DOI:
10.1039/D4SU00027G
(Perspective)
RSC Sustain., 2024,
2, 871-880
The 12 principles of green membrane materials and processes for realizing the United Nations' sustainable development goals†
Received
21st January 2024
, Accepted 21st February 2024
First published on 22nd February 2024
Abstract
Membrane science and technology has the potential to considerably contribute to most of the United Nations' sustainable development goals. This technology has diverse applications, including in mining, water treatment, healthcare, and space. Membranes directly impact the three pillars of sustainability, namely, the economy, environment, and society. Membrane materials and processes must be developed in line with green chemistry and engineering principles. Herein, the 12 principles of green membrane materials and processes are introduced to encourage and guide scientists, engineers, and practitioners to design, explore, and implement membranes efficiently and sustainably. Moreover, the membrane waste management hierarchy is introduced, and the importance of each principle and priorities for future research are established.
Sustainability spotlight
Membranes are widely used in applications such as water purification, petrochemical refining, pharmaceutical manufacturing, mining, construction, warfare, apparel, electronics, forensics, medical applications, and space exploration. They are at the core of filtration and separation processes and impact various industries. However, producing membrane materials typically involves high energy consumption, harmful chemicals, generation of substantial waste, and resource-intensive and environmentally damaging processes, which pose environmental threats and undermine sustainability. Using green chemistry and engineering principles specifically tailored to membrane materials and processes, sustainable membrane technology can be developed. To address the aforementioned challenges and align with the United Nations' sustainable development goals (UN-SDGs), I propose the 12 principles of green membrane materials and processes. These principles provide a strategic framework for fabricating sustainable membrane materials and developing sustainable membrane processes, thereby fostering a greener future for all. The contribution of the principles to the three pillars of sustainability is explained, particularly how they contribute to the United Nations' sustainable development goals. Moreover, their importance and research priorities are set, and a membrane waste management hierarchy is introduced.
|
1 Introduction
A series of 12 principles of green chemistry and related fields has been published, which represents pivotal milestones in the evolution of sustainable practices within the respective fields. These principles have been devised to address the increasing environmental concerns and minimize the adverse impacts of human activities on the planet; they have redefined chemical processes and technological advancements.
The 12 principles of green chemistry, introduced by Anastas and Warner,1 were a notable turning point that laid the foundation for the design and synthesis of molecules by prioritizing efficiency, safety, and environmental sustainability. Based on these principles, chemists were encouraged to innovate while minimizing waste, toxicity, and energy consumption. The initial set of principles was refined and tailored to specific disciplines. Anastas and Zimmerman outlined the 12 principles of green engineering in a seminal article,2 which was closely followed by The Sandestin Declaration with 65 chemists and engineers from the industry, academia, and government.3 These principles established a framework for engineers to integrate environmental considerations into the design, development, and operation of products and processes, demonstrating the need for sustainability in engineering practice.
Circular chemistry, which encompasses the principles of designing chemical systems with a focus on recycling, renewability, and minimizing waste, has more recently emerged and reflects a broader shift toward a circular economy. Circular chemistry principles have evolved to meet the demands of resource conservation and sustainable production methods. This holistic approach to chemistry aims to close the loop on materials and chemical processes, ensuring efficient resource usage and waste minimization. The 12 principles of green chemistry, green engineering, and circular chemistry were developed by scientists and engineers to align their practices to ensure environmental sustainability. These principles continue to inspire innovation and guide the way toward a more environmentally friendly and economically viable future.
Green metrics and health, safety, and environment pictogram-based semiquantitative comparison analyses for assessing the relative sustainability of membrane materials and processes have been developed.4–6 The obtained values should be used with a pinch of salt. Nonetheless, they can provide some comparison between materials and processes and assist in sustainable decision-making. Notably, the assessment performed on lab-scale membranes cannot be directly extrapolated to scaled-up membrane modules.
2 The 12 principles of green membrane materials
Membrane materials are widely used in applications such as water purification,7 petrochemical refining,8 pharmaceutical manufacturing,9 mining,10 construction,11,12 warfare,13 apparel,14 electronics,15 forensics,16,17 medical applications,18 and space exploration.19 They are at the core of filtration and separation processes and impact various industries. However, producing these materials typically involves high energy consumption, harmful chemicals, generation of substantial waste, and resource-intensive and environmentally damaging processes, which pose environmental threats and undermine sustainability. Using green chemistry and engineering principles specifically tailored to membrane materials, sustainable membrane technology can be developed. Several studies have reported green membrane materials.20,21 To address the aforementioned challenges and align with the United Nations' sustainable development goals (UN-SDGs), I propose the 12 principles of green membrane materials (Fig. 1). These principles provide a strategic framework for fabricating sustainable membrane materials, thereby fostering a greener future for membrane science and technology.
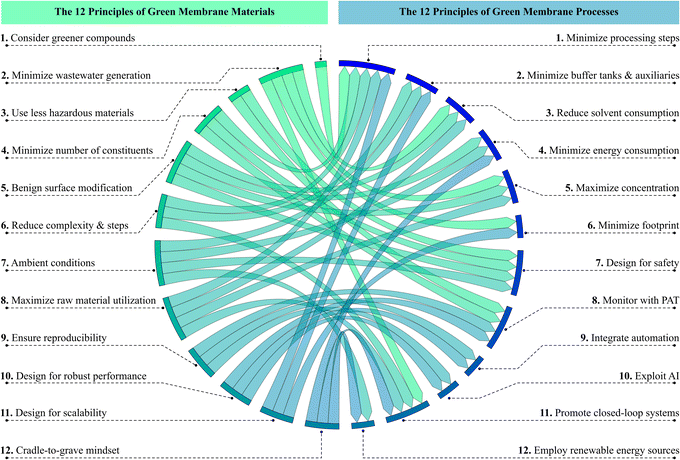 |
| Fig. 1 Interconnectivity of the 12 principles of green membrane materials and the 12 principles of green membrane processes. PAT = process analytical technology; AI = artificial intelligence. | |
The 12 principles of green membrane materials are briefly explained below, along with their importance in membrane science.
2.1 Consider greener compounds
Fossil-based and toxic solvents, monomers, polymers, and crosslinkers or other additives are used for membrane fabrication. Renewable and sustainable raw materials should be used instead to reduce the dependence on finite resources and minimize ecological impact. Membrane modules are complex and contain components such as a selective layer, supports, glues, and spacers. By replacing hazardous solvents with environmentally benign alternatives, safe working conditions can be ensured and ecological impact can be reduced. Designing membrane materials inspired by natural systems will enable harnessing the efficiency and sustainability of biological membranes.
2.2 Minimize wastewater generation
Large quantities of water are required for immersion precipitation during phase inversion or washing involved in membrane fabrication. Wastewater generation can be avoided by controlled evaporation, precipitation from the vapor phase, and thermally induced phase separation. Wastewater generation can be minimized using a high membrane area to coagulation bath volume ratio or using high concentrations of dope solutions.
2.3 Use less hazardous materials
Highly reactive, toxic, bi- or trifunctional monomers or crosslinkers are used for interfacial polymerization of thin film composite membranes and crosslinking of integrally skinned asymmetric membranes. Alternatively, less reactive and naturally sourced chemicals such as biomass-derived raw materials should be used, and the processing steps from biomass to the final membrane should be minimized. Environmentally benign chemicals should be used for surface modification if necessary. Overall, nontoxic components and additives should be used for membrane material fabrication to ensure the safety of both users and the environment.
2.4 Minimize the number of constituents
The number of raw materials and constituents in the final membrane material must be as low as possible. The use of chemical additives, such as plasticizers or stabilizers, must be minimized and those with low environmental impact must be used when necessary. All the ingredients during membrane fabrication are required to achieve the desired performance and effect. Therefore, the effect of all constituents must be decoupled. Membrane material synthesis should use minimal chemicals to promote environmentally friendly and resource-efficient processes.
2.5 Benign surface modification
After the formation of an initial membrane, surface modification is often required to fine-tune its properties or introduce new functionalities. Surface modifications require additional raw materials, solvents, processing steps, and purification steps and are therefore unfavorable from a sustainability perspective. Thus, this process should be avoided unless necessary to achieve the desired membrane function. Instead, one-pot alternatives, solventless approaches, and mild conditions, e.g., blending in dope solutions and cold plasma and performing ultraviolet treatments, can be considered.
2.6 Reduce complexity and steps
Membrane material fabrication is a complex multistep process. The number of fabrication steps can vary based on the membrane material, which should however be minimized by eliminating or combining them via one-pot approaches. Processes must be implemented to minimize the release of volatile organic compounds (VOCs) and other emissions causing air and water pollution.
2.7 Ambient conditions
The membrane fabrication processes must be optimized to minimize energy consumption and the associated greenhouse gas emissions. The chemistry, dissolution, and formulation must be performed at room temperature and atmospheric pressure. If these processes require higher temperatures and pressures, their deviance from the ambient conditions should be minimized. Aqueous solutions should not have low or high pH because the generated wastewater will require neutralization.
2.8 Maximize raw material utilization
The loss of valuable raw materials should be avoided, and their incorporation into the final product should be maximized. The mass balance of reactions and processing steps must be assessed for optimization. These strategies will reduce waste generation, mitigate environmental harm, and enhance sustainability.
2.9 Ensure reproducibility
The fabrication process should be sufficiently detailed to facilitate material reproduction. Based on Murphy's law, possible misinterpretation of membrane fabrication procedures must be mitigated. Membrane areas, solvent and antisolvent volumes, monomer and polymer concentrations, and molar equivalents should also be reported when applicable. While data reporting is more straightforward and a consensus has been reached by the community, in other areas, the experiments and reporting vary considerably. This hinders the direct comparison of membrane performance and the related development of the entire field. The reported guidelines22 must be collectively implemented. The lack of data digitalization and their open access calls for urgent action.
2.10 Design for robust performance
Membranes with extended lifespans and resistance to degradation must be fabricated, thereby reducing the need for frequent replacements and waste generation. Ecoresponsive properties can facilitate the effective implementation of membranes in various applications. Membrane materials with properties that respond to environmental changes must be developed, and their performance must be optimized while reducing resource consumption. Membranes with high selectivity and permeability should be fabricated to maximize their efficiency and reduce resource consumption in downstream processes.
2.11 Design for scalability
Innovative designs of new membrane materials and membrane preparation methods must account for scalability and industrial implementation. Some materials and methods can work extremely well on a small scale; however, their industrial implementation can be hindered by the lack of appropriate equipment at scale, high energy demand, incompatibility with existing module designs, and safety considerations. All materials—membranes, glue, seals, and spacers—must be compatible with each other and the feed stream of the intended application. The initial design of both materials and methods for membrane preparation should be practical; moreover, there is a need for more efficient module designs.
2.12 Cradle-to-grave mindset
Ecofriendly end-of-life options must be considered for used membrane materials, such as reuse, upcycling, recycling, depolymerization, biodegradation, and safe disposal, to minimize their environmental impact. These options are listed in the order of their importance and promotion of circular economy practices (Fig. 2). Membrane materials that can be reused without extensive treatment, easily upcycled to high-value materials, recycled and repurposed for low-value utilization, and can depolymerize the membrane and recover the monomer fractions must be developed. These materials should also be biodegradable. If all the above methods fail, then safe disposal followed by incineration with energy recovery should be used. Comprehensive life cycle assessments must be conducted to (i) evaluate the environmental impact of membrane preparation and (ii) identify opportunities for improvement.23–25 Composite materials enhance the membrane separation performance. However, the disassembly and recovery of constituents at the end of the membrane lifetime are cumbersome. Organocatalysts should be used instead of precious metal-based catalysts for polymerization and depolymerization.
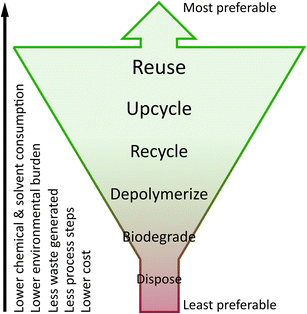 |
| Fig. 2 Ecofriendly end-of-life options for polymer membrane materials: membrane waste management hierarchy. | |
3 The 12 principles of green membrane processes
Membrane processes are pivotally used in several industrial separation processes, showcasing their versatility. In water treatment, membranes are used for desalination, removing impurities, and achieving potable water standards. In the pharmaceutical industry, they are used for the purification and concentration of drugs and biopharmaceuticals, ensuring the highest quality and efficacy of the final products. In natural product extraction, membrane processes enable the isolation and concentration of the target compounds. Moreover, membranes are extensively used in the food and beverage sector, facilitating the concentration and separation of components such as proteins, enzymes, and flavors. The petrochemical industry benefits from membranes in gas separation, enabling the purification of valuable components from complex mixtures. Additionally, membrane processes are employed in the field of environmental protection for air and gas purification and in the energy sector for hydrogen separation and carbon capture. This diverse range of applications underscores the indispensable role of membrane processes across various industrial sectors, contributing considerably to efficiency, sustainability, and advancement. The following are the 12 principles of green membrane processes, which are briefly described, highlighting their importance in membrane technology.
3.1 Minimize processing steps
Minimizing processing steps in membrane separations is crucial for enhancing efficiency, reducing operational costs, and promoting sustainability in industrial processes. Streamlining the separation processes accelerates the overall production timeline and minimizes energy consumption, contributing to a more ecofriendly operation. By reducing the number of processing steps, manufacturers can optimize resource utilization and reduce waste generation, aligning with environmentally conscious practices. Moreover, a simplified membrane separation process enhances system reliability, as fewer steps mean less maintenance and fewer opportunities for technical complications, failures, or errors. This efficiency translates into economic benefits and ensures consistent and high-quality outputs. Before membrane application, information on pretreatment and conditioning must be provided, and membranes should not be excessively washed and conditioned. Appropriate membrane materials and configurations (e.g., ultrafiltration, nanofiltration, reverse osmosis, and cascades) must be chosen based on the application requirements considering factors such as chemical compatibility, temperature resistance, and fouling propensity. Process integration and utilization of membrane rigs must be ensured across different production lines.
3.2 Minimize buffer tanks and auxiliaries
Minimizing buffer tanks and auxiliaries in membrane technology is essential for both economical and sustainable reasons. The elimination of buffer tanks facilitates the production line, resulting in a resource-efficient and cost-effective operation. By eliminating excess storage capacity, tanks between cascade stages, and auxiliary equipment, manufacturers can considerably reduce capital and operational expenses. This streamlined approach improves the overall efficiency of the entire plant and reduces the environmental footprint. The conservation of space and resources aligns with sustainable practices, promoting a more responsible use of equipment, materials, and energy. Additionally, fewer buffer tanks and auxiliaries contribute to a leaner and more agile manufacturing setup, enabling quicker response times and interventions via in-line analytics. The total gas or liquid volume in the separation stage is also reduced, thereby enhancing safety.
3.3 Reduce solvent consumption
Membrane design optimization is essential for maximizing the recovery of valuable resources (e.g., water, organic solvents, and solutes) from feed streams and reducing waste and resource consumption. The use of closed-loop systems must be enforced to recycle and reuse process water and minimize the release of pollutants into the environment. Manufacturers can decrease the discharge of harmful chemicals into water bodies, preventing aquatic pollution and safeguarding ecosystems. In pharmaceutical manufacturing, where solvents are crucial in drug synthesis, adopting solvent use minimization and recycling principles reduces environmental impact and enhances the safety of workers in production facilities. Moreover, reducing solvent consumption reduces VOC emissions and aligns with global efforts to combat climate change. Membrane-based solvent recovery systems can help companies comply with regulations and policies by offering a cleaner and more sustainable approach.
3.4 Minimize energy consumption
Membrane processes that require the least amount of energy for operation, such as using low-pressure membranes, should be designed and process conditions must be optimized. Using lower-pressure differentials across the membrane is ideal because more energy is used at higher pressures. Membranes must be regularly cleaned and maintained to prevent fouling, scaling, or degradation, which can increase resistance and energy consumption. Effective cleaning protocols must be implemented based on the nature of the feed solution and fouling mechanisms. Renewable energy sources, such as solar or wind power, should be used for membrane separation processes to reduce greenhouse gas emissions. Solar-powered membrane separation systems can find applications in rural and isolated communities for water, agriculture, and other sectors where decentralized and sustainable solutions are required. Options for energy recovery within the production line must be explored, such as using pressure exchangers, which transfer energy from a high-pressure fluid stream to a low-pressure one, and can save considerable input energy.
3.5 Maximize concentration
Working at high feed concentrations offers many advantages that greatly contribute to efficiency and sustainability. Reducing the use of solvents and carrier gases can reduce the production cost and minimize the environmental impact associated with solvent and gas production, transportation, and disposal. Using high concentrations of solvents and carrier gases will result in a more compact manufacturing process and less space and energy requirements, particularly for storage. Membranes can concentrate feed streams, and the decreased volume facilitates easier handling, storage, and transportation of products. Using high concentrations of solvents will ensure a more sustainable and efficient approach to chemical production, aligning with the global shift toward greener practices in the industry. Thus, using high concentrations of solvents is economically advantageous and positively impacts the ecological footprint and overall efficiency of chemical manufacturing processes. However, high concentrations pose several challenges such as (i) increased membrane fouling, which necessitates frequent cleaning and maintenance, resulting in operational downtime and (ii) increased energy consumption. Feed concentrations must be carefully selected as they may offset the general benefits of membrane application.
3.6 Minimize the footprint
A smaller physical footprint of a process can be more efficient and sustainable for several reasons. A compact manufacturing process often enables the implementation of just-in-time production methods. Minimizing the process footprint enables more efficient overall use of the product site and ultimately reduces the need for large inventories, lowers storage requirements and transportation costs, and preserves natural habitats. The compact and modular design of membrane systems minimizes the potential impact on surrounding environments and reduces the need for large-scale infrastructure, which can contribute to safety and environmental concerns. The layout and size of the membrane modules and the overall system must be determined by considering the number of stages, flow direction (e.g., crossflow or dead-end), and pretreatment requirements. A system that minimizes fouling, scaling, and maintenance requirements must be ensured, and in situ solvent recycling and a fewer number of buffer tanks and auxiliaries must be used.
3.7 Design for safety
While most membrane processes are generally undertaken close to ambient temperature and pressure, some have specific requirements and safety considerations. The membrane process can be performed at low and high temperatures and pressures. Compliance with relevant safety standards and regulations specific to the industry and location must be ensured. Membrane processes are often conducted in closed systems, which reduce the risk of exposure to hazardous materials. Closed systems help prevent leaks and spills, enhancing both safety and environmental protection. Environmental regulations for waste stream discharge or disposal should also be duly considered. Membrane processes typically operate with minimal noise and vibration, contributing to a safer working environment for personnel. This is in contrast to some other industrial processes that may involve loud machinery or high levels of vibration. The safe operation of membrane processes must be ensured by implementing appropriate safety measures and risk assessments.
3.8 Monitor with PAT
Membrane processes can be easily monitored and controlled, allowing for real-time adjustments of operational parameters. This enhances the ability of personnel to respond promptly to any issues, preventing potential safety hazards. Additionally, operating conditions such as pressure, temperature, and flow rates must be optimized to maximize membrane performance. A robust monitoring and control system must be implemented to track system performance, ensure consistent operation and product quality control, detect issues, and make process adjustments in real time. In-line or on-line analytical instruments must be used to monitor feed stream quality and system parameters for fault detection and prevention. Process analytical technology (PAT) can be used to minimize downtime, plan maintenance, and avoid failed batches with out of specification products during production. The data generated by PAT can be used for data-driven decision-making, allowing operators to make informed choices about process adjustments, maintenance schedules, and overall system optimization.
3.9 Integrate automation
Automation allows for real-time monitoring and control of various parameters in a membrane separation process. This ensures that the process operates under optimal conditions, thereby minimizing energy consumption and reducing waste generation. Automated systems can perform tasks with a high level of precision and accuracy, reducing errors and minimizing product losses. This contributes to higher overall yield and less waste in the manufacturing process. The integration of automation systems in membrane separation processes can optimize energy usage as it allows for adjusting parameters such as temperature, pressure, and flow rates based on real-time data. Such an integration will minimize energy consumption and reduce the environmental impact of the separation process. Automation can enhance continuous membrane processes by reducing the need for frequent startups and shutdowns. Continuous processes are generally more energy-efficient and provide better control over product quality, leading to improved efficiency and sustainability. Automation allows for remote monitoring and control, which enables operators to oversee the process from a central location, thereby reducing the need for on-site personnel and tasks that are hazardous for humans. This can include handling of toxic substances, high-pressure operations, sampling, and performing repetitive tasks resulting in human error. Thus, detailed records of system design, operation, maintenance, and performance must be maintained for future reference and compliance.
3.10 Exploit artificial intelligence
Machine learning can be leveraged in various ways to enhance and optimize membrane separation processes. Machine learning models can be trained to predict membrane separation performance, i.e., permeability, rejection, selectivity, and energy consumption. This helps in understanding and optimizing membrane processes and in designing more efficient membrane materials. Machine learning algorithms can be used to find optimal operating conditions such as pressure, temperature, process configurations, and flow rates which maximize separation efficiency and minimize energy consumption. Energy consumption must be optimized by using operating conditions that balance separation efficiency and energy usage. The models can be trained to identify anomalies during membrane processes, enabling the early detection of membrane failure and fouling and thereby preventing failed batches. Moreover, such models can assist in diagnosing the root causes of performance degradation and continuously learn from operational data to adapt and improve control strategies over time. Machine learning can also be used to analyze large datasets generated during membrane separation processes to extract valuable insights, patterns, and correlations that may not be apparent using traditional analysis methods. Their implementation can predict the remaining useful life of membranes and other components, enabling proactive maintenance and minimizing downtime as well as determining the most cost-effective timing for membrane replacement based on performance degradation trends. The successful implementation of machine learning requires access to high-quality data, appropriate feature selection, and thorough validation of the models under real-world conditions. Specific information on data-driven membrane technology for instance can be found in the literature.26–28
3.11 Promote closed-loop systems
Closed-loop systems minimize waste generation by optimizing the use of raw materials and reducing the disposal of byproducts. Closed loops allow for the efficient recovery and recycling of valuable resources, mitigating the impact of resource scarcity and, in turn, promoting a circular economy. The use of closed-loop systems must be encouraged to recycle and reuse process solvents and water and minimize the release of pollutants into the environment. Reduced waste generation will also lower the costs associated with waste treatment, disposal, and environmental remediation. Such systems enhance resource utilization, leading to cost savings by minimizing the need for additional raw materials. Consequently, they decrease dependency on external suppliers for certain raw materials, enhancing the security and stability of the supply chain. Moreover, closed-loop systems align with increasingly stringent environmental regulations, helping companies stay compliant with waste disposal management. To this end, membrane-based closed-loop separation processes such as in situ solvent, reagent, and catalyst recycling units must be integrated. Additionally, green metric analysis can be used to quantify the potential improvements in sustainability, e.g., wastewater intensity, solvent intensity, E factor, and mass productivity. Methods for the valorization of byproducts generated during the membrane separation process must be developed. Optimization of processes and finding alternative uses for waste materials will help minimize waste or lead to zero waste generation. A life cycle assessment of membrane processes must be conducted to identify environmental hotspots and areas for improvement, and strategies must be developed for the end-of-life phase of membranes,29,30 including recycling and responsible disposal.
3.12 Employ renewable energy sources
Traditional energy sources, such as fossil fuels, contribute considerably to greenhouse gas emissions. Using renewable energy sources, such as bioenergy, biomass, salinity gradient power, and solar, wind, or hydropower, for membrane separation processes will reduce greenhouse gas emissions. While fossil fuels are finite resources and their extraction and consumption lead to resource depletion, renewable energy sources are sustainable. This ensures a more stable and long-term energy supply for industrial processes as well as membrane separation processes. Research and development efforts have focused on designing membranes with lower energy requirements, allowing the exploitation of renewable energy. The integration of energy recovery devices, such as pressure exchangers or turbines, helps capture and reuse energy within membrane systems, making them more energy-efficient. Recent efforts in membrane-based gas and water separations combined with renewable energy systems have been reviewed.31–33 Note that membrane processes can be either powered by renewable energy or used to extract renewable energy (hydrogen from biomass gasification, biogas generation or upgrading, bioalcohol purification and recovery, and salinity gradient power).
A survey was conducted to identify the extent of study and importance of each green membrane material (Fig. 3a) and green membrane process (Fig. 3b) principle. The obtained data revealed that all principles were important, with scores of 3.55–4.87 for materials and 3.53–4.53 for processes, where 5 represents the highest score. Regarding the extent of the membrane literature covering each principle, the scores were considerably lower. The least studied area was the “cradle-to-grave mindset”, with a score of 1.97, whereas the most studied area with the highest score of 3.34 was the “reduce complexity and steps”. Further research in all areas is required to bridge the gap between the extent of the study and the importance of each principle. The high ratios of importance to the extent of the study indicate the principles that require immediate attention (Fig. 3c). The top three most-important areas highlighted for membrane materials are “cradle-to-grave mindset”, “minimize wastewater generation”, and “ensure reproducibility” and those for membrane processes are “integrate automation”, “monitor with PAT”, and “exploit AI”. Refer to the ESI† for the details of the survey.
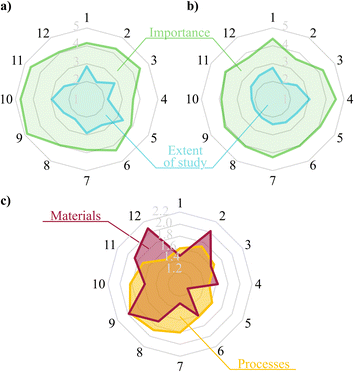 |
| Fig. 3 Extent of study in the literature versus the importance of each principle for green membrane materials (a) and processes (b) based on 142 responses in an anonymized survey. The higher the importance over extent ratio (c), the more research is required for the principle. Gridlines from the center to the outside correspond to the lowest (least important or least studied) to highest (most important or most studied) scores. The numbers 1–12 represent the 12 principles of green membrane materials and processes. Refer to the ESI† for the details of the survey. | |
4 Key membrane contributions to a sustainable future
According to the Brundtland report,34 sustainability has three main pillars: social, environmental, and economic. Membrane science and technology considerably contributes to these pillars (Fig. 4). The UN-SDGs also support these pillars by addressing global challenges for a sustainable, conscious world by 2030. The UN-SDGs provide a comprehensive framework to tackle interconnected issues, and membranes have a pivotal role in addressing many of these issues.
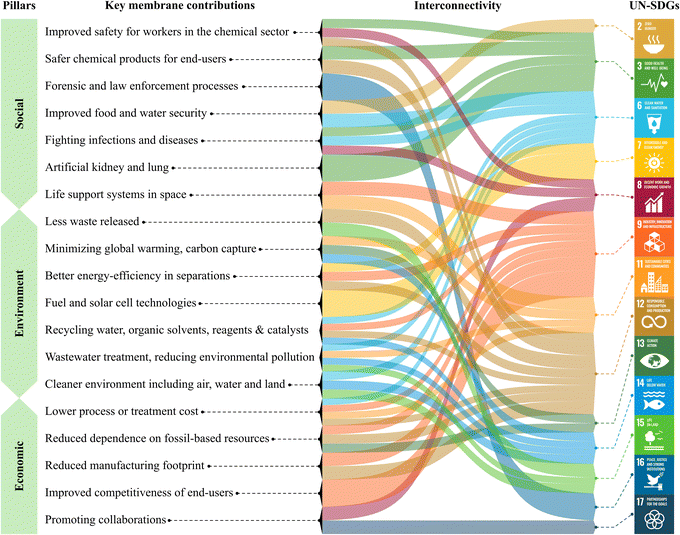 |
| Fig. 4 Mapping the potential contribution and benefits of green membrane science and technology to the United Nations' sustainable development goals, which are categorized based on the three pillars of sustainability: social, environmental, and economic. | |
4.1 Contributions to the social pillar
Membranes play a crucial role in providing access to clean water, which is a fundamental human right, by facilitating water purification and desalination processes. This ensures that communities have a sustainable and reliable source of safe drinking water and improves public health and well-being. Owing to the ambient operating conditions and use of closed-loop systems, membrane processes are often associated with improved safety for workers in the chemical sector. Membrane purification processes yield safer chemical products without toxic or hazardous impurities for end users. Membranes are widely used in forensic and law enforcement processes such as extracorporeal membrane oxygenation, fingerprint analysis, and synthetic skins. They separate, concentrate, and analyze biological samples, including DNA and proteins, thereby contributing to the investigation and resolution of criminal cases. Membranes play a crucial role in food and water security and support the growing population. Membranes with antiviral and antimicrobial properties are used in masks and for water and air filtration. Artificial kidneys and lungs are both specialized membranes that save lives. Current research directions also include membrane-based life support systems for space applications.
4.2 Contributions to the environmental pillar
Membrane-based technologies reduce the environmental footprint by offering more energy-efficient and environmentally friendly separation processes compared to traditional methods. Membrane filtration helps reduce pollution, protect ecosystems, and conserve resources by enabling the efficient recovery of valuable materials from industrial processes. They hold promise in minimizing global warming via carbon capture from industrial flue gases or even through direct air capture. Membranes are becoming integral parts of fuel cell and solar cell technologies. Moreover, they reduce environmental burden by recycling spent water, organic solvents, reagents, and catalysts.
4.3 Contributions to the economic pillar
Membrane technology promotes sustainable development by enhancing resource efficiency, reducing operational costs and waste generation, and fostering innovation in various industries. It offers lower process or treatment costs and a reduced manufacturing footprint. By maximizing the efficiency and integration of renewable energy systems, membranes can reduce dependence on fossil-based resources. Although the research and development phase for membrane science and technology is cumbersome, it can offer improved competitiveness for end users, while promoting collaborations.
The interconnectivity of the key membrane contributions to the three pillars of sustainability with the UN-SDGs is shown in Fig. 4. Membrane science and technology offers diverse tools to address these global challenges. This innovative technology, with its ability to harness the power of selective permeability, can address pressing global issues. Membranes have immense potential to revolutionize industries and mitigate the impact of climate change. Embracing these advancements not only signifies a commitment to environmental stewardship but also represents an investment in a brighter, more sustainable future for generations to come. Through the lens of membranes, we glimpse a world where challenges transform into opportunities and where innovation paves the way for a sustainable future. This is my call to action, urging scientists, engineers, and practitioners to embark on a journey of discovery, ingenuity, and collaboration—a journey that promises a sustainable and thriving planet(s) for the next generations.
5 Conclusions and future directions
The 12 principles of green membrane materials and processes offer a targeted and strategic approach for enhancing sustainability in the field of membrane science and technology and its application areas from underwater to space. These newly introduced principles have their limitations. These are not set in stone but were crafted to encourage researchers, engineers, and industry leaders to adopt sustainably responsible practices in membrane material and process development. By adhering to these principles, we can drive innovation, protect the environment, and contribute to a sustainable future where membrane materials play a pivotal role in mitigating global challenges. We can revolutionize membrane science and technology and propel it toward a greener and more eco-conscious era. Herein, the end-of-life scenarios for membranes were discussed and a membrane waste management hierarchy system was proposed. The spectra of potential contributions and benefits of green membrane science and technology to the UN-SDGs were discussed. These contributions were categorized based on the three pillars of sustainability. A survey revealed that the three top most-important areas of research for membrane materials are end-of-life treatments, wastewater generation minimization, and reproducibility assurance, and those for membrane processes are automation, in-line analytics, and machine learning.
Conflicts of interest
The author declares no conflict of interest.
Acknowledgements
The author thanks the survey participants from the membrane community who took the time to contribute and provide feedback. A special thanks goes to Gergo Ignacz for helping with data visualization. The research reported in this publication was supported by the funding received from the King Abdullah University of Science and Technology (KAUST).
References
-
P. T. Anastas and J. C. Warner, Green Chemistry: Theory and Practice, Oxford University Press, New York, 1998 Search PubMed
.
- P. T. Anastas and J. B. Zimmerman, Design through the Twelve Principles of Green Engineering, Environ. Sci. Technol., 2003, 37, 94A–101A, DOI:10.1021/es032373g
.
- M. Abraham and N. Nguyen, Green engineering: defining principles – results from the Sandestin conference, Environ. Prog., 2004, 22, 233–236, DOI:10.1002/ep.670220410
.
- F. Prézélus, D. Chabni, L. Barna, C. Guigui and J.-C. Remigy, A metrics-based approach to preparing sustainable membranes: application to ultrafiltration, Green Chem., 2019, 21, 4457–4469, 10.1039/C9GC01178A
.
- S.-H. Park, A. Alammar, Z. Fulop, B. A. Pulido, S. P. Nunes and G. Szekely, Hydrophobic thin film composite nanofiltration membranes derived solely from sustainable sources, Green Chem., 2021, 23, 1175–1184, 10.1039/D0GC03226C
.
- C. Yang, J. Cavalcante, B. Freitas, K. J. Lauersen and G. Szekely, Crude algal biomass for the generation of thin-film composite solvent-resistant nanofiltration membranes, Chem. Eng. J., 2023, 470, 144153, DOI:10.1016/j.cej.2023.144153
.
- X. Lu and M. Elimelech, Fabrication of desalination membranes by interfacial polymerization: history, current efforts, and future directions, Chem. Soc. Rev., 2021, 50, 6290–6307, 10.1039/D0CS00502A
.
- A. Iulianelli and E. Drioli, Membrane engineering: latest advancements in gas separation and pre-treatment processes, petrochemical industry and refinery, and future perspectives in emerging applications, Fuel Process. Technol., 2020, 206, 106464, DOI:10.1016/j.fuproc.2020.106464
.
- G. Szekely, M. F. Jimenez-Solomon, P. Marchetti, J. F. Kim and A. G. Livingston, Sustainability Assessment of Organic Solvent Nanofiltration: from Fabrication to Application, Green Chem., 2014, 16, 4440–4473, 10.1039/C4GC00701H
.
- B. A. Sharkh, A. A. Al-Amoudi, M. Farooque, C. M. Fellows, S. Ihm, S. Lee, S. Li and N. Voutchkov, Seawater desalination concentrate—a new frontier for sustainable mining of valuable minerals, npj Clean Water, 2022, 5, 9, DOI:10.1038/s41545-022-00153-6
.
- Y. Zhou, F. Fan, Y. Liu, S. Zhao, Q. Xu, S. Wang, D. Lu and Y. Long, Unconventional smart windows: materials, structures and designs, Nano Energy, 2021, 90, 106613, DOI:10.1016/j.nanoen.2021.106613
.
- G. Tian, Y. Fan, M. Gao, H. Wang, H. Zheng, J. Liu and C. Liu, Indoor thermal environment of thin membrane structure buildings: a review, Energy Build., 2021, 234, 110704, DOI:10.1016/j.enbuild.2020.110704
.
- V. G. Snider and C. L. Hill, Functionalized reactive polymers for the removal of chemical warfare agents: a review, J. Hazard. Mater., 2023, 442, 130015, DOI:10.1016/j.jhazmat.2022.130015
.
- W. Zhou, J. Yu and S. Zhang, Environmentally friendly waterproof and breathable membranes via electrospinning, J. Text. Inst., 2023, 115, 504–526, DOI:10.1080/00405000.2023.2201061
.
- G. Chen, A. Feldhoff, A. Weidenkaff, C. Li, S. Liu, X. Zhu, J. Sunarso, K. Huang, X.-Y. Wu, A. F. Ghoniem, W. Yang, J. Xue, H. Wang, Z. Shao, J. H. Duffy, K. S. Brinkman, X. Tan, Y. Zhang, H. Jiang, R. Costa, K. A. Friedrich and R. Kriegel, Roadmap for Sustainable Mixed Ionic-Electronic Conducting Membranes, Adv. Funct. Mater., 2023, 32, 2105702, DOI:10.1002/adfm.202105702
.
- C. V. Pyl, K. Dalzell, K. Menking-Hoggatt, T. Ledergerber, L. Arroyo and T. Trejos, Transfer and persistence studies of inorganic and organic gunshot residues using synthetic skin membranes, Food Chem., 2023, 34, 100498, DOI:10.1016/j.forc.2023.100498
.
- A. J. Layman and P. T. Lin, Extracorporeal membrane oxygenation in the forensic setting: a series of 19 forensic cases, J. Forensic Sci., 2022, 67, 243–250, DOI:10.1111/1556-4029.14918
.
- P. Aprile, D. Letourneur and T. Simon-Yarza, Membranes for Guided Bone Regeneration: A Road from Bench to Bedside, Adv. Healthcare Mater., 2020, 9, 2000707, DOI:10.1002/adhm.202000707
.
- P. Bernardo, A. Iulianelli, F. Macedonio and E. Drioli, Membrane technologies for space engineering, J. Membr. Sci., 2021, 626, 119177, DOI:10.1016/j.memsci.2021.119177
.
- W. Xie, T. Li, A. Tiraferri, E. Drioli, A. Figoli, J. C. Crittenden and B. Liu, Toward the Next Generation of Sustainable Membranes from Green Chemistry Principles, ACS Sustain. Chem. Eng., 2021, 9(1), 50–75, DOI:10.1021/acssuschemeng.0c07119
.
- S. P. Nunes, Z. Culfaz-Emecen, G. Z. Ramon, T. Visser, G. H. Koops, W. Jin and M. Ulbricht, Thinking the future of membranes: perspectives for advanced and new membrane materials and manufacturing processes, J. Membr. Sci., 2020, 598, 117761, DOI:10.1016/j.memsci.2019.117761
.
- H. A. Le Phuong, C. F. Blanford and G. Szekely, Reporting the unreported: the reliability and comparability of the literature on organic solvent nanofiltration, Green Chem., 2020, 22, 3397–3409, 10.1039/D0GC00775G
.
- J. Chen, R. Dai and Z. Wang, Closing the loop of membranes by recycling end-of-life membranes: comparative life cycle assessment and economic analysis, Resour., Conserv. Recycl., 2023, 198, 107153, DOI:10.1016/j.resconrec.2023.107153
.
- B. Li, S. Wang, X. J. Loh, Z. Li and T.-S. Chung, Closed-loop recyclable membranes enabled by covalent adaptable networks for water purification, Proc. Natl. Acad. Sci. U. S. A., 2023, 120, 2301009120, DOI:10.1073/pnas.2301009120
.
- R. Hardian, R. M. Cywar, E. Y.-X. Chen and G. Szekely, Sustainable nanofiltration membranes based on biosourced fully recyclable polyesters and green solvents, J. Membr. Sci. Lett., 2022, 2, 100016, DOI:10.1016/j.memlet.2022.100016
.
- G. Ignacz, A. K. Beke and G. Szekely, Data-driven future for nanofiltration: Escaping linearity, J. Membr. Sci. Lett., 2023, 3, 100040, DOI:10.1016/j.memlet.2023.100040
.
- C. F. Galinha and J. G. Crespo, From Black Box to Machine Learning: A Journey through Membrane Process Modelling, Membranes, 2021, 11, 574, DOI:10.3390/membranes11080574
.
- B. Addis, C. Castel, A. Macali, R. Misener and V. Piccialli, Data augmentation driven by optimization for membrane separation process synthesis, Comput. Chem. Eng., 2023, 177, 108342, DOI:10.1016/j.compchemeng.2023.108342
.
- C. Ye, V. S. D. Voet, R. Folkersma and K. Loos, Robust Superamphiphilic Membrane with a Closed-Loop Life Cycle, Adv. Mater., 2021, 33, 2008460, DOI:10.1002/adma.202008460
.
- R. Hardian, R. M. Cywar, E. Y.-X. Chen and G. Szekely, Sustainable nanofiltration membranes based on biosourced fully recyclable polyesters and green solvents, J. Membr. Sci. Lett., 2022, 2, 100016, DOI:10.1016/j.memlet.2022.100016
.
-
V. V. Teplyakov, M. G. Shalygin, D. A. Syrtsova and A. I. Netrusov, Membrane Gas Separation Combined with Renewable Energy Systems, Current Trends and Future Developments on (Bio-) Membranes: Renewable Energy Integrated with Membrane Operations, ed. A. Basile, A. Cassano and A. Figoli, Elsevier, 2019, ch. 13, pp. 319–354, DOI:10.1016/B978-0-12-813545-7.00013-1
.
- A. Ali, R. A. Tufa, F. Macedonio, E. Curcio and E. Drioli, Membrane technology in renewable-energy-driven desalination, Renewable Sustainable Energy Rev., 2018, 81, 1–21, DOI:10.1016/j.rser.2017.07.047
.
- M. G. Buonomenna and J. Bae, Membrane processes and renewable energies, Renewable Sustainable Energy Rev., 2015, 43, 1343–1398, DOI:10.1016/j.rser.2014.11.091
.
-
https://sustainabledevelopment.un.org/content/documents/5987our-common-future.pdf, accessed on, 3rd December, 2023.
|
This journal is © The Royal Society of Chemistry 2024 |
Click here to see how this site uses Cookies. View our privacy policy here.