DOI:
10.1039/D4RA06329E
(Paper)
RSC Adv., 2024,
14, 35971-35979
Synthesis of new-type, cost-effective and insensitive energetic materials via nitration of solid bituminous hydrocarbons†
Received
2nd September 2024
, Accepted 21st October 2024
First published on 11th November 2024
Abstract
A global trend for the development of energetic materials using various sources is promoted by researchers annually. Solid bituminous hydrocarbons can play a key role in carbon science as abundant, low-cost, and mineral carbonaceous substrates. This study focuses on the design and synthesis of a series of new energetic materials from natural asphalt (NA), petroleum pitch (PP) and petroleum bitumen (PB) as industrial and available solid bituminous hydrocarbons. Energetic materials NA-NO2, PP-NO2 and PB-NO2 were synthesized through the nitrification reaction. The heat of combustion, thermal behaviors and FTIR, elemental, BET, UV-vis, SEM, EDX-map, AFM, GC-MS and TG-DSC analyses were applied to identify and confirm that all were prepared successfully. Further, the physicochemical and energy properties of NA-NO2, PP-NO2 and PB-NO2 were calculated using EMDB V 1.0 software. Thermal analysis showed thermal stability and insensitivity of NA-NO2, PP-NO2 and PB-NO2 toward mechanical stimuli. The combustion heats of NA-NO2, PP-NO2 and PB-NO2 were measured using a calorimeter bomb via the ASTM D240 method and evolved high amounts of energy of 23
500, 23
450 and 23
360 kJ kg−1, respectively. The density of NA-NO2 was measured using the ASTM-D8176 test and confirmed to be 0.5 g cm−3, which can be considered the lightest energetic material. Based on the conducted studies and analyses, new energetic materials synthesized based on solid bituminous hydrocarbons are classified as first-generation energetic materials.
Introduction
Nowadays, organic nitro compounds are widely used in industrial applications as multilateral synthetic intermediates.1 These compounds are applied as key substrates for the preparation of useful materials such as building blocks to construct complex molecules in biological industries, agrochemicals, explosives, dyes, pharmaceuticals, polymers, perfumes, synthetic blocks, plastics, and manures and as catalytic substrates for organic reactions.2–4 In the past few decades, the study of new energetic materials has attracted the attention of many research groups due to their importance and value in propellants, explosives, and pyrotechnics.5–9 These materials can instantly release tremendous energy in response to a certain stimulus.10–12 The nitro group is the most important moiety of energetic organic materials, which is generally created via nitrolysis, direct nitration, oxidation, and rearrangement reactions that include nitrite anion or nitronium cation.13 Nitroaromatic compounds are a group of organic compounds with energetic groups that can decompose, ignite and explode due to heat and impact. Therefore, before the synthesis of these materials, it is necessary to pay attention to their thermochemical properties for storage, safe handling, and transportation.14 Energetic materials are categorized into three generations. The first-generation compounds such as 2,4,6-trinitrotoluene (TNT) are composed of benzene skeletons, which suffer from poor detonation properties. The second-generation energetic materials include compounds such as 1,3,5,7-tetranitrotetraazacyclooctane (HMX) and 1,3,5-trinitrotriazocyclohexane (RDX), which are derived from cyclic aliphatic and nitramino structures, and they have poor stability. The third-generation compounds such as 2,4,6,8,10,12-hexanitro-2,4,6,8,10,12-hexaazatetracyclododecane (CL-20) are derived from caged nitramino structures. These compounds have high sensitivity and favorable detonation properties.15–18
In recent years, some materials such as [60]fullerene polyglycidyl (C60-PG),19,20 bacterial cellulose (BC),21 carbon nanotubes (CNTs),22 cellulose-coated multiwalled carbon nanotube (C-coated MWCNT),23 cellulose,24 cellulose propionate,25 fullerene,26 polystyrene (PS),27 graphene oxide (GO)28 and single-walled carbon nanotubes (SCNTs)29 have been investigated as carbonaceous substrates for nitration reaction. They have been widely utilized due to their high specific surface area and the ability to graft groups on their surface area. However, most of these carbonaceous materials have limitations such as unavailability, high cost, poor stability, difficulty in nitration and low ratio of nitration.24,25,27–31 Additionally, a new method of thermal analysis was evaluated to determine the SIT self-ignition temperature of different bitumen nitrate mixtures. However, for nitration, bitumen mixed in NaNO3, Ni(NO3)2 and AgNO3 or AgI was prepared.32
Solid bituminous hydrocarbons such as natural asphalt (NA), petroleum pitch (PP), and petroleum bitumen (PB) are inexpensive, available and abundant materials that contain a high precursor of carbon (more than 70%). These carbon-containing materials are of interest for various applications such as dyes, road pavements, and building materials.31,33–35 NA is a heavy hydrocarbon and a type of bituminous material that is extracted in ready form through mineral extraction or from natural bitumen mines and resources. That contains about 80% carbon and 15% hydrogen, which is easily dissolved in tetrachloroethylene and carbon disulfide solvents.31,36 Also, recently NA support has been applied as a carbonaceous super adsorbent, which is used for rapid decolorization of aqueous dye solutions.37 Whereas, PP is one of the refinery petroleum derivatives and a complex mixture of polynuclear aliphatic and aromatic hydrocarbons, which has wide applications in the field of carbon fiber, feedstock for electrodes and supercapacitors.33,34,38 Moreover, PB is also one of the refinery petroleum derivatives, whose components include saturated and aromatic hydrocarbons, asphaltenes and resins.27 NA and PP are lumpy, black, and have a melting point above 180 °C.
Herein, in continuation of our previous research regarding the synthesis of new materials from natural asphalt, solid natural asphalt as a type of solid bituminous hydrocarbon has been nitrated for the synthesis of highly nitronatural asphalt (NA-NO2) under different conditions. In the following, we also nitrated petroleum pitch and petroleum bitumen for the synthesis of nitropetroleum pitch (PP-NO2) and nitropetroleum bitumen (PB-NO2) according to the natural asphalt nitrate conditions. Finally, the ability of these compounds in the field of energetic materials was evaluated and discussed.
Results and discussion
General procedure for nitration of solid bitumen hydrocarbons by HNO3/H2SO4
The synthesis method of NA-NO2, PP-NO2 and PB-NO2 is summarized as follows: first, 20 mL of H2SO4 was slowly added to a 100 mL round-bottom flask in an ice bath (∼−5 °C) containing 17.5 mL HNO3. Then, the mixture was stirred at room temperature for 15 min. In the next step, 2 g of the substrate was gradually added with stirring for 20 minutes. After 30 minutes of the reaction mixture, the temperature of the reaction was slowly increased to 60 °C and the reaction was allowed to continue for 5 hours. Subsequently, the reaction was completed, and 300 mL of distilled water was added to the reaction mixture. Then, the precipitate was filtered and washed several times with distilled water and finally dried at a temperature of 80 °C. In the end, 3.0, 2.75 and 2.60 g of brown powders of NA-NO2, PP-NO2 and PB-NO2 compounds were obtained, respectively.
Nitro natural asphalt synthesis (NA-NO2)
To determine the optimal reaction conditions, various factors such as elemental analysis, color, weight gain, and flammability of product (NA-NO2) were assayed. First, solid natural asphalt powder, 150–200 mesh, was nitrated through nitration using different reagents. Finally, HNO3/H2SO4 as a common and available reagent was selected for nitration of natural asphalt in high yield (Table 1, entry 3). This reagent was preferred to others due to more nitrogen content, lower ash content, faster burning and higher yield of the obtained target product. The synthetic route of the NA-NO2 is shown in Scheme 1.
Table 1 Optimizing the reaction conditions for the synthesis of NA-NO2 in the presence of different reagentsa
Entry |
Substrate |
Reagent(s) (ratio/mL) |
CHNS analysis |
Color |
Flammability |
Weight gainb (g) |
% C |
% N |
% H |
% S |
Reaction Condition: Substrate (2 g), various reagents, 6 h, 0–60 °C. The weight of the obtained product after nitration 2 g of substrate. Not flammable. These methods were not nitrated. |
1 |
Natural asphalt |
— |
61.76 |
0.86 |
7.34 |
7.38 |
Black |
—c |
— |
2 |
Natural asphalt |
HNO3 (17.5) |
70.85 |
5.61 |
3.44 |
5.43 |
Black |
F |
2.10 |
3 |
Natural asphalt |
HNO3/H2SO4 (17.5/20) |
46.91 |
6.11 |
4.68 |
5.52 |
Light brown |
F |
3.0 |
4 |
Natural asphalt |
HNO3/H2SO4/AC2O (17.5/20/5) |
49.76 |
6.80 |
4.52 |
1.42 |
Dark brown |
F |
2.20 |
5 |
Natural asphalt |
HNO3/H2SO4/AC2O (17.5/20/10) |
45.03 |
7.34 |
3.53 |
1.98 |
Brown |
F |
2.40 |
6 |
Natural asphalt |
HNO3/H2SO4/P2O5 (17.5/20/10 g) |
47.29 |
7.58 |
3.48 |
1.30 |
Light brown |
F |
2.42 |
7 |
Natural asphaltd |
HNO3/H2SO4/CaCl2 (17.5/20/10 g) |
— |
— |
— |
— |
Gray |
—c |
— |
8 |
Natural asphaltd |
NaNO2/KHSO4/H2O2 (1/0.8/0.03 g) |
— |
— |
— |
— |
Black |
—c |
— |
9 |
Petroleum pitch |
— |
82.27 |
1.03 |
6.70 |
4.88 |
Black |
—c |
— |
10 |
Petroleum pitch |
HNO3/H2SO4 (17.5/20) |
48.99 |
8.18 |
2.53 |
6.33 |
Brown |
F |
2.75 |
11 |
Petroleum bitumen |
HNO3/H2SO4 (17.5/20) |
50.42 |
6.67 |
7.42 |
10.99 |
Brown |
F |
2.60 |
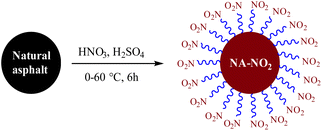 |
| Scheme 1 Nitration of natural asphalt. | |
Other reagents, including HNO3/H2SO4/CaCl2 and NaNO2/KHSO4/H2O2, were found to be ineffective in the nitrification of natural asphalt (Table 1, entries 7 and 8). Moreover, other nitrated reagents of entries 2 and 4–6 are mentioned in the ESI,† Table 1. The solubility and color of NA-NO2 were evaluated; it was found in light-brown color and completely soluble in aprotic solvents such as DMSO (Fig. 1 and 2). Additionally, NA-NO2 decomposed at temperatures above 300 °C. Although determining the exact active sites on natural asphalt for nitration is difficult, analyses and data show that both aromatic and aliphatic carbons in natural asphalt might be nitrated. Further, to gain insight into the burning rate of NA-NO2 high-speed images of the combustion process were recorded (Fig. 3). A lighter was used as the ignition source for the NA-NO2 flammability test.
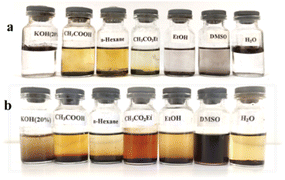 |
| Fig. 1 Solubility of natural asphalt (a) and NA-NO2 (b). | |
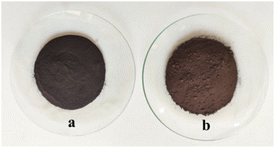 |
| Fig. 2 Color of natural asphalt (a) and NA-NO2 (b). | |
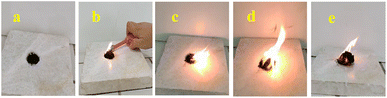 |
| Fig. 3 Continuous images of natural asphalt (a) burning using alighter (b–e). | |
In the continuation of research, petroleum pitch and petroleum bitumen as other available solid bituminous hydrocarbons were nitrated in parallel with natural asphalt powder in the same method. The results show that PP and PB were also successfully nitrated; based on elemental analysis, their nitrogen content was 8.18 and 6.67, respectively. They exhibited the same physical properties as NA-NO2. In addition, the burning test of PP-NO2 and PB-NO2 was investigated and demonstrated that they have poor flammability compared to NA-NO2 (Table 1, entries 10, 11).
After finding the best nitration reagent, the influence of natural asphalt amount, time and the ratio of acids (HNO3/H2SO4) on the efficiency of the reaction was assayed. Based on the nitrogen content and the weight of the obtained products, it can be concluded that the above factors affect the nitration reaction (Table 2).
Table 2 Optimization of the ratio of acids (HNO3/H2SO4) to natural asphalt for the synthesis of NA-NO2a
Entry |
Natural asphalt (g) |
Time (h) |
HNO3/H2SO4 (mL) |
CHNS |
Color |
Weight gain (g) |
% C |
% N |
% H |
% S |
Reaction Condition: natural asphalt (1–2 g), time (2–24 h), diverse ratio of acids, 0–60 °C. |
1 |
1 |
6 |
17.5/20 |
60.48 |
5.86 |
5.88 |
4.99 |
Brown |
2.3 |
2 |
1 |
6 |
4/5 |
55.27 |
5.98 |
4.37 |
5.56 |
Black |
2.17 |
3 |
1 |
6 |
2/3 |
56.55 |
5.37 |
4.38 |
5.36 |
Black |
2.09 |
4 |
2 |
24 |
17.5/20 |
50.97 |
5.77 |
4.70 |
5.95 |
Brown |
2.5 |
5 |
2 |
2 |
17.5/20 |
58.76 |
5.78 |
4.86 |
6.02 |
Black |
2.4 |
6 |
2 |
6 |
17.5/20 |
46.91 |
6.11 |
4.68 |
5.52 |
Light brown |
3.0 |
FTIR analysis
FTIR spectra of NA (a), NA-NO2 (b), PP-NO2 (c) and PB-NO2 (d) are enumerated in Fig. 4. In spectra a-d, peaks around 1440–1600 cm−1 and 2850–2924 cm−1 are related to aromatic double bands and aliphatic C–H stretching vibrations, respectively. Besides, the stretching vibrations related to N–H and O–H groups were observed in 3421–3450 cm−1. When the nitration reaction occurs on solid bitumen hydrocarbons such as natural asphalt (a), the peaks at 1718 cm−1 (b and c) and 1716 cm−1 (d) corresponding to the CO group appear, which can be due to the oxidation of OH group and the hydrolysis of amide to acid. In the case of spectra (b–d), symmetric and asymmetric stretching vibrations of NO2 groups were revealed in 1340 and 1541 cm−1. NO2 groups confirmed that the nitration process was successfully carried out on solid bitumen hydrocarbons. Furthermore, the FTIR spectra of the obtained products via other nitration methods are provided in ESI, Fig. S1 and S2,† respectively.
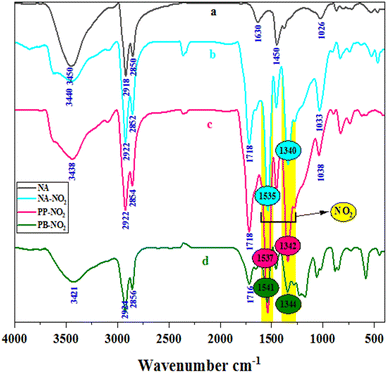 |
| Fig. 4 FTIR spectra of NA (a), NA-NO2 (b), PP-NO2 (c) and PB-NO2 (d). | |
UV-vis analysis
The UV-vis spectra of NA and NA-NO2 are given in Fig. 5. The absorption behavior of NA-NO2, PP-NO2 and RB-NO2 compounds are quite similar and their absorption peak appears around 222–270 nm that it is mainly due to π–π* and n–π* transitions while an absorption peak was not observed for natural asphalt. This demonstrates that the absorption peak of the molecules can originate from nitrobenzene moiety. UV-vis spectra PP-NO2 and PB-NO2 are given in Fig. S3 and S4.†
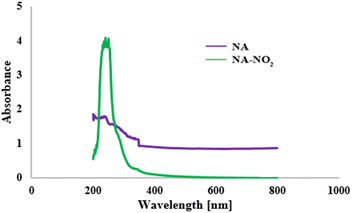 |
| Fig. 5 UV-visible absorption spectra for NA and NA-NO2. | |
BET analysis
In order to determine the surface area, volume and pore diameter of the NA (a) and NA-NO2 (b), nitrogen adsorption–desorption analysis was used under standard temperature and pressure conditions. According to the IUPAC classification, the nitrogen adsorption–desorption diagram of NA-NO2 showed the type III isotherm (Fig. 6).
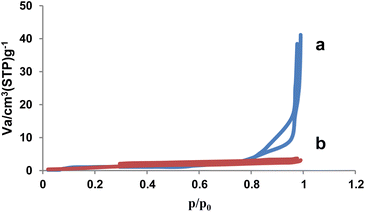 |
| Fig. 6 The N2 adsorption–desorption isotherm of NA (a) and NA-NO2 (b). | |
Based on BET data, surface area (SBET), total pore volume (Vtotal) and pore diameter (DBJH) of NA were obtained as 10.49 m2 g−1, 0.132 cm3 g−1 and 10.65 nm, respectively. The surface area of natural asphalt decreased to 4.34 m2 g−1 after nitration. The total pore volume and average pore diameter of the NA-NO2 were evaluated as 0.0065 cm3 g−1 and 1.66 nm, respectively. These results showed that NA-NO2 was successfully synthesized and confirmed the presence of NO2 groups on the natural asphalt molecular structure (Table 3).
Table 3 Textural properties of NA and NA-NO2 obtained by nitrogen adsorption–desorption analysis
Sample name |
SBET (m2 g−1) |
VTotal (cm3 g−1) |
DBJH (nm) |
NA |
10.49 |
0.132 |
10.65 |
NA-NO2 |
4.34 |
0.0065 |
1.66 |
SEM analysis
The morphology and particle size of NA-NO2 were determined using a scanning electron microscope. SEM images showed that the synthesized compound has spherical particles with an average diameter of 48–102 nm (Fig. 7).
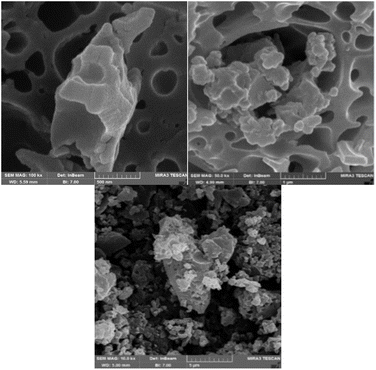 |
| Fig. 7 SEM images of NA-NO2. | |
EDX-map analysis
EDX analysis of the NA-NO2 compound confirmed the presence of C, N, O and S elements, which are also consistent with elements obtained from elemental analysis (Fig. 8). Furthermore, the map images are in agreement for the dispersion of all the elements (C, N, O and S) with the EDX results.
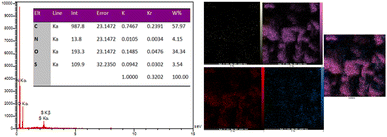 |
| Fig. 8 EDX and mapping analysis of NA-NO2. | |
AFM analysis
An atomic force microscope (AFM) was utilized to investigate 2D and 3D topography, surface texture, morphology, and size of NA-NO2 nanoparticles. The high-grade topography of hills and valleys illustrates that it is related to the porous nature of NA-NO2 (Fig. 9a). In addition, the 3D image revealed an average surface RMS roughness of 56.31 nm (Fig. 9b). This average roughness is useful for calculating the average height over the entire region. The analysis of texture, waviness and average roughness of NA-NO2 nanoparticles in the area of 1 × 1 μm2 is shown in Fig. 9c.
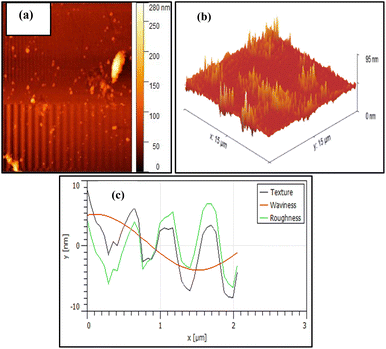 |
| Fig. 9 AFM images of the NA-NO2; (a) 2D image, (b) 3D image and (c) texture and roughness analysis. | |
Band gap energy
Based on UV-vis absorption data, direct and indirect band gap energies can be obtained for energetic materials such as NA-NO2, PP-NO2 and PB-NO2. These calculations are defined by eqn (1):39where A and Eg are the constant values and direct/indirect band gap energy, respectively.
Band gaps of solid bituminous nitrate hydrocarbons are shown in Fig. 10. Eg values of NA-NO2, PP-NO2 and PB-NO2 compounds have indirect band gaps of 4.59, 4.65 and 4.73 eV, respectively. Band gap energy calculations show that they are insulators. This exhibits that electron transfer from the valence band to the conduction band occurs more easily with a smaller band gap. NA-NO2 explodes faster compared to PP-NO2 and PB-NO2 due to its smaller band gap. Hence, it can be inferred that a relationship exists between explosive sensitivity and the band gap of the energetic materials based on solid bituminous hydrocarbons. This is consistent with experimental reports and software calculations. The Eg values corresponding to the direct band gap of NA-NO2, PP-NO2 and PB-NO2 were obtained as 4.52, 4.92 and 4.90 eV, respectively. The direct band gap Eg values of NA-NO2, PP-NO2 and PB-NO2 are shown in Fig. S5.†
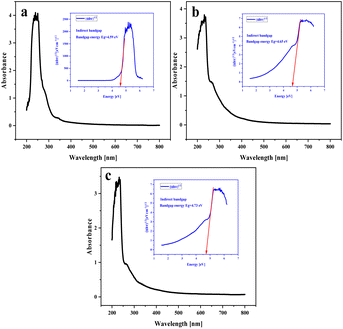 |
| Fig. 10 Indirect band gap energies (a) NA-NO2, (b) PP-NO2 (c) and PB-NO2. | |
In the gas chromatogram, the peaks corresponding to fragmented parts of the NA-NO2 molecule emerged at retention times of 11.977, 12.410, 24.143, 28.270 and 28.891 min (Fig. S6†). The characteristics of these fragmented molecules including molecular formula, molecular weight, proposed mass spectrum structure, base peak and peak height are shown in Table 4. The peaks of the fragmented molecules that appeared at different retention times may be due to their polarity changes. According to the results, the presence of these molecules was more probable in the synthesized sample, which was consistent with the GC chromatogram and the data obtained from the mass spectra. The mass spectra of fragmented molecules in NA-NO2 are shown in Fig. S7.† Proton nuclear magnetic resonance (1H-NMR) spectroscopy is a powerful tool in organic chemistry for identifying and analyzing molecular structures. According to the assignment of 1H-NMR spectrum of NA-NO2 the ratio of aliphatic, alkene and aromatic hydrogens was determined as 8
:
1
:
1 (Fig. S8†). The 1H-NMR spectrum shows that NA-NO2 could be considered an organic hydrocarbon.
Table 4 Summary of MS results for the fragmented molecules obtained from the NA-NO2 sample
Entry |
R.T.a (min) |
MFb |
MWc |
Proposed MSd |
Base peak |
Peak height |
% Of total |
Retention Time. Molecular Formula. Molecular Weight. Mass Spectrometry. |
1 |
11.977 |
C15H24O |
220 |
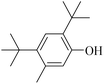 |
205 |
53 090 |
11.914 |
2 |
12.410 |
C15H24O |
220 |
 |
205 |
103 579 |
22.059 |
3 |
24.143 |
C14H31BO6Si2 |
362 |
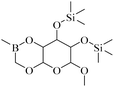 |
75 |
172 864 |
14.579 |
4 |
28.270 |
C11H16O4 |
212 |
 |
43 |
22 399 |
1.956 |
5 |
28.891 |
C12H22Si2 |
222 |
 |
207 |
36 283 |
4.159 |
Experimental section
Materials and apparatus
Solvents and chemicals were purchased from Merck chemical company, and natural asphalt was prepared from natural bitumen mines in the west of Iran. Pitch powder with 200 mesh from Bandar Abbas Refinery and petroleum bitumen with 60–70 grade was prepared from Jey Isfahan Refinery. Fourier transform infrared spectroscopy (FTIR) was performed by the KBr pellet method by FTIR (VERTEX 70, Bruker, Germany) spectroscopy. Agilent Technologies, Cary Series UV-vis Spectrophotometer, American, was used to measure the absorption of synthesized nitro-containing samples and their substrates. Thermogravimetric analysis (TGA) was conducted from ∼30 to 800 °C using TGA (NETZSCH, Germany). The nitrogen adsorption–desorption isotherms were measured on a Micromeritics, Asap2020, USA. unit at 77 K. Scanning electron microscopy (SEM) images were examined by FE-SEM on a TESCAN MIRA III (Czechia). The heat of combustion was measured by the ASTM-D240 test method using a calorimeter bomb. The content of density was determined using the ASTM-D8176 method at room temperature. Atomic force microscopy (AFM) images were collected on an ENTEGRA AFMNT, NT-MDT, Russian, instrument, and an elemental analysis was performed to determine % C, % H, % N, and % S using COSTECH-4010, Italy, instrument. GCMS analyses were performed with an Agilent 6890 technologies series Gas Chromatograph (GC) and Agilent 5973 Mass Spectrometer (MS). The GC separations were performed with an HP-5MS column (30 m × 250 μm × 0.25 μm) and helium gas (1 mL min−1).
Before the GCMS analysis, a quantity (1 μL) of each sample was dissolved in dimethyl sulfoxide (1 mL) and an aliquot (1 μL) of this solution was introduced by the splitless mode. The inlet heater was fixed at 270 °C, the pressure at 7.65 psi and the total flow was 41 mL min−1. The oven temperature was initially kept at 50 °C for 0 min, then heated at a linear rate of 10 °C min−1 until 290 °C, and eventually kept at this temperature for 30 min. The MS quadrupole temperature was set at 150 °C and the MS source temperature was 230 °C. The solvent delay time was 10 min. The MS was operated in the EMV mode (absolute).
Physicochemical and energetic properties. The physicochemical and energetic properties of NA-NO2, PP-NO2 and PB-NO2 as new energetic materials, including thermal stability, heat of combustion (ΔH) and density were investigated. Moreover, explosive parameters such as velocity of detonation, detonation pressure, detonation temperature, heat of detonation based on liquid H2O and vapour H2O, Average molecular weight of gaseous products, moles of gaseous per gram of explosive and oxygen balance were calculated using EMDB V 1.0 (ref. 40) software (Table 5).
Table 5 Physicochemical and energetic properties of NA-NO2, PP-NO2 and PB-NO2
Compound |
Tda [°C] |
VODb [m s−1] |
Pcjc [GPa] |
Tdetd [K] |
Qdete [kJ mol−1] |
Mf [g] |
αg |
OBh [Ω] |
ΔHi [kJ kg−1] |
Dpj |
Decomposition temperature by DSC (heating rate of 10 °C min−1). Velocity of detonation.41 Detonation pressure.42 Detonation temperature.43 Heat of detonation based on Liquid H2O and Vapour H2O.41 Average molecular weight of gaseous products.41 Moles of gaseous per gram of explosive.41 Oxygen balance.44 Heat of combustion (measured by bomb calorimetry). The combustion reaction of the synthesized compounds (calculated EMDB V 1.0). |
NA-NO2 |
338 |
4830 |
5.1 |
5738 |
2.86 |
26.56 |
0.0297 |
−66.95 |
23 500 |
3.06 N2 + 36.78 CO + 10.13 C(s) + 2.34 H2 |
PP-NO2 |
588 |
4650 |
4.2 |
6278 |
2.59 |
27.175 |
0.0271 |
−71.93 |
23 450 |
3.34 N2 + 24.5 CO + 25.92 C(s) + 3.71 H2 |
PB-NO2 |
590 |
4150 |
2.3 |
5236 |
1.87 |
24.95 |
0.0217 |
−88.28 |
23 360 |
4.09 N2 + 33.97 CO + 15.02 C(s) + 1.26 H2 |
The heat of combustion of NA-NO2, PP-NO2 and PB-NO2 was measured using a calorimeter bomb according to the ASTM D240 method. The heat of combustion is defined as the heat evolved using molecular oxygen when it is converted to standard oxidation products. NA-NO2, PP-NO2 and PB-NO2 produced 23
500, 23
450 and 23
360 kJ kg−1 heat of detonation, respectively (Table 5). In this way, NA-NO2 with 23
500 kJ kg−1 released energy is superior compared to some common energetic materials such as TNT, RDX, and HMX with released energies of 14
784 kJ kg−1, 8795.7 kJ kg−1 and 9232.6 kJ kg−1, respectively.14 These results confirmed that NA-NO2 has a higher heat of combustion compared to TNT, RDX and HMX. The density of NA-NO2 was measured by the ASTM-D8176 method and it was found to be 0.5 g cm−3 at room temperature. But the densities of TNT, RDX and HMX increase in the order: 1.65 < 1.80 < 1.91 g cm−3 (Tables 5 and 6).45 These differences confirmed that NA-NO2 has a lower density compared to them, so the nitrated natural bitumen compound can be considered among the lightest energetic compounds with low density.
Table 6 Comparison of physicochemical and energetic properties of NA-NO2 with TNT, RDX and HMX45
Compound |
Td [°C] |
VOD [m s−1] |
Pcj [Gpa] |
OB [Ω] |
ΔH [kJ kg−1] |
Da [g cm3] |
ISb [J] |
Density. Impact sensitivity. |
NA-NO2 |
338 |
4830 |
5.1 |
−66.95 |
23 500 |
0.5 |
— |
TNT |
290 |
7303 |
21.3 |
−73.97 |
14 784 |
1.65 |
15 (ref. 46) |
RDX |
210 |
8795 |
34.9 |
−21.61 |
8795.7 |
1.80 |
7.5 (ref. 46) |
HMX |
280 |
9144 |
39.2 |
−21.61 |
9232.6 |
1.91 |
7 (ref. 46) |
Another detonation parameter that is utilized for energetic materials is oxygen balance (OB). The progress of oxidation and combustion requires a sufficient amount of OB, the positive value of which leads to excellent detonation performance. Based on ΔH and OB parameters, it can be concluded that NA-NO2 burns faster than PP-NO2 and PB-NO2. The value of OB for TNT and two compounds RDX and HMX are −73.97 and −21.61, respectively. The differences in the above values can indicate that NA-NO2 performs superior to PP-NO2, PB-NO2 and TNT but poorer than RDX and HMX.45 These values are listed in Table 6. Comparing the detonation pressure of NA-NO2, PP-NO2 and PB-NO2, it shows that NA-NO2 is stronger than the other two compounds. However, they have a lower detonation pressure than TNT, RDX and HMX (Tables 5 and 6). The percentages of C, H, N, S and O elements in NA-NO2, PP-NO2 and PB-NO2 were obtained through CHNSO. Using these values, OB was calculated through the specified reference given in Table 5. Given that natural asphalt is a complex mixture primarily composed of hydrocarbons along with various functional groups, traces of metals and impurities, calculating equilibrium conditions can indeed be challenging. Therefore, the following empirical formula (CaHbNcOd)47 was applied to calculate the OB of NA-NO2, PP-NO2 and PB-NO2, ignoring impurities.
In addition, OB calculations related to NA-NO
2, PP-NO
2 and PB-NO
2 are summarized in Table S1.
†
Other parameters including decomposition temperature, detonation velocity and impact sensitivity of NA-NO2, PP-NO2 and PB-NO2 were compared with energetic materials such as TNT, RDX and HMX. The results exhibit that the high decomposition temperatures of NA-NO2, PP-NO2 and PB-NO2 are 338, 588 and 590 °C, respectively. More values of decomposition temperatures can indicate the thermal stability of NA-NO2, PP-NO2 and PB-NO2. This thermal stability can be attributed to pyrrole rings and π-conjugated structures in the synthesized energetic compounds. The impact sensitivity of NA-NO2, PP-NO2 and PB-NO2 was assayed and it showed that they are insensitive toward mechanical stimuli. The German Bundesanstalt für Mterialprüfung (BAM) was used to determine and calculate the impact sensitivity of NA-NO2, PP-NO2 and PB-NO2. While the impact sensitivity is generally used for determining the sensitivity of pure materials. It was found that the products are not sensitive even under heavy weights. The results showed that there was no explosion with the BAM test. While impact sensitivity of TNT, RDX and HMX decreases in the following order: 15 < 7.5 < 7 (Tables 5 and 6).
TG-DSC analysis. The thermal behavior of TG-DSC of NA-NO2, PP-NO2 and PB-NO2 were applied to the thermal decomposition performance. Fig. 11 illustrates the thermal decomposition curves of NA-NO2 (a), PP-NO2 (b) and PB-NO2 (c). It can be seen from Fig. 11a that the thermal decomposition of NA-NO2 includes two stages: in the first stage at 338 °C, an exothermic peak occurs, which is attributed to the decomposition at low temperature with a 30% mass loss. This stage of decomposition is related to the process of evaporation and sublimation. In the second stage, the exothermic peak appears at the temperature of 514 °C, which is dedicated to the complete decomposition of NA-NO2, where 66% of the mass has been lost. Fig. 11b and c are TG-DSC curves PP-NO2 and PB-NO2, respectively. The results present that both compounds go through an exothermic stage. The TG-DSC curves of PP-NO2 and PB-NO2 show similar decomposition processes. The exothermic peak in PP-NO2 and PB-NO2 appeared at 588 and 590 °C, respectively. At temperatures lower than 588 °C in PP-NO2 (b), a weight loss of about 47% was observed due to the water removal, evaporation and sublimation processes. In the case of PB-NO2 (c), these processes occurred before 590 °C with a mass loss of 46%. In both compounds, after the exothermic peaks of PP-NO2 and PB-NO2, the mass decreased by 52% and 51%, respectively, which corresponds to their complete decomposition.
 |
| Fig. 11 TG-DSC curves of NA-NO2 (a), PP-NO2 (b) and PB-NO2 (c). | |
Conclusions
To summarize, three solid bituminous hydrocarbons i.e. natural asphalt, petroleum pitch and petroleum bitumen were nitrated for the first time by a simple, low-cost and common HNO3/H2SO4 method. The nitrification reaction leads to the production of 3, 2.75 and 2.6 g and yields more than % 100 of energetic materials NA-NO2, PP-NO2 and PB-NO2 from 2 g of the substrate materials, respectively. Additionally, to explain the solubility behavior of NA-NO2, PP-NO2 and PB-NO2 compounds, diverse solvent systems were analyzed, and it was found that they were completely dissolved in aprotic solvents such as DMSO. Also, these compounds decompose at temperatures above 300 °C. The results show that these energetic materials are thermally stable and insensitive to mechanical stimuli. NA-NO2, PP-NO2 and PB-NO2 evolved very good heat of combustion of 23
500, 23
450 and 23
360 kJ kg−1, respectively. These features indicate that bitumen and its derivatives have the potential to be used as stable and insensitive energetic materials. We believe that according to the physicochemical properties and thermal behavior and the importance of the availability of cheap raw materials for the synthesis of energetic materials, the nitrated bituminous newly synthesized compounds can be expanded in a wide range of prospective applications in the field of other energetic materials.
Data availability
The data that support the findings of this study are available in the ESI.†
Author contributions
S. A.: validation, investigation, methodology, writing—original draft. M. S.: funding acquisition, supervision, project administration, conceptualization, resources.
Conflicts of interest
The authors declare no competing financial interest.
Acknowledgements
We would like to thank the Ilam University Research Council and the National Elite Foundation for their financial support.
References
- S. Muppidi, C. R. Kamatala, S. C. Voruvala and S. K. Mukka, Chem. Data Collect., 2019, 21, 100222 CrossRef CAS.
- Y.-X. Li, L.-H. Li, Y.-F. Yang, H.-L. Hua, X.-B. Yan, L.-B. Zhao, J.-B. Zhang, F.-J. Ji and Y.-M. Liang, Chem. Commun., 2014, 50, 9936–9938 RSC.
- R. Deng, K. You, L. Yi, F. Zhao, J. Jian, Z. Chen, P. Liu, Q. Ai and H. Luo, Ind. Eng. Chem. Res., 2018, 57, 12993–13000 CrossRef CAS.
- C. M. Wang, K. X. Tang, T. H. Gao, L. Chen and L. P. Sun, J. Org. Chem., 2018, 83, 8315–8321 CrossRef CAS.
- Q. L. Yan, M. Gozin, F. Q. Zhao, A. Cohen and S. P. Pang, Nanoscale, 2016, 8, 4799–4851 RSC.
- G. Tang, H. Wang, C. Chen, Y. Xu, D. Chen, D. Wang, Y. Luo and X. Li, RSC Adv., 2022, 12, 24163–24171 RSC.
- S. K. Shee, S. T. Reddy, J. Athar, A. K. Sikder, M. B. Talawar, S. Banerjee and M. A. S. Khan, RSC Adv., 2015, 5, 101297–101308 RSC.
- D. S. Kretić, I. S. Veljković, A. B. Đunović and D. Ž. Veljković, Molecules, 2021, 26, 5438 CrossRef.
- M. Tian, W. J. Chi, Q. S. Li and Z. S. Li, RSC Adv., 2016, 6, 47607–47615 RSC.
- B. Moses Abraham, RSC Adv., 2020, 10, 24867–24876 RSC.
- Y. Tang, G. H. Imler, D. A. Parrish and J. M. Shreeve, ACS Appl. Energy Mater., 2019, 2, 8871–8877 CrossRef CAS.
- T. Yan, H. Yang and G. Cheng, ACS Appl. Energy Mater., 2020, 3, 6492–6500 CrossRef CAS.
- G. Wang, T. Lu, G. Fan, C. Li, H. Yin and F. X. Chen, Chem.–Asian J., 2018, 13, 3718–3722 CrossRef CAS.
- K. Zarei, M. Atabati and S. Moghaddary, Chemom. Intell. Lab. Syst., 2013, 128, 37–48 CrossRef CAS.
- W. Yao, Y. Xue, L. Qian, H. Yang and G. Cheng, Energ. Mater. Front., 2021, 2, 131–138 CrossRef CAS.
- L. Hu, C. He, G. Zhao, G. H. Imler, D. A. Parrish and J. M. Shreeve, ACS Appl. Energy Mater., 2020, 3, 5510–5516 CrossRef CAS.
- Y. F. Gao, L. Zhang, L. He, Y. Zhao, N. Tang, W. L. Yuan and G. H. Tao, RSC Adv., 2015, 5, 54527–54534 RSC.
- X. Miao, X. Yang, Y. Li and S. Pang, Phys. Chem. Chem. Phys., 2023, 25, 18523–18544 RSC.
- J. Zhao, B. Jin, R. Peng, N. Deng, W. Gong, Q. Liu and S. Chu, RSC Adv., 2015, 5, 90422–90427 RSC.
- V. V. Chaban, E. E. Fileti and O. V. Prezhdo, J. Phys. Chem. Lett., 2015, 6, 913–917 CrossRef CAS PubMed.
- L. Chen, X. Cao, J. Gao, W. He, J. Liu, Y. Wang, X. Zhou, J. Shen, B. Wang, Y. He and D. Tan, ACS Appl. Nano Mater., 2021, 4, 1906–1915 CrossRef CAS.
- V. V. Chaban, S. Pal and O. V. Prezhdo, J. Am. Chem. Soc., 2016, 138, 15927–15934 CrossRef CAS.
- H. Kim, J. K. Cha, J. Kim and S. H. Kim, ACS Appl. Mater. Interfaces, 2020, 12, 28586–28595 CrossRef CAS.
- Y. A. Gismatulina, V. V. Budaeva and G. V. Sakovich, Propellants, Explos., Pyrotech., 2018, 43, 96–100 CrossRef CAS.
- A. El Nemr, A. Eleryan, M. Mashaly and A. Khaled, Polym. Bull., 2021, 78, 4149–4182 CrossRef CAS.
- F. Cataldo, O. Ursini and G. Angelini, Carbon N. Y., 2013, 62, 413–421 CrossRef CAS.
- G. N. Kiriro, I. W. Mwangi, S. Swaleh, R. Wanjau, P. Mbugua and J. C. Ngila, Int. J. Eng. Res. Sci. Technol., 2019, 151–163 Search PubMed.
- F. Guan, H. Ren, L. Yu, Q. Cui, W. Zhao and J. Liu, Nanomaterials, 2021, 11, 1–12 Search PubMed.
- A. Kazemzadeh and B. Mehdizadeh Naraghi, Asian J. Chem., 2012, 24, 4281–4284 CAS.
- F. Cataldo, O. Ursini and G. Angelini, Carbon N. Y., 2013, 62, 413–421 CrossRef CAS.
- H. Kohzadi and M. Soleiman-Beigi, New J. Chem., 2020, 44, 12134–12142 RSC.
- K. Okada, R. M. Nur and Y. Fujii, J. Hazard. Mater., 1999, 69, 245–256 CrossRef CAS.
- P. Chen, J. N. Metz, A. S. Mennito, S. Merchant, S. E. Smith, M. Siskin, S. P. Rucker, D. C. Dankworth, J. D. Kushnerick and N. Yao, Carbon N. Y., 2020, 161, 456–465 CrossRef CAS.
- I. N. Frolov, T. N. Yusupova, M. A. Ziganshin, E. S. Okhotnikova and A. A. Firsin, Colloid J., 2016, 78, 712–716 CrossRef CAS.
- H. Kohzadi and M. Soleiman-Beigi, Sci. Rep., 2021, 11, 24508 CrossRef CAS PubMed.
- T. Zolfaghari, M. Soleiman-Beigi and H. Kohzadi, ACS Omega, 2023, 8, 36152–36161 CrossRef CAS PubMed.
- S. Moradnejati, M. Soleiman-Beigi, E. G. Lemraski and M. Baghelani, Colloids Surf., A, 2024, 690, 133741 CrossRef CAS.
- X. He, N. Zhang, X. Shao, M. Wu, M. Yu and J. Qiu, Chem. Eng. J., 2016, 297, 121–127 CrossRef CAS.
- A. Hakimyfard, N. Zalpour and E. Sarvestan, Russ. J. Appl. Chem., 2022, 95, 756–764 CrossRef CAS.
- M. H. Keshavarz, T. M. Klapötke and M. Sućeska, Propellants, Explos., Pyrotech., 2017, 42, 854–856 CrossRef CAS.
- M. H. Keshavarz and T. M. Klapötke, Energetic Compounds: Methods for Prediction of Their Performance, Walter de Gruyter GmbH & Co KG, 2020 Search PubMed.
- M. H. Keshavarz and H. R. Pouretedal, Thermochim. Acta, 2004, 414, 203–208 CrossRef CAS.
- M. H. Keshavarz, Indian J. Eng. Mater. Sci., 2005, 12, 158–164 CAS.
- N. Kubota, Propellants and Explosives: Thermochemical Aspects of Combustion, John
Wiley & Sons, 2015 Search PubMed.
- H. Gao, Q. Zhang and M. S. Jean’ne, J. Mater. Chem. A, 2020, 8, 4193–4216 RSC.
- M. H. Keshavarz and T. M. Klapötke, The Properties of Energetic Materials: Sensitivity, Physical and Thermodynamic Properties, Walter de Gruyter GmbH & Co KG, 2021 Search PubMed.
- C. M. Tarver, Propellants, Explos., Pyrotech., 2010, 35, 494 CrossRef CAS.
|
This journal is © The Royal Society of Chemistry 2024 |
Click here to see how this site uses Cookies. View our privacy policy here.