DOI:
10.1039/D3SD00130J
(Paper)
Sens. Diagn., 2024,
3, 269-273
Vertically-grown Ag nanoplates on SeZnO3 nanosheets for an enhanced pressure sensing performance†
Received
31st May 2023
, Accepted 20th November 2023
First published on 21st November 2023
Abstract
As a piezoelectric ceramic material, SeZnO3 has received increasing attention for pressure sensing. However, the poor conductivity and low dielectric constant of bare SeZnO3 severely limit its wide applications. Herein, to improve the pressure sensing properties of SeZnO3, SeZnO3 nanosheets composited with Ag nanoplates were synthesized via a dissolution coprecipitation method, which exhibited a higher sensitivity (54.8 kPa−1) to external pressure with an excellent repeatability than that of bare SeZnO3 nanosheets (12.3 kPa−1). The enhanced pressure sensing properties of Ag/SeZnO3 nanocomposites could be attributed to an increased dielectric constant and an enhanced charge output. Moreover, the nanocomposite-based pressure sensors showed an accelerated response/recovery rate (0.7 s/2.7 s) because of the effective charge transfer between SnZnO3 and Ag, which was confirmed by XPS results. This Ag/SeZnO3 composite nanosheet-based pressure sensor demonstrates a potential for practical monitoring of human movement.
1. Introduction
Pressure sensors have received significant attention, showing widespread potential applications in wearable sensing devices,1 electronic skins (e-skins),2 and healthcare detection.3 To date, several sensing mechanisms have been employed for the fabrication of pressure sensors, including piezoresistive,4 capacitance,5 and piezoelectric6 sensing. Among them, capacitance-type pressure sensors with the advantages of a simple device structure, long-term stability, low power consumption, high sensitivity, and fast response have received special attention.7,8 In such types of devices, a dielectric sensing layer is commonly sandwiched between two parallel plate electrodes. It is believed that a higher dielectric constant and material stability are the prerequisites for the achievement of higher pressure-sensing properties.9–12
As a type of perovskite-type ceramic oxide, SeZnO3 has attracted increasing attention for pressure sensing applications due to its special crystal structure,13 large surface area, and abundant oxygen vacancies.14 SeZnO3 is a rare perovskite oxide with a valence combination of Se4+Zn2+O3. The theoretical calculation results revealed that SeZnO3 showed a ductile nature with excellent mechanical properties, exhibiting potential applications in pressure sensing.15 However, because of its poor conductivity and low dielectric constant, the research on SeZnO3-based pressure sensors is still in its infancy. Therefore, it is expected that the modulation of conductivity and dielectric constant can be helpful for the improvement of its pressure sensing properties. It was reported that the surface modification of noble metal nanoparticles, such as Ag, Au, and Pd,16 on pressure sensing materials can improve their electrical conductivity17 and dielectric constant.18 Among them, Ag nanoparticles are widely adopted as surface modification materials because of their low cost, simple preparation, high dielectric constant,19 and good conductivity.20 However, the modification of Ag nanoparticles with a uniform distribution and controllable morphological structure is still challenging.
Herein, SeZnO3 nanosheets were firstly synthesized via a dissolution coprecipitation method. Next, SeZnO3 nanosheets decorated with Ag nanoparticles were successfully prepared using a facile photo-reduction method. Moreover, by tuning the concentration of AgNO3, the morphological structure of Ag could be adjusted. The pressure-sensing results revealed that the Ag/SeZnO3 composite showed a higher sensitivity and faster response/recovery rate compared to the bare SeZnO3 nanosheets, which is attributed to its increased dielectric constant and enhanced charge output.
2. Experiments
2.1 Materials
Sodium selenite (Na2SeO3, >98%) was purchased from Shanghai Adamas Reagent Co. Ltd., China. Sodium dodecyl sulfonate (SDS, >99.7%) was purchased from Shanghai Lingfeng Chemical Reagent Co. Ltd., China. Silver nitrate (AgNO3, >99.7%) was purchased from Shanghai Aladdin Technology Co., Ltd., China. Zinc chloride anhydrous (ZnCl2, >99.7%), ethanol (anhydrous, >99.7%), and ethanediol (anhydrous, >99.7%) were purchased from Sinopharm Chemical Reagent Co., Ltd., China. Deionized (DI) water was purified using a Milli-Q System (Millipore). All materials were used without further purification.
2.2 Synthesis of SeZnO3 nanoplates and Ag nanosheets/SeZnO3 nanoplates
SeZnO3·H2O was synthesized via the dissolution coprecipitation method. Briefly, 0.4 g Na2SeO3 was dissolved in 10 mL DI water, followed by the addition of 0.9 g SDS. The mixed solution was stirred at 1500 rpm for 30 min, and then sonicated at 25 °C for 30 min to remove bubbles. The as-obtained viscous solution was added dropwise to a 0.01 M ZnCl2 aqueous solution under constant stirring at 1500 rpm for 30 min, and then transferred to an oven at 90 °C for 1 h. The resulting precipitate was collected by centrifugation and washed several times with DI water and ethanol. Finally, the washed precipitate was dried overnight at 70 °C and SeZnO3·H2O nanosheets were obtained. To remove the crystal water of SeZnO3·H2O, it was transferred to a tubular furnace and heated for 3 h under an air atmosphere at 400 °C.
Ag/SeZnO3 was synthesized via the photo-reduction method. Briefly, 0.09 g AgNO3 was added to 3 mL ethanediol. The mixture was sonicated for 15 min, and then 0.046 mg SeZnO3 was added under constant stirring at 1000 rpm for 30 min. The mixed solution was irradiated by a 150 W Xenon lamp for 30 min. The products were collected by centrifugation and washed several times with ethanol.
2.3 Apparatus and measurements
The as-prepared samples were characterized via scanning electron microscopy (SEM JEOL JSM-7800F, Japan), transmission electron microscopy (TEM JEOL 2100 F, Japan), high-resolution transmission electron microscopy (HRTEM JEOL 2100 Plus, Japan), X-ray diffraction (XRD, Smart Lab Rigaku, Japan) with Cu Kα radiation at λ = 1.54 Å, X-ray photoelectron spectroscopy (XPS, Versaprobe PHI 5000, Japan) and LCR digital electric bridge (Honghui TH26011BS, China). The dielectric constant was tested using a precision digital electric bridge (Agilent 4980A, USA).
2.4 Fabrication and test of pressure sensors
Briefly, 200 μL of dispersed SeZnO3 or Ag/SeZnO3 ethanol solution was dropped on coper tape (1 × 1 cm2). After the evaporation of ethanol, another layer of copper tape was covered on it to obtain the pressure sensing devices.
The abovementioned sensing devices were connected to an LCR. During the pressure testing, the starting pressure was set as 0 Pa (without loading extra pressure), and a target pressure was applied to the sensor with a 15 s holding time. The testing pressure was in the range of 34.8 Pa to 1240 Pa.
3. Results and discussion
Fig. 1a shows a schematic diagram of the process for the preparation of the Ag–SeZnO3 nanocomposite. Firstly, bare SnZnO3 nanosheets were prepared via the dissolution coprecipitation method with Na2SeO3, SDS, and ZnCl2 as precursors. Subsequently, the Ag/SeZnO3 composite nanosheets were prepared by air annealing, followed by the photo-reduction method. As shown in Fig. 1b, well-defined XRD peaks assigned to the (111), (112), (004), (211), and (213) planes of SeZnO3 (JCPDS No. 78-0446) can be clearly observed, indicating that SeZnO3 was successfully prepared. It can be found from the transmission electron microscopy (TEM) images (Fig. 1c) that the as-prepared SeZnO3 nanosheets exhibited a two-dimensional (2D) structure (transverse size = 1–2 μm) with a uniformly distributed pore structure on their surface. The elemental distribution of the SeZnO3 nanosheets was analyzed by energy-dispersive X-ray spectroscopy (EDS) mapping (Fig. S1†), which showed the uniform distribution of Se and Zn in the SeZnO3 nanosheets, and the stoichiometric ratio of Se
:
Zn
:
O in the SeZnO3 nanosheets was around 1
:
1
:
3. The crystal structure of the SeZnO3 nanosheets was further investigated by high-resolution TEM (HRTEM) (Fig. 1d), which showed interplanar distances of 0.25 nm and 0.31 nm, corresponding to the (114) and (120) crystal planes of the SeZnO3 nanosheets, respectively. In the case of the Ag/SeZnO3 nanocomposite, not only the diffraction peak of SeZnO3 could be observed, but an extra peak assigned to the (111) plane of Ag (JCPDS No. 04-0783) clearly found, as shown in Fig. 1e, which suggests that Ag/SeZnO3 was successfully prepared. Similarly, the Ag/SeZnO3 nanosheets also exhibited a 2D structure with an undamaged profile structure compared to the bare SeZnO3 nanosheet structure (Fig. 1f). Interestingly, it was found that Ag nanoplates were grown vertically on the surface of the SeZnO3 nanosheets. The elemental distribution in the Ag/SeZnO3 nanosheets was also analysed by EDS mapping (Fig. S2†), which showed the uniform distribution of Ag on the SeZnO3 nanosheet with an Se
:
Zn
:
Ag ratio of 1
:
1
:
1, further indicating the successful preparation of Ag/SeZnO3. The crystal structure of the Ag/SeZnO3 nanosheets was also investigated by HRTEM (Fig. 1d), which showed interplanar distances of 0.21 nm and 0.24 nm, corresponding to the (020) and (![[1 with combining macron]](https://www.rsc.org/images/entities/char_0031_0304.gif)
1) crystal planes of Ag, respectively.
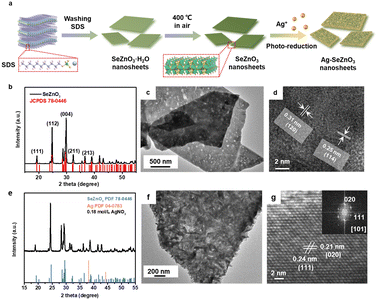 |
| Fig. 1 (a) A schematic diagram of the synthesis of SeZnO3 nanosheets. (b) The XRD patterns of SeZnO3 nanosheets. (c) The TEM image of SeZnO3 nanosheets. (d) The HRTEM image of SeZnO3 nanosheets. (e) The XRD patterns of Ag/SeZnO3 nanosheets. (f) The TEM image of Ag/SeZnO3 nanosheets. (g) The HRTEM image of Ag/SeZnO3 nanosheets (inset: the fast Fourier transform (FFT) pattern of the HRTEM image). | |
To further study the structure and phase evolution, the chemical composition and chemical bonding states of the as-prepared SeZnO3 and Ag/SeZnO3 nanocomposite were confirmed by XPS characterization. Fig. 2a shows the Se 3d XPS spectrum, which could be deconvoluted into two peaks (Se 3d5/2 and Se 3d3/2) at 58.7 and 59.2 eV, respectively, corresponding to the SeO32− state (Se–O binding structure of SeZnO3).21 It should be noted that the binding energy of Se 3d in the nanocomposite shifted towards a lower binging energy compared to the bare SeZnO3, owing to the weaker electronegativity of Ag compared to Se. The binding energy shift indicates the effective electron transfer between the SeZnO3 nanosheets and Ag nanoplates. In the Zn 2p spectra of SeZnO3 and Ag/SeZnO3 (Fig. 2b), the two peaks corresponding to Zn 2p1/2 and Zn 2p3/2 are located at 1044.8 eV and 1021.7 eV, respectively. The difference in the binding energy of these two peaks suggests that the Zn species was the Zn2+ state (Zn–O binding structure of SeZnO3).22 The O 1s XPS spectrum in Fig. 2c could be deconvoluted into two peaks, which are located at 530.6 and 531.3 eV, corresponding to lattice oxygen and oxygen vacancy, respectively. The peak assigned to lattice oxygen matched well with the above-mentioned Se 3d and Zn 2p spectra, further confirming the existence of Se–O (A site of SeZnO3) and Zn–O (B site of SeZnO3) in the SeZnO3 structure.23,24 In addition, the extra Ag 3d spectrum of the nanocomposite showed two peaks at 368.19 eV (Ag 3d5/2) and 374.19 (Ag 3d3/2), which can be assigned to the Ag0 state, further proving that Ag+ was successfully reduced to Ag0 by the photo-reduction method.25
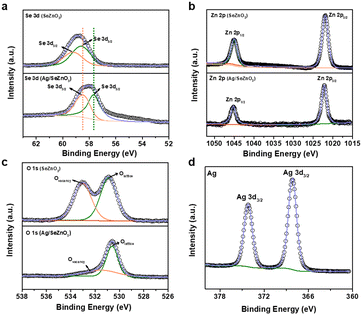 |
| Fig. 2 The XPS spectra of (a) Se 3d, (b) Zn 2p, and (c) O 1s of SeZnO3 nanosheets and Ag/SeZnO3 nanosheets and (d) Ag 3d of Ag/SeZnO3 nanosheets. The inserted dash lines can be used to determine the shift directions of the identified peaks. | |
Besides, to detail the effect of Ag on the morphological structure and the pressure sensing properties of the nanocomposite, the concentration of AgNO3 was also tuned, while keeping the other synthesis conditions unchanged. It was found that the morphological structure of Ag changed from nanoparticles to nanoplates (Fig. S3†) when increasing the AgNO3 concentration from 0.03 and 0.06 to 0.18 mol L−1. Moreover, the XRD patterns of the nanocomposites with different concentrations of AgNO3 are presented in Fig. S4,† all of which matched well with the (111), (112), (004), (211), and (213) planes of SeZnO3 (JCPDS No. 78-0446) and (111) plane of Ag (JCPDS No. 04-0783).
As a demonstration, the bare SeZnO3 and Ag/SeZnO3 nanocomposites with different contents of Ag were fabricated into pressure sensors to measure pressures in the range of 34.8 Pa to 1240 Pa (Fig. 3a). The sensor response was defined by (Cp − C0)/C0%, where C0 is the initial capacitance and Cp is the capacitance under external pressure. The response of the Ag/SeZnO3-based pressure sensor in the whole pressure range was higher than that of the SeZnO3-based pressure sensor. Moreover, with an increase in the AgNO3 concentration from 0.03 and 0.06 to 0.18 mol L−1, the responses of the nanocomposite also increased accordingly. The fitted pressure-response curves for the different pressure sensors are shown in Fig. 3b. The sensitivity of these pressure sensors was calculated as follows:
| Sensitivity = [(Ct − C0)/C0 × 100%]/ΔP | (1) |
where Δ
P is the variation in pressure. The sensitivity of Ag/SeZnO
3 with 0.06, 0.06 and 0.18 mol L
−1 AgNO
3 concentration was 23.2, 27.2 and 54.8 kPa
−1, respectively, while that of the bare SeZnO
3 is only 18.2 kPa
−1.
Fig. 3c shows the dynamic response-recovery curves of the Ag/SeZnO
3 (0.18 mol L
−1) and bare SeZnO
3-based sensors to 251.5 Pa. Interestingly, the Ag/SeZnO
3 (0.18 mol L
−1)-based pressure sensor showed a shorter response and recovery time (0.7 s/2.7 s) than that of the bare SeZnO
3-based pressure sensor (1.2 s/2.9 s). Besides, the durability of our sensor based on Ag/SeZnO
3 nanosheets was evaluated by sensing tests under repeated loading of 90.7 Pa and 160.7 Pa pressure. As shown in
Fig. 3d, the sensor exhibited stable sensing responses without obvious degradation after 40 cycles, suggesting its good stability.
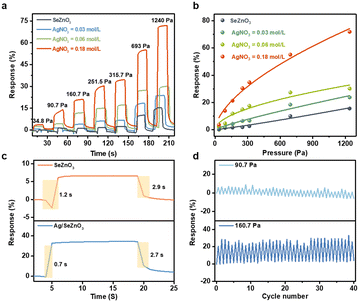 |
| Fig. 3 (a) The response and recovery curves of the pressure sensors based on SeZnO3 and Ag/SeZnO3 nanosheets. (b) The pressure-response curves of sensors based on SeZnO3 and Ag/SeZnO3 nanosheets. (c) The response and recovery time of pressure sensors based on SeZnO3 and Ag/SeZnO3 nanosheets under 251.5 Pa. (d) The long-term stability of sensor based on BiFeO3 nanoplates under 90.7 Pa and 160.7 Pa pressure. | |
To detail the enhanced pressure sensitivity of the nanocomposite, the equivalent circuit model based on the bare SnZnO3 and Ag/SnZnO3 nanocomposite were constructed. The whole capacitance of the as-fabricated sensors can be divided into many “mini capacitors”. As shown in Fig. 4a, it is believed that the number of electric connections between the bare SeZnO3 and electrodes is smaller than that of the Ag/SeZnO3 nanocomposites due to the decoration of Ag nanoplates with more contact sites. Therefore, the introduction of Ag nanoparticles can provide more electric connection between sensing materials and electrodes, leading to an increase in the series capacitance in nanocomposites-based pressure sensors. To further confirm the higher capacitance of the nanocomposite, the relative permittivity of the Ag/SeZnO3 nanosheets and bare SeZnO3 was also calculated, which was 119.29 and 33.63, respectively. According to the definition of capacitance, a higher permittivity implies a higher output capacitance, which is consistent with the experimental capacitance values. As shown in Fig. 4b, the initial capacitance of the nanocomposite increased with an increase in Ag concentration, which could increase the signal-to-noise ratio (SNR) of the pressure sensor and increase the measurement accuracy.26 Besides, according to the enhanced electrical conductivity of the nanocomposite, its electron density also increased with an increase in the Ag loading, which is beneficial for an enhancement in pressure sensitivity. The higher output capacitance of the nanocomposites can be helpful for the enhancement of pressure sensitivity.27 Besides, it was reported that the addition of Ag nanoparticles can enlarge the deformation of the sensing layer under external pressure, leading to the enhanced pressure sensitivity of the nanocomposite. Because of the effective electron transfer between Ag and SeZnO3 and the higher conductivity of Ag, the pressure-induced charge generation can be easily collected, leading to the fast response/recovery rate of the Ag/SeZnO3 nanocomposites.
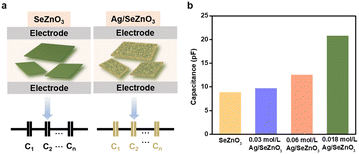 |
| Fig. 4 (a) A schematic illustration of SeZnO3- and Ag/SeZnO3-based pressure sensors. (b) The capacitance outputs of SeZnO3- and Ag/SeZnO3-based pressure sensors with different concentrations of Ag loading. | |
4. Conclusions
In summary, SeZnO3 nanosheets composited with Ag nanoparticles were successfully prepared via the dissolution coprecipitation method, followed by photoreduction, which exhibited enhanced pressure sensitivity with excellent repeatability compared to that of bare SeZnO3 nanosheets. With an increase in the concentration of AgNO3, the morphological structure of Ag could be tuned from nanoparticles to nanoplates. Moreover, the pressure sensitivity of the nanocomposite also increased with an increase in the amount of Ag. It is believed that the increased dielectric constant-induced higher output capacitance was beneficial for the higher sensitivity of the nanocomposite. Because of the effective charge transfer between Ag and the SeZnO3 nanosheets and the higher conductivity of Ag, the nanocomposite showed an accelerated response/recovery rate. The demonstration of Ag/SeZnO3-based pressure sensors can be helpful for the further improvement in the pressure sensing properties of materials.
Author contributions
The manuscript was written through the contributions of all authors. All authors have given approval for the final version of the manuscript.
Conflicts of interest
The authors declare no competing financial interest.
Acknowledgements
This work was supported by the National Key Basic Research Program of China (grant no.: 2021YFB3200302), the National Natural Science Foundation of China (grant no.: 51832001), the Fundamental Research Funds for the Central Universities of China, the Joint Research Funds of Department of Science & Technology of Shaanxi Province and Northwestern Polytechnical University (grant no.: 2020GXLH-Z-026 and 2020GXLH-Z-027).
Notes and references
- S. Gong, W. Schwalb, Y. Wang, Y. Chen, Y. Tang, J. Si, B. Shirinzadeh and W. Cheng, Nat. Commun., 2014, 5, 3132 CrossRef PubMed.
- J. Shi, Y. Dai, Y. Cheng, S. Xie, G. Li, Y. Liu, J. Wang, R. Zhang, N. Bai and M. Cai, Sci. Adv., 2023, 9, eadf8831 CrossRef CAS PubMed.
- S. Wang, W. Deng, T. Yang, G. Tian, D. Xiong, X. Xiao, H. Zhang, Y. Sun, Y. Ao and J. Huang, Nano Res., 2023, 16, 1330–1337 CrossRef.
- S. Wang, W. Deng, T. Yang, Y. Ao, H. Zhang, G. Tian, L. Deng, H. Huang, J. Huang and B. Lan, Adv. Funct. Mater., 2023, 2214503 CrossRef CAS.
- Z. Feng, Q. He, X. Wang, Y. Lin, J. Qiu, Y. Wu and J. Yang, ACS Appl. Mater. Interfaces, 2023, 15, 6217–6227 CrossRef CAS PubMed.
- Y. Zhang, F. Shi, C. Zhang, X. Sheng, Y. Zhong, H. Chong, Z. Yang and C. Wang, Chin. Chem. Lett., 2023, 34, 107700 CrossRef CAS.
- J. Qin, L. J. Yin, Y. N. Hao, S. L. Zhong, D. L. Zhang, K. Bi, Y. X. Zhang, Y. Zhao and Z. M. Dang, Adv. Mater., 2021, 33, 2008267 CrossRef CAS PubMed.
- Z. Shen, C. Yang, C. Yao, Z. Liu, X. Huang, Z. Liu, J. Mo, H. Xu, G. He and J. Tao, Mater. Horiz., 2023, 10, 499–511 RSC.
- R. Sheng, J. Mu, R. V. Chernozem, Y. R. Mukhortova, M. A. Surmeneva, I. O. Pariy, T. Ludwig, S. Mathur, C. Xu and R. Surmenev, ACS Appl. Mater. Interfaces, 2023, 15, 3731–3743 CrossRef CAS PubMed.
- L. Cheng, X. Hao, G. Liu, W. Zhang, J. Cui, G. Zhang, Y. Yang and R. Wang, Biosensors, 2023, 13, 131 CrossRef CAS PubMed.
- J. Zhang, M. Ahmadi, M. Serra, E. Jimenez-Pique, L. Llanes and G. Fargas, Ceram. Int., 2023, 49, 11579–11588 CrossRef CAS.
- H. Tao, J. Yin, Q. Zong, L. Zhao, D. Ergu, J. Ma, B. Wu and B. Ma, J. Alloys Compd., 2023, 935, 168142 CrossRef CAS.
- C. M. Magdalane, K. Kaviyarasu, J. J. Vijaya, B. Siddhardha and B. Jeyaraj, J. Photochem. Photobiol., B, 2016, 163, 77–86 CrossRef CAS PubMed.
- Y. S. Kim, G.-H. Lee, M.-C. Sung and D.-W. Kim, Chem. Eng. J., 2021, 406, 126896 CrossRef CAS.
- S. Cabuk, Philos. Mag., 2020, 100, 601–618 CrossRef CAS.
- H. Zhang, D. Zhang, B. Zhang, D. Wang and M. Tang, ACS Appl. Mater. Interfaces, 2022, 14, 48907–48916 CrossRef CAS PubMed.
- C. Sow, G. Mettela and G. U. Kulkarni, Annu. Rev. Mater. Res., 2020, 50, 345–370 CrossRef CAS.
- H. Wang, Z. Li, Z. Liu, J. Fu, T. Shan, X. Yang, Q. Lei, Y. Yang and D. Li, J. Mater. Chem. C, 2022, 10, 1594–1605 RSC.
- A. R. Chakhmouradian and P. M. Woodward, Phys. Chem. Miner., 2014, 41, 387–391 CrossRef CAS.
- R. Shi, Z. Lou, S. Chen and G. Shen, Sci. China Mater., 2018, 61, 1587–1595 CrossRef CAS.
- Z. Hou, S. Feng, P. Hei, T. Yang, Z. Ran, R. Zheng, X. Liao, C. Shu and J. Long, J. Power Sources, 2019, 441, 227168 CrossRef CAS.
- G. D. Park, J. H. Hong, J. H. Choi, J. H. Lee, Y. S. Kim and Y. C. Kang, Small, 2019, 15, 1901320 CrossRef PubMed.
- B. Ju, H. J. Song, G.-H. Lee, M.-C. Sung and D.-W. Kim, Energy Storage Mater., 2020, 24, 594–601 CrossRef.
- G. H. Lee, M. C. Sung, J. C. Kim, H. J. Song and D. W. Kim, Adv. Energy Mater., 2018, 8, 1801930 CrossRef.
- Y. Liu, L. Yang, Q. Chen, Z. Wang, Z. Yang, J. Cao, X. Wang, H. Li and X. Huang, Chem. – Eur. J., 2022, 28, e202200298 CrossRef CAS PubMed.
- J. Huang, X. Tang, F. Wang, Z. Wang, Y. Niu and H. Wang, Adv. Eng. Mater., 2022, 24, 2101767 CrossRef CAS.
- Z. Shen, X. Zhu, C. Majidi and G. Gu, Adv. Mater., 2021, 33, 2102069 CrossRef CAS PubMed.
|
This journal is © The Royal Society of Chemistry 2024 |
Click here to see how this site uses Cookies. View our privacy policy here.