DOI:
10.1039/D4SC00711E
(Review Article)
Chem. Sci., 2024,
15, 7010-7033
Rescuing zinc anode–electrolyte interface: mechanisms, theoretical simulations and in situ characterizations
Received
30th January 2024
, Accepted 5th April 2024
First published on 8th April 2024
Abstract
The research interest in aqueous zinc-ion batteries (AZIBs) has been surging due to the advantages of safety, abundance, and high electrochemical performance. However, some technique issues, such as dendrites, hydrogen evolution reaction, and corrosion, severely prohibit the development of AZIBs in practical utilizations. The underlying mechanisms regarding electrochemical performance deterioration and structure degradation are too complex to understand, especially when it comes to zinc metal anode–electrolyte interface. Recently, theoretical simulations and in situ characterizations have played a crucial role in AZIBs and are exploited to guide the research on electrolyte engineering and solid electrolyte interphase. Herein, we present a comprehensive review of the current state of the fundamental mechanisms involved in the zinc plating/stripping process and underscore the importance of theoretical simulations and in situ characterizations in mechanism research. Finally, we summarize the challenges and opportunities for AZIBs in practical applications, especially as a stationary energy storage and conversion device in a smart grid.
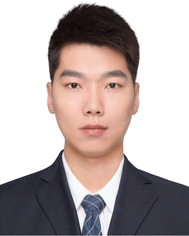 Zhenjie Liu | Zhenjie Liu is an associate research fellow at College of Materials Science and Engineering, Shenzhen University. He received his PhD degree from School of Applied Chemistry and Engineering (Changchun Institute of Applied Chemistry Chinese Academy of Sciences) at University of Science and Technology of China in 2019. His current research focuses on metal anodes for energy storage including alkali metal-ion and -oxygen batteries. |
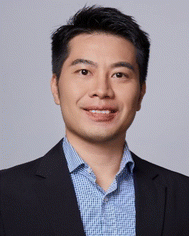 Yang Huang | Yang Huang is currently an assistant professor of the Advanced Materials Trust at The Hong Kong University of Science and Technology (Guangzhou). He obtained his bachelor and master degrees from Southwest Jiaotong University in Chengdu, Sichuan. Then, he obtained his PhD degree from City University of Hong Kong. His primary research focuses on low-dimensional materials with easily modifiable properties (e.g., transition metal carbides and nitrides, known as MXenes) and their applications in advanced micro-/nano-electronic devices (e.g., battery and supercapacitor). |
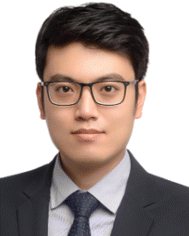 Zhe Hu | Zhe Hu is a professor at College of Materials Science and Engineering, Shenzhen University. He received his Bachelor's degree (2011) and Master's degree (2013) from Nankai University, China. He obtained his PhD from the University of Wollongong in 2019. His research focuses on advanced electrode materials, reaction mechanisms, and interface engineering of metal-ion batteries. |
1. Introduction
Since Kang et al. first proposed the concept of aqueous zinc-ion batteries (AZIBs),1 AZIBs have received tremendous attention due to their high safety, abundance, and satisfactory performance. Besides, the development of AZIBs promotes the studies on other aqueous batteries (e.g., Zn–I2 batteries), which share similar mechanism and cell configuration.2–4 However, currently, AZIBs still encounter many challenges that hinder their further development as a practical alternative to commercial batteries (e.g., Li-ion batteries). Although researchers have made great efforts to improve the electrochemical performance, some tough issues remain, including the co-intercalation of proton and Zn2+, dissolution of cathode materials, sluggish kinetics during charge and discharge, and unstable Zn metal anode (ZMA).5,6 Among these challenges, the ZMA is the most serious one, resulting in the quick capacity decay of AZIBs in their long-term service.
In the aqueous electrolyte, ZMA will undergo a chemical conversion reaction between Zn atoms and Zn2+, i.e., the plating/stripping of ZMA, during the discharge and charge processes. It is generally accepted that the problems occurring on the ZMA–electrolyte interface are the main reasons for ZMA's instability. For example, the nucleation and growth of Zn2+ on the ZMA surface during Zn plating is usually accompanied with the growth of irregular Zn dendrites, which will penetrate the separator membrane and eventually cause the short circuit in AZIBs. In addition, the side reactions taking place at the ZMA–electrolyte interface during the plating/stripping (e.g., hydrogen evolution reaction (HER) and corrosion) can cause low coulombic efficiency (CE) and low capacity, which considerably degrades the cycling stability of ZMA. In fact, the issues happening at the ZMA–electrolyte interface are interdependent and entangled with each other, as shown in Fig. 1, which would break the balance of the ZMA–electrolyte interface and finally lead to the failure of ZMA and AZIBs.7,8
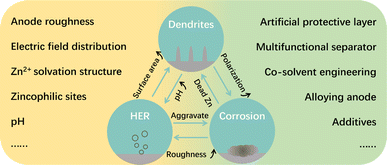 |
| Fig. 1 The issues, influencing factors and modification strategies of the ZMA–electrolyte interface. | |
When addressing the instability issues of ZMA, it requires a comprehensive understanding of the underlying mechanisms and influencing factors that are related to the ZMA–electrolyte interface. For instance, during Zn plating, the zinc ions near the ZMA–electrolyte interface will undergo a series of reaction steps, such as migration, desolvation, diffusion, and reduction at the nucleation sites. Due to the different electric field and Zn2+ distribution, Zn atoms prefer to accumulate and continuously grow at some protuberances of the ZMA surface, which results in Zn dendrites after repeated Zn plating. Therefore, the Zn plating result is intricately connected to the distribution of electric field, concentration of Zn2+, and amount of zincophilic sites, all of which could be influenced by the roughness of the ZMA–electrolyte interface.9–11 Moreover, Zn(H2O)62+, as the primary solvation structure in the aqueous electrolyte, is considered as a crucial factor that induces HER at the ZMA–electrolyte interface. The occurrence of HER would then lead to a localized pH elevation at the ZMA–electrolyte interface, thereby exacerbating the corrosion reaction at the surface of ZMA.12 Based on the above understanding, it is apparent that the stabilization of the ZMA–electrolyte interface, determined by interface roughness, Zn2+ solvation structure, and electrolyte pH, is the key for solving the problems of unstable ZMA in the aqueous electrolyte. Accordingly, the improvements of the ZMA–electrolyte interface should be conducive to enhancing the electrochemical performance of AZIBs in theory.13,14
Currently, many strategies have been developed to enhance the properties of the ZMA–electrolyte interface, for example, optimizing the crystalline structure of ZMA, constructing artificial interface on ZMA,15,16 designing multifunctional separator and current collector,17–19 and regulating the electrolyte compositions.20–23 To further improve these strategies for better AZIBs, it is important to uncover the relationships between interface structure and battery performance.24,25 There are many characterization methods that have been applied to investigate the structure of the ZMA–electrolyte interface. However, these methods are mostly ex situ techniques, which fail to provide continuous information to clearly illustrate the dynamic evolution of the ZMA–electrolyte interface. Such a lack of information of the interface structure from ex situ characterization might be less effective in guiding future research on the ZMA–electrolyte interface. Thus, in situ characterization methods that can provide abundant information of the battery during any period of charge and discharge are indispensable for explaining the structure and performance relationship of the ZMA–electrolyte interface. Moreover, as a supplementary technique for in situ characterizations, theoretical simulations provide detailed information about the structure change of the ZMA–electrolyte interface at atomic and electronic levels under specified conditions. Apparently, the combination of in situ characterizations and theoretical simulations should be an ideal scheme for understanding how to improve the ZMA–electrolyte interface. However, only a few studies summarize the important roles of in situ characterizations and theoretical simulations in the research on the ZMA–electrolyte interface.
To fill the gap of current studies, we focus on discussing three objects in this review, i.e., ZMA–electrolyte interface protective mechanisms, theoretical simulations, and in situ characterizations. At first, we systematically overview six protective mechanisms for enhancing the stability of the ZMA–electrolyte interface, including the provision of zincophilic sites, regulation of crystal orientation, modulation of solvation structure, reconstitution of hydrogen bond network, maintenance of pH, and formation of the solid electrolyte interphase (SEI) layer. Subsequently, we have discussed how common theoretical simulations and various advanced in situ characterizations are used to study the reaction kinetics of Zn plating/stripping and the dynamic changes at ZMA–electrolyte interface, and ultimately evaluate various optimization strategies and their influence on the battery performance. At the end of this review, we will provide our perspectives and insights into the future development of the ZMA–electrolyte interface and the in situ characterizations. We believe that our review will be helpful for designing the highly stable ZMAs for high-performance AZIBs.
2. Electrolyte engineering-induced protective mechanisms
In recent years, there has been a significant increase in research investigating various protection strategies that aim at enhancing the stability of the ZMA–electrolyte interface. Taking into account the simplicity and efficiency in controlling the electrolyte compositions, we primarily focus on summarizing the in situ electrolyte engineering strategies. Hence, the coverage of other protection strategies in this section is not exhaustive. More detailed information of other protection strategies can be obtained from ref. 26 and 27. The commonly used electrolyte engineering strategies can be classified into the following categories: electrolyte additives,28–30 co-solvent engineering,31–34 gel-electrolytes,35,36 deep eutectic electrolytes,37–39 and high concentration salts22,40–43 This section, as depicted in Fig. 2, presents a review of the mechanisms involved in electrolyte engineering, including the provision of more zincophilic sites, regulation of crystal orientation, modulation of solvation structure, weakening of the hydrogen bond network, maintenance of pH, and construction of the SEI layer.
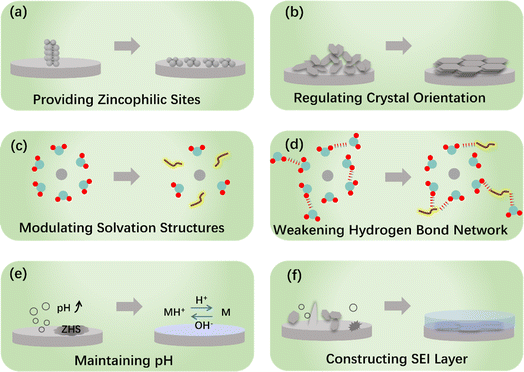 |
| Fig. 2 Protective mechanism of electrolyte engineering for ZMA. | |
Table 1 systematically summarizes the electrolyte composition and electrochemical properties of ZMA under different mechanisms. However, due to the lack of evaluation standard, the underlying mechanisms for each additive remain unclear. Currently, the main issues of additive strategies are the high additive dosage, low current density and shallow discharge depth, which fail to meet the application requirements. Moreover, the impacts of additive on the electrolyte stability and cathode compatibility are sometimes overlooked. Therefore, further studies are required to understand the ZMA–electrolyte interface, which mainly include the design and selection of electrolyte additive, the structure–function relationship between the additive/interface components and electrochemical properties, as well as the investigation of the dynamic performance and electrochemical behavior of ZMA.
Table 1 Comparison of performance reported for different protective mechanisms via electrolyte engineering
Protective mechanisms |
Electrolyte/anode |
Cycling performance [h (mA cm−2, mA h cm−2)] |
Reference |
Providing zincophilic sites |
0.2 wt% sericin/2 M ZnSO4 (ZS) |
2860 (1, 2) |
45
|
10 mM α-cyclodextrin (CD)/3 M ZS |
200 (5, 5) |
46
|
10 mM Ce2(SO4)3/1 M ZS |
700 (5, 1) |
47
|
8.5 mM La(NO3)3/2 M ZS |
1200 (1, 1) |
48
|
4 mM NiSO4/2 M ZS |
900 (1, 1) |
49
|
Regulating crystal orientation |
20 mM BMIm+/2 M ZS |
1400 (5, 5) |
62
|
500 mM sorbitol/1 M ZS |
480 (5, 5) |
63
|
β-CD/2 M ZS |
1700 (4, 2) |
65
|
5 vol% DX/2 M ZS |
1000 (5, 5) |
69
|
Cys-Zn@Zn |
2000 (2, 2) |
70
|
Modulating solvation structure |
0.5 wt% silk fibroin/1 M ZS |
>1600 (1, 1) |
77
|
1 M triethylmethyl-ammonium chloride/0.5 M ZnCl2 |
500 (5, 2.5) |
78
|
0.05 M ethylene diamine tetraacetic acid/1 M ZS |
3000 (5, 1) |
81
|
4 M 1-ethyl-3-methylimidazolium chloride/2 M ZS |
500 (1, 1) |
83
|
40 vol% methanol/5 mol kg−1 Zn(BF4)2/ethylene glycol |
1600 (2, 1) |
87
|
Weakening hydrogen bond network |
5 mM trehalose/1 M ZS |
1300 (5, 2.5) |
89
|
100 mM xylitol/2 M ZS |
1000 (5, 1) |
90
|
2 mg mL−1 CH6NPO3/2 M ZS |
900 (5, 2.5) |
91
|
DMF-50% + PEG-30%/2 M Zn(OTF)2 |
1000 (2, 2) |
92
|
4 mol kg−1 Zn(BF4)2 in ethylene glycol |
4000 (0.5, 0.25) |
94
|
2 M Zn(OTF)2 in 2H1D (volume ratio of H2O : DMF) |
>1000 (50, 50) |
95
|
Maintaining pH |
2 M LiCl/3 M ZS |
170 (0.2, 0.03) |
98
|
Acetic acid/tetramethylene sulfone/3 M Zn(OTF)2 |
300 (5, 5) |
99
|
75 mM Na4EDTA/2 M ZS |
2000 (5, 2) |
103
|
0.025 M NH4OAc/2 M ZS |
3500 (1, 1) |
104
|
40 vol% γ-butyrolactone/1.6 mol kg−1 ZnCl2 |
600 (10, 2) |
109
|
Constructing SEI layer |
20 mM Zn(NO3)2/3 M Zn(OTF)2 |
1200 (0.5, 0.5) |
119
|
1% fluoroethylene carbonate/2 M ZS |
1000 (4, 1) |
120
|
0.05 mM sulfanilamide/2 M ZS |
4800 (2, 2) |
123
|
25 mM Zn(H2PO4)2/1 M Zn(OTF)2 |
220 (5, 1) |
125
|
1.3 M ZnCl2–H2O–DMSO |
1000 (0.5, 0.5) |
127
|
2.1. Providing zincophilic sites
The operation of Zn nucleation involves the migration, desolvation, and diffusion of Zn2+, and the diffusion process precisely depends on the zincophilic sites. The dense zincophilic sites favor achieving a constant 3D diffusion process, thereby guiding the subsequent uniform plating of Zn. However, the rampant 2D diffusion process occurring at the ZMA–electrolyte interface would lead to the production of Zn dendrites. For instance, Zhang et al.44 proposed that the polyacrylamide additive with abundant acyl groups serves as a guiding intermediary to provide more nucleation sites. A uniform electric field and charge distribution are discovered, resulting in a smooth ZMA surface during cycling. Wang et al.45 selected sericin molecules as electrolyte additives, which contain zincophilic functional groups. The proposed electrolyte additive adsorbs on the ZMA surface, resulting in denser ZMA after Zn plating. Zhao et al.46 took advantage of the hydrophobic internal cavity and hydrophilic external surface of cyclodextrins to manipulate and boost the kinetics and stability of ZMA.
Furthermore, the incorporation of high valence cations additives, such as La3+ and Ce3+ ions, preferentially occupy the electron-rich active sites. This leads to Zn nucleation and growth taking place at relatively inert areas,47 weakening the repulsive force of electrical double layer (EDL)48 and guiding Zn nucleation towards gradual nucleation rather than instantaneous nucleation. Recently, Dai et al.49 introduced the concept of an “escort effect” of Ni2+ ion additives, which can deposit in advance and result in subsequent Zn plating via underpotential deposition. Regarding the relevant mechanisms, Xie et al.50 proposed a mesoporous Zn plating method, as illustrated in Fig. 3a. Hollow carbon spheres were chosen as the anode materials. Zn2+ was reduced to single-atom Zn on zincophilic sites in hollow carbon spheres, and then Zn clusters were formed by these single-atom Zn. These Zn clusters further expanded to form a mesoporous Zn network, leading to a uniform Zn plating layer. Apart from the electrolyte engineering, for more zincophilic site design, please consult ref. 51.
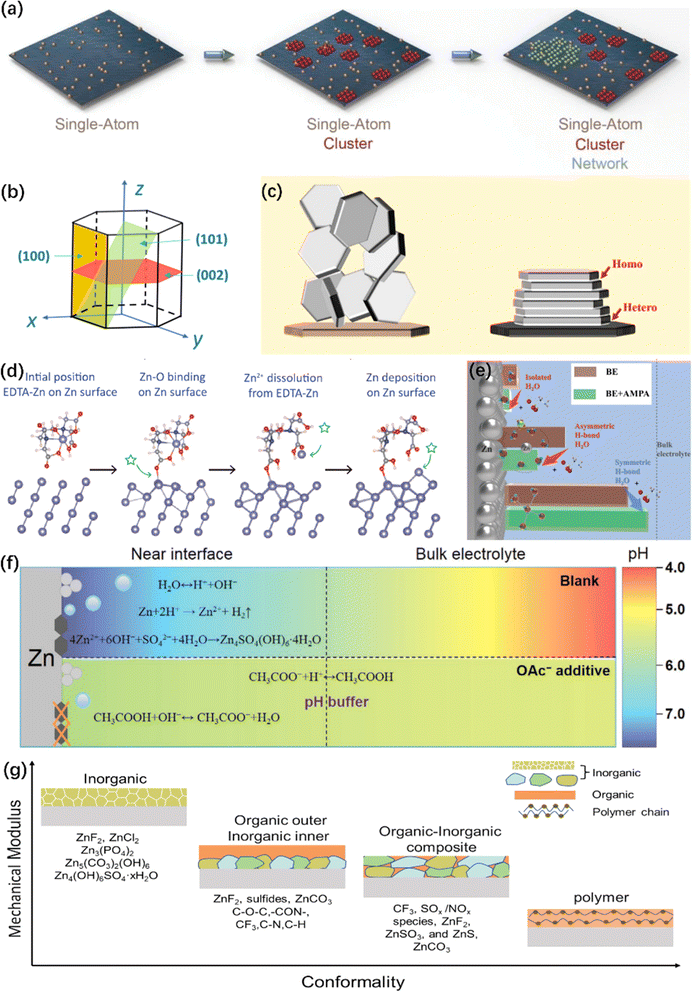 |
| Fig. 3 Illustration of electrolyte engineering for protecting ZMA. (a) Schematic illustration of the Zn deposition process.50 Copyright 2021, Wiley. (b) The illustration of the hexagonal close packed structure of Zn.52 Copyright 2023, Royal Society of Chemistry. (c) Scheme illustrating the design principle of epitaxial metal electrodeposition.56 Copyright 2019, AAAS. (d) Dynamic evolution of an EDTA–Zn molecule during Zn plating.81 Copyright 2022, Wiley. (e) Comparative schematic of interfacial water structures in different electrolytes.91 Copyright 2023, Wiley. (f) Schematic illustration of the pH evolution in different electrolytes and the interfacial pH buffer mechanism enabled by the OAc− anion.104 Copyright 2022, Wiley. (g) Mechanical characteristics of different types of SEI layer.25 Copyright 2023, Wiley. | |
2.2. Regulating crystal orientation
Zn has a typical hexagonal close-packed (hcp) structure, as shown in Fig. 3b,52 which is characterized by crystal planes with high relative texture coefficients (RTCs), predominantly including the (002), (100) and (101) crystal planes. Among all the Zn crystal planes, the (002) crystal plane has a low surface energy. The (002)-preferred orientation generally provides active sites along the edge and induces paralleled stacked Zn plating on the ZMA.53–55 Based on this characteristic, Zheng et al.56 reported the epitaxial regulation concept of the Zn nucleation and growth, as illustrated in Fig. 3c. Furthermore, owing to its higher free energy of H adsorption and stripping energy of Zn, the (002) crystal plane could effectively inhibit HER and significantly avoid the side reaction.35,55 Consequently, a number of studies have recently designed to optimize the growth of the (002) crystal plane. The common methods of the (002) crystal plane modulation, such as surface texture design, surface coating, separator modification and current density control, have been systematically reviewed in ref. 57–60.
Apart from the abovementioned design and optimization, electrolyte additives also play an ingrained role during the plating process due to their specific adsorption effects. Sun et al.61 conducted research on a series of organic additives and concluded that using different additives in the plating process can modify the crystallographic properties and surface morphology of the ZMA. In this regard, the functions of these additives can be summarized as below.
(i) The additives, such as sodium 3,3′-dithiodipropane sulfonate,52 1-butyl-3-methylimidazolium cation,62 and sorbitol,63 tend to adsorb on the other crystal planes except for (002). Therefore, more of the (002) crystal plane is exposed, inducing the preferential growth on the (002) crystal plane. For instance, the presence of I− additives significantly elevates the growth rate along the (100) direction, thus resulting in the final exposure of the (002) crystal plane.64
(ii) Some additives, such as β-cyclodextrin, nicotinamide, and 1,4-dioxane, prefer to adsorb horizontally on the (002) crystal plane, thus modulating the nucleation and diffusion pathways of Zn2+ and guiding the orientated deposition along a direction parallel to the (002) crystal plane.65–69
(iii) Additives, such as L-cysteine,70 selectively etch the bulk Zn substrate, especially the Zn(101) crystal plane, and contribute to more dominant (002) crystal plane exposure.
Very recently, there have been divergent viewpoints. On the one hand, achieving a stable cycling performance with high capacity from (002)-textured zinc is challenging due to the significant lattice distortion and uneven distribution of the electric field.71 On the other hand, it is found that the (002) crystal plane is chemically unstable and prone to be corroded by water in aqueous electrolytes, leading to the formation of detrimental zinc hydroxide sulfate hydrate (ZHS).72 More importantly, it is unknown whether the above strategies are still effective when a higher depth of discharge is applied.
2.3. Modulating solvation structure
It is well known that the strong solvation of Zn2+ with H2O molecules exacerbates the electrochemical polarization and charge transfer resistance of Zn2+.73 Moreover, the strong interactions will lead to the HER of solvated water.74 A systematic summary and comprehensive introduction on the evolution of the solvation structure affected by electrolyte additives is presented in ref. 13. Typically, Zn2+ is solvated with six water molecules to form hydrated zinc ions, i.e., [Zn(H2O)6]2+,75 leading to a high energy barrier of 289.3 kcal mol−1, and can be improved employing electrolyte additives.61,76 For instance, Xu et al.77 introduced silk fibroin (SF) as an electrolyte additive, and the [Zn(H2O)4(SF)]2+ solvation structure is formed. The desolvation process releases SF on the ZMA surface and in situ forms hydrostable and self-healable protective film. Yao et al. found that the triethylmethyl ammonium (TMA) cation can participate in the constitution of [Zn(SO4)2(TMA)3]+ structure in the electrolyte. The obtained solvated structure reduces the number of reactive H2O molecules and inhibits by-product formation.78 Moreover, methanol, as an antisolvent, can modulate the coordination structure of Zn2+.79,80 Based on the above-mentioned improvement of ZMA, it is necessary to analyze how additive molecules or cations inherently reconstruct the typical solvation structure, which could effectively improve the electrochemical performance. Yang et al. proposed a stability constant (K), which represents the equilibrium constant of the complexation reaction.81 This method is served as a universal standard to understand the anchoring strength between the additive ligands and solvated Zn2+, and the dynamic evolution of Zn plating process is shown in Fig. 3d. In addition, Shao's work82 reported that solvents with a higher donor number were favorable for stabilizing the ZMA–electrolyte interface as the donor number reflects the solvation ability between solvent molecules and Zn2+.
Apart from organic electrolyte additives or solvents, there are other categories of effective additives. Zhang et al.83 utilized a chloride salt with a bulky cation (1-ethyl-3-methylimidazolium chloride, EMImCl) to form an anion-type water-free solvation structure ZnCl42− in the electrolyte. They also designed an ammonium halide additive.84 I− is acted as an electron donor and coordinates with Zn2+ to form the solvation structure ZnI(H2O)5+. The stability of the solvation structure is effectively enhanced, making it much easier to inhibit HER.
2.4. Weakening hydrogen bond network
The high activity of H2O molecules poses a threat at the ZMA-electrolyte interface.85 In addition, the original hydrogen bond network among H2O molecules, which is an important indicator of HER,86 can be easily destroyed by applying co-solvents or deep eutectic electrolyte.87,88 Moreover, a new hydrogen bonding network containing multifunctional groups can be constructed, which in turn inhibits the activity of the H2O molecule.89 For instance, xylitol additive inhibits HER, accelerates cation migration by expelling active H2O molecules, and facilitates the reconstruction of the hydrogen bond network.90 Recently, a study demonstrates that (aminomethyl)phosphonic acid (AMPA) promotes the formation of an ordered hydrogen bond network at the interfacial H2O, resulting in the inhibition of water-induced H2 production (Fig. 3e).91 The reconstruction of the hydrogen bond network enlarges the electrochemical stability voltage range and the operational temperature range.92–94 To validate the fundamental role of additives in the broken hydrogen bond network, a series of Lewis basic organic molecules with lone pair electrons were proposed.95 Due to the unique strong electronegativity of the lone pair of electrons, the tetrahedral structure of H2O molecules and their original hydrogen bond network were broken.
2.5. Maintaining proton concentration (pH)
According to the Pourbaix diagram, it is indicated that HER is a pH-dependent reaction and an inevitable thermodynamic process. The sources of HER on ZMA can be attributed to the following three reasons: the high reactivity of solvated H2O, the purity of ZMA and the irregular surface morphology.96 The occurrence of HER results in the release of more OH−, leading to an elevation in pH value and exacerbating the corrosion reactions on ZMA. For a thorough understanding, please consult the pH evolution law of the ZMA–electrolyte interface and its impact mechanism on the formation of Zn dendrites, as firstly revealed by Yang et al.97
Therefore, the pH value of the ZAM–electrolyte interface is crucial, and the additives will disrupt the pH value of the pristine electrolyte. As the amount of additive is increased, the pH value is either increased or decreased: the lower suitable pH of the electrolyte can diminish the formation of ZHS,98,99 and an appropriate increase in the electrolyte pH benefits the suppression of HER;100,101 moreover, an excessively high pH value (>5.47) would exacerbate corrosion.102 For instance, a specific quantity of Na4EDTA will trigger the formation of the ZHS precipitate in the electrolyte.103 Therefore, a pH buffer electrolyte additive is required to keep an appropriate pH value, such as acetic acid/acetate (HOAc/OAc−),104,105 pyridine/pyridinium,106 and imidazole/imidazolium.107,108 These electrolyte additives act as pH regulators to help maintain an appropriate acid–base balance during the charge/discharge process, ultimately mitigating the interfacial HER and corrosion reactions (as depicted in Fig. 3f).104 Interestingly, Zhang et al. presented a molecular switch strategy that utilizes the reversible structural changes of γ-butyrolactone (GBL) and γ-hydroxybutyrate (GHB) under varying pH levels.109 In addition, certain coating protection or double salt electrolyte can also serve as a pH buffer.110–112
2.6. Constructing solid electrolyte interphase (SEI) layer
The in situ construction of an Zn2+ conductive SEI layer that can be achieved through the reduction and decomposition of electrolyte, exhibiting enhanced durability and stability in providing protective effects. The presence of this in situ layer effectively impedes corrosion and promotes a homogeneous distribution of cations, attributable to its chemical bonding with the anode surface. Nevertheless, the establishment of a compact and enduring SEI layer in aqueous electrolytes faces a considerable obstacle due to the concurrent production of gas and inert byproducts during the decomposition of these electrolytes.113 Additional insights into the formation and composition of SEI can be ascertained in ref. 114, and Fig. 3g illustrates the mechanical characteristics of different types of SEI layer.25 Therefore, the introduction of an additional concept, referred to as the EDL, becomes imperative as it considerably impacts the chemical properties and morphology of the SEI through the arrangement of molecular and ionic assemblies in close proximity to the anode.115 However, numerous additives merely adsorb onto the ZMA surface to generate a EDL without undergoing subsequent reduction to form an SEI. In response to this issue, Huang et al. conducted a comprehensive evaluation of 15 organic additives and identified the pivotal determinant of these additives' protective effectiveness as their capacity to generate an SEI layer.116
Unlike the traditional organic electrolyte, ZMA suffer from severe surface corrosion and the formation of non-uniform ZHS and ZnO compounds. By introducing a small quantity of Zn(OH)2 additive into the ZnSO4 electrolyte117 or Na2SO4 additives into zinc trifluoromethanesulfonate (Zn(OTF)2) electrolytes,118 the conversion of the non-uniform ZHS into a homogeneous and durable SEI layer is achieved. Li et al. designed a low-concentration aqueous Zn(OTF)2–Zn(NO3)2 electrolyte. An insulating Zn5(OH)8(NO3)2·2H2O passivation layer was first formed, which then transformed into a more stable Zn-ion conductive Zn5(CO3)2(OH)6 layer and ZnF2-rich SEI layer in sequence.119 From the perspective of composition, prior investigations demonstrate that the SEI layers enriched in ZnF2,120–122 ZnS123,124 and zinc phosphate (Zn3(PO4)2) are propitious to enhance the stability of the ZMA–electrolyte interface.125,126 These constituents of the SEI layer are either derived from the decomposition products of additives or the reduction of anions promoted by additives.
Apart from inorganic additives, organic additives play an equally important protective role. For instance, the ZnCl2–H2O–DMSO electrolyte forms an SEI layer based on Zn12(SO4)3Cl3(OH)15 through the decomposition of solvated DMSO.127 On the one hand, organic additives can construct an anode-molecular interface.128,129 On the other hand, they can decompose directly to produce organic–inorganic SEI layers.130,131 In summary, additives containing nitrogen or sulfur functional groups can provide significant protection. However, the precise mechanism by which these active groups participate in the formation process of the SEI layer, especially when it involves the capture of certain intermediates, is poorly understood. Therefore, the advancement of theoretical simulations and in situ characterizations will contribute to uncovering the underlying mechanisms.
3. Theoretical simulations
Theoretical simulations have been widely conducted in literatures to investigate the mechanisms of reactions happening at the ZMA–electrolyte interface. Using theoretical simulations can considerably improve the understanding of the fundamental mechanisms.132,133 This section will specifically summarize the functions of various theoretical simulation methods in investigating the ZMA–electrolyte interface.
3.1. COMSOL simulations
As mentioned earlier, the stability of the ZMA–electrolyte interface can be influenced by interface roughness. An uneven interface can induce the “tip effect”, which depends on the intensity of the electric field and the Zn2+ concentration near the ZMA–electrolyte interface.134 As shown in Fig. 4a and b, COMSOL simulation indicated that electrons and ions tend to accumulate at the sharp tips on bare ZMA. Additionally, micron-scale concavities or pits on ZMA can also enhance the intensity of the electric field.135,136 The former worsens dendrite growth, while the latter is more conducive to enhancing the stability of the ZMA–electrolyte interface because it leads to a uniform electric field and Zn2+ distribution. Consequently, more researches on electrode structure design have been reported, such as 3D-scaffold anode137,138 and Zn@CuNW anode.139–141 Following this theory simulation, researchers discovered that an exaggerated electric field heterogeneity occurs when the bending radius is less than 5 mm.142 In terms of electrolyte engineering, COMSOL simulation can be applied to determine whether the interface electric field and Zn2+ flux are homogeneous by preferentially adsorbing functional groups on the ZMA surface.143–145 Furthermore, COMSOL simulations were roughly estimated to predict the surface morphology and the hydrogen diffusion flux.122,146
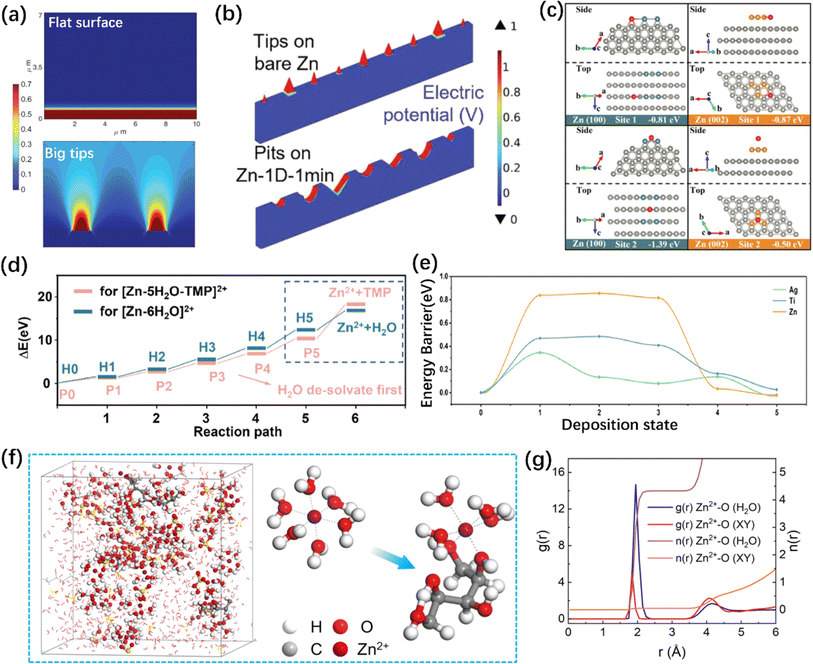 |
| Fig. 4 Illustration of theoretical simulations. (a) COMSOL simulation of Zn2+ diffusion and distribution with different conditions.135 Copyright 2019, Wiley. (b) Electric field distribution simulation results of ZMAs with different scratches.136 Copyright 2023, Wiley. (c) The adsorption energy of Zn at different sites on the (100) and (002) crystal planes.55 Copyright 2021, Wiley. (d) Comparison of the energy barrier required for normal and novel solvation structures to de-solvate through DFT calculation.166 Copyright 2023, Elsevier. (e) Energy profiles of Zn cluster at different deposition states.169 Copyright 2023, American Chemical Society. (f and g) Snapshot of the electrolyte containing xylitol additive (f) and its corresponding RDFs and CN (g) collected from MD simulations.30 Copyright 2023, Wiley. | |
3.2. Density functional theory (DFT) calculations
It is generally accepted that DFT calculations are indispensable tools in numerous scientific and engineering disciplines, providing valuable guidance and explanations for experiments. In this section, the application of DFT calculations for the research of the ZMA–electrolyte interface is described as follows.
(i) Tuning the correlations, such as the adsorption energy of additive on ZMA–electrolyte interface, binding energy of additive with Zn2+, free energy of H adsorption147,148 and energy of the stripping process.55,149 Calculating and comparing the adsorption energy of zinc atoms on different crystal plane of ZMA helps identify the dominant zincophilic sites and provide reasons why additives can inhibit the growth of Zn dendrites.44,50,150–153 Moreover, the charge density distribution and surface electrostatic potential intuitively reflect the strong interaction of Zn2+ and precise active site for Zn2+ nucleation,49,154,155 respectively. As shown in Fig. 4c, DFT calculations show that the surface configuration156 or special Zn deposition sites55 can impact the adsorption energy of Zn atoms. Aside from zincophilic sites, lower diffusion energy barriers support the formation of a 2D deposition mode, leading to uniform and dendrite-free Zn deposition.157,158 Then, a unique zincophobic repulsion mechanism was proposed in the presence of an additive adsorption layer.159,160
In addition, the binding energy between different additives and Zn2+ is closely related to the solvation structure. In traditional electrolyte, Zn2+ solvated with six water molecules forms a hydrated zinc ions, resulting in a formation energy of −5.58 eV.161 By comparing the binding energy or desolvation barriers of different solvation structures, researchers can identify the most stable solvated structure and simulate the desolvation process.162–165 As shown in Fig. 4d, DFT calculations indicated that the desolvation process for additive molecule detachment can be considered as a rate-determining step. In this case, additive molecules tend to replace the active H2O molecules in the solvation structure, thereby driving the active H2O molecules away from the ZMA–electrolyte interface during the desolvation process. Thus, the HER caused by active H2O molecules is alleviated.166 Furthermore, Zhou et al. firstly investigated the effects of the molecular electrostatic polarity on the desolvation of hydrated Zn2+, which is used as a key factor to select a suitable additive to regulate reversible Zn plating/stripping chemistry.167
(ii) Evaluating the kinetics and stability of the Zn2+ deposition and diffusion on ZMA surface.168 Conventionally, it was believed that a low adsorption energy and rapid Zn2+ diffusion coefficient contribute to the fast and uniform nucleation and deposition of Zn hexagonal crystal.143 For instance, by comparing the 3D charge density variances and Gibbs free energy of the deposited Zn2+, as well as the energy of the Zn cluster on different matrixes (Fig. 4e), an accelerated reaction kinetics and uniform Zn deposition were implemented on Ag surfaces.169 Furthermore, to thoroughly investigate the mechanism of Zn dendrite formation induced by residual stress and lattice defects, the Gibbs free energy of Zn crystals under different stress and defect states was evaluated using DFT calculations.170
3.3. Molecular dynamics (MD) simulations
MD simulation can provide an in-depth electrolyte analysis, such as anion solvation structure,171 ionic conductivity,172 and spontaneous chemical reactivity.173 From the perspective of molecular dynamics, the evolution of the electrode–electrolyte interfaces can be simulated (Fig. 4f and g).30 The applications of MD simulations in the research of AZIBs to date can be summarized as follows. (1) Exploring the solvation structure of Zn2+ and its corresponding radial distribution functions (RDFs) and coordination number (CN).174–176 (2) Elucidating the ionic diffusion behaviors in the electrolyte or the SEI layer.141,177–179 (3) Estimating the hydrogen bond network and activity of H2O.80,92,180 (4) Revealing the effects of additive molecules on the separator or ZMA.129,181
Therefore, MD simulations can help understand the changes in the electrolyte during a proposed system in a visualized way. For instance, an electrochemically and thermally stable Zn5(OH)6(CO3)2-containing SEI layer was successfully achieved by the decomposition of N,N-dimethylformamide (DMF).182 The corresponding MD simulation indicates that most of the Zn2+ migration occur in the Zn5(OH)6(CO3)2 phase along the [010] lattice plane. Moreover, the concentration-dependent effects in an electrolyte-containing propylene glycol (PG) additive were studied by the MD simulation, indicating that a self-assembled mediated film formation occurs at a low concentration.183 Recently, Yang et al. proposed a bulk-phase reconstructed ZMA with abundant zincophilic sites, which considerably improved the resistance to dendrite growth and side reactions even after deep stripping. In the case, MD simulations were employed to analyze the nitrogen bombardment process at different nitrogen species energies, substrate temperature, and substrate vacancy concentrations to guide the acquisition of a bulk-phase reconstructed ZMA.184
4.
In situ characterization
Theoretical simulations provide valuable insights into the protective mechanisms of electrolyte engineering strategies and guide their further development. Furthermore, experimental evidence, obtained through in situ characterizations, is also indispensable for a direct understanding of the mechanisms. In this section, we summarize the applications of various novel in situ characterizations that have been employed to investigate the ZMA–electrolyte interface, such as in situ visualizing characterizations, in situ spectroscopy/mass spectrometry characterizations, in situ physicochemical characterizations and other advanced characterizations. For a schematic representation of the relevant in situ characterizations and more detailed information about the in situ battery structure, please consult the references of 185–187.
4.1.
In situ visualizing characterization
4.1.1.
In situ optical microscopy (OM).
Similar to Li-ion batteries,188,189 it is essential to monitor the morphology and structure evolution of the ZMA in real-time. ZMA protection strategies have been well studied using in situ OM to investigate the differences of dendrite growth under different conditions. Without any protection strategies, irregular dendrites and gas bubbles form on the ZMA surface during the plating process, which is due to the inhomogeneous Zn nucleation and severe HER in traditional electrolyte (Fig. 5a).42 Moreover, during the stripping process, the partial dissolution of Zn could be observed (Fig. 5b),190 which leads to the formation of “dead Zn” and consequently low coulombic efficiency (CE).191,192 A dendrite-free ZMA can be achieved after the application of protection strategies.134,193–195 Through the in situ OM observation, pits are formed after the first stripping process. These pits exacerbate the subsequent growth of dendrites. In contrast, pre-deposited ZMA exhibits a more uniform morphology in subsequent cycles.196
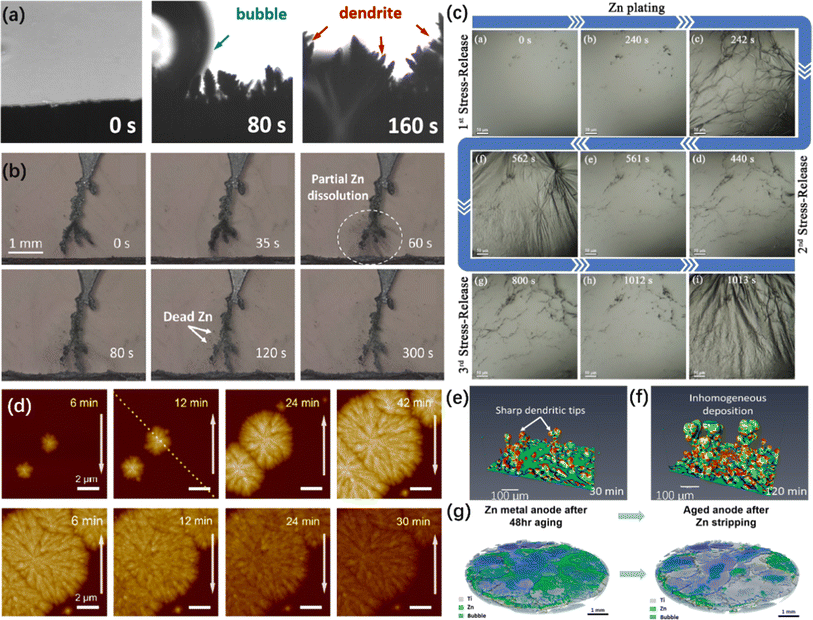 |
| Fig. 5
In situ visualizing characterizations of ZMA. (a) In situ OM of the ZMAs in traditional electrolytes during the plating process.42 Copyright 2023, Royal Society of Chemistry. (b) The dissolution of Zn dendrites and the production of dead Zn under the subsequent stripping process.190 Copyright 2023, American Chemical Society. (c) The stress-generation-release phenomena on the anode at different plating stages.197 Copyright 2022, Wiley. (d) In situ AFM images of nucleation and early growth and dissolution of Zn.204 Copyright 2021, American Chemical Society. (e and f) Selection of region of interest (ROI) demonstrating the distribution of the mean curvature of the Zn dendrite as a function of time at (e) 30 and (f) 120 min.190 Copyright 2023, American Chemical Society. (g) 3D rendered images from the anode of a pressured Zn/Ti battery scanned in situ X-CT.212 Copyright 2023, Elsevier. | |
Except for the above cross-section observation, the surface-section perspective is also extensively utilized to observe the interfacial flatness and nucleation sites.192 For instance, a stress-generation-release phenomena on the coating layers during the Zn plating process was directly observed, as shown in Fig. 5c. In detail, a large number of Zn grains emerge on the ZMA surface and soon vanish in a flash. As the plating time increases, significant fluctuations and wrinkles appear due to the huge stress exceeding the threshold coating layer strain. Immediately afterwards, the ZMA surface gradually recovers to a flat state due to the groove deposition model.197
In situ OM is also applied to reveal the effects of current density on Zn plating. Generally, higher current density is supposed to result in more Zn dendrite formation on the ZMA surface,198 which is considered as a guidance to control the plating behaviors and crystal orientation of Zn deposition by tuning the current densities.199 However, Yu et al. clearly demonstrated that the in situ OM technique used for observing ZMA is not a sufficiently reliable characterization for describing the HER and dendrite growth process due to the significant randomness of various deposition morphologies in different regions.27
4.1.2.
In situ atomic force microscopy (AFM).
In situ AFM is capable of providing surface roughness, Young's modulus, and 3D surface configuration images and is widely used in the field of energy storage devices.200–202 For AZIBs, the plating and stripping processes of Zn could be monitored by in situ AFM.203Fig. 5d illustrates the surface morphology evolution on ZMA within a single Zn plating/stripping process. During the plating process, two nascent nuclei emerge and then gradually turn into micron-sized particles through radial expansion. During the stripping process, Zn dendrites are homogeneously dissolved identified by a color change from dark yellow to light yellow.204 Besides, AFM images are used to monitor Zn dendrite formation at different current densities and depth of discharge. At a very early stage, the size of the dendrite increases while a higher current density is applied. Besides, the formation of Zn dendrites is accelerated with a higher depth of discharge.135
In addition, AFM is also used to support the effects of surface modification. For example, Chen et al. polished the Zn foil using sand papers with a proper grit size, which demonstrate a stable cycling performance. AFM images showed that Zn deposition mainly happens in the concaves generated by sand papers and proves that smaller grit size contributes to flatter anode surface, i.e., dendrite free surface.192 Zhang et al. performed in situ AFM to reveal the plating patterns in different electrolytes. As a result, a dot-distributed Zn nucleation mechanism was observed in traditional ZnSO4 electrolyte. However, an anion-type water-free Zn2+ solvation structure electrolyte leads to plane-distributed Zn nucleation.83 Keist et al. investigated the evolution of Zn deposition morphology using in situ AFM and concluded that uniformly distributed Zn nucleus gradually become larger and thicker in a layer-by-layer growth mode, leading to the smooth surface and improved cycling performance in an imidazolium-based ionic liquid electrolyte.155,205 Moreover, Wang et al. presented that a smoother hexagonal surface and pyramid-like structures with sharp edges were observed in a concentrated electrolyte through in situ AFM images, whereas a rough and undulating topography was observed in a dilute electrolyte.206 Despite the use of in situ AFM for the direct observation of the surface topology of ZMA during the first plating stage, using in situ AFM to monitor the formation of SEI layers or EDL remains underexplored.
4.1.3.
In situ X-ray computed tomography (X-CT).
X-ray computed tomography (X-CT)207,208 has been employed to achieve the 4D observation of the Zn plating/stripping process. As shown in Fig. 5e and f, after a statistical quantification of the mean curvature, the 3D rendering image for the entire domain can be drawn, and different colors represent different compositions.190,208 Therefore, X-CT is suitable for studying the 3D structure of ZMA, such as the surface morphology of the cycled Zn@3DCu3 anode209 and the spatial distribution of ZnO in porous ZMA.210 Meanwhile, Pu et al. employed the in situ X-CT technique to demonstrate plated Zn and Zn substrates without disassembling the battery. The obtained results further indicate that the epitaxial Zn does not possess interior defects after the plating.211 They also demonstrated that the gas bubbles generated on the Zn surface can physically deactivate Zn in the following plating/stripping processes, which is monitored by the in situ X-CT technique (Fig. 5g).212 In addition, the X-CT technique can verify the detailed and homogeneous Zn plating behavior after constructing a protective SEI layer or employing additives.213 For instance, Zhang et al. demonstrated that the homogeneous Zn plating behavior can be achieved on the hydrophobic–zincophilic SEI layer because a relatively flat surface has been detected by in situ X-CT,214 while extensive “dead Zn” was shown in in situ X-CT images when using additive-free electrolyte.215 Although the above mentioned examples demonstrate the potentials of the X-CT technique in promoting a deep understanding of the protective mechanism, several challenges still need to be overcome, including expanding the scanning range and improving the accuracy and resolution of the detected area.216,217
4.1.4.
In situ electron microscopy.
To monitor the local chemical reactions on the interface with higher resolution, electron microscopy, such as in situ scanning electrochemical microscopy (SECM) and in situ transmission electron microscopy (TEM), is employed. As shown in Fig. 6a, vertical oriented patterns are observed on the polished ZMA through in situ SECM. In contrast, an SEI layer can guide the horizontal accumulation of thin Zn sheets at the early stage of Zn deposition to suppress the growth of dendrites.218 As indicated by in situ TEM, particles and needle-like precipitates are formed on the Pt electrode during the plating process (Fig. 6b), occurring before 4 s and after 7 s, respectively. The dendritic branch angle is approximately 60°. During the stripping process (Fig. 6c), the particles near the Pt surface is more likely to be stripped away than the dendrite tips and the detached Zn dendrite is a potential risk for “dead Zn”.219 Very recently, an electrostatic shielding effect mechanism has been further confirmed via in situ liquid-cell TEM, which is close to the practical AZIBs batteries.220 In this case, as shown in Fig. 6d, LiCl will induce preferential secondary nucleation on the previously deposited Zn flakes along the (002) plane, resulting in the formation of stacked zinc flakes.
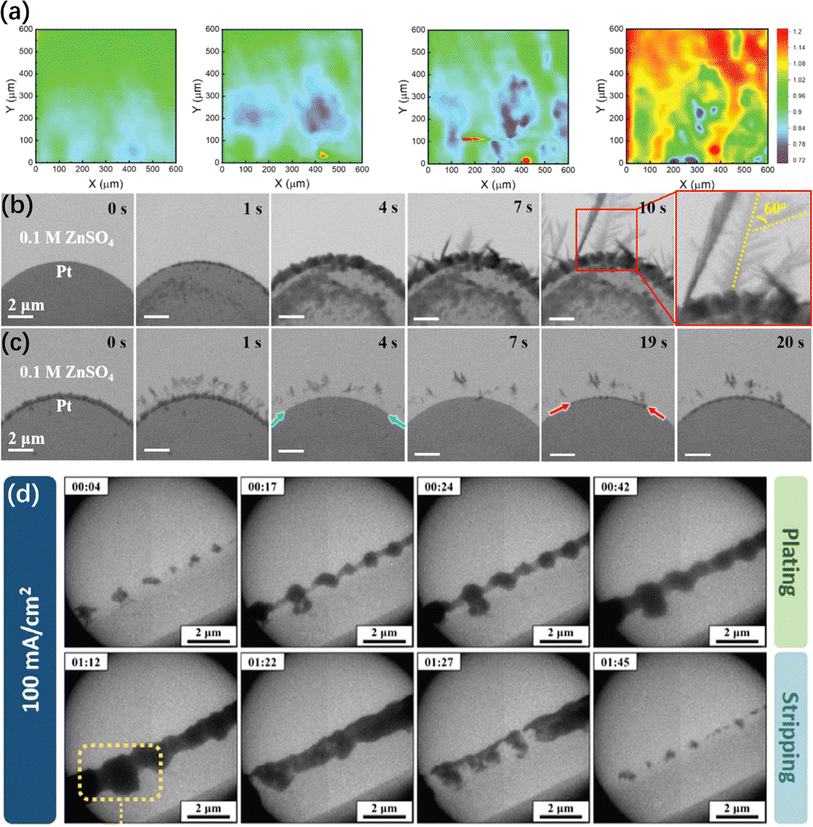 |
| Fig. 6 Other in situ electron microscopy characterizations of ZMA. (a) In situ SECM feedback imaging of Zn electrodeposition process on freshly polished Zn substrates.218 Copyright 2023, Wiley. (b and c) In situ TEM images of the zinc plating/stripping process on Pt electrode.219 Copyright 2021, Elsevier. (d) In situ electrochemical LC-TEM imaging of Zn plating/stripping with LiCl additive.220 Copyright 2024, Wiley. | |
4.2.
In situ spectroscopy/mass spectrometry characterizations
4.2.1.
In situ Raman spectroscopy.
In contrast to the visualization research discussed in the above section, in situ Raman spectroscopy can provide a deeper understanding of the vibration information of molecules. So far, in situ Raman spectroscopy has been widely used to analyze the corrosion behavior of ZMA.221,222 For instance, the gradually emerging O–H stretching vibration of ZHS at 3633 cm−1 indicates the existence of irreversible corrosion reaction.223 The spectrum intensity of the SO42− peak at 980 cm−1 becomes weakened during the plating process (Fig. 7a), suggesting that SO42− was consumed due to ZHS formation.224 Moreover, the side reaction HER generated more OH−, which further accelerates the formation of Zn(OH)42− species, hindering the subsequent transport of Zn2+. Therefore, a Raman peak located at 465 cm−1 in Fig. 7b, assigned to the Zn(OH)42− species, could be observed in the traditional electrolyte.225 The corrosion behavior can be suppressed by modifying ZMA via an oriented freezing process or thermal infusion strategy226,227 because the Zn(OH)42− peak at 465 cm−1 has disappeared, as shown in Fig. 7c.
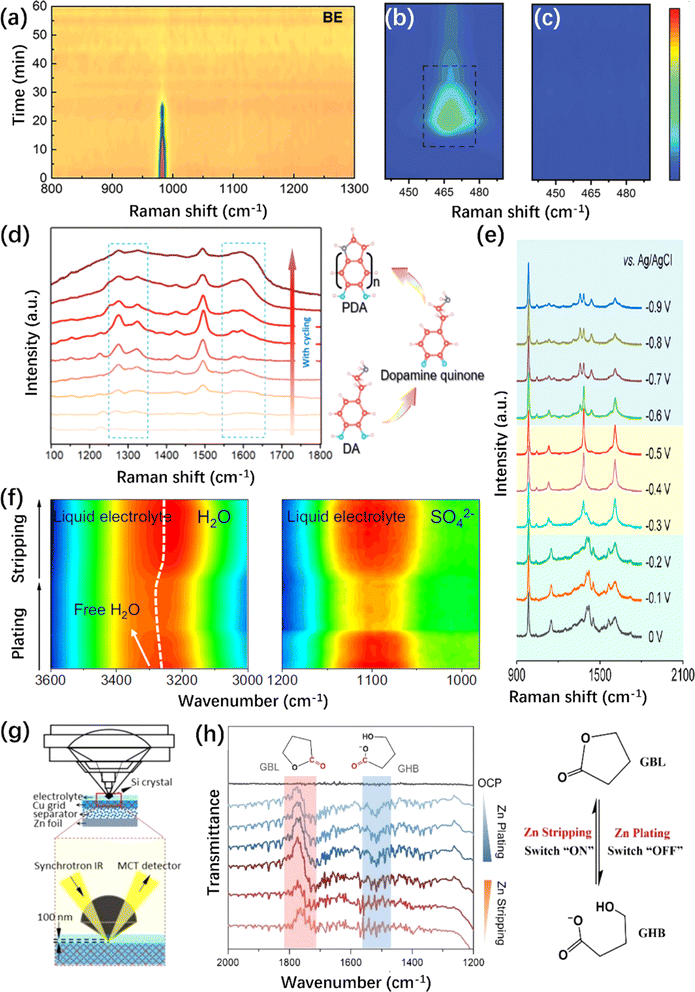 |
| Fig. 7
In situ Raman/FTIR spectroscopic characterizations of ZMA. (a) In situ Raman spectrum intensity map of (a) SO42− anion in pristine electrolyte.224 Copyright 2022, Wiley. (b and c) In situ Raman spectrum of Zn(OH)42− species on (b) Cu@Zn and (c) MGA@Zn anode.227 Copyright 2022, Wiley. (d) In situ Raman spectra of DA additive and its representative polymerization procedure for PDA.231 Copyright 2021, Royal Society of Chemistry. (e) In situ Raman spectra of the PI-COF electrode during the charging process.232 Copyright 2020, American Chemical Society. (f) In situ ATR-FTIR spectra of the O–H band and SO42− anion vibration.237 Copyright 2023, Springer Nature. (g) Illustration of piezo-controlled macro-ATR monitoring of the interfacial area of the electrode.238 Copyright 2023, Wiley. (h) In situ ATR-FTIR spectra of conformation changes between GBL and GHB.109 Copyright 2023, Wiley. | |
Referring to the complexity of the EDL or the SEI layer on the ZMA, in situ Raman is an effective tool to monitor the in situ formation of the EDL and SEI layer.228 For instance, with the increase in the deposition time, the vibration peaks of the 3-(1-methylimidazole)propanesulfonate (ImS) additive gradually increased and would not change upon cycling; it is supposed that ImS can adsorb on ZMA to form EDL without undergoing chemical decomposition.229 In addition, the gradual polymerization of the monomers to form the corresponding polymer is recorded by in situ Raman during cycling.230 As shown in Fig. 7d, the intermediates of in situ polymerization are detected, which would lead to the successful construction of a robust polydopamine layer on the ZMA eventually. This in situ polymeric SEI possesses abundant functional groups and outstanding hydrophilicity for regulating Zn nucleation to achieve dendrite-free Zn plating.231
In the case of artificially-constructed ZMAs, in situ Raman spectroscopy also plays a significant role in exploring the mechanism of Zn2+ storage. For instance, the vibration mode of a 2D polyarylimide covalent organic framework (PI–COF) indicates its reversible conversion during cycling (Fig. 7e).232 Furthermore, in situ Raman can be used to identify the preferential Zn2+ nucleation sites, such as the diacetylene bonds in the graphdiyne nanowalls233 and the O and OH terminal on the Ti3C2Tx MXene.234
4.2.2.
In situ Fourier transform infrared spectroscopy (FTIR).
In situ FTIR techniques can also support the study of ZMA by identifying the formation of new species and monitoring the decomposition of the electrolyte. Generally, the attenuated total reflection (ATR) configuration is used in in situ FTIR experiments, especially in battery systems. Amaral et al. have summarized a plenty of in situ FTIR configurations and their corresponding significant advancements.235 As for the ZMA–electrolyte interface, in situ FTIR has been widely employed to monitor molecular dynamics during plating/stripping, particularly the migration of Zn2+ and the desolvation process.91,236 As shown in Fig. 7f, during the plating process, the peak of the O–H band from the H2O molecule exhibits a blueshift, and the peak intensity of SO42− becomes weakened. These could be explained as a repulsion between H2O molecules and SO42− anions resulting from the desolvation of Zn2+.237 Liu et al. employed in situ synchrotron FTIR characterization to monitor the effects of electrolyte additives on the hydrogen bond network, and the corresponding configurations are illustrated in Fig. 7g.238 With the introduction of the additive, a redshift of O–H is monitored together with increased peak intensity, which means a new hydrogen bond network between H2O and additives is established and the general water derived hydrogen bond network is destroyed.39,239 Moreover, in situ FTIR enables the direct observation of the reduction behavior of additive molecules, such as dimethyl methylphosphonate (DMMP) and N,N-dimethylformamidium trifluoromethanesulfonate (DOTf).238,239 Zhang et al. reported γ-butyrolactone (GBL) as the electrolyte additive to stabilize the pH value at the ZMA–electrolyte interface.109 ATR-FTIR spectroscopy was used to monitor the transformation between GBL and γ-hydroxybutyrate (GHB) to unveil the mechanism for the adjustable pH in the battery system. Specifically, the reversible C
O vibration during Zn plating/stripping has been identified, as shown in Fig. 7h.
4.2.3.
In situ X-ray diffraction (XRD).
In situ XRD is mainly used to investigate the phase transformation of active materials.240,241 More details of the advanced in situ XRD characterizations about the cathodes for AZIBs are discussed in ref. 242–245. As for ZMA, in situ XRD technique can identify byproducts formation and measure crystal plane changes during the plating/stripping process. For instance, ZHS is a main byproduct while using ZnSO4 based electrolyte and can be easily identified in the XRD data. Moreover, the characteristic peaks of ZHS are irreversible (Fig. 8a).223,246 Secondly, the oriented deposition behavior of Zn is also a hot topic, which could be monitored by collecting the corresponding relative texture coefficients (RTCs) values of all the crystal planes by in situ XRD. For example, the preferred oriented Zn deposition on ZMA could be identified by the XRD result as the (002) peak gradually becomes stronger. Generally, the preferred Zn(002) deposition means a horizontal stacked Zn plate on ZMA, ensuring a smooth ZMA during cycling (Fig. 8b).234,247,248 Furthermore, in situ XRD can be used to study the evolution of ZMA structure and its reversibility, contributing to the analysis of “dead Zn” formation.227,249
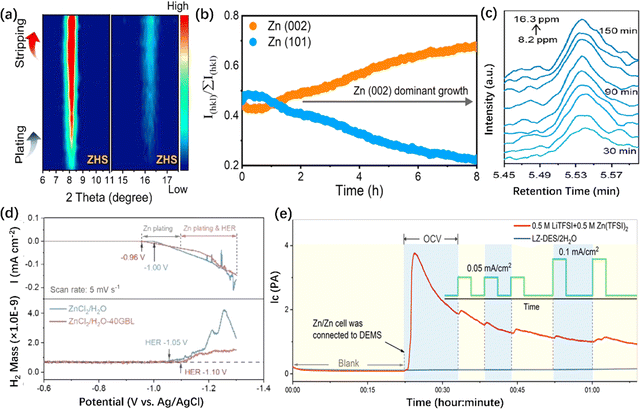 |
| Fig. 8
In situ X-ray diffraction/mass spectrometry characterizations of ZMA. (a) In situ XRD pattern of the ZMA without/with the HZTO protective layer.223 Copyright 2023, Wiley. (b) In situ XRD pattern and corresponding RTCs of the MXene array ZMA.234 Copyright 2023, Springer Nature. (c) In situ EC-GC of pristine ZMA during the plating/stripping process.250 Copyright 2023 American Chemical Society. (d) In situ DEMS characterizations of the electrolyte without/with GBL additive.109 Copyright 2023, Wiley. (e) In situ DEMS characterization of the electrolyte with 0.5 M LiTFSI + 0.5 M Zn(TFSI)2 and LZ-DES/2H2O electrolyte.252 Copyright 2019, Elsevier. | |
4.2.4.
In situ differential electrochemical mass spectrometry (DEMS) and gas chromatography (GC).
Generally, the amount of H2 produced by the modified or protected ZMA is much less than that produced by pristine ZMA, known as HER inhibition. Bubble formation is hardly seen in the modified system, but it does not mean that the HER is completely eliminated. Therefore, in situ electrochemical gas chromatography (EC-GC) or Differential Electrochemical Mass Spectrometry (DEMS) are employed. For EC-GC, the amount of gas production can be quantified over a specific time period (typically 15 minutes), as shown in Fig. 8c.74,103,250 Based on DEMS, continuous cumulative gas production can be detected.160,251 Furthermore, the combination of linear sweep voltammetry and DEMS can accurately distinguish the potentials for Zn plating and HER (Fig. 8d).109Fig. 8e demonstrates the H2 evolution during the open-circuit voltage (OCV) state.252–254 Also, the presence of plenty fluctuation peaks indicates the HER and released bubbles.255 Briefly, these in situ EC-GC or DEMS methods are primarily utilized for evaluating the H2 evolution rate and electrolyte stability.256
4.3.
In situ physicochemical characterizations
Intrinsic properties, such as impedance, mass, and electrolyte conditions, are also crucial factors for AZIBs. These intrinsic properties affect the electrochemical performance, interface reactions, and electrolyte stability. Investigating the changes in intrinsic properties holds great significance in improving the protection strategies, i.e., more stable ZMA–electrolyte interface, less side reaction, and higher safety.
4.3.1.
In situ electrochemical impedance spectroscopy (EIS).
Electrochemical impedance spectroscopy (EIS) is an essential method to study reaction kinetics at the ZMA-electrolyte interface and the evolution of the SEI layer.257,258 As shown in Fig. 9a, the in situ EIS results demonstrate that the interface resistance of the pristine electrolyte gradually increases. On the other hand, the interface impedance in taurine electrolyte is more stable even after a drastic reduction.14,259 Such a result reflects the fast interface transport kinetics, originating from the elimination of the generation of ZSH.260–262 In detail, during the plating process, the interface impedance decreases slightly, indicating that the newly deposited Zn nanoarrays expose more active sites.263 For a more comprehensive analysis, Dai et al. recorded the in situ EIS spectra and the performed distribution of relaxation time (DRT) analysis (Fig. 9b).49 The interfacial impedance (P3–P5) in the ZnSO4 electrolyte increases significantly after the first cycle of plating/stripping, while that in the Ni2+–ZnSO4 electrolyte remains relatively constant, corresponding to a significant decrease in the ZHS. In addition, in situ EIS can provide information about the surface roughness and “soft shorts” of ZMA during cycling.264,265
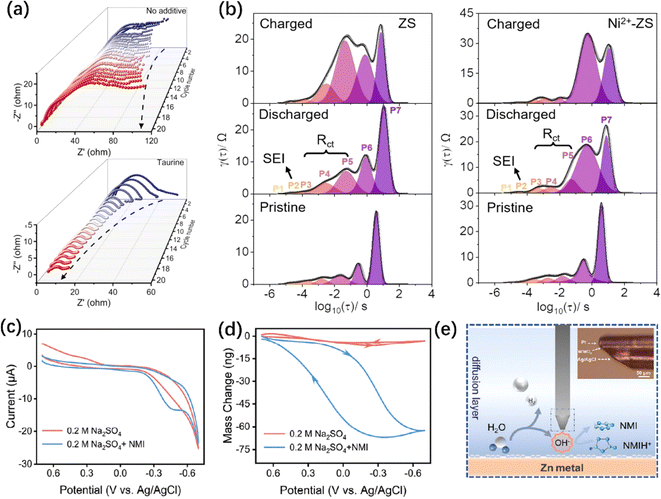 |
| Fig. 9
In situ physicochemical characterizations of ZMA. (a) In situ EIS of symmetrical batteries without/with taurine additive electrolyte.14 Copyright 2023, Wiley. (b) The distribution of relaxation times (DRT) plot of the in situ EIS data in ZS and Ni2+-ZS electrolyte.49 Copyright 2023, Wiley. (c and d) Cyclic voltammograms (CV) curves (c) and corresponding mass change (d) obtained from EQCM test.107 Copyright 2023, Wiley. (e) Diagram of UME detecting pH changes (inset is a microscopy image of pH UME).107 Copyright 2023, Wiley. | |
4.3.2.
In situ electrochemical quartz crystal microbalance (EQCM).
The electrochemical quartz crystal microbalance (EQCM), as a gravimetric analysis tool, establishes a relationship between the mass change and charge transfer of the active materials. Consequently, it can analyze the specific adsorption of additive, in-depth plating/stripping mechanisms, and formation of SEI.266,267 Zhang et al. carried out EQCM to assess the absorption behavior of N-methylimidazole (NMI) additive on ZMA (Fig. 9c and d). There is a significant mass change in the electrolyte containing NMI additive when the potential changes, which is attributed to the adsorption of NMIH+ on the interface at low potential and the desorption of NMIH+ at high potential.107 In addition, EQCM records a negligible mass change resulting from the adsorption and desorption of H atoms and H2O in the pristine electrolyte.268
The plating/stripping process of Zn2+ is generally believed as a two-electron reaction. However, Agrisuelas et al. conducted EQCM studies and characterized the presence of the Zn+ intermediate, suggesting that the plating/stripping of Zn2+ undergoes two consecutive single-electron transfer steps.269 In addition, EQCM is used to identify the side reactions such as the formation of byproduct. The mass change of ZMA is detected by EQCM during immersion in electrolyte with/without dissolved oxygen. Much faster mass increment is recorded due to the growth of byproducts induced by dissolved oxygen during the first resting state.270 Another example is the detection of SEI formation. Significant unbalanced data of coulombic loss and gravimetric mass change is observed in the non-aqueous Zn(TFSI)2 electrolyte due to the SEI formation process in the first three cycles. However, in the aqueous electrolyte, no significant loss of charge occurs, resulting in nearly 100% CE.271
4.3.3.
In situ proton concentration (pH).
Moreover, proton concentration in the electrolyte plays an important role in AZIBs, showing up as the pH value at the ZMA–electrolyte interface. Generally, because Zn2+ plating/stripping and HER process share an overlap potential range, which means that within the battery operation voltage range, HER is inevitably triggered.272,273 Symmetric batteries with conventional electrolyte suffer from a gradually increased pH environment, indicating the continuously occurring HER reaction.101,106,112,274 Therefore, researchers applied an electrolyte additive to maintain the stability of the pH value, which has been described in Section 2.5.14,101,275 Recently, Zhang et al.107 used a ternary pH ultra-microelectrode (UME, Fig. 9e) to detect the pH value by controlling the distance between the probe and ZMA to distinguish the pH evolution between the bulk and diffusion layers. The results indicate that the OH− species produced by HER will not diffuse into the bulk electrolyte because of the strong interactions between OH− and Zn2+ at the interface. However, there is no generally accepted suitable pH values for AZIBs because both low pH (2.8)102 and high pH (5.14)104 have been reported to favor ZMA stability.
4.4. Minority and advanced characterizations
Apart from the commonly used in situ characterizations mentioned above, some relatively rare but innovative strategies and characterizations have been used in AZIBs. As shown in Fig. 10a, the generation of bubble footprints can be observed on the surface of cycled ZMA, while in situ GC collects the bubbles and separates the hydrogen gas for analyzing whether the HER reaction is inhibited.276 The results indicate that uneven zinc deposition is more likely to occur around the bubbles, leading to the easier formation of dendrites. Moreover, a novel ultrasonic-guided wave technique was introduced (Fig. 10b) by Zhang et al. With the beginning of Zn plating, the velocity and attenuation of ultrasound change. These changes are related to the formation of dendritic structures on the ZMA–electrolyte interface. As dendrites grow, the attenuation of ultrasound increases, and the velocity decreases. The reason for its attenuation is that Zn dendrites increase the scattering and absorption of energy. Conversely, during the stripping process, the wave velocity increases.277
 |
| Fig. 10 Minority and advanced characterizations of ZMA. (a) Schematic of the configuration used for observing H2 evolution in situ.276 Copyright 2024, Springer Nature. (b) Schematic of a transducer-waveguide assembly and ultrasonic signals on a waveguide before (blue) and after (red) the cycling.277 Copyright 2022, Elsevier. (c) Schematics of a chromatic battery with a short circuit warning function.279 Copyright 2018, Royal Society of Chemistry. (d) Scheme illustrating the process of smartphone multispectral imaging reconstruction and usage for in situ energy storage monitoring.280 Copyright 2023, Wiley. | |
In addition, significant advancements and applications have been achieved in the integrated characterizations of full-battery. For instance, Zhang et al. reported a flexible pressure sensor composed of a solid-state ZIB, which can be used for accurate and continuous human pulse and limb movement detection. This ZIB-type pressure sensor can be used as both an energy storage device and an excellent pressure sensor, which effectively convert mechanical signals into electrical signals and output a stable high/low frequency response signal depending on the various interface resistance and isolation layer resistance.278 Similarly, a flexible and electrochromic AZIBs has been reported by Wang et al. Once a short circuit occurs in the battery, the voltage rapidly drops to 0 V, and the polypyrrole (PPy, as cathode) layer quickly transitions from the oxidized state to the reduced state, causing the battery's color to change from black (normal operation state) to bright yellow (short circuit state).279 Sun et al. proposed a smartphone computing multispectral imaging reconstruction (MSIRC) strategy to unlock the ion storage behaviors in cathode materials. As indicated in Fig. 10d, by leveraging the relative reflectance values at specific wavelengths, a “layer to layer” Zn2+ storage mechanism and excessive Zn2+ insertion was identified.280 Researchers used a smartphone to perform the in situ analysis of aqueous batteries through a transparent monitoring window. The authors extracted the optical characteristics of the materials using computational reconstruction methods, thereby enabling the monitoring of the chemical ion storage and real-time capacity changes of the materials. Most recently, artificial intelligence has become more and more popular. Further investigations may take the advantage of this powerful tool to guide the research design, help understand complex mechanisms and kinetics, and accelerate the acquisition of experimental and computational data.
5. Summary and outlook
In conclusion, AZIBs possess the advantages of high safety, low cost, and eco-friendliness and are one of the most promising energy storage and conversion devices for the applications in smart grid. Zn is considered as the most ideal anode material but encounters challenges such as Zn dendrites, HER, and corrosion. This review summarizes the theoretical simulations and multiscale in situ characterization for understanding the protective mechanism of the ZMA–electrolyte interface. Nonetheless, researches on AZIBs are still at its early stages, and there are many critical scientific issues and underlying mechanisms waiting to be disclosed, as detailed below.
(i) The stripping mechanisms receive less attention, despite the fact that the stripping process is the first step of ZMA in a full battery.184,281 As shown in Fig. 11a, the uneven stripping process leads to the formation of voids and/or cracks on ZMA, exposing highly active surface. The volume changes of ZMA after repeated cycles lead to the formation of interspace/crevices between the modified layer and ZMA. The modified layer is thus easier to separate from the ZMA and loses its protective effect.
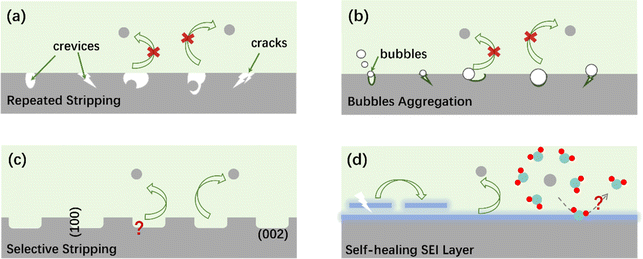 |
| Fig. 11 Scientific issues and prospects for the plating/stripping process of ZMAs. | |
(ii) Inhibiting the bubble formation is challenging since it is difficult to fully control the HER. As shown in Fig. 11b, the gradual aggregation of bubbles physically isolates some Zn with the electrolyte, leading to the capacity attenuation of ZMA. However, this issue is normally neglected since excessive Zn is applied.
(iii) Similar to the preferred oriented Zn plating, is it possible to achieve selective stripping processes? For instance, selectively stripping Zn(101) and exposing more favorable Zn(002) (Fig. 11c) would in turn promote the subsequent plating process along the (002) crystal surface.
(iv) Is the EDL completely covered with adsorption-type additives? If not, is there still a significant amount of solvated H2O that can directly contact ZMA? Therefore, it is crucial to distinguish the state of local environment from the near interface region to the bulk electrolyte.
(v) It is challenging to fabricate a functional SEI with high performance. For instance, when constructing the SEI layer, it is necessary to consider its thickness, mechanical strength, and self-healing ability. As shown in Fig. 11d, excellent self-healing ability is beneficial for extending the battery life. Moreover, it is important to investigate and understand how the composition and microstructure of SEI influence the desolvation and diffusion coefficient of Zn2+.
These issues severely affect the development of AZIBs in practical applications. It is important for researchers to understand the relationships among crystal structure, material composition, reaction mechanism, reaction kinetics, and electrochemical performance through advanced tools such as theoretical simulations and in situ characterizations mentioned in this review. Besides, when it comes to in situ characterizations, researchers need to pay more attention to the reliability and validity of the required data and quality for practical applications.
(i) Developing and integrating a variety of in situ characterizations that can operate closer to actual operating conditions are essential for a more accurate understanding of the dynamic changes at the ZMA–electrolyte interface.
(ii) Improving the temporal and spatial resolution of in situ characterizations is crucial to rapidly capture the electrochemical processes occurring and subtle structural changes, which are essential for understanding the operation mechanisms and optimizing the performance of AZIBs.
Author contributions
Z. L. conceptualized and reviewed the articles and drafted the manuscript. X. Z. and Z. L. surveyed the relevant literature and analyzed the table data. Y. H. and Z. H. revised and provided general oversight. All the authors have approved the final version of the manuscript.
Conflicts of interest
The authors declare no conflict of interest.
Acknowledgements
This work is supported by the National Natural Science Foundation of China (22209116), Ministry of Science and Technology of the People's Republic of China (2022YFB2402300), Guangdong Provincial Natural Science Foundation of China (21825302), and Shenzhen Science and Technology Program (KQTD20221101093605019). The authors appreciate the support from the Guangdong Provincial Key Laboratory of New Energy Materials Service Safety.
References
- C. Xu, B. Li, H. Du and F. Kang, Angew. Chem., Int. Ed., 2012, 51, 933–935 CrossRef CAS PubMed
.
- X. Li, L. Wang, Y. Fu, H. Dang, D. Wang and F. Ran, Nano Energy, 2023, 116, 108858 CrossRef CAS
.
- H. Chen, X. Li, K. Fang, H. Wang, J. Ning and Y. Hu, Adv. Energy Mater., 2023, 13, 2302187 CrossRef CAS
.
- D. Wang, Q. Li, Y. Zhao, H. Hong, H. Li, Z. Huang, G. Liang, Q. Yang and C. Zhi, Adv. Energy Mater., 2022, 12, 2102707 CrossRef CAS
.
- W. Du, E. H. Ang, Y. Yang, Y. Zhang, M. Ye and C. C. Li, Energy Environ. Sci., 2020, 13, 333–336 RSC
.
- C. Li, S. Jin, L. A. Archer and L. F. Nazar, Joule, 2022, 6, 1733–1738 CrossRef
.
- Z. Yi, G. Chen, F. Hou, L. Wang and J. Liang, Adv. Energy Mater., 2021, 11, 2003065 CrossRef CAS
.
- J. Yang, B. Yin, Y. Sun, H. Pan, W. Sun, B. Jia, S. Zhang and T. Ma, Nano-Micro Lett., 2022, 14, 42 CrossRef CAS PubMed
.
- G. Zhang, X. Zhang, H. Liu, J. Li, Y. Chen and H. Duan, Adv. Energy Mater., 2021, 11, 2003927 CrossRef CAS
.
- X. Lu, C. Zhao, A. Chen, Z. Guo, N. Liu, L. Fan, J. Sun and N. Zhang, Chem. Eng. J., 2023, 451, 138772 CrossRef CAS
.
- S. Chen, J. Chen, X. Liao, Y. Li, W. Wang, R. Huang, T. Zhao, S. Yan, Z. Yan, F. Cheng and H. Wang, ACS Energy Lett., 2022, 7, 4028–4035 CrossRef CAS
.
- Z. Cai, J. Wang and Y. Sun, eScience, 2023, 3, 100093 CrossRef
.
- J. Cao, D. Zhang, X. Zhang, Z. Zeng, J. Qin and Y. Huang, Energy Environ. Sci., 2022, 15, 499–528 RSC
.
- K. Ouyang, S. Chen, W. Ling, M. Cui, Q. Ma, K. Zhang, P. Zhang and Y. Huang, Angew. Chem., Int. Ed., 2023, 62, e202311988 CrossRef CAS PubMed
.
- L. Han, Y. Guo, F. Ning, X. Liu, J. Yi, Q. Luo, B. Qu, J. Yue, Y. Lu and Q. Li, Adv. Mater., 2023, 36, 2308086 CrossRef PubMed
.
- M. Wang, Y. Meng, K. Li, T. Ahmad, N. Chen, Y. Xu, J. Sun, M. Chuai, X. Zheng, Y. Yuan, C. Shen, Z. Zhang and W. Chen, eScience, 2022, 2, 509–517 CrossRef
.
- Y. Li, X. Peng, X. Li, H. Duan, S. Xie, L. Dong and F. Kang, Adv. Mater., 2023, 35, 202300019 Search PubMed
.
- X. Liu, Y. Fang, P. Liang, J. Xu, B. Xing, K. Zhu, Y. Liu, J. Zhang and J. Yi, Chin. Chem. Lett., 2021, 32, 2899–2903 CrossRef CAS
.
- C. Yang, P. Woottapanit, J. Cao, Y. Yue, D. Zhang, J. Yi, Z. Zeng, X. Zhang, J. Qin and Y. Wang, J. Mater. Chem. A, 2023, 11, 24902 RSC
.
- X. He, X. Kong and L. Wen, Nano Res. Energy, 2024, 3, e9120100 CrossRef
.
- C. Yang, X. Zhang, J. Cao, D. Zhang, P. Kidkhunthod, S. Wannapaiboon and J. Qin, ACS Appl. Mater. Interfaces, 2023, 15, 26718–26727 CrossRef CAS PubMed
.
- D. Dong, T. Wang, Y. Sun, J. Fan and Y. Lu, Nat. Sustain., 2023, 6, 1474–1484 CrossRef
.
- P. Woottapanit, C. Yang, J. Cao, W. Limphirat, S. S. n. ayuttaya, X. Zhang, P. Wangyao and J. Qin, ACS Appl. Energy Mater., 2023, 6, 10578–10584 CrossRef CAS
.
- D. Xiong, L. Yang, Z. Cao, F. Li, W. Deng, J. Hu, H. Hou, G. Zou and X. Ji, Adv. Funct. Mater., 2023, 33, 2301530 CrossRef CAS
.
- Y. Li, Z. Yu, J. Huang, Y. Wang and Y. Xia, Angew. Chem., Int. Ed., 2023, 62, e202309957 CrossRef CAS
.
- Y. Zeng, D. Luan and X. W. D. Lou, Chem, 2023, 9, 1118–1146 CAS
.
- X. Yu, Z. Li, X. Wu, H. Zhang, Q. Zhao, H. Liang, H. Wang, D. Chao, F. Wang, Y. Qiao, H. Zhou and S. Sun, Joule, 2023, 7, 1145–1175 CrossRef CAS
.
- Y. Liang, M. Qiu, P. Sun and W. Mai, Adv. Funct. Mater., 2023, 17, 2304878 CrossRef
.
- X. Feng, P. Li, J. Yin, Z. Gan, Y. Gao, M. Li, Y. Cheng, X. Xu, Y. Su and S. Ding, ACS Energy Lett., 2023, 8, 1192–1200 CrossRef CAS
.
- X. Yang, W. Li, Z. Chen, M. Tian, J. Peng, J. Luo, Y. Su, Y. Zou, G. Weng, Y. Shao, S. Dou and J. Sun, Angew. Chem., Int. Ed., 2023, 62, e202218545 Search PubMed
.
- A. Naveed, H. Yang, J. Yang, Y. Nuli and J. Wang, Angew. Chem., Int. Ed., 2019, 58, 2760–2764 CrossRef CAS
.
- Z. Shen, J. Mao, G. Yu, W. Zhang, S. Mao, W. Zhong, H. Cheng, J. Guo, J. Zhang and Y. Lu, Angew. Chem., Int. Ed., 2023, 62, e202218452 CrossRef CAS
.
- W. Zhang, F. Guo, H. Mi, Z. S. Wu, C. Ji, C. Yang and J. Qiu, Adv. Energy Mater., 2022, 12, 2202219 CrossRef CAS
.
- J. Cong, X. Shen, Z. Wen, X. Wang, L. Peng, J. Zeng and J. Zhao, Energy Storage Mater., 2021, 35, 586–594 CrossRef
.
- K. Wu, J. Cui, J. Yi, X. Liu, F. Ning, Y. Liu and J. Zhang, ACS Appl. Mater. Interfaces, 2022, 14, 34612–34619 CrossRef CAS PubMed
.
- L. Li, W. Li, X. Wang, X. Zou, S. Zheng, Z. Liu, Q. Li, Q. Xia and F. Yan, Angew. Chem., Int. Ed., 2022, 61, e202212512 CrossRef CAS PubMed
.
- H. Qiu, X. Du, J. Zhao, Y. Wang, J. Ju, Z. Chen, Z. Hu, D. Yan, X. Zhou and G. Cui, Nat. Commun., 2019, 10, 5374 CrossRef PubMed
.
- D. Han, T. Sun, R. Zhang, W. Zhang, T. Ma, H. Du, Q. Wang, D. He, S. Zheng and Z. Tao, Adv. Funct. Mater., 2022, 32, 2209065 CrossRef CAS
.
- M. Li, X. Wang, J. Hu, J. Zhu, C. Niu, H. Zhang, C. Li, B. Wu, C. Han and L. Mai, Angew. Chem., Int. Ed., 2023, 62, e202215552 CrossRef CAS
.
- Z. Khan, D. Kumar and X. Crispin, Adv. Mater., 2023, 35, 2300369 CrossRef CAS
.
- H. Du, Y. Dong, Q. J. Li, R. Zhao, X. Qi, W. H. Kan, L. Suo, L. Qie, J. Li and Y. Huang, Adv. Mater., 2023, 35, 2210055 CrossRef CAS
.
- Z. Liu, J. Ma, X. Liu, H. Wu, D. Wu, B. Chen, P. Huang, Y. Huang, L. Wang, Z. Li and S. Chou, Chem. Sci., 2023, 14, 2114–2122 RSC
.
- J. Cui, Z. Li, A. Xu, J. Li and M. Shao, Small, 2021, 17, 2100722 CrossRef CAS
.
- Q. Zhang, J. Luan, L. Fu, S. Wu, Y. Tang, X. Ji and H. Wang, Angew. Chem., Int. Ed., 2019, 58, 15841–15847 CrossRef CAS
.
- H. Wang, H. Li, Y. Tang, Z. Xu, K. Wang, Q. Li, B. He, Y. Liu, M. Ge, S. Chen, T. Hao, G. Xing and Y. Zhang, Adv. Funct. Mater., 2022, 32, 2207898 CrossRef CAS
.
- K. Zhao, G. Fan, J. Liu, F. Liu, J. Li, X. Zhou, Y. Ni, M. Yu, Y. Zhang, H. Su, Q. Liu and F. Cheng, J. Am. Chem. Soc., 2022, 144, 11129–11137 CrossRef CAS
.
- Y. Li, P. Wu, W. Zhong, C. Xie, Y. Xie, Q. Zhang, D. Sun, Y. Tang and H. Wang, Energy Environ. Sci., 2021, 14, 5563–5571 RSC
.
- R. Zhao, H. Wang, H. Du, Y. Yang, Z. Gao, L. Qie and Y. Huang, Nat. Commun., 2022, 13, 3252 CrossRef CAS PubMed
.
- Y. Dai, C. Zhang, W. Zhang, L. Cui, C. Ye, X. Hong, J. Li, R. Chen, W. Zong, X. Gao, J. Zhu, P. Jiang, Q. An, D. Brett, I. P. Parkin, G. He and L. Mai, Angew. Chem., Int. Ed., 2023, 62, e202301192 CrossRef CAS
.
- F. Xie, H. Li, X. Wang, X. Zhi, D. Chao, K. Davey and S. Z. Qiao, Adv. Energy Mater., 2021, 11, 2003419 CrossRef CAS
.
- C. Zhao, Y. Zhang, J. Guo, Z. Guo, A. Chen, N. Liu, X. Lu, X. Zhang and N. Zhang, Batteries Supercaps, 2023, 6, e202200478 CrossRef CAS
.
- Y. Lin, Z. Mai, H. Liang, Y. Li, G. Yang and C. Wang, Energy Environ. Sci., 2023, 16, 687–697 RSC
.
- Q. Li, Y. Zhao, F. Mo, D. Wang, Q. Yang, Z. Huang, G. Liang, A. Chen and C. Zhi, EcoMat, 2020, 2, e12035 CrossRef CAS
.
- H. G. Yang, H. S. Cheng, Z. Q. Shi, Z. Jin, L. Gang, C. S. Sean and H. M. C. G. Lu, Nature, 2008, 453, 638–641 CrossRef CAS PubMed
.
- M. Zhou, S. Guo, J. Li, X. Luo, Z. Liu, T. Zhang, X. Cao, M. Long, B. Lu, A. Pan, G. Fang, J. Zhou and S. Liang, Adv. Mater., 2021, 33, e2100187 CrossRef
.
- J. Zheng, Q. Zhao, T. Tang, J. Yin, C. D. Quilty, G. D. Renderos, X. Liu, Y. Deng, L. Wang, D. C. Bock, C. Jaye, D. Zhang, E. S. Takeuchi, K. J. Takeuchi, A. C. Marschilok and L. A. Archer, Science, 2019, 366, 645–648 CrossRef CAS PubMed
.
- W. Yuan, X. Nie, G. Ma, M. Liu, Y. Wang, S. Shen and N. Zhang, Angew. Chem., Int. Ed., 2023, 62, e202218386 CrossRef CAS PubMed
.
- T. Wang, J. Sun, Y. Hua, B. N. V. Krishna, Q. Xi, W. Ai and J. S. Yu, Energy Storage Mater., 2022, 53, 273–304 CrossRef
.
- Y. Zou, X. Yang, L. Shen, Y. Su, Z. Chen, X. Gao, J. Zhou and J. Sun, Energy Environ. Sci., 2022, 15, 517–538 Search PubMed
.
- Z. Zhang, D. Han, D. Fan, Y. Tao, Z. Weng and Q. Yang, Chem. Ind. Eng. Prog., 2023, 42, 2504–2515 Search PubMed
.
- K. E. K. Sun, T. K. A. Hoang, T. N. L. Doan, Y. Yu, X. Zhu, Y. Tian and P. Chen, ACS Appl. Mater. Interfaces, 2017, 9, 9681–9687 CrossRef CAS PubMed
.
- H. Zhang, Y. Zhong, J. Li, Y. Liao, J. Zeng, Y. Shen, L. Yuan, Z. Li and Y. Huang, Adv. Energy Mater., 2023, 13, 2203254 CrossRef CAS
.
- M. Qiu, S. Peng, A. Qin, G. Cui and W. Mai, Energy Storage Mater., 2022, 49, 463–470 CrossRef
.
- W. Yuan, X. Nie, Y. Wang, X. Li, G. Ma, Y. Wang, S. Shen and N. Zhang, ACS Nano, 2023, 17, 23861–23871 CrossRef CAS PubMed
.
- C. Meng, W. He, L. Jiang, Y. Huang, J. Zhang, H. Liu and J. J. Wang, Adv. Funct. Mater., 2022, 32, 2207732 CrossRef CAS
.
- M. Qiu, P. Sun, Y. Wang, L. Ma, C. Zhi and W. Mai, Angew. Chem., Int. Ed., 2022, 61, e202210979 CrossRef CAS PubMed
.
- J. Yang, H. Yan, H. Hao, Y. Song, Y. Li, Q. Liu and A. Tang, ACS Energy Lett., 2022, 7, 2331–2339 CrossRef CAS
.
- R. Feng, X. Chi, Q. Qiu, J. Wu, J. Huang, J. Liu and Y. Liu, ACS Appl. Mater. Interfaces, 2021, 13, 40638–40647 CrossRef CAS PubMed
.
- T. Wei, Y. Ren, Y. Wang, L. E. Mo, Z. Li, H. Zhang, L. Hu and G. Cao, ACS Nano, 2023, 17, 3765–3775 CrossRef CAS PubMed
.
- Q. Wen, H. Fu, Z. Wang, Y. Huang, Z. He, C. Yan, J. Mao, K. Dai, X. Zhang and J. Zheng, J. Mater. Chem. A, 2022, 10, 17501–17510 RSC
.
- Z. Liu, Z. Guo, L. Fan, C. Zhao, A. Chen, M. Wang, M. Li, X. Lu, J. Zhang, Y. Zhang and N. Zhang, Adv. Mater., 2023, 36, 2305988 CrossRef PubMed
.
- D. Xu, B. Chen, X. Ren, H. Chao, Z. Chang, A. Pan and H. Zhou, Energy Environ. Sci., 2024, 17, 642 RSC
.
- Z. Cao, P. Zhuang, X. Zhang, M. Ye, J. Shen and P. M. Ajayan, Adv. Energy Mater., 2020, 10, 2001599 CrossRef CAS
.
- F. Yang, J. A. Yuwono, J. Hao, J. Long, L. Yuan, Y. Wang, S. Liu, Y. Fan, S. Zhao, K. Davey and Z. Guo, Adv. Mater., 2022, 34, 2206754 CrossRef CAS PubMed
.
- M. Li, Z. Li, X. Wang, J. Meng, X. Liu, B. Wu, C. Han and L. Mai, Energy Environ. Sci., 2021, 14, 3796–3839 RSC
.
- Q. Zhang, K. Xia, Y. Ma, Y. Lu, L. Li, J. Liang, S. Chou and J. Chen, ACS Energy Lett., 2021, 6, 2704–2712 CrossRef CAS
.
- J. Xu, W. Lv, W. Yang, Y. Jin, Q. Jin, B. Sun, Z. Zhang, T. Wang, L. Zheng, X. Shi, B. Sun and G. Wang, ACS Nano, 2022, 16, 11392–11404 CrossRef CAS PubMed
.
- R. Yao, L. Qian, Y. Sui, G. Zhao, R. Guo, S. Hu, P. Liu, H. Zhu, F. Wang, C. Zhi and C. Yang, Adv. Energy Mater., 2022, 12, 2102780 CrossRef CAS
.
- J. Hao, L. Yuan, C. Ye, D. Chao, K. Davey, Z. Guo and S. Z. Qiao, Angew. Chem., Int. Ed., 2021, 60, 7366–7375 CrossRef CAS PubMed
.
- Y. Zhu, J. Hao, Y. Huang and Y. Jiao, Small Struct., 2023, 4, 2200270 CrossRef CAS
.
- R. Meng, H. Li, Z. Lu, C. Zhang, Z. Wang, Y. Liu, W. Wang, G. Ling, F. Kang and Q. H. Yang, Adv. Mater., 2022, 34, 2200667 Search PubMed
.
- J. Luo, L. Xu, Y. Zhou, T. Yan, Y. Shao, D. Yang, L. Zhang, Z. Xia, T. Wang, L. Zhang, T. Cheng and Y. Shao, Angew. Chem., Int. Ed., 2023, 62, e202302302 CrossRef CAS PubMed
.
- Q. Zhang, Y. Ma, Y. Lu, X. Zhou, L. Lin, L. Li, Z. Yan, Q. Zhao, K. Zhang and J. Chen, Angew. Chem., Int. Ed., 2021, 60, 23357–23364 CrossRef CAS PubMed
.
- Q. Zhang, Y. Ma, Y. Lu, Y. Ni, L. Lin, Z. Hao, Z. Yan, Q. Zhao and J. Chen, J. Am. Chem. Soc., 2022, 144, 18435–18443 CrossRef CAS PubMed
.
- W. Yang, Y. Yang, H. Yang and H. Zhou, ACS Energy Lett., 2022, 7, 2515–2530 CrossRef CAS
.
- L. F. Shen, B. A. Lu, Y. Y. Li, J. Liu, Z. C. Huang Fu, H. Peng, J. Y. Ye, X. M. Qu, J. M. Zhang, G. Li, W. B. Cai, Y. X. Jiang and S. G. Sun, Angew. Chem., Int. Ed., 2020, 59, 22397–22402 CrossRef CAS PubMed
.
- C. Cui, D. Han, H. Lu, Z. Li, K. Zhang, B. Zhang, X. Guo, R. Sun, X. Ye, J. Gao, Y. Liu, Y. Guo, R. Meng, C. Wei, L. Yin, F. Kang, Z. Weng and Q. H. Yang, Adv. Energy Mater., 2023, 13, 2301466 CrossRef CAS
.
- M. Yan, C. Xu, Y. Sun, H. Pan and H. Li, Nano Energy, 2021, 82, 105739 CrossRef CAS
.
- H. Li, Y. Ren, Y. Zhu, J. Tian, X. Sun, C. Sheng, P. He, S. Guo and H. Zhou, Angew. Chem., Int. Ed., 2023, 62, e202310143 CrossRef CAS PubMed
.
- H. Wang, W. Ye, B. Yin, K. Wang, M. S. Riaz, B. B. Xie, Y. Zhong and Y. Hu, Angew. Chem., Int. Ed., 2023, 62, e202218872 CrossRef CAS PubMed
.
- J. Zhang, P. Li, Y. Wang, Z. Zhao and Z. Peng, Adv. Funct. Mater., 2023, 33, 2305804 CrossRef CAS
.
- Z. Hu, Z. Song, Z. Huang, S. Tao, B. Song, Z. Cao, X. Hu, J. Wu, F. Li, W. Deng, H. Hou, X. Ji and G. Zou, Angew. Chem., Int. Ed., 2023, 62, e202309601 CrossRef CAS PubMed
.
- H. Ren, S. Li, B. Wang, Y. Zhang, T. Wang, Q. Lv, X. Zhang, L. Wang, X. Han, F. Jin, C. Bao, P. Yan, N. Zhang, D. Wang, T. Cheng, H. Liu and S. Dou, Adv. Mater., 2023, 35, e202309601 Search PubMed
.
- D. Han, C. Cui, K. Zhang, Z. Wang, J. Gao, Y. Guo, Z. Zhang, S. Wu, L. Yin, Z. Weng, F. Kang and Q. Yang, Nat. Sustain., 2022, 5, 205–213 CrossRef
.
- L. Zhou, F. Wang, F. Yang, X. Liu, Y. Yu, D. Zheng and X. Lu, Angew. Chem., Int. Ed., 2022, 61, e202208051 CrossRef CAS PubMed
.
- J. Chen, W. Zhao, J. Jiang, X. Zhao, S. Zheng, Z. Pan and X. Yang, Energy Storage Mater., 2023, 59, 102767 CrossRef
.
- Q. Yang, L. Li, T. Hussain, D. Wang, L. Hui, Y. Guo, G. Liang, X. Li, Z. Chen, Z. Huang, Y. Li, Y. Xue, Z. Zuo, J. Qiu, Y. Li and C. Zhi, Angew. Chem., Int. Ed., 2022, 61, e202112304 CrossRef CAS PubMed
.
- X. Guo, Z. Zhang, J. Li, N. Luo, G. Chai, T. S. Miller, F. Lai, P. Shearing, D. J. L. Brett, D. Han, Z. Weng, G. He and I. P. Parkin, ACS Energy Lett., 2021, 6, 395–403 CrossRef CAS
.
- X. Zhao, X. Zhang, N. Dong, M. Yan, F. Zhang, K. Mochizuki and H. Pan, Small, 2022, 18, e2200742 CrossRef PubMed
.
- R. Chen, W. Zhang, Q. Huang, C. Guan, W. Zong, Y. Dai, Z. Du, Z. Zhang, J. Li, F. Guo, X. Gao, H. Dong, J. Zhu, X. Wang and G. He, Nano-Micro Lett., 2023, 15, 81 CrossRef CAS PubMed
.
- J. Hao, L. Yuan, Y. Zhu, M. Jaroniec and S. Z. Qiao, Adv. Mater., 2022, 34, 2206963 CrossRef CAS PubMed
.
- W. Zhang, Y. Dai, R. Chen, Z. Xu, J. Li, W. Zong, H. Li, Z. Li, Z. Zhang, J. Zhu, F. Guo, X. Gao, Z. Du, J. Chen, T. Wang, G. He and I. P. Parkin, Angew. Chem., Int. Ed., 2023, 62, e2022126695 Search PubMed
.
- S. J. Zhang, J. Hao, D. Luo, P. F. Zhang, B. Zhang, K. Davey, Z. Lin and S. Z. Qiao, Adv. Energy Mater., 2021, 11, 2102010 CrossRef CAS
.
- D. Han, Z. Wang, H. Lu, H. Li, C. Cui, Z. Zhang, R. Sun, C. Geng, Q. Liang, X. Guo, Y. Mo, X. Zhi, F. Kang, Z. Weng and Q. H. Yang, Adv. Energy Mater., 2022, 12, 2102982 CrossRef CAS
.
- C. Lin, X. Yang, P. Xiong, H. Lin, L. He, Q. Yao, M. Wei, Q. Qian, Q. Chen and L. Zeng, Adv. Sci., 2022, 9, e2201433 CrossRef PubMed
.
- Y. Lyu, J. A. Yuwono, P. Wang, Y. Wang, F. Yang, S. Liu, S. Zhang, B. Wang, K. Davey, J. Mao and Z. Guo, Angew. Chem., Int. Ed., 2023, 62, e202303011 CrossRef CAS PubMed
.
- M. Zhang, H. Hua, P. Dai, Z. He, L. Han, P. Tang, J. Yang, P. Lin, Y. Zhang, D. Zhan, J. Chen, Y. Qiao, C. C. Li, J. Zhao and Y. Yang, Adv. Mater., 2023, 35, 2208630 CrossRef CAS PubMed
.
- Z. Zhao, P. Li, Z. Zhang, H. Zhang and G. Li, Chem. Eng. J., 2023, 454, 140435 CrossRef CAS
.
- S. J. Zhang, J. Hao, Y. Zhu, H. Li, Z. Lin and S. Z. Qiao, Angew. Chem., Int. Ed., 2023, 62, e202301570 CrossRef CAS PubMed
.
- S. Jin, F. Duan, X. Wu, J. Li, X. Dan, X. Yin, K. Zhao, Y. Wei, Y. Sui, F. Du and Y. Wang, Small, 2022, 18, 2205462 CrossRef CAS PubMed
.
- K. Qi, W. Zhu, X. Zhang, M. Liu, H. Ao, X. Wu and Y. Zhu, ACS Nano, 2022, 16, 9461–9471 CrossRef CAS PubMed
.
- Y. Jiao, F. Li, X. Jin, Q. Lei, L. Li, L. Wang, T. Ye, E. He, J. Wang, H. Chen, J. Lu, R. Gao, Q. Li, C. Jiang, J. Li, G. He, M. Liao, H. Zhang, I. P. Parkin, H. Peng and Y. Zhang, Adv. Funct. Mater., 2021, 31, 2107652 CrossRef CAS
.
- Z. Wang, H. Chen, H. Wang, W. Huang, H. Li and F. Pan, ACS Energy Lett., 2022, 7, 4168–4176 CrossRef CAS
.
- X. Wang, X. Li, H. Fan and L. Ma, Nano-Micro Lett., 2022, 14, 205 CrossRef CAS PubMed
.
- D. A. Rakov, J. Sun, P. V. Cherepanov, K. Arano, P. C. Howlett, A. N. Simonov, F. Chen and M. Forsyth, Energy Environ. Sci., 2023, 16, 3919–3931 RSC
.
- C. Huang, X. Zhao, Y. Hao, Y. Yang, Y. Qian, G. Chang, Y. Zhang, Q. Tang, A. Hu and X. Chen, Energy Environ. Sci., 2023, 16, 1721–1731 RSC
.
- W. Xin, L. Miao, L. Zhang, H. Peng, Z. Yan and Z. Zhu, ACS Mater. Lett., 2021, 3, 1819–1825 CrossRef CAS
.
- W. Yuan, G. Ma, X. Nie, Y. Wang, S. Di, L. Wang, J. Wang, S. Shen and N. Zhang, Chem. Eng. J., 2022, 431, 134076 CrossRef CAS
.
- D. Li, L. Cao, T. Deng, S. Liu and C. Wang, Angew. Chem., Int. Ed., 2021, 60, 13035–13041 CrossRef CAS PubMed
.
- D. Xie, Y. Sang, D. H. Wang, W. Y. Diao, F. Y. Tao, C. Liu, J. W. Wang, H. Z. Sun, J. P. Zhang and X. L. Wu, Angew. Chem., Int. Ed., 2023, 62, e202216934 CrossRef CAS PubMed
.
- Q. Jian, T. Wang, J. Sun, M. Wu and T. Zhao, Energy Storage Mater., 2022, 53, 559–568 CrossRef
.
- D. Wang, D. Lv, H. Peng, C. Wang, H. Liu, J. Yang and Y. Qian, Angew. Chem., Int. Ed., 2023, 62, e202310290 CrossRef CAS PubMed
.
- C. Huang, F. Huang, X. Zhao, Y. Hao, Y. Yang, Y. Qian, G. Chang, Y. Zhang, Q. Tang, A. Hu and X. Chen, Adv. Funct. Mater., 2023, 33, 2210197 CrossRef CAS
.
- Y. Liu, Y. An, L. Wu, J. Sun, F. Xiong, H. Tang, S. Chen, Y. Guo, L. Zhang, Q. An and L. Mai, ACS Nano, 2023, 17, 552–560 CrossRef CAS PubMed
.
- X. Zeng, J. Mao, J. Hao, J. Liu, S. Liu, Z. Wang, Y. Wang, S. Zhang, T. Zheng, J. Liu, P. Rao and Z. Guo, Adv. Mater., 2021, 33, 2007416 CrossRef CAS PubMed
.
- Y. Chu, S. Zhang, S. Wu, Z. Hu, G. Cui and J. Luo, Energy Environ. Sci., 2021, 14, 3609–3620 RSC
.
- L. Cao, D. Li, E. Hu, J. Xu, T. Deng, L. Ma, Y. Wang, X. Yang and C. Wang, J. Am. Chem. Soc., 2020, 142, 21404–21409 CrossRef CAS PubMed
.
- H. Qin, W. Kuang, N. Hu, X. Zhong, D. Huang, F. Shen, Z. Wei, Y. Huang, J. Xu and H. He, Adv. Funct. Mater., 2022, 32, 2206695 CrossRef CAS
.
- H. Yu, D. Chen, Q. Li, C. Yan, Z. Jiang, L. Zhou, W. Wei, J. Ma, X. Ji, Y. Chen and L. Chen, Adv. Energy Mater., 2023, 13, 2300550 CrossRef CAS
.
- C. Huang, X. Zhao, S. Liu, Y. Hao, Q. Tang, A. Hu, Z. Liu and X. Chen, Adv. Mater., 2021, 33, 2100445 CrossRef CAS PubMed
.
- Y. Song, J. Wang, X. Zhong, K. Wang, Y. Zhang, H. Liu, L. Zhang, J. Liang and R. Wen, Energy Storage Mater., 2023, 58, 85–93 CrossRef
.
- K. Feng, D. Wang and Y. Yu, Molecules, 2023, 28, 2721 CrossRef CAS PubMed
.
- X. Liu, Y. Guo, F. Ning, Y. Liu, S. Shi, Q. Li, J. Zhang, S. Lu and J. Yi, Nano-Micro Lett., 2024, 16, 111 CrossRef CAS PubMed
.
- Y. Mu, Z. Li, B. Wu, H. Huang, F. Wu, Y. Chu, L. Zou, M. Yang, J. He, L. Ye, M. Han, T. Zhao and L. Zeng, Nat. Commun., 2023, 14, 4205 CrossRef CAS PubMed
.
- Q. Yang, G. Liang, Y. Guo, Z. Liu, B. Yan, Z. Huang, X. Li, J. Fan and C. Zhi, Adv. Mater., 2019, 31, 1903778 CrossRef CAS PubMed
.
- Z. Wu, J. Zou, Y. Li, E. J. Hansen, D. Sun, H. Wang, L. Wang and J. Liu, Small, 2023, 19, 2206634 CrossRef CAS PubMed
.
- Y. Zeng, X. Zhang, R. Qin, X. Liu, P. Fang, D. Zheng, Y. Tong and X. Lu, Adv. Mater., 2019, 31, 1903675 CrossRef PubMed
.
- Y. Tian, Y. An, C. Wei, B. Xi, S. Xiong, J. Feng and Y. Qian, ACS Nano, 2019, 13, 11676–11685 CrossRef CAS PubMed
.
- S. Xie, Y. Li, X. Li, Y. Zhou, Z. Dang, J. Rong and L. Dong, Nano-Micro Lett., 2021, 14, 39 CrossRef PubMed
.
- X. Zhu, X. Li, M. L. K. Essandoh, J. Tan, Z. Cao, X. Zhang, P. Dong, P. M. Ajayan, M. Ye and J. Shen, Energy Storage Mater., 2022, 50, 243–251 CrossRef
.
- M. Zhao, J. Rong, F. Huo, Y. Lv, B. Yue, Y. Xiao, Y. Chen, G. Hou, J. Qiu and S. Chen, Adv. Mater., 2022, 34, 2203153 CrossRef CAS PubMed
.
- Q. Li, D. Wang, B. Yan, Y. Zhao, J. Fan and C. Zhi, Angew. Chem., Int. Ed., 2022, 61, e202202780 CrossRef CAS PubMed
.
- R. Zhao, X. Dong, P. Liang, H. Li, T. Zhang, W. Zhou, B. Wang, Z. Yang, X. Wang, L. Wang, Z. Sun, F. Bu, Z. Zhao, W. Li, D. Zhao and D. Chao, Adv. Mater., 2023, 35, 2209288 CrossRef CAS PubMed
.
- Z. Meng, Y. Jiao and P. Wu, Angew. Chem., Int. Ed., 2023, 62, e202307271 CrossRef PubMed
.
- Q. Gou, H. Luo, Q. Zhang, J. Deng, R. Zhao, O. Odunmbaku, L. Wang, L. Li, Y. Zheng, J. Li, D. Chao and M. Li, Small, 2023, 19, 2207502 CrossRef CAS PubMed
.
- M. Zhou, C. Fu, L. Qin, Q. Ran, S. Guo, G. Fang, X. Lang, Q. Jiang and S. Liang, Energy Storage Mater., 2022, 52, 161–168 CrossRef
.
- J. Greeley, T. F. Jaramillo, J. Bonde, I. B. Chorkendorff and J. K. Norskov, Nat. Mater., 2006, 5, 909–913 CrossRef CAS PubMed
.
- L. Hong, L. Y. Wang, Y. Wang, X. Wu, W. Huang, Y. Zhou, K. X. Wang and J. S. Chen, Adv. Sci., 2022, 9, 2104866 CrossRef CAS PubMed
.
- C. Xie, Y. Li, Q. Wang, D. Sun, Y. Tang and H. Wang, Carbon Energy, 2020, 2, 540–560 CrossRef CAS
.
- J. Zhang, W. Huang, L. Li, C. Chang, K. Yang, L. Gao and X. Pu, Adv. Mater., 2023, 35, e2300073 CrossRef PubMed
.
- P. Cao, J. Tang, A. Wei, Q. Bai, Q. Meng, S. Fan, H. Ye, Y. Zhou, X. Zhou and J. Yang, ACS Appl. Mater. Interfaces, 2021, 13, 48855–48864 CrossRef CAS PubMed
.
- Y. Li, S. Yang, H. Du, Y. Liu, X. Wu, C. Yin, D. Wang, X. Wu, Z. He and X. Wu, J. Mater. Chem. A, 2022, 10, 14399–14410 RSC
.
- T. Foroozan, V. Yurkiv, S. Sharifi-Asl, R. Rojaee, F. Mashayek and R. Shahbazian-Yassar, ACS Appl. Mater. Interfaces, 2019, 11, 44077–44089 CrossRef CAS PubMed
.
- S. Zhan, Y. Guo, K. Wu, F. Ning, X. Liu, Y. Liu, Q. Li, J. Zhang, S. Lu and J. Yi, Chem.–Eur. J., 2024, 30, e202303211 CrossRef CAS PubMed
.
- H. Yu, Y. Chen, W. Wei, X. Ji and L. Chen, ACS Nano, 2022, 16, 9736–9747 CrossRef CAS PubMed
.
- Y. Zhang, X. Han, R. Liu, Z. Yang, S. Zhang, Y. Zhang, H. Wang, Y. Cao, A. Chen and J. Sun, Small, 2022, 18, 2105978 CrossRef CAS PubMed
.
- F. Huang, X. Li, Y. Zhang, Y. Jie, X. Mu, C. Yang, W. Li, Y. Chen, Y. Liu, S. Wang, B. Ge, R. Cao, X. Ren, P. Yan, Q. Li, D. Xu and S. Jiao, Adv. Mater., 2022, 34, 2203710 CrossRef CAS PubMed
.
- V. Pande and V. Viswanathan, ACS Energy Lett., 2019, 4, 2952–2959 CrossRef CAS
.
- A. Bayaguud, X. Luo, Y. Fu and C. Zhu, ACS Energy Lett., 2020, 5, 3012–3020 CrossRef CAS
.
- Z. Liang, C. Li, D. Zuo, L. Zeng, T. Ling, J. Han and J. Wan, Energy Storage Mater., 2023, 63, 102980 CrossRef
.
- M. Wang, J. Ma, Y. Meng, J. Sun, Y. Yuan, M. Chuai, N. Chen, Y. Xu, X. Zheng, Z. Li and W. Chen, Angew. Chem., Int. Ed., 2023, 62, e202214966 CrossRef CAS PubMed
.
- F. Wu, Y. Chen, Y. Chen, R. Yin, Y. Feng, D. Zheng, X. Xu, W. Shi, W. Liu and X. Cao, Small, 2022, 18, 2202363 CrossRef CAS PubMed
.
- L. Ma, M. A. Schroeder, T. P. Pollard, O. Borodin, M. S. Ding, R. Sun, L. Cao, J. Ho, D. R. Baker, C. Wang and K. Xu, Energy Environ. Mater., 2020, 3, 516–521 CrossRef CAS
.
- C. Li, R. Kingsbury, A. S. Thind, A. Shyamsunder, T. T. Fister, R. F. Klie, K. A. Persson and L. F. Nazar, Nat. Commun., 2023, 14, 3067 CrossRef CAS PubMed
.
- S. Chen, D. Ji, Q. Chen, J. Ma, S. Hou and J. Zhang, Nat. Commun., 2023, 14, 3526 CrossRef CAS PubMed
.
- X. Luo, M. Zhou, Z. Luo, T. Shi, L. Li, X. Xie, Y. Sun, X. Cao, M. Long, S. Liang and G. Fang, Energy Storage Mater., 2023, 57, 628–638 CrossRef
.
- L. Zhou, R. Yang, S. Xu, X. Lei, Y. Zheng, J. Wen, F. Zhang and Y. Tang, Angew. Chem., Int. Ed., 2023, 62, e202307880 CrossRef CAS PubMed
.
- W. Li, Y. Yang, G. Zhang and Y. Zhang, Nano Lett., 2015, 15, 1691–1697 CrossRef CAS PubMed
.
- X. Zeng, S. Qian, J. Zhou, B. Hao, L. Zhang, Y. Zhou, Y. Shi, C. Zhu, X. Zhou, J. Liu, Y. Cheng, C. Yan and T. Qian, Nano Lett., 2023, 23, 1135–1143 CrossRef CAS PubMed
.
- C. Xie, S. Liu, Z. Yang, H. Ji, S. Zhou, H. Wu, C. Hu, Y. Tang, X. Ji, Q. Zhang and H. Wang, Angew. Chem., Int. Ed., 2023, 62, e202218612 CrossRef CAS PubMed
.
- N. Yao, X. Chen, Z. Fu and Q. Zhang, Chem. Rev., 2022, 122, 10970–11021 CrossRef CAS PubMed
.
- H. Su, W. Che, F. Tang, W. Cheng, X. Zhao, H. Zhang and Q. Liu, J. Phys. Chem. C, 2018, 122, 21108–21114 CrossRef CAS
.
- G. Agarwal, J. D. Howard, V. Prabhakaran, G. E. Johnson, V. Murugesan, K. T. Mueller, L. A. Curtiss and R. S. Assary, ACS Appl. Mater. Interfaces, 2021, 13, 38816–38825 CrossRef CAS PubMed
.
- N. Chang, T. Li, R. Li, S. Wang, Y. Yin, H. Zhang and X. Li, Energy Environ. Sci., 2020, 13, 3527–3535 RSC
.
- Z. Luo, Y. Xia, S. Chen, X. Wu, R. Zeng, X. Zhang, H. Pan, M. Yan, T. Shi, K. Tao, B. B. Xu and Y. Jiang, Nano-Micro Lett., 2023, 15, 205 CrossRef CAS PubMed
.
- M. He, J. Chen, A. Hu, Z. Yan, L. Cao and J. Long, Energy Storage Mater., 2023, 62, 102941 CrossRef
.
- Z. Hou, T. Zhang, X. Liu, Z. Xu, J. Liu, W. Zhou, Y. Qian, H. J. Fan, D. Chao and D. Zhao, Sci. Adv., 2022, 8, eabp8960 CrossRef CAS PubMed
.
- C. Guo, J. Zhou, Y. Chen, H. Zhuang, J. Li, J. Huang, Y. Zhang, Y. Chen, S. L. Li and Y. Q. Lan, Angew. Chem., Int. Ed., 2023, 62, e202300125 CrossRef CAS PubMed
.
- C. Tian, J. Wang, R. Sun, T. Ali, H. Wang, B. B. Xie, Y. Zhong and Y. Hu, Angew. Chem., Int. Ed., 2023, 62, e202310970 CrossRef CAS PubMed
.
- H. Du, K. Wang, T. Sun, J. Shi, X. Zhou, W. Cai and Z. Tao, Chem. Eng. J., 2022, 427, 131705 CrossRef CAS
.
- X. Yang, Z. Zhang, M. Wu, Z. P. Guo and Z. J. Zheng, Adv. Mater., 2023, 17, 2303550 CrossRef PubMed
.
- P. Xiong, Y. Kang, N. Yao, X. Chen, H. Mao, W. Jang, D. M. Halat, Z. Fu, M. Jung, H. Y. Jeong, Y. Kim, J. A. Reimer, Q. Zhang and H. S. Park, ACS Energy Lett., 2023, 8, 1613–1625 CrossRef CAS
.
- Y. Shang, P. Kumar, T. Musso, U. Mittal, Q. Du, X. Liang and D. Kundu, Adv. Funct. Mater., 2022, 32, 2200606 CrossRef CAS
.
- Z. Yang, C. Hu, Q. Zhang, T. Wu, C. Xie, H. Wang, Y. Tang, X. Ji and H. Wang, Angew. Chem., Int. Ed., 2023, 62, e202308017 CrossRef CAS PubMed
.
- J. Pu, C. Zhong, J. Liu, Z. Wang and D. Chao, Energy Environ. Sci., 2021, 14, 3872–3911 RSC
.
- Z. Zhang, B. Xi, X. Ma, W. Chen, J. Feng and S. Xiong, SusMat, 2022, 2, 114–141 CrossRef CAS
.
- B. Wu, Y. Mu, J. He, M. Li, Z. Li, Y. Chu, Y. Li and L. Zeng, Carbon Neutralization, 2023, 2, 310–338 CrossRef CAS
.
- B. Chen, H. Zhang, J. Xuan, G. J. Offer and H. Wang, Adv. Mater. Technol., 2020, 5, 2000555 CrossRef CAS
.
- H. Li and W. Wang, Curr. Opin. Electrochem., 2023, 41, 101376 CrossRef
.
- W. Du, Z. Zhang, F. Iacoviello, S. Zhou, R. E. Owen, R. Jervis, D. J. L. Brett and P. R. Shearing, ACS Appl. Mater. Interfaces, 2023, 15, 14196–14205 CAS
.
- J. Liu, S. L. Lim, J. Y. Zhong and B. L. Lim, Nat. Commun., 2022, 13, 7822 CrossRef CAS PubMed
.
- Z. Zhang, S. Said, K. Smith, Y. S. Zhang, G. He, R. Jervis, P. R. Shearing, T. S. Miller and D. J. L. Brett, J. Mater. Chem. A, 2021, 9, 15355–15362 RSC
.
- A. Chen, C. Zhao, J. Gao, Z. Guo, X. Lu, J. Zhang, Z. Liu, M. Wang, N. Liu, L. Fan, Y. Zhang and N. Zhang, Energy Environ. Sci., 2023, 16, 275–284 RSC
.
- Z. Hu, F. Zhang, Y. Zhao, H. Wang, Y. Huang, F. Wu, R. Chen and L. Li, Adv. Mater., 2022, 34, 2203104 CrossRef CAS PubMed
.
- Q. Ma, R. Gao, Y. Liu, H. Dou, Y. Zheng, T. Or, L. Yang, Q. Li, Q. Cu, R. Feng, Z. Zhang, Y. Nie, B. Ren, D. Luo, X. Wang, A. Yu and Z. Chen, Adv. Mater., 2022, 34, 2207344 CrossRef CAS PubMed
.
- Q. Li, A. Chen, D. Wang, Y. Zhao, X. Wang, X. Jin, B. Xiong and C. Zhi, Nat. Commun., 2022, 13, 3699 CrossRef CAS PubMed
.
- J. Gu, Y. Tao, H. Chen, Z. Cao, Y. Zhang, Z. Du, Y. Cui and S. Yang, Adv. Energy Mater., 2022, 12, 2200115 CrossRef CAS
.
- Y. Jeon, Y. Wu, Y. Zhang, C. Hwang, H. Lee, H. Song and N. Liu, Electrochim. Acta, 2021, 391, 138877 CrossRef CAS
.
- Z. Cai, J. Wang, Z. Lu, R. Zhan, Y. Ou, L. Wang, M. Dahbi, J. Alami, J. Lu, K. Amine and Y. Sun, Angew. Chem., Int. Ed., 2022, 61, e202116560 CrossRef CAS PubMed
.
- X. Zhang, J. Yang, Z. Ren, K. Xie, Q. Ye, F. Xu and X. Liu, New Carbon Mater., 2022, 37, 371–380 CrossRef CAS
.
- J. S. Keist, C. A. Orme, P. K. Wright and J. W. Evans, Electrochim. Acta, 2015, 152, 161–171 CrossRef CAS
.
- Z. Zhang, S. Said, K. Smith, R. Jervis, C. A. Howard, P. R. Shearing, D. J. L. Brett and T. S. Miller, Adv. Energy Mater., 2021, 11, 2101518 CrossRef CAS
.
- X. Zhou, Y. Lu, Q. Zhang, L. Miao, K. Zhang, Z. Yan, F. Li and J. Chen, ACS Appl. Mater. Interfaces, 2020, 12, 55476–55482 CrossRef CAS PubMed
.
- X. Zhou, Q. Zhang, Z. Hao, Y. Ma, O. A. Drozhzhin and F. Li, ACS Appl. Mater. Interfaces, 2021, 13, 53227–53234 CrossRef CAS PubMed
.
- J. S. Keist, J. A. Hammons, P. K. Wright, J. W. Evans and C. A. Orme, Electrochim. Acta, 2020, 342, 136073 CrossRef CAS
.
- S. Wang, Z. Wang, Y. Yin, T. Li, N. Chang, F. Fan, H. Zhang and X. Li, Energy Environ. Sci., 2021, 14, 4077 RSC
.
- J. Hack, D. Patel, J. J. Bailey, F. Iacoviello, P. R. Shearing and D. J. L. Brett, JPhys Mater., 2022, 5, 14001 CrossRef CAS
.
- J. Scharf, M. Chouchane, D. P. Finegan, B. Lu, C. Redquest, M. C. Kim, W. Yao, A. A. Franco, D. Gostovic, Z. Liu, M. Riccio, F. Zelenka, J. M. Doux and Y. S. Meng, Nat. Nanotechnol., 2022, 17, 446–459 CrossRef CAS PubMed
.
- J. S. Ko, K. Bishop, N. Seitzman, B. Chen, M. F. Toney and J. Nelson Weker, J. Electrochem. Soc., 2020, 167, 140520 CrossRef CAS
.
- D. P. Guida, A. C. Chuang, J. S. Okasinski, M. T. Wendling, X. H. Chadderdon and J. W. Gallaway, J. Power Sources, 2023, 556, 232460 CrossRef CAS
.
- S. D. Pu, C. Gong, Y. T. Tang, Z. Ning, J. Liu, S. Zhang, Y. Yuan, D. Melvin, S. Yang, L. Pi, J. J. Marie, B. Hu, M. Jenkins, Z. Li, B. Liu, S. Tsang, T. J. Marrow, R. C. Reed, X. Gao, P. G. Bruce and A. W. Robertson, Adv. Mater., 2022, 34, e2202552 CrossRef PubMed
.
- S. D. Pu, B. Hu, Z. Li, Y. Yuan, C. Gong, Z. Ning, C. Chau, S. Yang, S. Zhang, L. Pi, Y. T. Tang, J. Yue, T. J. Marrow, X. Gao, P. G. Bruce and A. W. Robertson, Joule, 2023, 7, 366–379 CrossRef CAS
.
- G. Qian, G. Zan, J. Li, S. J. Lee, Y. Wang, Y. Zhu, S. Gul, D. J. Vine, S. Lewis, W. Yun, Z. F. Ma, P. Pianetta, J. S. Lee, L. Li and Y. Liu, Adv. Energy Mater., 2022, 12, 2200255 CrossRef CAS
.
- W. Zhang, Q. Yao, C. Wang, R. Feng, N. Chen, J. Zhu and Z. Li, Adv. Funct. Mater., 2023, 17, 2303590 Search PubMed
.
- F. Rossi, L. Mancini, I. Sgura, M. Boniardi, A. Casaroli, A. P. Kao and B. Bozzini, ChemElectroChem, 2022, 9, e202101537 CrossRef CAS
.
- Y. Huang, D. Perlmutter, A. Fei-Huei Su, J. Quenum, P. Shevchenko, D. Y. Parkinson, I. V. Zenyuk and D. Ushizima, npj Comput. Mater., 2023, 9, 93–99 CrossRef
.
- J. Kosacki and F. Dogan, J. Electrochem. Soc., 2021, 168, 120540 CrossRef CAS
.
- J. Zhao, Z. Lv, S. Wang, Z. Chen, Z. Meng, G. Li, C. Guo, T. Liu and J. Hui, Small Methods, 2023, 7, 2300731 CrossRef CAS PubMed
.
- Y. Sasaki, K. Yoshida, T. Kawasaki, A. Kuwabara, Y. Ukyo and Y. Ikuhara, J. Power Sources, 2021, 481, 228831 CrossRef CAS
.
- Y. Yuan, S. D. Pu, M. A. Pérez-Osorio, Z. Li, S. Zhang, S. Yang, B. Liu, C. Gong, A. S. Menon, L. F. J. Piper, X. Gao, P. G. Bruce and A. W. Robertson, Adv. Mater., 2023, 36, 2307708 CrossRef PubMed
.
- T. Chen, F. Huang, Y. Wang, Y. Yang, H. Tian and J. M. Xue, Adv. Sci., 2022, 9, 2105980 CrossRef CAS PubMed
.
- X. Qian, L. Li, Y. Wang, Z. Tian, H. Zhong, W. Chen, T. Chen and J. Fu, Energy Storage Mater., 2023, 58, 204–214 CrossRef
.
- F. Ling, L. Wang, F. Liu, M. Ma, S. Zhang, X. Rui, Y. Shao, Y. Yang, S. He, H. Pan, X. Wu, Y. Yao and Y. Yu, Adv. Mater., 2023, 35, 2208764 CrossRef CAS PubMed
.
- J. Zhou, L. Zhang, M. Peng, X. Zhou, Y. Cao, J. Liu, X. Shen, C. Yan and T. Qian, Adv. Mater., 2022, 34, 2200131 CrossRef CAS PubMed
.
- J. Zhou, M. Xie, F. Wu, Y. Mei, Y. Hao, R. Huang, G. Wei, A. Liu, L. Li and R. Chen, Adv. Mater., 2021, 33, 2101649 CrossRef CAS PubMed
.
- J. Zhou, F. Wu, Y. Mei, Y. Hao, L. Li, M. Xie and R. Chen, Adv. Mater., 2022, 34, 2200782 CrossRef CAS PubMed
.
- J. Zhou, M. Xie, F. Wu, Y. Mei, Y. Hao, L. Li and R. Chen, Adv. Mater., 2022, 34, 2106897 CrossRef CAS PubMed
.
- K. Wang, F. Liu, Q. Li, J. Zhu, T. Qiu, X. Liu and X. Sun, Chem. Eng. J., 2023, 452, 139577 CrossRef CAS
.
- Y. Lv, M. Zhao, Y. Du, Y. Kang, Y. Xiao and S. Chen, Energy Environ. Sci., 2022, 15, 4748–4760 RSC
.
- Y. Qin, H. Li, C. Han, F. Mo and X. Wang, Adv. Mater., 2022, 34, 22007118 Search PubMed
.
- X. Zeng, K. Xie, S. Liu, S. Zhang, J. Hao, J. Liu, W. K. Pang, J. Liu, P. Rao, Q. Wang, J. Mao and Z. Guo, Energy Environ. Sci., 2021, 14, 5947–5957 RSC
.
- M. Yu, N. Chandrasekhar, R. K. M. Raghupathy, K. H. Ly, H. Zhang, E. Dmitrieva, C. Liang, X. Lu, T. D. Kühne, H. Mirhosseini, I. M. Weidinger and X. Feng, J. Am. Chem. Soc., 2020, 142, 19570–19578 CrossRef CAS PubMed
.
- X. Liu, K. Wang, Y. Liu, F. Zhao, J. He, H. Wu, J. Wu, H. P. Liang and C. Huang, Carbon Energy, 2023, 5, e343 CrossRef CAS
.
- J. Ruan, D. Ma, K. Ouyang, S. Shen, M. Yang, Y. Wang, J. Zhao, H. Mi and P. Zhang, Nano-Micro Lett., 2023, 15, 37 CrossRef CAS PubMed
.
- M. M. Amaral, C. G. Real, V. Y. Yukuhiro, G. Doubek, P. S. Fernandez, G. Singh and H. Zanin, J. Energy Chem., 2023, 81, 472–491 CrossRef CAS
.
- J. Hao, X. Li, S. Zhang, F. Yang, X. Zeng, S. Zhang, G. Bo, C. Wang and Z. Guo, Adv. Funct. Mater., 2020, 30, 2001263 CrossRef CAS
.
- G. Li, Z. Zhao, S. Zhang, L. Sun, M. Li, J. A. Yuwono, J. Mao, J. Hao, J. P. Vongsvivut, L. Xing, C. X. Zhao and Z. Guo, Nat. Commun., 2023, 14, 6526 CrossRef CAS PubMed
.
- S. Liu, J. P. Vongsvivut, Y. Wang, R. Zhang, F. Yang, S. Zhang, K. Davey, J. Mao and Z. Guo, Angew. Chem., Int. Ed., 2023, 62, e202215600 CrossRef CAS PubMed
.
- C. Li, A. Shyamsunder, A. G. Hoane, D. M. Long, C. Y. Kwok, P. G. Kotula, K. R. Zavadil, A. A. Gewirth and L. F. Nazar, Joule, 2022, 6, 1103–1120 CrossRef CAS
.
- M. Xia, T. Liu, N. Peng, R. Zheng, X. Cheng, H. Zhu, H. Yu, M. Shui and J. Shu, Small Methods, 2019, 3, 1900119 CrossRef
.
- K. V. Graae and P. Norby, ACS Appl. Energy Mater., 2022, 5, 11392–11401 CrossRef CAS
.
- R. Xue, Y. Zou, Z. Wang, L. Mao, H. Wang, M. Zhang, A. Shao, J. Liu, N. Yao, Y. Liu and Y. Ma, ACS Nano, 2023, 17, 17359–17371 CrossRef CAS PubMed
.
- H. Ge, X. Feng, D. Liu and Y. Zhang, Nano Res. Energy, 2023, 2, e9120039 CrossRef
.
- K. Lolupiman, P. Wangyao and J. Qin, J. Met., Mater. Miner., 2019, 29, 120–126 CAS
.
- J. J. Ye, P. H. Li, H. R. Zhang, Z. Y. Song, T. Fan, W. Zhang, J. Tian, T. Huang, Y. Qian, Z. Hou, N. Shpigel, L. F. Chen and S. X. Dou, Adv. Funct. Mater., 2023, 33, 2305659 CrossRef CAS
.
- L. Ma, Q. Li, Y. Ying, F. Ma, S. Chen, Y. Li, H. Huang and C. Zhi, Adv. Mater., 2021, 33, 2007406 CrossRef CAS PubMed
.
- Y. Liu, J. Hu, Q. Lu, M. Hantusch, H. Zhang, Z. Qu, H. Tang, H. Dong, O. G. Schmidt, R. Holze and M. Zhu, Energy Storage Mater., 2022, 47, 98–104 CrossRef
.
- J. Zhou, B. Hao, Y. Meng, H. Yang, W. Chen, L. Zhang, J. Liu, C. Yan and T. Qian, Nano Lett., 2023, 23, 10148–10156 CrossRef CAS PubMed
.
- X. Ni, J. Zhou, H. Ji, Y. Chen, H. Yu, Y. Zheng, T. Qian, M. Wang, L. Chen and C. Yan, Adv. Funct. Mater., 2023, 33, 2302293 CrossRef CAS
.
- C. Kao, C. Ye, J. Hao, J. Shan, H. Li and S. Qiao, ACS Nano, 2023, 17, 3948–3957 CrossRef CAS PubMed
.
- K. Liang, S. Huang, H. Zhao, W. Liu, X. Huang, W. Chen, Y. Ren and J. Ma, Adv. Mater. Interfaces, 2022, 9, 2200564 CrossRef CAS
.
- J. Zhao, J. Zhang, W. Yang, B. Chen, Z. Zhao, H. Qiu, S. Dong, X. Zhou, G. Cui and L. Chen, Nano Energy, 2019, 57, 625–634 CrossRef CAS
.
- J. Wang, H. Qiu, Z. Zhao, Y. Zhang, J. Zhao, Y. Ma, J. Li, M. Xing, G. Li and G. Cui, Chem. Res. Chin. Univ., 2021, 37, 328–334 CrossRef CAS
.
- Y. Huang, Y. Zhuang, L. Guo, C. Lei, Y. Jiang, Z. Liu, Y. Zhao, K. Xing, X. Wu, S. Luo, G. Chen, Z. Liu and Z. Hu, Small, 2023, 20, 2306211 CrossRef PubMed
.
- S. Wei, Z. Qi, Y. Xia, S. Chen, C. Wang, Y. Wang, P. Zhang, K. Zhu, Y. Cao, X. Guo, X. Yang, Q. Cui, X. Liu, X. Wu and L. Song, ACS Nano, 2022, 16, 21152–21162 CrossRef CAS PubMed
.
- Z. Zhao, J. Zhao, Z. Hu, J. Li, J. Li, Y. Zhang, C. Wang and G. Cui, Energy Environ. Sci., 2019, 12, 1938–1949 RSC
.
- M. Bockelmann, M. Becker, L. Reining, U. Kunz and T. Turek, J. Electrochem. Soc., 2018, 165, A3048–A3055 CrossRef CAS
.
- S. S. Zhang, K. Xu and T. R. Jow, Electrochim. Acta, 2006, 51, 1636–1640 CrossRef CAS
.
- K. Ouyang, D. Ma, N. Zhao, Y. Wang, M. Yang, H. Mi, L. Sun, C. He and P. Zhang, Adv. Funct. Mater., 2022, 32, 202109749 Search PubMed
.
- B. Qiu, K. Liang, W. Huang, G. Zhang, C. He, P. Zhang and H. Mi, Adv. Energy Mater., 2023, 13, 2301193 CrossRef CAS
.
- Z. Liu, R. Wang, Q. Ma, J. Wan, S. Zhang, L. Zhang, H. Li, Q. Luo, J. Wu, T. Zhou, J. Mao, L. Zhang, C. Zhang and Z. Guo, Adv. Funct. Mater., 2023, 32, 221458 Search PubMed
.
- J. Abdulla, J. Cao, P. Wangyao and J. Qin, J. Met., Mater. Miner., 2020, 30, 1–8 CrossRef CAS
.
- M. W. Na Li, Y. X. M. W. Chaohui, Y. Fan and Y. Shengxue, Energy Storage Mater., 2023, 635, 157704 Search PubMed
.
- Q. Li, A. Chen, D. Wang, Z. Pei and C. Zhi, Joule, 2021, 6, 269–279 Search PubMed
.
- G. Garcia, E. Ventosa and W. Schuhmann, ACS Appl. Mater. Interfaces, 2017, 9, 18691–18698 CrossRef CAS PubMed
.
- R. Qin, Y. Wang, Q. Zhao, K. Yang and F. Pan, Chin. J. Struct. Chem., 2020, 39, 605–614 CAS
.
- Y. Han, F. Wang, B. Zhang, L. Yan, J. Hao, C. Zhu, X. Zou, Y. Zhou and B. Xiang, Energy Storage Mater., 2023, 62, 102928 CrossRef
.
- G. Duan, Y. Wang, L. Sun, Z. Bao, B. Luo, S. Zheng, Z. Ye, J. Huang and Y. Lu, ACS Nano, 2023, 17, 22722–22732 CrossRef CAS PubMed
.
- J. Agrisuelas, J. Juan García-Jare O, D. Gimenez-Romero and F. Vicente, Electrochim. Acta, 2009, 54, 6046–6052 CrossRef CAS
.
- R. Sun, D. Han, C. Cui, Z. Han, X. Guo, B. Zhang, Y. Guo, Y. Liu, Z. Weng and Q. H. Yang, Angew. Chem., Int. Ed., 2023, 62, e202303557 CrossRef CAS PubMed
.
- S. Cora, S. Ahmad and N. Sa, ACS Appl. Mater. Interfaces, 2021, 13, 10131–10140 CrossRef CAS PubMed
.
- N. Dong, F. Zhang and H. Pan, Chem. Sci., 2022, 13, 8243–8252 RSC
.
- B. Lee, H. R. Seo, H. R. Lee, C. S. Yoon, J. H. Kim, K. Y. Chung, B. W. Cho and S. H. Oh, ChemSusChem, 2016, 9, 2948–2956 CrossRef CAS PubMed
.
- K. Wang, T. Qiu, L. Lin, F. Liu, J. Zhu, X. X. Liu and X. Sun, Chem. Sci., 2023, 14, 8076–8083 RSC
.
- M. Luo, T. C. Li, P. Wang, D. Zhang, C. Lin, C. Liu, D. Li, W. Chen, H. Y. Yang and X. Zhou, Nano Lett., 2023, 23, 9491–9499 CrossRef PubMed
.
- Z. Zheng, X. Zhong, Q. Zhang, M. Zhang, L. Dai, X. Xiao, J. Xu, M. Jiao, B. Wang, H. Li, Y. Jia, R. Mao and G. Zhou, Nat. Commun., 2024, 15, 753 CrossRef CAS PubMed
.
- Y. Zhang, H. Dong, T. Wang, G. He, I. P. Parkin and F. Cegla, J. Power Sources, 2022, 542, 231730 CrossRef CAS
.
- Q. Zhang, D. Lei, N. Liu, Z. Liu, Z. Ren, J. Yin, P. Jia, W. Lu and Y. Gao, Adv. Mater., 2022, 34, 2205369 CrossRef CAS PubMed
.
- J. Wang, J. Liu, M. Hu, J. Zeng, Y. Mu, Y. Guo, J. Yu, X. Ma, Y. Qiu and Y. Huang, J. Mater. Chem. A, 2018, 6, 11113–11118 RSC
.
- P. Sun, Z. Ji, M. Qiu, Y. Liu, K. Han, N. Chen, Z. L. Wang and W. Mai, Adv. Energy Mater., 2023, 17, 2302846 CrossRef
.
- Z. Pei, Nano Res. Energy, 2022, 1, e9120023 CrossRef
.
|
This journal is © The Royal Society of Chemistry 2024 |