DOI:
10.1039/D2MA00562J
(Review Article)
Mater. Adv., 2022,
3, 6085-6095
Sulfonated poly(ether ether ketone): efficient ion-exchange polymer electrolytes for fuel cell applications–a versatile review
Received
19th May 2022
, Accepted 24th June 2022
First published on 29th June 2022
Abstract
Fuel cell technology yields cleaner energy resources for diverse applications such as transport, power stationery, and portable devices. This review focuses on the role of sulfonated poly(ether ether ketone) (SPEEK) based proton conducting electrolyte membranes for fuel cell applications. The key objective of the review is to demonstrate the advantages of SPEEK-based composite membranes over Nafion by blending the SPEEK material with fluorinated polymer, hydrocarbon polymer, carbon-based materials, inorganic nanomaterials, etc. The proton conductivity and ion-exchange capacity of SPEEK polymer with various additives/fillers are highlighted. Since SPEEK polymer is produced in an eco-friendly approach, the composite membranes derived from SPEEK are much more appropriate for both PEMFC and DMFC applications. Herein, the comprised data displayed that the SPEEK-based composite membranes might be urgently considered a potential candidate for fuel cell systems.
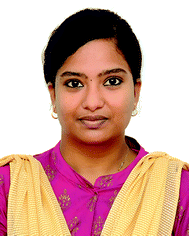
Berlina Maria Mahimai
|
Berlina Maria Mahimai completed her PhD degree in Chemistry from SRM Institute of Science and Technology, Kattankulathur, Tamil Nadu, India. She received her Master's degree in St. Joseph's College, Trichy, India, affiliated to Bharathidasan University in 2018. Her current research is focused on polymer electrolyte membranes doped with inorganic additives for fuel cell applications. |
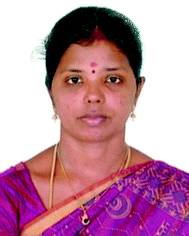
Gandhimathi Sivasubramanian
|
Gandhimathi Sivasubramanian completed her PhD degree from Anna University, Chennai. She received her Post Graduate degree in Physics from Sarah Tucker College affiliated to Manonmanium Sundaranar University. She is currently working as an Assistant Professor in Department of Physics, SRM Valliammai Engineering College, Kattankulathur, Tamil Nadu, India. She is working in the field of electrolyte membranes, fuel cell and laser physics. |
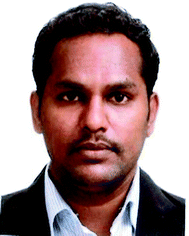
Karthikeyan Sekar
|
Karthikeyan Sekar is currently working as an Assistant Professor, at SRM Institute of Science and Technology, India. Previously he worked as Special Researcher at the University of Tokyo, Japan. He has received prestigious Japan Society for the Promotion of Science Invitational Fellowship 2022, and the Royal Society Newton International Alumni Grant 2021. Before that he has received the Japan Society for the Promotion of Science Postdoctoral Fellowship, Japan (2018 to 2020), and the Royal Society Newton International Fellow (2016 to 2018), UK. His research interest is toward the development of carbon-based materials as catalysts for energy and environmental applications. |
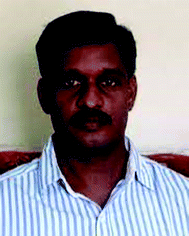
Dinakaran Kannaiyan
|
Dinakaran Kannaiyan is currently working as a Professor, in Department of Chemistry, Thiruvalluvar University, India. He has received prestigious JSPS Fellowship in 2006 and Brainpool invited scientist awarded by KRF, Government of South Korea in 2008. He is a member in Materials Research Society of India (IISC, Bengaluru) and Nano-Molecular Society of India (Hindustan College, Farah-Agra). His research interest includes polymer chemistry, nanohybrids and sensors. |
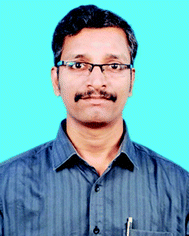
Paradesi Deivanayagam
|
Paradesi Deivanayagam completed his PhD degree in Chemistry from University of Madras, Tamilnadu, India. He is currently working as an Assistant Professor in Department of Chemistry, SRM IST, Kattankulathur Campus, Tamil Nadu, India. His research interest towards development of polymer electrolyte membranes for fuel cell applications. |
1. Introduction
A fuel cell is one of the vast enabling technologies for future sustainable hydrogen, carbon zero cycles, and circular economy. In a fuel cell, the chemical energy is converted into electrical energy with less environmental impact.1,2 In the past two decades, fuel cell applications are widely in demand in the form of engines, power stationary and portable power sources.3 In the electrochemical reactions of the fuel cell, the fuel is directly oxidized to produce water vapour, heat, and electricity. A variety of fuels such as ethanol, methanol, and hydrogen, are generally used in fuel cell systems. Therefore, electrochemical reactions in the fuel cell are explained as follows: hydrogen passes through the anode has changed into hydrogen ions, while electrons are released, which travel through an external circuit, and finally, reach the cathode for electrical current production.4 The prime component of the fuel cell is mainly the membrane electrode assembly (MEA), which consists of a gas diffusion layer, catalyst, and membrane.5 Focussing on the membrane situated between the anode and cathode, here membranes act as a conductor for the proton. The existing ions moved toward the cathode through the membrane by producing heat and water with free electrons. The mechanism of the fuel cell is depicted in Fig. 1.
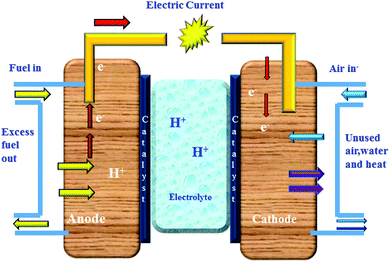 |
| Fig. 1 Schematic illustration of the fuel cell mechanism. | |
Fuel cells are divided into five different types according to their operating system, i.e., (i) Alkaline Fuel Cell (AFC) (ii) Phosphoric Acid Fuel Cell (PAFC) (iii) Molten Carbonate Fuel Cell (MAFC) (iv) Solid Oxide Fuel Cell (SOFC) and (v) Proton Exchange Membrane Fuel Cell (PEMFC).6 Various types of fuel cells and their properties are presented in Fig. 2. An ion-exchange membrane is used in various industrial process.7
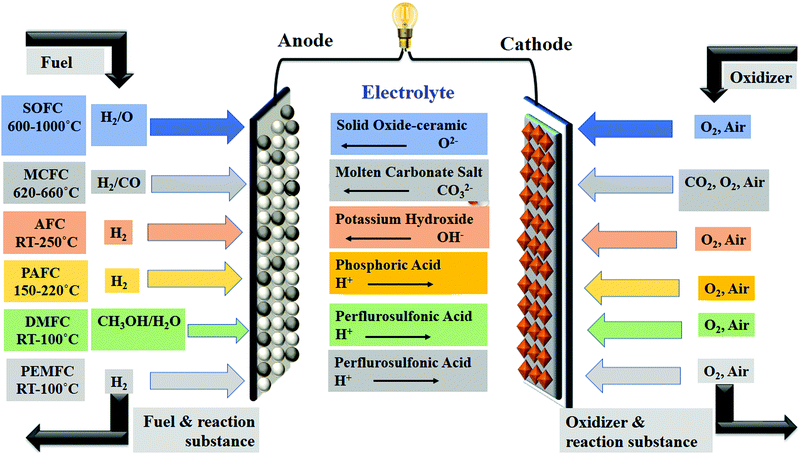 |
| Fig. 2 Various types of fuel cells and their properties. | |
Among membranes, PEMFC is a type of ion exchange membrane consisting of an ionic polymer carrying positive and negative charges in the moist state and enhancing the proton conductivity, corresponding reactions are provided in eqn (1)–(3),−8–10
| Anode electrode: 2H2 → 4H+ + 4e− | (1) |
| Cathode electrode: O2 → 4H+ + 4e− → 4H2O | (2) |
| Overall reaction: 2H2 + O2 → 2H2O | (3) |
First, Dupont developed the Nafion® membrane, which led to the large-scale manufacture with excellent conductivity and was used as a standard membrane for PEMFC.11–13 The structure of Nafion and its photographic image are shown in Fig. 3.
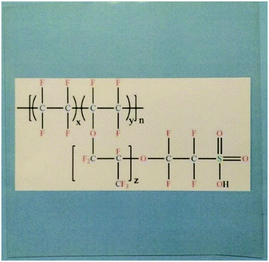 |
| Fig. 3 Structure and image of Nafion membrane. | |
Nafion® exists in the form of a hydrophobic phase with the hydrophilic sulfonic acid.14 Water is the basic need as a charge carrier in an electrolyte membrane for PEMFC and DMFC. Such that the membranes should always be kept in a hydrated state for good performance, but it affects the power density and system efficiency, in case water gets low. However, perfluorinated polymers are still unsatisfactory due to (i) high cost of production (ii) difficulty to work at high temperatures (iii) high permeability for reactants.15–17 To overcome the drawbacks of Nafion, researchers have focused on the alternative polymers, which are suitable to operate with HT–PEMFC and are also easy to synthesize in an economical way.18,19 Modifying Nafion with the additives such as CNT, silica, and functionalized clay blended with polymers have disadvantages in the form of cost and durability.20 In order to prepare the alternative electrolyte to Nafion, the following are the essential characteristics to fulfill the requirements.21
(i) Synthesize multiblock copolymer.
(ii) High-proton conductivity.
(iii) Cost-effective.
(iv) Branched polymer.
(v) Better oxidative stability.
(vi) Capability to withstand MEA fabrication.
The non-fluorinated hydrocarbon polymers mainly the aromatic polymer with bulky groups route to a high-performance PEMFC.22,23 Many advantages are noticed for the hydrocarbon-based polymers when compared with PFSE polymers, including structure, eco-friendly synthesis, ease of modification, and of course being inexpensive.24 Alternative membranes such as sulfonated polyether ketone (SPEEK), sulfonated polysulfone (SPSU), sulfonated polyphozphazene (SPPP), sulfonated polybenzimidazole (SPBI), sulfonated polyether sulfone (SPES), novel membranes are suitable for fabricating a working assembly in PEMFC.25Fig. 4 depicts the possible ways for the modification of polymer electrolyte membranes.
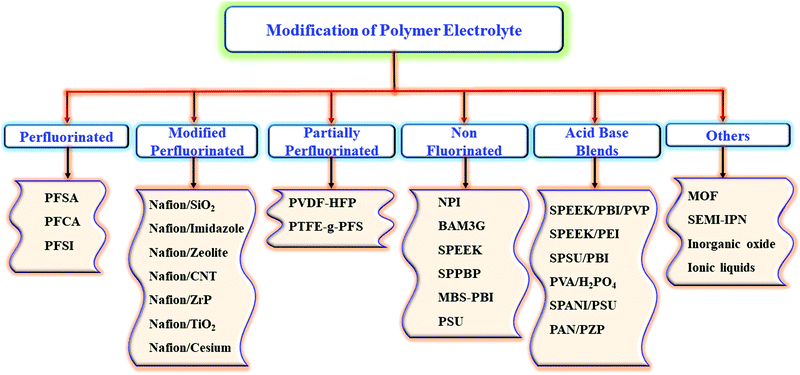 |
| Fig. 4 Classifications of modified polymer electrolyte fuel cell membranes. | |
Among these polymers, several studies are focused on S-PEEK polymers with interesting features such as excellent mechanical strength, high thermal stability, low methanol permeability, adequate proton conductivity, ease to handle, and are economical. These properties had upgraded the SPEEK as a promising hydrocarbon-based polymers for PEM to operate in both PEMFC and direct methanol fuel cells (DMFC).26,27 Recently, SPEEK was used in batteries too. The research group of Chen et al. 2021 synthesized various modified SPEEK for the high-performance batteries.28–31 It is a semi-crystalline polymer, amorphous in nature, and shows high thermal and chemical stabilities due to the presence of aromatic rings.32–34 It can be formed by post-sulfonation of commercial PEEK or pre-sulfonation by polymerization of various monomers in the synthesis method of (i) Friedel-craft acylation (ii) displacement reaction (iii) nickel-catalyzed coupling polymerization and (iv) ring-opening polymerisation involving monomers with sulfonic acid groups.35
To enhance the stability of the SPEEK membrane, it has been blended with other polymers, inorganic fillers, inorganic metal oxide, clays, nanoparticles, etc., The reason behind the incorporation of metal oxide into the polymers is to increase the membrane performance, such as selectivity, strength, permeability, hydrophilicity, conductivity, and ability to operate at HT–PEMFC.36 This review article describes in detail the advantages and disadvantages of modified SPEEK membranes by fillers, additives, and blending with other polymers.
2. Post Sulfonation of PEEK
Sulfonation reaction is one of the most versatile techniques to modify aromatic polymers. The sulfonation of PEEK was obtained via direct sulfonation using concentrated sulphuric acid.37 Initially, the PEEK powders were dried under vacuum for 12 h at 60 °C before sulfonation. The dried PEEK (2 g) was slowly added to 50 ml of concentrated sulphuric acid under continuous stirring at 30 to 40 °C for 1 h. After the addition of PEEK, the reaction temperature was raised to 60 °C with vigorous stirring. Then, the solution was slowly cooled to room temperature followed by transferring to ice-cooled water through a dropping funnel. The yielded precipitate was washed several times with deionized water until the pH reached neutral and then dried at 105 °C for 24 h in a hot-air oven. The scheme for the preparation of SPEEK is displayed in Fig. 5.
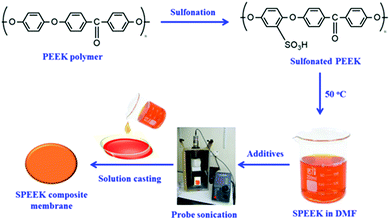 |
| Fig. 5 Schematic preparation of SPEEK membranes. | |
The degree of sulfonation (DS) of SPEEK was maintained by varying the reaction time and temperature. It was proved that the water uptake ability and proton conductivity of SPEEK depended on the DS value.38 It was shown that the increase in DS makes the polymer become more hydrophilic and absorbs more water, leading to the formation of water-mediated pathways for protons. In general, sulfonation of PEEK can be performed by the reagents concentrated sulphuric acid and chlorosulfonic acid. Even though the chlorosulfonic acid reagent was more advanced to an extent of sulfonation, it causes some degradation.39 Hence, sulphuric acid is essentially used to carry out the sulfonation reaction as it is free from degradation.40
2.1 Advantages over sulfonation
Poly(ether ether ketone) is a thermally stable, chemically resistant, and mechanically stable material. However, it cannot be directly used in fuel cell applications because of its fully hydrophobic segments. Hence, introducing the sulfonic acid group into PEEK polymer enhances the hydrophilicity, solubility in polar solvents, ion exchange capacity, and transport number. The solubility of the SPEEK membrane is reported as follows; (i) if the degree of sulfonation (DS) is around 30%, then it is soluble in DMF, DMAc, DMSO, and NMP under hot conditions only (ii) if the DS is around 40–70%, it is soluble in DMF, DMAc, DMSO, and NMP at room temperature (iii) if the DS is above 70%, it is soluble in methanol, and (iv) if the DS is 100%, it is soluble in hot water.41
3. Modification of SPEEK
In general, the sulfonation of SPEEK polymer is very sensitive to the reaction conditions such as reaction time, temperature, and inert atmosphere. The degree of sulfonation decreases or increases if the conditions are not maintained properly. The higher DS of SPEEK material causes large swelling at high temperatures and finally, it dissolves in water. For this reason, cross-linked, hybrid, and composite membranes are being studied to improve their properties. Higher DS always favoured excellent ion exchange and proton conductivity. Two mechanisms are involved in the transportation of ions in electrolytic membranes viz., (i) the Grotthuss mechanism and (ii) the vehicular mechanism. The clear proton transportation mechanism in the electrolyte membrane is presented in Fig. 6. Many studies have reported novel organic–inorganic composite membranes based on the SPEEK polymer.42
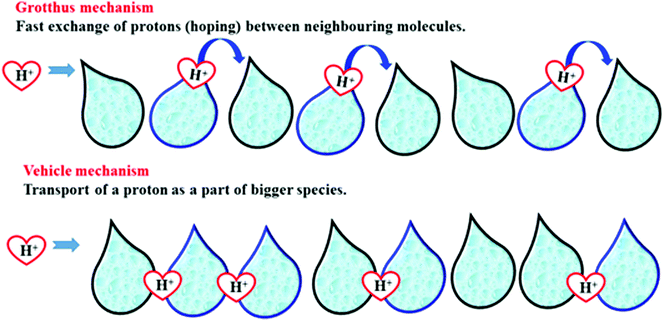 |
| Fig. 6 Proton transport mechanism in the fuel cell. | |
3.1. SPEEK blend membranes
The blend membrane of SPEEK with different polymers will further alleviate the proton conductivity of the resultant electrolyte membranes, and meet the demands of stability and life cycle for the membranes during the fuel cell operation.
3.1.1 Blending with non-fluorinated membranes.
Kanakasabai et al.43 reported that the polyvinyl alcohol (PVA) crosslinked with sulfosuccinic acid (PVA–SSA) blended with the SPEEK (DS = 0.7) to prepare PVA–SSA/SPEEK composite membranes. The results revealed that the blended polymers showed high tensile strength, but the IEC and water uptake of the blend membrane were lower than the pristine membrane. It may be low DS and crosslinking of PVA in the occurrence of SPEEK, which may be hindering the PVA–SSA reaction. The presence of SPEEK and the crosslinking of the PVA with SSA in the blend seem to lead to higher thermal stability. Under the hydrated conditions, the proton conductivity of PVA–SSA/SPEEK (70/30) was found to be 0.070 S cm−1.
Du et al.44 have developed a sulfonated poly (phthalazinone ether sulfone ketone) (SPPESK) and SPEEK used to prepare the blend proton exchange membrane. The reported SPPESK/SPEEK membrane exhibits a low swelling ratio and good water uptake. The proton conductivity of the blend membrane was reported as 0.212 S cm−1 at 80 °C.
3.1.2 Blending with Fluorinated membrane.
Apart from non-fluorinated blend membranes, SPEEK with fluorinated blend membranes was prepared by Inan et al.45 Water uptake and proton conductivity of the membranes were found to decrease with the addition of fluorinated polymers (PVDF–HFP). However, the reported proton conductivity of the SPEEK/PVDF–HFP membrane was sufficient to utilize the fuel cell operation. The characteristic results obtained from the blend membrane demonstrated that the non-fluorinated polymer blend with SPEEK showed excellent results for water uptake, swelling, and proton conductivity. Whereas, the fluorinated polymer blend with SPEEK is not much better but quite good.
Aygun et al.46 in their study, prepared a high ionic conduction boron phosphate (BP) doped sulfonated poly(ether ether ketone)/poly(vinylidene fluoride) (SPEEK/PVDF) blend membrane. SPEEK/PVDF/10BP achieved the maximum power density (242 mW cm2) and current density (400 mA cm2) at 0.6 V. At 80 °C, the proton conductivity of the SPEEK/PVDF/10BP sample was measured to be 39 mS cm−1. It was concluded that the addition of both the boron phosphate and the SPEEK/PVDF mix membrane showed promising outcomes for future fuel cell operations.
3.2 Cross-linked SPEEK by electron beam
Nowadays, the use of radiation for crosslinking in which an electron beam is widely used for polymers due to the advantage of insisting on the UV and thermal curing methods. The radiation cross-linking of the SPEEK membrane increased thermal, and mechanical properties, and maintained proton conductivity.
The hybrid SPEEK membrane crosslinked with UV and blended with biodegradable polymer limits the flexibility of the polymer chains with more compact network. Ramly et al.47 studied SPEEK with methylcellulose (MC), which were exposed to UV radiation with benzoin ethyl ether (BEE) as a photoinitiator. The radiation-induced demethylation, chain cleavage, acid group formation, and carbonyl in MC, led to enhanced hydrophilic behaviour. When the non-crosslinked membrane was crosslinked with BEE under UV for 30 min, the proton conductivity changed from 0.004 S cm−1 to 0.008 S cm−1 at 30 °C. Due to the denser structure, the UV membrane improved the dimensional stability after the crosslinking process.
Crosslinked SPEEK membranes were prepared by song et al.48 using the UV irradiation crosslinking method with a mixture of 1,4-butanediol divinyl ether (BDVE) and triallyl isocyanuarate (TAIC) in the ratio of 9
:
1. They found that the chemical stability and degree of cross-linking in the EB–SPEEK membranes were found to be increased by cross-linkers BDVE/TAIC. However, the water uptake, IEC and proton conductivity of the crosslinked membranes were decreased with higher loading of mixture in to the SPEEK polymer. When compared with the pristine membrane, the crosslinked membrane had good dimensional, mechanical strength, chemical, and thermal stability. The cross-linked membrane causes lower methanol permeability, but slightly reduced the proton conductivity. Hence, the results demonstrated that the EB irradiation of the SPEEK polymer improved the physicochemical properties.
3.2.1 Chemical crosslinking with SPEEK.
Many distinct additives are known in the literature, each with its unique crosslinking pathway, including cross-linking pathways using sulfonic acid groups and “free” hydrocarbon locations on the polymer chain.
Gupta et al. 201149 also looked at the influence of diol crosslinking agents' flexibility. To crosslink the SPEEK membrane, cyclohexane di-methanol (CDM) was utilised as the stiff crosslinking reagent and PEG (MW 200) as the flexible crosslinking reagent. The findings of conductivity and WU with various crosslinking agent ratios led to the conclusion that the best polymer to crosslinker ratio was 3
:
1. Furthermore, as compared to membranes crosslinked with the flexible crosslinker PEG, those crosslinked with the stiff CDM had worse characteristics. As a result, while crosslinking SAP, another factor to consider is the crosslinker's flexibility.
Sodaye et al.50 investigated the influence of the polyatomic alcohol linker length on the final membrane properties by crosslinking SPEEK with polyethylene glycol (PEG) of various molecular weights (MW/Da: 200, 400, 600, 3000, 6000, 10
000) and measuring the influence of the MW on the final membrane properties. The findings demonstrated that there was an optimal linker length for achieving the most effective stacking of macromolecular chains into hydrophobic and hydrophilic domains.
3.3 SPEEK modified with other polymers
A sulfonated-fluorinated, hydrophilic–hydrophobic block copolymer containing (sulfonated poly arylene biphenyl sulfone ether–decafluorobiphenyl) (SFBC) membrane, blended with SPEEK, was designed by Kim et al.51 The thermal stability using TGA, DSC, and mechanical properties were investigated in these membranes and found high performance upon increasing the loading of SPEEK blend with SFBC. When the wt.% of SPEEK increased, the temperature-dependent proton conductivity also increased, reaching a value of 0.091 S cm−1 for SFBC-50/SPEEK-20, which is 2.1 times higher than that of the pristine SFBC-50 membrane (0.043 S cm−1).
Kim et al.52 reported on a hybrid membrane with a ternary architecture consisting of sulfonated fluorinated multi-block copolymer (SFMC), blended with SPEEK, followed by loading with 1 to 5 wt.% of graphene oxide (GO) using simple monomer sulfonation to prepare a rigid hydrophobic backbone to blend the membrane. The hydrophilic–hydrophobic–hydrophilic structure of SFMC improved compatibility with SPEEK and GO, allowing for an extraordinary approach. IEC value indicated that SFSPG-5 reaches 1.60 meq g−1. The proton conductivity of the copolymer exhibits 0.119 S cm−1 at 90 °C for SFMC/SPEEK/GO-5 membrane. Therefore, the studies indicated that the crosslinked or hydrophilic–hydrophobic blends with SPEEK polymer resulted in excellent proton conductivity and thermo-mechanical properties.
Recently, phosphonate membranes have attracted additional consideration as substitute materials for developing new PEMFC applications. Abu et al.53 evaluated phosphonated polysulfone (PPSU–As) in the acid form with degrees of phosphonation (DP) of 0.4, 0.75, and 0.96 were successfully prepared and blended with the SPEEK that had DS of 0.75. –PO3H2 was capable of forming strong H bonds with acidic SPEEK polymers and, targeting swelling reduction with minimum sacrification of proton conductivity. When compared with the pristine SPEEK, the blend SPEEK/PPSU membrane showed lower methanol permeability, enhanced mechanical strength, and water uptake without the loss of proton conductivity. The blend membrane (30PPSU-A-0.96) showed higher proton conductivity when compared with the pristine SPEEK membrane. This performance continued up to 120 °C to reach a maximum conductivity of 0.124 S cm−1.
Polymer composites comprising SPEEK with 10 to 50 wt.% of poly (trimellitic anhydride chloride-co-4,4′-methylenedianiline) (PTCMA) with DS 53% was synthesized by Sultan et al.54 The water uptake of SPEEK/PTCMA (50 wt.%) was 11% at 25 °C. The highest proton conductivity of 0.004 S cm−1 at 90 °C was recorded in the composite membrane loaded with 20 wt.% PTCMA. Overall, the results showed an increase in PTCMA content and a decrease in the proton conductivity value. So, it can be concluded that the PTCMA will decrease the number of sulfonic acid groups, which increases the crystallinity of the composites and thereby reduces water uptake, which is an important step for proton transfer.
SPEEK with benzimidazole groups has noticeable benefits for low methanol crossover. However, there are drawbacks, such as low water uptake, poor solubility and mainly decreased conductivity value, although it has advantages of good mechanical strength, and high chemical, and thermal stabilities. Zhang et al.55 reported that increasing the PBI content from 5 to 20 wt.% decreases the proton conductivity values from 0.080 S cm−1 to 0.022 S cm−1. Recently, song et al.56 reported that SPEEK–Na with PBI was immersed in dilute acid to obtain an ionic SPEEK/PBI crosslinked membrane. Here, it forms an immense interaction of SPEEK/PBI not only improves the oxidation resistance and mechanical strength but also reduces the methanol crossover. The proton conductivity of the blend membrane with 20 wt% reached the value of 0.198 S cm−1 at 70 °C but when the weight percentage of PBI increases to 40%, it resulted in poor conductivity in the composite membrane. Such that the SPEEK doped with moderate PBI yields a productive output for the usage in DMFC fuel cells.
Nur Hidayati et al.57 proposed the natural polymer chitosan to blend with the SPEEK. Chitosan is a promising membrane with good chemical resistance and high hydrophilicity. When chitosan with hydroxyl and amine groups is modified with SPEEK, it exhibits good conductivity with low methanol permeability. Compared with pristine chitosan, the composite membrane of SPEEK/Chitosan showed lower water uptake and methanol permeability with 2.46 × 10−6 cm2 s−1 at room temperature. IEC values of SPEEK/Chitosan are higher, resulting in high proton conductivity. It was reported that SPEEK/Chitosan showed contrasting results for DMFC so further studies are to be considered.
3.4 SPEEK modified with inorganic materials and nanocomposites
Polymers impregnated with inorganic materials are ionically conductive. Polymers with the inorganic composites are gaining attraction due to the addition of various additives as they can operate at high temperatures compared to pristine polymers.58 SPEEK nanocomposite membranes have been prepared using different nanofillers, such as nanoclays, carbon nanotubes (CNTs), graphene, and nanostructured SPEEK fibres. These fillers displayed improved dispersion within the matrix as well as enhanced proton conductivity and mechanical stability.
Many researchers have used carbon as one of the main sources for blending with SPEEK because of its reduction in methanol crossover, and good mechanical and thermal stability. Sivasubrmanian et al.59 reported a SPEEK membrane doped with single-walled CNT (SWCNT) and fly ash (FA) prepared using a post sulfonation method, they prepared SPEEK (DS 65%) and incorporated it with SWCNT and FA using a solution casting method. The incorporation of SWCNT/FA into SPEEK enhanced the water uptake and mechanical properties, but a reduction in IEC was noticed. The SP–CNT–FA-8 nanocomposite membrane showed maximum proton conductivity of 0.027 S cm−1 at 30 °C and 0.034 S cm−1 at 90 °C. The conductivity of the composite membrane not only depended on the number of sulfonic acid groups present in the polymer backbone but also on the water uptake, which led to the good channeling.60
Numerous nanostructured clay materials have been used to blend with SPEEK to improve membrane properties. Jaafar et al.61 reported 2,4,6-triaminopyrimidine (TAP) nanoclay-based composite membrane, where TAP was acting as a compatibilizer to improve the compatibility between SPEEK and cloisite15A. They prepared three different composites as follows; (i) SPEEK with 1 wt% Cloisite15A (SP/Cl) (ii) SPEEK with 1 wt% Cloisite15A modified with 1 wt% of (TAP) (SP/Cl/TAP) and (iii) SPEEK with only 1 wt% of TAP (SP/TAP). The SP/Cl/TAP composite showed better proton conductivity of 0.003 S cm−1 when compared with the other two composites, but the values are lower compared to Nafion. Overall, the results indicated that the addition of TAP nanoclay promotes better dispersion and good performance of the membrane. Apart from this, Porchelvi et al.62 worked with montmorillonite (MMT) nanoclay and Gosalawit et al.63 worked with sulfonated MMT (SMMT). Both the membranes exhibited excellent performances while operating in the fuel cell.
The silica-based nanocomposite is also a key material for fuel cell applications, which showed good mechanical properties and water retention properties and the SPEEK/SiO2 composite showed good proton conductivity. Zhang et al.64 obtained SPEEK/SiO2 through an electrospinning process with an average fiber diameter of 232 nm. The SPEEK/SiO2 nanocomposite membrane displayed better water uptake and proton conductivity when compared to the Nafion and SPEEK membranes. The proton conductivity of 0.077 S cm−1 at 90 °C was observed in the composite membrane.
Inorganic nanoparticles incorporated into the SPEEK polymer matrix were developed to enhance the characteristics and properties of the native polymer. Nanoparticles such as TiO2, ZrO2, Al2O3, Fe3O4, etc. have a substantial impact on proton conductivity. Apart from this, a new metal oxide material praseodymium oxide (PSO) as an efficient inorganic additive impregnated with the SPEEK polymer possesses 60% DS reported by Gandhimathi et al.65 IEC and water uptake values increased when compared with the pristine SPEEK membrane. The proton conductivity of the composite membrane SP–PSO-10 exhibited a value of 0.018 S cm−1 at 30 °C and 0.028 S cm−1 at 90 °C, which is higher than that of the SPEEK membrane. Therefore, higher loading of PSO improved the physical and chemical properties of the composite membranes.
Gandhimathi et al.66 also reported a nanocomposite membrane by incorporating niobium pentoxide (NBO) into a SPEEK matrix polymer (DS 57%). The composite membranes displayed higher water uptakes and enhanced thermal stability when compared to the pristine SPEEK. The IEC value of the composite membrane was found to increase gradually from 1.62 to 1.80 meq. g−1. The proton conductivity of the SP–NBO-2.5 membrane was 0.019 S cm−1, whereas the SPEEK membrane loaded with 10 wt.% of NBO produced 0.028 S cm−1. Hence, the SP–NBO-10 membrane was considered a promising material for PEMFC applications. Table 1 provides the comparison of IEC and ionic conductivity of various reported SPEEK-based composite membranes. From the table, it can be identified that all SPEEK-based membranes exhibited proton conductivity on the order of 10−2 S cm−1.
Table 1 Comparison of IEC and proton conductivity of SPEEK-based PEM materials
Composite membranes |
IEC (meq. g−1) |
Proton conductivity (S cm−1) |
Power density (mW cm−2) |
Ref. |
SPEEK–SPI Blend-40 |
1.73 |
0.120 at 100 °C |
— |
67
|
SPEEK/EB/Y2O3 |
— |
0.080 at RT |
— |
68
|
SPEEK/BS/Y2O3 |
|
0.010 at 90 °C |
— |
|
SPEEK–OMB (benzene silica) |
— |
0.079 at 80 °C |
56 |
69
|
SPEEK–SSA (silica sulfuric acid) |
1.19 |
0.130 at 80 °C |
— |
70
|
SPEEK–BP (copolymers) |
|
0.0000001 at 50 °C |
— |
71
|
SPKCL (closite 30B) |
1.20* |
0.0197 at 100 °C |
— |
72
|
SPEEK–SSA (silica sulphonic acid) |
1.55 |
0.145 at 80 °C |
— |
73
|
SPEEK/Cloisite 15A/TAP |
0.75 |
0.0004 at RT |
213 |
74
|
SP/PPOSS (silsesquioxane) |
— |
0.043 at 80 °C |
— |
75
|
SPEEK/ZrP (zirconium phosphate) |
— |
0.079 at 150 °C |
— |
76
|
SPEEK/ZPMA (zirconium, phosphomolibdic acid) |
— |
0.072 at 80 °C* |
— |
77
|
SPEEK/sulfonated cyclodextrin |
1.91 |
0.060 at 80 °C* |
29.52 |
78
|
SPEEK/PVA/SGO/Fe3O4 |
1.43 |
0.084 at RT |
— |
79
|
SPEEK–Cs–TPA (cesium–tungstophosphoric acid) |
1.5* |
0.130 at 50 °C |
— |
80
|
SPEEK–BPPO (Semi-IPN) |
1.17 |
0.0029 at 50 °C |
30 |
81
|
SPEEK–PAMPS–TiO2 |
2.03 |
0.090 at RT |
283 |
82
|
SPEEK–PSSA–TiO2 |
1.98 |
0.075 at 25 °C |
245 |
|
SPEEK–SZ (Sulfated Zirconia) |
1.45 |
0.007 at 80 °C* |
— |
83
|
SPEEK/TPPS |
2.01 |
0.038 at 30 °C |
267 |
84
|
SPEEK/APDMS-grafted silica |
1.57 |
0.120 at 80 °C* |
— |
85
|
SPEEK/Amine grafted silica |
— |
0.035 at RT |
— |
86
|
SPEEK–HPA MCM-41 |
— |
0.007 at 140 °C |
— |
87
|
SPEEK/SiO2–SiWA |
— |
0.048 at RT |
— |
88
|
SPEEK/Zeolite beta crystals |
— |
0.130 at 60 °C |
10 |
89
|
SPEEK/AgGO–GO |
— |
0.037 at RT |
— |
90
|
SPEEK–PVB (nanofibre mat) |
1.71 |
0.003 at 130 °C |
— |
91
|
SPEEK/PIL/PA |
— |
0.004 at 160 °C |
— |
92
|
SPEEK/PW11V/rGO |
— |
0.064 at 65 °C |
— |
93
|
SPEEK/TiNFs |
— |
0.105 at 70 °C* |
57.1 |
94
|
SPEEK/PES/Fe3O4 |
0.33 |
0.0003 |
— |
95
|
SPEEK/PES/TiO2 |
0.29 |
0.0004 |
— |
|
SPEEK/PES/MoO3 |
0.31 |
0.0002 at RT |
— |
|
SPEEK/BaZrYO3 |
— |
0.091 at 80 °C |
44 |
96
|
SPEEK/SiWA/SO/AO |
— |
0.061 at RT |
— |
97
|
SPEEK–SiO2–PANI |
1.49 |
0.00036 at RT |
— |
98
|
SPEEK–ZrO2–PANI |
1.45 |
0.00033 at RT |
— |
|
SPEEK–TiO2–PANI |
1.51 |
0.00039 at RT |
7.98 |
|
SPEEK–AIL |
— |
0.0069 at 120 °C |
203 |
99
|
SPEEK/SGO |
2.3 |
0.055 at 80 °C |
378 |
100
|
SPEEK/ACNT |
1.28 |
0.160 at 90 °C |
96.02 |
101
|
SPEEK/FPAPB/Fe3O4–FGO |
1.66 |
0.011 at 120 °C |
— |
102
|
SPEEK/SPVdF–HFP/GO |
1.81 |
0.122 at 90 °C |
— |
103
|
SPEEK/CNC |
1.74 |
0.186 at 95 °C |
— |
104
|
PEEK/sSrZrO3@TiO2 |
1.16 |
0.121 at 80 °C |
140 |
105
|
SPEEK/ZCO |
1.46 |
0.009 at 30 °C |
— |
106
|
SPEEK/ZrO2/PIL |
— |
0.660 at750 °C |
— |
107
|
3.5 SPEEK-based IPNs
The preparation of a semi-interpenetrating polymer network (semi-IPN) has attracted attention due to the simplicity of the method for fabricating innovative PEMs with a variety of morphologies, improved mechanical performance, and reduced membrane swelling.108 Xupo Liu et al. developed a diamine cross-linker on Semi-IPNs of BPPO/SPEEK Membranes for the direct methanol fuel cell. The SPEEK polymer chains were interpenetrated into semi-IPNs created by an alkylation reaction between bromo benzyl groups of bromomethylated poly(phenylene oxide) and amine groups of the 2,2′-(ethylenedioxy)bis(ethylamine) cross-linker.
The experimental results demonstrated that the semi-IPN has a significant impact on the membrane's dimensional stability, mechanical strength, and methanol-permeation resistance.109 Paradesi et al., prepared semi-IPN by polymerizing poly (ethylene glycol) diacrylate using benzoyl peroxide as an initiator with SPEEK. The impedance results showed the reduced proton conductivity with increasing content of PEGDA in Semi-IPN. However, the hydrolytic stability of semi-IPN membranes was higher than that of SPEEK, resulting in high performance and hydrolytic stability of the PEG-based materials.110 Schematic illustration for the modification of the SPEEK matrix in various forms is presented in Fig. 7.
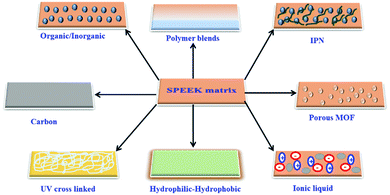 |
| Fig. 7 Modification of SPEEK in various forms. | |
3.6 SPEEK-based MOF and ZIF
Current modification work on SPEEK has been focused on the metal–organic framework (MOF) and zeolite imidazole framework (ZIF). MOFs or metal–organic frameworks are a class of porous materials and their structures are usually made up of metal ions joined with organic ligands by coordination bonds. MOFs are being studied for a variety of applications, the most promising ones are mainly energy storage and gas separation.111 Zhang et al.112 used hybrid material of SPEEK/HPW@MIL101, which contains MOF MIL-101 (Cr), to prepare nanohybrid membranes for PEMFC applications. The ionic conductivity of the MOF-loaded composite membrane was 7.25 times higher than that compared to the pristine SPEEK membrane. Letícia G. da Trindade et al.113 prepared SPEEK membrane with Zr-MOF by a casting method, and SPEEK/MOF composite membranes containing 7.5 wt% Zr-MOF exhibited high conductivity. The MOF's pore diameters aid in the aggregation of water molecules, which are held in place by hydrogen bonding within the pores.
ZIFs are a form of MOFs made up of tetrahedral metal ions (such as Zn2+, Co2+, Cu2+, and others) and imidazole and ZIFs are regarded as a good addition in the application of polymer-based PEMs due to their superior chemical and thermal stability, high microporosity in the cavities, and unique imidazole ring structure.114 Fuqiang Hu et al.115 reported a new SPEEK-based proton exchange membrane made by incorporating as-prepared ZIF–COOH and the addition of ZIF–COOH, resulting in a significant improvement in the mechanical properties, proton conductivity, and methanol permeability. Fortunately, the SPEEK/ZIF–COOH-5 had a proton conductivity of 0.0152 S cm−1 at 80 °C and tensile strength of 44.1 MPa, both were significantly higher than those of recast SPEEK. The generated SPEEK/ZIF composite membranes are shown to be potential candidates for promising PEM applications, and the prepared ZIF–COOH might be used to modify other polymers more efficiently.
4. Conclusion
Sulfonated poly (ether ether) ketone-based polymers are potential electrolyte membranes for fuel cell applications. This review article covered the recent work on the development of various SPEEK-based electrolyte membranes for use in PEMFC and DMFC applications. An ion exchange capacity and proton conductivity of SPEEK composite/blend membranes were compared to understand the suitability of these membranes for fuel cells. The major advantages of the SPEEK composite membrane include high proton exchange and low methanol crossover. Almost, all the SPEEK-related composite materials exhibited ionic conductivity in the order of 10−2 S cm−1, which was sufficient to operate as a membrane in a hydrogen-oxygen fuel cell. In the future, an investigation is needed to focus on the rise of affinity toward membranes with water, as it increases the proton conductivity and to use appropriate inorganic particles. Also, this review highlighted the role of various metal oxides over the SPEEK matrix and it is concluded that the SPEEK-based membranes are one of the remarkable proton-exchanging polymer electrolytes for use in fuel cells.
Conflicts of interest
There are no conflicts to declare.
Acknowledgements
We sincerely thank the Department of Chemistry, SRMIST, Kattankulathur campus for providing good infrastructure to carry out this review article.
References
- Q. Yan, H. Toghiani and H. J. Causey, J. Power Sources, 2006, 161, 492–502 CrossRef CAS
.
- Y. Cai, Z. Yue, Q. Jiang and S. Xu, J. Energy Chem., 2018, 27, 820–825 CrossRef
.
- S. Bose, T. Kuila, T. X. H. Nguyen, N. H. Kim, K. T. Lau and J. H. Lee, Prog. Polym. Sci., 2011, 36, 813–843 CrossRef CAS
.
- K. Jiao K and M. Ni, Int. J. Energy Res., 2017, 41, 1793–1797 CrossRef
.
- S. J. Peighambardoust, S. Rowshanzamir and M. Amjadi, Int. J. Hydrogen Energy, 2010, 35, 9349–9384 CrossRef CAS
.
-
T. Mokrani, Advances in Chemical Engineering, ed. Z. Nawaz, 2012, pp. 505–542, ISBN: 978-953-51-0392-9 Search PubMed
.
- S. S. Sekhon, B. S. Lalia, J. S. Park, C. S. Kim and K. Yamada, J. Mater. Chem., 2006, 16, 2256–2265 RSC
.
- N. Cele and S. S. Ray, Macromol. Mater. Eng., 2009, 294, 719–738 CrossRef CAS
.
- L. G. Da Trindade, L. Zanchet, P. C. Martins, K. M. Borba, R. D. Santos, R. D. S. Paiva, L. A. Vermeersch, E. A. Ticianelli, M. O. de Souza and E. M. Martini, Polymer, 2019, 179, 121723 CrossRef CAS
.
- K. Poonkuzhali, M. M. Berlina and D. Paradesi, RSC Adv., 2020, 10, 26521 RSC
.
- Z. Yao, Z. Zhang, L. Wu and T. Xu, J. Membr. Sci., 2014, 455, 1–6 CrossRef CAS
.
- J. M. Andújar and F. Segura, Renewable Sustainable Energy Rev., 2009, 13(9), 2309–2322 CrossRef
.
- S. Ahmed and Y. Cai, J. Appl. Polym. Sci., 2019, 136, 1–7 Search PubMed
.
- J. A. Asensio, E. M. Sanchez and P. Gomez-Romero, Chem. Soc. Rev., 2010, 39, 3210–3239 RSC
.
- K. Divya, M. S. S. A. Saraswathi, D. Rana, S. Alwarappan and A. Nagendran, Polymer, 2018, 147, 48–55 CrossRef CAS
.
- A. Muthumeenal, S. Neelakandan, P. Kanagaraj and A. Nagendran, Renewable Energy, 2016, 86, 922–929 CrossRef CAS
.
- S. R. Narayanan, T. I. Valdez and S. Firdosy, J. Electrochem. Soc., 2009, 156, B152–B159 CrossRef CAS
.
- H. Wang, X. Li, X. Zhuang, B. Cheng, W. Wang, W. Kang, L. Shi and H. Li, J. Power Sources, 2017, 340, 201–209 CrossRef CAS
.
- A. K. Sahu, S. Pitchumani, P. Sridhar and A. K. Shukla, Bull. Mater. Sci., 2009, 32, 285–294 CrossRef CAS
.
- S. L. Chen, A. B. Bocarsly and J. Benziger, J. Power Sources, 2005, 152, 27–33 CrossRef CAS
.
- F. Ahmad Zakila, S. K. Kamarudina and S. Basria, Renewable Sustainable Energy Rev., 2016, 65, 841–852 CrossRef
.
- H. Liao, K. Zhang, G. Xiao and D. Yan, J. Membr. Sci., 2013, 447, 43–49 CrossRef CAS
.
- K. Divya K, M. S. Sri Abirami Saraswathi and S. Alwarappan, Polymer, 2018, 155, 42–49 CrossRef
.
- K. Oh, K. Ketpang, H. Kim and S. Shanmugam, J. Membr. Sci., 2016, 507, 135–142 CrossRef CAS
.
- C. Laberty-Robert, K. Valle, F. Pereira and C. Sanchez, Chem. Soc. Rev., 2011, 40, 961–1005 RSC
.
- M. H. D. Othman, A. F. Ismail and A. Mustafa, Malaysian Polym. J., 2010, 5, 1–36 Search PubMed
.
- K. Prashantha and L. Joong-Hee, Polym. Int., 2007, 56, 371–375 CrossRef
.
- G. Wang, M. Zhang, Z. He, J. Zhang, J. Chen, R. Wang, A. Teng and Y. Dai, J. Appl. Polym. Sci., 2021, 138, 50592 CrossRef CAS
.
- A. Li, G. Wang, Y. Quan, X. Wei, F. Li, M. Zhang, R. I. Ur, J. Zhang, J. Chen and R. Wang, Ionics, 2020, 26, 2467–2475 CrossRef CAS
.
- A. Li, G. Wang, X. Wei, F. Li, M. Zhang, J. Zhang, J. Chen and R. Wang, J. Mater. Sci., 2020, 55, 16822–16835 CrossRef CAS
.
- G. Wang, F. Wang, A. Li, M. Zhang, J. Zhang, J. Chen and R. Wang, J. Appl. Polym. Sci., 2020, 137, 48830 CrossRef CAS
.
- G. Maier and J. Meier-Haack, Adv. Polym. Sci., 2008, 216, 1–62 CAS
.
- C. H. Park, C. H. Lee, M. D. Guiver and Y. M. Lee, Prog. Polym. Sci., 2011, 36, 1443–1498 CrossRef CAS
.
- N. Nishad Fathima, R. Aravindhan and D. Lawrence,
et al., SPEEK Polymeric Membranes for Fuel Cell Application and Their Characterization: A Review, J. Sci. Ind. Res., 2007, 66, 209–219 Search PubMed
.
- D. Shukla, Y. S. Negi, J. Uppadhyaya and V. Kumar, Polym. Rev., 2012, 52, 189–228 CrossRef CAS
.
- N. Sazali, M. F. Ghazali and J. Jaafar, J. Adv. Res. Fluid Mech. Therm. Sci., 2019, 2, 326–336 Search PubMed
.
- M. M. Berlina, K. Poonkuzhali, S. Gandhimathi and D. Paradesi, Polym. Technol. Mater., 2020, 59, 1791–1800 Search PubMed
.
- M. L. Di Vona ML and P. Knauth, Z. Phys. Chem., 2013, 227, 595–614 CrossRef
.
- M. T. Bishop, F. E. Karasz, P. S. Russo and K. H. Langley, Macromolecules, 1985, 18, 86–93 CrossRef CAS
.
- X. Jin, M. T. Bishop and T. S. Ellis, Br. Polym. J., 1985, 17, 4–10 CrossRef CAS
.
- M. Rikukawa and K. Sanui, Prog. Polym. Sci., 2000, 25, 1463–1502 CrossRef CAS
.
- A. R. Hakim, A. Purbasari, T. D. Kusworo and E. L. Dewi, Proceeding Int. Conf. Chem. Mater. Eng., 2012, 1–11 Search PubMed
.
- P. Kanakasabai, P. Vijay, A. P. Deshpande and S. Varughese, J. Power Sources, 2011, 196, 946–955 CrossRef CAS
.
- L. G. Du, X. M. Wu and X. M. Yan, Polym. Eng. Sci., 2012, 28, 148–152 CAS
.
- T. Y. Inan, D. Hacer, E. E. Unveren and E. Ekar, Int. J. Hydrogen Energy, 2010, 35, 12038–12053 CrossRef CAS
.
- A. Çalı, A. Şahin and A. R. Irfan, Int. J. Hydrogen Energy, 2022 DOI:10.1016/j.ijhydene.2022.05.171
.
- N. N. Ramly, N. A. Aini, N. Sahli, S. F. Aminuddin, M. Z. A. Yahya and A. M. M. Ali, Int. J. Hydrogen Energy, 2017, 42, 9284–9292 CrossRef CAS
.
- J. M. Song, S. Y. Lee, H. S. Woo, D. W. Shin, J. Y. Sohn, Y. M. Lee and J. Shin, J. Membr. Sci., 2014, 469, 209–215 CrossRef CAS
.
- D. Gupta and V. Choudhary, Int. J. Hydrogen Energy, 2011, 36, 8525–8535 CrossRef CAS
.
- M. Kumari, H. S. Sodaye, D. Sen and R. C. Bindal, Solid State Ionics, 2018, 316, 75–84 CrossRef CAS
.
- A. R. Kim, M. Vinothkannan and D. J. Yoo, Int. J. Hydrogen Energy, 2017, 42, 4349–4365 CrossRef CAS
.
- A. R. Kim, M. Vinothkannan and D. J. Yoo, J. Energy Chem., 2018, 27, 1247–1260 CrossRef
.
- N. Y. Abu-Thabit, S. A. Ali, S. M. J. Zaidi and K. Mezghani, J. Mater. Res., 2012, 27, 1958–1968 CrossRef CAS
.
- A. S. Sultan, J. K. Adewole, A. M. Al-Ahmed, M. Nazel and S. M. Zaidi, Int. Polym. Process., 2017, 32, 41–49 CrossRef CAS
.
- H. Zhang, X. Li and C. Zhao, J. Membr. Sci., 2008, 308, 66–74 CrossRef CAS
.
- M. Song, X. Lu, Z. Li, G. Liu, G. Yin and Y. Wang, Int. J. Hydrogen Energy, 2016, 41, 12069–12081 CrossRef CAS
.
- N. Hidayati, T. Harmoko, M. Mujiburohman and H. Purnama, AIP Conf. Proc., 2019, 2114, 060008 CrossRef
.
- E. Quartarone, S. Angioni and P. Mustarelli, Materials, 2017, 10, 687 CrossRef PubMed
.
- G. Sivasubramanian, K. Hariharasubramanian, P. Deivanayagam and J. Ramasamy, Polym. J., 2017, 49, 703–709 CrossRef CAS
.
- D. Paradesi, D. Samanta, A. B. Mandal and S. N. Jaishankar, RSC Adv., 2014, 4, 26193–26200 RSC
.
- J. Jaafar, I. F. Ismail and T. Matsuura, J. Membr. Sci., 2009, 345, 119–127 CrossRef CAS
.
- S. Porchelvi, R. Kannan, P. Bahavan Palani, K. Sainul Abidin and S. Rajashabala, Mater. Res. Innovations, 2019, 23, 33–38 CAS
.
- R. Gosalawit, S. Chirachanchai, S. Shishatskiy and S. P. Nunes, J. Membr. Sci., 2008, 323, 337–346 CrossRef CAS
.
- G. Zhang, Z. Zhou, C. Li C and H. Chu, J. Wuhan Univ. Technol., Mater. Sci. Ed., 2009, 24, 95–99 CrossRef CAS
.
- S. Gandhimathi, H. Krishnan and D. Paradesi, High Perform. Polym., 2020, 32, 296–305 CrossRef CAS
.
- S. Gandhimathi, H. Krishnan and D. Paradesi, Polym. Polym. Compos., 2019, 4, 1–10 Search PubMed
.
- X. Li, Y. Song and Z. Liu, High Perform. Polym., 2014, 26, 106–113 CrossRef
.
- J. Chen, Q. Guo, D. Li, J. Tong and X. Li, Prog. Nat. Sci.: Mater. Int., 2012, 22, 26–30 CrossRef
.
- E. B. Cho, D. X. Luu and D. Kim, J. Membr. Sci., 2010, 351, 58–64 CrossRef CAS
.
- L. Du, X. Yan, G. He, X. Wu, Z. Hu and Y. Wang, Int. J. Hydrogen Energy, 2012, 37, 11853–11861 CrossRef CAS
.
- R. T. S. M. Lakshmi, J. Meier-haack, K. Schlenstedt K, C. Vogel, V. Choudhary and I. K. Varma, J. Membr. Sci., 2005, 261, 27–35 CrossRef CAS
.
- V. R. Hande, S. K. Rath, S. Rao and M. Patri, J. Membr. Sci., 2011, 372, 40–48 CrossRef CAS
.
- Y. Li, X. Wang and M. Xie, High Perform. Polym., 2014, 26, 770–778 CrossRef
.
- J. Jaafar, A. F. Ismail, T. Matsuura and K. Nagai, J. Membr. Sci., 2011, 382, 202–211 CrossRef CAS
.
- D. Gupta and V. Choudhary, React. Funct. Polym., 2013, 73, 1268–1280 CrossRef CAS
.
- Y. Kozawa, S. Suzuki, M. Miyayama and T. Okumiya, Solid State Ionics, 2010, 181, 348–353 CrossRef CAS
.
- D. X. Luu and D. Kim, J. Membr. Sci., 2011, 371, 248–253 CrossRef CAS
.
- T. Yang and C. Liu, Int. J. Hydrogen Energy, 2011, 36, 5666–5674 CrossRef CAS
.
- H. Mighani and N. Farshchi, Macromolecules, 2013, 9, 102–110 CAS
.
- Y. Inan, E. Unveren and M. Kaya, Int. J. Hydrogen Energy, 2010, 5, 1–12 Search PubMed
.
- X. Liu, Y. Zhang, Y. Chen, C. Li, J. Dong, J. Wang, Z. Yang and H. Cheng, Energy Technol., 2018, 6, 2264–2272 CrossRef CAS
.
- P. Salarizadeh, M. Javanbakht and S. Pourmahdian, Int. J. Hydrogen Energy, 2019, 44, 3099–3114 CrossRef CAS
.
- Z. Mossayebi, T. Saririchi and S. Rowshanzamir, Int. J. Hydrogen Energy, 2016, 41, 12293–12306 CrossRef CAS
.
- A. Carbone, M. Gaeta and A. Romeo, ACS Appl. Energy Mater., 2018, 1, 1664–1673 CrossRef CAS
.
- M. J. Kayser, M. X. Reinholdt and S. Kaliaguine, J. Phys. Chem. B, 2011, 115, 2916–2923 CrossRef CAS PubMed
.
- M. J. Kayser, M. X. Reinholdt and S. Kaliaguine, J. Phys. Chem. B, 2010, 114, 8387–8395 CrossRef CAS PubMed
.
- S. M. J. Zaidi and M. I. Ahmad, J. Membr. Sci., 2006, 279, 548–557 CrossRef CAS
.
- M. Y. Chia, H. S. Thiam, L. K. Leong, C. H. Koo and L. H. Saw, Int. J. Hydrogen Energy, 2019, 45, 22315–22323 CrossRef
.
- S. Erce, H. Erdener and R. G. Akay, Int. J. Hydrogen Energy, 2009, 34, 4645–4652 CrossRef
.
- K. Ben Liew, J. X. Leong and W. R. Wan Daud, J. Power Sources, 2020, 449, 227490 CrossRef CAS
.
- J. L. Reyes-Rodriguez, O. Solorza-Feria and A. García-Bernabe, RSC Adv., 2016, 6, 56986–56999 RSC
.
- Q. Che and J. Yue, RSC Adv., 2016, 6, 111729–111738 RSC
.
- H. Cai, X. Lian and Q. Wu, J. Non-Cryst. Solids, 2016, 447, 202–206 CrossRef CAS
.
- C. Dong, Z. Hao and Q. Wang, Int. J. Hydrogen Energy, 2017, 42, 25388–25400 CrossRef CAS
.
- S. Elakkiya, G. Arthanareeswaran and K. Venkatesh, Int. J. Hydrogen Energy, 2018, 21750–21759 CrossRef CAS
.
- P. Hosseinabadi, K. Hooshyari and M. Javanbakht, New J. Chem., 2019, 43, 16232–16245 RSC
.
- A. F. Ismail, N. H. Othman and A. Mustafa, J. Membr. Sci., 2009, 329, 1829 CrossRef
.
- B. P. Tripathi and V. K. Shahi VK, Colloids Surf., A, 2009, 340, 10–19 CrossRef CAS
.
- S. Qu, Y. Sun and J. Li, Ionics, 2017, 23, 1607–1611 CrossRef CAS
.
- R. Kumar, M. Mamlouk and K. Scott, RSC Adv., 2014, 4, 617–623 RSC
.
- A. R. Kim, M. Vinothkannan and M. H. Song, Composites, Part B, 2020, 188, 107890 CrossRef CAS
.
- M. Vinothkannan, A. R. Kim and G. Gnana Kumar, RSC Adv., 2017, 7, 39034–39048 RSC
.
- M. Vinothkannan, A. R. Kim and K. S. Nahm, RSC Adv., 2016, 6, 108851–108863 RSC
.
- S. Bano, Y. S. Negi and R. Illathvalappil, Electrochim. Acta, 2019, 293, 260–272 CrossRef CAS
.
- G. Gnana Kumar and A. Manthiram, J. Mater. Chem. A, 2017, 5, 20497–20504 RSC
.
- M. Prathap, K. Poonkuzhali, M. M. Berlina and D. Paradesi, High Perform. Polym., 2020, 32, 984–991 CrossRef CAS
.
- J. A. F. L. Batalha, K. Dahmouche and R. B. Sampaio, Macromol. Mater. Eng., 2017, 302, 1–11. CrossRef
.
- M. Chao, H. Sheng, H. Dongmei and R. Shan, Hindawi, Adv. Polym. Technol., 2020 DOI:10.1155/2020/3845982
.
- L. Xupo, Z. Yunfeng, C. Yazhou and L. Cuicui, Energy Technol., 2018, 6, 2264–2272 CrossRef
.
- D. Paradesi and R. Alwar Ramanujam, J. Macromol. Sci., Part A: Pure Appl.Chem., 2012, 49, 191–200 CrossRef
.
- U. Mueller, M. Schubert and F. Teich, J. Mater. Chem., 2006, 16, 626–636 RSC
.
- Z. Bei, C. Ying and L. Zhen, Electrochim. Acta, 2017, 240, 186–194 CrossRef
.
- G. D. T. Letícia, M. N. B. Katiuscia and Z. Letícia, Mater. Chem. Phys., 2019, 236, 121792 CrossRef
.
- Z. Chen, D. Ying and R. J. Justin, J. Membr. Sci., 2012, 389, 34–42 CrossRef
.
- F. Hu, T. Wen-Chin, F. Zhong, B. Zhang, J. Wang, H. Liu, G. Zheng, C. Gong and S. Wen, New J. Chem., 2020, 44, 13788–13795 RSC
.
|
This journal is © The Royal Society of Chemistry 2022 |