Preparation of carbon nanotube-reinforced polyethylene nanocomposites with better anti-scaling and corrosion-resistant properties
Received
14th March 2023
, Accepted 20th June 2023
First published on 21st June 2023
Abstract
Anti-scaling technology for pipelines has always been a focus of oilfield industrial production. Compared with traditional metal pipes, polyethylene (PE) pipes have unique advantages in terms of corrosion resistance, surface friction resistance, and service life. In this paper, aiming at an enhancement of anti-scaling and corrosion-resistant properties, as well as increased mechanical properties, PE nanocomposites have been prepared by the introduction of modified carbon nanotubes (m-CNTs) into the PE matrix. To improve the interface compatibility of the composites, the CNTs were treated with reactive tetrabutyl titanate after nitric acid oxidation, which brings about uniform dispersion of the CNTs and intimate interface interaction. As the m-CNT fraction increases, the PE crystallinity displays a slight increase. Polarized microscopy shows that the scaling on the surface of the composite material is obviously reduced compared with pure PE, because the surface free energy of the composite material decreases. Moreover, due to the good dispersion, the composites show enhanced mechanical properties. That is, by adding 1.10 wt% CNTs, the tensile stress and impact toughness of the composites are 20.76 MPa and 37.89 kJ m−2, respectively, increases of 15.0% and 11.9% compared with pure PE. This paper supports the idea that the crystallinity of the PE matrix can be improved by adding CNTs, thereby increasing the corrosion resistance and anti-scaling properties. This work can provide inspiration for using the methods of scale inhibition and corrosion resistance in polymer nanocomposites.
Keywords: Carbon nanotube; Nanocomposite; Polyethylene; Anti-scaling; Corrosion-resistant.
1 Introduction
Pipeline scaling is a common problem in the petroleum industry.1–4 Scale in the pipeline can narrow the area of the cross-section of the conduits and increase the resistance to fluid transport.5,6 Therefore, it is desirable to pay more attention to anti-scaling technology. The formation of scale is mainly due to the precipitation of inorganic salts such as calcium carbonate, calcium sulfate and magnesium hydroxide.2,7 By preparing or coating materials with low surface free energy on the surface of metal pipelines, the difficulty of adhesion of scale to the surface is increased.8 Due to their low surface free energy and very convenient processing technology, various kinds of polymeric materials have been widely used in coating the inside of the pipelines and they show unique advantages in self-cleaning and anti-corrosion.9–11 However, the mechanical strength and hardness of most polymers are poor due to their intrinsic properties, which limits their broader application in pipelines.12 Therefore, the addition of various fillers to a polymer to improve its mechanical and functional properties and broaden its application range has been a research hotspot.13–19
Among the vast number of polymers, polyethene (PE) has been widely used in pipelines in the petroleum industry due to its low cost, facile processability, and moisture resistance. It can be high-crystalline, low-crystalline or amorphous.20 The modulus and strength of many of these materials are relatively low, which means that, besides electrical conductivity, other properties such as mechanical properties can also be significantly enhanced after adding nanofillers.21–28 In the harsh fluid environment in oilfield industrial production, PE pipe materials are easily eroded mainly from amorphous cracks to the whole, which leads to frequent replacement. If a facile and simple method can be used to increase the the crystallinity of the PE matrix, the corrosion resistance of the pipes is expected to be improved.
On the other hand, pipeline scaling has always been a serious problem. The water of oil injection wells is rich in various minerals.29–31 When the temperature, pressure and pH value change, scale is easily formed and it becomes a challenging task to remove the complex scale. In order to improve the anti-scaling performance and durability of coating materials based on PE polymers, nanocomposite materials have been made by introducing various kinds of nanofiller in an appropriate proportion. At present, researchers are committed to preparing polymer composites with both mechanical properties and scale inhibition performance. By adding various fillers into the polymer matrix, the defects of poor rigidity, hardness, and impact resistance of the polymer matrix have been proved to be improved in many studies.21,32–34 For instance, due to their reduction ability and barrier performance, graphene and some other two-dimensional nanosheets have been introduced to polymers as an effective anticorrosion coating, which can bring about enhanced mechanical strength and anti-scaling.35–38 Among nanofillers, CNTs have a specific one-dimensional structure in comparison with other dimensional nanofillers. Moreover, compared to graphene, the dispersion of CNTs has been scaled up, and the reduction in its price makes it possible for CNTs to be added into PE nanocomposites on a large scale.35,39–41 Due to their outstanding properties, especially high electrical conductivity and mechanical strength, it is found that the addition of such a 1D nanofiller can bring about an obvious enhancement in the mechanical properties and electrical conductivity of the nanocomposites.42–49 Despite a lot of literature on CNT/PE nanocomposites being reported, there are almost no reports concerned with the effect of carbon nanotubes on the anti-scaling and corrosion resistance of PE nanocomposites.11,14,15,50–55 Besides, CNTs can be functionalized and dispersed in some polymers for coating applications,56 like typical CNT-filled epoxy-based nanocomposites.57 Such a nanocomposite coating can bring about improved anti-corrosion ability in comparison with pure epoxy coating. However, the coating layer may encounter problems of peeling.
In this work, we report PE nanocomposites with excellent anti-scaling performance, which are fabricated by incorporating CNTs. To improve the interface compatibility of the composites, the CNTs were treated by nitric acid oxidation followed by reactive tetrabutyl titanate. Unlike previous modification methods, this paper provides a strategy which can also effectively disperse the CNTs with high aspect ratios in the PE matrix, resulting in intimate interfacial interactions. More importantly, this work reveals that the crystallization of PE can be increased by increasing the fraction of CNTs, leading to higher PE crystallinity and better corrosion resistance. Moreover, due to the good dispersion, the composites show enhanced mechanical properties. This is superior to many CNT–polymer nanocomposites that may show decreased mechanical strength due to the addition of a high content of nanofillers.58 The work here provides a simple yet effective method for research into scale inhibition and corrosion resistance.
2 Results and discussion
Fig. 1a shows the preparation steps for the m-CNTs. Due to the existence of defects, the surface of the CNTs can be oxidized with nitric acid to produce reactive groups like –OH and –COOH. After that, the surface of the CNTs is reacted with tetrabutyl titanate molecules. Fig. 1b compares optical photographs of the original CNTs and m-CNTs in ethanol, with a weight fraction of 0.2 wt%. After standing for two hours, the primary CNTs become agglomerated and precipitate to the bottom, while the m-CNTs can still retain a uniform dispersion, indicating that the dispersion of CNTs after modification has been obviously improved. This is expected to improve the interfacial bonding of the CNTs with polyethylene due to the grafted alkyl groups. Fig. 1c shows the SEM image of the m-CNTs. After treatment with HNO3 for 1 hour and reactive tetrabutyl titanate, the aggregated state of the CNTs had been broken, and the CNTs still maintained a large aspect ratio. Fig. 1d and e display the TEM images of the m-CNTs. A small amount of coating layer has been attached to the surface of the CNTs treated with tetrabutyl titanate, which may be the groups of –Ti–O–CH2–CH3 and partial TiO2. The element distribution mapping also showed that Ti and O were evenly encapsulated around carbon.59 This is consistent with the surface modifications of the CNTs, as illustrated in the experiments.
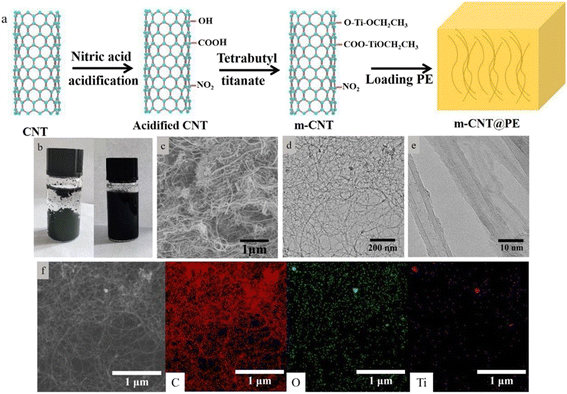 |
| Fig. 1 (a) Schematic diagram of surface modification steps with CNTs to make PE nanocomposites. (b) Comparison of optical photographs of the original CNTs and m-CNTs in ethanol. (c) SEM and (d and e) TEM images of the m-CNTs. (f) Elemental mapping of the m-CNTs. | |
According to a comparison of the Raman shifts of the CNTs during the modification steps (Fig. 2f), the ratio of the D peak to the G peak (ID/IG) of untreated CNTs is about 0.96, while those of the oxidized CNTs and m-CNTs are 0.84 and 0.67, respectively. This indicates that the acidification and grafting treatments cause no great damage to the nanotubes, and this functionalization method shows no great damage to the structural integrity of the nanotubes. Good retention of the structural integrity of the carbon nanotubes is beneficial to maintaining their good mechanical and thermal conductivity.
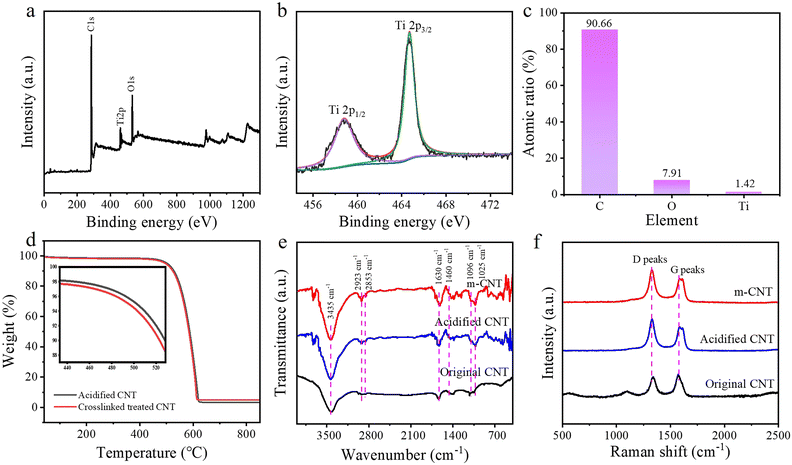 |
| Fig. 2 (a–c) XPS Ti2p spectra of the m-CNTs. (d) TGA curves of the acidified CNTs and m-CNTs. (e) FTIR and (f) Raman shifts of the different CNT samples. | |
Fig. 3a shows that the typical diffraction peaks of the CNT filler are located at 25.8° and 43.2°, corresponding to the (002) and (100) crystal planes, respectively. The results support the crystal structure of the carbon nanotubes still remaining after modification. Moreover, close to the (002) peak of the CNTs, a small peak at around 26.2° can be observed which should be ascribed to the (101) peak of TiO2. This indicates that a small fraction of tetrabutyl titanate might be converted to TiO2 on the CNTs during the modification. The XRD characterization of PE before and after the introduction of the CNTs are compared in Fig. 3a. PE shows obvious peaks at 21.5° and 23.9°, which are characteristic diffraction peaks of (110) and (200) crystal planes, respectively, which proves that it contains a partially crystalline structure. The results show that the characteristic peak of PE is still maintained after adding the m-CNTs, but the peak of the nanotubes is not obvious, which may be because they are well dispersed in the PE matrix. Fig. 3b compares nanocomposites with different contents of m-CNTs. It should be pointed out that the addition of the m-CNT nanofiller does not change the crystallization characteristics. With the increase in carbon nanotube filler content, the peak position of the polyethylene remains unchanged, only with the half peak width of the (110) crystal plane becoming narrowed, which may support a slight enhancement in crystallization.
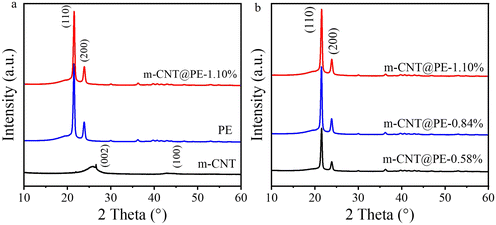 |
| Fig. 3 (a) XRD patterns of the CNT/PE nanocomposite, PE and CNT. (b) XRD patterns of the nanocomposites with increasing CNT content. | |
As shown in the XRD results, PE is a partially crystalline polymer. Fig. 4a shows the DSC melting curves of the nanocomposites. The melting peak temperature of the samples shows a little increase with increasing m-CNT content. Also, the enthalpy values of the nanocomposites have increased. The calculated melting enthalpies are 138.55 J g−1, 140.29 J g−1, 141.71 J g−1 and 149.25 J g−1, respectively, for pure polyethylene, and 0.58 wt%, 0.84 wt% and 1.10 wt% CNT/PE nanocomposites. The results support the idea that the degree of crystallinity of PE can be enhanced by the introduction of CNTs.
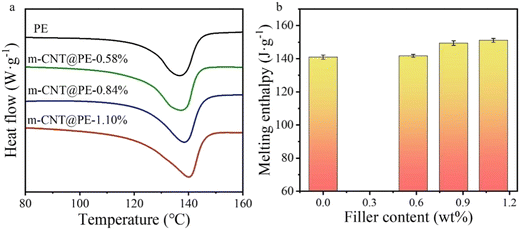 |
| Fig. 4 Comparison of (a) DSC melting curves and (b) enthalpy values of the nanocomposites with increasing m-CNT content. | |
Fig. 5a shows the stress–strain curves for pure PE and the nanocomposites. Compared with pure PE, the elongation at break of the composites shows no obvious decrease, while the yield stress of the composites with 0.58 wt%, 0.84 wt% and 1.10 wt% m-CNTs is increased to 18.40 MPa, 19.42 MPa and 20.76 MPa, respectively (Fig. 5b). The yield stress has increased by 1.94%, 7.59% and 15.02%, respectively. Fig. 5c further compares the Young's modulus of PE and the nanocomposites. The Young's modulus of the composite has increased from 128.42 MPa to 137.21 MPa, 142.15 MPa and 147.54 MPa, respectively (Fig. 5c), consistent with the enhanced mechanical strength. The increased mechanical properties support the finding that the m-CNTs have been uniformly dispersed into the PE matrix and bond well with it. The modified carbon nanotubes can play an effective role in stress transfer in the PE matrix.
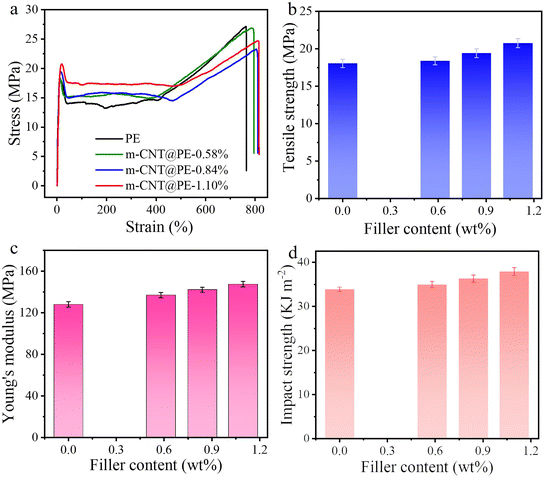 |
| Fig. 5 (a) Stress–strain curves; (b) yield stress; (c) Young's modulus; and (d) impact toughness of PE and CNT/PE nanocomposites. | |
The strengthening effect of the CNTs on PE not only increases the yield stress, but also enhances the toughness of PE. Fig. 5d shows a comparison of the impact toughness of the nanocomposites. According to the test results, the impact toughness of pure PE is 33.85 kJ m−2, and that of the nanocomposites with 0.58 wt%, 0.84 wt% and 1.096 wt% CNTs is improved to 34.93 kJ m−2, 36.28 kJ m−2 and 37.89 kJ m−2, respectively, in which the impact toughness of the 1.10 wt% nanocomposite has increased by 11.94%. It can be seen that with an increase in carbon nanotube content in the PE matrix, the comprehensive mechanical properties show a rising trend on the whole. The impact toughness of the nanocomposites convincingly shows that the m-CNTs interact well with the PE matrix, and the stress is transferred to the carbon nanotube bundle through the matrix. The CNTs in the matrix play a bridging role to disperse the load stress, delay tear stress leading to destruction of the composites, and improve the impact toughness of the composites.
Fig. 6a shows that the cross-section of PE is a wave-shaped layered crystal. After adding different m-CNTs into the PE matrix, the PE crystals become much smaller, as shown in Fig. 6b–d. Meanwhile, with an increase in nanotube filler, the layered crystal structure of the PE matrix becomes smaller. This supports the idea that the added m-CNTs can act as grain refiners to toughen the PE, consistent with the increase in mechanical strength of the nanocomposites. Moreover, the fracture surface of the CNT/PE nanocomposites is rough, with no CNTs observed being pulled out of the PE matrix, and there is no obvious phenomenon of large particle agglomeration. The results indicate that the CNTs hinder the cracking of the PE matrix.
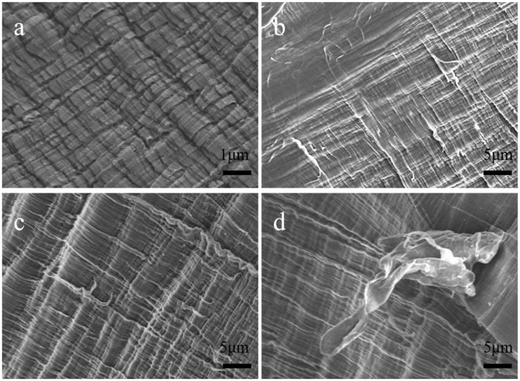 |
| Fig. 6 Cross-sectional SEM images of the materials: (a) PE; (b) 0.58 wt%; (c) 0.84 wt%; (d) 1.10 wt% CNT/PE nanocomposites. | |
Fig. 7 and 8 compare the fouling formation on pure PE and the 1.10 wt% CNT/PE nanocomposite. During this observation period, polarized microscopy shows that the CNT/PE nanocomposite displays less scale and fewer corrosion hole defects on the surface for the same time soaking in oilfield water. The results indicate that adding a certain amount of CNTs to PE can effectively inhibit the formation of scale and enhance the corrosion resistance of the PE matrix. The reason why the scaling on the surface of the composite material may be reduced should be related to the surface free energy of the nanocomposite material decreasing when the CNTs are added.
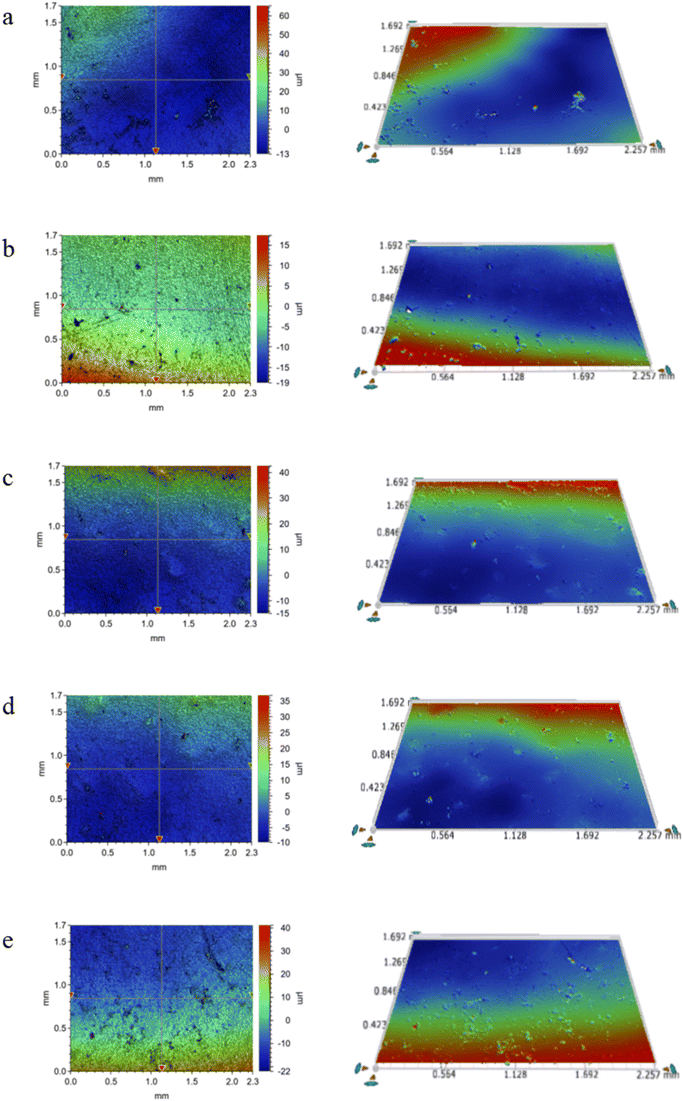 |
| Fig. 7 (a–e) Surface morphology (left) of a pure PE sample soaked in oilfield water for 10, 17, 24, 31 and 38 days, respectively, and the 3D topography (right) after flattening. | |
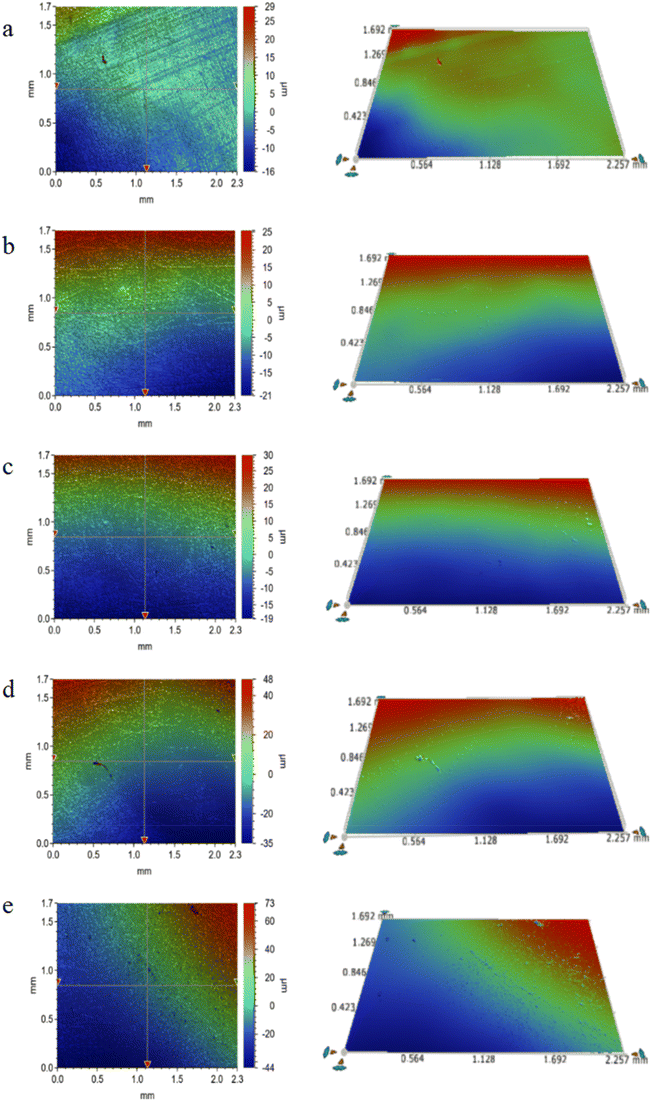 |
| Fig. 8 (a–e) Surface morphology (left) and 3D morphology (right) of the 1.10 wt% CNT/PE nanocomposite after being soaked in oilfield water for 10, 17, 24, 31 and 38 days, respectively. | |
Fig. 9 shows that the surface contact angle of pure PE is 90.8°, indicating that PE is a hydrophobic material. After adding CNTs into the PE matrix, the surface contact angle of all the nanocomposite materials has increased a little. The surface contact angles become 93.2°, 93.4°, and 93.8° for the 0.58 wt%, 0.84 wt%, and 1.10 wt% CNT/PE nanocomposites, respectively. The results support the idea that the hydrophobic property of PE has been enhanced with the increase in CNTs. The surface energy of polyethylene is 35.5 mJ m−2. It can be calculated that the surface energy of the composite material with 1.10 wt% CNTs is 29.65 mJ m−2, which is 16.47% lower than that of pure PE. Therefore, it becomes more difficult for impurities in water to be adsorbed on the surface of the material, avoiding the accumulation of dirt, which can bring about better anti-scaling performance.
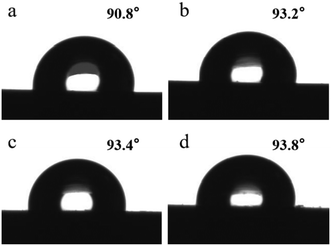 |
| Fig. 9 Surface contact angle of PE and the nanocomposites: (a) PE sample; (b–d) 0.58 wt%, 0.84 wt%, and 1.10 wt% CNT/PE nanocomposites. | |
To further confirm the anti-corrosion property, PE and CNT/PE nanocomposites of the same size were soaked in a concentrated sulfuric acid–hydrochloric acid (1
:
1 in volume) corrosive solution (80 °C, 5 min). After that, the mass loss of the samples was calculated and is shown in Fig. 10. Compared with pure PE, the mass loss of all the nanocomposite materials is less after corrosion in an acidic environment, which indicates that the addition of CNTs plays a reinforcing role in the PE matrix, consistent with the results for increased crystallinity.
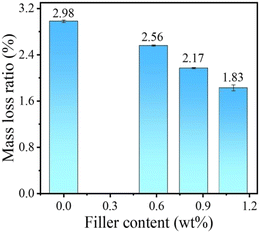 |
| Fig. 10 Comparison of the mass loss of PE and the CNT/PE nanocomposite after corrosion. | |
3 Conclusions
In summary, PE nanocomposites have been prepared by the introduction of m-CNTs into the PE matrix, which provide improved anti-scaling and corrosion-resistant properties, as well as increased mechanical properties. For better interface compatibility, the CNTs were treated with nitric acid oxidation and reactive tetrabutyl titanate, to obtain a uniform dispersion and intimate interface interaction. With an increase in the m-CNT fraction, the crystallinity of PE displays an increase and the surface free energy of the composite materials decreases. As a result, the scaling on the surface of the composite material is obviously reduced compared with pure PE, and the nanocomposites become more corrosion resistant. Moreover, due to the good dispersion, the composites show enhanced mechanical properties. That is, by adding 1.10 wt% m-CNTs, the tensile stress and impact toughness of the composites are 20.76 MPa and 37.89 kJ m−2, respectively, increases of 15.0% and 11.9% compared with pure PE. This paper supports the idea that the crystallinity of the PE matrix can be improved by adding CNTs, thereby increasing its corrosion resistance and anti-scaling properties. It has broad prospects in oilfield production and other industrial applications.
4 Experimental section
4.1 Materials
The CNTs were prepared by chemical vapor deposition using a fluidized bed reactor. They were multi-walled CNTs with lengths of more than 10 microns and diameters of 7–11 nanometers. Polyethylene was provided by Petrochina Daqing Chemical Research Center. Ethanol, nitric acid and tetrabutyl titanate were analytically pure and were purchased from Sinopharm Group Chemical Reagents Co., Ltd.
4.2 Modification of the CNTs
First, 200 g of the as-prepared CNT powder was mixed into 7% nitric acid solution. Then the mixture was stirred for 1 hour with a magnetic stirrer. After that, the nitric acid treated CNTs were collected from the suction filter by washing with ultrapure water until the filtrate became neutral. After drying in an oven for 24 hours, we had CNTs oxidized by nitric acid. Subsequently, 5 wt% tetrabutyl titanate–ethanol solution was prepared, and 100 g of the HNO3-oxided CNT was weighed and mixed into 2.5 L of the prepared tetrabutyl titanate–ethanol solution. Then the mixture was continuously stirred for 1.5 hours with a magnetic stirrer. After that, the CNTs were washed with ethanol and filtered with a suction filter funnel. After drying for 12 hours in an oven, the tetrabutyl titanate modified CNTs were obtained.
4.3 Melt extrusion-hot pressing of the nanocomposites
PE and the modified CNTs were mixed with an SJZ-45 experimental twin screw extruder at 210 °C. They were extruded according to the three weight proportions of 200
:
1.16, 200
:
1.69 and 200
:
2.21. The corresponding nanocomposites were PE/CNT pellets of 0.58 wt%, 0.84 wt% and 1.10 wt%, respectively.
4.4 Characterization
SEM experiments were conducted on a JEOL-2010 at 3.0 kV. TEM experiments were conducted on the JEM-2010 operated at 120 kV. Raman spectra were performed on a HR800 inVia with He–Ne laser excitation at 532 nm. The tensile properties of the samples were analyzed with a universal tensile testing machine MTS (SANS) CMT4502. The samples were dog-bone shaped with tested length, width and thickness of 20 mm, 4 mm and 2 mm, respectively. The tensile speed was 10 mm min−1. The impact toughness of the samples was analyzed with a JB-25 pendulum impact tester, and the samples were Charpy V-notch impact samples. Thermal analysis (TGA test, Q5000 IR) was used to obtain the thermal properties of the composites at a heating rate of 10 °C min−1 under nitrogen. The crystallization properties of the composites were obtained at room temperature with a heating rate of 10 °C min−1 with a DSC6200 from SEIKO Instrument Company, Japan. An XPS-Kratos-AXIS X-ray photoelectron spectrometer manufactured by the Spike Company of Germany was used to further study the surface structure of the CNTs. A white light interference three-dimensional microscope (Contour GTK) was used to analyze the dirt morphology and corrosion pits on the sample surface. The wetting angle of the composite surface was measured with an SL200B contact angle meter.
Conflicts of interest
The authors declare no competing financial interest.
Acknowledgements
This work was supported by the research fund of China National Petroleum Corporation (No. 2020E-2801(GF)).
References
- A. Benamor, A. G. Talkhan, M. Nasser, I. Hussein and P. C. Okonkwo, Effect of temperature and fluid speed on the corrosion behavior of carbon steel pipeline in Qatari oilfield produced water, J. Electroanal. Chem., 2018, 808, 218–227 CrossRef CAS.
- A. A. Olajire, A review of oilfield scale management technology for oil and gas production, J. Pet. Sci. Eng., 2015, 135, 723–737 CrossRef CAS.
- M. El-Said, M. Ramzi and T. Abdel-Moghny, Analysis of oilfield waters by ion chromatography to determine the composition of scale deposition, Desalination, 2009, 249, 748–756 CrossRef CAS.
- A. B. BinMerdhah, A. A. M. Yassin and M. A. Muherei, Laboratory and prediction of barium sulfate scaling at high-barium formation water, J. Pet. Sci. Eng., 2010, 70, 79–88 CrossRef.
- Y. Dong, Analysis on anti-corrosion and anti-scaling technology of water injection well in oil production plant, IOP Conf. Ser. Earth Environ. Sci., 2020, 514, 022005 CrossRef.
- B. Dong, Y. Xu, H. Deng, F. Luo and S. Jiang, Effects of pipeline corrosion on the injection water quality of low permeability in oilfield, Desalination, 2013, 326, 141–147 CrossRef CAS.
- G. Pei, C. Wang and L. Liu, Experimental study on the cause of inorganic scale formation in the water injection pipeline of tarim oilfield, J. Chem., 2014, 2014, 619834 Search PubMed.
- S. Pourhashem, A. Seif, F. Saba, E. G. Nezhad, X. Ji, Z. Zhou, X. Zhai, M. Mirzaee, J. Duan, A. Rashidi and B. Hou, Antifouling nanocomposite polymer coatings for marine applications: A review on experiments, mechanisms, and theoretical studies, J. Mater. Sci. Technol., 2022, 118, 73–113 CrossRef CAS.
- M. F. Montemor, Functional and smart coatings for corrosion protection: A review of recent advances, Surf. Coat. Technol., 2014, 258, 17–37 CrossRef CAS.
- L. Rassouli, R. Naderi and M. Mahdavain, The role of micro/nano zeolites doped with zinc cations in the active protection of epoxy ester coating, Appl. Surf. Sci., 2017, 423, 571–583 CrossRef CAS.
- R. Fürstner, W. Barthlott, C. Neinhuis and P. Walzel, Wetting and self-cleaning properties of artificial superhydrophobic surfaces, Langmuir, 2005, 21, 956–961 CrossRef PubMed.
- T. Zhu, X. Li, X. Zhao, X. Zhang, Y. Lu and L. Zhang, Stress-strain behavior and corresponding crystalline structures of four types of polyethylene under a wide range of strain rates, Polym. Test., 2022, 106, 107460 CrossRef CAS.
- S. V. Harb, S. H. Pulcinelli, C. V. Santilli, K. M. Knowles and P. A. Hammer, Comparative study on graphene oxide and carbon nanotube reinforcement of PMMA-siloxane-silica anticorrosive coatings, ACS Appl. Mater. Interfaces, 2016, 8, 16339–16350 CrossRef CAS PubMed.
- I. Hejazi, B. Hajalizadeh, J. Seyfi, G. M. M. Sadeghi, S.-H. Jafari and H. A. Khonakdar, Role of nanoparticles in phase separation and final morphology of superhydrophobic polypropylene/zinc oxide nanocomposite surfaces, Appl. Surf. Sci., 2014, 293, 116–123 CrossRef CAS.
- J. Seyfi, I. Hejazi, S.-H. Jafari, H. A. Khonakdar, G. M. Mohamad Sadeghi, A. Calvimontes and F. Simon, On the combined use of nanoparticles and a proper solvent/non-solvent system in preparation of superhydrophobic polymer coatings, Polymer, 2015, 56, 358–367 CrossRef CAS.
- N. Lachman and H. Daniel Wagner, Correlation between interfacial molecular structure and mechanics in CNT/epoxy nano-composites, Composites, Part A, 2010, 41, 1093–1098 CrossRef.
- R. Pratyush Behera, P. Rawat, S. Kumar Tiwari and K. Kumar Singh, A brief review on the mechanical properties of Carbon nanotube reinforced polymer composites, Mater. Today: Proc., 2020, 22, 2109–2117 CAS.
- Y. Lu, L. Liu, M. Tian, H. Geng and L. Zhang, Study on mechanical properties of elastomers reinforced by zinc dimethacrylate, Eur. Polym. J., 2005, 41, 589–598 CrossRef CAS.
- Q. Zhang, J.-Q. Huang, W.-Z. Qian, Y.-Y. Zhang and F. Wei, The road for nanomaterials industry: A review of carbon nanotube production, post-treatment, and bulk applications for composites and energy storage, Small, 2013, 9, 1237–1265 CrossRef CAS PubMed.
- M. Khoshsefat, A. Dechal, S. Ahmadjo, S. M. M. Mortazavi, G. Zohuri and J. B. P. Soares, Amorphous to high crystalline PE made by mono and dinuclear Fe-based catalysts, Eur. Polym. J., 2019, 119, 229–238 CrossRef CAS.
- W. Tang, M. H. Santare and S. G. Advani, Melt processing and mechanical property characterization of multi-walled carbon nanotube/high density polyethylene(MWNT/HDPE) composite films, Carbon, 2003, 41, 2779–2785 CrossRef CAS.
- D. Bikiaris, A. Vassiliou, K. Chrissafis, K. M. Paraskevopoulos, A. Jannakoudakis and A. Docoslis, Effect of acid treated multi-walled carbon nanotubes on the mechanical, permeability, thermal properties and thermo-oxidative stability of isotactic polypropylene, Polym. Degrad. Stab., 2008, 93, 952–967 CrossRef CAS.
- H. Meng, G. X. Sui, P. F. Fang and R. Yang, Effects of acid- and diamine-modified MWNTs on the mechanical properties and crystallization behavior of polyamide 6, Polymer, 2008, 49, 610–620 CrossRef CAS.
- D. Zhao, Q. Lei, C. Qin and X. Bai, Melt process and performance of multi-walled carbon nanotubes reinforced LDPE composites, Pigm. Resin Technol., 2006, 35(6), 341–345 CrossRef CAS.
- M. M. Zamani, A. Fereidoon and A. Sabet, Multi-walled carbon nanotube-filled polypropylene nanocomposites: High velocity impact response and mechanical properties, Iran. Polym. J., 2012, 21, 887–894 CrossRef CAS.
- M. Cadek, J. N. Coleman, K. P. Ryan, V. Nicolosi, G. Bister, A. Fonseca, J. B. Nagy, F. Béguin, K. Szostak and W. J. Blau, Reinforcement of polymers with carbon nanotubes: The role of nanotube surface area, Nano Lett., 2004, 4(2), 353–356 CrossRef CAS.
- X. Jia, Q. Zhang, M.-Q. Zhao, G.-H. Xu, J.-Q. Huang, W. Qian, Y. Lu and F. Wei, Dramatic enhancements in toughness of polyimide nanocomposite via long-CNT-induced long-range creep, J. Mater. Chem., 2012, 22(14), 7050–7056 RSC.
- B. M. Amoli, S. A. A. Ramazani and H. Izadi, Preparation of ultrahigh-molecular-weight polyethylene/carbon nanotube nanocomposites with a Ziegler–Natta catalytic system and investigation of their thermal and mechanical properties, J. Appl. Polym. Sci., 2012, 125, E453–E461 CrossRef CAS.
-
J. Yap, M. J. Fuller, L. A. Schafer and S. Kelkar, Removing iron sulfide scale: A novel approach, in Abu Dhabi International Petroleum Exhibition and Conference, 2010, p. SPE-138520-MS Search PubMed.
- D. S. Lakshmi, B. Senthilmurugan, E. Drioli and A. Figoli, Application of ionic liquid polymeric microsphere in oil field scale control process, J. Pet. Sci. Eng., 2013, 112, 69–77 CrossRef CAS.
- B. Senthilmurugan, B. Ghosh and S. Sanker, High performance maleic acid based oil well scale inhibitors-development and comparative evaluation, J. Ind. Eng. Chem., 2011, 17, 415–420 CrossRef CAS.
- N. Salah, A. M. Alfawzan, A. Saeed, A. Alshahrie and W. Allafi, Effective reinforcements for thermoplastics based on carbon nanotubes of oil fly ash, Sci. Rep., 2019, 9, 20288 CrossRef CAS.
- H. Fouad, R. Elleithy, S. M. Al-Zahrani and M. A.-H. Ali, Characterization and processing of high density polyethylene/carbon nano-composites, Mater. Des., 2011, 32, 1974–1980 CrossRef CAS.
- R. T. Tebeta, A. M. Fattahi and N. A. Ahmed, Experimental and numerical study on HDPE/SWCNT nanocomposite elastic properties considering the processing techniques effect, Microsyst. Technol., 2020, 26, 2423–2441 CrossRef CAS.
- H. Hiura, T. W. Ebbesen and K. Tanigaki, Opening and purification of carbon nanotubes in high yields, Adv. Mater., 1995, 7(3), 275–276 CrossRef CAS.
- H. Shen, J. Guo, H. Wang, N. Zhao and J. Xu, Bioinspired modification of h-BN for high thermal conductive composite films with aligned structure, ACS Appl. Mater. Interfaces, 2015, 7, 5701–5708 CrossRef CAS.
- T. Ramanathan, A. A. Abdala, S. Stankovich, D. A. Dikin, M. Herrera-Alonso, R. D. Piner, D. H. Adamson, H. C. Schniepp, X. Chen, R. S. Ruoff, S. T. Nguyen, I. A. Aksay, R. K. Prud'Homme and L. C. Brinson, Functionalized graphene sheets for polymer nanocomposites, Nat. Nanotechnol., 2008, 3, 327–331 CrossRef CAS PubMed.
- B. Ge, Z. Zhang, X. Zhu, X. Men, X. Zhou and Q. Xue, A graphene coated cotton for oil/water separation, Compos. Sci. Technol., 2014, 102, 100–105 CrossRef CAS.
- K. Esumi, M. Ishigami, A. Nakajima, K. Sawada and H. Honda, Chemical treatment of carbon nanotubes, Carbon, 1996, 34, 279–281 CrossRef CAS.
- X. Wang, Z. Z. Yong, Q. W. Li, P. D. Bradford, W. Liu, D. S. Tucker, W. Cai, H. Wang, F. G. Yuan and Y. T. Zhu, Ultrastrong, stiff and multifunctional carbon nanotube composites, Mater. Res. Lett., 2013, 1, 19–25 CrossRef CAS.
- K. Jiang, Q. Li and S. Fan, Spinning continuous carbon nanotube yarns, Nature, 2002, 419, 801–801 CrossRef CAS PubMed.
- T. Yamamoto and K. Kawaguchi, Synthesis of composite polymer particles with carbon nanotubes and evaluation of their mechanical properties, Colloids Surf., A, 2017, 529, 765–770 CrossRef CAS.
- A. V. Desai and M. A. Haque, Mechanics of the interface for carbon nanotube–polymer composites, Thin Walled Struct., 2005, 43, 1787–1803 CrossRef.
- B. A. I. Jinbo, Evidence of the reinforcement role of chemical vapour deposition multi-walled carbon nanotubes in a polymer matrix, Carbon, 2003, 41, 1325–1328 CrossRef.
- W.-H. Li, X.-H. Chen, Z. Yang and L.-S. Xu, Structure and properties of polypropylene-wrapped carbon nanotubes composite, J. Appl. Polym. Sci., 2009, 113, 3809–3814 CrossRef CAS.
- A. A. Zdanovich, S. I. Moseenkov, A. V. Ishchenko, V. L. Kuznetsov, M. A. Matsko and V. A. Zakharov, The morphology evolution of polyethylene produced in the presence of a Ziegler-type catalyst anchored on the surface of multi-walled carbon nanotubes, J. Appl. Polym. Sci., 2021, 138, 50528 CrossRef CAS.
- M. Nisar, C. P. Bergmann, J. Geshev, R. Quijada, T. Maraschin, N. R. de Souza Basso, E. G. Barrera and G. B. Galland, Synthesis of high-density polyethylene/rGO-CNT-Fe nanocomposites with outstanding magnetic and electrical properties, J. Appl. Polym. Sci., 2017, 134, 45382 CrossRef.
- L. Li, H. Shi, Z. Liu, L. Mi, G. Zheng, C. Liu, K. Dai and C. Shen, Anisotropic conductive polymer composites based on high density polyethylene/carbon nanotube/polyoxyethylene mixtures for microcircuits interconnection and organic vapor sensor, ACS Appl. Nano Mater., 2019, 2, 3636–3647 CrossRef CAS.
- E. Erfanian, M. Kamkar, D. Williams, Y. Zamani Keteklahijani, R. Salehiyan, S. S. Ray, M. Arjmand and U. Sundararaj, Dielectrorheology of aspect-ratio-tailored carbon nanotube/polyethylene composites under large deformations: Implications for high-temperature dielectrics, ACS Appl. Nano Mater., 2021, 4, 11493–11504 CrossRef CAS.
- Z. Wu, H. Wang, M. Xue, X. Tian, X. Ye, H. Zhou and Z. Cui, Facile preparation of superhydrophobic surfaces with enhanced releasing negative air ions by a simple
spraying method, Compos. Sci. Technol., 2014, 94, 111–116 CrossRef CAS.
- J. Yang, Z. Zhang, X. Men and X. Xu, Fabrication of stable, transparent and superhydrophobic nanocomposite films with polystyrene functionalized carbon nanotubes, Appl. Surf. Sci., 2009, 255, 9244–9247 CrossRef CAS.
- C.-F. Wang, W.-Y. Chen, H.-Z. Cheng and S.-L. Fu, Pressure-proof superhydrophobic films from flexible carbon nanotube/polymer coatings, J. Phys. Chem. C, 2010, 114, 15607–15611 CrossRef CAS.
- S. Sethi, L. Ge, L. Ci, P. M. Ajayan and A. Dhinojwala, Gecko-inspired carbon nanotube-based self-cleaning adhesives, Nano Lett., 2008, 8, 822–825 CrossRef CAS.
- I. Hejazi, G. M. M. Sadeghi, S. H. Jafari, H. A. Khonakdar, J. Seyfi, M. Holzschuh and F. Simon, Transforming an intrinsically hydrophilic polymer to a robust self-cleaning superhydrophobic coating via carbon nanotube surface embedding, Mater. Des., 2015, 86, 338–346 CrossRef CAS.
- S. Sethi and A. Dhinojwala, Superhydrophobic conductive carbon nanotube coatings for steel, Langmuir, 2009, 25, 4311–4313 CrossRef CAS.
- S. Imtiaz, M. Siddiq, A. Kausar, S. T. Muntha, J. Ambreen and I. Bibi, A Review Featuring Fabrication, Properties and Applications of Carbon Nanotubes(CNTs) Reinforced Polymer and Epoxy Nanocomposites, Chin. J. Polym. Sci., 2018, 36, 445–461 CrossRef CAS.
- C. M. Vu and Q. V. Bach, Oxidized multiwall carbon nanotubes filled epoxy-based coating: fabrication, anticorrosive, and mechanical characteristics, Polym. Bull., 2021, 78, 2329–2339 CrossRef CAS.
- M. Omastová, J. Prokeš, S. Podhradská and I. Chodák, Stability of electrical and mechanical properties of polyethylene/carbon black composites, Macromol. Symp., 2001, 170, 231–240 CrossRef.
- J. L. Sullivan, S. O. Saied and I. Bertoti, Effect of ion and neutral sputtering on single crystal TiO2, Vacuum, 1991, 42, 1203–1208 CrossRef CAS.
Footnote |
† These authors contributed equally. |
|
This journal is © Institute of Process Engineering of CAS 2024 |
Click here to see how this site uses Cookies. View our privacy policy here.