Drinking water contamination from the thermal degradation of plastics: implications for wildfire and structure fire response†
Received
12th September 2020
, Accepted 23rd November 2020
First published on 14th December 2020
Abstract
This study was conducted to determine if the thermal degradation of various plastic drinking water pipes (i.e., PEX, HDPE, PP, PVC, and CPVC) may be a source of drinking water contamination. Widespread volatile organic compound (VOC) contamination was found in water distribution systems following three wildfires in California. A potential source of this contamination was thought to be due to the degradation of plastic components in drinking water distribution systems. Eleven plastic drinking water pipes, across eight brands, were exposed to elevated temperatures (200 °C to 400 °C), and subsequently submerged in water or in n-hexane to observe the extent of VOC leaching. Results indicated that thermally damaged drinking water pipes can be sources of VOC leaching, with ten of the eleven materials leaching benzene, a carcinogen, into water. As exposure temperature increased, an increase in VOC leaching was observed in the polyethylene materials. Conversely, in the vinyl materials the significant mass loss associated with high exposure temperature was inversely proportional to the amount of BTEX leaching that was observed. Additional tentatively identified compounds (TICs), consisting primarily of aliphatic hydrocarbons, saturated ketones, or aromatic compounds, were found in the water (22 TICs) and n-hexane (134 TICs) leachate of burned plastics. This study has significant implications for both wildfire and structure fire recovery as plastic materials are increasingly being used in buried and building plumbing, and visual inspection is not a sufficient indicator of contamination risk.
Water impact
Plastic drinking water pipe thermal degradation and resulting water quality impacts were explored. Thermal damage prompted organic contaminant generation and leaching into drinking water, to include benzene and others. A high level of mass loss, specifically for the vinyl materials, was inversely proportional to leaching. Results should be considered by responders, utility, health and building officials before and after fire events.
|
1. Introduction
In the aftermath of wildfires and structure fires, long-term and potentially unforeseen challenges can exist for impacted communities, especially with regards to their drinking water supply.1–3 After recent wildfire events, volatile organic compound (VOC) contamination in U.S. drinking water systems has prompted questions about the source of these contaminants.1,4 One of these VOCs included benzene, a carcinogen, which was found at 40
000 μg L−1 and greater than 2217 μg L−1 concentrations in the water distribution systems following the Tubbs Fire (2017) and Camp Fire (2018), respectively.1,5,6 Both wildfires occurred in California, and contamination levels greatly exceeded the federal and California state long-term drinking water exposure limits by a factor of 200 to 40
000, and even short-term exposure limits of 26 μg L−1 (California) and 200 μg L−1 (USEPA).7–9 The Camp Fire sample was collected two months after the fire was contained. After six months, another Camp Fire water sample contained 530 μg L−1 benzene.1 Water infrastructure is critical to public health, and contamination can hinder recovery.10,11 More than one year was needed to remove chemical contamination from water systems impacted by the Tubbs Fire and the Camp Fire.
After wildfires, a variety of other VOCs have also been found in drinking water including, but not limited to, dichloromethane, naphthalene, styrene, tert-butyl alcohol, toluene, and vinyl chloride. Semi-volatile organic compounds (SVOC) are considered a contamination risk as well. SVOCs were detected in the distribution system following the Tubbs Fire, and in the ash following the Camp Fire, but drinking water testing for these contaminants was limited.1,12 It is hypothesized that the water contamination could be caused by (a) the degradation of plastic materials present in the water systems, (b) back siphoning of contaminated water from damaged building plumbing, and/or (c) contaminated air and/or ash sucked into the distribution system as it depressurized.1 During the recent 2020 CZU Lightning Complex Fire, water distribution infrastructure and building damage prompted system depressurization. VOC contamination of multiple water systems was found.4,13 Because private well owner systems can contain plastics, they were advised to test for VOCs and SVOCs after both the Camp Fire and CZU Lightning Complex Fire.14,15 California and Oregon state agencies recommend that wildfire impacted public water distribution systems test for VOCs and not SVOCs, and customers test their building plumbing for VOCs only.16–18 The dissimilar approach to water and infrastructure testing for the same problem underscores a need to investigate the potential contamination sources.
Plastic pipes are increasingly being used for water distribution system and building plumbing because of their flexibility and low cost. In particular, polyvinyl chloride (PVC) and high density polyethylene (HDPE) water distribution pipes are commonly used.19 The water mains affected by the Tubbs Fire were roughly 85% PVC, and one water system affected by the Camp Fire contained 35% PVC water mains.20 Service lines that convey water from the water main to the water meter and into the building are also commonly made from plastic material. There were approximately 10
480 service lines in the Paradise Irrigation District (Paradise, CA), and they can be made from crosslinked polyethylene (PEX), PVC, chlorinated polyvinyl chloride (CPVC), and HDPE.20–24 Once drinking water enters the building, it can travel through additional plastic pipes that convey cold and/or hot water in pipes made of PEX, PVC, HDPE, and polypropylene (PP).21,22,24,25 Building water piping constitutes 5 to 10 times the length of piping as compared to the length of piping in buried water distribution systems.26 Private drinking water wells can also consist of PVC and HDPE well pipes and service lines.
It is well established that VOCs can be released into the air from burned structures, and have been found in water used to extinguish structure fires as well.27,28 Temperatures caused by wildfire and structure fires can thermally damage plastic pipes (Fig. 1), and as a result may provide a reasonable source for the observed water contamination. The ground temperatures of wildfires and structure fires can range from 200 °C to 800 °C depending on a multitude of variables, including the fuel source and atmospheric conditions.29–31 The temperatures that plastic components will be exposed to will vary substantially depending on the surface temperature, the depth it is buried and its location within the walls of a structure. Such factors indicate that both buried pipes and building plumbing may be subject to a variety of temperatures potentially causing differing levels of thermal degradation throughout the system.
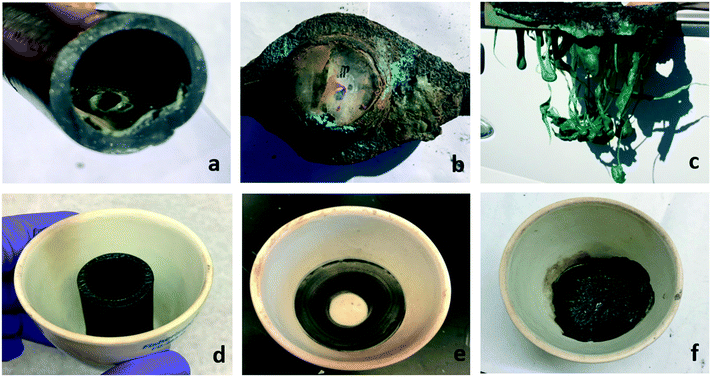 |
| Fig. 1 Images of fire-damaged water system components including (a) a HDPE plastic pipe, (b) a water meter, and (c) a water meter cover following the Camp Fire. Thermally degraded pipe samples in laboratory experiments include the (d) PEX-c pipe degraded at 300 °C, (e) HDPE pipe degraded at 300 °C, and (f) HDPE pipe degraded at 400 °C. | |
Plastic thermal degradation is a known source of VOC contamination in the air, but its potential to cause contamination in the drinking water has not been studied extensively. Specific contaminants found in the air due to HDPE, PP, PVC, and CPVC thermal degradation include a combination of benzene, toluene, ethylbenzene, and xylenes (otherwise known as BTEX) chlorobenzene, and naphthalene, among others (Table S1 of the ESI†). Many of these compounds were similarly present in the drinking water following the Tubbs and Camp Fires (Table S1†).32–36 A recent PVC sewer pipe thermal degradation study, in which the PVC was ignited using a torch and subsequently exposed to air or submerged in water for 7 days, indicated that the majority of compounds that leached into the water were alkanes and alkenes, followed by various aromatic compounds.33 Vinyl chloride and chlorobenzene, two contaminants discovered in the drinking water following both fires, were detected in water exposed to the damaged PVC but notably benzene was only detected in the air emissions.33 The lack of benzene found in the water exposed to damaged PVC sewer pipe underscores the need for additional information to identify the chemicals produced during plastic drinking water pipe thermal degradation. Further, there is a need to determine the degree to which a variety of degraded plastic pipes used to convey drinking water may be a source of contamination.
The goal of this study was to determine the potential contribution of thermally damaged plastic pipes to drinking water contamination after heat exposure. Here, various plastic drinking water pipes were exposed to a range of elevated temperatures (200 °C to 400 °C) and submerged in water or an organic solvent to observe organic chemical release. Relationships were also explored to link contaminant leaching across different pipe types and exposure temperatures.
2. Materials and methods
2.1 Standards and reagents
A mixed standard of benzene, toluene, ethylbenzene, o-xylene, m-xylene, and p-xylene (200 mg L−1 in methanol (MeOH)), was purchased from Restek Corporation. n-Hexane and MeOH were purchased from Fischer Scientific. Reagent grade water (18.2 MΩ cm) was produced from a Thermo Scientific Barnstead™ Nanopure™ water purification system.
2.2 Plastic pipes and characterization of thermal properties
A total of 11 different plastic pipe materials across eight brands was examined in this study (Table S2†). These included three PEX-a and two PEX-c pipe materials along with one of each PEX-c-EVOH (ethylene vinyl alcohol), PEX-b, HDPE, PP, PVC, and CPVC pipe materials (Table S2†). All of the pipes had a 1.9 cm [0.75 in] nominal diameter and were labelled as complying with the ASTM International and NSF International/American National Standards Institute standards for potable water use.21–25,37,38 The PEX-c-EVOH was a multi-barrier material and only approved for usage in building water systems, whereas the other PEX materials may be used as buried service lines or in building systems.21,37 HDPE, PVC, and CPVC materials are often used for buried water mains, buried service lines, and in building plumbing.22,23,37 The PP pipe is only used in indoor building plumbing.25,37 The PP pipe was obtained from a manufacturer in 2015, whereas the rest of the pipes were purchased in various retail stores in the Lafayette, IN area in either July 2019 or September 2016 (Table S2†).
Thermal transitions of all of the pipe materials as well as the residue generated under similar heating conditions were evaluated using a TA Instruments Q100 Thermogravimetric Analyzer (TGA). The initial sample weight that was tested was 13 to 18 mg. The furnace temperature was equilibrated at 40 °C, and temperature was then ramped at 10 °C min−1 to 1000 °C. A nitrogen gas flowrate of 60 mL min−1 was applied.
2.3 Experimental procedure
To thermally age the plastics, 5 g per sample, which corresponds to 5.0 to 8.4 cm [1.9 to 3.2 in] length pipe depending on the material, was heated in a porcelain crucible for 30 min at 200, 300, or 400 °C in a muffle furnace. These temperature regimes were chosen so that a range of degradation conditions could be evaluated, much like what would be expected with water distribution system infrastructure at various distances from the fire front. After sample heating, samples were cooled for 30 min in a desiccator. Each porcelain crucible was pre-conditioned before use by heating it to 110 °C for 30 min and cooling it for 15 min. Mass loss was determined by recording the mass of the crucible and the plastic pipe before thermal degradation and after cooling.
Once cooled, each pipe sample was then drilled into spirals using a 0.48 cm [3/16 in] drill bit. This step was conducted to help equalize the surface area amongst the different materials, as the surface area of the degraded plastics varied substantially. Additionally, the spirals helped maximize the extractable surface area allowing compound desorption to occur quickly. The spirals were then placed in 40 mL amber headspace free vials with 37 mL of reagent grade water or n-hexane for 7 d at ambient temperature (25 °C). Approximately 60 min to 90 min passed between the burned samples being removed from the furnace to the beginning of the extraction. After 7 d, 5 mL of the aqueous samples were placed in 10 mL crimp cap. As a control, unburned materials were also drilled and extracted using the same method.
In the end, all 11 pipe samples were thermally degraded at 400 °C and extracted in water or n-hexane as a screening step to identify the type and magnitude of compounds present. Based on these results, five materials (HDPE, PEXc-2, PP, PVC, and CPVC) were further thermally degraded at 200 °C and 300 °C and extracted in water. All experiments in this study were performed in triplicate.
2.4 Analytical methods
Aqueous and n-hexane extracts were analyzed using gas chromatography-mass spectrometry (GC/MS) (Shimadzu GC-2010 Plus GC coupled to a Shimadzu TQ8030 triple quadrupole MS) with headspace and direct injection methods, respectively. GC separation was carried out using an Agilent HP-5 column (30 m × 0.32 mm × 0.25 μm) where helium was used as a carrier gas and set at a flow rate of 1.2 mL min−1. The National Institute of Standards and Technology (NIST) database of mass spectra was used in tentatively identifying chemical compounds, and only those that matched over 70% were reported.33,39 TICs were reported because the USEPA considers TIC analysis to be “a useful tool that can aid in clean-up or treatment decisions by identifying compounds that might otherwise by missed at the site”.40 Chemical identification and quantification of BTEX was conducted using a mixed standard, while chlorobenzene-d5 was used as the internal standard.
The GC/MS headspace method involved incubating the aqueous samples at 50 °C and agitating them for 10 min. After this, a 500 μL headspace sample was injected using a 10
:
1 split mode. The injection temperature was held at 280 °C. The oven program was held at 40 °C for 4 min before increasing to 121 °C at 12 °C min−1, where it was held for another 4 min. The mass spectrometer was operated in the scan mode over a m/z range of 50 to 300 with the interface temperature set at 250 °C, and the ion source held at 200 °C. Selective ion monitoring (SIM) mode was used with m/z of 78, 91, 106, and 106 for quantification of benzene, toluene, ethylbenzene, and xylene, respectively. The method detection limits (MDLs) for benzene, toluene, ethylbenzene, and xylene were 0.57, 0.51, 0.55, and 0.89 μg L−1 respectively. Two of the three isomers of xylene eluted at the same time, and as a result, the two signals were combined, and the three isomers were treated as one compound.
The n-hexane extractions were analyzed using a direct injection method by injecting a 1 μL sample using a 10
:
1 split. The injection temperature was set at 280 °C. The oven program was held at 40 °C for 4 min, then was increased to 280 °C at 12 °C min−1, where it was held for 4 min. The mass spectrometer was operated in scan mode over the m/z range of 50 to 400. The interface temperature was set at 250 °C, and the ion source was set at 200 °C. Because benzene eluted in the solvent front, no quantification of BTEX was performed with the direct injection samples.
3. Results and discussion
3.1 Thermogravimetric characterization of plastic pipes
Results obtained from the TGA helped provide a better understanding of pipe composition, so their performance in the leaching experiments could be better interpreted. Vinyl materials (PVC and CPVC) were more susceptible to thermal degradation compared to the other materials examined (see Table 1 for key data values and Fig. S1† for thermograms). The first major mass loss was detected for PVC and CPVC materials at 300 °C and 316 °C, respectively, whereas PP and PE (HDPE and PEX) materials did not undergo significant degradation until 463 °C (PP) and >478 °C, respectively (Table 1). For PVC and CPVC, this first stage of mass loss is associated with dehydrochlorination, and about 40% of the original sample mass remained at 400 °C. PVC and CPVC materials also underwent a second significant mass loss around 475 °C and 483 °C, respectively (Table 1).41 Dehydrochlorination forms polyene chains, in which the double bonds are susceptible to chain scission, and this can lead to a second stage of substantial mass loss.42 Alternatively, HDPE and PEX generally undergo random polymer chain scission, which produce radicals which may propagate additional chain scissions, form double bonds, and drive hydrogen atom abstraction.43
Table 1 Thermal performance during material heating from 50 °C to 1000 °C
Material |
Thermal threshold |
Weight loss at specified temperaturec (wt%) |
Temperature (°C) |
T
onset (°C) |
T
deg (°C) |
Residue at 1000 °C (wt%) |
200 |
250 |
300 |
350 |
400 |
450 |
500 |
600 |
5 wt% |
50 wt% |
95 wt% |
1a and 1b denotes the same brand, but different pipes.
Values of residue and weight loss at 600 °C may be above 100% as the instrument has ±0.05 mg quantification limit.
wt% represents the percent of mass loss at a given temperature.
|
Cold water rated pipes |
PVC |
283, 426 |
300, 475 |
11 |
0.37 |
1.6 |
42 |
56 |
58 |
60 |
80 |
81 |
275 |
325 |
— |
HDPE |
439 |
483 |
4.8 |
0.13 |
0.24 |
0.38 |
0.65 |
1.3 |
17 |
95 |
95 |
435 |
462 |
482 |
Hot water rated pipes |
CPVC |
279, 425 |
316, 483 |
26 |
0.57 |
2.3 |
32 |
59 |
61 |
64 |
67. |
69 |
268 |
315 |
— |
PEX-a-1aa |
437 |
485 |
0.59b |
0.02 |
0.09 |
0.23 |
0.49 |
1.6 |
23 |
100 |
100 |
424 |
463 |
477 |
PEX-a-1ba |
427 |
478 |
0.9 |
0.0 |
0.03 |
0.16 |
0.65 |
3.1 |
40 |
99 |
99 |
409 |
455 |
473 |
PEX-a-2 |
433 |
483 |
1.9 |
0.17 |
0.41 |
0.73 |
1.3 |
3.5 |
29 |
98 |
98 |
410 |
460 |
478 |
PEX-b |
427 |
480 |
0.0 |
0.02 |
0.12 |
0.36 |
1.7 |
6.1 |
39 |
100 |
100 |
393 |
456 |
475 |
PEX-c-1aa |
430 |
480 |
2.0 |
0.19 |
0.32 |
0.52 |
1.1 |
3.2 |
34 |
98 |
98 |
412 |
457 |
476 |
PEX-c-1ba |
437 |
483 |
0.6b |
0.10 |
0.24 |
0.42 |
0.77 |
1.4 |
23 |
100 |
100 |
430 |
462 |
477 |
PEX-c-1-EVOH |
433 |
485 |
0.0 |
0.18 |
0.28 |
0.59 |
1.4 |
4.4 |
30 |
100 |
100 |
404 |
461 |
478 |
PP |
416 |
463 |
2.0 |
0.20 |
0.31 |
0.56 |
0.90 |
3.4 |
78 |
98 |
98 |
408 |
441 |
459 |
During heating, plastic additives such as antioxidants and stabilizers likely affected the thermal response, and some of these compounds were found in the new plastics. Di-tert-butylphenol, a degradation product of the antioxidant Irgafos 168®, was a tentatively identified compound (TIC) in all unburned materials except for HDPE and the vinyl plastics (Table S3†).44,45 In the unburned HDPE, di-tert butyl-hydroxybenzaldehyde, a degradation product of Irganox 1035®, was detected.45 Previous studies on hindered phenolic antioxidants, such as Irganox 1010® and 1035®, have shown that these compounds increase the thermal oxidative resistance in PE and PP by intercepting free radicals to prevent the formation of double bonds that are vulnerable to scission.46,47 Various heat stabilizers, such as organotins, are used for PVC and CPVC pipe production but were not targeted for analysis in the present study.48
PEX and PP pipes contained little residue at 1000 °C whereas a moderate amount of residue (4.8 wt%) was found for HDPE. It is known that HDPE pipe contains >2 wt% carbon black.24 Residue remaining at 1000 °C for other materials may be associated with fillers and inorganic materials. Because nearly all pipe thermal degradation temperatures were above 400 °C and the authors desired to have some physical materials available to extract with solvents after degradation, temperatures for damaging plastics in subsequent experiments were targeted at and below 400 °C.
3.2 Aqueous phase BTEX leaching from plastic pipes at 400 °C
Results showed that plastic pipe thermal exposure can generate BTEX, which can then leach from cooled plastics into water. BTEX was not found from new and non-thermally degraded plastics in water, while 10 of 11 thermally degraded plastic pipes leached at least one BTEX component (Fig. 2). The chemical leaching differences between products is likely attributed to differences between plastic characteristics and experimental conditions. PE materials lost less mass due to isothermal heating (5 wt% to 10 wt%) compared to the PVC and CPVC samples (61 wt% and 64 wt%, respectively) (Fig. 2). A detectable, but significantly lower amount of benzene and toluene was observed for the PVC pipe, and no BTEX was found for the CPVC pipe (Fig. 2). Additionally, there was a general trend of compound concentration leaching across the plastics where benzene > toluene > ethylbenzene ≈ xylene (Fig. 2). This trend could be attributed to several factors including compound production, water solubility, air volatilization, polymer solubility parameters, and/or partitioning into the aqueous phase. Octanol–water coefficients and solubility values mirror the trend of concentrations observed (Table S4†), indicating that benzene would most readily partition into the aqueous phase.
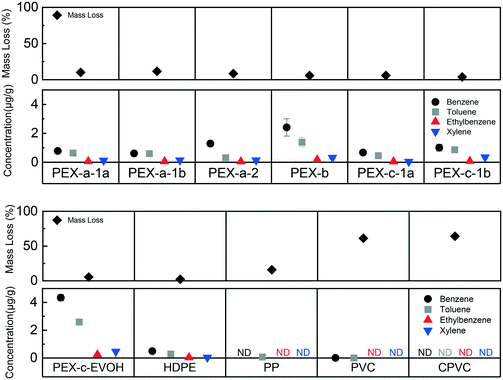 |
| Fig. 2 Average amount of benzene, toluene, ethylbenzene, and xylene leaching observed after burning each material at 400 °C and extracting in water for 7 days. The error bars reflect the standard deviation of the measurements (n = 3). If no error bars are visible, this indicates the error bars are smaller than the symbol size. ND indicates the compound was not detected above the MDL. | |
The discovery that BTEX was generated by thermally degraded plastic pipes is supported by prior literature focused on air testing. Benzene and toluene tend to be formed during the first stage of decomposition for vinyl material thermal degradation.49 Alkylated aromatics, such as ethylbenzene and xylene can be formed during a second degradation step due to chain scission and aromatization.49 VOC release from HDPE into air during pyrolysis (lack of oxygen) or combustion (presence of oxygen) occurs due a similar scission and aromatization mechanism, and previous studies have observed all four BTEX compounds.50,51 The results of this study suggest that BTEX may have been formed in the intact, but thermally degraded, plastics and subsequently leached into the water. The inverse relationship between BTEX in the aqueous phase and mass loss (Fig. 2) indicates that as structurally integrity becomes compromised, as was the case for the vinyl materials (Fig. S2–S5†), the volatile compounds tend to partition into air. To the best of the authors' knowledge, there have been no prior PEX thermal degradation studies that have found BTEX compounds in the air. Primary degradation products of PEX have been reported to include linear hydrocarbons and cyclical siloxane compounds, although PEX pipe is created by crosslinking HDPE and medium density polyethylene resins.52
Little to no BTEX was found for the PP pipe, which has a similar structure to HDPE. The onset degradation temperature of the PP pipe (416 °C) was lower than that of the HDPE and PEX materials (Table 1), and unsurprisingly, the PP had more mass loss (∼15 wt%) (Fig. 2) at the same temperature. In previous PP studies, benzene has been found in the air after pyrolysis between 300 °C to 600 °C.53,54 No prior studies were found that examined BTEX release into water from thermally damaged PP materials.
3.3 Influence of isothermal heating temperature
Different concentrations of BTEX were found in water after changing the isothermal heating temperature, such that two patterns emerged (Fig. 3). For the HDPE and PEX pipes, the amount of BTEX that leached into the water increased as the plastic degradation temperature increased from 200 °C to 400 °C (Fig. 3). Conversely, the greatest benzene concentration was found for the PVC pipe when exposed to 300 °C, with relatively less concentrations at 200 °C and 400 °C (Fig. 3). The CPVC pipe showed a similar pattern for benzene as the PVC pipe, however, at much lower concentrations (Fig. 3). This spike phenomenon for vinyl materials can potentially be explained by the lower amount of mass loss, where not all benzene produced during degradation volatilized out of the solid. The 300 °C exposure temperature was greater than the onset degradation temperature (Table 1) where dehydrochlorination would occur. However, the PVC pipe mass loss was only 23 wt% as opposed to 61 wt% at the 400 °C condition resulting in a more structurally intact plastic after degradation (Fig. S2†).
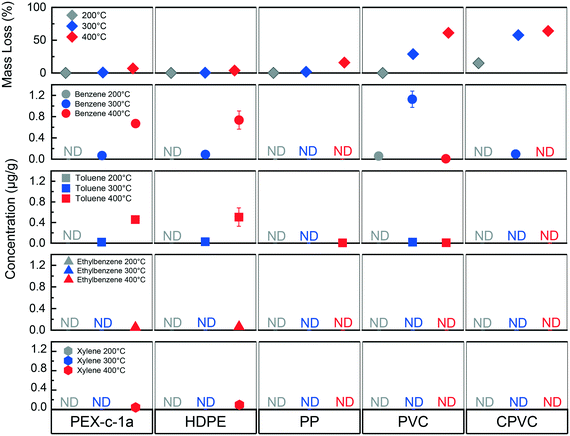 |
| Fig. 3 Mean BTEX concentration after extracting each burned material at 200 °C, 300 °C, and 400 °C in water. The error bars reflect the standard deviation of the measurements (n = 3). If no error bars are visible, it indicates they were smaller than the symbol size. ND indicates the compound was not detected. | |
Despite structural similarities for the vinyl pipes, benzene was only detected in water exposed to the CPVC pipe at a fraction of the amount it was found in water exposed to the PVC material (Fig. 3). This difference may be explained by the additional chlorine atoms present on the CPVC polymer chains resulting in a greater number of chlorine substituted aromatic products when CPVC was thermally degraded.34 A previous CPVC pyrolysis study found significantly more chlorobenzene in the air than benzene.34 Chlorobenzene was not a target of the authors' analytical method. Additionally, the chlorobenzene octanol–water coefficient is higher, and the solubility is lower than that of benzene, indicating that chlorobenzene would be less likely to partition into the water (Table S4†). Chlorobenzene was detected at concentrations as high as 50 μg L−1 in Santa Rosa and 5 μg L−1 in Paradise, both below the federal and California drinking water maximum contaminant levels of 100 μg L−1 and 70 μg L−1, respectively.1,7
Compared to vinyl pipes, greater BTEX concentrations were found as the degradation temperature increased for the HDPE and PEX materials (Fig. 3). The onset degradation temperature for both of these materials exceeds 430 °C (Table 1) which can explain why little to no BTEX leaching was observed at 200 °C and 300 °C. The increase in leaching between 300 °C and 400 °C can be attributed to the plastic pipes beginning to degrade and generating BTEX and other compounds. Elevated temperatures lead to the polymer chain undergoing chain scission resulting in the formation of alkenes.32 As the pipe is exposed to greater temperatures, the amount of polymer chain scission that occurs also increases. The increase in scission results in more alkene fragments that may subsequently undergo aromatization. A similar pattern was observed in a study of HDPE combustion by others, in which the benzene concentration in the air increased as the combustion temperatures increased from 500 °C to 800 °C.51 However, the increase in potential BTEX formation does not necessarily indicate that this trend of increased leaching as a function of temperature will continue.32 Both the partitioning of BTEX into the air and mass loss are also increasing with system temperature, indicating that there may be an optimal degradation temperature for observing the maximum BTEX formation much like what was observed with the PVC at 300 °C.
3.4 Leaching of non-BTEX compounds
Leaching promoted by water extraction.
Both the number and intensity of the peaks observed in the water extraction chromatograms changed with the heating temperature (Fig. S6–S16†). For the PE materials, as the exposure temperature increased, an increased number leached compounds were detected with greater magnitudes (Fig. S6–S13†). Conversely, the PVC pipe showed the greatest magnitude of leaching at 300 °C (Fig. S15†). Similar to what was observed with BTEX leaching, the maximum number of TICs observed in the water was highest for the PE materials, with 14 to 22 TICs being detected after degradation at 400 °C for each of the materials (Table 2 and Fig. S6–S13†). These TICs are hypothesized to be a mixture of saturated ketones and aromatic compounds (Table S3†). Of these TICs, propyl benzene and styrene were the only compounds (other than BTEX) that were detected in the water systems in both Santa Rosa and Paradise.1,6 Propyl benzene, observed in PEX-a2, PEX-b, PEX-c-1a, PEX-c-1b, and HDPE, (Table S6†) while not currently regulated, is a central nervous system depressant and has a 1-day health advisory concentration of 11 mg L−1.7,55 Styrene which was observed leaching from PVC (Table S6†), was found at a concentration of 460 μg L−1 and 6800 μg L−1 in Santa Rosa and Paradise respectively, both well above the 100 μg L−1 federal/California long-term exposure limit, and below 1 day USEPA health advisory concentration of 20 mg L−1.1,6,7,9 Both of these compounds could be contaminants of concern following future fire events.
Table 2 Comparison of BTEX (benzene, toluene, ethylbenzene, xylene) and TICs (tentatively identified compound) detection for the thermally damaged pipes across all temperatures tested. “✓” and “–” indicate the compound was observed or not, respectively
Material |
Confirmation of BTEX |
Number of TICs in extracta |
Components in Water |
B |
T |
E |
X |
Water |
n-Hexane |
TICs reported have NIST spectral database match indices of greater than 70%.33
|
Cold water pipes |
PVC |
✓ |
✓ |
– |
– |
4 |
41 |
HDPE |
✓ |
✓ |
✓ |
✓ |
14 |
100 |
Hot and cold water pipes |
CPVC |
✓ |
– |
– |
– |
3 |
32 |
PEX-a1-a |
✓ |
✓ |
✓ |
✓ |
19 |
123 |
PEX-a1-b |
✓ |
✓ |
✓ |
✓ |
16 |
122 |
PEX-a2 |
✓ |
✓ |
✓ |
✓ |
22 |
117 |
PEX-b |
✓ |
✓ |
✓ |
✓ |
18 |
127 |
PEX-c1-a |
✓ |
✓ |
✓ |
✓ |
19 |
133 |
PEX-c1-b |
✓ |
✓ |
✓ |
✓ |
17 |
134 |
PEX-c1-EVOH |
✓ |
✓ |
✓ |
✓ |
20 |
109 |
PP |
– |
✓ |
– |
– |
6 |
95 |
Leaching promoted by hexane extraction.
As expected, a greater number of peaks were observed in the n-hexane extracts (32 to 134) compared to the water extracts (3 to 22) for all plastics (see example for PEX-c-1a in Fig. 4 and all other pipe types in Fig. S17–S26†). For the degraded PEX, HDPE, and PP pipes, between 100 to 134 unique compounds were leached into n-hexane, whereas for the degraded PVC and CPVC pipes between 30 to 41 compounds were leached (Fig. 4 and S17–S26†). While most compounds extracted from the new pipes were either straight chain or branched alkanes of varying lengths (Table S3†), thermal exposure led alkenes to represent the majority of compounds detected in the leachate (Table S5†). These aliphatic hydrocarbons are products of alkane hydrocarbon chain scission and are not typical drinking water contaminants. They have low aqueous solubility, which is why they were only detected in the hexane extracts and are generally less toxic than their cyclical or aromatic counterparts.56,57
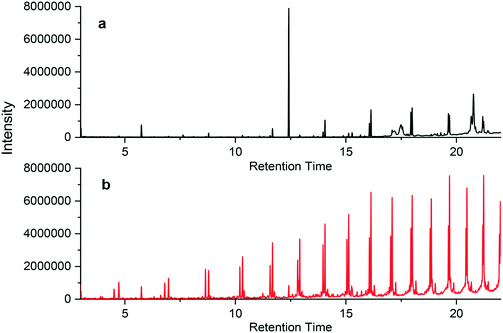 |
| Fig. 4 Chromatographs of PEX-c-1a when (a) unburned and (b) burned at 400 °C, where samples were extracted in n-hexane. The internal standard is the peak at 5.8 minutes. | |
Generally, both the magnitude of the peak and the number of compounds increased after burning the materials. However, one notable exception occurred for the PEX-c pipes; one peak (retention time of 12.5 min) for the unburned pipe was significantly larger than that of any of the burned peaks (Fig. 4 and S21†). This peak likely represented the compound, di-tert-butylbenzene, which has been shown to be an ultraviolet light or radiolysis degradation product of the antioxidant Irgafos 168®.58,59 This compound was only observed in the leachate of the PEX-c materials, in which the crosslinking occurs using beta irradiation. This may explain why the magnitude of this degradation product was so large.60 This peak decreased substantially in the burned plastic extract (Fig. 4 and S21†), indicating it may have been thermally decomposed.
4. Limitations and implications
There are several limitations of this work, but results indicate that exposing commercially available plastic drinking water pipes to heat can generate detectable BTEX that remains in the cooled product, and ultimately leaches into water (Fig. 3 and Table 2). Aqueous leaching results from this study indicated that if stagnant water was present in the degraded pipes, the estimated benzene concentrations would exceed 1100 μg L−1. These values were calculated assuming that all the benzene observed in the aqueous experiments leached into the volume of water that would fill the 5 g section of pipe that was thermally degraded. While this concentration is above short- and long-term federal and California drinking water exposure limits, it is below the maximum values observed following both the Tubbs and Camp Fires. This difference could be attributed to VOC loss into the air during thermal exposure and after heating but before leaching, meaning that the results presented here may underestimate BTEX leaching under more realistic conditions. Vapor pressure values (Table S4†) and literature-based evidence indicates that partitioning into the air occurred.32–35,50,51,53,54 Additionally, plastic components in a wildfire impacted distribution system may be exposed to a wide range of degradation regimes. For example, a controlled burn in northern California found that ground temperatures remained above 100 °C for up to 12 hours after the fire was contained. This extended exposure could influence the amount of BTEX that is generated in the plastics.30
Plastic pipes examined in this study were new, contained additives designed to help limit oxidation, and were not filled with water. In-service plastics may or may not be more susceptible to BTEX (and other TIC) formation. In-service pipes will have undergone some degradation, antioxidant loss, and can be coated with scales.61,62 It is known some trace metals, such as copper, may accelerate plastic degradation.62–64 Water exposure can also extract antioxidants and water itself can permeate PE materials at elevated temperature.65,66 Another complicating factor is that plastic formulation may have influenced the results. For example, it was reported organotin stabilizers in PVC can substantially decrease the amount of benzene and alkylated aromatics detected in air.67 As such, the specific additives used in the various pipes being examined may significantly affect the type and magnitude of contaminants released and those that remain in the damaged plastic. These phenomena, as well as the role of temperature, should be considered in future work.
Study results indicate that exposing plastic pipes to heat may pose subsequent water pipe safety concerns. No standards, testing recommendations or bank of data were found associated with water testing of damaged plastic water pipes in buildings after structure fires or wildfires. It is known that heat can radiate into and affect meter boxes, service lines, and building plumbing. Volatilization of plastic thermal degradation products can occur.32–34,36,50,68,69 VOCs/SVOCs have been produced from the burning of structures and biomass as well.27,70 The source and relative contribution of these contaminants to water contamination should be further examined including their fate the drinking water distribution systems and plumbing.
Plastics are increasingly being used for water infrastructure applications, and evidence shows they can be a source of wildfire-caused water contamination. As of October 2020, there had been more than 47
000 U.S. wildfires across 36 states.71 In 2019 there were nearly 500
000 structure fires in the U.S.72 Studies that examine the downstream fate of contaminants released by thermally damaged plastic to unaffected plastic infrastructure should be conducted. It is known plastics can sorb contaminants like BTEX and leach them out over time.60,61,73,74 Post-fire, chemical water testing should be conducted where drinking water infrastructure that contains plastic pipes, fittings, valves, gaskets, liners, and other components have been or may have been exposed to heat. Visual inspection of plastics would not determine whether or not the plastic will contaminate the drinking water it conveys. Additional work is needed to better understand this issue in light of the hundreds of thousands of fires occurring annually in the U.S., as it has been confirmed that water distribution networks and building plumbing infrastructure can be contaminated.
Conclusion
This work identified that plastic pipe thermal degradation can be a source of VOC and SVOC drinking water contamination, much like what was observed in the water distribution systems after the Tubbs Fire, Camp Fire, and CZU Lightning Complex Fire. Further, the implications of plastic pipe caused drinking water contamination extends beyond fire-prone regions to any structure fire where plastic pipes may have experienced elevated temperatures. In the present study, BTEX compounds were produced during thermal degradation and along with a variety of other organic compounds. Contaminants produced varied by brand of plastic pipe, type of plastic, and exposure temperature. The loss of VOCs emitted into air (which were not quantified here) and a variety of plastic additives likely influenced the results. Alternative antioxidants, stabilizers, and other plastic additives may influence the contaminants that were observed, and at what temperature they are formed. Additional work is needed to examine how various environmental, chemical, and plastic characteristics influence the formation of VOCs, SVOCs, and their subsequent leaching, rendering drinking water unsafe. VOCs are generated when plastic pipes are thermally damaged, and these contaminants can then leach from damaged plastics into drinking water prompting exceedances of health-based drinking water limits.
Conflicts of interest
There are no conflicts to declare.
Acknowledgements
Funding for this work was partially supported by the U.S. Environmental Protection Agency grant R836890, Lillian Gilbreth Fellowship Program at Purdue University, and the Purdue University Doctoral Fellowship program. The authors appreciate information provided by the Paradise Irrigation District (Kevin Phillips, Jim Ladrini, Bill Taylor, Mickey Rich, Laura Campra), Del Oro Water Company (John F. O'Farrell, Jim Roberts), City of Santa Rosa (Emma Walton, Joe Schiavone, Mark Shipman), and Water Works Engineers, LLC (Sami Kader, Michael Lindquist), among other organizations.
References
- C. R. Proctor, J. Lee, D. Yu, A. D. Shah and A. J. Whelton, Wildfire Caused Wide-Spread Drinking Water Distribution Network Contamination, AWWA Water Sci., 2020, 1–14, DOI:10.1002/aws2.1183.
-
National Academies of Sciences Engineering and Medicine, Implications of the California Wildfires for Health, Communities, and Preparedness, 2020, DOI:10.17226/25622.
- City of Detroit, Fire Recovery and Restoration of Drinking Water Temporary Facilities Timeline, Detroit, Oregon, 2020, available from: http://detroitoregon.us/wordpress_c/wp-content/uploads/2020/11/Water-Graphic.png Search PubMed.
- San Lorenzo Valley Water District, Benzene Detection at Creek Drive in Riverside Grove, Boulder Creek, California, 2020, available from: https://www.slvwd.com/sites/g/files/vyhlif1176/f/uploads/benzene_detection_at_creek_dr_swrcb_approved_9.9.2020.pdf Search PubMed.
-
International Agency for Research on Cancer, List of Classifications by Cancer Sites with Sufficient or Limited Evidence in Humans, Lyons, France, 2020, vol. 1–113, available from: https://monographs.iarc.fr/agents-classified-by-the-iarc/ Search PubMed.
-
Paradise Irrigation District, 2019 Paradise Annual Consumer Confidence Report, Paradise, California, 2019, available from: https://pidwater.com/docs/about-your-water/water-quality/1750-2019-consumer-confidence-report/file Search PubMed.
-
U.S. Environmental Protection Agency, 2018 Edition of the Drinking Water Standards and Health Advisories Tables, 2018 Search PubMed.
-
Office of Environmental Health Hazard Assessment California Environmental Protection; Pesticide, Estimated Risks from Short-Term Exposures to Benzene in Drinking Water, April 2019, 2019, available from: https://oehha.ca.gov/media/downloads/crnr/appendixd1final.pdf Search PubMed.
-
California Water Boards, Maximum Contaminant Levels And Regulatory Dates for Drinking Water: U.S. EPA vs California, 2018, pp. 6–9, available from: https://www.waterboards.ca.gov/drinking_water/certlic/drinkingwater/documents/ccr/mcls_epa_vs_dwp.pdf Search PubMed.
- L. A. Spearing and K. M. Faust, Cascading System Impacts of the 2018 Camp Fire in California: The Interdependent Provision of Infrastructure Services to Displaced Populations, Int. J. Disaster Risk Reduct., 2020, 50, 101822, DOI:10.1016/j.ijdrr.2020.101822.
-
T. Feo, S. Evans, A. Mace, S. Brady and B. Lindsey, The Costs of Wildfire in California: An Independent Review of Scientific and Technical Information; Sacramento, 2020, available from: https://ccst.us/wp-content/uploads/The-Costs-of-Wildfire-in-California-FULL-REPORT.pdf Search PubMed.
-
Tetra Tech Incorporated, Final Asessment of Ash Sampling-Camp Fire Incident, 2019 Search PubMed.
-
J. Katham, Parts of Boulder Creek without Water Due to Wildfire Damage, Santa Cruz Local. Santa Cruz, August 26, 2020, available from: https://santacruzlocal.org/2020/08/26/parts-of-boulder-creek-without-water-due-to-wildfire-damage/ Search PubMed.
-
Butte County, Butte Country Private Well Information: Post-Fire Well Safety and Testing Guideline, Oroville, Califronia, 2019, available from: https://buttecountyrecovers.org/documents/pws-051419/ Search PubMed.
-
County of Santa Cruz, Water Wells and Springs, Santa Cruz, California, 2020, available from: https://www.santacruzcounty.us/Portals/6/Env_Health/CZU_Fire/WaterWellFireReturn.pdf Search PubMed.
-
Oregeon Health Authority, Post-Wildfire VOC Sampling Guidance for Public Water Systems, 2020, available from: https://www.oregon.gov/oha/PH/HEALTHYENVIRONMENTS/DRINKINGWATER/PREPAREDNESS/Documents/post-wildfire-VOC-sampling-guidance.pdf Search PubMed.
-
State Water Resources Control Board, Information to Water Customers Regarding Water Quality in Buildings Located in Areas Damaged by Wildfire, August 9, 2019, 2019, available from: https://www.waterboards.ca.gov/drinking_water/programs/documents/benzenecustomeradvisoryfinal.pdf Search PubMed.
-
Oregon Health Authority, Customer Guidance Regarding Water Quality in Buildings Located in Areas Damaged by Wildfire, 2020, available from: https://www.oregon.gov/oha/PH/HEALTHYENVIRONMENTS/DRINKINGWATER/PREPAREDNESS/Documents/customer-guidance-wildfire.pdf Search PubMed.
-
S. Folkman, Water Main Break Rates In the USA and Canada: A Comprehensive Study Overall Pipe Breaks Up 27% In Six Years, 2018 Search PubMed.
-
A. J. Whelton, C. Proctor, J. Lee and A. D. Shah, VOC Fate in Water Systems Discussion to Support the Water Plumbing, 2019, available from: https://engineering.purdue.edu/PlumbingSafety/resources/Camp-Fire-VOC-in-Water-Systems-Purdue.pdf Search PubMed.
-
ASTM International, Standard Specification for Crosslinked Polyethylene (PEX) Tubing 1, 2020, DOI:10.1520/F0876-09.2.
-
ASTM, Standard Specification for Poly (Vinyl Chloride) (PVC) Plastic Pipe Fittings, Schedule, 2010, No. C, 2–7, DOI:10.1520/D2466-06.1.
-
ASTM International, ASM F439–11 Standard Specification for Chlorinated Poly (Vinyl Chloride) (CPVC) Plastic Hot- and Cold-Water Distribution Systmes, 2019, DOI:10.1520/D2846.
-
ASTM International, Standard Specification for Polyethylene (PE) Plastic Pipe (SIDR-PR) Based on Controlled Inside Diameter 1, 2012, DOI:10.1520/D2239-12A.2.
-
ASTM International, Standard Specification for Pressure-Rated Polypropylene (PP) Piping Systems, 2019, DOI:10.1520/F2389-15.2.
- G. V. Loganathan and J. Lee, Decision Tool for Optimal Replacement of Plumbing Systems, Civ. Eng. Environ. Syst., 2005, 22(4), 189–204, DOI:10.1080/10286600500279964.
-
T. Fabian, J. L. Borgerson, S. I. Kerber, P. D. Gandhi, C. S. Baxter, C. S. Ross, J. Lockey and J. Dalton, Firefighter Exposure to Smoke Particulates, 2010 Search PubMed.
- C. J. Wieczorek, B. Ditch and R. G. Bill, Environmental Impact of Automatic Fire Sprinklers: Part 2. Experimental Study, Fire Technol., 2011, 47(3), 765–779, DOI:10.1007/s10694-010-0192-7.
- D. G. Neary, C. C. Klopatek, L. F. DeBano and P. F. Ffolliott, Fire Effects on Belowground Sustainability: A Review and Synthesis, For. Ecol. Manage., 1999, 122(1–2), 51–71, DOI:10.1016/S0378-1127(99)00032-8.
- M. D. Busse, K. R. Hubbert, G. O. Fiddler, C. J. Shestak and R. F. Powers, Lethal Soil Temperatures during Burning of Masticated Forest Residues, Int. J. Wildland Fire, 2005, 14(3), 267–276, DOI:10.1071/WF04062.
-
S. M. Haase and S. S. Sackett, Effects of Prescribed Fire in Giant Sequoia-Mixed Conifer Stands in Sequoia and Kings Canyon National Parks. Tall Timbers Fire Ecol. Conf. Proc., 1998, pp. 236–243 Search PubMed.
- T. Ueno, E. Nakashima and K. Takeda, Quantitative Analysis of Random Scission and Chain-End Scission in the Thermal Degradation of Polyethylene, Polym. Degrad. Stab., 2010, 95(9), 1862–1869, DOI:10.1016/j.polymdegradstab. 2010.04.020.
- N. S. Chong, S. Abdulramoni, D. Patterson and H. Brown, Releases of Fire-Derived Contaminants from Polymer Pipes Made of Polyvinyl Chloride, Toxics, 2019, 7(4), 57, DOI:10.3390/toxics7040057.
- T. Urabe and T. Imasaka, Analysis of Thermal Decomposition Products Arising from Polyvinyl Chloride Analogs by Supersonic Jet/Multiphoton Ionization/Mass Spectrometry, Talanta, 2000, 52(4), 703–709, DOI:10.1016/S0039-9140(00)00423-9.
- I. Aracil, R. Font and J. A. Conesa, Semivolatile and Volatile Compounds from the Pyrolysis and Combustion of Polyvinyl Chloride, J. Anal. Appl. Pyrolysis, 2005, 74(1–2), 465–478, DOI:10.1016/j.jaap.2004.09.008.
- E. Pǎrpǎriţǎ, M. T. Nistor, M. C. Popescu and C. Vasile, TG/FT-IR/MS Study on Thermal Decomposition of Polypropylene/Biomass Composites, Polym. Degrad. Stab., 2014, 109, 13–20, DOI:10.1016/j.polymdegradstab. 2014.06.001.
-
International Code Council, 2018 International Plumbing Code, 2017 Search PubMed.
-
NSF International, NSF/ANSI 61: Drinking Water System Components Health Effects, Ann Arbor Search PubMed.
-
NIST Spectrometry Data Center, Mass Spectra Database, 2020 Search PubMed.
-
U. S. Environmental Protection Agency, Region III Quality Assurance Team Revision No.:2.5 TIC Frequently Asked Questions, 2006, available from: https://www.epa.gov/sites/production/files/2015-06/documents/tics.pdf Search PubMed.
- J. Yu, L. Sun, C. Ma, Y. Qiao and H. Yao, Thermal Degradation of PVC: A Review, Waste Manage., 2016, 48, 300–314, DOI:10.1016/j.wasman.2015.11.041.
- K. J. Jordan, S. L. Suib and J. T. Koberstein, Determination of the Degradation Mechanism from the Kinetic Parameters of Dehydrochlorinated Poly(Vinyl Chloride) Decomposition, J. Phys. Chem. B, 2001, 105(16), 3174–3181, DOI:10.1021/jp003223k.
- J. M. Sustaita-Rodríguez, F. J. Medellín-Rodríguez, D. C. Olvera-Mendez, A. J. Gimenez and G. Luna-Barcenas, Thermal Stability and Early Degradation Mechanisms of High-Density Polyethylene, Polyamide 6 (Nylon 6), and Polyethylene Terephthalate, Polym. Eng. Sci., 2019, 59(10), 2016–2023, DOI:10.1002/pen.25201.
- A. Makarov, C. Munch and T. Moehring, Analysis of Polyolefin Stabilizers and Their Degradation Products, J. Sep. Sci., 2010, 33(22), 3463–3475, DOI:10.1002/jssc.201000493.
- D. Brocca, E. Arvin and H. Mosbæk, Identification of Organic Compounds Migrating from Polyethylene Pipelines into Drinking Water, Water Res., 2002, 36(15), 3675–3680, DOI:10.1016/S0043-1354(02)00084-2.
- G. Zhang, C. Nam, L. Petersson, J. Jämbeck, H. Hillborg and T. C. M. Chung, Increasing Polypropylene High Temperature Stability by Blending Polypropylene-Bonded Hindered Phenol Antioxidant, Macromolecules, 2018, 51(5), 1927–1936, DOI:10.1021/acs.macromol.7b02720.
- Z. Fodor, K. Barabas, M. Iring and F. Tüdös, Thermo-Oxidation of Polyethylene Stabilized with Irganox 1010 and Tinuvin 622, Int. J. Polym. Mater. Polym. Biomater., 1990, 13(1–4), 227–235, DOI:10.1080/00914039008039478.
- O. M. Folarin and E. R. Sadiku, Thermal Stabilizers for Poly(Vinyl Chloride): A Review, Int. J. Phys. Sci., 2011, 6(18), 4323–4330, DOI:10.5897/IJPS11.654.
- H. Bockhorn, A. Hornung and U. Hornung, Mechanisms and Kinetics of Thermal Decomposition of Plastics from Isothermal and Dynamic Measurements, J. Anal. Appl. Pyrolysis, 1999, 50, 77–101 CrossRef CAS.
- R. Font, I. Aracil, A. Fullana and J. A. Conesa, Semivolatile and Volatile Compounds in Combustion of Polyethylene, Chemosphere, 2004, 57(7), 615–627, DOI:10.1016/j.chemosphere.2004.06.020.
- J. H. Hodgkin, M. N. Galbraith and Y. K. Chong, Combustion Products from Burning Polyethylene, J. Macromol. Sci., Part A: Pure Appl. Chem., 1982, 17(1), 35–44, DOI:10.1080/00222338208056463.
- E. Roumeli, A. Markoulis, T. Kyratsi, D. Bikiaris and K. Chrissafis, Carbon Nanotube-Reinforced Crosslinked Polyethylene Pipes for Geothermal Applications: From Synthesis to Decomposition Using Analytical Pyrolysis-GC/MS and Thermogravimetric Analysis, Polym. Degrad. Stab., 2014, 100(1), 42–53, DOI:10.1016/j.polymdegradstab. 2013.12.027.
- J. Michal and J. Mitera, The Combustion Products of Polymeric Materials, Fire Mater., 1985, 9(3), 111–116 CrossRef.
- V. Purohit and R. A. Orzel, Polypropylene: A Literature Review of the Thermal Decomposition Products and Toxicity, Internet J. Toxicol., 1988, 7(2), 221–242, DOI:10.3109/10915818809014521.
-
U. S. Environmental Protection Agency, Provisional Peer-Reviewed Toxicity Values for n-Propylbenzene, 2009, available from: https://cfpub.epa.gov/ncea/pprtv/documents/Propylbenzenen.pdf Search PubMed.
- M. Coates, D. W. Connell and D. M. Barron, Aqueous Solubility and Octan-1-Ol to Water Partition Coefficients of Aliphatic Hydrocarbons, Environ. Sci. Technol., 1985, 19(7), 628–632, DOI:10.1021/es00137a008.
- W. F. von Oettingen, The Toxicity and Potential Dangers of Aliphatic and Aromatic Hydrocarbons, Yale J. Biol. Med., 1942, 15(2), 167–184 CAS.
- E. Reingruber and W. Buchberger, Analysis of Polyolefin Stabilizers and Their Degradation Products, J. Sep. Sci., 2010, 33(22), 3463–3475, DOI:10.1002/jssc.201000493.
- R. Buchalla, C. Boess and K. W. Bögl, Characterization of Volatile Radiolysis Products in Radiation-Sterilized Plastics by Thermal Desorption-Gas Chromatography-Mass Spectrometry: Screening of Six Medical Polymers, Radiat. Phys. Chem., 1999, 56(3), 353–367, DOI:10.1016/S0969-806X(99)00311-4.
- A. J. Whelton and T. Nguyen, Contaminant Migration From Polymeric Pipes Used in Buried Potable Water Distribution Systems: A Review, Crit. Rev. Environ. Sci. Technol., 2013, 43(7), 679–751, DOI:10.1080/10643389.2011.627005.
- A. J. Whelton, A. M. Dietrich and D. L. Gallagher, Impact of Chlorinated Water Exposure on Contaminant Transport and Surface and Bulk Properties of High-Density Polyethylene and Cross-Linked Polyethylene Potable Water Pipes, J. Environ. Eng., 2011, 137(7), 559–568, DOI:10.1061/(asce)ee.1943-7870.0000366.
- X. Huang, K. J. Pieper, H. K. Cooper, S. Diaz-Amaya, D. Y. Zemlyanov and A. J. Whelton, Corrosion of Upstream Metal Plumbing Components Impact Downstream PEX Pipe Surface Deposits and Degradation, Chemosphere, 2019, 236, 124329, DOI:10.1016/j.chemosphere.2019.07.060.
- M. Salehi, X. Li and A. J. Whelton, Metal Accumulation in Representative Plastic Drinking Water Plumbing Systems, J. - Am. Water Works Assoc., 2017, 109(11), E479–E493, DOI:10.5942/jawwa.2017.109.0117.
-
D. Wright, Failure of Plastics and Rubber Products: Causes, Effects and Case Studies Involving Degradation, Rapra Technology Limited, Shawbury, 2001 Search PubMed.
- J. Viebke and U. W. Gedde, Antioxidant Diffusion in Polyethylene Hot-Water Pipes, Polym. Eng. Sci., 1997, 37(5), 896–911, DOI:10.1002/pen.11733.
- A. J. Whelton and A. M. Dietrich, Critical Considerations for the Accelerated Ageing of High-Density Polyethylene Potable Water Materials, Polym. Degrad. Stab., 2009, 94(7), 1163–1175, DOI:10.1016/j.polymdegradstab. 2009.03.013.
- I. C. McNeill, M. H. Mohammed and W. J. Cole, A Detailed Analysis of the Pyrolysis Products from Dioctyltin Maleate and Its Mixture with PVC, Polym. Degrad. Stab., 1998, 61(1), 95–108, DOI:10.1016/S0141-3910(97)00136-5.
- H. Bockhorn, A. Hornung, U. Hornung and D. Schawaller, Kinetic Study on the Thermal Degradation of Polypropylene and Polyethylene, J. Anal. Appl. Pyrolysis, 1999, 48(2), 93–109, DOI:10.1016/S0165-2370(98)00131-4.
- M. Blazsó and E. Jakab, Effect of Metals, Metal Oxides, and Carboxylates on the Thermal Decomposition Processes of Poly (Vinyl Chloride), J. Anal. Appl. Pyrolysis, 1999, 49, 125–143 CrossRef.
- T. F. Booze, T. E. Reinhardt, S. J. Quiring and R. D. Ottmar, A Screening-Level Assessment of the Health Risks of Chronic Smoke Exposure for Wildland Firefighters, J. Occup. Environ. Hyg., 2004, 1(5), 296–305, DOI:10.1080/15459620490442500.
-
N. I. F. Center, National Large Incident Year-to-Date Report 10/30/2020, 2020 Search PubMed.
-
M. Ahrens and B. Evart, Fire Loss in the United States during 2019, 2019 Search PubMed.
- G. Cao, K. Huang, A. J. Whelton and A. D. Shah, Formation and Sorption of Trihalomethanes from Cross-Linked Polyethylene Pipes Following Chlorinated Water Exposure, Environ. Sci.: Water Res. Technol., 2020, 6(9), 2479–2491, 10.1039/d0ew00262c.
- L. M. Haupert and M. L. Magnuson, Numerical Model for Decontamination of Organic Contaminants in Polyethylene Drinking Water Pipes in Premise Plumbing by Flushing, J. Environ. Eng., 2019, 145(7), 04019034, DOI:10.1061/(asce)ee.1943-7870.0001542.
Footnote |
† Electronic supplementary information (ESI) available. See DOI: 10.1039/d0ew00836b |
|
This journal is © The Royal Society of Chemistry 2021 |
Click here to see how this site uses Cookies. View our privacy policy here.