DOI:
10.1039/D4RA04767B
(Review Article)
RSC Adv., 2024,
14, 32668-32699
A review on recent progress and techniques used for fabricating superhydrophobic coatings derived from biobased materials
Received
1st July 2024
, Accepted 7th September 2024
First published on 17th October 2024
Abstract
Superhydrophobic coatings with remarkable water repellence have emerged as an increasingly prominent field of research with the growth of the material engineering and coating industries. Superhydrophobic coatings address the requirements of several application areas with characteristics including corrosion resistance, drag reduction, anti-icing, anti-fogging, and self-cleaning properties. Furthermore, the range of applications for superhydrophobic coatings has been substantially broadened by the inclusion of key performance features such as flame retardancy, thermal insulation, resistance to water penetration, UV resistance, transparency, anti-reflection, and many more. Numerous research endeavours have been focused on biomimetic superhydrophobic materials because of their distinct surface wettability. To develop superhydrophobic coatings with a long lifespan, scientists have refined the processes of material preparation and selection. To accomplish water repellency, superhydrophobic coatings are usually fabricated using harmful fluorinated chemicals or synthetic polymers. Utilising materials derived from biomass offers a sustainable alternative that uses renewable resources in order to eliminate the consumption of these hazardous substances. This paper provides an insight of several researches reported on the construction of superhydrophobic coatings using biomass materials such as lignin, cellulose, chitosan and starch along with the techniques used for the constructing superhydrophobic coatings. This study is a useful resource that offers guidance on the selection of various biobased polymers for superhydrophobic coatings tailored to specific applications. The further part of the paper put a light on different application of superhydrophobic coatings employed in various disciplines and the future perspectives of the superhydrophobic coatings.
1. Introduction
Coating industry has gained a lot of attention in the past several years. Its application is found in almost every known field such as aerospace, food packaging, textile automobile, paint, packaging, construction, paper and many more industries.1–4 Coatings that can sense the changes in the environment and respond accordingly are referred as smart coatings. Smart coatings such as self-healing, self-clean, anticorrosive, photo responsive, pH sensitive coatings are available in the market having a wide array of applications. The main criteria to achieve self-cleaning, self-healing, anticorrosive and anti-fogging surfaces is that they must be superhydrophobic. Superhydrophobic surfaces can repel or roll off the dirt, water or pollens coming in contact. Superhydrophobic surfaces are also found in natural components such as some of the plants, animals and insects. The magnitude of intermolecular interactions between contacting liquids and solids is an important factor in many natural processes on which wettability is determined. These surfaces operate as a water barrier in plants, limiting the accumulation of water. As a result, when water meets them, the water droplets roll off the surface, keeping it clean, inhibiting the adherence of dust and pollen and stopping the growth of microorganisms. In insects such as mosquito eyes, a superhydrophobic layer serves as an anti-fogging surface. The wings and the cuticles of the insects have a layer of superhydrophobic surface preventing the cuticles or wings from getting wet and keep them light weight (Fig. 1).5 To act superhydrophobic, a surface must possess properties such as low wettability. Wetting occurs when the liquid molecules interact more strongly with the solid molecules rather than interacting with themselves, which results in spreading of liquid molecules over the surface. Thus, when wettability is low the liquid condenses to sphere resulting in a contact angle greater than 150° making the surface superhydrophobic.5
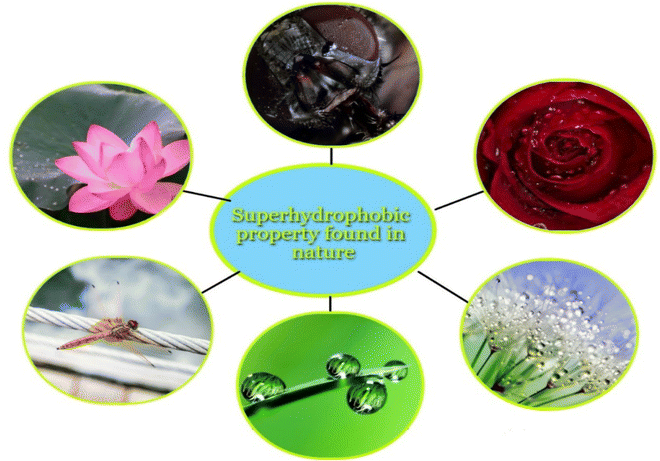 |
| Fig. 1 Superhydrophobic property found in nature: rose petals, eyes of mosquitoes, lotus leaves, cuticles of insects. | |
Contact angle refers to the angle between a tangent of the liquid droplet and a solid surface. Surface tension as well as surface energy depends on the contact angle that a liquid droplet exhibits. Surface roughness results in uneven surface which help to trap air between the gaps and prevent the accumulation of water which results in rolling off the water droplet, thus enhancing the superhydrophobic property.5 To achieve a superhydrophobic surface, it is necessary that the surface must have low surface energy and surface tension.6–8
Young, Wenzel, and Cassie–Baxter Young's theoretical models can describe the surface wetting behaviour. Where the thermodynamic equilibrium condition between the three phases i.e. solid, liquid and vapor describe the ideal and homogeneous solid surface. Surface roughness and chemical heterogeneity have a significant impact on the non-wetting characteristics of the solid surface. To understand this concept Wenzel and Cassie Baxter principles are used to evaluate the contact angle of the liquid droplet. Wenzel's model enables liquid to completely pass through the grooves, whereas Cassie Baxter's model prevents liquid from entering the pores and employs the trapped air to provide non-wetting characteristics. On superhydrophobic surfaces, a droplet of water typically exists in the Cassie–Baxter condition (Fig. 2).7,9
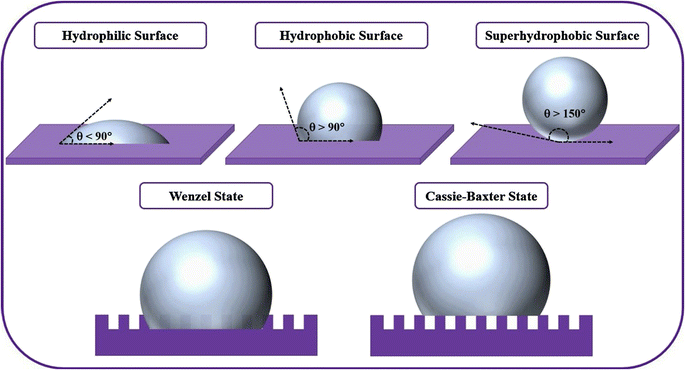 |
| Fig. 2 Representation of water droplet on hydrophilic surface, hydrophobic surface, superhydrophobic surface, water droplet in Wenzel state and water droplet in Cassie–Baxter state respectively.7 Reproduced from ref. 7 with permission from Progress in Organic Coatings (2019), copyright 2019. | |
Building widespread nano- and/or microscale roughness on a hydrophobic material with a low surface energy is one way to create superhydrophobic surfaces, and another is to modify an existing micro/nanostructured rough surface by coating it with a hydrophobic layer with a low surface energy.10,11 It has been observed that adjusting the size and dispersion of nanoparticles can influence the surface characteristics, wettability, and important coating characteristics of superhydrophobic surfaces.
2. Market of superhydrophobic coatings
Superhydrophobic coatings have gained a lot of attention over the past two decades. A lot of research has been done on superhydrophobic surfaces pertaining to its raw materials, preparations and potential applications. Being a hot research topic, several countries such as India, United States, South Korea, England, Japan, China etc. are showing interest in superhydrophobic surfaces in various disciplines such as engineering, material science, environment sciences, chemistry etc. An estimate report from QY Research (2020) that the global yield of SH surfaces was 546.29 tons in 2020 and according to the reports 29 companies worldwide deal with superhydrophobic coatings and provide meticulous analysis. Ten companies are significant for developing coatings on substrates like fabric, wood, and paper, whereas nineteen companies are significant for developing superhydrophobic coatings on smooth substrates like glass and metal. Of these, they present thirty-two commercial SH products, of which 56.3% are SH, 21.9% are SH and oleophobic, and 21.9% are superamphiphobic. Additionally, of the items, 38.3% are promoted as weather resistant, and 17.0% as abrasion resistant, 14.9% are impalement resistant, and 23.4% of the products make no mention of stability (Fig. 3).12
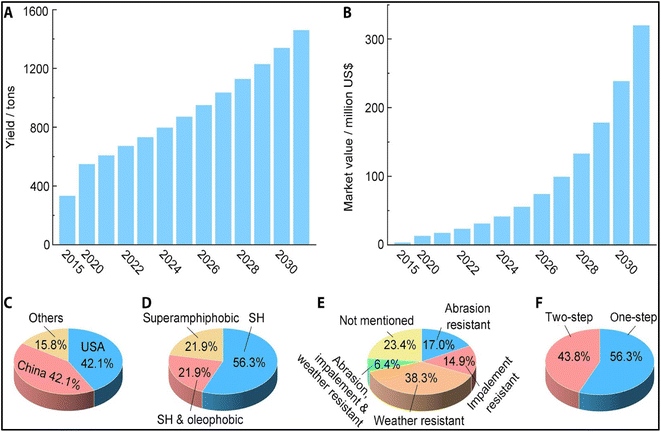 |
| Fig. 3 (A) Global yield, (B) market value of superhydrophobic surfaces. (C) Companies offering SH products that are appropriate for smooth substrates and are available commercially. Statistical evaluations of 32 marketed SH materials suitable for building SH surfaces on smooth substrates: (D) wettability, (E) stability, and (F) preparation method.12 Reproduced from ref. 12 with permission from Science Advances, copyright 2023. | |
3. Techniques for fabricating superhydrophobic coatings
The two primary techniques for creating superhydrophobic surfaces are the construction of micro- and nano-hierarchical structures on the hydrophobic substrates and the chemical modification of a hierarchically structured surface with components featuring low surface energy, such as fatty acid, polymers, hydrocarbons, and fluorocarbons. Different techniques are employed for fabricating superhydrophobic coatings. Several such techniques for fabricating superhydrophobic coating and a comparative study pertaining to their pricing, types and applications are discussed below (Table 1).
Table 1 Techniques used for fabricating superhydrophobic coatings
Techniques |
Cost |
Types |
Applications |
References |
Electrochemical deposition |
Expensive |
Anodic, galvanic, polymerization, electrodeposition, electrochemical, anodic oxidation |
Electronics, optoelectronics, photonics, magnetic devices, thermal energy storage, thermal transport, coatings, electrochromic windows, photovoltaic cells, biotechnology, life sciences |
13–15 and 16 |
Electrospinning |
Inexpensive |
Needle based electrospinning, coaxial electrospinning, tri axial electrospinning, miltichannel electrospinning, needle-less electrospinning, melt electrospinning, emulsion electrospinning, solution electrospinning |
Biomedical, drug delivery, filtration, process, energy sector, solar cell, sensors, coatings |
17 and 18 |
Wet chemical reactions |
Inexpensive |
Hydrothermal, colloidal chemistry, sono chemical, sol–gel, etching, phase transfer synthesis, precipitation |
Pharmaceuticals, polymer synthesis, photovoltaic devices, optoelectronics, ink printing, coatings |
19–21 |
Hydrothermal techniques |
Inexpensive |
Microwave-hydrothermal processing, sol gels hydrothermal methods, hydrothermal-electrochemical method, mechano-chemical hydrothermal method, ultrasound-assisted hydrothermal method, hot pressing hydrothermal method |
Electronic, semiconductors, bio-imaging, biosensors, drug delivery, coatings, gas sensor |
22–24 |
Dip coating technique |
Inexpensive |
Sol gel dip coating, spin assisted dip coating, multi-layer dip coating, vacuum assisted dip coating, photo assisted dip coating |
Self-cleaning, oil water separation, storage device, antibacterials, smart textile |
25 |
Spray coating |
Inexpensive |
Cold spray, high velocity oxy fuel spraying, twin wire arc spraying, flame spraying, atmospheric plasma, spraying, arc spraying |
Solar cell, industrial gas turbine, automotives, biomedicals, textile, paper |
26 |
Self-assembly & layer-by-layer |
Inexpensive |
Dip coating method, spin coating method, spray coating method, microfluidic method, 3D printing method |
Fuel cells, biomedical, biosensor, electrochemical devices, nanoparticles coating on microfibers |
27 and 28 |
Lithography |
Expensive |
Optical method, extreme ultraviolet method, electron beam method, X-ray method, ion beam method, soft lithography method |
Self-cleaning surfaces, microfluidic devices, smart surfaces, biotechnology |
29 and 30 |
3.1 Electrochemical deposition technique
This technique is simple, repeatable and requires less time for processing. In this technique micro and nanostructure surfaces are fabricated by electrochemical deposition. Here a thin coating is deposited on the surface using a solution consisting of charged ions or nanoparticles (Table 1 and Fig. 4).13–15 Electrodeposition can be categorized as non-metallic, composite, and metal (and its compounds) electrodeposition depending on the different types of deposition mediums used.32 Numerous factors impact the coating composition and surface design, which in turn will impact its hydrophobicity and anti-corrosion effectiveness in the electrochemical deposition process.16 The three fundamental components are the bath composition, electrodeposition time frame, and current density. To create superhydrophobic coatings, a variety of electrodeposition techniques are employed, including pulse, jet, magnetic field-induced, and ultrasound-assisted electrodeposition.33–38 In order to develop a superhydrophobic Ni–PTFE composite coating on the copper surface, Daniel et al. (2015)39 added polytetrafluoroethylene (PTFE) particles and saccharin (grain refiner) to the watt bath and electrodeposited the mixture for 30 minutes at a current density of 100 mA cm−2. The hydrophobicity of the coating surface grew progressively as the PTFE concentration in the composite deposition layer increased reaching a contact angle of 152°.39 By anodic electrodeposition in a solution containing ferric chloride and myristic acid, utilising aluminium alloy as the anode Zhang et al. (2019) developed a superhydrophobic coating with anticorrosive properties for the alloy's surface. Prior to electrodeposition, aluminium underwent oxidation to produce Al3+. Aluminium myristate was subsequently created by mixing it with CH3(CH2)COO− from myristic acid and depositing it on the anode surface. There was micro–nano structure covering the substrate's surface, with a contact angle of 155.1°.31,40
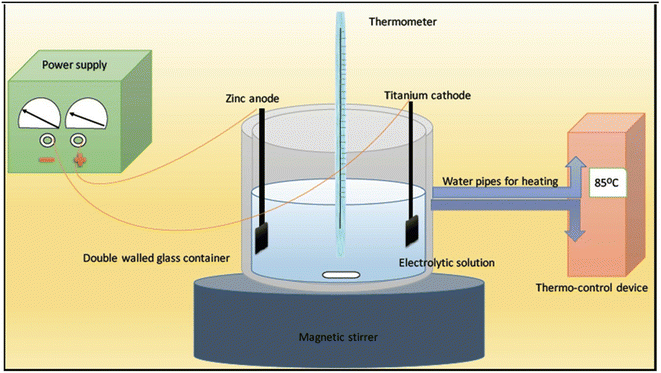 |
| Fig. 4 Electrochemical deposition technique.31 Reproduced from ref. 31 with permission from International Journal of Implant Dentistry, copyright 2017. | |
3.2 Electrospinning technique
Electrospinning technique has been determined to be the most effective method for creating nanofibers and hydrophobic coatings for nanocomposite materials, which are widely used in nanotechnology (Fig. 5). The basic components of this procedure are a roller or continuous collector, a high voltage root, and a syringe pump. Using a syringe pump, the prepared polymer solution is introduced and increased in a continuous flow, and the needle is linked to a high voltage root in the range of 3–30 kV.17,41 By using electrospinning, a broad variety of materials, such as polymers, short molecules, composites, carbon, metal oxides, metals, etc., can be spun into fibres. The widths of fibres can range from nanometres to micrometres, depending on factors such the solution concentration and viscosity, applied acceleration voltage, and molecular weight. Nanofibers' distinctive mechanical and physical characteristics, high surface-to-volume ratio, and porous structure make them ideal materials for filtration and super hydrophobicity applications. The system and process parameters are the ones that determine the fibre shape of electro spun fibres. The shape of the electro spun fibres can be changed to acquire hydrophobic surface qualities by modifying these parameter values. Spun mats that are superhydrophobic and produced employing the electrospinning method are interesting materials with a variety of applications. They serve applications in energy systems, membrane distillation, biomedical fields, oil–water separation, food packaging industries and other related areas (Table 1).17,18,42–45 By using electro-cospinning/spraying for combining silica nanoparticles and polymeric nanofibers, Su et al. (2019) developed a strong superhydrophobic composite membrane that can sustain superhydrophobicity for a prolonged period of ultrasonication.46
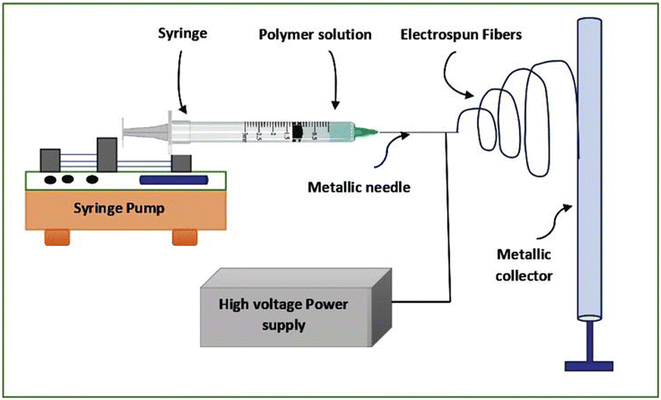 |
| Fig. 5 Electrospinning technique.17 Reproduced from ref. 17 with permission from IntechOpen, copyright 2023. | |
Since aluminium is easily susceptible to corrosion, biofouling, and the deposition of foreign elements, it reduces some of its durability when it meets liquids. In order to solve this issue, A. B. Radwan et al. (2024) created a highly corrosion-resistant superhydrophobic coating in which carbon nanotubes and poly(vinylidene fluoride-co-hexafluoropropylene) were created by spray painting and electrospinning. The dispersed carbon nanotubes were sprayed into the electro spun poly(vinylidene fluoride-co-hexafluoropropylene) (PVDF-HFP) to stop galvanic corrosion. The produced coatings demonstrated excellent corrosion resistance and a contact angle of about 156 ± 2°.47
3.3 Wet chemical reaction technique
The wet chemical reaction method is one of the most promising techniques because of its inexpensive cost, large-scale production capacity, effectiveness in controlling morphologies and dimensions of the micro/nano sized materials.48 A significant amount of work has been carried out to develop superhydrophobic surfaces that are durable employing the wet chemical strategy, which includes the sol–gel process, wet etch process, and liquid phase.19–21,49,50 In wet chemical reaction technique hydrophobic materials could potentially be introduced as post treatments subsequently on or during the synthesis process. The primary benefit of wet chemical reactions is that they just require a basic immersion to fabricate superhydrophobic surfaces. This also allows for some versatility because the technique may be used on substrates that come in a variety of sizes and forms.51 Flower-like microstructures were produced by T. Liu et al. (2007) by treating a copper surface with a tetra decanoic acid solution. The surface property changed from hydrophilic to hydrophobic and then to superhydrophobic with increasing solution concentration enabling its anticorrosive capacity against saline water.52
Using a facile immersion method Zhao et al. (2014) prepared a superhydrophobic film on magnesium alloy surface simply by immersing it in a solution of ferric chloride, tetra decanoic acid, ethanol and deionized water.53
Sol–gel one of the wet chemical reaction types is one of the most prevalent techniques for developing superhydrophobic coatings on various substrate surfaces (Fig. 6). Using this technology, colloidal particles ranging in size from 1 to 100 nm are dispersed in gels including a rigid network that is linked, submicrometer-sized voids and polymeric chains with an average length longer than 1 μm. As a result, the monomer is changed into a colloidal solution (sol), which starts the integrated network of the polymer or particle (gel). This technique can potentially be use on a wide range of substrates and doesn't require high pressure or temperature.54,55 To develop superhydrophobic copper wafer having a water contact angle of 155.4° Fan et al. (2012) first etched the copper surface in acid solution and subsequently coated it with sol–gel of vinyltrimethoxysilane, ethanol, water, and ammonia water. The prepared coating exhibited superhydrophobicity having a lot of potential to develop hierarchical structures at the micro and nanoscale with unique features, such as corrosion resistance and self-cleaning properties, delivering applications that are beneficial in a variety of sectors.56 Melina Espanhol-Soares et al. (2020) used a basic, one-step, and economical process utilizing tetraethyl orthosilicate (TEOS), citric acid, and ethanol using sol gel and spray coating processes to create a superhydrophobic coating on porous materials. Adequate hydrophobic coats were produced on the cotton fabric by using citric acid as the precursor for sol production. Greater hydrophobicity was achieved in the sol–gel solution by higher citric acid concentrations.57
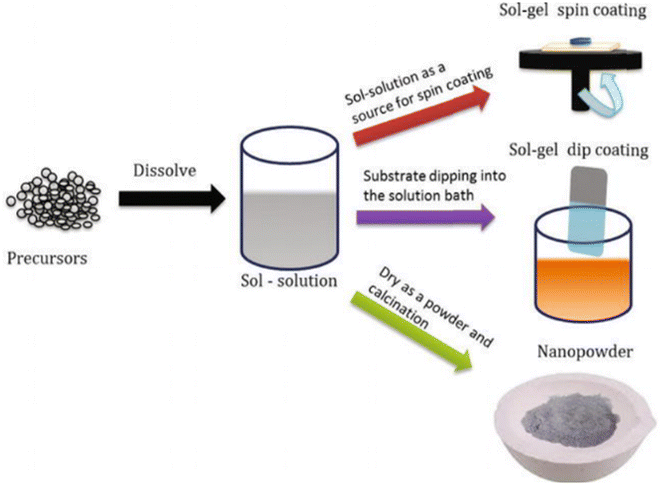 |
| Fig. 6 Sol–gel technique.54 Reproduced from ref. 54 with permission from InTech, copyright 2017. | |
3.4 Hydrothermal synthesis technique
In this process crystalline materials are synthesized under high pressure from heated aqueous solution. By applying high pressure surface roughness is achieved. It is an effective technique for synthesizing nanomaterials having unique and remarkable morphologies (Fig. 7). Since hydrothermal techniques simply require water or diluted H2O2 to form surface microstructures, they are considered to be more environmentally benign (Table 1).22–24,58–60 A simple, economical, one-step hydrothermal process was used by Feng et al. (2017) to create a superhydrophobic magnesium alloy surface. The resulting surface, which had a rough, hierarchical micro- and nanostructure, demonstrated outstanding corrosion resistance and self-cleaning capabilities.61 Using hydrothermal reaction and spraying techniques, Tao Zhang et al. (2023) created a superhydrophobic coating known as Al/ZnO–P.I.Z–FAS@PDA. The coating demonstrated qualities including wear resistance, self-cleaning, frost resistance, and corrosion resistance.62
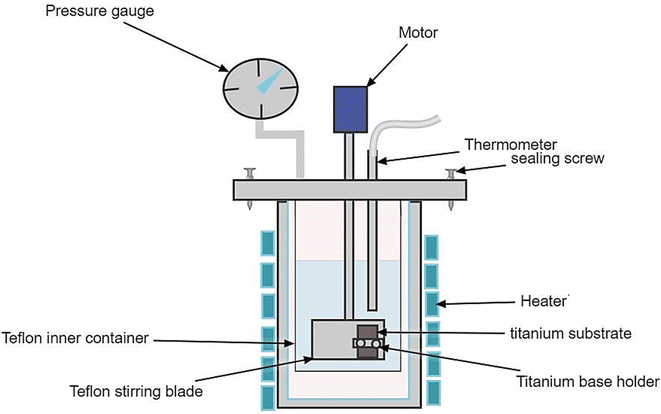 |
| Fig. 7 Hydrothermal synthesis technique. | |
3.5 Dip coating technique
Dip coating method is usually used for fabricating functional layers (Fig. 8). A wet liquid film is deposited by immersing the substrate in a solution containing desired materials and then drawn out into an atmosphere that contains water vapor. It is simple, inexpensive, dependable, and repeatable. A uniform liquid layer forms on the substrate's surface upon the substrate's removal from the solution. The volatile solvents evaporate leaving behind a thin coated layer on the substrate.25,63 The pace at which the substrate is drawn out of solution determines the film's thickness. The film formed is thinner when the substrate is drawn out at a faster pace. Dip coating technique serve advantages such as high output, uniformity, extreme durability, compactness, stable coating, ease of repair, and simultaneous coating of the substrate's top and bottom portions (Table 1).25,55 To enhance the hydrophobicity of a superhydrophobic epoxy paint through sandblasting and anchoring of SiO2 nanoparticles, Cui et al. (2009) dip coated it with modified epoxy adhesives.64 Using a vacuum dip coating process, Liu et al. (2010) constructed a compact nano TiO2 coating on an anodized aluminium surface serving an advantage of preventing corrosion in seawater.65 Using the organic–inorganic silica precursor methyltrimethoxysilane (MTMS) on quartz substrate employing the dip coating process, Mahadik et al. (2013) created a superhydrophobic coating.66
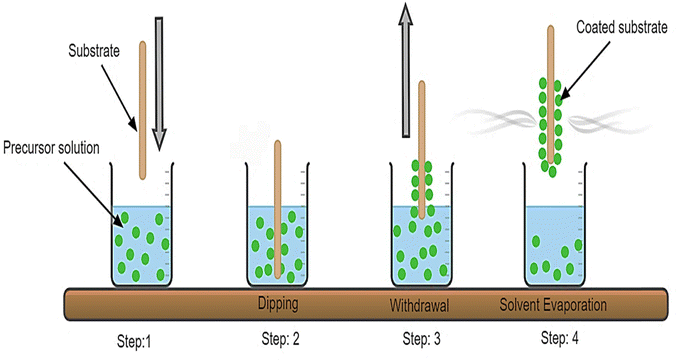 |
| Fig. 8 Dip coating technique. | |
3.6 Spray coating technique
In this technique, a spray gun is used for spraying a coating solution to the substrate (Fig. 9). Usually, heat or chemical techniques are used to melt the coating precursor. Numerous benefits come with this technique, including its simplicity, high availability, automation potential, speed, affordability, repairability, furthermore, this process may be used on substrates like textiles, metals, and plastics (Table 1).26,55,67 Xiang Liu et al. (2021) developed conductive superhydrophobic coating using simple layer by layer spray coating technique where the bottom layer consisted of polyphenylene sulfide (PPS) dissolved in ethanol and sprayed on the substrate then the top layer was prepared adding modified. After being stirred in ethanol for two hours under ultrasonic agitation, carbon nanofibers (CNFs), polytetrafluoroethylene (PTFE), CeO2 particulates, PPS, and PDMS were sprayed onto the bottom layer to create a conductive superhydrophobic composite coating. This coating was then cured by heating the sprayed samples at 330 °C for two hours.68 Assem Elzaabalawy et al. (2020) developed a economic and scalable spray coating fabrication technique using epoxy silica nanocomposite to construct robust and durable superhydrophobic coating where they modified epoxy using an amino functionalized polysiloxane to overcome its inherent high surface energy exhibiting a contact angle of approximately 165° and slide angles of about 3° on several substrates such as metals wood glass and textile.69
 |
| Fig. 9 Spray coating.67 Reproduced from ref. 67 with permission from IntechOpen, copyright 2022. | |
Many studies have been reported where anticorrosive and self-healing coating are developed using spray coating technique. To widen the range of applications for superhydrophobic coatings, durability is a vital aspect. With a purpose of enhancing the durability of the coatings Dawei Li et al. (2021) constructed a superhydrophobic coating using a simple and affordable process with a raw material consisting of fluorine-free suspension made up of lamellar mica powder (MP), functionalized SiO2, multilayer graphene oxide (GO), and epoxy modified silicone resin (MSR). The developed coating was capable of enduring a range of mechanical durability tests, intense UV radiation and cycles of high and low temperatures for seven days along with powerful chemical treatments. Furthermore, the coating had an exceptional self-healing capacity to withstand O2 plasma etching, along with self-cleaning property and corrosion resistance.70 By combining nano zinc oxide (nano-ZnO) and polydimethylsiloxane (PDMS), Xuewu Lui et al. (2022)71 developed a fluorine free anticorrosive, self-healing and environmentally friendly superhydrophobic composite using spray coating techniques. They reported a contact angle of 158.3 ± 1.7° and sliding angle of 6.2 ± 1.8° exhibiting an appreciable mechanical strength and abrasion resistance providing applications in different disciplines.71
3.7 Self-assembly technique and layer by layer deposition technique
The self-assembly technique assists in assembling an ordered system from its constituent parts, which were previously disordered (Fig. 10). The coating layers are produced with limited intervention and at a low temperature. With little assistance, it creates intricate structures. It produces the layer at a low temperature without the need for pricey machinery or a difficult procedure (Table 1).55,72 It has profound implications regarding the manner in which thin-film technology is developed. Layer by layer deposition technique builds multilayer grafts by using covalent bonding and electrostatic contact. It is a simple and inexpensive technique to develop alternating layers of thin-film coatings and can be employed to produce a wide range of materials, such as biological molecules, metals, polymers, ceramics and nanoparticles.27,28 A variety of approaches such as dip coating, spin coating, and spray coating assisted LBL approach are used in LBL procedures for deposition. By using LBL deposition technique Bravo et al. (2007) constructed a superhydrophobic glass surface on silicon wafer exhibiting high transparency and anti reflective properties.73
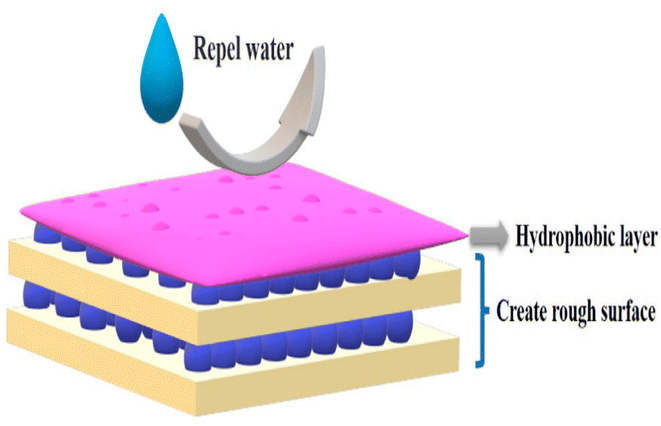 |
| Fig. 10 Self-assembly technique and layer by layer deposition technique.72 Reproduced from ref. 72 with permission from Molecules, copyright 2022. | |
With fullerene pyridyl derivatives, Yin et al. (2009) created thin gold films and self-assembling gold nanoparticles at the water–toluene interface. Because these materials are self-cleaning and self-repairing, they have important applications in optical, electrical, biosensor, and catalytic materials. Moreover, they display a 157° contact angle.74
3.8 Lithography technique
This method uses conventional chemical processes to generate a visual representation (Fig. 11). It generates two parts: a positive part that repels water and a negative part that retains water. This technique can generate a variety of patterns, such as star-shaped pots, squared pillars, circular pillars, and indented square pots with varying heights, diameters, and spacing. There are several methods for doing lithography such as photolithography, electron beam lithography, electron beam lithography, nano-imprint lithography, interference lithography (Table 1).29,30,75 Qi et al. (2009) generated pyramidal hierarchical structure on crystalline silicon wafer by employing KOH etching and silver catalytic etching which showed strong anti-reflection and superhydrophobicity after fluorinations. They achieved this by using the UV-assisted impression lithography process, which dispersed the Si structure throughout the film to generate the superhydrophobic substrate.76 Using electron beam lithography on wafer surfaces, Feng et al. (2011) built an appropriate roughness of the macroscopic hierarchical structure. After silanization, the wafer surfaces transformed to superhydrophobic with low surface energy and exhibited a contact angle of 160°.77 This technique is also used for preparing antifogging coatings which focuses on modification of surface roughness and building functional surface patterns directly on the substrates to develop antifogging behavior.78 By using this technique a polydimethylsiloxane (PDMS) elastomer-based monolithic micropillar structure was constructed, after which hydrogel micropatterns were assembled using inkjet printing in between the micropillar array to develop flexible, wet-style superhydrophobic anti fogging tapes by Hyeongjeong Kim et al. (2024) holding a broad range of applications for transparent materials and curvatures.79
 |
| Fig. 11 Lithography technique.75 Reproduced from ref. 75 with permission from Elsevier, copyright 2016. | |
Superhydrophobic coatings have several engineering applications such as self-clean, anti-corrosive anti-fouling, anti-fogging and anti-icing which to a greater extent decrease maintenance and work expenses also resulting in longer lifespan of metals as well as other materials used in day-to-day life. As these superhydrophobic coatings have a wide array of applications, its demand in the commercial market is increasing enormously but as these superhydrophobic coating are synthesized using petrochemicals and other harmful chemicals which are responsible for factor such as climate change, global warming, greenhouse effects, toxicity and further these non-renewable petrochemicals resources are depleting over the decades there is a need to look for an alternative. Biopolymers being abundantly available, renewable and non-toxic can prominently hold its strong position in the field of coatings.
4. Biopolymers used for constructing superhydrophobic coatings
The emergence of biopolymers has enabled researchers to look for a sustainable alternative to conventional petroleum derived materials. Biobased polymers are derived from biomass (polysaccharides, proteins and lipids). In some cases, biobased polymers are synthesized by epoxidation or acrylations of biobased monomers derived from natural oils. These biobased polymers can provide multiple functionalities and have extensive applications in the coating industry. Surface characteristics such as adhesion, wettability, water repellency, self-healing, anti-corrosion etc. can be improved using functionalized biobased polymers. Constant efforts are made to develop biobased coatings that have properties such as good mechanical strength and water resistance which match the performance with the conventional coating. Extensive research is carried out on biobased materials to build surface roughness and low wetting behaviour to develop superhydrophobic coatings. Several researchers have successfully developed self-healing, self-cleaning, anti-corrosive and flame retardant superhydrophobic coatings.
Quan-Yong Cheng et al. (2018) designed superhydrophobic coating by employing a spray coating technique on cotton substrate, using stearic acid as a low surface energy modifier, nano ZnO particles for roughness, and epoxidized soybean oil as an adhesive.80
With an aim to create a superhydrophobic surface on the cotton surface Qingbo Xu et al. initially etched the cotton fabric with phytic acid (PA), this roughened the fiber surface and therefore increased the fabric's surface roughness. The treated cotton fabric was then coated with stearic acid (STA) and epoxy soybean oil (ESO), which greatly decreased the fiber's surface energy. The final cotton fabric had a water contact angle of 156.3° and demonstrated outstanding superhydrophobic qualities. Regardless of the liquid pollutant or solid dust, the final cotton fabric's superhydrophobic coatings gave it exceptional self-cleaning qualities.81
Nanoparticles can help enhance properties such as surface morphology, for example, surface roughness making a coating superhydrophobic and are predominantly used to construct a new functionality along with improved performance in these biobased superhydrophobic coatings.82 Khairul Arifah Saharudin et al. (2018) used non-fluoro polydimethylsiloxane (PDMS) and waste palm oil fuel ash (POFA) to generate a superhydrophobic coating on the glass surface using a spray coating technique.83 Shen et al. (2020) fabricated non wettable coating for packaging application by spray coating soybean wax suspension in ethanol.84 Zhong et al. (2020) developed a bio-based liquid-repellent coating system using polydimethylsiloxane (PDMS) and hexamethoxymethylmelamine (HMMM) as liquid-repellent and curing agent respectively which showed exceptional water repellency, self-cleaning anti-graffiti and anti-fingerprint properties.85 Xinghua Wu et al. (2021) developed a breathable, anti-condensation superhydrophobic coating on cementitious substrate using biobased epoxy resins exhibiting its practical applications in resolving problems such as cracking, scaling and help improve the durability of modern buildings.86 Nusrat Celik et al. (2023) develop self-healing superhydrophobic coating using silica nanoparticles and carnauba wax where the coating not only exhibited self-healing and water repellency but was thermally stable after healing.87,88
Xiangzhao Wang et al. (2024) constructed a fully biobased epoxy vitrimer by curing epoxidized soybean oil (ESO) with a biobased imine containing curing agent that was obtained from 1,10-diaminodecane and vanillin. This was accomplished in a green, sustainable, photothermal, and recyclable approach. The ESO-based vitrimer's surface was coated with multiwalled carbon nanotubes (MWCNTs) to provide the superhydrophobic characteristic. Multiwalled carbon nanotubes (MWCNTs) enabling the formation of micro/nanostructures on the surface of the vitrimer which resulted which resulted in excellent anti/deicing and photothermal deicing property.89
Several research institute and scientist are in-exhaustively conducting research on superhydrophobic coating derived for biobased materials. Lignin, cellulose, chitosan and starch are extensively explored due to their easy availability, biodegradability and low cost. Superhydrophobic coatings developed from lignin, cellulose, chitosan and starch are discussed below.
4.1 Lignin
Lignin is a group of complex oxygen carrying organic polymers and is the second most abundant organic material found on the earth. It is found in plant cell walls and is hydrophobic in nature. Considering its availability and hydrophobic property it has huge potential to compete with the conventional hydrophobic coatings derived from fossil fuels which are rapidly exhausting.90,91 Lignin as a macromonomer can be utilized as a thermo-precursor in polyurethanes, polyesters epoxides and phenolic resins. Several studies are being conducted in a prospect to make use of lignin as a raw material for synthesizing polymer composites and adhesives.92 Being less hydrophilic than the other biopolymers it is found to have properties such as low wettability, UV resistance, antioxidant and antimicrobial properties. Thus, apart from the pulp and paper sector, lignin has significant possibilities for availability in biorefineries and offers interesting uses in the fields of polymer coatings, adsorbents, wood veneers, food packaging, biomaterials, fertilizers, corrosion inhibitors, and antifouling membranes.93,94
Jingda Huang et al. (2017) in their research instead of only working on cellulose nanocrystal (CNC) they used lignin-coated cellulose nanocrystal (L-CNC) aggregate. These particles possessed irregular sizes and had a rough surface comprising many hydroxyl groups which can be modified to provide hydrophobicity. They utilized low energy reagents to modify (L-CNC), followed by that, they used a sieve to evenly distribute the particles over an adhesive surface—such as double-sided tape or quickly-setting epoxy—and rolled them with a wooden bar. The resulting coating demonstrated exceptional mechanical strength against water jets, sandpaper abrasion, finger wipes, and knife scratches. It was also superhydrophobic, durable against high temperatures, acid and alkali solutions, and UV radiation (Fig. 12).95
 |
| Fig. 12 Illustration displaying the procedure for developing the composite superhydrophobic coating.95 Reproduced from ref. 95 with permission from Materials, copyright 2017. | |
A solvent free, cost effective, and scalable superhydrophobic coating was developed by Yajie Zhong et al. (2019) using fluoroalkyl silane modified lignocellulose nanofibrils (LCNFs) derived from low-cost wheat straws. Due to easy scalability and low cost of wheat straw these coatings have a potential application for a wide range of materials for self-cleaning surfaces. Studying that the edible lignin extract from the coffee beans have an ability to maintain micro and nanoscale structures Yiwen Zhang et al. (2019) fabricated superhydrophobic coatings using lignin and beeswax by simple scalable spray coating method which exhibited excellent adhesion to the substrate and thermal stability.96
In modern times, lignin can potentially be efficient and significantly add high value by utilizing lignin nanoparticles (LNPs).97 As lignin nanoparticles are non-toxic, environmentally resistant, have high thermal stability, and are biocompatible, they may find use as antioxidants, thermal/light stabilizers, reinforced materials, anti-UV materials, emulsion stabilizers, and nano/microcarriers.98 Owing to these characteristics Hang Wang et al. (2021) worked on self assembled lignin where they fabricated covalent–noncovalent forces stabilized lignin nanospheres (HT-LNS). Solvent exchange was used to generate LNS based on noncovalent bonds, which were then hydrothermally treated in a water environment to cross-link covalently. Thus, by taking advantage of the natural characteristics that lignin molecules go through when stimulated at high temperatures a new perspective for preparing enriched products derived from lignin was explored. When the coating was prepared, the nanospheres were not required to be hydrothermally treated; instead, they dissolved when organic solvents were applied, forming a thin coating that suggests lignin nanospheres stabilized by covalent–noncovalent forces can be used to prepare superhydrophobic coatings that can replace silica nanoparticles.99 In another work done by Changying Ren et al. (2022), they synthesized fluorine free superhydrophobic coating using hydrothermally treated lignin nanospheres (HLNP) replacing inorganic particles. They combined modifiers viz.; methyltrimethoxysilane (MTMS) and hexadecyltrimethoxysilane (HDTMS), along with the cellulose nano crystals and PDMS working as reinforcer and adhesive respectively were mixed with HLNPs and sprayed onto the wood surface. The prepared HLNPs/CNC/PDMS coating exhibited good thermostability, excellent UV resistances and a contact angle of 167°.100 Mengmeng Li et al. (2022) in their research prepared a superhydrophobic surface by mixing lignin nanospheres (LNPs) as a main structural material replacing inorganic particles, cellulose nanocrystals (CNCs) as a reinforcement material and PVA as an adhesive. Further to reduce surface energy perfluorooctyltrichlorosilane (FOTS) was added to obtain a superhydrophobic surface having appreciable mechanical strength against abrasion, longer UV resistance ascribed to ultraviolet absorption property and light stability of lignin (Fig. 13).101
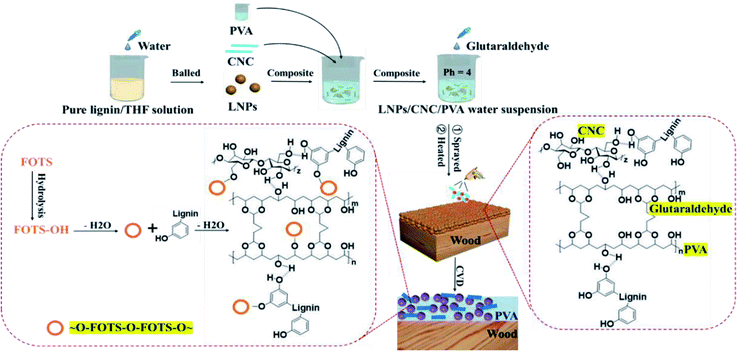 |
| Fig. 13 Schematic representation of the steps required for developing a superhydrophobic surface based on LNPs and the possible chemical reactions that may occur (FOTS).101 Reproduced from ref. 101 with permission from RSC Advances, copyright 2022. | |
To overcome the problem of poor mechanical strength, stability, faster aging of superhydrophobic coatings Jingda Haung et al. (2023) prepared an organic–inorganic coating where they utilized hydrothermal treated lignin nanoparticles (HLNPs/Fe3O4) composite as a prime material to construct a surface roughness for superhydrophobicity along with CNC and TiO2. The compatibility of CNC and TiO2 allowed them to disperse well with each other providing good abrasion resistance without affecting other properties. To evaluate the performance of the prepared coating on different substrates the coating was applied on wood and PU sponge where the coating on wood exhibited excellent superhydrophobicity and abrasion resistance and the coating on PU sponge showed appreciable oil absorption. Additionally, these coatings also endowed magnetic and flame-retardant properties (Fig. 14).102
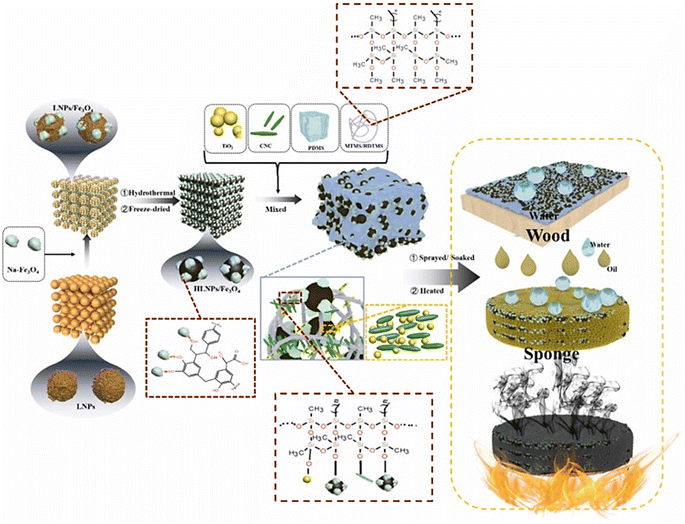 |
| Fig. 14 Diagram illustrating the superhydrophobic coating's fabrication procedure using HLNPs and Fe3O4.102 Reproduced from ref. 102 with permission from Journal of Environmental Chemical Engineering, copyright 2023. | |
Kraft lignin, a by-product from pulp and paper industries was explored for constructing superhydrophobic coating by Xue Liu et al. (2022) where they developed a low cost kraft-based lignin powder utilizing modified kraft lignin via 1H,1H,2H,2H-perfluorodecyl-triethoxysilane (PFDTES) substitution process. Subsequently, a superhydrophobic layer was produced by directly spraying the PFDTES–lignin powder over a range of substrates, including paper, metal, wood, and glass. These coatings possessed outstanding water repellency, had contact angle greater than 150° along with good friction resistance, acid, alkali and salt resistance. Additionally, these coatings maintained their superhydrophobicity even after 30 sandpaper wear cycles and 30 minutes of immersion in solutions containing 2 mol L−1 HCl, 0.25 mol L−1 NaOH, and 2 mol L−1 NaCl (Fig. 15).103
 |
| Fig. 15 Diagrammatic representation of the modification of lignin and the process of fabricating a durable superhydrophobic coating.103 Reproduced from ref. 103 with permission from Molecules, copyright 2022. | |
In another study Junsik Bang et al. (2022) developed a biobased wood hydrophobic coatings by blending Kraft lignin and carnauba wax where lignin was found to increase the micro roughness of the coated layer to attain wetting resistance along with improved physical stability due to robust interaction between wood surface and the coated layer.104
4.2 Cellulose
Cellulose is an inexhaustible biopolymer available on earth and profoundly used as a raw material in paper and cotton fibre industry.105 It has high thermal resistance and can help shield the UV rays. Cellulose based fibers have several essential properties such as decomposability, renewability further they have application in many polymer composites as they are burnable and non-toxic.106 As cellulose have more number of hydroxyl groups on the glucose rings there is an extensive hydrogen bonding observed between individual cellulose chains resulting in crystalline and amorphous areas which enables cellulose to possess properties such as high strength, durability, biocompatibility and stiffness. Nano cellulose is transparent, biodegradable, low density, and have stiffness higher than Kevlar fiber. Films prepared from nanocellulose are gaining a lot of importance due to easy fabrication processes. These nano cellulose coatings have potential applications in packaging, biomedical, green electronic industries.105,107 Research on the use of cellulose nanocrystals in functional materials is now an intensive field, with several researchers devoting their time to the investigation of this remarkable material. It is fascinating to alter and functionalize cellulose nanocrystals as it makes it possible to produce cutting-edge materials with novel or enhanced characteristics.108,109 Several successful attempts are reported where cellulose nanocrystals are used for fabricating coatings for various applications. While exploring the potentials of cellulose nanocrystals in the area of superhydrophobic coatings Quan-Yong Cheng (2018) fabricated renewable and degradable superhydrophobic coating for cotton fabric using dip coating method. For this they used cellulose nanocrystals as rough structure components, cured epoxidized soybean oil (CESO) as a binder and hexadecyltrimethoxysilane (HDTS) as a low surface energy modifier.110
In order to produce rough annular microparticles possessing hierarchical dual dimensions, Zhaodong Zhu et al. (2020) employed thermally aggregated of spray drying technique to accomplish uniform structure of cellulose nanocrystals (CNC) and carbon nanotubes (CNT). Cellulose nanocrystals (CNC) with carbon nanotubes (CNT) and waterborne polyurethane (PU) (CNC/CNT/PU) were first dispersed uniformly using ultrasound to get CNC/CNT/PU microparticles (CCPmp) which was further modified with methyltrimethoxysilane (MTMS) to provide low surface energy which resulted in (MCCPmp). Then finally (MCCPmp) and PDMS were dispersed in THF employing sonicator and then sprayed on a filter paper resulting in a superhydrophobic (MCCPmp) coating on the filter paper. The coating exhibited remarkable water in oil emulsion separation ability. Structure and characteristics of CNC proved significant for microparticle assembly and superhydrophobic modification. These coatings exhibited good abrasion resistance, electrical conductivity, antibacterial property and fast and easy water removal property which was achieved due to the efficient role of CNT (Fig. 16).111
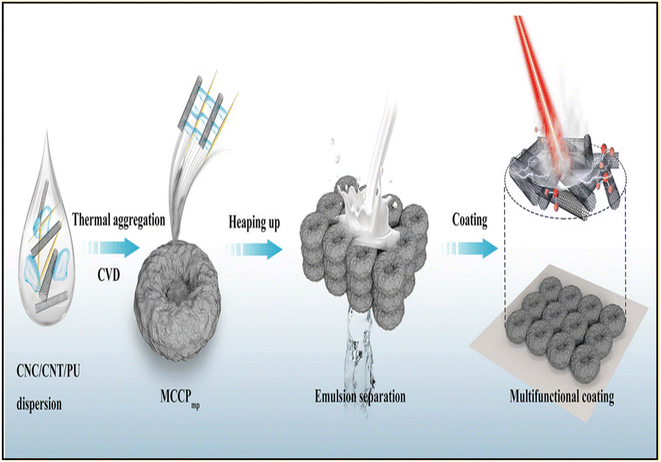 |
| Fig. 16 A schematic illustration of the multipurpose, durable, superhydrophobic coating's preparation procedure for swift and intelligent water removal.111 Reproduced from ref. 111 with permission from Carbohydrate Polymers, copyright 2020. | |
In another studies H. Xiang et al. (2022) prepared superhydrophobic coating with a sustainable approach utilizing cellulose nanocrystals, where octadecylamine (ODA) was anchored on the surface of CNC by the self-polymerization of tannic acid and Michael addition reaction between poly tannic acid coated CNCs (PTA@CNCs) and ODA. The developed ODA–PTA@CNC was dispersed in ethanol and coated to substrates like paper, cotton, and polyurethane. The exceptional superhydrophobicity was achieved due to the low surface energy of ODA and the multiscale roughness of the CNC nanorods. ODA–PTA@CNCs have a lot of potential uses in waterproof packaging, antifouling, and breathable textiles (Fig. 17).112
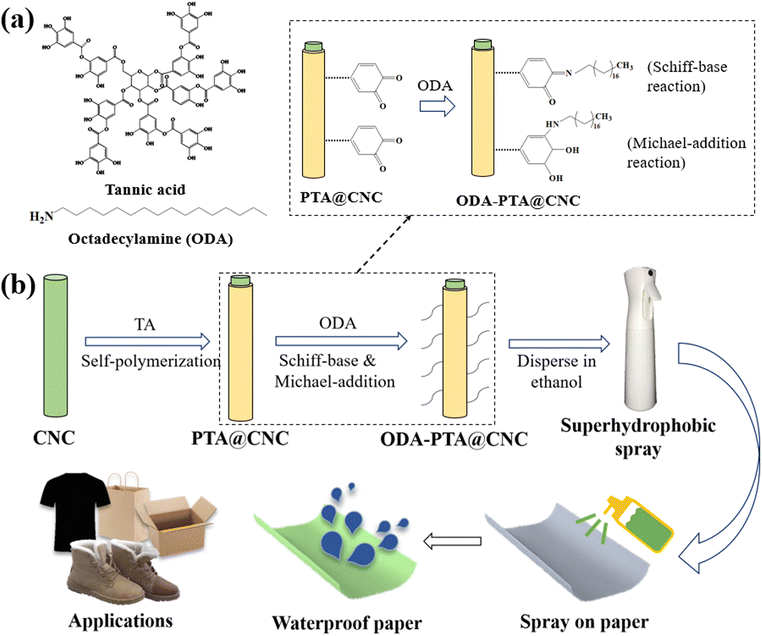 |
| Fig. 17 (a) Chemical reaction occurring the of preparing superhydrophobic coating. (b) Schematic representation of preparing superhydrophobic coating using CNCs (PTA@CNCs) and ODA and its applications.112 Reproduced from ref. 112 with permission from ACS Sustainable Chemistry & Engineering, copyright 2022. | |
Further, to resolve the challenge of low hydrophobicity and poor abrasion resistance of the wood, Zhupeng Zhang et al. (2023) used cellulose nanocrystals (CNC)–SiO2–phosphorylated lignin (PL) rods to prepare superhydrophobic coating. SiO2 was built in situ on (CNC) surface and was further modified by attaching lignin. Polydimethylsiloxane (PDMS) and epoxy resin both served as an adhesive. The application of this CNC@SiO2@PL coating was done simply by rolling or by spraying. These coatings showed excellent superhydrophobic properties owing to contact angle of about 157.4° and slide angle of 6°. Excellent mechanical strength and improved abrasion resistance was observed in this coating due to the high crystalline nature of cellulose (Fig. 18).113
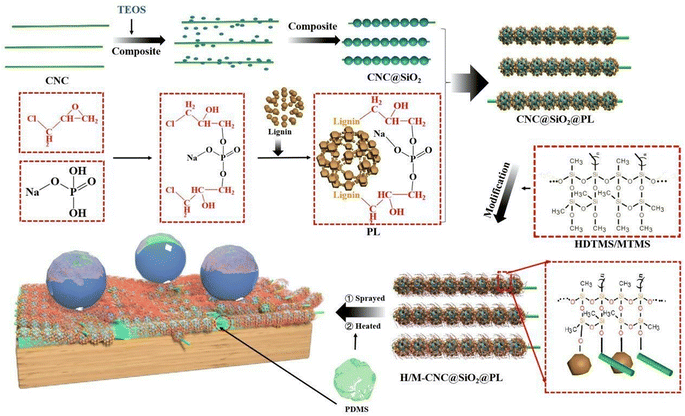 |
| Fig. 18 Scheme for preparation of superhydrophobic coatings using cellulose nanocrystals (CNC)–SiO2–phosphorylated lignin (PL) rods.113 Reproduced from ref. 113 with permission from Polymers, copyright 2023. | |
The hydrogen bonding between the hydroxyl groups of the surrounding fibers help build a robust fibrous network when cellulose fibers are reduced to either microfibres or nanofibres. As a result, when compared to nominal cellulose fiber sheets, such as paper and paper boards, the mechanical characteristics of the film formed from cellulose nanofibres stand superior.114 With an ecofriendly approach, Xi Chen et al. (2022) prepared superhydrophobic coating by utilising water as a dispersing medium. Methyltrimethoxysilane (MTMS), a surface energy modifier and hydrophobic SiO2 nanoparticles were dispersed in water assisted with cellulose nanofibers in order to avoid the use of organic/inorganic solvents. The SiO2@CNF-M coating exhibited a contact angle of 162°. It was observed that the presences of cellulose nanofibers improve the dispersion of SiO2 in water (Fig. 19).115
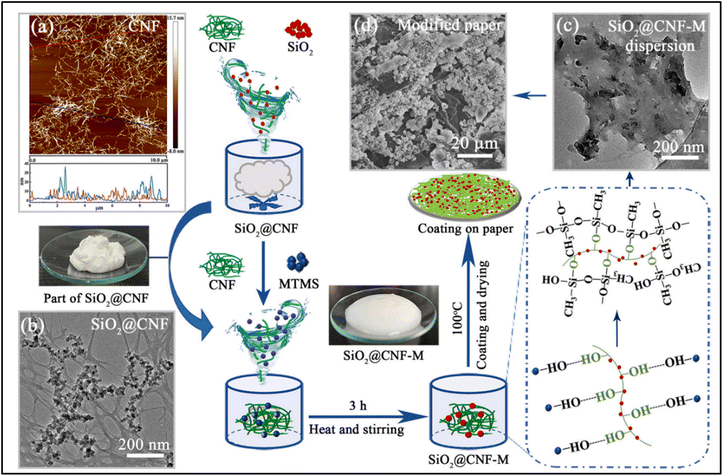 |
| Fig. 19 Schematic representation of fabricating SiO2@CNF-M water dispersion and the coating. (a) The AFM morphology of CNF. (b) The SiO2@CNF and (c) SiO2@CNF water dispersion's TEM morphology. (d) SiO2@CNF-M coated on paper SEM morphology.115 Reproduced from ref. 115 with permission from Carbohydrate Polymers, copyright 2022. | |
In another rare earth metal such as cerium dioxide was synthesized by Fan Xinyan et al. (2023)116 on the surface of cellulose nanofibers by co-precipitation method using cerium nitrate hexahydrate (Ce(NO3)3·6H2O) in different ratios to prepare cellulose based superhydrophobic coatings. The contact angle of these coating was found to exceed 150° having application on several substrates and showed excellent self-cleaning ability. Further this superhydrophobic coating not only was used as protective coating but also extends the application of rare earth metal oxidate in cellulose based superhydrophobic coatings.116 In another work by Taoran Wang and Yanyun Zhao (2021) designed a double layer superhydrophobic coating by first employing surfactant-free beeswax or camellia wax emulsions to provide the coatings low surface energy and high surface roughness. And the second layer was made up of cellulose nanofiber (CNF) and zein particles (ZP) or precipitated calcium carbonate PCC/CNF with varying thicknesses. Several types of liquid food were able to just roll as spheres without leaving a trace on the coatings. The second layer consisting of (PCC)/CNF showed improved mechanical properties and excellent thermal and cold stability. These superhydrophobic coatings prepared from biodegradable materials have several applications in the food packaging industry.117 With an innovative approach Kai Yi et al. (2022) fabricated fluorescent cellulose based multifunctional coating by grafting 5-(4,6-dichlorotriazinyl)aminofluorescein (DTAF) onto cellulose nanofiber (CNF) to produced −8 μm microparticles and then was hydrophobically modified using methyl trimethoxy silane combined with polydimethylsiloxane (PDMS) to attain superhydrophobicity and was coated on different substrate exhibiting a contact angle of about 156.6° and slide angle less than 10 along with abrasion resistance and acid resistance and had a promising performance in outdoor acid resistance for luminous decorative materials and anti-counterfeiting materials.118
Undecenoate cellulose esters (UCEs) with different degree of substitution (DS) can be used to construct superhydrophobic coating, the degree of substitution (DS) is the average number of substituents per anhydroglucose unit (AGU) and can range from 0 to 3 and have significant impact on the coating.119 Xiangyu Tang et al. (2021) used UCEs with DS of 1.9 comprises of spherical nanoparticles (NP) having arrangement of 112.8 nm. Further, self-assembly of these UCEs1.9 resulted into microparticles (MPs) from nanoparticle (NPs) by solvent exchange method. Further these form microparticles (MPs) were well dispersed in ethanol and sprayed on different substrates. The contact angle of these novel superhydrophobic coatings was greater than 150°, whereas the sliding angle was smaller than 10° and are projected to be a guaranteed competitor for developing biodegradable superhydrophobic coating material derived from sustainable cellulose.120
Decorative materials coated with superhydrophobic coating provides a long term durability and keep the materials aesthetically pleasing. In a study reported by Jinping Ren et al. (2021), color-tunable, strong superhydrophobic coatings were constructed using micro–nano particles of cellulose, chitosan, zein, and polytetrafluoroethylene (PTFE) combined with three primary dyes (methyl blue, methyl orange, and rhodamine B), 1H,1H,2H,2H-perfluorodecyltrimethoxysilane (FAS) that offered low surface energy, and [3-(trimethoxy silyl)propyl]ethylenediamine (AS) as an adhesive that adhered strongly to the substrate. This prepared superhydrophobic coating exhibited excellent water repellency, sandpaper abrasion resistance and can be used as a pigment for painting on a variety of substrates and has a promising potential in prolongation of artwork and decor materials (Fig. 20).121
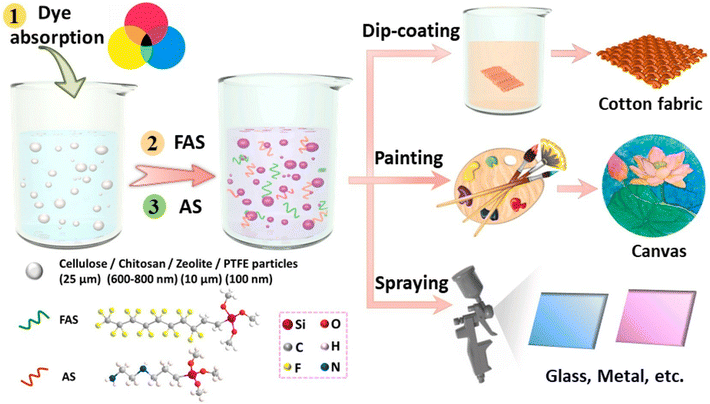 |
| Fig. 20 A schematic representation of preparation procedure of multi-coloured superhydrophobic coatings.121 Reproduced from ref. 121 with permission from Carbohydrate Polymers, copyright 2021. | |
An effective way to control light glare along with better light transmission and diffusion while conserving energy is by employing light management films. To deal with the problems associated complex fabrication using petroleum based polymers for constructing light management (LM) films which enables the regulations of transmitted light holding remarkable applications in the field of optoelectronics and energy-efficient buildings Yijia Song et al. (2021) developed a novel, sustainable superhydrophobic lignocellulose films possessing appreciable light management property enabled due to easy dissolution of wood pulp and effortless regeneration of corncob residue from xylitol production. The film was further spray coated with SiO2 nanoparticles to built superhydrophobic property. The prepared film possessed good transparency, high haze and significant UV resistance property providing stable indoor light distribution and can hold potential application in UV radiation shielding of smart buildings.122
In an attempt to mimic lotus leaf surface Hu Yucheng et al. (2023) developed biomimetic superhydrophobic cellulose-based composites by starting with a simple approach of mimicking the structure of a lotus leaf. For doing so, they employed precision imprinting to create a microstructure, followed by in situ grafting of low surface energy nanoparticles onto the surface of the cellulose composite films. With its self-cleaning ability, strong mechanical properties, biodegradability, and optical capabilities, the prepared biometric superhydrophobic cellulosic composite (BSCC) has been suggested as an counterfeit-proof agent for packaging, highlighting its widespread potential applications.123
In the latest studies reported by Kan et al. (2023), they performed the Schiff base reaction to develop a hydrophobic material based on cellulose by combining dialdehyde cellulose (DAC) with octadecylamine (ODA), further to enhance the surface roughness silica nanoparticle were used. The resulting superhydrophobic coating exhibited a contact angle of 155° and provided green approach to synthesize recyclable, biodegradable paper coating.124
4.3 Chitosan
Derived from the deacetylation of chitin, chitosan is an abundant biopolymer after cellulose. It can be found in the exoskeletons of insects and mollusks, the cell walls of certain fungi, and the shells of crustaceans (crab, shrimp, and lobster).125 It is the only polycation found in nature and its charge density is determined by the degree of deacetylation and on the pH of the medium it is present in. Chitosan is a derivative of chitin that has been entirely or partly deacetylated, typically has a deacetylation degree of no more than 65%. Several techniques such as dip coating, spray coating and many more are being studied for edible coatings for fruits, vegetables and meat.126
Factors such as solubility and hydrophobicity of the chitosan depend upon the degree of deacetylation and polymerization. Being a biopolymer it is found to have a wide range of biomedical applications in drug delivery, tissue engineering, immunity-enhancing, antitumor and anticancer effects, acceleration of calcium and iron absorption. Several studies have been reported where chitosan along with different nanoparticles and antimicrobial agents were used to develop coatings for food packaging which helped to increase the shelf life of the food product.127 Furthermore, harnessing chitosan nanoparticles to create superhydrophobic coatings has several advantages for biomedical textiles.128 It is biodegradable, bioactive, biocompatible, non-toxic, non-allergenic, making it a fascinating material for different types of application.129,130
Shuangfei Wang et al. (2018) prepared superhydrophobic coatings by one pot method using chitosan-based nanoparticles. The nanoparticles were formed by nanoprecipitation of a solution of synthesized organo-soluble chitosan stearoyl ester (CSSE) in a poor solvent and constructed superhydrophobic surface using these particles spray coating on the silicone wafer. These coatings showed good stability (Fig. 21).131
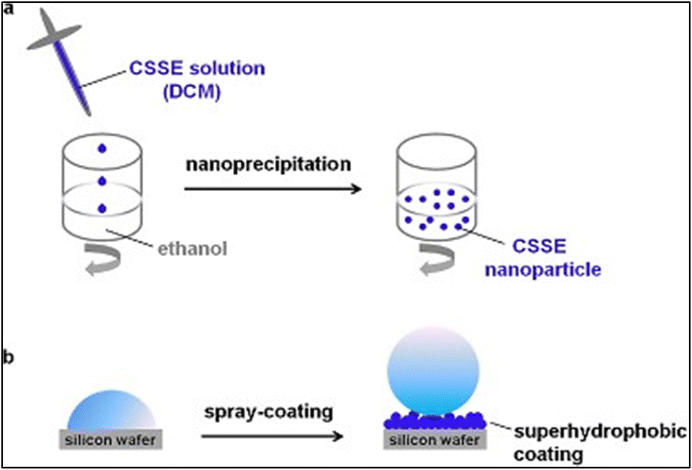 |
| Fig. 21 (a) Demonstration of one pot method used for preparation of SH coatings using chitosan stearoyl ester (CSSE). (b) Demonstration of superhydrophobic characteristics on silicon wafer.131 Reproduced from ref. 131 with permission from Carbohydrate Polymers, copyright 2018. | |
Today, cotton textiles are among the most widely used materials due to its exceptional qualities, including biodegradability, breathability, softness, comfort, and warmth, as well as their accessibility, affordability, and ease of use. Due to the molecular polyhydroxy structure, cotton readily absorbs moisture and humidity, which facilitates the growth of bacteria and other germs on the surface and their accumulation over time. This leads to a lack lustre finish and renders the material unusable in some regions. In order to increase cotton textiles' durability by physical or chemical alteration, it is crucial to provide hydrophobicity.132
With an approach enable hydrophobic characteristic M. Raeisi et al. (2021) fabricated chitosan/TiO2 nanocomposites on the surface of the cotton fabrics to attain superhydrophobicity using dip coating technique. The role of chitosan as a binding agent and high its compatibility with cellulose helped to achieve high adsorption of nanoparticles on the fabric's surface. The highest amount of TiO2 showed excellent superhydrophobicity exhibiting a contact angle at 160° and slide angle of 5°. The prepared coating displayed durability against harsh environment, UV resistance, protection against bacteria making it a promising material for clinical application of self-cleaning and antibacterial fabrics.133 In another work, Peng Qi et al. (2022) developed a superhydrophobic, flame retardant and sustainable coating for cotton fibers where chitosan/sodium polyborate polyelectrolyte (PEC)/water solution served as flame retardant layer and polydimethylsiloxane (PDMS)/tetrahydrofuran (THF) solution helped to attain superhydrophobicity. The micro–nano structures formed by the phase separated chitosan was covered using polydimethylsiloxane (PDMS) which improved the hydrophobicity of the coating. The prepared coating provided a new strategy to develop fireproof and waterproof cotton fabrics.134
UV resistant and photothermal cotton fabric coating using chitosan, tannic acid and polydimethylsiloxane was developed by Zheng et al. (2023) superhydrophobic. Initially, polytannic acid (PTA) was coated on cotton surface (Cot@PTA) followed by deposition of PTA and chitosan mixture on the (Cot@PTA) surface. The prepared (Cot@PTA@PTA–CS) surface exhibited a contact angle of 139.4 ± 1.5°. To further increase hydrophobicity they introduced polydimethylsiloxane in the coating which resulted into (Cot@PTA@PTA–CS@PDMS) exhibited a contact angle of about 153.0 ± 0.5° and sustained the contact angle up to 135.7 ± 3.9° and 137.2 ± 4.3° after 120 cycles of sandpaper abrasion and 600 times of Taber-type abrasion (Fig. 22).135
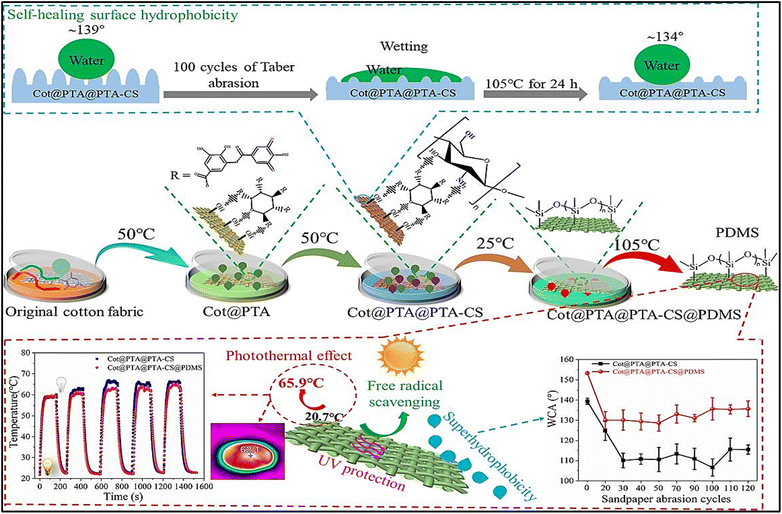 |
| Fig. 22 Preparation demonstration of SH coating on cotton fabric using chitosan, tannic acid and polydimethylsiloxane.135 Reproduced from ref. 135 with permission from Chemical Engineering Journal, copyright 2023. | |
An ecofriendly strategy was developed by Thirumalaisamy Suryaprabha et al. (2023) where they successfully synthesized chitosan–PAni–ZnO–STA composites and coated it on the cotton fibers. Chitosan was utilized to provide antimicrobial property, polyaniline was introduced to help generate reactive oxygen species, ZnO to construct surface roughness and low surface energy was achieved by stearic acid (STA). The coated cotton fibre exhibited a contact angle of about 154.4° and a slip angle of 8°, superhydrophobicity, better blood repellency and oil water separation (Fig. 23).136
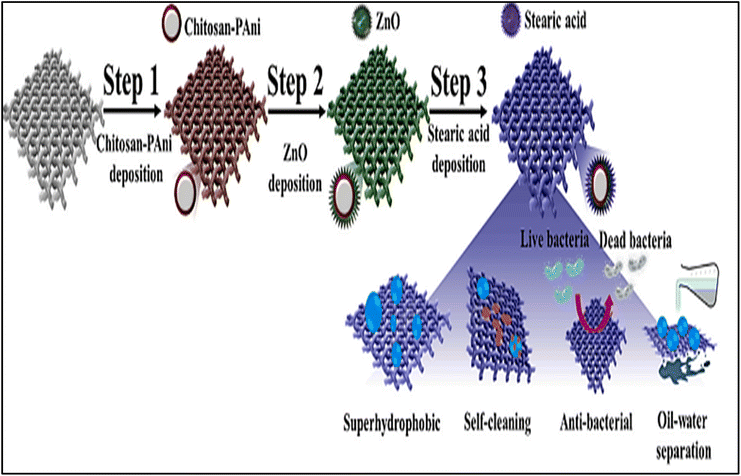 |
| Fig. 23 Schematic preparation of superhydrophobic cotton using chitosan–PAni–ZnO–STA composite coating.136 Reproduced from ref. 136 with permission from International Journal of Biological Macromolecules, copyright 2023. | |
Shanshan Deng et al. (2023) developed a multifunctional flame-retardant coating along with antibacterial properties and superhydrophobicity for cotton fabrics having potential application for home and public decorations and fire prone areas. They utilized phosphorylated chitosan in the first layer which provided efficient flame retardancy and antimicrobial property. Employing a silanization process, flame-retardant poly(2-hydroxyethyl methacrylate phosphate ester) (PHEMAP) particles were modified by perfluorooctyltriethoxysilane (FOS) in the next layer. A micro–nano dual-scale rough surface structure with an ultra-low surface energy was imparted by the modified PHEMAP coating, potentially giving the cotton fabric better hydrophobicity. Together, the two coating layers give the cotton fabric synergistic flame-retardancy and antibacterial properties in addition to superhydrophobicity and self-cleaning capabilities.137
Qianwen Xue et al. (2023) developed photothermal superhydrophobic cotton fabrics using chitosan (CS), amino carbon nanotubes (ACNTs) and octadecylamine (ODA). The coated cotton fabric showed prominent superhydrophobicity properties with contact angle of about 160°. When exposed to sunlight the surface temperature CS–ACNTs–ODA cotton fabric raised up to 70 °C showing excellent photothermal properties.138
By modifying the functional groups of chitosan with stearoyl chloride and freeze-drying the resulting superhydrophobic powder, Irene Tagliaro et al. (2023) developed a sustainable fluorine-free coating with fine-tuning of coating properties. They then carried out coating deposition using a solvent-free method through thermal treatment. The coatings displayed superior durability, hydrophobicity, and transparency.139
In order to develop a simple, affordable, and non-toxic superhydrophobic chitosan film, Mengting Yu et al. (2023) first assembled the films layer by layer using chitosan and sodium phytate. The film was then treated with stearic acid to reduce surface energy and immersed in ZnO nanoparticles to enhance surface roughness. Thus, superhydrophobic films were made from chitosan by varying the number of cycles of immersing ZnO nanoparticles and stearic acid treatments (Fig. 24).140
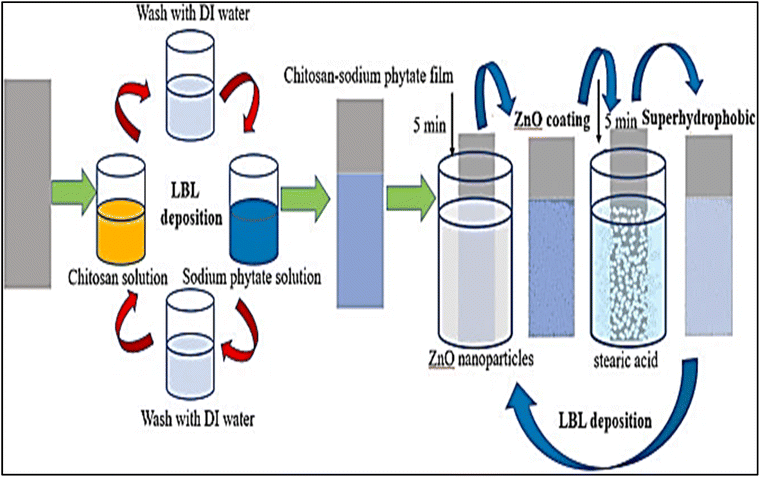 |
| Fig. 24 Schematic preparation process using chitosan by layer-by-layer assembly.140 Reproduced from ref. 140 with permission from International Journal of Biological Macromolecules, copyright 2023. | |
V. Selvaraj et al. (2023) developed a superhydrophobic filter paper through dip coating technique where they coated the filter paper with inorganic–organic hybrid nanocomposites. Zinc oxide nanoparticle was grafted with chitin and polycaprolactone and then chitosan polycaprolactone hybrid were coated on the paper which exhibited a contact angle of 145° for chitin–ZnO–polycaprolactone and 160° for chitosan–ZnO–polycaprolactone showing its promising superhydrophobic properties along with durability self-cleaning and biodegradability.141
4.4 Starch
Starch is the most familiar biopolymer found in nature which has been widely used in food, paper, beverages, textile and biofuel industries. In humans it provides energy by releasing glucose during cellular respiration.142 Starch mainly comprises amylose, amylopectin, lipid, protein, and to some extent minerals.143 It has advantages such as easy availability, low cost, easy film formation capacity, transparency, tastelessness and high oxygen barrier capacity. Starch based coatings are used to coat fruits and vegetables to increase their shelf life. Chemically modified starch is used in pharmaceutical industries for biodegradable coating.144 However, starch-based coatings have poor water resistance and poor mechanical strength. Several compounds such as surfactants, lipids, plasticizer and other polymeric materials are used to improve the film properties of these starch-based coatings.145
Yang Chen et al. (2020) prepared eco-friendly self-cleaning starch-based films using polydimethylsiloxane (PDMS) and ball milled montmorillonite (MMT) coatings. They coated starch-based films with PDMS which exhibited 75 contact angles of 115.2 ± 1.2°, thus to make the surface superhydrophobic they further sprayed the coated surface with MMT which exhibited a contact angle of 159.1° and slide angle of 3.6°. Here, this, MMT ball milled montmorillonite helped to increase the surface roughness and hydrophobicity and PDMS served as a intermediate between starch matrix and MMT as starch based films sprayed with only MMT showed good superhydrophobicity but weak adhesion. These coating have potential application in food packaging industries displaying properties such as anti-adhesion of liquid food and watery fruits (Fig. 25).146
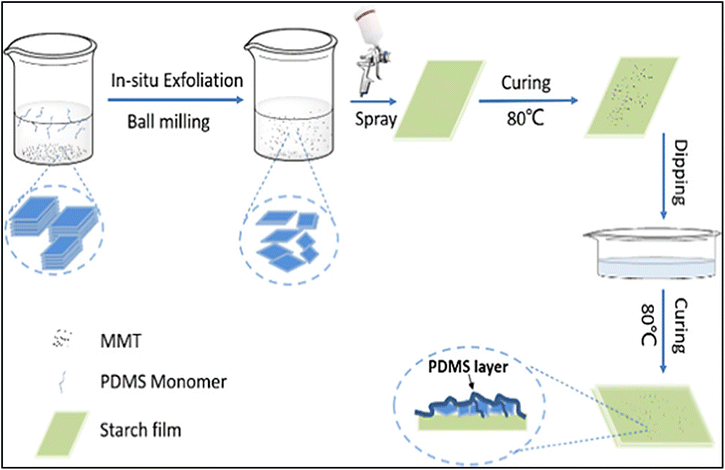 |
| Fig. 25 Schematic representation of process used for preparing eco-friendly self-cleaning starch-based films.146 Reproduced from ref. 146 with permission from ACS Sustainable Chemistry & Engineering, copyright 2020. | |
An ecofriendly nano based superhydrophobic coating was synthesized by Fan Wang et al. (2021). Here, enzymatic hydrolysis and recrystallization technique were employed for the production of starch nanoparticles (EHR-SNP). They combined starch nanoparticles (EHR-SNP) with nontoxic PDMS which provided low surface energy. Better water resistance was achieved due the micro and nanostructures formed by the SNP aggregates combined with PDMS covering. To give the coating pH responsiveness, anthocyanin-rich extract was artistically inserted into the SNP at the time of recrystallization. These coating exhibited a contact angle of 152.0°, slide angle less than 9.0° and self-cleaning property. The coating offers a lot of potential in developing cutting-edge, environmentally friendly materials that come into contact with food in order to support the sustainable development of resources for both every day and industrial use (Fig. 26).147,148
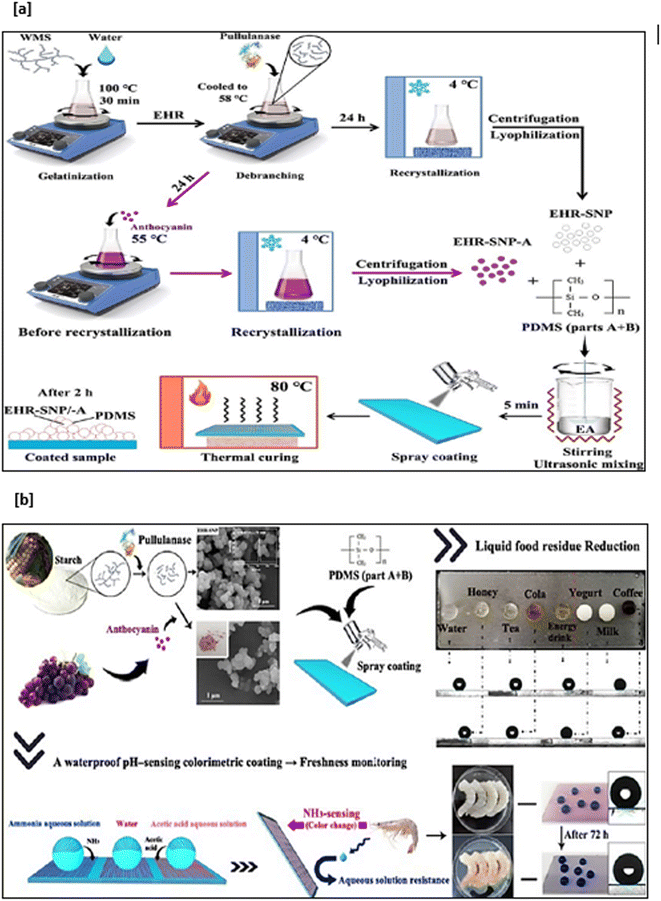 |
| Fig. 26 (a) Schematic representation of fabricating process of EHR-SNP, EHR-SNP-A, and nano-starch-based superhydrophobic coatings. (b) Evaluation of superhydrophobicity of the coating on different consumable liquids and for acid and basic liquids enabling pH sensing property.147 Reproduced from ref. 147 with permission from ACS Sustainable Chemistry & Engineering, copyright 2021. | |
In another study conducted by Mehran Ghasemlou et al. (2021) they developed a mechanically robust superhydrophobic surface through hybrid route employing a combination of soft imprinting and spin-coating. They conducted direct soft imprinting lithography onto the starch–polyhydroxyurethane–cellulose nanocrystals (SPC), then spin coated polydimethylsiloxane PDMS over the microcrystals. Further, grafted silica nanoparticles (SNPs) with vinyltriethoxysilane (VTES). The consecutive addition of nanocrystals SPC, PDMS which provided low surface tension and nanoscale roughness achieved by VTES help to construct a superhydrophobic surface exhibiting a contact angle of approximately 150° and a sliding angle less than 10° (Fig. 27).149
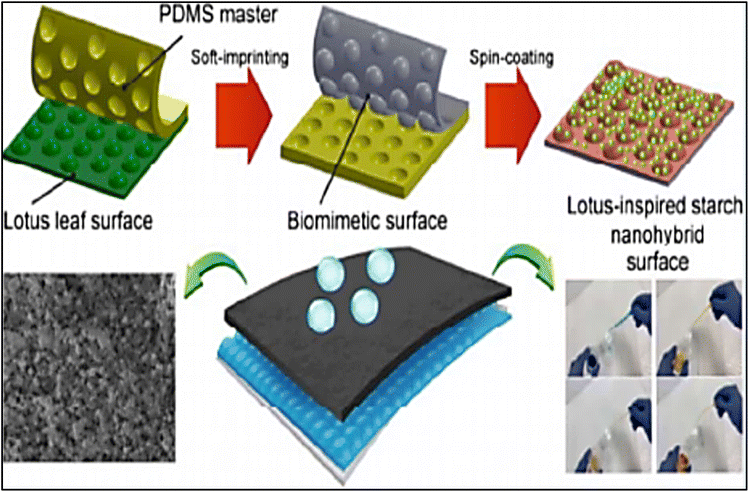 |
| Fig. 27 Illustration of fabrication procedure of superhydrophobic coatings using starch–polyhydroxyurethane–cellulose nanocrystals (SPC).149 Reproduced from ref. 149 with permission from ACS Applied Materials & Interfaces, copyright 2021. | |
Oluwamayomikun D. Akinfenwa et al. (2024) developed a superhydrophobic coating using electrodeposition technique to combine starch modified titanium oxide with zinc powder to prevent corrosion on mild steel having application in marine, transportation and petrochemical industries. The metal samples coated with this starch modified superhydrophobic coatings exhibited low corrosion rate.150
The about mentioned research suggests that it is possible to construct superhydrophobic coatings using starch. But till date very few studies are been reported using starch as a material for superhydrophobic material owing to its poor water resistances. It is possible to modify its hydrophilic character by alteration at its hydroxyl positions. Still a lot of potentials is yet to be explored pertaining to the starch based superhydrophobic coatings.
Applications. Superhydrophobic coatings serve application in the fields of automobiles, constructions, biomedical, solar plants etc. (Fig. 28). In the automotive sector, superhydrophobic coating becomes crucial for car safety when building a corrosion-resistant car body and a clean windshield that enables clear vision to the driver. Superhydrophobic coatings with exceptional water repellency and low water adhesion force are ideal for use in marine vessels, including cargo ships, service ships, navy warships, and submarines providing advantages such as increased durability and reduced energy consumption. The usage of solar energy is done in two ways which are photoelectric conversion and photothermal conversion which require photovoltaic panels. These photovoltaic panels are susceptible to dust accumulation and contamination reducing the efficiency and performance of these panels. Coating these panels with superhydrophobic, self-cleaning and anti-reflective properties help improve the efficiency and optical quality of the photovoltaic panels.11,151
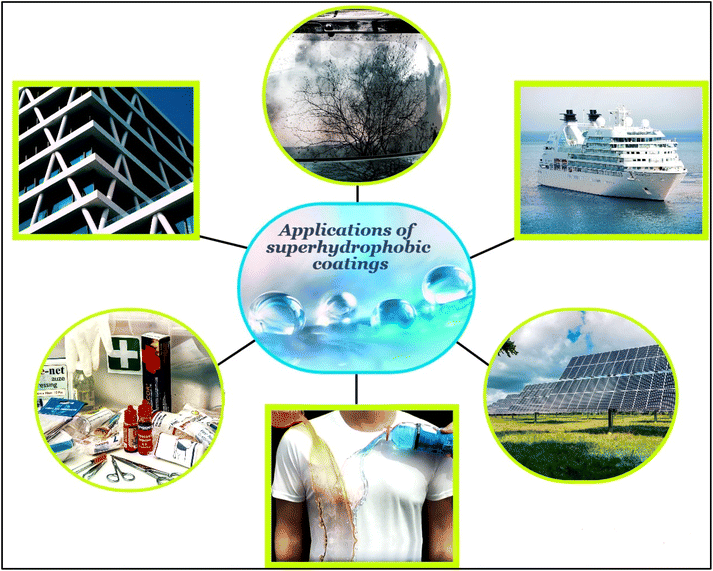 |
| Fig. 28 Applications of superhydrophobic coatings in solar, marine, automobile, textile, construction and medical industries. | |
Improving the durability of a building is the major concern of the construction industry as older buildings require more maintenance care as the durability of the concrete depends upon its permeability and the access of water and other toxic substances inside the concrete leading to detrimental reactions. Application of superhydrophobic coating not only helps resolve this concern but also helps to build antifouling, anti-corrosion, anti-icing, heat reflective and photoluminescence properties.152
With an increased use of sutures, catheters, contact lenses and other clinical materials the risk of iatrogenic infection is also increasing in recent years, further the problems caused by the iatrogenic infections are found to be more consequential than the original disease itself. To address this problem, considering the application of superhydrophobic coating on the surfaces of the biomedical materials can help resolve this problem as these coatings are often biologically inert, biocompatible and self-cleaning.153–155
Superhydrophobic fabrics are used in fabricating military garments, medical gowns, specialty gowns, sports gear, shoes, lab coats manufacturing and construction uniforms to exhibit self-cleaning properties and thus reduce the number of wash cycles.156
The primary factor responsible for electrical devices breakdown is water. Every year, water damage claims millions of mobile devices and numerous other gadgets. In today's largely electronic-dependent world, we rely on artificial materials that are waterproof in order to avoid destruction of electronics. Constructing a superhydrophobic surface on these electronic devices help in keeping the devices away from damages. In the field of automobiles where electric cars featuring autonomous driving technology are now in a boom. Superhydrophobic surface plays a crucial role as autonomous cars will depend heavily on its sensors and the precise data they collect to operate. As a result, the sensors must have a superhydrophobic surface to prevent dirt, water droplets and weathering of the sensor to provide correct signals.157 Sensors on the other hand need to provide features such as durability, mobility, flexibility, and transparency to adapt to dynamic service scenarios. Flexible sensors are categorised into temperature sensors gas sensors, photothermal sensors and photoelectric sensors and are designed to be capable of stretch, bend, and twist without breaking. But a high humidity environment may result in electrode fouling, circuit corrosion, or short circuits, all of which shorten service life and degrade performance. As a result, a critical area of attention in current scientific research is the study and development of superhydrophobic flexible sensors to improve their flexibility and dependability in such demanding conditions. Several studies are been reported on superhydrophobic flexible sensors serving applications in the field of smart wearables, motion detection, human health detection, anti-icing or de-icing, gesture detectors and anti-electromagnetic interference.158–161
5. Future perspectives
The future perspective of these superhydrophobic coatings is very promising and full of challenges as there is a wide range of applications for such types of coatings. A number of universities, research and development organizations, laboratories are researching on constructing superhydrophobic coatings, however, compared to the intensive efforts, the volume of industrial production of such coatings has not attained the desired outcomes. Although double hierarchical structures are often thought to be required for creating superhydrophobic coatings, these micro/nanostructures are flimsy and are destroyed easily. Several scientific and technical reasons must be studied to deal with the problems associated with practical applications of these superhydrophobic coatings.162
Comprehensive performances of superhydrophobic coatings, especially the mechanical strength, impalement resistance, abrasion resistance still have a huge expectancy of improvements. Research for fabricating superhydrophobic coatings on a large scale is still the biggest challenge as in most of the reported literature fabrication methods of superhydrophobic coatings are applicable only for small scale production and may not be profitable for the industries. Owing to it wide area of applications in the field of automotives, construction, electronics, health care, leather and a great potential to leap forward in the practical application of preventing rain attenuation of 5G/weather randomes, leak proof roofs, water repellent fabrics, marine electronics and food packaging more research must be conducted on how these superhydrophobic coatings can be developed on a large scale. Further, photothermal, flame retardant, pH sensing, electromagnetic functionalization in the superhydrophobic coating will boom the superhydrophobic market in near future. In the case of environment friendly, non-toxic and renewable biomass or biobased materials several factors such as availability, potentials, time taken to grow, ease of extraction and fabrication, time for production, ease of scalability etc. must be taken into account. Choosing a biobased material featuring all these properties is the biggest real time challenge. Standardization of evaluation methods must be administered to test the durability and robustness of these superhydrophobic coatings. Efforts should be made to improve the durability and methods which can simulate the problems that these superhydrophobic coatings are exposed with.
6. Conclusion
This review paper provided an overview of some of the techniques used for constructing superhydrophobic coating using biomass materials in the form of nanoparticles, nanocrystal or the material itself for the developing superhydrophobic coatings. Different techniques used for synthesizing these biomass-based superhydrophobic coatings have been schematically explained in this paper. Owing to the availability, renewability and cost effectiveness of lignin, cellulose, chitosan and starch, they can have a great potential to replace conventional materials used in developing superhydrophobic coating. Various properties such as self-cleaning, flame-retardant anti corrosion, pH sensing, antibacterials and anti-icing acquired by the constructed superhydrophobic coatings derived from the bioderived materials such as lignin, cellulose, chitosan and starch were highlighted. As the demand for electric vehicles is increasing the demand for sensors coated with self-cleaning coatings have also increased over the years. Owing to the advancement in the textile and footwear industries the demand for the superhydrophobic coating market has gained a lot of importance. Superhydrophobic coating in the textiles industry proves to be promising in saving water and energy required for cleaning resulting in reduced washing requirements and are expected to be long lasting and durable. With the increasing demand of superhydrophobic coating there is a need to explore more biobased materials competitive advantages and help maintain the balance between advance developments and protecting the environment.
Data availability
The authors confirm that the data supporting the finding of this study are available within the following articles.
Conflicts of interest
There are no conflicts to declare.
References
- E. Celia, T. Darmanin, E. Taffin de Givenchy, S. Amigoni and F. Guittard, Recent advances in designing superhydrophobic surfaces, J. Colloid Interface Sci., 2013, 402, 1–18 CrossRef CAS.
- N. J. Shirtcliffe, G. McHale, S. Atherton and M. I. Newton, An introduction to superhydrophobicity, Adv. Colloid Interface Sci., 2010, 161(1–2), 124–138 CrossRef CAS.
- D. Aslanidou, I. Karapanagiotis and C. Panayiotou, Superhydrophobic, superoleophobic coatings for the protection of silk textiles, Prog. Org. Coat., 2016, 97, 44–52 CrossRef CAS.
- J. J. Conde, P. Ferreira-Aparicio and A. M. Chaparro, Anti-corrosion coating for metal surfaces based on superhydrophobic electrosprayed carbon layers, Appl. Mater. Today, 2018, 13, 100–106 CrossRef.
- P. Nguyen-Tri, H. N. Tran, C. O. Plamondon, L. Tuduri, D. V. N. Vo and S. Nanda, et al., Recent progress in the preparation, properties and applications of superhydrophobic nano-based coatings and surfaces: a review, Prog. Org. Coat., 2019, 132, 235–256 CrossRef CAS.
- T. Darmanin and F. Guittard, Superhydrophobic and superoleophobic properties in nature, Mater. Today, 2015, 18(5), 273–285 CrossRef CAS.
- S. S. Latthe, R. S. Sutar, A. K. Bhosale, S. Nagappan, C. S. Ha and K. K. Sadasivuni, et al., Recent developments in air-trapped superhydrophobic and liquid-infused slippery surfaces for anti-icing application, Prog. Org. Coat., 2019, 137, 105373 CrossRef CAS.
- S. S. Antinate, A. Kavitha Sri, R. B. Jeen Robert, M. S. Subbulakshmi and G. S. O. Hikku, A review focused on the superhydrophobic fabrics with functional properties, J. Appl. Polym. Sci., 2023, 140(13), e53664 CrossRef.
- V. K. Mishra, R. Saini and N. Kumar, A review on superhydrophobic materials and coating techniques, IOP Conf. Ser.: Mater. Sci. Eng., 2021, 1168(1), 012026 Search PubMed.
- P. Roach, N. J. Shirtcliffe and M. I. Newton, Progress in superhydrophobic surface development, Soft Matter, 2008, 4(2), 224–240 RSC.
- A. Kausar, Nanomaterials for design and fabrication of superhydrophobic polymer coating, in Superhydrophobic Polymer Coatings, Elsevier, 2019, pp. 77–90 Search PubMed.
- L. Li, J. Wei, J. Zhang, B. Li, Y. Yang and J. Zhang, Challenges and strategies for commercialization and widespread practical applications of superhydrophobic surfaces, Sci. Adv., 2023, 9(42), eadj1554 CrossRef.
- E. I. Monaico, E. V. Monaico, V. V. Ursaki and I. M. Tiginyanu, Controlled Electroplating of Noble Metals on III-V Semiconductor Nanotemplates Fabricated by Anodic Etching of Bulk Substrates, Coatings, 2022, 12(10), 1521 CrossRef CAS.
- M. Mohammad, A. Ghadi and S. Fathi, Preparation of a Modified Electrode Using Electrodeposition of Cu Followed by Galvanic Replacement of Ag: Application for Electrocatalytic Oxidation of Ethylene Glycol, Russ. J. Electrochem., 2022, 58(3), 192–201 CrossRef.
- V. S. Protsenko and F. I. Danilov, Current Trends in Electrodeposition of Electrocatalytic Coatings, in Methods for Electrocatalysis, Springer International Publishing, Cham, 2020, pp. 263–299 Search PubMed.
- V. Branzoi, F. Branzoi and L. Pilan, Characterization of electrodeposited polymeric and composite modified electrodes on cobalt based alloy, Mater. Chem. Phys., 2009, 118(1), 197–202 CrossRef CAS.
- G. Kumar Sharma and N. Rachel James, Electrospinning: The Technique and Applications, in Recent Developments in Nanofibers Research, IntechOpen, 2023 Search PubMed.
- B. A. Venmathi Maran, S. Jeyachandran and M. Kimura, A Review on the Electrospinning of Polymer Nanofibers and Its Biomedical Applications, J. Compos. Sci., 2024, 8(1), 32 CrossRef CAS.
- J. Chen, Q. Ma, X. J. Wu, L. Li, J. Liu and H. Zhang, Wet-Chemical Synthesis and Applications of Semiconductor Nanomaterial-Based Epitaxial
Heterostructures, Nano-Micro Lett., 2019, 11(1), 86 CrossRef CAS.
- Z. Chen, D. Lu, J. Cao, F. Zhao, G. Feng and C. Xu, et al., Development of high-throughput wet-chemical synthesis techniques for material research, Materials Genome Engineering Advances, 2023, 1(1), e5 CrossRef.
- E. Della Gaspera, Special Issue “Wet Chemical Synthesis of Functional Nanomaterials”, Nanomaterials, 2021, 11(4), 1044 CrossRef.
- M. Shandilya, R. Rai and J. Singh, Review: hydrothermal technology for smart materials, Adv. Appl. Ceram., 2016, 115(6), 354–376 CrossRef CAS.
- M. Yoshimura and K. Byrappa, Hydrothermal processing of materials: past, present and future, J. Mater. Sci., 2008, 43(7), 2085–2103 CrossRef CAS.
- G. Yang and S. J. Park, Conventional and Microwave Hydrothermal Synthesis and Application of Functional Materials: A Review, Materials, 2019, 12(7), 1177 CrossRef CAS.
- X. Tang and X. Yan, Dip-coating for fibrous materials: mechanism, methods and applications, J. Sol-Gel Sci. Technol., 2017, 81(2), 378–404 CrossRef CAS.
- U. P. Gaur and E. Kamari, Applications of Thermal Spray Coatings: A Review, Journal of Thermal Spray and Engineering, 2024, 4, 106–114 CrossRef.
- Z. Zhang, J. Zeng, J. Groll and M. Matsusaki, Layer-by-layer assembly methods and their biomedical applications, Biomater. Sci., 2022, 10(15), 4077–4094 RSC.
- D. Rawtani and Y. K. Agrawal, Emerging Strategies and Applications of Layer-by-Layer Self-Assembly, Nanobiomedicine, 2014, 1, 8 CrossRef.
- A. S. I. Milionis, D. Fragouli, F. Brandi and A. Athanassiou, Combination of Lithography and Coating Methods for Surface Wetting Control, in Updates in Advanced Lithography, InTech, 2013 Search PubMed.
- E. Sharma, R. Rathi, J. Misharwal, B. Sinhmar, S. Kumari and J. Dalal, et al., Evolution in Lithography Techniques: Microlithography to Nanolithography, Nanomaterials, 2022, 12(16), 2754 CrossRef CAS.
- N. A. El-Wassefy, F. M. Reicha and N. S. Aref, Electro-chemical deposition of nano hydroxyapatite-zinc coating on titanium metal substrate, Int. J. Implant Dent., 2017, 3(1), 39 CrossRef CAS.
- M. Laad and B. Ghule, Fabrication Techniques of Superhydrophobic Coatings: A Comprehensive Review, Phys. Status Solidi A, 2022, 219(16), 2200109 CrossRef CAS.
- B. Pan, Y. Yao, L. Peng, Q. Zhang and Y. Yang, Ultrasound-assisted pulse electrodeposition of cobalt films, Mater. Chem. Phys., 2020, 241, 122395 CrossRef CAS.
- M. S. Chandrasekar and M. Pushpavanam, Pulse and pulse reverse plating—conceptual, advantages and applications, Electrochim. Acta, 2008, 53(8), 3313–3322 CrossRef CAS.
- L. Shen, Y. Wang, W. Jiang, X. Liu, C. Wang and Z. Tian, Jet electrodeposition multilayer nickel on the surface of sintered NdFeB and corrosion behaviours, Corros. Eng., Sci. Technol., 2017, 52(4), 311–316 CrossRef CAS.
- W. Zhuo, L. Shen, M. Qiu, Z. Tian and W. Jiang, Effects of flexible friction on the properties of nanocrystalline nickel prepared by jet electrodeposition, Surf. Coat. Technol., 2018, 333, 87–95 CrossRef CAS.
- D. Thiemig, C. Kubeil, C. P. Gräf and A. Bund, Electrocodeposition of magnetic nickel matrix nanocomposites in a static magnetic field, Thin Solid Films, 2009, 517(5), 1636–1644 CrossRef CAS.
- I. Tudela, Y. Zhang, M. Pal, I. Kerr and A. J. Cobley, Ultrasound-assisted electrodeposition of composite coatings with particles, Surf. Coat. Technol., 2014, 259, 363–373 CrossRef CAS.
- D. Iacovetta, J. Tam and U. Erb, Synthesis, structure, and properties of superhydrophobic nickel–PTFE nanocomposite coatings made
by electrodeposition, Surf. Coat. Technol., 2015, 279, 134–141 CrossRef CAS.
- D. Zhang, L. Li, Y. Wu, B. Zhu and H. Song, One-step method for fabrication of bioinspired hierarchical superhydrophobic surface with robust stability, Appl. Surf. Sci., 2019, 473, 493–499 CrossRef CAS.
- S. Thenmozhi, N. Dharmaraj, K. Kadirvelu and H. Y. Kim, Electrospun nanofibers: new generation materials for advanced applications, Mater. Sci. Eng., B, 2017, 217, 36–48 CrossRef CAS.
- J. Zhang, L. Liu, Y. Si, J. Yu and B. Ding, Rational design of electrospun nanofibrous materials for oil/water emulsion separation, Mater. Chem. Front., 2021, 5(1), 97–128 RSC.
- W. J. Al-Kaabi, S. Albukhaty, A. J. M. Al-Fartosy, H. K. Al-Karagoly, S. Al-Musawi and G. M. Sulaiman, et al., Development of Inula graveolens (L.) Plant Extract Electrospun/Polycaprolactone Nanofibers: A Novel Material for Biomedical Application, Appl. Sci., 2021, 11(2), 828 CrossRef CAS.
- B. J. Deka, J. Guo and A. K. An, Robust dual-layered omniphobic electrospun membrane with anti-wetting and anti-scaling functionalised for membrane distillation application, J. Membr. Sci., 2021, 624, 119089 CrossRef CAS.
- G. K. Sharma and N. R. James, Progress in Electrospun Polymer Composite Fibers for Microwave Absorption and Electromagnetic Interference Shielding, ACS Appl. Electron. Mater., 2021, 3(11), 4657–4680 CrossRef CAS.
- C. Su, T. Horseman, H. Cao, K. Christie, Y. Li and S. Lin, Robust Superhydrophobic Membrane for Membrane Distillation with Excellent Scaling Resistance, Environ. Sci. Technol., 2019, 53(20), 11801–11809 CrossRef CAS.
- A. B. Radwan, M. A. Ibrahim, E. H. Ismail, N. M. El Basiony, S. I. El-Hout and S. M. Zughaier, et al., Anticorrosion Properties of Robust and UV-Durable Poly(vinylidene fluoride-co-hexafluoropropylene)/Carbon Nanotubes Superhydrophobic Coating, Ind. Eng. Chem. Res., 2024, 63(3), 1380–1395 CrossRef CAS.
- Z. Guo, W. Liu and B. L. Su, Superhydrophobic surfaces: from natural to biomimetic to functional, J. Colloid Interface Sci., 2011, 353(2), 335–355 CrossRef CAS.
- D. Zhang, L. Wang, H. Qian and X. Li, Superhydrophobic surfaces for corrosion protection: a review of recent progresses and future directions, J. Coat. Technol. Res., 2016, 13(1), 11–29 CrossRef CAS.
- Q. Zeng, H. Zhou, J. Huang and Z. Guo, Review on the recent development of durable superhydrophobic materials for practical applications, Nanoscale, 2021, 13(27), 11734–11764 RSC.
- V. A. Ganesh, H. K. Raut, A. S. Nair and S. Ramakrishna, A review on self-cleaning coatings, J. Mater. Chem., 2011, 21(41), 16304 RSC.
- T. Liu, Y. Yin, S. Chen, X. Chang and S. Cheng, Super-hydrophobic surfaces improve corrosion resistance of copper in seawater, Electrochim. Acta, 2007, 52(11), 3709–3713 CrossRef CAS.
- L. Zhao, Q. Liu, R. Gao, J. Wang, W. Yang and L. Liu, One-step method for the fabrication of superhydrophobic surface on magnesium alloy and its corrosion protection, antifouling performance, Corros. Sci., 2014, 80, 177–183 CrossRef CAS.
- S. Thiagarajan, A. Sanmugam and D. Vikraman, Facile Methodology of Sol-Gel Synthesis for Metal Oxide Nanostructures, in Recent Applications in Sol-Gel Synthesis, InTech, 2017 Search PubMed.
- A. Kumar and D. Nanda, Methods and fabrication techniques of superhydrophobic surfaces, in Superhydrophobic Polymer Coatings, Elsevier, 2019, pp. 43–75 Search PubMed.
- Y. Fan, C. Li, Z. Chen and H. Chen, Study on fabrication of the superhydrophobic sol–gel films based on copper wafer and its anti-corrosive properties, Appl. Surf. Sci., 2012, 258(17), 6531–6536 CrossRef CAS.
- M. Espanhol-Soares, L. Costa, M. R. A. Silva, F. Soares Silva, L. M. S. Ribeiro and R. Gimenes, Super-hydrophobic coatings on cotton fabrics using sol–gel technique by spray, J. Sol-Gel Sci. Technol., 2020, 95(1), 22–33 CrossRef CAS.
- X. Xun, R. Zhu, J. Dong, T. Pan, M. Zhong and R. Zhang, et al., Superhydrophobic Light Alloy Materials with Corrosion-Resistant Surfaces, Research and Application of Materials Science, 2020, 2, 1–11 CrossRef.
- G. Yang and S. J. Park, Conventional and Microwave Hydrothermal Synthesis and Application of Functional Materials: A Review, Materials, 2019, 12(7), 1177 CrossRef CAS.
- M. Yoshimura and K. Byrappa, Hydrothermal processing of materials: past, present and future, J. Mater. Sci., 2008, 43(7), 2085–2103 CrossRef CAS.
- L. Feng, Y. Zhu, J. Wang and X. Shi, One-step hydrothermal process to fabricate superhydrophobic surface on magnesium alloy with enhanced corrosion resistance and self-cleaning performance, Appl. Surf. Sci., 2017, 422, 566–573 CrossRef CAS.
- T. Zhang, J. Deng and L. Z. Zhang, A photothermal self-healing superhydrophobic coating with anti-frosting and anti-corrosion properties, Prog. Org. Coat., 2023, 180, 107569 CrossRef CAS.
- I. A. Neacşu, A. I. Nicoară, O. R. Vasile and B. Ş. Vasile, Inorganic micro- and nanostructured implants for tissue engineering, in Nanobiomaterials in Hard Tissue Engineering, Elsevier, 2016, pp. 271–295 Search PubMed.
- Z. Cui, L. Yin, Q. Wang, J. Ding and Q. Chen, A facile dip-coating process for preparing highly durable superhydrophobic surface with multi-scale structures on paint films, J. Colloid Interface Sci., 2009, 337(2), 531–537 CrossRef CAS.
- T. Liu, F. Zhang, C. Xue, L. Li and Y. Yin, Structure stability and corrosion resistance of nano-TiO2 coatings on aluminum in seawater by a vacuum dip-coating method, Surf. Coat. Technol., 2010, 205(7), 2335–2339 CrossRef CAS.
- S. A. Mahadik, V. Parale, R. S. Vhatkara, D. B. Mahadik, M. S. Kavale and P. B. Wagh, et al., Superhydrophobic silica coating by dip coating method, Appl. Surf. Sci., 2013, 277, 67–72 CrossRef CAS.
- M. Jagdishbhai Patel, H. Baishya, R. Kant Gupta, R. Garai and P. Krishnan Iyer, Thin Film Solution Processable Perovskite Solar Cell, in Recent Advances in Multifunctional Perovskite Materials, IntechOpen, 2022 Search PubMed.
- X. Liu, K. Chen, D. Zhang and Z. Guo, Stable and Durable Conductive Superhydrophobic Coatings Prepared by Double-Layer Spray Coating Method, Nanomaterials, 2021, 11(6), 1506 CrossRef CAS.
- A. Elzaabalawy and S. A. Meguid, Development of novel superhydrophobic coatings using siloxane-modified epoxy nanocomposites, Chem. Eng. J., 2020, 398, 125403 CrossRef CAS.
- D. Li, L. Ma, B. Zhang and S. Chen, Large-scale fabrication of a durable and self-healing super-hydrophobic coating with high thermal stability and long-term corrosion resistance, Nanoscale, 2021, 13(16), 7810–7821 RSC.
- X. Li, J. Yan, T. Yu and B. Zhang, Versatile nonfluorinated superhydrophobic coating with self-cleaning, anti-fouling, anti-corrosion and mechanical stability, Colloids Surf., A, 2022, 642, 128701 CrossRef CAS.
- Y. Pan, L. Fu, J. Du, D. Zhang, T. Lü and Y. Zhang, et al., Layer-by-Layer Self-Assembly Coating for Multi-Functionalized Fabrics: A Scientometric Analysis in CiteSpace (2005–2021), Molecules, 2022, 27(19), 6767 CrossRef CAS.
- J. Bravo, L. Zhai, Z. Wu, R. E. Cohen and M. F. Rubner, Transparent Superhydrophobic Films Based on Silica Nanoparticles, Langmuir, 2007, 23(13), 7293–7298 CrossRef CAS.
- G. Yin, W. Xue, F. Chen and X. Fan, Self-repairing and superhydrophobic film of gold nanoparticles and fullerene
pyridyl derivative based on the self-assembly approach, Colloids Surf., A, 2009, 340(1–3), 121–125 CrossRef CAS.
- R. A. Lawson and A. P. G. Robinson, Overview of materials and processes for lithography, Front. Nanosci., 2016, 1–90 CAS.
- D. Qi, N. Lu, H. Xu, B. Yang, C. Huang and M. Xu, et al., Simple Approach to Wafer-Scale Self-Cleaning Antireflective Silicon Surfaces, Langmuir, 2009, 25(14), 7769–7772 CrossRef CAS.
- J. Feng, M. T. Tuominen and J. P. Rothstein, Hierarchical Superhydrophobic Surfaces Fabricated by Dual-Scale Electron-Beam-Lithography with Well-Ordered Secondary Nanostructures, Adv. Funct. Mater., 2011, 21(19), 3715–3722 CrossRef CAS.
- X. Gong, H. Yu, L. Wang, X. Liu, S. Ren and Y. Huang, et al., Recent progress in the mechanisms, preparations and applications of polymeric antifogging coatings, Adv. Colloid Interface Sci., 2022, 309, 102794 CrossRef CAS.
- H. Kim, Y. Lee, S. Jung and H. Lee, Micropatterned Hydrogel-Elastomer Hybrids for Flexible Wet-Style Superhydrophobic Antifogging Tapes, Adv. Funct. Mater., 2024, 34, 2470196 CrossRef.
- Q. Y. Cheng, M. C. Liu, Y. D. Li, J. Zhu, A. K. Du and J. B. Zeng, Biobased super-hydrophobic coating on cotton fabric fabricated by spray-coating for efficient oil/water separation, Polym. Test., 2018, 66, 41–47 CrossRef CAS.
- Q. Xu, X. Wang and Y. Zhang, Green and sustainable fabrication of a durable superhydrophobic cotton fabric with self-cleaning properties, Int. J. Biol. Macromol., 2023, 242, 124731 CrossRef CAS.
- P. N. Manoudis and I. Karapanagiotis, Modification of the wettability of polymer surfaces using nanoparticles, Prog. Org. Coat., 2014, 77(2), 331–338 CrossRef CAS.
- K. A. Saharudin, S. Sreekantan, N. Basiron, L. K. Chun, V. Kumaravel and T. K. Abdullah, et al., Improved super-hydrophobicity of eco-friendly coating from palm oil fuel ash (POFA) waste, Surf. Coat. Technol., 2018, 337, 126–135 CrossRef CAS.
- T. Shen, S. Fan, Y. Li, G. Xu and W. Fan, Preparation of Edible Non-wettable Coating with Soybean Wax for Repelling Liquid Foods with Little Residue, Materials, 2020, 13(15), 3308 CrossRef CAS.
- X. Zhong, L. Lv, H. Hu, X. Jiang and H. Fu, Bio-based coatings with liquid repellency for various applications, Chem. Eng. J., 2020, 382, 123042 CrossRef CAS.
- X. Wu, F. Yang, G. Lu, X. Zhao, Z. Chen and S. Qian, A breathable and environmentally friendly superhydrophobic coating for anti-condensation applications, Chem. Eng. J., 2021, 412, 128725 CrossRef CAS.
- N. Celik, F. Sahin, S. S. Ozel, G. Sezer, N. Gunaltay and M. Ruzi, et al., Self-Healing of Biocompatible Superhydrophobic Coatings: The Interplay of the Size and Loading of Particles, Langmuir, 2023, 39(9), 3194–3203 CrossRef CAS.
- N. Celik, I. Torun, M. Ruzi, A. Esidir and M. S. Onses, Fabrication of robust superhydrophobic surfaces by one-step spray coating: evaporation driven self-assembly of wax and nanoparticles into hierarchical structures, Chem. Eng. J., 2020, 396, 125230 CrossRef CAS.
- X. Wang, X. Huang, Z. Ji, H. Sheng and H. Liu, Planting Multiwalled Carbon Nanotubes onto Epoxidized Soybean Oil-Based Vitrimer to Construct a Biobased Photothermal Superhydrophobic Coating with Self-Healing and Closed-Loop Recyclability for Anti/Deicing, ACS Sustain. Chem. Eng., 2024, 12(18), 7147–7157 CrossRef CAS.
- E. Rojo, M. S. Peresin, W. W. Sampson, I. C. Hoeger, J. Vartiainen and J. Laine, et al., Comprehensive elucidation of the effect of residual lignin on the physical, barrier, mechanical and surface properties of nanocellulose films, Green Chem., 2015, 17(3), 1853–1866 RSC.
- M. M. Sreejaya, R. Jeevan
Sankar, K. Ramanunni, N. P. Pillai, K. Ramkumar and P. Anuvinda, Lignin-based organic coatings and their applications: a review, Mater. Today: Proc., 2022, 60, 494–501 CAS.
- T. A. Khan, J. H. Lee and H. J. Kim, Lignin-Based Adhesives and Coatings, in Lignocellulose for Future Bioeconomy, Elsevier, 2019, pp. 153–206 Search PubMed.
- J. Ruwoldt, F. H. Blindheim and G. Chinga-Carrasco, Functional surfaces, films, and coatings with lignin – a critical review, RSC Adv., 2023, 13(18), 12529–12553 RSC.
- M. Kienberger, Potential Applications of Lignin, in Economics of Bioresources, Springer International Publishing, Cham, 2019, pp. 183–193 Search PubMed.
- J. Huang, S. Wang and S. Lyu, Facile Preparation of a Robust and Durable Superhydrophobic Coating Using Biodegradable Lignin-Coated Cellulose Nanocrystal Particles, Materials, 2017, 10(9), 1080 CrossRef.
- Y. Zhang, J. Bi, S. Wang, Q. Cao, Y. Li and J. Zhou, et al., Functional food packaging for reducing residual liquid food: thermo-resistant edible super-hydrophobic coating from coffee and beeswax, J. Colloid Interface Sci., 2019, 533, 742–749 CrossRef CAS.
- J. Zhang, Z. Tian, X. Ji and F. Zhang, Fabrication Mechanisms of Lignin Nanoparticles and Their Ultraviolet Protection Ability in PVA Composite Film, Polymers, 2022, 14(19), 4196 CrossRef CAS.
- Z. Zhang, V. Terrasson and E. Guénin, Lignin Nanoparticles and Their Nanocomposites, Nanomaterials, 2021, 11(5), 1336 CrossRef CAS.
- H. Wang, F. Xiong, Y. Tan, J. Yang, Y. Qing and F. Chu, et al., Preparation and Formation Mechanism of Covalent–Noncovalent Forces Stabilizing Lignin Nanospheres and Their Application in Superhydrophobic and Carbon Materials, ACS Sustain. Chem. Eng., 2021, 9(10), 3811–3820 CrossRef CAS.
- C. Ren, M. Li, W. Huang, Y. Zhang and J. Huang, Superhydrophobic coating with excellent robustness and UV resistance fabricated using hydrothermal treated lignin nanoparticles by one-step spray, J. Mater. Sci., 2022, 57(39), 18356–18369 CrossRef CAS.
- M. Li, W. Huang, C. Ren, Q. Wu, S. Wang and J. Huang, Preparation of lignin nanospheres based superhydrophobic surfaces with good robustness and long UV resistance, RSC Adv., 2022, 12(18), 11517–11525 RSC.
- J. Huang, M. Li, C. Ren, W. Huang, Y. Miao and Q. Wu, et al., Construction of HLNPs/Fe3O4 based superhydrophobic coating with excellent abrasion resistance, UV resistance, flame retardation and oil absorbency, J. Environ. Chem. Eng., 2023, 11(1), 109046 CrossRef CAS.
- X. Liu, C. Gao, C. Fu, Y. Xi, P. Fatehi and J. R. Zhao, et al., Preparation and Performance of Lignin-Based Multifunctional Superhydrophobic Coating, Molecules, 2022, 27(4), 1440 CrossRef CAS.
- J. Bang, J. Kim, Y. Kim, J. K. Oh, H. Yeo and H. W. Kwak, Preparation and Characterization of Hydrophobic Coatings from Carnauba Wax/Lignin Blends, Journal of the Korean Wood Science and Technology, 2022, 50(3), 149–158 CrossRef.
- D. W. Wei, H. Wei, A. C. Gauthier, J. Song, Y. Jin and H. Xiao, Superhydrophobic modification of cellulose and cotton textiles: methodologies and applications, J. Bioresour. Bioprod., 2020, 5(1), 1–15 CrossRef CAS.
- G. David, N. Gontard and H. Angellier-Coussy, Mitigating the Impact of Cellulose Particles on the Performance of Biopolyester-Based Composites by Gas-Phase Esterification, Polymers, 2019, 11(2), 200 CrossRef.
- R. M. Cherian, A. Tharayil, R. T. Varghese, T. Antony, H. Kargarzadeh and C. J. Chirayil, et al., A review on the emerging applications of nano-cellulose as advanced coatings, Carbohydr. Polym., 2022, 282, 119123 CrossRef CAS.
- C. Moreau, A. Villares, I. Capron and B. Cathala, Tuning supramolecular interactions of cellulose nanocrystals to design innovative functional materials, Ind. Crops Prod., 2016, 93, 96–107 CrossRef CAS.
- J. Tang, J. Sisler, N. Grishkewich and K. C. Tam, Functionalization of cellulose nanocrystals for advanced applications, J. Colloid Interface Sci., 2017, 494, 397–409 CrossRef CAS.
- Q. Y. Cheng, C. S. Guan, M. Wang, Y. D. Li and J. B. Zeng, Cellulose nanocrystal coated cotton fabric with superhydrophobicity for efficient oil/water separation, Carbohydr. Polym., 2018, 199, 390–396 CrossRef CAS.
- Z. Zhu, S. Fu and A. H. Basta, A cellulose nanoarchitectonic: multifunctional and robust superhydrophobic coating toward rapid and intelligent water-removing purpose, Carbohydr. Polym., 2020, 243, 116444 CrossRef CAS.
- H. Xiang, B. Wang, M. Zhong, W. Liu, D. Yu and Y. Wang, et al., Sustainable and Versatile Superhydrophobic Cellulose Nanocrystals, ACS Sustain. Chem. Eng., 2022, 10(18), 5939–5948 CrossRef CAS.
- Z. Zhang, C. Ren, Y. Sun, Y. Miao, L. Deng and Z. Wang, et al., Construction of CNC@SiO2@PL Based Superhydrophobic Wood with Excellent Abrasion Resistance Based on Nanoindentation Analysis and Good UV Resistance, Polymers, 2023, 15(4), 933 CrossRef CAS.
- K. Shanmugam, N. Chandrasekar and R. Balaji, Barrier Performance of Spray Coated Cellulose Nanofibre Film, Micro, 2023, 3(1), 192–207 CrossRef.
- X. Chen, Y. Huang, L. Zhang, J. Liu, C. Wang and M. Wu, Cellulose nanofiber assisted dispersion of hydrophobic SiO2 nanoparticles in water and its superhydrophobic coating, Carbohydr. Polym., 2022, 290, 119504 CrossRef CAS.
- Fabrication and properties of multifunctional CeO2/cellulose nanofibers composite superhydrophobic coating.
- T. Wang and Y. Zhao, Fabrication of thermally and mechanically stable superhydrophobic coatings for cellulose-based substrates with natural and edible ingredients for food applications, Food Hydrocolloids, 2021, 120, 106877 CrossRef CAS.
- K. Yi, S. Fu and Y. Huang, Nanocellulose-based superhydrophobic coating with acid resistance and fluorescence, Prog. Org. Coat., 2022, 168, 106911 CrossRef CAS.
- M. Shakun, T. Heinze and W. Radke, Determination of the DS distribution of non-degraded sodium carboxymethyl cellulose by gradient chromatography, Carbohydr. Polym., 2013, 98(1), 943–950 CrossRef CAS.
- X. Tang, W. Huang, Y. Xie, Z. Xiao, H. Wang and D. Liang, et al., Superhydrophobic Hierarchical Structures from Self-Assembly of Cellulose-Based Nanoparticles, ACS Sustain. Chem. Eng., 2021, 9(42), 14101–14111 CrossRef CAS.
- J. Ren, F. Tao, X. Lu, H. Zhang, L. Gai and L. Liu, et al., Biomass-based superhydrophobic coating with tunable colors and excellent robustness, Carbohydr. Polym., 2021, 270, 118401 CrossRef CAS.
- Y. Song, Y. Xu, D. Li, S. Chen and F. Xu, Sustainable and Superhydrophobic Lignocellulose-Based Transparent Films with Efficient Light Management and Self-Cleaning, ACS Appl. Mater. Interfaces, 2021, 13(41), 49340–49347 CrossRef CAS.
- Y. Hu, M. Gan, Y. Xie, Y. Yu and Q. Feng, Facile fabrication of biometric cellulose-based films with superhydrophobicity and tunable optical performance, Appl. Surf. Sci., 2023, 637, 157924 CrossRef CAS.
- L. Kan, X. Zhang, Q. Huang, Y. Wang, M. Tian and Q. Huang, et al., Fabrication of cellulose-based and fluorine/silane free superhydrophobic paper by a green and sustainable approach, Ind. Crops Prod., 2023, 203, 117226 CrossRef CAS.
- D. Alemu, E. Getachew and A. K. Mondal, Study on the Physicochemical Properties of Chitosan and their Applications in the Biomedical Sector, Int. J. Polym. Sci., 2023, 2023, 1–13 CrossRef.
- V. Gigante, L. Panariello, M. B. Coltelli, S. Danti, K. A. Obisesan and A. Hadrich, et al., Liquid and Solid Functional Bio-Based Coatings, Polymers, 2021, 13(21), 3640 CrossRef CAS.
- Y. Xing, Q. Xu, X. Li, C. Chen, L. Ma and S. Li, et al., Chitosan-Based Coating with Antimicrobial Agents: Preparation, Property, Mechanism, and Application Effectiveness on Fruits and Vegetables, Int. J. Polym. Sci., 2016, 2016, 1–24 CrossRef.
- N. A. Ivanova and A. B. Philipchenko, Superhydrophobic chitosan-based coatings for textile processing, Appl. Surf. Sci., 2012, 263, 783–787 CrossRef CAS.
- R. A. I. Reshad, T. A. Jishan and N. N. Chowdhury, Chitosan and its broad applications: a brief review, SSRN Electronic Journal, 2021, 12, 1–13 Search PubMed.
- B. Koc, L. Akyuz, Y. S. Cakmak, I. Sargin, A. M. Salaberria and J. Labidi, et al., Production and characterization of chitosan-fungal extract films, Food Biosci., 2020, 35, 100545 CrossRef CAS.
- S. Wang, J. Sha, W. Wang, C. Qin, W. Li and C. Qin, Superhydrophobic surfaces generated by one-pot spray-coating of chitosan-based nanoparticles, Carbohydr. Polym., 2018, 195, 39–44 CrossRef CAS.
- Z. Li, J. Wu, Y. Wang, Y. Li, G. Huang and B. Fei, et al., A facile approach to obtain super-hydrophobicity for cotton fiber fabrics, RSC Adv., 2023, 13(14), 9237–9241 RSC.
- M. Raeisi, Y. Kazerouni, A. Mohammadi, M. Hashemi, I. Hejazi and J. Seyfi, et al., Superhydrophobic cotton fabrics coated by chitosan and titanium dioxide nanoparticles with enhanced antibacterial and UV-protecting properties, Int. J. Biol. Macromol., 2021, 171, 158–165 CrossRef CAS.
- P. Qi, S. Wang, W. Wang, J. Sun, H. Yuan and S. Zhang, Chitosan/sodium polyborate based micro-nano coating with high flame retardancy and superhydrophobicity for cotton fabric, Int. J. Biol. Macromol., 2022, 205, 261–273 CrossRef CAS.
- G. Zheng, Y. Cui, Z. Jiang, M. Zhou, Y. Yu and P. Wang, et al., Superhydrophobic, photothermal, and UV-resistant coatings obtained by polydimethylsiloxane treating self-healing hydrophobic chitosan-tannic acid surface for oil/water separation, Chem. Eng. J., 2023, 473, 145258 CrossRef CAS.
- T. Suryaprabha, H. Ha, B. Hwang and M. G. Sethuraman, Self-cleaning, superhydrophobic, and antibacterial cotton fabrics with chitosan-based composite coatings, Int. J. Biol. Macromol., 2023, 250, 126217 CrossRef CAS.
- S. Deng, F. Wang, M. Wang, N. Wu, H. Cui and Y. Wu, Integrating multifunctional highly efficient flame-retardant coatings with superhydrophobicity, antibacterial property on cotton fabric, Int. J. Biol. Macromol., 2023, 253, 127022 CrossRef CAS.
- Q. Xue, J. Wu, Z. Lv, Y. Lei, X. Liu and Y. Huang, Photothermal Superhydrophobic Chitosan-Based Cotton Fabric for Rapid Deicing and Oil/Water Separation, Langmuir, 2023, 39(28), 9912–9923 CrossRef CAS.
- I. Tagliaro, S. Seccia, B. Pellegrini, S. Bertini and C. Antonini, Chitosan-based coatings with tunable transparency and superhydrophobicity: a solvent-free and fluorine-free approach by stearoyl derivatization, Carbohydr. Polym., 2023, 302, 120424 CrossRef CAS.
- M. Yu, L. Yang, L. Yan, T. Wang, Y. Wang and Y. Qin, et al., ZnO nanoparticles coated and stearic acid modified superhydrophobic chitosan film for self-cleaning and oil–water separation, Int. J. Biol. Macromol., 2023, 231, 123293 CrossRef CAS.
- V. Selvaraj, T. Swarna Karthika, C. Mansiya and M. Alagar, ZnO nano grafted chitin–chitosan
based hybrid composite coated super hydrophobic filter paper for water flow cleaning and oil–water separation applications, New J. Chem., 2023, 47(28), 13397–13408 RSC.
- A. K. Shrestha and P. J. Halley, Starch Modification to Develop Novel Starch-Biopolymer Blends, in Starch Polymers, Elsevier, 2014, pp. 105–143 Search PubMed.
- S. C. Alcázar-Alay and M. A. A. Meireles, Physicochemical properties, modifications and applications of starches from different botanical sources, Food Sci. Technol., 2015, 35(2), 215–236 CrossRef.
- S. M. Amaraweera, C. Gunathilake, O. H. P. Gunawardene, N. M. L. Fernando, D. B. Wanninayaka and R. S. Dassanayake, et al., Development of Starch-Based Materials Using Current Modification Techniques and Their Applications: A Review, Molecules, 2021, 26(22), 6880 CrossRef CAS.
- M. Sapper and A. Chiralt, Starch-Based Coatings for Preservation of Fruits and Vegetables, Coatings, 2018, 8(5), 152 CrossRef.
- Y. Chen, H. Liu, L. Yu, Q. Duan, Z. Ji and L. Chen, Superhydrophobic Modification on Starch Film Using PDMS and Ball-Milled MMT Coating, ACS Sustain. Chem. Eng., 2020, 8(28), 10423–10430 CrossRef CAS.
- F. Wang, R. Chang, R. Ma, H. Qiu and Y. Tian, Eco-Friendly and pH-Responsive Nano-Starch-Based Superhydrophobic Coatings for Liquid-Food Residue Reduction and Freshness Monitoring, ACS Sustain. Chem. Eng., 2021, 9(30), 10142–10153 CrossRef CAS.
- F. Wang, R. Chang, R. Ma and Y. Tian, Eco-friendly and superhydrophobic nano-starch based coatings for self-cleaning application and oil-water separation, Carbohydr. Polym., 2021, 271, 118410 CrossRef CAS.
- M. Ghasemlou, P. H. Le, F. Daver, B. J. Murdoch, E. P. Ivanova and B. Adhikari, Robust and Eco-Friendly Superhydrophobic Starch Nanohybrid Materials with Engineered Lotus Leaf Mimetic Multiscale Hierarchical Structures, ACS Appl. Mater. Interfaces, 2021, 13(30), 36558–36573 CrossRef CAS.
- O. D. Akinfenwa, O. S. I. Fayomi, J. O. Atiba and B. E. Anyaegbuna, Development of starch-modified titanium oxide paired with zinc powder using the electrodeposition technique as a composite superhydrophobic coating for mild steel, Int. J. Adv. Des. Manuf. Technol., 2024, 130(5–6), 2847–2854 CrossRef.
- Y. Bai, H. Zhang, Y. Shao, H. Zhang and J. Zhu, Recent Progresses of Superhydrophobic Coatings in Different Application Fields: An Overview, Coatings, 2021, 11(2), 116 CrossRef CAS.
- L. d. R. S. Carneiro, M. Houmard and P. Ludvig, Recent Advances and New Discussions on Superhydrophobic Coatings and Admixtures Applied to Cementitious Materials, The Open Construction & Building Technology Journal, 2020, 14(1), 400–409 Search PubMed.
- L. Wang, X. Guo, H. Zhang, Y. Liu, Y. Wang and K. Liu, et al., Recent Advances in Superhydrophobic and Antibacterial Coatings for Biomedical Materials, Coatings, 2022, 12(10), 1469 CrossRef CAS.
- N. T. Mutters, F. Günther, A. Heininger and U. Frank, Device-related infections in long-term healthcare facilities: the challenge of prevention, Future Microbiol., 2014, 9(4), 487–495 CrossRef CAS.
- X. y. Xu, Y. f. Chen, Q. g. Tan, Z. j. Chen, Y. Li and W. g. Wu, et al., Construction of multilayer films with bactericidal and long-term antitumor drug release properties as a non-vascular stent coating for therapy in obstruction, J. Mater. Chem. B, 2019, 7(32), 4963–4972 RSC.
- C. Shillingford, N. MacCallum, T. S. Wong, P. Kim and J. Aizenberg, Fabrics coated with lubricated nanostructures display robust omniphobicity, Nanotechnology, 2014, 25(1), 014019 CrossRef CAS.
- S. Lu, Y. Zhao and E. A. P. Hellerman, UV-durable self-cleaning coatings for autonomous driving, Sci. Rep., 2024, 14(1), 8066 CrossRef CAS.
- X. Liu, K. Chen, D. Zhang and Z. Guo, One-Step Methods to Fabricate Durable Superhydrophobic Coatings for Flexible Electronic Sensors, Coatings, 2021, 11(1), 95 CrossRef CAS.
- L. Li, Y. Bai, L. Li, S. Wang and T. Zhang, A Superhydrophobic Smart Coating for Flexible and Wearable Sensing Electronics, Adv. Mater., 2017, 29(43), 1702517 CrossRef.
- L. Wu, L. Wang, Z. Guo, J. Luo, H. Xue and J. Gao, Durable and Multifunctional Superhydrophobic Coatings with Excellent Joule Heating and Electromagnetic Interference Shielding Performance for Flexible Sensing Electronics, ACS Appl. Mater. Interfaces, 2019, 11(37), 34338–34347 CrossRef CAS.
- X. Zhou, H. Zang, Y. Guan, S. Li and M. Liu, Superhydrophobic Flexible Strain Sensors Constructed Using Nanomaterials: Their Fabrications and Sustainable Applications, Nanomaterials, 2023, 13(19), 2639 CrossRef CAS.
- H. Y. Erbil, Practical Applications of Superhydrophobic Materials and Coatings: Problems and Perspectives, Langmuir, 2020, 36(10), 2493–2509 CrossRef CAS.
|
This journal is © The Royal Society of Chemistry 2024 |
Click here to see how this site uses Cookies. View our privacy policy here.