DOI:
10.1039/D3NH00178D
(Communication)
Nanoscale Horiz., 2023,
8, 1217-1225
Facile synthesis of high-entropy alloy nanoparticles on germanane, Ge nanoparticles and wafers†
Received
9th May 2023
, Accepted 26th June 2023
First published on 27th June 2023
Abstract
The unique solid-solution structure and multi-element compositions of high-entropy alloy nanoparticles (HEA NPs) have garnered substantial attention. Various methods have been developed to prepare a diverse array of HEA NPs using different substrates for support and stabilization. In this study, we present a facile surface-mediated reduction method to prepare HEA NPs (AuAgCuPdPt) decorated germanane (HEA NPs@GeNSs), and employ X-ray diffraction (XRD), Fourier-transform infrared spectroscopy (FTIR), X-ray photoelectron spectroscopy (XPS), and transmission electron microscopy (TEM) to characterize their structure, composition, and morphology. Subsequently, we demonstrate that the HEA NPs can be liberated from the surfaces of GeNSs as freestanding systems via straightforward exposure to UV light. We also explore germanium nanoparticles (GeNPs) as an alternative substrate for HEA NP formation/production, given their similarity to germanane and their Ge–H surface. Finally, we extend our investigation to bulk Ge wafers and demonstrate successful deposition of HEA NPs.
New concepts
We present the deposition of high-entropy alloy nanoparticles (HEA NPs) onto the surfaces of germanane, germanium nanoparticles (GeNPs) and bulk Ge via a surface-mediated reduction. Prior to this contribution, the synthesis of HEA NPs with the elemental composition of AuAgCuPdPt had been achieved using cryo-milling which is a top-down approach. Drawing inspiration from our previous report involving monometallic nanomaterial deposition on GeNSs, we demonstrate the deposition of HEA NPs onto germanane surfaces. After deposition, we successfully liberate freestanding HEA NPs from the GeNSs via UV light irradiation and show that the resulting NPs maintain their single-phase solid solution structure after liberation. Additionally, we investigate the generality of our approach and evaluate other Ge-based substrates as platforms for HEA NP formation and found that hydrogen-terminated Ge nanoparticles and Ge (100) wafers performed similarly. Overall, this work provides promising results in the field of nanomaterial deposition on germanium-based substrates and opens new avenues for the development of high-performance catalysts and electronic devices.
|
Introduction
The preparation and application of high-entropy alloy nanoparticles (HEA NPs) have emerged as an intriguing area of research.1 The vast attention being paid to these materials arises, in part, because they possess complex multi-element compositions and unique high-entropy solid-solution structures that provide exquisitely tunable reactivity and enhanced stability that are particularly attractive for catalyst design.2 The initial breakthrough in the general synthesis of HEA NPs that exhibit a wide compositional range (including many immiscible combinations) and large numbers of constituent elements (up to eight), was realized via the “carbo-thermal shock” method.3 Subsequently, a variety of other synthesis procedures have emerged, including vapor phase spark discharge, rapid radiative heating or annealing, low-temperature hydrogen spillover, and microwave heating.4–8 Many of these methods require specialized and costly infrastructure, and facile solution-based methods remain few in number.9 To date, a variety of substrates (e.g., carbon nanosheets,10 carbon nanofibers,11 graphene,12 TiO2,7 MoS213) have been demonstrated as promising supports for HEA NPs, revealing enhanced stability and catalytic performance. Notably, germanium-based materials have yet to be explored as a potential support for HEA NPs.
Germanane (GeNSs) is a 2-dimensional semiconductor that shares similarities with graphene; its atoms are arranged in a structure that closely resembles that of the (100) surfaces of hydrogen-terminated Ge.14 This material possesses an optical band gap ranging from 1.4–1.7 eV that depends on surface chemistry,15 and it has been successfully integrated into prototype devices, such as transistors and Li-ion batteries.16,17 The use of metal heterostructures containing GeNSs and other 2D semiconductors, such as Si-doped GeNSs, presents new opportunities due to their unique optical and electronic properties.18 For example, coupling the reactivity of metals with the optical properties of graphene has lead to photocatalysts capable of water splitting,19 while interfacing plasmonic metal nanoparticles with the electronic properties of GeNSs could yield materials with potential applications in solar energy conversion, photodetection, and sensing. To date, investigation of GeNSs–metal heterostructures has been limited, in part, because there are limited examples of methods that provide these emerging materials.20
Recently, we reported the preparation of metal nanoparticle-decorated germanane (M@GeNSs) via a solution-based method and demonstrated their reactivity in the selective photocatalytic aerobic oxidation of benzyl alcohol.21 This success led us to investigate the possibility of depositing high-entropy alloy nanoparticles (HEA NPs) onto germanane surfaces using a variation of our surface-mediated reduction method. Previous syntheses of HEA NPs with an elemental composition of AuAgCuPdPt have been limited to a top-down approach utilizing cryo-milling.22 Drawing inspiration from our previous report involving monometallic nanomaterial deposition on GeNSs, here we demonstrate the deposition of HEA NPs (AuAgCuPdPt) onto GeNSs surfaces (Scheme 1). Subsequent to deposition, we successfully liberate freestanding HEA NPs from the GeNSs via UV light irradiation and demonstrate the resulting NPs maintain their single-phase solid solution structure. With these promising results in hand, we explore the scope of various Ge-based substrates as platforms for growing HEA NPs. Knowing germanium nanoparticles (GeNPs) exhibit similar Ge–H surface moieties and that they are readily prepared,23 we also investigate these materials as reducing substrates for HEA NP growth. We conclude this study by extending our method to hydrogen-terminated Ge (100) wafers.
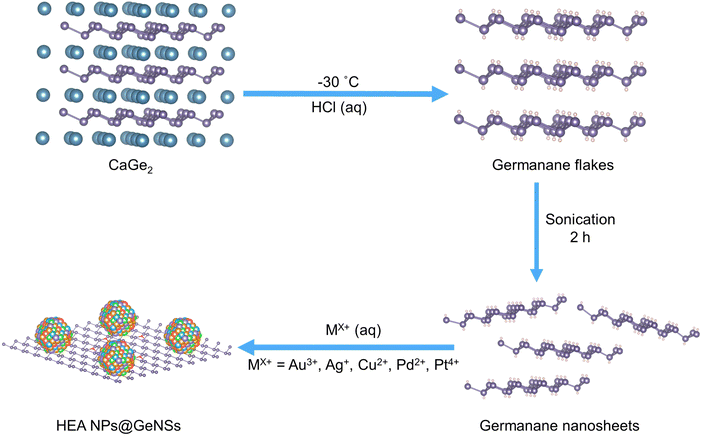 |
| Scheme 1 A pictorial representation of the formation of high-entropy nanoparticles on germanane. Germanane flakes were prepared via topotactic deintercalation of calcium ions from CaGe2. The flakes were subsequently sonicated in Milli-Q water for 2 h to obtain germanane nanosheets. An aqueous solution containing metal salts (i.e., AuCl3, AgNO3, CuCl2, PdCl2, and PtCl4) was added into the aqueous suspension of germanane nanosheets. Metal ions are reduced and deposited onto the germanane surfaces forming HEA NPs with the evolution of bubbles presumably comprising hydrogen. | |
Materials preparation and characterization
Germanane used in this study was prepared via topotactic deintercalation of calcium digermanide (Scheme 1).24 The resulting product was sonicated in water for 2 h to maximize exfoliation. Suspensions of GeNSs were then combined with an aqueous solution containing the metal salts of choice (i.e., AuCl3, AgNO3, CuCl2, PdCl2, PtCl4). Upon adding a solution of mixed metal salts to the GeNSs suspension, the Ge–H moieties on the GeNSs surfaces immediately reacted with the aqueous metal ions resulting in the deposition of size-polydisperse HEA NPs (AuAgCuPdPt) onto the GeNSs surfaces. This process was accompanied by the evolution of bubbles (presumably hydrogen) and a color change from red to black (Fig. S1, ESI†).
Powder X-ray diffraction (XRD) was used to interrogate the HEA NPs deposited on the GeNSs (HEA NPs@GeNSs) and reveals their crystal structure. The XRD pattern of HEA NPs@GeNSs showed reflections characteristic of the GeNSs, as well as reflections arising from the nanoparticles. The HEA NP related features are weak and broad due to their small crystallite size (Fig. S2a, ESI†). The reflection appearing in the range of 38°–41° (Fig. S2b, ESI†) corresponds to the (111) reflections of the single-phase solid solution HEA particles consistent with typical patterns reported for AuAgCuPdPt HEA NPs.25 Evaluation of the peak broadening of this reflection was performed using the Scherrer equation after considering the effects of instrumental broadening (Fig. S3a, ESI†); this analysis provided approximate crystallite size of 5.5 nm when taking into account peak broadening arising from decreased size (Fig. S3b, ESI†).26 These results are consistent with the successful deposition of HEA NPs while retaining the GeNSs structure. Synchrotron XRD analysis (Fig. S4, ESI†) showed a pattern with improved signal-to-noise ratio along with intense characteristic GeNSs reflections27 superimposed on the broad peak at 10.1° relating to the lattice parameter of 4.0607(3) Å.
To further investigate the nature of the HEA NPs@GeNSs, we evaluated the materials using Fourier-transform infrared (FTIR) and X-ray photoelectron (XPS) spectroscopies. The FTIR spectrum (Fig. S5, ESI†) of the parent GeNSs showed intense features associated with Ge–H stretching (2000 cm−1) and bending modes (830 cm−1 and 770 cm−1).28 Following deposition of the HEA NPs, the FTIR spectrum of HEA NPs@GeNSs displayed a prominent feature in the range of 700 to 890 cm−1 that we attribute to Ge–O vibrations.29 We also observed that the intensities of Ge–H associated features diminished, although they were still obvious. Our observations are similar to previous reports for metal-decorated germanane21 and silicane,30 and are consistent with the surface hydride functionalities reducing the metal ions, leaving surface dangling bonds on the GeNSs that are subsequently oxidized to form Ge–O–Ge and Ge–O–H moieties.
XPS provides additional information regarding composition, bonding environment, and oxidation states of elements in the presented materials. The survey XP spectrum of the HEA NPs@GeNSs was consistent with the FTIR and XRD analyses, showing evidence of oxidation and corresponding metal emissions (Fig. S6, ESI†). The metal compositions of the HEA NPs@GeNSs were calculated based upon the XP survey spectra integration, and the atomic percentage of each metal was approximately 2%, suggesting a homogeneous alloy (Table S1, ESI†).
The high-resolution XP spectra of HEA NPs@GeNSs showed emissions associated with the corresponding metal (i.e., Au, Ag, Cu, Pd, and Pt) deposits and the underlying GeNSs (Fig. S7, ESI†). The Ge 3d spectra were fitted to reveal a binding energy of 29.8 eV, which has been previously attributed to Ge in the nanosheets.26 We also note components appearing at 31.3 and 32.5 eV that have previously been attributed to Ge2+ and Ge4+ species, respectively (Fig. S7a, ESI†).24 The high resolution XP spectra of each metal (Fig. S7b–f, ESI†) show emissions at binding energies characteristic of the corresponding metallic state (i.e., Au 4f7/2, 83.9 eV; Ag 3d5/2, 367.9 eV; Cu 2p3/2, 932.5 eV; Pd 3d5/2, 335.2 eV; Pt 4f7/2, 71.0 eV).
Electron microscopy was used to study the nano-morphology of HEA NPs@GeNSs. High-resolution transmission electron microscopy (HRTEM) images confirm the deposition of nanocrystalline HEA NPs onto the GeNSs surfaces (Fig. 1), while brightfield TEM reveals the deposited metal nanoparticles are pseudospherical with dimensions 5.6 nm (Fig. S8, ESI†).31 High-angle annular dark-field scanning transmission electron microscopy (HAADF-STEM) (Fig. 1b) shows HEA NPs@GeNS morphologies consistent with brightfield imaging and energy dispersive X-ray (EDX) mapping confirms the co-localization of all metals in the morphological features in darkfield and HAADF-STEM (Fig. 1c–i). The EDX spectrum (Fig. S9, ESI†) provides signatures for Ge (i.e., ca. 15 atom%) and other five target metals (i.e., ca. 1.5 atom%). Taken together, and consistent with the XPS analysis, these data support our conclusion that the alloy is homogeneous and not subject to obvious surface segregation or phase separation.
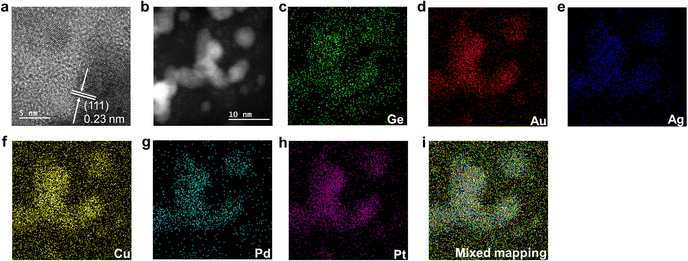 |
| Fig. 1 TEM and EDX analysis of HEA NPs@GeNSs. (a) High-resolution image showing characteristic metal (111) lattice spacing. (b) HAADF-STEM image and (c–i) corresponding EDX mapping of the indicated elements. | |
Liberation of HEA NPs
We also investigated the liberation of HEA NPs from GeNSs by exposing HEA NPs@GeNSs to UV light (Scheme 2). Upon exposure to UV light, the GeNSs were destroyed and the liberated HEA NPs were collected by centrifugation. Consistent with liberation, powder XRD showed no reflections associated with the GeNSs. In addition, the XRD data (Fig. S10a, ESI†) indicates the HEA NPs display a characteristic face-centred cubic structure as evidence by (111), (200), and (220) reflections appearing at 39.3°, 45.9°, and 66.3°, respectively. Further analysis of these broadened features using the Scherrer equation provided an estimated crystallite size of 6.1 nm (Fig. S10, ESI†). After considering the dependence of peak broadening on diffraction angle, the broadening distribution of the HEA NPs (Fig. S11, ESI†) shows, not unexpectedly that there is also strain-induced effects.
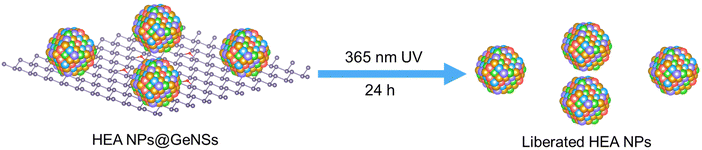 |
| Scheme 2 A pictorial illustration of the liberation of high-entropy nanoparticles from germanane. | |
XPS was used to gain further information about the composition and the oxidation states of the constituent elements that make up the HEA NPs. The survey spectrum (Fig. S12, ESI†) revealed trace amounts of Ge (i.e., 1.72 atom%), O (i.e., 19.5 atom%) and mainly consisted of the five metal components (i.e., 14.0 atom% for each metal) in consistent with the XRD results. Not surprisingly, fitting the Ge 3d spectrum provided the components at 31.3 and 32.5 eV that are attributed to the residual oxidized Ge species.24 The XP spectra of each metal (Fig. S13, ESI†) showed emissions at binding energies characteristic of the corresponding metallic state (i.e., Au 4f7/2, 83.7 eV; Ag 3d5/2, 367.8 eV; Cu 2p3/2, 932.4 eV; Pd 3d5/2, 335.1 eV; Pt 4f7/2, 70.9 eV). However, they also showed varying degrees of oxidation, as the decomposition of GeNSs exposed more of the HEA NP surface leading to some oxidation during liberation.
The morphology of the HEA NPs liberated from the GeNSs was evaluated using TEM. The HAADF-STEM imaging (Fig. S14a, ESI†) revealed spherical HEA NPs. The size of the HEA NPs after liberation was found to be 5.9 ± 1.8 nm, consistent with the preliberation dimensions. EDX mapping (Fig. S15, ESI†) provided evidence of the co-localization of morphological features in HAADF-STEM images and confirmed the presence of the five target metals. The EDX spectrum (Fig. S16, ESI†) showed a negligible Ge signal (i.e., 0.05 atom%) and metal signals (i.e., ca. 15 atom%), indicating the successful liberation of the HEA NPs.
Synthesis of HEA NPs@GeNPs
Having demonstrated the feasibility of using GeNSs as a multipurpose reducing agent and substrate for the growth of high-entropy alloy nanoparticles (HEA NPs) we endeavored to explore the scope of Ge substrates that could do the same. We first turned our attention to H-terminated germanium nanoparticles (H-GeNPs) that were prepared via thermal disproportionation of ‘Ge(OH)2’ followed by removal of the encapsulating oxide via aqueous HF etching.23 Upon addition of the mixed metal ion solution previously used for HEA NP deposition on GeNSs, the Ge–H moieties on the GeNP surfaces facilitated the immediate reduction of metal ions and with deposition of size-polydisperse HEA NPs (AuAgCuPdPt) onto the GeNP surfaces (Scheme 3). As expected, this process was also accompanied by the evolution of bubbles (Fig. S17, ESI†).
 |
| Scheme 3 A pictorial illustration of the formation of high-entropy nanoparticles on GeNPs. GeNPs were prepared via thermal disproportion of ‘Ge(OH)2’. The GeNPs/GeO2 were subsequently etched in the 25% HF for 1 h to remove the oxide. The mixed aqueous solution of metal salts (i.e., AuCl3, AgNO3, CuCl2, PdCl2, and PtCl4) was added into the aqueous suspension of GeNPs. Metal ions were reduced and deposited onto the germanane surfaces forming HEA NPs. | |
The HEA NPs@GeNPs were characterized using XRD and FTIR spectroscopy to investigate their crystal structure and bonding. The obtained HEA NPs@GeNPs possessed a single-phase solid solution crystal structure, as evidenced by the characteristic reflections of GeNP superimposed on a weak and broad peak within the 38°–41° range (Fig. S18a, ESI†).22 Scherrer analysis provided an estimate of crystallite size of 7.2 nm (Fig. S18b, ESI†). The FTIR spectrum showed a dominant Ge–O vibration feature in the range of 700 to 890 cm−1, while the Ge–H stretching at 2000 cm−1 was diminished (Fig. S19, ESI†),23 indicating that the surface hydride functionalities have reduced metal ions, leaving surface dangling bonds on the GeNPs that subsequently oxidized to form Ge–O–Ge and Ge–O–H moieties. These results are consistent with our previous observations for HEA NPs@GeNSs (vide supra).
XPS was used to investigate the elemental composition and oxidation states of the resulting HEA NPs@GeNPs. The survey spectrum showed the expected metal emissions (approximately 1 atom%) and Ge (24.6 atom%) in the sample (Fig. S20, ESI†). The high-resolution spectra of each metal within HEA NPs@GeNPs exhibited characteristic metallic binding energies (Fig. S21, ESI†), including Au 4f7/2, 84.0 eV; Ag 3d5/2, 367.9 eV; Cu 2p3/2, 932.3 eV; Pd 3d5/2, 335.1 eV; and Pt 4f7/2, 71.0 eV. The Ge 3d region (Fig. S21a, ESI†) provided a binding energy of 29.6 eV, consistent reports for Ge in the nanoparticles.32 Notably, the majority of Ge4+ species were observed at 32.5 eV, while some Ge2+ species were noted as evidenced by a feature at 31.7 eV. This observation suggests that the agglomeration of GeNPs during the reaction increased the likelihood of forming Ge–O–Ge bonds in the HEA NPs@GeNPs, resulting in a higher prevalence of Ge4+ species.
The morphology of HEA NPs@GeNPs was examined using a HAADF-STEM image (Fig. 2a). The size of the deposited HEA NPs, as measured in the brightfield image (Fig. S22, ESI†), was 6.8 ± 2.0 nm in agreement with Scherrer analysis of the corresponding XRD pattern.31 EDX mapping (Fig. 2b–i) is consistent with the deposited alloy nanoparticles being homogenous and the GeNP substrate was partially oxidized, consistent with the FTIR and XPS results. The EDX spectrum (Fig. S23, ESI†) further indicated an elemental composition of Au (1.6 atom%), Ag (1.5 atom%), Cu (1.3 atom%), Pd (1.1 atom%), and Pt (1.4 atom%) which agrees with the chemical composition determined by XPS.
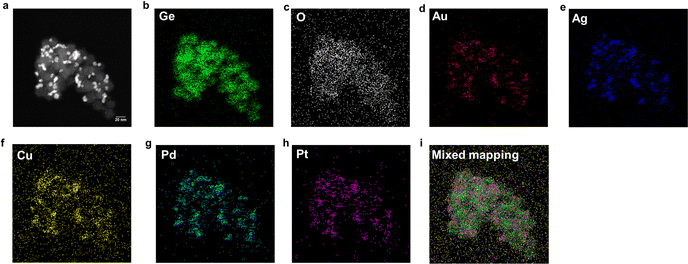 |
| Fig. 2 STEM and EDX analysis of HEA NPs@GeNPs. (a) HAADF-STEM image and (b–i) corresponding EDX mapping of the indicated elements. | |
Synthesis of HEA NPs by bulk Ge
Finally, we look to a bulk Ge wafer to explore the universality of our approach toward preparing HEA NPs. A precleaned Ge (100) wafer was immersed in a solution containing a predefined mixture of metal salts for 10 minutes. Doing so resulted in the deposition of HEA NPs on the Ge surface (Fig. S24a, ESI†). The solid solution structure of the deposited HEA NPs was characterized using powder XRD (Fig. S24b, ESI†) and showed a diminished intensity of the preferential reflection (100) at 67°, suggesting the crystallinity of Ge (100) decreased due to the deposition, and a broad reflection in the range of 38°–41°. The HEA NPs had a crystalline domain size of 35.3 nm, as determined by the Scherrer equation. SEM imaging showed the deposited HEA NPs had an average size of 32.4 ± 7.3 nm on the surface of the Ge wafer, with no obvious evidence of localized substrate etching observed (Fig. S25, ESI†). SEM/EDX measurement (Fig. S26 and S27, ESI†) indicated a homogenous distribution of the metal elements, with an atomic composition of Au (4.78 atom%), Ag (3.10 atom%), Cu (3.39 atom%), Pd (3.85 atom%), and Pt (4.64 atom%). For comparison, the chemical composition of the material was investigated by XPS (Fig. S28, ESI†), which revealed a surface atomic ratio of Au (6.53 atom%), Ag (4.97 atom%), Cu (5.39 atom%), Pd (5.79 atom%), Pt (5.64 atom%), and Ge (9.27 atom%). The weaker Ge emission observed in contrast to previous GeNS and GeNP experiments was attributed to the larger size of the deposited HEA NPs, which limited XPS probing to depth. The high-resolution XP spectrum of the Ge 3d region (Fig. S29a, ESI†) showed the presence of Ge1+ (binding energy at 30.3 eV) and Ge4+ (binding energy at 32.5 eV) species,33 indicating that after the removal of the native oxide, the surface Ge undergoes hydrolysis in the water forming Ge–H and Ge–OH on the surface. The generated Ge–H simultaneously reduced the metal ions, resulting in the deposition of the HEA NPs, which is consistent with the SEM images where no obvious local etching was observed. Overall, our study provides new insights into the synthesis and characterization of HEA NPs on the Ge surface and highlights the potential applications of our synthetic method in the bulk Ge system.
Conclusions
We present a facile method for the deposition of adherent high-entropy alloy nanoparticles (AuAgCuPdPt) onto the surfaces of germanium nanosheets (GeNSs). Our investigation confirms the preservation of the structural integrity of the GeNSs during the deposition process and the formation of high-entropy nanoparticles, as verified by X-ray diffraction (XRD) and X-ray photoelectron spectroscopy (XPS). Transmission electron microscopy (TEM) analysis reveals the distribution of the high-entropy alloy nanoparticles over the entire surface of the GeNSs. The subsequent liberation of the nanoparticles from the GeNSs through UV irradiation demonstrated their solid-solution structure and homogenous element distribution. We also demonstrate that HEA NPs can be prepared on the surface of agglomerated GeNPs via a straightforward synthetic route. We concluded by extending our investigation to bulk Ge, where deposition of HEA NPs on the surface of a wafer was demonstrated.
Experimental
Materials
Germanium (Ge, 99.999%), calcium (Ca, 99.0%), gold chloride (AuCl3, 99.99%), silver nitrate (AgNO3, 99.9999%), copper chloride (CuCl2, 99.999%), palladium chloride (PdCl2, 99.9%), platinum chloride (PtCl4, 99.999%) and hypophosphorous acid solution (50 wt% H3PO2 in water) were purchased from Sigma-Aldrich. Sodium hydroxide (NaOH) pellets, ammonium hydroxide (28–30 wt% NH4OH), hydrofluoric acid (electronic grade, 48–50% HF) hydrochloric acid (37 wt%, HCl), ethanol (anhydrous), isopropyl alcohol (anhydrous), acetone (HPLC grade) and toluene (HPLC grade) were purchased from Fisher Scientific. Germanium dioxide (GeO2, 99.99%) was purchased from Gelest. Milli-Q (18.2 MΩ·cm at 25 °C) water was used for all experiments. All organic solvents were dried using an Innovative Technology, Inc. Grubbs-type solvent purification system.
Synthesis of CaGe2
A stoichiometric mixture of calcium and germanium metals was pressed into a pellet and then melted together from both sides using an arc furnace.24
Synthesis of stacked cermanane
Germanane was synthesized via topotactic deintercalation of calcium ions from CaGe2 using a modified literature procedure.26 Briefly, 0.3 g (2.7 mmol) of freshly prepared granular CaGe2 was loaded into Schlenk flask charged with 30 mL of concentrated aqueous HCl that had been cooled to −30 °C. The reaction mixture was maintained at −30 °C for at least 7 days with regular agitation. The resulting grey flakes exhibited a metallic sheen and were filtered using a glass frit under nitrogen. The flakes were washed three times with ice-cold Milli-Q water and anhydrous ethanol before being dried in vacuo on the Schlenk line. The resulting shiny grey solid was stored in a nitrogen-filled glovebox under subdued light until further use.
Preparation of high-entropy nanoparticles-decorated germanium nanosheets (HEA NPs@GeNSs)
To prepare high entropy alloy nanoparticles-decorated germanium nanosheets (HEA NPs@GeNSs; HEA NPs = Au, Ag, Cu, Pt, Pd), germanane powder (73 mg; 1 mmol) was dispersed in 4 mL Milli-Q water. The mixture was sonicated in a bath sonicator for 2 hours to yield a red suspension of exfoliated GeNSs. Subsequently, an appropriate amount (0.01 mmol) of the anhydrous metal salt in question (AuCl3, AgNO3, CuCl2, PdCl2 and PtCl4) was dissolved in 1 mL of Milli-Q water together. The mixed metal salts solution (i.e., 0.1 mL) was added into the GeNS dispersion at room temperature under subdued light, resulting in a change of color from red to black. The mixture was stirred for 10 min, and the product was recovered by centrifugation and washed with Milli-Q water three times. The product was then dried for 12 hours under vacuum and subsequently stored in a nitrogen-filled glovebox under subdued light. Typical mass yields for this procedure were 55 mg. The resulting material was characterized using XRD, XPS, and TEM.
Liberation of high-entropy nanoparticles (HEA NPs)
To liberate the HEA NPs from the HEA NPs@GeNSs, HEA NPs@GeNSs powder (100 mg) was dispersed in 5 mL of Milli-Q water. The suspension was stirred and irradiated with a 360 nm UV LED light source for 24 h under a N2 atmosphere. After decomposition, the product was washed and centrifuged with 3 mL of Milli-Q water three time. The resulting product was then dried for 12 hours under vacuum and subsequently stored in a nitrogen-filled glovebox in subdued light.
Synthesis of germanium hydroxide
Germanium hydroxide was prepared using a modified literature synthesis.23 GeO2 (5 g) was added to a solution of 25 g NaOH in 35 mL of water in a 250 mL round-bottom flask and stirred until the white powder is dissolved. The mixture was then acidified slowly to pH 1 using an 80 mL solution of water and concentrated HCl (1
:
1), followed by the addition of 35 mL of hypophosphorous acid in water (50 wt% H3PO2). The mixture was refluxed at 120 °C for 4 hours under flowing Ar. The reaction was allowed to cool to 90 °C before adding 50 mL of NH4OH slowly through the condenser, which precipitated brown Ge(OH)2 out of solution. Caution! The reaction with ammonium hydroxide is very exothermic. The brown precipitate was collected by vacuum filtration and purified by twice re-dispersing and stirring in 300 mL of water. After the final collection by vacuum filtration, the brown-orange product was allowed to dry overnight on a double manifold vacuum.
Synthesis of germanium nanoparticles
Brown Ge(OH)2 powder was placed in a quartz boat and loaded into a Thermofisher Lindberg/Blue M tube furnace equipped with a quartz tube. The tube was charged with flowing argon gas (10 cm3 s−1) and the furnace was ramped to 400 °C at a rate of 5 °C min−1. After holding at the peak temperature for 1 hour, the furnace was cooled naturally to room temperature before collecting the sample, which was then weighed and transferred to a vial for storage. Hydride-terminated germanium nanoparticles were released from the sample through ethanolic hydrofluoric acid (HF) etching, using a modified literature procedure.32 Caution! HF is dangerous; extreme care and compliance with local regulations is required. In a 50 mL Teflon PFA (perflouroalkoxy) beaker, 0.1 g of the composite was dispersed in 6 mL of a mixture of ethanol and water (1
:
1), followed by the addition of 3 mL of concentrated HCl and 2 mL of aqueous (49%) HF. The mixture was stirred for 1 hour before extracting the liberated germanium nanoparticles with toluene into test tubes. The resulting dark brown colloidal solution was subjected to centrifugation at 5000 rpm for 5 minutes to obtain a dark brown pellet. This process was repeated twice more, dispersing the nanoparticle pellet in dry toluene between each centrifugation, and removing the supernatant.
Preparation of high-entropy nanoparticles from germanium nanoparticles (HEA NPs@GeNPs)
To prepare high entropy alloy nanoparticles from germanium nanoparticles (HEA NPs@GeNPs; HEA NPs = Au, Ag, Cu, Pt, Pd), germanium nanoparticles (72 mg; 1 mmol) were dispersed in 4 mL distilled water. Subsequently, a mixed metal salt solution (0.1 mL, 0.01 mmol L−1) was added to the GeNPs dispersion at room temperature, in subdued light, resulting in a color change from brown to black. The mixture was stirred for 10 minutes, and the product was recovered by centrifugation and washed with Milli-Q water three times. The product was then dried for 12 hours under vacuum and stored in a nitrogen-filled glovebox, while being shielded from light. Typical mass yields for this procedure were 50 mg. The resulting material was characterized using XRD, XPS, and TEM.
Preparation of high entropy nanoparticles on germanium wafer
A germanium shard was precleaned with acetone, isopropyl alcohol, and Milli-Q water to remove surface native oxide and dried under a nitrogen stream. Immediately thereafter, the germanium sample was immersed in a 5 mL mixed metal salt solution (0.05 mmol L−1) in a glass vial and kept in the dark for 10 minutes. Subsequently, the shard was carefully removed from the solution and rinsed three times with 5 mL of Milli-Q water. Finally, the shard was dried in a stream of flowing N2 gas and transferred to a nitrogen-filled glovebox, where it was maintained under subdued light.
Characterization.
Electron microscopy
Transmission electron microscopy (TEM) bright and dark field images were acquired using a JEOL JEM-ARM200CF S/TEM electron microscope at an accelerating voltage of 200 kV. High resolution (HR) TEM images were processed using Gatan Digital Micrograph software (Version 3.4.1). TEM samples were prepared by depositing a drop of a dilute toluene suspension of the sample in question onto a holey or ultra-thin carbon coated copper grid (obtained from Electron Microscopy Inc.). The grid bearing the sample was kept in a vacuum chamber at a base pressure of 0.2 bar for at least 24 h prior to data collection. The particle size distribution was assembled as an average shifted histogram as described by Buriak et al. for at least 300 particles in TEM.34
Secondary electron scanning electron microscopy (SEM) images were acquired using a Hitachi S4800 FESEM electron microscope at an accelerating voltage of 25 kV. Samples were mounted on a stainless-steel stub by using a conductive tape.
X-ray photoelectron spectroscopy (XPS)
XPS analyses were performed using a Kratos Axis Ultra instrument operating in energy spectrum mode at 210 W. The base and operating chamber pressure were maintained at 10−7 Pa. A monochromatic Al Kα source (λ = 8.34 Å) was used to irradiate the samples, and the spectra were obtained with an electron take-off angle of 90°. CasaXPS software (VAMAS) was used to interpret high-resolution spectra. All spectra were internally calibrated to the C 1s emission (284.8 eV) of adventitious carbon. After calibration, a Shirley-type background was applied to remove most of the extrinsic loss structure. The Ge 3d region was deconvoluted into the Ge 3d5/2 and 3d3/2 spin–orbit couple for the element Ge and the energy separation of these doublets was fixed at 0.58 eV and the Ge 3d3/2 to 3d5/2 area was fixed at 0.67.24 For the high-resolution XP spectra of metals, the spin–orbit couple energy separation and area were fixed and the spectral envelope was fit using a Lorentzian asymmetric line shape LA(a, b, n) where a and b define the asymmetry and n defines the Gaussian width. The various spectral regions were fit as follows: Au 4f was deconvoluted into the Au 4f7/2 and 4f5/2 spin–orbit couple and the energy separation of these doublets was fixed at 3.70 eV and the Au 4f7/2 to 4f5/2 area ratio was fixed at 0.75.35 Ag 3d was deconvoluted into the Ag 3d5/2 and 3d3/2 spin–orbit couple and the energy separation of these doublets was fixed at 6.00 eV and the Ag 3d3/2 to 3d5/2 area ration was fixed at 0.67.36 Cu 2p was deconvoluted into the Cu 2p3/2 and 2p1/2 spin–orbit couple and the energy separation of these doublets was fixed at 19.75 eV and the Cu 2p3/2 and 2p1/2 area ratio was fixed at 0.50.37 Pd 3d was deconvoluted into the Pd 3d5/2 and 3d3/2 spin–orbit couple and the energy separation of these doublets was fixed at 5.26 eV and the Ag 3d3/2 to 3d5/2 area ratio was fixed at 0.67.38 Pt 4f was deconvoluted into the Pt 4f7/2 and 4f5/2 spin–orbit couple and the energy separation of these doublets was fixed at 3.35 eV and the Pt 4f7/2 to 4f5/2 area ratio was fixed at 0.75.39
Powder X-ray diffraction (XRD) analysis
XRD measurements were conducted on a Bruker D8 Advance diffractometer using Cu-Kα1 (λ = 1.5406 Å) and Kα2 (λ = 1.5444 Å) radiation. Powder samples were mounted on a zero-background Si crystal sample holder and scanned over 2θ ranges of 10–100° with a scan step of 0.0015° s−1. The instrumental broadening effect was considered by measuring a NIST LaB6 standard sample with a same scanning speed. Jade 6 was used to fit the peak broadening with both size and strain effect. Synchrotron diffraction data were collected at the Canadian Light Source, utilizing the Brockhouse high energy wiggler (BXDS-WHE) beamline. The samples were prepared by loading them into polyimide Kapton with an inner diameter of 0.300 mm and outer diameter of 0.350 mm, using a magnetic sample holder in transmission mode. Powder data was collected using a Rayonix MX300HE 2D detector with a detector distance of 496.37 mm. The beam energy was set to 30.3383 keV, and the synchrotron radiation wavelength was calibrated using a LaB6 standard, which was found to be 0.40867 Å. Prior to integration, the background from the empty Kapton was subtracted.
Author contributions
Chuyi Ni: conceptualization, methodology, investigation, formal analysis, investigation, data curation, and writing – original draft. Kevin M. O’Connor: investigation, data creation, and writing – review and editing. Jonathan Trach: investigation, data creation, and writing – review and editing. Cole Butler: investigation, data creation, and writing – review and editing. Bernhard Rieger: supervision, resources, funding acquisition, and writing – review and editing. Jonathan G. C. Veinot: supervision, conceptualization, methodology, formal analysis, investigation, data curation, resources, funding acquisition, and writing – review and editing. All authors discussed the results and the implications of this manuscript. All authors have given approval to the final version of the manuscript.
Conflicts of interest
There are no conflicts to declare.
Acknowledgements
The authors recognize the continued generous funding from the Natural Science and Engineering Research Council (NSERC Discovery Grant program; RGPIN-2020-04045), the ATUMS training program supported by NSERC CREATE (CREATE-463990-2015) as well as the University of Alberta Faculties of Science and Graduate Studies, and Alberta Innovates Strategic Projects Program. We also thank the staff at Analytical and Instrumentation Laboratory in the Department of Chemistry at the University of Alberta for the assistance with FTIR analysis, and the University of Alberta Nanofab for support in collecting XPS data. C. Ni also thank Amelie Mühlbach during the German exchange at TUM.
References
- Y. Yao, Q. Dong, A. Brozena, J. Luo, J. Miao, M. Chi, C. Wang, I. G. Kevrekidis, Z. J. Ren, J. Greeley, G. Wang, A. Anapolsky and L. Hu, Science, 2022, 376 DOI:10.1126/science.abn3103.
- M. W. Glasscott, A. D. Pendergast, S. Goines, A. R. Bishop, A. T. Hoang, C. Renault and J. E. Dick, Nat. Commun., 2019, 10, 2650 CrossRef PubMed.
- Y. Yao, Z. Huang, P. Xie, S. D. Lacey, R. J. Jacob, H. Xie, F. Chen, A. Nie, T. Pu, M. Rehwoldt, D. Yu, M. R. Zachariah, C. Wang, R. Shahbazian-Yassar, J. Li and L. Hu, Science, 2018, 359, 1489–1494 CrossRef CAS PubMed.
- P.-C. Chen, X. Liu, J. L. Hedrick, Z. Xie, S. Wang, Q.-Y. Lin, M. C. Hersam, V. P. Dravid and C. A. Mirkin, Science, 2016, 352, 1565–1569 CrossRef CAS PubMed.
- N. Kumar, C. S. Tiwary and K. Biswas, J. Mater. Sci., 2018, 53, 13411–13423 CrossRef CAS.
- S. Gao, S. Hao, Z. Huang, Y. Yuan, S. Han, L. Lei, X. Zhang, R. Shahbazian-Yassar and J. Lu, Nat. Commun., 2020, 11, 2016 CrossRef CAS PubMed.
- K. Mori, N. Hashimoto, N. Kamiuchi, H. Yoshida, H. Kobayashi and H. Yamashita, Nat. Commun., 2021, 12, 3884 CrossRef CAS PubMed.
- H. Qiao, M. T. Saray, X. Wang, S. Xu, G. Chen, Z. Huang, C. Chen, G. Zhong, Q. Dong, M. Hong, H. Xie, R. Shahbazian-Yassar and L. Hu, ACS Nano, 2021, 15, 14928–14937 CrossRef CAS PubMed.
- D. Wu, K. Kusada, T. Yamamoto, T. Toriyama, S. Matsumura, S. Kawaguchi, Y. Kubota and H. Kitagawa, J. Am. Chem. Soc., 2020, 142, 13833–13838 CrossRef CAS PubMed.
- G. Zhu, Y. Jiang, H. Yang, H. Wang, Y. Fang, L. Wang, M. Xie, P. Qiu and W. Luo, Adv. Mater., 2022, 34, e2110128 CrossRef PubMed.
- Z. Huang, Y. Yao, Z. Pang, Y. Yuan, T. Li, K. He, X. Hu, J. Cheng, W. Yao, Y. Liu, A. Nie, S. Sharifi-Asl, M. Cheng, B. Song, K. Amine, J. Lu, T. Li, L. Hu and R. Shahbazian-Yassar, Nat. Commun., 2020, 11, 6373 CrossRef CAS PubMed.
- M. Y. Rekha, N. Mallik and C. Srivastava, Sci. Rep., 2018, 8, 8737 CrossRef CAS PubMed.
- K. M. B. Urs, N. K. Katiyar, R. Kumar, K. Biswas, A. K. Singh, C. S. Tiwary and V. Kamble, Nanoscale, 2020, 12, 11830–11841 RSC.
- W. L. B. Huey and J. E. Goldberger, Chem. Soc. Rev., 2018, 47, 6201–6223 RSC.
- S. Jiang, K. Krymowski, T. Asel, M. Q. Arguilla, N. D. Cultrara, E. Yanchenko, X. Yang, L. J. Brillson, W. Windl and J. E. Goldberger, Chem. Mater., 2016, 28, 8071–8077 CrossRef CAS.
- A. C. Serino, J. S. Ko, M. T. Yeung, J. J. Schwartz, C. B. Kang, S. H. Tolbert, R. B. Kaner, B. S. Dunn and P. S. Weiss, ACS Nano, 2017, 11, 7995–8001 CrossRef CAS PubMed.
- B. N. Madhushankar, A. Kaverzin, T. Giousis, G. Potsi, D. Gournis, P. Rudolf, G. R. Blake, C. H. van der Wal and B. J. van Wees, 2D Mater., 2017, 4, 021009 CrossRef.
- F. Zhao, Y. Feng, Y. Wang, X. Zhang, X. Liang, Z. Li, F. Zhang, T. Wang, J. Gong and W. Feng, Nat. Commun., 2020, 11, 1443 CrossRef CAS PubMed.
- L. H. Chen, H. T. Shen, W. H. Chang, I. Khalil, S. Y. Liao, W. A. Yehye, S. C. Liu, C. C. Chu and V. K. S. Hsiao, Nanomaterials, 2020, 10, 1985 CrossRef CAS PubMed.
- S. Ng and M. Pumera, Adv. Mater., 2023, 35, e2207196 CrossRef PubMed.
- C. Ni, M. Chevalier and J. G. C. Veinot, Nanoscale Adv., 2022, 5, 228–236 RSC.
- S. Nellaiappan, N. K. Katiyar, R. Kumar, A. Parui, K. D. Malviya, K. G. Pradeep, A. K. Singh, S. Sharma, C. S. Tiwary and K. Biswas, ACS Catal., 2020, 10, 3658–3663 CrossRef CAS.
- M. Javadi, D. Picard, R. Sinelnikov, M. A. Narreto, F. A. Hegmann and J. G. C. Veinot, Langmuir, 2017, 33, 8757–8765 CrossRef CAS PubMed.
- H. Yu, A. N. Thiessen, M. A. Hossain, M. J. Kloberg, B. Rieger and J. G. C. Veinot, Chem. Mater., 2020, 32, 4536–4543 CrossRef CAS.
- N. K. Katiyar, S. Dhakar, A. Parui, P. Gakhad, A. K. Singh, K. Biswas, C. S. Tiwary and S. Sharma, ACS Catal., 2021, 11, 14000–14007 CrossRef CAS.
- C. F. Holder and R. E. Schaak, ACS Nano, 2019, 13, 7359–7365 CrossRef CAS PubMed.
- H. Yu, T. Helbich, L. M. Scherf, J. Chen, K. Cui, T. F. Fässler, B. Rieger and J. G. C. Veinot, Chem. Mater., 2018, 30, 2274–2280 CrossRef CAS.
- E. Bianco, S. Butler, S. Jiang, O. D. Restrepo, W. Windl and J. E. Goldberger, ACS Nano, 2013, 7, 4414–4421 CrossRef CAS PubMed.
- L. Khomenkova, D. Lehninger, O. Kondratenko, S. Ponomaryov, O. Gudymenko, Z. Tsybrii, V. Yukhymchuk, V. Kladko, J. von Borany and J. Heitmann, Nanoscale Res. Lett., 2017, 12, 196 CrossRef CAS PubMed.
- C. Qian, W. Sun, D. L. H. Hung, C. Qiu, M. Makaremi, S. G. Hari Kumar, L. Wan, M. Ghoussoub, T. E. Wood, M. Xia, A. A. Tountas, Y. F. Li, L. Wang, Y. Dong, I. Gourevich, C. V. Singh and G. A. Ozin, Nat. Catal., 2018, 2, 46–54 CrossRef.
- S. L. A. Bueno, A. Leonardi, N. Kar, K. Chatterjee, X. Zhan, C. Chen, Z. Wang, M. Engel, V. Fung and S. E. Skrabalak, ACS Nano, 2022, 16, 18873–18885 CrossRef CAS PubMed.
- M. A. Hossain, M. Javadi, H. Yu, A. N. Thiessen, N. Ikpo, A. O. Oliynyk and J. G. C. Veinot, Nanoscale, 2020, 12, 6271–6278 RSC.
- Y. Zheng, J. Lapano, G. Bruce Rayner and R. Engel-Herbert, J. Vac. Sci. Technol., A, 2018, 36, 031306 CrossRef.
- S. L. Anderson, E. J. Luber, B. C. Olsen and J. M. Buriak, Chem. Mater., 2016, 28, 5973–5975 CrossRef CAS.
- Y. Zhang, X. Han, R. Liu, Y. Liu, H. Huang, J. Zhang, H. Yu and Z. Kang, J. Phys. Chem. C, 2012, 116, 20363–20367 CrossRef CAS.
- L. Ma, l Jia, X. Guo and L. Xiang, Chin. J. Catal., 2014, 35, 108–119 CrossRef CAS.
- M. C. Biesinger, Surf. Interface Anal., 2017, 49, 1325–1334 CrossRef CAS.
- M. C. Militello and S. J. Simko, Surf. Sci. Spectra, 1994, 3, 387–394 CrossRef CAS.
- C. R. O’Connor, M. A. Van Spronsen, M. Karatok, J. Boscoboinik, C. M. Friend and M. M. Montemore, J. Phys. Chem. C, 2021, 125, 10685–10692 CrossRef.
|
This journal is © The Royal Society of Chemistry 2023 |