysulfone |
0.5 wt% |
Ambient temperature |
10 mM NaCl |
2 M NaCl |
FO |
29.7 L m−2 h−1 |
3.564 g m−2 h−1 |
48 |
PRO |
56.2 L m−2 h−1 |
13.488 g m−2 h−1 |
Polysulfone |
0, 0.3, 0.6 and 0.9 wt% |
Ambient temperature |
DI water |
2 M NaCl |
FO |
33 L m−2 h−1 |
15.7 g m−2 h−1 |
4 |
PRO |
59.4 L m−2 h−1 |
31 g m−2 h−1 |
Polysulfone |
0, 0.5, 0.75 and 1 wt% |
Ambient temperature |
10 mM NaCl |
2 M NaCl |
FO |
29.7 L m−2 h−1 |
7.3 g m−2 h−1 |
14 |
PRO |
56.27 L m−2 h−1 |
14.14 g m−2 h−1 |
Polysulfone |
0.01, 0.05 and 0.1 wt% |
Ambient temperature |
10 mM NaCl |
0.5 M NaCl |
FO |
17.82 L m−2 h−1 |
2.17 g m−2 h−1 |
49 |
2.1 Low-dimensional carbon-based nanomaterials
In recent years, low-dimensional carbon-based nanomaterials such as carbon nanotubes (CNTs) and graphene oxide (GO) have drawn great attention from scholars worldwide. Low-dimensional carbon-based nanomaterials with abundant oxygen functional groups and high surface areas have shown a series of unique advantages in environmental engineering, such as facile organization and hydrophilic modification. Carbon-based nanomaterials are considered to be the principal element of nanotechnology to enhance membrane performance.50 Employing carbon-based materials in membrane preparation has recently become popular due to their unique properties, such as high specific surface area and smooth water channels.51
2.1.1 Carbon nanotubes. Since their discovery, CNTs have gained increasing attention due to their inner hollow cavities, which are similar to aquaporins. CNTs are composed of graphite lamellae rolled into columns.52–54 Due to their unique characteristics, such as high aspect ratios, molecularly smooth surfaces, nanoscale diameters and inner hollow cavities, CNTs are ideal candidates in various fields,55–58 particularly separation technology. Water molecules travel through the ultra-efficient molecular pipes orders of magnitude faster than through other pores of comparable size.59 This phenomenon is mainly due to the super-hydrophobic and smooth graphitic walls of CNTs, which offer nearly frictionless pathways for water flow. When CNTs are blended into polymer membranes, the additional pathways induced by CNTs and the nanoslits between the CNTs and polymers enhance the permeability of membranes.8 Moreover, CNTs have excellent bactericidal capabilities; they can destroy cytomembranes and disrupt the metabolic pathways of microorganisms.60 It has been widely reported that the permeability, antifouling capacity and mechanical strength of a membrane will significantly increase upon incorporation of CNTs.61–63 Although their high cost limits the large scale industrialization of CNTs, it is expected that this cost will decrease as the technology matures. CNTs represent promising building blocks in a number of industrial applications in the future.64Because CNTs show extraordinary performance and appear to be less susceptible to ICP,65 the possibility of incorporating CNTs into FO membranes has been investigated by several researchers.61,66–68 In 2010, Wang et al.30 synthesized a polyethersulfone/MWCNTs substrate for FO membranes. This was the first time that CNTs were blended into FO membranes. The results demonstrated that incorporating MWCNTs improved both the salt rejection and water permeability of FO membranes.
It is worthwhile to note that the main limitation of employing CNTs in polymeric membranes is their high hydrophobicity and low solubility in solution. Hence, surface functionalization of CNTs is needed to enhance their solubility in solution.69 Amini et al.8 fabricated amino MWCNTs and blended them in a 1,3-phenylendiamine aqueous solution to fabricate a nanocomposite active layer. The water flux and rejection of the resulting membranes improved. With increasing concentration of functionalized MWCNTs, the surface hydrophilicity of the membranes improved in aqueous solution. Similarly, Kunli Goh et al.3 functionalized MWCNTs with immobilized polyethyleneimine–poly(amide–imide) hollow fiber membranes. The results indicated that the fabricated membranes incorporated with MWCNTs showed good properties, including enhanced water permeability without obvious impact on the rejection.
Song et al.29 suggested a novel method to fabricate high performance FO membranes. They designed double-skinned membranes, which showed excellent solute rejection, and incorporated polydopamine with CNTs as the active layer by interfacial polymerization. They found that the CNTs had significant effects on the characteristics of the fabricated membranes. Therefore, it can be concluded that hybrid nanocomposite membranes incorporated with CNTs have higher FO water flux and remarkable antifouling capacity compared to conventional membranes.
Entangled CNTs with high flexibility70,71 and mechanical stiffness form a nonwoven network structure that is known as bucky-papers. Bucky-papers have high tensile moduli (over 1 GPa)72 and porosity.72,73 Bucky-papers can be readily assembled and form ultrathin lamellae from any grade of CNTs. Although binders are employed to stiffen the structures of bucky-papers, the porosity is not greatly influenced.74 Therefore, bucky-papers have drawn a great deal of attention75,76 in the water separation77 and purification74 industries. The high compressibility78 of bucky-papers restricts their use in reverse osmosis processes. Hence, researchers have turned their focus to FO due to the low pressures employed in this process. Dumée et al.79 investigated a novel approach to interfacial polymerization on the surfaces of bucky-paper materials which were functionalized with hydroxyl groups. The fabricated super-porous bucky-paper membranes exhibited high hydrophilicity and excellent FO characteristics.
2.1.2 Graphene oxide. Two-dimensional GO nanosheets are a typical nanomaterial with extremely high specific surface area and atomic degree thickness.80,81 Also, their surfaces contain abundant oxygen-containing functional groups, which can promote their interaction with polymers. Due to its unique structure and surface properties, GO is an ideal candidate for various applications.27,82–85 Among these, membrane separation is a promising application to benefit from GO. Compared with other fillers, the extremely high aspect- and surface area-to-volume ratios of GO nanosheets promote better interactions with the polymer matrix. These unique dimensional and surface properties of GO nanosheets offer excellent potential for fabricating composite materials with excellent physical properties, flexible chemical functionalization, strong hydrophilicity and excellent antifouling properties.80,86–88Studies using GO as a modifier to prepare nanofiltration and ultrafiltration hybrid nanocomposite membranes have achieved great improvements in hydrophilic and antifouling properties.86,89–91 However, water desalination with GO-based membranes still faces challenges and remains controversial. Some researchers have reported that solute rejection of GO-based membranes or reduced GO-based membranes is weak in water desalination,80,82,92–95 while other researchers have reported the opposite.96,97 This argument has limited the research and large scale development of GO-based membranes. To overcome this dilemma, Sun et al.98 studied and revealed the mechanism behind the controversy regarding GO-based membranes in water desalination. With the aid of isotope tracer labelling and molecular dynamics studies in water and ion diffusion, they showed the excellent potential of GO-based membranes in water desalination. Fig. 2 shows schematics of the mechanisms of water desalination and photographs of GO-based membranes with cross-sectional SEM images for concentration gradient-driven diffusion (Fig. 2(A)) and pressure-driven filtration (Fig. 2(B)). However, employing excess pressure will weaken the water–ion interactions with GO interlamination nanochannels and sequentially reduce the selectivity. Meanwhile, in concentration gradient-driven diffusion, GO-based membranes demonstrate intrinsic high water/ion selectivity, which confirms that GO is suitable for FO rather than pressure-driven filtration.
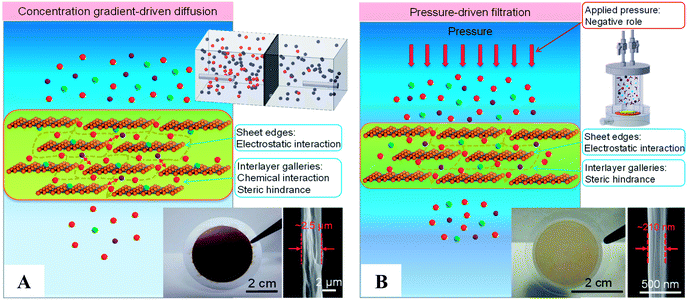 |
| Fig. 2 (A) Schematic of the mechanism of water desalination, experimental setup, and photograph of a lamellar GO membrane on a microfilter with a cross-sectional SEM image for concentration gradient-driven diffusion. (B) Schematic of the mechanism of water desalination, experimental setup, and photograph of a lamellar GO membrane on a microfilter with a crosssectional SEM image for pressure-driven filtration.98 | |
The potential of lamellar GO as a modification to improve the performance of FO membranes was also confirmed by Park et al.33 They blended lamellar GO with polysulfone to obtain an organic–inorganic hybrid nanocomposite FO support layer. Subsequently, an FO membrane with high permeability and selectivity was obtained. Additionally, the lower structural parameter and higher hydrophilicity also enhanced the water permeability of the FO membrane. Later, a GO hybrid nanocomposite FO support layer was employed to improve the hydrophilicity and anti-fouling performance of a membrane. However, GO could not provide its full benefits when it was buried inside the polymeric matrix. To take advantage of the excellent properties of GO, Shen et al.34 incorporated GO nanosheets with a polyamide active layer to fabricate a hybrid nanocomposite membrane for the FO process. This method utilized very little GO while attaining excellent performance, including high separation performance and water flux and decreased fouling propensity, by simply embedding a small quantity of GO into the support layer.
Maintaining the stability of a GO hybrid nanocomposite membrane is also necessary in water purification treatment. Simple blending or coating methods to fabricate GO hybrid nanocomposite membranes carry the risk of diffusing hydrophilic lamellar GO into the hydrosphere, which can be absorbed by aquatic creatures and thereby affect human beings. Hence, researchers have made efforts to prepare GO lamellae that are strongly bound to each other and the membrane to mitigate this risk. Hanaa et al.31 attached GO to the active layers of FO membranes through a poly L-lysine intermediary by both layer-by-layer (LbL) and hybrid grafting methods. The resulting hybrid FO membranes exhibited excellent antifouling properties. These membranes killed 99% of bacteria and showed reduced permeability compared to the original membrane. For the same purpose, Hegab et al.32 employed the bioadhesive polydopamine to immobilize GO onto the surface of FO membranes via self-assembly and oxidative polymerization methods. The fabricated membrane simultaneously possessed high permeability, high rejection and excellent antibiofouling properties.
Graphitic carbon nitride, which has a similar two-dimensional laminated structure to graphene, is a derivative of GO. It possesses excellent optical and chemical properties as well as good catalytic activity99 and thermal stability and has attracted increasing attention. Graphitic carbon nitride is a cellular structure with a plentiful curved lamellar morphology.100 It can enhance the hydrophilicity of membranes because its nitrogen atoms can form hydrogen bonds with water molecules. Wang et al.35 prepared graphitic carbon nitride as a modifier for a porous polyethersulfone support layer of FO membranes. The results revealed that a lower structural parameter and ICP were obtained, which suggests that graphitic carbon nitride is an effective modifier to enhance FO membrane performance.
2.1.3 Carbon nanofibers (CNFs). CNFs consist of rolled multi-layer graphite sheets with diameters in the range of 10 nm to 500 nm. Due to their excellent chemical activity and electroconductivity, high tensile moduli and strength, they are useful in many fields. CNFs are a quasi-one-dimensional carbon material with similarities to both CNTs and ordinary carbon fibers. Unlike CNTs or other carbon nanostructures, which have low dispersion and chemical inertness, the sidewalls of CNFs have higher chemical activity and can be readily chemically functionalized with more options. The edges of CNFs are exposed and their edge sites are active, which is beneficial to the chemical functionalization of the surface of CNFs to improve their dispersibility in casting solutions. Due to their high dispersibility in polymeric matrices, CNFs are considered to be a candidate for employment in the fabrication of high-performance membranes. Zoheir Dabaghian et al.37 synthesized a cellulose triacetate FO membrane incorporated with carboxylated CNFs via a phase inversion method. The modified membrane exhibited high water flux and low solute permeation. Tensile strength measurements confirmed that this parameter of the modified FO membrane was much higher than that of unmodified cellulose triacetate.
2.2 Nanomineral materials
Nanomineral materials, including montmorillonite, halloysite, and zeolites, are nanomaterials with enormous surface areas and porous structures. Nanomineral materials have numerous advantageous properties, such as porosity, good adsorption performance, stability, wide availability of raw materials, low cost, large specific surface area, good adsorption performance, light weight and lack of secondary pollution. Due to their unique structures and excellent properties, nanominerals are suitable for water purification. Studies revealed that the addition of nanomineral materials improves the water permeability and solute rejection of membranes, while the increased number of hydrophilic groups improves their anti-pollution properties. Dispersion of nanomineral materials is key to the preparation of thin film nanocomposite membranes. Sufficient dispersion in the membrane increases its pore size uniformity, porosity, and water flux. Moreover, nanomineral loading can result in high porosity and ideal hydrophilicity of membranes that mitigate the negative effects of ICP, which generally influences FO processes.
2.2.1 Halloysite nanotubes (HNTs). Alumina-silicates (also called HNTs) are nanominerals that can be obtained from natural origins and possess excellent biocompatibility. According to electric effects, HNTs exhibit dual charge functionality. Containing numerous siloxane groups, the ektexine of HNTs is negatively charged, while the endosexine is rich in hydroxyl groups and positively charged.101 Moreover, the tubular structure and low content of hydroxyl groups on the surface of HNTs endow them with good consistency in polymeric matrices.102 Due to these interesting properties, HNTs are promising modifiers in membrane separation processes.103 The influences of HNT incorporation on the filtration performance of FO membranes include hydrophilicity, porosity, roughness, water flux and the structural parameter. Although their structure is similar to that of CNTs, HNTs possess a unique dual charge functionality and significantly lower cost.104With the aim of improving membrane performance, Ghanbari et al.38 incorporated various concentrations of HNTs into the active layer of FO membranes by in situ interfacial polymerization. The results indicated that the water flux, rejection and antifouling properties of all the fabricated hybrid nanocomposite FO membranes were better than those of the pure polymeric membrane. Subsequently, the group blended HNTs into a polysulfone support layer to study the influence of HNTs on ICP behavior.39 The results showed that the incorporation of HNTs in the support layer can reduce the structural parameter and mitigate ICP.
2.2.2 Boehmite. Boehmite nanoparticles, which have the chemical composition AlOOH, contain abundant hydroxyl groups on their surfaces. Studies have revealed that due to their porous and hydrophilic structure, incorporating boehmite nanoparticles can enhance the performance of membranes, such as their water flux, structural parameter and separation performance.1,105,106 It was proved that 0.5 wt% capacity of boehmite nanoparticles could result in a threefold increment of water permeability and a decreased structural parameter of 0.53 mm without sacrificing solution rejection compared with the original pure membrane.1Zirehpour et al.1employed boehmite to modify cellulose triacetate FO membranes. A strong interaction formed due to hydrogenic reactions between the hydroxyl groups in boehmite and cellulose triacetate, which enhanced the compatibility between the polymeric matrix and boehmite nanoparticles. Hence, the fabricated membrane gave rise to more effective water flux.
2.2.3 Silica. Silica as an inorganic additive to prepare hybrid nanocomposite membranes has a wide range of applications due to its mild reactivity, thermal resistance, convenient operation, mechanical strength, small size, nontoxic nature, strong surface energy, good suspendability in aqueous solution and environmental friendliness.107–110 Researchers testified that the incorporation of silica nanoparticles afforded polymeric membranes with enhanced mechanical strength111–116 and thermal stability.117–120 In addition, silica nanoparticles have an impact on the polymerization reactions of the polymeric matrix.121 This property is due to the strong interactions at the interface between the silica and the polymeric matrix121 which is formed by the immobilized amorphous layer of polymer molecules on the silica nanoparticles. Because silica nanoparticles are smaller in size, they have better dispersion performance in solution. Silica/polyamide reverse osmosis membranes have higher water flux and rejection compared with unmodified reverse osmosis membranes,44 which provides a good choice for FO applications. Niksefat et al.44 fabricated polyamide nanocomposite FO membranes containing silica nanoparticles via in situ interfacial polymerization. The fabricated nanocomposite membrane exhibited greatly enhanced water permeability and solute rejection compared to the original membrane with silica loading concentrations between 0.01 and 0.1 wt%.Novel amorphous silica nanoparticle-incorporated poly(vinylidine fluoride) electrospun nanofiber mats were fabricated by Obaid et al.45 as support layers for FO membranes. The results showed that the membrane showed high salt rejection and water flux. Moreover, this formulation displayed the lowest structural parameter (S = 29.7 μm), which represents approximately 69% reduction compared to the pristine membrane. Electrospinning is an excellent technology to produce nanofiber films with advantages such as low tortuosity, high porosity, and low thickness. The nanofiber-composed scaffold structure is an ideal candidate as a support layer in FO processes; it has remarkable advantages in comparison to conventional sponge-like or finger-like pore structures. Nanofiber films as support layers possess unique advantages, including internally connected channels for salt and water transportation. This property can provide an excellent environment to mitigate ICP.122
2.2.4 Zeolite. Zeolite was the first nanomaterial to be induced into FO membranes. Before that, zeolite was frequently used as a modifier in polymeric membranes for gas separation or pervaporation due to its uniform pore size distribution, channel structures and abundant negatively charged sites. The unique sub-nanometer pores of zeolites provide shape selectivity, which improves the adsorption efficiency of gas molecules.123 Zeolite is composed of aluminosilicates, which provide negatively charged defect sites to neutralize the positive charges of protons and ultimately form Brønsted acid sites.124 These unique characteristics have drawn the attention of researchers and demonstrate the enormous potential of zeolite in separation processes. Some types of zeolite, such as NaA, are deemed to have the highest hydrophilicities among inorganic nanomaterials. They are so stable in most aqueous and organic solvents that it is difficult to break them off from the polymeric matrix.125 It has been testified that blending zeolite in the polyamide active layer of reverse osmosis membranes126–129 can enhance water flux without sacrificing solute rejection due to the presence of abundant sub-nanometer pores which play the role of preferential flow channels. In the separation process, water molecules pass through these tiny sub-nanometer pores, which are too small for solutes to cross.21 Therefore, incorporation of zeolite in polymeric FO membranes was demonstrated to improve their water permeability without significant loss of salt rejection. Although zeolite hybrid nanocomposite membranes were originally produced for gas separation and reverse osmosis processes, their substantially increased water flux also suggests their usefulness in FO. Furthermore, blending zeolite into the support layer results in enhanced porosity and mitigates the ICP effect in FO processes. Ma et al. blended NaY zeolite into the polyamide active layer; the resulting FO membrane exhibited higher water permeability, possibly because of the porous structure of zeolite.21 Subsequently, they incorporated zeolite nanoparticles into the support layer of FO membranes and fabricated a polysulfone hybrid nanocomposite matrix which exhibited higher porosity and hydrophilicity. The resulting membrane also showed significantly enhanced water permeability and a decreased substrate structural parameter compared to the original polysulfone support membrane.10
2.2.5 Nano-CaCO3. CaCO3 nanoparticles are among the most widespread, industrialized and inexpensive nanomaterials. The mature production technology of CaCO3 nanoparticles is due to their surface polarity and their readily tunable particle size in production processes.130 Thus, it is possible for CaCO3 nanoparticles to meet the heavy demand of large scale production of polymeric membranes and play the role of sacrificial components. Wu et al.40 blended CaCO3 nanoparticles into a polysulfone substrate and then dissolved it with hydrochloric acid to increase the porosity of the support layer. The higher porosity of the fabricated FO membrane led to a smaller structural parameter and, thus, decreased ICP, which is advantageous to enhance water permeability and reduce mass transfer resistance.Moreover, CaCO3 is a good biomineral which also has high hydrophilicity due to its ionic bonds and hydrogen bonds with water molecules. Inspired by bio-mineralization processes in nature and the intrinsic hydrophilicity of minerals, inorganic mineral coating is an alternative method to impart hydrophilicity to a support layer without sacrificing other functional properties. Biomineralization can form a stable organic–inorganic hybrid structure by the interactions between certain organic and inorganic ions. Qing et al.41 coated CaCO3 continuously and uniformly throughout a polyethersulfone support layer. Resulting from the intrinsic hydrophilicity of the CaCO3 coating, the hydrophilicity of the support layer was significantly increased and the structural parameter of the membrane was reduced to a similar value to those of cellulose-based membranes, with unchanged mechanical strength.
2.3 Metal/metal-oxide nanoparticles
For decades, metal nanoparticles and metal oxide nanoparticles have been widely used to address various environmental issues, especially in water desalination and regeneration.131–133 Metal nanoparticles and metal oxide nanoparticles are known to be environmentally friendly, stable to UV irradiation, antibacterial and highly hydrophilic.134 Due to the higher affinity of metal oxides to water, membranes incorporating metal and metal oxide nanoparticles are more hydrophilic than pure polymeric membranes.135 Additionally, some metal oxide nanoparticles have accessible reactive anchoring sites, such as hydroxyl and silanol groups, for further surface reactions to facilitate interactions with the polymer host matrix.136 Also, some metal and metal-oxide nanoparticles have unique properties, such as antibacterial properties and photochemical catalysis, which aid FO membrane processes.
2.3.1 Ag nanoparticles. Ag nanoparticles have the most comprehensive antibacterial spectrum; they are effective against various aquatic microorganisms, such as bacteria, fungi, and algae.137 Ag nanoparticles can destroy the cytomembrane and impede the metabolism of microorganisms by releasing dissolved Ag or producing active oxygen.138 Introducing Ag nanoparticles into membranes to filter water rich in microorganisms has been suggested as a method to alleviate the biological contamination resulting from blooms of microorganisms, resulting in innocuous and pollution-free water sources.139–141 The antibiofouling properties of Ag nanoparticles are durable. Their dissolving and releasing behaviors can be well tuned compared to those of Ag ions. Hence, Ag nanoparticles have gained increasing focus for their excellent antibiofouling properties.142 Ag nanoparticles have been incorporated into microfiltration,138,143 ultrafiltration,144,145 nanofiltration146 and reverse osmosis147 membranes by different methods, such as surface modification, blending and in situ interfacial polymerization. Subsequently, Liu et al.148 fabricated Ag hybrid nanocomposite nanofiltration and FO membranes by an LbL assembly method. The assembly of Ag nanoparticles in the membranes did not produce negative effects on the fabricated membrane. Also, even at a low concentration of Ag nanoparticles, the membrane performance in separation processes was significantly enhanced. Furthermore, the antibiofouling properties of the resulting Ag nanocomposite membranes were also greatly improved against both Gram-positive Bacillus subtilis and Gram-negative Escherichia coli.
2.3.2 TiO2 nanoparticles. TiO2 nanoparticles are one of the most promising metal oxide nanoparticles due to their high hydrophilicity and excellent photocatalytic properties with perfect mechanisms.149,150 As an acknowledged photocatalytic material, TiO2 has been extensively used in disinfection and decomposition applications; these characteristics also make TiO2 a promising anti-fouling modifier.25,151 Moreover, due to the chemical stability, controllable morphology, surface properties, photocatalytic function and antifouling performance of TiO2 nanoparticles, they are useful in membrane processes.152–156 Numerous studies regarding the introduction of TiO2 nanoparticles into membranes have confirmed its viability and effectiveness, leading not only to enhanced hydrophilicity and water permeability, but also to sterilization and antibiofouling abilities.151,157,158 The inherent photocatalytic properties of TiO2 aid in enhancing the antifouling performance of membranes159 by disintegrating macromolecular contaminants. Amini's group4 introduced TiO2 nanoparticles into a polysulfone support layer to reduce the structural parameter and alleviate the ICP of FO membranes. The resulting support layer exhibited both high hydrophilicity and porosity with the presence of TiO2 nanoparticles.However, the performance of hybrid nanocomposite membranes is restricted by nanoparticle agglomeration. Studies have been performed to enhance the consistency of TiO2 nanoparticles in the polymeric matrix and produce a uniform surface. Maryam Amini et al.160 used a silicane coupling agent to achieve chemical modification of TiO2 and incorporated it into a polyamide active layer by in situ interfacial polymerization. The results indicated that the introduction of modified TiO2 significantly changed the surface properties of FO membranes and mitigated the agglomeration behavior. The hybrid nanocomposite FO membranes showed high water flux and stable rejection rates at all TiO2 loading concentrations compared with the original membrane.
3. Effects of modification methods on FO membrane performance
In recent years, with the development of membrane separation techniques in water treatment and other fields, the requirements of membrane function, such as permeability, selectivity, anti-pollution, chemical and thermal stability, are becoming increasingly strict. Traditional membrane fabrication methods have difficulty meeting these application requirements. Therefore, researchers have begun to turn their focus to developing new composite membranes and modification methods to obtain satisfactory properties. Membrane modification is considered to be an effective method to improve the comprehensive performance of membranes. The modification methods can be divided into chemical modification and physical modification. Chemical modification methods include LbL assembly, grafting, and hydrolysis. Physical modification methods include blending methods, surface coating, and in situ interfacial polymerization. In this section, four main methods, including blending, in situ interfacial polymerization, surface grafting and LbL assembly, are listed and analyzed. Fig. 3 provides a schematic of these modification methods of nanocomposite membranes.
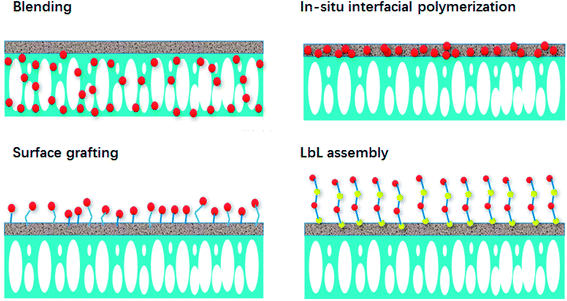 |
| Fig. 3 Schematic of various modification methods of nanocomposite membranes. | |
3.1 Blending
Blending is a simple and common method to prepare hybrid membranes that can be used with a large range of materials; it is one of the most important methods to modify polymeric membranes. The introduction of nanomaterials enhances the mechanical strength of membranes and prevents collapse and structure destruction of the porous support layer. The blending membranes are typically obtained by mixing an inorganic dispersed phase in a continuous polymeric matrix. Blending nanomaterials such as TiO2 nanoparticles,4,14 CNTs,30 porous zeolite nanoparticles10 and GO nanosheets35 into the support layer of FO membranes has been attempted, and the resulting membranes exhibited brilliant performance. Especially, these nanomaterials enhance the physical and structural characteristics of the support layer, which leads to increased hydrophilicity and/or porosity.33
Blending nanomaterials can significantly enhance membrane performance, such as water flux, rejection, stability, antifouling, and catalytic activity, in FO membrane separation processes;161–163 meanwhile, the adverse impact of ICP is mitigated.164 The size, dispersity, morphology and compatibility of the nanomaterials affect the performance of the fabricated membrane. Preparing membranes by blending is a simple process which is easy to operate, and the concentration of the components can be readily controlled. However, the inorganic components, especially nanoparticles, can readily aggregate. For the purpose of preventing inorganic nanomaterials from agglomerating and enhancing the consistency between the organic and inorganic phases, it is significant to modify the inorganic nanomaterials so as to obtain stronger interactions with the polymeric matrix. Additionally, incorporation of a solubilizing agent or crosslinking agent can enhance the consistency and modify the defects of the hybrid nanocomposite membranes. GO,33 CNTs,3,30 TiO2,4,14,48 zeolite,10 silica,10 and many other nanomaterials have been used in blending methods to synthesize FO membranes. Studies confirmed that blending nanomaterials into the support layers of FO membranes can effectively enhance water flux without reducing rejection, which results from the higher hydrophilicity and porosity conferred by the nanoadditive. In addition, the polymer layer can also benefit from the physical mechanics, magnetism, optics and conductivity, and catalytic and biomedical properties of doped inorganic nanoparticles.
3.2 In situ interfacial polymerization
In situ interfacial polymerization is defined as uniformly mixing inorganic particles with organic monomers and inducing monomer polymerization under appropriate conditions.156 The fabricated ultrathin film serves as the active layer of an asymmetric membrane. In situ interfacial polymerization methods include suspension polymerization, dispersion polymerization, emulsion polymerization and polymerization between the functional groups on the inorganic particles and the monomer so as to immobilize the polymer phase network structure as a chemical bond. In situ interfacial polymerization is convenient to operate; however, it does have challenges, such as facile agglomeration of the inorganic nanoparticles and uneven dispersion. Studies have confirmed that hybrid active layers fabricated by introducing nanomaterials in a monomer solution significantly improve membrane performance, such as water flux, solute rejection, catalytic activity, specific area, antifouling and thermal stability in membrane separation processes. To date, hybrid nanocomposite FO membranes fabricated by in situ interfacial polymerization methods have been developed by introducing TiO2,25,165 titanate nanotubes,49 MWCNTs,8 HNTs,38 silica,44 GO31,33 and zeolite21 into the polyamide active layer. This corresponds to the concept of nanocomposite membranes that incorporate nanomaterials into the active layers of conventional pure polymeric membranes.127
A conflict in FO separation processes is that solute rejection cannot increase simultaneously with water flux; this is called the trade-off effect. That is to say, a membrane with high water permeability usually has low rejection. Therefore, preparing FO membranes with both high flux and high solute rejection is a great challenge. Introducing inorganic nanomaterials in polyamide active layers via in situ interfacial polymerization is an effective solution of the trade-off effect which can not only improve the hydrophilicity, but can also impart antifouling properties to a membrane. The inorganic nanoparticles doped in the polyamide layer can increase the water flux of the membrane by providing water channels directly or by changing the network structure of the membrane. Therefore, the doping of porous inorganic nanomaterials into polyamide active layers has received focus to improve the separation performance of membranes.
3.3 Surface grafting
Surface grafting involves introducing inorganic nanoparticles or organic functional groups onto the surface of membranes through various methods, such as photoinitiation and induction by radiation. Free radical active sites are produced on the polymeric molecular chain of the membrane surface through a series of pretreatments, and the radical ion is then polymerized with the modified monomer. Analogous methods to introduce inorganic nanomaterials into polymeric membranes, such as blending and depositing, face a common problem: the binding forces between the nanomaterials and the polymeric membrane are so weak that the nanomaterials can be readily separated from the membrane. Connecting inorganic nanomaterials with the polymeric membrane by chemical bonds, such as surface grafting, is a good solution to enhance the immobility of hybrid nanocomposite membranes.166 This suggests that surface grafting is an ideal method to fabricate immobile and durable hybrid nanocomposite membranes. Zhong et al.167 fabricated nanofiltration membranes using sponge-like sulfonated polyphenylenesulfone support layers with positive charge via a UV-initiated grafting method. However, only photosensitive polymers can be used as support layer materials for UV grafting, which impedes the development of this method. Hegab et al.31 prepared hybrid nanocomposite FO membranes by surface grafting to introduce GO on the surface of a polyamide active layer.
3.4 Layer-by-layer (LbL) assembly
LbL assembly is used to alternately form oppositely charged polyelectrolyte thin films on a matrix which are connected by electrostatic absorption and van der Waals forces.36,168 LbL assembly has received focus because it is a convenient and versatile method to form active layers for high-performance nanofiltration,169,170 reverse osmosis and FO membranes.171,172 LbL is a highly versatile membrane preparation technology with good thermal stability, high solvent resistance, low operating expense, etc.173–175 Nanomaterials can be introduced into the layered structure of LbL assembly membranes flexibly with tunable loading components and structures. LbL assembly show great potential in industries such as water treatment and food processing.5,176 Employing LbL assembly, Liu et al.148 prepared Ag hybrid nanocomposite FO membranes. They assembled Ag nanoparticles on the surfaces of the FO membranes; at low loading concentrations of Ag nanoparticles, there was no negative impact on the membrane performance. The separation performance of the fabricated LbL assembly hybrid nanocomposite membranes was no less than those of most nanofiltration-like FO membranes. Furthermore, the Ag hybrid nanocomposite FO membranes demonstrated brilliant antibiofouling characteristics against both Gram-positive Bacillus subtilis and Gram-negative Escherichia coli. Hegab et al.32 prepared polydopamine/GO composites and introduced them onto the support layers of FO membranes via LbL assembly. The polydopamine played the role of reducing GO and bonding it onto the membrane surface via self-assembly and oxidative polymerization. The fabricated membrane possessed enhanced water flux and solute rejection as well as excellent antibiofouling performance.
4. Discussion and outlook
With the continuing development and progress in nanotechnology, novel methods have inspired the design and production of multifunctional hybrid nanocomposite FO membranes.177 Introducing inorganic nanomaterials can result not only in excellent separation performance but also in new functions that are inherited from the inorganic nanomaterials. Brand new insight has been provided to create the next generation of high performance FO membranes with antifouling properties, low ICP and decreased trade-off effects. Organic–inorganic hybrid nanocomposite FO membranes, in contrast with conventional polymeric membranes, are confirmed to have great promise to overcome the bottleneck of ICP. However, the applications of these nanocomposite FO membranes have yet to expand beyond the laboratory. Despite a series of excellent enhancements in performance, successful practical applications and commercialization are rare. Some challenges still exist for the large scale industrial application of FO membranes, including creating suitable draw solutes and building integrated sustainable FO systems. Draw solution is one of the key factors of FO processes which distinguishes FO from other pressure-driven membrane techniques. An ideal draw solution must furnish a high osmotic gradient and possess efficient recovery with low energy consumption. Furthermore, a system for water purification and draw solution reuse is also necessary. One example is an FO–ultrafiltration (FO–UF) series for desalination with an FO membrane as the main component for salt rejection and a UF membrane as a post processing method for regeneration of the draw solution.178 It has been suggested that more research should be focused on integrated FO systems, as they may be an important factor in the large scale industrial application of FO in the future.179,180
Regarding hybrid nanocomposite FO membranes, the main challenges include the agglomeration of nanomaterials, low filtration efficiency caused by ICP, and the high cost of nanomaterials. The commercialization of nanocomposite membranes for water treatment is still in its infancy. Therefore, more studies on organic–inorganic hybrid nanocomposite FO membranes are needed to achieve better performance and overcome the barriers that limit FO. This section discusses the challenges facing the practical application of nanocomposite FO and some advanced nanotechnology in the membrane field that is beneficial to FO.
First, agglomeration is one of the main obstacles to introducing nanoparticles in polymeric membranes; it leads not only to uneven distribution in the membrane but also to decreased separation abilities by changing membrane structures, such as surface morphology and porosity. Aggregation is a common phenomenon that occurs during the preparation of hybrid nanocomposite membranes and impedes the homogeneous dispersion of nanomaterials in the polymeric matrix. Many efforts have been made to alleviate this phenomenon, among which surface modification of nanomaterials and optimizing the fabrication conditions are conventional methods that have achieved improved dispersion of nanomaterials.
In addition to surface modification and technology optimization, multi-component composite nanomaterials182 have become increasingly popular in membrane preparation due to the various options and multiform characteristics provided by different nanomaterial combinations. For example, GO nanosheets were employed to stabilize Ag nanoparticles and enhance the contact between Ag and bacteria.181 Ag nanoparticles were dispersed uniformly on the surface of GO nanosheets as an FO membrane modifier to prevent their agglomeration. Fig. 4 shows a schematic of the synthesis route of Ag-decorated GO nanosheets, and HR-TEM images of the fabricated nanosheet are shown in Fig. 5. Similarly, Ghanbari et al.165 fabricated a TiO2/HNTs composite nanomaterial via a one-step solvothermal method as an additive for FO membranes. Regarding filtration performance, the hybrid nanocomposite membrane showed excellent water flux and solute rejection. Due to the hollow tubiform structure of HNTs and the addition of anti-fouling and photochemical catalysis abilities from TiO2, TiO2/HNTs is a beneficial modifier. These composite nanomaterials are promising in improving the antifouling behavior of polymeric FO membranes for organic pollution separation. Fig. 6 illustrates the TiO2 loading on the surface of the HNTs, and Fig. 7 shows transmission electron microscopy (TEM) images of TiO2/HNTs with different scale bars.
 |
| Fig. 4 Covalently bonded AgNP-decorated GO nanosheets through click chemistry on FO membranes: (A) in situ Ag nanoparticles synthesized onto the GO nanosheets, (B) amide forming reaction and thiol functionalization of the FO membrane, and (C) covalent bonding of the GO/Ag nanocomposites to the FO membrane surface.181 | |
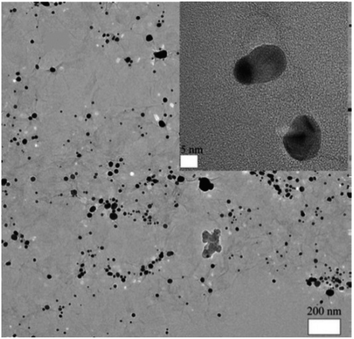 |
| Fig. 5 High resolution transmission electron microscopy (HR-TEM) images of the GO/Ag nanocomposite.181 | |
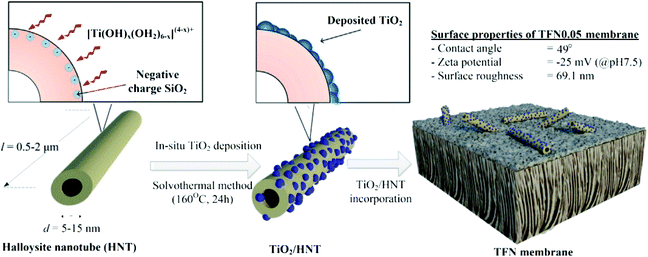 |
| Fig. 6 Schematic of TiO2 loading on the surface of HNTs.165 | |
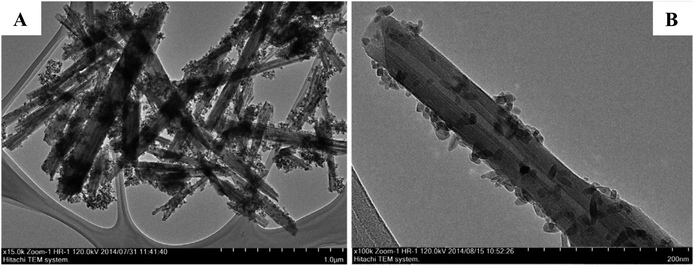 |
| Fig. 7 TEM images of TiO2/HNTs with different scale bars: (A) 1000 nm and (B) 200 nm.165 | |
Second, some nanomaterials can provide effective water transformation channels, such as CNTs. Recent computer simulation studies have indicated the high selectivity and water flux of CNTs; thus, they are ideal candidates for adsorption and separation applications.183,184 However, blending a small quantity of CNTs and similar nanomaterials cannot ensure that water molecules are induced to move only through the nanotubes. In order to make full use of the water transport channels of CNTs, for the first time in 2004, researchers incorporated an array of aligned CNTs across a polymer matrix vertically and compactly to form a well-organized nanoporous membrane structure.185 Fig. 8(A) shows a SEM micrograph of the as-grown MWCNTs. In Fig. 8(B), the ideal membrane structure diagram is presented. The lacunes between the CNTs are padded with a continuous polymer matrix, and the generally closed ends of the CNTs are etched open. Fig. 8(C) reveals the cleaved edge of the freestanding CNT membrane. After that, researchers began studying the mechanism of liquid transport through nano-sized channels. It was found that in the cavities of CNTs, the quantity of liquid transport was 1000 times greater than predicted. A microgeometry theory was proposed regarding the use of aligned CNTs186 for water treatment,187 and an approach to establishing an impeccable membrane system was provided.188 Among the studies on CNT-based nanocomposite membranes in the water treatment field, the aligned CNTs matrix is believed to be a potential candidate as a support layer of FO membranes. Its superpermeable property has great promise in increasing the water flux of FO membranes as well as decreasing ICP.
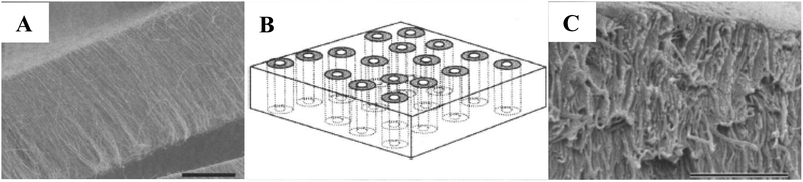 |
| Fig. 8 (A) An as-grown, dense MWCNTs array produced with an Fe-catalyzed chemical vapor deposition process. Scale bar, 50 μm. (B) Schematic of the target membrane structure. With a polymer embedded between the CNTs, a viable membrane structure can be readily produced, with the pore being the rigid inner-tube diameter of the CNT. (C) The cleaved edge of the CNT-PS membrane after exposure to H2O plasma oxidation. The PS matrix is slightly removed to contrast the alignment of the CNTs across the membrane. Scale bar, 2.5 μm.185 | |
Third, blending modification and surface modification are two main methods to introduce inorganic nanoparticles into organic polymer membranes.189,190 However, nanomaterials cannot be strongly anchored on the surface of the membranes by surface modifications such as coating. The nanomaterials may be lost in the filtration process, which not only affects the membrane performance, but can also readily cause secondary water pollution. Although blending nanomaterials with casting solution can mitigate the loss of nanomaterials, there is an inherent dilemma that most nanomaterials are embedded within the polymeric matrix when the film is formed. This phenomenon decreases the modification efficiency severely, and the advantage of the nanomaterial surface structure cannot be fully exploited. Based on the above problems, our group191 proposed a “blending-migration induced by a magnetic field” route to prepare nanocomposite membranes. We induced migration of magnetic nanomaterials to the top surface of the film using a magnetic field and fabricated an ultrafiltration membrane with hydrophilicity as well as antimicrobial and autocatalytic performance. Herein, a Fe3O4/GO–poly(vinylidene fluoride) hybrid ultrafiltration membrane was fabricated via a combination of magnetic field-induced casting and a phase inversion technique. Fe3O4/GO nanocomposites migrated toward the top surface of the membrane due to magnetic attraction and thereby rendered the surface highly hydrophilic, with robust resistance to fouling. Fig. 9 illustrates the main mechanism of GO migration under a magnetic field. Fig. 9(A) shows the procedure of the migration, while Fig. 9(B) shows the final results with/without a magnetic field. This technique is promising and useful for the preparation of support layers of FO membranes. The gradient distribution of nanomaterials in the polymeric matrix can enhance the utilization ratio of the nanomaterials and mitigate ICP effectively.
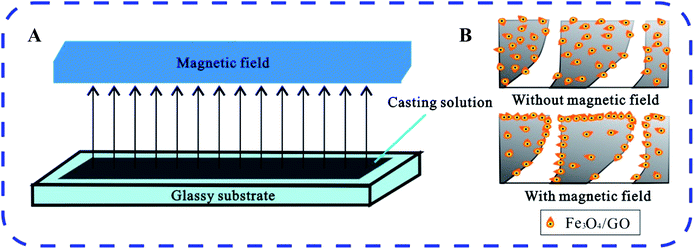 |
| Fig. 9 Schematic of the mechanism of GO migration under a magnetic field.191 | |
Finally, some negative critiques indicate that the nanomaterials commonly used in membrane preparation have high intrinsic cost, such as TiO2, Ag nanoparticles, and GO, related to their raw materials and preparation technologies. To date, there have been numerous laboratory-scale studies on organic–inorganic hybrid nanocomposite FO membranes. However, due to their cost and some other factors, very little large scale production or industrial application has been practiced. Therefore, developing low-cost nanomaterials and cost-effective FO membranes with execellent performance is a future goal. Cost-effective large scale membrane fabrication includes the supplies of nanomaterials, additional procedures for nanomaterial incorporation, and monitoring of the long-term stability of membranes under practical application conditions. The less expensive ZnO, CaCO3,40,41 HNTs,38,39 zeolite,10,21 etc. are seemingly more economically feasible substitutes. More studies are still needed to reduce the expense of nanomaterials and identify new nanomaterials with lower production costs.
Conflicts of interest
There are no conflicts to declare.
Acknowledgements
The work was funded by the National Natural Science Foundation of China (11575126), the Qaidam Salt Chemical Joint Fund of National Natural Science Foundation of China – People's Government of Qinghai Province (U1607117), the Natural Science Foundation of Tianjin (16JCZDJC36400) and the Science and Technology Plans of Tianjin (15PTSYJC00230).
References
- A. Zirehpour, A. Rahimpour, F. Seyedpour and M. Jahanshahi, Desalination, 2015, 371, 46–57 CrossRef CAS.
- P. Lu, S. Liang, T. Zhou, X. Mei, Y. Zhang, C. Zhang, A. Umar and Q. Wang, RSC Adv., 2016, 6 Search PubMed.
- K. Goh, L. Setiawan, L. Wei, W. Jiang, R. Wang and Y. Chen, J. Membr. Sci., 2013, 446, 244–254 CrossRef CAS.
- D. Emadzadeh, W. J. Lau, T. Matsuura, A. F. Ismail and M. Rahbari-Sisakht, J. Membr. Sci., 2014, 449, 74–85 CrossRef CAS.
- T. Cath, A. Childress and M. Elimelech, J. Membr. Sci., 2006, 281, 70–87 CrossRef CAS.
- M. Obaid, H. O. Mohamed, A. S. Yasin, O. A. Fadali, K. A. Khalil, T. Kim and N. A. M. Barakat, RSC Adv., 2016, 6, 104933 RSC.
- Q. Yang, K. Y. Wang and T. S. Chung, Environ. Sci. Technol., 2009, 43, 2800–2805 CrossRef CAS PubMed.
- M. Amini, M. Jahanshahi and A. Rahimpour, J. Membr. Sci., 2013, 435, 233–241 CrossRef CAS.
- D. Qin, Z. Liu, H. Bai and D. D. Sun, J. Mater. Chem. A, 2017, 5, 12183–12192 CAS.
- N. Ma, J. Wei, S. Qi, Y. Zhao, Y. Gao and C. Y. Tang, J. Membr. Sci., 2013, 441, 54–62 CrossRef CAS.
- Y. Q. Wang, R. W. Ou, Q. Q. Ge, H. T. Wang and T. W. Xu, Desalination, 2013, 330, 70–78 CrossRef CAS.
- J. W. Han, B. Kim, J. Li and M. Meyyappan, RSC Adv., 2013, 4, 549–553 RSC.
- Z. Yu, G. Zeng, Y. Pan, L. Lv, H. Min, L. Zhang and Y. He, RSC Adv., 2015, 5, 75998–76006 RSC.
- D. Emadzadeh, W. J. Lau, T. Matsuura, M. Rahbari-Sisakht and A. F. Ismail, Chem. Eng. J., 2014, 237, 70–80 CrossRef CAS.
- D. Emadzadeh, W. J. Lau and A. F. Ismail, Desalination, 2013, 330, 90–99 CrossRef CAS.
- D. L. Shaffer, J. R. Werber, H. Jaramillo, S. Lin and M. Elimelech, Desalination, 2015, 356, 271–284 CrossRef CAS.
- A. Achilli, T. Y. Cath, E. A. Marchand and A. E. Childress, Desalination, 2009, 239, 10–21 CrossRef CAS.
- E. S. Kim and B. L. Deng, J. Membr. Sci., 2011, 375, 46–54 CrossRef CAS.
- H. Y. Zhao, S. Qiu, L. G. Wu, L. Zhang, H. L. Chen and C. J. Gao, J. Membr. Sci., 2014, 450, 249–256 CrossRef CAS.
- W. C. L. Lay, Y. Liu and A. G. Fane, Water Res., 2010, 44, 21–40 CrossRef CAS PubMed.
- N. Ma, J. Wei, R. Liao and C. Y. Tang, J. Membr. Sci., 2012, 405–406, 149–157 CrossRef CAS.
- K. P. Lee, T. C. Arnot and D. Mattia, J. Membr. Sci., 2011, 370, 1–22 CrossRef CAS.
- Y. Zeng, L. Qiu, K. Wang, J. Yao, D. Li, G. P. Simon, R. Wang and H. Wang, RSC Adv., 2012, 3, 887–894 RSC.
- X. Li, K. Teng, J. Shi, W. Wang, Z. Xu, H. Deng, H. Lv and F. Li, J. Taiwan Inst. Chem. Eng., 2016, 60, 636–642 CrossRef CAS.
- M. Amini, A. Rahimpour and M. Jahanshahi, Desalin. Water Treat., 2016, 57, 14013–14023 CrossRef CAS.
- M. Yue, B. Zhou, K. Jiao, X. Qian, Z. Xu, K. Teng, L. Zhao, J. Wang and Y. Jiao, Appl. Surf. Sci., 2015, 327, 93–99 CrossRef CAS.
- T. Wu, B. Zhou, T. Zhu, J. Shi, Z. Xu, C. Hu and J. Wang, RSC Adv., 2015, 5, 7880–7889 RSC.
- K. Jiao, T. Zhu, X. Li, M. Shan, Z. Xu and Y. Jiao, J. Nanopart. Res., 2015, 17, 1–15 CrossRef CAS.
- X. Song, L. Wang, C. Y. Tang, Z. Wang and C. Gao, Desalination, 2015, 369, 1–9 CrossRef CAS.
- Y. Wang, R. Ou, Q. Ge, H. Wang and T. Xu, Desalination, 2013, 330, 70–78 CrossRef CAS.
- H. M. Hegab, A. ElMekawy, T. G. Barclay, A. Michelmore, L. Zou, C. P. Saint and M. Ginic-Markovic, ACS Appl. Mater. Interfaces, 2015, 7, 18004–18016 CAS.
- H. M. Hegab, A. ElMekawy, T. G. Barclay, A. Michelmore, L. Zou, C. P. Saint and M. Ginic-Markovic, Desalination, 2016, 385, 126–137 CrossRef CAS.
- M. J. Park, S. Phuntsho, T. He, G. M. Nisola, L. D. Tijing, X.-M. Li, G. Chen, W.-J. Chung and H. K. Shon, J. Membr. Sci., 2015, 493, 496–507 CrossRef CAS.
- L. Shen, S. Xiong and Y. Wang, Chem. Eng. Sci., 2016, 143, 194–205 CrossRef CAS.
- Y. Wang, R. Ou, H. Wang and T. Xu, J. Membr. Sci., 2015, 475, 281–289 CrossRef CAS.
- H. Salehi, M. Rastgar and A. Shakeri, Appl. Surf. Sci., 2017, 413, 99–108 CrossRef CAS.
- Z. Dabaghian and A. Rahimpour, Chem. Eng. Res. Des., 2015, 104, 647–657 CrossRef CAS.
- M. Ghanbari, D. Emadzadeh, W. J. Lau, S. O. Lai, T. Matsuura and A. F. Ismail, Desalination, 2015, 358, 33–41 CrossRef CAS.
- M. Ghanbari, D. Emadzadeh, W. J. Lau, H. Riazi, D. Almasi and A. F. Ismail, Desalination, 2016, 377, 152–162 CrossRef CAS.
- W. kuang, Z. Liu, H. Yu, G. Kang, X. Jie, Y. Jin and Y. Cao, J. Membr. Sci., 2016, 497, 485–493 CrossRef CAS.
- Q. Liu, J. Li, Z. Zhou, J. Xie and J. Y. Lee, Sci. Rep., 2016, 6, 19593 CrossRef PubMed.
- N.-N. Bui and J. R. McCutcheon, J. Membr. Sci., 2016, 518, 338–346 CrossRef CAS.
- Y. Huang, H. Jin, P. Yu and Y. Luo, Desalin. Water Treat., 2015, 57, 20177–20187 CrossRef.
- N. Niksefat, M. Jahanshahi and A. Rahimpour, Desalination, 2014, 343, 140–146 CrossRef CAS.
- M. Obaid, Z. K. Ghouri, O. A. Fadali, K. A. Khalil, A. A. Almajid and N. A. Barakat, ACS Appl. Mater. Interfaces, 2016, 8, 4561–4574 CAS.
- Z. Liu and Y. Hu, ACS Appl. Mater. Interfaces, 2016, 8, 21666–21673 CAS.
- E. Yang, K.-J. Chae, A. B. Alayande, K.-Y. Kim and I. S. Kim, J. Membr. Sci., 2016, 513, 217–225 CrossRef CAS.
- D. Emadzadeh, W. J. Lau, T. Matsuura, N. Hilal and A. F. Ismail, Desalination, 2014, 348, 82–88 CrossRef CAS.
- D. Emadzadeh, W. J. Lau, M. Rahbari-Sisakht, H. Ilbeygi, D. Rana, T. Matsuura and A. F. Ismail, Chem. Eng. J., 2015, 281, 243–251 CrossRef CAS.
- N. M. Mubarak, J. N. Sahu, E. C. Abdullah and N. S. Jayakumar, Sep. Purif. Rev., 2014, 43, 311–338 CrossRef CAS.
- P. S. Goh, B. C. Ng, W. J. Lau and A. F. Ismail, Sep. Purif. Rev., 2014, 44, 216–249 CrossRef.
- R. Das, M. E. Ali, S. B. A. Hamid, S. Ramakrishna and Z. Z. Chowdhury, Desalination, 2014, 336, 97–109 CrossRef CAS.
- Y. Wang, Z. Xu and L. Chen, Appl. Mech. Mater., 2010, 44–47, 2181–2185 CrossRef.
- Y. Wang, L. Chen and Z. Xu, Adv. Mater. Res., 2011, 150–151, 1106–1109 CAS.
- A. Kalra, S. Garde and G. Hummer, Proc. Natl. Acad. Sci. U. S. A., 2003, 100, 10175–10180 CrossRef CAS PubMed.
- Y. Chan and J. M. Hill, J. Membr. Sci., 2011, 372, 57–65 CrossRef CAS.
- X. F. Li, J. L. Yang, Y. H. Hu, J. J. Wang, Y. L. Li, M. Cai, R. Y. Li and X. L. Sun, J. Mater. Chem., 2012, 22, 18847–18853 RSC.
- H. J. Wang, G. P. Yin, Y. Y. Shao, Z. B. Wang and Y. Z. Gao, J. Power Sources, 2008, 176, 128–131 CrossRef.
- S. Kar, R. C. Bindal and P. K. Tewari, Nano Today, 2012, 7, 385–389 CrossRef CAS.
- H. J. Kim, Y. Baek, K. Choi, D. G. Kim, H. Kang, Y. S. Choi, J. Yoon and J. C. Lee, RSC Adv., 2014, 4, 32802–32810 RSC.
- Y. X. Jia, H. L. Li, M. Wang, L. Y. Wu and Y. D. Hu, Sep. Purif. Technol., 2010, 75, 55–60 CrossRef CAS.
- H. Q. Wu, B. B. Tang and P. Y. Wu, J. Membr. Sci., 2010, 362, 374–383 CrossRef CAS.
- H. A. Shawky, S. R. Chae, S. H. Lin and M. R. Wiesner, Desalination, 2011, 272, 46–50 CrossRef CAS.
- M. Endo, T. Hayashi, Y. A. Kim, M. Terrones and M. S. Dresselhaus, Philos. Trans. R. Soc., A, 2004, 362, 2223–2238 CrossRef CAS PubMed.
- H. Y. Ma, C. Burger, B. S. Hsiao and B. Chu, ACS Macro Lett., 2012, 1, 723–726 CrossRef CAS.
- J. H. Choi, J. Jegal and W. N. Kim, J. Membr. Sci., 2006, 284, 406–415 CrossRef CAS.
- L. Dumee, J. Lee, K. Sears, B. Tardy, M. Duke and S. Gray, J. Membr. Sci., 2013, 427, 422–430 CrossRef CAS.
- H. L. Li, Y. X. Jia and Y. D. Hu, Acta Phys.-Chim. Sin., 2012, 28, 573–577 CAS.
- Z. Zhao, K. Teng, N. Li, X. Li, Z. Xu, L. Chen, J. Niu, H. Fu, L. Zhao and Y. Liu, Compos. Struct., 2017, 159, 761–772 CrossRef.
- Y. Li and M. Kroger, Carbon, 2012, 50, 1793–1806 CrossRef CAS.
- A. Deneuve, K. Wang, I. Janowska, K. Chizari, D. Edouard, O. Ersen, M. J. Ledoux and C. Pham-Huu, Appl. Catal., A, 2011, 400, 230–237 CrossRef CAS.
- L. F. Dumee, K. Sears, J. Schutz, N. Finn, C. Huynh, S. Hawkins, M. Duke and S. Gray, J. Membr. Sci., 2010, 351, 36–43 CrossRef CAS.
- L. Dumee, K. Sears, J. Schutz, N. Finn, M. Duke and S. Gray, Desalin. Water Treat., 2010, 17, 72–79 CrossRef CAS.
- L. Dumee, V. Germain, K. Sears, J. Schutz, N. Finn, M. Duke, S. Cerneaux, D. Cornu and S. Gray, J. Membr. Sci., 2011, 376, 241–246 CrossRef CAS.
- L. F. Chen, H. Q. Xie, Y. Li and W. Yu, Mater. Lett., 2009, 63, 45–47 CrossRef CAS.
- A. Villa, M. Plebani, M. Schiavoni, C. Milone, E. Piperopoulos, S. Galvagno and L. Prati, Catal. Today, 2012, 186, 76–82 CrossRef CAS.
- K. Sears, L. Dumee, J. Schutz, M. She, C. Huynh, S. Hawkins, M. Duke and S. Gray, Materials, 2010, 3, 127–149 CrossRef CAS.
- R. L. D. Whitby, S. V. Mikhalovsky and V. M. Gun'ko, Carbon, 2010, 48, 145–152 CrossRef CAS.
- L. Dumée, J. Lee, K. Sears, B. Tardy, M. Duke and S. Gray, J. Membr. Sci., 2013, 427, 422–430 CrossRef.
- M. Hu and B. X. Mi, Environ. Sci. Technol., 2013, 47, 3715–3723 CrossRef CAS PubMed.
- Z. Xu, Y. Zhang, X. Qian, J. Shi, L. Chen, B. Li, J. Niu and L. Liu, Appl. Surf. Sci., 2014, 316, 308–314 CrossRef CAS.
- Y. Han, Z. Xu and C. Gao, Adv. Funct. Mater., 2013, 23, 3693–3700 CrossRef CAS.
- Y. Q. Sun, Q. O. Wu and G. Q. Shi, Energy Environ. Sci., 2011, 4, 1113–1132 CAS.
- Z. Xu, J. Zhang, M. Shan, Y. Li, B. Li, J. Niu, B. Zhou and X. Qian, J. Membr. Sci., 2014, 458, 1–13 CrossRef CAS.
- L. Chen, X. Li, L. Wang, W. Wang and Z. Xu, Polym. Compos., 2017, 38, 236–247 CrossRef.
- J. Lee, H. R. Chae, Y. J. Won, K. Lee, C. H. Lee, H. H. Lee, I. C. Kim and J. M. Lee, J. Membr. Sci., 2013, 448, 223–230 CrossRef CAS.
- B. X. Mi, Science, 2014, 343, 740–742 CrossRef CAS PubMed.
- F. Perreault, M. E. Tousley and M. Elimelech, Environ. Sci. Technol. Lett., 2014, 1, 71–76 CrossRef CAS.
- S. Zinadini, A. A. Zinatizadeh, M. Rahimi, V. Vatanpour and H. Zangeneh, J. Membr. Sci., 2014, 453, 292–301 CrossRef CAS.
- H. Y. Zhao, L. G. Wu, Z. J. Zhou, L. Zhang and H. L. Chen, Phys. Chem. Chem. Phys., 2013, 15, 9084–9092 RSC.
- Z. W. Xu, J. G. Zhang, M. J. Shan, Y. L. Li, B. D. Li, J. R. Niu, B. M. Zhou and X. M. Qian, J. Membr. Sci., 2014, 458, 1–13 CrossRef CAS.
- J. Q. Wang, P. Zhang, B. Liang, Y. X. Liu, T. Xu, L. F. Wang, B. Cao and K. Pan, ACS Appl. Mater. Interfaces, 2016, 8, 6211–6218 CAS.
- A. Akbari, P. Sheath, S. T. Martin, D. B. Shinde, M. Shaibani, P. C. Banerjee, R. Tkacz, D. Bhattacharyya and M. Majumder, Nat. Commun., 2016, 7, 12 Search PubMed.
- S. J. Gao, H. L. Qin, P. P. Liu and J. Jin, J. Mater. Chem. A, 2015, 3, 6649–6654 CAS.
- M. Li, J. Shi, C. Chen, N. Li, Z. Xu, J. Li, H. Lv, X. Qian and X. Jiao, J. Nanopart. Res., 2017, 19 Search PubMed.
- Y. Han, Y. Q. Jiang and C. Gao, ACS Appl. Mater. Interfaces, 2015, 7, 8147–8155 CAS.
- P. Z. Sun, Q. Chen, X. D. Li, H. Liu, K. L. Wang, M. L. Zhong, J. Q. Wei, D. H. Wu, R. Z. Ma, T. Sasaki and H. W. Zhu, NPG Asia Mater., 2015, 7, 8 Search PubMed.
- P. Sun, R. Ma, H. Deng, Z. Song, Z. Zhen, K. Wang, T. Sasaki, Z. Xu and H. Zhu, Chem. Sci., 2016, 7, 6988–6994 RSC.
- Y. J. Zhang, T. Mori, L. Niu and J. H. Ye, Energy Environ. Sci., 2011, 4, 4517–4521 CAS.
- Y. Hou, Z. H. Wen, S. M. Cui, X. R. Guo and J. H. Chen, Adv. Mater., 2013, 25, 6291–6297 CrossRef CAS PubMed.
- Y. Joo, Y. Jeon, S. U. Lee, J. H. Sim, J. Ryu, S. Lee, H. Lee and D. Sohn, J. Phys. Chem. C, 2012, 116, 18230–18235 CAS.
- Y. F. Chen, Y. T. Zhang, H. Q. Zhang, J. D. Liu and C. H. Song, Chem. Eng. J., 2013, 228, 12–20 CrossRef CAS.
- Y. S. Liu, X. Q. Jiang, B. J. Li, X. D. Zhang, T. Z. Liu, X. S. Yan, J. Ding, Q. Cai and J. M. Zhang, J. Mater. Chem. A, 2014, 2, 4264–4269 CAS.
- C. P. Li, J. Q. Wang, S. Q. Feng, Z. L. Yang and S. J. Ding, J. Mater. Chem. A, 2013, 1, 8045–8054 CAS.
- R. Wang, L. Shi, C. Y. Y. Tang, S. R. Chou, C. Qiu and A. G. Fane, J. Membr. Sci., 2010, 355, 158–167 CrossRef CAS.
- G. Hota, B. R. Kumar, W. J. Ng and S. Ramakrishna, J. Mater. Sci., 2007, 43, 212–217 CrossRef.
- L. Y. Yu, Z. L. Xu, H. M. Shen and H. Yang, J. Membr. Sci., 2009, 337, 257–265 CrossRef CAS.
- J. W. Cho and K. I. Sul, Polymer, 2001, 42, 727–736 CrossRef.
- T. Ogoshi and Y. Chujo, J. Polym. Sci., Part A: Polym. Chem., 2005, 43, 3543–3550 CrossRef CAS.
- M. Baghbanzadeh, A. Rashidi, D. Rashtchian, R. Lotfi and A. Amrollahi, Thermochim. Acta, 2012, 549, 87–94 CrossRef CAS.
- J. Vega-Baudrit, V. Navarro-Banon, P. Vazquez and J. M. Martin-Martinez, Int. J. Adhes. Adhes., 2006, 26, 378–387 CrossRef CAS.
- X. F. Yao, D. Zhou and H. Y. Yeh, Aerosp. Sci. Technol., 2008, 12, 223–230 CrossRef CAS.
- S. Sprenger, J. Appl. Polym. Sci., 2013, 130, 1421–1428 CrossRef CAS.
- X. Wang, L. Wang, Q. Su and J. P. Zheng, Compos. Sci. Technol., 2013, 89, 52–60 CrossRef CAS.
- O. Malay, O. Oguz, C. Kosak, E. Yilgor, I. Yilgor and Y. Z. Menceloglu, Polymer, 2013, 54, 5310–5320 CrossRef CAS.
- J. Yang and J. J. Zhao, Mater. Lett., 2014, 120, 36–38 CrossRef CAS.
- Y. L. Liu, C. Y. Hsu, W. L. Wei and R. J. Jeng, Polymer, 2003, 44, 5159–5167 CrossRef CAS.
- W. D. Liu, B. K. Zhu, J. Zhang and Y. Y. Xu, Polym. Adv. Technol., 2007, 18, 522–528 CrossRef CAS.
- H. Palza, R. Vergara and P. Zapata, Compos. Sci. Technol., 2011, 71, 535–540 CrossRef CAS.
- G. Bissadi and B. Kruczek, J. Therm. Anal. Calorim., 2014, 117, 73–83 CrossRef CAS.
- I. Ab Rahman and V. Padavettan, J. Nanomater., 2012, 132424 Search PubMed.
- X. X. Song, Z. Y. Liu and D. Sun, Adv. Mater., 2011, 23, 3256–3260 CrossRef CAS PubMed.
- F. Dorosti, M. R. Omidkhah, M. Z. Pedram and F. Moghadam, Chem. Eng. J., 2011, 171, 1469–1476 CrossRef CAS.
- A. J. J. Koekkoek, J. A. R. van Veen, P. B. Gerrtisen, P. Giltay, P. Magusin and E. J. M. Hensen, Microporous Mesoporous Mater., 2012, 151, 34–43 CrossRef CAS.
- S. L. Suib, Science, 2003, 302, 1335–1336 CrossRef CAS.
- S. H. Kim, S. Y. Kwak, B. H. Sohn and T. H. Park, J. Membr. Sci., 2003, 211, 157–165 CrossRef CAS.
- B. H. Jeong, E. M. V. Hoek, Y. S. Yan, A. Subramani, X. F. Huang, G. Hurwitz, A. K. Ghosh and A. Jawor, J. Membr. Sci., 2007, 294, 1–7 CrossRef CAS.
- M. L. Lind, A. K. Ghosh, A. Jawor, X. F. Huang, W. Hou, Y. Yang and E. M. V. Hoek, Langmuir, 2009, 25, 10139–10145 CrossRef CAS PubMed.
- M. L. Lind, D. E. Suk, T. V. Nguyen and E. M. V. Hoek, Environ. Sci. Technol., 2010, 44, 8230–8235 CrossRef CAS PubMed.
- H. Y. Liu, L. L. Liu, C. L. Yang, Z. H. Li, Q. Z. Xiao, G. T. Lei and Y. H. Ding, Electrochim. Acta, 2014, 121, 328–336 CrossRef CAS.
- Y. Q. Zhang, X. Bin Yang, Z. X. Wang, J. Long and L. Shao, J. Mater. Chem. A, 2017, 5, 7316–7325 CAS.
- X. B. Yang, X. Jiang, Y. D. Huang, Z. H. Guo and L. Shao, ACS Appl. Mater. Interfaces, 2017, 9, 5590–5599 CAS.
- X. Q. Cheng, K. Konstas, C. M. Doherty, C. D. Wood, X. Mulet, Z. L. Xie, D. Ng, M. R. Hill, L. Shao and C. H. Lau, ACS Appl. Mater. Interfaces, 2017, 9, 14401–14408 CAS.
- J. Y. Bottero, M. Auffan, J. Rose, C. Mouneyrac, C. Botta, J. Labille, A. Masion, A. Thill and C. Chaneac, C. R. Geosci., 2011, 343, 168–176 CrossRef CAS.
- X. M. Wang, X. Y. Li and K. M. Shih, J. Membr. Sci., 2011, 368, 134–143 CrossRef CAS.
- H. Wu, J. Mansouri and V. Chen, J. Membr. Sci., 2013, 433, 135–151 CrossRef CAS.
- Q. L. Li, S. Mahendra, D. Y. Lyon, L. Brunet, M. V. Liga, D. Li and P. J. J. Alvarez, Water Res., 2008, 42, 4591–4602 CrossRef CAS PubMed.
- S. J. Klaine, P. J. J. Alvarez, G. E. Batley, T. F. Fernandes, R. D. Handy, D. Y. Lyon, S. Mahendra, M. J. McLaughlin and J. R. Lead, Environ. Toxicol. Chem., 2008, 27, 1825–1851 CrossRef CAS PubMed.
- A. Mollahosseini, A. Rahimpour, M. Jahamshahi, M. Peyravi and M. Khavarpour, Desalination, 2012, 306, 41–50 CrossRef CAS.
- K. Zodrow, L. Brunet, S. Mahendra, D. Li, A. Zhang, Q. L. Li and P. J. J. Alvarez, Water Res., 2009, 43, 715–723 CrossRef CAS PubMed.
- M. Herzberg and M. Elimelech, J. Membr. Sci., 2007, 295, 11–20 CrossRef CAS.
- Y. Li, J. H. Ho and C. P. Ooi, Mater. Sci. Eng., C, 2010, 30, 1137–1144 CrossRef CAS.
- F. Diagne, R. Malaisamy, V. Boddie, R. D. Holbrook, B. Eribo and K. L. Jones, Environ. Sci. Technol., 2012, 46, 4025–4033 CrossRef CAS PubMed.
- J. S. Taurozzi, H. Arul, V. Z. Bosak, A. F. Burban, T. C. Voice, M. L. Bruening and V. V. Tarabara, J. Membr. Sci., 2008, 325, 58–68 CrossRef CAS.
- J. Huang, G. Arthanareeswaran and K. S. Zhang, Desalination, 2012, 285, 100–107 CrossRef CAS.
- S. Y. Lee, H. J. Kim, R. Patel, S. J. Im, J. H. Kim and B. R. Min, Polym. Adv. Technol., 2007, 18, 562–568 CrossRef CAS.
- H. L. Yang, J. C. T. Lin and C. Huang, Water Res., 2009, 43, 3777–3786 CrossRef CAS PubMed.
- X. Liu, S. Qi, Y. Li, L. Yang, B. Cao and C. Y. Tang, Water Res., 2013, 47, 3081–3092 CrossRef CAS PubMed.
- L. Djafer, A. Ayral and A. Ouagued, Sep. Purif. Technol., 2010, 75, 198–203 CrossRef CAS.
- A. Rahimpour, M. Jahanshahi, A. Mollahosseini and B. Rajaeian, Desalination, 2012, 285, 31–38 CrossRef CAS.
- Z. Xu, T. Wu, J. Shi, K. Teng, W. Wang, M. Ma, J. Li, X. Qian, C. Li and J. Fan, J. Membr. Sci., 2016, 520, 281–293 CrossRef CAS.
- Q. Q. Wang, X. T. Wang, Z. H. Wang, J. Huang and Y. Wang, J. Membr. Sci., 2013, 442, 57–64 CrossRef CAS.
- Y. H. Teow, A. L. Ahmad, J. K. Lim and B. S. Ooi, J. Appl. Polym. Sci., 2013, 128, 3184–3192 CrossRef CAS.
- G. Ghasemzadeh, M. Momenpour, F. Omidi, M. R. Hosseini, M. Ahani and A. Barzegari, Front. Environ. Sci. Eng., 2014, 8, 471–482 CrossRef CAS.
- Z. Xu, X. Li, W. Wang, J. Shi, K. Teng, X. Qian, M. Shan, C. Li, C. Yang and L. Liu, Ceram. Int., 2016, 42, 15012–15022 CrossRef CAS.
- X. Cheng, S. Ding, J. Guo, C. Zhang, Z. Guo and L. Shao, J. Membr. Sci., 2017, 536, 19–27 CrossRef CAS.
- N. A. A. Hamid, A. F. Ismail, T. Matsuura, A. W. Zularisam, W. J. Lau, E. Yuliwati and M. S. Abdullah, Desalination, 2011, 273, 85–92 CrossRef CAS.
- A. W. Zularisam, A. F. Ismail, M. R. Salim, M. Sakinah and H. Ozaki, Desalination, 2007, 212, 191–208 CrossRef CAS.
- A. Nguyen, L. D. Zou and C. Priest, J. Membr. Sci., 2014, 454, 264–271 CrossRef CAS.
- M. Amini, A. Rahimpour and M. Jahanshahi, Desalin. Water Treat., 2016, 57, 14013–14023 CrossRef CAS.
- J. Kim and B. Van der Bruggen, Environ. Pollut., 2010, 158, 2335–2349 CrossRef CAS PubMed.
- P. S. Tin, T. S. Chung, L. Y. Jiang and S. Kulprathipanja, Carbon, 2005, 43, 2025–2027 CrossRef CAS.
- J. N. Shen, H. M. Ruan, L. G. Wu and C. J. Gao, Chem. Eng. J., 2011, 168, 1272–1278 CrossRef CAS.
- J. n. Shen, C. c. Yu, H. m. Ruan, C. j. Gao and B. Van der Bruggen, J. Membr. Sci., 2013, 442, 18–26 CrossRef CAS.
- M. Ghanbari, D. Emadzadeh, W. J. Lau, T. Matsuura, M. Davoody and A. F. Ismail, Desalination, 2015, 371, 104–114 CrossRef CAS.
- R. Zhang, Y. Su, X. Zhao, Y. Li, J. Zhao and Z. Jiang, J. Membr. Sci., 2014, 470, 9–17 CrossRef CAS.
- P. S. Zhong, N. Widjojo, T. S. Chung, M. Weber and C. Maletzko, J. Membr. Sci., 2012, 417, 52–60 CrossRef.
- P. T. Hammond, Curr. Opin. Colloid Interface Sci., 1999, 4, 430–442 CrossRef CAS.
- R. Malaisamy and M. L. Bruening, Langmuir, 2005, 21, 10587–10592 CrossRef CAS PubMed.
- O. Y. Lu, R. Malaisamy and M. L. Bruening, J. Membr. Sci., 2008, 310, 76–84 CrossRef.
- Q. Saren, C. Q. Qiu and C. Y. Y. Tang, Environ. Sci. Technol., 2011, 45, 5201–5208 CrossRef CAS PubMed.
- S. Qi, C. Q. Qiu, Y. Zhao and C. Y. Tang, J. Membr. Sci., 2012, 405–406, 20–29 CrossRef CAS.
- C. Qiu, S. Qi and C. Y. Tang, J. Membr. Sci., 2011, 381, 74–80 CrossRef CAS.
- M. Herzberg, S. Kang and M. Elimelech, Environ. Sci. Technol., 2009, 43, 4393–4398 CrossRef CAS PubMed.
- P. Bertrand, A. Jonas, A. Laschewsky and R. Legras, Macromol. Rapid Commun., 2000, 21, 319–348 CrossRef CAS.
- S. Zhao, L. Zou, C. Y. Tang and D. Mulcahy, J. Membr. Sci., 2012, 396, 1–21 CrossRef CAS.
- X. Qu, P. J. Alvarez and Q. Li, Water Res., 2013, 47, 3931–3946 CrossRef CAS PubMed.
- M. M. Ling and T. S. Chung, Desalination, 2011, 278, 194–202 CrossRef CAS.
- L. Chekli, S. Phuntsho, H. K. Shon, S. Vigneswaran, J. Kandasamy and A. Chanan, Desalin. Water Treat., 2012, 43, 167–184 CrossRef CAS.
- T. S. Chung, S. Zhang, K. Y. Wang, J. Su and M. M. Ling, Desalination, 2012, 287, 78–81 CrossRef CAS.
- A. Soroush, W. Ma, Y. Silvino and M. S. Rahaman, Environ. Sci.: Nano, 2015, 2, 395–405 RSC.
- D. N. Wang, X. F. Li, J. J. Wang, J. L. Yang, D. S. Geng, R. Y. Li, M. Cai, T. K. Sham and X. L. Sun, J. Phys. Chem. C, 2012, 116, 22149–22156 CAS.
- C. Matranga, B. Bockrath, N. Chopra, B. J. Hinds and R. Andrews, Langmuir, 2006, 22, 1235–1240 CrossRef CAS PubMed.
- J. K. Holt, H. G. Park, Y. M. Wang, M. Stadermann, A. B. Artyukhin, C. P. Grigoropoulos, A. Noy and O. Bakajin, Science, 2006, 312, 1034–1037 CrossRef CAS PubMed.
- B. J. Hinds, N. Chopra, T. Rantell, R. Andrews, V. Gavalas and L. G. Bachas, Science, 2004, 303, 62–65 CrossRef CAS PubMed.
- J. J. Wang, G. P. Yin, Y. G. Chen, R. Y. Li and X. L. Sun, Int. J. Hydrogen Energy, 2009, 34, 8270–8275 CrossRef CAS.
- K. Dasgupta, S. Kar, R. Venugopalan, R. C. Bindal, S. Prabhakar, P. K. Tewari, S. Bhattacharya, S. K. Gupta and D. Sathiyamoorthy, Mater. Lett., 2008, 62, 1989–1992 CrossRef CAS.
- S. Kar, R. C. Bindal, S. Prabhakar, P. K. Tewari, K. Dasgupta and D. Sathiyamoorthy, Int. J. Nucl. Desalin., 2008, 3, 143–150 CrossRef CAS.
- P. Sabbatini, F. Yrazu, F. Rossi, G. Thern, A. Marajofsky and M. M. F. de Cortalezzi, Water Res., 2010, 44, 5702–5712 CrossRef CAS PubMed.
- V. Vatanpour, S. S. Madaeni, R. Moradian, S. Zinadini and B. Astinchap, J. Membr. Sci., 2011, 375, 284–294 CrossRef CAS.
- Z. Xu, T. Wu, J. Shi, W. Wang, K. Teng, X. Qian, M. Shan, H. Deng, X. Tian, C. Li and F. Li, ACS Appl. Mater. Interfaces, 2016, 8, 18418–18429 CAS.
Footnote |
† These authors contributed equally to this work. |
|
This journal is © The Royal Society of Chemistry 2018 |
Click here to see how this site uses Cookies. View our privacy policy here.