DOI:
10.1039/D4SE01567C
(Review Article)
Sustainable Energy Fuels, 2025,
9, 1414-1431
Review of issues and opportunities for glass supply for photovoltaic production at multiterawatt (TW) scale
Received
10th November 2024
, Accepted 3rd January 2025
First published on 23rd January 2025
Abstract
Current solar photovoltaic (PV) installation rates are inadequate to combat global warming, necessitating approximately 3.4 TW of PV installations annually. This would require about 89 million tonnes (Mt) of glass yearly, yet the actual production output of solar glass is only 24 Mt, highlighting a significant supply shortfall (3.7 times). Moreover, there is scarce information about the iron content of many sand deposits worldwide. Low-iron sand is required for PV glass production, to make the glass highly transparent and reduce the absorption of solar energy. Additionally, glass manufacturing leads to significant emissions, with fossil fuels being the primary energy source. Recycling offers a promising partial solution, with some available techniques enabling the clean recovery and reuse of end-of-life PV glass (cullet) for new panels. Similarly, methods such as the Hot Knife and Delam processes could recover entire glass cover sheets for potential reuse in new PV modules. Furthermore, there is an opportunity to establish new glass factories with lower emissions through strategies such as hydrogen fuel adoption, electrification, and waste heat recovery.
1. Introduction
Global energy demand has surged in recent decades due to population growth and technological advancements. However, this demand has primarily been met by fossil fuels, intensifying climate change through greenhouse gas emissions.1 Additionally, fossil fuel resources are unevenly distributed globally, leading to disparities in reliance among nations.2 In response to these challenges, extensive research has focused on identifying cleaner energy alternatives. Solar photovoltaics (PV)s have emerged as a promising solution, attracting significant attention, and witnessing rapid growth in demand.3–6 Global PV installed capacity reached 446 GW worldwide in 2023, with China leading with 235.5 GW, followed by the European Union (55.8 GW), US (33.2 GW), India (16.6 GW), etc.7
Studies suggest that achieving climate change mitigation goals, such as limiting global temperature rise to 1.5 °C, requires substantial PV deployment (Table 1). For instance, a 2016 prediction suggested a cumulative PV installation of 4.5 TW by 2050.16 In a recent study, it was suggested that to combat climate change, the annual deployment should ramp up from the current rate at 1 TW to reach 3.4 TW per year by 2037 and after reaching that, maintain the same pace at 3.4 TW per year. This would lead to a cumulative PV installation of 75 TW by 2050 (baseline scenario of our analysis).14 Such dramatic growth forecasts indicate a significant demand for photovoltaic modules in the foreseeable future.
Table 1 Different global PV growth scenarios considered by various studies
Reference |
Cumulative installed PV capacity (TW) in year |
Climate scenario and condition |
2030 |
2050 |
Haegel et al. (2017)8 |
5–10 |
— |
Decreasing module cost to $0.25 per W and increasing the efficiency of PV modules to 25% for cumulative deployment of 5–10 TW |
Bogdanov et al. (2019)9 |
7 |
22 |
100% electricity from renewable energy without fossil fuel and nuclear energy |
IRENA (2019)10 |
2.84 |
8.52 |
Achieving the Paris climate agreement through deep electrification and increased energy efficiency. Annual 270 GW and 372 GW of PV capacity additions by 2030 and 2050, compared to 94 GW added in 2018 |
Goldschmidt et al. (2021)11 |
— |
∼20–80 |
To prevent the world temperature from rising above 1.5 °C, the power conversion efficiency of the modules needs to increase (24.1–25.9% by 2030 and 27.8–30.7% by 2050) while capital cost needs to be decreased (40–10 cents per watt-peak by 2050 compared to the purchasing power of the currency in 2020) |
IEA (2021)12 |
0.63 |
1.26 |
134 GW additions per year in 2020 needs to ramp up to 630 GW additions per year by 2030 and then stay at 630 GW additions per year through 2050 |
IRENA (2022)13 |
5.2 |
14.03 |
The cumulative solar panel installation capacity must reach 5.2 TW by 2030 and 14.03 TW by 2050 to limit the global temperature increase below 1.5 °C |
Haegel et al. (2023)14 |
8 |
75 |
To limit the world temperature increase below 1.5 °C, PV installations needs to reach 3.4 TW per year by 2037 and then maintain a steady pace |
IEA (2023)15 |
0.82 |
1.64 |
134 GW additions per year in 2020 needs to ramp up to 820 GW additions per year by 2030 and then stay at 820 GW additions per year through 2050 |
Different technologies and materials have been used to manufacture these modules, but crystalline silicon (c-Si) PV technology dominates the market with over a 90% share.17 A c-Si PV module typically includes interconnected PV cells encased between weather-proof glass and a plastic laminated backsheet, connected electrically. Ethylene-vinyl acetate (EVA) or an alternative material (PET (polyethylene terephthalate) or PVF (polyvinyl fluoride)) encapsulates cells to withstand outdoor conditions.18 The front glass is tempered, while the backsheet may be made of Tedlar® or another glass sheet. Glass–glass (bifacial) PV modules are also increasing in market share. Glass, comprising 67% of a glass–backsheet module's weight (Table 2),19–21 is predominantly soda–lime–silicate (in about 90% modules), due to its low cost.11 This glass is typically 3.2 mm thick.22 Most modules have an aluminium frame, but frameless modules are also in production, for use with special mounting.23
Table 2 A “standard” c-Si monofacial PV module's weight and value composition. Adapted from ref. 18, which used ref. 19–21 to calculate these values. Unit price and recycled revenue assume recycling market prices (where available) or raw material prices
Material |
|
Unit price (USD per kg) |
Proportion of module by weight |
Recycled revenue (USD per m2) |
Glass |
Solar glass |
0.091 |
67% |
0.67 |
Frame |
Aluminum |
1.5 |
16% |
2.7 |
Ribbon |
Total |
|
0.9% |
0.56 |
|
Lead |
2 |
0.01% |
0.00 |
|
Copper |
4.4 |
0.8% |
0.38 |
|
Tin |
16 |
0.1% |
0.18 |
Solar cells |
Total |
|
4.7% |
3.1 |
|
Aluminum |
1.5 |
0.3% |
0.05 |
|
Silicon |
2.7 |
4.4% |
1.30 |
|
Silver |
647 |
0.03% |
1.79 |
Plastics |
Total |
|
11% |
|
|
PET |
N/A |
2.6% |
N/A |
|
PVF |
N/A |
0.8% |
N/A |
|
EVA |
N/A |
6.7% |
N/A |
|
Silicone |
N/A |
0.9% |
N/A |
The rapid expansion of PV manufacturing necessitates a substantial amount of glass, with forecasts suggesting consumption ranging from 64–259 million tonnes (Mt) and 122–215 Mt by 2100.11,24 This demand places significant pressure on raw materials for glass production. While recent research has addressed material demand and recycling strategies for PV production,25,26 challenges specific to PV glass production and recovery processes remain almost unexplored. Producing highly transparent PV glass requires low-iron silica sand and various other materials such as limestone, soda ash, dolomite, and alumina. According to two standards for PV glass manufacturing in China, national (GB/T 30984.1-2015)27 and industrial (T/CPIA 0028.1-2021),28 the Fe2O3 content of ultra-white patterned and float glasses should not be higher than 150 ppm. The PV glass industry uses antimony and its compounds to regulate the Fe2O3 content in the patterned glass to increase the glass clarity by oxidizing ferrous oxide (FeO) into Fe2O3.22 However, its presence poses challenges for float glass manufacturers due to potential reactions in the manufacturing process.29
The PV glass industry emits significant emissions. For instance, European glass factories emit around 0.74 tonnes (t) of CO2 per t of flat glass produced.30 However, regional differences in fuel and, to a much lesser extent, electricity sources, will affect this emission and the value can range between 0.65 and 0.76 t of CO2 per t of flat glass produced.30 Due to high melting temperatures, producing 1 t of glass requires 2–3 MWh of energy.31 Consequently, glass factories consume a significant amount of energy annually, with, for example, the UK glass sector consuming 0.5% of total UK energy in 2019.32 These factories heavily rely on conventional fuels like natural gas and coal, with European Union (EU) glass manufacturing factories consuming less than 1% of the natural gas consumed yearly across the EU.33
This study aims to address the challenges, such as supply risk of raw materials, high energy, and carbon emission, faced by the PV glass industry in detail. It reviews projected glass and raw material requirements for 3.4 TW annual production, examines issues concerning raw material scarcity, energy/environmental impacts, and waste management, and explores the role of recycling in addressing these challenges.
2. PV glass production process
Two main types of PV glass are ultra-white rolled and ultra-white float glass (both are types of flat glass but are formed differently and serve different purposes). The c-Si PV mainly uses ultra-white rolled glass, while ultra-white float glass is preferred for thin-film PVs for its smoother surface.34 Rolled glass, which is predominantly produced in China, dominates as PV front glass (95%) for c-Si PV modules.22 Low-iron rolled glass, with shallow front texturing and deeper rear texturing, minimizes specular reflection and glare, making it ideal for certain solar PV applications like those near airports.35
The production of ultra-white PV rolled glass involves two main stages: raw film production and deep processing (Fig. 1). In raw film production, five steps are typically followed: batching, melting, forming (calendaring), annealing, and edge breaking. The process starts with adding raw materials to the furnace to form molten glass at a temperature of around 1450 °C. The furnace used for PV glass has a deep pool depth and a stepped bottom design for precise heating and uniform composition. During forming, molten glass is compressed into a glass ribbon using rollers, with the bottom roller creating a deep texture and the upper roller applying a smoother pattern. After passing through the cooling lehr, cutting is done to remove the non-useable edges of the glass, and before packaging, the glass is cut into the preferred shape. Annealing is then conducted to remove thermal stress and ensure glass durability.22,34,36,37
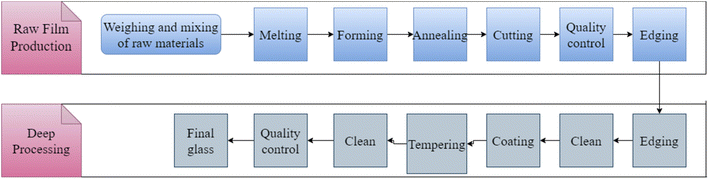 |
| Fig. 1 PV glass production process.36 | |
Deep processing (secondary processing after glass forming) includes tempering and coating.36 Tempering enhances glass strength and can be achieved through chemical ion exchange or physical methods. Physical tempering, commonly used in solar glass production, involves heating the glass above its softening point and rapidly cooling it to create compressive stress on the surface.34 This process (tempering) can increase glass strength to 4 to 6 times that of conventional flat glass. Following tempering, an anti-reflective (AR) film (coating) is applied to improve light transmittance, typically using the sol–gel method. Both tempering and coating processes require high temperatures (around 700 °C).34 Two primary processing pathways are followed: coating first and then tempering, or vice versa. Currently, the former route is favoured.36
The main difference between the production of rolled and float glass is the forming process. The forming process of float glass involves the continuous flow of molten glass from a pool kiln onto a relatively dense liquid tin surface. Through the combined results of gravity and surface tension, the glass liquid is spread and flattened on the surface of the liquid tin, after which the glass is annealed and cut.
The raw materials for PV glass must meet specific requirements, including low iron content and appropriate particle size. For instance, ultra-clear glass typically has an iron content 10–20 times lower than that for conventional glass (Fig. 2).36 Silica used in PV glass production must be low in iron, sourced from sand deposits or crushed quartzite rock. Materials with higher iron content can be used if they undergo purification processes such as acid leaching, flotation, and magnetic separation to reduce Fe2O3 levels.37,38
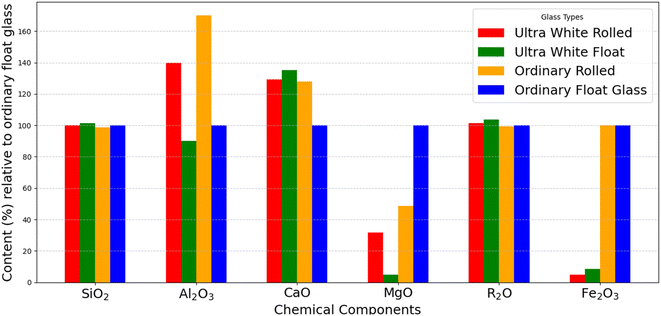 |
| Fig. 2 Chemical component of PV glass compared to ordinary float glass (“R2O” stands for alkali oxide).36 | |
Particle size is crucial in PV glass production. Large particles are hard to melt and can result in included grit, while small particles melt too quickly, leading to uneven heat conduction and agglomeration during melting. Additionally, heavy refractory minerals such as zircon and chromite, with stable chemical properties and high melting points, should be minimized in sand to prevent stone formation and ensure final glass quality. These minerals should be ≤5 ppm, with particle diameters ≤0.25 mm.39
Other essential raw materials for manufacturing ultra-white glass for PV include limestone, dolomite, soda ash, and feldspar. For instance, magnesium oxide from dolomite controls the crystallization and hardening speed of molten glass, while also acting as a flux to enhance melting performance. Limestone is crucial for ultra-white glass production as it reduces the viscosity of the molten glass.37
3. Present capacity and demand analysis for 3.4 TW growth
In this section, we first describe the glass requirements for the annual installation of 3.4 TW PVs, and then present the current solar glass capacity globally. After that, we determine the total material requirements for the annual installation of 3.4 TW PVs.
3.1. Projected glass requirements for PV use
The PV industry will need a significant amount of glass annually for 3.4 TW of PV production. According to the International Technology Roadmap for Photovoltaics (ITRPV),40 the efficiency of TOPCon and silicon heterojunction cells is expected to range from 22% to 24% over the next ten years. Therefore, this efficiency was incorporated into our model. For this calculation, we considered the average efficiency of modules using TOPCon (an n-type silicon solar cell with poly-Si/SiOx passivating contacts) and silicon heterojunction modules (featuring thin amorphous silicon layers deposited on crystalline silicon wafers) with a solar irradiance of 1000 W m−2 at air mass 1.5.40,41
Regarding glass thickness, the current standard is 3.2 mm, but there is a trend towards thinner glass (2 mm).40 In this study, our calculations are based on a thickness range from 2 mm to 5 mm, with 5 mm representing bifacial modules (total of front and rear glass).
Fig. 3 illustrates the projected annual global glass demand for PV, estimated at, for example, 89 Mt for 3.4 TW of PVs with 24% efficiency and 2.5 mm thickness. The figure highlights the significant influence of glass thickness and PV module efficiency on total glass requirements. For instance, at 22.25% efficiency, the demand ranges from around 95 Mt for a 2.5 mm thickness to about 121 Mt for a 3.2 mm thickness. Higher-efficiency panels require less panel area to generate the same amount of electricity, which means less glass is needed to cover the panels. Peters et al. also estimated glass demand, with their findings aligning closely with our estimates.41
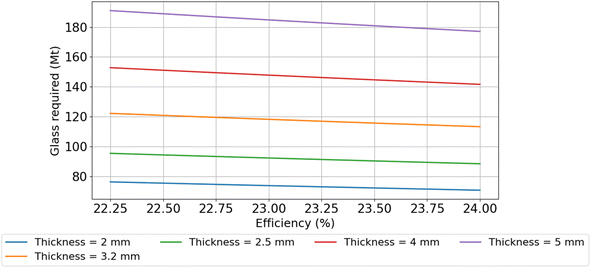 |
| Fig. 3 Projected PV glass demand for 3.4 TW per year of PV installation. | |
3.2. Present PV glass production capacity
The PV glass industry reported a significant surge (60%) in supply in 2022 due to the rapid growth of PV demand.42,43 This expansion has been fueled by two factors: the entry of new companies into the market, including float glass firms, and existing companies ramping up production, in response to expectations of growing demand. However, there appears to be a notable gap between production capacity and actual production. According to one unverified source,43 in 2022, the average global PV glass melting capacity was 84
000 tonne per day (t per day) (translating to an annual glass production capacity of around 30 million tonnes (Mt)), with China alone contributing around 94% of this capacity. By the end of May 2023, the average global PV glass melting capacity had increased to around 91
000 t per day (annual production capacity of 33 Mt), with China's market share rising to 99%. However, another unverified source found that,44 despite China's significant PV glass production capacity, the country's PV glass production was only 16 Mt in 2023 (by the end of August). If we extrapolate this number (16 Mt) over an entire year, the actual production is estimated to be around 24 Mt. So, annual production needs to increase by 3.8 times to meet the global annual demand of 89 Mt of glass for 3.4 TW per year per PV installation. Also, the production capacity needs to be increased by 2.7 times to meet up the demand for 3.4 TW per year of PV. It should be noted that the daily melting capacity of PV glass is derived from a non-peer-reviewed source as there is no publicly available literature on it.
One unverified source reported that, compared to China, other countries have much smaller scale PV glass manufacturing operations.45 According to another unverified source, in Asia, United Arab Emirates and India produce ultra clear glass (patterned and AR coated).46 In Europe, it has been reported that solar glass production is “practically no longer available,” with most of the glass imported from China.45 This assertion is supported by a report published in 2023.47 However, a non-peer reviewed source indicates that Europe does produce some ultra-clear glass, with manufacturers in Belgium (patterned), Germany (patterned and AR coated), Italy (AR coated), Liechtenstein (patterned and AR coated), Poland (ultra-clear and AR coated), and Turkey (patterned) contributing to this market.46 Two media news reported that, in South America, Brazil plans to manufacture solar glass,48 while in North America, two companies in USA produce ultra-clear glass.46 USA and Canada are also planning to ramp up their PV glass production plans.49
3.3. Material requirement
According to one source, producing 1 t of PV glass requires 130 kg of soda ash, 800 kg of quartz sand, and 800 kg of other raw materials.50 Another estimate suggests that 120 kg of dolomite, 14 kg of Glauber's salt (mirabilite), 254 kg of soda ash, 745 kg of low-iron quartz sand, and 117 kg of limestone are required.51 Using the values from the latter source, since it had a more comprehensive list, we calculate that 10.7 Mt of dolomite, 1.25 Mt of Glauber's salt (mirabilite), 22.6 Mt of soda ash, 66.3 Mt of sand, and 10.4 Mt of limestone are required to produce 89 Mt of glass.
Moving back in the value chain, we also projected the sand demand for 3.4 TW per year solar PV production (Fig. 4). We found that the world will need around 66 Mt per year of low-iron sand to produce enough glass for 3.4 TW per year solar PV installation (considering glass thickness of 2.5 mm, and PV panel efficiency of 24%). If bifacial modules (5 mm) are considered for the same efficiency, the sand demand will rise to 133 Mt per year.
 |
| Fig. 4 Sand required for annual 3.4 TW solar PV installation (5 mm refers to bifacial modules). | |
4. Issues in PV glass production
The PV glass industry faces several obstacles, such as material supply, high energy demand and carbon intensity of the production process and increasing waste volume. Furthermore, as mentioned above, the necessary future PV production will require a significant expansion of global PV glass manufacturing capacity. This section explores the details of these three obstacles.
4.1. Materials abundance and access
PV glass requires several raw materials, as mentioned above, but only sand is considered in this study since it constitutes the most significant material (75%) of the glass.52
Seven countries, including the United States, Norway, Australia, Russia, Mauritania, China, and Canada, possess substantial natural reserves of the low-iron, high-purity quartz sand crucial for PV glass production. Wang53 identified fourteen high-purity quartz deposits (both sand and rock) outside China, seven of which are actively mined and seven under investigation. Notably, the Spruce Pine Mine in the United States stands out as the largest reserve of high-purity quartz rock, with over 10 Mt of high-purity quartz raw material. In contrast, Australia holds significant sand reserves, exemplified by Mitsubishi's export of low-iron sand (100 ppm) from Cape Flattery in Queensland, with mineral resource estimated at 500 Mt.54 Additionally, two other silica sand mining projects are planned for the same region, by Metallica Minerals Ltd and Diatreme Resources Ltd.55 Furthermore, VRX Silica Ltd plans to exploit 208 Mt of low-iron sand resources at Muchea in Western Australia (Fig. 5), with potential markets including solar glass production.57 Dasajema Pty Ltd in Western Australia is also reported to have low-iron (65 ppm) sand (52 Mt) for solar glass production.58 A recent report states that a corporate presentation published by the Canadian Premium Sand company in 2023 indicates an iron content as low as 92 ppm in their Wanipigow, Manitoba sand. However, the report also notes that earlier drilling samples exhibited a higher iron content of 1300 ppm.54 High-purity quartz resources exist in regions like Anhui, Hunan, Hainan, Guangxi, and Guangdong in China59 but the iron content of the sand in these areas is not publicly specified. Vietnam, Malaysia, Cambodia, and Thailand also have high-quality quartz sand reserves. For instance, a detailed technological survey of Vietnam's Phong Dién district shows that the district holds over 50 Mt of high-quality quartz sand with iron content ranging from 100–680 ppm.60 A master's thesis reported that geochemical and granulometric analyses performed on sand samples from the east side of Kompong Som Bay, Cambodia, showed Fe2O3 levels lower than 200 ppm.61 Tested samples from Thailand's Tak province contain high-purity quartz sand with less than 100 ppm iron.62 Malaysia reportedly holds 149 Mt of sand with varying iron content ranges (the lowest reported as 10 ppm).63 Indonesia reportedly holds 2.1 billion tonnes of silica sand reserves, with 332 million tonnes ready for processing, although iron concentration is undeclared.64 The Xinyi Group plans to build a (not stated if ultra-white) glass factory in Indonesia, likely utilizing this sand.65,66 Brazil has a very significant sand resource, estimated at 96.7 Mt with an iron content as low as 48 ppm, with 2.4 ppm claimed to be accessible at one site after washing/scrubbing.54 In Cameroon's Supe area, quartz vein samples were analysed, revealing low-iron content sand measuring 100 ppm.67
 |
| Fig. 5 Some well documented low-iron sand resources (QLD-Queensland and WA-Western Australia).55,56 | |
Access to significant low-iron sand reserves is restricted by various factors such as natural hazards, transportation challenges, shipping permit and mining approval challenges, and environmental regulations. For instance, shipping from Cape Flattery, Australia, which lacks rail or road connectivity, must be through the Great Barrier Reef, a World Heritage Site, while national parks enclose the sand resource on land.68 Also, tropical cyclones pose a threat to the sand supply for a significant part of each year.69 Mitsubishi may only ship up to 3 Mt of sand annually, while Metallica has applied to construct a new jetty nearby to export up to 4 Mt per year.70 Also, according to media and government reports,71 Metallica,72 Galalar73 (both nearby the Mitsubishi site, and for which similar barriers apply), and Muchea projects all are awaiting mining permits.74
Community concerns also need to be considered for sand-mining activities. While limited peer-reviewed publications are available on this topic, various media reports have highlighted this concern. Opposition to silica sand processing plants for solar glass manufacturing has arisen in Riau Island, Indonesia,75 and Bangau Beach, Sabah, Malaysia, due to concerns over relocation, employment and health issues.76 Similar concerns have impacted silica sand mining projects in Missouri, US77 and Manitoba, Canada,78 where environmental issues prompted government intervention. In the case of Cape Flattery, compensation agreements have been established between Australian local indigenous landowners and the mining company.68
4.2. Energy and carbon intensity of glass production
It has been stated that every year glass factories worldwide consume around 500–700 million GJ of energy,79 although we note that production rates are highly variable, and significant expansion is expected due to growing PV demand. Fossil fuels have historically been used, significantly impacting the environment. Therefore, this section presents the energy and carbon intensity of the glass manufacturing process.
4.2.1. Energy intensity of glass production.
Sourcing and refining the raw materials needed to produce 1 t of molten glass require an estimated total energy of 3800–4800 MJ.80 Among these materials, soda ash production is the most energy-intensive, commonly manufactured using Solvay (synthetic), Trona (natural), or Hou (synthetic) processes. For instance, in the EU and UK, 99% of soda ash is produced via the Solvay process,32 which is estimated to use 6100–10
000 MJ of energy per tonne.32
The production of 1 t of glass requires around 12
000 MJ of specific energy, which varies according to the glass subsector and processing steps80 and, considering the energy needs of processing the glass, melting is the most energy-intensive.81 However, this number varies from study to study. Two studies reported that, melting accounts for around 60–70% of total energy consumption in the glass industry.81–83 The forming process is also energy-intensive, consuming up to 12% of primary energy,82 with the furnace being the primary energy consumer. The annealing process consumes 2–5% of total energy (gas is mostly used, but there is a growing trend towards using electricity to reduce CO2 emissions), while both electricity and gas are used in tempering (details of the energy use were not provided).82 European and US glass factories primarily rely on natural gas for 75–85% of their energy needs,84,85 contributing significantly to total gas consumption. For instance, in Italy, glass factories consume 1% of the national natural gas annually,79 while German factories consume 2% of theirs.33 China (the main producer of PV glass) has been reported to predominantly use coal (44.3%), followed by natural gas (15.5%), fuel oil (13.1%), electricity and other sources (27.15%).80 As a result, glass factories around the world would require a significant amount of natural gas. For example, producing 1 t of ultra-white float glass requires around 117 m3 of natural gas.86 Based on this number, the world requires 109 TW h of natural gas to produce 89 Mt of glass. Electricity (increasingly from renewable but still primarily from fossil sources) accounts for 10–15% of the total energy consumption in European and US glass factories, and the rest, 5–10%, comes directly from other fossil fuels.84
4.2.2. Carbon intensity of glass production.
The sourcing of raw materials also contributes significantly to gas emissions with global warming potential. For example, the Solvay process of soda ash production emits 0.7–1.0 t of carbon dioxide equivalent gases (CO2-eq.) to produce 1 t of soda ash.32 Overall, sourcing input materials contributes 330–350 kg of CO2-eq. to make 1 t of molten glass.32 Based on this number, 29.47–31.15 Mt of CO2-eq. will be emitted to source input materials to make molten glass for 89 Mt of glass.
Glass (including for PV applications) production, with its energy-intensive processes, contributes significantly to CO2 emissions, with global factories (container and flat) collectively emitting over 60 Mt annually.87 This amount (60 Mt) exceeds the yearly total CO2-eq. emissions of Portugal.84 In the EU, the glass sector emits over 20 Mt of CO2 annually.88 The UK's glass industry emits 1.7 Mt of CO2, while German glass factories emitted approximately 4 Mt in 2019.89,90
Glass production involves two types of emissions: direct (process) and indirect. Process emissions result from fossil fuel combustion and raw material reactions in the furnace. For example, approximately 600 kg of CO2-eq. is generated from the production of 1 t of glass in a gas-fired furnace. Of this, 450 kg comes from fossil fuel combustion, with the remainder from dissociation of carbonate raw materials.84 Based on this number (600 kg per t), the production of 89 MT of glass will emit 53.4 Mt of CO2-eq.
Indirect emissions occur mainly during electricity generation. For example, producing 1 tonne of ultra-white float glass requires around 111 kW h of electricity.86 To produce the 89 Mt of glass needed annually for a 3.4 TW PV installation, approximately 9.8 TW h of electricity are required annually. In China, the dominant producer of solar glass, generating 9.8 TW h of electricity emits around 9.58 Mt of CO2-eq., based on an emission factor of 0.97 kg CO2-eq. per kW per h.91 However, due to variation in electricity generation mixes, this number would be different in different countries. For instance, assuming the average electricity mix in each country,90 producing 89 Mt of PV glass in the US will result in emissions of approximately 5.4 Mt of CO2-eq. while the emissions would be around 6.6 Mt in Germany, 4.3 Mt in Japan and 0.89 Mt in Brazil. These significant CO2 emissions are very important, but there are other environmental impacts as well, discussed in the next section.
4.3. Other environmental impacts
Glass production also emits other gases and pollutants, such as NOx due to high-temperature combustion in air and SOx, which arises from sulfur content in the fossil fuels. Limited amounts of pollutants such as NaOH and KOH are also released during manufacturing.84 Glass production also generates fine dust due to waste gas scrubbing and cullet reclamation, leading to high dust pollution92 and particulate matter is emitted from molten glass and raw material evaporation, posing health risks like silicosis and cancer for glass workers.93,94 Water pollution is also a concern, with cooling processes and cullet cleaning consuming significant water. Discharged water may contain glass particles, soluble ingredients, organic compounds from lubricating oil, and treatment chemicals (dissolved salts and water treatment chemicals such as coagulants, biocides, flocculants, etc.) from the cooling-water system.95
Furthermore, sourcing of sand, the major raw material for glass production, is responsible for environmental degradation. Sand mining has severe consequences for biodiversity and ecosystems. Continuous extraction in places like Sri Lanka has endangered coral reefs96 while mining in water bodies worldwide has led to reductions in plankton and invertebrates.97,98 Land-based mining requires vegetation clearance, risking soil erosion and landform collapse.99 Increased traffic, pollution, and road deterioration from truck movement disrupt nearby environments and communities.100,101 Moreover, sand mining in riverbeds, such as in the Mekong River Delta in Vietnam, has altered flood frequency and impacted local food production,102,103 and has similarly affected regions like Mozambique and Kerala (India), according to some media reports.103,104
4.4. Waste volume
Increasing PV installations will inevitably lead to significant waste generation due to their finite lifetime. The IRENA report estimates cumulative PV waste of 60–78 Mt globally by 2050, using regular and early loss scenarios.16 Under the regular loss scenario, waste volume is projected to reach 1.7 Mt in 2030 and 60 Mt in 2050. Conversely, the early loss scenario forecasts waste volumes of 8 Mt in 2030 and 78 Mt in 2050.16 China is expected to contribute the most to this waste, with 20 Mt by 2050, followed by the US, Japan, Germany, and India (Table 3).16
Table 3 Projected PV waste from the most commonly cited waste report from IRENA.16
Countries |
Projected waste by 2030 in million metric tonnes (early loss scenario) |
Projected waste by 2030 in million metric tonnes (regular loss scenario) |
Projected waste by 2050 in million metric tonnes (early loss scenario) |
Projected waste by 2050 in million metric tonnes (regular loss scenario) |
China |
1.5 |
0.2 |
20 |
13.5 |
US |
1 |
0.4 |
10 |
7.5 |
Japan |
1 |
0.2 |
7.5 |
6.5 |
Germany |
1 |
0.4 |
7.5 |
4.5 |
India |
0.325 |
0.05 |
4.3 |
4.4 |
There are also other estimates of PV waste reported in the literature. A study by Hieslmair105 challenges the assumptions of the IRENA report, noting that by 2023, global PV deployment is already nearing the levels projected by IRENA for 2030 (1630 GW). Using PV deployment scenarios of 24 or 75 TW by 2050 and considering improved module efficiency and durability, Hieslmair estimated end-of-life (EOL) PV waste in 2050. Under the assumptions of steady improvement (the module reliability improves at a steady pace) and of 24 TW deployment by 2050, Hieslmair's study projected that cumulative PV waste could reach approximately 33 Mt by 2050.105 The study reported that PV waste would be around 38 Mt by 2050 under the assumption of 75 TW deployment and the nominal reliability scenario. Because glass constitutes a significant portion of a PV panel, this amount of PV waste will result in substantial glass waste. Hieslmair assumed that glass weighs 82% of the total weight of a PV panel.105 Based on that number, the expected glass waste will be around 27–31 Mt.
Note that, while PV waste appears substantial, it pales in comparison to waste generated by fossil fuels and traditional sources, at least up to 2050. For instance, oily sludge and coal waste from fossil fuels can be 2–5 times and 300–800 times greater than PV waste, respectively.106 By 2050, global municipal solid waste (MSW) is projected to exceed PV waste by 440–1300 times.106 Hieslmair also assessed the time it takes for various industries to accumulate 200 Mt of waste, revealing that coal mining is the worst (9 days), followed by oil production (15 days), MSW (1.2 months), coal ash (2 months), while the PV industry would take 40 years to generate the same amount of waste. Also, some fossil fuel industry wastes (oil sludge and coal ash) are toxic. On the other hand, the primary metal of concern in c-Si panels is lead (approximately, 0.01% by weight, used in solder for cell interconnection). According to Hieslmair,105 52 kt of lead will be introduced by coal ash annually in the waste stream compared to around 2 kt by PV. Furthermore, coal ash will also add 69.6 kt of arsenic and 2.4 kt of cadmium to the waste stream per year.105 While PV waste is less problematic than fossil fuel waste, reducing its impact remains essential.
5. Solutions (to issues of PV glass supply at TW scale)
This section deals with potential solutions to issues in PV glass supply. Recycling can address material, energy, and emission-related problems, while decarbonization is essential to tackle emission-related issues.
5.1. Recycling (as a solution to glass supply)
Currently, the landfilling of decommissioned PV modules is not sustainable due to environmental harm and loss of valuable materials.107 Toxic substances like lead (in solder of c-Si modules), cadmium, and tellurium (in CdTe modules) pose risks if they leach into groundwater and soil.108 Recycling presents an alternative, with two approaches: downcycling and high-quality recycling. Downcycling involves crushing, sieving, and material separation to obtain low-quality products suitable for applications like fiberglass production or construction materials.107,109,110 While downcycling addresses waste volume, it doesn't solve the material supply issue.
High-quality PV glass recycling, where recovered glass from EOL modules can potentially be used in new glass manufacturing has two forms: recovering high-quality cullet or whole glass sheets. Utilizing cullet offers benefits such as replacing primary raw materials, energy savings, and improving energy efficiency. For example, glass production requires 2671 MJ per tonne without cullet usage, which decreases to 1886 MJ per tonne with 100% cullet usage.111 CO2 emission is, consequently, reduced due to the energy savings from increased cullet use.80 For raw material saving, 118–122 kg of primary raw materials can be replaced by 100 kg of cullet.80 We are unaware of significant recycling of recovered PV glass into PV glass to date but a promising real-world example is Solarcycle, which will use cullet from PV glass in its new solar glass factory in Georgia.112 Similarly, AGC Europe will use recycling technology of Return of Silicon (ROSI) to extract cullet from EOL cover glass for use in flat glass manufacturing.113
But the use of external cullet in PV glass manufacturing faces some problems. Using recycled glass cullet as input for new cover glass production in PV has been hindered by quality concerns, particularly its iron contamination during the shredding process.114 Additionally, transportation challenges arise due to the cullet's low value and high weight, making high transportation costs hard to justify.115 Another issue is the presence of antimony, which is added to enhance light transmission in rolled glass but raises health and sustainability concerns due to its carcinogenic nature and potential for poisonous emissions during melting.29 Moreover, float glass manufacturers hesitate to accept cullet from external sources due to antimony's adverse effects on glass surface coloration and usability,29 although one Japanese industry report suggests that the problem might be manageable (details of the proposed process were not provided).116
Using collected glass sheets (without breaking them during the collection and separation processes) for new module manufacture would improve circularity compared to breaking into cullet and re-melting. Methods like the hot knife and Delaminating Resources Pty Ltd (“Delam”) process facilitate the recovery of whole glass sheets.117,118 This approach (reuse of whole glass) offers additional advantages such as energy and cost savings and emission reduction compared to using glass cullet. For example, materials are responsible for 48% of the total cost of PV glass production, followed by power (39%), other costs (9%), and labor (4%).119 When recycling cullet, the amount of input materials needed is reduced, but nearly the same energy and other costs are needed. But when recycling whole glass, all of the costs can be avoided. However, due to inconsistency in the PV industry and frequent changes in module dimensions, it has been infeasible in the past to reuse entire old glass sheets in new modules.
Now, there is a proposed plan to standardize PV modules.120 Trina Solar, one of the leading solar manufacturers, proposed three standardized module sizes: 450 W for residential, 550 W for commercial & industry, and 700 W for utility, and nine major manufacturers agreed to standard dimensions.121
5.1.1. Methods to recover glass cullet or whole glass from PV modules.
Researchers globally have explored various methods to recycle glass cullet or whole glass from end-of-life (EOL) PV waste, focusing on mechanical, chemical, and thermal approaches. Typically, the first step involves the removal of the aluminum frame, cables, and junction boxes.122 Subsequently, thermal or chemical delamination is conducted to remove the encapsulant (usually EVA) from the panels to recover glass.123 Thermal methods, such as combustion or pyrolysis, decompose EVA at around 500 °C, facilitating the separation of glass and solar cells.124 Alternatively, chemical solvents can achieve the same separation.125 These methods can be employed individually or in combination to enhance efficiency.124
Several mechanical and thermal treatments are available and utilized to recover glass. For example, mechanical delamination involves techniques including hot-knife,126–131 waterjet,132 shredding/milling,133,134 crushing,135–137 and high-pressure pulse.138–140 For example, in the hot-knife process, the module is positioned between two rollers, which move it along and hold it steady until it reaches a 1-meter-long steel blade heated to 180–200 °C, slicing the glass apart from the other layers of the laminate.122 Thermal treatment usually involves softening the EVA using heat and pyrolysis.122,124,141–147 For instance, Delam applied suction to separate the glass sheets after heating, manually removing the EVA to achieve whole sheet glass recovery.117 Belançon et al. also used a heat-assisted mechanical process to recover the whole sheet of glass. They softened the EVA by heating the panel on a preheated stove at 85 °C for half an hour, and then manually removed the laminated layers.31 However, the recovered glass resulting from these processes (except hot-knife) is not suitable for PV glass manufacturing. Glass recovered after shredding often gets contaminated with iron and, therefore, cannot be considered for the manufacture of new PV glass.114 Similarly, recovered glass after thermal treatment commonly contains metal impurities that make it unsuitable for new PV glass production.137 One potential solution is the use of chemical solvents to extract clean glass.129
Various chemical treatments utilize solvents to degrade EVA in PV waste.148 Successful separation of layers of PV laminates has been achieved with toluene,6,149 room temperature isopropanol,150 trichloroethylene,151,152 KOH–ethanol solution,153N,N′-dimethylpropyleneurea (DMPU),154 dibasic ester (DBE),155 hexane,156D-limonene,157 and supercritical CO2.158 Pagnanelli et al. compared solvent and thermal treatment methods and found that solvent treatment, using cyclohexane for the first time, resulted in superior quality glass suitable for new glass production.137 Toro et al. developed the “Photolife” process, involving mechanical shredding of the laminate and sieving to separate materials into coarse, intermediate, and fine fractions.159 Cyclohexane treatment then separates different layers, yielding glass powder, high-grade glass, aluminium frames, metallic filaments, PV cells, and a polymeric residue while also reducing the iron contamination from the shredding. Both methods were effective in recovering high-grade glass from end-of-life (EOL) PV waste.
5.2. Decarbonization
The following discusses different decarbonization options, such as fuel switching, waste heat recovery, batch preheating, batch pelletization, carbon capture, utilization and storage, and advances in heating and preheating, along with their carbon reduction potential (Table 4).
Table 4 Carbon reduction potential of different measures and technologies.84 We have added a new category of re-using the whole sheet of glass
Measures |
Technology |
Possible carbon reduction |
Challenges |
Carbon capture utilization and storage |
Carbon capture |
90% max |
High cost |
Lower carbon alternative |
Fuel switch |
75–85% |
Biofuel-limited resource |
Hydrogen-lower volumetric energy content |
|
Electric melting |
75–85% |
Requires reliable power grid |
Process |
Waste heat recovery |
15% max |
Fouled heat exchangers and high operational costs |
|
Preheating of raw materials |
15% max |
Dust carryover and clogging |
Circular economy |
Batch pelletisation |
5% max |
Possible contamination of batch materials |
|
Use of recycled flat glass (cullet) |
5% max |
High-quality |
|
Use of recovered whole sheet of glass from PV |
≤100% |
Glass gets broken during operation or collection |
Biomethane, hydrogen, and biogas offer promising avenues for decarbonizing the glass industry. Research indicates that biomethane could replace natural gas for heating raw materials,160,161 with, for example, the UK having sufficient biofuel capacity for its entire glass sector.162 Initial trials demonstrate the feasibility of substituting biogas for a portion of natural gas in glass-melting furnaces, as shown by a German factory co-firing biogas (30%) without compromising product quality.163 Hydrogen also shows potential, with trials from projects like Kopernikus P2X,164 HyGlass,165 Pilkington,166 and NSG167 highlighting its viability. These alternative fuels can be blended with natural gas and injected into pipelines, offering a pathway for reducing carbon emissions in the industry. It is expected that around 75–85% carbon reduction can be achieved through switching to carbon neutral fuel.84 However, these fuels face some problems.
While biofuels offer a lower-carbon alternative to fossil fuels, they often come with higher costs. Additionally, their limited availability poses a significant barrier.80 For instance, even if the flat glass industry were to utilize all annually produced biomethane, it would not be sufficient to meet the demand of all the float lines in the European Union.168 Moreover, glass manufacturers are wary of fluctuating gas compositions from various sources, which can affect product quality.80 Hydrogen, another potential alternative, faces technical challenges in glass factories due to its lower volumetric energy content and reduced radiation heat transfer compared to natural gas.169
Electric melting offers a promising alternative for glass factories with potential energy efficiency gains of up to 68%.170 Using an all-electric system could reduce energy input by 35%.171 Transitioning to renewable sources of electricity could also significantly reduce emissions, given the relative ease of sourcing it renewably. However, electric melting has its limitations. A very reliable power grid is required for operating an all-electric furnace and the glass composition needs to be changed due to different melting and fining behaviours.171 Also, the small furnace size is currently, a limiting factor for this technology.80
Enhancing waste heat recovery (WHR) is a promising decarbonization method that utilizes heat from the furnace exhaust gas, representing a significant portion (25–30%) of the furnace's energy input.172 This recovered heat can be used for various purposes, including generating electricity and heating materials, resulting in improved energy efficiency and reduced carbon emissions (maximum 15%).84 For instance, WHR implementation on a glass line could reduce energy consumption by 840 MJ per tonne of glass (around 7% of total energy use).173 However, challenges, like fouled heat exchangers and high operational costs, exist.84 Despite these challenges, the savings from improved energy efficiency can help reduce operational costs. But the net cost impact will depend on the trade-off between reduced energy use and increased maintenance costs.174
Batch preheating, where raw materials are heated using exhaust gas heat before being introduced into the furnace, offers energy and emission reductions in the glass industry. Furszyfer Del Rio et al. review various reports of significant savings including that have been demonstrated from use of cullet and batch preheating: savings of 8–12% of fuel related to melting in one case,84 energy savings of 12 to 20% in another, and a 7% reduction in CO2 emissions in a third.84 However, batch preheating suffers from problems like dust carryover and clogging.84
Innovations in glass factory furnaces offer promising ways to reduce emissions. Several furnaces, such as regenerative, recuperative, and oxyfuel furnaces, are available in the market. Regenerative furnaces use firebrick structures to store and transfer heat from waste combustion gases, while recuperative furnaces preheat combustion gas inside steel recuperators. Oxyfuel furnaces, on the other hand, burn fuel with pure oxygen instead of air, reducing nitrogen combustion and fuel consumption. Studies suggest that oxyfuel combustion could reduce flue gases by 60–70% and mitigate energy losses by 25–35% compared to conventional furnaces.84 Compared to efficient regenerative furnaces, oxyfuel furnaces save fuel from 5% to 20%.84
Microwave and plasma heating techniques have also been explored for their potential to reduce process time and energy consumption. Microwave heating enables swift, uniform heating while removing volatile components, with reported reductions in process time (by 34%) and energy consumption (by 25%).175 Plasma processes offer quick melting of raw glass powders with reduced environmental impacts,85 although high installation costs remain a barrier.176
As noted above, glass production emits CO2 as a byproduct of natural gas combustion for high-temperature melting. Carbon capture, utilization, and storage (CCS and CCUS), which can capture CO2 for synthetic fuels or storage, are considered necessary for decarbonizing the glass sector. One study found that integrating CCS could reduce emissions to around 90%.84 A UK company, C-capture, is testing this technology in two glass factories, demonstrating its practicality.177 However, high costs remain a drawback.85
Batch pelletization offers energy and emission savings in glass factories. This process involves forming raw materials into small pellets or granules with an aqueous binder before melting them in a furnace. After aging for at least 10 minutes, the materials are compacted, dried using flue gas heat, and then melted. It is estimated to provide a 7% energy-saving benefit.80 However, there is a possibility of contamination of batch materials from pelletizing equipment.80
Exploring alternative raw materials like biomass ash could also contribute to energy and emission savings by replacing virgin raw materials for glass industries. Biomass ash contains non-crystalline content, requiring less energy to melt and drive reactions compared to materials with crystalline content.161
6. Conclusion
In this review, we addressed the challenges associated with massive expansion of PV glass production. Meeting the challenge of global warming will require a significant expansion in PV glass production, which raises concerns regarding emissions and materials supply. The world requires around 89 Mt per year of glass for 3.4 TW per year PV installation, requiring the annual worldwide PV glass production capacity and actual production to increase by 2.7 times and 3.8 times, respectively. This rapid expansion would lead to substantial greenhouse gas emissions (CO2-eq.), including 40 Mt per year from fossil fuel combustion, 13.4 Mt per year from the disassociation of carbonate raw materials, and 9.58 Mt per year from electricity usage, although the electricity could be derived from renewable sources. Decarbonization strategies for glass production, including waste heat recovery and electric melting, present additional mitigation possibilities but face barriers such as high costs. Also, this rapid expansion in PV glass production will place significant pressure on the supply of materials such as low-iron sand. The calculated annual demand of 66 Mt for low-iron sand highlights the potential concerns regarding its availability and supply risk. However, the significance of this risk in relation to other PV components remains unknown. Further studies are needed to understand how the sand supply risk may affect the overall supply chain of PV.
The material stress problem could be partially solved through recycling, as some available processes allow clean recovery and reuse of end-of-life PV glass (cullet) for new panels. Similarly, Hot Knife and Delam can recover entire sheets of glass for potential reuse in new PV modules, eliminating the need for new glass production for PV. Future research should focus on overcoming barriers to decarbonization, and improving recycling methods that preserve the purity of recovered glass.
Data availability
Data on emissions from glass production in various countries, and on glass demand calculations, can be accessed viahttps://doi.org/10.57760/sciencedb.19842.
Conflicts of interest
There are no conflicts to declare.
Acknowledgements
This Project, the Australian Centre for Advanced Photovoltaics (ACAP), received funding from the Australian Renewable Energy Agency (ARENA). The views expressed herein are not necessarily the views of the Australian Government, and the Australian Government does not accept responsibility for any information or advice contained herein. ChatGPT was used to improve the clarity of the text and shorten it and translate non-English documents. The authors would like to thank Dr Pietro Peter Altermatt for help with Chinese patents.
References
-
IPCC, Summary for Policymakers, in Climate Change 2023: Synthesis Report. Contribution of Working Groups I, II and III to the Sixth Assessment Report of the Intergovernmental Panel on Climate Change, ed. H. Lee and J. Romero, IPCC, Geneva, Switzerland, 2023, pp. 1–34, DOI:10.59327/IPCC/AR6-9789291691647.001.
- F. Martins, C. Felgueiras and M. Smitková, Fossil fuel energy consumption in European countries, Energy Procedia, 2018, 153, 107–111, DOI:10.1016/j.egypro.2018.10.050.
- J. Pastuszak and P. Węgierek, Photovoltaic Cell Generations and Current Research Directions for Their Development, Materials, 2022, 15, 5542, DOI:10.3390/ma15165542.
- Y. Yue, Y. Zhuo, Q. Li and Y. Shen, Experimental and numerical study of extracting silver from end-of-life c-Si photovoltaic solar cells in rotating systems, Resour., Conserv. Recycl., 2022, 186, 106548, DOI:10.1016/j.resconrec.2022.106548.
- S. Song, C. He, Y. Zhuo, Y. Yue and Y. Shen, How particle sizes affect silver leaching from c-Si photovoltaic solar cells: Insights from integrated experimental and numerical investigations, Sol. Energy Mater. Sol. Cells, 2023, 261, 112520, DOI:10.1016/J.solmat.2023.112520.
- P. Dias, L. Schmidt, M. Monteiro Lunardi, N. L. Chang, G. Spier and R. Corkish,
et al., Comprehensive recycling of silicon photovoltaic modules incorporating organic solvent delamination – technical, environmental and economic analyses, Resour., Conserv. Recycl., 2021, 165, 105241, DOI:10.1016/j.resconrec.2020.105241.
-
G. Masson, E. Bosch, A. Van Rechem and M. de l'Epine, Snapshot of Global PV Markets 2024, 2024, DOI:10.69766/vhrf4040.
- N. M. Haegel, R. Margolis, T. Buonassisi, D. Feldman, A. Froitzheim and R. Garabedian,
et al., Terawatt-scale photovoltaics: Trajectories and challenges, Science, 2017, 356, 141–143, DOI:10.1126/science.aal1288.
- D. Bogdanov, J. Farfan, K. Sadovskaia, A. Aghahosseini, M. Child and A. Gulagi,
et al., Radical transformation pathway towards sustainable electricity via evolutionary steps, Nat. Commun., 2019, 10(1), 1–16, DOI:10.1038/s41467-019-08855-1.
-
IRENA, Future of Solar Photovoltaic: Deployment, Investment, Technology, Grid Integration and Socio-Economic Aspects (A Global Energy Transformation: Paper), International Renewable Energy Agency, Abu Dhabi, 2019, accessed: January 29, 2024 Search PubMed.
- J. C. Goldschmidt, L. Wagner, R. Pietzcker and L. Friedrich, Technological learning for resource efficient terawatt scale photovoltaics, Energy Environ. Sci., 2021, 14, 5147–5160, 10.1039/D1EE02497C.
-
IEA, Net Zero by 2050 – Analysis, 2021, https://www.iea.org/reports/net-zero-by-2050, accessed: January 29, 2024.
-
IRENA, World Energy Transitions Outlook 2022: 1.5°C Pathway, 2022, https://www.irena.org/Digital-Report/World-Energy-Transitions-Outlook-2022. accessed: January 29, 2024.
- N. M. Haegel, P. Verlinden, M. Victoria, P. Altermatt, H. Atwater and T. Barnes,
et al., Photovoltaics at multi-terawatt scale: Waiting is not an option, Science, 2023, 380, 39–42, DOI:10.1126/science.adf6957.
-
IEA, Net Zero Roadmap: A Global Pathway to Keep the 1.5 °C Goal in Reach – Analysis, 2023, https://www.iea.org/reports/net-zero-roadmap-a-global-pathway-to-keep-the-15-0c-goal-in-reach, accessed: January 29, 2024.
-
IRENA and IEA-PVPS, End-of-life management Solar Photovoltaic Panels, 2016, https://www.irena.org/publications/2016/Jun/End-of-life-management-Solar-Photovoltaic-Panels.
-
S. Philipps, Photovoltaics Report, Fraunhofer Institute for Solar Energy Systems, ISE with the Support of PSE Projects GmbH, 2024, https://www.ise.fraunhofer.de/en/publications/studies/photovoltaics-report.html, accessed: December 5, 2024.
- R. Deng, Y. Zhuo and Y. Shen, Recent progress in silicon photovoltaic module recycling processes, Resour., Conserv. Recycl., 2022, 187, 106612, DOI:10.1016/j.resconrec.2022.106612.
- R. Deng, N. L. Chang, Z. Ouyang and C. M. Chong, A techno-economic review of silicon photovoltaic module recycling, Renewable Sustainable Energy Rev., 2019, 109, 532–550, DOI:10.1016/j.rser.2019.04.020.
- A. Domínguez and R. Geyer, Photovoltaic waste assessment of major photovoltaic installations in the United States of America, Renew. Energy, 2019, 133, 1188–1200, DOI:10.1016/j.renene.2018.08.063.
-
R. Frischknecht, P. Stolz, L. Krebs, M. de Wild-Scholten, P. Sinha, V. Fthenakis, H. C. Kim, M. Raugei, M. Stucki, Life Cycle Inventories and Life Cycle Assessment of Photovoltaic Systems, International Energy Agency (IEA) PVPS Task 12, Report T12-19, 2020 Search PubMed.
- U. Blieske and G. Stollwerck, Glass and Other Encapsulation Materials, Semiconduct. Semimet., 2013, 89, 199–258, DOI:10.1016/B978-0-12-381343-5.00004-5.
-
A. Falk, C. Durschner and K.-H. Remmers, Photovoltaics for Professionals: Solar Electric Systems Marketing, Design and Installation, Routledge, 1st edn, 2007, DOI:10.4324/9781315065939.
- S. A. Khalifa, B. V. Mastrorocco, D. D. Au, S. Ovaitt, T. M. Barnes and A. C. Carpenter,
et al., Dynamic material flow analysis of silicon photovoltaic modules to support a circular economy transition, Prog. Photovoltaics Res. Appl., 2022, 30, 784–805, DOI:10.1002/pip.3554.
- R. Underwood, M. Kim, S. Drury, Y. Zhang, L. Wang and C. Chan,
et al., Abundant Material Consumption Based on a Learning Curve for Photovoltaic toward Net-Zero Emissions by 2050, Sol. RRL, 2023, 7, 2200705, DOI:10.1002/SOLR.202200705.
- L. Wang, Y. Zhang, M. Kim, M. Wright, R. Underwood and R. S. Bonilla,
et al., Sustainability evaluations on material consumption for terawatt-scale manufacturing of silicon-based tandem solar cells, Prog. Photovoltaics Res. Appl., 2023, 31, 1442–1454, DOI:10.1002/PIP.3687.
-
Standardization Administration of China, Solar glass - Part 1: Ultra-clear patterned glass. GB/T 30984.1-2015, 2015, https://www.chinesestandard.net/PDF/English.aspx/GBT30984.1-2015.
-
China Photovoltaic Industry Association, Glass for photovoltaic modules Part 1: Anti-reflection coating glass for front panel: T/CPIA 0028.1-2021[S], 2021, https://www.antpedia.com/standard/1114637153.html.
-
European Solar PV Industry Alliance, Addressing uncertain antimony content in solar glass for recycling, 2023, https://solaralliance.eu/wp-content/uploads/2023/10/Recommendation-on-Addressing-uncertain-antimony-content-in-solar-glass-for-recycling.pdf. accessed: October 29, 2023.
- A. Schmitz, J. Kamiński, B. Maria Scalet and A. Soria, Energy consumption and CO2 emissions of the European glass industry, Energy Policy, 2011, 39, 142–155, DOI:10.1016/j.enpol.2010.09.022.
- M. P. Belançon, M. Sandrini, F. Tonholi, L. S. Herculano and G. S. Dias, Towards long term sustainability of c-Si solar panels: The environmental benefits of glass sheet recovery, Renew. Energy Focus, 2022, 42, 206–210, DOI:10.1016/j.ref.2022.06.009.
- R. Hartwell, G. Coult and M. Overend, Mapping the flat glass value-chain: a material flow analysis and energy balance of UK production, Glass Struct. Eng., 2022, 1–26, DOI:10.1007/s40940-023-00218-z.
-
Glass Alliance Europe, Priority gas supply to the glass industry, 2022, https://glassallianceeurope.eu/wp-content/uploads/2022/06/2022-06-24-gae-gas-supply-to-the-glass-industry-input-on-prioritisation-criteria-summary_file.pdf, accessed 21 December 2024.
-
China Powder Network, What is the difference between the calendering method and the float method of photovoltaic glass? Explain it clearly in one article, 2023, https://news.cnpowder.com.cn/71856.html, accessed: October 29, 2023.
-
SunPower Corporation, Photovoltaic Systems: Lower Levels of Glare and Reflectance vs. Surrounding Environment. Technical sales summary, 2019, https://majorprojects.planningportal.nsw.gov.au/prweb/PRRestService/mp/01/getContent?AttachRef=SSD-10353-MOD-3%2120220309T001447.185GMT.
-
Sohu, Photovoltaic glass production process_original film, 2020, https://www.sohu.com/a/433776607_749304, accessed 29 October 2023.
-
Selection and market prospect analysis of quartz sand for ultra-white
glass-News-Information-China Powder Network, https://news.cnpowder.com.cn/43644.html, accessed 29 October 2023.
- C. Liu, W. Wang, H. Wang, C. Zhu and B. Ren, A Review on Removal of Iron Impurities from Quartz Mineral, Minerals, 2023, 13, 1128, DOI:10.3390/min13091128/S1.
-
Xinhai Mining. Low-iron quartz sand beneficiation process, chemicals and requirements for photovoltaic glass, 2023, https://www.ytxinhai.com/shiyingsha/3014.html, accessed 29 October 2023.
-
VDMA, International Technology Roadmap for Photovoltaic (ITRPV) 2022 Results, 14th edn, 2023, accessed: October 29, 2023 Search PubMed.
- I. M. Peters, J. Hauch and C. Brabec, Cradle-to-cradle recycling in terawatt photovoltaics: A vision of perpetual utility, Joule, 2024, 8, 899–912, DOI:10.1016/J.joule.2024.01.025.
-
L. Li, Current status of photovoltaic glass development, 2022, https://www.takomabattery.com/current-status-of-photovoltaic-glass-development/.
-
Sohu, 2024-2028 China Photovoltaic Glass Industry Development Forecast and Investment Analysis Report, 2024, https://www.sohu.com/a/759847247_121659750.
-
MIR Databank, News-September 22 – MIR Industry News Update, https://www.mirdatabank.ca/News/NewsDetail?id=150027, accessed 8 June 2024.
-
PV Manufacturing Europe, Scaling up is key, 2022, https://www.pveurope.eu/solar-modules/pv-manufacturing-europe-scaling-key, accessed 8 October 2024.
-
ENF Company Directory, Glass Manufacturers - Crystalline Panel Process, https://www.enfsolar.com/directory/material/glass, accessed 14 October 2024.
-
A. Chatzipanagi, A. Jaeger-Waldau, C. Cleret De Langavant, J. Gea Bermudez, S. Letout, A. Mountraki, A. Schmitz, A. Georgakaki, E. Ince, A. Kuokkanen and D. Shtjefni, Clean Energy Technology Observatory: Photovoltaics in the European Union – 2023, Status Report on Technology Development, Trends, Value Chains and Markets, Publications Office of the European Union, Luxembourg, 2023, DOI:10.2760/732675, JRC135034.
-
F. Couto, Brazil to have first 100% local solar panel factory, 2022, https://valorinternational.globo.com/business/news/2022/10/20/brazil-to-have-first-100percent-local-solar-panel-factory.ghtml, accessed 8 October 2024.
-
V. U. S. Thompson, Canada ramp up solar glass plans – PV Magazine International, 2024, https://www.pv-magazine.com/2024/05/18/how-north-america-could-become-the-crucible-for-solar-glass/, accessed 8 October 2024.
-
Overview analysis of China's photovoltaic glass industry, https://mp.weixin.qq.com/s/IuDnKms6hoEmhg5QZMQIFg, accessed: October 29, 2023.
-
D. Shitao, Photovoltaic glass industry research: the wind should be long-term, 2023, https://baijiahao.baidu.com/s?id=1758492184080607907%26wfr=spider%26for=pc, accessed: February 11, 2024.
- C. D. Westbroek, J. Bitting, M. Craglia, J. M. C. Azevedo and J. M. Cullen, Global material flow analysis of glass: From raw materials to end of life, Int. J. Ecol., 2021, 25, 333–343, DOI:10.1111/jiec.13112.
- J.-Y. Wang, Global high purity quartz deposits: Resources distribution and exploitation status, Acta Petrol. Mineral., 2021, 40, 131–141 CAS.
-
Rockstone Research, Homerun in Bahia: At the forefront of one of the world's highest quality silica sand districts, 2023, https://www.rockstone-research.com/index.php/en/research-reports/6140-Homerun-in-Bahia-At-the-forefront-of-one-of-the-worlds-highest-quality-silica-sand-districts, accessed 13 February 2024.
-
J.-F. Bertincourt, Australian silica sand sector, 2022, https://www.eveq.com/wp-content/uploads/2022/11/Australian-Silica-Sand-Sector.pdfandvariousothersources, accessed: February 11, 2024.
-
A. Golev, Silica sand in focus: abundant yet critical?, 2024, https://geoscience.data.qld.gov.au/blog/silica-sand-focus-abundant-yet-critical, accessed 17 December 2023.
-
VRX Silica Limited, Annual Report, 30 June 2023, https://announcements.asx.com.au/asxpdf/20230928/pdf/05vdwvwzvxxn2y.pdf.
-
D. Howell, New low iron (65 ppm) high purity (>99.95% SiO2) silica sand supply opportunity, https://wainvestments.com.au/wp-content/uploads/2023/03/HiTech-Silica-WA-Briefing-Note-24.01.15.pdf.
-
21 Finance, 2024, China Photovoltaic Glass Industry Research Report, 2023, https://m.21jingji.com/article/20231228/herald/9f903fa32627033b69153df9ac91129f.html, accessed 14 April 2024.
- M. Mikoláš, J. Drenda, T. Pechar, J. Tvrdý, M. Mikoláš, J. Mikušinec, J. Abrahámovský and B. Néč, The development of the glass industry in central Vietnam, Gospod. Surowcami Miner./Miner. Resour. Manag., 2017, 33, 143–162, DOI:10.1515/GOSPO-2017-0032.
-
S. Ros, Pre-feasibility Study of Silica Sand Processing Plant in Sihanoukville Province, Cambodia, Chulalongkorn University Theses and Dissertations (Chula ETD), 2018, DOI:10.58837/CHULA.THE.2018.265.
- P. Dararutana, P. Chetanachan, P. Wathanakul and N. Sirikulrat, Investigations on Local Quartz Sand for Application in Glass Industry, Acta Obstet. Gynecol. Scand., 2009, 13, 23–29, DOI:10.1142/9789812836182_0003.
- A. Ali, The silica-based industry in Malaysia, Bull. Geol. Soc. Malays., 2023, 46, 223–230, DOI:10.7186/bgsm46200337.
-
H. A. Y. Syafrizal, W. M. Hadiana, M. D. Rifaldi and P. Rasma. Characterization of Quartz Sand in Bangka and Central Kalimantan Region as Raw Material for Solar Panels, in International Symposium on Earth Science and Technology 2022, Japan, 2022 Search PubMed.
-
D. Karyza, Indonesia's quartz sand export ban seen to push domestic solar panel manufacturing, 2023, https://asianews.network/indonesias-quartz-sand-export-ban-seen-to-push-domestic-solar-panel-manufacturing/, accessed 16 December 2023.
-
M. Wright, Indonesia climbs the solar value chain, 2023, https://www.fdiintelligence.com/content/news/indonesia-climbs-the-solar-value-chain-82865, accessed 17 December 2023.
- N. A. Afahnwie, A. C. Kedia, C. E. Suh, C. Sigue and E. M. Shemang, Potential of QuartziticVeins in SW Cameroon for High-Purity Quartz, Int. J. Geosci., 2022, 13, 281–302, DOI:10.4236/ijg.2022.134015.
-
Flattery Silica Pty Ltd, Cape Flattery Silica Initial Advice Statement Report Final, 2023, accessed: February 11, 2024 Search PubMed.
-
M. Vujkovic, Tropical Cyclone Jasper crosses the coast near Wujal Wujal, north of Cairns, 2023, https://www.abc.net.au/news/2023-12-13/qld-tropical-cyclone-jasper-weather-pattern-warning-bom/103220130, accessed 20 December 2023.
-
Mirage, Queensland's silica sand meeting world-wide demand, 2021, https://www.miragenews.com/queenslands-silica-sand-meeting-world-wide-543199/, accessed 2 September 2023.
-
Queensland Government, Cape Flattery Silica Sand project, 2024, https://www.statedevelopment.qld.gov.au/coordinator-general/assessments-and-approvals/coordinated-projects/current-projects/cape-flattery-silica-sand-project, accessed 8 June 2024.
-
N. Dyson, Metallica bids for coordinated project consideration, 2023, https://www.miningmonthly.com/surface/news/1459785/metallica-bids-coordinated-project-consideration, accessed 8 June 2024.
-
S. Martin, Diatreme looking to fast-track silica mine approvals, 2023, https://capeyorkweekly.com.au/diatreme-looking-to-fast-track-silica-mine-approvals/6170/, accessed 8 June 2024.
-
WA investments, Muchea Silica Sand Project, 2024, https://wainvestments.com.au/projects/muchea-silica-sand-project/, accessed 8 June 2024.
-
H. Chen, Indonesian indigenous islanders are rallying against plans to build a Chinese funded factory on their homes, 2023, https://edition.cnn.com/2023/09/19/asia/indonesia-rempang-island-protests-chinese-factory-intl-hnk/index.html, accessed 29 October 2023.
-
J. Chan, Sabah CM says he will scrutinise proposed Kudat silica sand mining project, 2023, https://malaysia.news.yahoo.com/sabah-cm-says-scrutinise-proposed-072206813.html, accessed 29 October 2023.
-
A. Kite, Proposed Missouri silica sand mine loses appeal of its denied permit, 2023, https://missouriindependent.com/2023/10/17/proposed-missouri-silica-sand-mine-loses-appeal-of-its-denied-permit/, accessed 9 June 2024.
-
D. Bernhardt, and B. Kives, Manitoba rejects Sio Silica sand mining project, saying risk ‘simply too great’, 2024, https://www.cbc.ca/news/canada/manitoba/sio-silica-sand-mining-project-southeastern-manitoba-1.7117246, accessed 15 April 2024.
- A. Cantini, L. Leoni, S. Ferraro, F. De Carlo, C. Martini, F. Martini and M. Salvio, Technological Energy Efficiency Improvements in Glass-Production Industries and Their Future Perspectives in Italy, Processes, 2022, 10, 2653, DOI:10.3390/PR10122653.
- M. Zier, P. Stenzel, L. Kotzur and D. Stolten, A review of decarbonization options for the glass industry, Energy Convers. Manag. X, 2021, 10, 100083, DOI:10.1016/j.ecmx.2021.100083.
-
J. L. Pellegrino, Energy and Environmental Profile of the U.S. Glass Industry, 2002, DOI:10.2172/1218643.
-
TERI, Widening the coverage of PAT Scheme Sectoral Manual-Glass industry Prepared for Shakti Sustainable Energy Foundation, 2012, https://shaktifoundation.in/wp-content/uploads/2014/02/widening-of-pat-sectors-glass.pdf.
-
M. Hubert, Industrial Glass Processing and Fabrication, Springer Handbooks, 2019, pp. 1195–1231, DOI:10.1007/978-3-319-93728-1_34.
- D. D. Furszyfer Del Rio, B. K. Sovacool, A. M. Foley, S. Griffiths, M. Bazilian, J. Kim and D. Rooney, Decarbonizing the glass industry: A critical and systematic review of developments, sociotechnical systems and policy options, Renewable Sustainable Energy Rev., 2022, 155, 111885, DOI:10.1016/j.rser.2021.111885.
- Y. Yao, T. Watanabe, T. Yano, T. Iseda, O. Sakamoto, M. Iwamoto and S. Inoue, An innovative energy-saving in-flight melting technology and its application to glass production, Sci. Technol. Adv. Mater., 2008, 9(2), 025013, DOI:10.1088/1468-6996/9/2/025013.
-
Database - ecoinvent, https://ecoinvent.org/database/, accessed 16 April 2024.
-
C. Springer, and A. Hasanbeigi, Emerging Energy Efficiency and Carbon Dioxide Emissions-Reduction Technologies for the Glass Industry. Report, 2017, https://eta-publications.lbl.gov/publications/emerging-energy-efficiency-and-2.
-
Statista, Emissions from glass production worldwide and in Europe in 2022, 2024, https://www.statista.com/statistics/1071205/carbon-dioxide-emissions-from-glass-production-worldwide/.
-
British Glass, A clear future: UK glass manufacturing sector decarbonisation roadmap to 2050, 2024, https://www.britglass.org.uk/knowledge-base/resources-and-publications/clear-future-uk-glass-manufacturing-sector.
- M. Zier, N. Pflugradt, P. Stenzel, L. Kotzur and D. Stolten, Industrial decarbonization pathways: The example of the German glass industry, Energy Convers. Manag. X, 2023, 17, 100336, DOI:10.1016/j.ecmx.2022.100336.
- G. Yıldız, B. Çalış, A. E. Gürel and İ. Ceylan, Investigation of life cycle CO2 emissions of the polycrystalline and cadmium telluride PV panels, Environ. Nanotechnol. Monit. Manag., 2020, 14, 100343, DOI:10.1016/j.enmm.2020.100343.
-
GlassonWeb, Glass Production and Sustainability, 2020, https://www.glassonweb.com/article/glass-production-and-sustainability.
-
AGC Glass Europe, Environmental impact of flat glass production, 2024, https://www.agc-glass.eu/en/sustainability/decarbonisation/environmental-impact.
-
International Agency for Research on Cancer, Exposures in the Glass Manufacturing Industry - Beryllium, Cadmium, Mercury, and Exposures in the Glass Manufacturing Industry, available online: https://www.ncbi.nlm.nih.gov/books/NBK499748/, accessed on 3 November 2023.
-
I. F. C. Environmental, Health, and Safety Guidelines for Glass Manufacturing, 2007, https://documents1.worldbank.org/curated/en/890101490072833164/pdf/113621-WP-ENGLISH-Glass-Manufacturing-PUBLIC.pdf, accessed on 3 November 2023.
-
H. Kumara, Together for Justice Sand Mining in Sri Lanka Endangers Coral Reefs and Livelihoods - Together for Justice, 2017, https://www.presbyterianmission.org/together-justice/2017/03/13/sand-mining-sri-lanka-endangers-coral-reefs-livelihoods/, accessed December 14, 2023.
- L. Koehnken, M. S. Rintoul, M. Goichot, D. Tickner, A. C. Loftus and M. C. Acreman, Impacts of riverine sand mining on freshwater ecosystems: A review of the scientific evidence and guidance for future research, River Res. Appl., 2020, 36, 362–370, DOI:10.1002/rra.3586.
- D. C. N. Doloksaribu, T. A. Barus and K. Sebayang, The impact of marine sand mining on sea water quality in Pantai Labu, Deli Serdang Regency, Indonesia, IOP Conf. Ser. Earth Environ. Sci., 2020, 454, 012086, DOI:10.1088/1755-1315/454/1/012086.
- T. Gondo, H. Mathada and F. Amponsah-Dacosta, Regulatory and policy implications of sand mining along shallow waters of Njelele River in South Africa. Jàmbá, J. Disaster Risk Stud., 2019, 11, 12, DOI:10.4102/jamba.v11i3.727.
- M. A. Miller, A Transboundary Political Ecology of Volcanic Sand Mining, Ann. Assoc. Am. Geogr., 2021, 112, 78–96, DOI:10.1080/24694452.2021.1914539.
- E. F. da Silva, D. F. Bento, A. C. Mendes, F. G. da Mota, L. C. S. Mota and A. I. T. Fonseca,
et al., Environmental impacts of sand mining in the city of Santarém, Amazon region, Northern Brazil, Environ. Dev. Sustain., 2020, 22, 47–60, DOI:10.1007/s10668-018-0183-2.
- E. Park, H. L. Ho, D. D. Tran, X. Yang, E. Alcantara and E. Merino,
et al., Dramatic decrease of flood frequency in the Mekong Delta due to river-bed mining and dyke construction, Sci. Total Environ., 2020, 723, 138066, DOI:10.1016/j.scitotenv.2020.138066.
-
D. Datta, Uncontrolled sand mining led to Kerala floods. This is only waiting to happen again, 2018, https://www.dailyo.in/variety/kerala-floods-sand-mining-sand-mafia-illegal-mining-soil-erosion-rivers-26297, accessed October 28, 2023.
-
S. Goswami, This coastal village in Mozambique now at the mercy of Chinese mining company, 2018, https://www.downtoearth.org.in/news/mining/mozambique-s-coastal-village-at-mercy-of-chinese-mining-company-60121, accessed October 28, 2023.
-
H. Hieslmair, Contextualizing PV end-of-life waste DNV, 2023, https://www.dnv.com/Publications/contextualizing-pv-end-of-life-waste-248306, accessed January 28, 2024.
- H. Mirletz, H. Hieslmair, S. Ovaitt, T. L. Curtis and T. M. Barnes, Unfounded concerns about photovoltaic module toxicity and waste are slowing decarbonization, Nat. Phys., 2023, 19(10), 1376–1378, DOI:10.1038/s41567-023-02230-0.
- K. Máčalová, V. Václavík, T. Dvorský, R. Figmig, J. Charvát and M. Lupták, The Use of Glass from Photovoltaic Panels at the End of Their Life Cycle in Cement Composites, Materials, 2021, 14, 6655, DOI:10.3390/ma14216655.
- A. M. Curtin, C. A. Vail and H. L. Buckley, CdTe in thin film photovoltaic cells: Interventions to protect drinking water in production and end-of-life, Water-Energy Nexus, 2020, 3, 15–28, DOI:10.1016/j.wen.2020.03.007.
- G. Ansanelli, G. Fiorentino, M. Tammaro and A. Zucaro, A Life Cycle Assessment of a recovery process from End-of-Life Photovoltaic Panels, Appl. Energy, 2021, 290, 116727, DOI:10.1016/j.apenergy.2021.116727.
- P. M. Tembo and V. Subramanian, Current trends in silicon-based photovoltaic recycling: A technology, assessment, and policy review, Sol. Energy, 2023, 259, 137–150, DOI:10.1016/j.solener.2023.05.009.
-
O. Kodak, F. Sadeghi-Khaneghah, A. E. Ş. Konukman, L. Kılıç, N. Arzan and G. Dural, Energy Usage in Glass Industry: Past, Today, and Tomorrow, Proceedings of the 2022 International Symposium on Energy Management and Sustainability, 2023, pp. 101–111, DOI:10.1007/978-3-031-30171-1_12.
-
J. Dlouhy, Solar Factory Plans Add to Georgia Clean Manufacturing Boom, 2024, https://finance.yahoo.com/news/solar-factory-plans-add-georgia-153551994.html, accessed 17 April 2024.
-
AGC, AGC Glass Europe and Photovoltaic Recycling Pioneer ROSI Announce Strategic Partnership to Advance Circularity in The Glass Industry, 2024, https://www.agc.com/en/news/detail/1207608_2814.html.
- J. A. Tsanakas, A. van der Heide, T. Radavičius, J. Denafas, E. Lemaire and K. Wang,
et al., Towards a circular supply chain for PV modules: Review of today's challenges in PV recycling, refurbishment and re-certification, Prog. Photovoltaics Res. Appl., 2020, 28, 454–464, DOI:10.1002/pip.3193.
-
R. Davio, This packet provides information about how and why to use recycled glass in roadway construction and maintenance projects, https://ftp.dot.state.tx.us/pub/txdot-info/gsd/pdf/yrr_feb.pdf, accessed February 15, 2024.
-
AGC, Achieves Success in Demonstration Test of Solar Panel Cover Glass Recycling, 2023, https://www.agc.com/en/news/detail/<?ccdc_no 1205454?>1205454<?ccdc END?>_2814.html.
-
Delaminating Resources Pty Ltd Delamination Process Video - YouTube, https://www.youtube.com/watch?v=Vj4l6sv8c5c, accessed 29 October 2023.
-
Shinryo Corporation, FY 2020 Demonstration Project for Early Social Implementation of a Decarbonized Metal Recycling System, 2021, https://www.env.go.jp/content/900532392.pdf, accessed February 5 2025 Search PubMed.
-
China Photovoltaic Glass Industry Research Report, 2024, https://solar.ofweek.com/2023-12/ART-260008-8420-30621471_2.html, accessed November 1, 2024.
-
A. Bhambhani, Standardized PV Panel Size Gets Unanimous Votes, 2023, https://taiyangnews.info/standardized-module-size-gets-unanimous-votes/./, accessed January 20, 2024.
-
S. Chunduri, TrinaSolar's Golden Size Modules for Different Applications, 2023, https://taiyangnews.info/trinasolars-golden-size-modules-for-different-applications/./, accessed January 20, 2024.
- M. M. Lunardi, J. P. Alvarez-Gaitan, J. I. Bilbao and R. Corkish, Comparative Life Cycle Assessment of End-of-Life Silicon Solar Photovoltaic Modules, Appl. Sci., 2018, 8, 1396, DOI:10.3390/APP8081396.
-
T. Y. Wang, J. C. Hsiao and C. H. Du, Recycling of materials from silicon base solar cell module, Conference Record of the IEEE Photovoltaic Specialists Conference, 2012, pp. , pp. 2355–2358, DOI:10.1109/PVSC.2012.6318071.
- P. S. S. Camargo, A. d. S. Domingues, J. P. G. Palomero, M. P. Cenci, A. C. Kasper and P. R. Dias,
et al., c-Si PV module recycling: Analysis of the use of a mechanical pre-treatment to reduce the environmental impact of thermal treatment and enhance materials recovery, Waste Manage. Res., 2023, 41(11), 1661–1673 CrossRef CAS PubMed.
- M. Vellini, M. Gambini and V. Prattella, Environmental impacts of PV technology throughout the life cycle: Importance of the end-of-life management for Si-panels and CdTe-panels, Energy, 2017, 138, 1099–1111, DOI:10.1016/J.energy.2017.07.031.
-
O. Tomioka, Japanese companies work on ways to recycle a mountain of solar panels, 2016, https://asia.nikkei.com/magazine/20161117-INCOMING/Tech-Science/Japanese-companies-work-on-ways-to-recycle-a-mountain-of-solar-panels, accessed October 20, 2023.
- A. Heiho, I. Suwa, Y. Dou, S. Lim, T. Namihira and T. Koita,
et al., Prospective life cycle assessment of recycling systems for spent photovoltaic panels by combined application of physical separation technologies, Resour., Conserv. Recycl., 2023, 192, 106922, DOI:10.1016/j.resconrec.2023.106922.
-
S. R. Yu and Q. Y. Yang, Improvement on recycling process and life cycle assessment of photovoltaic panel, in Proceedings of the EcoDesign 2013 International Symposium, 2013, pp. 4–6 Search PubMed.
- C. C. Farrell, A. I. Osman, R. Doherty, M. Saad, X. Zhang and A. Murphy,
et al., Technical challenges and opportunities in realising a circular economy for waste photovoltaic modules, Renewable Sustainable Energy Rev., 2020, 128, 109911, DOI:10.1016/j.rser.2020.109911.
- H. Trivedi, A. Meshram and R. Gupta, Recycling of photovoltaic modules for recovery and repurposing of materials, J. Environ. Chem. Eng., 2023, 11, 109501, DOI:10.1016/j.jece.2023.109501.
- P. Cerchier, M. Dabalà, L. Pezzato, M. Tammaro, A. Zucaro and G. Fiorentino,
et al., Silicon-PV panels recycling: technologies and perspectives, Metall. Ital., 2022, 114, 16–26 Search PubMed.
-
K. Wambach, C. Libby and S. Shaw, Advances in Photovoltaic Module Recycling: Literature Review and Update to Empirical Life Cycle Inventory Data and Patent Review, IEA PVPS Task 12, IEA PV Power Systems Programme. Report IEA-PVPS T12-28:2024, ISBN 978-3-907281-56-7 Search PubMed.
- M. F. Azeumo, G. Conte, N. M. Ippolito, F. Medici, L. Piga and S. Santilli, Photovoltaic module recycling, a physical and a chemical recovery process, Sol. Energy Mater. Sol. Cells, 2019, 193, 314–319, DOI:10.1016/J.solmat.2019.01.035.
- P. Dias, L. Schmidt, L. B. Gomes, A. Bettanin, H. Veit and A. M. Bernardes, Recycling Waste Crystalline Silicon Photovoltaic Modules by Electrostatic Separation, J. Sustain. Metallurgy Metall., 2018, 4, 176–186, DOI:10.1007/s40831-018-0173-5.
- J. Li, S. Yan, Y. Li, Z. Wang, Y. Tan and J. Li,
et al., Recycling Si in waste crystalline silicon photovoltaic panels after mechanical crushing by electrostatic separation, J. Clean. Prod., 2023, 415, 137908, DOI:10.1016/j.jclepro.2023.137908.
- G. Granata, F. Pagnanelli, E. Moscardini, T. Havlik and L. Toro, Recycling of photovoltaic panels by physical operations, Sol. Energy Mater. Sol. Cells, 2014, 123, 239–248, DOI:10.1016/j.solmat.2014.01.012.
- F. Pagnanelli, E. Moscardini, G. Granata, T. Abo Atia, P. Altimari and T. Havlik,
et al., Physical and chemical treatment of end of life panels: An integrated automatic approach viable for different photovoltaic technologies, Waste Manage., 2017, 59, 422–431, DOI:10.1016/j.wasman.2016.11.011.
- S. M. Nevala, J. Hamuyuni, T. Junnila, T. Sirviö, S. Eisert and B. P. Wilson,
et al., Electro-hydraulic fragmentation vs conventional crushing of photovoltaic panels – Impact on recycling, Waste Manage., 2019, 87, 43–50, DOI:10.1016/j.wasman.2019.01.039.
- Y. Akimoto, A. Iizuka and E. Shibata, High-voltage pulse crushing and physical separation of polycrystalline silicon photovoltaic panels, Miner. Eng., 2018, 125, 1–9, DOI:10.1016/j.mineng.2018.05.015.
- P. Zhao, J. Guo, G. Yan, G. Zhu, X. Zhu and Z. Zhang,
et al., A novel and efficient method for resources recycling in waste photovoltaic panels: High voltage pulse crushing, J. Clean. Prod., 2020, 257, 120442, DOI:10.1016/j.jclepro.2020.120442.
- S. Wang and Y. Shen, Particle-scale modelling of the pyrolysis of end-of-life solar panel particles in fluidized bed reactors, Resour., Conserv. Recycl., 2022, 183, 106378, DOI:10.1016/j.resconrec.2022.106378.
- L. Zhang and Z. Xu, Separating and recycling plastic, glass, and gallium from waste solar cell modules by nitrogen pyrolysis and vacuum decomposition, Environ. Sci. Technol., 2016, 50, 9242–9250, DOI:10.1021/acs.est.6b01253.
- P. Dias, S. Javimczik, M. Benevit and H. Veit, Recycling WEEE: Polymer characterization and pyrolysis study for waste of crystalline silicon photovoltaic modules, Waste Manage., 2017, 60, 716–722, DOI:10.1016/J.wasman.2016.08.036.
- R. Wang, E. Song, C. Zhang, X. Zhuang, E. Ma and J. Bai,
et al., Pyrolysis-based separation mechanism for waste crystalline silicon photovoltaic modules by a two-stage heating treatment, RSC Adv., 2019, 9, 18115–18123, 10.1039/C9RA03582F.
- V. Fiandra, L. Sannino, C. Andreozzi, F. Corcelli and G. Graditi, Silicon photovoltaic modules at end-of-life: Removal of polymeric layers and separation of materials, Waste Manage., 2019, 87, 97–107, DOI:10.1016/J.wasman.2019.02.004.
-
L. Frisson, K. Lieten, T. Bruton, K. Declercq, J. Szlufcik, H. de Moor, et al., Recent Improvements in Industrial PV Module Recycling, Sixteenth European Photovoltaic Solar Energy Conference, 2020, pp. 2160–2163, DOI:10.4324/9781315074405-25.
-
J. R. Bohland and I. I. Anisimov, Possibility of recycling silicon PV modules, Conference Record of the IEEE Photovoltaic Specialists Conference, 1997, pp. 1173–1175, DOI:10.1109/PVSC.1997.654298.
- X. Wang, X. Tian, X. Chen, L. Ren and C. Geng, A review of end-of-life crystalline silicon solar photovoltaic panel recycling technology, Sol. Energy Mater. Sol. Cells, 2022, 248, 111976, DOI:10.1016/J.solmat.2022.111976.
- Q. Liao, S. Li, F. Xi, Z. Tong, X. Chen and X. Wan,
et al., High-performance silicon carbon anodes based on value-added recycling strategy of end-of-life photovoltaic modules, Energy, 2023, 281, 128345, DOI:10.1016/J.energy.2023.128345.
- P. F. A. Prado, J. A. S. Tenório and D. C. R. Espinosa, Alternative method for materials separation from crystalline silicon photovoltaic modules, Miner., Met. Mater., 2017, 277–282, DOI:10.1007/978-3-319-52192-3_27.
- T. Doi, I. Tsuda, H. Unagida, A. Murata, K. Sakuta and K. Kurokawa, Experimental study on PV module recycling with organic solvent method, Sol. Energy Mater. Sol. Cells, 2001, 67, 397–403 CrossRef CAS.
- S. Pang, Y. Yan, Z. Wang, D. Wang, S. Li and W. Ma,
et al., Enhanced separation of different layers in photovoltaic panel by microwave field, Sol. Energy Mater. Sol. Cells, 2021, 230, 111213, DOI:10.1016/J.solmat.2021.111213.
- Y. Yan, Z. Wang, D. Wang, J. Cao, W. Ma and K. Wei,
et al., Recovery of Silicon via Using KOH-Ethanol Solution by Separating Different Layers of End-of-Life PV Modules, JOM, 2020, 72, 2624–2632, DOI:10.1007/s11837-020-04193-6.
- K. Li, Z. Wang, C. Liu, D. Wang, G. Li and X. Chen,
et al., A green method to separate different layers in photovoltaic modules by using DMPU as a separation agent, Sol. Energy Mater. Sol. Cells, 2022, 245, 111870, DOI:10.1016/j.solmat.2022.111870.
- K. Li, D. Wang, K. Hu, C. Liu, Z. Wang and G. Li,
et al., Recycling of solar cells from photovoltaic modules via an environmentally friendly and controllable swelling process by using dibasic ester, Clean Technol. Environ. Policy, 2023, 25, 2203–2212, DOI:10.1007/s10098-023-02496-1.
- P. M. Tembo, M. Heninger and V. Subramanian, An Investigation of the Recovery of Silicon Photovoltaic Cells by Application of an Organic Solvent Method, ECS J. Solid State Sci. Technol., 2021, 10, 025001, DOI:10.1149/2162-8777/abe093.
- D. M. Abdo, T. Mangialardi, F. Medici and L. Piga, D-Limonene as a Promising Green Solvent for the Detachment of End-of-Life Photovoltaic Solar Panels under Sonication, Processes, 2023, 11, 1848, DOI:10.3390/PR11061848.
- É. S. Lovato, L. M. Donato, P. P. Lopes, E. H. Tanabe and D. A. Bertuol, Application of supercritical CO2 for delaminating photovoltaic panels to recover valuable materials, J. CO2 Util., 2021, 46, 101477, DOI:10.1016/j.jcou.2021.101477.
-
L. Toro, F. Pagnanelli, G. Granata, and E. Moscardini, Process for treating spent photovoltaic panels, 2014, https://patents.google.com/patent/EP2997169A1/en.
-
Verallia testing biogas for glass melting process | GlassOnline.com - The World's Leading Glass Industry Website, https://www.glassonline.com/verallia-testing-biogas-for-glass-melting-process/, accessed October 29, 2023.
- W. Deng, D. J. Backhouse, F. Kabir, R. Janani, M. Bigharaz, A. Wardlo, M. Marshall, R. Ireson and P. Bingham, An ancient technology could help deliver decarbonisation, Glass Int., 2019, 42(7), 47–49 Search PubMed.
-
G. Futures, BEIS Industrial Fuel Switching Phase 2 Alternative Fuel Switching Technologies for the Glass Sector Final Report, 2019, accessed October 29, 2023 Search PubMed.
- M. Fiehl, J. Leicher, A. Giese, K. Görner, B. Fleischmann and S. Spielmann, Biogas as a co-firing fuel in thermal processing industries: implementation in a glass melting furnace, Energy Procedia, 2017, 120, 302–308, DOI:10.1016/J.EGYPRO.2017.07.221.
-
Kopernikus-Projekte: P2X: Power-to-X projects in Germany, 2023, https://www.kopernikus-projekte.de/en/projects/p2x/ptx_projects, accessed 5 September 2023.
-
NRW.Energy4Climate, HyGlass, https://www.energy4climate.nrw/themen/best-practice/hyglass, accessed 5 September 2023.
-
G. Morris, Pilkington UK to scale low carbon glass production under hydrogen plans, 2024, https://www.glass-international.com/news/pilkington-uk-to-scale-low-carbon-glass-production-under-hydrogenplans#:%7E:text=PilkingtonUKwillscaleits,zero%2Demissionhydrogeneachday, accessed 5 September 2023.
-
G. Morris, NSG to test hydrogen fuel for glassmaking at St Helens site, 2020, https://www.glass-international.com/news/nsg-to-use-hydrogen-fuel-for-glassmaking-at-st-helens-site, accessed 5 September 2023.
-
Glass for Europe, Flat-glass-climate-neutral-Europe, https://glassforeurope.com/2050-flat-glass-in-a-climate-neutral-europe/, accessed October 29, 2023.
-
F. Simon, Glass industry boss: Replacing old windows can bring huge energy savings, 2020, https://www.euractiv.com/section/energy/interview/glass-industry-boss-replacing-old-windows-can-bring-huge-energy-savings/, accessed: April 11, 2024.
- S. Lechtenböhmer, L. J. Nilsson, M. Åhman and C. Schneider, Decarbonising the energy intensive basic materials industry through electrification – Implications for future EU electricity demand, Energy, 2016, 115, 1623–1631, DOI:10.1016/J.ENERGY.2016.07.110.
-
Eurotherm Limited, The efficient future for the glass industry is “all-electric”, 2017, https://www.eurotherm.com/au/glass-manufacture-au/the-efficient-future-for-the-glass-industry-is-all-electric/, accessed: April 13, 2024.
- S. Karellas, D. Giannakopoulos, C. S. Hatzilau, I. Dolianitis, G. Skarpetis and T. Zitounis, The potential of WHR/batch and cullet preheating for energy efficiency in the EU ETS glass industry and the related energy incentives, Energy Effic., 2018, 11, 1161–1175, DOI:10.1007/s12053-017-9587-3.
- Z. Li, X. He, Y. Wang, B. Zhang and H. He, Design of a flat glass furnace waste heat power generation system, Appl. Therm. Eng., 2014, 63, 290–296, DOI:10.1016/J.APPLTHERMALENG.2013.10.038.
- M. Trafczynski, M. Markowski and K. Urbaniec, Energy saving and pollution reduction through optimal scheduling of cleaning actions in a heat exchanger network, Renewable Sustainable Energy Rev., 2023, 173, 113072, DOI:10.1016/J.RSER.2022.113072.
-
S. J. Friedmann, Z. Fan and K. E. Tang, Low-carbon heat solutions for heavy industry: sources, options, and costs today, 2019, https://www.energypolicy.columbia.edu/publications/low-carbon-heat-solutions-heavy-industry-sources-options-and-costs-today/.
- V. S. Sikarwar, M. Hrabovský, G. Van Oost, M. Pohořelý and M. Jeremiáš, Progress in waste utilization via thermal plasma, Prog. Energy Combust. Sci., 2020, 81, 100873, DOI:10.1016/J.PECS.2020.100873.
-
Carbon Herald, First Carbon Capture Projects at Glass Plants Launched By C-Capture, 2022, https://carbonherald.com/first-carbon-capture-projects-at-glass-plants-launched-by-c-capture/.
|
This journal is © The Royal Society of Chemistry 2025 |
Click here to see how this site uses Cookies. View our privacy policy here.