Rethinking nitrate reduction: redirecting electrochemical efforts from ammonia to nitrogen for realistic environmental impacts†
Received
15th January 2024
, Accepted 19th March 2024
First published on 19th March 2024
Abstract
The excessive use of nitrate in agriculture and industry poses a significant threat to human health and ecosystems. To effectively manage the nitrogen cycle (N-cycle) in nature and to deal with nitrate pollution in wastewater, various electrochemical approaches have been developed to convert nitrate into N-products. Recent research works have focused their efforts on electrochemical nitrate reduction (eNO3R) to ammonia (NH3) as “an alternative approach to the Haber–Bosch process” while reducing the environmental impacts. However, when considering challenges due to the low concentration of nitrate in wastes and difficulties in extracting as-synthesized NH3 and comparing this scale with the scale of current NH3 and nitrate production, such an eNO3R to NH3 approach at the largest possible scale, even without examining its economic viability and overall environmental implications, will have an insignificant impact. Therefore, we recommend that rational implementation approaches for nitrate treatment should involve converting nitrate ions at low concentrations into nitrogen (N2) gas or recycling them at high concentrations to produce other nitrate chemicals or fertilizers.
Broader context
With the growing world population and increasing human activities, nitrate pollution in water bodies has caused severe health and environmental issues. To provide clean drinking water and balance the nitrogen cycle (N-cycle) in nature, numerous research efforts have focused on removing nitrate from wastewater using electrochemical approaches. Several recent studies have claimed that converting waste nitrate into ammonia (NH3) with high catalytic performance provides an alternative approach to the Haber–Bosch process. Unfortunately, such a “waste-to-wealth” conversion will likely have insignificant impacts and should be considered an unnecessary distraction. To deliver realistic environmental impacts, our analysis deems that the low-concentration nitrate in wastewater should be directly converted into harmless N2 gas through electrochemical reactions, and for the case of high concentrations, nitrate ions should be recycled and purified to generate nitrate chemicals or fertilizers.
|
Background
Ammonia (NH3), as one of the most important chemicals, plays a vital role, particularly in the production of fertilizers for agriculture that feeds the world population.1–3 The global production of NH3 reaches over 180 million tonnes (Mt) per year with a market value of ∼US$75 billion.4–6 This massive amount of NH3 is produced through the conventional Haber–Bosch process, accounting for 1–2% of the world's energy demand and contributing to 1–1.5% of annual anthropogenic CO2 emissions.7,8 Around 75% of NH3 is utilized in the agricultural sector for the production of fertilizers and synthesis of nitric acid (HNO3), another critical industrial feedstock for manufacturing fertilizers.9 The remaining ∼25% is employed in plastics, explosives, food and synthetic fibers manufacturing industries.10 In particular, almost 100% of nitric acid production relies on the energy-intensive Ostwald process: NH3 oxidation at high temperatures (600–900 °C) and pressure (410–1000 kPa).1,11,12 The global production of nitric acid totals approximately 60 Mt per year, with a market value of around US$30 billion, of which about 70% is exploited to produce ammonium nitrate (NH4NO3) as a modern agricultural fertilizer.11,13 Moreover, about 13% of nitric acid is used for organic oxidation reactions, which also constitute a vital intermediate for organic nitrations. The remaining nitric acid is consumed for the synthesis of other materials and chemical processes. This signifies the essential roles of large nitric acid production and its utilization in fertilizer industries. Furthermore, the escalating global population and economic activities will continue to increase the demand for nitric acid production in the future. Its excessive use for agricultural purposes and the improper disposal of industrial wastes, however, can lead to health and environmental issues.
Nitrate contamination in drinking water (NO3− > 10 N-mg L−1) mainly results from agricultural and industrial activities and has health impacts, such as causing methemoglobinemia, cancer, and thyroid problems.14–17 In addition, the rising NO3− concentration can disrupt the natural N-cycle by releasing reactive nitrogen species into the environment. Table 1 lists the concentrations of nitrate in various types of contaminated wastewater.16 Concerning public health, the World Health Organization (WHO) recommends maximum contaminant levels of 10, 0.03, and 0.4 N-mg L−1, respectively, for NO3−, NO2−, and NH4+ in drinking water.18
Table 1 Various types of nitrate-polluted wastewater and criteria for drinking water
Type of wastewater |
pH |
N-species |
Nitrate concentration (N-mg L−1) |
Polluted groundwater19 |
Unknown |
NO3−, NO2−, NH4+ |
12–18 |
Textile wastewater20 |
7 |
NO3− |
104 |
Industrial wastewater21 |
7.9 |
NO3−, NH4+ |
582.4 |
Low-level nuclear wastewater22 |
Alkaline |
NO3−, NO2−, Ru(NO(NO2)4(OH))2− |
27 300 |
Drinking water18 |
6.5–8.5 |
NO3−, NO2−, NH4+ |
<10 |
Electrochemical NO3− Reduction (eNO3R) to NH3
Impractical potential
To address nitrate pollution in wastewater and mitigate the natural N-cycle imbalance, a growing number of studies have been reported on the electrochemical NO3− reduction to NH3 (Fig. 1), with strong catalytic performances achieved, including a current density as high as ∼1 A cm−2 and ∼100% faradaic efficiencies.23–25 Some reports have even asserted that electrochemical NO3− reduction to NH3 under ambient conditions utilizing nitrate wastes as feedstock could be an alternative to the conventional Haber–Bosch process.26–29 Although significant progress has been made in the electrochemical conversion of NO3− to NH3 in terms of current densities and faradaic efficiencies, the feasibility of large-scale NH3 production remains highly questionable due to the insufficient concentration and low capacity of nitrates feedstock in real wastewater. Taking the widespread fertilizer ammonium nitrate as an example, about 17% of nitrate ions would leach to the groundwater as nitrate contaminants annually.30 Even if those nitrate contaminants can be successfully converted to NH3 with 100% selectivity using an electrochemical approach, the estimated amount of ammonia produced would only be about 2 Mt year−1. Such a “waste-to-wealth” conversion approach is insignificant compared to the NH3 production accomplished using the conventional Haber–Bosch process, even without considering the energy needs for NO3− collection and reduction, and NH3 separation, purification, and compression, and a significant amount of the NH3 produced would be oxidized for the nitric acid production.
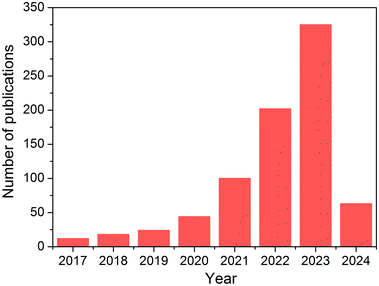 |
| Fig. 1 Number of publications per year on “electrochemical nitrate reduction to ammonia.” Source: Web of Science on Mar. 29, 2024. | |
Unintentional environmental challenges
In another area of research that focuses on adopting environmentally friendly approaches to address nitrate contaminants in wastewater, various technologies such as reverse osmosis, bacterial denitrification, and ion exchange are currently being employed on a commercial scale.31 However, those technologies are expensive and require harsh reaction conditions. In contrast, electrochemical reduction of nitrate to ammonia powered by renewable electricity would seem to be a more sustainable method for treating wastewater than existing commercial technologies,32,33 but, unfortunately, may not be economically viable despite the reported high selectivity and efficiency of NO3−-to-NH3 conversion due to the resulting low concentration of NH3.34 Moreover, any NH3 not completely isolated would itself be a more serious contaminant than NO3− in wastewater.
Conclusion and outlook
In summary, electrochemical NO3− reduction to NH3 may show some scientific merits, but when considering practical and industrial implementations, this process will likely play an insignificant role in either NO3− contaminants removal or NH3 production.35,36 When dealing with NO3− contaminants in real wastewater, NO3− should not be converted to NH3 at any concentration range: at high concentrations, NO3− is a more valuable feedstock (as it has to be produced from NH3), with the production costs and energy consumption of NH3 using the electrochemical NO3− reduction process being 2.04 times higher than those of the Haber–Bosch process (the detailed calculation is provided in Table S1, ESI†);37 at low concentrations, NH3 produced from reducing NO3− becomes a more serious contaminant. For a more feasible and meaningful N-cycle to address nitrate pollution issues, following directions are recommended.
I. NO3− reduction to N2
In wastewater denitrification, instead of focusing on converting NO3− to NH3, directly converting low-concentration nitrate (10–1
000 N-mg L−1) into harmless N2 gas through electrocatalysis powered by renewable electricity would be more practical (Route I, Fig. 2 and eqn (1)).38,39 Alternatively, NO3− can be converted into NH3 first on the cathode side, followed by the oxidation of NH3 at the anode side to produce N2 with the assistance of chloride ions in wastewater (Route II, Fig. 2, and eqn (2)–(5)),40,41 and in this way, risks induced by the potential byproducts of the eNO3R process, such as ClO3−, trichloromethane, bromodichloromethane, or dibromochloromethane, are mitigated or avoided.42,43 Such a route can also be applied for removing NH3/NH4+ from wastewater. | 2NO3− + 12H+ + 10e− → N2 + 6H2O | (1) |
| NO3− + 9H+ + 8e− → NH3 + 3H2O | (2) |
| Cl2 + H2O → 2H+ + ClO− + Cl− | (4) |
| 3ClO− + 2NH4+ → N2 + 2H+ + 3Cl− + 3H2O | (5) |
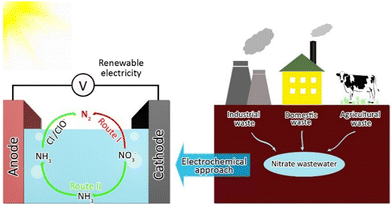 |
| Fig. 2 Schematic diagram of electrochemical reduction of nitrate to nitrogen gas for wastewater denitrification. | |
II. NO3− recovery
In the case of wastewater containing nitrate at high concentrations (above 1
000 N-mg L−1), a more pragmatic approach can be recycling and purifying nitrate salts to produce NO3− chemicals or fertilizers rather than converting them into NH3.44,45
III. Coupling with CO2 reduction for value-added N-fertilizers
Value-added N-fertilizers might be generated or co-produced during the removal of nitrate from wastewater. For instance, urea can be produced by coupling NO3− reduction with CO2 reduction.46,47 An electrochemical approach has been recently reported for recovering NH3/NH4+ from manure wastewater and co-producing NH4+-rich fertilizer.48 These technologies, however, are still in their early stages. Investigations of larger-scale implementation, improvement of energy efficiencies, and economic viability optimization will be needed to create meaningful impacts.
Conflicts of interest
There are no conflicts to declare.
Acknowledgements
This work was financially supported by King Abdullah University of Science and Technology (KAUST).
References
- J. G. Chen, R. M. Crooks, L. C. Seefeldt, K. L. Bren, R. M. Bullock, M. Y. Darensbourg, P. L. Holland, B. Hoffman, M. J. Janik, A. K. Jones, M. G. Kanatzidis, P. King, K. M. Lancaster, S. V. Lymar, P. Pfromm, W. F. Schneider and R. R. Schrock, Science, 2018, 360, eaar6611 CrossRef PubMed.
- C. Smith, A. K. Hill and L. Torrente-Murciano, Energy Environ. Sci., 2020, 13, 331–344 RSC.
- S. Chatterjee, R. K. Parsapur and K.-W. Huang, ACS Energy Lett., 2021, 6, 4390–4394 CrossRef CAS.
- Global Data, Global Ammonia Industry Outlook to 2025 – Capacity and Capital Expenditure Forecasts with Details of All Active and Planned Plants, 2021.
- U.S. Geological Survey, Mineral commodity summaries 2023: U.S. Geological Survey, Reston, VA, 2023, p. 210, DOI:10.3133/mcs2023.
-
G. Schnitkey, Fertilizer prices higher for 2019 crop, farmdoc daily, Department of Agricultural and Consumer Economics, UIUC, 2018. https://farmdocdaily.illinois.edu/2018/09/fertilizerprices-higher-for-2019-crop.html.
-
J. Nørskov and J. Chen, Sustainable Ammonia Synthesis, U.S. Department of Energy, Dulles, VA, 2016 Search PubMed.
- F. Jiao and B. Xu, Adv. Mater., 2019, 31, e1805173 CrossRef PubMed.
- D. Erdemir and I. Dincer, Int. J. Energy Res., 2020, 45, 4827–4834 CrossRef.
- International Energy Agency (IEA), Ammonia Technology Roadmap, IEA, Paris, 2021 Search PubMed.
- ChemAnalyst, Nitric Acid Market Analysis, 2023, https://www.chemanalyst.com/industry-report/nitric-acid-market-615 Search PubMed.
- C. A. Grande, K. A. Andreassen, J. H. Cavka, D. Waller, O.-A. Lorentsen, H. Øien, H.-J. Zander, S. Poulston, S. García and D. Modeshia, Ind. Eng. Chem. Res., 2018, 57, 10180–10186 CrossRef CAS.
-
M. C. E. Groves, “Nitric Acid,” in Kirk-Othmer Encyclopedia of Chemical Technology, John Wiley & Sons, 5th edn, 2020, https://doi.org/10.1002/0471238961.1409201803120118.a01.pub3 Search PubMed.
- Q. Hu, Y. Qin, X. Wang, Z. Wang, X. Huang, H. Zheng, K. Gao, H. Yang, P. Zhang, M. Shao and C. He, Energy Environ. Sci., 2021, 14, 4989–4997 RSC.
- D. Chen, S. Zhang, D. Yin, W. Li, X. Bu, Q. Quan, Z. Lai, W. Wang, Y. Meng, C. Liu, S. Yip, F. R. Chen, C. Zhi and J. C. Ho, Adv. Energy Mater., 2022, 13, 2203201 CrossRef.
- P. H. van Langevelde, I. Katsounaros and M. T. M. Koper, Joule, 2021, 5, 290–294 CrossRef.
-
S. Shukla and A. Saxena, Handbook of Environmental Materials Management, Springer, 2018, pp. 1-21, https://doi.org/10.1007/978-3-319-58538-3_20-1 Search PubMed.
- WHO, Guidelines for drinking-water quality: incorporating the first and second addenda, 4th edn, 2022 Search PubMed.
- E. Abascal, L. Gomez-Coma, I. Ortiz and A. Ortiz, Sci. Total Environ., 2022, 810, 152233 CrossRef CAS PubMed.
- L. Su, K. Li, H. Zhang, M. Fan, D. Ying, T. Sun, Y. Wang and J. Jia, Water Res., 2017, 120, 1–11 CrossRef CAS PubMed.
- R. Chauhan and V. C. Srivastava, Chem. Eng. J., 2020, 386, 122065 CrossRef CAS.
- I. Katsounaros, M. Dortsiou and G. Kyriacou, J. Hazard. Mater., 2009, 171, 323–327 CrossRef CAS PubMed.
- L. Mi, Q. Huo, J. Cao, X. Chen, H. Yang, Q. Hu and C. He, Adv. Energy Mater., 2022, 12, 2202247 CrossRef CAS.
- S. Li, D. Han, G. Jiang, Z. Han, H. Lu, J. Gao, X. Wang, Y. Wang, C. Geng, Z. Weng and Q.-H. Yang, ACS Appl. Energy Mater., 2023, 6, 5067–5073 CrossRef CAS.
- Z. Xu, L. Wan, Y. Liao, M. Pang, Q. Xu, P. Wang and B. Wang, Nat. Commun., 2023, 14, 1619 CrossRef CAS PubMed.
- F. Lv, M. Sun, Y. Hu, J. Xu, W. Huang, N. Han, B. Huang and Y. Li, Energy Environ. Sci., 2023, 16, 201–209 RSC.
- N. Zhou, Z. Wang, N. Zhang, D. Bao, H. Zhong and X. Zhang, ACS Catal., 2023, 13, 7529–7537 CrossRef CAS.
- X. Li, X. He, J. Yao, K. Dong, L. Hu, J. Chen, L. Zhang, X. Fan, Z. Cai, S. Sun, D. Zheng, M. S. Hamdy, Q. Liu, Y. Luo, Y. Liao and X. Sun, ChemSusChem, 2023, e202300505 CrossRef CAS PubMed.
- J. Li, H. Liu, F. Du, L. Liu, Y. Gu, C. Li, C. Guo and H. Wang, Chem. Eng. J., 2023, 471, 144488 CrossRef CAS.
- K. Guillard and K. L. Kopp, J. Environ. Qual., 2004, 33, 1822–1827 CrossRef CAS PubMed.
- M. Duca and M. T. M. Koper, Energy Environ. Sci., 2012, 5, 9726 RSC.
- Y. Liu, M. Chen, X. Zhao, H. Zhang, Y. Zhao and Y. Zhou, Chem. Eng. J., 2023, 475, 146176 CrossRef CAS.
- Y. Wang, W. Zhou, R. Jia, Y. Yu and B. Zhang, Angew. Chem., Int. Ed., 2020, 59, 5350–5354 CrossRef CAS PubMed.
-
Nat. Catal., 2022, 5, 1071–1072 Search PubMed.
- S. Garcia-Segura, M. Lanzarini-Lopes, K. Hristovski and P. Westerhoff, Appl. Catal., B, 2018, 236, 546–568 CrossRef CAS.
- Z. Wu, Y. Song, Y. Liu, W. Luo, W. Li and J. Yang, Chem. Catal., 2023, 3, 100786 CrossRef CAS.
- H. Jiang, G. F. Chen, O. Savateev, J. Xue, L. X. Ding, Z. Liang, M. Antonietti and H. Wang, Angew. Chem., Int. Ed., 2023, 62, e202218717 CrossRef CAS PubMed.
- H. Zhang, C. Wang, H. Luo, J. Chen, M. Kuang and J. Yang, Angew. Chem., Int. Ed., 2023, 62, e202217071 CrossRef CAS PubMed.
- J. Lim, Y. Chen, D. A. Cullen, S. W. Lee, T. P. Senftle and M. C. Hatzell, ACS Catal., 2022, 13, 87–98 CrossRef.
- H. Luo, S. Li, Z. Wu, Y. Liu, W. Luo, W. Li, D. Zhang, J. Chen and J. Yang, Adv. Mater., 2023, e2304695 CrossRef PubMed.
- X. Zhao, K. Zhao, X. Quan, S. Chen, H. Yu, Z. Zhang, J. Niu and S. Zhang, Chem. Eng. J., 2021, 415, 128958 CrossRef CAS.
- L. Su, D. Han, G. Zhu, H. Xu, W. Luo, L. Wang, W. Jiang, A. Dong and J. Yang, Nano Lett., 2019, 19, 5423–5430 CrossRef CAS PubMed.
- F. Zhang, J. Luo, J. Chen, H. Luo, M. Jiang, C. Yang, H. Zhang, J. Chen, A. Dong and J. Yang, Angew. Chem., Int. Ed., 2023, 62, e202310383 CrossRef CAS PubMed.
- J. Kim, M.-J. Hwang, S.-J. Lee, W. Noh, J. M. Kwon, J. S. Choi and C.-M. Kang, Bioresour. Technol., 2016, 205, 269–273 CrossRef CAS PubMed.
- R. Mohammadi, D. L. Ramasamy and M. Sillanpää, Desalination, 2021, 498, 114726 CrossRef CAS.
- Y. Luo, K. Xie, P. Ou, C. Lavallais, T. Peng, Z. Chen, Z. Zhang, N. Wang, X.-Y. Li, I. Grigioni, B. Liu, D. Sinton, J. B. Dunn and E. H. Sargent, Nat. Catal., 2023, 6, 939–948 CrossRef CAS.
- C. Lv, L. Zhong, H. Liu, Z. Fang, C. Yan, M. Chen, Y. Kong, C. Lee, D. Liu, S. Li, J. Liu, L. Song, G. Chen, Q. Yan and G. Yu, Nat. Sustainability, 2021, 4, 868–876 CrossRef.
- R. Wang, K. Yang, C. Wong, H. Aguirre-Villegas, R. Larson, F. Brushett, M. Qin and S. Jin, Nat. Sustainability, 2024 DOI:10.1038/s41893-023-01252-z.
|
This journal is © The Royal Society of Chemistry 2024 |
Click here to see how this site uses Cookies. View our privacy policy here.