DOI:
10.1039/D4TB01603C
(Paper)
J. Mater. Chem. B, 2025,
13, 3895-3905
E-seed skin: a carbohydrate–protein hybrid nanostructure for delayed germination and accelerated growth†
Received
23rd July 2024
, Accepted 12th February 2025
First published on 17th February 2025
Abstract
The main purpose of the seed industry is to cater seeds with desired strength and viability, for which seed coating is a basic requirement. Herein, a hybrid coating of an electrosprayed protein (collagen) on electrospun nanofibers having a multidentate zinc-reinforced carbohydrate (pectin)/PVA composite (PVA/Pec/Zn/Col-NF) was developed. The zinc ensured covalent binding with the –OH in pectin/PVA in addition to the native galvanic binding between the polymers. Along with this, hydrogen bonding interactions between the –NH2 groups of electrosprayed collagen and the –OH groups in PVA/pectin further enabled the formation of a highly stable nanostructure. Controlled electrodeposition of collagen nanoparticles on the PVA/Pec/Zn-NF led to a decreased surface roughness scale with enhanced moisture resistance. The humidity resistance of the coating and the participation of zinc as a nutrient delayed the germination by 8 days and accelerated the tomato seedling's growth by approximately two times, respectively. The presence of zinc in the coating formulation enabled oxidative stress protection by boosting the superoxide dismutase activity. Moreover, the fungal resistance of the coating enabled the seeds to germinate even in the presence of phytopathogens. Thus, the approach of using the developed PVA/Pec/Zn/Col-NF coating material to construct a tight packing without affecting viability of the seed demonstrates a pioneering seed coating technique for increasing global food security amidst climate change and global warming.
1. Introduction
Seeds serve as consecrated energy links between successive generations, carrying vital genetic information for the continuity of life. Seed coating will play an important role in meeting the Food and Agriculture Organization's estimates of approximately 70–100% food production increase by 2050.1,2 This technology prevents premature breaking of seeds in dormancy due to humidity, pathogen infection, and poor nutrient supply for the initial establishment and provides seeds with the desired vigor and viability. This, in turn, supports a highly valuable million-dollar agricultural economy.
Cucumber seedlings treated with silicon dioxide quantum dots have been shown to stimulate plant growth.3 Another report has demonstrated the use of polymeric microgels as seed priming agents to enhance the germination of cucumber seedlings by facilitating iron uptake.4 To further improve this, coatings with nutrients such as zinc and other elements in nanoforms have been attempted.5–7 On the other hand, for endophytic pathogen and nematode control, a polyethylene glycol (PEG) blend with natural and synthetic antimicrobial agents has been prepared and tested.8–11 Furthermore, a two-layered biopolymer-based seed coating has been used to improve seed performance in semi-arid regions with water-deficient conditions.12 The above attempts were performed using techniques such as dip coating, spraying, fluidized bed, rotating drum, and rotary coating.13 Recently, advanced nanotechnology-based techniques, such as electrospinning, based on an electrohydrodynamic phenomenon are gaining importance in synthesizing nanofibers with diameters ranging from tens to hundreds of nanometers. The electrospinning approach is superior to traditional methods in terms of high surface area-to-volume ratio to cater the seeds with more nutrients, no residual solvent, and good thermal/mechanical stability.14–16
In the context of polymers, their structural and functional properties, such as hydrophilicity and hydrophobicity, are directly associated with the type of functional groups present in them. Hence, the choice of polymers is a crucial step while designing materials for seed coating, considering the control of various biological factors, such as seed viability and germination, nutrient release, and biotic and abiotic stress. Polyvinylpyrrolidone (PVP), a polymer listed in the GRAS (Generally Recognized As Safe) category, has been employed for nanofiber formation and coating on cowpea seeds.17,18 To make PVP flexible, it was blended with poly(vinyl alcohol) (PVA) and coated on canola seeds.19,20 Since the above coatings were not water resistant, the combination of PVP with poly(diethoxy) phosphazene (PPZ) was used to provide hydrophobicity.21 Parallelly, to improve the hydrophobicity with the use of biopolymers, acetylated cellulose has been synthesized and used for seed coating. The modified cellulose needs acetone/dimethylacetamide mixture to form a homogeneous solution for the electrospinning of cellulose diacetate, which raises environmental concerns.22,23
Recently, the concept of multifunctional films has been encouraged. To demonstrate this through a green approach, a cannabis extract having natural terpenoids has been developed as an antifungal film with chitosan.24 Chitosan nanoparticles loaded with essential oil have been explored for their antifungal effect.25 Similarly, cogon grass extract has been used for nanoparticle coating, stabilization, and antimicrobial properties.26 In a dynamic approach, photosensitive azo groups with carbohydrates have been made into a photo-controllable antimicrobial film through surface tension tuning.27 The nanostructures formed by electrospinning can give additional functions such as hydrophobicity and water diffusion. On the other hand, additional eco-friendly and natural components such as ceresin wax have been used to improve the hydrophobicity in agro-coatings.28
In the present work, a combination of electrospinning and electrospraying has been employed to construct hierarchical multifunctional laminar nanostructures29,30 with the aim of bringing stability, hydrophobicity, and nutrient supply to the seeds in the form of nano-coatings. Thus, collagen is electrosprayed onto electrospun PVA/Pectin/Zn nanofibers. Here, electrospraying takes place at a relatively low concentration and produces micro/nanoparticles that can enhance hydrophobicity.31 In addition, collagen, a well-known protein, available as waste from the leather industry, is used to form an epidermal coating on PVA/Pectin/Zn nanofibers to ensure elasticity, mechanical strength, and essential nutrient supply. Zinc acts as a cofactor for superoxide dismutase, the first antioxidant enzyme involved in the detoxification pathway of free radicals produced by energetically active mitochondrial action during seed germination.32,33 Thus, zinc can accelerate growth, and ensure antimicrobial properties against phytopathogens. These multifunctional properties of the coatings were tested on the seeds of an economically important crop viz., tomato (Solanum lycopersicum). Thus, we envisage that the combination of polymers and zinc ions with different properties can provide the advantages of preventing early seed germination and improving overall crop growth through a single coating.
2. Experimental
2.1 Chemicals
Poly(vinyl alcohol) (PVA, average molecular weight = 92.5 kDa; Himedia), pectin (Pec, average molecular weight = 37.5 kDa; SRL), type I collagen (Col) powder isolated from calf skin (molecular weight = 300 kDa) from Central Leather Research Institute, Chennai, glacial acetic acid (Sigma-Aldrich), sodium hypochlorite (Sigma-Aldrich, available chlorine content 4%–4.99%), polyvinyl pyrrolidone (SRL), nitroblue tetrazolium chloride (SRL), methionine, ferric-ethylene diamine-tetra acetic acid, potato dextrose broth, granulated (Himedia), agar (Himedia) and zinc sulfate heptahydrate (Himedia) were used to conduct all the experiments in this study. All chemicals and reagents were used without any further purification.
2.2. Synthesis of collagen-electrosprayed PVA/Pectin/ZnSO4 nanofibers (PVA/Pec/Zn/Col-NF) as a seed coating material
The synthesis of PVA/Pec/Zn/Col-NF was carried out in two steps: step 1: electrospinning and step 2: electrospraying (Fig. 1).
 |
| Fig. 1 Schematic of tomato seed coating with PVA/Pec/Zn/Col-NF. (a) Step 1: electrospinning of PVA/Pec/Zn to coat tomato seeds with PVA/Pec/Zn nanofibers and (b) step 2: electrospraying of collagen on seeds coated with PVA/Pec/Zn-NF. | |
2.2.1. Electrospinning of PVA/Pectin/ZnSO4 nanofibers (PVA/Pec/Zn-NF).
First, 0.6 g PVA was dissolved in 10 mL distilled water with stirring for 1 h at 80 °C. The solution was allowed to cool down followed by the addition of 0.2 g pectin. A mixture of PVA and pectin was obtained in water after continuous stirring for 2 h at room temperature (RT). After this, zinc sulphate heptahydrate powder was added to the above mixture to maintain the salt concentration at 0.3 mM in the solution. Finally, a PVA/Pec/Zn homogeneous solution was obtained after stirring for 1 h at RT. The PVA/Pec/Zn solution was filled in a 5 mL plastic (Dispo Van) syringe with a stainless-steel needle. Electrospinning was performed using an Espin Nanotech machine (Super ES2 model) equipped with a high-voltage power supply, a syringe pump, and a stainless-steel plate collector in a horizontal orientation at room temperature and ∼30% relative humidity. A positive DC voltage of 18 kV was applied to the needle tip and the distance from the needle tip to the collector was kept at 14 cm. The PVA/Pec/Zn solution was pumped using a syringe pump at a flow rate of 0.3 mL h−1. The PVA/Pec/Zn-NF (bare nanofibers without the seed) were collected on an electrically grounded static collector as a non-woven mat on aluminium foil and stored for further use.
2.2.2. Electrospraying of collagen to prepare PVA/Pec/Zn/Col-NF.
Following electrospinning, 0.8% homogeneous collagen solution prepared in 30% glacial acetic acid as a solvent using a homogenizer was electrosprayed over the PVA/Pec/Zn-NF under similar parameters for 0.5, 1, 1.5, 3, and 6 h with a PVA
:
Pec
:
Col weight ratio of 7
:
3
:
1.67, 7
:
3
:
3.33, 7
:
3
:
5, 7
:
3
:
7.5 and 7
:
3
:
15, respectively, to obtain the PVA/Pec/Zn/Col-NF (bare nanofibers without the seed).
2.3. Material characterization
A Bruker D8 Advance diffractometer with a Cu Kα1 source of radiation (λ = 1.5406 Å) at 25 mA and 40 kV was used for obtaining the X-ray diffraction (XRD) patterns of the samples. Fourier transform infrared (FTIR) spectroscopic analysis was done using a Bruker Vertex 70 series spectrometer in attenuated total reflectance mode. The structural characteristics and elemental composition (energy dispersive X-ray analysis, EDAX) of the coating material were obtained after electrospinning and electrospraying using a JEOL JSM IT300 field emission scanning electron microscope (FESEM). The particle/fiber distribution graphs for calculating the average diameter of nanofibers and nanoparticles (n = 50 each) were derived using ImageJ software. AFM imaging was done using an Oxford atomic force microscope in tapping mode. The water contact angle of the coating material and the surface tension of the precursor solution were determined using a KRUSS ADVANCE drop-shape analyzer through the sessile and pendant drop methods, respectively. A Bruker DektakXT Vision 64® surface profilometer was used to quantify the surface roughness of the coating material. The viscosity of the precursor solution was analyzed using an Anton Paar MCR 302 SN81518722 rheometer and a CP50-2 SN36079 as a measuring system. Absorbance was measured using a Tecan Infinite 200 PRO system at 570 nm for the estimation of superoxide dismutase activity. All measurements were done at room temperature.
2.3.1. Crystallinity Index (CI) calculation.
The CI was calculated using the XRD integration method by calculating the ratio of area under crystalline peaks to the total area under crystalline and amorphous peaks using eqn (1).34 |  | (1) |
where Ac is the area under crystalline peaks and Aa represents the area under amorphous peaks.
2.3.2. Water vapor permeability.
Water vapor permeability of PVA/Pec/Zn-NF and PVA/Pec/Zn/Col-NF was checked at 25 °C under different relative humidity conditions (40%, 50%, 60%, 70% and 80%). For this, PVA/Pec/Zn-NF and PVA/Pec/Zn/Col-NF were cut and wrapped over vials (mouth diameter = 1.5 cm) filled with distilled water. Vials were weighed and placed in a controlled-humidity chamber. The decrease in the weight of the vials was monitored after seven days. Experiments were done in duplicate. Water vapor permeability (WVP) was calculated using eqn (2).35 |  | (2) |
where Δm is the change in the mass of the vial in a given time (Δt), T is the thickness of nanofiber films, A is the exposed area of nanofiber films, and Psat is the saturation pressure of water vapor outside the vial according to relative humidity (%RH).
2.4. Procedure for seed coating
To perform the seed coating, initially, sterilized tomato seeds were embedded over an electrospun layer of PVA/Pec/Zn-NF on aluminium foil. Next, an additional PVA/Pec/Zn electrospinning cycle was performed on seeds embedded PVA/Pec/Zn-NF aluminium foil to ensure even coating on both the sides of seeds. Electrospinning was performed for 5 h on each side of the seeds. Following this, homogeneous collagen solution was electrosprayed and coated over the PVA/Pec/Zn-NF coated seeds for 6 h with a PVA
:
Pec
:
Col weight ratio of 7
:
3
:
15 on each side of the PVA/Pec/Zn-NF coated seeds to form a layer of collagen nanoparticles. For comparison studies, seed coating was also performed with PVA/Pec-NF and PVA/Pec/Zn-NF.
2.5. Characterization of coated tomato seeds
The surface morphology and cross-sectional view of the coated and uncoated seeds were observed using scanning electron microscopy with an accelerating voltage of 15 kV. For the thickness measurement, the coated seeds were cross-sectioned using a microtome (ThermoScientific, HM525 NX).
2.5.1. Relative Humidity (RH) experiment.
To test the stability of the coating to humidity, the uncoated and coated (PVA/Pec/Zn-NF and PVA/Pec/Zn/Col-NF) tomato seeds were placed in a humidity-controlled incubator (Metrex Scientific Instruments). The relative humidity range tested was 40%, 50%, 60%, 70%, and 80% for 7 days. The experiment was carried out in triplicate. Seeds were regularly weighed to determine the amount of moisture absorbed by the coating material, through the gravimetric method. The moisture uptake (MU) percentage was calculated using eqn (3).36 |  | (3) |
where m1 is the weight of seeds after 7 days, and m0 is the weight of seeds on the 0th day.
2.5.2. Drying rate.
Uncoated and coated (PVA/Pec/Zn-NF and PVA/Pec/Zn/Col-NF) seeds were kept in a humidity-controlled chamber at 60% RH for 7 days. The initial moisture uptake percentage was calculated using eqn (3). Seeds were dried at 30 °C for 24 h. The amount of water evaporated during the drying process (Mw) and drying rate (DR) were calculated using eqn (4) and (5), respectively.37 The experiment was carried out in duplicate. |  | (4) |
where M0 is the initial weight of seeds, Mi is the initial moisture content before drying, Mf is the final moisture content after drying. |  | (5) |
where t is the drying time.
2.5.3. Seed germination experiment.
The coated (PVA/Pec-NF, PVA/Pec/Zn-NF, and PVA/Pec/Zn/Col-NF) and uncoated seeds were incubated over Whatman filter paper soaked in water placed in Petri-dishes (15 seeds per treatment). The seeds were allowed to grow in this setup under dark conditions for 15 days at room temperature, with regular watering at definite intervals. Experiments were done in duplicate. Germination percentage (G%) and average length of seedlings were measured after incubation for 15 days.38 The germination percentage (G%) was calculated using eqn (6). |  | (6) |
2.5.4. Superoxide dismutase (SOD) assay.
The nitroblue tetrazolium (NBT) test was carried out to estimate the activity of superoxide dismutase.33 Fresh shoot tissues (0.5 gm) from seedlings grown for 15 days were homogenized in 0.1 M phosphate buffer saline (pH 7) containing polyvinyl pyrrolidone (1%) in a pestle and mortar. The extract was centrifuged at 14
000 g for 30 min at 4 °C to get the supernatant. The reaction mixture (4 mL) consisting of 0.15 mM Fe-EDTA, 20 mM methionine, 0.12 mM NBT, and 500 μL supernatant was prepared. Samples were illuminated for 30 min using a fluorescent lamp. Unilluminated samples were used as a blank. Absorbance measured at 570 nm was used to calculate the enzyme activity. One unit of enzyme is defined as the amount of enzyme required to cause 50% inhibition in the reduction of NBT.
2.5.5. Fungal resistance of coated seeds.
To determine the anti-fungal property, the seed germination efficiency of the coated (PVA/Pec-NF, PVA/Pec/Zn-NF, and PVA/Pec/Zn/Col-NF) and uncoated seeds was monitored in the presence of Colletotrichum capsici fungal mat. The fungal mycelia were allowed to grow on potato dextrose agar plates along with uncoated and coated seeds (5 seeds per treatment). The plates were incubated at 28 °C and regularly monitored for 15 days. The experiment was performed in duplicate. The germination percentage and average seedling length were calculated as described above.
2.6. Biodegradability test
To confirm the biodegradability of the seed coating material, a standard soil burial test was carried out using soil collected from the Institute of Nanoscience and Technology. Stones, debris, and hard clumps from the soil were removed and the soil was kept in a foam box. A small amount of PVA/Pec/Zn/Col-NF coating material was weighed and placed inside the soil at a depth of ∼5 cm. The setup was incubated for 60 days, with watering at regular intervals. After every 10 days, samples were taken out to quantify the degradation gravimetrically. For the gravimetric analysis, the samples removed from the soil were rinsed with water to remove unwanted soil particles and air-dried before weighing. The experiment was carried out in triplicate. The percentage of weight loss at each interval was calculated using eqn (7) as mentioned below.39 |  | (7) |
where M1 is the initial weight of the coating material, and M2 is the weight of the coating material at each interval.
2.7. Statistical analysis
Data obtained from different experiments were analyzed using OPSTAT (one-factor analysis) to determine statistical significance at various levels. All graphs were plotted using Origin Pro 9 software.
3. Results and discussion
The fabrication of the eco-friendly seed coating material was performed by two sequential steps: (1) electrospinning of PVA/Pec/Zn nanofibers on tomato seeds as the foundation layer with flexibility and mechanical strength, along with nutrition and antimicrobial properties, and (2) electrospraying of collagen on PVA/Pec/Zn-NF coated seeds (Fig. 1). Here, the low viscous collagen electrospraying resulted in the formation of a hydrophobic coating to restrict the undesirable early seed germination.
3.1. Coating material characterization
The initial formation of PVA/Pec/Zn through electrospinning resulted in the formation of a highly entangled fibrous network with an average diameter of ∼102 nm (Fig. S1a and b, ESI†). The elemental mapping of the PVA/Pec/Zn-NF in Fig. S1c–f (ESI†) confirms the uniform distribution of Zn across the NF structure. Following this, collagen nanoparticles were electrosprayed on the PVA/Pec/Zn-NF mat for 30 min and 6 h, which are shown in Fig. S2a (ESI†) and Fig. 2a, respectively. As can be seen, the nanofibrous PVA/Pec/Zn-NF network is distinctly visible with the deposition of spherical collagen nanoparticles on individual fibers after 30 min (Fig. S2a, ESI†) and it is completely covered with collagen nanoparticles wherein the PVA/Pec/Zn nanofibrous network is concealed after 6 h (Fig. 2a and Fig. S2c, ESI†). The cross-sectional FESEM image of collagen nanoparticles electrosprayed on the PVA/Pec/Zn-NF mat for 6 h is shown in Fig. S2b (ESI†). The average diameter of electrosprayed collagen nanoparticles was found to be ∼240 nm (Fig. S2c and d, ESI†). AFM images of PVA/Pec/Zn-NF before and after electrospraying of collagen for 6 h are shown in Fig. S3 (ESI†). The AFM image of PVA/Pec/Zn-NF shows a fibrous network, whereas PVA/Pec/Zn/Col-NF demonstrates a uniform deposition of collagen nanoparticles over the nanofibrous mat after 6 h of electrospraying. Hence, these results correlate well with the respective FESEM images i.e., Fig. S1a and S2 (ESI†) and Fig. 2a.
 |
| Fig. 2 (a) FESEM image of collagen electrosprayed for 6 h over PVA/Pec/Zn-NF; (b) FTIR spectra of PVA/Pec/Zn/Col-NF, PVA/Pec/Zn-NF, and PVA/Pec-NF; deconvoluted C 1s XPS spectra of (c) PVA/Pec-NF, (d) PVA/Pec/Zn-NF, and (e) PVA/Pec/Zn/Col-NF; (f) XRD patterns of PVA/Pec/Zn/Col-NF, PVA/Pec/Zn-NF, and PVA/Pec-NF. | |
The morphological variation of PVA/Pec/Zn-NF and PVA/Pec/Zn/Col-NF could be attributed to the surface tension and viscosity of the precursor solution used for electrospinning and electrospraying, respectively. Here, the surface tension and viscosity of the PVA/Pec/Zn solution were 58 mN m−1 and 359 mPa s, respectively, which favored the formation of a stable Taylor cone to result in nanofiber formation, whereas very high surface tension, i.e., 115 mN m−1, and low viscosity, i.e., 86 mPa s of collagen solution dominate the phenomenon of Rayleigh instability, which resulted in rapid disintegration of the liquid jet into fragmented spherical nanoparticles.40 Further, the appearance of amide I (1657 cm−1), amide II (1533 cm−1), amide III (1242 cm−1), amide A (3063 cm−1) and amide B (2925 cm−1) bands from collagen; O–H and C–O stretching vibrations around 3300 and 1100 cm−1, respectively, from both PVA and pectin; and C–C stretching vibration at 1014 cm−1 from pectin (Fig. S4, ESI†) in the FTIR spectra of PVA/Pec/Zn/Col-NF and PVA/Pec/Zn-NF confirms the hybrid coating (Fig. 2b).
Following this, XPS analysis was performed to understand the chemical interactions between coating components. The appearance of a strong N peak in the XPS survey spectrum of PVA/Pec/Zn/Col-NF along with Zn, C, and O peaks confirms successful electrospraying of collagen on PVA/Pec/Zn-NF (Fig. S5a, ESI†), which is absent in PVA/Pec/Zn-NF. Further, C 1s core level spectra of PVA/Pec-NF, PVA/Pec/Zn-NF, and PVA/Pec/Zn/Col-NF were deconvoluted to understand the chemical modification to the sequential addition. The shift of the C–O bond peak in PVA/Pec-NF from 285.9 eV in pectin and 286.1 eV in PVA (Fig. S5b and c, ESI†) to a higher binding energy of 286.2 eV suggests the formation of intermolecular hydrogen bonds between the O–H and COOH groups of PVA and pectin, respectively (Fig. 2c).41 Next, the addition of Zn to PVA/Pec resulted in the appearance of a peak at 285.8 eV, which corresponds to the C–O–Zn bond (Fig. 2d), indicating the covalent bonding of Zn with the O–H groups of PVA and pectin. Deconvoluted C 1s spectra of PVA/Pec/Zn/Col-NF show a C–N (amide bond) peak at 285.6 eV in addition to the C–O–Zn bond (Fig. 2e).42 Further to understand the binding between PVA/Pec/Zn-NF and the collagen nanoparticle layer, the N 1s core level spectrum of PVA/Pec/Zn/Col-NF was deconvoluted. A shift was observed for the N–C bond to a higher binding energy of 399.7 eV (Fig. S5d, ESI†) from 399.5 eV for the pristine collagen fiber,43 which can be attributed to the formation of hydrogen bonds between the N atom of the collagen nanoparticle layer and the H atom of hydroxyl groups in PVA/pectin (C–N⋯HO–C).
The XRD data show reduced crystallinity of PVA/Pec/Zn/Col-NF in comparison to the PVA-NF, PVA/Pec-NF, and PVA/Pec/Zn-NF from 45% to 30%, as depicted in Fig. 2f and Table S1 (ESI†), which imparts an amorphous behavior to the coating material and provides significant stability to the coating.
3.2. Physical characterization
Following the chemical characterization, the strength and hydrophobicity of the coating material without the tomato seeds were probed to ensure stability and water resistance. For strength measurement, Young's modulus of the coating material was quantified from the stress–strain curve (Fig. S6, ESI†). The PVA/Pec/Zn/Col-NF coating material shows a relatively higher Young's modulus (∼3 MPa) as compared to PVA/Pec/Zn-NF (∼2 MPa), PVA/Pec-NF (∼1 MPa) and PVA-NF (∼0.25 MPa) (Fig. 3a). Hence, further studies were limited to PVA/Pec/Zn/Col-NF and PVA/Pec/Zn-NF. The hydrophobicity of the coating material was determined by measuring the water contact angle. The coating material has developed a hydrophobic nature after the electrospraying of collagen (∼126°) from a hydrophilic PVA/Pec/Zn-NF (∼51°) (Fig. S7a and b, ESI†). To understand the reason behind this, subsequently, the impact of the duration of electrospraying on the hydrophobicity of the coating material was explored, which revealed a significant rise in the water contact angle from ∼ 60° to ∼126° after 6 h of electrospraying (Fig. 3b). This may be attributed to the material surface properties such as roughness and surface energy, which influence the surface's contact angle. The surface roughness of the coating material is reduced ∼2-fold after electrospraying collagen on PVA/Pec/Zn-NF for 6 h from the micron to the nano range (Fig. 3c and Fig. S8a–f, ESI†). Hence, the reduction in surface roughness from the micron to the nano range with increasing weight percentage of collagen deposition (14%, 25%, 33%, 43% and 60% calculated by dividing the weight of collagen deposited by the total weight of PVA/Pec/Zn/Col-NF at 0.5, 1, 1.5, 3 and 6 h of electrospraying) would result in enhanced hydrophobicity as smoother surfaces with a low surface area exhibit low surface energy compared to rough surfaces. A highly rough surface implies a greater surface area, leading to reduced contact angle with more wetting, and vice versa.44 The decrease in the rate of contact angle increase after 3 h of collagen electrospraying may be due to the saturation of surface energy. In addition, the high surface tension of the collagen solution led to the formation of a nanoparticle layer with low surface energy and high contact angle, leading to a highly hydrophobic surface. Further, to verify this, the water vapor permeability of the coating material was examined at 40%, 50%, 60%, 70% and 80% relative humidity. PVA/Pec/Zn/Col-NF shows reduced water vapor permeability in comparison to PVA/Pec/Zn-NF in all ranges of relative humidity (Fig. 3d), thereby demonstrating superior hydrophobicity of the coating material.
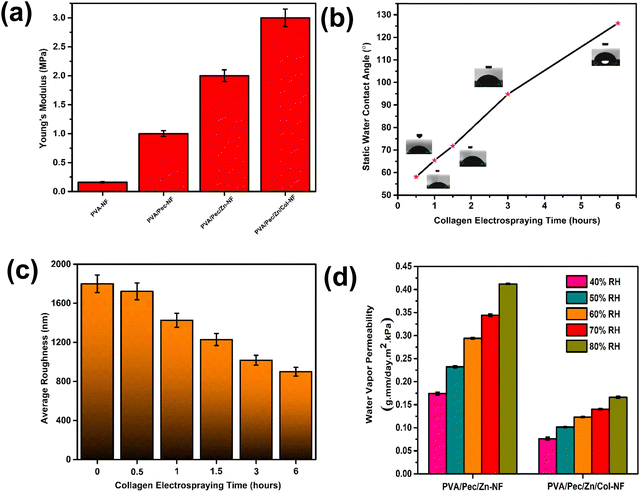 |
| Fig. 3 (a) Graphical representation of Young's modulus of PVA-NF, PVA/Pec-NF, PVA/Pec/Zn-NF, and PVA/Pec/Zn/Col-NF; (b) impact of duration of collagen electrospraying on the static water contact angle of PVA/Pec/Zn/Col-NF; (c) average roughness of PVA/Pec/Zn-NF and PVA/Pec/Zn/Col-NF at different hours of electrospraying; and (d) water vapor permeability of PVA/Pec/Zn-NF and PVA/Pec/Zn/Col-NF at different RH. | |
3.3 Coated seed characterization
The excellent hydrophobicity achieved through optimized electrospinning and electrospraying conditions of the coating material motivated us to carry out tomato seed coating. The surface morphology of the PVA/Pec/Zn/Col-NF coated seed (Fig. 4b) showed a significantly smooth surface as compared to the uncoated seed (Fig. 4a). The cross-sectional images of the uncoated and PVA/Pec/Zn/Col-NF coated seeds are shown in Fig. S9a and b (ESI†), respectively. Next to determine the thickness of the coating, the cross-sectional morphology of PVA/Pec/Zn-NF and PVA/Pec/Zn/Col-NF coated seeds was captured using FESEM (Fig. 4c and d). The higher magnification images of PVA/Pec/Zn-NF and PVA/Pec/Zn/Col-NF coated seeds showed the presence of ∼40 and ∼60 μm thick layers, respectively (Fig. 4e and f). The additional 20 μm thickness of PVA/Pec/Zn/Col-NF originates from the electrosprayed collagen nanoparticles (Fig. 4f, inset).
 |
| Fig. 4 FESEM images showing the surface morphology of (a) the uncoated and (b) PVA/Pec/Zn/Col-NF-coated seeds after 6 h of electrospraying. Cross-sectional FESEM images of (c) PVA/Pec/Zn-NF- and (d) PVA/Pec/Zn/Col-NF-coated seeds. Magnified images of (e) PVA/Pec/Zn-NF- and (f) PVA/Pec/Zn/Col-NF-coated seeds with coating thickness measurements. The inset of f shows a 20 μm thick electrosprayed collagen layer after 6 h of electrospraying. | |
3.3.1. Characterization for industrial application.
A major challenge faced by the industry during seed storage is early seed germination, which is due to moisture uptake. To quantify the water uptake, the coated (PVA/Pec/Zn-NF and PVA/Pec/Zn/Col-NF) and uncoated seeds were incubated at different relative humidity ranging from 40% to 80% for 7 days, and measured gravimetrically. At 40% RH, none of the treatments showed moisture absorption (Fig. 5a), whereas at 50% RH, only PVA/Pec/Zn/Col-NF coated seeds exhibited zero moisture uptake. Further, an increase in the RH from 60% to 80% led to a rise in moisture uptake percentage for all the treatments proportionally. However, PVA/Pec/Zn/Col-NF and PVA/Pec/Zn-NF coated seeds show relatively reduced moisture uptake in the 60% to 80% RH range, as compared to uncoated seeds. This can be due to the slow diffusion of water vapor through a porous network of nanofibers bound tightly due to the multivalent binding between the glycol group and Zn.45 The zero tolerance at 50% RH by PVA/Pec/Zn/Col-NF further highlights the role of the hydrophobic collagen nanoparticle layer in addition to the electrospun PVA/Pec/Zn-NF network. Hence, these findings suggest that PVA/Pec/Zn/Col-NF can serve as a stable coating material for seed storage.
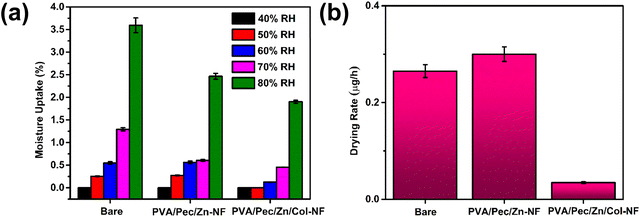 |
| Fig. 5 (a) Moisture uptake of bare (uncoated), PVA/Pec/Zn-NF- and PVA/Pec/Zn/Col-NF-coated seeds at different RH and (b) drying rate of uncoated, PVA/Pec/Zn-NF- and PVA/Pec/Zn/Col-NF-coated seeds. | |
A comparison between the drying rates of uncoated and coated seeds, PVA/Pec/Zn/Col-NF coated seeds, showed a lower rate of water evaporation as compared to uncoated and PVA/Pec/Zn-NF coated control seeds (Fig. 5b). This may be because of the higher roughness (Fig. 3c) in the control seeds with more surface area leading to the increased rate of evaporation.
3.3.2. Germination study.
Although the coating qualifies the seed for storage, it is important to understand whether the coating is suitable for germination. All the coated seeds showed above 80% germination within the 13th day after incubation; thus, the seed did not undergo significant toxicity due to the coating (Fig. 6a–e). An interesting observation here is that the treatment PVA/Pec/Zn/Col-NF showed a delay in germination by 8 days, whereas PVA/Pec-NF and PVA/Pec/Zn-NF showed a delay in the range of 2–3 days only, compared to uncoated bare seeds (Fig. 6e). A more interesting observation in this experiment is that the average seedling length is higher in all the coated (PVA/Pec-NF, PVA/Pec/Zn-NF, and PVA/Pec/Zn/Col-NF) seeds in comparison to uncoated bare seeds (Fig. 6f). Among the coated seeds, the PVA/Pec/Zn-NF coated seeds have a higher average seedling length i.e., ∼5.5 cm as compared to PVA/Pec/Zn/Col-NF coated seeds (∼4.2 cm) after 15 days of incubation. However, considering the delay in germination observed in PVA/Pec/Zn/Col-NF treatment, the rate of growth is almost the same as in PVA/Pec/Zn-NF. The accelerated growth in the treatments with the zinc ion in the fiber may be due to the enhanced antioxidant participation, which was further confirmed using a superoxide dismutase estimation assay.33 The SOD activity was significantly higher in PVA/Pec/Zn-NF and PVA/Pec/Zn/Col-NF coated seeds containing zinc as compared to controls without zinc (Fig. 7), highlighting the role of SOD enzyme in neutralizing harmful superoxide radicals. This result demonstrates the importance of the zinc ion in the coating system, which enhances seed protection under oxidative stress conditions. The collective results suggested that PVA/Pec/Zn/Col-NF coated seeds show a regulatory control of seed germination with desirable seedling length.
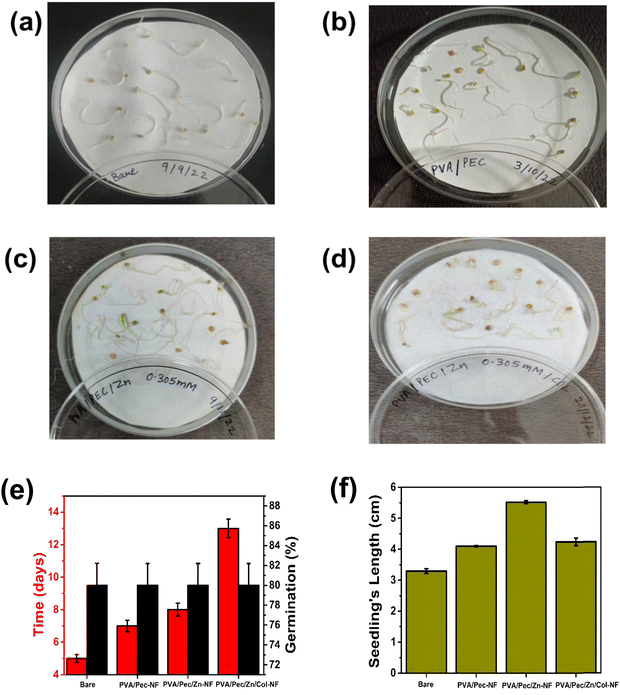 |
| Fig. 6 Images showing germination of (a) uncoated, (b) PVA/Pec-NF-, (c) PVA/Pec/Zn-NF-, and (d) PVA/Pec/Zn/Col-NF-coated seeds after 15 days of incubation. Graphs showing (e) the number of days required for 80% germination of seeds and (f) the average length of seedlings in all treatments after 15 days of incubation. | |
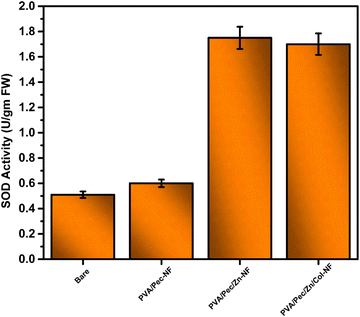 |
| Fig. 7 Graph showing the SOD activity of bare, PVA/Pec-NF-, PVA/Pec/Zn-NF-, and PVA/Pec/Zn/Col-NF-coated seeds grown for 15 days. | |
3.3.3. Fungal resistance of coated seeds.
One of the major biotic stresses faced by the seeds in the rhizosphere is fungal infection. Here, the impact of seed coating on fungal infection resistance was evaluated by checking the germination percentage in the presence of Colletotrichum mycelia. The PVA/Pec/Zn/Col-NF (treatment) coated seeds showed 80% germination with ∼1.5 cm seedling length, whereas a complete loss of germination was observed in the case of control experiments (uncoated, PVA/Pec-NF and PVA/Pec/Zn-NF coated seeds) (Fig. 8a and b and Fig. S10a–d, ESI†). This may be attributed to the presence of the outermost hydrophobic collagen nanoparticle layer, which provides a less humid environment and unfavorable anthracnose epidemiology conditions and thereby minimizes the threat of fungal outbreaks.46
 |
| Fig. 8 Graphical illustration of (a) percent germination and (b) average seedlings length of bare, PVA/Pec-NF-, PVA/Pec/Zn-NF (control experiments), and PVA/Pec/Zn/Col-NF (treatment)-coated seeds grown in the presence of Colletotrichum mat for 15 days, and (c) biodegradability of PVA/Pec/Zn/Col-NF at different intervals (0, 10, 20, 30, 40, 50, and 60 days). | |
3.4. Biodegradability
The environment friendly property of the PVA/Pec/Zn/Col-NF coating material was determined by studying the biodegradability of the material through a soil burial test. The coating material buried under the soil was examined at regular intervals for 60 days. In this duration, ∼30% degradation was observed (Fig. 8c). Thus, the coating material possesses the eco-friendly property, as in the total duration of the crop production around 100 days, the coating material is expected to degrade almost completely, as the later part of the degradation is expected to be relatively faster than the initial rate of degradation. This can be because of the formation of a porous structure during the degradation process, thus increasing the surface area for microbial attack.47
4. Conclusions
In summary, a successful bio-based seed coating has been developed by electrospraying collagen on electrospun PVA/Pec/Zn-NF. The optimized collagen electrospraying provided excellent hydrophobicity, which in turn delayed the seed germination and maintained the potency for long time storage in humid conditions. Further, the multifunctional characteristics of the coating material, such as hydrophobicity, low roughness, low water vapor permeability, high superoxide dismutase activity, and low moisture uptake, have improved the overall seed viability in terms of germination percentage and fungal resistance. Thus, the developed biodegradable hybrid seed coating network paves the way for next-generation sustainable agriculture and farming.
Abbreviations
PVA | Poly(vinyl alcohol). |
Pec | Pectin. |
Zn | Zinc. |
Col | Collagen. |
NF | Nanofibers. |
RH | Relative humidity. |
PVP | Polyvinylpyrrolidone. |
GRAS | Generally recognized as safe. |
PPZ | Poly(diethoxy) phosphazene. |
CLRI | Central Leather Research Institute. |
CI | Crystallinity index. |
WVP | Water vapor permeability. |
MU | Moisture uptake. |
G (%) | Germination percentage. |
OPSTAT | Online statistical analysis tool. |
Data availability
Data will be made available upon request.
Conflicts of interest
There are no conflicts to declare.
Acknowledgements
P. S. thanks INST for fellowship and research facilities. T. P. thanks CSIR-CLRI for funding through the Sustainable Environment Research Group Project under the Sustainability Theme. CSIR-CLRI Communication No. 1987. V. S. thanks the Government of India DBT (BT/PR36476/NNT/28/1723/2020).
References
-
A. Nikos and B. Jelle, World agriculture towards 2030/2050: the 2012 revision. ESA Working Paper No. 12-03, Food and Agriculture Organization of the United Nations, 2012 DOI:10.22004/ag.econ.288998.
- M. Safari, E. Dehghan and A. Rohani, ACS Agric. Sci. Technol., 2023, 3, 918–925 CrossRef CAS.
- Y. Li, W. Li, H. Zhang, R. Dong, D. Li, Y. Liu, L. Huang and B. Lei, J. Mater. Chem. B, 2019, 7, 1107–1115 RSC.
- F. B. Alves, H. E. Andrada, B. A. Fico, J. S. Reinaldi, D. C. Tavares, I. S. Squarisi, G. S. Montanha, L. G. Nuevo, H. W. P. de Carvalho, C. A. Perez and E. F. Molina, J. Agric. Food Chem., 2024, 72, 14570–14580 CrossRef CAS PubMed.
- P. Kumari, N. Kumari, C. Mohan, C. Chinglenthoiba and K. T. T. Amesho, Int. J. Biol. Macromol., 2024, 257, 128278 CrossRef CAS PubMed.
- B. Ndaba, A. Roopnarain, B. Vatsha, S. Marx and M. Maaza, ACS Agric. Sci. Technol., 2022, 2, 1218–1229 CrossRef CAS.
- L. Abeywardana, M. de Silva, C. Sandaruwan, D. Dahanayake, G. Priyadarshana, S. Chathurika, V. Karunaratne and N. Kottegoda, ACS Agric. Sci. Technol., 2021, 1, 230–239 CrossRef CAS.
- Y. Gu, Y. Pang, D. Yang, Y. Qian, H. Lou and M. Zhou, Ind. Crops Prod., 2022, 182, 114877 CrossRef CAS.
- F. H. Haghighi, M. Mercurio, S. Cerra, T. A. Salamone, R. Bianymotlagh, C. Palocci, V. R. Spica and I. Fratoddi, J. Mater. Chem. B, 2023, 11, 2334–2366 RSC.
- M. B. Cadena, G. M. Preston, R. A. L. Van der Hoorn, N. A. Flanagan, H. E. Townley and I. P. Thompson, Ind. Crops Prod., 2018, 124, 755–764 CrossRef.
- M. de Souza Alves, E. A. D. P. de Medeiros, C. da Silva Barbosa Pereira, Y. N. Moreira, J. da Silva Cappato, R. de Paulo Osorio, C. J. Riger, L. V. dos Santos, R. D. Mesquita, E. G. Pontes and M. A. A. de Souza, Ind. Crops Prod., 2023, 199, 116760 CrossRef.
- A. T. Zvinavashe, J. Laurent, M. Mhada, H. Sun, H. M. E. Fouda, D. Kim, S. Mouhib, L. Kouisni and B. Marelli, Nat. Food, 2021, 2, 485–493 CrossRef PubMed.
- I. Rocha, Y. Ma, P. Souza-Alonso, M. Vosátka, H. Freitas and R. S. Oliveira, Front. Plant Sci., 2019, 10, 1357 CrossRef PubMed.
- J. Xue, T. Wu, Y. Dai and Y. Xia, Chem. Rev., 2019, 119, 5298–5415 CrossRef CAS PubMed.
- D. Li and Y. Xia, Adv. Mater., 2004, 16, 1151–1170 CrossRef CAS.
- L. Hao, M. Guan, Q. Zheng, M. Zhou, Z. Yin, H. Zhou and X. Zhou, Environ. Sci.: Nano, 2023, 10, 2343–2358 RSC.
- V. Krishnamoorthy and S. Rajiv, ACS Sustainable Chem. Eng., 2017, 5, 146–152 CrossRef CAS.
- V. Krishnamoorthy, G. Elumalai and S. Rajiv, New J. Chem., 2016, 40, 3268–3276 RSC.
- Z. Hussain, M. A. Khan, F. Iqbal, M. Raffi and F. Y. Hafeez, J. Agric. Food Chem., 2019, 67, 5085–5095 CrossRef CAS PubMed.
- A. Sikder, A. K. Pearce, S. J. Parkinson, R. Napier and R. K. O’Reilly, ACS Appl. Polym. Mater., 2021, 3, 1203–1217 CrossRef CAS.
- V. Krishnamoorthy and S. Rajiv, J. Cleaner Prod., 2018, 177, 69–78 CrossRef CAS.
- B. V. Farias, T. Pirzada, R. Mathew, T. L. Sit, C. Opperman and S. A. Khan, ACS Sustainable Chem. Eng., 2019, 7, 19848–19856 CrossRef CAS.
- T. Xu, C. Ma, Z. Aytac, X. Hu, K. W. Ng, J. C. White and P. Demokritou, ACS Sustainable Chem. Eng., 2020, 8, 9537–9548 CrossRef CAS.
- M. Menossi, G. Tejada, S. L. Colman, D. Nercessian, J. R. Mendieta, G. A. Islan and V. A. Alvarez, Colloids Surf., A, 2024, 685, 133207 CrossRef CAS.
- M. Mondejar-Lopez, A. Rubio-Moraga, A. J. Lopez-Jimenez, J. C. G. Martinez, O. Ahrazem, L. Gomez-Gomez and E. Niza, Carbohydr. Polym., 2022, 277, 118815 CrossRef CAS.
- K. Moorthy, K.-C. Chang, P.-J. Yu, W.-J. Wu, M.-Y. Liao, H.-C. Huang, H.-C. Chien and C.-K. Chiang, New J. Chem., 2022, 46, 15301–15312 RSC.
- Y. Hu, W. Zou, V. Julita, R. Ramanathan, R. F. Tabor, R. Nixon-Luke, G. Bryant, V. Bansal and B. L. Wilkinson, Chem. Sci., 2016, 7, 6628–6634 RSC.
- B. Su, M. Yang, B. Gao, Z. Li, X. Zhao, S. Zhang, D. Cheng, T. Shen, Y. Yao and Y. Yang, J. Cleaner Prod., 2024, 452, 142145 CrossRef CAS.
- L.-C. Hu, C.-H. Xue, B.-Y. Liu, X.-J. Guo, J.-H. Wang and F.-Q. Deng, ACS Appl. Polym. Mater., 2022, 4, 3343–3351 CrossRef CAS.
- S. Sett, M. W. Lee, M. Weith, B. Pourdeyhimi and A. L. Yarin, J. Mater. Chem. B, 2015, 3, 2147–2162 RSC.
- A. Esidir, N. B. Kiremitler, M. Kalay, A. Basturk and M. S. Onses, ACS Appl. Polym. Mater., 2022, 4, 5952–5964 CrossRef.
- W. Ma, X. Guan, J. Li, R. Pan, L. Wang, F. Liu, H. Ma, S. Zhu, J. Hu, Y.-L. Ruan, X. Chen and T. Zhang, Proc. Natl. Acad. Sci. U. S. A., 2019, 116, 4716–4721 CrossRef CAS PubMed.
- A. Singh, N. B. Singh, I. Hussain, H. Singh, V. Yadav and S. C. Singh, J. Biotechnol., 2016, 233, 84–94 CrossRef CAS PubMed.
- A. Osorio-Madrazo, L. David, S. Trombotto, J.-M. Lucas, C. Peniche-Covas and A. Domard, Biomacromolecules, 2010, 11, 1376–1386 CrossRef CAS PubMed.
- A. Buslovich, B. Horev, V. Rodov, A. Gedanken and E. Poverenov, J. Mater. Chem. B, 2017, 5, 2655–2661 RSC.
- R. D. Guha, E. O. Danilov, K. Berkowitz, O. Oluwajire and L. R. Grace, ACS Appl. Polym. Mater., 2023, 5, 400–411 CrossRef CAS.
- E. L. Rulazi, J. Marwa, B. Kichonge and T. Kivevele, ACS Omega, 2023, 8, 43304–43317 CrossRef CAS PubMed.
- G. Kan, W. Zhang, W. Yang, D. Ma, D. Zhang, D. Hao, Z. Hu and D. Yu, Mol. Genet. Genomics, 2015, 290, 2147–2162 CrossRef CAS PubMed.
- L. Liu, Y. Ni, Y. Zhi, W. Zhao, M. Pudukudy, Q. Jia, S. Shan, K. Zhang and X. Li, Macromolecules, 2020, 53, 936–945 CrossRef CAS.
- E. Simsek, K. Acatay and Y. Z. Menceloglu, Langmuir, 2012, 28, 14192–14201 CrossRef CAS PubMed.
- F. Lin, Z. Wang, J. Chen, B. Lu, L. Tang, X. Chen, C. Lin, B. Huang, H. Zeng and Y. Chen, J. Mater. Chem. B, 2020, 8, 4002–4015 RSC.
- S. Thareja and A. Kumar, J. Phys. Chem. C, 2021, 125, 24837–24848 CrossRef CAS.
- J. Guo, H. Wu, X. Liao and B. Shi, J. Phys. Chem. C, 2011, 115, 23688–23694 CrossRef CAS.
- J. A. Juárez-Moreno, A. Ávila-Ortega, A. I. Oliva, F. Avilés and J. V. Cauich-Rodríguez, Appl. Surf. Sci., 2015, 349, 763–773 CrossRef.
- D. Fernandez-Villa, M. R. Aguilar and L. Rojo, J. Mater. Chem. B, 2024, 12, 7153–7170 RSC.
- A. Saxena, R. Raghuwanshi, V. K. Gupta and H. B. Singh, Front. Microbiol., 2016, 7, 1527 Search PubMed.
- E. M. N. Polman, G.-J. M. Gruter, J. R. Parsons and A. Tietema, Sci. Total Environ., 2021, 753, 141953 CrossRef CAS PubMed.
|
This journal is © The Royal Society of Chemistry 2025 |
Click here to see how this site uses Cookies. View our privacy policy here.