DOI:
10.1039/D1NR01134K
(Review Article)
Nanoscale, 2021,
13, 11679-11711
A review of the microwave-assisted synthesis of carbon nanomaterials, metal oxides/hydroxides and their composites for energy storage applications
Received
19th February 2021
, Accepted 15th May 2021
First published on 30th June 2021
Abstract
Currently, nanomaterials are considered to be the backbone of modern civilization. Especially in the energy sector, nanomaterials (mainly, carbon- and metal oxide/hydroxide-based nanomaterials) have contributed significantly. Among the various green approaches for the synthesis of these nanomaterials, the microwave-assisted approach has attracted significant research interest worldwide. In this context, it is noteworthy to mention that because of their enhanced surface area, high conducting nature, and excellent electrical and electrochemical properties, carbon nanomaterials are being extensively utilized as efficient electrode materials for both supercapacitors and secondary batteries. In this review article, we briefly demonstrate the characteristics of microwave-synthesized nanomaterials for next-generation energy storage devices. Starting with the basics of microwave heating, herein, we illustrate the past and present status of microwave chemistry for energy-related applications, and finally present a brief outlook and concluding remarks. We hope that this review article will positively convey new insights for the microwave synthesis of nanomaterials for energy storage applications.
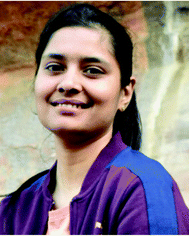 Nitika Devi | Nitika Devi is an Asst. Professor in the Department of Physics & Materials Science, Shoolini University, Himachal Pradesh, India. She has done M.Sc. physics (2015) from Himachal Pradesh University, Shimla. She obtained her Ph.D. degree in Physics (2021) from Central University of Himachal Pradesh. She has been working in the area of energy storage devices such as fuel cells, supercapacitors, batteries and also on the synthesis and application of carbon materials and its composites based on carbon nanotubes, graphene and their derivatives. |
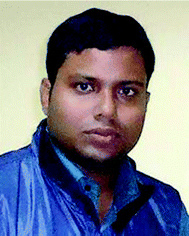 Sumanta Sahoo | Dr Sumanta Sahoo is working as an Asst. Professor in Madanapalle Institute of Technology & Science, Andhra Pradesh, India. He got his Ph.D. degree in Materials Science from the Materials Science Centre, Indian Institute of Technology Kharagpur (I.I.T. Kharagpur), West Bengal, India. He worked at the Korea Advanced Institute of Science and Technology (KAIST) (Graphene Research Center: Postdoctoral researcher: 2013–2014) Daejeon, South Korea, Yeungnam University (School of Chemical Engineering; International Research Professor: 2015–2017), Daegu, South Korea, and Indian Institute of Technology, Dhanbad, Jharkhand, India (Department of Chemistry; National Postdoctoral Fellow: 2018–2019). Dr Sahoo is an active researcher in the field of graphene, MXene, supercapacitor electrodes based on graphene, conducting polymers, and metal oxides/mixed metal oxides; and ternary nanocomposites for Li-ion batteries and fabrication of asymmetric supercapacitor devices. Dr Sahoo has published 53 peer-reviewed research/review articles in refereed international journals and 2 book chapters. According to the Google Scholar site, Dr. Sahoo has total citations of 2131 with the h-index of 26 and i-10 index of 40. |
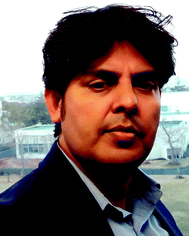 Rajesh Kumar | Dr Rajesh Kumar is Ramanujan Fellow in the Indian Institute of Technology, Kanpur (I.I.T. Kanpur), India. Previously, he was an International JSPS (Japan Society for the Promotion of Sciences) (standard) Postdoctoral Fellow (2018–2020) in Toyohashi University of Technology, Toyohashi, Japan. He obtained his B.Sc. and M.Sc. (Physics) Degrees from Allahabad University, Allahabad, India. After that he received his Ph.D. degree in Physics from the Department of Physics, Banaras Hindu University (B.H.U.), Varanasi, India. Soon after completing his Ph.D., he joined the Korea Advanced Institute of Science and Technology (KAIST) (Graphene Research Center), Daejeon, South Korea (May 2012–May 2014) to carry out postdoctoral research. Afterward, he moved to the Department of Materials Science and Engineering, Yonsei University, Seoul, South Korea to work as a Brain Korea 21 (BK-21) Research Professor. In 2015, he joined the Centre for Semiconductor Components and Nanotechnology, University of Campinas (UNICAMP), Campinas, Brazil as a CNPq postdoctoral fellow/visiting scientist (Mar. 2015–Dec. 2017). In Sept 2017, he got distinguished FAPESP (Sao Paulo Research Foundation Fellowship) postdoctoral fellowship and moved (Jan 2018) to the State University of Sao Paulo, Presidente Prudente, Brazil. Dr Kumar is serving as an editorial board member and reviewer for several journals of international repute. Dr Kumar has published 8 international book chapters and more than 75 research/review articles in peer-reviewed SCI refereed international journals. His main research interests are synthesis of 2D layered materials (graphene based materials/inorganic layered materials) for energy related applications. |
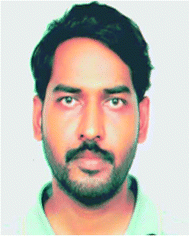 Rajesh Kumar Singh | Dr Rajesh Kumar Singh is an Asst. Professor in the School of Physical and Material Sciences, Central University of Himachal Pradesh, Himachal Pradesh, India. He obtained his Ph.D. Degree in Physics from the Institute of Sciences, Banaras Hindu University (B.H.U) Varanasi, India. He then spent 4 years (2011–2015) at the Indian Institute of Technology (B.H.U.) Varanasi as a Postdoctoral Fellow. His current research interests include hydrogen storage materials, solid oxide fuel cells, Supercapacitors, Li-ion batteries and synthesis of carbon nanostructures-metal/metal oxide self-assembly and their applications in various energy related areas. Dr Singh has published more than 70 peer reviewed international research/review articles including 4 book chapters. |
1. Introduction
Clean and renewable energy-related achievements and issues are highly concerning aspects in the 21st century due to the increasing pollution, and consequently enhancement in global warming on the Earth.1–5 The emission of harmful gases from factories and combustion from vehicles due to use of limited fossil fuel are one of the main reasons for the presence of greenhouse gases in the atmosphere, air pollution and climate change.6–9 Also, due to the increasing population worldwide, the consumption of limited fossil fuels is increasing continuously, and pollution is an unavoidable issue in the foreseeable future, which are the biggest challenges in society. Considering these unavoidable harmful issues and the threat to human life associated with environmental pollution, attention is focused on the design of value-added and cost-effective materials as electrodes for efficient utilization in energy storage and conversion processes.10–21
Among the energy storage devices, supercapacitors and secondary batteries have attracted widespread attention from researchers and are considered potential energy devices due to their good energy/power storage capacity, ultra-long term cycling stability, flexible operating temperature and environmentally friendly nature.22–25 In energy storage devices, the energy density, power density and robust cyclability properties are significant indicators to evaluate their performance.26–35 To improve these properties in energy storage devices, the performance of supercapacitors and batteries depend highly on the nature of electrode materials. For electrode materials, researchers have developed various high surface area carbon materials and metal oxide/hydroxide-based composites/hybrids. Recently, carbon materials modified with metal oxides/hydroxides using various methods have been utilized as energy storage electrodes in supercapacitors and secondary batteries.36–52
Nowadays, with continuous development in nanomaterial synthesis, the microwave (MW)-assisted approach has attracted significant attention from researchers due to its uniform heating inside materials.53–58 This is also because of the exceptional features of MW heating such as fast synthesis, selective heating without interaction with the surroundings and cost efficiency. MW generates direct volumetric heating and heat is simultaneously produced in the whole system, which results in fast heating.59–65 Selective heating can be performed during synthesis and is controlled due to the dielectric properties of materials.66–75 Nowadays, MW-irradiation (MWI) is frequently utilized for the synthesis of various types of carbon materials, metal oxides and metal hydroxides for energy-related electrode materials. Initially, the use of MWI was limited to inorganic synthesis and not used for organic synthesis. This is because of the non-polar nature of organic solvents, which do not support dielectric heating. However, nowadays several alternatives for this problem have been invented.76 In the case of carbon materials, the interaction mechanism is different from dielectric heating. In carbon materials, free electrons play a crucial role in heating.77Fig. 1 shows a schematic representation for the use of MW for the synthesis of carbon-based and metal oxide/hydroxide-containing materials for energy storage electrodes.
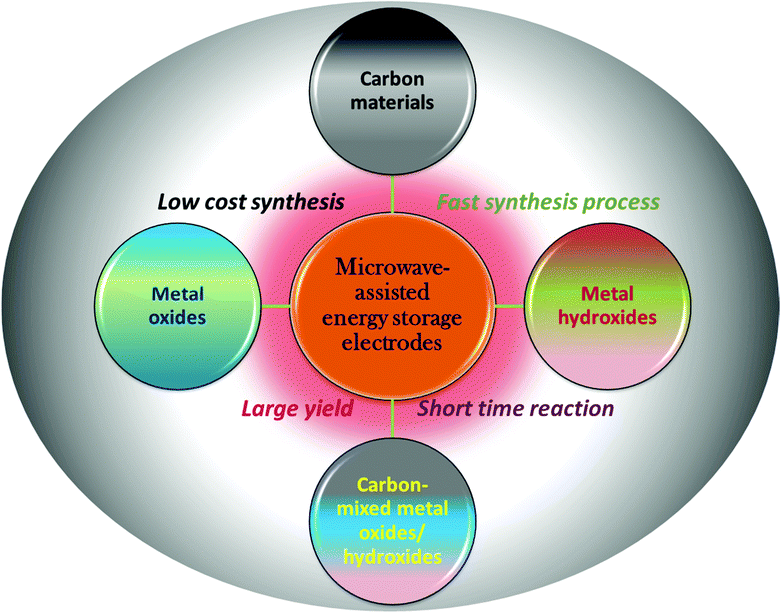 |
| Fig. 1 Schematic illustration of the use of MW-assisted synthesis of energy storage materials and its advantage. | |
In energy conversion devices, the MW-assisted approach has also been applied for the synthesis of carbon-modified electrodes materials for fuel cells.78–85 MW-assisted synthesis was employed to obtain a carbon black-supported polytetrafluoroethylene (PTFE/C) nanocomposite, which delivered an output power of 0.66 W cm−2.81 The Pt/carbon nanotube (CNT) composite obtained via MW-assisted synthesis was used as a high-performing catalyst for the oxygen reduction reaction in a proton-exchange membrane fuel cell.82 Carbon-supported ternary Pt–Sn–Rh alloy nanoparticles were synthesized using MW and applied for fuel cells, displaying good mass activities (2.18 A mgPt−1 and 1.70 A mgPt−1) for the ethanol and methanol oxidation reaction, which were 5.7 and 3.7 times greater than that of a commercial Pt/C catalyst, respectively.83 Recently, N-doped and oxygen-functionalized carbon nanoonion-supported Pd nanoparticles were synthesized via MW and used as an electrocatalyst, which exhibited a good current density (17.4 mA cm−2), long-term stability (6.9 mA cm−2), and fast electron transfer towards the ethanol oxidation reaction in alkaline medium.84 A reduced graphene oxide (rGO)-CuS-ZnS hybrid nanocomposite was synthesized via MW and used as a cathode, exhibiting a power generation of 1692 ± 15 mW m−2 and open circuit potential of 761 ± 9 mV.85
MWI is electromagnetic waves and prominently used in the telecommunication industry and its wavelength spectrum range appears between radio waves and the infrared region. The MW wavelengths in this range are from 1 m to 1 mm and the corresponding frequency is 0.3 GHz to 300 GHz. Domestic MW ovens (kitchen MW ovens) function at the frequency of 2.45 GHz, which is already in the range 0.3–300 GHz. Also, MWI plays an important role in scientific research especially in materials science for the synthesis of materials.86–94
2. Microwave: simple and fast approach
MWI provides much faster heat distribution compared to conventional heating due to its unique volumetric heating in materials. Heating by MWI is different from conventional heating in which heating occurs by conduction and convection processes. Also, MWI-assisted heating is a cost-efficient approach for laboratory synthesis and domestic use.95–98Fig. 2 presents a schematic comparison of the temperature distribution profile and heat transfer during MW-assisted and conventional heating. In MW-assisted heating, initially the particle interior is hotter than the particle surface. In MW-assisted heating, a temperature gradient occurs from the centre to the particle surface, whereas in conventional heating, a temperature gradient occurs from the particle surface to the centre. Thus, in MW-assisted heating, (e.g., under pyrolysis conditions), the volatile matter moves from the higher-temperature particle interior to the lower-temperature surface.99–102
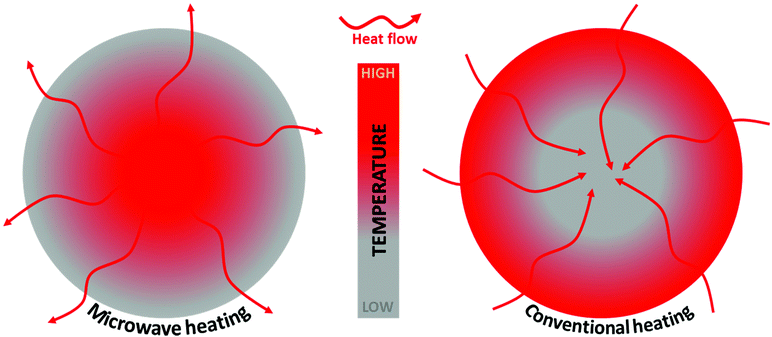 |
| Fig. 2 Schematic representation of the temperature gradient and heat flow due to MW and conventional heating. | |
2.1. Microwave heating: mechanism
MW heating mechanism is mainly dependent on the nature of the irradiated/exposed materials. The MW interaction is extremely dependent on the nature of the material and the degree of interaction. It is different for conductors, insulators, and dielectric materials.103 Three types of mechanisms have been mentioned in the literature when a material is irradiated/exposed to MWI. The common interaction phenomena are reflection, absorption and transmittance. Electrical conductors such as metals are reflectors of MWI. Some materials (quartz and PTFE) allow the transmission of MWI. Thus, conductors cannot be heated by MWs because they do not absorb MWI. However, polar liquids containing molecules and polar molecules are good absorbers of MW radiation, and consequently heat very quickly after MWI due to dipolar interactions and ionic conduction.103,104 When different dipoles and ions interact with electromagnetic waves, they accelerate with the frequency of the electromagnetic waves. Both ions and dipoles try to flip their orientation with the frequency of the electromagnetic waves. In both cases, flipping of their orientation is delayed due to the frictional forces of the surrounding ions and dipoles. This delay is called the relaxation time, and the energy losses during this period are liberated as heat, which spreads inside and uniformly heats the material. MW heating depends on some factors among which the dielectric parameter is crucial. The penetration depth is another important factor for the heating of materials, which is defined as103,104 |  | (1) |
where f is the frequency, c is the capacitance and ε° is the dielectric constant of free space. It can be seen from this equation that the penetration depth increases with an increase in capacitance and decrease in frequency. In case of an MW reflector (conducting medium is metal), the penetration depth becomes null because the capacitance for metal is zero. If the penetration depth is infinite, it means that MWs transmit from the materials without any absorption. Two other important quantities for defining the dielectric properties of materials are the loss tangent (δ) and dielectric constant. The dielectric constant (ε) of a material is the sum of the real (ε′) and imaginary permittivity (ε′′). It can be written as follows:
The real part of the dielectric constant deals with the absorbance of MW radiation and the imaginary part deals with loss. The MW absorption ability of a material is generally defined by the loss tangent, which can be written as95,96,103–105
| tan δ = ε′/ε′′ | (3) |
A large loss tangent value means good MW absorption, and thus the material characteristics such as penetration depth, dielectric constant and loss tangent should be carefully studied before the selection of materials for MW absorbance.
Fig. 3 shows the transmission, absorption and reflection of some materials, which are defined by the dielectric loss factor and power absorbed. According to Fig. 3, it can be concluded that the materials present between two extreme values of dielectric loss factor are best for MW absorption. In many chemistry reactions assisted by MWI and heating, they mainly depend on the solvents involved. Thus, there are some common solvents that are being used. The common solvents with their loss tangent values and dielectric constants are presented in Table 1. It can be seen that there is a corresponding increase in loss tangent with an increase in the dielectric constant. Thus, the selection of a particular solvent is required to maintain the heat for a desired reaction. Depending on the values of tan
δ, the solvents are classified as (i) tan
δ > 0.5, higher MW absorption solvent, (ii) tan
δ > 0.1, medium MW absorption solvent, and (iii) tan
δ < 0.1, low MW absorption solvent.76
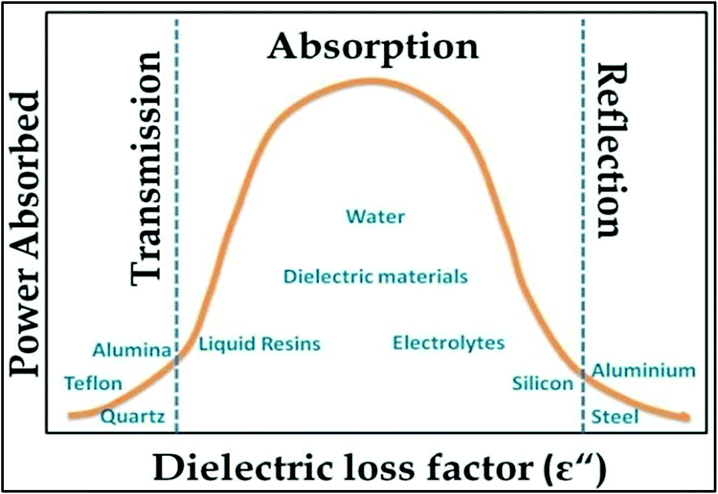 |
| Fig. 3 Dependence of reflection, absorption and transmittance on dielectric loss factor process.97 Reprinted (adapted) with permission from ref. 97, copyright (1999), Elsevier B.V. All rights reserved. | |
Table 1 Some important solvents with their dielectric constant and loss tangent values106
Solvent |
Dielectric constant |
Loss tangent (tan δ) |
Hexane |
1.9 |
— |
Benzene |
2.3 |
— |
Carbon tetrachloride |
2.2 |
— |
Chloroform |
4.8 |
0.091 |
Acetic acid |
6.1 |
0.174 |
Ethyl acetate |
6.2 |
0.059 |
THF |
7.6 |
0.047 |
Methylene chloride |
9.1 |
0.042 |
Acetone |
20.6 |
0.054 |
Ethanol |
24.6 |
0.941 |
Methanol |
32.7 |
0.659 |
Acetonitrile |
36.0 |
0.062 |
Dimethylformamide |
36.7 |
0.161 |
Dimethylsulfoxide |
47.0 |
0.825 |
Formic acid |
58.0 |
0.722 |
Water |
80.4 |
0.123 |
2.2. Microwave versus conventional thermal heating
MW heating provides several advantages compared to conventional heating due to its fast, uniform heating, cost efficiency and reduced energy consumption. MW heating is a volumetric heating, which means the material absorbs radiation and directly converts it into heat. Conversely, in the case of conventional thermal heating, heating takes place via conduction and convection processes and is transferred from the surface to molecules. Also, MW radiation relies on dielectric heating, which gives rise to selective heating. Past studies have shown a comparison between MW and conventional heating in the synthesis of materials. Ma et al.107 studied the synthesis of BaTiO3via MW and conventional heating and suggested that MW heating gives rise to a larger c/a ratio (lattice parameters) and needs shorter time for crystallization. MWI has been used in different synthetic processes, especially to achieve uniform and selective heating. MW radiation is preferably used in the powder metallurgy and ceramic fields for sintering processes. Sintering by MW heating offers good physical and mechanical strength, reduced energy consumption and shorter reaction duration. Oghbaei et al.108 explained the difference between MW and conventional sintering and discussed the basic aspects of MW heating and conventional heating.109 Volumetric heating results in uniform heating, whereas conventional heating has a temperature gradient, which is not good for mechanical strength and homogeneous morphology in materials. Also, inorganic and organic reactions can occur at much faster rates with MW heating compared to conventional heating.96,110 Berlan et al.111 studied the reaction rates for the cycloaddition reaction performed in xylene or dibutylether and found that the effects were more pronounced in the case of polar solvents. A schematic representation of the reaction is shown in Fig. 4a. The effect of different heating processing on the yield of the reaction mixture is shown in Fig. 4b and c. It can be seen from Fig. 4b and c that for xylene and dibutyl ether, MW heating resulted in a large product yield in a shorter time compared to conventional heating.111
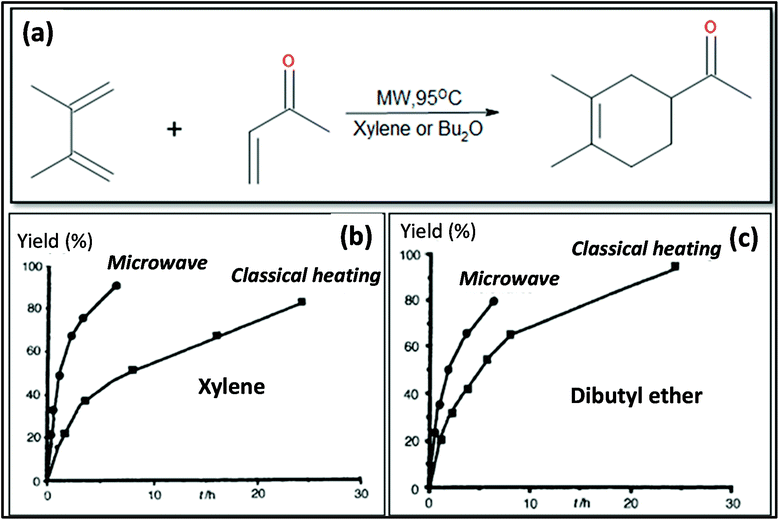 |
| Fig. 4 (a) Schematic molecular representation and MW condition. (b) and (c) Effects of different types of heating on product yield for xylene and dibutyl ether.111 Reprinted (adapted) with permission from ref. 111, copyright (1991), Elsevier B.V. All rights reserved. | |
Hydrolysis of adenosine triphosphate showed a 25-times faster rate using MW heating compared to conventional heating.112 MW heating increases the kinetic energy of the solvent through volumetric heating and hydrolysis completely depends on the temperature of the reaction mixture (not on the heating method), where the temperature was better controlled by MW heating.112 In addition to increase the reaction rate, one can also achieve selective product by controlling the power of the MW radiation. The Arrhenius kinetic model can be written as113
|  | (4) |
|  | (5) |
Applying conventional heating, the obtained product is a mixture of P1 and P2, but after increasing the heating rate by using MW heating, it is possible to produce product P1 only by adding reagents R1, R2 and R3. This type of situation is called induced heating, as shown in Fig. 5a. There is another possibility, which is called inversion heating, where careful control and fast heating gives rise to product P2, but in the case of conventional heating, essentially product P1 can be obtained. The inversion heating condition is shown in Fig. 5b.113 Thus, reactivity can be changed by selective heating.
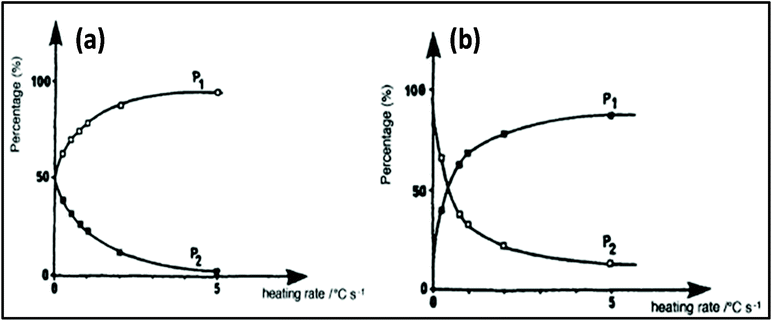 |
| Fig. 5 Controlling rate of reaction using MW heating: (a) induced heating and (b) inversion heating.113 Reprinted (adapted) with permission from ref. 113, copyright (1993), Elsevier B.V. All rights reserved. | |
Thus, it can be concluded that MW heating gives rise to uniform heating and better selective product yield. These characteristics of MW radiation make it useful for synthesis via inorganic and organic chemical reactions.
3. Microwave-assisted synthesis
MW radiation is conventionally used for the synthesis of various materials such as carbon materials, metal oxides, and metal hydroxides and other organic/inorganic materials. The interactions of MW radiation is different for various types of materials.
3.1. Carbon nanomaterials
Carbon nanomaterials are good absorbers of MW and interact in different ways with MWI, which is different from the dielectric heating phenomenon. In the case of carbon nanomaterials, the large numbers of free electrons available in these materials are responsible for heating after MWI. When electromagnetic radiation interacts with electrons, the electrons try to oscillate with the same phase of electromagnetic radiation, but the radiation changes their phase very quickly and oscillating electrons cannot match with the same phase. This phase lag results in energy dissipation in the form of heat inside carbon materials. Other interesting phenomena also occur during MWI, when the kinetic energy of an electron increases, it causes a spark, and consequently ionization in the surrounding in the form of plasma.77,114 Accordingly, carbon nanomaterials can be easily modified with metal oxides via MWI to form composite/hybrid structures. Devi et al.115 reported the MW-assisted synthesis of graphene and its derivative and concluded that MWI can be effectively applied for these syntheses. The dielectric loss factors of some carbon materials are presented in Table 2. Due to their good absorption of MW, carbon materials can also be used in other applications as a heat receptor.77
Table 2 Dielectric loss factor of some carbon materials at a frequency of 2.45 GHz and at room temperature, 298 K (ref. 77)
Carbon material |
tan δ |
Ref. |
Coal |
0.02–0.08 |
116 and 117 |
Carbon foam |
0.05–0.20 |
118
|
Charcoal |
0.11–0.29 |
119 and 120 |
Carbon black |
0.35–0.83 |
121 and 122 |
Activated carbon |
0.57–0.80 |
119, 123 and 124 |
Activated carbon |
0.22–2.95 |
125
|
Carbon nanotube |
0.25–1.14 |
126 and 127 |
CSi nanofibres |
0.58–1.00 |
128
|
The good absorbing nature of carbon materials has been utilized in processes such as the pyrolysis of biomass and waste77,129,130 and soil remediation.131,132 Here carbon materials are used as a receptor for MW radiation to provide the required heating temperature for these reactions. Accordingly, carbon materials make these synthetic processes less time consuming, reducing the energy consumption.133–135 The production of carbon nanofilaments is an example of these processes, which previously involved expensive and long processes. For the synthesis of carbon nanofilaments, activated carbon was irradiated by MW in the presence of CH4/N2 and CH4/CO2. In both cases, activated carbon acts as both a catalyst and receptor.136,137 The production of nanofilaments is not possible via the conventional heating method. This is because MW heating encourages the formation of nanofilaments in an entirely different way that is not possible with conventional heating. Ko et al.138 employed MW radiation for the purification of carbon nanotubes in nitric acid. The functionalization of carbon nanotubes takes a long time and involves many steps. This problem can also be solved by using MW-assisted functionalization. Reactions such as amidation and 1,3-dipolar cycloaddition for the functionalization of carbon nanotubes can be done within 15 min. The additional advantages of using MW heating for functionalization is no need for the use of toxic agents, uniform dispersion and undamaged carbon nanotubes.139 MW heating has also been used for the production of many carbon-based products from graphite such as isotropic anisotropic pitch-based carbon powder, expanded graphite with a layered structure having a larger interlayer separation than the natural graphite,140 and synthesis of ordered mesoporous graphite carbon materials. MW heating also makes the conventionally used hydrothermal and sol–gel processes much simpler and faster.141 Traditionally, activated carbon is produced via the activation of organic precursors at high temperatures up to 1173 K. However, with MW radiation, completion of the reaction can be achieved in a short time and at a much lower temperature, that is, from 673 to 1073 K.142 Norman and Cha et al.143 reported the activation of char for the synthesis of microporous activated carbon. MW heating has also been used for removing functionalities or reduction of activated carbon. There are other processes that have been simplified and shortened by applying MW heating such as the vulcanization of rubber, MW-assisted polyol process, and drying of carbon xerogels. There are several reports on the use of MW heating for inducing pyrolysis with a carbon mixture and various metal oxides.77,129–132,144–146 Thus, the MW absorption property of carbon materials makes their synthesis and modification much simpler compared to conventional thermal heating methods.
3.2. Metal oxide nanomaterials
MW heating is also becoming popular for synthesis in areas such as inorganic, organic, and polymer chemistry and biochemical processes. MW radiation has been successfully used for the synthesis of metal nanoparticles with different shapes, sizes, morphologies, and compositions. The nature of nanoparticles is highly dependent on their physical and structural characteristics. Many processes such as solvothermal synthesis, template-assisted synthesis, and thermolysis of precursors have been used for the synthesis of metal nanoparticles.147–149 The use of MW heating in these syntheses provides a way for the large-scale production and controlling the size of nanoparticles. MWI decreases the activation energy of a reaction with an increase in the reaction rate. The high internal energy results in the fast decomposition of the precursor and fast nucleation growth, resulting in homogeneous morphological and controlled compositional changes in nanoparticles. MW heating also controls the critical size of particles via uniform heating rates. Diverse dimensional nanoparticles have been fabricated by controlling the heating time of the reaction and using suitable solvents.150–157
The size and morphology of nanoparticles are affected by the growth and nucleation processes. These mechanisms are described by the classical nucleation theory for the growth and nucleation of nanoparticles.158–160 Nucleation can be of two types, namely, homogeneous nucleation and heterogeneous nucleation. In the case of homogeneous nucleation, no other particles are necessary and the precursor material itself forms a cluster for nucleation. However, for heterogeneous nucleation, the presence of foreign particles is required for the nucleation and growth of nanoparticles. The growth of nanoparticles eventually gives rise to the formation of nanocrystals. This can be summarized in three steps, i.e., nucleation, growth and completion of growth, which is commonly known as Ostwald ripening. In Ostwald ripening two processes occur, which are growth and diffusion limited aggregation and are mainly dependent on temperature. MWI offers constant temperature throughout the solution/material due to fast heating rate and inward heating.
Researchers have synthesized metal ferrite (MFe2O3, M = Fe, Mn, Co, Ni, and Zn) via the assistance of MWI.161 In this process, in addition to precursor materials, oleic acid and oleylamine were used as ligating solvents. The results showed a change in morphology by changing the MWI time and also by making some compositional changes. Fig. 6 presents the effect of MWI duration on the morphology of Fe2O3. Bilecka et al.162 reported the MW-assisted synthesis of ZnO nanoparticles. The synthesis of ZnO involves esterification and is a first order reaction. The rate constant of the reaction was calculated to be significantly high in case of MW heating (15 nm3 min−1) in comparison to conventional heating (3.9 nm3 min−1). These results give clear evidence of the effective heating by MW. Another report on the synthesis of ZnO oxide showed morphological changes with a change in the MWI heating time. It was found under similar conditions, heating for 30 s resulted in the formation of cube-shaped nanoparticles, whereas heating for 60 s resulted in the formation of ZnO nanorods,67 as shown in Fig. 7.
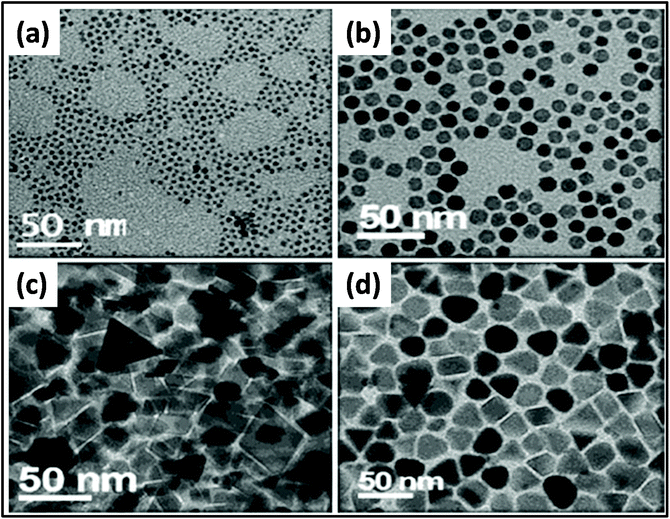 |
| Fig. 6 TEM images of Fe3O4: effect of using different compositions and times of MWI. (a) 4 nm and (b) 20 nm prepared using the same ratio of oleic acid to oleylamine (1 : 1) at different MW times (6–8 min and 15–18 min, respectively). (c) Triangular and prism shapes and (d) quasi cubes and triangular shapes prepared using oleic acid to oleylamine ratios of 2 : 1 and 3 : 1, respectively.161 Reprinted (adapted) with permission from ref. 161, copyright (2013), Springer. All rights reserved. | |
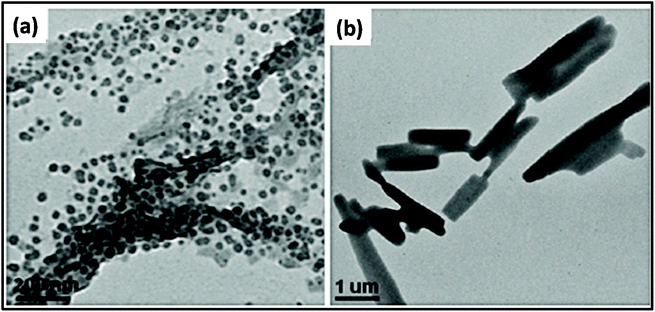 |
| Fig. 7 TEM images of ZnO nanostructures prepared by MWI of 0.1 M zinc acetate solution in pure oleic acid for 30 s (a) and 60 s (b).161 Reprinted (adapted) with permission from ref. 161, copyright (2013), Springer. All rights reserved. | |
MW-assisted methods for the synthesis of other metal oxides such as TiO2, CeO2, and rare earth oxides (M2O3, M = Pr, Nd, Sm, Gd, Tb, and Dy) have also been reported.163–165 These metal oxides were further used in many applications such as optical communication, oxidation of heavy metal oils, and UV shielding. Transition metal oxides are extensively used in energy storage applications. The MW-assisted synthesis of these metal oxides makes the process cost efficient and easy. Huang et al.166 developed α-MnO2 nanofibers using an MW-assisted hydrothermal method. This synthesis was performed at 200 °C temperature with a holding time of 10 s–30 min. MnO2 exists in the α, β, γ and δ phases. Chen et al.167 synthesized all the phases of MnO2via MW-assisted synthesis utilizing the reduction reaction of MnCl2-KMnO4 under MWI. There are other reports on the MW-assisted synthesis of different metal oxides such as Co3O4
168,169 and NiO.170 TiO2 materials were prepared via both conventional and MW heating, in which MW-assisted synthesis resulted in higher crystallinity in a shorter processing time. The MW-assisted synthesis was completed in 30–60 min, whereas conventional heating took 8–12 h for completion.171
3.3. Metal hydroxide nanomaterials
Metal hydroxides have also been synthesized via MWI and used in many energy storage applications such as rechargeable batteries and supercapacitors.172–180 The synthesis time and cost are very important for the commercialization of materials, which can both be efficiently improved by MW heating. Xu et al.178 studied the hydrothermal synthesis of 3D flowerlike α-Ni(OH)2via MW-assisted and conventional heating. The XRD pattern of the product, as shown in Fig. 8a, reveals highly intense peaks in the case of MW-assisted synthesis compared to conventional heating. MW heating is more beneficial for the crystalline structure of materials compared to conventional heating. Also, a morphological study showed that particles prepared via the MW-assisted method were uniform in shape and size, which was not in the case of conventional synthesis. This uniformity in the shape and size of particles is due to the uniform and rapid heating by MWs. One group described the preparation of α-Ni(OH)2 employing MW heating.179 Ni(NO3)2·6H2O was used as a precursor in ethanol solvent and heated at 150 °C for 15 min. This green product α-Ni(OH)2 was further transformed into NiO via calcination at 300 °C, 350 °C, and 400 °C. The growth mechanism for the formation of α-Ni(OH)2 followed the same steps as discussed previously for metal oxides. Briefly, nucleation occurs when Ni2+ ions are reduced with ethanol in the presence of MW heating. Once α-Ni(OH)2 nucleation occurs, then its growth is dominated by the Ostwald ripening phenomenon. The morphology of α-Ni(OH)2 is dominated by 2D layers, which further grow and give rise to a flower-type morphology.179 The SEM and TEM images of the synthesized α-Ni(OH)2 are shown in Fig. 8b and c, respectively. The calcined product NiO showed very good cyclic stability and a specific capacitance of 277 F g−1.179
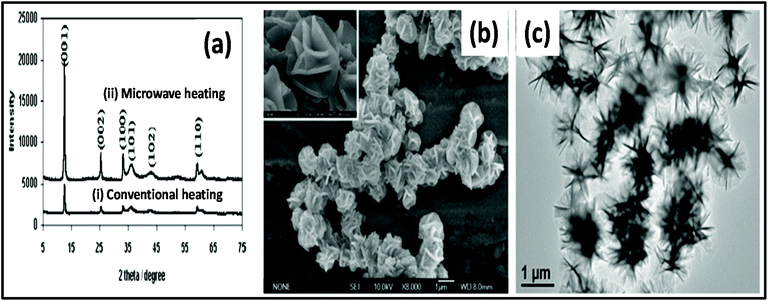 |
| Fig. 8 (a) XRD pattern of α-Ni(OH)2 synthesized by (i) conventional heating method and (ii) MW heating method.178 (b) SEM image of α-Ni(OH)2 and (c) TEM image of α-Ni(OH)2.179 Reprinted (adapted) with permission from ref. 178 and 179, copyright (2008 and 2010), the American Chemical Society. | |
The growth of α-Ni(OH)2 using MW-assisted synthesis was also demonstrated by Zhu et al.172 The specific capacitance of α-Ni(OH)2 was 4172.5 F g−1 at a current density of 1 A g−1. Besides Ni(OH)2, there are many other transition metal hydroxides that have been synthesized by MW heating. For example, Liu et al.180 synthesized layered cobalt hydroxide nanocones intercalated with dodecylsulphate (DS) ions. The product showed a nanocone-type morphology, in which the size of the tip diameter was 20 nm and the bottom diameter was 400 nm with the length of the cone of 2 μm. For 10 min heating at 100 °C, a mixed morphology of nanocones and sheets was obtained, but on increasing the holding time to 30 min, only nanocones were formed.180 Some groups also discussed the formation of composites of two metal hydroxides such as Zn–Al double layered structure and composite of CoxNi1−x(OH)2 nanosheets. Chen et al.181 fabricated nanosheets of Co–Ni hydroxide using MW, applying 40% of the maximum power of 1250 W for 3 min, resulting in the composition of Co0.2Ni0.8(OH)2 having a hexagonal nanosheet morphology. A comparative study was also performed to determine the effect of conventional heating and MW heating on the synthesis of a Zn–Al SDS composite. The results confirmed that MW heating is much faster than the conventional method and endows the material with good crystallinity.182
3.4. Carbon mixed metal oxide/hydroxide nanomaterials
It is known that carbon materials contain good MW absorption capacity and many carbon allotropes and nanostructures are used in many applications.183,184 Thus, the MW-assisted formation of composites can improve the synthesis process, form homogeneous composites and enhance the material efficiency. Composites of carbon and metal oxides/hydroxides have been significantly used in energy storage such as supercapacitors and batteries.185–196 In conventional heating, the synthesis mechanisms commonly lead to heterogeneous nucleation due to the temperature gradient. However, in MW-assisted synthesis, carbon materials mostly act as a substrate given that they have good absorption capacity toward MWs. Also, the presence of carbon materials and the concentration of the precursor materials considerably affect the morphological-dependent characteristics. Kim et al.197 studied the morphology of an rGO and Co/Ni(G/CoNi) hydroxide composite. It was deduced that with a change in the composition of CoNi, the morphology of the product changes. For the compositional ratio of 4
:
1 (G/CoNi), a sheet-like morphology was formed, whereas for 1
:
4 ratio, aggregation of the CoNi particles occurred, which resulted in the formation of a nanosphere-type of morphology. The advantage associated with MW-assisted synthesis is that the reduction of graphite oxide and the formation of the composite occur simultaneously. The composite also gave a superior electrochemical performance with a specific capacitance of 1622 F g−1 for G-CoNi 2
:
1.197Fig. 9 reveals the effect of MWI time on the morphology of multi-walled CNT (MWCNT)/Ag nanoparticles. The diameter of Ag nanoparticles varies with a variation in the MW irradiation time. Composites were prepared by mixing silver acetate as a silver source and MWCNT powder in a stoichiometric ratio using a mortar and pestle. This mixture was then irradiated for 60 min at the power of 300 W and temperature of ∼300 °C. A similar study was conducted using conventional heating methods, in which the average diameter of the nanoparticle was 40–50 nm. However, in the case of the MW-assisted synthesis, the average diameter of the nanomaterial was much larger, i.e., 20–100 nm.198 Loupy et al.199 revealed that MW-assisted synthesis produced a 90% increase in yield compared with conventional synthesis. Several studies confirmed that the increase in yield is purely because of non-thermal MW effects. Numerous studies have demonstrated the formation of CNTs and metal hydroxide and metal oxide composites.200,201
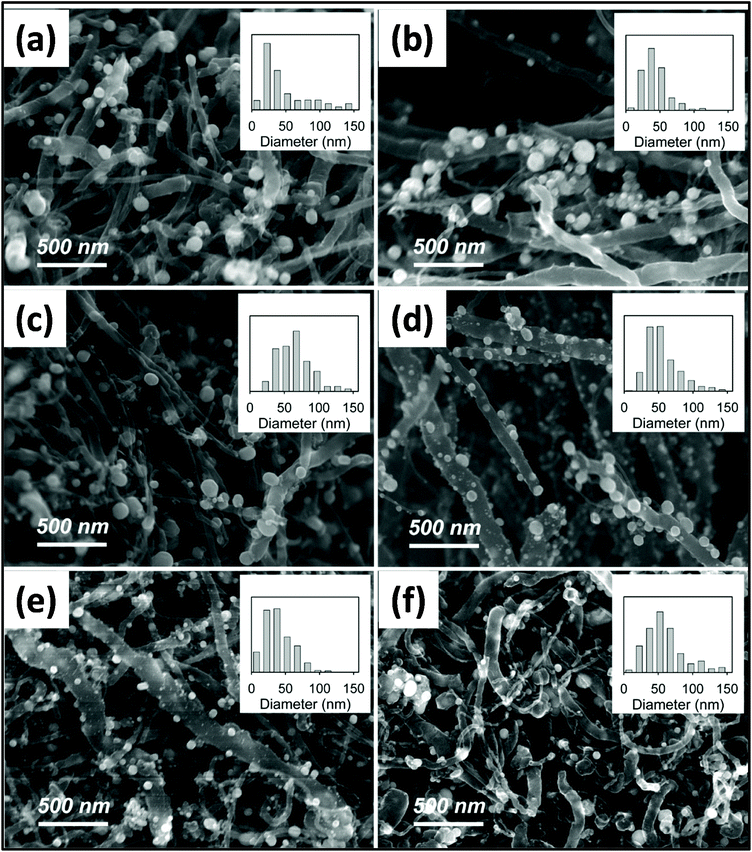 |
| Fig. 9 SEM images of various samples of silver/MWCNT starting material (a) 1 min, (b) 2 min, (c) 5 min, (d) 10 min, (e) 30 min, and (f) 60 min, of MWI.198 Reprinted (adapted) with permission from ref. 198, copyright (2011), the American Chemical Society. | |
A CNT/RuO2 composite was obtained by Kim et al.,202,203 in which the uniform distribution and loading of nanoparticles on CNT was achieved by controlled heating. Up to 70% loading of RuO2 with an average diameter of 2 nm was achieved. Guo et al.204 prepared uniform carbon-coated ZnO nanorods via MW-assisted synthesis and studied their photocatalytic activity cytotoxicity. Prior to MWI, the surface of the ZnO rods was modified by amino groups. The system was then irradiated at 100 °C for 30 min, resulting in the formation of the composite. The TEM and SEM images of the samples revealed that rods were uniform with an average size of ∼12 nm. The particle size distribution is shown in the inset of the graph in Fig. 10a.
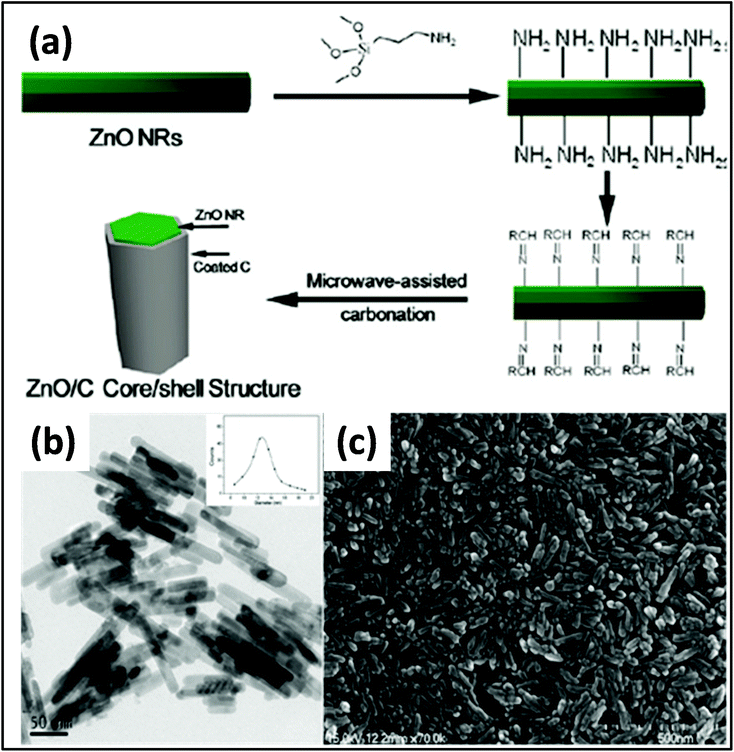 |
| Fig. 10 (a) Schematic diagram showing the synthesis of carbon-coated ZnO. (b) TEM (inset: average size distribution of 200 rods) and (c) SEM images of ZnO nanorods.204 Reprinted (adapted) with permission from ref. 204, copyright (2009), the American Chemical Society. | |
3.5. Current state of the art on microwave-assisted synthesis: carbon nanomaterials and metal oxide/hydroxide nanomaterials
The current trend of MW synthesis is mainly focused on the development of advanced carbon materials with high porosity, enhanced surface area, and superior mechanical properties. Nano-structured carbon materials are significantly synthesized using various MW routes including MW-assisted pyrolysis, MW-induced hydrothermal/solvothermal process, and MW-assisted activation.205 In a recent study, N-doped and oxygen-functionalized carbon nanoonions were combined with Pd nanoparticles through MW heating.206 The resultant composite was utilized as an efficient anode electrocatalyst for alkaline fuel cells. In another report, Eskalen et al. demonstrated the MW-assisted hydrothermal synthesis of carbon dots from acid linter waste.207 The carbon dots displayed efficiency for fluorescence cancer imaging and human cell growth inhibition properties. Moreover, carbon quantum dots were synthesized using citric acid and urea in a domestic MW oven.208 A dark brown cluster of carbon quantum dots was prepared within a period of 300 s. A pictorial overview of the color change in the intermediates of this MW synthetic route is shown in Fig. 11. This special type of carbon material displayed enhanced optical properties, which can be efficient for organic solar cells.
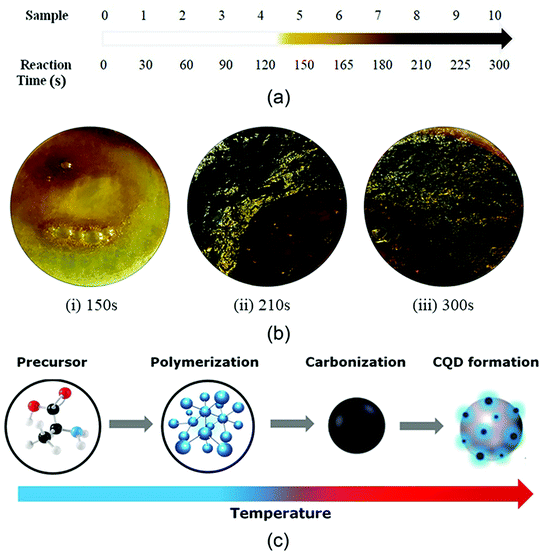 |
| Fig. 11 (a) Change in sample color with reaction time. (b) Samples depicting the change in color and CQD formation upon heat treatment of (i) 150 s, (ii) 210 s, and (iii) 300 s. (c) Reaction pathway for the synthesis of CQDs with an increase in temperature.208 Reprinted (adapted) with permission from ref. 208, copyright (2020), Taylor & Francis Group. All rights reserved. | |
The MW-assisted synthesis process was further extended to the synthesis of N,S-doped carbon dots using citric acid and thiourea.209 With the MW power of 550 W, the doped carbon nanomaterial was synthesized within only 5 min, indicating a rapid and efficient synthetic route. The doped carbon dots demonstrated extensive mercury ion sensing properties. In a recent study, Xia et al. demonstrated the ultrafast MW-assisted synthesis of N-doped mesoporous carbon on Ni foam.210 A strong MW power of 1000–2000 W was applied to melamine-loaded resol-coated Ni foam under an N2 atmosphere for only 3 min to synthesize this special type of carbon material. The MW heating process was further implemented to produce a composite of histidine-functionalized graphene quantum dots and Ni–Co layered double hydroxide (LDH).211 The composite displayed superior electrochemical performances, and thus can be applied in the fabrication of supercapacitor electrodes. MW synthesis route has also been found to be beneficial for the development of other supercapacitor electrodes. For example, graphene was combined with MoS2 through MW heating using sodium molybdate dihydrate (Na2MoO4·2H2O) as the Mo precursor and L-cysteine as the sulfur source and reducing agent.212 Besides graphene, CNT was also combined with a metal oxide such as NiO through MWI at a high power of 560 W for 10 min in a domestic MW oven.213 The current MW reaction process was successful with the assistance of H2O2. Similar to the previous report, the current composite also demonstrated excellent electrochemical performances for application in supercapacitors. All these studies clearly indicate the impact of the MW synthetic route for producing nanostructured carbon materials with versatile application potential.
The MW synthetic route has been considered an eco-friendly, green, and sustainable synthetic approach for the production of metal oxides with nano-architectures. In recent years, MW heating was found to be more beneficial compared to the conventional heating approach in terms of reaction time and product yield.214 For example, the MW-assisted hydrothermal approach was employed by Zhang et al. to synthesize beta-bismuth(III) oxide (β-Bi2O3) nanopowder.215 The synthetic approach was successful in reducing the reaction time from 24 h to 2 h. The resultant metal oxide demonstrated superior photocatalytic properties for the degradation of methyl orange. Mixed metal oxides are a new class of metal oxides, which are suitable for many future applications. In this case, Hashemzehi et al. reported a MW-assisted solution combustion process to produce a Cu–Zn–Al mixed metal oxide.216 In another report, a Ti/(RuO2)0.5(IrO2)0.5 anode was synthesized through an MW heating process at a high MW power of 700 W for application in the dye degradation process.217 A comparative study on the dye degradation properties of the mixed metal oxide synthesized via conventional and MW heating clearly indicated the superior performance of the MW-synthesized metal oxide. Moreover, a CoMnMgAl mixed oxide catalyst was synthesized through an MW-assisted self-combustion process.218 The mixed metal oxide exhibited promising catalytic activity for the total oxidation of toluene. For sensing applications, MW technology has also been employed. For example, a CuO/ZnO heterojunction composite was synthesized through an MW-epoxy-assisted hydrothermal method.219 This composite demonstrated promising H2S gas sensing properties. To understand the MW synthetic approach, the synthesis process of this metal oxide-based composite is schematically shown in Fig. 12. In another report, a nanocomposite based on CdO and MgO was synthesized through an MW-assisted green approach using the acetate precursors of Cd and Mg.220 This composite displayed excellent antimicrobial, anti-breast and anti-lung cancer activity. Superior antibacterial activity was further exhibited by (Ag, Co)-codoped CuO nanoparticles, which were synthesized through the MWI approach.221 In a typical process, all the precursor materials were irradiated with the MW energy of 2.45 GHz at the corresponding power of 800 W for 30 min.
 |
| Fig. 12 Schematic illustration of the MW synthetic approach for CuO/ZnO heterojunction: (a) complete synthetic process and (b) various samples prepared in this study.219 Reprinted (adapted) with permission from ref. 219, copyright (2020), the American Chemical Society. | |
For further property enhancement, metal oxides have been combined with carbon nanomaterials through the MWI process. For example, in a recent study, Kumar et al. proposed a MWI approach for the synthesis of an Mn3O4-Fe2O3/Fe3O4@rGO ternary hybrid for the fabrication of advanced supercapacitor electrodes.222 Using graphite oxide as the precursor for graphene, the authors applied a high MWI power (900 W) for only 30 s to achieve the ternary hybrid. It is important to mention that the consecutive exfoliation and reduction of graphite oxide to form graphene are possible through MWI. A schematic of the synthetic approach and the mechanism of the synthesis of the ternary hybrid are presented in Fig. 13.
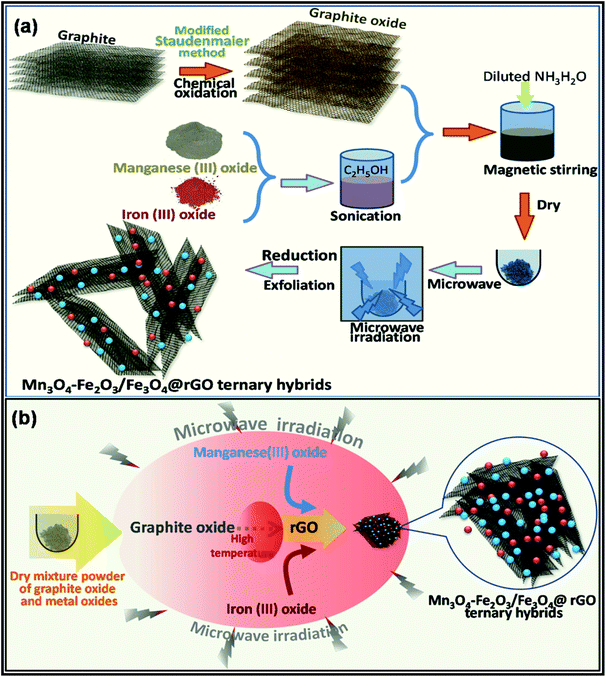 |
| Fig. 13 Schematic presentation of the (a) synthesis process and (b) mechanism of MW-assisted formation of Mn3O4-Fe2O3/Fe3O4@rGO ternary hybrid.222 Reprinted (adapted) with permission from ref. 222, copyright (2020), Elsevier B.V. All rights reserved. | |
A MW-induced hydrothermal process was employed to synthesize a ternary nanocomposite based on Fe3O4, rGO, and MoO3 for energy storage application.223 In the presence of MWI, the hydrothermal reaction time was restricted to only 1 h. Table 3 provides a summary of the various works based on the MW-assisted synthesis of metal oxides, metal hydroxides, and composites of carbon materials/metal oxides/hydroxides and their related applications.
Table 3 Summary of some of the published reports on the MW-assisted synthesis of metal oxides, metal hydroxides, and composites of carbon materials/metal oxides/hydroxides and their applications
Material |
Material type |
Precursors/solvent |
Morphology and structure of materials |
MW condition |
Results/application |
Ref. |
PVP: polyvinylpyrrolidone; DMF: N,N-dimethylmethanamide; PEG: polyethylene glycol; and EtOH: ethanol. |
Metal oxide |
MgO, NiO, ZnO, ZrO2, Fe2O3, Al2O3 |
Magnesium ethylate, zinc acetate tetrahydrate, nickel acetate tetrahydrate, aluminium-tri-sec-butoxide, ferric acetate, zirconium(IV) isopropoxide/ethyl acetate, ethanol, PVP |
Amorphous powder with particle size in the range of 0.7–3.7 nm after annealing. |
30 min |
Nanoparticles prepared by MW-assisted synthesis |
224
|
|
Bi2O3 |
Bi(NO3)3·5H2O, nitric acid/H2O |
Nanorods |
6 min refluxing at medium power of MW oven |
Cost effective for synthesis of Bi2O3 nanorods |
225
|
|
|
PVP, NaOH |
Diameter ∼100 nm; length: several micrometers/monoclinic crystalline α-Bi2O3 |
|
|
|
|
CeO2 |
(Ce(NO3)3·6H2O), HAuCl4·4H2O, sodium hydroxide/urea, ammonia, and ethanol |
14 nm spheres assembled in hollow spheres (260 nm) |
170 °C for 30 min |
Good absorption capacity for heavy metal ions |
226
|
|
Co3O4 |
Cobalt nitrate and urea |
Foamy porous morphology with cubic spinel structure. |
15 min at 2.45 GHz, 800 W. |
Coercivity value was 56.7 Oe. |
227
|
|
CuO |
Cu(CH3COO)2/EtOH NaOH, PEG |
Sphere morphology with average size of 4 nm and single-phase monoclinic CuO |
10 min heating with 20 MW heating cycles (6 s ON/24 s OFF) |
Band gap estimated to be 2.43 eV |
228
|
|
α-Fe2O3 |
FeCl3·6H2O/HCl |
Spheres 31–66 nm with α-Fe2O3 |
2–8 h |
Effect of MWI on morphology and other aspects affecting characteristics |
229
|
|
|
|
|
100–160 °C |
|
|
|
Cr2O3, MoO2, CoO, Mn2O3 |
K4Fe(CN)6, K3Co(CN)6, K3Mn(CN)6, K3Mo(CN)8, K3Cr(CN)6/H2O |
Octahedral, spherical, rod, pine tree, snowflake-like assemblies 1–5 mm with orthorhombic Mn2O3, cubic Cr2O3, MoO2, CoO structures |
3 h at 180 °C, >1 atm |
Obtained nanoparticles can be used for biomedical and catalytic properties |
230
|
|
In2O3, Tl2O3 |
Indium(III) chloride, thallium(III) chloride/NH4OH |
Hexagons 22 nm (In2O3) and spherical nanoparticles (Tl2O3) with BCC In2O3, and cubic Tl2O3 |
60 m (MW cycles: 12 s ON/7 s OFF) reflux |
BCC structured In2O3 and cubic Tl2O3 were prepared |
231
|
|
PdO |
PdCl2/H2O, PVP, NaOH NaOAc, C6H5CO2Na |
Spheres 1.8–3.2 nm and σ = 25% with FCC structure |
8 min refluxing at 900 W with 10% output power |
Palladium oxide nanoparticles with FCC structure synthesized |
232
|
|
SnO2 |
SnCl4·5H2O/H2O, urea |
SnO2 nanoparticles (size: 3 nm) |
15 min refluxing with a 650 W power with 10% output |
Optical measurement showed a band gap of 4.5 eV |
233
|
|
TiO2 |
TiCl4, HCl, NH4OH |
TiO2 nanorods (diameter: 20–30 nm; length: 150–250 nm) |
5 min–8 h, 25–80 °C, 1 atm |
Facile approach for synthesis of TiO2 |
234
|
|
WO3 |
Na2WO4·2H2O, H2O, (NH4)2SO4, HCl |
WO3 nanowires (diameter: 5–10 nm; length: 8–10 μm) |
20 min–3 h, 150 °C, >1 atm |
High electrocatalytic activity for hydrogen evolution reaction |
235
|
|
ZnO |
Zn(OAc)2, hydrolyzed in diethylene glycol (DEG) |
ZnO colloidal nanocrystal clusters (nanocrystal size: 8 nm; cluster size: 57 to 274 nm) |
1–5 min steps, 120–180 °C, 1 atm |
Highly sensitive sensor for sensing humidity |
236
|
|
ZrO2 |
ZrOCl2·8H2O/NaOH |
Spheres 10–20 nm with monoclinic structure |
120 min at 194 °C at 14 atm |
Nanosized and crystalline particles of ZrO2 were obtained |
237
|
Metal hydroxide |
α-Ni(OH)2 |
Ni(NO3)3·6H2O/EtOH, urea |
3D flower-like morphology with size of 700 nm–1 mm and it is α-Ni(OH)2 single phase |
90 °C for 15 min |
Enhanced electrochemical activity due to flower-like morphology |
178
|
|
Mg(OH)2 |
Mg(NO3)2/H2O, NaOH |
Fibre like 20–40 nm, 100–150 nm with a hexagonal phase |
4 days under MW (20 W) at 25 °C |
Fibre-like Mg(OH)2 was synthesized |
238
|
Carbon |
rGO-ZnO |
Zn(AC)2·2H2O, RGO sheets |
ZnO nanocrystals are anchored on wrinkly rGO sheets,239 ZnO nanorods apparently originate from a centre forming flower-like morphologies distributed on the surface of rGO240 |
300 W for 10 min,239 MW treatment for 30 min240 |
Photoactivity for the decolorization of dyes under visible light,239 adsorption-photocatalysis240 |
239 and 240 |
|
GQDs-CuO nanoneedles |
Cupric acetate, GO/NaOH, H2O, H2O2 |
GQDs/CuO nanocomposite has a spindle-shaped structure of 80 ± 10 nm in length and 16 ± 5 nm in width and structure of CuO is monoclinic |
Under 800 W at 200 °C for 8 min |
For the sensing of the H2O2 and glucose |
149
|
|
Graphene-CuO |
Cupric acetate, GO/DMF |
Quasi-spherical CuO nanoparticles embedded on graphene sheets, 30–50 nm in size with CuO monoclinic crystal structure |
800 W for 20 min |
For the detection of bisphenol-A |
241
|
|
CNT-RuO2 |
RuCl3, CNT/H2O and NH3 |
Average diameters of RuO2 nanoparticles 1–2 nm |
∼700 W for 30 s |
For electrochemical supercapacitors |
242
|
|
CNT-MnO2 |
KMnO4, CNT, nitric acid |
MnO2 can be rapidly nucleated on the wall of CNTs |
10 min MWI at 700 W |
Specific capacitance based on MnO2was 944 and 522 F g−1 at 1 and 500 mV s−1 |
243
|
|
Graphene/hierarchy structure MnO2 |
KMnO4, MnSO4·H2O, GO/H2O |
MnO2 nanospheres with a size in the range of 100 to 200 nm uniformly distributed on graphene sheet and structure of MnO2 is birnessite type. |
75 °C for 30 min (the controlled power was approximately 450 W) |
Specific capacitance of 244 F g−1 at a current density of 100 mA g−1 |
167
|
|
NiAl-layered double hydroxide/rGO |
Ni(NO3)2·6H2O, Al(NO3)3·9H2O and GO |
NiAl-LDH nanosheets are attached to the surface of rGO and structure of NiAl-LDHs is hexagonal |
MWI for 2 h at 100 °C |
Specific capacitance of 1630 F g−1 at 1 A g−1 in 6 M KOH |
244
|
4. Recent trends on microwave-assisted hydrothermal/solvothermal synthesis of organic nanomaterials
Similar to other synthetic areas, MW heating is significant in solvent-mediated hydrothermal/solvothermal organic synthesis. MW-assisted organic synthesis can be done using water or other polar solvents. Many organic reactants are insoluble in water, which results in an inhomogeneous solution. However, MW heating relies on dielectric heating, and thus the behavior of a particular solvent changes with a change in temperature due to the change in dielectric constant. The dielectric constant of water is 78 at 25 °C and 20 at 300 °C, respectively. Thus, at high temperature, water can act as a pseudo-organic solvent for many organic syntheses. MW heating also makes solvent-free synthesis feasible.76,245,246 Organic synthesis proceeding in water and other solvents is heavily applied in industrial applications.
4.1. Hydrolysis of benzyl alcohol and benzamide
These reactions usually take approximately 35 min and 1 h for the hydrolysis of benzyl chloride and benzamide, respectively. However, when these reactions are carried by MWI, they proceeded for only 3 min (benzyl alcohol) and 7 min (benzamide).246–248
The yield obtained was large compared to the reaction carried under conventional synthetic conditions.
4.2. Esterification
A small amount of conc. H2SO4 was used as a catalyst and 6 min was required for completion of the reaction.249
Various organic reactions assisted by MWI have been studied by many researchers. Some of these reactions are shown below as Schemes 1,250 2,251 3,252 and 4
253 in Fig. 14. Scheme 1 was carried by Shi et al.,250 where they synthesized thiazolo[3,2-α]pyridines and also checked their anti-oxidant and cytotoxic activities. It was previously reported that these types of compounds show high biological activities.254 Isoniazid (INH) (Scheme 2) was also synthesized via the MW-assisted reaction of various benzaldehydes and dimedone in water with a catalytic amount of p-dodecylbenzenesulfonic acid (DBSA). These synthesized compounds were analyzed further for their anti-TB activity toward Mycobacterium tuberculosis (H37Rv) [MTB].251 Schemes 1 and 2 are examples of N-heterocycle organic reactions. MW heating is also capable of carrying out many other organic reactions such as cross-coupling reactions,252 Huisgen 1,3-dipolar cycloadditions,253 hydration of nitrile and hydrogenation reactions,255 and synthesis of β- and γ-hydroxy sulfides.256 Scheme 3 corresponds to two organic reactions, where one is for the Sonogashira cross coupling of aryl iodide and bromides, which was introduced by Ley et al.252 This reaction gave a very good yield of 99% under MWI. The second reaction shown in Scheme 4 is an example of Huisgen 1,3-dipolar cycloaddition.253 MW-assisted hydration of nitrile and hydrogenation reactions for the synthesis of magnetite silica-decorated ruthenium hydroxide (Fe3O4-SiO2-Ru(OH)x) was performed and these compounds were further applied in the synthesis of dyes,255 pharmaceuticals, etc. Thus, this discussion clearly indicates that MW-assisted synthesis also has a significant contribution in the field of organic chemistry.
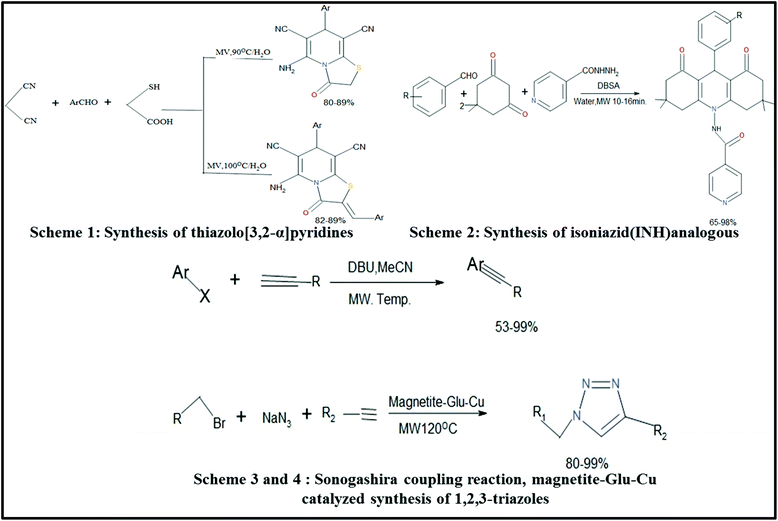 |
| Fig. 14 Scheme for synthesis via the MW-assisted method.76,250–252 | |
4.3. Microwave-assisted synthesized nanomaterials for energy related applications: past and present
The synthesis of nanomaterials using MWI has attracted significant interest because of its easy reaction completion, cost effectiveness, selective heating, etc. In the next section, some of the reported works on MW-assisted-synthesized nanomaterials are described, which were further used in many energy-related applications such as supercapacitors and batteries.
4.4. Supercapacitors
Metal and metal oxide/hydroxide nanoparticles have been used for supercapacitor applications as electrode materials. Zhang et al.257 synthesized γ-MnO2 and α-MnO2 using MWI in 5–30 min. The morphology results showed that as the radiation holding time increased, the morphology of MnO2 was affected. With an increase in MWI time from 5 min to 30 min, the number of nanowires and nanoplatelets increased together with an increase in their length, as shown in Fig. 15. Fig. 15a–f correspond to the synthesis in acidic conditions and Fig. 15g–l correspond to the synthesis in neutral conditions at different MW heating times. In acidic conditions, an urchin-like nanostructure morphology was formed, which consisted of uniform nanorods. In the neutral case, the MnO2 showed a nanoplatelet and nanowire morphology. This indicates that the experimental conditions significantly affect the products. The highest specific capacitance offered by MnO2 was 311 F g−1 at a current density of 0.2 A g−1, which was obtained for γ-MnO2 nanoparticles. Thus, this method provides a way that is much more cost efficient and less time consuming compared to the conventional synthesis method. Also, this provides a way of controlling morphological aspects by controlling the heating time.257 Co3O4 was synthesized using MW heating at 240 W for 5 min. Co(NO3)2·6H2O was used as the cobalt source and water and ammonia were used as the solvent and for maintaining the pH of the solution, respectively. After MW treatment, the precipitates were calcined at 300 °C for 1 h. The size of the nanoparticles was found to be uniform and the mean particle size was 24 nm. The uniform size of the nanoparticles was due to the uniform heating by MWI. Electrochemical measurements of these nanoparticles gave the maximum specific capacitance of 346 F g−1 at a scan rate of 5 mV s−1. The specific capacitance was the maximum at a low current density and low scan rates.258 Wang et al.259 reported the electrochemical properties of a composite of metal/metal oxide nanoparticles on graphene synthesized via MW-assisted one-pot synthesis. The metal used for the formation of this composite was PtRu and the metal oxide was SnO2.259Fig. 16 shows the cyclic voltammetry (CV) and galvanometric charge/discharge curves for the samples MnO2-A-5 and MnO2-N-5, where 5 is the MW holding time and N and A mean neutral and acidic conditions, respectively. It was found from the CV that the entire curve showed a rectangular shape, which did not change much with an increase in the scan rate, indicating that the material has good capacitive reversibility. This good specific behavior was due to the unique morphology of the material. According to the galvanometric charge/discharge curves, the maximum specific capacitance was 311 F g−1 at a current density of 0.2A g−1 in the case of MnO2-N-5, which was less than that of MnO2-A-5 (163 F g−1). This difference was because of the large surface area of MnO2-N-5, which was 76 m2 g−1. Another report was published on the MW-assisted synthesis of RuO2 by Devadas et al.260 The calculated specific capacitance was 737 F g−1 at a scan rate of 2 A g−1. Kumar et al.261 also synthesized copper-tungstate nano-powder via MW-assisted synthesis. The nano-powder of Cu-WO4 showed a specific capacitance of 77 F g−1.261 There are many reports on different types of nanomaterials and their further use for supercapacitors applications such as Mn3O4
262 and NiCo2O4.263
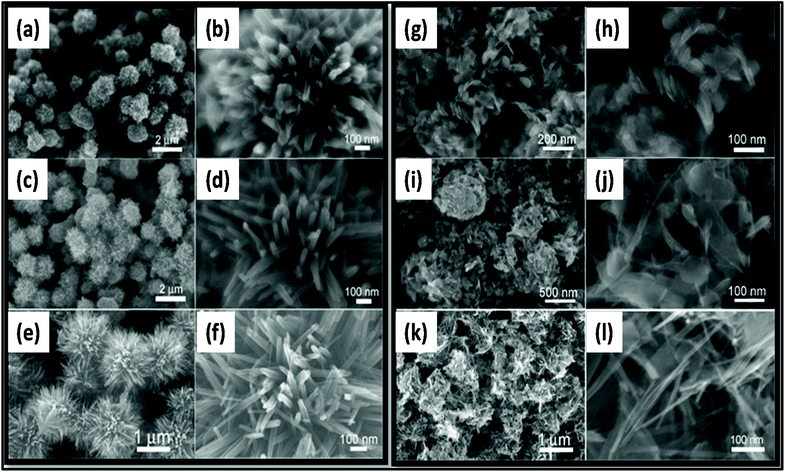 |
| Fig. 15 SEM images of MnO2 prepared at (a, b, g, and h) 5 min, (c, d, i, and j) 10 min, and (e, f, k, and l) 30 min under (a–f) acidic condition and (g–l) neutral condition.257 Reprinted (adapted) with permission from ref. 257, copyright (2013), Elsevier B.V. All rights reserved. | |
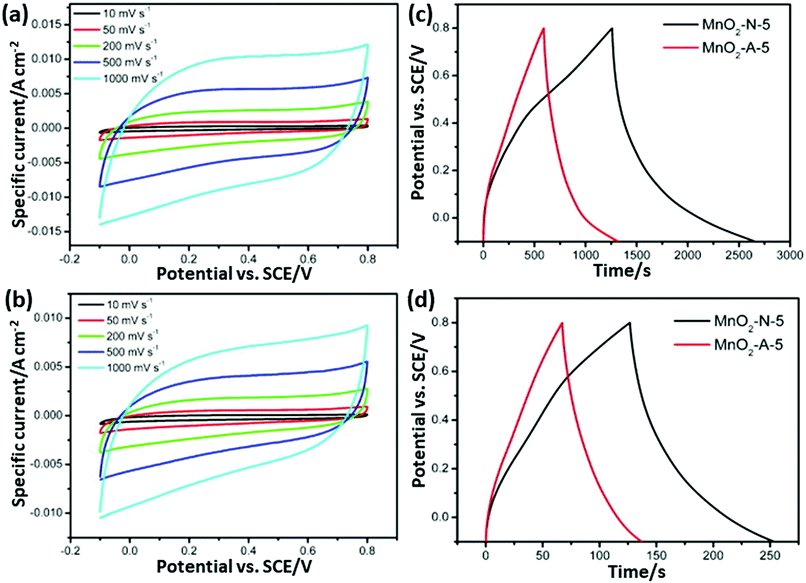 |
| Fig. 16 (a and b) CV curves of MnO2-N-5 and MnO2-A-5 at different scan rates and (c and d) charge/discharge curves of MnO2-N-5 and MnO2-A-5 at current densities of 0.2 A g−1 and 1 A g−1, respectively.257 Reprinted (adapted) with permission from ref. 257, copyright (2013), Elsevier B.V. All rights reserved. | |
Nowadays, researchers are highly focused on the synthesis of electrode materials using MW-assisted methods. The low-cost synthesis of 3D flower-like NiCo microspheres via the MW route without using any template/surfactant under atmospheric pressure for electrode materials in supercapacitors was reported by Li et al.175 The electrochemical analysis showed that the NiCo electrodes exhibited a specific capacitance of 1120 and 996 F g−1 at 1 at 10 A g−1, respectively. After 2000 cycles, the capacitance reached 122.5% of its initial value at 10 A g−1 and retained 93.8% at 30 A g−1 after another 1000 cycles. The asymmetric supercapacitor with NiCo as the positive electrode and activated carbon from coal as the negative electrode exhibited an energy density of 42.5 W h kg−1. Chandrasekaran et al.264 reported the MW-assisted synthesis of mesoporous hollow MnCuAl layered triple hydroxide nanocomposites as electrode materials in symmetrical supercapacitors. The Mn–Cu–Al layered triple hydroxide exhibited 93.46% of its initial capacitance after 5000 cycles. The symmetric solid-state supercapacitor device using Mn–Cu–Al layered triple hydroxide delivered an energy density of 101.75 W h kg−1 at a power density of 900 W kg−1. Xia et al.265 demonstrated the MW-assisted synthesis of layered metal hydroxide nanosheet arrays for aqueous hybrid supercapacitors (Fig. 17a). The Ni(OH)2 nanosheets arrays delivered a capacitance of 2516 and 1273 F g−1 at 1 and 20 A g−1, respectively (Fig. 17b). The Ni(OH)2//activated carbon aqueous hybrid supercapacitor delivered an energy density up to 66.7 W h kg−1 at 400 W kg−1 with cycle stability of 85.2% (Fig. 17c and d).
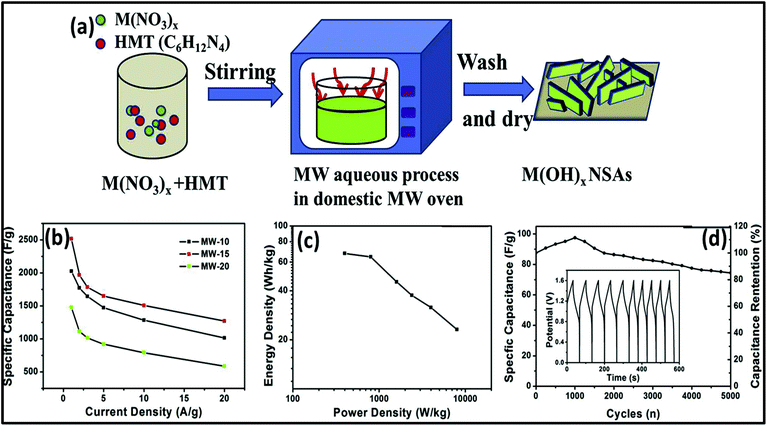 |
| Fig. 17 (a) Schematic of MW-assisted synthesis of layered metal hydroxide nanosheet arrays, (b) specific capacitance vs. current density of Ni(OH)2 nanosheet arrays, (c) Ragone plot and (d) cycle curves of Ni(OH)2 nanosheet arrays//activated carbon aqueous hybrid supercapacitor. Reprinted (adapted) with permission from ref. 265, copyright (2019), Elsevier B.V. All rights reserved. | |
The MW-assisted synthesis of 3D-connected α-Ni(OH)2 sheets as supercapacitor electrode materials was reported by William et al.266 The 3D-connected α-Ni(OH)2 sheet electrodes exhibited a specific capacitance of 549 F g−1 at 2 A g−1 and capacitance retention of 87.3% even after 10
000 charge/discharge cycles. The supercapacitor device (α-Ni(OH)2/polyurethane foam-6 M KOH/activated carbon) delivered an energy density of 57 W h kg−1 at a power density of 601 W kg−1. Fu et al.267 described the MW deposition synthesis of Ni(OH)2/sorghum stalk biomass carbon electrode materials for supercapacitors. Biomass carbon was synthesized using sorghum stalk as the raw material, and Ni(OH)2 was decorated on the sorghum stalk biomass carbon via a MW deposition method, as shown in Fig. 18a. The Ni(OH)2/sorghum stalk biomass carbon exhibited specific capacitances of 889.2 and 490.1 F g−1 at a current density of 2 and 20 A g−1, respectively (Fig. 18b). It showed good stability with the capacitance retention of 95.9% over 30
000 cycles at 20 A g−1 (Fig. 18c).
 |
| Fig. 18 (a) Synthesis of Ni(OH)2/sorghum stalk biomass carbon, (b) specific capacitance of Ni(OH)2/sorghum stalk biomass carbon composite and (c) cyclic property and columbic efficiency of Ni(OH)2/sorghum stalk biomass carbon composite. Reprinted (adapted) with permission from ref. 267, copyright (2020), Elsevier B.V. All rights reserved. | |
The MW-assisted thermal treatment-based synthesis of 3D N-doped graphene coated with ZnO/NiO nanoparticles as electrodes in supercapacitors was suggested by Zhang et al.268 ZnO/NiO nanoparticles with a size in the range of 10–20 nm were anchored on 3D N-doped graphene, which exhibited a specific capacitance of 1839.4 F g−1 at a current density of l A g−1. After 6000 charge/discharge cycles at 10 A g−1, the specific capacitance of the ZnO/NiO/3DNG electrode achieved 93% retention of its initial capacitance. The ZnO/NiO/3D N-doped graphene composite exhibited the maximum energy density of 35.32 W h kg−1 with the power density 139.72 W kg−1 at current density of 10 A g−1. Kim et al.269 described the MW-assisted synthesis of Fe3O4/rGO as a supercapacitor electrode. Crystalline Fe3O4 was dispersed on the surface of rGO nanosheets, which avoided the re-aggregation due to the van der Waals interaction between the neighboring rGO sheets. The Fe3O4/rGO composite showed a specific capacitance of 972 F g−1 at the current density of 1 A g−1, which was higher than that of rGO (251 F g−1) and Fe3O4 (183 F g−1).
The MW approach was employed for the synthesis of NiO/NiS@CNT nanocomposites in 60 s for supercapacitors, which exhibited long cycling stability.270 NiO/NiS@CNT showed a specific capacitance of 809.7 F g−1 at 1 A g−1 and cycling stability of 100% retention after 20
000 cycles at 5 A g−1. In another study, Zheng et al.271 reported the synthesis of NiO/Ni3S2@graphite nanocomposites via MW as a supercapacitor electrode. Graphite flakes were decorated with NiO/Ni3S2, giving the capacitance of 768 F g−1 at 1 A g−1. After 1000 cycles, the NiO/Ni3S2@graphite electrode showed a specific capacitance of 692 F g−1 at 1 A g−1 with a capacitance retention of 90%. The NiO/Ni3S2@graphite and active carbon electrode-based asymmetric supercapacitor exhibited a specific capacitance of 68.5 F g−1 at 1 A g−1, energy density of 28.86 W h kg−1 and power density of 0.77 kW kg−1 with cycling stability of 80% retention after 2000 cycles. Faid et al.272 demonstrated the synthesis of ternary mixed NiCoFeO4 nanorods via an MW process as an asymmetric supercapacitor electrode. The synthesized NiCoFeO4 nanorods showed a specific capacitance of 1263 F g−1 (at 1 A g−1) and cyclic stability of 97.2% capacitance retention after 2000 cycles. The asymmetric supercapacitor using the NiCoFeO4 nanorods exhibited a power density of 10 kW kg−1, energy density of 9.8 W h kg−1, coulombic efficiency of 95.5%, and capacitance retention of 94% after 4000 cycles. Sun et al.273 reported the MW-assisted hydrothermal synthesis of a CNTs@NiMn2O4 core–shell nanocomposite for asymmetric supercapacitors. The schematic representation in Fig. 19a shows the formation of the CNTs@NiMn2O4 core–shell nanocomposite. The CNT@NiMn2O4 core–shell nanocomposite exhibited a specific capacitance 915.6 F g−1 at a current density of 1 A g−1 and cycling stability of 93.0% capacitance retention after 5000 cycles at 5 A g−1 (Fig. 19b). The asymmetric supercapacitor device using CNT@NiMn2O4 as the positive electrode exhibited an energy density of 36.5 W h kg−1 at a power density of 800 W kg−1 with cycling stability of 82.8% capacitance retention after 10
000 cycles at 5 A g−1 (Fig. 19c).
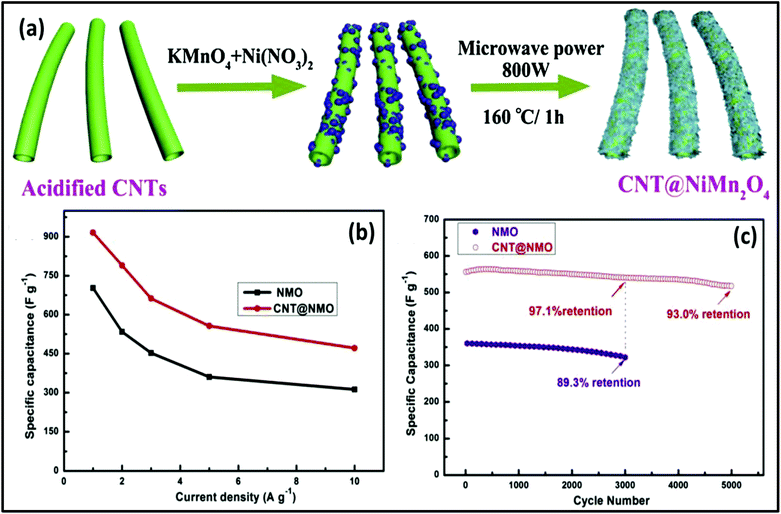 |
| Fig. 19 (a) Schematic representation of the formation of CNT@NiMn2O4 nanocomposite, (b) specific capacitance of NiMn2O4 and CNT@NiMn2O4 nanocomposite at different current densities and (c) cycling stability of NiMn2O4 and CNT@NiMn2O4 nanocomposite at 5 A g−1. Reprinted (adapted) with permission from ref. 273, copyright (2020), Elsevier B.V. All rights reserved. | |
MW-assisted graphene derivatives combined with various types of metal oxides have been used as promising electrode materials for supercapacitors.274–278 The synthesis of V2O5/graphene composites as electrode materials in supercapacitors using the MW method was reported by Fu et al.279 The V2O5/graphene composites were used in symmetrical supercapacitors, demonstrating specific capacitances of 673.2 and 474.6 F g−1 at 1 and 10 A g−1, respectively with 96.8% capacitance retention after 10
000 cycles at 1 A g−1. The assembled supercapacitor devices showed an energy density of 46.8 W h kg−1 and 32.9 W h kg−1 at a power density of 499.4 W kg−1 and 4746.0 W kg−1, respectively. Kumar et al.280 described the synthesis of ZnO nanoparticles anchored on rGO nanosheets via the MW approach for supercapacitor electrodes. The synthesized ZnO@rGO nanocomposite showed a specific capacitance of 102.4 F g−1 at 30 mV s−1 and cyclic stability of 82.5% for 3000 cycles at 100 mV s−1.
4.5. Batteries
MW-assisted synthesis has also been used for the fabrication of materials for battery applications given that it is simple, cost efficient, not time consuming and nanoparticles with different morphologies can be prepared.277 MW-assisted hydrothermal synthesis was employed for the synthesis of nanoflower and nanoparticle spinel of Li4Ti5O12. In this synthesis, LiOH and titanium tetraisopropoxide were used as precursors with water as the solvent. The synthesis was carried out in an MW-assisted hydrothermal system at 130–170 °C with a holding time of 20 min. Subsequently, the product was calcined at 550 °C for 6 h in air. The morphology of both samples prepared at 130 °C and 170 °C was studied, as shown in Fig. 20a–d. It was found that the sample prepared at 130 °C exhibited a flower-like morphology and that prepared at 170 °C consisted of different-sized nanoparticles. The flower dimensions varied from 500–900 nm and the nanoparticle size varied from tens of nanometers to hundreds of nanometers. The surface area measurements indicated the presence of mesoporous and macroporous nanoparticles, and the calculated surface area of the flower was 48 cm2 g−1 and 12.1 cm2 g−1 for the nanoparticles. Fig. 20e and f show the cyclic CV for the nanoflowers and nanoparticles of Li4Ti5O12, respectively. There were two peaks in both cases, which correspond to the reduction and oxidation of Li. There was a significant voltage difference in both cases, and the anodic and cathodic peaks were not symmetrical. This was because of the slow Li insertion and extraction due to bulk spinel, which was formed due to the agglomeration of the nanoparticles. Also, the overlapping of the peaks for the nanoflower signified good reversibility, whereas in case of spinel, there was no overlapping for each cycle. Fig. 21 shows galvanostatic charge/discharge and cyclic stability study. The first discharge capacity for the nanoflowers and nanoparticles reached 176 mA h g−1 and 109.8 mA h g−1 with an irreversible cycling capacity of 14% and 12%, respectively.281 Thus, the MW hydrothermal method is an efficient method for synthesizing materials for application in batteries. Other reports are also available on the MW synthesis of many other types of nanoparticles. Rai et al.282 reported the MW synthesis of NiO nanoparticles, which can act as electrode material in Li-ion batteries (LIBs). It was found that these NiO nanoparticles showed a high discharge capacity of 1111.08 mA h g−1 and maintained 80% of this capacity after 20 cycles.282 Also MW-assisted-synthesized Co3O4 nanoflakes showed a specific capacity of 883 mA h g−1 at a current rate of 0.1C.283 MW-assisted graphene composites with nanoparticles and metal oxides can also be used as electrode materials for LIBs. Baek et al.284 synthesized SnO2 and Fe3O4/graphene nanocomposites via a one-pot MW-assisted non-aqueous sol–gel approach for LIBs. There are many more reports showing that MW-assisted methods have the capability to synthesize efficient electrode materials for LIBs.285,286 MW-assisted-synthesized nanoparticles also showed very good photocatalytic properties. Other authors have also reported similar types of work.287–289
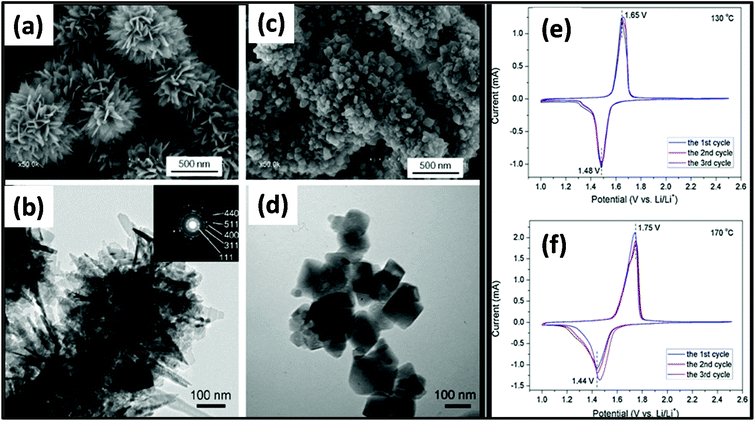 |
| Fig. 20 (a and c) SEM images of Li4Ti5O12 synthesized at 130 °C and (b and d) TEM images of Li4Ti5O12 synthesized at 170 °C. (e and f) CV curves of Li4Ti5O12 prepared at (e) 130 °C and (f) 170 °C in the first three cycles at a scan rate of 0.2 mV s−1.281 Reprinted (adapted) with permission from ref. 281, copyright (2012), Elsevier B.V. All rights reserved. | |
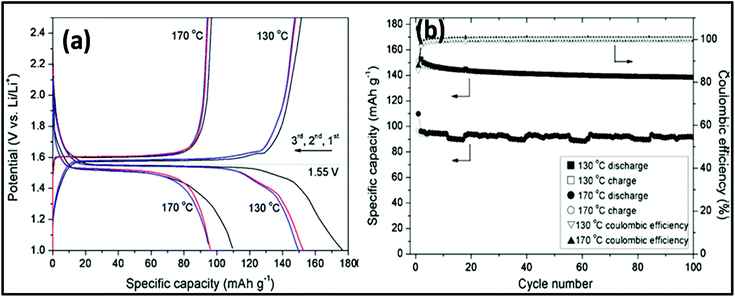 |
| Fig. 21 (a) Galvanostatic charge/discharge curves for Li4Ti5O12 prepared at 130 °C and 170 °C between 1 and 2.5 V at a current density of 200 mA g−1. (b) Cycling performance of Li4Ti5O12 prepared at 130 °C and 170 °C measured at a current density of 200 mA g−1.281 Reprinted (adapted) with permission from ref. 281, copyright (2012), Elsevier B.V. All rights reserved. | |
In recent years, the MW-assisted approach has significantly improved battery technology.290–303 Mainly, for the fabrication of secondary battery electrodes, the MW synthetic route has become highly significant.304–312 Among the various secondary batteries, LIBs are the most popular.313–318 Accordingly, an anode material based on the Co3O4/CeO2 heterostructure was synthesized in an MW digester at a temperature of 100 °C for 1 h for LIB application.319 For this MW synthetic process, a Co–Ce metal–organic framework precursor was used. The anode displayed a high capacity of 1131.2 mA h g−1 at the current density of 100 mA g−1 after 100 charge/discharge cycles. A schematic of the synthesis process and battery performance of the Co3O4/CeO2 heterostructure are shown in Fig. 22. In a recent report, MW-synthesized high-quality rGO exhibited excellent electrochemical performance for application as both an anode and cathode material for LIBs.309 For example, as an LIB anode, the rGO electrode exhibited an enhanced capacity of 750 mA h g−1, and as an LIB cathode, it displayed the promising capacity retention of 70%. In another report, an MW-synthesized composite based on CuC2O4·xH2O and graphene demonstrated excellent electrochemical performances as an anode material for LIB application.312 With 5.42 wt% graphene, the composite demonstrated the superior discharge/charge capacity of 1043/1013 mA h g−1. Further, an MW-assisted solution combustion process was employed for the synthesis of rGO-wrapped Li(Ni1/3Co1/3Mn1/3)O2, which exhibited a discharge capacity of 209.2 mA h g−1.290 In a recent report, a one-step MW heating process was employed for synthesizing micro/nanoscale LiFePO4/graphene, which exhibited the maximum discharge capacity of 166.3 mA h g−1 at the current of 0.1 C.320 The composite was considered a suitable candidate for next-generation cathode material for LIBs. MW synthesis was further extended to produce an LIB anode material based on Ge/GeO2 and graphene.321 The composite exhibited excellent cycling stability.
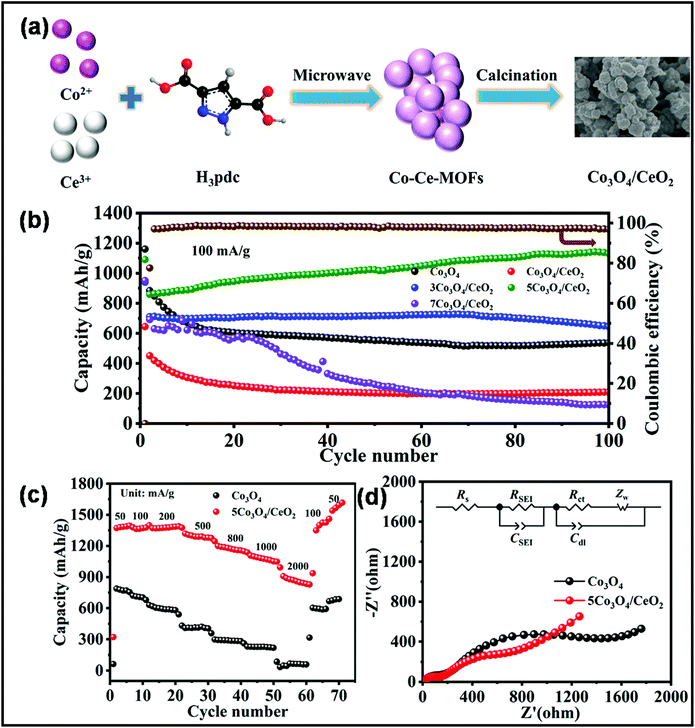 |
| Fig. 22 (a) Schematic illustration of the preparation of Co3O4/CeO2, (b) cycling performance of as-obtained samples at 100 mA g−1, (c) rate performance of Co3O4 and 5Co3O4/CeO2, and (d) Nyquist plots of Co3O4 and 5Co3O4/CeO2 after 100 cycles and the equivalent circuit diagram of the cells.319 Reprinted (adapted) with permission from ref. 319, copyright (2021), Elsevier B.V. All rights reserved. | |
Recently, Tariq et al. proposed an MW-assisted chemical precipitation technique to synthesize composites of LiMn2O4 (LMO), CNTs, and graphene nanoplatelets (GNPs).322 As a cathode material for LIBs, LMO/CNT displayed a discharge capacity of 124 mA h g−1, whereas the LMO/GNP composite exhibited the maximum capacity of 127 mA h g−1 at the current of 0.1 C. A schematic representation of the synthesis process and the corresponding electrochemical performance of these composites are shown in Fig. 23.
 |
| Fig. 23 (a) Schematic of the experimental details for the synthesis of LiMn2O4/CNT/GNP nanocomposite. (b) Galvanostatic charge/discharge behavior of LiMn2O4/GNPs, LiMn2O4-CNTs and pristine LiMn2O4 at 0.1 C and 25 °C (b) 1st cycle and (c) 50th cycle.322 Reprinted (adapted) with permission from ref. 322, copyright (2021), Wiley, All rights reserved. | |
Besides LIBs, the MW approach has also been further extended to Na-ion battery (SIB) applications.323–328 For example, Mao et al.326 reported an MW-assisted glycerol-mediated hydrothermal process for the synthesis of Na3V2(PO4)2F3/carbon nanospheres, which exhibited a capacity of 106 mA h g−1 at the current of 0.5 C after 100 cycles as a cathode material for SIBs. These recent studies on the MW synthetic approach evidently demonstrate its huge impact and extensive potential in modern science and technology.
5. Conclusions, outlook and future prospective
MW-assisted synthesis has many unique features, which makes it a potentially suitable method for large-scale industrial production. MW heating is fast and uniform due to volumetric and dielectric heating, resulting in selective heating processes. In the case of conventional heating, heating is due to conduction and convection and heat transfers from one molecule to another. This phenomenon restricts uniform temperature and is slow. Conversely, MW heating is dielectric heating due to the ions and dipoles in materials, which readily interact with radiation. The delay in the flipping of dipoles and ions while trying to flip their direction with the phase of electromagnetic radiation is called the relaxation time. This relaxation results in the loss of energy, which is liberated in the form of heat. The nature of these interactions is different for different materials. In carbon materials, MW heating involves different mechanisms besides ionic and dielectric heating and involves free electrons. The exposure of MWI to organic reactions is less compared to inorganic materials because of the non-polar nature of organic solvents. MW is used in organic reactions nowadays because the dielectric property varies with temperature and water/other liquids can be used as a solvent at high temperatures. Most of the organic reactions are carried out by MW heating using water as the solvent. Also, many reactions show that the reaction rates and product yield increase in the presence of MWI. Thus, many metal oxides, metal hydroxides, and organic materials have been synthesized by employing MW heating. In the case of carbon materials, generally, heterogeneous nucleation occurs, given that in these composites, the carbon materials act as the substrate during the synthesis. Various shapes, sizes, and morphologies of materials can be controlled easily with MWI. MWI-assisted hydrothermal and solvothermal processes for the synthesis of nanomaterials are less time consuming, which in most cases takes very long for completion. The MW-assisted-synthesized products can be further employed for many energy storage and conversion applications such as supercapacitors, batteries, and photovoltaics. Thus, MWI makes the synthesis of materials much more feasible, cost effective, and selective for commercial applications and large-scale industrial production.
Herein, we delivered a brief, selective, and systematic literature review on the MW-assisted synthesis and energy-related application of carbon nanomaterials and metal oxides/hydroxides. Although ample work has already been done in this hot field, the MW-assisted synthesis process has some drawbacks. Mainly, in terms of commercial aspects, the MW route is still not popular. Among the various energy storage devices, supercapacitors and secondary batteries are considered as the best solutions for the ever-growing demand of future electronics. Accordingly, due to its shorter reaction time, the MW synthetic route has huge potential for the construction of these devices. Besides energy storage devices, the MW approach has been extended to other applications including EMI shielding, wastewater treatment, bio-medical application, fuel cells, and solar cells. Therefore, future advancement in MW chemistry will be highly beneficial for mankind. The future prospective of MW technology is discussed in the next section.
As discussed in the previous section, the MW synthesis approach has several advantages and can be considered as a star technology in the future. However, to make this approach commercially viable, researchers need to focus on few features. The future research on MW technology can be directed towards the follow points
1. The basic mechanism of MW heating has not been clearly understood to date. Thus, more fundamental research on this topic is highly required.
2. For large-scale production, MW technology has several drawbacks. The production of MW reactors for large batches with high yield and excellent repeatability is extremely advantageous.
3. The heating is very fast and the heat transfer to surrounding media (gas or liquid) is relatively slow, and very high temperatures not obtainable under the common thermal equilibrium conditions can be reached. To enhance the uniformity, a proper absorber needs to be chosen and the penetration depth and frequency of the electromagnetic waves controlled. Homogeneous heating can improve the quality of the product.
4. For battery applications, the initial decay in capacity after the 1st cycle is associated with the formation of a solid electrolyte interface (SEI). Future research on carbon nanomaterials should be focused on reducing the formation of the SEI.
5. For supercapacitor applications, the smart combination of EDLC-type (such as carbon nanomaterials) and pseudocapacitive (metal oxide or conducting polymers) materials is highly desirable. MW technology should be broadly extended to combine carbon materials with other suitable materials. It is important to note that recently, the MW approach has been extended towards the development of these smart combinations.
6. Detailed theoretical investigation on isotropic and anisotropic MW heating can open a new door for future research in this field.
Lastly, MW technology is growing exponentially daily. However, still this technology has a way to go for its commercialization.
Conflicts of interest
There are no conflicts to declare.
Acknowledgements
One of the author (R. Kumar) received financial assistance from the Science and Engineering Research Board (SERB), Department of Science & Technology (DST), New Delhi under Ramanujan Fellowship/award (SB/S2/RJN-159/2017).
Notes and references
- M. A. Bagherian and K. Mehranzamir, Energy Convers. Manage., 2020, 224, 113454 CrossRef.
- L. Li, J. Lin, N. Wu, S. Xie, C. Meng, Y. Zheng, X. Wang and Y. Zhao, Energy Built Environ., 2020 DOI:10.1016/j.enbenv.2020.12.002.
- M. S. Nazir, M. Bilal, H. M. Sohail, B. Liu, W. Chen and H. M. N. Iqbal, Int. J. Hydrogen Energy, 2020, 45, 22113–22124 CrossRef CAS.
- K. Ravindra, M. Kaur-Sidhu and S. Mor, Sci. Total Environ., 2021, 145657, DOI:10.1016/j.scitotenv.2021.145657.
- M. M. Vanegas Cantarero, Energy Res. Soc. Sci., 2020, 70, 101716 CrossRef.
- G. Q. Chen, J. S. Li, B. Chen, C. Wen, Q. Yang, A. Alsaedi and T. Hayat, Renewable Sustainable Energy Rev., 2016, 65, 345–355 CrossRef CAS.
- M. E. Munawer, J. Sustainable Min., 2018, 17, 87–96 CrossRef.
- J. Pei, Y. Wen, Y. Li, X. Shi, J. Zhang, R. Li and Q. Du, Constr. Build. Mater., 2014, 72, 41–47 CrossRef.
- K. Yin, A. Ahamed and G. Lisak, Waste Manage., 2018, 78, 401–416 CrossRef CAS PubMed.
- B. Esser, F. Dolhem, M. Becuwe, P. Poizot, A. Vlad and D. Brandell, J. Power Sources, 2021, 482, 228814 CrossRef CAS.
- M. Fu, Z. Zhang, Z. Zhu, Q. Zhuang, W. Chen, H. Yu and Q. Liu, J. Colloid Interface Sci., 2021, 588, 795–803 CrossRef CAS PubMed.
- B. Gang, F. Zhang, X. Li, B. Zhai, X. Wang and Y. Song, J. Energy Storage, 2021, 33, 102132 CrossRef.
- Y. Ge, Z. Liu, Y. Wu and R. Holze, Electrochim. Acta, 2021, 366, 137390 CrossRef CAS.
- O. Gorduk, M. Gencten, S. Gorduk, M. Sahin and Y. Sahin, J. Energy Storage, 2021, 33, 102049 CrossRef.
- Y. He, X. Yuan, G. Zhang, H. Wang, T. Zhang, W. Xie and L. Li, Sci. Total Environ., 2020, 766, 142382 CrossRef PubMed.
- Y. Pan, E. Yu, D. Wang and H. Deng, J. Alloys Compd., 2021, 858, 157662 CrossRef CAS.
- L. Zhang, W. Wang, X. Ma, S. Lu and Y. Xiang, Nano Today, 2021, 37, 101074 CrossRef CAS.
- M. Zhang, W. Zhou and W. Huang, J. Energy Chem., 2021, 57, 291–303 CrossRef.
- L. Zhao, Z. Sun, H. Wan, H. Liu, D. Wu, X. Wang and X. Cui, Electrochim. Acta, 2020, 354, 136718 CrossRef CAS.
- L. Zheng, H. Yang, Y. Bai and C. Wu, J. Energy Chem., 2021, 60, 229–232 CrossRef.
- R. Kumar, E. Joanni, R. Savu, M. S. Pereira, R. K. Singh, C. J. L. Constantino, L. T. Kubota, A. Matsuda and S. A. Moshkalev, Energy, 2019, 179, 676–684 CrossRef CAS.
- R. Kumar, S. Sahoo, E. Joanni, R. K. Singh, W. K. Tan, K. K. Kar and A. Matsuda, Prog. Energy Combust. Sci., 2019, 75, 100786 CrossRef.
- R. Kumar, R. K. Singh, D. P. Singh, E. Joanni, R. M. Yadav and S. A. Moshkalev, Coord. Chem. Rev., 2017, 342, 34–79 CrossRef CAS.
- R. Kumar, E. Joanni, R. K. Singh, D. P. Singh and S. A. Moshkalev, Prog. Energy Combust. Sci., 2018, 67, 115–157 CrossRef.
- R. Kumar, S. Sahoo, E. Joanni, R. K. Singh, R. M. Yadav, R. K. Verma, D. P. Singh, W. K. Tan, A. Pérez del Pino, S. A. Moshkalev and A. Matsuda, Nano Res., 2019, 12, 2655–2694 CrossRef CAS.
- R. Kumar, H.-J. Kim, S. Park, A. Srivastava and I.-K. Oh, Carbon, 2014, 79, 192–202 CrossRef CAS.
- V. S. Avvaru, I. J. Fernandez, W. Feng, S. J. Hinder, M. C. Rodríguez and V. Etacheri, Carbon, 2021, 171, 869–881 CrossRef CAS.
- M. Hu, H. Zhang and R. Lv, Prog. Nat. Sci.: Mater. Int., 2020, 30, 20–27 CrossRef CAS.
- J.-M. Lim, S. Kim, N. S. Luu, J. R. Downing, M. T. Z. Tan, K.-Y. Park, J. C. Hechter, V. P. Dravid, K. He and M. C. Hersam, Matter, 2020, 3, 522–533 CrossRef.
- Q. Wang and W. A. Daoud, J. Power Sources Adv., 2020, 4, 100018 CrossRef.
- J. Wen, D. Zhao and C. Zhang, Renewable Energy, 2020, 162, 1629–1648 CrossRef.
- X. Xu, J. Yang, X. Zhou, S. Jiang, W. Chen and Z. Liu, Chem. Eng. J., 2020, 397, 125525 CrossRef CAS.
- Z. Yang, J. Tian, Z. Ye, Y. Jin, C. Cui, Q. Xie, J. Wang, G. Zhang, Z. Dong, Y. Miao, X. Yu, W. Qian and F. Wei, Energy Storage Mater., 2020, 33, 18–25 CrossRef.
- S. Zhang, B. S. Huang, C. Shi, Q. Xu and Y. Zhu, Colloids Surf., A, 2020, 605, 125243 CrossRef CAS.
- R. Kumar, E. Joanni, R. K. Singh, E. T. S. G. da Silva, R. Savu, L. T. Kubota and S. A. Moshkalev, J. Colloid Interface Sci., 2017, 507, 271–278 CrossRef CAS PubMed.
- J. Bi, H. Wu, L. Wang, X. Pang, Y. Li, Q. Meng and L. Wang, Electrochim. Acta, 2021, 367, 137409 CrossRef CAS.
- Z. Fan, J. Chen, B. Zhang, F. Sun, B. Liu and Y. Kuang, Mater. Res. Bull., 2008, 43, 2085–2091 CrossRef CAS.
- Y. Huang, H. Wang, Y. Jiang and X. Jiang, Mater. Lett., 2020, 276, 128261 CrossRef CAS.
- S. J. Keszei, P. Pekker, C. Fehér, S. Balogh, M. Jakab, L. Nagy and R. Skoda-Földes, Microporous Mesoporous Mater., 2020, 308, 110380 CrossRef CAS.
- R. Kumar, R. Savu, E. Joanni, A. R. Vaz, M. A. Canesqui, R. K. Singh, R. A. Timm, L. T. Kubota and S. A. Moshkalev, RSC Adv., 2016, 6, 84769–84776 RSC.
- J. Lin, L. Sun, Z. Cao, D. Yin, F. Liang, Y. Wu and L. Wang, Electrochim. Acta, 2016, 222, 1716–1723 CrossRef CAS.
- Z. Liu, C. Pan, W. Li, S. Wei, M. Zhang and S. Chen, Electrochim. Acta, 2020, 338, 135897 CrossRef CAS.
- Z. Liu, D. Tian, F. Shen, P. C. Nnanna, J. Hu, Y. Zeng, G. Yang, J. He and S. Deng, J. Power Sources, 2020, 458, 228057 CrossRef CAS.
- G. Qu, Y. Zhou, J. Zhang, L. Xiong, Q. Yue and Y. Kang, iScience, 2020, 23, 101396 CrossRef CAS PubMed.
- R. Kumar, R. K. Singh and D. P. Singh, Renewable Sustainable Energy Rev., 2016, 58, 976–1006 CrossRef CAS.
- N. Wang, Y. Wu, G. Han, H. Song, W. Hou and H. Wang, Diamond Relat. Mater., 2020, 105, 107766 CrossRef CAS.
- H. Wu, L. Lu, Y. Zhang, Z. Sun and L. Qian, Colloids Surf., A, 2016, 502, 26–33 CrossRef CAS.
- P. Zhang, Y. Yang, Z. Ma, Y. Wang, Y. Pan and C. Lu, Mater. Lett., 2016, 164, 421–424 CrossRef CAS.
- R. Kumar, R. K. Singh, P. K. Dubey, D. P. Singh, R. M. Yadav and R. S. Tiwari, Adv. Mater. Interfaces, 2015, 2, 1500191 CrossRef.
- Z. Zheng, Y. Du, Q. Feng, Z. Wang and C. Wang, J. Mol. Catal. A: Chem., 2012, 353–354, 80–86 CrossRef CAS.
- Q. Zhou, M. Bao and X. Ni, Surf. Coat. Technol., 2021, 406, 126660 CrossRef CAS.
- S. M. Youssry, I. S. El-Hallag, R. Kumar, G. Kawamura, A. Matsuda and M. N. El-Nahass, J. Electroanal. Chem., 2020, 857, 113728 CrossRef CAS.
- C. Antonio and R. T. Deam, J. Mater. Process. Technol., 2005, 169, 234–241 CrossRef CAS.
- S. S. R. Geedipalli, V. Rakesh and A. K. Datta, J. Food Eng., 2007, 82, 359–368 CrossRef.
- J. He, Y. Yang, H. Zhu, K. Li, W. Yao and K. Huang, Appl. Therm. Eng., 2020, 178, 115594 CrossRef.
- D. Jain, J. Tang, F. Liu, Z. Tang and P. D. Pedrow, Innovative Food Sci. Emerging Technol., 2018, 48, 274–286 CrossRef CAS.
- S. Taghian Dinani, M. Hasić, M. Auer and U. Kulozik, Food Bioprod. Process., 2020, 124, 121–130 CrossRef CAS.
- H. Zhu, J. He, T. Hong, Q. Yang, Y. Wu, Y. Yang and K. Huang, Appl. Therm. Eng., 2018, 141, 648–658 CrossRef.
- F. Gulisano and J. Gallego, Constr. Build. Mater., 2021, 278, 121993 CrossRef CAS.
- L. Hou, Y. Zhang, L. Chen and X. Wang, LWT, 2021, 139, 110614 CrossRef CAS.
- P. Song, Y. Lei, X. Hu, C. Wang, J. Wang and Y. Tang, J. Colloid Interface Sci., 2020, 574, 421–429 CrossRef CAS PubMed.
- T. A. Thu Dao, H. K. Webb and F. Malherbe, Food Hydrocolloids, 2021, 113, 106475 CrossRef CAS.
- D. Wu, W. Sun, S. Liu and C. Qu, Constr. Build. Mater., 2021, 266, 121180 CrossRef.
- Q. Ye, Z. Peng, G. Li, Y. Liu, M. Liu, L. Ye, L. Wang, M. Rao and T. Jiang, J. Cleaner Prod., 2021, 286, 124919 CrossRef CAS.
- R. K. Singh, R. Kumar, D. P. Singh, R. Savu and S. A. Moshkalev, Mater. Today Chem., 2019, 12, 282–314 CrossRef CAS.
- T. Ichikawa, T. Matsuo, T. Tachikawa, T. Yamada, T. Yoshimura, M. Yoshimura, Y. Takagi, Y. Sawama, J.-i. Sugiyama, Y. Monguchi and H. Sajiki, ACS Sustainable Chem. Eng., 2019, 7, 3052–3061 CrossRef CAS.
- A.-M. Galan, I. Calinescu, A. Trifan, C. Winkworth-Smith, M. Calvo-Carrascal, C. Dodds and E. Binner, Chem. Eng. Process., 2017, 116, 29–39 CrossRef CAS.
- J. Y. Xing, X. L. Song, B. Bai, S. K. Lu and H. P. Liu, Appl. Mech. Mater., 2014, 448–453, 3005–3008 Search PubMed.
- T. Sumi and S. Horikoshi, Radiat. Phys. Chem., 2015, 114, 31–37 CrossRef CAS.
- M. T. Bevacqua, T. Isernia, F. G. Praticò and S. Zumbo, Autom. Constr., 2021, 121, 103426 CrossRef.
- J. Fukushima and H. Takizawa, Mater. Chem. Phys., 2016, 172, 47–53 CrossRef CAS.
- S. Horikoshi, M. Kamata, T. Sumi and N. Serpone, Int. J. Hydrogen Energy, 2016, 41, 12029–12037 CrossRef CAS.
- C. S. Lee, E. Binner, C. Winkworth-Smith, R. John, R. Gomes and J. Robinson, Chem. Eng. Sci., 2016, 149, 97–103 CrossRef CAS.
- D. Nagao, J. Fukushima, Y. Hayashi and H. Takizawa, Ceram. Int., 2015, 41, 14021–14028 CrossRef CAS.
- K. Wang, G. Dimitrakis and D. J. Irvine, Chem. Eng. Process., 2017, 122, 389–396 CrossRef CAS.
- M. B. Gawande, S. N. Shelke, R. Zboril and R. S. Varma, Acc. Chem. Res., 2014, 47, 1338–1348 CrossRef CAS PubMed.
- J. Menéndez, A. Arenillas, B. Fidalgo, Y. Fernández, L. Zubizarreta, E. G. Calvo and J. M. Bermúdez, Fuel Process. Technol., 2010, 91, 1–8 CrossRef.
- R. Kumar, R. Savu, R. K. Singh, E. Joanni, D. P. Singh, V. S. Tiwari, A. R. Vaz, E. T. S. G. da Silva, J. R. Maluta, L. T. Kubota and S. A. Moshkalev, Carbon, 2017, 117, 137–146 CrossRef CAS.
- R. Kumar, E. T. S. G. da Silva, R. K. Singh, R. Savu, A. V. Alaferdov, L. C. Fonseca, L. C. Carossi, A. Singh, S. Khandka, K. K. Kar, O. L. Alves, L. T. Kubota and S. A. Moshkalev, J. Colloid Interface Sci., 2018, 515, 160–171 CrossRef CAS PubMed.
- L. V. Kumar, S. Addo Ntim, O. Sae-Khow, C. Janardhana, V. Lakshminarayanan and S. Mitra, Electrochim. Acta, 2012, 83, 40–46 CrossRef CAS PubMed.
- Z. Q. Tian, X. L. Wang, H. M. Zhang, B. L. Yi and S. P. Jiang, Electrochem. Commun., 2006, 8, 1158–1162 CrossRef CAS.
- A. Bharti, G. Cheruvally and S. Muliankeezhu, Int. J. Hydrogen Energy, 2017, 42, 11622–11631 CrossRef CAS.
- X. Hu, P. Song, X. Yang, C. Wang, J. Wang, Y. Tang, J. Zhang and Z. Mao, J. Taiwan Inst. Chem. Eng., 2020, 115, 272–278 CrossRef CAS.
- L. L. Sikeyi, T. D. Ntuli, T. H. Mongwe, N. W. Maxakato, E. Carleschi, B. P. Doyle, N. J. Coville and M. S. Maubane-Nkadimeng, Int. J. Hydrogen Energy, 2021, 46, 10862–10875 CrossRef CAS.
- S. Mahalingam, S. Ayyaru and Y.-H. Ahn, Chemosphere, 2021, 278, 130426 CrossRef CAS PubMed.
- X. Feng, H. Dai, J. Zhu, L. Ma, Y. Yu, H. Zhu, H. Wang, Y. Sun, H. Tan and Y. Zhang, Int. J. Biol. Macromol., 2021, 171, 1–9 CrossRef CAS PubMed.
- X. Gui, Y. Chen, Z. Zhang, L. Lei, F. Zhu, W. Yang, Y. Guo and M. Chu, Biomaterials, 2020, 248, 120009 CrossRef CAS PubMed.
- H. Jia, T. Wang, W. Chen, S. Ding, T. Luo and Q. Sun, Cold Reg. Sci. Technol., 2021, 184, 103248 CrossRef.
- N. Lee, J. H. Bang, H. W. Kim and H. Jeon, Ceram. Int., 2020, 47(8), 10628–10634 CrossRef.
- M. Ma, Y. Zhang, X. Chen, H. Li, Z. Sui and H. Corke, J. Cereal Sci., 2020, 95, 103072 CrossRef CAS.
- D. Souri, N. Salimi and M. Ghabooli, Inorg. Chem. Commun., 2021, 123, 108345 CrossRef CAS.
- Y. Wang, T. Chen, C. Huang, Y. Wang, J. Wu and B. Sun, J. Electroanal. Chem., 2020, 867, 114181 CrossRef CAS.
- Y. Yin, C. Ma, W. Li, S. Luo, Y. Liu, X. Wu, Z. Wu and S. Liu, Ind. Crops Prod., 2021, 160, 113091 CrossRef CAS.
- X. Zhang, Z. Chen, J. Zhang, X. Ye and S. Cui, Chem. Phys. Lett., 2021, 762, 138127 CrossRef CAS.
- A. Metaxas, Power Eng. J., 1991, 5, 237–247 CrossRef.
- F. Langa, P. de la Cruz, A. de la Hoz, A. Díaz-Ortiz and E. Díez-Barra, Contemp. Org. Synth., 1997, 4, 373–386 RSC.
- E. T. Thostenson and T. W. Chou, Composites, Part A, 1999, 30, 1055–1071 CrossRef.
- S. Chandrasekaran, S. Ramanathan and T. Basak, Food Res. Int., 2013, 52, 243–261 CrossRef CAS.
- Y. Zhang, W. Zhao, B. Li and G. Xie, J. Energy Resour. Technol., 2018, 140(4), 040802 CrossRef.
- J. E. Omoriyekomwan, A. Tahmasebi, J. Dou, R. Wang and J. Yu, Fuel Process. Technol., 2021, 214, 106686 CrossRef CAS.
- P. Chen, Q. Xie, M. Addy, W. Zhou, Y. Liu, Y. Wang, Y. Cheng, K. Li and R. Ruan, Bioresour. Technol., 2016, 215, 163–172 CrossRef CAS PubMed.
- J. E. Omoriyekomwan, A. Tahmasebi, J. Zhang and J. Yu, Energy Convers. Manage., 2019, 192, 88–99 CrossRef CAS.
- J. Sun, W. Wang and Q. Yue, Materials, 2016, 9, 231 CrossRef PubMed.
- D. Stuerga, Microwaves Org. Synth., 2006, 2, 1–59 Search PubMed.
-
H. Fröhlich, 1949, Theory of dielectrics; dielectric constant and dielectric loss, Oxford, Clarendon Press Search PubMed.
- B. Wathey, J. Tierney, P. Lidström and J. Westman, Drug Discovery Today, 2002, 7, 373–380 CrossRef CAS PubMed.
- Y. Ma, E. Vileno, S. L. Suib and P. K. Dutta, Chem. Mater., 1997, 9, 3023–3031 CrossRef CAS.
- M. Oghbaei and O. Mirzaee, J. Alloys Compd., 2010, 494, 175–189 CrossRef CAS.
- D. E. Clark, D. C. Folz and J. K. West, Mater. Sci. Eng., A, 2000, 287, 153–158 CrossRef.
- K. D. Raner, C. R. Strauss, F. Vyskoc and L. Mokbel, J. Org. Chem., 1993, 58, 950–953 CrossRef CAS.
- J. Berlan, P. Giboreau, S. Lefeuvre and C. Marchand, Tetrahedron Lett., 1991, 32, 2363–2366 CrossRef CAS.
- W. C. Sun, P. M. Guy, J. H. Jahngen, E. F. Rossomando and E. G. Jahngen, J. Org. Chem., 1988, 53, 4414–4416 CrossRef CAS.
- D. Stuerga, K. Gonon and M. Lallemant, Tetrahedron, 1993, 49, 6229–6234 CrossRef CAS.
- T. Kim, J. Lee and K.-H. Lee, Carbon Lett., 2014, 15, 15–24 CrossRef.
-
N. Devi, R. Kumar and R. K. Singh, in Graphene Functionalization Strategies: From Synthesis to Applications, ed. A. Khan, M. Jawaid, B. Neppolian and A. M. Asiri, Springer Singapore, Singapore, 2019, pp. 279–311, DOI:10.1007/978-981-32-9057-0_12.
- J.-K. Yang and Y.-M. Wu, Fuel, 1987, 66, 1745–1747 CrossRef CAS.
- S. Marland, A. Merchant and N. Rowson, Fuel, 2001, 80, 1839–1849 CrossRef CAS.
- Z. Fang, C. Li, J. Sun, H. Zhang and J. Zhang, Carbon, 2007, 45, 2873–2879 CrossRef CAS.
- S. Challa, W. Little and C. Cha, J. Microwave Power Electromagn. Energy, 1994, 29, 131–137 Search PubMed.
- K. Wu, T. Ting, G. Wang, C. Yang and C. Tsai, Synth. Met., 2008, 158, 688–694 CrossRef CAS.
- J. Ma, M. Fang, P. Li, B. Zhu, X. Lu and N. Lau, Appl. Catal., A, 1997, 159, 211–228 CrossRef CAS.
- J. Atwater and R. Wheeler, J. Mater. Sci., 2004, 39, 151–157 CrossRef CAS.
- J. E. Atwater and R. R. Wheeler Jr., Carbon, 2003, 41, 1801–1807 CrossRef CAS.
- J. Atwater and R. Wheeler Jr., Appl. Phys. A, 2004, 79, 125–129 CrossRef CAS.
- E. A. Dawson, G. Parkes, P. A. Barnes, G. Bond and R. Mao, Carbon, 2008, 46, 220–228 CrossRef CAS.
- H. Lin, H. Zhu, H. Guo and L. Yu, Mater. Res. Bull., 2008, 43, 2697–2702 CrossRef CAS.
- L. Zhang and H. Zhu, Mater. Lett., 2009, 63, 272–274 CrossRef CAS.
- Y. Yao, A. Jänis and U. Klement, J. Mater. Sci., 2008, 43, 1094–1101 CrossRef CAS.
- J. Menéndez, A. Domínguez, Y. Fernández and J. Pis, Energy Fuels, 2007, 21, 373–378 CrossRef.
- K. Majdzadeh-Ardakani and M. M. B. Holl, Prog. Mater. Sci., 2017, 87, 221–245 CrossRef.
- P. Monsef-Mirzai, M. Ravindran, W. R. McWhinnie and P. Burchill, Fuel, 1995, 74, 20–27 CrossRef CAS.
- A. Mokhlisse, M. B. Chanâa and A. Outzourhit, Fuel, 2000, 79, 733–742 CrossRef.
- A. Zlotorzynski, Crit. Rev. Anal. Chem., 1995, 25, 43–76 CrossRef CAS.
- K. E. Haque, Int. J. Miner. Process., 1999, 57, 1–24 CrossRef CAS.
- D. A. Jones, T. Lelyveld, S. Mavrofidis, S. Kingman and N. Miles, Resour., Conserv. Recycl., 2002, 34, 75–90 CrossRef.
- Y. Fernández, B. Fidalgo, A. Domínguez, A. Arenillas and J. Á. Menéndez, Carbon, 2007, 45(8), 1706–1709 CrossRef.
- B. Fidalgo, Y. Fernández, L. Zubizarreta, A. Arenillas, A. Domínguez, J. Pis and J. Menéndez, Appl. Surf. Sci., 2008, 254, 3553–3557 CrossRef CAS.
- F.-H. Ko, C.-Y. Lee, C.-J. Ko and T.-C. Chu, Carbon, 2005, 43, 727–733 CrossRef CAS.
- Y. Wang, Z. Iqbal and S. Mitra, Carbon, 2005, 43, 1015–1020 CrossRef CAS.
- T. Wei, Z. Fan, G. Luo, C. Zheng and D. Xie, Carbon, 2009, 47, 337–339 CrossRef CAS.
- G. A. Tompsett, W. C. Conner and K. S. Yngvesson, ChemPhysChem, 2006, 7, 296–319 CrossRef CAS PubMed.
-
H. I. Lee, J. H. Kim, S. H. Joo, H. Chang, D. Seung, O.-S. Joo, D. J. Suh, W.-S. Ahn, C. Pak and J. M. Kim, Letters to the Editor, 2007, 45, 2843–2854.
- L. M. Norman and C. Cha, Chem. Eng. Commun., 1995, 140, 87–110 CrossRef.
- P. Monsef-Mirzai, M. Ravindran, W. R. McWhinnie and P. Burchill, Fuel, 1992, 71, 716–717 CrossRef CAS.
- M. B. Chanaa, M. Lallemant and A. Mokhlisse, Fuel, 1994, 73, 1643–1649 CrossRef CAS.
- J. Menéndez, M. Inguanzo and J. Pis, Water Res., 2002, 36, 3261–3264 CrossRef.
- Y. Li, M. A. Malik and P. O'Brien, J. Am. Chem. Soc., 2005, 127, 16020–16021 CrossRef CAS PubMed.
- J. A. Dahl, B. L. Maddux and J. E. Hutchison, Chem. Rev., 2007, 107, 2228–2269 CrossRef CAS PubMed.
- L. Zhang, X. Hai, C. Xia, X.-W. Chen and J.-H. Wang, Sens. Actuators, B, 2017, 248, 374–384 CrossRef CAS.
- D. L. Boxall and C. Lukehart, Chem. Mater., 2001, 13, 806–810 CrossRef CAS.
- J. Liang, Z. Deng, X. Jiang, F. Li and Y. Li, Inorg. Chem., 2002, 41, 3602–3604 CrossRef CAS PubMed.
- R. Harpeness and A. Gedanken, Langmuir, 2004, 20, 3431–3434 CrossRef CAS PubMed.
- J. A. Gerbec, D. Magana, A. Washington and G. F. Strouse, J. Am. Chem. Soc., 2005, 127, 15791–15800 CrossRef CAS PubMed.
- A. B. Panda, G. Glaspell and M. S. El-Shall, J. Am. Chem. Soc., 2006, 128, 2790–2791 CrossRef CAS PubMed.
- S. Kundu, L. Peng and H. Liang, Inorg. Chem., 2008, 47, 6344–6352 CrossRef CAS PubMed.
- H.-Q. Wang and T. Nann, ACS Nano, 2009, 3, 3804–3808 CrossRef CAS PubMed.
- A. F. Zedan, S. Sappal, S. Moussa and M. S. El-Shall, J. Phys. Chem. C, 2010, 114, 19920–19927 CrossRef CAS.
- V. K. LaMer and R. H. Dinegar, J. Am. Chem. Soc., 1950, 72, 4847–4854 CrossRef CAS.
-
K. F. Kelton, in Solid state physics, Elsevier, 1991, vol. 45, pp. 75–177 Search PubMed.
- B. Peters, J. Chem. Phys., 2011, 135, 044107 CrossRef PubMed.
-
N. P. Herring, A. B. Panda, K. AbouZeid, S. H. Almahoudi, C. R. Olson, A. Patel and M. El-Shall, in Metal Oxide Nanomaterials for Chemical Sensors, Springer, 2013, pp. 245–284 Search PubMed.
- I. Bilecka, P. Elser and M. Niederberger, ACS Nano, 2009, 3, 467–477 CrossRef CAS PubMed.
- M. Yada, H. Kitamura, A. Ichinose, M. Machida and T. Kijima, Angew. Chem., Int. Ed., 1999, 38, 3506–3510 CrossRef CAS PubMed.
- R. Si, Y. W. Zhang, L. P. You and C. H. Yan, Angew. Chem., Int. Ed., 2005, 44, 3256–3260 CrossRef CAS PubMed.
- A. B. Panda, G. Glaspell and M. S. El-Shall, J. Phys. Chem. C, 2007, 111, 1861–1864 CrossRef CAS.
- H. Huang, S. Sithambaram, C. H. Chen, C. K. Kithongo, L. Xu, A. Iyer, H. F. Garces and S. L. Suib, Chem. Mater., 2010, 22, 3664–3669 CrossRef CAS.
- Z. Chen, J. Li, Y. Chen, Y. Zhang, G. Xu, J. Yang and Y. Feng, Particuology, 2014, 15, 27–33 CrossRef CAS.
- S. K. Meher and G. R. Rao, J. Phys. Chem. C, 2011, 115, 25543–25556 CrossRef CAS.
- J. Wang, B. Niu, G. Du, R. Zeng, Z. Chen, Z. Guo and S. Dou, Mater. Chem. Phys., 2011, 126, 747–754 CrossRef CAS.
- C.-Y. Cao, W. Guo, Z.-M. Cui, W.-G. Song and W. Cai, J. Mater. Chem., 2011, 21, 3204–3209 RSC.
- A. B. Corradi, F. Bondioli, B. Focher, A. M. Ferrari, C. Grippo, E. Mariani and C. Villa, J. Am. Ceram. Soc., 2005, 88, 2639–2641 CrossRef CAS.
- Y. Zhu, C. Cao, S. Tao, W. Chu, Z. Wu and Y. Li, Sci. Rep., 2014, 4, 5787 CrossRef CAS PubMed.
- J. Fang, M. Li, Q. Li, W. Zhang, Q. Shou, F. Liu, X. Zhang and J. Cheng, Electrochim. Acta, 2012, 85, 248–255 CrossRef CAS.
- C.-C. Hu, C.-T. Hsu, K.-H. Chang and H.-Y. Hsu, J. Power Sources, 2013, 238, 180–189 CrossRef CAS.
- J. Li, M. Wei, W. Chu and N. Wang, Chem. Eng. J., 2017, 316, 277–287 CrossRef CAS.
- Y. Tao, Z. Haiyan, L. Ruiyi, L. Zaijun, L. Junkang, W. Guangli and G. Zhiquo, Electrochim. Acta, 2013, 111, 71–79 CrossRef CAS.
- J. Xu, Z. Ju, J. Cao, W. Wang, C. Wang and Z. Chen, J. Alloys Compd., 2016, 689, 489–499 CrossRef CAS.
- L. Xu, Y.-S. Ding, C.-H. Chen, L. Zhao, C. Rimkus, R. Joesten and S. L. Suib, Chem. Mater., 2008, 20, 308–316 CrossRef CAS.
- Y. Ren and L. Gao, J. Am. Ceram. Soc., 2010, 93, 3560–3564 CrossRef CAS.
- X. Liu, R. Ma, Y. Bando and T. Sasaki, Angew. Chem., 2010, 122, 8429–8432 CrossRef.
- G. Chen, S. S. Liaw, B. Li, Y. Xu, M. Dunwell, S. Deng, H. Fan and H. Luo, J. Power Sources, 2014, 251, 338–343 CrossRef CAS.
- M. Hussein, Z. Zainal and C. Y. Ming, J. Mater. Sci. Lett., 2000, 19, 879–883 CrossRef CAS.
- R. Kumar, W. C. Macedo, R. K. Singh, V. S. Tiwari, C. J. L. Constantino, A. Matsuda and S. A. Moshkalev, ACS Appl. Nano Mater., 2019, 2, 4626–4636 CrossRef CAS.
- R. Kumar, A. V. Alaferdov, R. K. Singh, A. K. Singh, J. Shah, R. K. Kotnala, K. Singh, Y. Suda and S. A. Moshkalev, Composites, Part B, 2019, 168, 66–76 CrossRef CAS.
- N. H. Aminuddin Rosli, K. S. Lau, T. Winie, S. X. Chin and C. H. Chia, Mater. Chem. Phys., 2021, 262, 124274 CrossRef CAS.
- Domga, M. Karnan, F. Oladoyinbo, G. B. Noumi, J. B. Tchatchueng, M. J. Sieliechi, M. Sathish and D. K. Pattanayak, Electrochim. Acta, 2020, 341, 135999 CrossRef CAS.
- A. A. B. Hamra, H. N. Lim, N. M. Huang, N. S. K. Gowthaman, H. Nakajima and M. M. Rahman, J. Mol. Struct., 2020, 1220, 128710 CrossRef CAS.
- S. Liu, S. Sarwar, H. Zhang, Q. Guo, J. Luo and X. Zhang, Electrochim. Acta, 2020, 364, 137320 CrossRef CAS.
- L. Luo, Y. Zhou, W. Yan, X. Wu, S. Wang and W. Zhao, Electrochim. Acta, 2020, 360, 137010 CrossRef CAS.
- C. Miao, X. Yin, G. Xia, K. Zhu, K. Ye, Q. Wang, J. Yan, D. Cao and G. Wang, Appl. Surf. Sci., 2021, 543, 148811 CrossRef CAS.
- P. Periasamy, T. Krishnakumar, V. P. Devarajan, M. Sandhiya, M. Sathish and M. Chavali, Mater. Lett., 2020, 274, 127998 CrossRef CAS.
- K.-d. Seong, X. Jin, D. Kim, J. M. Kim, D. Ko, Y. Cho, M. Hwang, J.-H. Kim and Y. Piao, J. Electroanal. Chem., 2020, 874, 114464 CrossRef CAS.
- Z. Tang, S. Tang, Q. Li, Z. Wei and T. Zhou, J. Colloid Interface Sci., 2021, 582, 312–321 CrossRef CAS PubMed.
- V. M. Vimuna, A. R. Athira, K. V. Dinesh Babu and T. S. Xavier, Diamond Relat. Mater., 2020, 110, 108129 CrossRef CAS.
- F. Zhao, D. Xie, W. Huang, X. Song, M. Aurang Zeb Gul Sial, H. Wu, F. Deng, Q. Zhang, J. Zou and X. Zeng, J. Colloid Interface Sci., 2020, 580, 160–170 CrossRef CAS PubMed.
- F. Zhao, D. Xie, X. Song, H. Wu, Q. Zhang, J. Zou and X. Zeng, Appl. Surf. Sci., 2021, 539, 148260 CrossRef CAS.
- Y. Kim, E.-s. Cho, S.-J. Park and S. Kim, J. Ind. Eng. Chem., 2016, 33, 108–114 CrossRef CAS.
- Y. Lin, D. W. Baggett, J.-W. Kim, E. J. Siochi and J. W. Connell, ACS Appl. Mater. Interfaces, 2011, 3, 1652–1664 CrossRef CAS PubMed.
- A. Loupy, D. Monteux, A. Petit, J. M. Aizpurua, E. Domínguez and C. Palomo, Tetrahedron Lett., 1996, 37, 8177–8180 CrossRef CAS.
- T. J. Imholt, C. A. Dyke, B. Hasslacher, J. M. Perez, D. W. Price, J. A. Roberts, J. B. Scott, A. Wadhawan, Z. Ye and J. M. Tour, Chem. Mater., 2003, 15, 3969–3970 CrossRef CAS.
- S. C. Motshekga, S. K. Pillai, S. S. Ray, K. Jalama and R. W. M. Krause, J. Nanomater., 2012, 2012, 691503 Search PubMed.
- Z. Jian, P. Liu, F. Li, P. He, X. Guo, M. Chen and H. Zhou, Angew. Chem., Int. Ed., 2014, 53, 442–446 CrossRef CAS PubMed.
- J.-Y. Kim, K.-H. Kim, S.-H. Park and K.-B. Kim, Electrochim. Acta, 2010, 55, 8056–8061 CrossRef CAS.
- Y. Guo, H. Wang, C. He, L. Qiu and X. Cao, Langmuir, 2009, 25, 4678–4684 CrossRef CAS PubMed.
- D. Grekov, P. Pré and B. J. Alappat, Renewable Sustainable Energy Rev., 2020, 124, 109743 CrossRef.
- L. L. Sikeyi, T. D. Ntuli, T. H. Mongwe, N. W. Maxakato, E. Carleschi, B. P. Doyle, N. J. Coville and M. S. Maubane-Nkadimeng, Int. J. Hydrogen Energy, 2021, 46(18), 10862–10875 CrossRef CAS.
- H. Eskalen, S. Uruş, S. Cömertpay, A. H. Kurt and Ş. Özgan, Ind. Crops Prod., 2020, 147, 112209 CrossRef CAS.
- P. Kumar, G. Bhatt, R. Kaur, S. Dua and A. Kapoor, Fullerenes, Nanotubes, Carbon Nanostruct., 2020, 28, 724–731 CrossRef CAS.
- M. Pajewska-Szmyt, B. Buszewski and R. Gadzała-Kopciuch, Mater. Chem. Phys., 2020, 242, 122484 CrossRef CAS.
- X. Xia, C.-F. Cheng, Y. Zhu and B. D. Vogt, Microporous Mesoporous Mater., 2021, 310, 110639 CrossRef CAS.
- H. Qiu, X. Sun, S. An, D. Lan, J. Cui, Y. Zhang and W. He, J. Colloid Interface Sci., 2020, 567, 264–273 CrossRef CAS PubMed.
- M. Fu, Z. Zhu, W. Chen, H. Yu and Q. Liu, J. Mater. Sci., 2020, 55, 16385–16393 CrossRef CAS.
- V. Sannasi, K. U. Maheswari, C. Karthikeyan and S. Karuppuchamy, Ionics, 2020, 26, 4067–4079 CrossRef CAS.
- A. Kumar, Y. Kuang, Z. Liang and X. Sun, Mater. Today Nano, 2020, 100076 CrossRef.
- Y. Zhang, Q. Shao, C. Chen, H. Jiang, F. Su, Q. Hu and Z. Guo, Powder Technol., 2020, 370, 226–236 CrossRef CAS.
- M. Hashemzehi, V. Pirouzfar, H. Nayebzadeh and A. Alihosseini, Adv. Powder Technol., 2020, 31, 1470–1479 CrossRef CAS.
- I. M. Gonzaga, A. R. Dória, V. M. Vasconcelos, F. M. Souza, M. C. dos Santos, P. Hammer, M. A. Rodrigo, K. I. Eguiluz and G. R. Salazar-Banda, J. Electroanal. Chem., 2020, 874, 114460 CrossRef CAS.
- J. Cañón, M. Velasquez, R. Molina and S. Moreno, Mol. Catal., 2020, 493, 111080 CrossRef.
- D. Y. Nadargi, M. S. Tamboli, S. S. Patil, R. B. Dateer, I. S. Mulla, H. Choi and S. S. Suryavanshi, ACS Omega, 2020, 5, 8587–8595 CrossRef CAS PubMed.
- K. Kannan, D. Sivasubramanian, P. Seetharaman and S. Sivaperumal, Optik, 2020, 204, 164221 CrossRef CAS.
- N. Thakur and K. Kumar, J. Environ. Chem. Eng., 2020, 8, 104011 CrossRef CAS.
- R. Kumar, S. M. Youssry, K. Z. Ya, W. K. Tan, G. Kawamura and A. Matsuda, Diamond Relat. Mater., 2020, 101, 107622 CrossRef CAS.
- A. J. Khan, M. S. Javed, M. Hanif, Y. Abbas, X. Liao, G. Ahmed, M. Saleem, S. Yun and Z. Liu, Ceram. Int., 2020, 46, 3124–3131 CrossRef CAS.
- K. Rao, K. Mahesh and S. Kumar, Bull. Mater. Sci., 2005, 28, 19–24 CrossRef CAS.
- S. Anandan and J. J. Wu, Mater. Lett., 2009, 63, 2387–2389 CrossRef CAS.
- C.-Y. Cao, Z.-M. Cui, C.-Q. Chen, W.-G. Song and W. Cai, J. Phys. Chem. C, 2010, 114, 9865–9870 CrossRef CAS.
- L.-H. Ai and J. Jiang, Powder Technol., 2009, 195, 11–14 CrossRef CAS.
- H. Wang, J.-Z. Xu, J.-J. Zhu and H.-Y. Chen, J. Cryst. Growth, 2002, 244, 88–94 CrossRef CAS.
- H. Katsuki and S. Komarneni, J. Am. Ceram. Soc., 2001, 84, 2313–2317 CrossRef CAS.
- V. Polshettiwar, B. Baruwati and R. S. Varma, ACS Nano, 2009, 3, 728–736 CrossRef CAS PubMed.
- C. R. Patra and A. Gedanken, New J. Chem., 2004, 28, 1060–1065 RSC.
- K. Wang, T. Huang, H. Liu, Y. Zhao, H. Liu and C. Sun, Colloids Surf., A, 2008, 325, 21–25 CrossRef CAS.
- J.-J. Zhu, J.-M. Zhu, X.-H. Liao, J.-L. Fang, M.-G. Zhou and H.-Y. Chen, Mater. Lett., 2002, 53, 12–19 CrossRef CAS.
- X. Jia, W. He, X. Zhang, H. Zhao, Z. Li and Y. Feng, Nanotechnology, 2007, 18, 075602 CrossRef PubMed.
- A. Phuruangrat, D. J. Ham, S. J. Hong, S. Thongtem and J. S. Lee, J. Mater. Chem., 2010, 20, 1683–1690 RSC.
- X. Hu, J. Gong, L. Zhang and J. C. Yu, Adv. Mater., 2008, 20, 4845–4850 CrossRef CAS.
- F. Bondioli, A. M. Ferrari, C. Leonelli, C. Siligardi and G. C. Pellacani, J. Am. Ceram. Soc., 2001, 84, 2728–2730 CrossRef CAS.
- H. Wu, M. Shao, J. Gu and X. Wei, Mater. Lett., 2004, 58, 2166–2169 CrossRef CAS.
- Y. Liu, Y. Hu, M. Zhou, H. Qian and X. Hu, Appl. Catal., B, 2012, 125, 425–431 CrossRef CAS.
- N. P. Herring, S. H. Almahoudi, C. R. Olson and M. S. El-Shall, J. Nanopart. Res., 2012, 14, 1277 CrossRef.
- Y. Tian, Y. Liu, W.-p. Wang, X. Zhang and W. Peng, Electrochim. Acta, 2015, 156, 244–251 CrossRef CAS.
- S. Yan, H. Wang, P. Qu, Y. Zhang and Z. Xiao, Synth. Met., 2009, 159, 158–161 CrossRef CAS.
- J. Yan, Z. Fan, T. Wei, J. Cheng, B. Shao, K. Wang, L. Song and M. Zhang, J. Power Sources, 2009, 194, 1202–1207 CrossRef CAS.
- M. Li, J. Cheng, J. Fang, Y. Yang, F. Liu and X. Zhang, Electrochim. Acta, 2014, 134, 309–318 CrossRef CAS.
- C. R. Strauss and R. W. Trainor, Aust. J. Chem., 1995, 48, 1665–1692 CrossRef CAS.
- M. A. Surati, S. Jauhari and K. Desai, Arch. Appl. Sci. Res., 2012, 4, 645–661 Search PubMed.
- R. N. Gedye, F. E. Smith and K. C. Westaway, Can. J. Chem., 1988, 66, 17–26 CrossRef CAS.
- R. N. Gedye, W. Rank and K. C. Westaway, Can. J. Chem., 1991, 69, 706–711 CrossRef CAS.
- R. Gedye, F. Smith, K. Westaway, H. Ali and L. Baldisera, Tetrahedron Lett., 1986, 27, 279–282 CrossRef CAS.
- F. Shi, C. Li, M. Xia, K. Miao, Y. Zhao, S. Tu, W. Zheng, G. Zhang and N. Ma, Bioorg. Med. Chem. Lett., 2009, 19, 5565–5568 CrossRef CAS PubMed.
- T. H. Manjashetty, P. Yogeeswari and D. Sriram, Bioorg. Med. Chem. Lett., 2011, 21, 2125–2128 CrossRef CAS PubMed.
- J. Sedelmeier, S. V. Ley, H. Lange and I. R. Baxendale, Eur. J. Org. Chem., 2009, 2009, 4412–4420 CrossRef.
- R. N. Baig and R. S. Varma, Green Chem., 2013, 15, 1839–1843 RSC.
- H. Park, K. Y. Hwang, Y. H. Kim, K. H. Oh, J. Y. Lee and K. Kim, Bioorg. Med. Chem. Lett., 2008, 18, 3711–3715 CrossRef CAS PubMed.
- R. N. Baig and R. S. Varma, Chem. Commun., 2012, 48, 6220–6222 RSC.
- B. R. Vaddula, R. S. Varma and J. Leazer, Eur. J. Org. Chem., 2012, 2012, 6852–6855 CrossRef CAS.
- X. Zhang, X. Sun, H. Zhang, D. Zhang and Y. Ma, Electrochim. Acta, 2013, 87, 637–644 CrossRef CAS.
- S. Vijayakumar, A. K. Ponnalagi, S. Nagamuthu and G. Muralidharan, Electrochim. Acta, 2013, 106, 500–505 CrossRef CAS.
- S. Wang and X. Wang, Electrochim. Acta, 2011, 56, 3338–3344 CrossRef CAS.
- A. Devadas, S. Baranton, T. W. Napporn and C. Coutanceau, J. Power Sources, 2011, 196, 4044–4053 CrossRef CAS.
- R. D. Kumar and S. Karuppuchamy, Ceram. Int., 2014, 40, 12397–12402 CrossRef.
- X. She, X. Zhang, J. Liu, L. Li, X. Yu, Z. Huang and S. Shang, Mater. Res. Bull., 2015, 70, 945–950 CrossRef CAS.
- Y. Lei, J. Li, Y. Wang, L. Gu, Y. Chang, H. Yuan and D. Xiao, ACS Appl. Mater. Interfaces, 2014, 6, 1773–1780 CrossRef CAS PubMed.
- N. I. Chandrasekaran and M. Manickam, Int. J. Hydrogen Energy, 2017, 42, 26475–26487 CrossRef CAS.
- G. Xia and S. Wang, Ceram. Int., 2019, 45, 20810–20817 CrossRef CAS.
- J. J. William, I. M. Babu and G. Muralidharan, Mater. Chem. Phys., 2019, 224, 357–368 CrossRef CAS.
- M. Fu, Z. Zhu, Z. Zhang, Q. Zhuang, W. Chen and Q. Liu, J. Alloys Compd., 2020, 846, 156376 CrossRef CAS.
- M. Zhang, T. Ma, Y. Wang, D. Pan and J. Xie, J. Mater. Sci.: Mater. Electron., 2018, 29, 6991–7001 CrossRef CAS.
- J. Kim, Y. Jung and S. Kim, Carbon Lett., 2019, 29, 411–418 CrossRef.
- Y. Zheng, Y. Tian, S. Liu, X. Tan, S. Wang, Q. Guo, J. Luo and Z. Li, J. Alloys Compd., 2019, 806, 170–179 CrossRef CAS.
- Y. Zheng, Y. Tian, H. Zhang, Q. Guo and J. Luo, Inorg. Chem. Commun., 2019, 110, 107596 CrossRef CAS.
- A. Y. Faid and H. Ismail, Mater. Today Energy, 2019, 13, 285–292 CrossRef.
- Y. Sun, X. Du, J. Zhang, N. Huang, L. Yang and X. Sun, J. Power Sources, 2020, 473, 228609 CrossRef CAS.
- R. Kumar, R. K. Singh, A. R. Vaz, R. Savu and S. A. Moshkalev, ACS Appl. Mater. Interfaces, 2017, 9, 8880–8890 CrossRef CAS PubMed.
- R. Kumar, R. K. Singh, P. K. Dubey, D. P. Singh and R. M. Yadav, ACS Appl. Mater. Interfaces, 2015, 7, 15042–15051 CrossRef CAS PubMed.
- R. Kumar, R. K. Singh, R. Savu, P. K. Dubey, P. Kumar and S. A. Moshkalev, RSC Adv., 2016, 6, 26612–26620 RSC.
- R. Kumar, R. K. Singh, A. V. Alaferdov and S. A. Moshkalev, Electrochim. Acta, 2018, 281, 78–87 CrossRef CAS.
- R. Kumar, M. M. Abdel-Galeil, K. Z. Ya, K. Fujita, W. K. Tan and A. Matsuda, Appl. Surf. Sci., 2019, 481, 296–306 CrossRef CAS.
- M. Fu, Q. Zhuang, Z. Zhu, Z. Zhang, W. Chen, Q. Liu and H. Yu, J. Alloys Compd., 2020, 862, 158006 CrossRef.
- R. Kumar, S. M. Youssry, M. M. Abdel-Galeil and A. Matsuda, J. Mater. Sci.: Mater. Electron., 2020, 31, 15456–15465 CrossRef.
- J. Liu, X. Li, J. Yang, D. Geng, Y. Li, D. Wang, R. Li, X. Sun, M. Cai and M. W. Verbrugge, Electrochim. Acta, 2012, 63, 100–104 CrossRef CAS.
- A. K. Rai, L. T. Anh, C.-J. Park and J. Kim, Ceram. Int., 2013, 39, 6611–6618 CrossRef.
- S. Chen, Y. Zhao, B. Sun, Z. Ao, X. Xie, Y. Wei and G. Wang, ACS Appl. Mater. Interfaces, 2015, 7, 3306–3313 CrossRef CAS PubMed.
- S. Baek, S.-H. Yu, S.-K. Park, A. Pucci, C. Marichy, D.-C. Lee, Y.-E. Sung, Y. Piao and N. Pinna, RSC Adv., 2011, 1, 1687–1690 RSC.
- Y. Wang and J. Y. Lee, J. Power Sources, 2005, 144, 220–225 CrossRef CAS.
- T. Muraliganth, A. V. Murugan and A. Manthiram, Chem. Commun., 2009, 7360–7362 RSC.
- W. Yang, L. Zhang, Y. Hu, Y. Zhong, H. B. Wu and X. W. Lou, Angew. Chem., 2012, 124, 11669–11672 CrossRef.
- P. Kundu, C. Nethravathi, P. A. Deshpande, M. Rajamathi, G. Madras and N. Ravishankar, Chem. Mater., 2011, 23, 2772–2780 CrossRef CAS.
- K. M. Garadkar, L. A. Ghule, K. B. Sapnar and S. D. Dhole, Mater. Res. Bull., 2013, 48, 1105–1109 CrossRef CAS.
- A. Habibi, M. Jalaly, R. Rahmanifard and M. Ghorbanzadeh, J. Alloys Compd., 2020, 834, 155014 CrossRef CAS.
- M. Kheradmandfard, H. Minouei, N. Tsvetkov, A. K. Vayghan, S. F. Kashani-Bozorg, G. Kim, S. I. Hong and D.-E. Kim, Mater. Chem. Phys., 2021, 262, 124265 CrossRef CAS.
- Y. Liu, Y. Zhang, Y. Liu, J. Zhu, Z. Ge, Z. Li and Y. Chen, Carbon, 2021, 173, 809–816 CrossRef CAS.
- S. Pindar and N. Dhawan, Sustainable Mater. Technol., 2020, 25, e00157 CrossRef CAS.
- S. Pindar and N. Dhawan, Process Saf. Environ. Prot., 2021, 147, 226–233 CrossRef CAS.
- P. H. Salame and M. Devakar, Ceram. Int., 2020, 46, 28844–28850 CrossRef CAS.
- A. Uctepe, E. Demir, B. Tekin, B. Dursun, O. Ozturk, O. Sel and R. Demir-Cakan, Solid State Ionics, 2020, 354, 115409 CrossRef CAS.
- S. Wang, Y. Zhu, X. Sun, S. An, J. Cui, Y. Zhang and W. He, Colloids Surf., A, 2021, 615, 126276 CrossRef CAS.
- X. Wang, Z. Liu, Y. Tang, J. Chen, D. Wang and Z. Mao, J. Power Sources, 2021, 481, 228924 CrossRef CAS.
- E. Zhang, B. Wang, J. Wang, H. Ding, S. Zhang, H. Duan, X. Yu and B. Lu, Chem. Eng. J., 2020, 389, 124407 CrossRef CAS.
- J. Zhang, A. Tahmasebi, J. E. Omoriyekomwan and J. Yu, Fuel Process. Technol., 2021, 213, 106714 CrossRef CAS.
- Y. Zhao, B. Liu, L. Zhang and S. Guo, J. Hazard. Mater., 2020, 384, 121487 CrossRef CAS PubMed.
- Y. Zhao, B. Liu, L. Zhang and S. Guo, J. Hazard. Mater., 2020, 396, 122740 CrossRef CAS PubMed.
- N. Zhou, W. Qin, C. Wu and C. Jia, J. Alloys Compd., 2020, 834, 155073 CrossRef CAS.
- Y. Fu, Y. He, Y. Yang, L. Qu, J. Li and R. Zhou, J. Alloys Compd., 2020, 832, 154920 CrossRef CAS.
- M. Liu, Q. Zhao, H. Liu, J. Yang, X. Chen, L. Yang, Y. Cui, W. Huang, W. Zhao, A. Song, Y. Wang, S. Ding, Y. Song, G. Qian, H. Chen and F. Pan, Nano Energy, 2019, 64, 103942 CrossRef CAS.
- C.-H. Lu, N. Naresh, P. S. Kumar and S. Som, Ceram. Int., 2019, 45, 19517–19521 CrossRef CAS.
- Z. W. Lu, Y. H. Wang, Z. Dai, X. P. Li, C. Y. Zhang, G. Z. Sun, C. S. Gong, X. J. Pan, W. Lan, J. Y. Zhou and E. Q. Xie, Electrochim. Acta, 2019, 325, 134920 CrossRef CAS.
- S. Wang, Y. Zhu, X. Sun, H. Liu, J. Cui, Y. Zhang and W. He, Inorg. Chem. Commun., 2020, 121, 108188 CrossRef CAS.
- J. Wu, J. Zhao, B. Vaidhyanathan, H. Zhang, A. Anshuman, A. Nare and S. Saremi-Yarahmadi, Materialia, 2020, 13, 100833 CrossRef CAS.
- S. Yang, F. Ji, Z. Wang, Y. Zhu, K. Hu, Y. Ouyang, R. Wang, X. Ma and C. Cao, Electrochim. Acta, 2019, 324, 134864 CrossRef CAS.
- X. Yang, Y. Tian, S. Sarwar, M. Zhang, H. Zhang, J. Luo and X. Zhang, Electrochim. Acta, 2019, 311, 230–243 CrossRef CAS.
- C. Zhang, B. Zheng, Z. Song, S. Shi and H. Mao, Ceram. Int., 2020, 46, 1018–1025 CrossRef CAS.
- J. C.-Y. Jung, P.-C. Sui and J. Zhang, J. Energy Storage, 2021, 35, 102217 CrossRef.
- P. Lyu, X. Liu, J. Qu, J. Zhao, Y. Huo, Z. Qu and Z. Rao, Energy Storage Mater., 2020, 31, 195–220 CrossRef.
- X. Wang, X. Wei, J. Zhu, H. Dai, Y. Zheng, X. Xu and Q. Chen, eTransportation, 2021, 7, 100093 CrossRef.
- X. Zhang, X. Sun, X. Li, X. Hu, S. Cai and C. Zheng, J. Energy Chem., 2021, 59, 343–363 CrossRef.
- S. Zhao, Z. Guo, K. Yan, S. Wan, F. He, B. Sun and G. Wang, Energy Storage Mater., 2021, 34, 716–734 CrossRef.
- P. Zhu, D. Gastol, J. Marshall, R. Sommerville, V. Goodship and E. Kendrick, J. Power Sources, 2021, 485, 229321 CrossRef CAS.
- Y. Kang, Y.-H. Zhang, Q. Shi, H. Shi, D. Xue and F.-N. Shi, J. Colloid Interface Sci., 2021, 585, 705–715 CrossRef CAS PubMed.
- S. Liu, P. Yan, H. Li, X. Zhang and W. Sun, Front. Chem., 2020, 8, 104 CrossRef CAS PubMed.
- J.-H. Koo and S.-M. Paek, Nanomaterials, 2021, 11, 319 CrossRef CAS PubMed.
- H. A. Tariq, J. J. Abraham, R. A. Shakoor, S. Al-Qaradawi, M. R. Abdul Karim and U. Chaudhry, Energy Storage, 2020, 2, e202 CrossRef CAS.
- B. Dursun, E. Topac, R. Alibeyli, A. Ata, O. Ozturk and R. Demir-Cakan, J. Alloys Compd., 2017, 728, 1305–1314 CrossRef CAS.
- D. Li, D. Yan, J. Ma, W. Qin, X. Zhang, T. Lu and L. Pan, Ceram. Int., 2016, 42, 15634–15642 CrossRef CAS.
- X. Liu, T. Chen, H. Chu, L. Niu, Z. Sun, L. Pan and C. Q. Sun, Electrochim. Acta, 2015, 166, 12–16 CrossRef CAS.
- Y. Mao, X. Zhang, Y. Zhou and W. Chu, Scr. Mater., 2020, 181, 92–96 CrossRef CAS.
- W. Qin, T. Chen, T. Lu, D. H. C. Chua and L. Pan, J. Power Sources, 2016, 302, 202–209 CrossRef CAS.
- Z.-J. Zhang, Y.-X. Wang, S.-L. Chou, H.-J. Li, H.-K. Liu and J.-Z. Wang, J. Power Sources, 2015, 280, 107–113 CrossRef CAS.
|
This journal is © The Royal Society of Chemistry 2021 |
Click here to see how this site uses Cookies. View our privacy policy here.