DOI:
10.1039/D4NA00475B
(Paper)
Nanoscale Adv., 2024,
6, 5398-5408
A Pd-containing ionic liquid modified magnetic graphene oxide nanocomposite (Fe3O4/GO–IL–Pd) as a powerful catalyst for the reduction of nitrobenzenes
Received
8th June 2024
, Accepted 18th August 2024
First published on 19th August 2024
Abstract
A novel palladium-containing ionic liquid-modified magnetic graphene oxide nanocomposite (Fe3O4/GO–IL–Pd) is synthesized and its catalytic performance is studied in the reduction of nitrobenzenes. The Fe3O4/GO–IL–Pd nanocomposite was characterized by using FT-IR, PXRD, SEM, EDS, VSM, and TG analyses. These analyses showed good magnetic properties and high stability of the designed composite. Different derivatives of nitrobenzenes were applied as substrates, giving corresponding anilines in high to excellent yields (89–96%) at short reaction times (10–15 minutes). Also, the stability, reproducibility, and reusability of the Fe3O4/GO–IL–Pd nanocomposite were investigated under applied conditions. A leaching experiment was also performed to study the nature of the Fe3O4/GO–IL–Pd catalyst under the conditions used.
1. Introduction
As a type of nitrogen-containing organic compound, aniline derivatives have several applications in chemical industries such as dyes, antioxidants, medicines, and agricultural chemicals.1–4 In addition, anilines are building blocks for the preparation of rubber products, textiles, electronic instruments, photography, coatings, pharmaceuticals, consumer goods, etc.5 An efficient method for the preparation of aniline derivatives is the reduction of nitrobenzenes by using molecular hydrogen,6 hydrazine hydrate,7 NaBH4,8 sodium hydrosulfite,9 and sodium formate.10 Considering the slow or impossible conversion of nitrobenzenes to aniline derivatives, the reduction of these compounds is performed in the presence of homogeneous metal catalysts.11,12 Due to the limitations of homogeneous catalysts such as non-recoverability, difficulty in separation of products, and high cost of their extraction and processing, researchers are looking for cheaper and more accessible catalysts or the maximum use of the catalytic capacity of these valuable metals. Stabilization of homogeneous catalysts on solid supports is considered one of the suitable methods to solve these limitations.13–15 Some recent reports about immobilization of metal catalysts on solid supports are Cu-MOF,16 Fe3O4@Fritillaria/Pd,17 Ni/carbon,18 and AuNP@PPh2–PIILP.19
Among different catalytic supports, carbon nanostructures are very attractive owing to their low price, high strength, and good stability.19–21 In addition, due to their high surface area, low weight, great flexibility, and outstanding electrical conductivity, carbon materials such as graphite, graphene oxide (GO), and fullerenes have many applications in medicine, agriculture, drug delivery, and chemistry.19,22,23 Among these, graphene oxide, obtained from the oxidation of graphene, has monolayered sp2 hybridization with unique chemical and physical properties. The carboxyl and hydroxyl functions of GO make it a suitable support for the stabilization of organic and inorganic compounds.24–31 For example, various chemicals such as UiO-66–(COOH)2,27 chitosan, graphite carbon nitride,32 and gelatin are well immobilized on GO.33 However, separation of GO is difficult due to the presence of amphoteric groups in its structure. Therefore, coating GO on magnetic nanoparticles (MNPs), to form magnetic-GO composites, solves this problem and improves its performance to expand catalytic applications.34,35 Some advantages of magnetic-GO nanocomposites are their easy synthesis, high surface area, and easy separation from the reaction medium.36,37 Different magnetic nanoparticles such as Co3O4, NiO2, Fe2O3, and Fe3O4 have been used to magnetize GO-containing composites. Among these, Fe3O4 is the best one due to its more stability, less toxicity, and high biodegradability and biocompatibility.38,39 According to the literature, various composites containing GO and magnetic nanoparticles such as GO/CoFe2O4,40 AMGO–Glu@Fe3O4,41 F3O4@GO/PS,42 a-Fe2O3–rGO,43 graphene/Fe3O4/NiO,44 and rGO/NiO,45 have been prepared.
On the other hand, imidazolium-based ionic liquids (ILs) have been proposed as excellent stabilizers for transition metal (TM) nanocatalysts to prevent their accumulation in catalytic transformations and increase their stability.46,47 Properties such as high thermal stability, adjustable hydrophobicity, low vapor pressure, and high conductivity make ILs an excellent stabilizer for TMs.48
According to the above, in this research work, a novel ionic liquid-modified magnetic graphene oxide nanocomposite supported palladium (Fe3O4/GO–IL–Pd) catalyst has been prepared and characterized and its catalytic application has been investigated in the reduction of nitrobenzenes. The novelty of this work includes the use of non-toxic and green compounds such as ionic liquids and graphene oxide in the designed nanocomposite. The ionic liquid acts as a green medium that prevents the aggregation and leaching of palladium during the reaction process. Furthermore, graphene oxide, with its high surface area, enhances the loading of catalytically active sites. Additionally, Fe3O4 imparts magnetic properties to the catalyst, allowing for easy separation and recovery using an external magnetic field. These features result in low toxicity, good biocompatibility, high catalytic activity, and high recoverability of the designed composite.
2. Experimental section
2.1. General
All chemicals including iron(II) chloride tetrahydrate (99%), iron(III) chloride hexahydrate (99%), tetramethoxysilane (TMOS, 99%), (3-aminopropyl)triethoxysilane (APTES, 98%), graphite powder, benzaldehydes (97–99%), palladium acetate (98%), DMSO, toluene and ethanol were purchased from Fluka, Merck and Sigma-Aldrich companies. Energy-dispersive X-ray spectroscopy (EDS) was performed using a SAMX (France) EDS instrument. The morphology of the particles was determined by using a SIGMA VP scanning electron microscope (FE-SEM) (Germany). Fourier transform infrared (FT-IR) spectroscopy was performed on a Bruker-Vector 22 spectrometer (Germany). Powder X-ray diffraction (PXRD) was performed using a Bruker D8 ADVANCE diffractometer (Germany). Thermal gravimetric analysis (TGA) was carried out using a Netzsch STA 409 PC/PG apparatus (Germany). The magnetic properties were measured by using a vibrating sample magnetometer (VSM) of Meghnatis Daghigh Kavir Company (Iran).
2.2. Preparation of Fe3O4@SiO2–NH/GO
At first, 0.5 g of graphene oxide was well dispersed in 20 mL of water for 20 minutes. Then, 1 g of Fe3O4@SiO249 was added to the reaction vessel. The obtained mixture was heated to 70 °C and 0.5 mL of (3-aminopropyl)triethoxysilane (APTES) was added drop by drop while stirring vigorously for 3 hours. The product was magnetically separated and after washing with ethanol, it was dried at 65 °C for 7 h and denoted as Fe3O4@SiO2–NH/GO.
2.3. Preparation of Fe3O4@SiO2–NH/GO–IL
For this, first, 1 g of Fe3O4@SiO2–NH/GO nanocomposite was well dispersed in 50 mL of toluene. Then, 0.5 mmol of 1-methyl-3-(3-trimethoxysilylpropyl)imidazolium chloride was added and the obtained mixture was refluxed for 24 hours in an oil bath. The resulting material was separated using an external magnet, washed with ethanol, dried at 65 °C for 6 h, and denoted as Fe3O4@SiO2–NH/GO–IL.
2.4. Preparation of Fe3O4@SiO2–NH/GO–IL–Pd
For this, 1 g of Fe3O4@SiO2–NH/GO–IL was completely dispersed in 30 mL of DMSO. After adding 1.5 mmol of Pd(OAc)2, the obtained combination was stirred at RT for 24 h. The resulting material was separated by using an external magnet, washed with ethanol and distilled water, dried at 65 °C for 6 h, and denoted as Fe3O4/GO–IL–Pd. According to the ICP analysis, the loading of palladium in/on the material framework was found to be 0.29 mmol Pd per one gram of Fe3O4/GO–IL–Pd.
2.5. Reduction of nitrobenzenes using Fe3O4/GO–IL–Pd
For this, 1 mmol of nitrobenzene derivative, 0.05 g of the Fe3O4/GO–IL–Pd catalyst (1.45 mol% pd), and 5 mL of water were well mixed at RT. After adding 2 mmol of NaBH4, the obtained combination was stirred at RT for the appropriate time indicated in Table 2. Upon the completion of the reaction, Fe3O4/GO–IL–Pd was separated by using an external magnet, and aniline derivatives resulted after the recrystallization of the crude mixture in EtOH.
3. Results and discussion
The preparation of the Fe3O4/GO–IL–Pd nanocomposite is shown in Scheme 1. First, graphene oxide was reacted with propylamine-modified Fe3O4@SiO2 (Fe3O4@SiO2–NH2) to deliver the Fe3O4@SiO2–NH2/GO nanocomposite. Then, the surface of Fe3O4@SiO2–NH2/GO was chemically modified with IL to give the Fe3O4@SiO2–NH2/GO–IL material. Finally, this material was treated with palladium acetate salt to deliver the Fe3O4/GO–IL–Pd nanocatalyst. The PXRD, FT-IR, SEM, EDS, EDS-mapping, and TG analyses were used to characterize this catalyst.
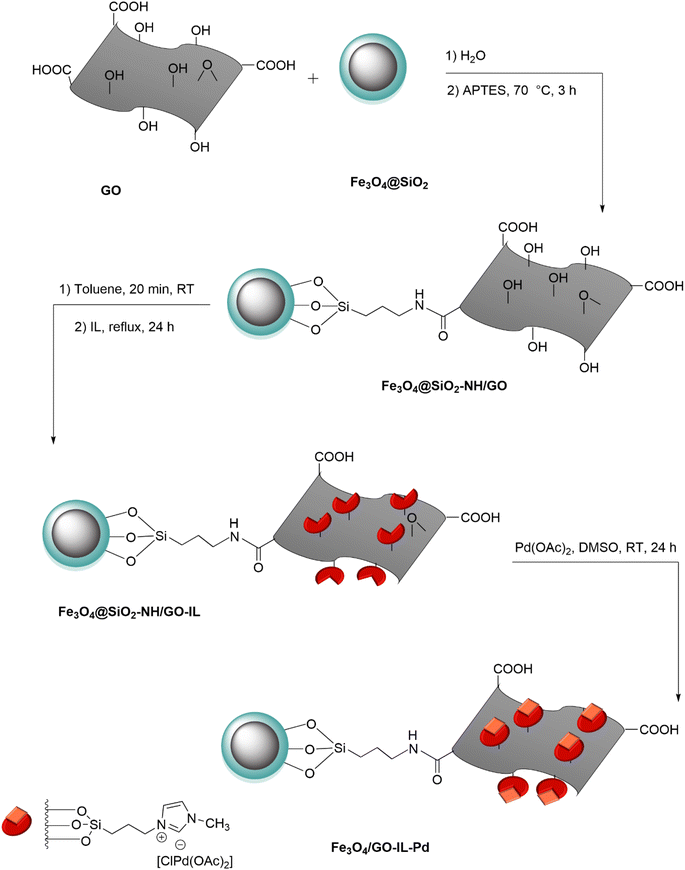 |
| Scheme 1 Preparation of Fe3O4/GO–IL–Pd. | |
The FT-IR analysis of GO and Fe3O4/GO–IL–Pd is shown in Fig. 1. For these samples, the strong peak at 3474 cm−1 is due to the O–H bonds of the material surface. For Fe3O4/GO–IL–Pd, the signals at 2835 and 2945 cm−1 are attributed to the C–H bonds of IL-propyl groups (Fig. 1b). Also, the peaks at 1750, 1625, and 1100 cm−1 are related to carboxyl C
O, aromatic C
C, and C–O bonds of GO, respectively (Fig. 1a and b).50 Moreover, the peaks at 110 and 550 cm−1 are corresponded to the Si–O–Si and Fe–O bonds of Fe3O4/GO–IL–Pd, respectively (Fig. 1b).51
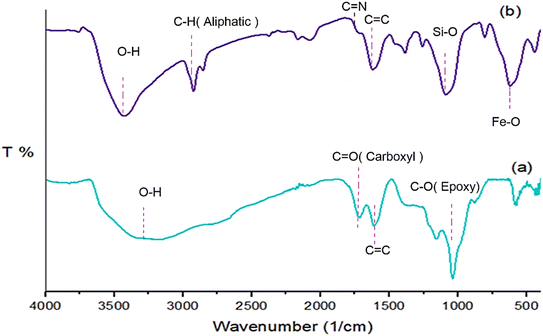 |
| Fig. 1 FT-IR of (a) GO and (b) Fe3O4/GO–IL–Pd. | |
The scanning electron microscopy (SEM) analysis was performed to study the morphology of the Fe3O4@SiO2 and Fe3O4/GO–IL–Pd materials (Fig. 2). As shown, the Fe3O4@SiO2 nanoparticles exhibit a predominantly spherical morphology (Fig. 2a). The SEM image of Fe3O4/GO–IL–Pd clearly showed that the Fe3O4@SiO2 NPs are uniformly dispersed across the layered and folded surface of the GO (Fig. 2b), indicating the successful stabilization of Fe3O4@SiO2 NPs to GO.
 |
| Fig. 2 SEM image of (a) Fe3O4@SiO2 and (b) Fe3O4/GO–IL–Pd. | |
EDS analysis of the Fe3O4/GO–IL–Pd nanocatalyst showed the existence of N, O, C, Si, Fe, and Pd signals (Fig. 3). This confirms the successful immobilization of the ionic liquid/Pd complex on Fe3O4/GO.
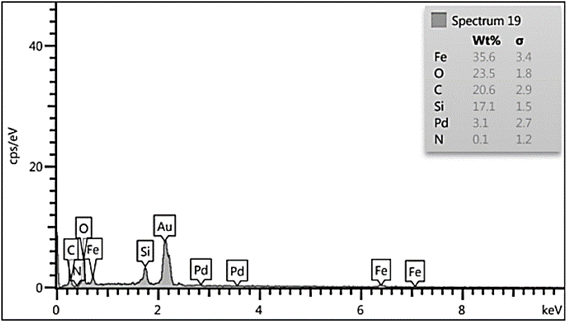 |
| Fig. 3 EDS analysis of Fe3O4/GO–IL–Pd. | |
The EDS mapping analysis also showed that all the above-mentioned elements are well distributed in the prepared nanocomposite (Fig. 4).
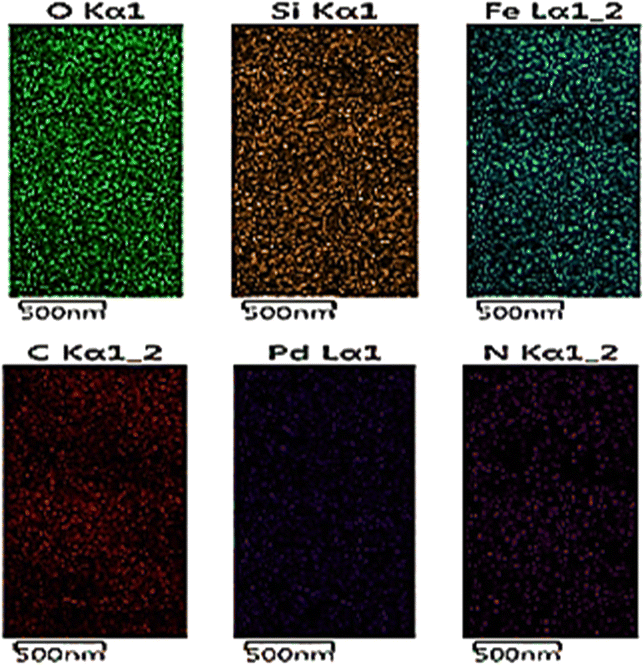 |
| Fig. 4 EDS mapping of Fe3O4/GO–IL–Pd. | |
The magnetic characteristics of the prepared nanocomposites were considered using VSM analysis. It was found that the saturation magnetization values of Fe3O4, Fe3O4@SiO2, and Fe3O4/GO–IL–Pd magnetic nanocomposites are, respectively, 66, 55, and 40 emu g−1. The reduction in magnetic properties after the modification process confirms the successful coating of silica and functionalized graphene oxide on the surface of the Fe3O4 nanoparticles (Fig. 5). This characteristic is very important, especially in the catalysis and adsorption processes.
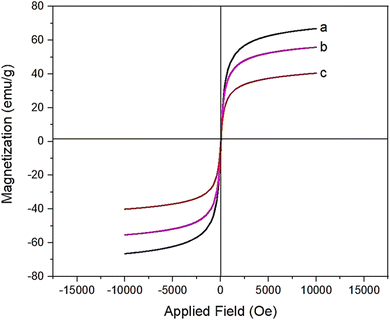 |
| Fig. 5 VSM diagrams of (a) Fe3O4, (b) Fe3O4@SiO2 and (c) Fe3O4/GO–IL–Pd. | |
The thermal stability of the designed Fe3O4/GO–IL–Pd nanocomposite was investigated by TG analysis (Fig. 6). The TGA results showed three weight losses at 10–150 °C, 151–230 °C and 235–560 °C. The first weight loss (10 to 150 °C) is related to the solvent removal from the surface of the nanocomposite. The second weight loss in the range of 151 to 230 °C is attributed to the elimination of the immobilized organic groups (ionic liquid and propyl amine) from the nanocomposite structure. The final weight loss at temperatures above 235 °C is assigned to the removal of remaining ionic liquids and also the decomposition of GO moieties.
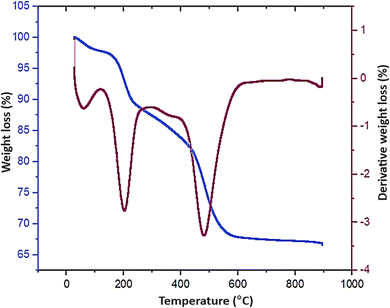 |
| Fig. 6 TGA of Fe3O4/GO–IL–Pd. | |
The crystalline structures of the Fe3O4, Fe3O4@SiO2–NH/GO, and Fe3O4/GO–IL–Pd nanomaterials were evaluated by powder XRD analysis (Fig. 7). As seen, the PXRD pattern of all materials demonstrates eight characteristic peaks at 2θ of 18.3°, 30.3°, 35.6°, 43.3°, 53.7°, 57.4°, 63°, and 74.3° corresponding, respectively, to the (111), (220), (311), (400), (422), (511), (440) and (533) planes. The pattern is completely matched with that of the Fe3O4 standard sample (JCPDS card, file no. 19-0629).52–54 This finding indicates that the Fe3O4 NPs have preserved their crystalline structure during the modification steps.55,56
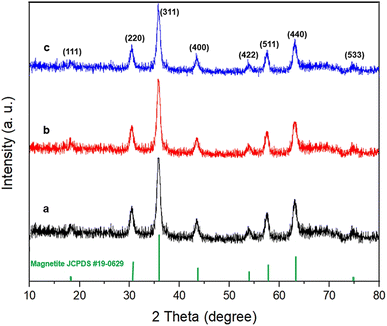 |
| Fig. 7 PXRD pattern of (a) Fe3O4, (b) Fe3O4@SiO2–NH/GO and (c) Fe3O4/GO–IL–Pd. | |
After characterization, the prepared Fe3O4/GO–IL–Pd nanocatalyst was used in the reduction of nitrobenzenes at RT. Optimal conditions were determined by examining the impact of the nanocatalyst and solvents (water, ethanol, and methanol) on the reduction of nitrobenzene in the presence of NaBH4 as a model reaction (Table 1). It was found that switching the solvent from ethanol and methanol to water improves catalytic efficiency and reaction yield (Table 1, entries 1–3). The study also demonstrated that in the presence of 0.05 g of Fe3O4/GO–IL–Pd nanocatalyst (1.45 mol% Pd), the best yield is obtained (Table 1, entries 3–5). Importantly, where the reaction was done using Pd-free Fe3O4/GO–IL, Fe3O4@SiO2–NH/GO, and Fe3O4@SiO2–NH2 nanocomposites (Table 1, entries 6–8), no product was obtained, confirming that the reaction is catalyzed by immobilized palladium species. Accordingly, the use of 0.05 g of Fe3O4/GO–IL–Pd, water solvent, and RT were selected as optimum conditions (Table 1, entry 4).
Table 1 Optimization of the reaction conditions in the reduction of nitrobenzene
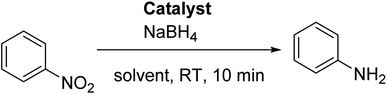
|
Entry |
Catalyst (g) |
Solvent |
TONa |
TOFb |
Yield (%) |
Turnover number [defined as yield (%)/cat. (mol%)].
Turnover frequency [defined as TON/reaction time (h)].
|
1 |
Fe3O4/GO–IL–Pd (0.03) |
EtOH |
59.8 |
373.75 |
52 |
2 |
Fe3O4/GO–IL–Pd (0.03) |
MeOH |
55.17 |
344.81 |
48 |
3 |
Fe3O4/GO–IL–Pd (0.03) |
Water |
80.45 |
281.25 |
70 |
4 |
Fe3O4/GO–IL–Pd (0.05) |
Water |
65.51 |
409.43 |
95 |
5 |
Fe3O4/GO–IL–Pd (0.08) |
Water |
40.94 |
255.87 |
95 |
6 |
Fe3O4/GO–IL (0.05) |
Water |
— |
— |
N. R. |
7 |
Fe3O4/GO (0.05) |
Water |
— |
— |
N. R. |
8 |
Fe3O4@SiO2–NH2 (0.05) |
Water |
— |
— |
N. R. |
After optimization of the conditions, different nitrobenzenes were used as substrates to check the activity of the catalyst. The results showed that all nitrobenzene derivatives containing both electron-donating and electron-withdrawing substituents deliver corresponding aniline products in a high yield. This finding confirms the high performance of the designed Fe3O4/GO–IL–Pd catalyst in the reduction of a wide range of nitrobenzenes (Table 2). It is important to note that where 3-nitrobenzaldehyde was used as a substrate, 2 mol% of catalyst and 3 mmol of NaBH4 were used. In this reaction, both nitro and aldehyde substituents were reduced, respectively, to corresponding amine and alcohol groups (Table 2, entry 5).
Table 2 Reduction of nitrobenzene derivatives in the presence of the Fe3O4/GO–IL–Pd nanocompositea
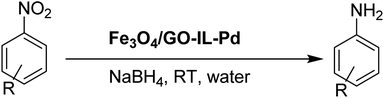
|
Entry |
R |
Time (min) |
Yield (%) |
TON |
TOF |
Mp (°C) found |
Mp (°C) reported |
Reaction conditions: nitrobenzene (1 mmol), NaBH4 (2 mmol), Fe3O4/GO–IL–Pd catalyst (0.05 g containing 1.45 mol% Pd), H2O (5 mL) and RT.
|
1 |
H |
10 |
95 |
65.51 |
409.43 |
181–183 |
182–184 [ref. 57] |
2 |
4-NH2 |
15 |
95 |
65.51 |
262.04 |
138–140 |
136–139 [ref. 58] |
3 |
2-OH |
10 |
89 |
61.37 |
383.56 |
171–173 |
170–75 [ref. 51] |
4 |
4-OH |
10 |
96 |
66.20 |
413.75 |
182–184 |
181–183 [ref. 58] |
5 |
3-CHO |
15 |
95 |
65.51 |
262.04 |
91–93 |
92–95 [ref. 59] |
Next, the recoverability and reusability of Fe3O4/GO–IL–Pd were tested in the model reaction. To do this, after the reaction was completed, the catalyst was separated by using a magnet, washed with ethanol, dried, recovered, and reused in the next run. These steps were repeated several times and it was found that the Fe3O4/GO–IL–Pd catalyst could be reused at least seven times while maintaining its performance (Fig. 8).
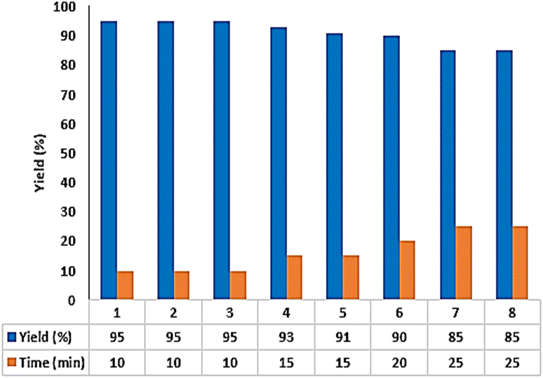 |
| Fig. 8 Recoverability and reusability of the Fe3O4/GO–IL–Pd catalyst. | |
A leaching experiment was also done to investigate the nature of Fe3O4/GO–IL–Pd under applied conditions. To do this, after 45% progress of the reaction, Fe3O4/GO–IL–Pd was separated using a magnet. Then, the reaction development of the residue was checked for 2 h, in which no significant yield was seen. The analysis of atomic absorption (AA) also showed no presence of palladium in the residue confirming high stability and no leaching of supported Pd species under applied conditions.
To investigate the chemical and structural stability of the catalyst under the applied conditions, PXRD, SEM, and EDS analyses were conducted on the recovered catalyst after seven recovery times. As illustrated in Fig. 9, the PXRD pattern of the recovered Fe3O4/GO–IL–Pd catalyst exhibited eight peaks at 2θ = 18.3°, 30.3°, 35.6°, 43.3°, 53.7°, 57.4°, 63°, and 74.3° which is in good agreement with the PXRD pattern of the fresh nanocatalyst. This analysis confirms the remarkable stability of the crystalline structure of magnetite NPs after multiple cycles of reuse and recovery.
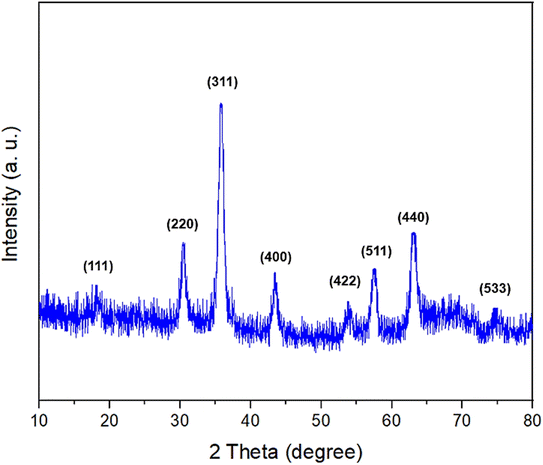 |
| Fig. 9 PXRD pattern of the recovered Fe3O4/GO–IL–Pd catalyst. | |
The SEM image of the recovered Fe3O4/GO–IL–Pd catalyst also revealed a morphology similar to that of the fresh catalyst, confirming the high structural stability of the designed material under the applied conditions (Fig. 10).
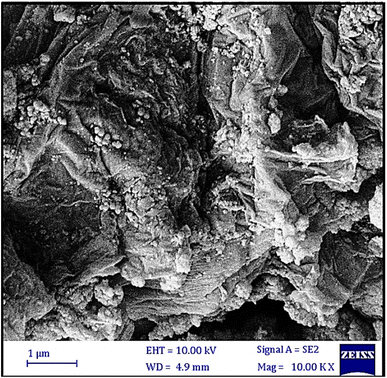 |
| Fig. 10 SEM image of the recovered Fe3O4/GO–IL–Pd catalyst. | |
As depicted in Fig. 11, the EDS pattern of the recovered catalyst exhibits no significant difference compared to the EDS of the fresh Fe3O4/GO–IL–Pd catalyst. These findings demonstrate the high stability of the catalyst following multiple cycles of recovery and reuse.
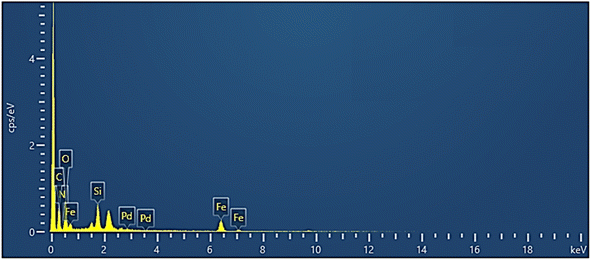 |
| Fig. 11 EDS spectrum of the recovered Fe3O4/GO–IL–Pd catalyst. | |
A plausible mechanism for the reduction of nitrobenzenes using the Fe3O4/GO–IL–Pd catalyst is presented in Scheme 2. In this mechanism, borohydride ions (BH4−) are dispersed and adsorbed onto the nanocomposite surface, facilitating electron transfer from NaBH4 to the nitroarene compound, mediated by palladium. The nucleophilic attack of negatively charged hydrogen at the Pd–H site on the electrophilic nitro functional group, followed by hydrogen transfer, leads to the formation of the reduced product.60
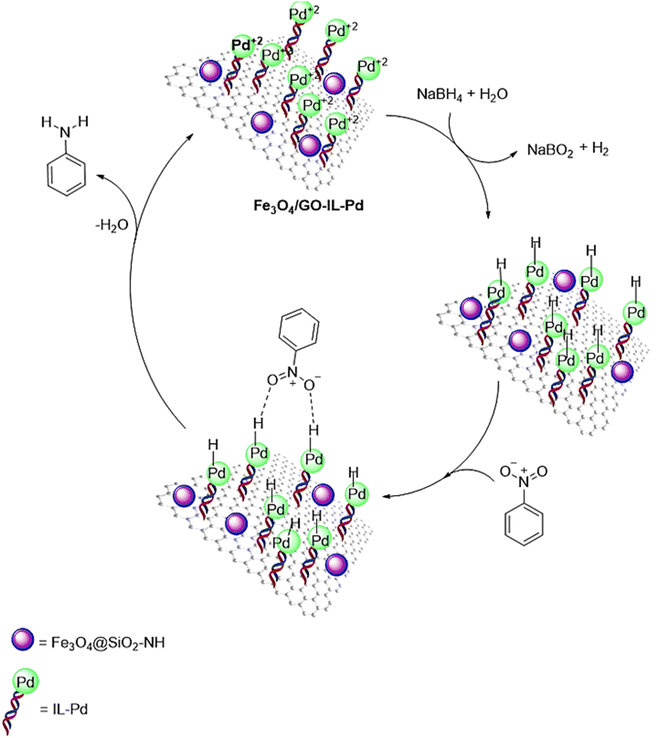 |
| Scheme 2 A plausible mechanism for the reduction of nitrobenzenes using Fe3O4/GO–IL–Pd. | |
Finally, the performance of the designed Fe3O4/GO–IL–Pd catalyst was compared with that of the reported catalysts in the model reaction (Table 3). As shown, the designed nanocomposite is relatively more efficient than the previous catalysts, especially in terms of recovery times and solvent usage. The higher performance of Fe3O4/GO–IL–Pd may be attributed to its magnetic nature, as well as the key role of immobilized ILs in protecting Pd species from leaching.
Table 3 Comparison of the catalytic performance of Fe3O4/GO–IL–Pd with that of previously reported catalysts in the reduction of nitrobenzene
Catalyst |
Conditions |
Yield (%) |
Recovery times |
Ref. |
NiNPs/DNA |
H2O, NaBH4, RT, 2 h, 2 mol% of catalyst |
99 |
4 |
61
|
CuO–GO |
H2O, NaBH4, RT, 30 min, 50 mg of catalyst |
98 |
5 |
62
|
Fe3O4@Cur/Mel-Ag |
NaBH4 (2.0 mmol)/0.04 g K2CO3/pH (8.0), 70 °C, 10 min, 0.02 g of catalyst |
98 |
4 |
63
|
GA–Pd/ZnO |
MeOH, H2 atmosphere, RT, 2 h, 10 mg of catalyst |
98 |
4 |
64
|
Fe3O4/GO–IL–Pd |
Water, NaBH4, RT, 10 min, 0.05 g of catalyst |
95 |
7 |
This work |
4. Conclusion
In this work, a magnetic nanocomposite containing Fe3O4@SiO2 and graphene oxide (GO) modified with an ionic liquid–Pd complex (Fe3O4/GO–IL–Pd) was prepared, characterized, and applied as a powerful catalyst for the reduction of nitrobenzenes. The SEM image showed a morphology containing layered graphene oxide and spherical iron oxide nanoparticles. The EDS analysis confirmed the good distribution of expected C, N, O, Si, Pd, and Fe elements in the designed nanocomposite. The good magnetic properties of the Fe3O4/GO–IL–Pd nanocomposite were confirmed by using VSM analysis. The TG analysis showed high thermal stability of the synthesized nanocomposite. The FT-IR analysis confirmed the successful synthesis of the expected functional groups in this nanocomposite.65 The PXRD pattern also confirmed that the crystallinity of Fe3O4 NPs is preserved after modification steps.66–68 The Fe3O4/GO–IL–Pd nanocomposite was successfully used as a catalyst in the reduction of nitrobenzenes giving corresponding anilines in high yield. The Fe3O4/GO–IL–Pd nanocatalyst was recovered and reused seven times with no significant decrease in its performance. The high durability and stability of the recovered catalyst were confirmed by using PXRD, SEM, and EDS analyses.
Data availability
The original contributions presented in the study are included in the article, further inquiries can be directed to the corresponding author.
Conflicts of interest
There are no conflicts to declare.
Acknowledgements
The authors thank Yasouj University and the Iran National Science Foundation (INSF) for supporting this work.
References
- L. Wang, P. Li, Z. Wu, J. Yan, M. Wang and Y. Ding, Synthesis, 2003, 2003, 2001–2004 CrossRef.
- S. Piña Jr, D. M. Cedillo, C. Tamez, N. Izquierdo, J. G. Parsons and J. J. Gutierrez, Tetrahedron Lett., 2014, 55, 5468–5470 CrossRef.
- N. Daems, J. Wouters, C. Van Goethem, K. Baert, C. Poleunis, A. Delcorte, A. Hubin, I. F. Vankelecom and P. P. Pescarmona, Appl. Catal., B, 2018, 226, 509–522 CrossRef CAS.
- F. Harraz, S. El-Hout, H. Killa and I. Ibrahim, J. Catal., 2012, 286, 184–192 CrossRef CAS.
- J. Wang, Z. Yuan, R. Nie, Z. Hou and X. Zheng, Ind. Eng. Chem. Res., 2010, 49, 4664–4669 CrossRef CAS.
- P. Lara and K. Philippot, Catal. Sci. Technol., 2014, 4, 2445–2465 RSC.
- A. Corma, C. González-Arellano, M. Iglesias and F. Sánchez, Appl. Catal., 2009, 356, 99–102 CrossRef CAS.
- S. Menuel, B. Léger, A. Addad, E. Monflier and F. Hapiot, Green Chem., 2016, 18, 5500–5509 RSC.
- C. T. Redemann and C. E. Redemann, Org. Synth., 2003, 29, 8 Search PubMed.
- K. Abiraj, G. R. Srinivasa and D. C. Gowda, Can. J. Chem., 2005, 83, 517–520 CrossRef CAS.
- J. Kielhorn, C. Melber, D. Keller and I. Mangelsdorf, Int. J. Hyg. Environ. Health, 2002, 205, 417–432 CrossRef CAS PubMed.
- L. L. Jewell and B. H. Davis, Appl. Catal., 2006, 310, 1–15 CrossRef CAS.
- X.-F. Wu, H. Neumann and M. Beller, Chem. Rev., 2013, 113, 1–35 CrossRef CAS PubMed.
- M. Khanmohammadi, S. Amani, A. B. Garmarudi and A. Niaei, Chin. J. Catal., 2016, 37, 325–339 CrossRef.
- J. C. Védrine, Chin. J. Catal., 2019, 40, 1627–1636 CrossRef.
- J. Tang, S. Zhang, X. Chen, L. Zhang, L. Du and Q. Zhao, Catalysts, 2023, 13, 956 CrossRef CAS.
- H. Veisi, B. Karmakar, T. Tamoradi, R. Tayebee, S. Sajjadifar, S. Lotfi, B. Maleki and S. Hemmati, Sci. Rep., 2021, 11, 4515 CrossRef CAS PubMed.
- X. Lu, J. He, R. Jing, P. Tao, R. Nie, D. Zhou and Q. Xia, Sci. Rep., 2017, 7, 2676 CrossRef PubMed.
- T. Windhorst and G. Blount, Mater. Des., 1997, 18, 11–15 CrossRef CAS.
- C. Hu, Y. Lin, J. W. Connell, H. M. C. heng, Y. Gogotsi, M. Titirici and L. Dai, Adv. Mater., 2019, 31(13), 1806128 CrossRef PubMed.
- F. Dénès, A. Pérez-Luna and F. Chemla, Chem. Rev., 2010, 110, 2366–2447 CrossRef PubMed.
- M. Azizi-Lalabadi, H. Hashemi, J. Feng and S. M. Jafari, Adv. Colloid Interface Sci., 2020, 284, 102250 CrossRef CAS PubMed.
- M. J. Sweetman, S. May, N. Mebberson, P. Pendleton, K. Vasilev, S. E. Plush and J. D. Hayball, C, 2017, 3, 18 Search PubMed.
- A. B. Seabra, A. J. Paula, R. de Lima, O. L. Alves and N. Durán, Chem. Res. Toxicol., 2014, 27, 159–168 Search PubMed.
- W. Yu, L. Sisi, Y. Haiyan and L. Jie, RSC Adv., 2020, 10, 15328–15345 RSC.
- D. C. Marcano, D. V. Kosynkin, J. M. Berlin, A. Sinitskii, Z. Sun, A. Slesarev, L. B. Alemany, W. Lu and J. M. Tour, ACS Nano, 2010, 4, 4806–4814 CrossRef CAS PubMed.
- C. Chung, Y.-K. Kim, D. Shin, S.-R. Ryoo, B. H. Hong and D.-H. Min, Acc. Chem. Res., 2013, 46, 2211–2224 CrossRef CAS PubMed.
- M. F. Lanjwani, M. Tuzen, M. Y. Khuhawar and T. A. Saleh, Inorg. Chem. Commun., 2024, 159, 111613 CrossRef CAS.
- R. Ullah and M. Tuzen, J. Mol. Struct., 2023, 1285, 135509 CrossRef CAS.
- J. Ali, S. Bibi, W. B. Jatoi, M. Tuzen, M. A. Jakhrani, X. Feng and T. A. Saleh, Mater. Today Commun., 2023, 106840 CrossRef CAS.
- Z. Ali, R. Ullah, M. Tuzen, S. Ullah, A. Rahim and T. A. Saleh, Trends Environ. Anal. Chem., 2023, 37, e00187 CrossRef CAS.
- M. Amiri, H. Salehniya and A. Habibi-Yangjeh, Ind. Eng. Chem. Res., 2016, 55, 8114–8122 CrossRef CAS.
- Z. Cheng, Y. Dai, X. Kang, C. Li, S. Huang, H. Lian, Z. Hou, P. Ma and J. Lin, Biomaterials, 2014, 35, 6359–6368 CrossRef CAS PubMed.
- M. Dolatabadi, T. Świergosz, C. Wang and S. Ahmadzadeh, Arabian J. Chem., 2023, 16, 104424 CrossRef CAS.
- A. H. Cahyana, A. R. Liandi, M. Maghdalena, R. T. Yunarti and T. P. Wendari, Ceram. Int., 2022, 48, 18316–18323 CrossRef CAS.
- N. Chadha, M. Y. Bhat, S. Hashmi and P. Saini, J. Energy Storage, 2022, 46, 103789 CrossRef.
- A. H. Mahvi, D. Balarak and E. Bazrafshan, Int. J. Environ. Anal. Chem., 2023, 103, 3501–3521 CrossRef CAS.
- M.-L. Ye, Y. Zhu, Y. Lu, L. Gan, Y. Zhang and Y.-G. Zhao, Talanta, 2021, 230, 122299 CrossRef CAS PubMed.
- A. Kirschning, L. Kupracz and J. Hartwig, Chem. Lett., 2012, 41, 562–570 CrossRef CAS.
- L. Nirumand and S. Farhadi, New J. Chem., 2023, 47, 4845–4859 RSC.
- M. Yan, Q. Liang, W. Wan, Q. Han, S. Tan and M. Ding, RSC Adv., 2017, 7, 30109–30117 RSC.
- Y. Li, J. Qiu, S. Ye, L. Wang, C. Yang, P. Sun and C. Wang, New J. Chem., 2017, 41, 14137–14144 RSC.
- Y. Zhu, S. Cheng, W. Zhou, J. Jia, L. Yang, M. Yao, M. Wang, J. Zhou, P. Wu and M. Liu, ACS Sustain. Chem. Eng., 2017, 5, 5067–5074 CrossRef CAS.
- P. Hariani, M. Said, R. A. Salni, N. Aprianti and E. Sthephanie, Global NEST J., 2023, 25, 36–43 CAS.
- H. Zhang, X. Tian, C. Wang, H. Luo, J. Hu, Y. Shen and A. Xie, Appl. Surf. Sci., 2014, 314, 228–232 CrossRef CAS.
- M. Neysi and D. Elhamifar, Front. Chem., 2023, 11, 1112911 CrossRef CAS PubMed.
- N. V. Plechkova and K. R. Seddon, Chem. Soc. Rev., 2008, 37, 123–150 RSC.
- B. Karimi, M. Tavakolian, F. Mansouri and H. Vali, ACS Sustain. Chem. Eng., 2018, 7, 3811–3823 CrossRef.
- R. Nemati, D. Elhamifar, A. Zarnegaryan and M. Shaker, Inorg. Chem. Commun., 2022, 145, 109934 CrossRef CAS.
- U.-a. Kanta, V. Thongpool, W. Sangkhun, N. Wongyao and J. Wootthikanokkhan, J. Nanomater., 2017, 2017, 2758294 Search PubMed.
- P. Mofatehnia, G. M. Ziarani, D. Elhamifar and A. Badiei, J. Phys. Chem. Solids, 2021, 155, 110097 CrossRef CAS.
- G. Antarnusa, P. D. Jayanti, Y. R. Denny and A. Suherman, Materialia, 2022, 25, 101525 CrossRef CAS.
- E. Suharyadi, T. Alfansuri, L. S. Handriani, N. A. Wibowo and H. Sabarman, J. Mater. Sci.: Mater. Electron., 2021, 32, 23958–23967 CrossRef CAS.
- H. He, Y. Zhong, X. Liang, W. Tan, J. Zhu and C. Yan Wang, Sci. Rep., 2015, 5, 10139 CrossRef CAS PubMed.
- M. Vahidian, D. Elhamifar and M. Shaker, Polyhedron, 2020, 178, 114326 CrossRef CAS.
- M. Shaker and D. Elhamifar, Colloids Surf., A, 2021, 608, 125603 CrossRef CAS.
-
A. C. Company, Catalog Handbook of Fine Chemicals, Aldrich Chemical Company, 2000 Search PubMed.
- Z. Kiani, R. Zhiani, S. Khosroyar, A. Motavalizadehkakhky and M. Hosseiny, Inorg. Chem. Commun., 2021, 124, 108382 CrossRef CAS.
- J. A. Lazzús, Ind. Eng. Chem. Res., 2009, 48, 8760–8766 CrossRef.
- M. Gholinejad, M. Shojafar and J. M. Sansano, J. Iran. Chem. Soc., 2020, 17, 2033–2043 CrossRef CAS.
- M. Niakan and Z. Asadi, Catal. Lett., 2019, 149, 2234–2246 CrossRef CAS.
- K. Zhang, J. M. Suh, T. H. Lee, J. H. Cha, J. W. Choi, H. W. Jang, R. S. Varma and M. Shokouhimehr, Nano Convergence, 2019, 6, 1–7 CrossRef PubMed.
- N. Khaleghi, M. Forouzandeh-Malati, F. Ganjali, Z. Rashvandi, S. Zarei-Shokat, R. Taheri-Ledari and A. Maleki, Sci. Rep., 2023, 13(1), 5225 CrossRef CAS PubMed.
- P. Supriya, B. Srinivas, K. Chowdeswari, N. Naidu and B. Sreedhar, Mater. Chem. Phys., 2018, 204, 27–36 CrossRef CAS.
- K. Taheri, D. Elhamifar, S. Kargar and A. Zarnegaryan, RSC Adv., 2023, 13, 16067–16077 RSC.
- M. Neysi and D. Elhamifar, Front. Chem., 2024, 12, 1336855 CrossRef CAS PubMed.
- R. Nemati, D. Elhamifar, A. Zarnegaryan and M. Shaker, Appl. Organomet. Chem., 2021, 35, e6409 CrossRef CAS.
- Z. Haydari, D. Elhamifar, M. Shaker and M. Norouzi, Appl. Surf. Sci., 2021, 5, 100096 CrossRef.
|
This journal is © The Royal Society of Chemistry 2024 |
Click here to see how this site uses Cookies. View our privacy policy here.