DOI:
10.1039/D3RA06910A
(Review Article)
RSC Adv., 2024,
14, 478-491
Recent progress in TiO2–biochar-based photocatalysts for water contaminants treatment: strategies to improve photocatalytic performance
Received
11th October 2023
, Accepted 11th December 2023
First published on 2nd January 2024
Abstract
Toxic organic pollutants in wastewater have seriously damaged human health and ecosystems. Photocatalytic degradation is a potential and efficient tactic for wastewater treatment. Among the entire carbon family, biochar has been developed for the adsorption of pollutants due to its large specific surface area, porous skeleton structure, and abundant surface functional groups. Hence, combining adsorption and photocatalytic decomposition, TiO2–biochar photocatalysts have received considerable attention and have been extensively studied. Owing to biochar's adsorption, more active sites and strong interactions between contaminants and photocatalysts can be achieved. The synergistic effect of biochar and TiO2 nanomaterials substantially improves the photocatalytic capacity for pollutant degradation. TiO2–biochar composites have numerous attractive properties and advantages, culminating in infinite applications. This review discusses the characteristics and preparation techniques of biochar, presents in situ and ex situ synthesis approaches of TiO2–biochar nanocomposites, explains the benefits of TiO2–biochar-based compounds for photocatalytic degradation, and emphasizes the strategies for enhancing the photocatalytic efficiency of TiO2–biochar-based photocatalysts. Finally, the main difficulties and future advancements of TiO2–biochar-based photocatalysis are highlighted. The review gives an exhaustive overview of recent progress in TiO2–biochar-based photocatalysts for organic contaminants removal and is expected to encourage the development of robust TiO2–biochar-based photocatalysts for sewage remediation and other environmentally friendly uses.
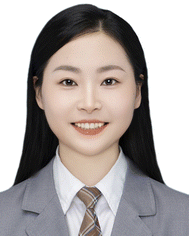 Yunfang Liu | Yunfang Liu is a graduate student in the School of Science at Beihua University under the supervision of Dr Yibo Ma. Her research directions mainly focus on preparing TiO2–biochar-based materials and their applications in photocatalysis. |
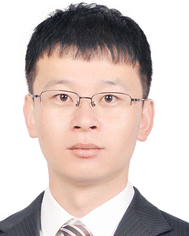 Xiaowei Dai | Dai Xiaowei, an attending physician, works at the Second Hospital of Jilin University in Changchun, China. He mainly studies urology and male reproductive diseases, such as male infertility, sexual dysfunction, and assisted reproductive technology. Academic Part-time: Young member of the Andrology Branch of the Chinese Society of Traditional Chinese Medicine Information. Young member of the Reproductive Medicine Branch of Wu Jieping Foundation. Youth member of the Reproductive Medicine Branch of the Chinese Society of Traditional Chinese Medicine. Member of the Standing Committee of the Maternal and Child Health and Andrology Society of the Chinese Sexuality Society. |
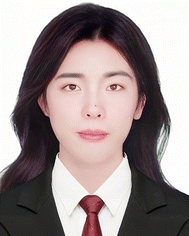 Jia Li | Jia Li received her B.S. in Physics from Changchun University in Jilin, China in 2010, and her M.S. and Ph.D. in condensed matter physics from Jilin University in China in 2015. She works at the School of Science at Beihua University in Jilin, China. For many years, she has been engaged in the research and development of new materials and physical properties. Her current research focuses on developing new carbon-based related materials, such as low-dimensional diamond and boron–carbon–nitrogen sandwich structures, exploring new structures and their electronic and optical properties, and expanding their applications in photocatalysis, nanoelectronic devices, and sensors. |
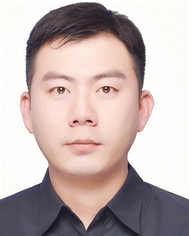 Jian Zhang | Jian Zhang received his Ph.D. degree from Jilin University in 2016. He is now a Graduate Supervisor at the College of Science Beihua University. His research focuses on the synthesis and characterization of low-dimensional layered nanomaterials and the structural design and physical properties of nanomaterials under high pressure conditions. |
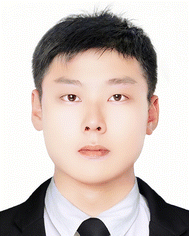 Yibo Ma | Yibo Ma received his B.S. in Physics from Jilin Normal University, Siping, China, in 2012 and his M.S. and Ph.D. in condensed matter physics from Jilin University, Changchun, China, in 2017. He works at the School of Science at Beihua University in Jilin, China. He won the “Best Researcher Award” at the “International Research Awards on Advanced Nanomaterials and Nanotechnology” in 2023 for his pioneering contributions to nanomaterials design for the photocatalysis field. His current research focuses on preparing carbon-based materials such as biochar and diamond and their applications in photocatalysis, supercapacitors, and biosensors. |
1. Introduction
Global concern has been sparked by the fact that water pollution endangers human life and harms ecosystems.1,2 It has been reported that numerous toxic organic contaminants, such as phenolic compounds, polymers, cyanides, and detergents, reside in sewage.3–6 Several human diseases, even cancer, have been related to organic pollutants in water.7,8 Therefore, hazardous contaminants found in wastewater must be appropriately disposed of to protect human health and the environment and to guarantee safe discharge. Most organic pollutants are recalcitrant, toxic, and have weak biodegradability. Thus, they cannot be degraded absolutely via traditional treatment techniques (for example, adsorption, biodegradation, and direct burning).9,10 Developing a promising treatment technology is paramount for effectively degrading contaminants and ensuring sustainable development. The photoelectrocatalytic water splitting experiment for H2 evolution under ultraviolet light in 1972 led to the development of photocatalysis technology.11,12 Notably, solar energy is a renewable, clean resource, and photocatalytic technology as an advanced oxidation process offers compelling advantages over conventional strategies for coping with chemical pollutants, such as mild reactions, no additional emissions, high degradation efficiency, and energy savings.13–15
The core of photocatalytic degradation of pollutants is to develop highly efficient and inexpensive photocatalysts. Titanium dioxide (TiO2) nanoparticles are now regarded as one of the best photocatalytic materials because they have unique electrical and optical properties, are chemically stable, and don't harm living things.16 However, the TiO2 photocatalyst, which has a broad energy band gap (3.0–3.2 eV) and can only soak up radiation in the near ultraviolet (UV) zone (approximately 5% of the total sunlight spectrum), is limited to visible light applications.17 Furthermore, most single-component photocatalysts are provided in the form of tiny particles (such as nanoscale), which effectively increases the specific surface area of the material and aids in enhancing the photocatalytic effect. However, it is more noteworthy that tiny particles can also greatly enhance the intermolecular force, leading to agglomeration effects during the treatment of pollutants, which hinder the effective decomposition of pollutants. At the same time, the recycling and reuse of nanoscale catalysts also face challenges.18 To alleviate the drawbacks, integrating photocatalytic materials with substrate materials for modification has been gradually developed and utilized. Representative substrates, including carbon materials (like activated carbon, multiwalled carbon nanotube, and reduced graphene oxide), zeolites, porous polymers, and metal–organic frameworks have been employed to investigate desirable, high-performance photocatalytic materials.19–21 Considering the quick recombination rate of photoinduced carriers and the low thermal stability of most substrates, carbon materials are superior in photocatalytic degradation applications.22 Carbon–TiO2 composites have drawn growing interest as outstanding photocatalysts since carbon materials can serve as electron traps for gathering photoinduced carriers from the photocatalyst surface.23,24 At the same time, carbon doping is an efficient approach for introducing impurities into the TiO2 lattice, which decreases the band gap and extends visible light absorption.25 Biochar is extraordinarily competitive among carbonaceous materials due to its rich in natural resources, non-metallic nature, acid and alkali resistance, and exceptional ecological sustainability, as well as its good physicochemical characteristics, including a high specific surface area, a porous framework, oxygen-containing groups, intrinsic minerals, and active binding sites.26–28 These characteristics are advantageous for the binding and growth of photocatalyst nanoparticles, leading to significant loadings, robust stability, and remarkable organic waste photodegradation capabilities.29,30 Therefore, biochar is an excellent support for TiO2-based catalysts, and in recent years, TiO2–biochar-based photocatalysts have been recommended and studied widely.
The combination of TiO2 semiconductor and biochar offers several advantages:
(1) Pristine biochar is an appropriate photocatalytic material.31–34 Several advanced oxidation processes, like Fenton-like oxidation, photocatalysis, sonocatalysis, and electrocatalysis, have utilized biochar catalysts.35–38
(2) As a supporting material for TiO2 photocatalysts, biochar has a stable structure and easy recovery.
(3) The porous structure and large specific surface area of biochar provide solid guarantees for the adsorption of pollutants, which can effectively increase the contact between pollutants and TiO2 photocatalysts, shorten the carrier migration path, and improve the photocatalytic effect.
(4) Biochar helps create vacancies, acting as photoelectron traps for captured TiO2, thereby suppressing the annihilation of photogenerated e−–h+ pairs. Concurrently, biochar enhances the heat resistance of photocatalysts, reducing their band gap and boosting the response to light sources.39
(5) The composite, coupled with biochar and TiO2 semiconductor, could present unique and complementary physicochemical properties in favor of water treatment applications.40
However, there are also many challenges associated with the combination of biochar and TiO2 photocatalysts:
(1) The preparation method of the composite photocatalysts directly affects the bonding strength between biochar and TiO2. The nonspecific binding of TiO2 photocatalysts may lead to a significant decrease in their effectiveness over time.
(2) The impurities and functional groups in biomass, influenced by factors such as growth environment, can lead to unpredictable performance of each batch of prepared biochar.
(3) The strong biochar adsorption also hinders the recycling of composite photocatalysts.
(4) Improperly applied amounts of biochar shade the light of TiO2 photocatalyst, affecting the generation efficiency of carriers.
It is time to review this intriguing topic to recapitulate current developments and, fundamentally, to acquire an in-depth knowledge of the application of TiO2 biochar-based materials in photocatalytic decontamination. This review will concentrate on the synthesis methods, physicochemical properties, advantages, and photocatalytic capacity of TiO2–biochar-based photocatalysts to remove organic effluent pollutants. Three aspects of some prospective photocatalytic efficiency enhancement strategies are highlighted. Lastly, the significant obstacles and prospects of photocatalysts based on TiO2–biochar are presented.
2. Biomass for biochar production
Biochar is a unique and renewable carbonaceous substance derived from decomposing biomass residues in oxygen-depleted conditions.41 Its porous structure and multitudinous oxygen-containing functional groups on its surface make it suitable for binding pollutant molecules.42 In addition, biochar's fitting compatibility and catalytic properties make it an exceptional pollutant removal material for practical application in photocatalysis.43
2.1 Preparation methods of biochar
It is widely accepted that biomass is the primary source of biochar's feedstock. Carbon-rich biomasses can be regenerated from agricultural and forestry byproducts, garbage, woody products, plants, animal manures, and dietary leftovers.44,45 It comprises both lignocellulosic (woody products, agricultural and forestry byproducts, plants) and non-lignocellulosic products (garbage and animal leftovers).46,47 Thermochemical techniques can directly convert these numerous forms of biomass into biochar materials.48 The most investigated thermochemical treatment methods are oxygen-limited pyrolysis and hydrothermal charring.
Pyrolysis is mainly divided into slow pyrolysis, fast pyrolysis, and flash pyrolysis. Among them, slow pyrolysis has been extensively adopted because of its substantial biochar yield, simple operation, and low cost.49,50 Zhang et al.51 produced biochar by pyrolyzing leftovers from a school cafeteria in oxygen-depleted conditions. The resultant biochar with an even surface was considered an appropriate supporter for attaching BiOBr. Zhang et al.52 prepared biochar using crop straws as a precursor by pyrolysis at 600 °C for 120 min under limited oxygen conditions. Luo et al.53 crushed poplar to obtain poplar sawdust and then heated it at 600 °C under N2 atmosphere to obtain biochar (BC), which served as a conductive aisle in the ZnFe2O4/BC/ZnO composite to improve the transportation of photoexcited electrons. Meanwhile, pyrolysis could be used to fabricate biochar doped with other elements. For instance, Wang et al.54 mixed urea and pine biochar at a particular mass ratio to produce N-modified biochar by pyrolyzing in a vacuum muffle furnace at 500 °C for 120 min. The heating temperature is one of the crucial points for producing biochar via pyrolysis. According to previous studies,55–57 researchers commonly set the heating temperature at 300–900 °C. Generally, the surface area and pore quantity of biochar increase as the degree of heat rises. However, pyrolyzing biomass at an excessively extreme temperature may cause the carbon skeleton to split, leading to the opposite result.58,59 Various pyrolysis procedures will produce biochar with unique physicochemical features and varying application efficacy.60 In addition, Shi et al.61 prepared biochar with different pyrolysis temperatures, which manifested that the photocatalytic ability of biochar rose as pyrolysis temperature decreased. Therefore, an in-depth study of how heating temperature affects biochar's surface features and physicochemical characteristics is worthwhile for the further development of biochar. Overall, modulating heating rates and maintaining an exact response temperature could prove challenging in the pyrolysis process.27
The other efficient method for preparing biochar is hydrothermal carbonization (HTC). Typically, HTC is conducted at comparatively lower temperatures and more significant pressures for converting biomass to biochar.62 Xu et al.63 reported that N-doped carbons were generated by HTC at 200–260 °C using sewage sludge, rice husk, and cellulose as precursory biomass materials. Cai et al.64 employed crushed peanut shells as raw biomass materials by hydrothermal reaction in the existence of iron chloride and hexamethylenediamine (HDA) to produce magnetic HDA-modified biochar. Liu et al.65 added measured lotus powder to a nitrate solution (La(NO3)3·6H2O and Fe(NO3)3·6H2O were mixed with deionized water) and then carried out a hydrothermal reaction at 180 °C for 90 min. Lastly, C-doped LaFeO3/biochar was produced by calcining the sample. Moreover, because carbon content relates directly to ash quantity and pyrolysis temperature, biochar with the desired carbon and ash content can be produced by modulating the hydrothermal temperature.45 Compared with pyrolysis, HTC has a higher product yield (up to 88%) and lower energy consumption.66 HTC is needed for subsequent processes, such as filtration, centrifugation, and drying, to obtain the desired biochar.
Besides that, the combination of pyrolysis and the HTC process has been conventionally utilized to dope elements into biochar or form biochar-based composites. Talukdar et al.67 successfully synthesized Ag3PO4/Fe3O4 co-doped bamboo-derived activated biochar via two-step processes. Specifically, bamboo-derived activated biochar (BAB) was generated by pyrolysis at 500 °C, followed by a wet chemical process to produce an Ag3PO4/Fe3O4 co-doped BAB composite. Chen et al.68 first prepared micro–mesoporous carbon sheets (MMCSs) by pyrolyzing the luffa sponge in a tubular furnace, followed by KOH activation. Then, the obtained MMCSs were mixed with thiourea and dispersed into the distilled water to construct micro–mesoporous carbon sheets doped with nitrogen and sulfur via a hydrothermal reaction.
Varying raw materials, production conditions, and modification techniques can alter the surface features of biochar.49,69–71 The type of biomass material has the most significant impact on biochar's fixed carbon and ash contents. Biochar with a high ash content is unsuitable for capturing or eliminating contaminants due to its diminished adsorption sites and micropore surface areas.49,72 Acid modification can remove the ash and organic matter from biochar, resulting in porous structures and oxygen-containing functional groups.6,73–75 Biochar's specific surface area can be increased, and its aromaticity can be altered through alkali modification.76 Besides, while metal modification might create additional catalytic active sites, pristine adsorption sites may be occupied, or porous structures may be blocked.77 Thus, the design of the doping site and the loading ratio on biochar should be deeply considered. Overall, biochar's surface properties correlate with catalytic performance, so optimizing preparation strategies for biochar catalytic application is imperative.
2.2 Adsorption over pristine biochar
The remarkable characteristic of biochar is its adsorption capacity because of its porous nature, enormous specific surface area, and adequate functional groups.78 Applications in the adsorption and decomposition of contaminants necessitate a porous material with a high surface area. The specific surface area and porosity may affect the biochar's adsorption capacity and the location of catalytically active sites, thereby determining its performance.79 More opportunities for contaminants to connect with biochar surface functional groups and photocatalysts can be obtained in the biochar with a greater surface area and porosity, accelerating adsorption and decomposition rates. Composite photocatalysts are better at breaking down pollutants than single-phase materials because more pollutants stick to the surface of the composite, and more active species can be generated for degradation reactions.26 To obtain porous and functionalized biochar, Ma et al.80 mixed tobacco stem powder with K2CO3 and low-density polyethylene in a certain mass ratio, followed by pyrolyzing at 900 °C under Ar atmosphere. The produced biochar with an extensive specific surface area and porosity enhanced the potential for adsorption and promoted the separation of photogenerated carriers. In Wu et al.'s study,81 potassium hydroxide-modified algae-based biochar was successfully fabricated by calcining in the muffle furnace. Briefly, 6 g of prepared biochar was combined with various proportions of KOH. Subsequently, the mixture was calcined in a muffle furnace at 800 °C. The prepared composite material (PEBC) with a weight ratio of 0.5 between biochar and KOH can achieve a maximum adsorption ability of 744.32 mg g−1 for sulfamethoxazole, which is far superior to other adsorbents. The test results of PEBCs indicate that the introduction of KOH in the preparation process of macroalgal biochar can effectively modulate the pore structure of the material, increase specific surface area, expand pore volume, and optimize pore size distribution, ultimately obtaining more adsorption sites and promoting pore filling. It is worth noting that the K element in the raw material helps to generate reducing gases (CO and H2) during the calcination process, which not only accelerates the formation of the biochar's porous structure but also reduces high-valence metals to low-valence states.82
The adsorption mechanism of biochar on pollutants varies at different pyrolysis temperatures, including multilayer reaction, pore filling, mass transfer, π–π stacking interaction, and partition.83,84 At low temperatures, electrostatic interactions and hydrogen bonding are the main factors; at high temperatures, the pore filling and π–π stacking interaction dominates.31 Specifically, the oxygen-containing functional groups (hydroxyl, carboxyl, carbonyl, and ester groups) on the surface of biochar can rapidly adsorb pollutants and transfer them to photocatalysts through π–π stacking, electrostatic attraction, and hydrophobic interactions.85 For example, Yu et al.86 produced a ZnO/biochar composite photocatalyst that has strong electrostatic adsorption performance and can achieve a removal rate of 95.19% for MB.
3. Synthesis strategies for TiO2–biochar-based photocatalysts
TiO2 is commonly employed as a photocatalyst due to its various advantageous properties, such as effective oxidizing capability, extraordinary chemical stability, and low toxicity.49,87,88 Biochar can be used as a supporting material and possesses excellent electrical conductivity, which has great applicability potential in the realm of photocatalytic oxidation.11 Combining TiO2 with biochar is required to enhance the photocatalytic efficiency of semiconductors to remove organic contaminants. Synthesis strategies for TiO2–biochar-based materials have been widely investigated over the past few years. Generally, hydrothermal synthesis is a typical method to prepare TiO2 nanoparticles. Regarding biochar, as mentioned above, a popular production process is biomass pyrolysis in oxygen-scarce environments. Here, the preparation strategies of TiO2–biochar-based nanocomposites will be introduced by two sectors: in situ approaches and ex situ synthesis strategies. TiO2 growth and loading biochar onto TiO2 can be achieved simultaneously using in situ synthesis approaches. Typically, in situ approaches include solvothermal synthesis, sol–gel, chemical co-precipitation, and pyrolysis. An ex situ manufacturing approach attains the biochar combination by reworking the produced TiO2 and biochar. Ex situ strategies mainly include impregnation–calcination, microwave treatment, plasma treatment, hydrothermal process, and bio-chemical method. TiO2–biochar-based photocatalysts synthesized in recent years using these methods are summarized in Table 1.
Table 1 Summary of the preparation methods and their photocatalytic degradation activity of recently reported TiO2–biochar-based photocatalysts
Photocatalysts |
Method |
In/Ex situ |
Pollutants |
Maximum activity |
References |
PMBC@TiO2 |
Sol–gel |
In situ |
Sulfadiazine |
94.6% 150 min |
89 |
TiO2/pBC |
Sol–gel |
In situ |
Sulfamethoxazole |
91.27% 180 min |
75 |
TiO2/biochar |
Pyrolysis |
In situ |
Methyl orange |
96.88% 150 min |
90 |
Pyrolytic char/TiO2 |
Sol–gel |
In situ |
Phenol |
99% 300 min |
91 |
C–TiO2 |
Pyrolysis |
In situ |
Methylene blue |
59% 360 min |
92 |
Biochar–TiO2 |
Chemical co-precipitation |
In situ |
Methylene blue |
99.2% 240 min |
93 |
TiO2–MCDs |
Microwave treatment |
Ex situ |
Methylene blue |
83% 120 min |
94 |
Biochar–nano TiO2 |
Sol–gel |
In situ |
Toluene |
70.1% 300 min |
82 |
Ni-T/AC |
Sol–gel |
In situ |
Crystal violet |
99% 120 min |
95 |
C–TiO2 |
Microwave treatment |
Ex situ |
Tetracycline hydrochloride |
70% 120 min |
96 |
TiO2/Salvinia molesta |
Impregnation–calcination |
Ex situ |
Acid orange 7 dye |
90% 240 min |
97 |
TiO2/D500 |
Impregnation–calcination |
Ex situ |
Phenol |
77.7% 180 min |
11 |
TiO2@BC |
Impregnation–calcination |
Ex situ |
Phenanthrene |
63.68% 180 min |
6 |
C/TiO2 |
Plasma treatment |
Ex situ |
Formaldehyde |
73.7% 180 min |
98 |
N–TiO2/N–biochar |
Pyrolysis |
In situ |
Methyl orange |
97.6% 90 min |
99 |
Biochar–TiO2 |
Impregnation–calcination |
Ex situ |
Methyl orange |
97.1% 60 min |
100 |
Zn–TiO2/pBC |
Sol–gel |
In situ |
Sulfamethoxazole |
81.21% 180 min |
73 |
Ag-doped biochar/g-C3N4/TiO2 |
Solvothermal synthesis |
In situ |
TC-HCl |
90.4% 80 min |
26 |
TiO2/BC |
Sol–gel |
In situ |
Reactive Brilliant Blue KN-R |
99.71% 60 min |
101 |
TiO2/Fe–C |
Solvothermal synthesis |
In situ |
Acetaminophen |
100% 360 min |
102 |
Ag/C, N co-doped, Ov-TiO2/C |
Solvothermal synthesis |
In situ |
2,4-Dichlorophenol |
95% 150 min |
103 |
Biochar/TiO2 |
Sol–gel |
In situ |
Sulfamethoxazole |
91% 360 min |
104 |
Ag/TiO2/biochar |
Pyrolysis |
In situ |
Methyl orange |
97.48% 60 min |
105 |
N–TiO2–Fe3O4–biochar |
Pyrolysis |
In situ |
Methylene blue |
99.99% 300 min |
106 |
Biochar–TiO2 |
Impregnation–calcination |
Ex situ |
Diclofenac |
90% 120 min |
107 |
3.1 In situ synthesis
3.1.1 Solvothermal synthesis. The solvothermal method, analogous to hydrothermal, is widely applied to produce catalyst nanoparticles. The solvothermal reaction occurs by dissolving the poorly soluble or insoluble substances to generate crystals under relatively high temperatures and pressure in a closed system.18 More importantly, the solvothermal method can yield well-crystalline nanomaterials by moderately tuning preparation conditions (such as temperature and residence time).108 Biochar is introduced to TiO2 precursor to fabricate TiO2–biochar composites via the solvothermal method, an effective and typical in situ synthesis process. Using solvothermal, Wu et al.103 successfully generated flower-like C, N co-doped, Ov-TiO2/C composites. In detail, the prepared bagasse–urea complex was mixed into tetrabutyl titanate acetic acid solution, and then the mixed solution initiated a solvothermal reaction in an autoclave at 180 °C for 720 min. The final product was sintered at 450 °C in N2 atmosphere for 120 min. Fig. 1(a) and (b) is the SEM of the obtained samples. The characterization result showed that the flower-like TiO2 particles were successfully decorated on the surface of biochar. In Fig. 1(c), the XRD pattern indicated that as-prepared flower-like TiO2 particles show a classical anatase structure and a few weak peaks of the rutile phase. Therefore, the solvothermal method is efficient and convenient for preparing TiO2–biochar nanocomposites.
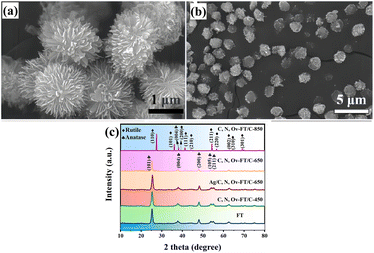 |
| Fig. 1 (a) SEM images of flower-like TiO2, (b) C, N, Ov-flower-like TiO2/C-650. (c) Typical XRD patterns of as-prepared all samples.103 | |
3.1.2 Sol–gel. Sol–gel refers to the method by which organic metal compounds or inorganic salts are solidified through solution, sol, gel, and heat-treated to become oxides or other solid compounds.9 For example, synthesizing of TiO2–biochar nanocomposites, the biochar and titanate are stirred evenly in a specific solvent. Then, the pH of the solution is adjusted by nitric acid, and finally, the anti-solvent is added to form a sol. At the same time, the sample can be heated to accelerate the gelation process.109 Fig. 2 is the flow chart of Guo et al.82 preparing biochar–nano TiO2 cross-linked structure by sol–gel method. He first added rice husk biochar to anhydrous ethanol containing tetrabutyl titanate and diluted nitric acid, then calcined the dried sample at 400 °C under N2 protection. The heat treatment process can remove the organic compounds and accelerate the crystallization of sol–gel oxides.110 The specific surface area of biochar–nano TiO2 is 779.87 m2 g−1, which is 6.5 times that of pure TiO2. This also directly proves that the composite of biochar and TiO2 can effectively increase the specific surface area of the sample and further enhance the adsorption performance of the material for pollutants in the photocatalytic process.
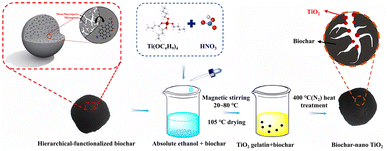 |
| Fig. 2 Preparation process of biochar–nano TiO2.82 | |
3.1.3 Chemical co-precipitation. Chemical co-precipitation is an essential and straightforward strategy for synthesizing metal oxide catalysts, which is performed by combining anions and cations in a solution and producing insoluble solid precipitation.9 Fazal et al.93 synthesized biochar–TiO2 composites using a wet precipitation approach. In brief, already prepared biochar (produced from macroalgae by pyrolysis) was dispersed in isopropanol, followed by the dropwise addition of titanium(IV) isopropoxide. The product was then elevated to 80 °C to exhaust the solvent. The sample was then placed in a muffle furnace heated to 400 °C with airflow for 300 min. The SEM images exhibited that the spherical TiO2 nanoparticles were evenly modified onto the biochar surface. Also, Herath et al.111 successfully decorated Fe2TiO5 nanoparticles on biochar (BC) using a chemical co-precipitation method and a heat treatment process. The XRD examination of Fe2TiO5 and Fe2TiO5/BC corroborated the successful deposition of Fe2TiO5 on the biochar surface.
3.1.4 Pyrolysis. Mian et al.106 fabricated N-doping TiO2–Fe3O4–biochar composites through one-step pyrolysis of FeCl3–Ti(OBu)4 laden agar biomass, and the formation of N-doping was achieved via under NH3 atmosphere. TiO2 obtained by hydrolyzing tetrabutyl titanate is in situ grown onto biochar, followed by pyrolysis, a feasible synthetic path of TiO2–biochar composites. Luo et al.112 added tetrabutyl titanate into distilled water solution and introduced as-prepared biochar into the system. The solution was vigorously stirred to ensure that biochar was well distributed. Subsequently, the obtained dried TiO2/biochar intermediates were activated at 500 °C for 120 min to form TiO2/biochar composites.
3.2 Ex situ synthesis
3.2.1 Impregnation–calcination. Recently, Li et al.6 effectively utilized the soaking calcination to synthesize TiO2@BC ex situ, which differs from the in situ chemical co-precipitation method, where the already prepared TiO2 was directly used. In addition, it can be adopted that TiO2 and biochar are mixed by manual mechanical grinding, followed by calcining to prepare the composites. For instance, Lazarotto et al.107 pyrolyzed the mixture of spent coffee biomass and TiO2 via manual mechanical mixing to prepare biochar–TiO2 composites. In the procedure, the biomass was converted into TiO2-impregnated biochar. Therefore, employing the impregnation–calcination method to prepare TiO2–biochar-based photocatalysts is attractive owing to its easy operation, cost-effectiveness, and reduced refuse production.
3.2.2 Microwave treatment. Microwave treatment is an advanced technology for the ex situ synthesis of TiO2–biochar-based photocatalysts. Its prominent advantages are short heating treatment time and a safe operation process. The microalgae-based carbon dots (MCDs) were adorned on the outside of TiO2 nanoparticles by Vu Nu et al.94 via a straightforward microwave procedure. Due to the incorporation of MCDs, the photodegradation efficiency of the TiO2–MCDs composite was enhanced. In particular, as photosensitizers of electron acceptors, MCDs can acquire photogenerated electrons and boost the utilization of visible light. Notably, microwave power exerts a significant influence on the properties of synthesized composites.49 Oseghe and his coworker96 fabricated pine cone-derived C-doped TiO2 composites by microwave heating treatment at 600, 800, and 1000 W powers (labeled CT600, CT800, and CT1000, respectively). The studies showed that the BET surface area of composites decreased as microwave power increased. CT800 is better at breaking down tetracycline hydrochloride than other composites because it is more catalytic, has a lower rate of photogenerated carrier annihilation, and has more active species for the redox reaction.
3.2.3 Plasma treatment. Dielectric barrier discharge (DBD), a promising technique for preparing and modifying photocatalysts, has been shown to broaden the utilization of TiO2 in the non-UV region.113 Several reports have demonstrated that titanium undergoes a transformation of its crystalline and amorphous crystal structures after hydrogen plasma etching, which can promote the utilization of visible light, reduce the binding of photoinduced carriers, and facilitate elemental doping, thus having an extended application in environmental protection.114 Recently, Tan et al.98 successfully synthesized bamboo carbon/TiO2 composites by H2 plasma using the DBD method (Fig. 3). The results showed that the composite with a 5% bamboo carbon weight ratio has a more meso/microporous structure, narrower band gap width, and lower electron–hole complexation rate and exhibits a good removal effect on formaldehyde.
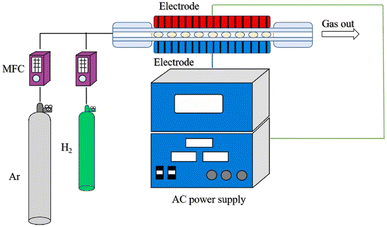 |
| Fig. 3 Sketch of the hydrogen dielectric barrier discharge modified system.98 | |
3.2.4 Other methods. Some new protocols for preparing TiO2–biochar-based photocatalysts, such as the hydrothermal process and bio-chemical method, have been developed for ex situ synthesis. Recently, Alomairy et al.32 adopted the bio-chemical method for synthesizing biochar-modified TiO2/CoFe2O4 core–shells. The primary process of integrating biochar with the TiO2/CoFe2O4 core–shell is ultrasonic irradiation, which is considered a feasible and effective tactic. Characteristic results displayed that biochar is conducive to reducing the agglomeration of TiO2/CoFe2O4 core–shell nanoparticles. Sánchez-Silva et al.115 prepared hydrochar–TiO2 composite (HC–TiO2) via a hydrothermal process using Byrsonima crassifolia stones (BCS) as biomass materials. Photodegradation experiments showed that HC–TiO2 can achieve 77% removal efficiency of crystal violet (20 mg L−1) within 90 min under UV light. Also, the reusability experiments indicated that the HC–TiO2 composite has excellent stability for 5 times cycles.
4. Advantages of TiO2–biochar-based materials in photocatalytic degradation
We summarized some of the latest TiO2–biochar-based photocatalysts and TiO2–non-biochar-based photocatalysts in Table 2. The results indicated that TiO2–biochar-based photocatalysts generally exhibited superior photocatalytic performances and larger specific surface areas than TiO2–non-biochar-based photocatalysts. In detail, the advantages of TiO2–biochar-based materials in photocatalytic degradation can be embodied in five aspects as follows:
Table 2 Comparisons of the photocatalytic properties of TiO2–biochar-based photocatalysts and TiO2–non-biochar-based photocatalysts
Photocatalysts |
Biochar-based/non-biochar based |
Light source |
Pollutants |
Dosage (mg) |
Efficiency |
SBET (m2 g−1) |
Ma (mg g−1) |
References |
M (mg g−1) is denoted as the pollutant mass removed by per unit mass of photocatalyst. |
Au/TiO2/BCP |
Biochar-based |
400 W mercury lamp |
Tetracycline |
8 |
98.4% (180 min) |
1291.1 |
492 |
34 |
40 mg L−1 (100 mL) |
AC/TiO2 |
Biochar-based |
UV light |
17α-Ethinylestradiol |
5 |
96.23% (120 min) |
34.28 |
11.5 |
125 |
6 mg L−1 (10 mL) |
TiO2/BC |
Biochar-based |
30 W UV lamp |
Bisphenol A |
100 |
97.6% (60 min) |
821 |
48.8 |
126 |
50 mg L−1 (100 mL) |
BC/A/R-TiO2 |
Biochar-based |
300 W xenon lamp |
Tetracycline |
100 |
99.5% (120 min) |
315.8 |
124.4 |
127 |
50 mg L−1 (250 mL) |
TiO2/CNTs |
Non-biochar-based |
1000 W xenon lamp |
Methylene blue |
200 |
86.95% (180 min) |
— |
13 |
128 |
30 mg L−1 (100 mL) |
TiO2-graphene |
Non-biochar-based |
250 W mercury lamp |
Phenol |
300 |
89.56% (240 min) |
62.728 |
8.9 |
129 |
10 mg L−1 (300 mL) |
N-doped TiO2/SiO2 |
Non-biochar-based |
16 W LED light |
Methylene blue |
100 |
72% (720 min) |
115.4 |
— |
130 |
1 × 10−5 M (100 mL) |
TiO2/MXene |
Non-biochar-based |
500 W mercury lamp |
Methylene blue |
10 |
96.44% (60 min) |
60.47 |
115.7 |
131 |
60 mg L−1 (20 mL) |
ZIF-67/F–TiO2 |
Non-biochar-based |
500 W xenon lamp |
Tetracycline |
30 |
87% (60 min) |
73.93 |
58 |
132 |
20 mg L−1 (100 mL) |
4.1 Abundant reserves
Biomass contains nearly all of the living things on the planet and the biological material produced, processed, and expelled by them.116 Its broad existence and plentiful stocks ensure the creation of TiO2–biochar composites. Therefore, biochar has a conspicuous advantage in feedstock costs compared to other carbon materials and serves an essential function green energy. Moreover, TiO2 nanomaterials that are cost-effective and have low toxicity can achieve a promising and long-term application in photocatalysis. Consequently, from the perspective of reserves, TiO2–biochar materials are recommended for cheap manufacturing and a green economy.
4.2 Large specific surface area
TiO2–biochar-based nanocomposites derived from biomass materials as carbon sources possess large specific surface areas because of biomass carbon's natural hierarchical porous microstructure.117 Specifically, macropores promote rapid fluid movement, whereas mesopores and micropores ensure complete interaction between contaminants and the photocatalyst surface. Also, biochar with a more porous structure makes TiO2–biochar-based photocatalysts better at capturing light by taking advantage of how light reflects and scatters in the pores. More importantly, the surface active centers and exposed atoms of the materials increase with specific surface areas. These active sites and unsaturated atoms help stabilize the catalytic process's intermediates and reduce the activation barrier.118 In our previous study,34 we reported a novel Au nanoparticles/TiO2 nanorods/biochar (Au/TiO2/BCP) photocatalyst with a massive specific surface area of 1291.10 m2 g−1. Photodegradation results demonstrated that Au/TiO2/BCP reached a removal efficiency of 98.4% for degradation tetracycline, and per unit mass can remove 492 mg tetracycline. Therefore, the pollutant degradation rate is considerably improved using TiO2–biochar-based photocatalysts.
4.3 Boosting the adsorption of pollutants
Since the photocatalytic oxidation process happens on the exterior of the photocatalyst, a superior surface-based adsorption performance is necessary for the efficient destruction of contaminants.119 Biochar has more surface functional groups (such as hydroxyl and carboxyl groups) than activated carbon, which is one of the most pivotal factors influencing adsorption efficacy.120 As a result, more pollutants in wastewater can be adsorbed and decomposed near the surface of photocatalysts, thereby achieving high photocatalytic efficiency, which is a crucial step in developing feasible applications of photocatalysts in wastewater treatment.
4.4 Strong interaction between biochar and TiO2
Owing to the strong interaction between carbon materials and metal Ti atoms, biochar and TiO2 can form a close contact structure. This improves the material's physical and chemical properties and the separation and migration of photoinduced charge, enhancing the lifetime of carriers and making them less likely to recombine.121 For instance, Zhai et al.122 manifested that TiO2/bio-char had higher abilities of adsorption and decomposition for methylene blue than the bio-char, for which this composite existed a benign interaction between TiO2 and bio-char and offered an enhanced electron transport efficiency.
4.5 Accelerating charge migration in the TiO2–biochar-based composites
In a TiO2–biochar composite photocatalysis system, biochar with appropriate conductivity can serve as an electron trap and a transit channel, promoting the separation and migration of photoinduced charge carrier pairs of TiO2 and boosting the redox reaction. Furthermore, more reactive oxygen species can be generated by TiO2–biochar composites, thereby enhancing the photocatalytic activity.123 Hsu et al.124 successfully deposited TiO2 on the carbon nanospheres to construct carbon@titania yolk–shell nanostructures. The XRD results (Fig. 4a) indicated that TiO2 hollow nanospheres prepared by sol–gel and calcination possess anatase structure. As shown in Fig. 4b, owing to the presence of carbon nanospheres, photoexcited electrons on the TiO2 can be transferred, effectively inhibiting the recombination of electron–hole pairs.
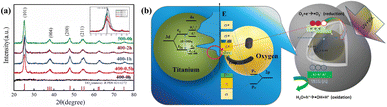 |
| Fig. 4 (a) X-ray diffraction patterns of nanospheres. (b) The mechanism of mobile electron transfer and hole increase under UV-vis illumination.124 | |
5. Strategies for improving photocatalytic performance of TiO2–biochar-based photocatalysts
5.1 In terms of biochar
The improved strategies for biochar can be concluded in two aspects. For one thing, the preparation temperature of biochar was found to have significant effects on its features and the performance of the TiO2–biochar photocatalyst. Xie et al.133 fabricated biochar utilizing three distinct pyrolysis temperatures (300–700 °C). The results demonstrated that the TiO2–biochar prepared at 500 °C displayed the most effective purification of manufactured rainwater, as the stable tubular structure of the biochar facilitated TiO2 nanoparticle attachment. For another, the surface modification of biochar is a vital point in achieving a uniform dispersion of nano-TiO2 photocatalysts. Acid oxidization can erode the biochar surface, introduce functional groups, and expose more adsorption sites conducive to controllable superficial growth.104,134 The TiO2 particles loaded on the surface of acid-treated biochar are smaller than those on untreated surfaces. This is because acid oxidation can effectively reduce the clumping of nanoparticles.82 Besides, biochar with a hierarchical porous structure can be achieved via activating an alkali, such as KOH.101,135 As a result, selecting suitable preparation conditions and functionalized treatment technology for biochar is an attractive tactic for enhancing its physical and chemical characteristics.
5.2 In terms of TiO2
The exposed facets of nanocrystals can easily affect chemical reactions on the external layers of photocatalysts during the photodegradation process. More importantly, different crystal facets present different surface atomic arrangements and crystallographic orientations, which determine the spatial charge separation between facets and reactive sites and diverse molecule absorption abilities.136,137 Qu et al.138 investigated the photocatalytic water splitting performance of anatase TiO2 with predominant {001} facets and {111} facets, showing that the {001} facets displayed higher activity. The substantial amount of surface undercoordinated Ti atoms and the surface atoms' strained configuration are advantageous for water adsorption and dissociation. Besides, as shown in Fig. 5, in situ photochemical probing reactions have corroborated that more nucleation sites exist on the {001} facets of anatase TiO2. In addition, utilizing the strong oxidation ability of TiO2 (001) facets, Li et al.139 successfully designed a MoS2/Au/TiO2 heterogeneous photocatalyst with highly-exposed (001) facets of TiO2. Notably, the photogenerated holes in this composite are primarily on the large TiO2 (001) facets. This means that more oxidation sites are exposed, which speeds up the photocatalytic removal process. Thus, to boost the photocatalytic capacity of TiO2–biochar-based photocatalysts, it is crucial to tune the exposed facets of TiO2 nanocrystals during the manufacture of TiO2–biochar-based composites.
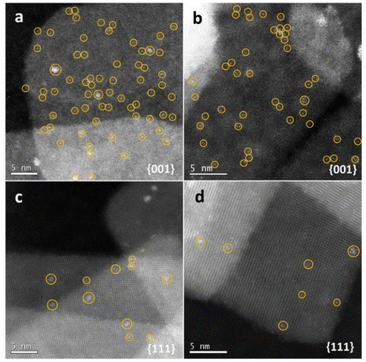 |
| Fig. 5 Photo-deposition of Pt on different facets after one minute of illumination. (a and b) HAADF images of Pt deposited on {001} facets. (c and d) HAADF images of Pt deposited on {111} facets.138 | |
On the other hand, controlling the configuration of TiO2 nanocrystals at the microscopic level cannot merely accelerate the movement of charges but also facilitate mass delivery, resulting in an enhanced photocatalytic performance for the disintegration of organic toxins.140 Herein, Song et al.141 synthesized TiO2 nanomaterials with three different morphologies (nanocones, nanorods, and nanoparticles) using a Na2EDTA-assisted hydrothermal technique (Fig. 6a), which were used as catalysts for the photoelectrocatalytic (PEC) removal of pollutants. The outcomes of the degradation experiment revealed that the nanocone-shaped TiO2 (99.3%) had superior PEC performance compared to the nanorod-shaped TiO2 (82.8%) and nanoparticle-shaped TiO2 (62.7%) (Fig. 6b). This makes it easier to complete the mass transfer between catalysts with a conical array structure. Notably, the nanocone structure possesses a potent built-in electric field that facilitates carrier separation and migration, a prerequisite for producing active oxides. In addition, Zhang et al.142 synthesized well-aligned sub-10 nm TiO2 nanowire arrays with adjustable corrugated structures by a distinctive mono micelle-directed assembly tactic (Fig. 7). Characterization results demonstrated that ultrathin corrugated TiO2 nanowire arrays could separate photocarriers, transfer charges, and activate surface holes all at the same time. The remarkable optoelectronic behaviors are predominately determined by the exceedingly large surface area and rapid charge separation capability of the as-prepared, unusual TiO2 arrangements. Consequently, it is desirable to finely manipulate the configuration of TiO2 nanocrystals to ameliorate the photocatalytic efficiency of TiO2–biochar-based photocatalysts.
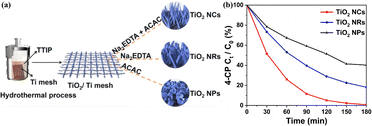 |
| Fig. 6 (a) Synthesis scheme of TiO2 catalysts with different structures by a Na2EDTA-assisted hydrothermal approach. (b) The percentage of 4-CP degradation.141 | |
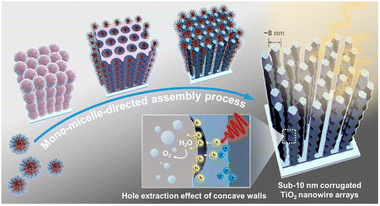 |
| Fig. 7 Schematic illustration of the formation process for the ultrathin corrugated TiO2 nanowire arrays synthesized via the monomicelle-directed assembly approach.142 | |
5.3 The synergistic effect of biochar and TiO2
Finding the optimal amount of carbonaceous material to add to TiO2 when making TiO2–biochar-based photocatalysts is important for biochar and TiO2 to work together and for the photocatalytic activity to improve. Xie et al.133 fabricated TiO2–biochar composites using three various TiO2–biochar mass proportion values by combining the necessary quantities of TiO2 and biochar. The research results indicated that the purification effect of the TiO2/biochar composite on artificial wastewater decreases with a decrease in mass ratio. This is because low mass ratio biochar blocks TiO2, weakens the transmission between light and TiO2, and loses photocatalytic efficiency.143 However, too high a quality ratio can backfire, and the advantages of biochar materials cannot be fully utilized. Lu et al.90 made several kinds of TiO2/biochar composite catalysts with varying biochar-to-Ti mass ratios. They designated it as CTx, where x (x = 0.1/1, 0.2/1, 0.5/1, 0.8/1, 1/1) indicated the biochar-to-Ti mass ratios. In the photocatalytic oxidation experiments of methyl orange, CT0.2/1 showed the best effect, with a decolorization rate of nearly 97% and a mineralization rate of nearly 83%. It indicates a synergistic effect between biochar and catalyst, and adding a proper amount of biochar can promote the photocatalytic process.
Besides that, TiO2–biochar nanocomposites with controllable porous microstructure and uniform morphology can be constructed via coupling with the template method, which contributes to the exposure of adequate activity sites for photocatalytic reactions. Wang et al.144 fabricated hierarchical porous titanium dioxide/carbon nanocomposites (TiO2/C) by introducing ice and nanoscaled silica as soft and hard templates for porosity modulating. The as-prepared TiO2/C nanocomposites exhibited more effective photocatalytic activity compared to their counterparts lacking templating, which can be assigned to the instructed porous structure and distinctive shape, which offer transfer avenues for electrolytes and photogenerated charge carriers, thereby enhancing the effectiveness of the degradation process.
6. Conclusions and future perspectives
In summary, TiO2, as an excellent photocatalyst, has been applied for almost half a century. To overcome the drawbacks of TiO2 and further broaden its application range, biochar, a novel carbonaceous material with fascinating physicochemical properties and environmental benignancy, is employed to couple with TiO2 in the field of photocatalysis. Mainly, TiO2–biochar-based composites have been extensively used to photodegrade organic contaminants in wastewater. Outstanding photocatalytic performance is required for TiO2–biochar-based composites to be extensively applied and developed quickly. The reasoned design and manufacturing of TiO2–biochar-based photocatalysts provide a potent means of enhancing the efficiency of light capture and photogenerated carrier separation. Through substantial research, multiple techniques and strategies have been adopted to prepare and modify TiO2–biochar-based photocatalysts. In this review, we introduced the characteristics of biochar and summarized the synthesis approaches (including in situ and ex situ means), advantages, and strategies for optimizing the performance of TiO2–biochar-based photocatalysts. However, TiO2–biochar-based photocatalysts still need to be adequately explored. Although the distinctive advantages of TiO2–biochar composites should be approved, the properties of TiO2–biochar composites should be adequately researched, and the shortcomings of TiO2–biochar-based photocatalysts in the application of photodegradation pollutants should be rationally realized. These preliminary investigations are essential for the advancement of photocatalysts based on TiO2–biochar. In the following aspects, several significant improvements in the research on TiO2–biochar-based photocatalysts can be accomplished.
First, as a dominating feature of biochar materials, the porous structure closely correlates with biochar's adsorption ability and photocatalytic performance. Meanwhile, the definite effect mechanisms have yet to be entirely explored. Thus, follow-up research concerning the mechanism of the porous structure of biochar remains to be done.
Second, regarding the combination of biochar and TiO2 nanoparticles, the different loading proportions of TiO2 on the surface and porous channels of biochar affecting photocatalytic activity have been extensively studied. Nonetheless, the specific interaction of TiO2 load proportions and the as-synthesized composites of physical and chemical properties needs to be more explicit. In the future, the quantitative structure–activity relationship (QSAR) of TiO2 load proportions and structural/optical features (e.g., BET, pore volume, pore type, and light absorption ability) of TiO2–biochar-based composites is desirable to investigate thoroughly, which has a significant effect on the understanding and reasonable design of high-performance TiO2–biochar-based photocatalysts.
Third, the computational calculation for the pathways of TiO2–biochar-based photocatalysts degradation pollutants is an effective means to investigate the decomposition process of pollutants. Unfortunately, limited by the fact that it is challenging to build the theoretical calculation model due to the complex structure of biochar, the theoretical calculation of photocatalytic degradation pollutants by TiO2–biochar-based photocatalysts has yet to be developed comprehensively. More efforts on the theoretical calculation of TiO2–biochar-based photocatalysts are necessary, including the adsorption mechanism between photocatalysts and pollutants, electrons transfer routes, and the minute decomposition pathway of contaminants.
Fourth, although we summarized many different methods for preparing TiO2–biochar-based photocatalysts in this review, large-scale manufacture still needs to be improved in real-world applications. Also, the high production costs always limit the industrialization process of TiO2–biochar-based photocatalysts. In order to decrease the costs of photocatalytic elimination of organic pollutants in water further using TiO2–biochar-based photocatalysts, some appropriate strategies should be extensively investigated.
Fifth, most studies of TiO2–biochar-based photocatalysts for the degradation of pollutants were implemented under UV light, although a favorable removal efficiency can be reached. Engineering strategies of TiO2–biochar-based photocatalysts should be explored to tune intrinsic physicochemical properties and to expand the response of visible light. Besides, developing multi-functional and highly active TiO2–biochar-based photocatalysts is needed to degrade the wastewater that consists of various persistent pollutants. Therefore, further investigation of TiO2–biochar-based photocatalysts can focus on adjusting properties and regeneration to adapt to practical applications.
It is worth exploring these aspects we discussed, for which TiO2–biochar-based materials have a promising future for photocatalytic degradation. Reasonable design and superior performance for TiO2–biochar-based photocatalysts can conspicuously boost the development of wastewater treatment and energy conversion. This review will present a comprehensive cognizance of TiO2–biochar-based photocatalysts. In the future, broader application fields of TiO2–biochar-based materials could be realized through more research, such as applying them in solar cells, adsorption, and supercapacitors.
Author contributions
YL: investigation, review, editing, writing—original draft; XD: review and editing; JL: review and editing; SC: investigation; JZ: review and editing; YM: investigation, writing, review, editing, validation, and supervision; all authors read and approved the final manuscript.
Conflicts of interest
There are no conflicts to declare.
Acknowledgements
Authors thank the Free Exploring Basic Research Project of Natural Science Foundation of Jilin Province (No. YDZJ202301ZYTS267), the Science and Technology Research Project of Jilin Province Education Department (No. JJKH20210032KJ, No. JJKH20230055KJ and No. JJKH20230056KJ), and Youth Science and Technology Innovation Team of Beihua University (No. BHQNTD202206) for the financial support of this work.
References
- G. D. Değermenci, N. Değermenci, V. Ayvaoğlu, E. Durmaz, D. Çakır and E. Akan, J. Cleaner Prod., 2019, 225, 1220–1229 CrossRef
. - J. Bai, R. Wang, Y. Li, Y. Tang, Q. Zeng, L. Xia, X. Li, J. Li, C. Li and B. Zhou, J. Hazard. Mater., 2016, 311, 51–62 CrossRef CAS PubMed
. - G. Rangarajan, A. Jayaseelan and R. Farnood, J. Cleaner Prod., 2022, 346, 131155 CrossRef CAS
. - M. Qiu, L. Liu, Q. Ling, Y. Cai, S. Yu, S. Wang, D. Fu, B. Hu and X. Wang, Biochar, 2022, 4, 19 CrossRef CAS
. - C. N. C. Hitam and A. A. Jalil, J. Environ. Manage., 2020, 258, 110050 CrossRef CAS
. - J. J. Liu, S. N. Sun, J. Liu, Y. Kuang, J. W. Shi, L. Z. Dong, N. Li, J. N. Lu, J. M. Lin, S. L. Li and Y. Q. Lan, J. Am. Chem. Soc., 2023, 145, 6112–6122 CrossRef CAS PubMed
. - Q. Aemig, A. Helias and D. Patureau, Water Res., 2021, 188, 116524 CrossRef CAS PubMed
. - S. Wang and J. Wang, Chem. Eng. J., 2019, 356, 350–358 CrossRef CAS
. - R. B. Rajput, S. N. Jamble and R. B. Kale, J. Environ. Manage., 2022, 307, 114533 CrossRef CAS
. - Z. Guo, D. Kodikara, L. S. Albi, Y. Hatano, G. Chen, C. Yoshimura and J. Wang, Water Res., 2023, 231, 118236 CrossRef CAS PubMed
. - N. Hou, X. Li, X. Jiang, N. Zhang, R. Wang and D. Li, Sci. Total Environ., 2022, 844, 157145 CrossRef CAS
. - A. Fujishima and K. Honda, Nature, 1972, 238, 37–38 CrossRef CAS
. - F. Li, T. Huang, F. Sun, L. Chen, P. Li, F. Shao, X. Yang and W. Liu, Appl. Catal., B, 2022, 317, 121725 CrossRef CAS
. - M. Chen, Z. Ye, L. Wei, J. Yuan and L. Xiao, J. Am. Chem. Soc., 2022, 144, 12842–12849 CrossRef CAS PubMed
. - Y. Ma, X. Xu, T. Yang, Y. Shen, F. Jiang, Y. Zhang, X. Lv, Y. Liu, B. Feng, G. Che and L. Wang, J. Alloys Compd., 2024, 970, 172663 CrossRef CAS
. - S. Lotfi, K. Fischer, A. Schulze and A. I. Schafer, Nat. Nanotechnol., 2022, 17, 417–423 CrossRef CAS PubMed
. - S. Livraghi, M. C. Paganini, E. Giamello, A. Selloni, C. D. Valentin and G. Pacchioni, J. Am. Chem. Soc., 2006, 128, 15666–15671 CrossRef CAS PubMed
. - X. Liu, C. Wan, X. Li, S. Wei, L. Zhang, W. Tian, K.-T. Yong, Y. Wu and J. Li, Front. Environ. Sci. Eng., 2020, 15, 54 CrossRef
. - S. Dekkouche, S. Morales-Torres, A. R. Ribeiro, J. L. Faria, C. Fontàs, O. Kebiche-Senhadji and A. M. T. Silva, Chem. Eng. J., 2022, 427, 131476 CrossRef CAS
. - H. Wang, X. Li, Y. Jiang, M. Li, Q. Xiao, T. Zhao, S. Yang, C. Qi, P. Qiu, J. Yang, Z. Jiang and W. Luo, Angew Chem. Int. Ed. Engl., 2022, 61, e202200465 CrossRef CAS PubMed
. - Y. Sun, G. Li, Y. Gong, Z. Sun, H. Yao and X. Zhou, J. Hazard. Mater., 2021, 403, 124019 CrossRef CAS PubMed
. - C. Sushma and S. G. Kumar, Inorg. Chem. Front., 2017, 4, 1250–1267 RSC
. - M. M. Kandy, Sustainable Energy Fuels, 2020, 4, 469–484 RSC
. - A. Kongkanand and P. V. Kamat, ACS Nano, 2007, 1, 13–21 CrossRef CAS PubMed
. - S. Yu, H. J. Yun, Y. H. Kim and J. Yi, Appl. Catal., B, 2014, 144, 893–899 CrossRef CAS
. - J. Kuan, H. Zhang, H. Gu, Y. Zhang, H. Wu and N. Mao, Nanotechnology, 2022, 33, 345402 CrossRef
. - S. Ahmad, L. Liu, S. Zhang and J. Tang, J. Hazard. Mater., 2023, 446, 130727 CrossRef CAS
. - R. Shan, J. Han, J. Gu, H. Yuan, B. Luo and Y. Chen, Resour., Conserv. Recycl., 2020, 162, 105036 CrossRef
. - Y. Luo, Y. Wang, F. Hua, M. Xue, X. Xie, Y. Xie, S. Yu, L. Zhang, Z. Yin, C. Xie and Z. Hong, J. Hazard. Mater., 2023, 443, 130300 CrossRef CAS
. - L. Shi, L. Liang, J. Ma, Y. Meng, S. Zhong, F. Wang and J. Sun, Ceram. Int., 2014, 40, 3495–3502 CrossRef CAS
. - T. Jiang, B. Wang, B. Gao, N. Cheng, Q. Feng, M. Chen and S. Wang, J. Hazard. Mater., 2023, 442, 130075 CrossRef CAS PubMed
. - S. Alomairy, L. Gnanasekaran, S. Rajendran and W. F. Alsanie, Environ. Res., 2023, 238, 117169 CrossRef CAS
. - J. Wang, G. Wang, T. Yu, N. Ding, M. Wang and Y. Chen, RSC Adv., 2023, 13, 24237–24249 RSC
. - Y. Liu, L. Wang, X. Dai, J. Zhang, J. Li, Y. Ma, Q. Han and Y. Dong, J. Alloys Compd., 2024, 976, 172985 CrossRef CAS
. - M. Z. Afzal, P. Zu, C. M. Zhang, J. Guan, C. Song, X. F. Sun and S. G. Wang, J. Hazard. Mater., 2022, 434, 128879 CrossRef CAS
. - V. Gadore, S. R. Mishra and M. Ahmaruzzaman, J. Environ. Manage., 2023, 334, 117496 CrossRef CAS PubMed
. - Y. Xie, R. Xiong, J. Li, W. Li, X. Yang and H. Tong, J. Environ. Manage., 2023, 333, 117428 CrossRef CAS
. - C. Zhang, H. Li, X. Yang, X. Tan, C. Wan and X. Liu, J. Environ. Manage., 2022, 324, 116445 CrossRef CAS PubMed
. - G. Cheng, F. Xu, J. Xiong, F. Tian, J. Ding, F. J. Stadler and R. Chen, Adv. Powder Technol., 2016, 27, 1949–1962 CrossRef CAS
. - Z. Mengting, T. A. Kurniawan, R. Avtar, M. H. D. Othman, T. Ouyang, H. Yujia, Z. Xueting, T. Setiadi and I. Iswanto, J. Hazard. Mater., 2021, 405, 123999 CrossRef CAS PubMed
. - C. Nzediegwu, M. Arshad, A. Ulah, M. A. Naeth and S. X. Chang, Bioresour. Technol., 2021, 320, 124282 CrossRef CAS PubMed
. - J. Fito, K. K. Kefeni and T. T. I. Nkambule, Sci. Total Environ., 2022, 829, 154648 CrossRef CAS PubMed
. - S. Sutar, S. Otari and J. Jadhav, Chemosphere, 2022, 287, 132200 CrossRef CAS PubMed
. - S.-H. Kong, S.-K. Loh, R. T. Bachmann, S. A. Rahim and J. Salimon, Renewable Sustainable Energy Rev., 2014, 39, 729–739 CrossRef CAS
. - B. Yang, J. Dai, Y. Zhao, J. Wu, C. Ji and Y. Zhang, Biochar, 2022, 4, 51 CrossRef CAS
. - J. Liu, H. Jia, M. Mei, T. Wang, S. Chen and J. Li, Process Saf. Environ. Prot., 2022, 167, 77–88 CrossRef CAS
. - S. Ahmad, X. Zhu, X. Wei and S. Zhang, J. Environ. Manage., 2021, 283, 111981 CrossRef CAS
. - P. Lisowski, J. C. Colmenares, O. Mašek, D. Łomot, O. Chernyayeva and D. Lisovytskiy, J. Anal. Appl. Pyrolysis, 2018, 131, 35–41 CrossRef CAS
. - C. Liu, D. Hao, J. Ye, S. Ye, F. Zhou, H. Xie, G. Qin, J. Xu, J. Liu, S. Li and C. Sun, Adv. Energy Mater., 2023, 13, 2204126 CrossRef CAS
. - S. Praveen, J. Jegan, T. Bhagavathi Pushpa, R. Gokulan and L. Bulgariu, Biochar, 2022, 4, 10 CrossRef CAS
. - X. Zhang, Y. Wu, A. S. Giwa, J. Xiong, S. Huang and L. Niu, Chemosphere, 2022, 297, 134152 CrossRef CAS PubMed
. - C. Zhang, W. Xiong, Y. Li, L. Lin, X. Zhou and X. Xiong, J. Hazard. Mater., 2023, 442, 130013 CrossRef CAS PubMed
. - J. Luo, Y. Wu, M. Jiang, A. Zhang, X. Chen, Y. Zeng, Y. Wang, Y. Zhao and G. Wang, Chemosphere, 2023, 311, 137041 CrossRef CAS PubMed
. - T. Wang, S. Liu, W. Mao, Y. Bai, K. Chiang, K. Shah and J. Paz-Ferreiro, J. Hazard. Mater., 2020, 389, 121827 CrossRef CAS
. - L. Kong, Y. Gao, Q. Zhou, X. Zhao and Z. Sun, J. Hazard. Mater., 2018, 343, 276–284 CrossRef CAS PubMed
. - Z. Zhao, T. Nie and W. Zhou, Environ. Pollut., 2019, 254, 113015 CrossRef CAS PubMed
. - J. Shi, J. Wang, L. Liang, Z. Xu, Y. Chen, S. Chen, M. Xu, X. Wang and S. Wang, J. Hazard. Mater., 2021, 401, 123382 CrossRef CAS PubMed
. - J. Du, L. Zhang, T. Liu, R. Xiao, R. Li, D. Guo, L. Qiu, X. Yang and Z. Zhang, Bioresour. Technol., 2019, 274, 73–82 CrossRef CAS PubMed
. - F. U. Haider, X. Wang, U. Zulfiqar, M. Farooq, S. Hussain, T. Mehmood, M. Naveed, Y. Li, C. Liqun, Q. Saeed, I. Ahmad and A. Mustafa, Ecotoxicol. Environ. Saf., 2022, 248, 114322 CrossRef CAS PubMed
. - A. El-Naggar, A. H. El-Naggar, S. M. Shaheen, B. Sarkar, S. X. Chang, D. C. W. Tsang, J. Rinklebe and Y. S. Ok, J. Environ. Manage., 2019, 241, 458–467 CrossRef CAS PubMed
. - H. Shi, M. Wang, B. Wang, Q. Huang and S. Gao, J. Hazard. Mater., 2020, 392, 122277 CrossRef CAS PubMed
. - S. Ahmad, X. Zhu, Q. Wang, X. Wei and S. Zhang, J. Anal. Appl. Pyrolysis, 2021, 160, 105330 CrossRef CAS
. - Z.-X. Xu, X.-Q. Deng, S. Zhang, Y.-F. Shen, Y.-Q. Shan, Z.-M. Zhang, R. Luque, P.-G. Duan and X. Hu, Green Chem., 2020, 22, 3885–3895 RSC
. - W. Cai, J. Wei, Z. Li, Y. Liu, J. Zhou and B. Han, Colloids Surf., A, 2019, 563, 102–111 CrossRef CAS
. - W. Liu, X. Li, X. Chu, S. Zuo, B. Gao, C. Yao, Z. Li and Y. Chen, Chemosphere, 2022, 294, 133763 CrossRef CAS PubMed
. - J. S. Cha, S. H. Park, S.-C. Jung, C. Ryu, J.-K. Jeon, M.-C. Shin and Y.-K. Park, J. Ind. Eng. Chem., 2016, 40, 1–15 CrossRef CAS
. - K. Talukdar, B. M. Jun, Y. Yoon, Y. Kim, A. Fayyaz and C. M. Park, J. Hazard. Mater., 2020, 398, 123025 CrossRef CAS PubMed
. - F. Chen, M. Zhang, L. Ma, J. Ren, P. Ma, B. Li, N. Wu, Z. Song and L. Huang, Sci. Total Environ., 2020, 730, 138930 CrossRef CAS PubMed
. - S. Li, S. Harris, A. Anandhi and G. Chen, J. Cleaner Prod., 2019, 215, 890–902 CrossRef CAS
. - C. Xia, Y. Liang, X. Li, H. A. Garalleh, M. Garaleh, J. M. Hill and A. Pugazhendhi, Environ. Res., 2023, 218, 114947 CrossRef CAS
. - Y. Mei, J. Xu, Y. Zhang, B. Li, S. Fan and H. Xu, Bioresour. Technol., 2021, 325, 124732 CrossRef CAS PubMed
. - H. Lyu, Q. Zhang and B. Shen, Chemosphere, 2020, 240, 124842 CrossRef CAS PubMed
. - X. Xie, S. Li, H. Zhang, Z. Wang and H. Huang, Sci. Total Environ., 2019, 659, 529–539 CrossRef CAS PubMed
. - J. Wang and S. Wang, J. Cleaner Prod., 2019, 227, 1002–1022 CrossRef CAS
. - H. Zhang, Z. Wang, R. Li, J. Guo, Y. Li, J. Zhu and X. Xie, Chemosphere, 2017, 185, 351–360 CrossRef CAS PubMed
. - D. J. Faheem, S. H. Kim, M. A. Hassan, S. Irshad and J. Bao, Environ. Sci. Pollut. Res. Int., 2020, 27, 37286–37312 CrossRef
. - Q. Du, S. Zhang, J. Song, Y. Zhao and F. Yang, J. Hazard. Mater., 2020, 389, 122115 CrossRef CAS PubMed
. - Y. Lu, Y. Cai, S. Zhang, L. Zhuang, B. Hu, S. Wang, J. Chen and X. Wang, Biochar, 2022, 4, 45 CrossRef CAS
. - A. Kumar, G. Sharma, M. Naushad, A. H. Al-Muhtaseb, A. Kumar, I. Hira, T. Ahamad, A. A. Ghfar and F. J. Stadler, J. Environ. Manage., 2019, 231, 1164–1175 CrossRef CAS PubMed
. - Y. Ma, T. Zhang, P. Zhu, H. Cai, Y. Jin, K. Gao and J. Li, Sci. Total Environ., 2022, 821, 153453 CrossRef CAS PubMed
. - Y. Wu, H. Cheng, D. Pan, L. Zhang, W. Li, Y. Song, Y. Bian, X. Jiang and J. Han, J. Environ. Manage., 2021, 293, 112912 CrossRef CAS PubMed
. - D. Guo, D. Feng, Y. Zhang, Z. Zhang, J. Wu, Y. Zhao and S. Sun, Fuel Process. Technol., 2022, 229, 107200 CrossRef CAS
. - T. Zheng, S. Ouyang and Q. Zhou, Biochar, 2023, 5, 5 CrossRef CAS
. - X. Cai, J. Li, Y. Liu, Z. Yan, X. Tan, S. Liu, G. Zeng, Y. Gu, X. Hu and L. Jiang, J. Chem. Technol. Biotechnol., 2017, 93, 783–791 CrossRef
. - Q. Huang, S. Song, Z. Chen, B. Hu, J. Chen and X. Wang, Biochar, 2019, 1, 45–73 CrossRef
. - F. Yu, F. Tian, H. Zou, Z. Ye, C. Peng, J. Huang, Y. Zheng, Y. Zhang, Y. Yang, X. Wei and B. Gao, J. Hazard. Mater., 2021, 415, 125511 CrossRef CAS
. - A. Bayles, S. Tian, J. Zhou, L. Yuan, Y. Yuan, C. R. Jacobson, C. Farr, M. Zhang, D. F. Swearer, D. Solti, M. Lou, H. O. Everitt, P. Nordlander and N. J. Halas, ACS Nano, 2022, 16, 5839–5850 CrossRef CAS PubMed
. - J. Schneider, M. Matsuoka, M. Takeuchi, J. Zhang, Y. Horiuchi, M. Anpo and D. W. Bahnemann, Chem. Rev., 2014, 114, 9919–9986 CrossRef CAS
. - C. X. Yang, Q. Zhu, W. P. Dong, Y. Q. Fan and W. L. Wang, Langmuir, 2021, 37, 9253–9263 CrossRef CAS PubMed
. - L. Lu, R. Shan, Y. Shi, S. Wang and H. Yuan, Chemosphere, 2019, 222, 391–398 CrossRef CAS PubMed
. - V. Makrigianni, A. Giannakas, C. Daikopoulos, Y. Deligiannakis and I. Konstantinou, Appl. Catal., B, 2015, 174–175, 244–252 CrossRef CAS
. - T. Xia, Z. Ma, M. Ai, K. Qian, S. Zhu, M. Rong, P. Zhang, Y. Ye and W. Qin, Chemosphere, 2021, 267, 128927 CrossRef CAS PubMed
. - T. Fazal, A. Razzaq, F. Javed, A. Hafeez, N. Rashid, U. S. Amjad, M. S. Ur Rehman, A. Faisal and F. Rehman, J. Hazard. Mater., 2020, 390, 121623 CrossRef CAS PubMed
. - T. T. Vu Nu, N. H. Thi Tran, P. L. Truong, B. T. Phan, M. T. Nguyen Dinh, V. P. Dinh, T. S. Phan, S. Go, M. Chang, K. T. Loan Trinh and V. Van Tran, Environ. Res., 2022, 206, 112631 CrossRef CAS PubMed
. - Z. Wu, Y. Xue, Z. Gao, Y. Li, L. Zhang, X. Yang, X. Liu and Z. Chen, Environ. Sci. Pollut. Res. Int., 2021, 28, 6491–6503 CrossRef CAS PubMed
. - E. O. Oseghe and A. E. Ofomaja, J. Environ. Manage., 2018, 223, 860–867 CrossRef CAS PubMed
. - S. Silvestri, M. G. Gonçalves, P. A. da Silva Veiga, T. T. d. S. Matos, P. Peralta-Zamora and A. S. Mangrich, J. Environ. Chem. Eng., 2019, 7, 102879 CrossRef CAS
. - Y. Tan, W. Zhao, L. Sun, R. Zhang, J. Hou, S. Fu, W. Xu and R. Zhang, J. Cleaner Prod., 2022, 369, 133280 CrossRef CAS
. - Z. Xiong, H. Chen, L. Lu, R. Shan, Y. Zhang, H. Yuan and Y. Chen, ACS Omega, 2023, 8, 791–803 CrossRef CAS PubMed
. - Y. Jiang and A. Liu, Environ. Sci. Pollut. Res. Int., 2023, 30, 31923–31934 CrossRef CAS PubMed
. - Y. Zhou, H. Zhang, L. Cai, J. Guo, Y. Wang, L. Ji and W. Song, Materials, 2018, 11, 1709 CrossRef PubMed
. - M. Penas-Garzon, A. Gomez-Aviles, J. Bedia, J. J. Rodriguez and C. Belver, Materials, 2019, 12, 378 CrossRef CAS PubMed
. - C. Wu, J. Zhang, B. Fang, Y. Cui, Z. Xing, Z. Li and W. Zhou, J. Cleaner Prod., 2021, 329, 129723 CrossRef CAS
. - J. R. Kim and E. Kan, J. Environ. Manage., 2016, 180, 94–101 CrossRef CAS PubMed
. - R. Shan, L. Lu, J. Gu, Y. Zhang, H. Yuan, Y. Chen and B. Luo, Mater. Sci. Semicond. Process., 2020, 114, 105088 CrossRef CAS
. - M. M. Mian, G. Liu, B. Yousaf, B. Fu, R. Ahmed, Q. Abbas, M. A. M. Munir and L. Ruijia, J. Environ. Sci., 2019, 78, 29–41 CrossRef CAS PubMed
. - J. S. Lazarotto, V. Lima Brombilla, S. Silvestri and E. L. Foletto, Appl. Organomet. Chem., 2020, 34, e6001 CrossRef CAS
. - C. Bie, H. Yu, B. Cheng, W. Ho, J. Fan and J. Yu, Adv. Mater., 2021, 33, e2003521 CrossRef PubMed
. - C. Wan, Y. Jiao and J. Li, Colloid Polym. Sci., 2016, 294, 1281–1287 CrossRef CAS
. - S. Wang, L. Ji, B. Wu, Q. Gong, Y. Zhu and J. Liang, Appl. Surf. Sci., 2008, 255, 3263–3266 CrossRef CAS
. - A. Herath, C. Navarathna, S. Warren, F. Perez, C. U. Pittman Jr and T. E. Mlsna, J. Colloid Interface Sci., 2022, 614, 603–616 CrossRef CAS PubMed
. - H. Luo, S. Yu, M. Zhong, Y. Han, B. Su and Z. Lei, J. Alloys Compd., 2022, 899, 163287 CrossRef CAS
. - Q. Chen, A. Ozkan, B. Chattopadhyay, K. Baert, C. Poleunis, A. Tromont, R. Snyders, A. Delcorte, H. Terryn, M. P. Delplancke-Ogletree, Y. H. Geerts and F. Reniers, Langmuir, 2019, 35, 7161–7168 CrossRef CAS PubMed
. - B. Li, Z. Zhao, Q. Zhou, B. Meng, X. Meng and J. Qiu, Chemistry, 2014, 20, 14763–14770 CrossRef CAS PubMed
. - J. M. Sánchez-Silva, A. Aguilar-Aguilar, G. J. Labrada-Delgado, E. G. Villabona-Leal, H. J. Ojeda-Galván, J. L. Sánchez-García, H. Collins-Martínez, M. V. López-Ramón and R. Ocampo-Pérez, Environ. Res., 2023, 231, 116280 CrossRef PubMed
. - A. D. Gupta, H. Singh, S. Varjani, M. K. Awasthi, B. S. Giri and A. Pandey, Sci. Total Environ., 2022, 849, 157831 CrossRef CAS PubMed
. - Y. Dong, W. Du, X. Gao and M. Guo, J. Cleaner Prod., 2022, 365, 132827 CrossRef CAS
. - Z. Sun, N. Talreja, H. Tao, J. Texter, M. Muhler, J. Strunk and J. Chen, Angew Chem. Int. Ed. Engl., 2018, 57, 7610–7627 CrossRef CAS PubMed
. - J. Chung, J. W. Chung and S. Y. Kwak, Phys. Chem. Chem. Phys., 2015, 17, 17279–17287 RSC
. - P. Lisowski, J. C. Colmenares, O. Mašek, W. Lisowski, D. Lisovytskiy, A. Kamińska and D. Łomot, ACS Sustainable Chem. Eng., 2017, 5, 6274–6287 CrossRef CAS
. - Z. Mou, Y. Wu, J. Sun, P. Yang, Y. Du and C. Lu, ACS Appl. Mater. Interfaces, 2014, 6, 13798–13806 CrossRef CAS PubMed
. - S. Zhai, M. Li, D. Wang, L. Zhang, Y. Yang and S. Fu, J. Cleaner Prod., 2019, 220, 460–474 CrossRef CAS
. - D. Kanakaraju and A. Chandrasekaran, Sci. Total Environ., 2023, 868, 161525 CrossRef CAS PubMed
. - C. H. Hsu, W. H. Huang, C. J. Lin, C. H. Huang, Y. C. Chen, K. Kumar, Y. G. Lin, C. L. Dong, M. K. Wu, B. J. Hwang, W. N. Su, S. Y. Chen and C. L. Chen, Small, 2023, 19, e2203881 CrossRef PubMed
. - J. Song, M. Shi, L. Xia, J. Dai, L. Luo, H. Wang, L. Shu and J. Fengzhi, Chemosphere, 2023, 333, 138930 CrossRef CAS PubMed
. - D. V. Thuan, T. T. H. Chu, H. D. T. Thanh, M. V. Le, H. L. Ngo, C. L. Le and H. P. Thi, Environ. Res., 2023, 236, 116789 CrossRef CAS PubMed
. - M. An, Z. Yang, B. Zhang, B. Xue, G. Xu, W. Chen and S. Wang, J. Environ. Chem. Eng., 2023, 11, 110367 CrossRef CAS
. - P. Akhter, F. Ali, A. Ali and M. Hussain, Diamond Relat. Mater., 2024, 141, 110702 CrossRef CAS
. - D. Heltina, D. I. Mastura, A. Amri, M. P. Sembiring and Komalasari, Mater. Today: Proc., 2023, 87, 293–298 CAS
. - S. Samangsri, T. Areerob and S. Chiarakorn, Res. Chem. Intermed., 2022, 49, 1649–1664 CrossRef
. - S. Zhang, M. Cai, J. Wu, Z. Wang, X. Lu, K. Li, J.-M. Lee and Y. Min, Catal. Commun., 2023, 174, 106594 CrossRef CAS
. - M. Zhang, J. Wang, X. Yuan, Y. Zhang, L. Wang, Y. Xie, Y. Xing and C. Hou, Appl. Surf. Sci., 2023, 637, 157881 CrossRef CAS
. - Y. Xie, A. Liu, E. R. Bandala and A. Goonetilleke, J. Water Process Eng., 2022, 48, 102913 CrossRef
. - J. Li, N. Liang, X. Jin, D. Zhou, H. Li, M. Wu and B. Pan, Chemosphere, 2017, 171, 66–73 CrossRef CAS PubMed
. - S. Luo, S. Li, S. Zhang, Z. Cheng, T. T. Nguyen and M. Guo, Sci. Total Environ., 2022, 806, 150662 CrossRef CAS PubMed
. - J. Yu, J. Low, W. Xiao, P. Zhou and M. Jaroniec, J. Am. Chem. Soc., 2014, 136, 8839–8842 CrossRef CAS PubMed
. - X. Yang, Z. Chen, W. Zhao, C. Liu, X. Qian, M. Zhang, G. Wei, E. Khan, Y. Hau Ng and Y. Sik Ok, Chem. Eng. J., 2021, 405, 126806 CrossRef CAS PubMed
. - J. Qu, Y. Wang, X. Mu, J. Hu, B. Zeng, Y. Lu, M. Sui, R. Li and C. Li, Adv. Mater., 2022, 34, e2203320 CrossRef PubMed
. - X. Li, S. Anwer, Q. Guan, D. H. Anjum, G. Palmisano and L. Zheng, Adv. Sci., 2022, 9, e2200346 CrossRef PubMed
. - A. Kumar, P. Choudhary, A. Kumar, P. H. C. Camargo and V. Krishnan, Small, 2022, 18, e2101638 CrossRef PubMed
. - R. Song, H. Chi, Q. Ma, D. Li, X. Wang, W. Gao, H. Wang, X. Wang, Z. Li and C. Li, J. Am. Chem. Soc., 2021, 143, 13664–13674 CrossRef CAS PubMed
. - P. Zhang, Z. Tian, Y. Kang, B. He, Z. Zhao, C. T. Hung, L. Duan, W. Chen, Y. Tang, J. Yu, L. Mai, Y. F. Li, W. Li and D. Zhao, J. Am. Chem. Soc., 2022, 144, 20964–20974 CrossRef CAS PubMed
. - G. Wang, W. Feng, X. Zeng, Z. Wang, C. Feng, D. T. McCarthy, A. Deletic and X. Zhang, Water Res., 2016, 94, 363–370 CrossRef CAS PubMed
. - H. Wang, M. Qu, S. Wang, X. Liu and L. Li, Adv. Sustainable Syst., 2019, 3, 1800169 CrossRef
.
|
This journal is © The Royal Society of Chemistry 2024 |