DOI:
10.1039/C9TC05710B
(Perspective)
J. Mater. Chem. C, 2020,
8, 441-463
Realising the potential of thermoelectric technology: a Roadmap
Received
18th October 2019
, Accepted 27th November 2019
First published on 28th November 2019
Abstract
All machines from jet engines to microprocessors generate heat, as do manufacturing processes ranging from steel to food production. Thermoelectric generators (TEGs) are solid-state devices able to convert the resulting heat flux directly into electrical power. TEGs therefore have the potential to offer a simple, compact route to power generation in almost every industrial sector. Here, in a Roadmap developed with wide-ranging contributions from the UK Thermoelectric Network and international partners, we present the science and technology that underpins TEGs. We outline how thermoelectric (TE) technology capable of generating power outputs from microwatts to tens/hundreds kW, and potentially to MW, can have an impact across a wide range of applications in powering devices, ranging from medical to building monitoring, the internet of things, transportation and industrial sectors. The complementary application of TE technology in cooling affords additional opportunities in refrigeration and thermal management. Improved waste-heat harvesting and recovery and more efficient cooling offer significant opportunities to reduce energy usage and CO2 emissions. We provide an overview of the key challenges associated with the development of new materials and devices that offer higher power output, while matching TE solutions to the wide range of applications that would benefit from energy harvesting. There is an existing supply chain to develop, manufacture and integrate thermoelectric devices into a broad range of end-user sectors all with global market potential: the full realisation of which will require new state-of-the-art manufacturing techniques to be embraced in order to drive down costs through high-volume manufacturing to widen the application base.
1. Introduction
1.1 Energy and power generation
1.1.1 Energy and greenhouse gases.
The Paris climate agreement of 20151 on energy has the objectives to reduce greenhouse gas emissions by at least 20% compared to 1990 levels (Fig. 1) or by 30%, if the conditions are right (provided that other developed countries commit themselves to comparable emission reductions and that developing countries contribute adequately according to their responsibilities and respective capabilities); to increase the share of renewable energy sources in our final energy consumption to 20%; and to achieve a 20% increase in energy efficiency. Recent estimates are that ca. 37% of greenhouse gas (GHG) emissions are from the power generating sector with a further 17% (marginally less than the total for transportation including automotive) coming from manufacturing industries, with energy-intensive industries such as steel making being the biggest contributors.
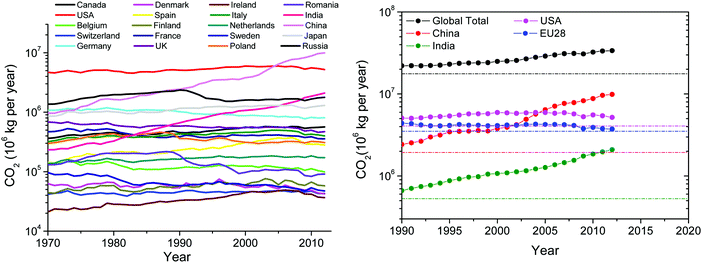 |
| Fig. 1 Left – CO2 emissions per year for selected EU 28 countries compared to major economies; right – CO2 emissions per year since 1990 for the major world economies, relative to the target of a 20% reduction from 1990 levels by 2020. The plots have been generated from data in ref. 2. | |
There is enormous potential to make significant efficiency savings in these sectors by recovering useful energy from waste heat, reducing the demand for externally supplied electrical power and the greenhouse gas emissions that arise from its generation.
1.1.2 Heat recovery and cooling: the scale of the challenges – waste heat and cooling.
All machines from jet engines to microprocessors generate heat, as do manufacturing processes ranging from steel to food production. For example, up to 60% of energy in the internal combustion engine is wasted as heat (with transportation already noted above as a significant source of CO2 emissions), and in Europe typically 8% of the greenhouse gas (GHG) emissions are from heavy duty vehicles, a percentage which is predicted to increase to 30% as other sectors reduce emissions.3
An analysis of industrial waste heat3 (Fig. 2) reveals that 80% of industrial waste heat is released as a heated gas at temperatures between 373 and 573 K. Removal of heat is frequently a priority in cooling of electronics, computer warehouses and in air conditioning. The latter is a major consumer of energy (around 10% across Europe), as is chilling of food where an estimated 29% of a typical hypermarket's energy is used in chillers.4
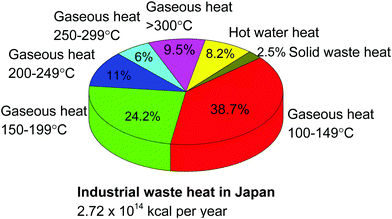 |
| Fig. 2 Waste heat distribution for industry. (Adapted from ref. 3.) | |
Conventional methods to convert heat energy use rotating ‘Rankine cycle’ machinery (e.g. pumps or turbines) but can be difficult to scale efficiently and require maintenance. Waste heat and inefficient cooling represent unnecessary GHG emissions, although it should be noted that some energy loss is necessary to maintain a non-zero heat flow. For example, maximum power output in an efficient power plant approaches the Curzon–Ahlborn efficiency5
, lower than the theoretical maximum given by the Carnot efficiency (1 − Tc/Th), owing to the finite rate of heat exchange between the working fluid and heat reservoirs. Recovered energy is generally used to lower the associated system power input, but waste heat energy is increasingly being investigated for applications ranging from industrial scale processes to the powering of wireless sensors, relevant for the internet of things (IoT). Estimates of the waste heat inventory are difficult to compile, but taking the UK as an example, energy consumption by sector (illustrated in Fig. 3) indicates that heat recovery in transportation applications (including road, commercial, public and private, rail and marine) would be especially attractive.
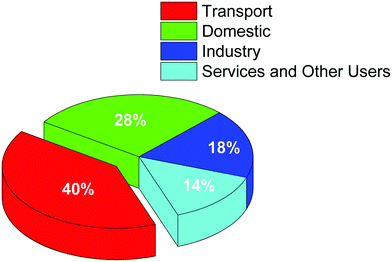 |
| Fig. 3 UK energy consumption by sector. (Data taken from ref. 6.) | |
1.1.3 Benefits of the solid state approach using thermoelectrics.
Thermoelectric generators (TEGs) are solid-state devices that convert a heat flux directly into electrical power and therefore have the potential to offer a simple, compact solution. TEGs can also operate in reverse and effect cooling upon passage of an electric current (known as the Peltier effect). TEGs are made mostly from semiconducting, inorganic compounds. They have no moving parts and can be retrofitted to existing waste-heat sources or integrated into the total system. They are readily scalable from electronic chip-size to tens/hundreds kW units. The operating conditions of the application determine the type of materials used and the device design. They can be very reliable and are the power-conversion source of choice in hostile environments such as remote pumping stations for oil pipelines and space satellites. They also have considerable potential for off-grid electricity generation.
1.2 The Seebeck and Peltier effects
The thermoelectric phenomenon is the conversion of heat energy into electrical energy, and vice versa, using solid-state materials. If a temperature gradient (dT) exists across two dissimilar materials (a and b) which are in contact then a potential difference (dV) is generated between the free ends of the circuit. This is described by the Seebeck effect. The Seebeck coefficient (α) is defined by: |  | (1) |
If the generated dV is applied across some external electrical resistance a current will flow, and the Seebeck effect provides the basis of a power generation mode; the reverse process of passing a current through a thermoelectric to extract heat is the basis of the refrigeration mode (Fig. 4).
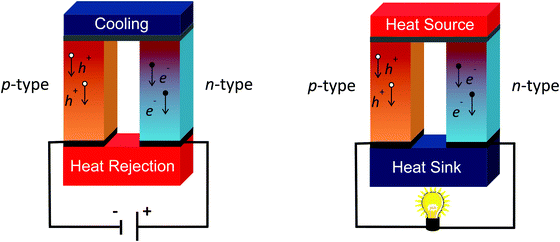 |
| Fig. 4 A representation of the TE effect in (left) a Peltier cooler and (right) a TE generator. Charge carriers move from one end of the thermocouple, carrying entropy and heat towards the other end. Both n- and p-type materials are necessary for a complete device. | |
The efficiency of a thermoelectric device is directly related to the performance of the semiconducting materials from which it is composed. The materials’ performance is embodied in a dimensionless figure of merit, ZT, incorporating the Seebeck coefficient (S), electrical conductivity (σ) and thermal conductivity (κ), which may be formulated as:
|  | (2) |
The thermal conductivity has contributions both from charge carriers (
κe) and lattice vibrations (
κL). High performance requires a large Seebeck coefficient and low thermal conductivity, characteristic of non-metallic systems, to be combined with a high electrical conductivity, more usually found in metallic phases. Consequently
S,
σ and
κ cannot be optimized independently, presenting a challenge in the design of high-performance materials. The best compromise is generally found in semiconducting materials with charge carrier densities in the range 10
19–10
20 cm
−3. Traditionally, device efficiency (
η) is calculated approximately (using the materials figure of merit) by:
| 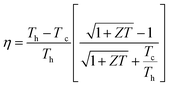 | (3) |
where
Th/
Tc is the temperature of the hot/cold junction and
ZT is the average for the device over the temperature range
Tc to
Th. An increase in the average
ZT over the temperature range of operation of the device has a more marked impact on efficiency than merely increasing the maximum figure of merit of the component semiconductors. However, it is necessary to distinguish between
ZT for the material and
ZT for the device (indicated by bold italic text here). Snyder and Snyder
7 demonstrated that for a finite temperature difference (
Th −
Tc) the thermoelectric device
ZT, based on any type of material, is given by:
| 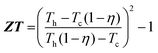 | (4) |
where the maximum efficiency
η is calculated from the temperature dependent properties
S(
T),
σ(
T) and
κ(
T) between the hot side and cold side temperatures. Some form of spreadsheet calculation is required to generate the final efficiency value.
1.3 Designing for thermoelectric applications
The most commonly used technique to characterize thermoelectric generators (TEGs) at the module level involves maintaining a constant temperature gradient across the device while varying the electrical load conditions. Typically a manufacturer will provide a set of curves for different temperature differences (50 °C, 100 °C, 200 °C, 300 °C, etc.) showing the variation in output power and load voltage with output current. This “constant temperature” approach disregards the variation of the heat flux through the TEG due to the parasitic Peltier effect which is proportional to the load current. From a designer's perspective it is usually desirable to operate the TEG system at its maximum power point (MPP), i.e., when the load resistance is matched to that of the module; the condition defined by the maximum power transfer theorem. However, this condition is formed from a purely electrical point of view and it does not consider any thermal interactions in the TEG system that may be influenced by the Peltier contribution to the heat flow.
Typically the hot-side energy source available for TEG application is “limited” waste heat, therefore the temperature gradient across the module will not remain constant. This means that the conditions used to characterize TE modules are not comparable with the operational conditions of the TEG when integrated in a real system. Because of this, there may be significant mismatches in the TEG performance predictions between characterization and application and the inclusion of the Peltier effect on the system performance is essential for determination of actual system operation.
If such a “constant heat” characterization is performed with the conditions of a TEG integrated in an application, the impact of the parasitic Peltier effect on power generation can be quantified and then reduced by operating the module at a lower current. This will lead to an increase in the temperature gradient across the module and hence also overall power generation (since power is proportional to V2) compared to the values predicted using only the maximum power transfer theorem condition.
Generally some form of electrical conditioning is required between the variable output voltage of the TEG and the fixed voltage requirement of the load. This is accomplished using a power converter which attempts to extract the maximum amount of energy from the TEG module. In order to implement the latest high performance MPP algorithms, the power converter requires information of the TEG temperature.
In order to get the best possible performance from the TEG module the correct mounting of the device in the thermal system is essential. The following general guidelines are widely accepted:
• The hot and cold-side heat exchangers should be flat (<0.05 mm) and polished for heat transfer (roughness < 1 μm). Heat exchanger surfaces should be parallel to one another.
• The recommended clamping pressure depends on the thermal transfer compound and is 1.1 MPa (175 kg for a 40 × 40 mm module) for graphite. Achieving the required pressure can be challenging for weight-sensitive applications (e.g. automotive).
• Graphite coating on the module faces offers the best long-term performance since it does not dry out at high temperature. Modules are available without a graphite coating if thermal grease is to be used. This offers a slight (<3%) reduction in output power but with approximately half the clamping pressure.
• Gap fillers with a thermal conductivity of >2 W m−1 K−1 are not recommended and are likely to lead to significantly reduced output power from the system.
1.4 Inorganic materials
1.4.1 Factors in materials selection.
Current commercial TE devices are composed of Bi2Te3 appropriately doped to produce the required n- and p-type variants. Whilst offering good performance at temperatures close to ambient, there are two principal factors associated with Bi2Te3 that limit future applications.
Abundance.
Tellurium is a relatively scarce element, with a terrestrial abundance of ca. 1 ppb. A recent analysis, (Periodic Table of Endangered Elements) conducted by the Chemistry Innovation KTN identifies tellurium as one of the top 9 “at risk elements”,8 while it has also been identified as a critical mineral by the US Government.9 Terrestrial reserves have been estimated at ca. 30
000 Mt, which would make large-scale adoption of telluride-based thermoelectric technology difficult. Tellurium is obtained (but not always separated) as a by-product of copper ores. Therefore its availability is also limited. Coupled with a rising demand for tellurium from other technologies, including photovoltaic, these factors provide a strong driver for the development of new TE materials comprised of earth-abundant elements.
Performance.
Bi2Te3-Based devices exhibit a maximum ZT that approaches unity at temperatures in the range 350 ≤ T/K ≤ 450. This equates to efficiency of the order of 2–3% for energy harvesting applications. At higher temperatures, the figure of merit falls off markedly and Bi2Te3 melts at 853 K. Given the wide range of hot-side temperatures for energy harvesting applications, there is a need to develop a portfolio of materials, with thermoelectric properties optimized to the temperature range of the application.
In creating new materials for the applications outlined in Section 4, a number of additional materials constraints apply. These include:
Materials stability.
Under operating conditions, TE devices are subjected to significant temperature gradients for extended periods. The component materials need to be stable with respect to both oxidation and sublimation under such conditions. These demands increase as the hot side temperature is raised. Given the inherent instability with respect to aerial oxidation of many advanced TE materials, the complementary development of protective coatings is likely to be a priority.
Scalable production.
Many of the applications identified in Section 3 will require high production volumes of TE devices. Conventional metallurgy is unlikely to provide the large quantities of material required, particularly where protective (inert gas or vacuum) environments are required during production. Mechanochemical alloying is likely to play an increasing role in scalable production of TEs, whilst solution-based methods offer an attractive alternative in favourable cases.
Processability of the powders.
Bi2Te3 is produced by a melt-based process, although the congruently-melting composition is bismuth-rich. This necessitates tellurium-enrichment of the melt to produce the intrinsic semiconducting, stoichiometric phase, potentially leading to compositional inhomogeneities. By contrast, many of the advanced thermoelectric materials recently discovered do not melt congruently, precluding synthesis form the melt. Such materials are therefore generally produced in powder form. Consequently, device fabrication requires consolidation of the powders into ingots, from which thermoelements may be cut. Consolidation methods are required that produce mechanically-robust ingots with the appropriate microstructure. Moreover, the methodology needs to be scalable. This will require the extension of hot pressing and Spark Plasma Sintering methods to larger ingots and the application of novel manufacturing methods, developed in other sectors, including 3D printing, aerosol deposition and capacitive discharge sintering.
Availability of compatible n- and p-type materials.
Thermoelectric module performance is determined by the thermoelectric properties of the n- and p-type materials of which it is composed. High performance requires both n- and p-type legs to exhibit comparable figures of merit. The availability of complementary n- or p-type materials frequently imposes a barrier to the construction of next-generation modules. In addition to well-matched physical properties, the thermal expansion coefficients of the n- and p-type materials need to be comparable in order to avoid the introduction of stresses under the operating conditions of the device. Flexible contacts may offer a way of alleviating this problem.
1.4.2 Materials design strategies.
Advances in the understanding of the relationship between chemical composition, structure (over multiple length scales) and thermoelectric properties has led to the emergence of a number of materials design strategies that will guide the search for new high performance materials. Many of these seek to achieve a degree of separation between the electrical and thermal contributions to the figure of merit.
These strategies include:
Phonon-glass electron crystal (PGEC).10.
Localized vibrational modes of weakly bound atoms introduced into vacant sites within a semiconducting framework, serve to scatter heat-carrying phonons. This provides a means of reducing the lattice component of the thermal conductivity (κL) without impacting negatively on the electrical transport properties of the framework.
Nanoinclusions and nanocomposites.11,12.
Compositional inhomogeneities within a semiconducting matrix can create endotaxially-embedded nanoinclusions. These scatter acoustic phonons with no significant impact on the charge carriers. A variant of this method is the introduction of nanoparticles of a second phase to form a physical mixture with a thermoelectric material of proven performance, prior to consolidation. This can produce significant reductions in thermal conductivity.
Grain boundary engineering.13.
The increasing realization of the importance of microstructure on thermoelectric properties has led to significant efforts to manipulate the scattering of heat-carrying phonons at grain boundaries, including selective precipitation of a second phase at grain boundaries. Dense dislocation arrays formed at low-energy grain boundaries scatters mid-frequency phonons with a minimal effect on electron transport.
Band structure modification.14.
Improvements in thermoelectric power factor have been targeted through band engineering to increase the valley degeneracy, Nv. The resulting increase in carrier mobility enhances the TE properties. High Nv is favoured by high symmetry and a small energy separation between bands of different character: chemical substitution provides a means of tuning this separation. In an alternative approach, the introduction of post-transition-series impurity atoms can lead to perturbations in the density of states of a semiconductor through the creation of resonant states, which leads to significant enhancements in the figure of merit.
Phonon-liquid-electron-crystal (PLEC).15.
At elevated temperatures, highly mobile ions can assume a liquid-like state within an otherwise rigid crystalline matrix. The resulting disorder induces significant reductions in the lattice contribution to the thermal conductivity (κL), without impacting negatively on the electrical properties. However, concerns that the high ionic mobility can lead to migration of the mobile species to the electrodes and hence degradation of the material, as a result of the potential difference created, need to be addressed if PLECs are to be implemented.
Energy filtering.16.
The concept is that carriers with a mean energy substantially below the Fermi level are “filtered” by potential barriers and hence do not contribute to transport, enabling a reduction in electrical conductivity and improvement in Seebeck coefficient to be acheived. It was believed to be most effective when the distance between the potential barriers are comparable to the carrier mean free path. In recent years there has been less support for the mechanism, and in some cases alternative explanations have been proposed.17
Low-dimensionality.18.
Structures of reduced dimensionality exhibit a more highly structured density of states (DOS) than conventional bulk 3D materials. Theoretical work indicates that significant enhancements in the Seebeck coefficient may be realised by tuning the Fermi level to sharp discontinuities in the DOS. The increased scattering of phonons resulting from the larger number of interfaces associated with low dimensionality has perhaps a greater beneficial impact on thermoelectric performance.
These design strategies can be applied to a wide range of materials, with properties that are matched to the different temperatures of operation. The emphasis on materials containing Earth-abundant elements will grow. Increasingly, we are likely to see a combination of approaches adopted that simultaneously address the electronic and thermal contributions to the figure of merit. The range of advanced TE materials includes:
1.4.3 Bulk inorganic materials.
While it is not the intention to provide a comprehensive survey of inorganic materials that are under investigation, the principal categories of inorganic material (Table 1), together with their key features, are briefly outlined in this section. In-depth coverage of the families of materials identified here, is provided by a number of recent review articles19–25 to which the reader is referred for further information.
Table 1 Thermoelectric figures of merit for representative examples of the families of thermoelectric materials
TE family |
Representative examples |
n/p |
Peak ZT |
Temperature of maximum ZT/K |
Chalcogenides26 |
Bi2Te3−xSex |
n |
1.15 |
370 |
AgPb18SbTe20 |
n |
2.2 |
800 |
Pb0.96Sr0.04Te doped with Na |
p |
2.2 |
915 |
Cu10.5NiZn0.5Sb4S13 |
p |
1.03 |
723 |
Cu5FeS4 |
p |
0.55 |
543 |
|
Oxides27 |
LaCrO3 |
p |
0.14 |
1600 |
La0.15Sr0.775TiO3−δ |
n |
0.41 |
973 |
Zn0.98Al0.02O |
n |
0.3 |
1272 |
Ca3Co3.9Fe0.1O9 |
p |
0.39 |
1000 |
|
PLEC phases26 |
Cu2−xSe |
p |
1.5 |
1000 |
Cu2−xS |
p |
1.7 |
1000 |
Cu7PSe6 |
p |
0.35 |
575 |
|
Oxy-chalcogenides26 |
Bi0.875Ba0.125CuSeO |
p |
1.4 |
923 |
BiOCu0.975Se |
p |
0.81 |
923 |
Bi0.975Cu0.975SeO |
p |
0.84 |
750 |
|
Skutterudites28 |
Ba0.08La0.05Yb0.04Co4Sb12 |
n |
1.7 |
850 |
Yb0.25La0.60Fe2.7Co1.3Sb12 |
p |
0.99 |
700 |
|
Intermetallics29 |
Yb14MnSb11 |
p |
1.04 |
1228 |
YbZn0.4Cd1.6Sb2 |
p |
1.2 |
700 |
Zn4Sb3 |
p |
1.3 |
673 |
|
Clathrates30 |
Ba8Ge16Ge30 |
n |
1.35 |
900 |
Ba8Ge16Al3Ge27 |
p |
0.61 |
760 |
Yb0.5Ba7.5Ga16Ge30 |
n |
1.1 |
950 |
|
Half-Heuslers31 |
TiNiSn |
n |
0.4 |
775 |
Zr0.3Hf0.65Ta0.05NiSn |
n |
0.85 |
870 |
Hf0.44Zr0.44Ti0.12CoSb0.8Sn0.2 |
n |
1.0 |
1073 |
|
Silicon–germanium alloys32 |
Si0.8Ge0.2 doped with P |
n |
1.3 |
1173 |
Si0.8Ge0.2 doped with B |
p |
0.95 |
1223 |
|
Metal silicides32 |
Mg2Sn0.7Si0.3 doped with Sb |
n |
1.3 |
700 |
Mg1.86Li0.14Si0.3Sn0.7 |
p |
0.5 |
750 |
MnSix (1.71 ≤ x ≤ 1.75) |
p |
0.6 |
800 |
Chalcogenides.
These are amongst the most studied TE materials. In addition to Bi2Te3 at the heart of commercial modules, PbTe has been considered a candidate for high-temperature operation. Recent work has focused on endotaxially embedded nanoinclusions in PbTe, exemplified by the LAST-m phases, leading to figures of merit in excess of 1.5 at high temperatures. The need for alternatives containing earth-abundant elements has led to figures of merit approaching unity for the corresponding binary selenides and sulphides. Environmental concerns surrounding lead have motivated extension to the tin congeners. SnSe exhibits an exceptional figure-of-merit, although concerns have been expressed about the reproducibility of the result. Chalcogenides for operation in the mid-range of temperatures include a variety of layered and pseudo-layered materials for which ZT ≈ 0.5 may be attained.
Drawing inspiration from the world of minerals, synthetic derivatives of tetrahedrite have been shown to exhibit ZT ≈ 1.0 at 700 K. Mineral chemistry may provide a rich vein of potential thermoelectric materials in the future. Work on synthetic derivatives has already included those of shandites, colusites, argyrodites and bornites.
PLECs.
The observation of ZT = 1.5 at 1000 K in the superionic conductor Cu2−xSe has stimulated work on copper-containing chalcogenides more generally. In particular, efforts are being made to create materials in which substantial reductions in thermal conductivity arising from copper-ion mobility can be achieved without the detrimental effects on device performance that arise from ionic conductivity.
Oxides.
Metal oxides offer advantages for high-temperature applications, owing to their stability in air at elevated temperatures and ready abundance. Their ionic nature results in a relatively low electrical conductivity. The challenge is to improve the electrical properties without impacting negatively on thermal conductivity. Typically this involves doping a stoichiometric phase. Substitution in the perovskite SrTiO3 has been widely studied. The insights into composition–structure–property relationships that have emerged from wide-ranging investigations of perovskites for non-TE applications suggest considerable opportunities for the discovery of new TE phases. Other oxide TE phases include a range of layered cobaltites, the structures of many of which are incommensurate, which itself has a beneficial impact on thermal transport properties.
Oxy-chalcogenides.
Mixed anion compounds have received limited attention as potential thermoelectrics. The differing bonding preferences of oxide and chalcogenide ions leads to ion segregation and the creation of two-dimensional building blocks. The more ionic oxide units favour low thermal conductivity, while covalency promotes high mobility semiconduction. Whilst the thermal conductivity is low, efforts are required to improve the electrical properties through chemical substitution. ZT ≈ 0.8 has already been realised by judicious substitution. There is considerable scope for exploration of new structure types containing alternative oxide/chalcogenide building blocks to the fluorite/antifluorite that have formed the basis of the majority of investigations to date.
Skutterudites.
This family of materials, derived from CoSb3, represents a realization of the PGEC concept. The key feature of skutterudites is the presence of a large cavity, into which weakly bound guest species can be placed. In addition to effecting reductions of almost an order of magnitude in thermal conductivity, through localised vibrational modes (termed rattling modes), guest species transfer electrons to the framework. Therefore optimization of the framework composition is often required in order to maximise the figure of merit. Filler atoms of different mass and size exhibit different resonance frequencies. Multiple filling scatters heat-carrying phonons over a wider energy range, producing even greater reductions in thermal conductivity. The maximum figures of merit of singly filled materials exceed unity, whilst multiple filling leads to ZT = 1.7. The maximum figures of merit tend to occur at temperatures in the range 700–900 K, making the materials candidates for power generation in the intermediate to high temperature range. This includes applications in the automotive sector. Chemical substitution can be used to produce both n- and p-type variants, providing chemically-compatible legs (thermoelements) for a device. At high temperatures, oxidation and/or sublimation of antimony may occur, leading to significant degradation of performance under the operating conditions of a device. The development of protective coatings should be a high priority to facilitate exploitation of skutterudite-based devices.
Intermetallics.
Zintl phases possess complex crystal structures in which electron transfer between an electropositive species such as a rare-earth or alkaline earth atom and a complex anion of electronegative main-group elements confers salt-like characteristics. Investigation of the thermoelectric properties of Zintl phases is at a comparatively early stage. Initial results suggest that they are promising candidates for high temperature materials (Yb14MnS11 exhibits ZT ≈ 1 at 1200 K for example) as the exceptionally low lattice thermal conductivity is sufficient to overcome performance limitations that would otherwise arise from a low electronic mobility.
Generally the maximum figures of merit are observed at high temperatures (>1000 K). Synthesis is often challenging as high temperatures and extended reaction times are required; induction heating enables synthesis to be carried out from the molten elements at ∼2400 K. Narrow phase boundaries limit the accessible range of carrier concentrations, whilst the creation of chemically-compatible n- and p-type components can be problematic.
Clathrates.
These intermetallic phases possess a cage-like structure of main-group metal atoms with electropositive species incorporated within the cage. In this respect they have parallels with skutterudites, whilst the bonding is described in terms of the Zintl concept analogous to the intermetallics outlined above. From a thermoelectric perspective, the important phases are those termed ‘type I’ of general formula A8E46, which include those containing the more earth-abundant elements, silicon and aluminium. The materials are narrow band-gap semiconductors. The A cations exhibit rattling type vibrations and the materials offer another example of PGEC behaviour, with thermal conductivities typically below 2 W m−1 K−1. Both n- and p-type clathrates may be prepared. Figures of merit for polycrystalline materials are typically in the range of ZT = 0.7–0.9, with higher values being attained for single crystals. The maximum figures of merit are achieved at 800–900 K, making them suitable for energy recovery in the intermediate to high temperature range.
Half Heuslers.
Bonding in the intermetallic half-Heusler compounds, X(YZ) where X, Y and Z are respectively an electropositive element, a transition-series element and a main-group element, can also be considered within the framework of Zintl compounds. Unusually from a thermoelectric perspective, the half-Heuslers exhibit relatively high thermal conductivities (3–4 W m−1 K−1), which are compensated by large power factors (up to 6 mW m−1 K−2) leading to figures of merit in the region of unity in the range 700–900 K with suitable doping. The majority of high performance materials are n-type, although p-type behaviour has also been observed. There is significant scope to improve the thermoelectric performance by reducing the thermal conductivity. Adoption of a hierarchical approach to phonon scattering across multiple length scales is necessary. Phase segregation can be induced during synthesis from high-temperature melts using an appropriate heating/cooling profile, thereby introducing compositional inhomogeneities, which have a beneficial effect on thermal conductivity. The existence of competing binary and Heusler phases can lead to uncertainties in composition, sample homogeneity and reproducibility and TE properties that are sensitively dependent on sample processing.
Si–Ge alloys.
Silicon is the second most abundant element in the earth's crust making TE materials based on silicon attractive candidates for large-scale implementation of the technology. However, the thermal conductivity of elemental silicon is extremely high (148 W m−1 K−1), although it can be reduced through the addition of ca. 30% of germanium. Silicon–germanium alloys are used in radioisotope thermoelectric generators for deep-space probes. Both n- and p-type variants can be produced, with respective figures of merit reaching 1.0 and 0.7. Efforts to improve the thermoelectric performance of silicon have focused on reducing the thermal conductivity through methods such as nanocompositing with a second phase, or by grain size reduction to increase phonon scattering.
Nanostructuring leads to enhancements in the figures of merit; n- and p-type derivatives reaching ZT = 1.3 and 0.95 at very high temperatures (ca. 1200 K). In addition to the high temperatures required for maximum performance, the inclusion of the expensive element germanium significantly increases the material cost, to a level which is likely to be prohibitive to implementation in anything other than niche applications. Efforts are therefore required to reduce the germanium content in the alloys while retaining similar levels of performance.
Metal silicides.
The ready availability of silicon has led to an investigation of TE properties of materials in which it is combined with other Earth-abundant elements. Alkaline-earth silicides show promising n-type behaviour. Doping of Mg2Si leads to ZT in the range 0.5–0.7, whilst band engineering through alloying with the corresponding stannide has raised the figure of merit to 1.3 at 700 K. In addition to issues associated with fabrication, arising from the brittleness of the materials, the principal limitation on alkaline-earth silicides is the absence of a compatible p-type analogue that exhibits comparable performance over the same range of temperatures: lithium-doped Mg2(Si,Sn) being amongst the best with ZT = 0.5 at 750 K. In the search for new high-performance materials, the net has widened to encompass transition-metal silicides. Manganese silicides, suitably doped with main-group or transition-series elements, exhibit a peak ZT = 0.4–0.6. Of the other transition-metal silicides investigated to date, rhenium silicide exhibits good n-type behaviour, although the cost of rhenium is likely to be prohibitive. Metal silicides are ripe for further exploration and optimisation, particularly through band engineering and nanostructuring.
1.5 Organic thermoelectrics
1.5.1 Introduction.
Organic thermoelectric materials (OTEs) are emerging candidates for TE applications. They are characterised by their low thermal conductivity, mechanical flexibility, elemental abundance and their solubility which enables manufacture by scalable printing techniques (inkjet, slot-die, roll-to-roll etc.). Whilst it seems unlikely in the near term that OTE materials will replace inorganics in standard device architectures, they lend themselves towards certain non-conventional geometries and applications not accessible by incumbent technology.
1.5.2 Target applications.
Lower power factors (PFs) and ZT than their inorganic counterparts mean that organic OTEGs are candidates for low-power applications near room temperature where their other properties are beneficial (flexibility, shock resistance, processability, sensing, biocompatibility, low toxicity etc.).
Two such application areas that have been identified are:
• Power sources for wireless sensor networks and internet of things (minimum power requirements 70 μW; ΔT = 25 °C, operating temperature: 40–250 °C, area: 1–10 cm2). ΔT for this application could come from water pipes and hot surfaces (Fig. 5a).
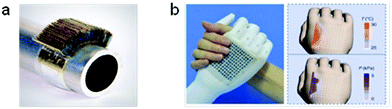 |
| Fig. 5 (a) A printed and folded OTEG wrapped around a hot water pipe; (b) a self-powered dual pressure–temperature sensor patch on a prosthetic arm. (Image by F. Zhang, et al., Nat. Commun., 2015, 6, 8356 under licence CC BY 4.0.) | |
• Body-centred autonomous microelectronics (minimum power requirements 70 μW; ΔT = 5 °C, operating temperature: 37 °C, output voltage: 10 mV, area: 1–10 cm2). It is notable that IMEC, Belgium developed a wireless electroencephalography system with sub-microWatt power consumption that was powered by a TEG.33
In addition self-powered sensors may also be realised where the OTE material used to generate power is also sensitive to pressure, temperature, humidity, biological markers etc. A self-powered dual temperature–pressure sensitive “e-skin” based on OTE materials is one example of this (Fig. 5b34).
1.5.3 Current materials and properties.
p-Type.
The current state-of-the-art for p-type OTEs is poly(3,4-ethylenedioxythiophene) (PEDOT) which has ZT of up to 0.4 when doped with polystyrene sulfonate (PSS),35 Being air-stable and processable from water solution, PEDOT:PSS is compatible with industrial processes.
n-Type.
The current state-of-the-art n-type OTE are organometallic coordination polymers, in particular poly(Ni-ethylenetetrathiolate). These show PFs >400 μW m−1 K−2 and ZT of 0.30 at room-temperature. The material is air-stable, but non-soluble and so doesn’t have the processing advantages offered by other organic materials.
Composites.
The limiting parameter for organic thermoelectric materials is typically the electrical conductivity (σ < 1000 S cm−1 for OTE). Nonetheless organic materials can easily be processed with more conductive materials such as carbon nanotubes or graphene.36 These can achieve significantly higher power factors (several 10s μW m−1 K−2) at the expense of ZT37 (i.e. for higher power devices with lower efficiency).
1.6 Thin-film thermoelectric generators
Bi2Te3 and Sb2Te3 are the archetypal thermoelectric materials which have shown their worth for decades in Peltier devices. They have the highest ZT values of any material in the temperature range of room temperature to about 200 °C and have a long track record of development and optimisation. An ideal sweet spot exists for these material types in thin-film energy harvesting TE micro-generators for smart, possibly flexible, IoT applications including medical applications related to harvesting of body heat.
The figure-of-merit of thermoelectric materials, ZT, which determines their efficiency, does not contain any geometrical parameters and thin-film thermoelectrics could generate large amounts of energy. Furthermore, the possibility of nanoscale devices is theoretically predicted to lead to significant enhancement of the ZT value and experimental confirmation of the effects of quantum confinement is a key scientific driver. In terms of applications, a difficulty for thin-film TEGs is to ensure that parasitic effects are minimized and that system performance approaches that for material and device properties. Due to the scales involved, the interfacial effects also play a large role. These can be beneficial, where direct deposition of TEs onto substrates leads to very good thermal coupling, or detrimental where interfacial reactions between substrate and TE during processing or use, decrease the thermal coupling.
In particular, thermal conductivity has to be lower than the ZT trade-offs suggest to ensure that the temperature drops over the TE material. Furthermore, the geometry can bring problems. Whereas for bulk TEGs, the TE legs are separated by air or other gasses, in thin film TEGs electrical insulators with considerable thermal conductivity might be required as substrates. Lastly the contacts to the metal connections, both electrically and thermally, have to be optimized to enable thin film TEGs to be of practical use in more than niche applications. Examples of thin film thermoelectrics are shown in Fig. 6 and 7.
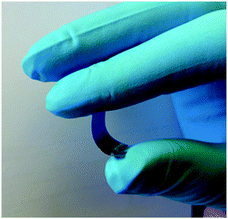 |
| Fig. 6 A piece of flexible, thin-film silicon. (Image used with permission of Dr N. Bennett, Heriot Watt University.) | |
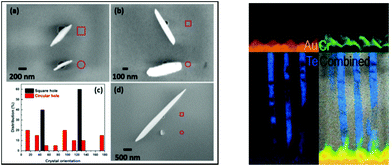 |
| Fig. 7 (left) Oriented Bi2Te3 nanosheets produced by selective chemical vapour deposition (right) nanowires of Te (diameter 10 nm) by supercritical fluid electrodeposition. (Images by R. Huang et al., 2016, Sci. Rep., 6, 27593, under licence CC BY 4.0.) | |
2. MODULES
2.1 Device manufacture considerations
Architecture.
Thermoelectric modules are typically arranged in the standard vertical or ‘π’ formation with n-type and p-type thermoelements or ‘legs’ arranged electrically in series and thermally in parallel (Fig. 8). There are electrodes on the hot side and cold side with the material chosen dependent on the thermoelectric material used. Module design is typically defined by the leg length, L, and aspect ratio – the ratio, r, of the leg length to the leg cross sectional area, A.
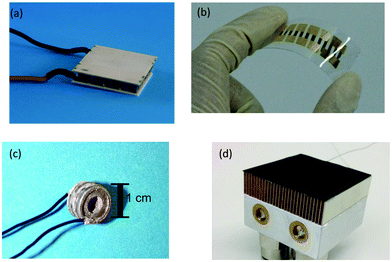 |
| Fig. 8 Arrangements of thermoelements: (a) standard ‘π’-type geometry;38 (b) flexible array.39 (Image reproduced from Philos. Trans. R. Soc., A, 2014, 372, 20130008 with permission of The Royal Society); (c) annular structure.40 (Image used with permission of Prof. G. Min, University of Cardiff); (d) stack structure.41 (Image reproduced from Mater. Today: Proc., 2015, 2, 538–547, with permission from Elsevier.) | |
The other main arrangement of thermoelectric elements is the lateral formation which is typically used for flexible thin film module designs. There are other more experimental designs including annular; concentric rings arranged around a pipe for extracting waste heat energy; and ‘stack’, layers of thermoelectric sheet materials joined together (see Fig. 8 for examples).
Module geometry.
This is an important consideration when designing a system for TE energy generation. If there is a plentiful source of heat energy available, then a low-aspect-ratio design with short legs can be utilised to maximise the power generated. This does however come at the expense of efficiency. If limited heat energy is available, a high-aspect-ratio design can be used to maximise efficiency at the expense of power generation. Another consideration is the power-to-material-volume ratio. If exotic materials with a limited abundance are used to create a module, it may be economically beneficial to reduce the volume of the legs whist maintaining the same aspect ratio, so as to conserve the module performance. A balance must be obtained; if the volume of the thermoelements is too small then thermal contact resistance and electrical resistance may start to impact on module power output and efficiency.
Electrically insulating substrate.
Commercial bismuth telluride modules typically have top and bottom plates made from aluminium oxide but AlN/Si3N4 has also been used for niche applications. The substrate serves two purposes, (i) to isolate the thermoelement pairs and (ii) provide structural support of the legs within the module. Thin film organic/inorganic modules typically use novel substrates such polyimide films or anodized aluminium which allows printing of the module electrodes on top of the insulating layer.
Thermally insulating encapsulation material.
Although commercial bismuth telluride modules used for Peltier cooling tend not to be encapsulated (working temperatures are typically less than 100 °C), TEG modules employ thermal insulation, as the hot-side working temperature can easily reach 200–300 °C. Oxidation of the thermoelectric materials and the solders is a possibility as well as the loss of TE material due to vaporisation, both of which can lead to the long-term degradation of performance. Higher temperature modules require more extreme encapsulation methods such as ceramic fillers, aerogels or full metallic or ceramic encapsulation.
Joining materials.
The choice of joining material is dependent on the operating temperature of the module, with the maximum operating temperature typically 50–100 °C less than the melting point of the joining material. For operating temperatures less than 450 °C, lead-free solders are usually employed; for temperatures above 450 °C a braze is utilised. Copper and nickel electrodes typically employ a silver-based braze while aluminium electrodes require an aluminium-based braze. Joining materials need to be carefully chosen to avoid thermal stresses. To prevent the diffusion of material between the electrode and solder, barrier layer coatings are employed.
Electrical contact resistance.
This is a key consideration when designing modules since it represents a loss mechanism that can reduce the output of modules. The contact resistance is usually multiplied by the cross-sectional area of the leg to give the specific contact resistance (SCR). The SCR is dependent on a number of factors such as the materials composition and operating temperature and the choice of bonding materials and barrier layers are important factors when considering long-term performance of the module.
Thermal contact resistance.
Thermal contact resistance can influence the performance of a thermoelectric module both in Seebeck and Peltier mode. Any significant gaps resulting in air pockets at the interface between the module and heat exchanger can dramatically reduce heat conduction. Surface polishing is one possible solution but this is expensive and time consuming. Alternatively, thermal transfer pastes can be employed; they can be easily applied and provide a close contact between the two surfaces. Pastes do have a limited operating temperature and may degrade with time. Consequently, the use of a graphite interface layer is increasingly preferred by module manufacturers.
2.2 Current module research
Low temperature.
Bulk (flexible).
A team lead by Öztürk42 has developed a novel concept based on the standard thermoelectric architecture but that is completely flexible. Bismuth telluride based legs are connected by electrodes which are made of an indium–gallium eutectic which is liquid under ambient conditions. The legs and electrodes are encapsulated and held in place by an elastomer which allows complete flexibility and has been shown to have self-healing properties if an electrical connection becomes damaged. The intended use is for a non-intrusive power supply generating electrical power from body heat to supply medical devices. Currently the limitation on the device is the low power generated. This could be improved through improving the thermal conductivity of the elastomer.
Printed thermoelectrics.
Thanks to the advances in printing technology (2-D and 3-D) it is now possible to print thermoelectric modules accurately in a two stage process. The first stage is to take an ink which has the thermoelectric material in suspension and print onto the substrate. Subsequent layers can then be added to form the 3-D printed structure. The second stage is to sinter the thermoelectric material together to form a mechanically strong and electrically conducting material which maintains the thermoelectric properties. In principle it should also be possible to print the electrodes and the insulating layer which would simplify the manufacture of modules considerably.
Mid temperature.
There is a large volume of research and manufacture into devices that operate in the mid-temperature range by companies, research organisations and universities all over the world. Table 2 provides a selective highlight of the main material systems from which modules are being produced and gives examples of where they have been integrated into an applied test system. The Fraunhofer IPM (Germany), are currently taking materials developed in the lab and up-scaling to industrial-scale prototyping of thermoelectric modules. They are investigating two material systems, skutterudites and half-Heuslers and have invested in large scale Spark Plasma Sintering (SPS) and Pick and Place technologies to produce 160 modules in a single test batch. This holistic approach supports the transition from materials development to full-scale application testing and is supporting industry in the implementation of future technologies.
Table 2 Some example manufacturers and systems installed for various mid-temperature systems
Material system |
Typical operating range/°C |
Selected module manufacturers and efficiencies |
Selected systems installed and power output/W |
Alphabet energy ceased trading in 2018.
|
Tetrahedrites–magnesium silicide |
200–600 |
Alphabet energya 5% @ T = 300 K43 |
Alphabet energy claims a system produces 900 W of power from a hot gas temperature of 550 °C and flow rate of 9 m3 min−1 |
|
Skutterudites |
300–600 |
NASA 8% @ T = 400 K44 Marlow 7% @ T = 460 K45 Fraunhofer 7% @ T = 430 K46 |
NASA eMMRTG system can produce 145 W. |
BMW have installed a 57 W system |
|
Half Heuslers |
300–700 |
Fraunhofer 5–6% @ T = 530 K47 |
200 W generator tested by Evident Thermoelectrics |
|
PbTe-TAGS |
200–600 |
NASA 6% @ T =330 K44 |
NASA have installed a 110 W RTG system on two space missions. |
300 W generator tested by BMW. |
Segmented modules.
Segmented modules hold great promise for enhanced efficiency for a given temperature difference. Typical ZT for a given material peaks over a narrow temperature range with the average ZT over the temperature range being much lower. As discussed in Section 2.2 an increase in the average ZT over the temperature range of operation has a greater impact on efficiency than increases in the maximum ZT. It is possible to improve the average ZT by using a combination of thermoelectric materials joined together in the leg structure, thereby producing higher efficiencies. However, forming a segmented module is a complicated process with different materials having different thermal and mechanical properties. Without careful design, stress points could appear in the module under operating conditions. Although joints are typically the strongest part of a module, the region directly next to the joint is a potential failure point. The more joints present in a module, the greater the chance of a mechanical failure. NASA has led the way in developing segmented couples, with their skutterudite–Bi2Te3 systems, with an efficiency of 13.5% reported.48 Lidong Chen's group in China has recently published an efficiency of 12% for a skutterudite:Bi2Te3 module.49 The AIST group in Japan report an efficiency of 7.5% for a clathrate single crystal/Bi2Te3 segmented module with a power output of 0.87 W and a hot side temperature of 380 °C.50
High temperature.
Si–Ge has long been established as the material system to use at high temperatures of 600–1000 °C (and above) since its development for radioisotope thermoelectric generators (RTGs) in the Voyager space missions. Subsequently this system has been used in automotive waste heat recovery (Nissan, Japan) but was found to be limited in its usefulness due to the lower average operating temperatures of automotive engines.51 Further enhancement in the ZT value at lower temperatures, or the use of segmentation, is required to make Si–Ge commercially viable.
Another contender for high temperature applications are the ceramic oxide material systems. Most of the research is still at the laboratory stage but commercial modules are now becoming available with reasonable power outputs but limited efficiencies. TECTEG MFR have a ceramic metal oxide TEG available which is capable of generating 12.3 W at a temperature difference of 750 K (hot side temperature 800 K).52
3. Thermoelectric applications
3.1 Automotive/internal combustion applications/challenges
The principal application areas for TE in the light duty (passenger car and light freight vehicles) are respectively HVAC (heating ventilation and air conditioning) and WHR (waste heat recovery) from engine systems, and in particular the engine exhaust flow. The relative simplicity of the TE architecture is a good match to the passenger53 car application where increases in complexity and mass carry a high penalty.
HVAC systems may consume up to 3 kW of engine power to support the refrigeration pump and air circulation. Proposals for TE based systems will use devices to heat or cool the incoming air and to manage the temperature of surfaces close to the vehicle occupants.
Proposals for WHR visualise a heat exchanger in the exhaust gas flow with heat transfer to ambient air or engine coolant. Limitations include the very high temperatures that can occur under transient conditions, elevated back pressure applied to the engine and interference with the temperature distribution required for treatment of the exhaust gas.
In heavy duty and larger applications of engines (above 300 kW rated power output), TE technologies face a stiffer challenge. The lifetime fuel consumption of such engines usually exceeds twenty times their value which opens up a wider range of technology options that includes Rankine cycle and supplementary expansion of exhaust gases. However, the solid state and distributed nature of TE power supplies is attractive as a solution for wireless sensor networks in high value applications of engines such as marine, power generation and locomotives. Similarly, even with the anticipated reduction in the numbers of new petrol and diesel cars from 2040 there will still be significant opportunities for TE power in hybrid and related vehicles for several decades.
While the pressure for fuel economy varies as fuel costs vary, the need to meet the requirements of carbon dioxide emissions legislation currently provides the greatest pressure on the light-duty sector. TEGs are mentioned in both the EU2021 CO2 regulations and the US EPA/NHTSA 2025 Fuel Economy/CO2 regulations. In both cases they are referred to as ‘off-cycle’ credits, meaning potential additional credits which cannot be measured on the formal test cycles (credits here refer to the calculated reduction in fleet emissions). In both Europe and United States TE is only one of a series of possible measures that passenger car manufacturers can adopt to meet the new requirements.
Recent activity in the UK has included the Innovate UK funded VIPER and VIPER2 projects (Fig. 9). See for example Brennan et al.54 for comments on the challenges facing the design of heat exchangers. EU funded projects in which UK organisations have played a role include PowerDriver (2012–2014) and more recently, Integral (started 2017) and Ecochamps (2016–2018). Experience from the VIPER project suggested that cost projections for a TEG based on Bi2Te3 were too high to make for a viable product.
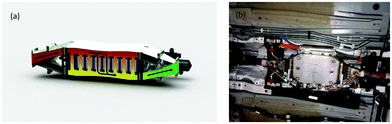 |
| Fig. 9 (a) Image of VIPER2 thermoelectric module for vehicle application, (b) VIPER2 module fitted to underside of test vehicle. (Images courtesy of the Innovate UK funded VIPER2 programme and used with permission.) | |
While VIPER used bismuth telluride (Bi2Te3) and VIPER2 used metal silicide materials as the thermoelectric element, a consortium made up of Reading, Cardiff and Loughborough Universities (UKTEG) worked under EPSRC funding to develop skutterudite materials for the WHR application. The particular attraction of skutterudite materials is their ability to work at normal engine exhaust temperatures. The result of this work included n and p forms of material well matched to the exhaust temperatures of a small passenger car engine.55 Power output predictions over formal test cycles suggest average outputs of 300–500 W with a heat exchange architecture that still has the potential for significant improvement.
It is clear from the VIPER and UKTEG experience that new manufacturing techniques are needed to facilitate the kind of heat-exchanger architectures that will be cost effective through being well matched to the conditions of the engine exhaust. From recent work on catalyst systems reported in the United States56 and earlier activity57 in the explicit temperature management of catalyst systems there is a developing interest in the integration of the principal exhaust system functions that may include TE components.
Energy harvesting using waste heat from internal combustion engines (ICEs) would extend beyond the automotive sector if efficient materials containing abundant elements were to become available. Even with the 2017 announcement by UK Government58 of the plan to end the sale of all new conventional petrol and diesel cars and vans by 2040, there will still be very large numbers of vehicles in the UK and overseas which are totally or partially reliant on ICEs well beyond 2040. A recent report from MIT59 suggests that by 2050 between 60 and 90% of light and standard vehicles (depending on energy change scenario) will still use ICEs. Indeed there are many other ICE-based applications in transportation and other sectors. With marine transportation accounting for ca. 5% of global CO2 emissions (over twice that of aviation), TE energy recovery in the marine sector would have a significant impact on the worldwide emissions total. The electrical power provided would augment or replace that from the on-board diesel-fuelled generator sets (0.5–1.5 MW output) that are commonly used to provide on-board electrical power and which add significantly to a vessel's fuel consumption. Early trials at the Maine Maritime Academy60 using current generation commercial (Bi2Te3) TE modules have demonstrated that TE power generation holds considerable promise for the maritime industry but that new high efficiency materials are required to achieve economic viability.
3.2 Wireless sensing
Wireless sensing networks (WSN) are of increasing interest and importance for condition monitoring and control in a wide variety of environments from industrial to domestic. The sensing could include: wearables for medical diagnostics; sensors in domestic settings to control appliances or the building environment, wearables in sport in order to provide real-time performance data, industrial plants for remote monitoring of gas flows, temperatures, pressures needed for process control, aerospace, monitoring of key functions in jet engines. Different types of WSN have been in use for many years but the rapid expansion of connectivity has led to the internet of things (IoT), or the inter-networking of physical devices, providing network connectivity which will enable these objects to collect and exchange data. There are estimates that the IoT will consist of about 50 billion objects by 2020.61 This will provide increasing opportunities for thermoelectric powered systems.
WSN have very modest power requirements in the μW–mW region. Some of the existing TE power-harvesting systems can operate with temperature differences as low as 2 °C.62 For such TEGs, only small quantities of material would be required, making it an application area suitable for thin and thick film TEs perhaps, which would make integration with the electronic devices more straightforward.
3.3 Aerospace
In the aerospace sector, radioisotope TEGs have been used by NASA for over 50 years for a variety of missions and craft; latterly these have included the Mars Rover, Curiosity, the Galileo satellites, New Horizons space probes, and Cassini spacecraft.63 Commercial and military aircraft already use sensors and sensor networks powered by thermoelectric generators to monitor the aircraft skin for damage that can cause stresses and structural weakness.64 A traditional bismuth telluride TEG generating 20 to 30 mW of power from the heat of normally operating turbine engine bearings, would be enough to power a network of embedded sensors.
TE devices are also used in the aerospace sector for avionics cooling: black box coolers; drinking water coolers; space vehicle refrigerator/freezers; temperature control for space telescopes/cameras. Size and weight considerations are paramount in the aerospace industry and performance per unit weight is the key parameter. The current low efficiencies may impose a constraint on applications such as cabin air-conditioning where large amounts of cooling are required.
New areas of application that would be opened up to new high-efficiency devices would include energy recovery from waste heat from jet engines on aircraft. Effective use of waste heat is of growing importance in the aviation industry. Initially, restricting TEGs to the provision of power for non-safety-critical functions, such as in-flight entertainment systems, would obviate many of the barriers to implementation in a heavy safety-regulated industry. Indeed BAE Systems Military Aircraft and Information (MAI) at Warton are already considering potential applications for thermoelectrics on future combat aircraft projects which include: (i) aircrew clothing – multiple applications of integral novel materials/devices within fabric, including thermoelectrics; (ii) supplementary electrical power generation from propulsion jet pipe, using thermoelectrics; (iii) incorporation of thermoelectrics within certain heat exchangers to enhance system performance.
3.4 Wearable/implantable thermoelectrics
3.4.1 Level of performance required.
For commercial applications, conversion efficiency is not necessarily as important as cost and power output. Ultimately, any solution will need to be able to power or at least charge devices in a way that surpasses current/future battery technology, either in terms of cost or convenience of recharging/replacing. To use TEG's alone to power wearables at room temperature is a big challenge and would require new safe materials that are cheaper to produce at scale and can achieve much higher ZTs than have been demonstrated before. Below are examples of some of the most promising emerging materials for wearable thermoelectrics.
Electronically conducting polymers.
There are many electronically conducting polymers, for example, polypyrrole (PPY), polyaniline (PANI), polythiophene (PTH), poly(3,4-ethylene dioxythiophene) (PEDOT), polyacetylene (PA), and their derivatives. However, poly(2,7-carbazole), PEDOT, and PEDOT:polystyrenesulfonate (PEDOT:PSS) are good candidates for thermoelectric applications due to their process ability, high electronic conductivity and low thermal conductivity, low cost, tenability in various sizes and shapes, and environmentally-friendly nature. In general, the figures of merit (ZT) reported for these materials so far are not high enough for high efficiency conversion of heat to electricity. Hence it is imperative to improve the figure-of-merit values further by using latest technologies and different approaches.
Carbon nanomaterials.
The main drawback of using carbon materials for thermoelectric application is their high thermal conductivity. However, the thermal conductivity could be altered by nanostructuring materials. For instance, nanowires do not conduct heat due to phonon-boundary scattering or phonon dispersions. Carbon nanotubes, carbon nanowires and graphene are potential candidates for TE materials due their good electrical conductivity and the thermal conductivity could be adjusted. In addition, high mechanical strength and high thermal stability are advantages for flexible TE devices.
Carbon nanotubes.
Carbon nanotubes (CNTs) are one-dimensional carbon nanomaterials with diameters and thicknesses in the nanoscale region. n- and p-type CNTs can be fabricated, which is beneficial for manufacturing TE prototypes. Doping results in a decrease of thermal conductivity by up to 75% as a result of the defects induced inside the multiwall carbon nanotubes (MWCNTs). By oxygen doping it should be possible to increase the density of charge carriers, and thereby the Seebeck coefficient. A five cell p- and n-type MWCNTs thermoelectric module could produce a thermoelectric power of 16 μW at 27 °C.65
Graphene.
Graphene possesses very high electrical conductivity, with a very high electron mobility of 1000–7000 cm2 V s−1.66 For example, Wei et al. reported a thermopower of 50–100 μV K−1 at room temperature for a graphene sample exfoliated onto a thin layer of SiO2.67 Nevertheless, in spite of the high power factor, the overall ZT value of graphene is limited by its very high thermal conductivity.68 Efforts to reduce its thermal conductivity have focussed on the introduction of defects, such as by plasma treatment, enabling a three-fold increase in ZT.68 While it is unlikely that graphene will find direct application as a thermoelectric, except perhaps in very confined geometries (such as nanoribbons69), it is an extremely valuable component of thermoelectric composites.70,71
3.4.2 Intermediate steps that would open up new opportunities.
There are a range of designs from single stage TE modules to multistage TE modules. In one recent example72 a single stage module consisting of 250 p–n pairs was successfully fabricated on a 50 × 50 mm flexible substrate. The maximum output power density was 158 mW cm−2, corresponding to an efficiency of 1.8%. Although the multi stage TE module is not ideal for wearable TE generators in term of flexibility, weight, comfort, it is still the most popular design for high power generation.
For a staged commercialisation of wearable TEG, a series of steps beginning with commercially-available Bi2Te3 based TEG technology at room temperature, and then a multi stage TEG design would be the best route for improving the energy conversion efficiency. As advanced materials, derived from polymeric and carbonaceous materials, optimised for the operating temperatures become available, they would begin to replace Bi2Te3 in wearable devices. A multi stage design would be a stand-alone device rather than being integrated into the textiles. While this would not represent the optimum solution, it would demonstrate the proof of principle and begin to raise awareness of the technology with the general public.
The next step would be to embed TE generators into textiles and develop solution processing TE technology such as textile coating and ink-printing. Thus, nanostructuring, solution or organic based TE generators are of interest. Lu et al.73 reported a process of nanostructured Bi2Te3 and Sb2Te3 deposited on silk fabric to fabricate columns of n- and p-types of TE generator. This technology has potential for commercial, wearable TE generators, if it can be made at scale.
3.4.3 Technical constraints and principal markets for wearable thermoelectrics.
The structural complexity,74 difficulties in fabrication of high-quality materials,75 low energy conversion efficiency and fabrication cost76 are currently the biggest limitations for wearable thermoelectrics.
For wearable TEGs integrated into e-textiles that incorporate conductive fibres in the textile itself, e-textile TEGs, certain criteria need to be met. Any future solution would need to be:
• Flexible while possessing a high mechanical strength.
• Comfortable, environmentally friendly.
• Highly compatible, lightweight, modifiable.
• Easily embedded into human clothing while allowing them to retain enough of the clothing's desirable physical qualities (i.e. stretchable, foldable, washable, breathable, comfortable).
• Made from abundant raw materials, in order to keep material costs down.
Sporting and military would be the most appropriate markets due to the higher temperature differences generated through physical activity. For the military, the principal application of wearable thermoelectrics is likely to be the cooling of personal protection suits and environmental control within armoured vehicles. An increase in military activities in hot climates increases the need for a better solution. A significant improvement in ZT performance would expand the potential of this market enormously.
Inside the human body the average heat flow is 58.2 W per square meter due to the basal metabolic rate; this could be as high as 100 W per square meter during physical activity. However, the human body has a high thermal resistance at ambient temperatures below 20–25 °C77 which reduces heat flow. Depending on the location on the body, heat flow can be anywhere between 1 to 10 mW cm−2 for typical indoor conditions. There will also be a difference between heat flow from a naked skin surface and through a textile garment. Clothing will ultimately affect the way heat will flow from the body to the surroundings and this must be considered during the design phase. As such, comparatively little heat is dissipated from the skin due to the thermal insulation of clothes (typically 3–6 mW cm−2).
The largest area of the body with the most stable temperature at different ambient conditions (temperature, wind, sunlight, etc.) is the trunk. However, this also presents the hardest task for adaption and implementation into e-textiles due to the criteria mentioned above. The skin temperature is still around 20–25 °C on the scale of centimetres. Therefore, the heat flow of a TEG embedded device would depend not only on the skin temperature, but also on the local thermal resistance of the human body (i.e., the thermal resistance between the body core and the chosen location on the skin).
Mechanical design is as important as device design because it affects not only the relationship between the thermal transportation and the contact but also the performance of a device. It must be comfortable, allowing high mobility, and also be flexible and biocompatible. Mechanically flexible devices can be achieved by direct fabrication on plastic foil, or by peeling off a polymer layer deposited on a rigid substrate by ink-printing.78
The criteria for a system integrated into a piece of clothing is that it must be thin, lightweight, waterproof, bendable and sustain repeated laundry and pressing or high temperatures. High accelerations and mechanical shocks during machine washing should also be considered; protection may be required. However, implementing protection methods might adversely affect the power output and partially decrease the convective and radiation heat transfer from the TEG.
3.5 Building scale integration
3.5.1 Thermoelectric wireless sensor networks.
In recent years there has been growing interest in the construction of sustainable high performance buildings where the ambient building environment can be controlled in a dynamic way. The traditional methods of controlling temperature, humidity, air quality and artificial lighting etc., are through the installation of distributed wireless sensor networks (WSNs). These can result in energy savings of approximately 20% and a major step towards real Smart Building Management.79 Unfortunately, traditional WSN rely on battery powered sensor systems, with inherent disadvantages of the need for regular and long term maintenance. Such limitations could be overcome by WSN systems powered by stand-alone, micro-scale thermoelectric generators, which obtain their power by energy harvesting. Millimeter scale TEGs such as those produced by Kim et al.80 are reported to be able to generate 270 μW of electrical power, which is sufficient to broadcast data in a wireless sensor node.80 Huang et al.79 reported a very effective TEG powered building WSN demonstrator which worked with temperature differences of 3–8 °C. Later Kuchle and Love81 employed thermoelectric sensing loops and realised a WSN system which could monitor directly temperature and magnetic field strength via an integrated Hall monitor.
3.5.2 Transpired solar collector systems.
Other opportunities for building scale integration of thermoelectric devices include solar thermal collection by Transpired Solar Collector (TSC) in industrial buildings.82,83 This is an established technology that can produce significant savings in heating costs (Table 3). Thermoelectric devices can be integrated into TSC to enable building-scale generation of power from the heat generated by near-infra red. The efficiency of these systems could be increased by combining with thermoelectric generators to power the electrical systems of the TSC system.
Table 3 Commercial UK installations of transpired solar collectors for ventilation air heating82
Project |
Location |
TSC area m2 |
Predicted energy savings kW h per year |
Jaguar/Land Rover |
Leamington Spa |
268 |
80 530 |
Beaconsfield services |
Beaconsfield |
255 |
99 235 |
Premier park |
Winsford, Cheshire |
580 |
130 000 |
Sainsbury's distribution |
Pineham |
947 |
256 093 |
CA group rollforming mill |
Evenwood |
1211 |
299 000 |
International paints |
Felling, Gateshead |
100 |
31 169 |
Royal mail |
Swan Valley |
800 |
233 396 |
3.6 Application of TE in general industry and power generation
The most successful and widely reported applications of TE have tended to be in “high value” environments. With cost reduction and improved engineering, TEGs suitable for general industrial use are emerging for application in metals and glass manufacturing. Processes are characterised by high temperature gas flows that flow through ducts and chimneys, facilitating the deployment of TEG systems.
The United States Department of Energy (DoE) in its 2015 Quadrennial Review of Technology84 highlights the energy sectors where there is substantial potential for “retrofit” energy recovery systems. Case studies illustrate the benefits. Alphabet Energy offered a TE based WHR system for diesel generator sets able to recover 25 kW from the exhaust stream of a 1 MW rated engine. A review of a steel mini-mill in Jewett, Texas demonstrated substantial energy recovery from hot steel slabs during the rolling process.
While the direct application of TEGs to industrial processes offers substantial opportunities for energy recovery, there are also niche applications where the strategic deployment of a high temperature TE system can offer significant thermodynamic advantages that may lead to the simplification of the plant.85
3.7 Nuclear industry
Nuclear fission reactors produce considerable quantities of heat to create steam that drives the mechanical turbines, which generate electrical power. However, there are inherent limitations in the efficiency. For example a typical reactor producing 1000 MW (thermal) operates at 25–30% efficiency as a result of constraints imposed by the Carnot cycle and the limitations of steam turbines. Such plants produce a steady supply of low-grade waste heat.
Extraction of energy from this waste heat would not only improve the overall operating efficiency of a plant, thereby reducing fuel consumption but also lessen environmental problems associated with the release of very hot water into neighbouring water courses. It has been proposed that a static energy recovery system, incorporating a TE converter operating at the bottom cycle (525 to 365 K) would markedly increase the total utilization of a reactor's thermal energy in a small gas-cooled reactor.
3.8 Geothermal applications
Decommissioned offshore oil platforms have been suggested as a source of geothermal heat. Temperatures at the depth of a worked-out reservoir are 80–100 °C higher than at the surface. It has been estimated that up to 10 MW may be generated by exploiting the temperature difference between seawater at the surface and that which has replaced oil in the subterranean reservoir. However, with current thermoelectric conversion efficiencies, the economics of power transmission to the mainland are not favourable.
4. Thermoelectric energy harvesters: market forecasts
The global market for thermoelectric generators in 2017 is estimated86 to be US$ 320 million and is projected to grow to US$ 720 million with a growth rate of 14.5% from 2015 to 2021. North America is expected to dominate with over two thirds of the market, and to retain supremacy over the period. However, Asia Pacific and European countries are projected to grow at relatively higher rates. Beyond 2021 continued growth is expected with the market for thermoelectric energy harvesters reaching $875 million by 2023,87 and $1500 million by 2028,88 with thermoelectrics ahead of piezoelectrics in terms of investment and commercialisation.
The thermoelectric generator market is divided into four main segments, namely waste heat recovery, energy harvesting, direct power generation, and co-generation. In 2015, waste heat recovery was the largest segment of the thermoelectric generator market. In spite of policy changes in the UK38 and elsewhere about planned reductions in sales of new petrol and diesel cars, a significant fraction of the automobiles on the road will still contain internal combustion engines.39 The automotive sector was one of the key applications areas in 2015 and is expected to remain an important market. Aerospace and industrial heat applications are in second and third positions. The industrial segment is expected to see considerable growth in the next few years due to the availability of low-cost devices.
Another area that is expected to grow significantly in the coming decade is the low power, sub-watt TEG market, with predicted compound annual growth rate of more than 110% from 2014 to 2020.89 These low power TEGs are focussed on two main applications area: infrastructure and buildings, and industrial and professional. Along with the emerging thin film/thick film devices they should be well suited to the expanding WSN and IoT markets.
5. Opportunities and future needs
Solid-state heat management for energy harvesting and cooling are global business opportunities. The current global market for TE devices is approximately $300 M and is predicted to grow to over $1.5 Bn by 2028 (Section 4) if the technical challenges associated with performance, cost and materials availability can be overcome. Therefore, business opportunities exist in the supply of TEG systems to a wide range of industries including manufacturing, nuclear, defence, geothermal, solar and sensors. The challenge now is to capitalise on recent advances in TEG materials from the academic and industrial communities90 and develop practical, system-level demonstrations that will greatly facilitate the uptake of the technology across business sectors. Examples of the opportunities for TE harvesting and cooling across a range of industry sectors are given in Section 5.4. The market will be driven by: environmental protection, replacement of CFCs, use of waste heat, improvement in use of energy and global warming.
With no change in ZT performance, the market should grow by about 15% per annum. Reliability of the finished device is of key importance in all sectors. Manufacturability and yield are critical. Material processing and module production technologies are often proprietary. It may be difficult to convince suppliers to invest in any modifications to these that are needed, in order to use the new material. For cooling applications, compressor-based technology is very dominant and will take time to displace, even with higher-performance thermoelectric technology.
5.1 Materials
5.1.1 Bulk thermoelectrics.
There exist today a very wide range of bulk materials (Section 1) from the traditional and very well established metallic tellurides, skutterudites and half Heuslers, to the sulphides, oxides, organic materials and composites. Whilst integration of the individual thermoelectric elements in TEG packages without degrading performance sets manufacturing challenges there are also fundamental materials challenges. Although peak ZT is still an important criterion for thermoelectrics and there are established strategies to increase electrical conductivity and reduce thermal conductivity in order to increase ZT, the importance of achieving a high average ZT over the temperature profile of the device is also becoming increasingly recognised. In recent years a number of novel approaches to improving materials’ performance have emerged (Section 1.4.2). More theoretical and experimental investigations are required to better understand the materials at the nanoscale and to develop strategies to design material nanostructures that will lead to significantly improved ZT performance.
All of the known thermoelectric materials have well defined temperature ranges, or windows, where the material performs at near maximum thermoelectric conversion efficiency. In some cases the peak temperature windows are at very modest temperatures whilst for others it occurs at much higher temperatures, requiring the use of tandem modules to maximise thermoelectric power conversion from large temperature gradients. Specific challenges for bulk materials are to increase the overall ZT of the material, without degrading thermal or mechanical stability, but also to increase the width of the thermal window for thermoelectric power conversion. For applications involving transport any weight increase should be avoided, thus lightweight materials based on Earth-abundant, cheap elements are preferred.
5.1.2 Thin-film thermoelectrics.
As a direct consequence of module size, thin-film generators are not appropriate for large-scale energy generation or recovery. However, thin-film, energy harvesting TE micro-generators are ideally suited for smart, possibly flexible, “internet of things” applications including remote sensing and medical applications related to body heat harvesting.
One key issue related to the development of thermoelectric materials, particularly thin-film thermoelectrics, is the scarcity of reliable, reproducible data. A round-robin sample exchange and calibration effort within the thin-film community would be very valuable both to establish and validate the performance data and the reasons for differences in the data. Indeed this applies to many other types of TE materials.
5.1.3 Organic thermoelectrics.
n-Type OTEs.
The development of doped n-type semiconductors is lagging behind p-type; the main reason being the high electron affinities (−3 to −4 eV) of many n-type semiconductors, making doping under ambient conditions difficult due to enhanced reactivity. To advance, the development of organic thermoelectric materials, novel air-stable dopants for n-type semiconductors need to be developed.
Self-powered sensors.
Organic semiconductors are in general very sensitive to their environment, and exploiting this in combination with their thermoelectric properties has great potential for self-powered sensors, i.e. devices where the power source is also the sensing element. Self-powered dual pressure–temperature sensors have been demonstrated,34 but the possibilities could be expanded to sensors of humidity, salts, biological markers, and toxins amongst others.
Cost in OTE.
In OTEG development, module cost per Watt ($ per W) is best addressed by increasing ZT.37 Currently models of thermoelectricity for organic materials are borrowed from the inorganic community. However charge transport in organic materials occurs by different and quite complex routes and is not universally understood. Equally the origin of the Seebeck coefficient in organics is not resolved, and methods to minimise thermal conductivity have not been extensively explored. Computational and experimental research on these key questions is still much needed. Nonetheless for organic materials (including n-types) it can be appropriate to pursue synthesis-cost-reduction approaches to expand the possible range of applications. The cost of substrates, heat exchangers and manufacture are as important as synthesis costs.
Doping strategies.
Doping in OTEs generally comes from blending with molecular dopants. Unfavourable morphologies and dopant-phase separation are commonly observed which limit the carrier concentrations in many OTEs. Strategies to maximise the degree of doping in these materials are needed. These are likely to be by chemical design (of semiconductors and dopants) and ink formulation. Chemical design strategies to doping would include control of miscibility of semiconductor and dopant, as well as new self-doped materials and intrinsically conducting polymers.
Molecular design.
Most OTE materials are borrowed from the organic electronics field. There has been relatively little effort to design bespoke materials for the application due to a lack of design rules. Development of OTE material design rules by computation and experiment are a priority.
Printing and processing.
Technologies for printing sub-micron organic electronic materials are well developed, but there will need to be significant adaptation to OTE which requires printing of thick films (10s–100s μm). Thus far, thick film printing has yielded reduced electrical conductivities, particularly in the out-of-plane orientation which is the usual direction of current flow in an OTEG. Similar challenges are faced for blade coating, extrusion, melt processing, etc. These challenges may be addressed by new ink formulations, process control and by redesigning device geometry.
Composite materials.
Organic materials can be readily processed into composites by a range of scalable techniques. A new range of composite materials aimed at OTE applications will open up many possibilities. These could be composites to boost electrical conductivity by combining the OTE with a more conductive material; or composites to bring additional functionality such as enhanced flexibility, stretchability, ion sensing and pressure sensitivity amongst others.
5.1.4 Flexible thermoelectrics.
Flexible materials, which are likely to be organic or composite in nature offer many possibilities in the wearable and medical sectors. The wearables already include clothing for sport and military personnel (Section 3.4) and there are growing opportunities for clothing for aircrew, where integrating novel materials/devices (including thermoelectrics) within the fabric will enable control temperature within the suits. For medical applications, temperature differences of 2 °C over an area 4 cm2 should be sufficient to power ultra-low-power medical monitors for temperature, flow rates, ECG, EEG, etc. Low thermal conductivity may be more important than high ZT for wearable medical applications. More general challenges that require more work are joining of new composite materials in TE modules, development of protective coatings and mechanical durability.
5.1.5 Modelling of thermoelectrics.
Developments in modelling techniques and the increase in high-performance computing allow materials modelling to underpin experimental research for the search and characterisation of new thermoelectric materials. For example, there is increasing use of high-throughput computational screening to identify target structures and compositions that not only allow the stability of the phase to be verified but also whether the figure of merit, ZT is of a sufficient value to be worthy of further consideration. Indeed, in the US, the Material Genome Initiative91 has been particularly effective in supporting high-throughput computational materials design. Modelling can also underpin and rationalize the different components of the structure and their contribution to the TE figure of merit, which is currently unattainable experimentally. This includes the search for dopants and microstructures, particularly nanostructures, to lower the thermal conductivity, while increasing Seebeck and electronic conductivity through band engineering.
Our fundamental understanding of carrier transport inside bulk materials has improved significantly in the last decade, mostly as a result of the use of first-principles approaches combined with high-performance computing. However, some key challenges will need to be addressed in order to take a step forward towards the design of complex nanostructured materials for the next-generation of thermoelectric devices. For instance, the Seebeck coefficient is very sensitive to the relative position of the conduction and valence bands (band-gap) and to the band curvature near the gap edges. The accurate description of these features goes beyond the standard DFT. New numerical approaches have recently been proposed to overcome these issues, offering new avenues to be explored in the near future.
Another big challenge is the development of accurate and efficient computational tools to predict electrical transport coefficients. The main issue here is a proper description of the dynamics of carriers, while accounting for the relevant carriers’ scattering mechanisms. In this context, the Boltzmann transport equation (BE) offers a framework for a detailed microscopic description of transport in metals and semiconductors. This is a computationally challenging problem, which will require in the future further optimizations to describe materials of interests for thermoelectric applications.
Finally, further advances are needed to understand and predict carrier (electrons or phonons) transport in the presence of interfaces. Indeed, for instance, boundaries can have a significant effect on the overall thermal resistance as the interface density increases in nanostructured composite materials. As the structure of interfaces varies significantly from one grain to the other, the actual microscopic details of an interface are usually unknown, and this makes it very hard to compare theory with experiment. First-principles approaches can be used to model perfect interfaces at low temperatures, but it is very challenging to predict trends reliably. Future efforts are needed to overcome these limitations, by using other numerical methods based on molecular dynamics or the Green's function approach.
5.2 Thermoelectric generators and systems
5.2.1 Modules.
The main focus of thermoelectric research is rightly placed on materials development to improve thermoelectric module performance. There are a few areas of device research which can complement this research and help advance the technology:
(i) Batch scale and reproducibility. A longstanding issue has been the step from laboratory development of a new material through scale up to mass production with high reproducibility of batches. Attention to the critical issues here with accelerated life-time testing would be valuable.
(ii) Module system efficiency. Most TEG systems require more than one module and sometimes multiple materials each with different peak ZT values. Further work on understanding how modules interact with each other and maximise their overall performance is important for minimising the drop from module efficiency to system efficiency.
(iii) Thermal interface materials. Currently for high temperature applications graphite is the material used. Could it be possible to grow thermal interface materials on the module substrate or develop a process which will smooth the surface of the module without the need for polish?
(iv) Joining material research. There are very few solders/brazes which operate between 300–500 °C. The currently-available silver brazes have melting points above 600 °C and are expensive.
5.2.2 Electronics for thermoelectric power generation.
The principle of using a DC → DC power converter to produce a constant output voltage from the temperature-dependent voltage from a thermoelectric generator (TEG) is well established. In many cases the desire is to maximise the total amount of energy extracted from the TEG material, and to do this the input impedance of the converter is adjusted to match the internal impedance of the TEG at any given instant. A particular challenge for low voltage electronic converters is to establish the first switching event. Once switching operation is established, operation down to as little as 25 mV from the TEG is quite practicable. From a systems perspective it is essential that the electronic converter is considered as part of the overall thermoelectric design from the outset. Areas that require particular attention are:
(i) Establishing the Maximum Power Point. The maximum power transfer theorem dictates the required converter impedance at the module level. However, thermal gradients at the system level can lead to higher available power from the thermoelectric material. In general this deviation from the predictions of the maximum power transfer theorem has to be empirically determined over the operating range of the TEG system which requires new control algorithms for the electronic control.
(ii) The voltage/current compromise. Many of the “new” TE materials such as silicides and skutterudites have a low electrical resistance which leads to a low output voltage and high output current. From an electronics perspective, losses increase as the square of the current flowing, and hence high current systems have an inherent disadvantage in terms of the maximum efficiency attainable.
(iii) Conversion and tracking efficiency. There are two figures of merit for the TEG converter: the accuracy with which it can track the real maximum power point (target >99%) and the intrinsic converter efficiency (target >97%). The former is largely determined by the control algorithm. A tracking algorithm that incorporates measurement of the ΔT on a TEG module has been demonstrated to produce 7% more power than predicted by the maximum power transfer system alone. Much work is needed to convert this class of algorithms from “system specific” to “generic”.
(iv) High-temperature electronics. In order to reduce the mass of the electrical interconnection between the TEG and the converter, the converter is moved closer to the TEG array which leads to a higher operating temperature, pushing the performance of available electronics to the limit. For this and high temperature TEG applications, new electronic devices are required to maintain the desired conversion efficiency under such conditions.
5.2.3 Technological & manufacturing opportunities.
Already, earth-abundant materials have been demonstrated in laboratory studies to be suitable for replacing expensive bismuth telluride in certain TEG applications. The next generation of materials are incorporating advances in nanotechnology including nano-structuring, 2-D layered materials (graphene and graphene-like) that promise to show performance improvements beyond bismuth telluride. It is noted that more efficient materials need to be developed with an emphasis on maximising the average value of the figure of merit (ZT) rather than the maximum value, and optimising ZT for the application.
When coupled with advances in the other system components such as heat exchangers and thermal interface materials, TEG solutions to waste-heat recovery or cooling will be better able to offer alternatives to existing technologies as well as create new markets. The current generation TEG has multiple components – thermoelements, barrier/diffusion layers, solders/brazes, contacts, electrically insulating ceramics, all of which need to be assembled by (currently) hand. This is labour-intensive and therefore costly. Thus scale-up know-how is a key objective in order to reduce cost, which in turn will open up a wider range of applications.
There is potential to exploit innovative manufacturing including 3-D printing, reel-to-reel and more robotic processing with existing materials. This should also enable the development of conformal, customised systems that enable much improved thermal interface-matching. Thus, there is plenty of room for the TEG industry to benefit more from economies of scale and novel processing methods including multi-kilogram semiconductor powder preparation to fast-throughput powder-sintering operations. We note that the environments and power ranges for waste-heat conversion to electrical power are particularly diverse, i.e. from jet engines to body sensors, and so require correspondingly diverse TEG materials.
Design and fabrication of new device architectures and provision of materials that enable novel architectures are required. One approach to improve the automation/production of TEGs would be to use processes such as printing, additive layer manufacturing, and adaptation of semiconductor industry processing tools. Heat transfer at interfaces and heat exchangers are an important aspect of integrated design. Increased understanding through modelling of what happens at interfaces is likely to be needed. Flexible or conformal module formats will help more efficient heat transfer from the source to the hot/cold sink. One approach to meet this challenge is being met by the availability of novel organic and hybrid TEG electrode compositions as well as inorganic ones, which in-turn require innovations in their large-scale manufacture and system packaging.
5.3 Applications sectors
5.3.1 Transport – automotive.
Power range opportunities: a few hundred Watts to a kilowatt.
Power-train development for transport is undergoing significant changes with the progressive entry of hybrid and full electric vehicles into commercial fleets. For the conventional internal combustion engine, legislative drivers are forcing manufacturers to look for new ways of improving fuel economy such as the use of TEGs for utilising waste heat. In 2015 the UK used 57 million tons oil equivalent for all forms of transport (mainly road) with an associated CO2 release of ∼167 × 106 metric tonnes. Even modest waste-heat conversion with a 10% efficient TEG is calculated to decrease the net UK CO2 transport sector emissions by several million tons. In addition, better management of passenger/driver comfort through selective cooling (or heating) could open up new TEG applications within the vehicle. Fig. 10 shows a Technology Road Map for TEG and Peltier modules for automotive applications.
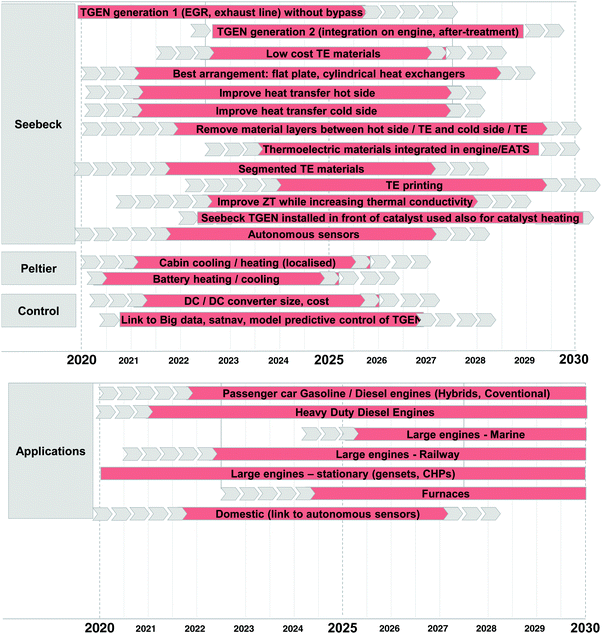 |
| Fig. 10 Roadmap for TEGs and Peltier devices for Automotive sector. (Image courtesy of Ricardo plc.) | |
5.3.2 Stationary applications – heavy industry.
Power range opportunities: a few hundreds of kW or higher.
The traditional high-heat producing industries such as cement, steel and glass offer clear opportunities for energy harvesting although the proportion of national energy consumption is now less than for domestic space-heating. The retail and service sectors offer interesting opportunities for heat management using TEGs where, for example, heat produced from refrigeration units is presently untapped for energy scavenging.
5.3.3 Consumer/IoT/medical/sensors.
Power range opportunities: mW or less.
For consumer-based electronics, IoT and sensor networks, energy scavenging options are of interest in prolonging battery life or even dispensing with batteries altogether. In applications where self-powering sensors are needed then the existence of a temperature gradient, large or small, can be sufficient to power periodic or continuous data transmission for a wide range of uses including the fast growing home-care sector and could be exploited in the medical sector.
5.3.4 Multi-sector.
Power range opportunities: mW to MW.
Table 4 shows examples of opportunities for thermoelectric harvesting and the potential range of industry sectors which could benefit. The list is not exhaustive but demonstrates the wide variety of applications with power ranges from mW to MW.
Table 4 Examples of opportunities for TE harvesting & cooling showing the potential range of industry sectors which could benefit92
Opportunity |
Sector |
Exhaust gas heat recovery for fuel efficiency |
Automotive |
Heat shielding & cooling |
Automotive |
Heat recovery for powering electrical systems |
Aerospace |
Airframes-thermal management |
Aerospace |
Heavy duty marine heat harvesting |
Marine |
Food distribution & in-store chillers |
Retail/food |
Personal and space cooling |
Consumer/buildings |
Recovery of heat in energy intensive process industries |
Manufacturing |
Cooling of electronics |
Electronics |
Powering of wearable electronics & sensors for health |
Healthcare |
Powering wireless sensor networks |
Internet of things |
Combined heat & power – increase electrical efficiency |
Energy |
Solar heat harvesting |
Energy |
Geothermal heat harvesting |
Energy |
6. Conclusions and recommendations
There has been significant growth in global research activity in thermoelectrics over the past thirty years and has led to the previously assumed upper limit of ZT ≈ 1.0, being exceeded in a number of materials at elevated temperatures, through judicious application of new design strategies. Much of the growth in research activity has been facilitated by increased investment from a variety of governmental and non-governmental bodies. The establishment of the European Thermoelectrics Society in 1995 has provided a focus for work in Europe and its annual meeting acts as forum for an exchange of ideas. The International Conference on Thermoelectrics, organised under the auspices of the International Thermoelectric Society rotates annually between Europe, North America and Asia and performs a similar role for the global community of researchers.
In order to reap the benefits from initial developments and to be able to exploit the growing market and opportunities for thermoelectrics, investment and support are required for a new generation of thermoelectric materials that exploits the synergies between experimental and computational expertise, novel device architectures, associated novel manufacturing and materials preparation techniques and system integration. Drawing on the information contained in the current document, together with the work of Kajikawa,93 who in 2012 developed a Roadmap that focuses primarily on applications sections with projected developments in efficiency, we formulate the Roadmap presented in Fig. 11 for the exploitation of thermoelectric technology, with advances in materials and system performance.
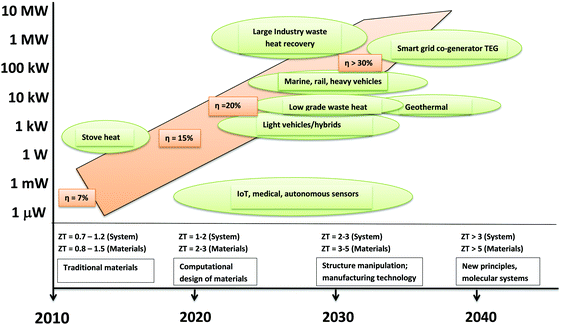 |
| Fig. 11 A Roadmap for the exploitation of thermoelectric technology, where ZT is the thermoelectric figure of merit and η the efficiency. | |
Progress towards objectives presented in Fig. 11 requires advances in theoretical understanding, materials, manufacturing and system design. In particular:
(i) Theoretical, modelling and experimental investigations of materials at the nanoscale to develop strategies to design material nanostructures giving significantly improved ZT performance. This could for instance be encouraged through specific calls from funding agencies aimed at fundamental studies such as those described in this document.
(ii) Development of next generation of thermoelectrics by incorporating advances in nanotechnology (including nano-structuring, 2-D layered materials, graphene and graphene-like) that promise performance improvements beyond bismuth telluride. This could be encouraged by fostering further collaborations with nano-technology focused groups, through, e.g. cross-departmental collaborations within higher education/research institutions.
(iii) Development of novel high performance TE materials composed of earth-abundant elements to meet current and developing needs (sectors will include automotive, heavy industry, aerospace, marine and nuclear), with an emphasis on maximising the average value of the figure of merit (ZT) rather than the maximum value.
(iv) Application of advanced manufacturing techniques to improve the production of thermoelectric generators through new materials processes including printing, additive layer manufacturing, and adaptation of semiconductor industry processing tools.
(v) A round-robin sample exchange and calibration effort within the thermoelectric materials community to establish and validate the performance data and the reasons for differences in the data; this should include both bulk and thin film materials. The results of this community effort would be presented at international meetings on thermoelectrics and published as a ‘consortium’ scientific contribution.
(vi) Focussed effort to understand and overcome packaging and interface issues, including thermally-induced mechanical stresses limiting thermoelectric performance, long-term stability and durability.
(vii) Development of integrated manufacturing processes that facilitate the routine assembly of novel device architectures to match the shape of the heat source, and address heat transfer aspects including heat-exchangers.
(viii) Devices tailored for the very wide range of applications from body sensors, medical devices and IoT to industrial plant, trucks and jet engines.
(ix) An industrial network covering solid-state heating and cooling be set up to promote information exchange and collaboration, to identify opportunities for synergy across different end-use sectors, which links-in with the academic sector.
(xi) Support for demonstrator-projects that encompass materials scale-up through to prototype system testing, and exploitation of novel high-performance materials in a cost-effective manner.
(x) Support for funding instruments to enable an integrated approach to thermoelectric activities thereby strengthening the global R&D community.
Conflicts of interest
There are no conflicts to declare.
Acknowledgements
The authors wish to acknowledge the financial support of the UK Engineering and Physical Sciences Research Council (Award: EP/L014068). We also acknowledge the assistance of members of the UK Thermoelectric Network and other colleagues with the preparation of this document. In particular, we thank Dr J. Alaria, Dr D. Alvarez-Ruiz, Prof. R. Ambrosi, Prof. P. Bartlett, Dr M. Baxendale, Dr N. Bennett, Dr E. Bilotti, Dr N. Bonini, Dr J.-W. Bos, Dr M. Carnie, Dr Y. Chao, Dr E. Don, Prof. R. Dorey, Dr O. Fenwick, Prof. J. Goff, Dr R. Grau-Crespo, Prof. D. Gregory, Prof. K de Groot, Dr E. Guilmeau, Prof. A. Hector, Dr D. M. Kepaptsoglou, Dr S. King, Dr J. Konig, Prof. A. Knox, P. Kunovski, Prof. C. Lambert, Dr F. Linseis, Prof T. Mori, Prof. G. Min, Dr I. Nandhakumar, Prof. S.C. Parker, Prof. D. Paul, Dr M. Philips Prof. M. Reece, Dr R. Potter, Dr Q.M. Ramasse, Prof. G. Reid, Prof M. Rosseinsky, Dr C. Rouaud, Dr B. Schroeder, K. Simpson, Prof. D. Sinclair, Dr J. Siviter, Prof. G.P. Srivastava, Dr E. Smith, S.J. Smith, Prof. R. Stobart, Dr P. Vaqueiro, Prof A. Veziridis, Prof. A. Walsh, Dr C. Weber, Prof A. Weidenkaff, Dr H. Williams, Prof. S. Woodward and Dr S. Aminorroaya Yamini for their contributions.
Notes and references
- United Nations Framework Convention on Climate Change, Paris Agreement. FCCC/CP/2015/10/Add.1; Report of the Conference of the Parties on its twenty-first session, held in Paris from 30 November to 13 December 2015.
-
M. Muntean, D. Guizzardi, E. Schaaf, M. Crippa, E. Solazzo, J. G. J. Olivier and E. Vignati, Fossil CO2 Emissions of all World Countries - 2018 Report, EUR 29433 EN, Publications Office of the European Union, Luxembourg, 2018, ISBN 978-92-79-97240-9, DOI: 10.2760/30158, JRC113738.
-
T. Kajikawa, in Thermoelectrics Handbook: Macro to Nano, ed. D. M. Rowe, CRC Press, Boca Raton, 2006, vol. 50, pp. 804–831 Search PubMed
.
-
A. Abela, L. Hamilton, R. Hitchin, A. Lewry and C. Pout, Study on energy use by air-conditioning: final report. BRE Client Report for the Department of Energy & Climate Change, HPR218-1001 2016.
- F. L. Curzon and B. Ahlborn, Efficiency of a Carnot engine at maximum power output, Am. J. Phys., 1975, 43, 22–24 CrossRef
.
-
I. MacLeay, K. Harris and A. Annut, Digest of UK Energy Statistics 2015, in Department of Energy & Climate Change National Statistics, edn, 2015.
- G. J. Snyder and A. H. Snyder, Figure of merit ZT of a thermoelectric device defined from materials properties, Energy Environ. Sci., 2017, 10, 2280–2283 RSC
.
- E. Davies, Chem. World, 2011, 50 Search PubMed
.
- U.S. Geological Survey, 2019 Mineral commodity summaries 2019: U.S. Geological Survey, p. 200, DOI: 10.3133/70202434.
-
G. A. Slack, in CRC Handbook of Thermoelectrics, ed. D. M. Rowe, CRC Press, Boca Raton, 1995, ch. 34, pp. 407–440 Search PubMed
.
- M. G. Kanatzidis, Nanostructured thermoelectrics: The New Paradigm?, Chem. Mater., 2010, 22, 648–659 CrossRef CAS
.
- L. D. Zhao, B. P. Zhang, J. F. Li, M. Zhou, W. S. Liu and J. Liu, Thermoelectric and mechanical properties of nano-SiC-dispersed Bi2Te3 fabricated by mechanical alloying and spark plasma sintering, J. Alloys Compd., 2008, 455, 259–264 CrossRef CAS
.
- S. Kim II, K. H. Lee, H. A. Mun, H. S. Kim, S. W. Hwang, J. W. Roh, D. J. Yang, W. H. Shin, X. S. Li, Y. H. Lee, G. J. Snyder and S. W. Kim, Dense dislocation arrays embedded in grain boundaries for high-performance bulk thermoelectrics, Science, 2015, 348, 109–114 CrossRef PubMed
.
- J. P. Heremans, B. Wiendlocha and A. M. Chamoire, Resonant levels in bulk thermoelectric semiconductors, Energy Environ. Sci., 2012, 5, 5510–5530 RSC
.
- H. Liu, X. Shi, F. Xu, L. Zhang, W. Zhang, L. Chen, Q. Li, C. Uher, T. Day and G. J. Snyder, Copper ion liquid-like thermoelectrics, Nat. Mater., 2012, 11, 422–425 CrossRef CAS PubMed
.
- B. Liu, J. Hu, J. Zhou and R. Yang, Thermoelectric transport in nanocomposites, Materials, 2017, 10, 418 CrossRef PubMed
.
- D. Narducci, Energy Filtering and Thermoelectrics: Artifact or Artifice?, J. Nanosci. Nanotechnol., 2017, 17, 1663–1667 CrossRef CAS PubMed
.
- L. D. Hicks and M. S. Dresselhaus, Thermoelectric figure of merit of a one-dimensional conductor, Phys. Rev. B: Condens. Matter Mater. Phys., 1993, 47, 16631–16634 CrossRef CAS PubMed
.
- P. Ren, Y. Liu, J. He, T. Lv, J. Gao and G. Xu, Recent advances in inorganic material thermoelectrics, Inorg. Chem. Front., 2018, 5, 2380 RSC
.
- A. V. Powell, Recent developments in Earth-abundant copper-sulfide thermoelectric materials, J. Appl. Phys., 2019, 126, 100901 CrossRef
.
- X. Shi, L. Chen and C. Uher, Recent advances in high-performance bulk thermoelectric materials, Int. Mater. Rev., 2016, 61, 379–415 CrossRef CAS
.
- G. Tan, L.-D. Zhao and M. G. Kanatzidis, Rationally Designing High-Performance Bulk Thermoelectric Materials, Chem. Rev., 2016, 116, 12123–12149 CrossRef CAS PubMed
.
- C. Gayner and K. Kamal, Recent advances in thermoelectric materials, Prog. Mater. Sci., 2016, 83, 330–382 CrossRef CAS
.
- J. Shuai, J. Mao, S. Song, Q. Zhang, G. Chen and Z. Ren, Recent progress and future challenges on thermoelectric Zintl materials, Mater. Today Phys., 2017, 1, 74–95 CrossRef
.
- S. J. Poon, Half Heusler compounds: promising materials for mid-to-high temperature thermoelectric conversion, J. Phys. D: Appl. Phys., 2019, 52, 493001 CrossRef CAS
.
-
A. V. Powell and P. Vaqueiro, in Thermoelectric Materials and Devices, ed. I. Nandhakumar, N. M. White, S. Beeby, Royal Society of Chemistry, Cambridge, 2017, ch. 2, pp. 27–59 Search PubMed
.
- S. Hébert, R. Daou, Y. Bréard, D. Pelloquin, E. Guilmeau, F. Gascoin, O. Lebedev and A. Maignan, Searching for new thermoelectric materials: some examples among oxides, sulfides and selenides, J. Phys.: Condens. Matter, 2016, 28, 013001 CrossRef PubMed
.
- M. Rull-Bravo, A. Moure, J. F. Fernandez and M. Martin-Gonzalez, Skutterudites as thermoelectric materials: revisited, RSC Adv., 2015, 5, 41653–41667 RSC
.
- E. S. Toberer, A. F. May and G. J. Snyder, Zintl chemistry for designing high efficiency thermoelectric materials, Chem. Mater., 2010, 22, 624–634 CrossRef CAS
.
- H. Kleinke, New bulk materials for thermoelectric power generation: clathrates and complex antimonides, Chem. Mater., 2010, 22, 604–611 CrossRef CAS
.
- J. W. G. Bos and R. A. Downie, Half-heusler thermoelectrics: a complex class of materials, J. Phys.: Condens. Matter, 2014, 26, 433201 CrossRef PubMed
.
- A. Nozariasbmarz, A. Agarwal, Z. A. Coutant, M. J. Hall, J. Liu, R. Liu, A. Malhotra, P. Norouzzadeh, M. C. Öztürk, V. P. Ramesh, Y. Sargolzaeiaval, F. Suarez and D. Vashaee, Thermoelectric silicides: a review, Jpn. J. Appl. Phys., 2017, 56, 05DA04 CrossRef
.
- V. Leonov and R. J. M. Vullers, Wearable thermoelectric generators for body-powered devices, J. Electron. Mater., 2009, 38, 1491–1498 CrossRef CAS
.
- F. Zhang, Y. Zang, D. Huang, C. Di and D. Zhu, Flexible and self-powered temperature–pressure dual-parameter sensors using microstructure-frame-supported organic thermoelectric materials, Nat. Commun., 2015, 6, 8356 CrossRef CAS PubMed
.
- G. H. Kim, L. Shao, K. Zhang and K. P. Pipe, Engineered doping of organic semiconductors for enhanced thermoelectric efficiency, Nat. Mater., 2013, 12, 719 CrossRef CAS PubMed
.
- C. Cho, K. L. Wallace, P. Tzeng, J.-H. Hsu, C. Yu and J. C. Grunlan, Outstanding low temperature thermoelectric power factor from completely organic thin films enabled by multidimensional conjugated nanomaterials, Adv. Energy Mater., 2016, 6, 1502168 CrossRef
.
- C. Dames, Cost optimization of thermoelectric materials for power generation: the case for zt at (almost) any cost, Scr. Mater., 2016, 111, 16–22 CrossRef CAS
.
-
J. P. Bazzo, J. C. C. Silva, E. G. Carati, M. Vogt and T. Lukasievicz, Digital control system using a thermoelectric cell for temperature electronic devices testing, Proceedings First Latin American Symposium on Circuits and Systems (LASCAS), 2010, (IEEE, 2010), pp. 1–4.
- F. Jiao, C. Di, Y. Sun, P. Sheng, W. Xu and D. Zhu, Inkjet-printed flexible organic thin-film thermoelectric devices based on p- and n-type poly(metal 1,1,2,2-ethenetetrathiolate)s/polymer composites through ball-milling, Philos. Trans. R. Soc., A, 2014, 372, 20130008 CrossRef PubMed
.
- G. Min and D. M. Rowe, Ring-structured thermoelectric module, Semicond. Sci. Technol., 2007, 22, 880–883 CrossRef CAS
.
- A. Schönecker, B. Kraaijveld, A. E. van Til, A.
J. Böttger, P. Brinks, M. Huijben and M. D. Heijer, Cost efficient manufacturing of silicide thermoelectric materials and modules using rgs technique, Mater. Today: Proc., 2015, 2, 538–547 Search PubMed
.
- F. Suarez, D. P. Parekh, C. Ladd, D. Vashaee, M. D. Dickey and M. C. Öztürk, Flexible thermoelectric generator using bulk legs and liquid metal interconnects for wearable electronics, Appl. Energy, 2017, 202, 736–745 CrossRef
.
- B. Alexander, A. Boscoe, M. Cabot, P. Dawsey, L. E. Barreau and R. Griffith, Berkeley-HAAS Case Series Alphabet Energy: Thermoelectrics and Market Entry, Calif. Manage. Rev., 2012, 55, 149–160 CrossRef
.
-
T. Hammel, R. Bennett and B. Sievers, Evolutionary upgrade for the multi-mission radioisotope thermoelectric generator (MMRTG), Proc. 2016 IEEE Aerospace Conference (IEEE 2016), pp. 1–8.
- J. R. Salvador, J. Y. Cho, Z. Ye, J. E. Moczygemba, A. J. Thompson, J. W. Sharp, J. D. Koenig, R. Maloney, T. Thompson, J. Sakamoto, H. Wang and A. A. Wereszczak, Conversion efficiency of skutterudite-based thermoelectric modules, Phys. Chem. Chem. Phys., 2014, 16, 12510–12520 RSC
.
- J. R. Salvdor, J. Y. Cho, Z. Ye, J. E. Moczygemba, A. J. Thompson, J. W. Sharp and J. D. König, Thermal to electrical energy conversion of skutterudite-based thermoelectric modules, J. Electron. Mater., 2013, 42, 1389–1399 CrossRef
.
- K. Bartholome, B. Balke, D. Zuckermann, M. Köhne, M. Müller, K. Tarantik and J. König, Thermoelectric modules based on half-heusler materials produced in large quantities, J. Electron. Mater., 2014, 43, 1775–1781 CrossRef CAS
.
- M. S. El-Genk, H. H. Saber, T. Caillat and J. Sakamoto, Tests results and performance comparisons of coated and un-coated skutterudite based segmented unicouples, Energy Convers. Manage., 2006, 47, 174–200 CrossRef CAS
.
- Q. Zhang, J. Liao, Y. Tang, M. Gu, C. Ming, P. Qiu, S. Bai, X. Shi, C. Uher and L. Chen, Realizing a thermoelectric conversion efficiency of 12% in bismuth telluride/skutterudite segmented modules through full-parameter optimization and energy-loss minimized integration, Energy Environ. Sci., 2017, 10, 956–963 RSC
.
-
K. Koumoto and T. Mori, Thermoelectric Nanomaterials: Materials Design and Applications, Springer Berlin, Heidelberg, 2013 Search PubMed
.
-
K. Ikoma, M. Munekiyo, K. Furuya, M. A. K. M. Kobayashi, T. A. I. T. Izumi and K. A. S. K. Shinohara, Thermoelectric module and generator for gasoline engine vehicles, in Proceedings ICT98, XVII International Conference on Thermoelectrics, IEEE, 1998, pp. 464–467.
- Data Sheet CMO-32-62S, TecTeg Manufacturers, Aurora, Ontario, Canada (https://tecteg.com/wp-content/uploads/2014/09/CMO-32-62S-OXIDE-ONLY-new.pdf).
- J. Yang and F. R. Stabler, Automotive applications of thermoelectric materials, J. Electron. Mater., 2009, 38, 1245–1251 CrossRef CAS
.
-
D. Brennan, R. Gilchrist and B. Wicksteed, Heat exchanger design and analysis for an automotive thermoelectric generator, VTMS11: Vehicle Thermal Management Systems Conference Proceedings, Woodhead Publishing, Coventry, 2013, pp. 115–126 Search PubMed
.
-
Z. Yang, J. Prado Gonjal, M. Phillips, S. Lan, A. Powell, P. Vaqueiro, M. Gao, R. Stobart and R. Chen, Improved thermoelectric generator performance using high temperature thermoelectric materials, SAE Technical Paper, 2017-01-0121, 2017.
- J. P. Roy, A. Ghoniem, R. Panora, J. Gehret, B. Falls, D. Wallace and D. Ott, Development and testing of the ultera® dual stage catalyst system on gasoline-fueled light duty vehicles (LDV's), SAE Int. J. Passeng.
Cars Mech. Syst., 2017, 10, 157–168 CrossRef
.
-
J. Sullivan, System and method for reducing vehicle emissions and/or generating hydrogen, US Pat., US20060179819A1, 2006 Search PubMed
.
- Department for Environment, Food and Rural Affairs, UK Government, UK plan for tackling roadside nitrogen dioxide concentrations: Technical Report, DEFRA, July 2017.
-
J. Heywood and D. MacKenzie, On the road toward 2050: potential for substantial reductions in light-duty vehicle energy use and greenhouse gas emissions, Massachusetts Institute of Technology, Sloan Automotive Laboratory Engineering Systems Division, MIT Energy Initiative Report, MIT, November 2015.
-
P. A. Wlodkowski, P. W. Sarnacki and T. T. Wallace, A hybrid marine vessel – supplemented by a thermoelectric generator (teg) power system – as a case study for reducing emissions and improving diesel engine efficiency, Proceedings of the 12thAnnual General Assembly of IAMU, 2012, pp. 313–318.
- J. Pawlick, J. T. Chen and Q. Y. Zhu, iSTRICT: An interdependent strategic trust mechanism for the cloud-enabled internet of controlled things, IEEE Trans. Inf. Foren. Sec., 2019, 14, 1654–1669 Search PubMed
.
- M. Haras and T. Skotnicki, Thermoelectricity for IoT - a review, Nano Energy, 2018, 54, 461–476 CrossRef CAS
.
-
G. L. Bennett, J. J. Lombardo, R. J. Hemler, G. Silverman, C. W. Whitmore, W. R. Amos, E. W. Johnson, R. W. Zocher, J. C. Hagan and R. W. Englehart, The general purpose heat source radioisotope thermoelectric generator a truly general-purpose space RTG, Proceedings of Space technology and Applications International Forum 2008, AIP Conf. Proc., 2008, vol. 969, 663.
- J. M. Dilhac, R. Montheard, M. Batleur, V. Boitier, P. Durand-Estebe and P. Tounsi, Implementation of thermoelectric generators in airliners for powering battery-free wireless sensor networks, J. Electron. Mater., 2014, 43, 2444–2451 CrossRef CAS
.
- I. Kunadian, R. Andrews, M. Pinar Mengüç and D. Qian, Thermoelectric power generation using doped MWCNTs, Carbon, 2009, 47, 589–601 CrossRef CAS
.
- Y. M. Zuev, W. Chang and P. Kim, Thermoelectric and magneto thermoelectric transport measurements of graphene, Phys. Rev. Lett., 2009, 102, 096807 CrossRef PubMed
.
- P. Wei, W. Bao, Y. Pu, C. N. Lau and J. Shi, Anomalous thermoelectric transport of Dirac particles in graphene, Phys. Rev. Lett., 2009, 102, 166808 CrossRef PubMed
.
- Y. Anno, Y. Imakita, K. Takei, S. Akita and T. Arie, Enhancement of graphene thermoelectric performance through defect engineering, 2D Mater., 2017, 4, 025019 CrossRef
.
- H. Sevinçli, C. Sevik, T. Çağın and G. Cuniberti, A bottom-up route to enhance thermoelectric figures of merit in graphene nanoribbons, Sci. Rep., 2013, 3, 1228 CrossRef PubMed
.
- Y. Lin, C. Norman, D. Srivastava, F. Azough, L. Wang, M. Robbins, K. Simpson, R. Freer and I. A. Kinloch, Thermoelectric Power Generation from Lanthanum Strontium Titanium Oxide at Room Temperature through the Addition of Graphene, ACS Appl. Mater. Interfaces, 2015, 29, 15898–15908 CrossRef
.
- Y. Y. Hsieh, Y. Zhang, L. Zhang, Y. Fang, S. Narayan Kanakaraaj, J.-H. Bahk and V. Shanov, High thermoelectric power-factor composites based on flexible three-dimensional graphene and polyaniline, Nanoscale, 2019, 11, 6552–6560 RSC
.
- T. Sugahara, Y. Ekubara, N. V. Nong, N. Kagami, K. Ohta, L. T. Hung, M. Okajima, S. Nambu and K. Suganuma, Fabrication with semiconductor packaging technologies and characterization of a large-scale flexible thermoelectric module, Adv. Mater. Technol., 2019, 4, 1800556 Search PubMed
.
- Z. Lu, H. Zhang, C. Mao and C. M. Li, Silk fabric-based wearable thermoelectric generator for energy harvesting from the human body, Appl. Energy, 2016, 164, 57–63 CrossRef CAS
.
- S. P. Beeby, M. J. Tudor and N. M. White, Energy harvesting vibration sources for microsystems applications, Meas. Sci. Technol., 2006, 17, R175 CrossRef CAS
.
- D. Shen, J.-H. Park, J. H. Noh, S.-Y. Choe, S.-H. Kim, H. C. Wikle and D.-J. Kim, Micromachined PZT cantilever based on SOI structure for low frequency vibration energy harvesting, Sens. Actuators, A, 2009, 154, 103–108 CrossRef CAS
.
-
V. Leonov, Energy harvesting for self-powered wearable devices, in Wearable Monitoring Systems, ed. A. Bonfiglio and S. D. De Rossi, Springer US, New York, 2011, pp. 27–49 Search PubMed
.
- V. Leonov, Human machine and thermoelectric energy scavenging for wearable devices, ISRN Renewable Energy, 2011, 2011, 785380 CrossRef
.
-
L. Petti, P. Aguirre, N. Münzenrieder, G. A. Salvatore, C. Zysset, A. Frutiger, L. Büthe, C. Vogt and G. Tröster, Mechanically flexible vertically integrated a-igzo thin-film transistors with 500 nm channel length fabricated on free standing plastic foil, 2013 IEEE Int. Electron Devices Meet., 2013, pp. 11.4.1–11.4.4.
-
Q. Huang, C. Lu, M. Shaurette and R. Cox, Environmental thermal energy scavenging powered wireless sensor network for building monitoring, in Proceedings of the 28th ISARC, Seoul, Korea, 2011, pp. 1–36.
- Y. J. Kim, H. M. Gu, C. S. Kim, H. Choi, G. Lee, S. Kim, K. K. Yi, S. G. Lee and B. J. Cho, High-performance self-powered wireless sensor node driven by a flexible thermoelectric generator, Energy, 2019, 162, 526–533 CrossRef
.
- J. J. Kuchle and N. D. Love, Self-powered wireless thermoelectric sensors, Measurement, 2014, 47, 26–32 CrossRef
.
- R. Hall, X. Wang, R. Ogden and L. Elghali, Transpired solar collectors for ventilation air heating, Energy, 2011, 164, 101–110 Search PubMed
.
-
H. A. Alfarra, Architectural integration of transpired solar thermal technology in building envelopes and associated technological innovation analysis, PhD thesis, University of Cardiff, 2014 Search PubMed
.
- US Department of Energy, Quadrennial Technology Review: An assessment of energy technologies and research opportunities, US Department of Energy, September 2015.
-
K. Yazawa and A. Shakouri, D135 exergy analysis of cost effective thermoelectric topping cycles, The Proceedings of the National Symposium on Power and Energy Systems, 2014, 19, pp. 137–138.
- Market Research Engine, Global Thermoelectric Generators Market Research Report - Industry Analysis, Size, Share, Growth, Trends and Forecast, 2014–2021, 2017.
- IDTech, IDTechEx report - Thermoelectric Energy Harvesting to 2023, in: IDTech edn, 2017.
- IDTechEx, IDTechEx report - Thermoelectric Energy Harvesting to 2028, in: IDTechEx (edn) 2018.
- Sub-Watt Thermoelectric Energy Harvesting Industry & Market Report, 2016, Infinergia Consulting, Grenoble, France.
- EPSRC Thermoelectric Network, 2018, http://www.thermoelectricnetwork.com/.
- M. L. Green, J. Hattrick-Simpers, G. Kusne and Z. Trautt, The materials genome initiative revolution, SAMPE J., 2019, 55, 6–13 Search PubMed
.
-
R. Potter, Heat recovery and cooling using thermoelectrics – exploiting UK strengths for commercial and environmental benefits in A position paper for Department of Business, Innovation and Skills (edn), 2017.
-
T. Kajikawa, Thermoelectric Roadmap, Shonan Institute of Technology, Japan, 2012 Search PubMed
.
|
This journal is © The Royal Society of Chemistry 2020 |