DOI:
10.1039/C8NH00446C
(Communication)
Nanoscale Horiz., 2019,
4, 1077-1091
“Ion sliding” on graphene: a novel concept to boost supercapacitor performance†
Received
28th November 2018
, Accepted 8th April 2019
First published on 9th April 2019
Abstract
Efficient ionic transport in nanoporous carbon electrodes is pivotal for the development of high-rate electrochemical capacitive energy storage in supercapacitors (SCs). Over the past decade, the understanding of the charging/discharging mechanisms in nanostructured carbon electrodes and the elucidation of confinement and desolvation of ions in electrically charged carbon nanopores have spurred the development of advanced SCs holding ever-increasing energy density. Crucially, these advancements have to be accomplished without sacrificing the extraordinary power handling and cycling lifetime of the SC. In this work, we investigated the interaction between single-/few-layer graphene (SLG/FLG) flakes or activated carbon (AC) films and 1 M tetraethylammonium tetrafluoroborate (TEABF4) in propylene carbonate (PC) by lateral force microscopy (LFM) measurements. We unravel that the electrolyte nanotribology on SLG/FLG flakes incorporated into AC-based electrodes is effective at boosting the power performance of commercial-like SCs (active material mass loading ∼10 mg cm−2), thus maximizing the advantage of using nanoporous nanocarbon electrodes with high energy density. At a charge/discharge (CD) current density of 0.1 A g−1, our hybrid AC:SLG/FLG-based SC shows a 30% increase of specific capacitance (Cg) compared to the reference device, i.e., the AC-based one (Cg from 76.8 F g−1 to 98.2 F g−1). At higher CD current densities (>1 A g−1), the AC-based device displays a resistive behaviour, while the AC:SLG/FLG-based SCs still exhibit a Cg of 23.9 and 5.2 F g−1 at CD current densities as high as 2.5 and 5 A g−1, respectively. Beyond the control of the nanoporosity of carbon materials and the inter-ionic interaction of the electrolytes, the rationalization of the relationship between the nanotribology of nanocarbons and the performance of the corresponding SCs offers new opportunities to optimize the SC design compatibly with established high-throughput industrial manufacturing.
New concepts
The understanding of the charging/discharging mechanisms in nanostructured carbon electrodes and the elucidation of confinement and de-solvation of ions in electrically charged carbon nanopores have recently spurred the development of advanced supercapacitor (SCs) holding ever-increasing energy density. Crucially, these advancements have to be accomplished without sacrificing the extraordinary power handling of the SC. Here, we show that the management of the nanotribological properties of both active materials and electrolytes can be a new paradigm to overcome the classic dichotomy of energy density and power density in SCs. In fact, the advantage of conceiving an efficient ion transport within high-surface area electrodes allows for ideal access of ions into both meso- and micro-pores, which is mandatory for ideal rate-independent high energy densities. In particular, we unravel that the single-/few-layer graphene (SLG/FLG) flakes act as friction-free “ion slides” for supercapacitor electrolytes. Such an intriguing feature allows us to boost the electrochemical performance of commercial-like SCs by incorporating SLG/FLG flake activated carbon films with high mass loading.
|
Introduction
Supercapacitors (SCs), also known as electrical double-layer capacitors, are electrochemical energy storage systems, which rely on electric double-layer formation (i.e., ion adsorption) at electrode/electrolyte interfaces.1–5 Supercapacitors have a higher energy storage capacity compared to capacitors thanks to the high-surface area of their electrodes,6,7 which are based on commercially available nanoporous carbon-structures8,9 (up to pore size smaller than 1 nm).2,10,11 Due to the intrinsic reversibility of ion adsorption processes, SCs store and release energy in second/sub-second timescales,12 which means they can complement or even replace batteries (typically operating over minute/hour timescales)12 for high-power (>10
000 W kg−1) applications13,14 (including regenerative breaking in electric and hybrid electric vehicles,15,16 short-term energy storage17 in consumer electronics18 and communication systems,19 or burst-mode power delivery20–22). Simultaneously, SCs provide superior lifetime (∼millions of cycles)23,24 compared to batteries (several hundred cycles).25–27 The latter suffer intercalation-induced stresses that can cause material swelling28,29 and subsequent electrode failure.30 In order to extend the application field of SCs, recent research aimed to increase the energy density of SCs (<10 W h kg−1 for commercial SCs13), since the latter is still significantly inferior to that of batteries (30–70 W h kg−1 for Ni–Cd,31 50–120 W h kg−1 for Ni–MH batteries,32,33 150–270 W h kg−1 for Li-ion batteries34).35,36 To increase the energy density, major strategies handled with tailoring the nanoporous structures of the carbon electrodes,6,37–39 controlling the interaction between carbon, solvent molecules and ions,3,40 and enlarging the operating voltage window of the electrolytes.41,42 To speed-up the development of new materials and architectures, recent studies, including in situ electrochemical quartz crystal microbalance,43,44 spectroscopy,45–47 diffraction48–50 and atomistic simulation of electrosorbed ions in nanoconfined environments,51,52 have been directed at the understanding of the physical mechanism underlying the charge storage in SCs. In particular, the finding of charge storage in pores smaller than the size of solvated electrolyte ions2 has paved the way towards the design of nanoporous carbon electrodes with an extraordinary energy density (e.g., >20 W h kg−1 for a “full” device, including active material, current collectors, electrolyte, separator, binder and packaging).39,53 Yet, no studies have dealt with the tribological effects between active materials and electrolytes used for SCs. Herein, we rationalize the exploitation of the tribological properties of single/few-layer graphene (SLG/FLG) flakes, showing that they act as “ion-slides” to enhance the operating power of conventional activated carbon (AC)-based SCs.54 Graphene and its derivatives have been previously exploited as SC materials,55–58 since theoretical specific surface area (SSA) (∼2630 m2 g−1) of graphene should provide a theoretical specific capacitance of ∼550 F g−1.59 Moreover, the extraordinary electrical conductivity of graphene (charge carrier mobility of ∼105 cm2 V−1 s−1)60–62 should facilitate the electron transport in mesoporous films, charging the electrode surface to be active for an ion electrosorbing process.55–57 However, graphene flakes tend to restack during their film deposition due to van der Waals forces63–65 and horizontally orient with respect to their current collectors.66,67 This limits the surface area accessible to the electrolyte, especially in SCs with high active material mass loading (∼10 mg cm−2) to guarantee high energy/power density in commercial energy storage units,68–70 in which the weight of the active material has to account for more than 30% of the total mass of the packaged device.69 This drawback has been mitigated by engineering graphene-based structures with different topological complexities: from zero-dimensional (0D) graphene quantum dots,71,72 to three-dimensional (3D) graphene foams73,74 and graphene-based hydrogels.75,76 However, the fabrication of such structures usually involves chemical functionalization77,78 or template-assisted growth,79,80 which poses severe limitations for the industrial manufacturing of SCs.81 It is not the case of SCs based on AC, which can also hold SSA exceeding 3000 m2
g−1,80,82i.e., superior to the theoretical value of graphene, covering almost the entire current SC market.81,83 Currently, the major drawback of AC relies on the fact that only ∼1/3 of its SSA is effectively accessible to the solvated ions in the electrolyte84–86 due to the lack of efficient ion transport in “closed micropores”,87–90i.e., inaccessible micropores that have no connection with the porous surroundings.
With the scope to fully exploit the SSA of AC, here we show that the tribological properties of the SLG/FLG flakes in the electrolyte/solvent system facilitate the access of ions into nanoporous AC, which allows both energy and power density of commercial SCs to be enhanced. We reveal that a friction force (FF) between ions and active materials is displayed by AC, while SLG/FLG flakes effectively act as friction-free “ion slides”. This result opens new pathways for frictional property management in designing nanoporous electrodes for SCs, as well as novel power-generation devices.
Results and discussion
Graphene flake production by wet-jet milling
With the aim of targeting commercial applications, we produced graphene flakes by wet-jet milling (WJM)-assisted exfoliation91,92 of graphite in N-methyl-2-pyrrolidone (NMP). As demonstrated in our previous works,91 WJM-assisted exfoliation of graphite is a technique which allows production of high-quality SLG/FLG dispersions in large volumes (litre-scale) with a high concentration (gram per litre-scale) in short times (second/minute-scale).91,93 The details of the WJM process are reported in the Experimental section, as well as in the ESI† (see Fig. S1). Briefly, the time required to produce 1 g of SLG/FLG (t1
gram) is 2.55 min, the volume of solvent required to produce 1 g of SLG/FLG (V1
gram) is 0.1 L and the exfoliation yield (Y), defined as the ratio between the weight of the final graphitic flakes and the weight of the starting graphite material, is ∼100%.91 We previously demonstrated,91 that these metric values overcome those of the most common exfoliation techniques, often claiming high-scalability,94,95 reported to date.96–102 The morphology of representative WJM-produced graphene flakes is shown in Fig. 1a and b where atomic force microscopy (AFM) and transmission electron microscopy (TEM) images evidence irregular shaped nm-thick flakes. The electron diffraction pattern corresponding to the TEM image (inset to Fig. 1b) indicates the crystalline nature of the flakes. Morphological statistical analysis (Fig. 1c and d) shows that the thickness and the lateral size of the exfoliated flakes follow a lognormal distribution, as displayed by fragmented systems,103 peaked at ∼1.5 nm and ∼480 nm, respectively. These data indicate that the exfoliated flakes are SLG/FLG. Raman spectroscopy measurements were performed to confirm the structural quality of the exfoliated flakes,104–109 as well as their single-/few-layer-enriched composition.110 The typical Raman spectrum of exfoliated graphene flakes shows, as fingerprints, the G (E2g phonon at the Brillouin zone centre, ∼1585 cm−1),104,105,111 D (breathing modes of sp2 rings requiring a defect for its activation by double resonance, ∼1380 cm−1),105,111–113 D′ (∼1620 cm−1)114 and 2D (∼2700 cm−1)105 peaks (see ESI† for detailed discussion of the origin of the Raman modes).104–106,115Fig. 1e shows the Raman spectra of the starting graphite and the WJM-produced flake sample, normalized to the G peak. The Raman spectrum of the WJM-produced sample exhibited an increase of the D peak compared to those of native graphite. In particular, Raman statistical analysis (see ESI,† Fig. S2) shows that the ratio between the intensities of the D and G peaks (I(D)/I(G)) ranges between 0.1 and 1.2 for the WJM-processed sample, whereas I(G) > I(D) for graphite, in agreement with previous studies on both graphene flakes and graphite.116–120 These studies have shown that intrinsic defects are located at the edges of the graphene flakes and, in the absence of a defective basal plane, I(D)/I(G) varies inversely with the crystal size.116–120
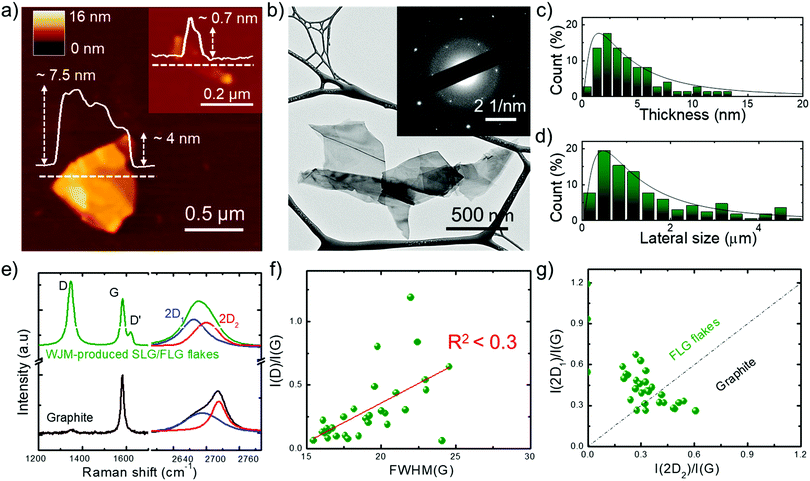 |
| Fig. 1 Morphological and structural characterization of the WJM-produced SLG/FLG flakes. (a) Representative AFM and (b) TEM images of WJM-produced SLG/FLG flakes. The inset panel in (a) shows an AFM image of an isolated SLG flake. The inset panel in (b) shows the electron diffraction pattern of the TEM image, revealing the crystalline nature of the flakes. (c) AFM statistical analysis of the thickness and (d) TEM statistical analysis of the lateral dimension of the SLG/FLG flakes. (e) Comparison between the Raman spectra of the graphite (black) and WJM-produced SLG/FLG flakes (green). Their multi-peak Lorentzian fitting shows the contribution of the different 2D modes (blue line: 2D1; red line: 2D2). (f) Plot of I(D)/I(G) vs. FWHM(G) where R2 < 0.3 indicates no correlation between these parameters. (g) Plot of I(2D1)/I(G) vs. I(2D2)/I(G). The dashed line I(2D1)/I(G) = I(2D2)/I(G) represents the multilayer condition (∼5 layers).104,105,110 | |
However, defects can also occur on the basal planes of the flakes (i.e., in the sp2 carbon lattices). For such flakes, I(D)/I(G) positively correlates with the amount of disorder.116–120 In order to assess the crystal quality of the exfoliated SLG/FLG flakes, the plot of I(D)/I(G) vs. FWHM(G) can be used to identify the nature of the defects.121,122 The plot of I(D)/I(G) vs. FWHM(G) (Fig. 1f) does not show a linear correlation (R2 < 0.3), which means that the WJM process did not induce in-plane defects into the graphene flakes.121,122 The analysis of the 2D peak allows the estimation of the flake thickness. In fact, graphite exhibits a 2D peak that results from two contributions, named 2D1 and 2D2. The intensity of 2D2 is around twice that of 2D1.105,123 Multi-layer graphene (>5 layers) exhibits a 2D peak, which is almost identical, in terms of intensity and lineshape, to the one of graphite.116,124 Few-layer graphene, instead, has a 2D1 peak more intense than the 2D2.105,123 Lastly, SLG exhibits a 2D peak given by a single sharp contribution, which corresponds to 2D1.104 The analysis of the I(2D1)/I(G) vs. I(2D2)/I(G) plot (Fig. 1g) allows carrying out an estimation of the thickness of the exfoliated flakes. In fact, data that fall above that line (i.e., I(2D1) > I(2D2)) correspond to flakes having less than 5 layers, while those below (i.e., I(2D1) < I(2D2)) refer to flakes with more than 5 layers (electronically indistinguishable from graphite104,105). Consequently, data in Fig. 1g confirm that the WJM-produced flakes are SLG and FLG91,110 in agreement with the AFM analysis (Fig. 1a and c). X-ray photoelectron spectroscopy (XPS) measurements (see details in the ESI,† Fig. S3) proved that the WJM process effectively produced high-quality SLG/FLG flakes since the spectra showed that the C 1s spectrum is dominated by a component peaking at 284.4 eV attributed to sp2 structures. These results exclude the formation of graphene oxide during the WJM process, whose functional groups can alter the chemical interaction of ions with pristine graphene.125–127
Solvent and ion nanotribology on nanocarbons
Mechanical friction of graphene-based materials has been intensively studied128 under vacuum,129 dry gases,130,131 or ambient conditions,127,132,133 for their application as solid lubricant materials132,134 and potential wear resistance coatings in mechanical/electrochemical micro/nanosystems.127,129,135 However, only a few studies investigated the nanoscale interaction of graphene (as well as of other nanocarbons) with liquids, including both polar (e.g., water)136,137 and nonpolar (e.g., dodecane)136,137 solvents, for electrochemical applications. Moreover, to our knowledge, the dependence of the FF of graphene-based materials on the presence of electrolytes (for example those used for SCs) in a solvent is uncharted.
To fill this shortfall, and to apply the outcomes into SC technology, we investigated the interaction between the SLG/FLG flake film (obtained by doctor blade deposition of concentrated WJM-produced SLG/FLG dispersion) and 1 M tetraethylammonium tetrafluoroborate (TEABF4) in propylene carbonate (PC), a conventional organic electrolyte used in SCs,41,138 by lateral force microscopy (LFM) measurements, as sketched in Fig. 2a. The analysis has also been performed on commercial AC (AB-520, MTI Corp.),139 which was used as a benchmark SC material. Lateral force microscopy measurements can be performed with an AFM-setup by detecting the cantilever torsional deflection, while scanning across the sample surface in contact mode.140,141 The FF positively correlates with the output voltage signal resulting from the measurements of the lateral deflection of the cantilever (see Experimental section for further details).135 The difference between forward and reverse traces of torsion of the tip (“friction force loop”) provides insight into the frictional and adhesion properties of the sample,142–146 as well as the dynamics of the electrolyte at the interface with solids in solutions.136,137,147 The FF between the LFM cantilever tip and the sample surface depends on the properties of the tip, the film and the liquid environment.136,137 The capillary forces, which significantly contribute in an ambient atmosphere due to the formation of a water meniscus between the cantilever tip and the film,148 can be effectively eliminated when the film is immersed in liquid environments.136,137 The same tip was then used during LFM measurements to exclude its contribution in the comparative force analysis of the results obtained for different films.149 The same analysis has also been performed on commercial AC (AB-520, MTI Corp.).139 The active material films were deposited onto Al foil (current collector) with a mass loading of ∼10 mg cm−2, compatible with the requirements of industrial SC manufacturing (mass loading at least of 5 mg cm−2, corresponding to an electrode thickness between 50–200 μm).68,69 Such mass loading allows our results to be directly applied in practical SCs, without overestimating the experimental performance of the active materials,68,69,150 as often reported by adopting μg cm−2-scale mass loading.68,69,150Fig. 2b and c report top-view scanning electron microscopy (SEM) images of the AC and SLG/FLG flake films, respectively, evidencing the differences between the corresponding morphologies. The SLG/FLG flake film is composed of stacked graphene flakes adopting a preferential in-plane disposition, while the AC film presents a mesoporous structure given by nanoparticles with a variable dimension, ranging from 0.1 μm to 10 μm. Nanoparticles with sub-μm dimensions are also present, sometimes in aggregate form, filling the space between the largest AC particles. Carbon black is considered the main source of these nanoparticles.83 The root mean square roughness (Rrms) calculated by the AFM scan is 104.7 nm and 873.4 nm for SLG/FLG flake and AC films, respectively. Fig. 2d and e show the LFM responses to the lateral deflection of the cantilever tip as a function of normal load (L) (ranging from 0 to 18 nN) at a scan rate of 25 μm s−1 over SLG/FLG flake and AC films, respectively, in PC with and without the electrolyte (TEABF4, 1 M). Noteworthily, FF (and therefore the lateral deflection) is proportional to L, in agreement with Amontons’ law:151,152FF = SCA + μL, in which SC is the critical shear stress, A is the contact area and μ is the friction coefficient between the AFM tip and the sample surface (considering the presence of both solvent and electrolyte). The term SCA represents the adhesion force at L = 0. Although μ is typically considered a material constant, experiments evidenced variation of μ with L and contact time,153,154 providing phenomenological corrections.155–157 This variation can cause deviations from the linear regression expressed by Amontons’ law.153,154 Taking into account such considerations, the results clearly show that lateral deflection (i.e., the FF) in PC is significantly higher on the AC film compared to the SLG/FLG-based one. This effect arises from the small nanoscale roughness of the SLG/FLG flake film compared to the AC film. In fact, as indicated before, AFM analysis (inset to Fig. 2d and e) shows a root mean square roughness (Rrms) of 873.5 nm and 104.7 nm for AC and SLG/FLG flake films, respectively. Interestingly, the presence of TEABF4 significantly increases the FF of the AC film, while no changes of FF are observed for the SLG/FLG flake film. We interpreted the increase of FF in AC as arising from the accumulation of electrolyte in the proximity of the AFM tip that promotes the formation of a solid-like interlocking layer, which increases FF.136,158,159 Notably, it has been reported that organic liquids are solid-like or have diverging viscosities when they are confined to films less than 5–8 molecular layer thick.160–165 Theoretical models support our interpretation. In fact, as the confinement increases, the translational entropy available to the organic molecules decreases until it is thermodynamically favourable for them to condense to an ordered phase, displaying a solid-like behaviour even at a temperature at which the bulk is a fluid.165–167 Therefore, the fluidity of the electrolyte in AC is supposed to be limited by the nanoconfinement effects provided by the film roughness, while the flat surface of SLG/FLG flakes can effectively squeeze out the interfacial region providing fluid-like conditions similar to the solely solvent.136 In addition, the long range two-dimensional (2D)-order of the sp2 lattice of SLG/FLG flakes, as shown by Raman and XPS analysis (Fig. 1e, f and Fig. S3, ESI,† respectively), intrinsically acts as a “slide” for ions, fastening the electrolyte transport compared to the AC films. The “slide-like behaviour” of the SLG/FLG flakes agrees with the ultra-low nanoscale frictional properties previously reported for few-layer graphene films,125,141,168 which behave similarly to super-lubricating highly oriented pyrolytic graphite (HOPG) films (μ < 0.01).169–171 Noteworthily, previous theoretical172 and experimental125,173 studies demonstrated that super-lubricating properties of graphene-based materials are exhibited only in high-purity graphene, discarding similar behaviour for defective graphene including sp3 domains,125,127,174 as well as for graphene oxide films.125–127 In particular for graphene oxide, its surface enriched with oxygen functionalities forms hydrogen bonds enhancing the friction in the presence of polar and/or charged moieties.125,126,174,175 These observations also justify the choice of the WJM production method for the graphene flakes, which avoids the formation of oxide and defects in contrast to what happens with other production/processing methods,91 such as the reduction of graphene oxide.95,176,177
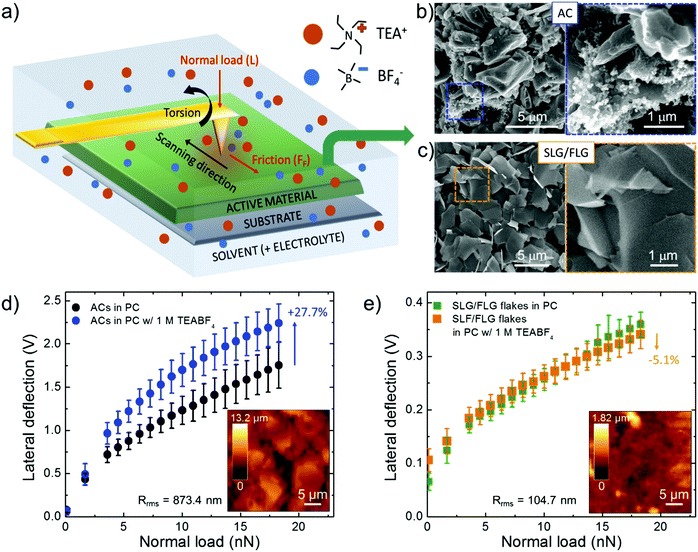 |
| Fig. 2 Solvent and ion nanotribology on AC and SLG/FLG flakes. (a) Sketch of the LFM measurement setup. (b and c) Top-view SEM images of AC and SLG/FLG flake films deposited onto Al foil. The corresponding areas delimited by dashed squares are magnified in the right panels. (d and e) Lateral force microscopy measurements of AC and SLG/FLG flake films in PC with and without 1 M TEABF4. The inset panels in (d and e) show the AFM topography of the films. The Rrms values corresponding to the AFM images are also reported. | |
Fabrication and characterization of supercapacitors
The elucidation of the PC and TEABF4 nanotribology on SLG/FLG flakes and AC films served to formulate hybrid AC:SLG/FLG electrode materials enhancing the electrochemical performance of AC-based SCs, which represent the benchmark technology adopted at a massive industrial level.81,83 Experimentally, the as-produced SLG/FLG flakes were mixed with commercial AB-520 AC at various AC:SLG/FLG weight ratios (90
:
10, 80
:
20, 50
:
50 w/w) to obtain SC active materials (herein named AC:SLG/FLG (90
:
10), AC:SLG/FLG (80
:
20), and AC:SLG/FLG (50
:
50)). The SC electrodes were fabricated by mixing the as-produced active materials with carbon black (conductive agent) and polyvinylidene fluoride (PVDF) (binder) with an 85
:
10
:
5 weight ratio in NMP (1
:
3 solid/liquid weight content ratio), until homogenized paste-like consistencies (slurry) were obtained. The as-produced pastes were subsequently deposited onto Al foil by the doctor blade technique, and dried at 60 °C, obtaining the SC electrodes. Electrodes based solely on SLG/FLG flakes or AC as active materials were also produced as references. The mass loading of the electrodes was ∼10 mg cm−2, in agreement with requirements of commercially available SCs.68,69 As discussed in the previous section, the selected mass loading avoids overestimation of the experimental performance of the active materials,68,69,150 as often reported for SLG/FLG-based SCs by adopting μg cm−2-scale mass loading.68,69,150 Symmetric SCs were fabricated by stacking the as-produced electrodes within CR2032 coin cells, using a PVDF membrane (0.2 μm pore size) as the separator and 1 M TEABF4 in PC as the electrolyte. Additional details regarding the fabrication of the SCs are reported in the Experimental section. Fig. S4a–e (ESI†) show representative cross-sectional SEM images of the SC electrodes. The reference AC electrode shows a macro/mesoporous network consisting of particles including AC and carbon black, with lateral dimension ranging from the sub-μm- to the tens of μm-scale (Fig. S4a, ESI†), in agreement with the material datasheets.139 The hybrid AC:SLG/FLG (90
:
10) and AC:SLG/FLG (80
:
20) electrodes resemble mostly the morphology of the AC electrode, suggesting that SLG/FLG flakes are randomly distributed within the AC network (Fig. S4b and c, ESI†). Differently, the structure of the AC:SLG/FLG (50
:
50) electrode displays laminar domains within the AC-based network (Fig. S4d, ESI†). Lastly, the SLG/FLG electrode shows a laminar structure (Fig. S4e, ESI†), as expected by a film based on graphene flakes.63–67 The SSAs of the electrodes are estimated by Brunauer, Emmett and Teller (BET) analysis178 of physisorption measurement with Kr at 77 K (Fig. S4f–j, ESI†).179–182 It is worth noting that Kr was preferred to N2 because the quadrupole moment of N2 (0.27 Å2)183,184 limits the access of the gas into the micropores, giving trivial porosity values for pore size <1 nm.179,181,182 Contrary to N2, Kr does not have a quadrupole moment and can easily access the micropores up to its cross-sectional area (reported between 0.11 and 0.22 nm2 per atom at 77 K, depending on possible arrangements of adsorbed species on surface, as well as appropriate ranges of relative pressure),185,186 thus suitable for physisorption characterization of microporous carbons.182,185,186 The pore size distributions were calculated by Kr physisorption measurements at 87 K using the Kr(87) Thin Film Pore Size Method based on Non-Local Density Functional Theory (NLDFT) (Fig. S4k–o, ESI†).187,188 The obtained BET SSAs (SSABET) and D-values (D20, D50 and D90, corresponding to the intercepts for 20%, 50% and 90% of the cumulative mass) of the electrodes are summarized in Table 1. The SSABET for the AC electrode is comparable to that indicated by the material datasheet (1666 ± 100 m2 g−1).139 The low SSABET values measured for AC:SLG/FLG (50
:
50) and SLG/FLG are ascribed to the restacking of the SLG/FLG flakes during their film deposition.63–65 Interestingly, for AC:SLG/FLG (90
:
10), AC:SLG/FLG (80
:
20), the SSABET increases compared to the AC. As previously reported, carbon nanoparticles (both AC and carbon black) act as effective spacers avoiding the re-stacking of graphene flakes.79,189 This allows the use of the native SSA of SLG/FLG to be fully exploited,190 creating highly packed wrinkled SLG/FLG-incorporated AC structures with SSABET higher than those of SLG/FLG and AC electrodes. Synergistically, SLG/FLG flakes can enhance the access of gas into the AC network. The activated carbon electrode has a multimodal pore size distribution peaking at ∼0.75, ∼0.80 and ∼1.20 nm (Fig. S4k, ESI†). Differently, AC:SLG/FLG and SLG/FLG electrodes have nanoporous structures with a pore size mainly inferior to 1 nm (Fig. S4l–o, ESI†). The peaks and the FWHMs of the pore size distribution progressively increase with increasing SLG/FLG content (Fig. S4l–o, ESI†). However, the pore size distribution of the SLG/FLG electrode shows also a peak at ∼6.1 nm, with mesopores larger than those exhibited by hybrid electrodes.
Table 1 SSABET and D-values of the electrodes
Electrode |
SSABET (m2 g−1) |
D20 (nm) |
D50 (nm) |
D90 (nm) |
AC |
1426 |
0.76 |
1.08 |
1.84 |
AC:SLG/FLG (90 : 10) |
2121 |
0.72 |
0.80 |
1.68 |
AC:SLG/FLG (80 : 20) |
1597 |
0.75 |
0.81 |
1.69 |
AC:SLG/FLG (50 : 50) |
631 |
0.76 |
0.84 |
1.70 |
SLG/FLG |
40 |
0.87 |
1.05 |
5.86 |
The close-packed structures of AC:SLG/FLG, as evidenced by morphological characterization (Fig. S4, ESI†), result in lower sheet resistances (Rsheet) (39 ± 2 Ω sq−1, 26 ± 2 Ω sq−1 and 15 ± 2 Ω sq−1 for AC:SLG/FLG (90
:
10), AC:SLG/FLG (80
:
20), and AC:SLG/FLG (50
:
50), respectively) compared to those of both AC (76 ± 3 Ω sq−1) and SLG/FLG (82 ± 14 Ω sq−1). In fact, the carbon nanoparticles in the hybrid electrodes can act as conductive bridges between SLG/FLG flakes, thus creating highly conductive carbon paste.191–193 However, in close-packed structures, the presence of pores with sub-nm dimension can give rise to “closed micropores”,87–90 which can limit the electrochemically accessible surface area during the operation of SCs.194 As will be shown in the next section will show that the peculiar tribology of SLG/FLG flakes prevents the latter issues. Lastly, contact angle measurements for PC with and without the electrolyte on the different electrode films revealed contact angle values equal to zero for all the cases. This result indicates that all the produced electrode films have an optimal absorbability of this organic electrolyte, which is in fact used in commercial-like AC-based SCs.41,138
Electrochemical characterization
In order to achieve a large electrochemically accessible area of the electrodes, the multimodal pore size distribution of AC (D50 > 1 nm), as optimized for commercial active material formulations,139 should be preferred to the monomodal one of hybrid electrodes (D50 < 0.85 nm).195 However, this key-guideline does not consider the tribological properties of the active materials, which could challenge the conventional rules for designing advanced SCs. The synergistic effect of the morphological and tribological properties of the active materials on the electrochemical performance of the SCs was evaluated by both cyclic voltammetry (CV) and galvanostatic charge/discharge (CD) cycling measurements. The latter was used for calculating the gravimetric capacitance (Cg) of the SC electrodes, as given by Cg = 4 × (|i|td)/(mΔV),196,197 where |i| is the module of the applied current (i), td is the discharge time, m is the total mass of the electrodes (mass of active material + mass of carbon black + mass of PVDF + mass of Al collector) and ΔV is the voltage window of the measurement. Fig. 3a and b show the CV curves of the produced SCs at voltage scan rates of 10 mV s−1 and 100 mV s−1, respectively. The nearly-rectangular CV shapes and the absence of current redox peaks indicate that the electrodes show double-layer capacitive behaviour in the corresponding voltage ranges.6,196 These data prove the absence of graphene oxide, which typically results in pseudo-capacitance contribution.56,198,199 Although graphene oxide can enhance the capacitance, the pseudo-capacitance related reaction can limit the rate capability200–202 and cycling life201,202 of the SCs, hindering practical high-power applications. The voltage range of 3.5 V was selected as the upper limit operative voltage (V+) of PC on graphitic materials,203 at which the parasitic redox reaction caused by electrolyte decomposition starts to occur,41,204 as shown by the whisker-like features in the CV curve at a voltage scan rate of 10 mV s−1 (Fig. 3a). At such a voltage scan rate, AC:SLG/FLG (90
:
10)- and AC:SLG/FLG (80
:
20)-based SCs show current density (0.41 A g−1 and 0.33 A g−1 at V+/2, respectively) higher than that of the AC-based reference (0.29 A g−1 at V+/2). In the SCs based on AC:SLG/FLG, the current density decreases by increasing the weight content of SLG/FLG in the active materials, reaching the minimum values for the SLG/FLG-based SC (<0.01 A g−1 at V+/2).
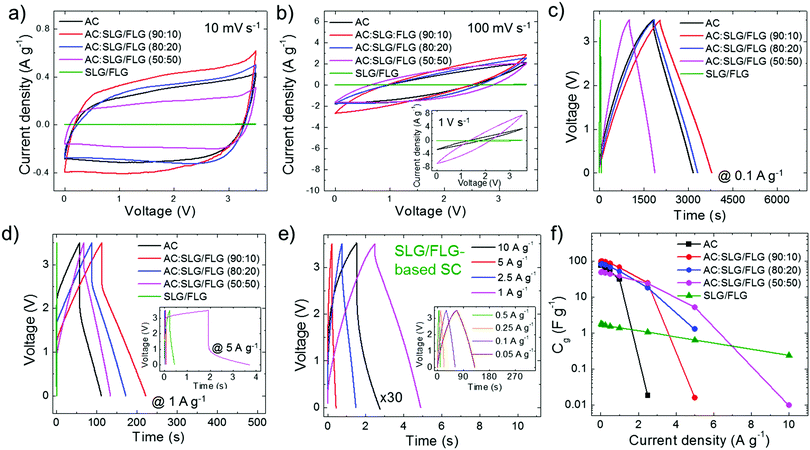 |
| Fig. 3 Electrochemical characterization of the SCs. (a and b) CV curves of the as-produced SCs at voltage scan rates of 10 mV s−1 and 100 mV s−1, respectively. The inset panel in (b) shows the CV curves of AC-, AC:SLG/FLG (50 : 50)- and SLG/FLG-based SCs at a voltage scan rate of 1 V s−1. (c and d) CD curves of the as-produced SCs at current densities of 0.1 A g−1 and 1 A g−1, respectively. The inset panel in (d) shows the CD curves of AC:SLG/FLG-, and SLG/FLG-based SCs at a current density of 5 A g−1. (e) CD curves of SLG/FLG-based SCs at various current densities (ranging between 1 and 10 A g−1). The inset panel in (e) shows the CD curves at low current densities (ranging from 0.05 to 0.5 A g−1). (f) Plot of electrode Cgvs. current densities, as derived by the CD measurements of the SCs. | |
This behaviour can be attributed to the restacking63–65 and the in-plane orientation (perpendicular to the current collector)66,67 of the SLG/FLG flakes in the absence of any spacer components.79,189,190 At 100 mV s−1, the shapes of the CV curves become biconvex (lens-shaped), especially for AC and AC:SLG/FLG (90
:
10)-based SCs (Fig. 3b). This means that only a fraction of capacitive states is retained with the applied voltage. In fact, the high mass loading of the electrodes (∼10 mg cm−2), as required for effective packaging in commercial-like SCs, results in an “areal” current density of tens of mA cm−2. In particular, at a high voltage scan rate (e.g., 1 V s−1, inset to Fig. 3b), this causes the emergence of resistive voltage drops originating from the electrolyte resistance across the nano/mesoporous active material films,196,205–208 as well as the electrical resistance of the metal collectors and active films.196,205 However, the deviation from the ideal rectangular CV shape is reduced with increasing the weight content of SLG/FLG in the active materials of the SCs. Noteworthily, the SLG/FLG-based SC still exhibits a capacitive behaviour at a voltage scan rate of up to 50 V s−1 (Fig. S5a and b, ESI†), where both AC- and AC:SLG/FLG-based SCs display resistive performance (Fig. S5c, ESI†). Fig. 4c and d display the CD curves obtained for the SCs at a current density of 0.1 A g−1 and 1 A g−1, respectively. At 0.1 A g−1 (Fig. 3c), the CD curves have a triangular shape, which is an indication of the double-layer capacitive behaviour of the SCs.56,198,199 The AC:SLG/FLG (90
:
10) and AC:SLG/FLG (80
:
20)-based SCs have shown higher td (1735.8 s and 1462.6 s, respectively) compared to the AC-based reference (1354.2 s). By further increasing the weight content of SLG/FLG in the SC active material, the td decreases to the minimum values recorded for the AC:SLG/FLG-based SCs (i.e., 867.2 s). At 1 A g−1 (Fig. 3d), CD curves show a resistive voltage drop at the half-cycle, originating from both the electrolyte resistance across the nano/mesoporous active material films,196,205–208 and the electrical resistance of the metal collectors and active films.196,205 By increasing the current density to 5 A g−1 (inset to Fig. 3d), the voltage drops increase up to values superior to V+ for AC-, AC:SLG/FLG (90
:
10)-, AC:SLG/FLG (80
:
20)-based SCs, which start to exhibit resistive behaviour. Differently, both AC:SLG/FLG (50
:
50)- and SLG/FLG-based SCs still show a capacitive behaviour. In particular, the SLG/FLG-based SC exhibits nearly triangular-shaped CD curves at a current density as high as 10 A g−1 (Fig. 3e). Fig. 3f shows the Cg of the SC electrodes calculated from the CD curve at current densities ranging from 0.05 to 10 A g−1. These data indicate that the use of SLG/FLG flakes in AC films increases both the maximum Cg (99.2 F g−1 for the AC:SLG/FLG (90
:
10)-based SC, as calculated at the lowest current densities of 0.05 A g−1) and the rate capability of the SCs (up to >5 and >10 A g−1 for AC:SLG/FLG (50
:
50)- and SLG/FLG-based SCs, respectively) compared to the AC-based SC (Cg = 76.7 F g−1 at 0.05 A g−1 and rate capability up to 2.5 A g−1). As shown in Fig. 4a, maximum Cg values (Cg
AC:SLG/FLG
(90:10) > Cg
AC:SLG/FLG
(80
:
20) > Cg
AC > Cg
AC:SLG/FLG
(50
:
50) > Cg
SLG/FLG) positively correlate with the electrode SSAs calculated by BET analysis (SSAAC:SLG/FLG
(90
:
10) > SSAAC/SLG:FLG
(80
:
20) > SSAAC > SSAAC:SLG/FLG (50
:
50) > SSASLG/FLG). Under these conditions, the electrolyte transport kinetics likely affords the access of ions totally into the surface area of the electrodes. The capacitance trend is severely altered with increasing current density (Fig. 4b) until to be completely overturned at 10 A g−1, at which the SLG/FLG-based SC shows the maximum Cg value (0.24 F g−1). At 5 A g−1, the AC:SLG/FLG (50
:
50)-based electrode exhibits a Cg > 5 F g−1, while, in contrast, the other hybrid SCs display a resistive behaviour. The large mesoporosity of the SLG/FLG-based SC (Fig. S4o, ESI†) can be the origin of its excellent rate capability. However, for the AC:SLG/FLG-based electrodes, the trend shown in Fig. 4b cannot be attributed to the porosity (and/or morphology) of SC electrodes, since it does not show any correlation between Cg and D90 (Fig. 4c). For hybrid electrode-based SCs, Fig. 4d shows that Cg tends to positively correlate with the SLG/FLG weight content in the active materials when a high current density (>5 A g−1) is applied. At 5 A g−1, the AC- and AC:SLG/FLG (90
:
10)-based SCs show a resistive behaviour, and the highest Cg value is achieved by the hybrid electrode-based SCs with the highest SLG/FLG flake content in the active material, i.e., AC:SLG/FLG (90
:
10). The Cg of the SLG/FLG-based SC is limited due to its relatively low SSABET compared to the ones of the hybrid electrode-based SCs. However, the SLG/FLG-based SC is the only device still displaying a capacitive behaviour at the highest current density of 10 A g−1. Consequently, we first attributed the high-rate capability of the SLG/FLG-based SCs to the tribology properties of the SLG/FLG flakes (which positively correlate with their weight content in the active material), which act as “ion slides” for the case of 1 M TEABF4 in PC. This agrees with the analysis of the LFM measurements (Fig. 2d and e), showing an almost unchanged FF on SLG/FLG flakes with and without the electrolyte in the solvent.
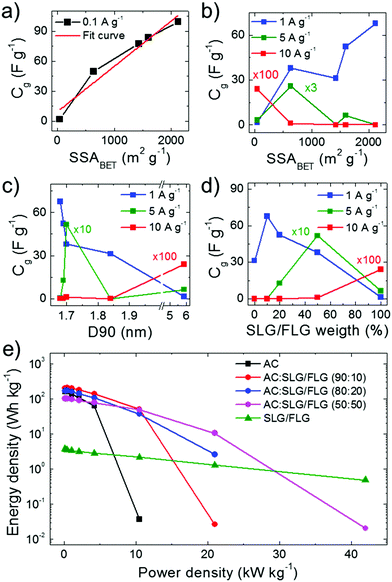 |
| Fig. 4 Performance analysis of the SCs. (a and b) Dependence of the electrode Cg on the SSABET of the SC electrodes at CD current densities of 0.1 A g−1 (panel a), and 1, 5 and 10 A g−1 (panel b). (c) Dependence of the electrode Cg on the D90 of the SC electrodes at CD current densities of 1, 5, and 10 A g−1. (d) Dependence of the electrode Cg on the SLG/FLG weight content in the active material of the SC electrodes at CD current densities of 1, 5, and 10 A g−1. In panels (b–d) some data have been multiplied by the factors shown along the corresponding curves. (e) Ragone plots (energy density vs. power density) of the SCs. | |
The Ragone plots obtained for the SC electrodes under study are shown in Fig. 4e, revealing that the use of SLG/FLG enables the SCs to operate at high power density (>20 kW kg−1), while retaining their energy density. For example, the AC:SLG/FLG (50
:
50)-based SC exhibited an energy density >10 W h kg−1 for power density >20 kW kg−1, while AC-based SCs have shown only a resistive behaviour. Furthermore, the SLG/FLG-based SC achieved an energy density of ∼0.5 W h kg−1 at power density >40 kW kg−1. Once again, it is important to indicate that these results have been obtained with SCs adopting a commercial-like active material mass loading of ∼10 mg cm−2, which accounts for about 30% of the total mass of the packaged commercial EC.69
Therefore, as commented in ref. 69, our data provide a true performance evaluation of SCs used for energy storage applications. The comparison of our data with relevant literature on SCs is not straightforward since the latter often investigate SCs adopting active material mass loadings one or two orders of magnitude lower than 10 mg cm−2, and therefore their gravimetric performance could be strongly overestimated in commercial-like device architectures.69
Conclusions
We have provided novel insights into the practical use of single-/few-layer graphene (SLG/FLG) flakes in mesoporous activated carbon (AC) films to positively impact the electrochemical performance of commercial-like supercapacitors (SCs) (i.e., SCs adopting high active material mass loading of ∼10 mg cm−2). Our results reveal that the nanotribological properties between electrolytes and the nanocarbons are pivotal in providing high-accessibility of the ions to mesoporous electrode films. In particular, we have shown that the ions of an established SC electrolyte (i.e., 1 M TEABF4 in propylene carbonate) efficiently slide over the SLG/FLG flakes. Consequently, the incorporation of SLG/FLG into high-specific surface area (SSA) AC-based nanoporous structures enables the enhancement of the electrochemical performance of SCs. At a charge/discharge (CD) current density of 0.1 A g−1, our SC-based on AC:SLG/FLG (90
:
10) has shown a Cg (98.2 F g−1) increased by almost 30% compared to the one of the AC-based reference (76.8 F g−1). Such SLG/FLG-induced improvements in the SC performance have been explained by the increase of SSA after the SLG/FLG incorporation into the AC film. At higher CD current densities (>1 A g−1), the AC-based reference displayed a resistive behaviour, while the AC:SLG/FLG-based SCs continued to exhibit capacitive performance. In particular, AC:SLG/FLG (50
:
50) still exhibited a Cg of 23.9 and 5.2 F g−1 at CD current densities as high as 2.5 and 5.0 A g−1, respectively. Furthermore, SLG/FLG-based SCs have shown an optimal capacitive retention with increasing CD current density up to 10.0 A g−1. The optimal capacitive behaviour at high CD current densities (≥1.0 A g−1) for SLG/FLG and AC:SLG/FLG-based electrodes has been attributed to the peculiar nanotribological properties of the electrolyte ions on the SLG/FLG flakes. The management of the nanotribological properties of both active materials and electrolytes can be a new paradigm to overcome the classic dichotomy of energy density and power density in SCs. In fact, the advantage of conceiving an efficient ion transport within high-SSA electrodes allows for ideal access of ions in both meso- and micro-pores, which is mandatory for ideal rate-independent high energy densities. Such rationale allows us to design commercial-like SLG/FLG-based SCs with superior energy/power density performance compared to the AC-based benchmark. It must be noted that the simultaneous presence of high SSA (>2000 m2 g−1), and fast ion and electron transport in nanoporous (pore size < 1 nm) carbon materials pave the way towards the realization of high performance SCs with high active material mass loading (∼10 mg cm−2), which is a strict requirement in commercial-like SCs.69 Here, active material weight has to account for about more than 30% of the total mass of the packaged device, otherwise their “true” gravimetric performance drastically decreases (by a factor >10 for active material mass loading of 1 mg cm−2).69 In fact, the added-value of “graphene flakes” in SCs can readily impact on the SCs market since all the results shown here have been obtained with commercially available AC, scalable production of SLG/FLG flakes (i.e., wet-jet milling – WJM – exfoliation of graphite), and industrial-like electrode manufacturing. Prospectively, the study of the tribological properties of the SLG/FLG flakes could be extended also to other electrolyte/solvent systems to generalize the application of the “ion sliding” on graphene concept into advanced SCs.
Experimental
Wet-jet milling-assisted exfoliation of graphite
The WJM-assisted exfoliation process of graphite comprised a first step of preparing a dispersion of graphite in a dispersant solvent and a subsequent exfoliation step. As previously described in ref. 91, 200 g of graphite flakes (+100 mesh, Sigma Aldrich) were mixed with 20 L of NMP (>97%, Sigma Aldrich) by a mechanical stirrer (Eurostar digital Ika-Werke). It is noteworthy that NMP was used as the dispersant solvent because its surface tension (40.8 mJ m−2)209 is close to the surface free energy of graphite (∼62 mJ m−2).209,210 Therefore, the choice of NMP reduced the Gibbs free energy of the solvent/graphite mixture (theoretical minimum reached when surface tension of the solvent is equal to surface energies of graphite),209 which has to be minimized for attaining the ideal exfoliation condition.209,211,212 As sketched in Fig. S1 (ESI†), a hydraulic piston supplied a pressure of 250 MPa to push the as-prepared mixture into a set of 5 different perforated and interconnected disks, named processor. Two jet streams originated at the second disk that consisted of two holes with a diameter of 1 mm. Then, the jet streams collided between the second and the third disks, given by a nozzle (i.e., a half-cylinder channel) of diameter 0.3 mm. The shear force generated by the solvent when the sample passed through such a nozzle promoted the graphite exfoliation, as theoretically described in ref. 91. The sample was then separated into two jet streams, which recombined in the last disk before leaving the processor. Immediately after the processor, the sample was cooled down by means of a chiller. The processed sample was then collected. The wet-jet milling process was repeated passing the sample through the 0.15 mm nozzle. Finally, a third exfoliation step was carried out by adjusting the diameter of the nozzle to 0.10 mm. The as-obtained dispersion was dried in a rotary evaporator (Heidolph HEIVAP INDUSTRIAL, FKV Srl, Italy) setting the bath temperature at 80 °C and gradually lowering the pressure to 5 mbar, allowing the evaporation of NMP. Subsequently, 1.5 L of dimethyl sulfoxide (DMSO) (Merck KGaA, Germany) were added to SLG/FLG flakes. The resulting dispersion was then poured into five aluminium Petri disks (300 mL nominal capacity) and placed in a refrigerator at −15 °C. After 1 h, the Petri dishes were inserted into a single-chamber freeze dryer (Martin Christ Alpha 2-4LSC plus), where the temperature of the condenser was already set to −85 °C. The sublimation was carried out at a temperature of −10 °C and a pressure of 0.1 mbar. After 50 h, the powder was extracted from the freeze dryer and stocked in plastic containers.
Characterization of materials
Transmission electron microscopy images were taken with a JEM 1011 (JEOL) TEM (thermionic W filament), operating at 100 kV. Morphological and statistical analysis was carried out by using ImageJ software (NIH)213 and OriginPro 9.1 software (OriginLab),214 respectively. The samples for the TEM measurements were prepared by drop casting a 1
:
50 diluted WJM-produced SLG/FLG dispersion in NMP onto ultrathin C-films on holey carbon coated 400 mesh Cu grids (Ted Pella Inc.). The grids were stored under vacuum at room temperature to remove the solvent residues.
Atomic force microscopy measurements were performed by using a Bruker Innova atomic force microscope in tapping mode. To prepare the samples, SLG/FLG flake dispersions were drop-cast onto freshly-cleaved mica sheets (G250-1, Agar Scientific Ltd, Essex, UK) and dried overnight at 500 °C under vacuum. Atomic force microscopy images were acquired in scan areas of 5 × 5 μm2 (512 points per line) by using silicon probes with a frequency of 300 kHz and spring constant of 40 N m−1. The statistical analysis of the thickness was studied by measuring the profile of 150 flakes on various AFM images with Gwyddion 2.51 software. The thickness distribution was plotted and fitted with a log-normal curve by Origin 9.1 software.214
Raman spectroscopy measurements were carried out on a Renishaw microRaman invia 1000 using a 50× objective (numerical aperture of 0.75), with an excitation wavelength of 514.5 nm and an incident power on the samples of 5 mW. The samples were prepared by drop casting a 1
:
30 diluted WJM-produced SLG/FLG dispersion in NMP onto a Si wafer covered with 300 nm thermally grown SiO2 (LDB Technologies Ltd). Bulk graphite was analysed in the powder form. For each sample, 50 spectra were collected. Origin 9.1 software214 was used to perform the deconvolution and the statistical data analysis.
X-ray photoelectron spectroscopy analysis was performed using a Kratos Axis UltraDLD spectrometer. The sample was obtained by drop casting the WJM-produced SLG/FLG dispersion in NMP onto Au-coated silicon wafers. The sample was then dried at 200 °C overnight to remove solvent residuals. The XPS spectra were acquired using a monochromatic Al Kα source operating at 20 mA and 15 kV. The analysis was carried out on a 300 μm × 700 μm area. High-resolution spectra of C 1s and Au 4f peaks were collected at a pass energy of 10 eV and energy step of 0.1 eV. Energy calibration was performed setting the Au 4f7/2 peak at 84.0 eV. Data analysis was carried out with CasaXPS software (version 2.3.17).
The frictional behaviour of the SLG/FLG flakes and AC films, obtained by doctor blade deposition of concentrated WJM-produced SLG/FLG and AC dispersions in NMP, was evaluated in PC with or without 1 M TEABF4 by using a Nanowizard III (JPK Instruments, Germany). Lateral force microscopy measurements were performed by using a single beam silicon cantilever (CSC38, Micromasch) with a nominal spring constant of 0.09 N m−1 and a tip with a typical radius of curvature of 8 nm. The actual spring constant of each cantilever was determined using the thermal noise method. The FF values positively correlate with the output voltage signal (VAFM) resulting from the measurements of the lateral deflection of the cantilever, in agreement with FF = (GTD × h × KL × VAFM)/(L × SDIF),135 where GTD is the gain torsion/deflection ratio, h is the height of the tip, KL is the lateral spring constant, L is the length of the cantilever and SDIF is the normal deflection sensitivity. The FF between probes and the sample surface was measured by scanning perpendicularly to the long axis of the cantilever and increasing the applied L incrementally from 0 to 18 nN. Since our aim was to compare the FF values between the AFM silicon tip and the two different film surfaces (AC and SLG/FLG) in PC (with and without TEABF4 electrolyte), KL and SDIF have not been determined. Consequently, the LFM responses have been reported as lateral deflection (i.e., VAFM) vs. L. The same tip was then used during LFM measurements to exclude its contribution in the comparative force analysis of the results obtained for different films.149 The crosstalk between normal and lateral signals was minimized by calculating the lateral deflection as half the difference between the values obtained in the two scan directions (trace and retrace).149 The LFM responses were obtained by scanning 5 lines of 50 μm over the entire L range and acquiring 256 points per line at a scan rate of 25 μm s−1. Measurements were repeated at 10 different locations and the arithmetic mean value of the LFM response at each L has been reported with the corresponding standard deviation.
Fabrication of the electrodes and the supercapacitors
The active materials of the SCs were obtained by mixing dried SLF/FLG flakes with commercial AC (AB-520, MTI Corp.). SLG/FLG
:
AC weight ratios of 10
:
90, 20
:
80, 50
:
50 were investigated. Activated carbon and SLG/FLG flakes were also used solely as reference active materials. Subsequently, the active materials were mixed with carbon black (acetylene, >99.9%, Alfa Aesar) and PVDF (average molecular weight ∼534
000, Sigma Aldrich) with an 85
:
10
:
5 weight ratio in a small volume of NMP (99%, Sigma Aldrich) until a homogenized paste-like consistency is obtained (slurry). The SC electrodes were prepared by depositing such pastes onto Al foil by the doctor blade technique. The corresponding pastes were dried with a hot plate at 60 °C and later, in a glass oven vacuum system (B-585 Kugelrohr, Buchi®) at 120 °C overnight in order to remove the water absorbed by the active carbon and residual NMP. The SCs were fabricated in a symmetric configuration by stacking two identical electrodes within coin cells (CR2032 cases, springs and spacers purchased from MTI Corp.) by using a compact crimper (MSK-PN110-S, MTI Corp.). A PVDF membrane with a pore size of 0.2 μm (Amersham™ Hybond™) and 1 M TEABF4 (>99%, Sigma Aldrich) in PC (anhydrous, >99%, Sigma Aldrich) were used as the separator and electrolyte, respectively. The coin cells were assembled into an Ar-filled glovebox with concentrations of moisture and O2 below 0.1 ppm.
Characterization of the electrodes and the supercapacitors
Scanning electron microscopy analysis of SC electrodes was performed using a Helios Nanolab® 600 DualBeam microscope (FEI Company) and 5 kV and 0.2 nA as measurement conditions. The SEM images of the electrodes were collected without any metal coating or pre-treatment.
The surface morphology of the electrodes was analysed by means of a Nanowizard III AFM system (JPK Instruments, Germany), coupled with an AxioObserver D1 (Zeiss, Germany) inverted optical microscope. The images were acquired by using quantitative imaging (QI) mode, an AFM mode based on force measurements. V-Shaped DNP silicon nitride cantilevers (Bruker, Billerica, MA, USA) with a nominal spring constant of 0.06 N m−1, resonance frequency in air in the 40–70 kHz range and typical curvature radius of 20–60 nm were used. The actual spring constant of each cantilever was determined in situ, using the thermal noise method. Images of 50 × 50 μm2 were collected acquiring a large set of force–distance (FD) curves (128 × 128) at a velocity of 30 μm s−1 with a maximum force load of 5 nN and a curve length of 250 nm.
Specific surface area and pore size distribution measurements of SC electrodes were carried out on an Autosorb-iQ (Quantachrome) by Kr physisorption at temperatures of 77 and 87 K, respectively. The specific surface areas were calculated using the multipoint BET model,178 considering equally spaced points in the P/P0 range of 0.009–0.075. P0 is the vapour pressure of Kr at 77 K, corresponding to 2.63 Torr.179,180–182 The pore size distribution was calculated by the Kr(87) Thin Film Pore Size Method using NLDFT.187,188 Before the measurements, the samples were degassed for 1 h at 60 °C under vacuum conditions to eliminate weakly adsorbed species.
Sheet resistance of the electrodes was measured by a four-probe method215 using a Jandel RM3000 Test Unit.
Contact angle measurements for PC with and without 1 M TEABF4 on the electrode films were obtained by using DATAPHYSICS, an OCA-15 set-up and liquid electrolyte drop volume of 3 μL.
The electrochemical measurements were performed with a potentiostat/galvanostat (VMP3, Biologic). Cyclic voltammetry measurements were carried out at various voltage scan rates, ranging from 0.01 to 50 V s−1. Galvanostatic CD measurements were carried out at different current densities, ranging from 0.05 to 10 A g−1.
Conflicts of interest
There are no conflicts to declare.
Acknowledgements
The work has been supported by the European Union's Horizon 2020 research and innovation program under grant agreements No. 785219 – GrapheneCore2. We thank the Electron Microscopy facility – Istituto Italiano di Tecnologia for support in TEM data acquisition; Nanochemistry facility, Istituto Italiano di Tecnologia for support in material characterization; IIT Clean Room facility for the access to carry out SEM/EDS measurements; Smart Materials facility, Istituto Italiano di Tecnologia and specially to Dr Riccardo Carzino for the contact angle measurements; Material Characterization facility, Istituto Italiano di Tecnologia, for support in AFM data acquisition. The authors would like to thank Dr L. Silvestri (Graphene Labs, Istituto Italiano di Tecnologia) for the preparation of active carbon-based pastes and films; and Stefano Bortolotti (BeDimensional Spa.) for the graphic arts.
Notes and references
- A. C. Forse, C. Merlet, J. M. Griffin and C. P. Grey, J. Am. Chem. Soc., 2016, 138, 5731–5744 CrossRef CAS PubMed.
- J. Chmiola, G. Yushin, Y. Gogotsi, C. Portet, P. Simon and P. L. Taberna, Science, 2006, 313, 1760–1763 CrossRef CAS PubMed.
- M. Salanne, B. Rotenberg, K. Naoi, K. Kaneko, P. L. Taberna, C. P. Grey, B. Dunn and P. Simon, Nat. Energy, 2016, 1, 16070 CrossRef CAS.
- P. Simon and Y. Gogotsi, Nat. Mater., 2008, 7, 845–854 CrossRef CAS PubMed.
-
B. E. Conway, Electrochemical supercapacitors: scientific fundamentals and technological applications, Springer Science & Business Media, Germany, 2013 Search PubMed.
- G. Wang, L. Zhang and J. Zhang, Chem. Soc. Rev., 2012, 41, 797–828 RSC.
- Y. Jun, W. Qian, W. Tong and F. Zhuangjun, Adv. Energy Mater., 2013, 4, 1300816 Search PubMed.
- L. L. Zhang and X. S. Zhao, Chem. Soc. Rev., 2009, 38, 2520–2531 RSC.
- X. Chen, R. Paul and L. Dai, Natl. Sci. Rev., 2017, 4, 453–489 CrossRef CAS.
- E. Raymundo-Piñero, K. Kierzek, J. Machnikowski and F. Béguin, Carbon, 2006, 44, 2498–2507 CrossRef.
- C. John, L. Celine, T. Pierre-Louis, S. Patrice and G. Yury, Angew. Chem., Int. Ed., 2008, 47, 3392–3395 CrossRef PubMed.
- P. Simon, Y. Gogotsi and B. Dunn, Science, 2014, 343, 1210–1211 CrossRef CAS PubMed.
- J. R. Miller and P. Simon, Science, 2008, 321, 651–652 CrossRef CAS PubMed.
-
T. A. Smith, J. P. Mars and G. A. Turner, 2002 IEEE 33rd Annual IEEE Power Electronics Specialists Conference. Proceedings (Cat. No. 02CH37289), 2002, vol. 1, pp. 124–128.
- F. Naseri, E. Farjah and T. Ghanbari, IEEE Trans. Veh. Technol., 2017, 66, 3724–3738 Search PubMed.
- R. Teymourfar, B. Asaei, H. Iman-Eini and R. Nejati Fard, Energy Convers. Manage., 2012, 56, 206–214 CrossRef.
- X. Luo, J. Wang, M. Dooner and J. Clarke, Appl. Energy, 2015, 137, 511–536 CrossRef.
- N. A. Kyeremateng, T. Brousse and D. Pech, Nat. Nanotechnol., 2016, 12, 7 CrossRef PubMed.
- T. Ma, H. Yang and L. Lu, Appl. Energy, 2015, 153, 56–62 CrossRef.
- H. Lee, G. L. Bullard, G. E. Mason and K. Kern, IEEE Trans. Magn., 1989, 25, 324–330 CrossRef.
- L. Gao, R. A. Dougal and S. Liu, IEEE Trans. Power Electron., 2005, 20, 236–243 CrossRef.
- C. E. Holland, J. W. Weidner, R. A. Dougal and R. E. White, J. Power Sources, 2002, 109, 32–37 CrossRef CAS.
- A. González, E. Goikolea, J. A. Barrena and R. Mysyk, Renewable Sustainable Energy Rev., 2016, 58, 1189–1206 CrossRef.
- F. Wang, X. Wu, X. Yuan, Z. Liu, Y. Zhang, L. Fu, Y. Zhu, Q. Zhou, Y. Wu and W. Huang, Chem. Soc. Rev., 2017, 46, 6816–6854 RSC.
- V. Etacheri, R. Marom, R. Elazari, G. Salitra and D. Aurbach, Energy Environ. Sci., 2011, 4, 3243–3262 RSC.
-
J.-M. Tarascon and M. Armand, Materials for Sustainable Energy, Co-Published with Macmillan Publishers Ltd, UK, 2010, pp. 171–179 Search PubMed.
- M. Kassem, J. Bernard, R. Revel, S. Pélissier, F. Duclaud and C. Delacourt, J. Power Sources, 2012, 208, 296–305 CrossRef CAS.
- J. N. Reimers and J. R. Dahn, J. Electrochem. Soc., 1992, 139, 2091–2097 CrossRef CAS.
- T. Ohzuku, Y. Iwakoshi and K. Sawai, J. Electrochem. Soc., 1993, 140, 2490–2498 CrossRef CAS.
- C. Peabody and C. B. Arnold, J. Power Sources, 2011, 196, 8147–8153 CrossRef CAS.
- M. Winter and J. O. Besenhard, Chem. Unserer Zeit, 2004, 33, 252–266 CrossRef.
- M. A. Fetcenko, S. R. Ovshinsky, B. Reichman, K. Young, C. Fierro, J. Koch, A. Zallen, W. Mays and T. Ouchi, J. Power Sources, 2007, 165, 544–551 CrossRef CAS.
- Y. Liu, H. Pan, M. Gao and Q. Wang, J. Mater. Chem., 2011, 21, 4743–4755 RSC.
- B. C. Melot and J.-M. Tarascon, Acc. Chem. Res., 2013, 46, 1226–1238 CrossRef CAS PubMed.
- M. A. Hannan, M. M. Hoque, A. Mohamed and A. Ayob, Renewable Sustainable Energy Rev., 2017, 69, 771–789 CrossRef.
- B. Dunn, H. Kamath and J.-M. Tarascon, Science, 2011, 334, 928–935 CrossRef CAS PubMed.
- B. François, P. Volker, B. Andrea and F. Elzbieta, Adv. Mater., 2014, 26, 2219–2251 CrossRef PubMed.
- C. Largeot, C. Portet, J. Chmiola, P.-L. Taberna, Y. Gogotsi and P. Simon, J. Am. Chem. Soc., 2008, 130, 2730–2731 CrossRef CAS PubMed.
- Y. Zhu, S. Murali, M. D. Stoller, K. J. Ganesh, W. Cai, P. J. Ferreira, A. Pirkle, R. M. Wallace, K. A. Cychosz, M. Thommes, D. Su, E. A. Stach and R. S. Ruoff, Science, 2011, 332, 1537–1541 CrossRef CAS PubMed.
- P. Simon and Y. Gogotsi, Acc. Chem. Res., 2013, 46, 1094–1103 CrossRef CAS PubMed.
- C. Zhong, Y. Deng, W. Hu, J. Qiao, L. Zhang and J. Zhang, Chem. Soc. Rev., 2015, 44, 7484–7539 RSC.
- A. Balducci, J. Power Sources, 2016, 326, 534–540 CrossRef CAS.
- M. D. Levi, G. Salitra, N. Levy, D. Aurbach and J. Maier, Nat. Mater., 2009, 8, 872 CrossRef CAS PubMed.
- J. M. Griffin, A. C. Forse, W. Y. Tsai, P. L. Taberna, P. Simon and C. P. Grey, Nat. Mater., 2015, 14, 812 CrossRef CAS PubMed.
- M. Deschamps, E. Gilbert, P. Azais, E. Raymundo-Piñero, M. R. Ammar, P. Simon, D. Massiot and F. Béguin, Nat. Mater., 2015, 14, 812 CrossRef PubMed.
- F. W. Richey, B. Dyatkin, Y. Gogotsi and Y. A. Elabd, J. Am. Chem. Soc., 2013, 12, 351 Search PubMed.
- A. C. Forse, J. M. Griffin, C. Merlet, J. Carretero-Gonzalez, A. R. O. Raji, N. M. Trease and C. P. Grey, Nat. Energy, 2013, 35, 12818–12826 Search PubMed.
- C. Prehal, D. Weingarth, E. Perre, R. T. Lechner, H. Amenitsch, O. Paris and V. Presser, Energy Environ. Sci., 2015, 8, 1725–1735 RSC.
- S. Boukhalfa, L. He, Y. B. Melnichenko and G. Yushin, Angew. Chemi., Int. Ed., 2013, 52, 4618–4622 CrossRef CAS PubMed.
- C. Prehal, C. Koczwara, N. Jäckel, A. Schreiber, M. Burian, H. Amenitsch, M. A. Hartmann, V. Presser and O. Paris, Nat. Energy, 2017, 2, 16215 CrossRef CAS.
- C. Merlet, B. Rotenberg, P. A. Madden, P.-L. Taberna, P. Simon, Y. Gogotsi and M. Salanne, Nat. Mater., 2012, 11, 306 CrossRef CAS PubMed.
- C. Merlet, C. Péan, B. Rotenberg, P. A. Madden, B. Daffos, P. L. Taberna, P. Simon and M. Salanne, Nat. Commun., 2013, 4, 2701 CrossRef CAS PubMed.
- X. Yang, C. Cheng, Y. Wang, L. Qiu and D. Li, Science, 2013, 341, 534–537 CrossRef CAS PubMed.
- M. Yassine and D. Fabris, Energies, 2017, 10, 1340 CrossRef.
- M. Pumera, Energy Environ. Sci., 2011, 4, 668–674 RSC.
- B. Xu, S. Yue, Z. Sui, X. Zhang, S. Hou, G. Cao and Y. Yang, Energy Environ. Sci., 2011, 4, 2826–2830 RSC.
- M. D. Stoller, S. Park, Y. Zhu, J. An and R. S. Ruoff, Nano Lett., 2008, 8, 3498–3502 CrossRef CAS PubMed.
- W. Yang, M. Ni, X. Ren, Y. Tian, N. Li, Y. Su and X. Zhang, Curr. Opin. Colloid Interface Sci., 2015, 20, 416–428 CrossRef CAS.
- J. Xia, F. Chen, J. Li and N. Tao, Nat. Nanotechnol., 2009, 4, 505 CrossRef CAS PubMed.
- M. Q. Long, L. Tang, D. Wang, L. Wang and Z. Shuai, J. Am. Chem. Soc., 2009, 131, 17728–17729 CrossRef CAS PubMed.
- J. H. Chen, C. Jang, S. Xiao, M. Ishigami and M. S. Fuhrer, Nat. Nanotechnol., 2008, 3, 206 CrossRef CAS PubMed.
- X. Du, I. Skachko, A. Barker and E. Y. Andrei, Nat. Nanotechnol., 2008, 3, 491 CrossRef CAS PubMed.
- J. Li and M. Östling, Crystals, 2013, 3, 163–190 CrossRef CAS.
- J. H. Lee, N. Park, B. G. Kim, D. S. Jung, K. Im, J. Hur and J. W. Choi, ACS Nano, 2013, 7, 9366–9374 CrossRef CAS PubMed.
- Y. Wang, Y. Wu, Y. Huang, F. Zhang, X. Yang, Y. Ma and Y. Chen, J. Phys. Chem. C, 2011, 115, 23192–23197 CrossRef CAS.
- J. J. Yoo, K. Balakrishnan, J. Huang, V. Meunier, B. G. Sumpter, A. Srivastava, M. Conway, A. L. Mohana Reddy, J. Yu, R. Vajtai and P. M. Ajayan, Nano Lett., 2011, 11, 1423–1427 CrossRef CAS PubMed.
- Z. Wu, K. Parvez, X. Feng and K. Müllen, Nat. Commun., 2013, 4, 2487 CrossRef PubMed.
- M. D. Stoller and R. S. Ruoff, Energy Environ. Sci., 2010, 3, 1294–1301 RSC.
- Y. Gogotsi and P. Simon, Science, 2011, 334, 917–918 CrossRef CAS PubMed.
- Y. Song, T.-Y. Liu, G.-L. Xu, D.-Y. Feng, B. Yao, T.-Y. Kou, X.-X. Liu and Y. Li, J. Mater. Chem. A, 2016, 4, 7683–7688 RSC.
- L. Wen-Wen, F. Ya-Qiang, Y. Xing-Bin, C. Jiang-Tao and X. Qun-Ji, Adv. Funct. Mater., 2013, 23, 4111–4122 CrossRef.
- Q. Chen, Y. Hu, C. Hu, H. Cheng, Z. Zhang, H. Shao and L. Qu, Phys. Chem. Chem. Phys., 2014, 16, 19307–19313 RSC.
- S. Drieschner, M. Weber, J. Wohlketzetter, J. Vieten, E. Makrygiannis, B. M. Blaschke, V. Morandi, L. Colombo, F. Bonaccorso and J. A. Garrido, 2D Mater., 2016, 3, 45013 CrossRef.
- O. Bubnova, Nat. Nanotechnol., 2017, 12, 190 CrossRef CAS PubMed.
- Y. Xu, Z. Lin, X. Huang, Y. Wang, Y. Huang and X. Duan, Adv. Mater., 2013, 25, 5779–5784 CrossRef CAS PubMed.
- Y. Xu, Z. Lin, X. Huang, Y. Liu, Y. Huang and X. Duan, ACS Nano, 2013, 7, 4042–4049 CrossRef CAS PubMed.
- Z. S. Wu, A. Winter, L. Chen, Y. Sun, A. Turchanin, X. Feng and K. Müllen, Adv. Mater., 2012, 24, 5130–5135 CrossRef CAS PubMed.
- Y. Xue, D. Yu, L. Dai, R. Wang, D. Li, A. Roy, F. Lu, H. Chen, Y. Liu and J. Qu, Phys. Chem. Chem. Phys., 2013, 15, 12220–12226 RSC.
- Z. Lei, N. Christov and X. S. Zhao, Energy Environ. Sci., 2011, 4, 1866–1873 RSC.
- Y. Ping, Y. Gong, Q. Fu and C. Pan, Prog. Nat. Sci.: Mater. Int., 2017, 27, 177–181 CrossRef CAS.
- https://www.idtechex.com/research/reports/supercapacitor-technologies-and-markets-2018-2028-000568.asp (data accesed on 01/09/2018).
- L. Wei and G. Yushin, Nano Energy, 2012, 1, 552–565 CrossRef CAS.
- V. V. N. Obreja, A. Dinescu and A. C. Obreja, Int. Rev. Electr. Eng., 2010, 5, 272 Search PubMed.
- O. Barbieri, M. Hahn, A. Herzog and R. Kötz, Carbon, 2005, 43, 1303–1310 CrossRef CAS.
- M. Endo, T. Maeda, T. Takeda, Y. J. Kim, K. Koshiba, H. Hara and M. S. Dresselhaus, J. Electrochem. Soc., 2001, 148, A910–A914 CrossRef CAS.
- G. Lota, T. A. Centeno, E. Frackowiak and F. Stoeckli, Electrochim. Acta, 2008, 53, 2210–2216 CrossRef CAS.
- A. G. Pandolfo and A. F. Hollenkamp, J. Power Sources, 2006, 157, 11–27 CrossRef CAS.
- K. Kierzek, E. Frackowiak, G. Lota, G. Gryglewicz and J. Machnikowski, Electrochim. Acta, 2004, 49, 515–523 CrossRef CAS.
- G. Salitra, A. Soffer, L. Eliad, Y. Cohen and D. Aurbach, J. Electrochem. Soc., 2000, 147, 2486–2493 CrossRef CAS.
- G. Gryglewicz, J. Machnikowski, E. Lorenc-Grabowska, G. Lota and E. Frackowiak, Electrochim. Acta, 2005, 50, 1197–1206 CrossRef CAS.
- A. E. Del Rio Castillo, V. Pellegrini, A. Ansaldo, F. Ricciardella, H. Sun, L. Marasco, J. Buha, Z. Dang, L. Gagliani, E. Lago, N. Curreli, S. Gentiluomo, F. Palazon, P. Toth, E. Mantero, M. Crugliano, A. Gamucci, A. Tomadin, M. Polini and F. Bonaccorso, Mater. Horiz., 2018, 5, 890–904 RSC.
- S. Bellani, F. Wang, G. Longoni, L. Najafi, R. Oropesa-Nuñez, A. E. Del Rio Castillo, M. Prato, X. Zhuang, V. Pellegrini, X. Feng and F. Bonaccorso, Nano Lett., 2018, 18, 7155–7164 CrossRef CAS PubMed.
-
A. E. Del Rio Castillo, A. Ansaldo, V. Pellegrini and F. Bonaccorso, Exfoliation materials by wet-jet milling techniques, P. number: W. Exfoliation materials by wet-jet milling techniques, WO2017/089987 A1, 2017 Search PubMed.
- F. Bonaccorao, A. Bortolotta, J. N. Coleman and C. Backes, Adv. Mater., 2016, 28, 6136–6166 CrossRef PubMed.
- F. Bonaccorso, A. Lombardo, T. Hasan, Z. Sun, L. Colombo and A. C. Ferrari, Mater. Today, 2012, 15, 564–589 CrossRef CAS.
- K. R. Paton, E. Varrla, C. Backes, R. J. Smith, U. Khan, A. O’Neill, C. Boland, M. Lotya, O. M. Istrate, P. King, T. Higgins, S. Barwich, P. May, P. Puczkarski, I. Ahmed, M. Moebius, H. Pettersson, E. Long, J. Coelho, S. E. O’Brien, E. K. McGuire, B. M. Sanchez, G. S. Duesberg, N. McEvoy, T. J. Pennycook, C. Downing, A. Crossley, V. Nicolosi and J. N. Coleman, Nat. Mater., 2014, 13, 624 CrossRef CAS PubMed.
- E. Varrla, K. R. Paton, C. Backes, A. Harvey, R. J. Smith, J. McCauley and J. N. Coleman, Nanoscale, 2014, 6, 11810–11819 RSC.
- W. Zhao, M. Fang, F. Wu, H. Wu, L. Wang and G. Chen, J. Mater. Chem., 2010, 20, 5817–5819 RSC.
- U. Khan, H. Porwal, A. O’Neill, K. Nawaz, P. May and J. N. Coleman, Langmuir, 2011, 27, 9077–9082 CrossRef CAS PubMed.
- M. Lotya, P. J. King, U. Khan, S. De and J. N. Coleman, ACS Nano, 2010, 4, 3155–3162 CrossRef CAS PubMed.
- P. G. Karagiannidis, S. A. Hodge, L. Lombardi, F. Tomarchio, N. Decorde, S. Milana, I. Goykhman, Y. Su, S. V. Mesite, D. N. Johnstone, R. K. Leary, P. A. Midgley, N. M. Pugno, F. Torrisi and A. C. Ferrari, ACS Nano, 2017, 11, 2742–2755 CrossRef CAS PubMed.
- V. Nicolosi, M. Chhowalla, M. G. Kanatzidis, M. S. Strano and J. N. Coleman, Science, 2013, 340, 1226419 CrossRef.
- K. Kouroupis-Agalou, A. Liscio, E. Treossi, L. Ortolani, V. Morandi, N. M. Pugno and V. Palermo, Nanoscale, 2014, 6, 5926–5933 RSC.
- A. C. Ferrari, J. C. Meyer, V. Scardaci, C. Casiraghi, M. Lazzeri, F. Mauri, S. Piscanec, D. Jiang, K. S. Novoselov, S. Roth and A. K. Geim, Phys. Rev. Lett., 2006, 97, 187401 CrossRef CAS PubMed.
- A. C. Ferrari and D. M. Basko, Nat. Nanotechnol., 2013, 8, 235 CrossRef CAS PubMed.
- L. Najafi, S. Bellani, B. Martín-García, R. Oropesa-Nuñez, A. E. Del Rio Castillo, M. Prato, I. Moreels and F. Bonaccorso, Chem. Mater., 2017, 29, 5782–5786 CrossRef CAS.
- S. Bellani, L. Najafi, B. Martín-García, A. Ansaldo, A. E. Del Rio Castillo, M. Prato, I. Moreels and F. Bonaccorso, J. Phys. Chem. C, 2017, 121, 21887–21903 CrossRef CAS.
- M. S. Dresselhaus, A. Jorio, M. Hofmann, G. Dresselhaus and R. Saito, Nano Lett., 2010, 10, 751–758 CrossRef CAS PubMed.
- J.-B. Wu, M.-L. Lin, X. Cong, H.-N. Liu and P.-H. Tan, Chem. Soc. Rev., 2018, 47, 1822–1873 RSC.
- F. Bonaccorso, P.-H. Tan and A. C. Ferrari, ACS Nano, 2013, 7, 1838–1844 CrossRef CAS PubMed.
- L. Yang, J. Deslippe, C.-H. Park, M. L. Cohen and S. G. Louie, Phys. Rev. Lett., 2009, 103, 186802 CrossRef PubMed.
- A. C. Ferrari and J. Robertson, Phys. Rev. B: Condens. Matter Mater. Phys., 2000, 61, 14095–14107 CrossRef CAS.
- A. C. Ferrari and J. Robertson, Phys. Rev. B: Condens. Matter Mater. Phys., 2001, 64, 75414 CrossRef.
- C. Y. Su, Y. Xu, W. Zhang, J. Zhao, X. Tang, C. H. Tsai and L. J. Li, Chem. Mater., 2009, 21, 5674–5680 CrossRef CAS.
- C. Thomsen and S. Reich, Phys. Rev. Lett., 2000, 85, 5214 CrossRef CAS PubMed.
- M. M. Lucchese, F. Stavale, E. H. M. Ferreira, C. Vilani, M. V. O. Moutinho, R. B. Capaz, C. A. Achete and A. Jorio, Carbon, 2010, 48, 1592–1597 CrossRef CAS.
- A. Eckmann, A. Felten, A. Mishchenko, L. Britnell, R. Krupke, K. S. Novoselov and C. Casiraghi, Nano Lett., 2012, 12, 3925–3930 CrossRef CAS PubMed.
- A. C. Ferrari, Solid State Commun., 2007, 143, 47–57 CrossRef CAS.
- M. Lotya, Y. Hernandez, P. J. King, R. J. Smith, V. Nicolosi, L. S. Karlsson, F. M. Blighe, S. De, Z. Wang, I. T. McGovern, G. S. Duesberg and J. N. Coleman, J. Am. Chem. Soc., 2009, 131, 3611–3620 CrossRef CAS PubMed.
- L. G. Cançado, A. Jorio, E. H. M. Ferreira, F. Stavale, C. A. Achete, R. B. Capaz, M. V. O. Moutinho, A. Lombardo, T. S. Kulmala and A. C. Ferrari, Nano Lett., 2011, 11, 3190–3196 CrossRef PubMed.
- M. V. Bracamonte, G. I. Lacconi, S. E. Urreta and L. E. F. Foa Torres, J. Phys. Chem. C, 2014, 118, 15455–15459 CrossRef CAS.
- J. N. Coleman, Acc. Chem. Res., 2013, 46, 14–22 CrossRef CAS PubMed.
- M. S. Dresselhaus, G. Dresselhaus and M. Hofmann, Philos. Trans. R. Soc., A, 2008, 366, 231–236 CrossRef CAS PubMed.
- A. Das, B. Chakraborty and A. K. Sood, Bull. Mater. Sci., 2008, 31, 579–584 CrossRef CAS.
- D. Berman, A. Erdemir, A. V. Zinovev and A. V. Sumant, Diamond Relat. Mater., 2015, 54, 91–96 CrossRef CAS.
- J. Chen, I. Ratera, J. Y. Park and M. Salmeron, Phys. Rev. Lett., 2006, 96, 236102 CrossRef PubMed.
- Y. Peng, Z. Wang and K. Zou, Langmuir, 2015, 31, 7782–7791 CrossRef CAS PubMed.
- D. Akinwande, C. J. Brennan, J. S. Bunch, P. Egberts, J. R. Felts, H. Gao, R. Huang, J.-S. Kim, T. Li, Y. Li, K. M. Liechti, N. Lu, H. S. Park, E. J. Reed, P. Wang, B. I. Yakobson, T. Zhang, Y.-W. Zhang, Y. Zhou and Y. Zhu, Extreme Mech. Lett., 2017, 13, 42–77 CrossRef.
- T. Filleter, J. L. McChesney, A. Bostwick, E. Rotenberg, K. V. Emtsev, T. Seyller, K. Horn and R. Bennewitz, Phys. Rev. Lett., 2009, 102, 86102 CrossRef CAS PubMed.
- C. Lee, X. Wei, Q. Li, R. Carpick, J. W. Kysar and J. Hone, Phys. Status Solidi, 2009, 246, 2562–2567 CrossRef CAS.
- C. Lee, Q. Li, W. Kalb, X.-Z. Liu, H. Berger, R. W. Carpick and J. Hone, Science, 2010, 328, 76–80 CrossRef CAS PubMed.
- D. Berman, A. Erdemir and A. V. Sumant, Carbon, 2013, 54, 454–459 CrossRef CAS.
- H. Lee, N. Lee, Y. Seo, J. Eom and S. Lee, Nanotechnology, 2009, 20, 325701 CrossRef PubMed.
- D. Berman, A. Erdemir and A. V. Sumant, Mater. Today, 2014, 17, 31–42 CrossRef CAS.
- L. Y. Lin, D. E. Kim, W. K. Kim and S. C. Jun, Surf. Coat. Technol., 2011, 205, 4864–4869 CrossRef CAS.
- B. J. Robinson, N. D. Kay and O. V. Kolosov, Langmuir, 2013, 29, 7735–7742 CrossRef CAS PubMed.
- A. Akbari, S. E. Meragawi, S. T. Martin, B. Corry, E. Shamsaei, C. D. Easton, D. Bhattacharyya and M. Majumder, ACS Appl. Mater. Interfaces, 2018, 10, 2067–2074 CrossRef CAS PubMed.
-
P. Simon, T. Brousse and F. Favier, Supercapacitors Based on Carbon or Pseudocapacitive Materials, John Wiley & Sons, New Jersey, United States, 2017 Search PubMed.
-
http://www.mtixtl.com/HighSurfaceActiveCarbonForSuper-CapacitorElectrode200g/Bag-E.aspx, data accesed on 01/09/2018.
- R. W. Carpick and M. Salmeron, Chem. Rev., 1997, 97, 1163–1194 CrossRef CAS PubMed.
- R. Buzio, A. Gerbi, S. Uttiya, C. Bernini, A. E. Del Rio Castillo, F. Palazon, A. S. Siri, V. Pellegrini, L. Pellegrino and F. Bonaccorso, Nanoscale, 2017, 9, 7612–7624 RSC.
- U. D. Schwarz, P. Köster and R. Wiesendanger, Rev. Sci. Instrum., 1996, 67, 2560–2567 CrossRef CAS.
- M. A. Lantz, S. J. O’Shea, A. C. F. Hoole and M. E. Welland, Appl. Phys. Lett., 1997, 70, 970–972 CrossRef CAS.
- R. W. Carpick, D. F. Ogletree and M. Salmeron, Appl. Phys. Lett., 1997, 70, 1548–1550 CrossRef CAS.
- W. S. Choi, J. Heo, I. Chung and B. Hong, Thin Solid Films, 2005, 475, 287–290 CrossRef CAS.
- L.-Y. Lin, D.-E. Kim, W.-K. Kim and S.-C. Jun, Surf. Coat. Technol., 2011, 205, 4864–4869 CrossRef CAS.
- M. Ricci, W. Trewby, C. Cafolla and K. Voïtchovsky, Sci. Rep., 2017, 7, 43234 CrossRef CAS PubMed.
- J. B. Pethica and W. C. Oliver, Phys. Scr., 1987, 61 CrossRef CAS.
- E. Tocha, H. Schönherr and G. J. Vancso, Langmuir, 2006, 22, 2340–2350 CrossRef CAS PubMed.
- Z. Sanliang and P. Ning, Adv. Energy Mater., 2014, 5, 1401401 Search PubMed.
- F. P. Bowden, D. Tabor and F. Palmer, Am. J. Phys., 1951, 19, 428 CrossRef.
-
V. L. Popov, Contact mechanics and friction: Physical principles and applications, Springer-Verlag, Berlin Heidelberg, Germany, 2010 Search PubMed.
- V. L. Popov, J. Starcevic and A. E. Filippov, Tribol. Lett., 2010, 39, 25–30 CrossRef CAS.
- O. Ben-David and J. Fineberg, Phys. Rev. Lett., 2011, 106, 254301 CrossRef PubMed.
- C. H. Scholz, Nature, 1998, 391, 37 CrossRef CAS.
- P. Berthoud, T. Baumberger, C. G’Sell and J.-M. Hiver, Phys. Rev. B: Condens. Matter Mater. Phys., 1999, 59, 14313–14327 CrossRef CAS.
- O. Ben-David, S. M. Rubinstein and J. Fineberg, Nature, 2010, 463, 76 CrossRef CAS PubMed.
- U. Raviv, P. Laurat and J. Klein, Nature, 2001, 413, 51 CrossRef CAS PubMed.
- J. P. Gao, W. D. Luedtke and U. Landman, Tribol. Lett., 2000, 9, 3 CrossRef CAS.
- S. Granick, Science, 1991, 253, 1374–1379 CrossRef CAS PubMed.
- J. Klein and E. Kumacheva, J. Chem. Phys., 1998, 108, 6996 CrossRef CAS.
- C. L. Rhykerd, M. Schoen, D. J. Diestler and J. H. Cushman, Nature, 1987, 330, 461 CrossRef CAS.
- J. N. Israelachvili, P. M. McGuiggan and A. M. Homola, Science, 1988, 240, 189–191 CrossRef CAS PubMed.
- P. A. Thompson, M. O. Robbins and G. S. Grest, Isr. J. Chem., 1995, 35, 93–106 CrossRef CAS.
- J. Gao, W. D. Luedtke and U. Landman, Phys. Rev. Lett., 1997, 79, 705 CrossRef CAS.
- D. Chandler, J. D. Weeks and H. C. Andersen, Science, 1983, 220, 787–794 CrossRef CAS PubMed.
- A. Tkachenko and Y. Rabin, Langmuir, 1997, 13, 7146–7150 CrossRef CAS.
- D. Marchetto, C. Held, F. Hausen, F. Wählisch, M. Dienwiebel and R. Bennewitz, Tribol. Lett., 2012, 48, 77–82 CrossRef CAS.
- L. Jinjin, G. Tianyang and L. Jianbin, Adv. Sci., 2018, 5, 1700616 CrossRef PubMed.
- Z. Deng, A. Smolyanitsky, Q. Li, X.-Q. Feng and R. J. Cannara, Nat. Mater., 2012, 11, 1032 CrossRef CAS PubMed.
- J. Ruan and B. Bhushan, J. Appl. Phys., 1994, 76, 8117–8120 CrossRef CAS.
- L.-F. Wang, T.-B. Ma, Y.-Z. Hu and H. Wang, Phys. Rev. B: Condens. Matter Mater. Phys., 2012, 86, 125436 CrossRef.
- D. Berman, A. Erdemir and A. V. Sumant, Carbon, 2013, 59, 167–175 CrossRef CAS.
- X. Zeng, Y. Peng, H. Lang and L. Liu, Sci. Rep., 2017, 7, 41891 CrossRef CAS PubMed.
- J. Zhang, W. Lu, J. M. Tour and J. Lou, Appl. Phys. Lett., 2012, 101, 123104 CrossRef.
- S. Pei and H.-M. Cheng, Carbon, 2012, 50, 3210–3228 CrossRef CAS.
- O. C. Compton and S. T. Nguyen, Small, 2010, 6, 711–723 CrossRef CAS PubMed.
- S. Brunauer, P. H. Emmett and E. Teller, J. Am. Chem. Soc., 1938, 60, 309–319 CrossRef CAS.
- K. S. Walton and R. Q. Snurr, J. Am. Chem. Soc., 2007, 129, 8552–8556 CrossRef CAS PubMed.
- G. Fagerlund, Mater. Constr., 1973, 6, 239–245 CrossRef CAS.
- S. ang, D. Minami and K. Kaneko, Microporous Mesoporous Mater., 2015, 209, 72–78 CrossRef.
- T. Matthias, K. Kaneko, A. V. Neimark, J. P. Olivier, F. Rodriguez-Reinoso, J. Rouquerol and K. S. W. Sing, Pure Appl. Chem., 2015, 87, 1051–1069 Search PubMed.
- C. Greenhow and W. V. Smith, J. Chem. Phys., 1951, 19, 1298–1300 CrossRef CAS.
- L. E. Drain, Trans. Faraday Soc., 1953, 49, 650–654 RSC.
- I. M. K. Ismail, Langmuir, 1992, 8, 360–365 CrossRef CAS.
- K. S. W. Sing, Carbon, 1994, 32, 1311–1317 CrossRef CAS.
- P. I. Ravikovitch, A. Vishnyakov, R. Russo and A. V. Neimark, Langmuir, 2000, 16, 2311–2320 CrossRef CAS.
- P. I. Ravikovitch and A. V. Neimark, Langmuir, 2006, 22, 11171–11179 CrossRef CAS PubMed.
- C. X. Guo and C. M. Li, Energy Environ. Sci., 2011, 4, 4504–4507 RSC.
- C. Zheng, X. Zhou, H. Cao, G. Wang and Z. Liu, J. Power Sources, 2014, 258, 290–296 CrossRef CAS.
- C. Phillips, A. Al-Ahmadi, S.-J. Potts, T. Claypole and D. Deganello, J. Mater. Sci., 2017, 52, 9520–9530 CrossRef CAS.
- https://www.tedpella.com/semmisc_html/sempaint.htm#anchor16050, data accesed on01/09/2018.
- https://dyenamo.se/dyenamo_electrode_pastes.php, data accessed on 01/09/2018.
- Z. Yang, J. Ren, Z. Zhang, X. Chen, G. Guan, L. Qiu, Y. Zhang and H. Peng, Chem. Rev., 2015, 115, 5159–5223 CrossRef CAS PubMed.
- S. Kondrat, C. R. Pérez, V. Presser, Y. Gogotsi and A. A. Kornyshev, Energy Environ. Sci., 2012, 5, 6474–6479 RSC.
- N. Devillers, S. Jemei, M.-C. Péra, D. Bienaimé and F. Gustin, J. Power Sources, 2014, 246, 596–608 CrossRef CAS.
- R. Kötz and M. Carlen, Electrochim. Acta, 2000, 45, 2483–2498 CrossRef.
- Y.-H. Lee, K.-H. Chang and C.-C. Hu, J. Power Sources, 2013, 227, 300–308 CrossRef CAS.
- Z. Lin, Y. Liu, Y. Yao, O. J. Hildreth, Z. Li, K. Moon and C. Wong, J. Phys. Chem. C, 2011, 115, 7120–7125 CrossRef CAS.
- B. Zhao, P. Liu, Y. Jiang, D. Pan, H. Tao, J. Song, T. Fang and W. Xu, J. Power Sources, 2012, 198, 423–427 CrossRef CAS.
- R. Raccichini, A. Varzi, S. Passerini and B. Scrosati, Nat. Mater., 2014, 14, 271 CrossRef PubMed.
- F. Yan, L. Bin, J. Yuying, L. Xianglong, W. Bin, S. Qi, K. Feiyu and Z. Linjie, Adv. Mater., 2012, 24, 6348–6355 CrossRef PubMed.
- T. Devarajan, S. Higashiya, C. Dangler, M. Rane-Fondacaro, J. Snyder and P. Haldar, Electrochem. Commun., 2009, 11, 680–683 CrossRef CAS.
- S. Pohlmann, C. Ramirez-Castro and A. Balducci, J. Electrochem. Soc., 2015, 162, A5020–A5030 CrossRef CAS.
- S. Fletcher, V. J. Black and I. Kirkpatrick, J. Solid State Electrochem., 2014, 18, 1377–1387 CrossRef CAS.
- S. Fletcher, I. Kirkpatrick, R. Dring, R. Puttock, R. Thring and S. Howroyd, J. Power Sources, 2017, 345, 247–253 CrossRef CAS.
- X. Liu, X. Dai, G. Wei, Y. Xi, M. Pang, V. Izotov, N. Klyui, D. Havrykov, Y. Ji, Q. Guo and W. Han, Sci. Rep., 2017, 7, 45934 CrossRef CAS PubMed.
- S. Yoon, J. H. Jang, B. H. Ka and S. M. Oh, Electrochim. Acta, 2005, 50, 2255–2262 CrossRef CAS.
- Y. Hernandez, V. Nicolosi, M. Lotya, F. M. Blighe, Z. Sun, S. De, I. T. McGovern, B. Holland, M. Byrne, Y. K. Gun’Ko, J. J. Boland, P. Niraj, G. Duesberg, S. Krishnamurthy, R. Goodhue, J. Hutchison, V. Scardaci, A. C. Ferrari and J. N. Coleman, Nat. Nanotechnol., 2008, 3, 563 CrossRef CAS PubMed.
- A. Capasso, A. E. Del Rio Castillo, H. Sun, A. Ansaldo, V. Pellegrini and F. Bonaccorso, Solid State Commun., 2015, 224, 53–63 CrossRef CAS.
- J. N. Coleman, Adv. Funct. Mater., 2009, 19, 3680–3695 CrossRef CAS.
-
C. M. Hansen, Hansen Solubility Parameters: A User's Handbook, CRC Press, New York, United States, 2013 Search PubMed.
- C. A. Schneider, W. S. Rasband and K. W. Eliceiri, Nat. Methods, 2012, 9, 671 CrossRef CAS PubMed.
- E. Seifert, J. Chem. Inf. Model., 2014, 54, 1552 CrossRef CAS PubMed.
- F. M. Smits, Bell Syst. Tech. J., 2018, 37, 711–718 CrossRef.
Footnote |
† Electronic supplementary information (ESI) available. See DOI: 10.1039/c8nh00446c |
|
This journal is © The Royal Society of Chemistry 2019 |