DOI:
10.1039/D4RA00794H
(Paper)
RSC Adv., 2024,
14, 25685-25694
A study on value addition of cow dung-based anaerobic sludge for biomethane and bio-oil production via co-liquefaction with rice straw and clam shells as a catalyst†
Received
31st January 2024
, Accepted 25th July 2024
First published on 15th August 2024
Abstract
The waste management sector is moving towards sustainable approaches for facilitating resource-recovery possibilities. Agriculture residue (rice straw), cow dung (cattle waste), and clam shells from the ocean are the primary waste materials possessing a huge value addition opportunity. In this study, the effective usage of rice straw and anaerobic sludge from cow dung for bio-energy production was studied. Cow dung was initially anaerobically processed for the generation of biomethane and sludge in a digester for a retention time of 40 days. The anaerobic sludge with rice straw was hydrothermally processed in varying proportions of 1
:
0, 0
:
1, 1
:
1,1
:
2, 2
:
1, 3
:
1, 1
:
3 and temperatures of 240–360 °C for 1 hour with varying biomass loads of 50, 75, 100, 125, and 150 g. Additionally, clam shells, one of the best bioresources, were used as a catalyst in the hydrothermal process at concentrations of 0.2–1 wt%. The maximum bio-oil produced was 36.23 wt% at a temperature of 320 °C, with a biomass load of 100 g, mixed proportion of 2
:
1 and catalyst loading of 0.6 wt%. The produced bio-oil comprised hydrocarbons, aldehydes, and carboxylic acids, as confirmed through GC-MS. In the anaerobic study, ≈0.018 m3 cumulative gas was produced at a retention time of 40 days. The biochar had a higher carbon content and its feasibility for further usage shows promise towards sustainability.
1. Introduction
Managing waste irrespective of the source has demanded attention in the past few decades owing to climate change issues. Among the many technologies attempted for the conversion of plant- or animal-based waste, waste-to-energy transformation technologies are more sought after owing to their dual benefits of waste management and energy recovery.1 Automated batch anaerobic reactors have been used to study the influence of hybrid substrates in biogas yield for higher methanation. In earlier studies, biogas potential was an important parameter for evaluating the choice of substrates. While yield remains an important parameter for selecting the substrate to be converted to biogas, the composition of biogas also influences the choice of the substrates. For any substrate, including animal waste, to be processed for biogas production, the C/N ratio, pH value, and content of volatile solids and total solids are crucial aspects to consider.
Biogas production and subsequent methanation are becoming popular, with many researchers focussing on anaerobic sludge to explore its potential as a source of energy. With the immense emphasis on biogas production, the management of digestate, a moisture-rich organic and mineral mixture, becomes significantly important. Typically, a 1 MW biogas power plant produces 40 tonnes of digestate, which is expected to increase with increasing plant capacities. The huge capacity and high value of digestate provides scope for newer developments in the field of bio-energy.2 Digestates obtained after the generation of biogas via the anaerobic digestion of varied biomasses prove to be different in their characteristics. After biogas recovery and limiting the time the digestate is held in the digestor, the disposal and transportation of nutrient-rich slurry is difficult owing to its composition. The handling of digestate after separating it into liquid and solid fractions for soil-nutrient supplementation has been studied earlier. While the liquid fraction can be diluted several times and used as a growth medium, the solid fraction has numerous benefits when applied on agricultural fields directly or after being dried, composted or pelletized.3–6
Digestate application as a nutrient supplement is still in its nascent stage of study, while the application of the same for methane production also remains underexplored. Consequently, the present study focused on evaluating in detail the characteristics of cow dung-based anaerobic sludge for biomethane and bio-oil production. Biogas production in different types of digesters, including the fixed dome, floating roof, balloon, and strong plastic bag digesters,7 by co-digestion has been investigated. It has been found that variations in the substrate characteristics are not ideal for achieving an effective biogas yield. To improve digestion of the substrate by improving its properties, co-digestion has been widely applied.8 A detailed study was performed on the influence of the TSS, VS, and lignin of the substrates, including the manure of cattle, pig, and poultry, and it was found that inhibition of the methane yield was correlated to a higher percentage of lignin in the substrate.9 However, the synergistic effect of high-lignin cow dung anaerobic sludge with rice straw is yet to be explored. It was thus attempted in this study by employing a co-liquefaction process for biomethane and bio-oil production.
Hydrothermal reactors10 have been successfully used to carry out the liquefaction process with single and mixed substrates, both in the presence and absence of catalysts.11 The activation energy of the substrates plays a major role during the process. To address the energy requirement for the reaction, catalysts have been utilized to study the kinetics of the hydrothermal liquefaction process. Apart from speeding up the reaction, several catalysts for liquefying various substrates have been reported to achieve better quantity and quality of the bio-oil. Both homogeneous and heterogeneous catalyst systems, including alkaline salts, organic acids, transition metals, and metal oxides have been tested for bio-oil production.12
In this study, the effective usage of bioresources, like cow dung, rice straw, anaerobic sludge, and clam shells, were tested for bio-energy production (Fig. 1). The novelty of the study is the effective integration of such resources for their sustainable usage and better product recovery. In this study, the anaerobic study was performed for 40 days with 6 kg of cow dung. Hydrothermal liquefaction (HTL) experiments were performed with cow dung, rice straw, and in mixed proportions of 1
:
0, 0
:
1, 1
:
1,1
:
2, 2
:
1, 3
:
1, 1
:
3 and temperatures of 240–360 °C for 1 hour with varying biomass loads of 50, 75, 100, 125, and 150 g, respectively. The HTL products were recovered, characterized via FT-IR, GC-MS, elemental analysis, and their reuse possibilities were explored.
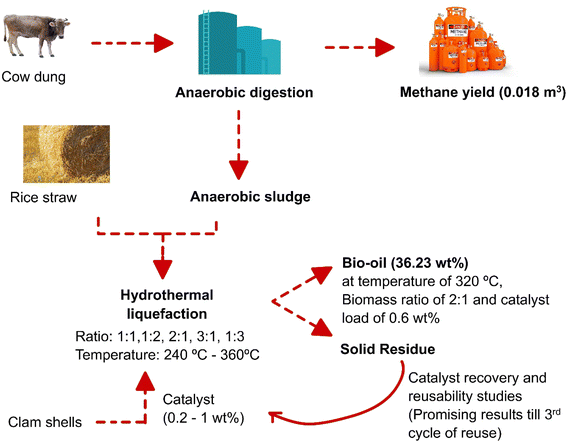 |
| Fig. 1 Hydrothermal liquefaction of rice straw and cow dung after anaerobic digestion towards sustainable waste utilization for bio-oil production. | |
2. Experimental
2.1 Catalyst synthesis and characterization
The clam shells were collected from the seashore off Mahabalipuram in the district of Tamil Nadu to synthesize an eco-friendly catalyst. The collected clam shells were cleaned under running tap water and dried at 180 °C for 10 h using a hot air oven. The hot-air-dried clam shells were then fine powdered using a ball mill and sieved to obtain a uniform size. The fine-powdered clam shells were then calcined at 600 °C for 3 h. The obtained calcinated powder of about 40 g was then mixed with 750 mL of 2 N hydrochloric acid (HCl) and 750 mL of 2 N sodium hydroxide (NaOH) and stirred at room temperature for 80 min. During the vigorous mixing, the mixture gets turbid and calcium hydroxide (Ca (OH)2) precipitation occurs. The precipitated calcium hydroxide was then washed with distilled water and dried at 100 °C for 6 h using a hot air oven. Finally, the obtained calcium hydroxide was used as a catalyst in the further hydrothermal liquefaction process.
2.2 Anaerobic digestion of cow dung
A lab-scale anaerobic digestion was performed using a 30 L capacity cylindrical digester for 40 days with an initial feed of 6 kg of cow dung. The effect of pH of the cow dung was evaluated for biomethane formation. Effective mixing was performed using a mechanical stirrer in order to enhance the reaction rates to prevent clogging problems. The anaerobic reaction was performed at 35 °C and maintained at the same temperature throughout the digestion process. The gas production during the anaerobic digestion was collected in air-tight collection bags. The volatile matter, pH, and COD of the digester were monitored continuously at regular intervals. The total cylindrical capacity of the digester was not used completely and a head space was left for the gas production. The produced gas was then collected from the sampling ports from the top of the digester and analysed for its composition using a gas meter. The produced gas composition was then analysed by gas chromatography (GC).
2.3 Biomass collection and characterization
The biomass of rice straw was collected near Cuddalore, district of Tamil Nadu, India, while the cow dung was collected from a cattle farm near Kalavakkam, district of Tamil Nadu, India. Anaerobic sludge obtained from the lab-scale anaerobic digester was taken for further studies. Each of the biomasses was characterized for its moisture content, ash content, fixed carbon, volatile compounds, and CHNS analysis. The moisture content and ash content were characterized as per the ASTM standards. Analysis of the carbon, hydrogen, nitrogen, sulphur, and oxygen contents was performed using a PerkinElmer 2400 series CHNS analyser. Thermogravimetric analysis (TGA) was performed to understand the pyrolytic behaviour of each of the biomasses under a nitrogen environment. Each of the biomass was heated at varying heating rates of 10, 20, 30, 40 and 50 °C min−1 from 25 °C to 800 °C.
2.4 Hydrothermal liquefaction experiments
The biomass of rice straw (RS) and the anaerobic sludge (AS) were subjected to hydrothermal liquefaction (HTL) at a ratio of 1
:
1,1
:
2, 2
:
1, 3
:
1, 1
:
3 in a high-pressure autoclave reactor (4598, Parr reactor) equipped with a temperature and auto cooling controller. The residues present in the reactor were removed using water at 350 °C for 3 h before beginning the experiment. Biomass samples of about 50, 75, 100, 125, and 150 g were liquefied with 1000 mL water in the temperature range between 240–360 °C for a reaction time of 1 h. The HTL reactor was continuously stirred at 680 rpm under a nitrogen environment at about 5 MPa. The effect of the synthesized catalyst from clam shells was studied with varying concentrations of 0.2–1 wt%. After completion of the liquefaction process, the heater unit was turned off and further cooling was performed to recover the products. The gaseous products were collected and analysed before dismantling the reactor. The biocrude oil was recovered from the HTL reactor and processed for bio-oil extraction.
2.5 HTL products recovery
The biocrude oil acquired from the hydrothermal liquefaction process was processed further for bio-oil extraction and solid residue recovery. Hexane was used as a solvent for the extraction of bio-oil-rich hydrocarbons from the obtained biocrude oil. The excess hexane was removed using a rotary vacuum evaporator. The bio-oil phase having hydrocarbons was from the organic phase, whereas the wastewater consisted of acid components and lower molecular weight compounds. The bio-oil yield and higher heating value (HHV) were calculated using eqn (1) and (2). |
 | (1) |
|
HHV (MJ Kg−1) = 0.338 × C + 1.428 × (h − O/8)
| (2) |
2.6 HTL products characterization
The composition of the acquired bio-oil was then evaluated using a gas chromatography system (YL Clarity 7500 GC) equipped with a flame ionization detector (FID). Helium was used as a carrier gas at a flow rate of 1 mL min−1. The analysis was done from the initial temperature of the column of 50 °C and increased to 300 °C at a rate of 5 °C min−1 and held at that final temperature for 5 min. Functional group analysis of the bio-oil was carried out using a Fourier-transform infrared (FT-IR) and Raman spectrometer obtained from Bruker Company (EQUINOX 55).
2.7 Catalyst recovery and reusability
Solid residue recovered after bio-oil extraction from the HTL process has a higher composition of carbon and also some left-over unused catalyst. The novelty of this study was to use this solid residue as a catalyst in a hydrothermal liquefaction process for bio-oil production. The solid residue was thus heated in a furnace for 20 min at high temperature to remove the ash content and then washed to extract the unused catalyst. The reusability study was performed for 5 consecutive cycles. The catalyst load was optimized for a better bio-oil yield from the results of the catalyst loading experiments.
3. Results and discussion
3.1 Catalyst characterization
The catalyst used in this study was a bio-resource material, as an initiative towards the effective usage of natural biomaterial wastes for energy recovery. Clam shells are effective catalysts as their chemical composition is rich in calcium oxide. The clam shells were analysed using SEM and BET. The SEM image (Fig. 2) confirmed the presence of agglomerates on the surface, which is an effective sign of the potential catalytic application. The average particle size was 36 nm and surface area was 38.6 m2 g−1, respectively. The major idea behind the usage of clam shell was its non-toxic, eco-friendly, and cost-effective nature. A recent study using clam shell as a catalyst in the HTL process of Scenedesmus obliquus showed a surface area of 42 m2 g−1 and particle size of 40 nm.13
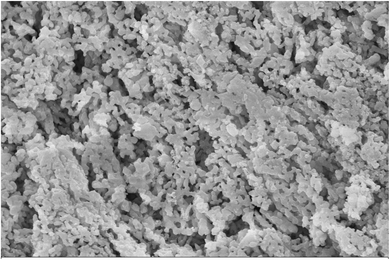 |
| Fig. 2 SEM image of clam shells obtained from natural resources for use as a catalyst. | |
3.2 Biomass characterization
3.2.1 Thermogravimetric analysis. Thermogravimetric analysis (TGA) was used to predict the thermal stability of the waste biomasses and their pyrolytic behaviour in accordance with existing literature.14 TGA has three steps, the first of which is likely to be moisture removal, the second pyrolysis, and the third carbonaceous component degradation. TGA was performed over a wide temperature range (100–800 °C) to determine the pyrolytic temperature for the experiments, as shown in Fig. 3. Analysis of the biomass showed the degradation and loss of moisture, organic compounds, and carbonaceous molecules of the biomass at three different stages, in which the moisture was removed in the first stage below 200 °C. The organic substances were degraded in the second stage at temperatures of 200–600 °C. After 600 °C, weight loss was 22, 21, 19, 18, and 19 wt% for the biomasses of RS and AS in proportions of 1
:
01, 1
:
02, 2
:
01, 1
:
03, and 3
:
01, respectively. A similar pattern has been documented in prior literature.15,16
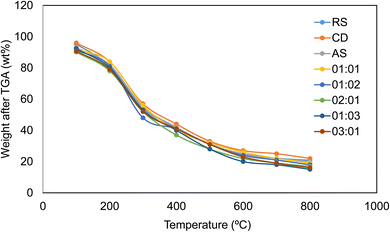 |
| Fig. 3 Thermogravimetric analysis of RS, CD, and AS biomasses. | |
3.2.2 Proximate and ultimate elemental analysis. The proximate and ultimate elemental analyses of RS, CD, and AS were performed before the hydrothermal liquefaction reaction process. The quality and yield of the bio-oil depend on the composition of the biomass. According to research, the composition of biomass feedstock can influence the calorific value of bio-oil. In particular, a low ash content biomass is best advised for bio-oil production.17 The ultimate analysis for the raw biomasses of CD, RS, and AS showed they comprised carbon contents of 36.8, 41.3, and 39.8 wt%; nitrogen contents of 3.2, 3.89, and 2.8 wt%; hydrogen contents of 7.4, 3.89, and 6.5 wt%; sulfur contents of 0.28, 1.26, and 1.39 wt%; and oxygen contents of 52.32, 49.66, and 49.51 wt%, respectively. Further, the high heating values (HHVs) of the raw biomasses (CD, RS, and AS) were 13.66648, 19.65001, and 13.89687 MJ Kg−1; the H/C contents were 2.413043, 1.130266, and 1.959799; and the O/C contents were 1.066304, 0.901816, and 0.932977. Similarly, the elemental compositions of the biomasses with RS
:
AS proportions of 1
:
01, 1
:
02, 2
:
01, 1
:
03, and 3
:
01 were analysed and the results showed carbon contents of 38, 36, 39, 40, and 37 wt%; hydrogen of 8.1, 7.9, 7.5, 7.4, and 7.6 wt%; nitrogen of 2.3, 2.4, 3.1, 2.7, and 2.8 wt%; sulfur of 0.9, 1.1, 0.8, 0.78, and 1.23 wt%; and oxygen of 50.7, 52.6, 49.6, 49.12, and 51.37 wt%. The higher heating value (HHV) for each biomass according to the aforementioned proportions was 251
685, 14.0601, 15.0384, 15.31928, and 14.18926 MJ kg; H/C was 2.558795, 2.63333, 2.307692, 2.22, and 2.464865; and O/C was 1.000658, 1.095833, 0.953846, 0.921, and 1.041284.Proximate analysis for the raw proportionated biomasses of CD, RS, and AS was next performed in which the moisture content was 8.4%, 11.2%, and 9.8%; the ash content was 14.5%, 6.8%, and 7.6%; the volatile matter was 58.6%, 59.6%, and 54.23%; and the fixed carbon was 18.5%, 22.4%, and 28.37%. For the aforementioned proportionated biomasses of CD, RS, and AS at 1
:
01, 1
:
02, 2
:
01, 1
:
03, and 3
:
01, the moisture content % was 10.2, 9.8, 8.910.2, and 9.2; ash content % was 8.9, 9.4, 8.7, 9.5, and 9.1; volatile matter % was 51.3, 49.8, 52.6, 53.1, and 49.8; and fixed carbon % was 29.6, 31, 29.8, 27.2, and 31.9, respectively.
3.3 Anaerobic digestion process
The cumulative biogas production from the anaerobic digestion of cow dung for a period of 40 days is shown in Fig. 4. It could be seen that the biogas production was lesser in the initial stages and the later ending stages. The lag phase generated in the microbial consortium for adapting to the newer environment was the major reason contributing to the lower biogas production in the initial stages of the methanation process. The lag phase was accompanied by an exponential growth of the microbial community, which led to the presence of more living cells in the stationary phase.18 The biogas production in the batch process mainly depends on the presence and count of the methanogenic bacteria.19,20 The maximum biogas production per day was seen in the 2nd weekend of the study. Biogas production was seen to reduce at the later stages of the study, which was due to the change in pH of the digestate, and the presence of ammoniacal nitrogen inside the reactor. Indeed, it is well known that a higher concentration of ammoniacal nitrogen is toxic to methanogens.21 From the batch study, it was seen that the total cumulative biogas produced from the cow dung was 0.018 m3 at a retention time of 40 days. From this preliminary study, it was found that the temperature, pH, ammoniacal nitrogen, inoculum, and retention time are the major factors that contribute to the biogas production. Co-digesting manure with HTL-PW (process water) from wheat straw-manure by co-HTL yielded methane (43–49% of the chemical oxygen demand, COD) at concentrations of up to 17.8 gCOD L−1, whereas HTL-PW from sewage sludge yielded methane (43% of the COD) at up to only 12.8 gCOD L−1 and complete inhibition occurred at 17 gCOD L−1.22
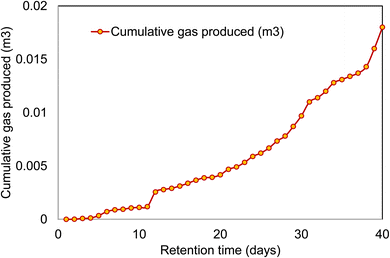 |
| Fig. 4 Cumulative gas production from cow dung via anaerobic digestion. | |
3.4 Hydrothermal liquefaction studies
3.4.1 Effect of temperature. This section discusses and deals with the composition and yield of the aforementioned proportioned biomasses of RS
:
AS. The bio-oil, solid residue, aqueous phase, and gaseous phase are the main four products obtained from the hydrothermal liquefication process.23 The effect of the thermal conditions on bio-oil was tested at various temperatures ranging from 240 °C to 360 °C with varying waste biomass to anaerobic sludge ratios. Fig. 5 depicts the fluctuation of the yield for the different biomass ratios with the liquefaction temperature. An increase in bio-oil generation was observed when temperature was increased from 300 °C to 320 °C, with the highest bio-oil yield of 32% by weight recorded, followed by a decline in yield to 30% at 360 °C. The solid residues as by-products of biochar are heterogeneous materials extracted from the HTL products of different biomass ratios under controlled conditions. An 11.7 wt% yield was obtained when the temperature was at 320 °C, as shown in Fig. 6. Agricultural wastes, such as rice straw (RS), provide an opportunity to decrease waste production while also upgrading the same into value-added products. Moreover, from energy, environmental, and economic standpoints, RS is a resourceful agricultural residue with the potential for complete valorisation and diverse product production capabilities.24
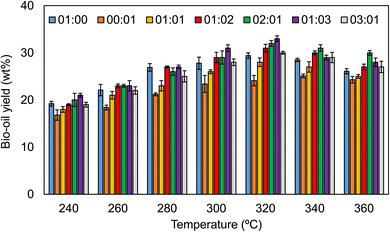 |
| Fig. 5 Effect of temperature on bio-oil yield (%). | |
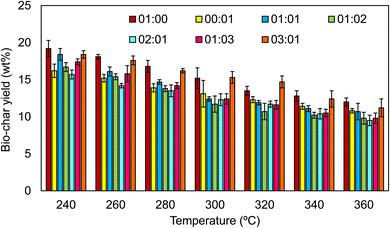 |
| Fig. 6 Effect of temperature on biochar yield (%). | |
3.4.2 Effect of biomass load. The hydrothermal liquefaction product yield obtained by the different waste biomass to anaerobic sludge proportions is shown in Fig. 7. The biomass loading at different compositions at 320 °C is elaborated as well. The biomass loading at 100 g L−1 resulted in a higher bio-oil yield than at 150 g L−1, which could be attributed to the lack of solvent and biomass degradation for depolymerization of the biomass. It was recently discovered that a suitable amount of solvent is necessary for successful biomass decomposition to produce liquefied products.25 The maximum yield of bio-oil was 29.7 wt% when using 100 g L−1 biomass at a temperature of 320 °C. At these same conditions, the by-products produced were 16 wt% biochar, 24.3 wt% aqueous phase, and 30 wt% gaseous phases, respectively. Processing rice crop waste results in a unique combination of lignocellulosic and starchy waste streams largely available for value-added bio-oil extraction. As such, the complex variety of compositions is one of the challenges to be still faced at the industrial level for achieving the full exploitation of all rice by-products into biofuels.26
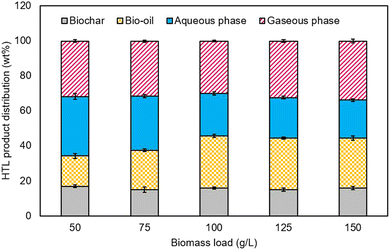 |
| Fig. 7 Effect of biomass load. | |
3.4.3 Effect of the biomass composition. The biomass composition is the primary factor that affects the yield of bio-oil. Here, the rice straw and anaerobic sludge wastes were liquified at different biomass ratios (1
:
1, 1
:
2, 2
:
1, 3
:
1, 1
:
3) and added at an optimized temperature of 320 °C for 100 g L−1, as indicated in Fig. 8. Of the five different biomass loading composition rates tested, the ratio of 2
:
1 (RS
:
AS) produced the highest yield of bio-oil, approximately 33.6 wt%, under the optimized conditions (320 °C). Sometimes, increasing the biomass composition and temperature (360 °C) led to a lower production yield of the desired bio-oil same as in Fig. 5. Processing the rice straw at 350 °C, 18 MPa, 30 min led to the highest biocrude yield from HTL (36.4 wt%). Also, ions like K+, PO43−, and NH4+ accumulated in the aqueous phase from the rice straw.27
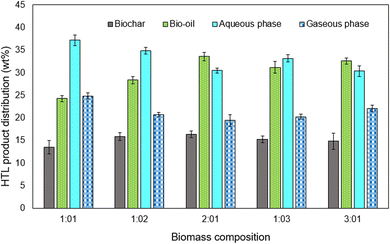 |
| Fig. 8 Effect of biomass composition. | |
3.4.4 Effect of the catalyst. The performance of the synthesized catalyst made from clam shells was studied at different catalyst concentration loads for obtaining the highest bio-oil yield. Catalyst concentrations of 0.2–1.0 wt% for 100 g of biomass at a temperature of 320 °C were studied. From Fig. 9, it can be seen that the increase in catalyst loading from 0.6 wt% to 0.8 wt% led to a high bio-oil yield, while further increasing the catalyst load to 1.0 wt% actually reduced the bio-oil yield. The maximum achieved bio-oil yield was found to be 37.12% with the catalyst concentration of 0.8 wt%, while the gas phase yield was 27.18 wt%, with the composition of gases including carbon dioxide, hydrogen, ammonia, and carbon monoxide.
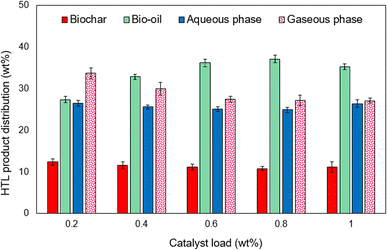 |
| Fig. 9 Effect of the catalyst on HTL product distribution from 2 : 1 mixed biomass (rice straw and anaerobic sludge). | |
3.5 HTL products characterization
3.5.1 Bio-oil properties. The elemental compositions and the estimated HHVs of the bio-oils acquired from cow dung, rice straw, anaerobic sludge, and a 2
:
1 ratio of rice straw and anaerobic sludge were determined. The C, H, N, S, and O contents of cow dung and rice straw were found to be 58, 6.8, 0.8, 0.13, 34.27 wt% and 59, 4.5, 1.1, 0.45, and 34.95 wt%. Likewise, the C, H, N, S, and O contents of anaerobic sludge and the 2
:
1 ratio of rice straw
:
anaerobic sludge were found to be 58.4, 5.9, 0.7, 0.37, and 34.63 wt% and 66, 7.5, 0.2, 0.18, and 26.12 wt%. The HHV of each of the bio-oil for cow dung was 23.19721, for rice straw was 20.12943, for anaerobic sludge was 21.98295, and for the 2
:
1 ratio of rice straw and anaerobic sludge was 28.35558. Among the four different bio-oils, the highest HHV was seen for the 2
:
1 ratio of rice straw and anaerobic sludge while the least HHV was observed for the rice straw bio-oil. The H/C of bio-oil for cow dung was 1.406897, for rice straw was 0.915254, for anaerobic sludge was 1.212329, and for the 2
:
1 ratio of rice straw to anaerobic sludge was 1.363636. The O/C of bio-oil from cow dung was 0.443147, for rice straw was 0.44428, for anaerobic sludge was 0.444735, and for the 2
:
1 ratio of rice straw to anaerobic digestion was 0.296818.The bio-oil obtained from rice straw, anaerobic sludge and the mixed (2
:
1) material showed kinematic viscosities of 6.13, 7.28, and 7.63 mm2 s−1, and densities of 968, 921, and 971 kg m−3, respectively. A higher viscosity bio-oil would need a high pressurized pumping system for ensuring ignition of the combustion chambers of the engine. Also, a catalytic cracking effect may lead to a reduction in the kinematic viscosity of bio-oil. Here, the breakdown of high carbon chains results in fragmentation of the compounds present in the bio-oil, which in turn reduces the viscosity of the bio-oil.28
3.5.2 FT-IR analysis. The FT-IR spectra helped to identify the functional groups present on the surface of the material. The FT-IR spectra of bio-oils produced from rice straw, anaerobic sludge, and the mixed biomass (2
:
1) are shown in Fig. 10–12. The peaks were categorized in the range of 3000–3600 cm−1 corresponding to N–H and O–H stretching vibrations. Peaks were seen at 3437.05, 3402.72, and 3350.70 cm−1 for the rice straw, anaerobic sludge, and mixed biomass (2
:
1) individually. Further, the peak at 2918.15 cm−1 corresponded to C
O functional groups. The bio-oils obtained from rice straw (peaks at 1705.82, 1616.43, 1383.72, 1102.30 cm−1), anaerobic sludge (peaks at 1697.96, 1602.47,1435.62, 1273.02 cm−1), and mixed biomass (peaks at 1614.46, 1515.28, 1373.20, 1109.85 cm−1) showed the presence of carbonyl groups, C–O groups, and aromatic composites. In a study of the hydrothermal liquefaction of Prosopis juliflora biomass, the bio-oil obtained displayed peaks at 3314.03 cm−1 corresponding to O–H and N–H stretching. Further, peaks were observed at 2111.87 cm−1 corresponding to C–H stretching vibrations.29
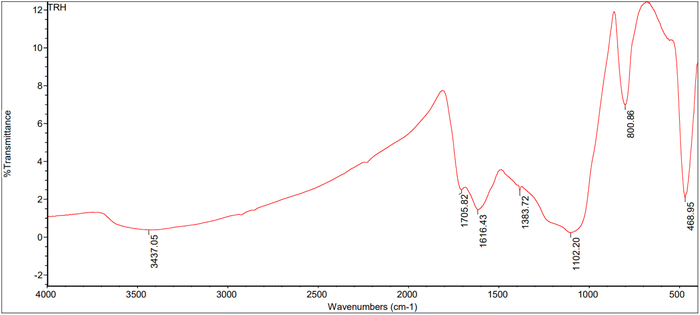 |
| Fig. 10 FT-IR spectra of bio-oil obtained from rice straw. | |
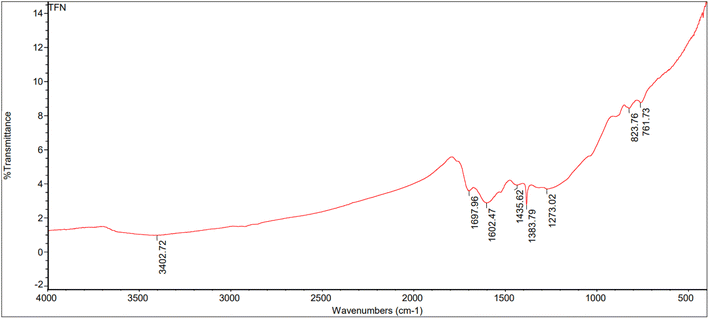 |
| Fig. 11 FT-IR spectra of bio-oil obtained from anaerobic sludge. | |
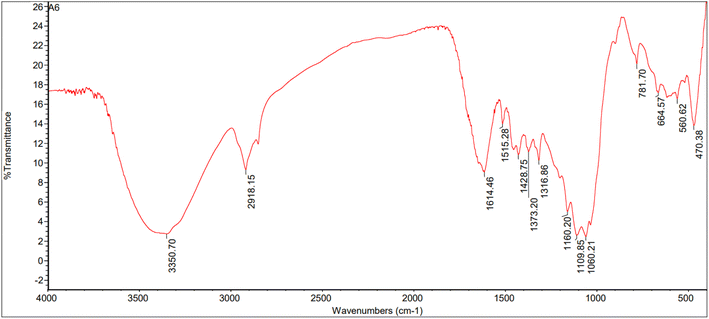 |
| Fig. 12 FT-IR spectra of bio-oil obtained from mixed RS and AS (2 : 1 ratio). | |
3.5.3 GC-MS analysis. The molecular composition and the specific concentration of molecules from the bio-oils were analysed using GC (FID)-MS. The bio-oil compositions of rice straw, anaerobic sludge, and the 2
:
1 ratio of rice straw and anaerobic sludge were investigated for determining their molecular compositions. Each of the bio-oils were studied for the presence of hydrocarbons, furfurals, carboxylic acids, aldehydes, and others. From Fig. 13, the highest percentage of hydrocarbons was seen in the 2
:
1 ratio of rice straw and anaerobic sludge-based bio-oil while the lowest hydrocarbon content was obtained from the anaerobic sludge bio-oil. The remaining furfurals, carboxylic acids, aldehydes, and other components were comparatively less abundant compared to the hydrocarbons. The carboxylic content was seen to be more or less the same at about 15 wt% in both the rice straw and 2
:
1 ratio of rice straw and anaerobic sludge. The highest number of aldehydes was seen in the rice straw-based bio-oil. In general, the compounds in bio-oil can be categorized as alkanes, aromatics, phenolics, ketones, and alkenes.30 The nitrogen content in the bio-oil can be reduced by deamination, cyclization, and amino acid cracking processes.31
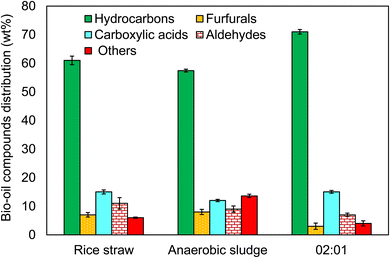 |
| Fig. 13 GC-MS profile of bio-oil obtained from individual and mixed biomasses. | |
3.6 Biochar analysis and catalyst reusability recommendation
The hydrothermal experiments revealed the formation of biochar as a by-product. Biochar has numerous applications and scope in a wide research area. The biochars obtained from anaerobic sludge, rice straw, and in their combination (2
:
1) were analysed for via CHNS to show its C/N ratio. The biochar obtained from the HTL of anaerobic sludge comprised C, H, N, S, and O as 78.9, 1.9, 0.15, 1.2, and 17.85 wt%, individually. Similarly, biochar from the HTL of rice straw had C, H, N, S, and O contents of 83, 1.8, 0.3, 2.4, and 12.5 wt%, individually. The combined biomass (2
:
1) comprised C, H, N, S, and O of 82.6, 2.1, 0.14, 0.9, and 14.26 wt%, respectively. All three biochars (anaerobic sludge, rice straw, and mixed) showed HHVs of 26.19, 28.39, and 28.37 MJ kg−1 respectively. The H/C ratios were 0.26, 0.28, and 0.30 and the O/C ratios were 0.11, 0.16, and 0.12 for the biochars obtained from the HTL of rice straw, anaerobic sludge, and mixed biomass.
To reduce the economic feasibility of the overall process, reuse of the catalyst is desired. The reusability of the biochar and HTL aqueous phase has been attracting much attention from researchers globally in a wide domain. These studies will pave the way for showing the feasibility, economics, and sustainability of the process.32 Biochar-based catalyst recovery involves oven drying and furnace-based activation, but would reduce the dependency on new loadings of catalyst for consecutive cycles.
3.7 Catalyst reusability
Recycling and reuse are among the most important factors that define the economics of the processes. In the hydrothermal process, the proper usage of resources will help to techno economic analysis. In addition to the usage of the catalyst in the HTL process, the reuse of the catalyst would improve the efficiency. From the HTL process, the unused catalyst can be recovered as a solid residue and then activated for reusage in the HTL process. Fig. 14 shows the effect of the catalyst reusability on the hydrothermal liquefaction process. The solid residue was recovered and activated to remove the carbon residues. Further, the formation of the solid residue was increased with increasing the reuse cycles from 13.2 wt% to 19.7 wt%, respectively, while, the bio-oil yield decreased from 36.5 wt% to 21.7 wt% at fifth cycle. Reusability of the catalyst showed good efficiency for 3 consecutive cycles, but beyond that the interactions in the reaction process decreased, which eventually decreased the bio-oil yield.
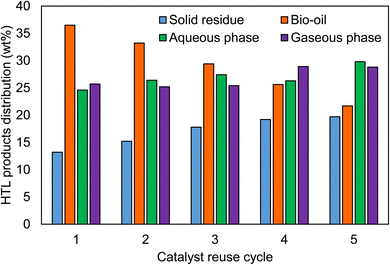 |
| Fig. 14 Catalyst reusability study and products distribution in the HTL process. | |
Next, the catalyst used in the HTL process was recovered from the solid residue and then characterized. Here, the solid residue was heated in a furnace to remove the excess carbon and was then washed for catalyst recovery. The average particle sizes of the recovered catalyst from the 1st cycle to 5th cycle were 34.1, 33.9, 33.8, 33.6, 33.4 nm and the surface areas were 36.7, 36.5, 36.2, 35.8, 34.8 m2 g−1, respectively. The major idea behind the usage of clam shell was its non-toxic, eco-friendly, and cost-effective nature.
4. Conclusion
The sustainable usage of cow dung and rice straw could pave the way for better bio-energy production. The use of cow dung in anaerobic digestion for a retention time of 40 days produced a cumulative gas amount of 0.018 m3. Also, anaerobic sludge in combination with rice straw (1
:
2) was hydrothermally processed for bio-oil production of 36.23 wt% at a temperature of 320 °C, at a biomass load of 100 g and catalyst load of 0.6 wt%. The biochar comprised C, H, N, S, and O at 82.6, 2.1, 0.14, 0.9, and 14.26 wt%, respectively. The bio-oils obtained from rice straw, anaerobic sludge, and mixed (2
:
1) showed kinematic viscosities of 6.13, 7.28, and 7.63 mm2 s−1, and densities of 968, 921, and 971 kg m−3, respectively. This study provides further ideas for improving the sustainability, scale-up, and industrialization of process in line with the UN sustainable development goals (SDGs). In future, this study needs to be compared with the pure calcium oxide to depict its efficiency. This study provides integrated approaches to utilize rice straw, cow dung, and clam shells for resource recovery. In future, numerous approaches, like catalyst inclusion for higher efficiency and multiple products recovery from the processes, could be studied.
Data availability
The data presented in this study are available from the corresponding author upon reasonable request.
Author contributions
Conceptualization, H. S. A., M. R. K. and A. H. S.; methodology, A. H. S., J. A. M., M. O. A. and A. H.; software, A. H. S., M. R. K., J. A. M. and A. H.; validation, I. A. A., M. R. K. and M. O. A.; formal analysis, I. A. A., M. R. K., J. A. M., M. O. A. and A. H.; investigation, H. S. A., I. A. A., M. R. K., M. O. A. and A. H. S.; resources, A. H. S. and I. A. A.; data curation, I. A. A., J. A. M., M. O. A. and A. H.; writing – original draft, A. H. S., J. A. M. and H. S. A.; writing – review & editing, H. S. A.; visualization, J. A. M.; supervision, H. S. A. and A. H. S.; funding acquisition, A. H. S. All authors have read and approved the manuscript.
Conflicts of interest
The authors declare no conflicts of interest.
Acknowledgements
The authors extend their appreciation to the Deputyship for Research and Innovation, the Ministry of Education in Saudi Arabia, for funding this research through project number IFKSUDR-E162.
References
- N. Nwokolo, P. Mukumba, K. Obileke and M. Enebe, Processes, 2020, 8, 1224 CrossRef CAS.
- M. Szymańska, H. E. Ahrends, A. K. Srivastava and T. Sosulski, Appl. Sci., 2022, 12, 4052 CrossRef.
- W. Czekała, J. Dach, R. Dong, D. Janczak, K. Malińska, K. Jóźwiakowski, A. Smurzyńska and M. Cieślik, Biosyst. Eng., 2017, 160, 25–29 CrossRef.
- T. Chen, X. Qiu, H. Feng, J. Yin and D. Shen, Bioresour. Technol., 2021, 325, 124706 CrossRef CAS PubMed.
- Y. Qiao, S. Zhang, C. Quan, N. Gao, C. Johnston and C. Wu, Fuel, 2020, 279, 118525 CrossRef CAS.
- F. Monlau, C. Sambusiti, E. Ficara, A. Aboulkas, A. Barakat and H. Carrère, Energy Environ. Sci., 2015, 8, 2600–2621 RSC.
- G. Lissens, P. Vandevivere, L. De Baere, E. M. Biey and W. Verstraete, Water Sci. Technol., 2001, 44, 91–102 CrossRef CAS PubMed.
- T. Böjti, K. L. Kovács, B. Kakuk, R. Wirth, G. Rákhely and Z. Bagi, Anaerobe, 2017, 46, 138–145 CrossRef PubMed.
- Y. Li, R. Zhang, G. Liu, C. Chen, Y. He and X. Liu, Bioresour. Technol., 2013, 149, 565–569 CrossRef CAS PubMed.
- S. Xiu, A. Shahbazi, C. W. Wallace, L. Wang and D. Cheng, Energy Convers. Manage., 2011, 52, 1004–1009 CrossRef CAS.
- A. Taghipour, U. Hornung, J. A. Ramirez, R. J. Brown and T. J. Rainey, J. Cleaner Prod., 2021, 289, 125582 CrossRef CAS.
- A. A. Shah, K. Sharma, M. S. Haider, S. S. Toor, L. A. Rosendahl, T. H. Pedersen and D. Castello, Processes, 2022, 10, 207 CrossRef CAS.
- J. Arun, K. P. Gopinath, P. SundarRajan, R. Malolan, S. Adithya, R. S. Jayaraman and P. S. Ajay, Bioresour. Technol., 2020, 310, 123443 CrossRef CAS PubMed.
- J. Arun, P. Varshini, P. K. Prithvinath, V. Priyadarshini and K. P. Gopinath, Bioresour. Technol., 2018, 261, 182–187 CrossRef CAS PubMed.
- J. Arun, K. P. Gopinath, R. Sivaramakrishnan, S. Shyam, N. Mayuri, S. Manasa and A. Pugazhendhi, Bioresour. Technol., 2021, 319, 124116 CrossRef CAS PubMed.
- A. Mathanker, D. Pudasainee, A. Kumar and R. Gupta, Fuel, 2020, 271, 117534 CrossRef CAS.
- T. EswaryDevi, R. Parthiban, J. Arun and K. P. Gopinath, Biomass Convers. Biorefin., 2022, 1–14 Search PubMed.
- I. M. Alfa, S. O. Dahunsi, O. T. Iorhemen, C. C. Okafor and S. A. Ajayi, Bioresour. Technol., 2014, 157, 270–277 CrossRef CAS PubMed.
- M. I. Simeon, J. Edache and D. A. Eyeowa, Biogas production from the co-digestion of cow dung and poultry droppings using a plastic cylindrical digester, Proceedings of the 2017 Annual Conference of the School of Engineering & Engineering Technology (SEET), The Federal University of Technology, Akure, Nigeria, 2017 Search PubMed.
- A. Nopharatana, P. C. Pullammanappallil and W. P. Clarke, Waste Manage., 2007, 27, 595–603 CrossRef CAS PubMed.
- S. Borowski, J. Domański and L. Weatherley, Waste Manage., 2014, 34, 513–521 CrossRef CAS PubMed.
- W. V. Macêdo, R. D. Harpøth, J. S. Poulsen, N. de Jonge, C. H. Fischer, L. M. Agneessens, J. L. Nielsen, P. Biller, C. K. Rickers and L. Vergeynst, Bioresour. Technol., 2024, 399, 130559 CrossRef PubMed.
- S. Bhat, V. B. Borugadda and A. K. Dalai, Fuel, 2021, 305, 121602 CrossRef CAS.
- S. Singh, G. Kaur, D. P. Singh, S. Arya and M. Krishania, Process Saf. Environ. Prot., 2024, 184, 314–333 CrossRef CAS.
- N. Khan, P. Chowdhary, A. Ahmad, B. S. Giri and P. Chaturvedi, Bioresour. Technol., 2020, 309, 123294 CrossRef CAS PubMed.
- A. P. Gupte, M. Basaglia, S. Casella and L. Favaro, Renewable Sustainable Energy Rev., 2022, 167, 112673 CrossRef CAS.
- S. Harisankar, R. V. Mohan, V. Choudhary and R. Vinu, Bioresour. Technol., 2022, 351, 127031 CrossRef CAS PubMed.
- F. A. Dawodu, O. O. Ayodele and T. Bolanle-Ojo, Egypt. J. Pet., 2014, 23, 191–199 CrossRef.
- J. Arun, K. P. Gopinath, R. Sivaramakrishnan, S. Shyam, N. Mayuri, S. Manasa and A. Pugazhendhi, Bioresour. Technol., 2021, 319, 124116 CrossRef CAS PubMed.
- B. Jayakishan, G. Nagarajan and J. Arun, Bioresour. Technol., 2019, 283, 303–307 CrossRef PubMed.
- L. Leng, L. Yang, J. Chen, S. Leng, H. Li, H. Li, X. Yuan, W. Zhou and H. Huang, Bioresour. Technol., 2020, 315, 123801 CrossRef CAS PubMed.
- S. S. Vigneshwar, A. Swetha, K. P. Gopinath, J. Arun, R. Sivaramakrishnan and A. Pugazhendhi, Int. J. Energy Res., 2021, 45, 19909–19920 CrossRef CAS.
|
This journal is © The Royal Society of Chemistry 2024 |
Click here to see how this site uses Cookies. View our privacy policy here.