DOI:
10.1039/D3QI00314K
(Research Article)
Inorg. Chem. Front., 2023,
10, 3015-3024
Design of a robust rod-packing scandium–organic framework for C2Hx/CO2 separation, CO2 storage, and catalytic CO2 cycloaddition†
Received
18th February 2023
, Accepted 8th April 2023
First published on 8th April 2023
Abstract
The exploration of efficient CO2 capture and conversion techniques is of great importance for global sustainable development. Herein, a novel bi-microporous Sc-MOF, named [Sc3(NTB)2(CH3COO)3] (SNNU-616-Sc, NTB = nitrilotribenzoic acid), was successfully designed and utilized for CO2 storage and catalytic conversion. The linear [Sc3(COO)6] trinuclear clusters were linked by triple acetate anions into 1D chains, which were further extended by NTB linkers and interleaved to produce the 3D robust rod-packing Sc-MOF with two types of open channels of about 12 Å and 3.8 Å, respectively. Notably, the bare N atom from NTB ligands can not only act as active sites to adsorb CO2 molecules, but also provide Lewis basic sites for the CO2 fixation reaction. Together with the high framework stability and two types of microporous open channels, SNNU-616-Sc shows high adsorption selectivity to effectively separate CO2 from CO2–C2Hx binary mixtures (C2Hx = acetylene, C2H2; ethylene, C2H4; ethane, C2H6), and a CO2 storage capacity of 30 mmol g−1 (273 K and 29 bar), which surpasses most MOF adsorbents. Moreover, SNNU-616-Sc can also serve as an efficient recyclable catalyst for CO2 fixation with epoxides in the presence of tetrabutylammonium bromide as a co-catalyst without any organic solvent under mild conditions. Particularly, for the catalytic reaction of CO2 cycloaddition with epoxide bromopropane, the yields of cyclic carbonates can reach up to 97.5% with the selectivity higher than 98% and a conversion of 99%.
Introduction
The greenhouse gas carbon dioxide is the main cause of global warming, and its excessive emissions caused by the combustion of fossil fuel can bring about a series of serious environmental issues, such as extreme weather, ocean acidification, and the greenhouse effect.1,2 It is extremely critical to develop efficient technologies for the mitigation of CO2 emission to tremendously reduce the energy crisis and concurrently diminish environmental issues.3–5 In order to achieve this purpose, many contributions have been made by researchers in various fields in recent years.6,7
On the one hand, physical capture technology for CO2 molecules using porous solid adsorbents and the selective separation of CO2 from the C2-hydrocarbons produced from industrial manufacture8–10 have attracted researchers’ particular interest, as well as developing a series of materials for selective CO2 capture and separation from C2-hydrocarbons (C2H2, C2H4 and C2H6).11–18 On the other hand, to face environmental problems, converting CO2 to value-added chemical products for CO2 aftertreatment that can achieve a carbon-neutral energy cycle in the environment has also raised considerable concerns.2,19 Considering that the multifunctional applications of cyclic carbonates, such as solvents, degreasers, electrolytes in lithium-ion batteries, and precursors for the synthesis of fine chemicals and various polycarbonates,20,21 adding the excellent properties of stability and low toxic, the conversion of CO2 into cyclic carbonate becoming the most promising strategies for CO2 fixation.22 However, it is challenging to develop efficient, economical, and recyclable heterogeneous catalysts for CO2 conversion because of the high thermodynamic energy barrier for the inert C
O bond of CO2 molecules. Summing up the above, developing a kind of efficient CO2 capture and conversion technique with mild operating conditions and low energy consumption would decrease the global energy demand and carbon emission.
In recent decades, metal–organic frameworks (MOFs), a kind of promising crystalline porous material constructed from functionally organic linkers coupled with metal ions/clusters, have drawn much attention due to their high specific surface area, excellent porosity, regular pore systems, good chemical stability, and various topologies.23–31 Considering the exploitation of new absorbents, MOF materials are undoubtedly used as a candidate to ease the emission of greenhouse gases due to the advantages above and play important roles in catalyzing CO2 cycloaddition with epoxides in the CO2 fixation reaction.32–34
Given all this, a novel highly stable bi-microporous Sc-MOF (SNNU-616-Sc) with bare Lewis basic nitrogen sites was successfully synthesized to develop efficient CO2 capture and conversion materials. Thanks to the synergistic effects of extra-stability, open N sites and bi-microporosity, SNNU-616-Sc exhibits top-level CO2 storage capacity and efficient separation ability for the binary mixture of CO2–C2-hydrocarbons. Moreover, 1D channels with a size of about 12 Å in this structure can improve the mass transfer rate of the substrate during the catalytic reaction, which makes the SNNU-616-Sc material an efficient recyclable catalyst for CO2 fixation with epoxides. And the possible reaction mechanism for the catalytic reaction of CO2 cycloaddition was also discussed.
Experimental section
Materials and methods
Sc(NO3)3·9H2O, nitrilotribenzoic acid (H3NTB), N,N-dimethylformide (DMF), acetonitrile (CH3CN), and acetic acid (CH3COOH) were from commercial sources without further purification. Powder X-ray diffraction (PXRD) data were collected on a MiniFlex 600 X-ray diffractometer over the 2θ range of 5–50° using Cu Kα radiation at room temperature. Thermogravimetric analyses (TGA) were carried out in the range of 25–900 °C using an HCT-1 thermal analyzer with a heating rate of 2 °C min−1 under a N2 atmosphere. The high pressure gas adsorption performance for CO2 was analyzed on a BSD-PH high pressure gas sorption analyzer. Gas adsorption isotherms under 1 bar were obtained by using a 3-Flex surface-area and pore-size analyzer, and CO2, C2H4, C2H2, C2H6 and N2, and all gases used in the adsorption experiment were of 99.99% purity. Breakthrough experiments were conducted on a home-built dynamic gas breakthrough set-up.
Synthesis
Synthesis of [Sc3(NTB)2(CH3COO)3] (SNNU-616-Sc).
NTB (9 mg, 0.024 mmol) and Sc(NO3)3·9H2O (11 mg, 0.048 mmol) were dissolved in a mixed solution of 2 mL DMF and 2 mL CH3CN in a 25 mL glass vial, and then 0.5 mL of CH3COOH were added to this solution and sealed. After sonication for 10 minutes, the raw materials were completely dissolved to obtain a clear solution, and then the vial was placed into the oven and heated to 120 °C for 6 days. After the temperature dropped to room temperature, yellowish block crystals of SNNU-616-Sc were obtained and washed with fresh DMF. The crystal photo of the optical microscope is shown in Fig. S1.†
X-Ray single crystal structure determination
The diffraction data of the single crystal sample for SNNU-616-Sc were collected using a Bruker APEX-II CCD with GaKα (λ = 1.34139) radiation at 170 K. The structure was solved and refined by direct methods using the SHELXS program. All non-hydrogen atoms were refined anisotropically. The detailed crystallographic data and the structure refinement parameters of SNNU-616-Sc are summarized in Table S1.† Selected bond lengths and bond angles are given in Table S2.†
Gas adsorption
Before the measurements of gas adsorption, samples were exchanged with fresh pentane solvent and vacuum heated at 393 K for 10 h to obtain activated MOF samples. In order to evaluate the permanent porosity of SNNU-616-Sc, N2 adsorption measurements were conducted at 77 K. Gas adsorption measurements of activated samples for single components (CO2, C2H4, C2H2, and C2H6) at different temperatures (273 K, 283 K, and 298 K) were performed to evaluate the feasibility of SNNU-616-Sc MOF as an adsorbent material to separate CO2 from the CO2–C2Hx mixtures. High pressure gas adsorption performance analysis for CO2 was conducted at different temperatures to evaluate the storage ability of SNNU-616-Sc.
Breakthrough experiments
To further verify the actual binary CO2–C2-hydrocarbon separation performance, breakthrough column experiments were conducted for activated SNNU-616-Sc. About 500 mg of MOF samples were filled in a stainless-steel column (a length of 12 cm, an inner diameter of 0.44 cm, an external diameter of 0.6 cm), and helium was passed with the flow rate of 20 mL min−1 under ambient pressure at room temperature for 12 h to activate further. Subsequently, a CO2–C2Hx (50/50) mixture gas was passed into the column. Before each testing, a helium flow of 30 mL min−1 had to be maintained for 2–3 h to remove the air and residual gas molecule from the column.
Catalytic CO2 cycloaddition
Before the catalytic trials, SNNU-616-Sc was activated at 393 K under high vacuum (10−6 Torr) for 10 h. The activated-MOF catalyst (20 mg), epoxide substrates (20 mmol), and nBu4NBr (32 mg, 0.1 mmol) were placed in a Teflon sample holder inside a stainless-steel reactor. Before the catalytic reactions, the system was filled with CO2 to get rid of the residual air and then the reactor was sealed and pressurized with CO2 until 0.8 MPa, and the reactions proceeded at 80 °C for 8 h under stirring. After the catalytic reaction, the reactor was cooled in a water bath, and then ethyl acetate was added into the reactor and the product was taken out. The as-obtained suspension was finally centrifuged to obtain the liquid supernatant and diluted with ethyl acetate. After that, the product was analysed by gas chromatography with a flame ionization detector. For the recycling tests, the supernatant liquid was carefully removed after each catalytic run, and the solid catalyst was washed with acetone and dried to remove all volatile compounds before reusing for further catalytic cycles.
Results and discussion
Structural analysis
Single crystal X-ray diffraction analysis revealed that SNNU-616-Sc crystallizes in the trigonal system, space group R
. Each Sc(III) atom connects six O atoms to form an octahedral coordination model (Fig. 1a), and adjacent three Sc(III) atoms are linked by six carboxylates from six NTB organic linkers to afford a linear [Sc3(COO)6] trinuclear cluster. As shown in Fig. 1b, each NTB ligand connects three linear trinuclear clusters. Each linear trinuclear motif is bridged by three acetate anions, generating a 1D metal–organic chain (Fig. 1d). Three neighbour 1D chains were further connected by NTB linkers (Fig. 1c) in different directions, and thus interleaved to produce the 3D architecture of SNNU-616-Sc (Fig. 1e and f). Notably, two types of 1D channels with different sizes are observed along the c-axis direction, which are larger hexagonal and smaller triangular channels with their sizes of about 12 Å and 3.8 Å, respectively (Fig. 1e). Furthermore, the 1D Sc-carboxylate chains can be regarded as rod-like secondary building units, which make SNNU-616-Sc a novel rod-packing metal–organic framework.
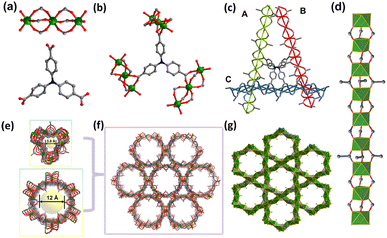 |
| Fig. 1 The structures of SNNU-616-Sc: (a) the linear [Sc3(COO)6] trinuclear cluster; (b) the linkage between [Sc3]-clusters and the NTB ligand; (c) the distribution of three 1D chains from different directions; (d) the detailed structure of the 1D chain extended by acetate anions and [Sc3]-clusters; (e) two types of 1D open channels with different sizes; (f) and (g) the 3D framework viewed along the c-axis direction. | |
It is noted that the small pore with a size of 3.8 Å is obviously fitting for selective CO2 adsorption (CO2, 3.18 × 3.33 × 5.36 Å3; C2H2, 3.32 × 3.34 × 5.7 Å3; C2H4, 3.28 × 4.18 × 4.84 Å3; C2H6, 4.08 × 3.81 × 4.82 Å3).35 Combined with the bare nitrogen atoms as efficient adsorptive sites for CO2 molecules, SNNU-616-Sc should be a good candidate for CO2 adsorption and separation applications under low pressure. The other pore of about 12 Å is large enough to facilitate not only high-pressure storage for CO2, but also rapid diffusion of molecules inside the pores, which can be expected to offer a confined space to accelerate the mass transfer and facilitate the catalytic reaction. Clearly, SNNU-616-Sc has great potential as a tri-functional material for C2Hx/CO2 separation, CO2 storage, and catalytic CO2 fixation.
Stability measurements and porosity characterization
The phase purity of the as-synthesized and activated SNNU-616-Sc MOF samples was confirmed by PXRD measurements (Fig. 2a). The chemical stability was measured by the treatment of MOF samples (30 mg) in solution (10 mL) with different pH values. The PXRD patterns of the as-synthesized and treated MOF samples matched well with the simulated pattern from the data of single crystal X-ray diffraction. These results indicated that SNNU-616-Sc can keep the skeleton intact for more than 48 h in the solutions with a wide pH value range from 3 to 11. The TGA curves (Fig. S2†) showed that the main temperature points of collapse for the SNNU-616-Sc sample before and after solvent exchange were similar. At the very beginning, the weight loss for the solvent-exchanged sample was observed below 373 K because of the loss of solvent molecules. After that, the skeleton was stable up to about 720 K under a N2 atmosphere and the framework will collapse over this temperature, which confirms the high thermal stability of SNNU-616-Sc.
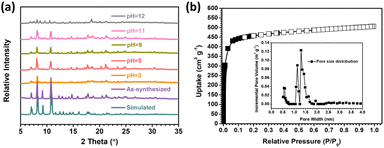 |
| Fig. 2 (a) PXRD patterns for SNNU-616-Sc after different treatments; (b) N2 adsorption–desorption isotherms at 77 K and the pore size distributions for SNNU-616-Sc. | |
N2 adsorption–desorption isotherms at 77 K confirmed that SNNU-616-Sc has excellent textural properties and exhibits permanent microporosity, as evidenced by reversible type I adsorption isotherms (Fig. 2b). The pore size distributions (PSD) determined by non-local density functional theory (NLDFT) are presented in Fig. 2b (inset). Two main types of pore sizes are observed, which are basically in accordance with the results indicated by the single crystal structure. Moreover, the Brunauer–Emmett–Teller specific surface area calculated from N2 adsorption isotherms is 1398 m2 g−1 and the pore volume is 0.87 cm3 g−1 for SNNU-616-Sc, which further indicate the great adsorption ability because the adsorption ability of the materials for CO2 largely depends on the specific surface area and the micropore volume of the adsorbent.36 In comparison to the reported MOF materials, the BET surface area of SNNU-616-Sc is less than those of MOF-177 (4508 m2 g−1),37 ZJU-195a (1722 m2 g−1),38 and MOF-505 (1547 m2 g−1),37 and but higher than those of many famous reported MOF materials, such as MIL-53 (Cr) (1197 m2 g−1),39 UPC-110 (1384 m2 g−1),40 SNNU-45 (1007 m2 g−1),41 and NKMOF-1-Ni (382 m2 g−1).42
Gas adsorption
The single-component gas adsorption experiments for CO2, C2H4, C2H2, and C2H6 were first conducted at different temperatures to explore the CO2 adsorption and separation performance for SNNU-616-Sc. According to Fig. 3, the CO2 uptake is 36.3 cm3 g−1 at 298 K and 1.0 bar. Under the same conditions, these values for C2H4, C2H2, and C2H6 are 69.6, 76.3, and 77.7 cm3 g−1, respectively. Obviously, SNNU-616-Sc shows much higher uptake capacity for C2-hydrocarbons than for CO2. In addition, the steeper adsorption curves of C2H4, C2H2, and C2H6 in the range of low pressure were reflected in a wide range of temperatures from 273 K to 298 K, which indicate stronger interactions with the MOF skeleton and indicate great potential for the separation of CO2 molecules from the C2-hydrocarbons.
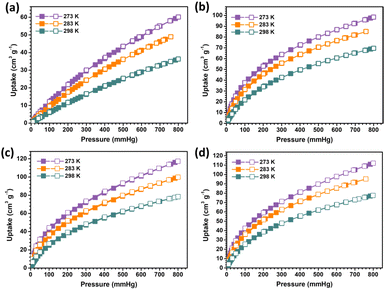 |
| Fig. 3 The gas adsorption isotherms at different temperatures: (a) CO2; (b) C2H4; (c) C2H2; and (d) C2H6. | |
The adsorption heat (Qst) in SNNU-616-Sc was further calculated based on the virial equations (eqn (S1) and (S2)†) to evaluate the binding strength between the MOF and gas molecules. The value of adsorption heat for CO2 at zero-coverage (20.3 kJ mol−1) is much lower than the values of C2H4 (27 kJ mol−1), C2H2 (28.7 kJ mol−1), and C2H6 (27.5 kJ mol−1) (Fig. 4a and S3†). These results indicate stronger interactions with the MOF skeleton for C2Hx than CO2 molecules, which are line with the adsorption curves under lower pressure. In addition, the −Qst value at zero-coverage of CO2 is less than those of many best CO2-uptake MOFs such as UTSA-74a (25 kJ mol−1),43 NKMOF-1-Ni (40.9 kJ mol−1),42 JCM-1 (33.4 kJ mol−1),44 and JXNU-5 (25.2 kJ mol−1),45 indicating the low regenerative energy consumption of SNNU-616-Sc during the process of recycling.
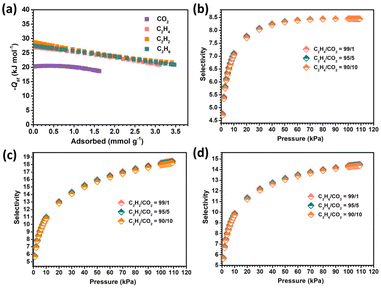 |
| Fig. 4 The calculated adsorption enthalpy for different gases (a), and the IAST separation selectivity at 298 K in SNNU-616-Sc for C2H4/CO2 (b), C2H2/CO2 (c), and C2H6/CO2 (d). | |
The ideal adsorbed solution theory (IAST) was applied to calculate the separation performance for binary CO2–C2Hx mixtures. The adsorption isotherms at 298 K were fitted by the Langmuir–Freundlich equation (eqn (S3)†). As shown in Fig. S4,† the calculated equimolar mixed gas selectivity values of C2H4/CO2, C2H2/CO2, and C2H6/CO2 at 298 K and 1.0 bar are 8.4, 16.5, and 13.5, respectively. The C2Hx/CO2 separation ability for different components at 298 K was further calculated (Fig. 4b–d), which shows that with the increase of pressure, the selectivity values increase. This can be attributed to the lateral interactions between CO2 molecules that were enhanced as the mixture pressure increased.46 Particularly, one percent of CO2 in the binary mixture of C2Hx/CO2 still show good separation selectivity, indicating the excellent ability of removing trace CO2 from the CO2–C2Hx mixtures. In general, SNNU-616-Sc has good separation potential to remove CO2 from the binary mixture of CO2–C2-hydrocarbons.
Breakthrough experiments
To confirm the practical separation performance of SNNU-616-Sc for the CO2–C2Hx mixture, breakthrough experiments were conducted. The binary mixture of CO2–C2Hx was injected into a packed column with a flow rate of 2.0 mL min−1 at 298 K to evaluate the separation performance. As depicted in Fig. 5a, the CO2 molecule broke through the bed quickly after feeding the gas mixture into the fixed adsorption column, while the detection time for C2H4, C2H2, and C2H6 is later than that of CO2 for these three kinds of binary mixtures, showing that the component of C2-hydrocarbons can remain for a longer time in comparison to the CO2 molecules in the breakthrough column. According to the breakthrough curves, CO2 molecules broke through the column at a time of 14.7 min g−1, whereas the time for C2H4, C2H2, and C2H6 was retained in the adsorption bed for 32.7, 31.6, and 34.9 min g−1, respectively, which indicate the stronger interaction between C2-hydrocarbons and the skeleton of SNNU-616-Sc than that of CO2, in line with the results of adsorption enthalpy. And the breakthrough time gaps for these three kinds of binary mixtures (C2H4/CO2, C2H2/CO2, C2H6/CO2) are similar to each other, which indicate an excellent separation performance based on the porous absorbent material SNNU-616-Sc. The actual capture amount of four kinds of gases calculated from the breakthrough curves (eqn (S5) and (S6)†) was 0.89, 1.7, 1.75, and 1.9 mmol g−1 for CO2, C2H4, C2H2, and C2H6, respectively. And the separation factors for C2H4/CO2, C2H2/CO2, and C2H6/CO2 were 1.91, 1.97 and 2.13. Moreover, the purity of the obtained CO2 from the three mixtures is above 99.5%.
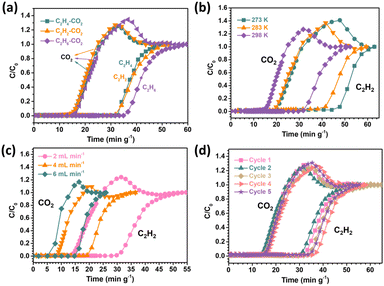 |
| Fig. 5 Breakthrough curves of SNNU-616-Sc under 1 bar for three equimolar mixtures at 298 K with the flow rate of 2 mL min−1 (a), the C2H2/CO2 mixture at different temperatures with a flow rate of 2 mL min−1 (b), the C2H2/CO2 mixture with different flow rates at 298 K (c), and five recycling breakthrough curves for C2H2/CO2 at 298 K with a flow rate of 2 mL min−1 (d). | |
Moreover, the breakthrough experiments of the C2H2/CO2 binary mixture under different conditions were further conducted to explore the effects of temperature and gas flow rate on the separation performance in actual application. As shown in Fig. 5b, the separation interval time of SNNU-616-Sc for C2H2/CO2 is 15.8 min g−1 at 298 K and 1 bar, which increases with the decreasing temperature. The separation time is shorter than that of reported materials such as JCM-1,44 UTSA-74a,47 and FJU-90a,48 and comparable to the benchmark ZJUT-2a,49 and UPC-200(Al)-F-BIM.50 At 283 K and 273 K, the separation interval times reach 21.2 min g−1 and 25.4 min g−1, respectively. On the other hand, when the flow rate decreases, the separation interval time increases clearly, but when the gas flow rate increases, a shorter separation interval time and smaller transfer mass were observed (Fig. 5c). Even with a flow rate of 6 mL min−1, the C2H2/CO2 separation interval time still is about 10 min g−1.
Ideal gas adsorbents should have good recyclability in practical industrial applications. Five successive C2H2/CO2 dynamic breakthrough experiments were carried out on SNNU-616-Sc at 298 K and 1 bar with a flow rate of 2 mL min−1 to evaluate the recyclability. As shown in Fig. 5d, almost constant breakthrough curves indicate its outstanding recyclability and stability. Furthermore, the breakthrough curves at different temperatures for C2H4/CO2 and C2H6/CO2 were also evaluated and are depicted in Fig. 6. Similar to the C2H2/CO2 mixture, the separation interval time increases to about 30 and 25 min g−1 for C2H6/CO2 and C2H4/CO2 mixtures at 273 K. In our opinion, the smaller triangular channels with a size of 3.8 Å in the structure of Sc-MOF should mainly contribute to the prominent C2Hx/CO2 separation performance, which surpasses many famous MOF adsorbents and makes SNNU-616-Sc a great adsorbent for practical separation in industrial applications.
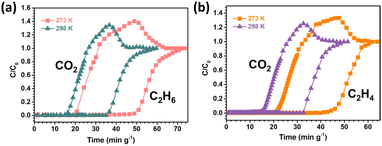 |
| Fig. 6 The breakthrough curves at different temperatures under 1 bar with the flow rate of 2 mL min−1 for C2H6/CO2 (a) and C2H4/CO2 (b). | |
High-pressure CO2 storage
The single-component CO2 adsorption isotherm of SNNU-616-Sc has no tendency of gentle curve in comparison to the other three C2-hydrocarbon gases from 0 to 1 bar, which indicates that SNNU-616-Sc may be can adsorb much more CO2 under higher pressure. At the same time, taking the high BET specific surface area (1398 m2 g−1) and larger pore size of 1D hexagonal channels (12 Å) into account, SNNU-616-Sc should be more propitious to high-pressure CO2 storage. High-pressure CO2 adsorption results at different temperatures for SNNU-616-Sc show that the storage capacity can reach as high as 30 mmol g−1 (672.2 cm3 g−1 and 48.8 wt%) at 273 K and 29 bar (Fig. 7a and Table S4†), which is slightly lower than the performance of MFM-160a (32 mmol g−1, 19.8 bar) and superior to most MOFs reported at 273 K (Fig. S7†), such as MIL-125-Ti (10.761 mmol g−1, 9.8 bar),51 β-Zn (8 mmol g−1, 28 bar),52 MIX-MIL-125-Ti (7.71 mmol g−1, 9.8 bar),51 MOF-74-Mg (∼7 mmol g−1, 30 bar),53 MFC-1 (6.7 mmol g−1, 30 bar),53 MIL-100-Fe (0.62 mmol g−1, 30 bar),53 and MMC1 (∼0.6 mmol g−1, 30 bar).53 At room temperature, SNNU-616-Sc still can take up CO2 of 17.1 mmol g−1 (384.3 cm3 g−1, 29 bar), which was competitive with many famous MOFs under the same conditions like MOF-505 (18 mmol g−1, 30 bar),37 MIL-101-Cr (14.38 mmol g−1, 40 bar),54 MIL-53-Cr (10.6 mmol g−1, 25 bar),39 and MIL-53-Al (9.5 mmol g−1, 25 bar).55 Besides, SNNU-616-Sc displays excellent reusability for CO2 storage under at least five regeneration conditions (Fig. 7b).
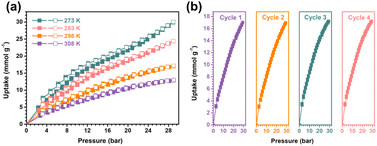 |
| Fig. 7 The high-pressure CO2 adsorption–desorption curves at different temperatures (a) and the recyclability results (b) at 298 K. | |
GCMC simulations
GCMC simulations were further adopted for SNNU-616-Sc to investigate the probable adsorption sites of CO2 and C2-hydrocarbons in the MOF skeleton. As shown in Fig. S8,† the probable sites of CO2 molecules in SNNU-616-Sc are mainly distributed in triangular channels with a suitable pore size, and the second sites are distributed in the surroundings of the N atom sites from the NTB ligands. SNNU-616-Sc shows three same binding site distribution toward C2H2, C2H4, and C2H6, in which the first two adsorptive sites are the same as for CO2 molecules. The third sites are within the larger hexagonal channels. So, the number of adsorptive sites for C2-hydrocarbons is clearly more than those for CO2 molecules in the structure of SNNU-616-Sc, combined with the suitable pore volume and the higher strength of the interaction between C2 hydrocarbons and the skeleton than the CO2 molecules, and further supports the efficient separation performance of CO2 molecules from C2Hx/CO2 mixtures.
The difference in the interactions between guest molecules and the MOF skeleton in the SNNU-616-Sc may arise from the Lewis basic bare N sites. The binding sites of CO2, C2H4, C2H2 and C2H6 were further evaluated by modelling studies. The distances of C–H⋯N for C2-hydrocarbons (C2H4, C2H2, and C2H6) and O
C⋯N for CO2 molecules were obtained. As given in Fig. 8, the O
C⋯N distance for CO2 molecules (5.05 Å) is markedly longer than the C–H⋯N distances for C2-hydrocarbons (C2H4, 4.4 Å; C2H2, 4.98 Å; C2H6, 4.19 Å), showing stronger interactions of C2-hydrocarbons than CO2, which also offers theoretic support for the effective CO2–C2-hydrocarbon separation performance.
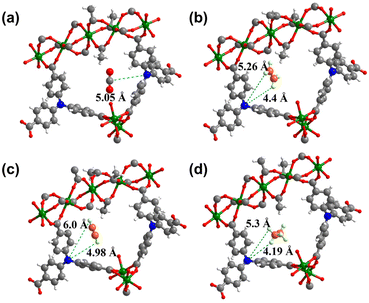 |
| Fig. 8 The binding sites between bare N sites and CO2 (a), C2H4 (b), C2H2 (c) and C2H6 (d) molecules calculated by modelling studies for SNNU-616-Sc. | |
Cycloaddition of CO2 with epoxides
The prominent CO2 adsorption and separation performances of SNNU-616-Sc encourage us to further investigate the catalytic activity for cycloaddition of epoxides with CO2. Accordingly, a series of epoxide substrates were examined for the synthesis of the corresponding cyclic carbonates in the presence of SNNU-616-Sc as a catalyst at 0.8 MPa CO2 pressure and 353 K (Table 1). As for entry 1 to entry 3, epoxides with alkyl chains of different lengths were used as substrates for the reaction, and the yields of epoxypropane, epoxybutane, and epoxy hexane were 95.8%, 94.2%, and 73.6%, respectively. Among them, epoxy hexane with the longest alkyl chain showed the lowest yield, which indicated that the catalyst activity of the cycloaddition reaction declined with the increase of steric hindrance. So, the effective size of the epoxides is necessary to facilitate their entrance into the channel to close the catalytically active sites. Only 74.6% of epoxy hexane was converted due to its difficult diffusion into the pores of the catalyst, and the difficulty of ring opening due to the large steric hindrance of the benzene ring hindering the Br− attack also resulted in its low conversion. Moreover, SNNU-616-Sc exhibits highly efficient catalytic activity with a yield of 97.5% in carbonate formation after 8 h with 99% conversion and 98.6% selectivity when epoxide bromopropane was used as a reactant in the presence of nBu4NBr as a co-catalyst (Table 1, entry 5).
Table 1 Catalytic performance of SNNU-616-Sc for the CO2 cycloaddition reaction with different epoxides
No |
Substrate |
PCO2 (MPa) |
T (°C) |
t (h) |
Yield (%) |
Con. (%) |
Select. (%) |
Reaction conditions: epoxide = 20 mmol; catalyst = 20 mg SNNU-616-Sc; nBu4NBr = 0.1 mmol, 32 mg; semi-batch reaction; determined by GC. Without a catalyst. Catalyst = Sc(NO3)3·9H2O. Catalyst = NTB ligand. |
1 |
|
0.8 |
80 |
8 |
95.8 |
97.2 |
95.6 |
2 |
|
0.8 |
80 |
8 |
94.2 |
99.9 |
94.3 |
3 |
|
0.8 |
80 |
8 |
73.6 |
74.6 |
94.2 |
4 |
|
0.8 |
80 |
8 |
90.2 |
92.3 |
97.7 |
5 |
|
0.8 |
80 |
8 |
97.5 |
99 |
98.6 |
6a |
|
0.8 |
80 |
8 |
52.5 |
47.5 |
98.8 |
7b |
|
0.8 |
80 |
8 |
74.0 |
81.9 |
90.4 |
8c |
|
0.8 |
80 |
8 |
37.7 |
36.7 |
99.8 |
The blank experiment (entry 6) by only adding the cocatalyst nBu4NBr was conducted under the same conditions without SNNU-616-Sc, and the yield of cyclic carbonates is only 52.5% with a low conversion rate of 47.5%, indicating that nBu4NBr played an important role in ring opening, but it is deemed insufficient in improving the catalytic activity due to the lack of sufficient catalytic sites and mass transfer channels of the substrate. From the entries 5 and 6, Sc(NO3)3·9H2O metal salts or NTB ligands are used as catalysts added to the reaction in the presence of nBu4NBr, which shows clearly lower catalytic activity in comparison to the SNNU-616-Sc MOF catalyst. Therefore, the catalytic sites and mass transfer channels are of great significance in the catalytic reactions of CO2 cycloaddition.
Recyclability is a critical criterion for an effective heterogeneous catalysis. The cycling experiments for epoxide bromopropane were also conducted under the same conditions (80 °C, 8 h, 0.8 MPa of CO2 pressure) after easy separation and a simple filtration for SNNU-616-Sc, and washed several times with acetone. Fig. 9a shows that the recycled MOF catalyst can be reused up to at least five consecutive times without any considerable activity attenuation, showing an excellent recyclability. Moreover, the regenerative SNNU-616-Sc catalyst was analysed by PXRD. The PXRD patterns for the fresh MOF and recovered catalyst after 5 cycles are in full agreement with each other, further supporting the extraordinary catalytic stability of the SNNU-616-Sc catalyst (Fig. 9b).
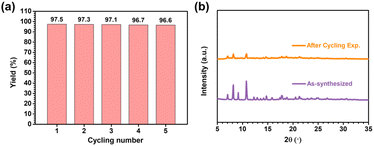 |
| Fig. 9 (a) The yield of epoxide bromopropane for five catalytic cycles; (b) PXRD patterns for SNNU-616-Sc samples after the CO2 cycloaddition reactions. | |
Temperature-programmed desorption (TPD) of CO2 and NH3 analysis were performed to investigate the acid–base nature of the catalyst. As shown in Fig. S9,† SNNU-616-Sc shows an obvious peak at about 523 K for TPD-CO2, and TPD-NH3 has very little peaks over the whole range of temperatures, indicating the presence of strong basic sites in this structure and almost no acidic sites in the catalyst. The results of TPD analyses confirmed that the SNNU-616-Sc catalyst offers strong basic sites for the CO2 cycloaddition catalytic reactions.
Cycloaddition reaction mechanism
Based on the single crystal structure, CO2 adsorption and catalytic CO2 cycloaddition of SNNU-616-Sc with epoxides, a plausible catalytic reaction mechanism was proposed.56 As shown in Fig. 10, in the first step, the bare N sites with lone pair electrons acted as Lewis basic sites to activate CO2 molecules. In the second step, Br− anions generated from the co-catalyst attack the less hindered C atom of the coordinated epoxides, followed by a ring-opening step. Thereafter, activated CO2 interacts with the oxygen anion of the opened epoxy ring, forming an alkyl carbonate anion, and the corresponding cyclic carbonate is generated through ring closure with the elimination of the bromide ion. So, the good catalytic performance of SNNU-616-Sc is believed to be attributed to the synergistic effect of the basic catalytic sites and large mass transfer 1D channels in the presence of nBu4NBr.
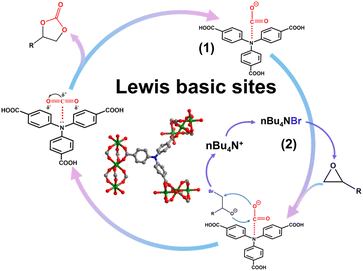 |
| Fig. 10 The proposed catalytic mechanism of SNNU-616-Sc for CO2 cycloaddition. | |
Conclusions
In this work, a robust rod-packing Sc-MOF with two types of micropores and Lewis basic bare N atoms was synthesized and utilized for CO2 adsorption and conversion. Benefitting from the synergistic effects of high chemical and thermal stability, bi-microporous open channels, and bare N sites, the Sc-MOF exhibits not only a prominent separation ability of CO2 from C2Hx–CO2 binary mixtures, but also an extra-high CO2 storage capacity. Remarkably, the Sc-MOF also can act as an excellent catalyst for CO2 cycloaddition with epoxides with high productivity, prominent selectivity, and good recyclability. In general, we offer a helpful route to explore novel CCS materials with high CO2 adsorption and conversion performance under mild conditions, which are critical for the global energy demand and carbon emission.
Author contributions
Hong-Juan Lv: methodology, data collection and analysis, and writing the original draft. Shu-Cong Fan: investigation and data analysis. Yu-Cheng Jiang: formal analysis. Shu-Ni Li: investigation and resources. Quan-Guo Zhai: supervision, checking & editing, and funding acquisition.
Conflicts of interest
There are no conflicts to declare.
Acknowledgements
This work is financially supported by the National Natural Science Foundation of China (22071140), the Natural Science Foundation of Shaanxi Province (2021JLM-20), and the Fundamental Research Funds for the Central Universities (GK202101002).
References
- D. Gilfillan and G. Marland, CDIAC-FF: Global and National CO2 Emissions from Fossil Fuel Combustion and Cement Manufacture: 1751–2017, Earth Syst. Sci. Data, 2021, 13, 1667–1680 CrossRef.
- S. S. A. Shah, T. Najam, M. Wen, S.-Q. Zang, A. Waseem and H.-L. Jiang, Metal–Organic Framework-Based Electrocatalysts for CO2 Reduction, Small Struct., 2022, 3, 2100090 CrossRef CAS.
- J. Yu, L.-H. Xie, J.-R. Li, Y. Ma, J. M. Seminario and P. B. Balbuena, CO2 Capture and Separations Using MOFs: Computational and Experimental Studies, Chem. Rev., 2017, 117, 9674–9754 CrossRef CAS PubMed.
- L. Lei, Y. Cheng, C. Chen, M. Kosari, Z. Jiang and C. He, Taming Structure and Modulating Carbon Dioxide (CO2) Adsorption Isosteric Heat of Nickel-Based Metal Organic Framework (MOF-74(Ni)) for Remarkable CO2 capture, J. Colloid Interface Sci., 2022, 612, 132–145 CrossRef CAS PubMed.
- Y. Ding, Z. Pang, K. Lan, Y. Yao, G. Panzarasa, L. Xu, M. Lo Ricco, D. R. Rammer, J. Y. Zhu, M. Hu, X. Pan, T. Li, I. Burgert and L. Hu, Emerging Engineered Wood for Building Applications, Chem. Rev., 2023, 123(5), 1843–1888 CrossRef CAS PubMed.
- F. A. Philip and A. Henni, Enhancement of Post-Combustion CO2 Capture Capacity by Incorporation of Task-Specific Ionic Liquid into ZIF-8, Microporous Mesoporous Mater., 2022, 330, 111580 CrossRef CAS.
- D. Fu and M. E. Davis, Carbon Dioxide Capture with Zeotype Materials, Chem. Soc. Rev., 2022, 51, 9340–9370 RSC.
- Y. Xie, H. Cui, H. Wu, R.-B. Lin, W. Zhou and B. Chen, Electrostatically Driven Selective Adsorption of Carbon Dioxide over Acetylene in an Ultramicroporous Material, Angew. Chem., Int. Ed., 2021, 60, 9604–9609 CrossRef CAS PubMed.
- Z. Zhang, S. B. Peh, R. Krishna, C. Kang, K. Chai, Y. Wang, D. Shi and D. Zhao, Optimal Pore Chemistry in an Ultramicroporous Metal-Organic Framework for Benchmark Inverse CO2/C2H2 Separation, Angew. Chem., Int. Ed., 2021, 60, 17198–17204 CrossRef CAS PubMed.
- L. Jiao, J. Y. R. Seow, W. S. Skinner, Z. U. Wang and H.-L. Jiang, Metal–Organic Frameworks: Structures and Functional Applications, Mater. Today, 2019, 27, 43–68 CrossRef CAS.
- Z. Zhu, J. Hu, X. Geng, B. Qin, K. Ma, Y. Wang and J. Gao, Process Design of Carbon Dioxide and Ethane Separation using Ionic Liquid by Extractive Distillation, J. Chem. Technol. Biotechnol., 2018, 93, 887–896 CrossRef CAS.
- H. Wang, M. Fan, Z. Zhang, J. Hao and C. Wang, Control of Cryogenic Extractive Distillation Process for Separating CO2−C2H6 Azeotrope, Comput. Chem. Eng., 2019, 128, 384–391 CrossRef CAS.
- H. Wang, C. Wang, Z. Zhang, M. Fan, X. Yan and F. Li, Selection of State Equation and Innovative Process Design for Removing CO2 by Azeotropic Distillation, Chem. Eng. Technol., 2021, 44, 710–722 CrossRef CAS.
- S. Wang, Q. Yang and C. Zhong, Adsorption and Separation of Binary Mixtures in a Metal-Organic Framework Cu-BTC: A Computational Study, Sep. Purif. Technol., 2008, 60, 30–35 CrossRef CAS.
- I. V. Zandvoort, E.-J. Ras, R. D. Graaf and R. Krishna, Using Transient Breakthrough Experiments for Screening of Adsorbents for Separation of C2H4/CO2 Mixtures, Sep. Purif. Technol., 2020, 241, 116706 CrossRef.
- G. Xu, Z. Meng, X. Guo, H. Zhu, K. Deng, C. Xiao and Y. Liu, Molecular
Simulations on CO2 Adsorption and Adsorptive Separation in Fullerene Impregnated MOF-177, MOF-180 and MOF-200, Comput. Mater. Sci., 2019, 168, 58–64 CrossRef CAS.
- H. J. Jun, D. K. Yoo and S. H. Jhung, Metal-organic Framework (MOF-808) Functionalized with Ethyleneamines: Selective Adsorbent to Capture CO2 under Low Pressure, J. CO2 Util., 2022, 58, 101932 CrossRef CAS.
- Y. Wan, Y. Miao, R. Zhong and R. Zou, High-Selective CO2 Capture in Amine-Decorated Al-MOFs, Nanomaterials, 2022, 12, 4056–4065 CrossRef CAS PubMed.
- L. Wang, Y. Dong, T. Yan, Z. Hu, A. A. Jelle, D. M. Meira, P. N. Duchesne, J. Y. Y. Loh, C. Qiu, E. E. Storey, Y. Xu, W. Sun, M. Ghoussoub, N. P. Kherani, A. S. Helmy and G. A. Ozin, Black Indium Oxide a Photothermal CO2 Hydrogenation Catalyst, Nat. Commun., 2020, 11, 2432 CrossRef CAS PubMed.
- T. Lescouet, C. Chizallet and D. Farrusseng, The Origin of the Activity of Amine-Functionalized Metal–Organic Frameworks in the Catalytic Synthesis of Cyclic Carbonates from Epoxide and CO2, ChemCatChem, 2012, 4, 1725–1728 CrossRef CAS.
- R. Babu, A. C. Kathalikkattil, R. Roshan, J. Tharun, D.-W. Kim and D.-W. Park, Dual-Porous Metal Organic Framework for Room Temperature CO2 Fixation via Cyclic Carbonate Synthesis, Green Chem., 2016, 18, 232–242 RSC.
- Y. Tang, W. Chen, R. Liu, L. Wang, Y. Pan, R. Bi, X. Feng, M. He, Q. Chen and Z. Zhang, Solvent-Free CO2 Fixation Reaction Catalyzed by MOFs Composites Containing Polycarboxylic Acid Ligands, ChemistrySelect, 2021, 6, 5350–5355 CrossRef CAS.
- Z. J. Chen, M. R. Mian, S. J. Lee, H. Y. Chen, X. Zhang, K. O. Kirlikovali, S. Shulda, P. Melix, A. S. Rosen, P. A. Parilla, T. Gennett, R. Q. Snurr, T. Islamoglu, T. Yildirim and O. K. Farha, Fine-Tuning a Robust Metal-Organic Framework toward Enhanced Clean Energy Gas Storage, J. Am. Chem. Soc., 2021, 143, 18838–18843 CrossRef CAS PubMed.
- J. Pei, X.-W. Gu, C.-C. Liang, B. Chen, B. Li and G. Qian, Robust and Radiation-Resistant Hofmann-Type Metal–Organic Frameworks for Record Xenon/Krypton Separation, J. Am. Chem. Soc., 2022, 144, 3200–3209 CrossRef CAS PubMed.
- L. Liu, S. Du, X. Guo, Y. Xiao, Z. Yin, N. Yang, Y. Bao, X. Zhu, S. Jin, Z. Feng and F. Zhang, Water-Stable Nickel Metal–Organic Framework Nanobelts for Cocatalyst-Free Photocatalytic Water Splitting to Produce Hydrogen, J. Am. Chem. Soc., 2022, 144, 2747–2754 CrossRef CAS PubMed.
- J.-D. Xiao and H.-L. Jiang, Metal–Organic Frameworks for Photocatalysis and Photothermal Catalysis, Acc. Chem. Res., 2019, 52, 356–366 CrossRef CAS PubMed.
- Y.-Y. Xue, X.-Y. Bai, J. Zhang, Y. Wang, S.-N. Li, Y.-C. Jiang, M.-C. Hu and Q.-G. Zhai, Precise Pore Space Partitions Combined with High-Density Hydrogen-Bonding Acceptors within Metal–Organic Frameworks for Highly Efficient Acetylene Storage and Separation, Angew. Chem., Int. Ed., 2021, 60, 10122–10128 CrossRef CAS PubMed.
- J. Wang, Y. Zhang, Y. Su, X. Liu, P. Zhang, R.-B. Lin, S. Chen, Q. Deng, Z. Zeng, S. Deng and B. Chen, Fine Pore Engineering in a Series of Isoreticular Metal-Organic Frameworks for Efficient C2H2/CO2 separation, Nat. Commun., 2022, 13, 200 CrossRef CAS PubMed.
- X. Zhang, R.-B. Lin, H. Wu, Y. Huang, Y. Ye, J. Duan, W. Zhou, J.-R. Li and B. Chen, Maximizing Acetylene Packing Density for Highly Efficient C2H2/CO2 Separation through Immobilization of Amine Sites within a Prototype MOF, Chem. Eng. J., 2022, 431, 134184 CrossRef CAS.
- X.-J. Kong and J.-R. Li, An Overview of Metal–Organic Frameworks for Green Chemical Engineering, Engineering, 2021, 7, 1115–1139 CrossRef CAS.
- J.-R. Li, J. Yu, W. Lu, L.-B. Sun, J. Sculley, P. B. Balbuena and H.-C. Zhou, Porous Materials with Pre-Designed Single-Molecule Traps for CO2 Selective Adsorption, Nat. Commun., 2013, 4, 1538 CrossRef PubMed.
- B. Parmar, P. Patel, R. S. Pillai, R. K. Tak, R. I. Kureshy, N.-U. H. Khan and E. Suresh, Cycloaddition of CO2 with an Epoxide-Bearing Oxindole Scaffold by a Metal–Organic Framework-Based Heterogeneous Catalyst under Ambient Conditions, Inorg. Chem., 2019, 58, 10084–10096 CrossRef CAS PubMed.
- G. Yunjang, C. Youngson and P. Dae-Won, Catalytic Performance of CPM-200-In/Mg in the Cycloaddition of CO2 and Epoxides, Catalysts, 2021, 11, 430–444 CrossRef.
- S.-C. Fan, S.-Q. Chen, J.-W. Wang, Y.-P. Li, P. Zhang, Y. Wang, W. Yuan and Q.-G. Zhai, Precise Introduction of Single Vanadium Site into Indium–Organic Framework for CO2 Capture and Photocatalytic Fixation, Inorg. Chem., 2022, 61, 14131–14139 CrossRef CAS PubMed.
- W. Xie, L. Yang, J. Zhang and X. Zhao, The Adsorptive Separation of Ethylene from C2 Hydrocarbons by Metal–Organic Frameworks, Chem. – Eur. J., 2023, e202300158 CrossRef PubMed.
- Y. Cao, Y. Zhao, Z. Lv, F. Song and Q. Zhong, Preparation and Enhanced CO2 Adsorption Capacity of UiO-66/Graphene Oxide Composites, J. Ind. Eng. Chem., 2015, 27, 102–107 CrossRef CAS.
- A. R. Millward and O. M. Yaghi, Metal−Organic Frameworks with Exceptionally High Capacity for Storage of Carbon Dioxide at Room Temperature, J. Am. Chem. Soc., 2005, 127, 17998–17999 CrossRef CAS PubMed.
- L. Zhang, K. Jiang, Y. Li, D. Zhao, Y. Yang, Y. Cui, B. Chen and G. Qian, Microporous Metal–Organic Framework with Exposed Amino Functional Group for High Acetylene Storage and Excellent C2H2/CO2 and C2H2/CH4 Separations, Cryst. Growth Des., 2017, 17, 2319–2322 CrossRef CAS.
- X. Zhou, W. Huang, J. Liu, H. Wang and Z. Li, Quenched Breathing Effect, Enhanced CO2 Uptake and Improved CO2/CH4 Selectivity of MIL-53(Cr)/Graphene Oxide Composites, Chem. Eng. Sci., 2017, 167, 98–104 CrossRef CAS.
- W. Fan, X. Wang, X. Liu, B. Xu, X. Zhang, W. Wang, X. Wang, Y. Wang, F. Dai, D. Yuan and D. Sun, Regulating C2H2 and CO2 Storage and Separation through Pore Environment Modification in a Microporous Ni-MOF, ACS Sustainable Chem. Eng., 2019, 7, 2134–2140 CrossRef CAS.
- Y.-P. Li, Y. Wang, Y.-Y. Xue, H.-P. Li, Q.-G. Zhai, S.-N. Li, Y. Jiang, M.-C. Hu and X. Bu, Ultramicroporous Building Units as a Path to Bi-microporous Metal-Organic Frameworks with High Acetylene Storage and Separation Performance, Angew. Chem., Int. Ed., 2019, 58, 13590–13595 CrossRef CAS PubMed.
- Y.-L. Peng, T. Pham, P. Li, T. Wang, Y. Chen, K.-J. Chen, K. A. Forrest, B. Space, P. Cheng, M. J. Zaworotko and Z. Zhang, Robust Ultramicroporous Metal–Organic Frameworks with Benchmark Affinity for Acetylene, Angew. Chem., Int. Ed., 2018, 57, 10971–10975 CrossRef CAS PubMed.
- F. Luo, C. Yan, L. Dang, R. Krishna, W. Zhou, H. Wu, X. Dong, Y. Han, T.-L. Hu, M. O'Keeffe, L. Wang, M. Luo, R.-B. Lin and B. Chen, UTSA-74: A MOF-74 Isomer with Two Accessible Binding Sites per Metal Center for Highly Selective Gas Separation, J. Am. Chem. Soc., 2016, 138, 5678–5684 CrossRef CAS PubMed.
- J. Lee, C. Y. Chuah, J. Kim, Y. Kim, N. Ko, Y. Seo, K. Kim, T. H. Bae and E. Lee, Separation of Acetylene from Carbon Dioxide and Ethylene by a Water-Stable Microporous Metal–Organic Framework with Aligned Imidazolium Groups inside the Channels, Angew. Chem., Int. Ed., 2018, 57, 7869–7873 CrossRef CAS PubMed.
- R. Liu, Q.-Y. Liu, R. Krishna, W. Wang, C.-T. He and Y.-L. Wang, Water-Stable Europium 1,3,6,8-Tetrakis(4-carboxylphenyl)pyrene Framework for Efficient C2H2/CO2 Separation, Inorg. Chem., 2019, 58, 5089–5095 CrossRef CAS PubMed.
- Z. Zhang, S. Xian, Q. Xia, H. Wang, Z. Li and J. Li, Enhancement of CO2 Adsorption and CO2/N2 Selectivity on ZIF-8 via Postsynthetic Modification, AIChE J., 2013, 59, 2195–2206 CrossRef CAS.
- F. Luo, C. Yan, L. Dang, R. Krishna, W. Zhou, H. Wu, X. Dong, Y. Han, T. L. Hu, M. O'Keeffe, L. Wang, M. Luo, R. B. Lin and B. Chen, UTSA-74: A MOF-74 Isomer with Two Accessible Binding Sites per Metal Center for Highly Selective Gas Separation, J. Am. Chem. Soc., 2016, 138, 5678–5684 CrossRef CAS PubMed.
- Y. Ye, Z. Ma, R.-B. Lin, R. Krishna, W. Zhou, Q. Lin, Z. Zhang, S. Xiang and B. Chen, Pore Space Partition within a Metal–Organic Framework for Highly Efficient C2H2/CO2 Separation, J. Am. Chem. Soc., 2019, 141, 4130–4136 CrossRef CAS PubMed.
- H.-M. Wen, C. Liao, L. Li, L. Yang, J. Wang, L. Huang, B. Li, B. Chen and J. Hu, Reversing C2H2−CO2 Adsorption Selectivity in an Ultramicroporous Metal–Organic Framework Platform, Chem. Commun., 2019, 55, 11354–11357 RSC.
- W. Fan, S. Yuan, W. Wang, L. Feng, X. Liu, X. Zhang, X. Wang, Z. Kang, F. Dai, D. Yuan, D. Sun and H.-C. Zhou, Optimizing Multivariate Metal–Organic Frameworks for Efficient C2H2/CO2 Separation, J. Am. Chem. Soc., 2020, 142, 8728–8737 CrossRef PubMed.
- Z. H. Rada, H. R. Abid, J. Shang, Y. He, P. Webley, S. Liu, H. Sun and S. Wang, Effects of Amino Functionality on Uptake of CO2, CH4 and Selectivity of CO2/CH4 on Titanium Based MOFs, Fuel, 2015, 160, 318–327 CrossRef CAS.
- S. Galli, N. Masciocchi, G. Tagliabue, A. Sironi, J. A. R. Navarro, J. M. Salas, L. Mendez-Liñan, M. Domingo, M. Perez-Mendoza and E. Barea, Polymorphic Coordination Networks Responsive to CO2, Moisture, and Thermal Stimuli: Porous Cobalt(II) and Zinc(II) Fluoropyrimidinolates, Chem. – Eur. J., 2008, 14, 9890–9901 CrossRef CAS PubMed.
- R. Ben-Mansour, N. A. A. Qasem and M. A. Habib, Adsorption Characterization and CO2 Breakthrough of MWCNT/Mg-MOF-74 and MWCNT/MIL-100(Fe) Composites, Int. J. Energy Environ. Eng., 2018, 9, 169–185 CrossRef CAS.
- S. Pourebrahimi, M. Kazemeini and L. Vafajoo, Embedding Graphene Nanoplates into MIL-101(Cr) Pores: Synthesis, Characterization, and CO2 Adsorption Studies, Ind. Eng. Chem. Res., 2017, 56, 3895–3904 CrossRef CAS.
- S. Pourebrahimi, M. Kazemeini, E. Ganji Babakhani and A. Taheri, Removal of the CO2 from Flue Gas Utilizing Hybrid Composite Adsorbent MIL-53(Al)/GNP Metal-Organic Framework, Microporous Mesoporous Mater., 2015, 218, 144–152 CrossRef CAS.
- H.-G. Jin, F. Chen, H. Zhang, W. Xu, Y. Wang, J. Fan and Z.-S. Chao, Postmetalation of a New Porphyrin Ligand-Based Metal–Organic Framework for Catalytic Oxidative Carboxylation of Olefins, J. Mater. Sci., 2020, 55, 16184–16196 CrossRef CAS.
|
This journal is © the Partner Organisations 2023 |