DOI:
10.1039/D1GC03054J
(Critical Review)
Green Chem., 2021,
23, 8305-8331
Progress in marine derived renewable functional materials and biochar for sustainable water purification
Received
23rd August 2021
, Accepted 6th October 2021
First published on 6th October 2021
Abstract
Global water scarcity is increasing day-by-day due to population explosion, urbanization and rapid industrialization. Inevitably, surface water is widely contaminated by various hazardous geogenic, organic and inorganic contaminants, also by untreated industrial effluents and unscientific human activities. On the other hand, the rapid worldwide increase in consumption of petroleum products has inspired researchers to develop renewable and sustainable materials for water purification applications. Significantly, biomass-derived materials are promising substitutes for depleting resources. Specifically, marine-based biomaterials, for instance, chitin/chitosan, seaweeds and seaweed-based polysacharides (agarose, alginate, cellulose, carrageenan) are abundant, environmentally friendly, and renewable biomaterials that are considered an appropriate solution for environmental contamination. Over past few decades various studies have focused on marine-based and seaweed-polysaccharide-based composites because of their renewability and sustainability for water purification. A number of reviews exist for biopolymer-based material applications in water purification; but to promote marine-derived biomaterials for water purification, a critical review between conventional materials and emerging approaches using seaweed-derived materials is needed. Hence, the present review study is the first of its kind, shedding light on the selection of diverse marine-derived biomaterials, as well as their important physical and chemical properties, in order to design functional materials for water purification applications. Further, the present review critically assesses the high-performance marine-derived functional materials exploited for existing state-of-the-art water purification technologies. Marine-derived materials with unique properties, such as inbuilt functionality, high mechanical strength, and prominent surface area and their prominence in developing high-performance sustainable materials for water purifications are reviewed. Furthermore, the review also discusses the various methodologies developed for the preparation of multifunctional carbonaceous materials using marine-derived biomaterials. Such biochar compete with commercial activated carbon and graphene owing to their unique properties. Also, the challenges in implementing the developed functional biomaterials in state-of-the-art water purification technologies and future prospects are discussed.
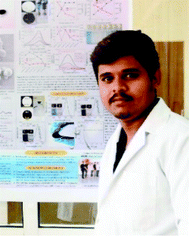 Halanur M. Manohara | Dr Manohara Halanur M. completed his PhD in chemistry from the Centre for Nano and Material Sciences, Jain University. He graduated from Tumkur University, Tumkur, India, in 2015 following which he received his Master's degree in 2017 in Chemistry from Jain University, Bangalore, India. His current research interests include the development of state-of-the-art functional modules such as biopolymer-based hydrogels, aerogels and composite membranes for wastewater treatment. He also obtained the AWSAR Award-2020 in a contest organized by the Department of Science and Technology, India for his best research story. |
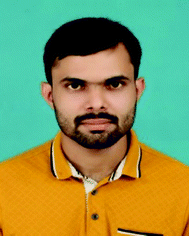 Sooraj S. Nayak | Mr Sooraj worked as a Project Assistant at CNMS, Jain University, Bangalore, Karnataka, India. He completed an MSc in chemistry in 2020 from Alva's college, Karnataka, India. Since childhood, he was fascinated by science and accordingly chose a career in chemistry. He also believes that material science has true potential to revolutionize the way of living in synergy with nature to make the world a better place. Mr Sooraj is looking forward to working in fields such as water treatment, nanotechnology and biomaterials. |
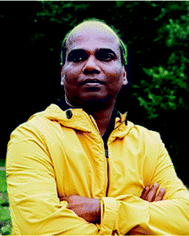 Gregory Franklin | Dr Gregory Franklin is a professor at IPG PAS, Poznan, Poland. He received his PhD in plant biotechnology from the University of Madras, India in 2001. Since then he has held various research positions in the USA, Saudi Arabia and Portugal before moving to Poland in 2015. He is an interdisciplinary scientist whose research focuses on plant nanotechnology and materials science. Understanding the fundamental mechanisms of green chemistry and the interaction between plants and nanomaterials is the main focus of his research team. |
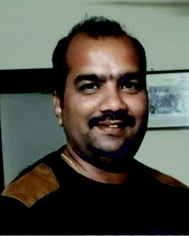 Sanna Kotrappanavar Nataraj | Dr S. K. Nataraj is currently working as a Professor at CNMS, Jain University, Bangalore, India. He obtained his PhD in 2008 in Polymer Science from Karnataka University, Dharwad, India. Immediately after the completion of his PhD, he pursued three Postdoctoral Associate assignments at Chonnam National University, South Korea (2007–2009), Institute of Atomic Molecular Sciences, Academia Sinica (2009–10), Taiwan and the Cavendish Laboratory, University Cambridge, UK (2010–2013). He was awarded the DST-INSPIRE Faculty Award (2013–2015) at CSIR-CSMCRI, Bhavnagar. His main areas are the development of sustainable materials and processes for Energy and Environmental applications including water treatment. |
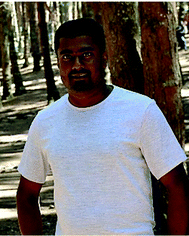 Dibyendu Mondal | Dr Dibyendu Mondal is an ERA chair holder in the NANOPLANT project at IPG PAS, Poznan, Poland from September 2021. He received a PhD in Chemical Science from CSIR-CSMCRI, India in 2015. From 2015 to 2017 he was a postdoc at CICECO, University of Aveiro, Portugal and then he joined CNMS, Jain University, India as an assistant professor in 2017. His main research areas focus on value addition of bio resources within the biorefinery concept; green solvents mediated the packaging of biomolecules. He is also fascinated by designing green nanocomposites for task-specific applications, such as biocatalysis, water purification, and in plant science. |
1. Introduction
Over the past few decades, biomass valorisation as a green renewable resource has received a lot of attention globally from research sectors and industries.1–3 With the rapid deterioration in renewable fossil fuel resources and growing environmental problems, many researchers are attempting to produce biofuels,4 value-added chemicals,5 carbonaceous materials6 as well as functional composites for various applications.7,8 With diminishing resources for synthetic polymers, such as petroleum and non-renewable carbon sources, there has been growing interest in biomass-derived macromolecules because of their unique characteristics and because they are potential substitutes for synthetic polymers.9,10 Importantly, they are abundant, biodegradable, economic, non-toxic and also it is easy to manipulate their physico-chemical properties for desired applications. About 70% of the Earth's surface is covered by ocean which represents a vast resource of biodiversity. Moreover, marine organisms have adapted to extreme environments, such as high salinity, pH, high pressure and temperature and, hence, their biochemical composition provides an exceptional reservoir to explore and design functional materials.11,12 Seaweed-based materials from the oceans, produced in copious quantities of over 19 million tonnes and either harvested from the oceans or cultured annually, are promising feedstocks for the production of sustainable functional materials.13,14 Seaweeds are found throughout the world's oceans and are mainly classified as brown seaweed (Phaeophyta) and red seaweed (Rhodophyta), which are exclusively marine, and green seaweed (Chlorophyta) which are freshwater and terrestrial, based on their colour appearance.15,16 Seaweed contains a huge amount of bioactive components, such as pigments, phenols, proteins, polysaccharides, and bioactive peptides. A vast amount of research has explored marine-derived biomaterials as food sources and their health benefits have been demonstrated. Further, various value-added chemicals, biopolymers, carbohydrates and macromolecules have been successfully extracted and employed for various applications, such as biofuel production,17 catalysis,18,19 energy storage and conversion,20–22 biological applications and environmental applications (Fig. 1).23 Consequently, there is an increase in attention towards developing a marine bioprocess industry to valorise biomaterials into valuable functional materials through facile chemical processes.
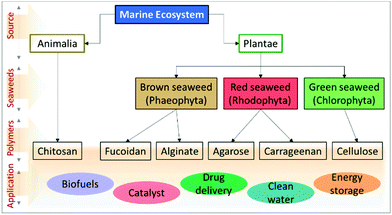 |
| Fig. 1 Flow chart representing the types of marine-derived biomaterials and extracted biomacromolecules. | |
On the other hand, with the increase in global water scarcity, the supply of affordable potable water is a massively challenging proposition throughout the world. Rapid industrialization and rising environmental contamination of natural water sources need to be tackled on a priority basis. Unfortunately, current water purification technologies are noneconomic and inefficient for meeting existing demands.24,25 Besides this, most existing materials are non-biodegradable and difficult to recycle, and disposal of these materials can cause secondary pollution that has led to rising concerns by occupational and environmental health experts that they are more harmful materials than previously encountered ones in causing serious threat to life forms.3,26 Therefore, there is a growing concern to develop low-cost, sustainable efficient functional materials using biopolymers or polymeric organic molecules acquired from renewable resources.26–28 Apart from cellulose from terrestrial plant-based materials, seaweed-derived macromolecules are the most exploited materials in water purification technologies thanks to their remarkable mechanical strength, enriched functionalities, moderate surface area and chemical stability. Generally, polysaccharide derivatives showed high removal efficiency for various organic contaminants (e.g. dyes, drugs, pesticides) and inorganic contaminants (fluoride, phosphates, heavy metal ions) via biosorption, adsorption, coagulation, reduction and oxidation.29,30 In particular, seaweed-based biomaterials possess extensive hydroxyl and amine functionalities and exhibit considerably high metal binding capacity and selectivity attributed to metal–ligand interaction, which creates the opportunity to develop efficient functional materials for water purification technologies.31 However, inevitably seaweed-derived materials need to be reformed through chemical or physical surface modifications in order to remove these organic compounds, since they dissolve in water with varying pH values.
Hence, over the past few decades various research groups have extensively developed derivatives of seaweed-based biomaterials by simple complexation with polymers, biopolymers, and nanocomposites. Further, they have also utilised them as a low-cost feedstock to prepare valuable carbonaceous materials with high surface area, surface functionality, and heteroatom and metal doped carbonaceous materials by following simple high-temperature treatment.32 Thus, the present review sheds light on various seaweed-derived macromolecules used to engineer and develop high-performance seaweed-based materials, their physico-chemical properties and potential application in water purification technologies. Further, this review will encourage material scientists to fully utilise the hidden potential of marine-derived biomaterials in the field of sustainable water purification.
2. Raw seaweed-based materials
Generally seaweed-based materials containing a huge amount of organic polymers made up of carbohydrates and proteins are produced globally on a large scale from red, green and brown seaweeds.33 Understanding their structure and diversity in chemical composition can help us gain insight into material design and can also inspire the development of high-performance materials.
Although, seaweeds have significant importance in food and industrial applications, in the late 20th century, extensive research was done utilising marine-derived materials such as seaweeds and polysaccharides for ion exchange, adsorption or biosorption applications after suitable chemical pre-treatment (Fig. 2).34 The biosorption capability of seaweeds is related to the chemical composition of the cell walls. Seaweed generally contains extensive amounts of hydroxyl, acetamide, amine, amide, sulfate and phosphate functional groups, significantly enabling metal–ligand interaction, which helps in capturing heavy metal ions from an aqueous medium.35–37 In particular, alginate is more responsible for the biosorption in brown algae, carragenan in red seaweed and agarose in green seaweed.38 Various seaweeds exhibit notable biosorption capacity for heavy metal ions and are listed in Table 1. In 1987, Volesky and Kuyucak established the biosorption of silver ions from waste industrial effluents using Sargassum seaweed and patented the same.39 Several interaction mechanisms, such as coordination, chelation, electrostatic interaction, complexation, ion-exchange and physical adsorption have been anticipated for the separation of heavy metal ions. Lately, Sargassum has also been explored for the adsorption of lead, copper and cadmium ions with notable biosorption capacity attributed to several advantages, such as high efficiency and affinity for toxic metals, ease of operation, minimisation of the volume of chemical and biological sludge to be disposed of, and low operating cost.40,41
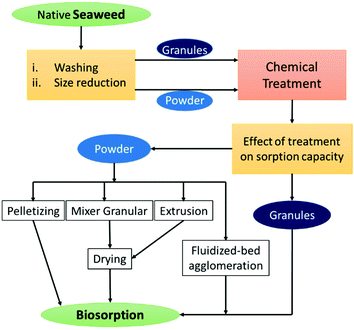 |
| Fig. 2 General schematic representation of the preparation of biosorbents from seaweeds. | |
Table 1 Seaweed and seaweed-derived high-performance carbonaceous materials explored for water purification applications
Sl. no. |
Seaweed-based biomass |
Modifying agent |
Pollutants |
Ads. ( g) |
Ref. |
01 |
Sargassum sp. |
— |
Pb |
1.1 mmol |
40
|
Cu |
0.9 mmol |
02 |
Sargassum sp. |
— |
Cd |
0.7 mmol |
41
|
03 |
Padina spp. |
— |
Pb |
1.2 mmol |
40
|
Cu |
1.1 mmol |
04 |
Gracillaria spp. |
— |
Pb |
0.4 mmol |
40
|
Cu |
0.5 mmol |
05 |
Sargassum vulgare
|
— |
Cd |
87 mg |
40
|
Cu |
59 mg |
06 |
Fucus vesiculosus
|
— |
Cr III |
1.2 mmol |
42
|
Cr VI |
0.8 mmol |
07 |
Ascophyllurn nodosum
|
NaOH treatment |
Co |
160 mg |
43
|
08 |
Ulva spp. |
Alkali treatment |
Cd |
90.7 mg |
44
|
Zn |
74.6 mg |
Cu |
57.3 mg |
09 |
Durvillaea potatorum
|
CaCl2 solution treatment |
Ni II |
1.1 mmol |
45
|
Cd II |
1.1 mmol |
46
|
10 |
Ecklonia radiata
|
CaCl2 solution treatment |
Pb |
1.6 mmol |
47
|
Cu |
1.3 mmol |
11 |
Durvillaea potatorum
|
CaCl2 solution treatment |
Pb |
1.3 mmol |
47
|
Cu |
1.1 mmol |
12 |
Sargassum filipendula
|
Dealginated, acid treatment |
Cu |
3.5 mmol |
48
|
13 |
Sargassum fluitans
|
Acid wash, protonated |
U VI |
560 mg |
49
|
14 |
Enteromorpha torta
|
Immobilised in alginate |
134Ce |
12.6 mmol |
50
|
15 |
Seaweed community biomass |
Alkali treatment |
Zn II |
115.1 mg |
51
|
16 |
Red seaweed |
Citric acid |
Crystal violet |
217.3 mg |
52
|
17 |
Stoechospermum marginatum
|
(i) Propylamine, (ii) methanol, (iii) formaldehyde, (iv) formic acid |
Acid orange II |
(i) 71 mg, (ii) 29 mg, (iii) 34 mg, (iV) 15 mg |
53
|
Further, researchers have demonstrated that Durvillaea potatorum and Ecklonia radiata display higher biosorption capacity for nickel, copper and lead ions compared to Sargassum.45,47,54 In fact, biosorption occurs in two stages: (i) rapid ion-exchange with surface functionalities, and (ii) slow biosorption into the multi-structured material. It is important to note that seaweed-based materials are capable of adsorbing only cationic pollutants. The anionic surface charge of the seaweeds repels anionic pollutants and exhibits poor biosorption. Researchers have also demonstrated chemical activation, such as an acid/alkali wash to activate surface functionalities and enhance the biosorption, with further soaking in calcium, magnesium and potassium salts to prevent the leaching of alginate.43,47 However, dealginated biomass waste was also explored for biosorption where remarkable efficiency was obtained for the separation of copper ions.48 This may be due to the voids created after alginic extraction. Interestingly, seaweed-immobilised alginic beads showed superior biosorption for radioactive cesium.50 Similarly, agar-extracted Gelidium sesquipedale exhibited a considerable amount of Cd(II) biosorption, and equilibrium and kinetic behaviour were further studied to promote the scaling-up process.55 Furthermore, waste seaweed also showed excellent separation of Pb/Cu and Pb/Cd in a fixed-bed column through a robust ion-exchange process.56 Similarly, research efforts were made to functionalize seaweed biomaterials for dye biosorption, but the adsorption capacity was comparatively low.52,53,57 Interestingly, seaweeds were also utilised to prepare biogenic TiO2 and silver nanoparticles which exhibit photocatalytic activity for the degradation of organic pollutants.31,58 On the other hand, the contamination of natural habitats with micro-plastics is an emerging concern. Thus, a lot of research has been conducted to develop bio-based plastic using non-renewable resources.59 Remarkably, in a recent flurry of research, seaweed residue was utilised to develop biodegradable plastics.60 Interestingly, the inorganic salts present in the microalgae act as a filler and crosslinker which enhances the practical feasibility of the bioplastic. This finding opens up a new research arena of utilising seaweed residues for the preparation of bioplastics. Despite substantial progress in understanding seaweed-based materials for biosorption and other applications over decades of unceasing research, seaweed-assisted biosorption is still limited to the bench scale. This is due to the poor recyclability, comparatively low biosorption capacity, challenging desorption processes and risk of macromolecules and nanocomposites leaching into the reaction medium during biosorption.61,62 Also, feasible seaweed-assisted biosorption demands a crucially engineered and developed reactor system and a critical understanding of the processes. With the above-mentioned limitations on seaweed-based biosorption, extensive efforts were made to design and develop functionalised seaweed-derived macromolecules and marine-based discrete biomaterials for various applications. With an extracted distinct macro-molecule with familiar physico-chemical properties, one can tune the adsorption–desorption processes and control the leaching of composites. Over past decades, marine-derived bio-macromolecules, such as alginates, chitin/chitosan, agar/agarose, carrageenan, cellulose, collagen, and fucoidan (Fig. 3) have been developed as highly efficient functional materials for the purification of contaminated groundwater, industrial and domestic wastewater, and also in desalination processes. Fig. 4 shows the number of studies reported from 1995 until now, which indicate a massive growth in marine-derived materials for adsorption, biosorption, membrane filtration and advanced oxidation processes. Accordingly, we first discuss the structure–property relationship of chitosan and various seaweed-derived biopolymers and then summarize the different approaches developed to prepare high-performance hybrid materials.
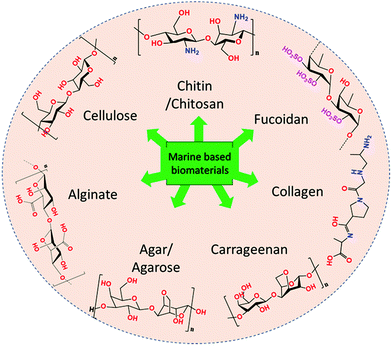 |
| Fig. 3 Various biomacromolecules derived from marine biomaterials and their chemical structures. | |
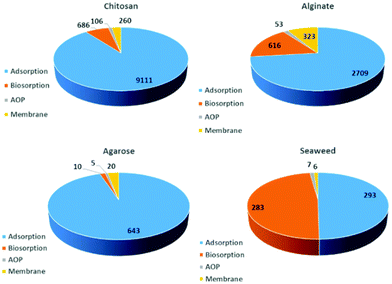 |
| Fig. 4 Approximate distribution of publications dealing with majorly used marine-derived biopolymers for adsorption, biosorption, advanced oxidation processes (AOP) and membrane filtration according to the Web of Science from 1995 to July 2021. | |
3. Chitin/chitosan
Chitin/chitosan are the most abundant, renewable, marine-based, N-containing polysaccharides found in the exoskeletons of crustaceans, crabs, insects, algae, fungi and shrimp shells.63,64 Globally, 10 billion tonnes of chitin have been biosynthesised and 1.5 million tonnes of chitins are commercially available.65 Chitin is a linear polysaccharide first identified in 1884, made up of (2-amino-2-deoxy-D-glucose) D-glucosamine and N-acetyl-2-amino-2-deoxy-D-glucose (N-acetyl-D-glucosamine) units which are linked by 1–4-β-glycosidic bonds and it is the only source of chitosan. Structurally, the N-acetyl-2-amino-2-deoxy-D-glucose monomer is largely found in chitin, whereas the concentration of 2-amino-2-deoxy-D-glucose is high in chitosan. Chitin/chitosan are semi-crystalline in nature due to the presence of inter- and intramolecular hydrogen bonding. Chitosan is generally obtained by the deacetylation of chitin.66 In 1894, Hopper demonstrated deacetylated chitin using potassium hydroxide solution, later named chitosan.67 Significantly, in acidic pH, protonated ammonium (pKa (–NH3+) = 6.3) disrupts the crystalline nature of chitosan, leading to the solubilization of the polymer in an aqueous medium. In fact, chitosan is the only cationic polymer available in nature and is the only commercially available water-soluble cationic polymer, which makes it an important candidate in designing various sustainable functional materials.68 Chitosan containing hydroxyl groups and reactive amine functionality in its structure is extensively utilised to prepare high-performance functional materials in a desired physical form due to its water solubility. It readily interacts with charged organic and inorganic species through electrostatic interaction, coordination, metal–ligand interaction and through weak van der Waals forces or hydrogen bonding. Altogether chitosan can be considered an eco-friendly complexing agent because of its renewability, economic cost, nontoxicity, hydrophilicity and biodegradability.69
Further, its chemical properties, such as being a polyelectrolyte at acidic pH, high reactivity, coagulation, flocculation and biosorption properties, resulting from the presence of reactive hydroxyl and mostly amine groups in the macromolecular chains make it a most prominent candidate for water purification applications. In 1969, Muzzaiulli discovered that chitosan can collect natural heavy metal ions from seawater by a chelating effect.70 In 1974, Friedman and group systematically explored the metal ion binding capacity of chitosan for the first time along with other biopolymers,71 while the application of chitosan in wastewater treatment was demonstrated in 1976.69,72,73 Since then extensive research has been carried out to develop efficient low-cost chitin/chitosan-based materials for water purification, especially as adsorbents for the separation of organic and inorganic contaminants (Fig. 5).
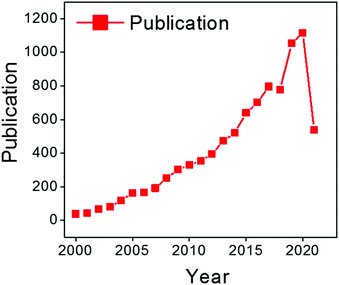 |
| Fig. 5 Distribution of publications on chitosan for adsorption per year according to the Web of Science from 2000 to July 2021. | |
Over the past few decades, chitosan being a cationic biopolymer has received a great deal of attention for coagulation–flocculation processes due to its ability to form polyelectrolyte complexes in an aqueous medium.74,75 Chitosan was successfully demonstrated for the flocculation of kaolin suspension,76 algal cells,77,78 river silt,79 humic acid solution,80Chlorella,81 tetracycline,82 dyes,83 pesticides,84 heavy metal ions85etc. Various modified chitosans, such as chitosan glutamate, chitosan hydrochloride, and carboxymethyl chitosan, exhibited excellent contamination removal due to effective interaction with pollutants.80,86 A study also demonstrated that a chitosan composite exhibited a higher percentage of removal compared to commercially applied flocculants, such as polyaluminum chloride and silicate for organic contaminants and solid suspended particles in water treatment.55 Thus, chitosan has been widely explored because the process is efficient even at low dosage, with a quicker depositing velocity, easier sludge treatment, and biodegradability and it exhibited high efficiency in coagulating and flocculation organic matter, inorganic ions and solid particles.87,88 Interestingly, chitosan was also used for the flocculation of oil–water emulsion attributed to the hydrophilic nature of chitosan, which is explained in a later part of the review (section 3.3).
3.1 Decontamination of organic contaminated water
Over the past few decades, textile, pharmaceutical and many other industries have raised serious concerns as they have been releasing organic contaminants, such as dyes, pharmaceutical drugs, pesticides, surfactants etc., containing untreated wastewater into the environment, which has caused severe health issues to human beings, and terrestrial and aquatic living organisms.89,90 Interestingly, chitosan-based beads,91 thin films,92 biocomposite membranes,93 hydrogels and aerogels94 were widely explored for the separation of such organic contaminants. The amine functionality in the chitosan intensely remains as an active site for the adsorption of organic moieties depending on the pH of the reaction medium.95 Further, with an increase in the amine functionalities, diminishing the degree of acetylation enhances the adsorption of dye molecules. Thus, various modifications of chitosan were achieved by (i) crosslinking reactions with multifunctional moieties and (ii) grafting of highly functionalised monomers or polymers.96 Both techniques yield chitosan derivatives with superior properties, such as improved surface functionality, enhancement of active sites, and also physical, chemical and thermal stability.97 In the case of grafting, auxiliary chemicals are required to form a stable composite with chitosan, whereas crosslinking may lead to reduced functionalities. The functionalities of chitosan have been enhanced by grafting with various chemicals—such as poly(methyl methacrylate),98,99 diethylene triamine,100 polypropylene imine,101 sulfonic acid,102 and β-cyclodextrin,103,104 and also with nanomaterials, such as graphene oxide (GO),105 reduced graphene oxide (rGO),106,107 and single-walled and multi-walled carbon nanotubes (SWCNT & MWCNT)108,109—further, establishing their application in water purification.
Over past decades, exfoliated graphene oxides have been extensively studied due to their excellent adsorption capacity attributed to huge polar moieties, such as epoxy, hydroxy, and carboxy groups and high surface area.110–112 A group led by Prof. Saleh has established the use of GO for various applications, such as powerful adsorbents,113 sensors,114 photocatalysts,115 and also as a filler in membranes116 to treat the water obtained as a by-product of the petrochemical industry.117–119 Thus, graphene oxide was widely utilised to prepare chitosan composites for water purification applications. By stacking into a continuous membrane, GO with a two-dimensional lamellar structure and single-atom thickness has shown advantages in water purification.120–122 Chen et al. have prepared a GO-chitosan hydrogel through self-assembly of GO within a chitosan network. The hydrogel exhibited enhanced adsorption through a column filtration mode for a comparison of cationic and anionic dyes. It is also observed that the performance increases with an increase in GO content.123 Later, Kamal et al. demonstrated tetraethyl orthosilicate crosslinked GO/chitosan film for Congo red dye separation with excellent adsorption capacity.124 Interestingly, the GO/chitosan composite shows robust separation of organic dyes under ultra-sonication, which is advantageous in a real-time scenario.125
Recently, GO/chitosan aerogels with high mechanical strength were demonstrated for the separation of various organic contaminants.126,127 On the other hand, the development of magnetic composites has attracted various research groups around the globe. It is suggested that a magnetic property can be enabled by incorporating magnetic composites like Fe3O4 into the chitosan network. The chitosan forms stable composites with metal composites through metal–ligand interaction with the hydroxyl and amine groups. The magnetic composites can be prepared by both in situ and ex situ processes.107,128 Efforts were made to enhance adsorption by grafting with cyclodextrin129 and GO130 along with magnetic composites. The hydrophobicity and surface functionality of cyclodextrin and GO enhance the adsorption capacity of chitosan. Advantageously, chitosan exhibits antibacterial activity by binding to the negatively charged bacterial cell wall, causing disruption of the cell. Thus, magnetic chitosan/GO composites demonstrated antibacterial activity against Escherichia coli from an aqueous medium.131 Further, the antibacterial property was enhanced by introducing silver nanoparticles into the chitosan network through the photocatalytic reduction of silver nitrate, and the composite was used for adsorption of various dye molecules.132 Recently, chitosan-based novel magnetic nano-adsorbents in the fluid state were prepared via a facile in situ co-precipitation method. The magnetic adsorbent exhibited robust separation and superior adsorption capacity of 1724 mg g−1 for Congo red dye and was easily recyclable with magnetic assistance.133 Further, various chitosan-based hydrogels and aerogels were demonstrated for organic contaminant separation.134,135 Among them, aerogels are promising candidates due to high active surface contact with the pollutants and easy implementation.
A polydopamine-modified chitosan-based aerogel was reported for the separation of organic dyes along with heavy metal ions.136 The enhanced adsorption is attributed to the large number of amine and catechol groups on its molecule. Similarly, polydopamine-modified carboxymethyl cellulose-based aerogel was also evaluated for cationic and anionic dye separation.137 Also, low-cost fly-ash and GO-immobilised chitosan aerogel were explored for reactive orange 16 dye, which exhibited moderate adsorption.138 Fly-ash is a low-cost mineral residue obtained after burning charcoal in an electricity generating plant.139 Chitosan was also used to exfoliate a phyllosilicate, and further crosslinked with rGO to form a porous hydrogel with remarkable mechanical strength without the aid of a crosslinker (Fig. 6).140 Further the porous hydrogel was used for chromium separation. Recently, our group has reported iron and aluminium composite-functionalised adsorption-based aerogel membranes for dye, pharmaceutical and pesticide separation.141 These studies suggested that economical aerogels can be prepared by functionalising chitosan aerogel for the efficient decontamination of organic wastewater.
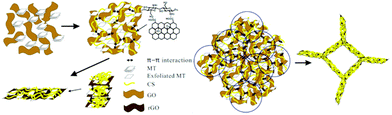 |
| Fig. 6 Schematic representation of the fabrication of a composite hydrogel with a porous structure.140 | |
On the other hand, photodegradation and advanced oxidation processes (AOPs) are promising wastewater treatment technologies which are widely used around the world.142,143 Various research groups have demonstrated chitosan-based catalysts for the degradation of organic pollutants via photodegrdation144 or AOPs. TiO2,145,146 Ag147 and ZnO148,149 immobilised chitosan composites were widely used for photocatalysis. TiO2 is an n-type semiconductor initiating photocatalytic oxidation at a wavelength of 320 nm. Thus, TiO2-impregnated chitosan composites were widely developed for the degradation of various organic contaminants. Zainal et al. cast a TiO2-chitosan composite based thin film over a glass support and examined its photocatalytic activity.150 The composite showed excellent removal of model organic contaminants via the combined effect of adsorption and photodegrdation. Later, TiO2-encapsulated chitosan beads and surface-imprinted beads were developed for a continuous photocatalytic mode of organic dye and pesticide degradation.146,151 In general, emerging contaminants such as pharmaceutical drugs are difficult separate through adsorption or membrane filtration, so degradation is the most suitable technique for such contaminants.151,152 Apparently, the surface-decorated composite shows robustness due to the greater exposure of active sites. However, there is a high chance of the leaching of nanocomposite deposited over the surface during the impregnation treatment, which harms the recyclability and also induces additional pollution into the system. Recently, catalysts for AOPs were also developed, such as a Fenton catalyst,153 cobalt oxide,154 ZnS155 and ferrocene156 functionalised chitosan materials. However, they are still limited to lab-scale demonstrations due to the requirement of a high loading of active catalyst and the consumption of a large amount of peroxide and persulfate chemicals.
Membrane technology is widely used for wastewater treatment, drinking water treatment and desalination due to its low production cost, operational simplicity and ease of scaling up.157 However, conventional membranes are mostly derived from petroleum-derived polymers or synthetic polymers which exhibit threats to the environment after disposal. Moreover, conventional membranes suffer from biofouling and low permeability.158 Chitosan has gained increasing interest as a membrane material due to its hydrophilicity, ease of modification, biocompatibility, and remarkable affinity to organic molecules and inorganic metals. Over the past two decades various chitosan-based crosslinked and composite membranes have been widely developed for wastewater treatment.93 Evidently, functionalisation or modification of chitosan polymer significantly enhance the performance; thus, various crosslinking agents, such as organic molecules,159–162 metal salts163–165 and inorganic acids,166 have been demonstrated. The crosslinking causes shrinkage of the polymer, which leads to a reduced porous structure helping in the high removal of pollutants; however, it also reduces the flux rate. On the other hand, composite membranes can be produced by blending with synthetic polymers,167 biopolymers, metal composites, carbonaceous materials168etc. The blending of two oppositely charged polymers leads to polyelectrolyte complexes. Since chitosan is the only cationic polymer, it has been widely used to prepare biocompatible polyelectrolyte complexes with alginate, carboxylate cellulose, poly(acrylic acid) (PAA) and other anionic polymers. The blending leads to highly selective water permeability with enhanced mechanical and thermal stability. To enhance the hydrophilicity of the membrane, chitosan was blended with poly(vinyl alcohol) (PVA), alginate, poly(ethylene glycol) etc. Whereas a hydrophobic membrane was obtained by blending with polysulfone, polyacrylonitrile, polyvinylidenefluoride etc. Thus, according to the nature of the pollutant, monomers or polymers were selected for desired molecular separation.
Recently, there has been a growing interest in developing thin film composite (TFC) membranes due to their advantages, such as anti-fouling property and enhanced recyclability. TFC membranes consist of an active thin layer formed by interfacial polymerisation which determines the performance of a membrane and a macro-porous support which gives it mechanical strength.93,169,170 Commercially, a polyamide membrane is a widely used TFC membrane due to its remarkable mechanical strength, but it suffers from low flux and biofouling, which led to efforts to replace the polyamide layer, with limited success.171,172 Recently our group has successfully demonstrated silver crosslinked chitosan as an active layer over a polysulfone membrane (Fig. 7). The chitosan-based membrane not only exhibits anti-fouling propensity, it also showed a superior pure water flux of 100 L m−2 h−1 (LMH).174 The membrane exhibited >98% rejection for dyes and tannery wastewater with a flux rate of up to 30 LMH. Further, the flux and rejection of the membrane were enhanced by immobilising a spiral-like carbonaceous material in the active chitosan layer.173 Interestingly, the multifunctional helical structured carbon acts as a crosslinker, a hydrophilic membrane filler which led to the superior membrane performance. Thus, a chitosan-based membrane could be a potential membrane for an effective pre-treatment of various industrial organic wastewaters.
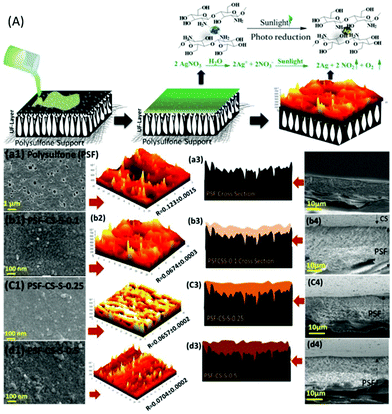 |
| Fig. 7 (A) Schematic representation of the fabrication of a chitosan-based thin film membrane over a polysulfone support. (a–d) SEM, AFM analysis, schematic representation and cross-section of the membrane showing the surface topology and the roughness of the membrane with varying concentrations of chitosan.174 | |
3.2 Decontamination of inorganic contaminated water
Heavy metal ions are very toxic/hazardous and should be eliminated from wastewater and drinking water. Heavy metals are generally the group of metals/metalloids with an atomic density of more than 4000 kg m−3.175 Many processes are conventionally used for the removal of heavy metals from water and wastewater; however, trace concentrations of heavy metals in effluents remain a great concern where restrictive standards should be passed before discharge. Various operations, including ion exchange, flotation, electro-coagulation, solvent extraction, membrane filtration, and adsorption have been used for the elimination of metals from aqueous environments.176 Among them, the adsorption technique is the most widely studied phenomenon due to the ability of chitosan to form coordinate or metal–ligand interactions with the heavy metal ions and inorganic anions attributed to its enormous amine and hydroxyl functionality, which also helps in the recovery of heavy metal ions.91,177 Chitosan and its derivatives are the most promising adsorbents for the separation of heavy metal ions, such as As(III/V), Fe(II/III), Pb(II), Cr(VI), Cu(II), Ni(II), Hg(II), Ag(I) etc., and inorganic nutrients, such as nitrate, sulfate, fluoride, chloride etc. Further, they have been extensively reviewed for their separation efficiency.29,90,178–181 Thus, the present section provides a brief explanation of the various strategies for preparing high-performance adsorbents for metal ions and inorganic nutrients.
For various chitosan-based crosslinked materials, such as beads, hydrogels, aerogels, polymeric composites, grafting a functional group onto them was widely demonstrated to synthesise an efficient adsorbent for the adsorption of inorganic contaminants.182–184 Glutaraldehyde, epichlorohydrin and ethylene glycol diglycidyl ether are the most commonly used crosslinkers for chitosan. However, crosslinking of chitosan generally leads to a non-porous macrostructure and diminished functionalities which limits their adsorption capacity.90,185 This is because the hydroxyl groups and amine functional groups react with the crosslinker, leading to a decrease in active adsorption sites. Further, researchers have developed a low-cost grafting method for the preparation of high-performance hybrid materials. The modification of chitosan led to an increase in surface functionality, which is crucial for the adsorption technique. Monomers like succinic acid, acrylic acid and itaconic acid were used to graft carboxyl groups onto the chitosan.186 Ethylene diamine tetra acetate, thiourea and cyclodextrin are the other popular grafting agents for chitosan.96,187 By tuning the pH with respect to the pKa value of a composite, cationic and anionic pollutants can be selectively adsorbed over the composites. Chitosan-based hybrids were also prepared with biomaterials such as nanoclays, silica, cellulose, agarose, alginate, polyvinyl alcohol, and nanofibrils.96,188,189 These composites enhance the functionalities, and induce mechanical strength and also chemical stability. Due to the high functionality, heavy metal ions were successfully separated from an aqueous medium through electrostatic interaction. Another important strategy is to introduce carbonaceous materials, such as GO, rGO, CNT, hydrothermal and activated carbons.190–192 Due to a synergistic combination of the high surface area of carbonaceous materials and the high functionality of chitosan or chitosan derivatives, they provide superior adsorption of inorganic contaminants.193
On the other hand, extensive efforts have been made to immobilise active metal composites, such as iron, aluminium, zirconium, silver, or molybdenum, into the chitosan network. Interestingly, chitosan has the ability to bind colloidal nanoparticles in the ratio 500 wt%/wt% attributed to its enriched multifunctionality.194 The synergistic combination of active metal composites and chitosan has shown superior adsorption capacity for various contaminants. Significantly, metal/chitosan composites were commercialised thanks to their low cost, biodegradability and excellent recyclability. For example, Pradeep and group demonstrated an antimicrobial composite made by immobilizing silver nanoparticles and AlOOH into the chitosan network.194 Interestingly, the polymeric network was developed for the controlled release of silver nanoparticles, which helps in the decontamination of pathogens; further, AlOOH successfully scavenged arsenic, lead and iron ions. They also developed and commercialised an FeOOH-chitosan composite for real groundwater contaminated by arsenate and ferric ions and demonstrated it as a point-of-use filter for drinking water in various parts of India.195 The chitosan not only effectively immobilised the metal nanocomposites, it further exhibited the controlled release of silver nanoparticles for antibacterial activity. Interestingly, these composites also exhibited a remarkable adsorption capacity for fluoride; however their performance was hindered by the presence of co-anions such as phosphate, nitrate and chloride.196 Inspired by this, we have designed and developed an α-FeOOH and γ-AlOOH functionalised chitosan-based ultrafast permeable, hydrophilic aerogel for scavenging fluoride from contaminated groundwater (Fig. 8A).141 The aerogel successfully purified 4734 L of fluoride-contaminated groundwater (Fig. 8B), and further exhibited a maximum adsorption capacity of 102 mg g−1 for arsenic and 81.5 mg g−1 for fluoride. Researchers have also developed magnetic composites because of their many advantages like easy collection of adsorbents from an aqueous medium and enhanced adsorption of metal ions due to the magnetic property.197–200 Further, the selective separation of metals of inorganic contaminants can be achieved by ion-imprinting technology. The process involves adding a target template ion into the chitosan solution prior to crosslinking followed by removal of the template ion.201–203 The created void will selectively adsorb the targeted ions.
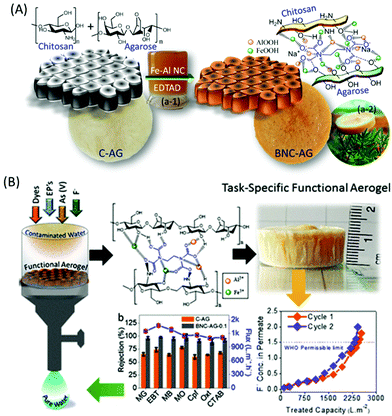 |
| Fig. 8 (A) Fabrication of iron and aluminium based composite functionalised aerogel and (B) performance of the aerogel membrane for the separation of dyes, pharmaceutical drugs, surfactants and fluoride ions from an aqueous medium.141 | |
3.3 Oil–water separation
The escalating discharge of industrial oily-wastewater and frequent worldwide occurrence of oil-spillage accidents demand highly efficient materials for oil–water purification. Over the past few decades, various physical and chemical treatments have been established to separate oil from water.204,205 Flocculation is one such type of chemical treatment, where chemical agents separate the oil–water mixture by destabilization of the oil–water emulsion via neutralising the surface charges of the emulsion droplets. However, the process requires a huge amount of chemicals, and thus requires low-cost, biodegradable and nontoxic demulsifiers and flocculants.206 The polyelectric nature and higher charge density of chitosan in an acidic medium assist the efficient flocculation of oil from an oil–water emulsion.206 The flocculation is dominant due to charge neutralization instead of bridging. Thus low-cost chitosan-based flocculant exhibited greater efficacy than traditional coagulants, such as alum or polyaluminum chloride.206
Chitosan exhibits up to 99% separation of oil from palm oil mill effluent due to the synergistic combination of adsorption, effective agglomeration and coagulation. Further, hydrophobically modified chitosan enhances the separation of oil from sodium dodecyl sulfate stabilised oil–water emulsion attributed to its hydrophobicity and surface functionalities.207 However, the cost of chitosan is high compared with most inorganic flocculants, which restricts its commercialisation.208 Zhang et al. prepared a hydrophilic, underwater superoleophobic, anti-oil-fouling chitosan/PVA based mesh inspired by shrimp shells.222 More than 99% separation was achieved through a gravity-driven filtration system with or without hyper-salinity. Interestingly, enhanced performance was observed with a silica-impregnated chitosan mesh attributed to the high surface area of the silica composite. Later, a biopolymer aerogel system has emerged as a prominent functional material for the separation of an oil–water emulsion. Meena and co-workers have demonstrated a highly crosslinked chitosan/agarose-based biohybrid aerogel membrane for the efficient separation (>99%) of water from real oil-spill wastewater collected from a shipbreaking yard (Fig. 9a–c); further preparation and application of the biobased aerogel process were patented.210,211 The chitosan acts as a support network and provides hydrophilic channels for water to pass through it (Fig. 9d–f). Thus, a flux rate of up to 600 LMH with >99% rejection was obtained in a crossflow membrane filtration mode. Similarly, various attempts were made to prepare an aerogel using superhydrophilic209 and superhydrophobic212 modified chitosan. Also, hybrid aerogels were prepared using alginate,213 cellulose,214 polydopamine212etc. to enhance the mechanical strength, chemical stability and permeability of the aerogel membrane. Interestingly, nanocomposites such as GO and TiO2-impregnated aerogel membranes, enhance oil-absorption,215 and induce a self-cleaning property in the aerogel membranes.215 Recently, we have demonstrated an Fe–Al composite functionalised chitosan aerogel exhibiting >99% separation of an oil–water emulsion with ultrahigh permeation attributed to the superhydrophilic nature of chitosan.141 Herein, the metal composites not only enhance the hydrophilicity of the membrane but also enable multifunctional properties. Interestingly, one can tune the path structure for liquid transport through unidirectional freeze drying.216,217 In sum, low-cost, biodegradable chitosan-based membrane are promising candidates for practical oil–water separation applications.
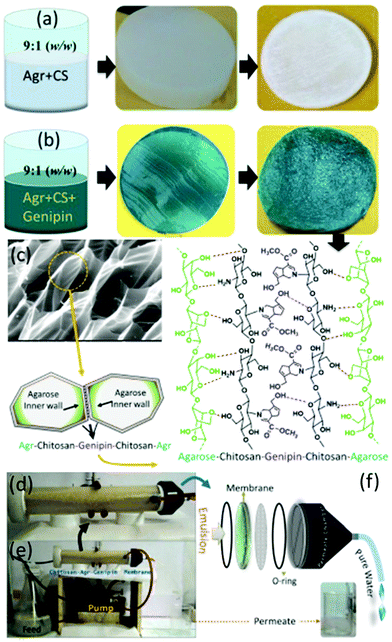 |
| Fig. 9 (a–c) Schematic and digital images of highly crosslinked, superhydrophilic agarose/chitosan aerogel. (d–f) Cross-flow membrane filtration of crude oil based emulsion separation.210 | |
3.4 Solar-assisted water evaporation
Solar-assisted water distillation is a promising facile technique to produce fresh water. Recently, there has been an increase in attention paid to developing highly efficient solar–thermal conversion materials for water evaporation. In a general strategy, researchers have immobilized a highly efficient solar–thermal converter catalyst in a high surface area matrix. In this regard, chitosan is a perfect candidate since the high surface functional groups can efficiently accommodate nanocatalysts and its natural hydrophilic nature will enhance the water permeability throughout the system. Zhou et al. designed highly hydratable polymeric hybrid hydrogels using PVA and chitosan.218 Conductive polypyrrole was infused as a light-absorbing catalyst. The hydrogel exhibits a superior water evaporation rate of 3.6 kg m−2 h−1 under 1-sun illumination. Likewise, Wang et al. substituted PVA with polyacrylamide and obtained a similar conversion efficiency; however, it showed long-term stability against sat and bacterial accumulation.219 Further, an rG-induced chitosan hydrogel was reported as a salt-resistant solar–thermal converter with an efficiency of 86% for water evaporation.220 The induced rGO acts as a spacer and enhances the transport of water within the hydrogel system and also the compression strength. Wang et al. fabricated a double-layered GO–chitosan/ZnO scaffold for solar steam generation by keeping a GO layer on the top.221 The hybrid aerogel exhibits a steam generation rate of 13.5 kg m−2 h−1 under 10-sun illumination. Similarly, silver nanoparticles,222,223 molybdenum carbide,224 melanin-coated titania hollow nanospheres225 and MnO2 nanowires226 immobilised chitosan-based materials were examined for solar steam generation. In sum, these low-cost, highly efficient advanced materials show potential applications in practical solar-driven wastewater treatment.
4. Alginate
Alginate is an anionic polysaccharide extracted from the component of the cell walls of brown algae and an exopolysaccharide of some bacteria such as Pseudomonas and Azotobacter. To be more specific, it is a copolymer of α-L-guluronic acid and β-D-mannuronic acid linked together by β-1,4-glycosidic bonds.227 Commercially, alginate is produced using Laminaria hyperborea, Laminaria digitata, Laminaria japonica, Eclonia maxima, Macrocystis pyrifera, Durvillea Antarctica, Lessonia nigrescens, and Sargassum spp.228 Alginate salts are generally water soluble, possess an excellent gelling property and are hydrophilic in nature due to extensive hydroxyl and carboxylic functionalities. Thus, they are extensively utilized in wastewater remediation, which is further attributed to their structural stability, high water permeability, biodegradability, and nontoxic nature.229 Interestingly, numerous studies have indicated that the efficiency of alginates can be improved by developing hybrids with suitable materials. Over the past decade, alginate-based hybrid materials have been developed using synthetic polymers, biopolymers and inorganic metal salts or composites which yielded multi-functional beads, hydrogels, aerogels and membranes for efficient water purification.230 Such various strategies used to develop high-performance materials are discussed here.
4.1 Decontamination of organic contaminated water
It was observed that alginate plays a critical role in the biosorption efficiency or ion-exchange capacity exhibited by brown seaweeds.38 This suggested that alginate would be an excellent candidate for sorption application. In the late 20th century, researchers studied the biosorption and adsorption efficiency of alginate and its hybrids mainly for heavy metal ions231–233 and for some organic contaminants.234,235 Later, over the past two decades, alginate-based materials have attracted immense research interest due to their chemical stability and biocompatibility. Calcium alginates are the most studied materials for adsorption; however, generally they are non-porous and exhibit a limited surface area.236 Thus, many strategies—such as gelation with boehmite,237 incorporation of surfactants and porogens such as NaCl, CaCO3,238 and preparing composites with various biomaterials such as nanoclays239—were demonstrated to prepare porous alginate materials. Surfactants such as sodium dodecyl sulfate240 or cetyltrimethylammonium bromide241 create a porous structure through non-spherical simultaneous micelles which act as a pore-forming template in alginate hydrogels. Further, grafting of alginate composites is another important technique to obtain high-performance materials. Various monomers and polymers were used, such as acryl amide,242 tannic acid,243 cyclodextrin, polyacrylamide,244 PVA,245 itaconic acid etc. to enhance the efficiency of alginate-based materials.
Shao et al. have demonstrated 2-acrylamido-2-methylpropa-1-propanesulfonic acid grafted over sodium alginate through hydrogen bonding for the ultrahigh adsorption of methylene blue, which showed a maximum adsorption capacity of 2977 mg g−1.246 Whereas, a polyethyleneimine-grafted MXene incorporated double-network structured alginate aerogel exhibited an ultrahigh adsorption of 3568 mg g−1 for Congo red dye.247 Similarly, ZnO-impregnated PAA-grafted alginate hydrogel and TiO2-impregnated acrylic-acid-grafted alginate hydrogels248 have shown superior adsorption capacities of 1539 mg g−1 and 2257 mg g−1 for cationic methylene blue dye, respectively, attributed to electrostatic interaction between the carboxyl groups of grafted alginate and the high surface area of ZnO.249 Furthermore, various hybrid composites have been prepared by incorporating GO, rGO, CNT,250 or activated carbon251 into the polymeric network to enhance the sorption capacity. A high specific surface area, surface functionality and mechanical stability enhance the performance of alginate-based materials for the separation of dyes, pharmaceutical drugs and pesticides.
GO-functionalised alginate beads showed a maximum adsorption capacity of up to 342.6 mg g−1 for bisphenol A, which is several times higher than conventional adsorbents.252 Recently, calcium-alginate-based membranes have shown a superior adsorption capacity of 3506 mg g−1 for methylene blue dye.253 Significantly, silver-nanoparticle-incorporated alginate-based adsorbents were explored as a point-of-use microorganism disinfectant during the purification of drinking water.254 Similar efforts were made to prepare metal composites255 immobilized alginate composites, such as zeolite,256 boehmite, goethite,256 molecular organic frameworks,257 and magnetic composites. Further, alginate-based catalysts for photocatalytic degradation and AOPs were also demonstrated. In 2000, iron-encapsulated alginate gel beads were demonstrated for the Fenton degradation of orange II dye. Later, in 2005, a chitosan–alginate-based polyelectrolyte microshell constructed via a layer-by-layer self-assembly technique was demonstrated for the photo-assisted Fenton degradation of dye molecules. Over the past decade a renewed interest was observed for the utilisation of alginate for photocatalysis. Efforts were made to immobilise TiO2,258,259 ZnO,260 g-C3N4,261 La(OH)3,262 Ag3PO4,263 and CuO264 into an alginate matrix and their photocatalytic activity was successfully demonstrated. Alginate acts as an efficient dispersive medium and controls the agglomeration of nanocomposite during self-assembly, thus facilitating an excellent degradation reaction. Hence, alginate could be a potential candidate for photodegrdation and AOPs reactions.
4.2 Decontamination of inorganic contaminated water
In general, sodium alginate can form an “egg-box structure” by interacting with multivalent metal ions through a sol–gel precipitation which yields polymer beads.265 Specifically, multivalent metals like Ca(II) have the ability to form guluronate structures like eggs in an egg box, and the alginate chains bind them together with junction zones.266 Over past decades, immense research has been conducted to develop highly functionalised, porous alginate-based materials for the robust separation of inorganic contaminants through adsorption267 and membrane filtration.268 Interestingly, reports have suggested that alginate shows higher adsorption of heavy metal ions than chitosan due to the large number of active adsorption sites.269,270 Various factors affect the binding capacity and affinity of alginate towards heavy metal ions, such as the nature of the pollutants, their net charge, the morphology of the materials, pH, temperature and existing ions in the aqueous medium, and also the functionality and surface area of the materials. Calcium and iron crosslinked alginate-based materials showed a low adsorption capacity for heavy metal ions due to their non-porous surface and low specific surface area.271 Thus, the majority of the work has focused on the modification of alginate by grafting, hybridising with organic or inorganic composites and blending with synthetic or biopolymers. Polyethylenimine-grafted alginate aerogels have exhibited an ultrahigh adsorption capacity for Cr(VI) of 431 mg g−1, whereas the addition of Mxene has enhanced it up to 539 mg g−1.247,272 In another study, 2-acrylamido-2-methylpropa-1-propanesulfonic acid grafted sodium alginate showed a superior adsorption capacity of 2042 mg g−1 for Pb(II) ions.246 Acrylic acid or PAA grafting is the most successful modification strategy to enhance the adsorption capacity of alginate-based materials. PAA-sodium alginate nanofibrous hydrogels have exhibited an excellent adsorption capacity of 591.7 mg g−1 for Cu(II) ions.273 Significantly, a nanofibril-based membrane showed up to 99% separation efficiency with a flux rate of 868 LMH even in a more concentrated solution. It is observed that the thickness of the membrane directly influences the separation efficiency, and excellent rejection was obtained for a membrane with a thickness of 200 μm. Significantly, a 3D macroporous alginate/akaganeite composite aerogel was established as a point-of-use filter for arsenic separation from drinking water with a flux rate of 20–25 mL min−1 under gravity.274 The robust separation from the scaffold is attributed to the efficient adsorption capacity of akaganeite. Further, an GO/alginate-based yttrium-impregnated hydrogel has shown an excellent adsorption capacity of 288.9 mg g−1 for fluoride.275 Also, the hydrogel-based filter has shown excellent separation of fluoride in continuous filtration mode, attributed to a robust ion-exchange reaction between hydroxide groups and fluoride anions, which promises its application to treat fluoride-contaminated water. Yttrium-immobilized GO alginate hydrogels have also shown a maximum adsorption capacity of 273 mg g−1 for As(V), ascribed to H-bonds, electrostatic interaction and π–π interaction.276 Recently, our group demonstrated an aluminium-composite-impregnated chitosan–alginate-based biomaterial scaffold with silver nanoparticles for drinking water and industrial wastewater purification (Fig. 10).277 The aluminium composite provides active adsorption sites, whereas the silver nanoparticles afford an antibacterial property. Notably, the performance of the material was examined through commercializable models, such as teabag-like pouches and a column filter for the separation of fluoride and chromate ions.
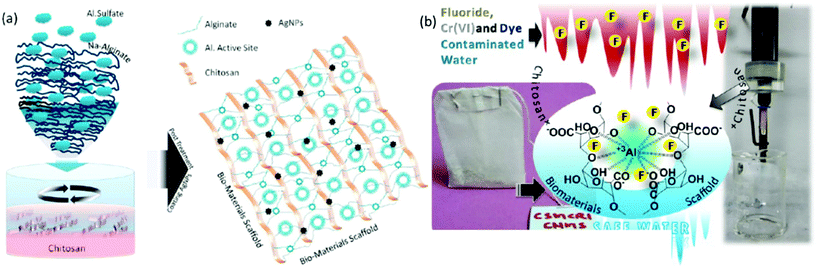 |
| Fig. 10 (a) Schematic representation of the preparation of an aluminium-composite-impregnated sodium alginate and chitosan-based biomaterial scaffold. (b) Shows the application of the bio-composite for the separation of dyes, Cr(VI) and fluoride through a teabag model and a continuous flow method.277 | |
4.3 Oil–water separation
A superhydrophilic alginic-based polymer is a promising candidate for oil–water separation due to its affinity towards water and high absorption capacity. Moreover, alginate gels can be easily converted into porous aerogels by simple supercritical drying or freeze drying. Since alginate exhibits a salt-tolerant property in a marine environment, a group of researchers demonstrated a superoleophobic sodium alginate based aerogel for oil–seawater separation. However, they used cellulose nanocrystals as a filler in order to enhance the mechanical stability of the alginate aerogel. The hybrid aerogel successfully separated oil from an oil–seawater mixture with >99% efficiency along with remarkable recyclability.278 Further, an alginate-based self-cleaning aerogel was reported by immobilising multifunctional TiO2, which exhibited underwater oleophobicity and subsequently up to 99% oil–water separation efficiency.279 Thus, the report successfully addressed the fouling issue by enabling the self-cleaning property. The adsorbed oil molecules can be photocatalytically biodegradable under sunlight, which leads to regeneration of the aerogel surface. Further, a chitosan/alginate hybrid hydrogel and an ampholytic membrane were also demonstrated for oil–water separation.213,280 The hydrogel was prepared by coating chitosan/alginate over a copper mesh and the membrane was obtained by subsequent freeze drying. Significantly, the membrane exhibited >99% oil–water separation efficiency with a flux rate of 680 LMH. Furthermore, efforts were made to produce a highly efficient, durable and renewable aerogel by the incorporation GO into the alginate network.281 The aerogel exhibited underwater super oleophobicity with an oil–water separation efficiency of >99% with a superior flux rate of 3.5 × 103 LMH. Thus, the results suggest that alginate-based aerogels could be a potential solution to cleaning up oil spillages in seawater.
5. Agar/agarose
Agar is the oldest employed phycocolloid which is soluble in boiling water and is mainly used in the synthesis of solid microbiological culture media. It is a hydrophilic polysaccharide extracted from certain red algae and is mainly composed of neutrally charged agarose and charged fraction agaropectin, a composition similar to starch. Commercially, agarose is produced using Gelidium sp. and Gracilaria sp. which exist as a supporting structure in the cellular walls of the seaweeds.282 Among agarose and agaropectin, agarose is a gelling fraction and becomes soluble in near boiling water. Upon cooling, the polymeric chains self-assemble into helical fibers that ultimately aggregate to form a hydrogel.283 Structurally, agarose is a linear polysaccharide with repetitive units of D-galactose and 3,6-anhydro-L-galactose, linked by alternating α-(1,3) and β-(1,4) glycosidic bonds. The presence of active C-2 and C-4 hydroxyl groups makes it an excellent candidate for water purification.284 Areco et al. immobilised Ulva lactuca, in an agar matrix for the biosorption of bivalent heavy metal ions such as copper, zinc, cadmium and lead.285 The dead biomass was dispersed in an aqueous agar medium to prepare an alga/agar composite. However, suspended alga showed better separation efficiency in a fixed-bed assisted continuous flow medium compares to an alga/agar composite. This can be attributed to readily available, freely distributed functionalities of alga in suspended medium enabling superior biosorption. Efforts were made to prepare various organic and inorganic composites of carbon dots,286 Fe, Fe2O3,287 hydroxyapatite288 and organic polymers with agar for the adsorption of pollutants. Li and his group have prepared magnetic agarose microspheres for the separation of radionuclides.287 A stable Fe2O3/agarose composite was formed by chelation with metal ions and it exhibited maximum adsorption capacities of 1.15 mmol g−1 and 1.27 mmol g−1 for U(VI) and Eu(III) radionuclides. Chen et al. synthesised an Fe-agarose nanocomposite and demonstrated its application in the separation of trichloroethylene and Cr(VI).289 The Fe NPs were uniformly distributed inside the agarose hydrogels and reduced Cr(VI) to Cr(III).
Various strategies were developed to prepare excellent agar/agarose-based hydrogels and aerogels for water purification applications. Rani et al. investigated the biosorption capability of agar-based hydrogel.290 The hydrogel was prepared by free radical copolymerization of acrylamide and N,N′-methylene bis-acrylamide which exhibited a remarkable swelling behaviour of up to 550% and superhydrophilicity attributed to the hydrophilic nature of agar molecules. These two properties are the key factors for the biosorption of heavy metal ions. The hydrogel exhibited affinity in the order Fe3+ > Mn2+ > Ni2+ > Cr3+ depending on the atomic radius of the heavy metal ions. Further, the hydrogel also exhibits notable adsorption of methylene blue dye. Interestingly, enhanced dye adsorption was observed from GO-immobilised agar hydrogel.291 This is due to the enriched active sites and high surface area of the GOs. Seow et al. prepared an agarose-based superhydrophilic aerogel by simple freeze drying. The aerogel exhibited considerable adsorption capacity; however, its mechanical strength is unclear.283 In 2014, our group demonstrated a highly crosslinked, novel supe-rhydrophilic agarose/gelatine (9
:
1) based aerogel for sustainable oil–water emulsion separation.210 The genipin crosslinks the cylindrical agarose chain, and phases were separated by non-crosslinked gelatine co-gel. Subsequently, gelatine forms a hydrogen bond with the agarose, which is confirmed by colour changes in the hydrogel. Upon freeze drying, the readily formed ice crystals in the agarose walls sublimated to form hydrophilic channels (Fig. 11).211 As a result, the aerogel membrane exhibited a remarkable rejection of >99% with a flux rate up to 500 LMH for the cross-flow mode oil–water emulsion separation and aqueous–organic solvent mixture.
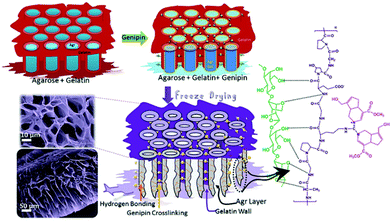 |
| Fig. 11 Schematic representation of genipin crosslinked agarose–gelatine hydrogel formation and superhydrophilic, porous biobased aerogel membrane formation.211 | |
Recently, Wang et al. fabricated a fluorinated, superoleophilic agarose/GO hybrid aerogel with microchannels for the selective absorption of oil. Superhydrophobicity induced by fluorine functionalization enhances the organic solvent absorption up to 187 g g−1. Interestingly, rGO-impregnated agarose hydrogel beads also exhibit superior adsorption of water-soluble organic moieties, including pharmaceutical drugs attributed to π–π interaction with rGO.292 The GO interaction with the carboxyl group of the agarose enabled better dispersion of hydrophobic GO by avoiding aggregation; on other hand, GO acts as a crosslinker to form water-stable agarose beads. The rGO/agarose composite beads exhibit a maximum adsorption capacity of 321.7 mg g−1 for Rhodamine B and 196.4 mg g−1 for aspirin. Whereas the GO/agar-based aerogel with GO content up to 80% exhibits a maximum adsorption capacity of 578 mg g−1 for methylene blue dye with excellent recyclability.293 Agarose aerogel were also used in membrane distillation application. Aerogel will assist in reducing surfactant wetting by avoiding contact of the active membrane with the highly concentrated surfactants.294
Recently, a functional double-layer silver-poly(sodium-p-styrenesulfonate)-agarose gel/agarose gel was demonstrated for solar-assisted water evaporation (Fig. 12).295 The silver-functionalised active agarose top layer induces a solar light–thermal transformation whereas the bottom hydrophilic agarose gel acts as an efficient water-transport medium, leading to excellent water vaporisation of up to 2.1 kg m−2 h−1 under 1-sun illumination. Further, agarose-based hybrid materials were developed with carrageenan,296 polyurethane,297 polyvinyl alcohol,298 and maltodextrin299 for the separation of organic contaminants and also for catalytic reduction. Agar/agarose-based materials were also explored for degradation applications. The carbon-nitride-immobilised agar-based hybrid aerogel showed excellent photodegradation of dyes, antibiotics and phenol.300,301 The hybrid aerogel exhibited superior performance to carbon nitride alone or a 60%-TiO2-agar hydrogel via the synergistic effect of adsorption and photocatalysis. The hybrid hydrogels can be easily recyclable and the active photocatalyst can be straightforwardly recoverable by heat treatment.302 The carbon-nitride-impregnated agarose-based beads also prominently exhibit mercury ion adsorption.303 Further, zeolitic imidazolate framework (ZIF-8) functionalised carbon-nitride-immobilized agar aerogel exhibited superior adsorption of anionic pollutants.304 This strategy of enhancing the activity by avoiding agglomeration of nanocomposites through immobilization in a biopolymeric network promotes potential applications of nanocomposites with poor dispersability. Furthermore, Patra et al. synthesised a bimetallic-functionalised agar-based aerogel as an excellent adsorbent and photocatalyst.305 The agar@Fe/Pd hybrid nanoparticles exhibited maximum adsorption capacities of 875 mg g−1 and 780 mg g−1 for MB and RhB, respectively. The nanocomposite effectively degrading dyes in the presence of BH4− was attributed to redox reactions triggered by the electrons released from the metal composites. In another study, a laccase-immobilized agarose aerogel was demonstrated for bisphenol degradation.306 Excellent degradation of endocrine-disrupting chemicals was obtained even with a small concentration of agarose-supported laccase. Moreover, a degradation efficiency of >90% was retained even after the 15th cycle.
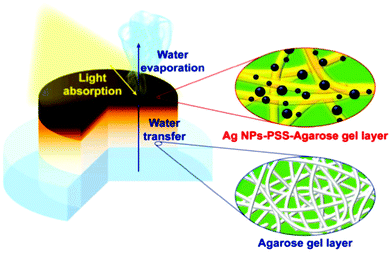 |
| Fig. 12 Schematic representation of agarose-based double-layer hydrogel for solar-assisted water evaporation.295 | |
6. Carrageenan and other seaweed-derived polysaccharides
Carrageenan, fucoidan, and seaweed-derived cellulose are other biomacromolecules explored for water purification applications. Among them, carrageenan is widely utilised for the preparation of functional polymer gels, beads, membranes and nanocomposites. Carrageenan is a unique linear polysaccharide enriched with sulfate functionalities and has the ability to form polyanions. Structurally, carrageenan is made of alternating 1,3 glycosidic-linked β-D-galactopyransose units and 1,4 glycosidic-linked 3,6-anhydro-α-D-galactopyranose units or 1,4 glycosidic-linked α-D-galactopyranose units and is commercially obtained by extraction from certain red seaweeds.307,308 Acrylamide-grafted carrageenan nanocomposites and hydrogels were explored for the adsorption of organic dyes, but a comparatively low adsorption capacity was observed.309,310 Cellulose/carrageenan hybrids were also explored for organic dye and heavy metal ion adsorption; however, the composites exhibit relatively low adsorption.311–313 Thus, various carrageenan-based hybrid materials were prepared with GO,314,315 chitosan,316 alginate, hydroxyapatite,317 polydopamine,318 polyacrylamide,310 TiO2319 and zeolites.320 A GO composite of carrageenan exhibits a high adsorption capacity of 658.4 mg g−1 for malachite green,314 whereas a poly(acrylamide-co-diallyldimethylammonium chloride)-modified aerogel membrane efficiently separates viscous oil and organic dyes with >96% rejection and a flux rate of 40 LMH.315 The high adsorption capacity and the enhanced separation efficiency are due to multifunctional hydrophobic GO. Similarly, an amine-functionalised TiO2-immobilised carrageenan hydrogel exhibits a superior adsorption capacity of 833 mg g−1 for malachite green, attributed to its large surface area, functionality and good affinity.319 Liang et al. demonstrated magnetic Fe2O3/chitosan/carrageenan hybrid macrospheres for the adsorption of dyes and heavy metal ions.316 The magnetic composite displayed notable adsorption capacities of 190 mg g−1, 118 mg g−1, 17.9 mg g−1, and 10.8 mg g−1 for Congo red, methylene blue, Cu(II) and Cr(III), respectively; however, efficient separation was observed in fixed-bed column filtration. Choudhury et al. prepared a poly(N-vinylpyrrolidone-co-acrylic acid)/carrageenan hybrid biocomposite which exhibited high adsorption capacities of 362.5 mg g−1 and 398 mg g−1 for Safranine T and brilliant cresyl blue dye, respectively.321 The hydrophilic –COOH, –OH and sulfate group from acrylic acid and carrageenan provide active sites for efficient adsorption through electrostatic interaction. Interestingly, polydopamine-functionalised carrageenan-based aerogel exhibited a high adsorption capacity for heavy metal ions.318 The terminal amine functionality of polydopamine can form a coordination complex with heavy metal ions and the active sites were further enhanced by the hydroxyl and sulfate groups of carrageenan. The aerogel showed maximum adsorption capacities of 105 mg g−1, 144.9 mg g−1, 133 mg g−1, 158.7 mg g−1, and 128 mg g−1 for Cr(VI), Co(II), Mn(II), Cu(II), and Cd(II), respectively, attributed to high surface area and surface functionalities.
Cellulose is a most abundant, renewable, low-cost biopolymer, mostly extracted from terrestrial plants or biomass. However, cellulose can also be extract from green, red and brown seaweed biomaterials.322 Cellulose is insoluble in water and most common organic solvents; thus cellulose fibres are mostly explored to prepare functional materials. Hamid and group have functionalised seaweed (Avicennia marina) derived cellulose acetate with nano-manganese oxide and utilised it for the adsorption of heavy metal ions.322 Higher adsorption capacities of 82 mg g−1 and 192.8 mg g−1 were obtained for Cd(II) and Pb(II), respectively. Further, Yang et al. demonstrated the application of a seaweed-derived cellulose-based aerogel for solar-assisted water evaporation.323Ulva (Enteromorpha) prolifera derived nanocellulose was crosslinked along with polyvinyl alcohol to form a hydrogel. The self-floating freeze-dried aerogel generated up to 1.4 kg m−2 h−1 water vapour under 1-sun illumination. Thus, nanocellulose was utilised as a building block for high-performance functional materials. Another seaweed-derived macromolecule, fucoidan, was also used for the sorption of heavy metal ions.324–326 Fucoidan is a long polysaccharide enriched with sulfate functional groups. Considerable amounts of Pb(II), Cd(II), Zn(II) and Cu(II) were adsorbed from the fucoidan-based biosorbents, attributed to anionic surface charge and cation exchange capacity.
7. Seaweed-derived carbonaceous materials for water purification
Biomass-derived carbonaceous materials have been extensively explored for various applications because they are economical, environmentally friendly, and can be produced at a large scale. Besides, the valorisation of biomass to produce functional materials is significant over consumption of petroleum-derived products and can be easily commercialized in the near future.327 Moreover, the biomass-derived carbon materials are biodegradable and evidence shows that biomass-derived carbon can potentially substitute high-cost graphene and graphene oxide derivatives, carbon nanotubes and many metal-based nanocomposites. Additionally, one can design and prepare highly porous, heteroatom-doped and metal-doped graphitic carbonaceous materials by carefully choosing a suitable biomass with additional functionalities of interest.328,329 They are generally prepared by hydrothermal carbonization or high-temperature pyrolysis or both. In the literature, the majority of biochars reported are obtained from terrestrial lingo-cellulosic feedstocks, which generally yield a carbonaceous product with a C-content of more than 70% with low or negligible nutritive value.13 It is necessary to induce auxiliary chemicals to obtain carbon with functionalities. For the first time, Zerban and Freeland (1918) prepared biochar from the seaweed Macrocystis pyrifera by heating it to about 800–900 °C for the decolourisation of molasses. However, over the past decade, marine-derived biomaterials have been widely used as carbon precursors for the preparation of multifunctional carbonaceous materials with several advantages. Marine-based biomaterials are inherently enriched with heteroatom-based functionalities and metal ions make them excellent candidates for the preparation of multifunctional carbon.330 Due to an excessive metal ion content and integrated heteroatom functionalities, they are vastly used for the template-free synthesis of highly porous carbon, while the gases liberated during the pyrolysis create a mesoporous structure, thus avoiding additional reagents for activation.331 Interestingly, they have also been utilised for the production of graphene/graphitic carbon for various applications, such as energy storage and conversion, as highly efficient adsorbents,332 and for CO2 capture and sensors. However, the present review focuses on the design and development of functional carbonaceous materials for use in efficient water purification.
Various research groups have utilised raw seaweeds to prepare carbonised products due to the presence of significant amounts of metal ions, such as K, Na, Ca, Zn, Mg and Fe, along with heteroatoms such N and P.32 Additionally, seaweeds are abundant, and thus advantageous in terms of cost and labour for commercial production. Due to the presence of metal ions, hierarchical porous carbons can be obtained by simple acid washing after the pyrolysis.333 Substantially, the obtained product will also be doped with heteroatoms, which is beneficial for several applications. However, a study showed that the carbonized product obtained from brown-seaweed-based species possesses higher C and H contents and lower S content than red-seaweed-derived biochar.13 Thus various strategies have been developed to tune the physico-chemical properties of carbonaceous materials, such as porosity, metal ion doping and heteroatom doping, and their efficiencies in adsorbing dyes,13 heavy metal ions and other pollutants are discussed below and are summarised in Table 2.
Table 2 Seaweed and seaweed-derived high-performance carbonaceous materials explored for water purification applications
Sl. no. |
Biomaterial |
Preparation condition |
Doping |
Surface area |
Performance of material |
Ref. |
01 |
Kelp biomass |
(i) Pyrolysis at 500 °C for 1.5 h; (ii) KOH activation at 600–900 °C, for 2 h followed by acid wash |
N-Doped carbon |
977–1900 m2 g−1 |
≈100% degradation of 40 mg L−1 ofloxacin in 60 min |
376
|
02 |
Enteromorpha biomass |
(i) Pyrolysis at 500 °C for 1.5 h; (ii) KOH activation at 600–900 °C, for 1 h followed by acid wash |
Fe/N-carbon |
Up to 983 m2 g−1 |
≈100% degradation of paracetamol in 250 s |
343
|
03 |
Enteromorpha
|
Pyrolysis at 500, 700 or 900 °C for 2 h |
Fe/N/C |
— |
Selective and powerful nonradical oxidation |
328
|
04 |
Enteromorpha prolifera
|
Single-step KOH activation and pyrolysis at 700 °C for 1 h followed by acid wash |
— |
1262 m2 g−1 |
Max. adsorption of 910 mg g−1 for methylene blue |
344
|
05 |
Enteromorpha
|
(i) Pyrolysis at 400 °C for 1.5 h; (ii) K2CO3 activation at 500–900 °C, for 2 h followed by acid wash |
N-Doped carbon |
979–2641 m2 g−1 |
>95% degradation of 5 mg L−1 sulfamethoxazole (100 mL) in 90 min |
377
|
06 |
Enteromorpha prolifera
|
(i) Functionalisation of seaweed with Fe(OH)3; (ii) pyrolysis at 400 & 800 °C for 2 h |
γ-Fe2O3-Carbon |
708–780 m2 g−1 |
Max. adsorption of 95.23 mg g−1 for Cr(VI) |
378
|
07 |
Spirulina
|
Pyrolysis at 400, 700 or 900 °C for 1.5 h followed by acid wash |
N-Doped carbon |
370 m2 g−1 |
Inactivating Escherichia coli via nonradical oxidation |
369
|
08 |
Ulva fasciata + FeCl3 |
Pyrolysis at 800 °C for 2 h |
Fe/FeS-carbon |
139.7 –376.8 m2 g−1 |
Max. adsorption of 645 ± 10 mg g−1 for Pb(II), 100 mg g−1 for Cr(VI), 970 mg g−1 for Congo red, 909 mg g−1 for crystal violet, 664 mg g−1 for methyl orange, 402 mg g−1 for methylene blue. |
339
|
09 |
Sargassum tenerrimum
|
Choline chloride + FeCl3/SnCl3/ZnCl3 activation and pyrolysis at 700–900 °C for 2 h |
Fe, Zn, Sn-carbon |
132–331.7 m2 g−1 |
Max. adsorption of 75.5 mg g−1 for fluoride |
332
|
10 |
Ascophyllum nodosum
|
KOH-treated hydrothermal carbon prepared at 200 °C for 10 min |
Ca-carbon |
11.3 m2 g−1 |
Max. adsorption of 12.3 mg g−1 for vanadium(V) |
379
|
11 |
Ulva lactuca, Ulva reticulata and Caulerpa scalpelliformis |
Pyrolysis at 300 or 500 °C for 2 h |
— |
— |
Up to 140.5 mg g−1 for remazol dyes |
330
|
12 |
Carrageenan |
(i) Hydrothermal treatment at 200 °C for 20 h; (ii) KOH activation at 700 °C for 4 h followed by acid wash |
— |
2800 m2 g−1 |
Max. adsorption of 459 mg g−1 for ciprofloxacin |
335
|
13 |
Chitosan |
(i) Hydrothermal treatment at 170–210 °C for 20 h; (ii) pre-carbonized at 300 °C for 30 min; (iii) carbonized at 600–800 °C for 2 h followed by acid wash |
— |
521–2464 m2 g−1 |
Max. adsorption of 1599 mg g−1 for methylene blue |
337
|
14 |
Chitosan |
(i) Freeze drying; (ii) KOH activation at 800 °C for 3 h followed by acid wash |
N-Doped carbon |
1756 m2 g−1 |
Removes 20 mg bisphenol A within 10 min |
338
|
15 |
Chitosan + FeCl3 |
Hydrothermal treatment at 180 °C for 48 h |
Fe2O3-C |
59.6 m2 g−1 |
Max. adsorption of 1.54 mmol g−1 for Cu(II), and 2 mmol g−1 for Cr(VI) |
380
|
16 |
Chitosan + FeCl3 |
(i) Freeze drying; (ii) KOH activation at 600–800 °C for 2 h |
N/Fe2O3-C |
250–600 m2 g−1 |
Max. adsorption of 263 mg g−1 mg g−1 for Cr(VI) |
381
|
17 |
Calcium alginate |
Pyrolysis at 400, 600 or 800 °C for 2 h followed by acid wash |
— |
112–405 m2 g−1 |
Max. adsorption of 56 mg g−1 for Cr(VI) |
382
|
18 |
Calcium alginate hydrogel |
Pyrolysis at 500, 800 or 1000 °C for 2 h |
— |
221.7–310.8 m2 g−1 |
Max. adsorption of 7059 mg g−1 for malachite green, 2390 mg g−1 for crystal violet, and 6964 mg g−1 for acid fuchsin |
383
|
19 |
Sodium alginate + melamine + Co(NO3)2 |
Pyrolysis at 500, 600, 700, 800 or 900 °C for 2 h |
N/Co/C |
207.1 m2 g−1 |
Excellent degradation of ponceau, p-nitrophenol and tetracycline, methylene blue in 5 min |
371
|
20 |
Cellulose/collagen + FeCl3 |
(i) Freeze drying; (ii) pyrolysis 550 or 900 °C for 2 h; and (iii) KOH activation at 800 °C for 2 h |
N-Doped carbon |
664.3 m2 g |
Max. adsorption of 238.2 mg g−1 for malachite green and 230.4 mg g−1 for methylene blue |
367
|
7.1 Porous carbonaceous materials
An increase in demand for high-performance sustainable materials has generated tremendous efforts in the areas of design and the synthesis of multifunctional porous carbons. Various techniques, such as hydrothermal treatment followed by high-temperature pyrolysis, acid washing, KOH activation, and template-assisted carbonization have been demonstrated to prepare porous carbonaceous materials. Marine-based biomaterials, especially seaweeds, naturally containing metal ions can help to create a porous structure after calcination assisted by acid washing.328 However, carbonization of seaweed-derived materials, such as carrageenan, chitosan and alginate, produces highly porous carbon with a remarkable specific surface area compared to the biomass itself. For example, Li et al. developed S-doped carbon with a highest surface area of 4037 m2 g−1 by carbonizing an Fe-carrageenan aerogel followed by KOH activation at 800 °C.334 An aerogel with a natural porous structure was carbonized up to 600 °C followed by acid washing to remove iron sulfides, yielding a nanoporous structure. Further, KOH activation at 800 °C enhances the porosity to produce a carbonaceous material with the highest specific surface area. In another study, single-step KOH activation of hydrothermally derived carrageenan carbon produced porous carbon materials with a surface area of 2800 m2 g−1 which is superior to the surface area of commercial activated carbons.335 The obtained carbon exhibits a maximum adsorption capacity of 459 mg g−1 for the drug ciprofloxacin, which is several times higher than commercial adsorbents. On the other hand, Liang and group synthesised porous carbon materials with an ultrahigh surface area of 3532 m2 g−1 by two-step carbonization.336 Firstly, it was hydrothermally treated at 200 °C for 2 h followed by KOH activation and carbonization which led to the nanoporous structure. Deng et al. attempted to prepare high surface area carbon by three-step carbonization using chitosan.337 Firstly, spherical carbon was prepared by hydrothermal treatment. During the process, acid-catalysed depolymerisation and hydrolysis of glycosidic linkage was followed by condensation polymerisation, resulting in spherical hydrochars. Further, annealing at high temperature results in a hierarchical honeycomb-like structured carbon with a high surface area of 2464 m2 g−1. Significantly, the carbon materials displayed an ultrahigh adsorption capacity up to 1599 mg g−1 for methylene blue. With a similar procedure, alginate yielded a porous carbon with a notable specific surface area of 749.2 m2 g−1.32 Further, Xu et al. prepared hierarchical porous structured carbon with a surface area 1756 m2 g−1 through rapid freezing-assisted carbonization.338 The material exhibited a remarkable separation efficiency for emerging pollutants such as bisphenol A. Interestingly, the material also exhibited excellent electrical conductivity.
Numerous raw seaweed biomaterials were also carbonized to obtain highly porous carbon. The carbonization of raw biomass is economically significant, since it involves simple pre-treatments such as washing and drying. Our group has developed porous carbon with a notable specific surface area from Ulva fasciata and Sargassum tenerrimum for the adsorption of dyes, heavy metal ions and fluoride from an aqueous medium.332,339 Recently, we have demonstrated a single-step synthesis of exfoliated carbon nanosheets with a notable surface area of 700 m2 g−1 using Salicornia brachiate (Fig. 13).340 The inherent salt creates meso- and microporosity; moreover, it assists the exfoliation of carbon materials and avoids the stacking of graphene sheets. Considerably, the carbon displayed remarkable adsorption capacity for heavy metal ions. Similarly, various seaweeds, such as kelp biomass, marine macro-algae, Enteromorpha prolifera341 and Enteromorpha biomass were also developed as low-cost precursors for the synthesis of porous carbon and their application in water purification was explored.342–344
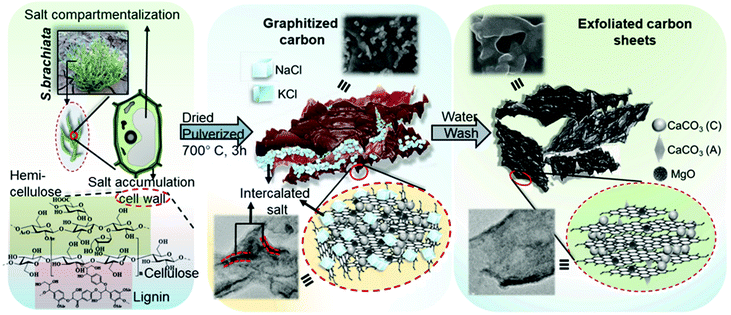 |
| Fig. 13 Schematic representation of the complete process for the fabrication of porous carbon nanosheets from Salicornia brachiata biomass.340 | |
7.2 Heteroatom-doped carbonaceous materials
Heteroatom-doped carbon materials are interesting candidates for energy storage and conversion, water purification, catalysis and many other applications. Heteroatoms such as N, S and P have different atomic orbitals, atomic radii and electronegativity, providing active sites, which greatly enhance the performance of carbon materials for various applications. Thus, remarkable efforts have been made to prepare heteroatom-doped materials using various biomasses, especially those inheriting such functionalities. Marine-derived biomaterials naturally have a large number of amine, phosphate and sulfate functionalities and are excellent candidates to prepare heteroatom-doped carbon without the aid of external chemicals.
For the first time Titirici and group demonstrated the hydrothermal synthesis of nitrogen-containing carbon by using chitosan as a carbon and nitrogen source.345 Chitosan is naturally rich in nitrogen content (∼7 wt%) due to amine and acetamide groups in its structure, making it a promising candidate to prepare carbon materials containing an N-content up to 7–13 wt%.346 Significantly, annealing of chitosan-based materials provides pyridinic-N, pyrrolic-N and graphitic N-doped carbon materials (Fig. 14).347 Various attempts were made to prepare N-doped carbon with mesoporosity by high-temperature pyrolysis treatment;348,349 however, the nitrogen content was comparatively low, which may account for the high-temperature treatment.350 Interestingly, one can enhance the N-content in carbon materials even under temperature treatment by introducing additional chemicals during the pyrolysis.351,352 The reports suggested that an increase in the carbonization temperature leads to a substantial decrease in N-content.353 Nitrogen functionalities of chitosan are known to coordinate with metal ions, suggesting the application of N-doped carbon in water purification applications. Zhong et al. explored the adsorption capacity of hydrothermal carbon obtained from chitosan for radioactive elements. The N-doped carbon exhibited a maximum adsorption capacity of 273 mg g−1 for U(VI).354,355 Further, the adsorption efficiency was increased up to 408 mg g−1 by an ion-imprinted technique before hydrothermal treatment which enhanced the selectivity for the target ion.355
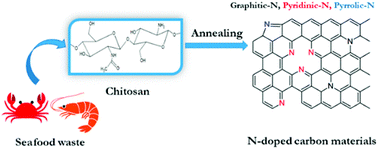 |
| Fig. 14 Pyrridinic, pyrrolic and graphitic N-doped carbonaceous materials derived from chitosan.347 | |
Later, Shen et al. prepared N-doped carbon by hydrothermally treating chitosan from 130 °C to 220 °C and investigated the effect of reaction temperature on tuning the physico-chemical properties of N-doped carbon.356 Significantly, HTC prepared at 160 °C showed superior adsorption capacity which decreased with an increase in temperature. Notably, incomplete carbonization of chitosan was observed when hydrothermally treated at 140 °C. Further, numerous N-doped activated carbons were explored for their adsorption capacity of dyes,357 phenolic pollutants,358 heavy metal ions and, also, gaseous pollutants.356,359 Hameed et al. reported the one-step preparation of porous N-doped carbon by impregnating NaOH into the chitosan flakes and then carbonizing them at high temperature followed by an acid wash.360 The obtained mesoporous activated carbon exhibited a considerable uptake capacity of 143.5 mg g−1 for methylene blue dye; however, in later studies, KOH-activated N-doped carbon showed an excellent adsorption capacity up to 926 mg g−1 for malachite green dye.357 In another study, a graphitic N-doped highly porous carbon aerogel was prepared from chitosan using KOH activation.338 The material behaved as an excellent adsorbent and catalyst for the degradation of phenolic contaminants. Further, ZnCl2-activated carbon was utilised as an efficient adsorbent for various phenolic pollutants and showed a maximum adsorption capacity of 893 mg g−1 for 2,4-dichlorophenol.358 The excellent adsorption capacity of these carbon materials is attributed to the increase in surface polarities, enhanced porosity and improved active sites within the carbon framework. Thus, auxiliary chemicals greatly affect the adsorption capacity of carbon. Interestingly, N-doped carbons were also explored as electrocatalysts for H2O2 electrosynthesis for direct application in Fenton-based electrochemical water treatments.346,351 Although it was not an optimum electrocatalyst, it was demonstrated to be a potentially low-cost and eco-friendly material for water treatment.
Apart from chitosan, various seaweeds, for example, Ulva fasciata,339,361,362Spirulina, Enteromorpha,342,363Lessonia nigrescens, Meristhoteca senegalensis,364 and many seaweed-derived biomaterials, such as alginates,365 carrageenans366 and collagen367 were utilised for the preparation of S,N-doped carbon with or without auxiliary chemicals.368 Chen and group prepared self-N-doped biochar from Spirulina residue for non-radical oxidation of Escherichia coli bacteria.369 Huang et al. prepared N-doped graphitic carbon material from kelp for peroxymonosulfate activation.343 The catalytic degradation process followed the combined reaction of both radical and non-radical pathways of degradation of ciprofloxacin with excellent recyclability and, importantly, independent of metal elements. In both studies, biochar played a versatile role in the activation of peroxysulfate via an electron transfer regime. On the other hand, carrageenan is a naturally sulfate-rich biopolymer; but the carrageenan-derived carbonaceous materials did not possess a significant amount of sulfur. Thus, intensive research efforts were made to functionalise it with metal nanocomposites.
7.3 Metal-doped carbonaceous materials
Carbonaceous materials reinforced with metal nanocomposites show excellent physico-chemical properties for multifunctional applications. In an attempt to prepare a highly porous carbon, our group has demonstrated the scalable production of Fe3O4/Fe-doped graphene carbon by soft-template-assisted pyrolysis using Sargassum tenerrimum (a brown seaweed).332 Various metal-based deep eutectic solvents were used as soft templates to prepare porous graphene sheets. The deep eutectic solvent acts as a template to create porous carbon and also acts as source of metal ions to prepare Fe, Zn and Sn doped carbon materials (Fig. 15).332
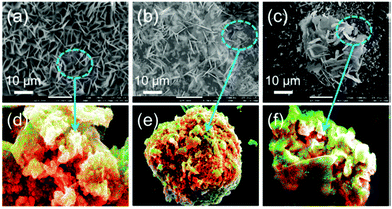 |
| Fig. 15 (a–c) SEM images and (d–f) elemental mapping of graphene-like carbon material obtained by treating Sargassum tenerrimum with iron, tin and zinc based DES, respectively.332 | |
Further, the obtained carbonaceous material exhibited a high surface area and showed a considerable amount of fluoride adsorption from fluoride-rich groundwater attributed to the cationic surface charge.332 Interestingly, the iron-functionalised carbon exhibits a magnetic property, making it easy to recover from the aqueous medium. We have demonstrated the solvent-free synthesis of graphitic carbon via one-step pyrolysis of Ulva fasciata in the presence of FeCl3 as a templating agent and iron precursor.339 At elevated temperature, the sulfur-rich biomass has a tendency to convert into sulfides; thus, the carbon materials were doped nanostructured Fe/FeS. The porous graphitic carbon showed superior adsorption efficiency for dyes and heavy metal ions. Further, Enteromorpha biomass largely containing iron in its structure was widely explored to prepare Fe-doped carbon. The iron composite in the carbon structure provides active sites for adsorption and also efficiently activates peroxysulfate for radical and nonradical assisted advanced oxidation processes.328,342 Lin et al. prepared non-zero-valent iron-based carbon material (Fe0/Fe3C) for adsorption and degradation applications by pyrolising alginate.376 At low temperature (<500 °C), Fe2O3/Fe3O4 was formed and transformed into Fe3S when heated to >700 °C. Apart from iron composites, titanium oxide,366,370 cobalt oxide,371,374 zinc oxide,372 magnesium oxide,373 and silver nanoparticle375 doped carbonaceous materials were prepared using seaweed or seaweed-derived biomaterials. Generally, metal salts were added as auxiliary chemicals prior to carbonizing, which act as both template and source of metal ion. For example, our group fabricated a TiO2-functionalised carbonaceous photocatalyst using carrageenan for solar-assisted degradation. Interestingly, the surface of the carbon materials is enriched by Brønsted acidic sites caused by sulfur doping, enhancing the photocatalytic activity.366 The catalyst exhibited complete degradation of dyes within 3–4 h; however, upon using a solar concentrator, the degradation time was reduced to <5 min. Further, Zhao et al. demonstrated Co/N-doped carbon by chelating cobalt with sodium alginate prior to carbonization for advanced oxidation processes.371 The bivalent cobalt releases an electron to produce a sulfate radical for degradation of organic molecules in a short interval. Thus, a synergistic combination of an active metal composite with a low-cost functional carbonaceous material shows promising applications in sustainable water purification. Overall, the carbonaceous materials obtained from marine-derived materials are promising candidates for environmental applications because they are economical, biodegradable and can be recyclable.
8. Future prospect and conclusions
In sum, marine-derived functional biomaterials are excellent candidates for sustainable water purification applications, attributed to in-built surface functionalities and tunable features. Moreover, they are abundant, renewable, and hence, low-cost and biodegradable. Significantly, huge research development in marine-derived functional materials was accomplished by addressing sustainable water purification. About 70% of the Earth's surface is covered by ocean and this signifies a vast resource of biodiversity. Hence, much attention has been focused on the effective utilisation of marine-derived biomaterials, such as seaweed and chitin, and seaweed-derived macromolecules, such as alginate, agarose, and carrageenan as promising sustainable candidates for water purification. On the other hand, marine-derived materials were also utilised as low-cost feedstocks to prepare valuable multifunctional carbonaceous materials with high porosity, remarkable surface functionality, and metal-functionalised carbon for various applications. Even with the extensive development of highly efficient biosorbents, membranes, and photocatalysts, the materials failed to transfer into commercial application due to complicated implementation and economic feasibility in large-scale operation. Most of the experimental results are predominantly limited to a laboratory scale and fail to be reproduced under flexible environmental conditions. Further, pilot-scale applications of these materials are inadequate for the following reasons:
i. Although seaweeds are low-cost, abundant biosorbents, their poor physical and chemical instability causes the leaching of chemical moieties into the aqueous medium, limiting their practical application. Also, the efficient recyclability of seaweeds remains a challenge.
ii. Chitosans are eco-friendly, non-toxic biodegradable polymers which can potentially substitute conventional synthetic polymers; but their solubility in an acidic medium and nonporous composites limits their large-scale application.
iii. Besides being hydrophilic, the main drawback with chitosan, alginate and agarose-based materials is their propensity to swell.
iv. Generally, partial desorption of contaminants was observed due to the enriched surface hetero-functionality; thus, complete regeneration of composites is challenging.
v. Further, chitosan, alginate and agarose-based materials exhibit comparably low mechanical strength, which requires blending with mechanically stable polymers.
By addressing these shortcomings, one can design and significantly develop highly efficient materials for point-of-use sustainable wastewater treatment in the near future. It is notable that the majority of reports are based on empirical approaches and lack molecular-level design. Marine biodiversity includes thousands of seaweed species, exploration of which from various geographical locations could identify additional biomaterials with better structural stability, mechanical strength etc. Thus, relevant strategies urgently need to be developed. In addition, the potential of other marine-derived biomaterials and their combinations might be evaluated for water purification applications. On the other hand, carbonaceous materials derived from marine-derived biomaterials exhibit a graphitic nature, high porosity and surface functionality, which could potentially substitute high-cost carbonaceous materials, such as graphene derivatives and carbon nanotubes, for water purification applications. However, very few and a specific class of seaweed-based biopolymers have been explored as sources for biochar and advanced functional 2D carbon materials. Given the diversity of seaweeds, marine invertebrates, and several other carbon resources, it is imperative to broaden the applicability of such abundant resources for the task-specific conversion of functional 2D carbon materials for facile water purification and beyond. Similarly, seaweed-based biopolymer hybrids show excellent performance in solar-assisted water steam generation applications, attributed to the hydrophilicity and high water vapour permeability of the polymers. Although considerable work has been accomplished in the development of marine-derived functional biomaterials for water purification, much work is particularly required to establish their potential application to meet current demand.
Conflicts of interest
There are no conflicts to declare.
Acknowledgements
DM thanks RSC Research fund grant (R21-9087288636) for financial support. SKN acknowledge Nanomission Project SR/NM/NT-1073/2016, and Talent Attraction Programme funded by the Community of Madrid (2017-T1/AMB5610).
Notes and references
- Y. Zhu, C. Romain and C. K. Williams, Nature, 2016, 540, 354–362 CrossRef CAS PubMed.
- A. Gandini, T. M. Lacerda, A. J. F. Carvalho and E. Trovatti, Chem. Rev., 2016, 116, 1637–1669 CrossRef CAS PubMed.
- Z. Wang, M. S. Ganewatta and C. Tang, Prog. Polym. Sci., 2020, 101, 101197 CrossRef CAS.
- D. M. Alonso, J. Q. Bond and J. A. Dumesic, Green Chem., 2010, 12, 1493–1513 RSC.
- R. A. Sheldon, Green Chem., 2014, 16, 950–963 RSC.
- Z. Wang, D. Shen, C. Wu and S. Gu, Green Chem., 2018, 20, 5031–5057 RSC.
- W.-J. Liu, H. Jiang and H.-Q. Yu, Chem. Rev., 2015, 115, 12251–12285 CrossRef CAS PubMed.
- D. Kai, M. J. Tan, P. L. Chee, Y. K. Chua, Y. L. Yap and X. J. Loh, Green Chem., 2016, 18, 1175–1200 RSC.
- A. K. Mohanty, M. Misra and L. T. Drzal, J. Polym. Environ., 2002, 10, 19–26 CrossRef CAS.
- A. A. Koutinas, A. Vlysidis, D. Pleissner, N. Kopsahelis, I. L. Garcia, I. K. Kookos, S. Papanikolaou, T. H. Kwan and C. S. K. Lin, Chem. Soc. Rev., 2014, 43, 2587–2627 RSC.
- M. Jin, Y. Gai, X. Guo, Y. Hou and R. Zeng, Mar. Drugs, 2019, 17, 656 CrossRef CAS PubMed.
- M. H. Centella, A. Arévalo-Gallegos, R. Parra-Saldivar and H. M. N. Iqbal, J. Cleaner Prod., 2017, 168, 1559–1565 CrossRef CAS.
- D. A. Roberts, N. A. Paul, S. A. Dworjanyn, M. I. Bird and R. de Nys, Sci. Rep., 2015, 5, 9665 CrossRef CAS PubMed.
-
Á. M. Mathiesen, Food and Agriculture Organization of the United Nations, 2015 Search PubMed.
- M. A. Hashim and K. H. Chu, Chem. Eng. J., 2004, 97, 249–255 CrossRef CAS.
- K. Vijayaraghavan, J. Jegan, K. Palanivelu and M. Velan, Sep. Purif. Technol., 2005, 44, 53–59 CrossRef CAS.
- G. Pablo, J. S. Gomes-Dias, C. M. Rocha, A. Romaní, G. Garrote and L. Domingues, Bioresour. Technol., 2020, 299, 122613 CrossRef PubMed.
- H. L. Parker, J. R. Dodson, V. L. Budarin, J. H. Clark and A. J. Hunt, Green Chem., 2015, 17, 2200–2207 RSC.
- D. Kühbeck, G. Saidulu, K. R. Reddy and D. D. Díaz, Green Chem., 2012, 14, 378–392 RSC.
- X. Wu, W. Xing, J. Florek, J. Zhou, G. Wang, S. Zhuo, Q. Xue, Z. Yan and F. Kleitz, J. Mater. Chem. A, 2014, 2, 18998–19004 RSC.
- M. Y. Song, H. Y. Park, D. S. Yang, D. Bhattacharjya and J. S. Yu, ChemSusChem, 2014, 7, 1755–1763 CrossRef CAS PubMed.
- S. K. Nataraj, C.-H. Wang, H.-C. Huang, H.-Y. Du, S.-F. Wang, Y.-C. Chen, L.-C. Chen and K.-H. Chen, ChemSusChem, 2012, 5, 392–395 CrossRef CAS PubMed.
- S. Ling, W. Chen, Y. Fan, K. Zheng, K. Jin, H. Yu, M. J. Buehler and D. L. Kaplan, Prog. Polym. Sci., 2018, 85, 1–56 CrossRef CAS PubMed.
- H. M. Manohara, K. Aruchamy, S. Chakraborty, N. Radha, M. R. Nidhi, D. Ghosh, S. K. Nataraj and D. Mondal, ACS Sustainable Chem. Eng., 2019, 7, 10143–10153 CrossRef CAS.
- V. T. Sharma, H. M. Manohara, S. V. Kamath, D. Mondal and S. K. Nataraj, Chemosphere, 2020, 259, 127421 CrossRef CAS PubMed.
- S. Bandehali, H. Sanaeepur, A. E. Amooghin, S. Shirazian and S. Ramakrishna, Sep. Purif. Technol., 2021, 269, 118731 CrossRef CAS.
- J. R. Dodson, H. L. Parker, A. M. García, A. Hicken, K. Asemave, T. J. Farmer, H. He, J. H. Clark and A. J. Hunt, Green Chem., 2015, 17, 1951–1965 RSC.
- G. Fadillah, O. A. Saputra and T. A. Saleh, Trends Environ. Anal. Chem., 2020, 26, e00084 CrossRef CAS.
- J. R. Dodson, H. L. Parker, A. M. García, A. Hicken, K. Asemave, T. J. Farmer, H. He, J. H. Clark and A. J. Hunt, Green Chem., 2015, 17, 1951–1965 RSC.
- M. Nasrollahzadeh, M. Sajjadi, S. Iravani and R. S. Varma, Carbohydr. Polym., 2020, 116986 Search PubMed.
- N. Shi, X. Li, T. Fan, H. Zhou, J. Ding, D. Zhang and H. Zhu, Energy Environ. Sci., 2011, 4, 172–180 RSC.
- D. Mondal, M. Sharma, C.-H. Wang, Y.-C. Lin, H.-C. Huang, A. Saha, S. K. Nataraj and K. Prasad, Green Chem., 2016, 18, 2819–2826 RSC.
- H. Harrysson, M. Hayes, F. Eimer, N.-G. Carlsson, G. B. Toth and I. Undeland, J. Appl. Phycol., 2018, 30, 3565–3580 CrossRef CAS.
- S. Wang, S. Zhao, B. B. Uzoejinwa, A. Zheng, Q. Wang, J. Huang and A. E.-F. Abomohra, Energy Convers. Manage., 2020, 222, 113253 CrossRef CAS.
- V. Murphy, H. Hughes and P. McLoughlin, Water Res., 2007, 41, 731–740 CrossRef CAS PubMed.
- R. H. Vieira and B. Volesky, Int. Microbiol., 2000, 3, 17–24 CAS.
-
C. Ortiz-Calderon, H. C. Silva and D. B. Vásquez, Biomass volume Estimation and Valorization for energy, 2017 Search PubMed.
- M. M. Figueira, B. Volesky, V. S. T. Ciminelli and F. A. Roddick, Water Res., 2000, 34, 196–204 CrossRef CAS.
-
B. Volesky and N. Kuyucak, Google Patents, 1988 Search PubMed.
- P. X. Sheng, Y. P. Ting, J. P. Chen and L. Hong, J. Colloid Interface Sci., 2004, 275, 131–141 CrossRef CAS PubMed.
- P. X. Sheng, Y.-P. Ting and J. P. Chen, Ind. Eng. Chem. Res., 2007, 46, 2438–2444 CrossRef CAS.
- V. Murphy, H. Hughes and P. McLoughlin, Chemosphere, 2008, 70, 1128–1134 CrossRef CAS PubMed.
- N. Kuyucak and B. Volesky, Biotechnol. Bioeng., 1989, 33, 823–831 CrossRef CAS PubMed.
- Y. Suzuki, T. Kametani and T. Maruyama, Water Res., 2005, 39, 1803–1808 CrossRef CAS PubMed.
- Q. Yu and P. Kaewsarn, Sep. Sci. Technol., 2000, 35, 689–701 CrossRef CAS.
- J. T. Matheickal, Q. Yu and G. M. Woodburn, Water Res., 1999, 33, 335–342 CrossRef CAS.
- J. T. Matheickal and Q. Yu, Bioresour. Technol., 1999, 69, 223–229 CrossRef CAS.
- G. R. de Freitas, M. G. A. Vieira and M. G. C. da Silva, Ind. Eng. Chem. Res., 2018, 57, 11767–11777 CrossRef CAS.
-
J. Yang and B. Volesky, in Process Metallurgy, ed. R. Amils and A. Ballester, Elsevier, 1999, vol. 9, pp. 483–492 Search PubMed.
- H. Omar, A. Abdel-Razek and M. Sayed, J. Nat. Sci., 2010, 8, 214–221 Search PubMed.
- F. Deniz and A. Karabulut, Ecol. Eng., 2017, 106, 101–108 CrossRef.
- A. Essekri, N. Aarab, A. Hsini, Z. Ajmal, M. Laabd, M. El Ouardi, A. Ait Addi, R. Lakhmiri and A. Albourine, J. Dispersion Sci. Technol., 2020, 1–14 CrossRef.
- M. Kousha, E. Daneshvar, M. S. Sohrabi, M. Jokar and A. Bhatnagar, Chem. Eng. J., 2012, 192, 67–76 CrossRef CAS.
- T. A. Davis, B. Volesky and R. H. S. F. Vieira, Water Res., 2000, 34, 4270–4278 CrossRef CAS.
- V. J. P. Vilar, C. M. S. Botelho and R. A. R. Boaventura, Water Res., 2006, 40, 291–302 CrossRef CAS PubMed.
- V. J. Vilar, J. M. Loureiro, C. M. Botelho and R. A. Boaventura, J. Hazard. Mater., 2008, 154, 1173–1182 CrossRef CAS PubMed.
- R. Angelova, E. Baldikova, K. Pospiskova, Z. Maderova, M. Safarikova and I. Safarik, J. Cleaner Prod., 2016, 137, 189–194 CrossRef CAS.
- P. Balaraman, B. Balasubramanian, D. Kaliannan, M. Durai, H. Kamyab, S. Park, S. Chelliapan, C. T. Lee, V. Maluventhen and A. Maruthupandian, Waste Biomass Valorization, 2020, 11, 5255–5271 CrossRef CAS.
- C. Zhang, P.-L. Show and S.-H. Ho, Bioresour. Technol., 2019, 289, 121700 CrossRef CAS PubMed.
- C. Zhang, C. Wang, G. Cao, D. Wang and S.-H. Ho, J. Hazard. Mater., 2020, 388, 121773 CrossRef CAS PubMed.
- D. Aderhold, C. J. Williams and R. G. J. Edyvean, Bioresour. Technol., 1996, 58, 1–6 CrossRef CAS.
- B. R. C. Vieira, A. M. A. Pintor, R. A. R. Boaventura, C. M. S. Botelho and S. C. R. Santos, J. Environ. Manage., 2017, 192, 224–233 CrossRef CAS PubMed.
- S. Z. Rogovina, C. V. Alexanyan and E. V. Prut, J. Appl. Polym. Sci., 2011, 121, 1850–1859 CrossRef CAS.
- K. Kurita, Mar. Biotechnol., 2006, 8, 203 CrossRef CAS PubMed.
- D. Elieh-Ali-Komi and M. R. Hamblin, Int. J. Adv. Res., 2016, 4, 411–427 CAS.
- P. Sahariah and M. Másson, Biomacromolecules, 2017, 18, 3846–3868 CrossRef CAS PubMed.
- F. Hoppe-Seyler, Ber. Dtsch. Chem. Ges., 1894, 27, 3329–3331 CrossRef CAS.
- C. P. Jiménez-Gómez and J. A. Cecilia, Molecules, 2020, 25, 3981 CrossRef PubMed.
- P. Samoila, A. C. Humelnicu, M. Ignat, C. Cojocaru and V. Harabagiu, Chitin Chitosan: Prop. Appl., 2019, 429–460 Search PubMed.
- R. A. Muzzarelli and O. Tubertini, Talanta, 1969, 16, 1571–1577 CrossRef CAS PubMed.
- M. S. Masri, F. W. Reuter and M. Friedman, J. Appl. Polym. Sci., 1974, 18, 675–681 CrossRef.
- W. A. Bough and B. WA, Process Biochem., 1976, 11, 13 Search PubMed.
- M. Rinaudo, Prog. Polym. Sci., 2006, 31, 603–632 CrossRef CAS.
- D. Zeng, J. Wu and J. F. Kennedy, Carbohydr. Polym., 2008, 71, 135–139 CrossRef CAS.
- F. Renault, B. Sancey, P.-M. Badot and G. Crini, Eur. Polym. J., 2009, 45, 1337–1348 CrossRef CAS.
- R. Divakaran and V. N. S. Pillai, Water Res., 2001, 35, 3904–3908 CrossRef CAS PubMed.
- C. Dong, W. Chen and C. Liu, Bioresour. Technol., 2014, 170, 239–247 CrossRef CAS PubMed.
- R. Divakaran and V. N. S. Pillai, J. Appl. Phycol., 2002, 14, 419–422 CrossRef CAS.
- R. Divakaran and V. N. S. Pillai, Water Res., 2002, 36, 2414–2418 CrossRef CAS PubMed.
- S. Bratskaya, S. Schwarz and D. Chervonetsky, Water Res., 2004, 38, 2955–2961 CrossRef CAS PubMed.
- Y.-S. Cheng, Y. Zheng, J. M. Labavitch and J. S. VanderGheynst, Process Biochem., 2011, 46, 1927–1933 CrossRef CAS.
- S. Jia, Z. Yang, W. Yang, T. Zhang, S. Zhang, X. Yang, Y. Dong, J. Wu and Y. Wang, Chem. Eng. J., 2016, 283, 495–503 CrossRef CAS.
- Z. Yang, H. Yang, Z. Jiang, T. Cai, H. Li, H. Li, A. Li and R. Cheng, J. Hazard. Mater., 2013, 254, 36–45 CrossRef PubMed.
- L. Ghimici and I. A. Dinu, Sep. Purif. Technol., 2019, 209, 698–706 CrossRef CAS.
- B. Liu, X. Chen, H. Zheng, Y. Wang, Y. Sun, C. Zhao and S. Zhang, Carbohydr. Polym., 2018, 181, 327–336 CrossRef CAS PubMed.
- Z. Yang, H. Li, H. Yan, H. Wu, H. Yang, Q. Wu, H. Li, A. Li and R. Cheng, J. Hazard. Mater., 2014, 276, 480–488 CrossRef CAS PubMed.
- P. Loganathan, M. Gradzielski, H. Bustamante and S. Vigneswaran, Environ. Sci.: Water Res. Technol., 2020, 6, 45–61 RSC.
- C. Kaseamchochoung, P. Lertsutthiwong and C. Phalakornkhule, Water Environ. Res., 2006, 78, 2210–2216 CrossRef CAS PubMed.
- H. Karimi-Maleh, A. Ayati, R. Davoodi, B. Tanhaei, F. Karimi, S. Malekmohammadi, Y. Orooji, L. Fu and M. Sillanpää, J. Cleaner Prod., 2021, 125880 CrossRef CAS.
- W. W. Ngah, L. Teong and M. M. Hanafiah, Carbohydr. Polym., 2011, 83, 1446–1456 CrossRef.
- S. Mincke, T. G. Asere, I. Verheye, K. Folens, F. Vanden Bussche, L. Lapeire, K. Verbeken, P. Van Der Voort, D. A. Tessema, F. Fufa, G. Du Laing and C. V. Stevens, Green Chem., 2019, 21, 2295–2306 RSC.
- U. Baruah, A. Konwar and D. Chowdhury, Nanoscale, 2016, 8, 8542–8546 RSC.
- W.-Z. Qiu, Q.-Z. Zhong, Y. Du, Y. Lv and Z.-K. Xu, Green Chem., 2016, 18, 6205–6208 RSC.
- X. Shen, J. L. Shamshina, P. Berton, G. Gurau and R. D. Rogers, Green Chem., 2016, 18, 53–75 RSC.
- G. Gibbs, J. M. Tobin and E. Guibal, J. Appl. Polym. Sci., 2003, 90, 1073–1080 CrossRef CAS.
- I. O. Saheed, O. W. Da and F. B. M. Suah, J. Hazard. Mater., 2020, 124889 Search PubMed.
- K. Z. Elwakeel, M. A. Abd El-Ghaffar, S. M. El-kousy and H. G. El-Shorbagy, Chem. Eng. J., 2012, 203, 458–468 CrossRef CAS.
- X. Jiang, Y. Sun, L. Liu, S. Wang and X. Tian, Chem. Eng. J., 2014, 235, 151–157 CrossRef CAS.
- V. Singh, A. K. Sharma, D. N. Tripathi and R. Sanghi, J. Hazard. Mater., 2009, 161, 955–966 CrossRef CAS PubMed.
- Y. Yan, B. Xiang, Y. Li and Q. Jia, J. Appl. Polym. Sci., 2013, 130, 4090–4098 CAS.
- M. Sadeghi-Kiakhani, M. Arami and K. Gharanjig, J. Appl. Polym. Sci., 2013, 127, 2607–2619 CrossRef CAS.
- G. Z. Kyzas, D. N. Bikiaris and D. A. Lambropoulou, J. Mol. Liq., 2017, 230, 1–5 CrossRef CAS.
- S. Sharma and N. Rajesh, J. Environ. Chem. Eng., 2017, 5, 1927–1935 CrossRef CAS.
- Y. Jiang, B. Liu, J. Xu, K. Pan, H. Hou, J. Hu and J. Yang, Carbohydr. Polym., 2018, 182, 106–114 CrossRef CAS PubMed.
- M. Salzano de Luna, C. Ascione, C. Santillo, L. Verdolotti, M. Lavorgna, G. G. Buonocore, R. Castaldo, G. Filippone, H. Xia and L. Ambrosio, Carbohydr. Polym., 2019, 211, 195–203 CrossRef CAS PubMed.
- Z. Li, X. Song, S. Cui, Y. Jiao and C. Zhou, RSC Adv., 2018, 8, 8338–8348 RSC.
- L. Fan, C. Luo, X. Li, F. Lu, H. Qiu and M. Sun, J. Hazard. Mater., 2012, 215–216, 272–279 CrossRef CAS PubMed.
- A. ZabihiSahebi, S. Koushkbaghi, M. Pishnamazi, A. Askari, R. Khosravi and M. Irani, Int. J. Biol. Macromol., 2019, 140, 1296–1304 CrossRef CAS PubMed.
- H. Mahmoodian, O. Moradi, B. Shariatzadeha, T. A. Salehf, I. Tyagi, A. Maity, M. Asif and V. K. Gupta, J. Mol. Liq., 2015, 202, 189–198 CrossRef CAS.
- Q. Liu, J. Shi, J. Sun, T. Wang, L. Zeng and G. Jiang, Angew. Chem., 2011, 123, 6035–6039 CrossRef.
- K. Thakur and B. Kandasubramanian, J. Chem. Eng. Data, 2019, 64, 833–867 CrossRef CAS.
- D. C. d. S. Alves, B. Healy, T. Yu and C. B. Breslin, Materials, 2021, 14, 3655 CrossRef CAS PubMed.
- A. O. Salawudeen, B. S. Tawabini, A. M. Al-Shaibani and T. A. Saleh, Environ. Nanotechnol. Monit. Manag., 2020, 13, 100288 Search PubMed.
- G. Fadillah, W. P. Wicaksono, I. Fatimah and T. A. Saleh, Microchem. J., 2020, 159, 105353 CrossRef CAS.
- A. M. Alansi, T. F. Qahtan and T. A. Saleh, Adv. Mater. Interfaces, 2021, 8, 2001463 CrossRef CAS.
- A. Q. Al-Gamal, W. S. Falath and T. A. Saleh, J. Mol. Liq., 2021, 323, 114922 CrossRef CAS.
- B. O. Abdullahi, E. Ahmed, H. Al Abdulgader, F. Alghunaimi and T. A. Saleh, J. Mol. Liq., 2021, 325, 115057 CrossRef CAS.
- I. Ali and T. A. Saleh, Appl. Catal., A, 2020, 598, 117542 CrossRef CAS.
- T. A. Saleh, Trends Environ. Anal. Chem., 2020, 25, e00080 CrossRef CAS.
- K. Haruna and T. A. Saleh, J. Environ. Chem. Eng., 2021, 9, 104967 CrossRef CAS.
- T. A. Saleh and S. A. Al-Hammadi, Chem. Eng. J., 2021, 406, 125167 CrossRef CAS.
- T. A. Saleh, K. Haruna and A.-R. I. Mohammed, J. Mol. Liq., 2021, 325, 115060 CrossRef CAS.
- Y. Chen, L. Chen, H. Bai and L. Li, J. Mater. Chem. A, 2013, 1, 1992–2001 RSC.
- M. A. Kamal, S. Bibi, S. W. Bokhari, A. H. Siddique and T. Yasin, React. Funct. Polym., 2017, 110, 21–29 CrossRef CAS.
- P. Banerjee, S. R. Barman, A. Mukhopadhayay and P. Das, Chem. Eng. Res. Des., 2017, 117, 43–56 CrossRef CAS.
- M. Salzano de Luna, C. Ascione, C. Santillo, L. Verdolotti, M. Lavorgna, G. G. Buonocore, R. Castaldo, G. Filippone, H. Xia and L. Ambrosio, Carbohydr. Polym., 2019, 211, 195–203 CrossRef CAS PubMed.
- Z. Yi, L. Huajie, L. Mingchun and X. Meihua, J. Mol. Struct., 2020, 1209, 127973 CrossRef CAS.
- L. Fan, C. Luo, M. Sun, X. Li, F. Lu and H. Qiu, Bioresour. Technol., 2012, 114, 703–706 CrossRef CAS PubMed.
- L. Fan, C. Luo, M. Sun, H. Qiu and X. Li, Colloids Surf., B, 2013, 103, 601–607 CrossRef CAS PubMed.
- L. Li, L. Fan, C. Luo, H. Duan and X. Wang, RSC Adv., 2014, 4, 24679–24685 RSC.
- Y. Jiang, J.-L. Gong, G.-M. Zeng, X.-M. Ou, Y.-N. Chang, C.-H. Deng, J. Zhang, H.-Y. Liu and S.-Y. Huang, Int. J. Biol. Macromol., 2016, 82, 702–710 CrossRef CAS PubMed.
- B. Ramalingam, M. M. R. Khan, B. Mondal, A. B. Mandal and S. K. Das, ACS Sustainable Chem. Eng., 2015, 3, 2291–2302 CrossRef CAS.
- M. Hui, P. Shengyan, H. Yaqi, Z. Rongxin, Z. Anatoly and C. Wei, Chem. Eng. J., 2018, 345, 556–565 CrossRef CAS.
- N. Singh, S. Riyajuddin, K. Ghosh, S. K. Mehta and A. Dan, ACS Appl. Nano Mater., 2019, 2, 7379–7392 CrossRef CAS.
- H. Tu, Y. Yu, J. Chen, X. Shi, J. Zhou, H. Deng and Y. Du, Polym. Chem., 2017, 8, 2913–2921 RSC.
- D.-M. Guo, Q.-D. An, Z.-Y. Xiao, S.-R. Zhai and D.-J. Yang, Carbohydr. Polym., 2018, 202, 306–314 CrossRef CAS PubMed.
- C. Lei, F. Wen, J. Chen, W. Chen, Y. Huang and B. Wang, Polymer, 2021, 213, 123316 CrossRef CAS.
- W. Zhu, X. Jiang, F. Liu, F. You and C. Yao, Polymers, 2020, 12, 2169 CrossRef CAS PubMed.
- Saakshy, K. Singh, A. B. Gupta and A. K. Sharma, J. Cleaner Prod., 2016, 112, 1227–1240 CrossRef CAS.
- P. Yu, H.-Q. Wang, R.-Y. Bao, Z. Liu, W. Yang, B.-H. Xie and M.-B. Yang, ACS Sustainable Chem. Eng., 2017, 5, 1557–1566 CrossRef CAS.
- M. H. Mruthunjayappa, V. T. Sharma, K. Dharmalingam, S. K. Nataraj and D. Mondal, ACS Appl. Bio Mater., 2020, 3, 5233–5243 CrossRef CAS.
- D. Ma, H. Yi, C. Lai, X. Liu, X. Huo, Z. An, L. Li, Y. Fu, B. Li and M. Zhang, Chemosphere, 2021, 130104 CrossRef CAS PubMed.
- S. Mozia, Sep. Purif. Technol., 2010, 73, 71–91 CrossRef CAS.
- M. A. M. Adnan, B. L. Phoon and N. M. Julkapli, J. Cleaner Prod., 2020, 261, 121190 CrossRef.
- P. Demircivi and E. B. Simsek, Water Sci. Technol., 2018, 78, 487–495 CrossRef CAS PubMed.
- G. Xiao, H. Su and T. Tan, J. Hazard. Mater., 2015, 283, 888–896 CrossRef CAS PubMed.
- P. Wu, H. Peng, Y. Wu, L. Li, X. Hao, B. Peng, G. Meng, J. Wu and Z. Liu, J. Electron. Sci. Technol., 2020, 18, 100019 CrossRef.
- S. Preethi, K. Abarna, M. Nithyasri, P. Kishore, K. Deepika, R. Ranjithkumar, V. Bhuvaneshwari and D. Bharathi, Int. J. Biol. Macromol., 2020, 164, 2779–2787 CrossRef CAS PubMed.
- A. M. Saad, M. R. Abukhadra, S. Abdel-Kader Ahmed, A. M. Elzanaty, A. H. Mady, M. A. Betiha, J. J. Shim and A. M. Rabie, J. Environ. Manage., 2020, 258, 110043 CrossRef CAS PubMed.
- Z. Zainal, L. K. Hui, M. Z. Hussein and A. H. Abdullah, J. Hazard. Mater., 2009, 164, 138–145 CrossRef CAS PubMed.
- A. Balakrishnan, S. Appunni and K. Gopalram, Int. J. Biol. Macromol., 2020, 161, 282–291 CrossRef CAS PubMed.
- X. Wang, J. Song, J. Huang, J. Zhang, X. Wang, R. Ma, J. Wang and J. Zhao, Appl. Surf. Sci., 2016, 390, 190–201 CrossRef CAS.
- S. Cheng, C. Zhang, J. Li, X. Pan, X. Zhai, Y. Jiao, Y. Li, W. Dong and X. Qi, Carbohydr. Polym., 2021, 262, 117951 CrossRef CAS PubMed.
- M. R. Abukhadra, A. Adlii and B. M. Bakry, Int. J. Biol. Macromol., 2019, 126, 402–413 CrossRef CAS PubMed.
- A. A. P. Mansur, H. S. Mansur, F. P. Ramanery, L. C. Oliveira and P. P. Souza, Appl. Catal., B, 2014, 158–159, 269–279 CrossRef CAS.
- K.-Y. A. Lin, J.-T. Lin and H. Yang, Carbohydr. Polym., 2017, 173, 412–421 CrossRef CAS PubMed.
- T. Oe, H. Koide, H. Hirokawa and K. Okukawa, Desalination, 1996, 106, 107–113 CrossRef CAS.
- R. Zhang, Y. Liu, M. He, Y. Su, X. Zhao, M. Elimelech and Z. Jiang, Chem. Soc. Rev., 2016, 45, 5888–5924 RSC.
- M. Beppu, R. Vieira, C. Aimoli and C. Santana, J. Membr. Sci., 2007, 301, 126–130 CrossRef CAS.
- M. M. Beppu, R. S. Vieira, C. G. Aimoli and C. C. Santana, J. Membr. Sci., 2007, 301, 126–130 CrossRef CAS.
- A. Mochizuki, Y. Sato, H. Ogawara and S. Yamashita, J. Appl. Polym. Sci., 1989, 37, 3375–3384 CrossRef CAS.
- X. P. Wang, Z. Q. Shen and F. Y. Zhang, J. Appl. Polym. Sci., 1998, 69, 2035–2041 CrossRef CAS.
- G. Qunhui, H. Ohya and Y. Negishi, J. Membr. Sci., 1995, 98, 223–232 CrossRef CAS.
- D. Anjali Devi, B. Smitha, S. Sridhar and T. M. Aminabhavi, J. Membr. Sci., 2005, 262, 91–99 CrossRef CAS.
- W. Won, X. Feng and D. Lawless, Sep. Purif. Technol., 2003, 31, 129–140 CrossRef CAS.
- M. Gierszewska and J. Ostrowska-Czubenko, Carbohydr. Polym., 2016, 153, 501–511 CrossRef CAS PubMed.
- S. Liu, Z. Wang and P. Song, ACS Sustainable Chem. Eng., 2018, 6, 4253–4263 CrossRef CAS.
- J. Wang, X. Gao, J. Wang, Y. Wei, Z. Li and C. Gao, ACS Appl. Mater. Interfaces, 2015, 7, 4381–4389 CrossRef CAS PubMed.
- Y. Song, Q. Hu, T. Li, Y. Sun, X. Chen and J. Fan, Chem. Eng. J., 2018, 352, 163–172 CrossRef CAS.
- J. Xu, X. Feng and C. Gao, J. Membr. Sci., 2011, 370, 116–123 CrossRef CAS.
- R. Kumar, A. M. Isloor and A. F. Ismail, Desalination, 2014, 350, 102–108 CrossRef CAS.
- A. Giwa, N. Akther, V. Dufour and S. W. Hasan, RSC Adv., 2016, 6, 8134–8163 RSC.
- M. Halakarni, A. Mahto, K. Aruchamy, D. Mondal and S. K. Nataraj, Chem. Eng. J., 2021, 417, 127911 CrossRef CAS.
- N. R. Maalige, K. Aruchamy, V. Polishetti, M. Halakarni, A. Mahto, D. Mondal and S. K. Nataraj, Carbohydr. Polym., 2021, 254, 117297 CrossRef PubMed.
- K. H. Vardhan, P. S. Kumar and R. C. Panda, J. Mol. Liq., 2019, 290, 111197 CrossRef CAS.
- X. Liu, Q. Hu, Z. Fang, X. Zhang and B. Zhang, Langmuir, 2009, 25, 3–8 CrossRef CAS PubMed.
- T. Jin, T. Liu, E. Lam and A. Moores, Nanoscale Horiz., 2021, 6, 505–542 RSC.
- M. Nasrollahzadeh, M. Sajjadi, S. Iravani and R. S. Varma, Carbohydr. Polym., 2021, 251, 116986 CrossRef CAS PubMed.
- G. Crini, Prog. Polym. Sci., 2005, 30, 38–70 CrossRef CAS.
- M. J. Ahmed, B. H. Hameed and E. H. Hummadi, Carbohydr. Polym., 2020, 247, 116690 CrossRef CAS PubMed.
- V. K. Thakur and S. I. Voicu, Carbohydr. Polym., 2016, 146, 148–165 CrossRef CAS PubMed.
- K. H. Prashanth and R. Tharanathan, Trends Food Sci. Technol., 2007, 18, 117–131 CrossRef CAS.
- M. J. Zohuriaan-Mehr, Iran. Polym. J., 2005, 14, 235–265 CAS.
- J. Roosen and K. Binnemans, J. Mater. Chem. A, 2014, 2, 1530–1540 RSC.
- D. Zhang, L. Wang, H. Zeng, B. Rhimi and C. Wang, Environ. Sci. Nano, 2020, 7, 793–802 RSC.
- J. Wang and C. Chen, Bioresour. Technol., 2014, 160, 129–141 CrossRef CAS PubMed.
- G. Jing, L. Wang, H. Yu, W. A. Amer and L. Zhang, Colloids Surf., A, 2013, 416, 86–94 CrossRef.
- J. Roosen, J. Spooren and K. Binnemans, J. Mater. Chem. A, 2014, 2, 19415–19426 RSC.
- Y. Zhang, M. Yin, L. Li, B. Fan, Y. Liu, R. Li, X. Ren, T.-S. Huang and I. S. Kim, Carbohydr. Polym., 2020, 243, 116461 CrossRef CAS PubMed.
- S. Mallakpour, E. Azadi and C. M. Hussain, New J. Chem., 2021, 45, 3756–3777 RSC.
- M. Ahmed, B. Hameed and E. Hummadi, Carbohydr. Polym., 2020, 116690 CrossRef CAS PubMed.
- G. Yu, Y. Lu, J. Guo, M. Patel, A. Bafana, X. Wang, B. Qiu, C. Jeffryes, S. Wei and Z. Guo, Adv. Compos. Hybrid Mater., 2018, 1, 56–78 CrossRef CAS.
- M. J. Sweetman, S. May, N. Mebberson, P. Pendleton, K. Vasilev, S. E. Plush and J. D. Hayball, C, 2017, 3, 18 Search PubMed.
- M. U. Sankar, S. Aigal, S. M. Maliyekkal, A. Chaudhary, Anshup, A. A. Kumar, K. Chaudhari and T. Pradeep, Proc. Natl. Acad. Sci. U. S. A., 2013, 110, 8459–8464 CrossRef CAS PubMed.
- A. A. Kumar, A. Som, P. Longo, C. Sudhakar, R. G. Bhuin, S. S. Gupta, Anshup, M. U. Sankar, A. Chaudhary, R. Kumar and T. Pradeep, Adv. Mater., 2017, 29, 1604260 CrossRef PubMed.
- Z. Wan, W. Chen, C. Liu, Y. Liu and C. Dong, J. Colloid Interface Sci., 2015, 443, 115–124 CrossRef CAS PubMed.
- Z. Marková, K. Šišková, J. Filip, K. Šafářová, R. Prucek, A. Panáček, M. Kolář and R. Zbořil, Green Chem., 2012, 14, 2550–2558 RSC.
- Z. Yu, X. Zhang and Y. Huang, Ind. Eng. Chem. Res., 2013, 52, 11956–11966 CrossRef CAS.
- J. Li, B. Jiang, Y. Liu, C. Qiu, J. Hu, G. Qian, W. Guo and H. H. Ngo, J. Cleaner Prod., 2017, 158, 51–58 CrossRef CAS.
- G. L. Rorrer, T. Y. Hsien and J. D. Way, Ind. Eng. Chem. Res., 1993, 32, 2170–2178 CrossRef CAS.
- P. E. Hande, S. Kamble, A. B. Samui and P. S. Kulkarni, Ind. Eng. Chem. Res., 2016, 55, 3668–3678 CrossRef CAS.
- D. Kong, N. Wang, N. Qiao, Q. Wang, Z. Wang, Z. Zhou and Z. Ren, ACS Sustainable Chem. Eng., 2017, 5, 7401–7409 CrossRef CAS.
- Q. Wang, X. Liu, M. Zhang, Z. Wang, Z. Zhou and Z. Ren, Ind. Eng. Chem. Res., 2019, 58, 6670–6678 CrossRef CAS.
- H. N. Doan, P. P. Vo, A. Baggio, M. Negoro, K. Kinashi, Y. Fuse, W. Sakai and N. Tsutsumi, ACS Appl. Poly. Mater., 2021 Search PubMed.
- J. Ma, X. Fu, W. Xia, R. Zhang, K. Fu, G. Wu, B. Jia, S. Li and J. Li, J. Hazard. Mater., 2021, 126529 CrossRef CAS PubMed.
- A. Pinotti, A. Bevilacqua and N. Zaritzky, J. Surfactants Deterg., 2001, 4, 57–63 CrossRef CAS.
- S. Bratskaya, V. Avramenko, S. Schwarz and I. Philippova, Colloids Surf., A, 2006, 275, 168–176 CrossRef CAS.
- R. Yang, H. Li, M. Huang, H. Yang and A. Li, Water Res., 2016, 95, 59–89 CrossRef CAS PubMed.
- J. Liu, P. Li, L. Chen, Y. Feng, W. He, X. Yan and X. Lü, Surf. Coat. Technol., 2016, 307, 171–176 CrossRef CAS.
- J. P. Chaudhary, N. Vadodariya, S. K. Nataraj and R. Meena, ACS Appl. Mater. Interfaces, 2015, 7, 24957–24962 CrossRef CAS PubMed.
-
(a)
R. Meena, N. D. Sanandiya, J. P. Chaudhary, D. Mondal and S. K. Nataraj, 2015056273A4, 2015;
(b) J. P. Chaudhary, S. K. Nataraj, A. Gogda and R. Meena, Green Chem., 2014, 16, 4552–4558 RSC.
- N. Cao, Q. Lyu, J. Li, Y. Wang, B. Yang, S. Szunerits and R. Boukherroub, Chem. Eng. J., 2017, 326, 17–28 CrossRef CAS.
- W. Zhou, Y. Fang, P. Li, L. Yan, X. Fan, Z. Wang, W. Zhang and H. Liu, ACS Sustainable Chem. Eng., 2019, 7, 15463–15470 CrossRef CAS.
- H. Zhang, Y. Li, R. Shi, L. Chen and M. Fan, Carbohydr. Polym., 2018, 200, 611–615 CrossRef CAS PubMed.
- J. Hu, J. Zhu, S. Ge, C. Jiang, T. Guo, T. Peng, T. Huang and L. Xie, Surf. Coat. Technol., 2020, 385, 125361 CrossRef CAS.
- L. Yi, J. Yang, X. Fang, Y. Xia, L. Zhao, H. Wu and S. Guo, J. Hazard. Mater., 2020, 385, 121507 CrossRef CAS PubMed.
- M. Wang, Y. Ma, Y. Sun, S. Y. Hong, S. K. Lee, B. Yoon, L. Chen, L. Ci, J.-D. Nam, X. Chen and J. Suhr, Sci. Rep., 2017, 7, 18054 CrossRef PubMed.
- X. Zhou, F. Zhao, Y. Guo, B. Rosenberger and G. Yu, Sci. Adv., 2019, 5, eaaw5484 CrossRef CAS PubMed.
- T. Xu, Y. Xu, J. Wang, H. Lu, W. Liu and J. Wang, Chem. Eng. J., 2021, 415, 128893 CrossRef CAS.
- F. Wang, D. Wei, Y. Li, T. Chen, P. Mu, H. Sun, Z. Zhu, W. Liang and A. Li, J. Mater. Chem. A, 2019, 7, 18311–18317 RSC.
- X.-Y. Wang, J. Xue, C. Ma, T. He, H. Qian, B. Wang, J. Liu and Y. Lu, J. Mater. Chem. A, 2019, 7, 16696–16703 RSC.
- S. Zhang, F. Lu, L. Tao, N. Liu, C. Gao, L. Feng and Y. Wei, ACS Appl. Mater. Interfaces, 2013, 5, 11971–11976 CrossRef CAS PubMed.
- M. Zhang, W. Xu, M. Li, J. Li, P. Wang and Z. Wang, J. Bionic Eng., 2021, 18, 30–39 CrossRef.
- F. Yu, Z. Chen, Z. Guo, M. S. Irshad, L. Yu, J. Qian, T. Mei and X. Wang, ACS Sustainable Chem. Eng., 2020, 8, 7139–7149 CrossRef CAS.
- X. Wang, Z. Li, Y. Wu, H. Guo, X. Zhang, Y. Yang, H. Mu and J. Duan, ACS Appl. Mater. Interfaces, 2021, 13, 10902–10915 CrossRef CAS PubMed.
- M. S. Irshad, X. Wang, M. S. Abbasi, N. Arshad, Z. Chen, Z. Guo, L. Yu, J. Qian, J. You and T. Mei, ACS Sustainable Chem. Eng., 2021, 9, 3887–3900 CrossRef CAS.
- B. Rehm and S. Valla, Appl. Microbiol. Biotechnol., 1997, 48, 281–288 CrossRef CAS PubMed.
- I. P. S. Fernando, W. Lee, E. J. Han and G. Ahn, Chem. Eng. J., 2020, 391, 123823 CrossRef CAS.
- S. D. Bhat and T. M. Aminabhavi, Sep. Purif. Rev., 2007, 36, 203–229 CrossRef CAS.
- J.-S. Yang, Y.-J. Xie and W. He, Carbohydr. Polym., 2011, 84, 33–39 CrossRef CAS.
- Z. Aksu, G. Egretli and T. Kutsal, J. Environ. Sci. Health, Part A: Toxic/Hazard. Subst. Environ. Eng., 1999, 34, 295–316 CrossRef.
- Y. Sag, M. Nourbakhsh, Z. Aksu and T. Kutsal, Process Biochem., 1995, 30, 175–181 CrossRef CAS.
- J. H. Min and J. G. Hering, Water Res., 1998, 32, 1544–1552 CrossRef CAS.
- K. SAITO, T. MURATA and T. MORI, Int. J. Food Sci. Technol., 1994, 29, 715–719 CrossRef CAS.
- G. Annadurai, R.-S. Juang and D.-J. Lee, Adv. Environ. Res., 2002, 6, 191–198 CrossRef.
- R. Aravindhan, N. N. Fathima, J. R. Rao and B. U. Nair, Colloids Surf., A, 2007, 299, 232–238 CrossRef CAS.
- E. Prouzet, Z. Khani, M. Bertrand, M. Tokumoto, V. Guyot-Ferreol and J.-F. Tranchant, Microporous Mesoporous Mater., 2006, 96, 369–375 CrossRef CAS.
- C. Wang, H. Liu, Q. Gao, X. Liu and Z. Tong, Carbohydr. Polym., 2008, 71, 476–480 CrossRef CAS.
- A. Ely, M. Baudu, M. O. S. A. O. Kankou and J.-P. Basly, Chem. Eng. J., 2011, 178, 168–174 CrossRef CAS.
- S. Peretz, D. F. Anghel, E. Vasilescu, M. Florea-Spiroiu, C. Stoian and G. Zgherea, Polym. Bull., 2015, 72, 3169–3182 CrossRef CAS.
- S. Partap, A. Muthutantri, I. U. Rehman, G. R. Davis and J. A. Darr, J. Mater. Sci., 2007, 42, 3502–3507 CrossRef CAS.
- S. Pashaei-Fakhri, S. J. Peighambardoust, R. Foroutan, N. Arsalani and B. Ramavandi, Chemosphere, 2021, 270, 129419 CrossRef CAS PubMed.
- T. Hu, Q. Liu, T. Gao, K. Dong, G. Wei and J. Yao, ACS Omega, 2018, 3, 7523–7531 CrossRef CAS PubMed.
- J. Fan, Z. Shi, M. Lian, H. Li and J. Yin, J. Mater. Chem. A, 2013, 1, 7433–7443 RSC.
- W. Wang, Y. Zhao, H. Bai, T. Zhang, V. Ibarra-Galvan and S. Song, Carbohydr. Polym., 2018, 198, 518–528 CrossRef CAS PubMed.
- Z.-j. Shao, X.-l. Huang, F. Yang, W.-f. Zhao, X.-z. Zhou and C.-s. Zhao, Carbohydr. Polym., 2018, 187, 85–93 CrossRef CAS PubMed.
- Y. Feng, H. Wang, J. Xu, X. Du, X. Cheng, Z. Du and H. Wang, J. Hazard. Mater., 2021, 416, 125777 CrossRef CAS PubMed.
- S. Thakur, S. Pandey and O. A. Arotiba, Carbohydr. Polym., 2016, 153, 34–46 CrossRef CAS PubMed.
- E. Makhado, S. Pandey, K. D. Modibane, M. Kang and M. J. Hato, Int. J. Biol. Macromol., 2020, 162, 60–73 CrossRef CAS PubMed.
- K. Sui, Y. Li, R. Liu, Y. Zhang, X. Zhao, H. Liang and Y. Xia, Carbohydr. Polym., 2012, 90, 399–406 CrossRef CAS PubMed.
- A. F. Hassan, A. M. Abdel-Mohsen and M. M. G. Fouda, Carbohydr. Polym., 2014, 102, 192–198 CrossRef CAS PubMed.
- L. Gan, H. Li, L. Chen, L. Xu, J. Liu, A. Geng, C. Mei and S. Shang, Colloid Polym. Sci., 2018, 296, 607–615 CrossRef CAS.
- Q. Li, Y. Li, X. Ma, Q. Du, K. Sui, D. Wang, C. Wang, H. Li and Y. Xia, Chem. Eng. J., 2017, 316, 623–630 CrossRef CAS.
- S. Lin, R. Huang, Y. Cheng, J. Liu, B. L. Lau and M. R. Wiesner, Water Res., 2013, 47, 3959–3965 CrossRef CAS PubMed.
- X. Li, H. Lu, Y. Zhang, F. He, L. Jing and X. He, Appl. Surf. Sci., 2016, 389, 567–577 CrossRef CAS.
- V. S. Munagapati and D.-S. Kim, Ecotoxicol. Environ. Saf., 2017, 141, 226–234 CrossRef CAS PubMed.
- Y. Kong, Y. Zhuang, K. Han and B. Shi, Colloids Surf., A, 2020, 588, 124360 CrossRef CAS.
- S. Sarkar, S. Chakraborty and C. Bhattacharjee, Ecotoxicol. Environ. Saf., 2015, 121, 263–270 CrossRef CAS PubMed.
- S. K. Papageorgiou, F. K. Katsaros, E. P. Favvas, G. E. Romanos, C. P. Athanasekou, K. G. Beltsios, O. I. Tzialla and P. Falaras, Water Res., 2012, 46, 1858–1872 CrossRef CAS PubMed.
- S. K. Mohamed, S. H. Hegazy, N. A. Abdelwahab and A. M. Ramadan, Int. J. Biol. Macromol., 2018, 108, 1185–1198 CrossRef CAS PubMed.
- D. Hao, Q. Huang, W. Wei, X. Bai and B.-J. Ni, J. Cleaner Prod., 2021, 314, 128033 CrossRef CAS.
- D. Qian, L. Bai, Y.-S. Wang, F. Song, X.-L. Wang and Y.-Z. Wang, Ind. Eng. Chem. Res., 2019, 58, 13133–13144 CrossRef CAS.
- K. Wanchai, Key Eng. Mater., 2017, 751, 689–694 Search PubMed.
- I. Hasan, C. Shekhar, I. I. B. Sharfan, R. A. Khan and A. Alsalme, ACS Omega, 2020, 5, 32011–32022 CrossRef CAS PubMed.
- L. Li, Y. Fang, R. Vreeker, I. Appelqvist and E. Mendes, Biomacromolecules, 2007, 8, 464–468 CrossRef CAS PubMed.
- S. Peretz and O. Cinteza, Colloids Surf., A, 2008, 319, 165–172 CrossRef CAS.
- Lalhmunsiama, R. R. Pawar, S.-M. Hong, K. J. Jin and S.-M. Lee, J. Mol. Liq., 2017, 240, 497–503 CrossRef CAS.
- N. Fatin-Rouge, A. Dupont, A. Vidonne, J. Dejeu, P. Fievet and A. Foissy, Water Res., 2006, 40, 1303–1309 CrossRef CAS PubMed.
- K. Yu, J. Ho, E. McCandlish, B. Buckley, R. Patel, Z. Li and N. C. Shapley, Colloids Surf., A, 2013, 425, 31–41 CrossRef CAS.
- Y. Vijaya, S. R. Popuri, V. M. Boddu and A. Krishnaiah, Carbohydr. Polym., 2008, 72, 261–271 CrossRef CAS.
- P. Singh, S. K. Singh, J. Bajpai, A. K. Bajpai and R. B. Shrivastava, J. Mater. Res. Technol., 2014, 3, 195–202 CrossRef CAS.
- Y. Yan, Q. An, Z. Xiao, W. Zheng and S. Zhai, Chem. Eng. J., 2017, 313, 475–486 CrossRef CAS.
- M. Wang, X. Li, T. Zhang, L. Deng, P. Li, X. Wang and B. S. Hsiao, Colloids Surf., A, 2018, 558, 228–241 CrossRef CAS.
- A. Sinha, B. G. Cha and J. Kim, ACS Appl. Nano Mater., 2018, 1, 1940–1948 CrossRef CAS.
- J. He, A. Cui, F. Ni, S. Deng, F. Shen and G. Yang, J. Colloid Interface Sci., 2018, 531, 37–46 CrossRef CAS PubMed.
- J. He, F. Ni, A. Cui, X. Chen, S. Deng, F. Shen, C. Huang, G. Yang, C. Song, J. Zhang, D. Tian, L. Long, Y. Zhu and L. Luo, Sci. Total Environ., 2020, 701, 134363 CrossRef CAS PubMed.
- A. Kumar, P. Paul and S. K. Nataraj, ACS Sustainable Chem. Eng., 2017, 5, 895–903 CrossRef CAS.
- Y. Li, H. Zhang, M. Fan, J. Zhuang and L. Chen, Phys. Chem. Chem. Phys., 2016, 18, 25394–25400 RSC.
- J. Dai, Q. Tian, Q. Sun, W. Wei, J. Zhuang, M. Liu, Z. Cao, W. Xie and M. Fan, Composites, Part B, 2019, 160, 480–487 CrossRef CAS.
- Y. Li, H. Zhang, C. Ma, H. Yin, L. Gong, Y. Duh and R. Feng, Carbohydr. Polym., 2019, 226, 115279 CrossRef CAS PubMed.
- J. Zhuang, J. Dai, S. H. Ghaffar, Y. Yu, Q. Tian and M. Fan, Surf. Coat. Technol., 2020, 388, 125551 CrossRef CAS.
- F. S. Mostafavi and D. Zaeim, Int. J. Biol. Macromol., 2020, 159, 1165–1176 CrossRef CAS PubMed.
- W. Y. Seow and C. A. E. Hauser, J. Environ. Chem. Eng., 2016, 4, 1714–1721 CrossRef CAS.
- N. A. Alygizakis, J. Urík, V. G. Beretsou, I. Kampouris, A. Galani, M. Oswaldova, T. Berendonk, P. Oswald, N. S. Thomaidis, J. Slobodnik, B. Vrana and D. Fatta-Kassinos, Environ. Int., 2020, 138, 105597 CrossRef CAS PubMed.
- M. M. Areco, S. Hanela, J. Duran and M. dos Santos Afonso, J. Hazard. Mater., 2012, 213–214, 123–132 CrossRef CAS PubMed.
- N. Gogoi, M. Barooah, G. Majumdar and D. Chowdhury, ACS Appl. Mater. Interfaces, 2015, 7, 3058–3067 CrossRef CAS PubMed.
- J. Li, Z. Guo, S. Zhang and X. Wang, Chem. Eng. J., 2011, 172, 892–897 CrossRef CAS.
- Q. Zhang, S. Dan and K. Du, Ind. Eng. Chem. Res., 2017, 56, 8705–8712 CrossRef CAS.
- F. Luo, Z. Chen, M. Megharaj and R. Naidu, Chem. Eng. J., 2016, 294, 290–297 CrossRef CAS.
- G. U. Rani, A. K. Konreddy and S. Mishra, Int. J. Biol. Macromol., 2018, 117, 902–910 CrossRef CAS PubMed.
- T. Tang, K. Goossens, S. J. Lu, D. Meng and C. W. Bielawski, RSC Adv., 2020, 10, 29287–29295 RSC.
- C. Cheng, Y. Cai, G. Guan, L. Yeo and D. Wang, Angew. Chem., Int. Ed., 2018, 57, 11177–11181 CrossRef CAS PubMed.
- L. Chen, Y. Li, Q. Du, Z. Wang, Y. Xia, E. Yedinak, J. Lou and L. Ci, Carbohydr. Polym., 2017, 155, 345–353 CrossRef CAS PubMed.
- P.-J. Lin, M.-C. Yang, Y.-L. Li and J.-H. Chen, J. Membr. Sci., 2015, 475, 511–520 CrossRef CAS.
- Z. Sun, J. Wang, Q. Wu, Z. Wang, Z. Wang, J. Sun and C.-J. Liu, Adv. Funct. Mater., 2019, 29, 1901312 CrossRef.
- O. Duman, T. G. Polat, C. Diker and S. Tunç, Int. J. Biol. Macromol., 2020, 160, 823–835 CrossRef CAS PubMed.
- M. S. J. Khan, S. B. Khan, T. Kamal and A. M. Asiri, Polym. Test., 2019, 78, 105983 CrossRef CAS.
- B. N. Hoang, T. T. Nguyen, Q. P. T. Bui, L. G. Bach, D.-V. N. Vo, C. D. Trinh, X.-T. Bui and T. D. Nguyen, J. Appl. Polym. Sci., 2020, 137, 48904 CrossRef CAS.
- J. Shao, Z. Zhang, S. Zhao, S. Wang, Z. Guo, H. Xie and Y. Hu, Starch, 2019, 71, 1800281 CrossRef.
- M. Zhang, W. Jiang, D. Liu, J. Wang, Y. Liu, Y. Zhu and Y. Zhu, Appl. Catal., B, 2016, 183, 263–268 CrossRef CAS.
- L. Tan, C. Yu, M. Wang, S. Zhang, J. Sun, S. Dong and J. Sun, Appl. Surf. Sci., 2019, 467–468, 286–292 CrossRef CAS.
- N. X. D. Mai, J. Bae, I. T. Kim, S. H. Park, G.-W. Lee, J. H. Kim, D. Lee, H. B. Son, Y.-C. Lee and J. Hur, Environ. Sci. Nano, 2017, 4, 955–966 RSC.
- M. Shorie, H. Kaur, G. Chadha, K. Singh and P. Sabherwal, J. Hazard. Mater., 2019, 367, 629–638 CrossRef CAS PubMed.
- W. Zhang, S. Shi, W. Zhu, L. Huang, C. Yang, S. Li, X. Liu, R. Wang, N. Hu, Y. Suo, Z. Li and J. Wang, ACS Sustainable Chem. Eng., 2017, 5, 9347–9354 CrossRef CAS.
- S. Patra, E. Roy, R. Madhuri and P. K. Sharma, J. Ind. Eng. Chem., 2016, 33, 226–238 CrossRef CAS.
- T. Brugnari, M. G. Pereira, G. A. Bubna, E. N. de Freitas, A. G. Contato, R. C. G. Corrêa, R. Castoldi, C. G. M. de Souza, M. Polizeli, A. Bracht and R. M. Peralta, Sci. Total Environ., 2018, 634, 1346–1351 CrossRef CAS PubMed.
- M. Dul, K. J. Paluch, H. Kelly, A. M. Healy, A. Sasse and L. Tajber, Carbohydr. Polym., 2015, 123, 339–349 CrossRef CAS PubMed.
- L. Li, R. Ni, Y. Shao and S. Mao, Carbohydr. Polym., 2014, 103, 1–11 CrossRef CAS PubMed.
- G. R. Mahdavinia, A. Massoudi, A. Baghban and B. Massoumi, Iran. Polym. J., 2012, 21, 609–619 CrossRef CAS.
- G. R. Mahdavinia and A. Asgari, Polym. Bull., 2013, 70, 2451–2470 CrossRef CAS.
- K. H. Kamala, S. Dacroryb, S. Alic, K. A. Alid and S. Kamelb, Desalin. Water Treat., 2019, 165, 281–289 CrossRef.
- C. Liu, A. M. Omer and X. K. Ouyang, Int. J. Biol. Macromol., 2018, 106, 823–833 CrossRef CAS PubMed.
- M. Jabli, S. G. Almalki and H. Agougui, Int. J. Biol. Macromol., 2020, 156, 1091–1103 CrossRef CAS PubMed.
- M. Yang, X. Liu, Y. Qi, W. Sun and Y. Men, J. Colloid Interface Sci., 2017, 506, 669–677 CrossRef CAS PubMed.
- A. Prasannan, J. Udomsin, H.-C. Tsai, M. Sivakumar, C.-C. Hu, C.-F. Wang, W.-S. Hung and J.-Y. Lai, J. Membr. Sci., 2020, 603, 118026 CrossRef CAS.
- X. Liang, J. Duan, Q. Xu, X. Wei, A. Lu and L. Zhang, Chem. Eng. J., 2017, 317, 766–776 CrossRef CAS.
- H. Agougui, M. Jabli and H. Majdoub, J. Appl. Polym. Sci., 2017, 134, 45385 CrossRef.
- F. H. H. Abdellatif and M. M. Abdellatif, Cellulose, 2020, 27, 441–453 CrossRef CAS.
- A. Pourjavadi, M. Doulabi and M. Doroudian, J. Iran. Chem. Soc., 2014, 11, 1057–1065 CrossRef CAS.
- H. Mittal, A. Al Alili and S. M. Alhassan, Cellulose, 2020, 27, 8269–8285 CrossRef CAS.
- S. Choudhury and S. K. Ray, Carbohydr. Polym., 2018, 200, 305–320 CrossRef CAS PubMed.
- A. A. Yakout, R. H. El-Sokkary, M. A. Shreadah and O. G. A. Hamid, Carbohydr. Polym., 2016, 148, 406–414 CrossRef CAS PubMed.
- L. Yang, N. Li, C. Guo, J. He, S. Wang, L. Qiao, F. Li, L. Yu, M. Wang and X. Xu, Chem. Eng. J., 2021, 417, 128051 CrossRef CAS.
- V. R. A. Ferreira, M. A. Azenha, C. M. Pereira and A. F. Silva, J. Appl. Polym. Sci., 2020, 137, 48842 CrossRef CAS.
- V. R. A. Ferreira, M. A. Azenha, C. M. Pereira and A. Fernando Silva, Reactive and Functional Polymers, 2017, 115, 53–62 CrossRef CAS.
- V. R. A. Ferreira, M. A. Azenha, A. G. Bustamante, M. T. Mêna, C. Moura, C. M. Pereira and A. F. Silva, Mater. Today Commun., 2016, 8, 172–182 CrossRef CAS.
- C. Senthil and C. W. Lee, Renewable Sustainable Energy Rev., 2021, 137, 110464 CrossRef CAS.
- L. Peng, X. Duan, Y. Shang, B. Gao and X. Xu, Appl. Catal., B, 2021, 287, 119963 CrossRef CAS.
- S. K. Bhatia, A. K. Palai, A. Kumar, R. K. Bhatia, A. K. Patel, V. K. Thakur and Y.-H. Yang, Bioresour. Technol., 2021, 340, 125644 CrossRef PubMed.
- R. Gokulan, G. G. Prabhu, A. Avinash and J. Jegan, Desalin. Water Treat., 2020, 184, 340–353 CrossRef CAS.
- J. Wang, P. Nie, B. Ding, S. Dong, X. Hao, H. Dou and X. Zhang, J. Mater. Chem. A, 2017, 5, 2411–2428 RSC.
- M. Sharma, D. Mondal, N. Singh, K. Upadhyay, A. Rawat, R. V. Devkar, R. A. Sequeira and K. Prasad, ACS Sustainable Chem. Eng., 2017, 5, 3488–3498 CrossRef CAS.
- L. Hencz, X. Gu, X. Zhou, W. Martens and S. Zhang, J. Mater. Sci., 2017, 52, 12336–12347 CrossRef CAS.
- D. Li, G. Chang, L. Zong, P. Xue, Y. Wang, Y. Xia, C. Lai and D. Yang, Energy Storage Mater., 2019, 17, 22–30 CrossRef.
- J. Nogueira, M. António, S. M. Mikhalev, S. Fateixa, T. Trindade and A. L. Daniel-da-Silva, Nanomaterials, 2018, 8, 1004 CrossRef PubMed.
- A. A. H. Saeed, N. Y. Harun, S. Sufian, A. A. Siyal, M. Zulfiqar, M. R. Bilad, A. Vagananthan, A. Al-Fakih, A. A. S. Ghaleb and N. Almahbashi, Sustainability, 2020, 12, 10318 CrossRef CAS.
- W. Deng, S. Tang, X. Zhou, Y. Liu, S. Liu and J. Luo, Carbohydr. Polym., 2020, 247, 116736 CrossRef CAS PubMed.
- K. Lu, Z. Min, J. Qin, P. Shi, J. Wu, J. Fan, Y. Min and Q. Xu, Sci. Total Environ., 2021, 752, 142282 CrossRef CAS PubMed.
- A. Mahto, A. Kumar, J. P. Chaudhary, M. Bhatt, A. K. Sharma, P. Paul, S. K. Nataraj and R. Meena, J. Hazard. Mater., 2018, 353, 190–203 CrossRef CAS PubMed.
- A. Mahto, A. Singh, K. Aruchamy, A. Maraddi, G. R. Bhadu, N. S. Kotrappanavar and R. Meena, Sustainable Mater. Technol., 2021, 29, e00292 CrossRef CAS.
- M. Zhu, A. Xia, Q. Feng, X. Wu, C. Zhang, D. Wu and H. Zhu, Energy Technol., 2020, 8, 1901215 CrossRef CAS.
- C. Chen, T. Ma, Y. Shang, B. Gao, B. Jin, H. Dan, Q. Li, Q. Yue, Y. Li, Y. Wang and X. Xu, Appl. Catal., B, 2019, 250, 382–395 CrossRef CAS.
- Y.-m. Huang, G. Li, M. Li, J. Yin, N. Meng, D. Zhang, X.-q. Cao, F.-p. Zhu, M. Chen, L. Li and X.-j. Lyu, Sci. Total Environ., 2021, 754, 141999 CrossRef CAS PubMed.
- X.-y. Li, D. Han, J.-f. Xie, Z.-b. Wang, Z.-q. Gong and B. Li, RSC Adv., 2018, 8, 29237–29247 RSC.
- L. Zhao, N. Baccile, S. Gross, Y. Zhang, W. Wei, Y. Sun, M. Antonietti and M.-M. Titirici, Carbon, 2010, 48, 3778–3787 CrossRef CAS.
- A. Khan, M. Goepel, J. C. Colmenares and R. Gläser, ACS Sustainable Chem. Eng., 2020, 8, 4708–4727 CrossRef CAS.
- A. Khan, M. Goepel, J. C. Colmenares and R. Gläser, ACS Sustainable Chem. Eng., 2020, 8, 4708–4727 CrossRef CAS.
- M. Inagaki, M. Toyoda, Y. Soneda and T. Morishita, Carbon, 2018, 132, 104–140 CrossRef CAS.
- M.-M. Titirici, R. J. White and L. Zhao, Green, 2012, 2, 25–40 CrossRef CAS.
- A. Olejniczak, M. Lezanska, J. Wloch, A. Kucinska and J. P. Lukaszewicz, J. Mater. Chem. A, 2013, 1, 8961–8967 RSC.
- G. Daniel, Y. Zhang, S. Lanzalaco, F. Brombin, T. Kosmala, G. Granozzi, A. Wang, E. Brillas, I. Sirés and C. Durante, ACS Sustainable Chem. Eng., 2020, 8, 14425–14440 CrossRef CAS.
- Q. Liu, Y. Duan, Q. Zhao, F. Pan, B. Zhang and J. Zhang, Langmuir, 2014, 30, 8238–8245 CrossRef CAS PubMed.
- L. Liu, Q.-F. Deng, X.-X. Hou and Z.-Y. Yuan, J. Mater. Chem., 2012, 22, 15540–15548 RSC.
- W.-L. Zhang, Z.-B. Zhang, X.-H. Cao, R.-C. Ma and Y.-H. Liu, J. Radioanal. Nucl. Chem., 2014, 301, 197–205 CrossRef CAS.
- X. Zhong, Y. Sun, Z. Zhang, Y. Dai, Y. Wang, Y. Liu, R. Hua, X. Cao and Y. Liu, J. Radioanal. Nucl. Chem., 2019, 322, 901–911 CrossRef CAS.
- F. Shen, J. Su, X. Zhang, K. Zhang and X. Qi, Int. J. Biol. Macromol., 2016, 91, 443–449 CrossRef CAS PubMed.
- Q. Jin, Y. Li, D. Yang and J. Cui, RSC Adv., 2018, 8, 1255–1264 RSC.
- Y. Liu, L. Li, Z. Duan, Q. You, G. Liao and D. Wang, Colloids Surf., A, 2021, 610, 125728 CrossRef CAS.
- L. Zeng, X. Li, S. Fan, J. Mu, M. Qin, X. Wang, G. Gan, M. Tadé and S. Liu, ACS Sustainable Chem. Eng., 2019, 7, 5057–5064 CrossRef CAS.
- F. Marrakchi, M. J. Ahmed, W. A. Khanday, M. Asif and B. H. Hameed, Int. J. Biol. Macromol., 2017, 98, 233–239 CrossRef CAS PubMed.
- B. Chen, C. Zhang, L. Niu, X. Shi, H. Zhang, X. Lan and G. Bai, Chem. – Eur. J., 2018, 24, 3481–3487 CrossRef CAS PubMed.
- R. Gupta, N. Vadodariya, A. Mahto, J. P. Chaudhary, D. B. Parmar, D. N. Srivastava, S. K. Nataraj and R. Meena, J. Appl. Electrochem., 2018, 48, 37–48 CrossRef CAS.
- C. Chen, T. Ma, Y. Shang, B. Gao, B. Jin, H. Dan, Q. Li, Q. Yue, Y. Li and Y. Wang, Appl. Catal., B, 2019, 250, 382–395 CrossRef CAS.
- E. Raymundo-Piñero, M. Cadek and F. Béguin, Adv. Funct. Mater., 2009, 19, 1032–1039 CrossRef.
- S. Bo, X. Zhao, Q. An, J. Luo, Z. Xiao and S. Zhai, RSC Adv., 2019, 9, 5009–5024 RSC.
- J. P. Chaudhary, A. Mahto, N. Vadodariya, F. Kholiya, S. Maiti, S. K. Nataraj and R. Meena, RSC Adv., 2016, 6, 61716–61724 RSC.
- M. Yu, Y. Han, J. Li and L. Wang, Int. J. Biol. Macromol., 2018, 115, 185–193 CrossRef CAS PubMed.
- D. Nandan, G. Zoppellaro, I. Medřík, C. Aparicio, P. Kumar, M. Petr, O. Tomanec, M. B. Gawande, R. S. Varma and R. Zbořil, Green Chem., 2018, 20, 3542–3556 RSC.
- S.-H. Ho, Y.-d. Chen, R. Li, C. Zhang, Y. Ge, G. Cao, M. Ma, X. Duan, S. Wang and N.-q. Ren, Water Res., 2019, 159, 77–86 CrossRef CAS PubMed.
- L. Shao, H. Liu, W. Zeng, C. Zhou, D. Li, L. Wang, Y. Lan, F. Xu and G. Liu, Appl. Surf. Sci., 2019, 478, 1017–1026 CrossRef CAS.
- X. Zhao, Q.-D. An, Z.-Y. Xiao, S.-R. Zhai and Z. Shi, Chem. Eng. J., 2018, 353, 746–759 CrossRef CAS.
- N. Farhadian, R. Akbarzadeh, M. Pirsaheb, T. C. Jen, Y. Fakhri and A. Asadi, Int. J. Biol. Macromol., 2019, 132, 360–373 CrossRef CAS PubMed.
- K.-W. Jung and K.-H. Ahn, Bioresour. Technol., 2016, 200, 1029–1032 CrossRef CAS PubMed.
- S. Bo, X. Zhao, Q. An, J. Luo, Z. Xiao and S. Zhai, RSC Adv., 2019, 9, 5009–5024 RSC.
- N. Alhokbany, T. Ahama, Ruksana, M. Naushad and S. M. Alshehri, Composites, Part B, 2019, 173, 106950 CrossRef CAS.
- C. Lei, Y. Song, F. Meng, Y. Sun, D. C. W. Tsang, K. Yang and D. Lin, Sci. Total Environ., 2021, 756, 143866 CrossRef CAS PubMed.
- Y. Qi, B. Ge, Y. Zhang, B. Jiang, C. Wang, M. Akram and X. Xu, J. Hazard. Mater., 2020, 399, 123039 CrossRef CAS PubMed.
- Y. Wang, Q. Yang, J. Chen, J. Yang, Y. Zhang, Y. Chen, X. Li, W. Du, A. Liang, S.-H. Ho and J.-S. Chang, J. Hazard. Mater., 2020, 395, 122658 CrossRef CAS PubMed.
- B. Ghanim, T. F. O'Dwyer, J. J. Leahy, K. Willquist, R. Courtney, J. T. Pembroke and J. G. Murnane, J. Environ. Chem. Eng., 2020, 8, 104176 CrossRef CAS.
- X. Wang, C. Zhan, Y. Ding, B. Ding, Y. Xu, S. Liu and H. Dong, ACS Sustainable Chem. Eng., 2017, 5, 1457–1467 CrossRef CAS.
- L. Guo, Q.-D. An, Z.-Y. Xiao, S.-R. Zhai and L. Cui, ACS Sustainable Chem. Eng., 2019, 7, 9237–9248 CrossRef CAS.
- W. Zheng, Q. An, Z. Lei, Z. Xiao, S. Zhai and Q. Liu, RSC Adv., 2016, 6, 104897–104910 RSC.
- X. Tian, H. Zhu, X. Meng, J. Wang, C. Zheng, Y. Xia and Z. Xiong, ACS Sustainable Chem. Eng., 2020, 8, 12755–12767 CrossRef CAS.
|
This journal is © The Royal Society of Chemistry 2021 |