DOI:
10.1039/D2TA02268K
(Paper)
J. Mater. Chem. A, 2022,
10, 20111-20120
Synthesis, crystal structure, and properties of stoichiometric hard tungsten tetraboride, WB4†
Received
21st March 2022
, Accepted 9th August 2022
First published on 30th August 2022
Abstract
Tungsten tetraboride has been known so far as a non-stoichiometric compound with a variable composition (e.g. WB4−x, WB4+x). Its mechanical properties could exceed those of hard tungsten carbide, which is widely used nowadays in science and technology. The existence of stoichiometric WB4 has not been proven yet, and its structure and crystal chemistry remain debatable to date. Here we report the synthesis of single crystals of the stoichiometric WB4 phase under high-pressure high-temperature conditions. The crystal structure of WB4 was determined using synchrotron single-crystal X-ray diffraction. In situ high-pressure compressibility measurements show that the bulk modulus of WB4 is 238.6(2) GPa for B′ = 5.6(0). Measurements of mechanical properties of bulk polycrystalline sub-millimeter size samples under ambient conditions reveal a hardness of ∼36 GPa, confirming that the material falls in the category of superhard materials.
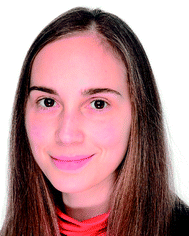 Elena Bykova | Elena Bykova received her PhD from Bayerisches Geoinstitut, University of Bayreuth, Germany. She worked as a postdoctoral researcher at the Extreme Conditions Beamline at the PETRA III synchrotron (Germany) and at Earth & Planets Laboratory, Carnegie Institution for Science (USA). Her research interests are mainly focused on developing methodologies of single-crystal X-ray diffraction experiments at high pressures and temperatures, in order to study materials related to mineral physics and materials sciences. In 2018, in recognition of her outstanding achievements in the field of ultra-high-pressure crystallography, she received the Max von Laue Prize from the German Crystallographic Society. |
Introduction
Inexpensive hard and superhard (with a Vickers hardness of around 40 GPa and above) materials are in much demand for various industrial applications. Novel carbides,1 nitrides,2–8 borides,9–23 and other compounds of transition metals,24,25 which can potentially combine high hardness and promising optical, electronic, and other properties, are the focus of extensive investigations.26–28 Nowadays, one of the most widely used hard materials for commercial applications is tungsten carbide, WC. This fact motivates investigations of other potentially hard tungsten compounds, primarily, borides.29–37 Among them, a phase referred to as “WB4”,38–49 and its several derivatives (e.g., W1−xB3, WB4−x, WB4+x, WB4.2, and WB5−x)50–56 were identified as highly promising candidates, whose mechanical characteristics (e.g. theoretical and experimental values of HV vary from 30 to 45 GPa (ref. 26,44,45,47,49 and 54)) could exceed those of WC (Vickers hardness HV∼ 18–20 GPa (ref. 57)). However, the crystal chemistry of the “WB4” phase has remained debatable for decades, and thus, often, it is not clear what material is being considered in a particular publication.
Based on high-quality powder diffraction data, several probable structural models for the “WB4” phase were suggested (hexagonal unit cell, a ∼5.20 Å, c ∼6.34 Å, Fig. 1a–d).38,39,42–45,47,58 In contrast, theoretical calculations suggested an alternative crystal structure for “WB4” (sp.gr. P63/mmc, a ∼2.93–2.96 Å, c ∼10.9–11.0 Å, Fig. 1f),31,36,37,48 but it has not been experimentally observed to date.
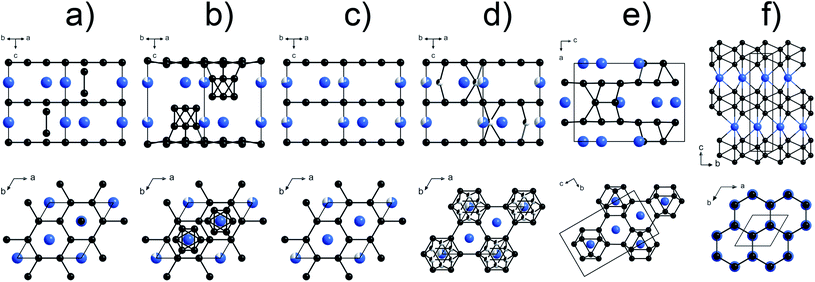 |
| Fig. 1 Various models of the crystal structure proposed for WB4: (a) the crystal structure of WB4 by Romans and Krug;39 (b) W1.83B9 by Nowotny et al.;58 (c) W1−xB3 following Lundström and Rosenberg59 and Zeiringer et al.;42 (d) WB4.2 by Lech et al.;47 (e) WB5 by Kvashnin et al.;34,54 (f) theoretically predicted stoichiometric WB4.31,36,37,48 The blue spheres represent tungsten atoms, the black spheres are boron atoms, and the partially filled spheres indicate defect B or W sites. | |
Recently, one more boron-rich phase, WB5 was first predicted (sp. gr. Pmmn, a = 6.369, b = 5.199, c = 8.993 Å, Fig. 1 e)34 and then synthesized in the form of two boron-deficient phases, WB4.18 and WB4.86.54 Crystal structures of these WB5, WB4.18 and WB4.86 phases were found to be very similar to those reported earlier for the seemingly “WB4” phase and its derivatives.38,39,42 This finding may suggest that: (i) the stoichiometric WB5 phase is actually the “parent” for the family of boron-deficient phases WB5−x (0 ≤ x < 1.6) reported to date; (ii) a genuine stoichiometric WB4 phase for which a different crystal structure was predicted31,36,37,48 probably has not been synthesized yet, and previous claims of its synthesis were likely due to confusion with one of the WB5−x phases.54
In this work, we report the first synthesis of single crystals of the so far “elusive” stoichiometric WB4 phase and an accurate determination of its crystal structure by single-crystal X-ray diffraction. In order to synthesize the phase, we first performed a fast screening of chemical reactivity of the W–B system up to 30 GPa and then scaled-up the amount of the WB4 phase using a multi-anvil apparatus. We find that a crystal structure of the genuine WB4 phase indeed differs from previous experimentally-determined models for the seemingly “WB4” phase,26,38,39,42,44,45,47,49,59 while, it is well consistent with the one predicted for WB4.31,36,37,48 Examinations of mechanical properties of the single- and polycrystalline samples of WB4 confirm the hard nature of this phase.
Experimental procedures
Synthesis of WB4 single crystals in diamond anvil cells
For high-pressure high-temperature experiments, we have used a BX90 type DAC60 equipped with Boehler-Almax diamonds with a 200 μm culet size (60° opening angle). In between diamonds, we placed a rhenium gasket pre-indented to 25 μm thickness with a hole of about 100 μm in diameter that served as a pressure chamber. Inside the pressure chamber, we placed a thin tungsten plate sandwiched between pre-compressed amorphous boron powder together with a small ruby sphere (for pressure estimation). Neon was used both as a pressure transmitting medium and as a pressure standard.61
The laser-heating coupled with XRD measurements were conducted at the 13-IDD beamline at the Advanced Photon Source, Argonne National Laboratory (Pilatus CdTe 1M detector, X-ray wavelength λ = 0.2952 Å, focal spot ∼ 3 μm).62 The sample-to-detector distance, coordinates of the beam center, tilt angle and tilt plane rotation angle of the detector images were calibrated using NIST LaB6. Lasers were focused down to a flat top of about 10 μm in diameter. The sample temperature was measured by the standard spectroradiometry method63 using an Acton SP-2360 imaging spectrograph coupled with a PI-MAX3 1024i ICCD camera from Princeton Instruments. Pressure values and maximum heating temperatures are given in Table S1.†
After each laser heating cycle, a detailed X-ray diffraction map was collected around the heated spot in order to determine the phase composition of the reaction product. At each pressure point, single-crystal XRD images were collected in different spots with the decent quality of the diffraction data (up to six data collection procedures) in order to determine phase composition of the reaction product. The single-crystal XRD images were recorded while rotating the sample about a single ω-axis from −30 to +30° in small steps of 0.5°.
The DIOPTAS software64 was used for preliminary phase analysis and calculation of pressures from the positions of the XRD lines of Ne. Powder XRD patterns were analyzed using a JANA2020, where the unit cell parameters of the phases in the multi-phase mixtures were refined from the full-profile Le Bail fit.65
Synthesis of WB4 single crystals in multi-anvil assemblies
The WB4 samples were synthesized under high-pressure high-temperature (HP-HT) conditions using multi-anvil presses at the Bayerisches Geoinstitut (BGI).66 Typically, the samples were synthesized at 20 GPa under heating at 1800–2000 °C for several hours (Table S1†). We used standard multi-anvil assemblies with LaCrO3-heaters and W3Re/W25Re thermocouples for temperature determination. Sample capsules were prepared from 50 μm thick tungsten foil (99.95% purity, HMW Hauner GmbH & Co. KG company). We followed several synthetic routes, including mixing of fine powders of tungsten and boron and mixing of tungsten foil with boron powder. The latter allowed fabrication of microscopic single crystals at the border of the tungsten foil; whereas, the former could fabricate relatively large polycrystals. Besides the above tungsten foil, we used tungsten powder (99.9% purity, Chempur company) for mixing with boron powder. In preliminary testing syntheses, we used a powder of amorphous boron (95–97% purity, Chempur company), while for synthesis of chemically pure samples, we ground into powder the β-boron crystals (99.5% purity, Chempur company). Structural and chemical analyses of the samples were performed by X-ray diffraction using a three-circle Bruker diffractometer (SMART APEX CCD detector, Incoatec IμS 3.0 microfocus X-ray source, Ag-Kα radiation), and by scanning electron microscopy (SEM) using a LEO-1530 instrument, respectively. Other details and procedures were similar to those described before.67,68
Measurements of single-crystal compressibility
A single crystal of WB4 (black, plate-shape, 10 × 10 × 5 μm3) pre-selected on an in-house single-crystal diffractometer was loaded in a membrane-driven BX90 type DAC equipped with Boehler-Almax diamonds with a 250 μm culet size (60° opening angle, Re gasket). A small ruby sphere and a Ne pressure-transmitting medium were used for pressure determination. The WB4 crystal in the diamond anvil cell was compressed to about 54 GPa with a pressure step of 1–4 GPa. The single-crystal XRD pattern of the sample was measured at each pressure point (narrow ω-scanning from −30 to +30°, 0.5° steps).
The XRD experiments were conducted at the Extreme Conditions Beamline P02.2 at PETRA III, Hamburg, Germany (PerkinElmer XRD1621 flat panel detector, λ = 0.2900 Å, KB-mirror focusing, focal spot ∼ 3 μm). The sample-to-detector distance, coordinates of the beam center, tilt angle and tilt plane rotation angle of the detector images were calibrated using CeO2.
Single-crystal X-ray diffraction
The single-crystal XRD data (the unit cell determination, integration of the reflection intensities, and empirical absorption correction) were processed using the CrysAlisPro software.69 In the cases of multi-phase and multi-grain samples (which, for instance, are being formed after laser heating), we manually searched for peaks belonging to the most intense grains using the reciprocal space Ewald explorer implemented in CrysAlisPro. After the unit cell indexing, the unit cell and orientation matrix obtained were used for further data integration.
A single crystal of orthoenstatite ((Mg1.93,Fe0.06)(Si1.93,Al0.06)O6, Pbca, a = 18.2391(3), b = 8.8117(2), and c = 5.18320(10) Å) was used to calibrate the instrument model of CrysAlisPro (the sample-to-detector distance, the detector's origin, offsets of the goniometer angles, rotation of the X-ray beam and the detector around the instrument axis).
The crystal structures were determined by using SHELXT,70 a structure solution program that uses the method of intrinsic phasing. The crystal structure was refined against F2 on all data using full-matrix least-squares with the SHELXL71 software. SHELXT and SHELXL programs were implemented in the Olex2 software package.72 Since the body of the diamond anvil cell shadows more than 50% of the diffraction reflections, the reflection datasets were incomplete. In order to improve the data/parameter ratio, only atomic thermal parameters of tungsten were refined in anisotropic approximation. Another refinement strategy where boron atoms have been also refined anisotropically with a RIGU rigid-bond restraint gave no significant improvements in R1/wR2 values but rather brought a problem with elongated/negative ADPs for most B atoms; therefore, it was not applied.
A detailed summary of the crystal structure refinements together with the unit cell parameters, atomic coordinates and isotropic displacement parameters is given in Table S2.† The X-ray crystallographic coordinates have been deposited at the Inorganic Crystal Structure Database (ICSD), and the deposition numbers are given in Table S2.†.
Measurements of the hardness and Young's modulus
Nanoindentation was performed using a Nanoindenter G200 platform (KLA, Milpitas, CA, USA), equipped with a Berkovich diamond tip (Synton MDP, Nidau, Switzerland) and by the continuous stiffness method (CSM).73 The indents were separated by a distance of at least 10 μm, so that their plastic zones did not overlap.74 The indentations were performed on different areas of the sample, which respectively appeared homogeneous and heterogeneous in the optical micrographs as can be seen in Fig. S1,† and are assumed to be single crystalline and polycrystalline, and the size of the single crystalline areas could reach 30 microns. All in all, 20 measurements were performed. For each test, loading was performed at a constant strain-rate of 0.1 s−1 up to a maximal indentation depth of at least 900 nm. A 2 nm large CSM oscillation superimposed at 41 Hz on the loading signal was used to continuously measure the hardness and Young's modulus with increasing indentation depth. The acquired data were evaluated using the Oliver–Pharr method.75,76 For this purpose, the diamond punch geometry was calibrated in fused silica, and the machine frame stiffness correction was refined so as to obtain a constant stiffness-squared-over-load ratio during indentation on the samples. The mechanical properties were averaged over the indentation depth range 700–900 nm in order to minimize tip blunting effects at shallow depth. The conversion of the reduced moduli to Young's moduli was performed assuming a Poisson's ratio of 0.2 for WB4.31 The conversion from the nanoindentation hardness HIT to the Vickers hardness HV was carried out with a factor of 0.9269.77
Results and discussion
Synthesis of single crystals and polycrystals
Single crystals and polycrystals of WB4 were synthesized under high-pressure high-temperature (HP-HT) conditions using both large-volume multi-anvil presses at BGI and laser-heated diamond anvil cells (DACs). In the experiments using the DAC, a WB4 phase (sp.gr. P63/mmc, a = 2.8481(3) Å, c = 10.752(2) Å) was first detected at 30.3(5) GPa after a laser heating of up to 2300(100) K. As can be seen in Fig. 2, single crystals of WB4 are formed together with a W2B phase (sp.gr. I4/mcm, a = 5.4257(10) Å, c = 4.6189(12) Å), WB (sp.gr. I41/amd, a = 3.0325(4) Å, c = 16.558(3) Å) and a phase with a R-centered hexagonal unit cell (a = 2.9143(5)Å; c = 20.463(5) Å). The latter lattice parameters belong to a tungsten boride for which two chemical compositions have been proposed, namely, W2B5 (ref. 78) and W2B4 (ref. 79 and 80) (below we use W2B5 notation). Such a wide variety of the W
:
B ratios can be explained by a design of our DAC experiments. In the reaction chamber, tungsten foil was embedded between two pieces of pre-compressed boron powder, which results in inhomogeneous distribution of the reactants across the reaction chamber and their insufficient mixing. More boron-rich borides likely formed in the spots with local excess of boron, while borides with a larger W
:
B ratio formed in the boron-poor regions. We cannot exclude that thermal gradients typical of the laser heating (at least + −100 K) could lead to chemical variety of the resulting products.
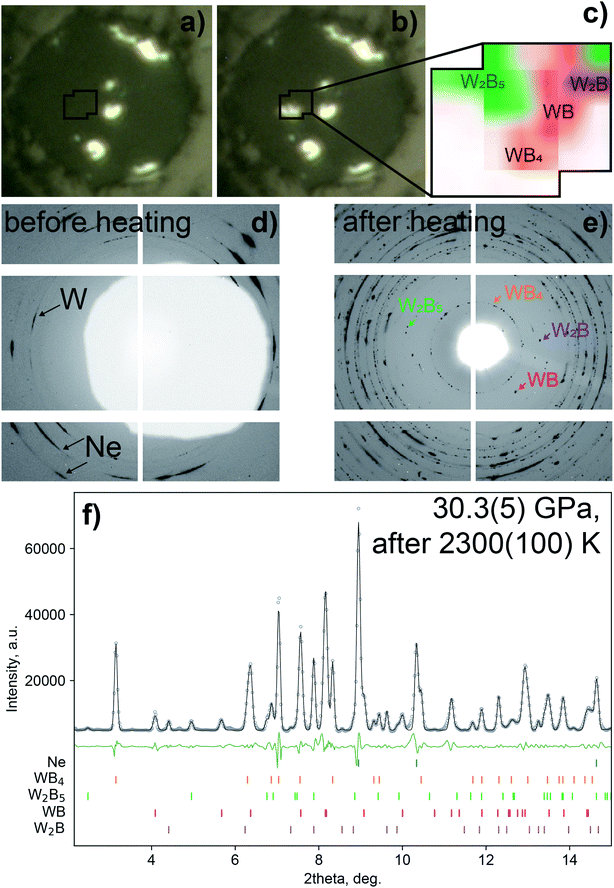 |
| Fig. 2 Synthesis of tungsten borides at high pressure. Microscopic images of the pressure chamber before (a) and after (b) the laser heating at 30.3(5) GPa, and the inset (c) shows phase distribution around the heated area obtained by X-ray diffraction mapping of the heated area. By using a combination of powder and single-crystal XRD methods, four borides of tungsten were identified in the pressure chamber, namely, WB4, W2B5, WB and W2B. Corresponding fragments of 2D diffraction images in the low-2θ region show diffraction peaks before (d) and after a laser heating (e). A white area at (d) is a shadow from a beam stop to block scattering from X-ray transparent glassy carbon mirrors used for on-axis laser heating. The lower image (f) shows the powder X-ray diffraction data collected at 30.3(5) GPa after a laser heating of up to 2300(100) K (λ = 0.2952 Å): the experimental data are shown by grey circles (the background was subtracted), a Le Bail fit – by the black solid line, and a difference curve – by the green solid line; the ticks show predicted positions of the diffraction peaks. The Le Bail fit showing profiles of the individual phases is given in supplementary Fig. S2.† | |
In the multi-anvil experiments, tungsten tetraboride (as well as a byproduct, WB2) can be successfully synthesized at 20 GPa and 2073 K. It should be noted that no WB5 or any of its derivatives have been found among the reaction products neither in the multi-anvil nor in DAC experiments.
Crystal structure and comparison with previous results
From the synthesis products, we selected high-quality single crystals of WB4 and determined their crystal structure by single-crystal X-ray diffraction (Fig. S3†). In the crystal structure of tungsten tetraboride (Fig. 3a and b), the metal atoms form the flat hexagonal close packed layers perpendicular to the c-axis that follow the ABABA… sequence. Covalently-bonded boron networks are located between layers of tungsten atoms. The networks consist of two puckered layers connected through short B–B bonds (notated as d3 in Fig. 3a). Such layers are formed by condensed six-membered rings of boron in a chair-like conformation, which one can find, for example, in grey arsenic (A7-type) and in a high-pressure modification of black phosphorus (Fig. 3c).81 The crystal structure of WB4 demonstrates a close similarity to one of hard ReB2, which has the same arrangement of metal atoms, while its boron network is formed only by a one puckered layer.82 The single-crystal XRD data show that tungsten and boron atoms fully occupy their positions, leaving no vacancies. The crystal structure we experimentally determined fully agrees with theoretical predictions.31,36,37,48
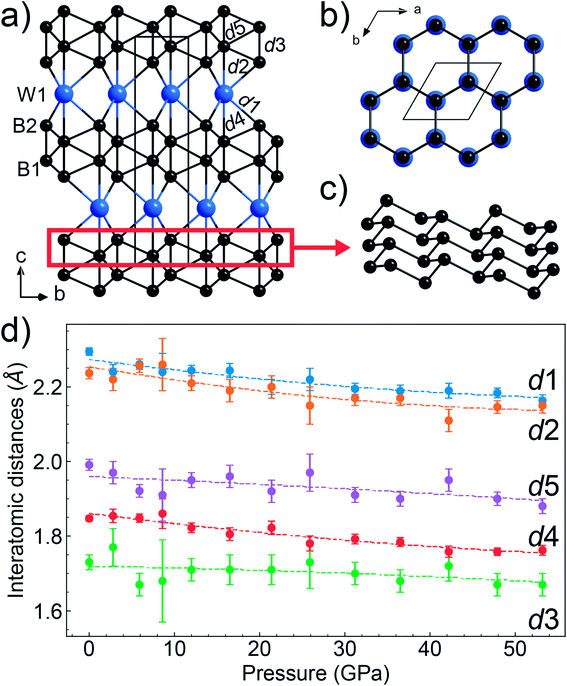 |
| Fig. 3 Crystal structure of WB4 projected down the a-axis (a) and c-axis (b). All structures consist of hexagonal layers of W atoms (blue spheres) interchanging with the network formed by covalently bonded boron atoms (black spheres). The red rectangle highlights a single puckered layer formed by condensed six-membered rings of boron in a chair-like conformation, and the layer in a different projection is shown in (c). Compressibility of interatomic distances and bonds in WB4 (d): d1, d2 – W⋯B distances and d3-d5 – B⋯B bonds. The solid symbols – data retrieved from the single-crystal diffraction measurements, and the dashed lines are the 2nd-order polynomial fits of compression data serving as a guide to the eye. | |
Both early38,39 and recent26,42,44,45,47,49 experimental structural studies of the “WB4” phase proposed a different crystal structure, which is built from interchanging defect close-packed metal layers and planar boron honeycomb layers and interstitial boron atoms (Fig. 1a–e). A structural similarity to WB5 suggests that all the “WB4” phases reported in previous publications were, likely, boron-deficient WB5−x, but not genuine stoichiometric WB4.54 Furthermore, it was predicted that the genuine stoichiometric WB4 phase is thermodynamically stable only above 1 GPa,54 and hence, ambient-pressure syntheses were unlikely to be capable to fabricate it.
Mechanical properties
We examined the mechanical properties of our WB4 crystals by measurements of single-crystal compressibility using pressure-dependent single crystal X-ray diffraction up to 54 GPa (Fig. 4) and by measurements of both hardness and Young's modulus.
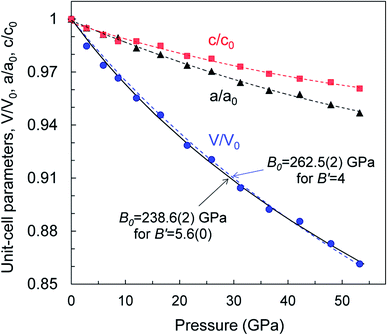 |
| Fig. 4 Pressure dependencies of relative variations in the unit-cell volume and lattice parameters of a WB4 single crystal at 295 K. Error bars are smaller than symbols' size. | |
The high pressure in situ single crystal X-ray diffraction studies up to 54 GPa were carried out using a neon quasi-hydrostatic pressure-transmitting medium. The WB4 sample showed no phase transitions under compression up to 54 GPa, and we could follow pressure evolutions of its unit cell parameters. Fitting the third-order Birch–Murnaghan equation of state to the volumetric data, we estimated the bulk modulus to be B0 = 238.6(2) GPa for B′ = 5.6(0) and B0 = 262.5(2) GPa for fixed B′ = 4 (Fig. 4). As seen from this plot, the WB4 crystal has a sizable difference in axial compressibility, and along the c-axis, it is the most incompressible. The shortest B–B bonds (denoted as d3 Fig. 3a) in the crystal structure are oriented along the c-axis and have the lowest compressibility compared to the other B–B bonds and W⋯B contacts (Fig. 3d); therefore, we can expect that these bonds largely contribute to the axial incompressibility. The bulk modulus of WB4 appeared to be smaller than that for WB5−x phases: B0 ∼ 304–342 GPa with fixed B′ = 4 (see ref. 83 and refs therein). On the other hand, stoichiometric WB4 shows no lattice parameter softening around 42 GPa, as has been observed previously for a non-stoichiometric phase.83
The hardness and Young's modulus
The nanoindentation hardness and Young's modulus measurements are shown in Fig. 5. In the likely single crystalline areas, they returned average values of HIT = 40.2(5) GPa (corresponding to HV = 37.3(5) GPa) and E = 482(30) GPa. Likewise, for the likely polycrystalline area, the hardness was found to be HIT = 35.9(1.6) GPa (corresponding to HV = 33.3(1.5) GPa) and the Young's modulus E = 551(24) GPa (Fig. 5). These magnitudes confirm that WB4 is a hard material and generally agrees with previous experimental estimations of hardness for seemingly “WB4” (WB5−x) phases to be about HV ∼ 30–45 GPa (ref. 26,44,45,47,49 and 54) (see Table 1 for comparison of mechanical properties). The elastic and plastic properties of hard solids are known to correlate with each other.84 Given the above experimentally-determined values of the bulk modulus (B0 = 262.5(2) for B = 4) (Fig. 4) and hardness (HV = 37.3(5) and 33.3(1.5) GPa)(Fig. 5a and b) for single- and polycrystalline samples of WB4, one can calculate their shear moduli (G) by using an empirical formula proposed by X. Q. Chen et al. and verified by numerous examples as follows:85,86
where k = G/B0. The returned values of the shear moduli of G = 227(2) and 214(5) GPa for single- and polycrystalline samples, respectively, are in a good agreement with the literature data (Table 1). The Pugh modulus ratios (B0/G) are 1.16(1) and 1.23(3), respectively. These values are much less than 1.75, – the threshold magnitude, which differentiates between brittle (B0/G < 1.75) and ductile (B0/G > 1.75) materials.87 Hence, WB4 is a brittle material and cannot be deformed in a ductile manner.
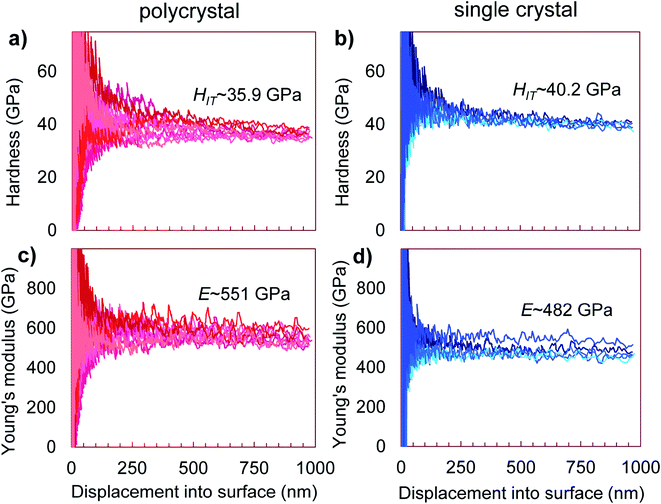 |
| Fig. 5 The nanoindentation hardness, HIT (a and b), and Young's modulus, E (c and d) of polycrystals (a and c) and single crystals (b and d) of WB4 at 295 K. Each plot combines several tests and shows average values. | |
Table 1 Mechanical properties of stoichiometric WB4 (isotropic bulk modulus B, shear modulus G, Young's modulus E and estimated values of Vickers' hardness HV; all units are in GPa) compared with reported literature values for various models of WB4, WB5 and their derivativesa
Phase |
Space group |
|
B
|
G
|
B/G |
E
|
H
V
|
Reference |
Calculated using the empirical models of: a – Chen,85 b – Šimůnek,91 c – Tian,92 d – Gao,93 and e – Mazhnik–Oganov;94 f – experimental hardness measured at an applied load of 0.49 N.
|
hP10-WB4 |
P63/mmc |
Exp. |
262.5(2) |
227(2) |
1.16(1) |
482(30) |
37.3(5) |
This work – single crystal |
|
|
Exp. |
262.5(2) |
214(5) |
1.23(3) |
551(24) |
33.3(1.5) |
This work – polycrystal |
|
|
Calc. |
294 |
215 |
1.367 |
519 |
28–35a |
17
|
|
|
Calc. |
292 |
213 |
1.371 |
514 |
21.3b |
88
|
|
|
Calc. |
299 |
217 |
1.378 |
525 |
29.0a |
31
|
|
|
Calc. |
302 |
259 |
1.166 |
604 |
40.0a |
36
|
|
|
Calc. |
297 |
217 |
1.372 |
523 |
28.8c |
37
|
hP15-WB4 |
R-3m |
Calc. |
299 |
137 |
2.182 |
356 |
11.3a |
31
|
|
|
Calc. |
308 |
253 |
1.217 |
596 |
37–42a |
17
|
hP20-WB4 |
P63/mmc |
Exp. |
304(10) |
|
|
|
46.2(1.2)f |
26
|
|
|
Exp. |
339(3) |
|
|
553(14) |
43.3(2.9)f |
44
|
|
|
Calc. |
392 |
104 |
|
|
41.1d |
43
|
|
|
Calc. |
328 |
129 |
2.543 |
325 |
|
29
|
|
|
Calc. |
300 |
102 |
2.941 |
274 |
5.2a |
89
|
|
|
Calc. |
298 |
85 |
3.506 |
233 |
3.2a |
31
|
WB4.2 |
P63/mmc |
Calc. |
280 |
245 |
1.143 |
569 |
39.7e |
54
|
WB5 |
Pmmn
|
Calc. |
287 |
267 |
1.075 |
611 |
44.9a |
36
|
|
|
Calc. |
295 |
270 |
1.093 |
621 |
44.7e |
54
|
WB5–x–WB2 (50/50%) |
|
Exp. |
|
|
|
|
29.3(2.3)f |
90
|
WB5–x–WB2 (67/33%) |
|
Exp. |
|
|
|
|
38.7(1.1)f |
90
|
Conclusions
We have successfully synthesized single crystals of the predicted but so far “elusive” stoichiometric WB4 phase, determined its crystal structure by single-crystal X-ray diffraction and investigated its mechanical properties. A hexagonal crystal structure of stoichiometric tungsten tetraboride is formed by hexagonal close-packed single tungsten atom layers, which interchange with covalently-bonded boron two-layer networks with short B–B bonds along the c-axis. The latter bonds contribute to the anisotropic character of axial compressibility. Our single-crystal diffraction data suggest that tungsten atoms fully occupy their crystallographic positions, while no additional interstitial boron atoms with partial occupancy could be identified. In situ high-pressure study shows that the bulk modulus of WB4 is 238.6(2) GPa. Measurements of mechanical properties of bulk polycrystalline samples under ambient conditions reveal a hardness of ∼36 GPa. Our work solved the long-standing challenge of the “WB4” phase and confirmed its high technological potential as a hard material. Further enhancement of its mechanical properties could be achieved by alloying with other elements, as it was demonstrated on a non-stoichiometric polymorph of WB4.2.44,47 This phase allows hosting a wide variety of transition metals in its structure forming ternary alloys. As a result, its own Vickers microindentation hardness can increase from ∼43 GPa to 51–56 GPa by addition of 6–8% of Ti, Zr or Hf95 and to 53–54 GPa by addition of 2–10 at% of Ta, Mn or Cr96 (the values were measured under an applied load of 0.49 N). Incorporation of group III transition metals (Y and Sc) and selected lanthanoids (Gd, Tb, Dy, Ho, and Er) also improves hardness values and oxidation resistance.97
Author contributions
Elena Bykova: investigation, conceptualization, formal analysis, funding acquisition, and writing – original draft; Sergey V. Ovsyannikov: investigation, formal analysis, and writing – original draft; Maxim Bykov: investigation and writing – review & editing; Yuqing Yin: investigation; Timofey Fedotenko: investigation and data curation; Hendrik Holz: investigation and formal analysis; Stefan Gabel: investigation and formal analysis; Benoit Merle: investigation, formal analysis, and writing – original draft; Stella Chariton: investigation and data curation; Vitali B. Prakapenka: investigation, data curation, methodology, and writing – review & editing; Natalia Dubrovinskaia: resources and writing – review & editing; Alexander F. Goncharov: resources and writing – review & editing; Leonid Dubrovinsky: funding acquisition, resources, and writing – review & editing.
Conflicts of interest
There are no conflicts to declare.
Acknowledgements
E. B, M. B. and A. F. G. acknowledge support of the Carnegie Institution of Washington. E. B. acknowledges financial support from the program ‘Promotion of Equal Opportunities for Women in Research and Teaching’ funded by the Free State of Bavaria. M. B. acknowledges the support of Deutsche Forschungsgemeinschaft (DFG project BY112/2-1). Portions of this work were performed at GeoSoilEnviroCARS (The University of Chicago, Sector 13), Advanced Photon Source (APS), Argonne National Laboratory. GeoSoilEnviroCARS is supported by the National Science Foundation – Earth Sciences (EAR – 1634415). This research used resources of the Advanced Photon Source, a U.S. Department of Energy (DOE) Office of Science User Facility operated for the DOE Office of Science by Argonne National Laboratory under Contract No. DE-AC02-06CH11357. This research used resources from the Center for Nanoanalysis and Electron Microscopy (CENEM) at Friedrich-Alexander University Erlangen-Nürnberg.
References
- Y. Liang, X.-F. Wei, C. Gu, J.-X. Liu, F. Li, M. Yan, X. Zheng, Z. Han, Y. Zhao, S. Wang, J. Yang, W. Zhang, L. Kou and G.-J. Zhang, ACS Appl. Mater. Interfaces, 2021, 13, 14365–14376 CrossRef CAS PubMed.
- A. Zerr, R. Riedel, T. Sekine, J. E. Lowther, W. Y. Ching and I. Tanaka, Adv. Mater., 2006, 18, 2933–2948 CrossRef CAS.
- A. Zerr, G. Miehe, G. Serghiou, M. Schwarz, E. Kroke, R. Riedel, H. Fueß, P. Kroll and R. Boehler, Nature, 1999, 400, 340–342 CrossRef CAS.
- K. Watanabe, T. Taniguchi and H. Kanda, Nat. Mater., 2004, 3, 404–409 CrossRef CAS PubMed.
- S. Vogel, A. T. Buda and W. Schnick, Angew. Chemie Int. Ed., 2018, 57, 13202–13205 CrossRef CAS PubMed.
- P. Wang, S. Wang, Y. Zou, J. Zhu, D. He, L. Wang and Y. Zhao, Crystals, 2021, 11, 614 CrossRef CAS.
- M. Bykov, S. Chariton, H. Fei, T. Fedotenko, G. Aprilis, A. V. Ponomareva, F. Tasnádi, I. A. Abrikosov, B. Merle, P. Feldner, S. Vogel, W. Schnick, V. B. Prakapenka, E. Greenberg, M. Hanfland, A. Pakhomova, H.-P. Liermann, T. Katsura, N. Dubrovinskaia and L. Dubrovinsky, Nat. Commun., 2019, 10, 2994 CrossRef PubMed.
- M. Bykov, E. Bykova, A. V. Ponomareva, I. A. Abrikosov, S. Chariton, V. B. Prakapenka, M. F. Mahmood, L. Dubrovinsky and A. F. Goncharov, Angew. Chemie Int. Ed., 2021, 60, 9003–9008 CrossRef CAS PubMed.
- B. Albert, Angew. Chemie Int. Ed., 1998, 37, 1117–1118 CrossRef CAS PubMed.
- H. Gou, L. Hou, J. Zhang, H. Li, G. Sun and F. Gao, Appl. Phys. Lett., 2006, 88, 221904 CrossRef.
- B. Petermüller, C. Neun, K. Wurst, L. Bayarjargal, D. Zimmer, W. Morgenroth, M. Avalos-Borja, I. G. Becerril-Juarez, M. J. Mühlbauer, B. Winkler and H. Huppertz, Inorg. Chem., 2018, 57, 10341–10351 CrossRef PubMed.
- B. Petermüller, C. Neun, M. Stekiel, D. Zimmer, M. Tribus, K. Wurst, B. Winkler and H. Huppertz, Chem.–Eur. J., 2018, 24, 14679–14685 CrossRef PubMed.
- C. Neun, B. Petermüller, E. Haussühl, L. Bayarjargal, K. Wurst, T. Götsch, S. Penner, W. Morgenroth, I. G. Becerril-Juarez, M. Avalos-Borja, H. Huppertz and B. Winkler, Solid State Sci, 2020, 105, 106211 CrossRef CAS.
- H. Tang, X. Gao, J. Zhang, B. Gao, W. Zhou, B. Yan, X. Li, Q. Zhang, S. Peng, D. Huang, L. Zhang, X. Yuan, B. Wan, C. Peng, L. Wu, D. Zhang, H. Liu, L. Gu, F. Gao, T. Irifune, R. Ahuja, H.-K. K. Mao and H. Gou, Chem. Mater., 2020, 32, 459–467 CrossRef CAS.
- B. Zhao, X. Wang, L. Yu, Y. Liu, X. Chen, B. Yang, G. Yang, S. Zhang, L. Gu and X. Liu, Adv. Funct. Mater., 2022, 32, 2110872 CrossRef CAS.
- H.-Y. Chung, M. B. Weinberger, J.-M. Yang, S. H. Tolbert and R. B. Kaner, Appl. Phys. Lett., 2008, 92, 261904 CrossRef.
- H. Gou, Z. Li, H. Niu, F. Gao, J. Zhang, R. C. Ewing and J. Lian, Appl. Phys. Lett., 2012, 100, 111907 CrossRef.
- H. Gou, N. Dubrovinskaia, E. Bykova, A. A. Tsirlin, D. Kasinathan, W. Schnelle, A. Richter, M. Merlini, M. Hanfland, A. M. Abakumov, D. Batuk, G. Van Tendeloo, Y. Nakajima, A. N. Kolmogorov and L. Dubrovinsky, Phys. Rev. Lett., 2013, 111, 157002 CrossRef PubMed.
- A. Knappschneider, C. Litterscheid, D. Dzivenko, J. A. Kurzman, R. Seshadri, N. Wagner, J. Beck, R. Riedel and B. Albert, Inorg. Chem., 2013, 52, 540–542 CrossRef CAS PubMed.
- A. Knappschneider, C. Litterscheid, N. C. George, J. Brgoch, N. Wagner, J. Beck, J. A. Kurzman, R. Seshadri and B. Albert, Angew. Chem. Int. Ed., 2014, 53, 1684–1688 CrossRef CAS PubMed.
- H. Gou, A. A. Tsirlin, E. Bykova, A. M. Abakumov, G. Van Tendeloo, A. Richter, S. V. Ovsyannikov, A. V. Kurnosov, D. M. Trots, Z. Konôpková, H.-P. Liermann, L. Dubrovinsky and N. Dubrovinskaia, Phys. Rev. B: Condens. Matter Mater. Phys., 2014, 89, 064108 CrossRef.
- E. Bykova, A. A. Tsirlin, H. Gou, L. Dubrovinsky and N. Dubrovinskaia, J. Alloys Compd., 2014, 608, 69–72 CrossRef CAS.
- G. Akopov, M. T. Yeung and R. B. Kaner, Adv. Mater., 2017, 29, 1604506 CrossRef PubMed.
- S. B. Schneider, D. Baumann, A. Salamat, Z. Konôpková, H.-P. Liermann, M. R. Schwarz, W. Morgenroth, L. Bayarjargal, A. Friedrich, B. Winkler and W. Schnick, Chem. Mater., 2012, 24, 3240–3246 CrossRef CAS.
- B. Fuchs, D. Johrendt, L. Bayarjargal and H. Huppertz, Angew. Chemie Int. Ed., 2021, 60, 21801–21806 CrossRef CAS PubMed.
- Q. Gu, G. G. Krauss and W. Steurer, Adv. Mater., 2008, 20, 3620–3626 CrossRef CAS.
- G. Akopov, L. E. Pangilinan, R. Mohammadi and R. B. Kaner, APL Mater, 2018, 6, 070901 CrossRef.
- Z. Zhang, A. Mansouri Tehrani, A. O. Oliynyk, B. Day and J. Brgoch, Adv. Mater., 2021, 33, 2005112 CrossRef CAS PubMed.
- E. Zhao, J. Meng, Y. Ma and Z. Wu, Phys. Chem. Chem. Phys., 2010, 12, 13158 RSC.
- Q. Tao, D. Zheng, X. Zhao, Y. Chen, Q. Li, Q. Li, C. Wang, T. Cui, Y. Ma, X. Wang and P. Zhu, Chem. Mater., 2014, 26, 5297–5302 CrossRef CAS.
- X.-Y. Cheng, X.-Q. Chen, D.-Z. Li and Y.-Y. Li, Acta Crystallogr. Sect. C Struct. Chem., 2014, 70, 85–103 CrossRef CAS.
- T. Moscicki, J. Radziejewska, J. Hoffman, J. Chrzanowska, N. Levintant-Zayonts, D. Garbiec and Z. Szymanski, Ceram. Int., 2015, 41, 8273–8281 CrossRef CAS.
- N. G. Szwacki, Sci. Rep., 2017, 7, 1–6 CrossRef PubMed.
- A. G. Kvashnin, H. A. Zakaryan, C. Zhao, Y. Duan, Y. A. Kvashnina, C. Xie, H. Dong and A. R. Oganov, J. Phys. Chem. Lett., 2018, 9, 3470–3477 CrossRef CAS PubMed.
- Z. Qin, W. Gong, X. Song, M. Wang, H. Wang and Q. Li, RSC Adv, 2018, 8, 35664–35671 RSC.
- C. Zhao, Y. Duan, J. Gao, W. Liu, H. H. Dong, H. H. Dong, D. Zhang and A. R. Oganov, Phys. Chem. Chem. Phys., 2018, 20, 24665–24670 RSC.
- A. Yang, Y. Duan, M. Peng, L. Shen and H. Qi, Appl. Phys. A, 2022, 128, 152 CrossRef CAS.
- A. Chretien and J. Helgorsky, CR, 1961, 252, 742–744 CAS.
- P. A. Romans and M. P. Krug, Acta Crystallogr., 1966, 20, 313–315 CrossRef CAS.
- J. Dong, H. Li, J. Wang, Z. Guo, J. Liao, X. Hao, X. Zhang and D. Chen, J. Phys. Chem. C, 2019, 123, 29314–29323 CrossRef CAS.
- Y. Wang, Y. Wu, Y. Lu, X. Wang, Y. Duan and M. Peng, Vacuum, 2022, 196, 110731 CrossRef CAS.
- I. Zeiringer, P. Rogl, A. Grytsiv, J. Polt, E. Bauer and G. Giester, J. Phase Equilibria Diffus., 2014, 35, 384–395 CrossRef CAS.
- M. Wang, Y. Li, T. Cui, Y. Ma and G. Zou, Appl. Phys. Lett., 2008, 93, 101905 CrossRef.
- R. Mohammadi, A. T. Lech, M. Xie, B. E. Weaver, M. T. Yeung, S. H. Tolbert and R. B. Kaner, Proc. Natl. Acad. Sci., 2011, 108, 10958–10962 CrossRef CAS PubMed.
- J. V. Rau, A. Latini, R. Teghil, A. De Bonis, M. Fosca, R. Caminiti and V. Rossi Albertini, ACS Appl. Mater. Interfaces, 2011, 3, 3738–3743 CrossRef CAS PubMed.
- X.-L. Wu, X.-L. Zhou and J. Chang, Int. J. Mod. Phys. B, 2015, 29, 1550103 CrossRef CAS.
- A. T. Lech, C. L. Turner, R. Mohammadi, S. H. Tolbert and R. B. Kaner, Proc. Natl. Acad. Sci., 2015, 112, 3223–3228 CrossRef CAS PubMed.
- X. Li, Y. Tao and F. Peng, J. Alloys Compd., 2016, 687, 579–585 CrossRef CAS.
- G. Akopov, M. T. Yeung, I. Roh, Z. C. Sobell, H. Yin, W. H. Mak, S. I. Khan and R. B. Kaner, Chem. Mater., 2018, 30, 3559–3570 CrossRef CAS.
- H. Gou, Z. Li, L.-M. Wang, J. Lian and Y. Wang, AIP Adv, 2012, 2, 012171 CrossRef.
- X. Cheng, W. Zhang, X.-Q. Chen, H. Niu, P. Liu, K. Du, G. Liu, D. Li, H.-M. Cheng, H. Ye and Y. Li, Appl. Phys. Lett., 2013, 103, 171903 CrossRef.
- E. M. Carnicom, J. Strychalska-Nowak, P. Wiśniewski, D. Kaczorowski, W. Xie, T. Klimczuk and R. J. Cava, Supercond. Sci. Technol., 2018, 31, 115005 CrossRef.
- W. Gong, C. Liu, X. Song, Q. Li, Y. Ma and C. Chen, Phys. Rev. B, 2019, 100, 220102 CrossRef CAS.
- A. G. Kvashnin, D. V. Rybkovskiy, V. P. Filonenko, V. I. Bugakov, I. P. Zibrov, V. V. Brazhkin, A. R. Oganov, A. A. Osiptsov and A. Y. Zakirov, Adv. Sci., 2020, 7, 2000775 CrossRef CAS PubMed.
- C. Gu, Y. Liang, X. Zhou, J. Chen, D. Ma, J. Qin, W. Zhang, Q. Zhang, L. L. Daemen, Y. Zhao and S. Wang, Phys. Rev. B, 2021, 104, 014110 CrossRef CAS.
- K. D. Shumilov, Z. Mehmedović, H. Yin, P. Poths, S. Nuryyeva, I. Liepuoniute, C. Jang, I. Winardi and A. N. Alexandrova, J. Phys. Chem. C, 2021, 125, 9486–9496 CrossRef CAS.
-
F. Cardarelli, Materials Handbook. A Concise Desktop Reference, Springer London, London, 2nd edn, 2008 Search PubMed.
- H. Nowotny, H. Haschke and F. Benesovsky, Monatshefte für Chemie – Chem. Mon., 1967, 98, 547–554 CrossRef CAS.
- T. Lundström and I. Rosenberg, J. Solid State Chem., 1973, 6, 299–305 CrossRef.
- R. Letoullec, J. P. Pinceaux and P. Loubeyre, High Press. Res., 1988, 1, 77–90 CrossRef.
- Y. Fei, A. Ricolleau, M. Frank, K. Mibe, G. Shen and V. Prakapenka, Proc. Natl. Acad. Sci. U. S. A., 2007, 104, 9182–9186 CrossRef CAS PubMed.
- V. B. Prakapenka, A. Kubo, A. Kuznetsov, A. Laskin, O. Shkurikhin, P. Dera, M. L. Rivers and S. R. Sutton, High Press. Res., 2008, 28, 225–235 CrossRef CAS.
-
D. L. Heinz and R. Jeanloz, in High-Pressure Research in Mineral Physics: A Volume in Honor of Syun-iti Akimoto, ed. M. H. Manghnani and Y. Syono, Terra Scientific Publishing, 1987, vol. 39, pp. 113–127 Search PubMed.
- C. Prescher and V. B. Prakapenka, High Press. Res., 2015, 35, 223–230 CrossRef CAS.
- V. Petříček, M. Dušek and L. Palatinus, Zeitschrift für Krist. – Cryst. Mater., 2014, 229, 345–352 CrossRef.
- D. Frost, B. Poe, R. Trønnes, C. Liebske, A. Duba and D. Rubie, Phys. Earth Planet. Inter., 2004, 143–144, 507–514 CrossRef CAS.
- S. V Ovsyannikov, M. Bykov, S. A. Medvedev, P. G. Naumov, A. Jesche, A. A. Tsirlin, E. Bykova, I. Chuvashova, A. E. Karkin, V. Dyadkin, D. Chernyshov and L. S. Dubrovinsky, Angew. Chem., Int. Ed., 2020, 59, 5632–5636 CrossRef PubMed.
- S. V. Ovsyannikov, H. Gou, A. E. Karkin, V. V. Shchennikov, R. Wirth, V. Dmitriev, Y. Nakajima, N. Dubrovinskaia and L. S. Dubrovinsky, Chem. Mater., 2014, 26, 5274–5281 CrossRef CAS.
-
CrysAlisPro Softw, Syst. version 1.171.40.84a, Rigaku Oxford Diffraction, Oxford, UK Search PubMed.
- G. M. Sheldrick, Acta Crystallogr. Sect. A Found. Adv., 2015, 71, 3–8 CrossRef PubMed.
- G. M. Sheldrick, Acta Crystallogr. Sect. C Struct. Chem., 2015, 71, 3–8 CrossRef PubMed.
- O. V. Dolomanov, L. J. Bourhis, R. J. Gildea, J. A. K. Howard and H. Puschmann, J. Appl. Crystallogr., 2009, 42, 339–341 CrossRef CAS.
- B. Merle, V. Maier-Kiener and G. M. Pharr, Acta Mater, 2017, 134, 167–176 CrossRef CAS.
- P. Sudharshan Phani and W. C. Oliver, Mater. Des., 2019, 164, 107563 CrossRef CAS.
- W. C. Oliver and G. M. Pharr, J. Mater. Res., 1992, 7, 1564–1583 CrossRef CAS.
- W. C. Oliver and G. M. Pharr, J. Mater. Res., 2004, 19, 3–20 CrossRef CAS.
- Metallic materials—Instrumented indentation test for hardness and materials parameters—Part 1: Test method. Int. Stand. ISO 14577–1, 2002.
- R. Kiessling, A. Wetterholm, L. G. Sillén, A. Linnasalmi and P. Laukkanen, Acta Chem. Scand., 1947, 1, 893–916 CrossRef CAS.
- M. Kayhan, E. Hildebrandt, M. Frotscher, A. Senyshyn, K. Hofmann, L. Alff and B. Albert, Solid State Sci, 2012, 14, 1656–1659 CrossRef CAS.
- M. Frotscher, W. Klein, J. Bauer, C.-M. Fang, J.-F. Halet, A. Senyshyn, C. Baehtz and B. Albert, Zeitschrift für Anorg. und Allg. Chemie, 2007, 633, 2626–2630 CrossRef CAS.
- J. C. Jamieson, Science, 1963, 139, 1291–1292 CrossRef CAS PubMed.
- H.-Y. Y. Chung, M. B. Weinberger, J. B. Levine, A. Kavner, J.-M. M. Yang, S. H. Tolbert and R. B. Kaner, Science, 2007, 316, 436–439 CrossRef CAS PubMed.
- M. Xie, R. Mohammadi, Z. Mao, M. M. Armentrout, A. Kavner, R. B. Kaner and S. H. Tolbert, Phys. Rev. B: Condens. Matter Mater. Phys., 2012, 85, 1–8 Search PubMed.
- D. M. Teter, MRS Bull, 1998, 23, 22–27 CrossRef CAS.
- X. Q. Chen, H. Niu, D. Li and Y. Li, Intermetallics, 2011, 19, 1275–1281 CrossRef CAS.
- X.-Q. Chen, H. Niu, C. Franchini, D. Li and Y. Li, Phys. Rev. B: Condens. Matter Mater. Phys., 2011, 84, 121405 CrossRef.
- S. F. Pugh, Dublin Philos. Mag. J. Sci., 1954, 45, 823–843 CrossRef CAS.
- M. Zhang, H. Yan, Q. Wei and H. Wang, Comput. Mater. Sci., 2013, 68, 371–378 CrossRef CAS.
- Y. Liang, Z. Fu, X. Yuan, S. Wang, Z. Zhong and W. Zhang, Europhys. Lett., 2012, 98, 66004 CrossRef.
- A. Y. Pak, D. V. Rybkovskiy, Y. Z. Vassilyeva, E. N. Kolobova, A. V. Filimonenko and A. G. Kvashnin, Inorg. Chem., 2022, 61, 6773–6784 CrossRef CAS PubMed.
- A. Šimůnek and J. Vackář, Phys. Rev. Lett., 2006, 96, 085501 CrossRef PubMed.
- Y. Tian, B. Xu and Z. Zhao, Int. J. Refract. Met. Hard Mater., 2012, 33, 93–106 CrossRef CAS.
- F. Gao, J. He, E. Wu, S. Liu, D. Yu, D. Li, S. Zhang and Y. Tian, Phys. Rev. Lett., 2003, 91, 015502 CrossRef PubMed.
- E. Mazhnik and A. R. Oganov, J. Appl. Phys., 2019, 126, 125109 CrossRef.
- G. Akopov, M. T. Yeung, C. L. Turner, R. Mohammadi and R. B. Kaner, J. Am. Chem. Soc., 2016, 138, 5714–5721 CrossRef CAS PubMed.
- M. Xie, R. Mohammadi, C. L. Turner, R. B. Kaner, A. Kavner and S. H. Tolbert, Appl. Phys. Lett., 2015, 107, 041903 CrossRef.
- G. Akopov, M. T. Yeung, I. Roh, Z. C. Sobell, H. Yin, W. H. Mak, S. I. Khan and R. B. Kaner, Chem. Mater., 2018, 30, 3559–3570 CrossRef CAS.
|
This journal is © The Royal Society of Chemistry 2022 |
Click here to see how this site uses Cookies. View our privacy policy here.