Force-controlled robotic mechanochemical synthesis†
Received
28th June 2024
, Accepted 9th September 2024
First published on 16th September 2024
Abstract
We demonstrate a novel mechanochemical synthesis method using a robotic powder grinding system that applies a precisely controlled and constant mechanical force. This approach significantly enhances reproducibility and enables detailed analysis of reaction pathways. Our results indicate that robotic force control can alter the reaction rate and influence the reaction pathway, highlighting its potential for elucidating chemical reaction mechanisms and fostering the discovery of new chemical reactions. Despite its significance, the application of a controllable constant force in macroscale mechanochemical synthesis remains challenging. To address this gap, we compared the reproducibilities of various mechanochemical syntheses using conventional manual grinding, ball milling, and our novel robotic approach with perovskite materials. Our findings indicate that the robotic approach provides significantly higher reproducibility than conventional methods, facilitating the analysis of reaction pathways. By manipulating the grinding force and speed, we revealed that robotic force control can alter both the reaction rate and pathway. Consequently, robotic mechanochemical synthesis has significant potential for advancing the understanding of chemical reaction mechanisms and discovering new reactions.
1 Introduction
Mechanochemistry or mechanochemical synthesis, involves chemical reactions activated by mechanical energy.1,2 This process is promising for synthesizing functional materials, such as energy-related materials3–5 and metal–organic frameworks (MOFs),6,7 and is considered a green chemical reaction due to its solvent-free and low-energy requirements.8 Moreover, to enhance the understanding of these reactions, there is a need for more reproducible and controllable approaches to synthesis.9
Traditional mechanochemistry typically involves tools like manual mortars and pestles or ball mills in batch processes, and screw extruders for continuous flow production.10,11 However, these methods often face challenges in reproducibility and scalability. For research scale processes, manual grinding is labor-intensive and variable, and ball mills suffer from limitations like nonuniform reagent distribution. Manual grinding is labor- and time-intensive, and the results vary depending on the operator, causing reproducibility problems. Similarly, ball mills have limitations, such as the size and weight of the balls and the nonuniform distribution of reagents in the jar, and these limitations also cause reproducibility issues. Despite the recognized importance of the mechanical factors in mechanochemical synthesis,12,13 synthesis under precisely controlled mechanical force still needs to be examined.
To address these issues, we propose a force-controlled mechanochemical synthesis approach, depicted in Fig. 1, using a robotic powder grinding system with a mortar and pestle.14,15 This method enables precise control over grinding force and speed, allowing for a better understanding of mechanochemical reactions under varying mechanical conditions. In this method, a soft gel jig is used and aids in the mechanochemical reaction by applying a constant force between the mortar and the pestle. Furthermore, this method enables precise control over the grinding force and speed, and the mechanochemical reaction can be clarified under varying mechanical experimental conditions.
 |
| Fig. 1 Diagram adjusting reaction pathways via varying force and speed during grinding. | |
In this study, the effectiveness of our proposed robotic mechanochemical synthesis system is demonstrated through three experiments with perovskite as the target material. In the first experiment, the reproducibilities of the mechanochemical reactions using manual grinding, ball milling, and robotic grinding are compared, with emphasis on the importance of force control in the mechanochemical synthesis. In the second experiment, the parameters of force were found to significantly influence the mechanochemical reactions. In the third experiment, the grinding speed was shown to have a substantial impact on mechanochemical reactions.
In summary, our contributions are as follows:
(1) We compared the reproducibilities of manual grinding, ball milling, and robotic force-controlled mechanochemical syntheses. The robotic mechanochemical synthesis exhibited the least variability; thus, the controlled force application enables more reproducible experiments in mechanochemical synthesis.
(2) We also investigated the reaction path by controlling the grinding force and speed. Our results revealed that the grinding force affected the reaction pathway; additionally, the reaction pathway also differed with respect to the grind speed even when the grinding force was the same. This finding indicated the possibility of controlling reaction pathways in mechanochemical reactions through the grinding force and speed.
The remainder of this paper is organized as follows. Section 2 introduces the related works. Section 3 describes the robotic mechanochemical synthesis system. Section 4 provides the experimental results. Section 5 discusses the results from this study. Finally, Section 6 provides a summary this study and indicates future research directions.
2 Related works
We discuss various mechanochemistry methods, examine the process parameters and analyze mechanochemical reactions as outlined in relevant literature.
2.1 Mechanochemistry methods
In initial studies, mechanochemical synthesis was conducted using a mortar and pestle.16 However, this method is inefficient due to limitations in the applied power, labor-intensive nature, and low reproducibility.17 To compensate for the power limitations, some studies have been where ultrasonic treatment18 or annealing19 were used as post-treatment after grinding with a mortar and pestle. Subsequently, ball mills, which can efficiently advance reactions with high energy, became commonly used.20 However, one of the challenges associated with ball milling is the difficulty of effectively stirring the powder. To overcome this issue, highly fluidic catalysts have been developed.21 Notably, not all research has shifted to using ball mills; even in relatively recent studies, mortar and pestles are used when the reaction efficiency is not critical and when uniform mixing with small amounts of reagents is needed.22,23 In our proposed robotic mechanochemical synthesis system, in addition to grinding with a mortar and pestle, mixing with a spatula is performed to ensure uniform progression of the reaction. Furthermore, the ability to consistently apply force enables higher reproducibility compared to ball mills.
2.2 Mechanochemical process parameters
Investigating the relationship between process parameters and mechanochemical reactions is important for reaction control. In the past, research on the reaction predictions using modeling based on the input energy was performed.24,25 Furthermore, studies showed that both reaction rates and crystal polymorphism could be controlled by changing the input energy or force.12,26 Studies were also performed from a mechanical perspective, considering factors such as the compression stress and shear stress; however, most of these studies were on a microscale.27,28 Studies have examined the impact of the compression stress on a macroscopic scale using specialized synthesis equipment.29 Since conventional ball mills cause a wide variation in compressive and shear stresses,30 it is likely that the consideration of compressive stress and shear stress is insufficient. Our proposed robotic mechanochemical synthesis method enables the investigation with commercially available mortars and pestles under consistent force conditions on a macroscale, enabling comparisons of the reproducibility with past studies. Furthermore we can examine the effects under various process conditions by varying force and speed. Thus, our proposed method is suitable for quantitatively examining the impact of synthesis conditions on mechanochemical reactions.
2.3 Mechanochemical reaction mechanism
To elucidate the mechanisms of mechanochemical reactions, direct reaction analysis are investigated from various perspectives. Monitoring the grinding progress of reactions in real time are possible.17,31–33 In particular, the X-ray diffraction (XRD) and Raman spectroscopy were used for in situ analysis in the ball milling.34,35 Additionally, some research also involves the analysis of reaction kinetics in mechanochemical reactions.36,37 Commonly employed shake mills are inadequate due to their substantial heat generation when mechanical impacts are assessed. For this reason, rotational mills have also been used for investigations;13 however, they require a large amount of sample material, posing limitations for conducting numerous trials. Compared to these methods, our proposed method using a mortar and pestle provides the advantages of reduces heat generation to focus on mechanical factors analysis and enable experiments with a small amount of sample material. Therefore, a robotic mechanochemical synthesis system with mortar and pestle is suitable for analyzing reaction mechanisms on a laboratory scale.
3 Robotic mechanochemical synthesis system
This section details the setup of the robotic mechanochemical synthesis system, including the platform specifications, motion planning strategies, and force control mechanisms.
3.1 Platform
The robotic mechanochemical synthesis system (Fig. 2) consisted of a Universal Robots UR5e robotic arm, a soft jig, a pestle, and a small silicone spatula. We designed a soft jig to convert the displacement into a force to enable smooth grinding with a constant force. A pestle was used for grinding, and a spatula was used for gathering the powder. Additionally, by attaching bearings to the spatula, the powder was efficiently collected by allowing the spatula to follow along the walls of the mortar. A commercial mortar with a horizontal diameter of 80 mm and a depth of 32 mm (AS ONE, deep-type agate mortar, and pestle) and the robotic arm were attached to an aluminum frame. The robot was connected to a desktop PC running ROS Noetic on Ubuntu 20.04. The computer used to control robot is equipped with a Ryzen 9 7900 CPU and 64 GB of memory. The soft jig, shown in the upper right of Fig. 2, was made from cut gel cubes (SUTLLA10-100-100 and UTSLL10-100-100, MISUMI) measuring 1.5 cm × 1.5 cm × 1 cm and 3D-printed parts made of acrylonitrile-butadiene-styrene (ABS). These jigs were previously developed to absorb the grinding impacts between the mortar and pestle.
 |
| Fig. 2 The robotic mechanochemical synthesis setup was used to perform the experiments. The robotic arm and mortar were fixed on the aluminum frame. The robot had a pestle and spatula attached via a soft jig which consists of gel cubes and 3D-printed parts. | |
3.2 Motion planning
In our research, we employed a circular motion for the grinding motion with the mortar and pestle; this motion has been shown to be an effective grinding technique in a prior study.14 The diameter of the circular motion during grinding was set to 16 mm; this approximately matched the size of the pestle tip. Additionally, a spiral motion was utilized for the powder gathering process with the spatula. The spatula was rotated by the bearing to contact the mortar wall, facilitating a simple yet effective spiral motion. The depth of these motions was determined based on the ellipsoidal model of the inner surface of the mortar, with the axis length of the ellipsoid set to 36 mm, corresponding to the depth of the mortar. The 6D poses of the designed motions were computed and converted into joint trajectories using TrackIK. The robot's operation was governed by these joint trajectories, which were controlled by a joint trajectory controller within the Robot Operating System (ROS) environment. The grinding speed was adjusted by controlling the joint movement velocity between the waypoints. We alternated between 20 rotations of grinding motion and 1 cycle of powder gathering motion; this process effectively advanced the grinding process in each experiment. The mortar needed to be securely fixed to the aluminum frame using a jig, and the center coordinates needed to be adjusted beforehand to minimize positional errors at the arm's tip during grinding.
3.3 Force control with soft jig
In this research, we propose a force control method with a soft jig. We applied the approximate spring properties of the soft gel in the soft jig. The spring constant was estimated with the force and pestle tip values. The force measurements were obtained via a force–torque sensor mounted on the flange of a UR5e robotic arm. The position of the pestle tip was determined using MoveIt within the ROS framework. Experiments were conducted by bringing the pestle tip into contact with a flat plane on the table. Fig. 3 shows the corresponding reaction force of the soft jig with a SUTLLA type gel as a function of the displacement of the pestle. Although the results exhibited hysteresis characteristics, a clear linear relationship was observed for both the forward path and the backward path. When this relationship was subjected to linear regression of the forward path, the spring constant was determined to be 20
957.7 N m−1. Another type of gel, USUTLLA also exhibited a clear linear relationship (Fig. S1†). We attained a controllable constant force using accurate control of the position of the pestle by a robotic arm. We investigated the mechanochemical reactions while the precisely controlled applied forces were varied using a robotic mechanochemical synthesis system.
 |
| Fig. 3 Graph illustrating the displacement of pose Z and the sensed force data. A linear relationship is observed between the displacement force magnitude. | |
4 Results
Our primary objective was to verify that the proposed system was more reproducible than conventional methods in mechanochemical synthesis. After confirming the reproducibility of the results, we conducted experiments to analyze the kinetics of the mechanochemical reactions under various force and speed conditions.
4.1 Setup
We used the robotic mechanochemical synthesis system described in Section 3.1. In each trial, we ground 774.0 mg of CsBr (Wako, 99.9%) and 1323.0 mg of PbBr2 (Strem Chemicals, 98%) to obtain a stoichiometric 1
:
1 molar ratio. In addition, we confirmed the existence of the following phases—CsBr and PbBr2 as reactants and CsPbBr3 and Cs4PbBr6 as products—from the Rietveld analysis of the obtained XRD patterns. The assumed reaction phases were established based on previous literature. This study implicated unidirectional reactions of the four types of substances.13
CsPbBr3 + 3CsBr → Cs4PbBr6 |
Cs4PbBr6 + 3PbBr2 → 4CsPbBr3 |
For the initial experiment, ball milling was performed using a Mixer Mill (Retsch, MM400) at 30 Hz for 5 minutes. The grinding process with a mortar and pestle was performed manually and robotically for 30 minutes each. All experiments were conducted using the reagents that were taken directly from the container to approximate commonly used experimental conditions. To ensure accuracy and consistency, each experiment was repeated three times.
In the second experiment, the effect of the forces applied during grinding on the reaction was investigated. However, as the force increased, the deformation of the gel also increased; this potentially caused a deviation in the trajectory of the pestle tip. Based on preliminary experiments, the force range for this study was set to 10 and 20 N.
In the third experiment, the influence of the grinding speed on the reaction was examined. Since the robot could have challenges operating along the designed trajectory if the speed was too slow or too fast, preliminary investigations were conducted to determine the feasible grinding speeds. Consequently, the experiments were carried out at 120 rpm and 60 rpm.
In the second and third experiments, we measured the post-reaction samples using XRD for the reaction rate and path analysis. In mechanochemical reactions, a spontaneous reaction progression known as “aging” is well-documented.7,38 Therefore, measurements were conducted immediately after grinding to minimize the impact of grinding on the results. Due to its large particle size, the CsBr reagent was ground and determined to be less than 100 μm in size. This prereduction in size was performed to ensure that the energy was not consumed in the grinding process itself, enabling an accurate assessment of the impact of grinding force and speed on the mechanochemical reaction rate and pathway. PbBr2 was used directly without pre grinding since its median particle size distribution of approximately 30 μm was sufficiently small.
For all experiments, the sample preparation, the setup of the XRD instrument and the measurements were manually performed. On the other hand, the data analysis was conducted automatically by BBO-Rietveld analysis39 to determine the weight fractions of the phases. The analysis was conducted using a Ryzen Threadripper 2990WX CPU with 128 GB of memory, and the processing time for each sample was approximately 20 minutes.
4.2 Results
In the initial experiment, we conducted mechanochemical synthesis three times using manual grinding, ball milling, and robotic grinding, respectively, to compare reproducibility and efficiency across these methods. We used automated Rietveld analysis to estimate the mean and standard deviation of the weight fractions.
Fig. 4 provides the means and standard deviations of the weight fractions for the four components with error bars. Our results showed that robotic grinding yielded significantly lower standard deviations for the four components compared to other methods, particularly for Cs-rich components. This indicates higher reproducibility in robotic mechanochemical synthesis.
 |
| Fig. 4 Graph illustrating the weight fractions of the mechanochemical synthesis for each method. | |
We successfully achieved high reproducibility in the robotic mechanochemical synthesis. Subsequent experiments investigated the effects of varying grinding force and speed on reaction kinetics using robotic grinding. Fig. 5 shows the weight fractions obtained from the Rietveld analysis of each reaction phase. In the second experiment, we compared the left and center panels of Fig. 5 to investigate the impact of the grinding force. The results indicated that a higher grinding force led to the formation of a larger amount of Cs4PbBr6 compared to that of CsPbBr3. Notably, at a grinding force of 20 N, CsBr was depleted in the latter stages, resulting in the consumption of Cs4PbBr6 and the generation of CsPbBr3.
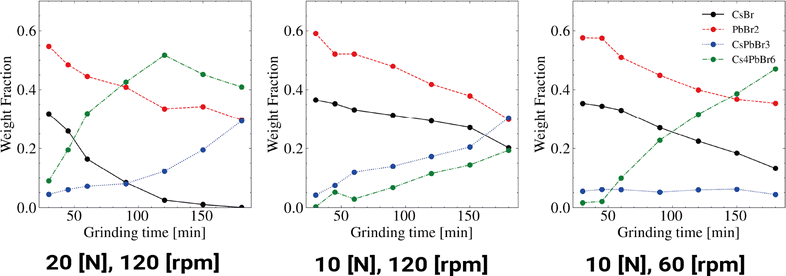 |
| Fig. 5 Graph illustrating the weight fractions of the mechanochemical reactions under each grinding force and speed condition. | |
In the third experiment, we compared the center and right panels of Fig. 5 to examine the influence of the grinding speed. These results demonstrated that a higher grinding speed resulted in the formation of a larger amount of CsPbBr3 compared to that of Cs4PbBr6.
These findings highlight the potential for controlling reaction pathways through precise adjustments in force and speed.
5 Discussion
Compared to conventional methods, our robotic mechanochemical synthesis with a precise constant force control results in higher reproducibility and enables the investigation of reaction rate constants due to force variations.
The initial experimental results demonstrated significantly better reproducibility in robotic mechanochemical synthesis, especially for compounds requiring precise force control. We find notable differences in the Cs-rich components. These differences likely stem from the robust bonding of CsBr, which requires frequent mixing to induce mechanochemical reactions. Manual frequent mixing and uniform grinding is labor-intensive, and ball milling applies force primarily in the direction of the compression, resulting in insufficient agitation. In contrast, our robotic mechanochemical synthesis system provides frequent mixing and uniform grinding, ensuring a consistent chemical environment. As a result, the mechanochemical reactions are able to uniformly proceed under these conditions.
The second and third experiments highlight differences in reaction pathways caused by variations in grinding force and speed. Higher force influences the formation of Cs4PbBr6, while higher speed affects the formation of CsPbBr3. These results suggest the possibility of dynamically controlling reaction pathways in mechanochemical synthesis through precise controls in force and speed, likely relating to compressive and shear stresses.
While the emphasis thus far has been on the outcomes of this research, there are four limitations to this study. The first limitation is scalability. The proposed method applies uniform force using a mortar and pestle, which is effective on a laboratory scale but poses challenges when scaling up to an industrial level. It has been noted in the literature40 that as the amount of reagents increases, it becomes more difficult to apply uniform force. Therefore, a method that seamlessly bridges laboratory-scale processes to industrial-scale applications is required. The second limitation pertains to the complexity of implementation. Although the code and tools for this method are made publicly available, the implementation cost is higher compared to traditional methods. However, by employing a robot arm, the system's flexibility is enhanced, allowing for the application of mechanochemical synthesis to high-throughput experiments previously conducted with solid-phase or liquid-based methods. Since there is a trade-off between system flexibility and implementation complexity,41 it is important to choose the appropriate method based on the specific objectives. The third limitation relates to environmental impact and energy efficiency. Mechanochemical synthesis is recognized for its advantages in energy efficiency and low environmental impact.9 However, it is necessary to further discuss whether the use of robotic methods provides additional benefits in reducing environmental impact and improving energy efficiency compared to traditional methods. The fourth limitation concerns the types of materials that can be applied. While this study demonstrated the application of the method to perovskite materials, there are various materials that can be synthesized using a mortar and pestle. Future work will aim to expand the application to other materials.
6 Conclusion
We developed a robotic mechanochemical synthesis method with precise force control, achieving highly reproducible and controllable mechanochemical reactions. This method offers significant improvements over traditional techniques in terms of consistency and reaction pathway control. We applied a robotic powder grinding system to mechanochemistry to achieve a mechanochemical reaction under constant force. We further confirmed that precise force control during mechanochemical synthesis is critical for achieving reproducibility and reaction control.
Our contributions include:
(1) Demonstrating the application of a robotic powder grinding system for mechanochemical synthesis, achieving highly consistent results compared to manual grinding and ball milling.
(2) Investigating the reaction progress under varying grinding forces and speeds, showing significant changes in reaction pathways and the potential for dynamic control of mechanochemical reactions.
In this study, we investigated the mechanochemical reaction mechanism for a specific alkali halide lead perovskite system. In our future work, to further understand this mechanism, we plan to verify these findings with a broader range of materials such as organic molecules and mechanical conditions such as the effect of the force direction. The force-controlled robotic mechanochemical synthesis approach enables the attainment of a more comprehensive understanding of mechanochemical synthesis.
Data availability
The data and code supporting the findings of this study are openly available. The robotic powder grinding code is accessible at GitHub via [https://github.com/quantumbeam/powder_grinding], and the BBO-Rietveld analysis code is also available at GitHub via [https://github.com/quantumbeam/BBO-Rietveld]. We have uploaded all the data and code used in this study at GitHub, which can be accessed via the following link: https://github.com/quantumbeam/Force-Controlled-Robotic-Mechanochemical-Synthesis. All repositories include detailed documentation and usage instructions to ensure reproducibility of the results. All information related to the robotic mechanochemical synthesis is included in the aforementioned repositories and the ESI† provided with this article. The ESI† contains detailed descriptions of experimental procedures, additional figures, and tables supporting the main text. The supplementary materials and additional data can be accessed through the Digital Discovery journal's online platform. By providing access to these datasets and code repositories, we aim to maintain high standards of transparency, research reproducibility, and to promote the reuse of our findings.
Author contributions
K. O. conceptualized the project. Y. N. led the design, construction, and experimental work of the robotic mechanochemical synthesis system. K. K. contributed to the mechanochemical synthesis experiments and Y. T. contributed to the interpretation of the results. M. H. and Y. U. contributed to the design of the robotic system. All authors contributed to the writing of the manuscript.
Conflicts of interest
To the best of our knowledge, the named authors have no conflict of interest, financial or otherwise.
Acknowledgements
This work was partly supported by the JST-Mirai Program (Grant Number JPMJMI21G2), the JST Moonshot R&D (Grant Number JPMJMS2236), and the MEXT Program—Data Creation and Utilization-Type Material Research and Development Project (Digital Transformation Initiative Center for Magnetic Materials), Grant Number JPMXP1122715503.
Notes and references
- J.-L. Do and T. Friščić, ACS Cent. Sci., 2017, 3, 13–19 CrossRef CAS PubMed.
- T. Friščić, C. Mottillo and H. M. Titi, Angew. Chem., 2020, 132, 1030–1041 CrossRef.
- F. Palazon, Y. El Ajjouri and H. J. Bolink, Adv. Energy Mater., 2020, 10, 1902499 CrossRef CAS.
- R. Schlem, C. F. Burmeister, P. Michalowski, S. Ohno, G. F. Dewald, A. Kwade and W. G. Zeier, Adv. Energy Mater., 2021, 11, 2101022 CrossRef CAS.
- X. Liu, Y. Li, L. Zeng, X. Li, N. Chen, S. Bai, H. He, Q. Wang and C. Zhang, Adv. Mater., 2022, 34, 2108327 CrossRef CAS PubMed.
- M. Klimakow, P. Klobes, A. F. Thünemann, K. Rademann and F. Emmerling, Chem. Mater., 2010, 22, 5216–5221 CrossRef CAS.
- M. J. Cliffe, C. Mottillo, R. S. Stein, D.-K. Bučar and T. Friščić, Chem. Sci., 2012, 3, 2495–2500 RSC.
- S. Głowniak, B. Szczęśniak, J. Choma and M. Jaroniec, Mater. Today, 2021, 46, 109–124 CrossRef.
- S. L. James, C. J. Adams, C. Bolm, D. Braga, P. Collier, T. Friščić, F. Grepioni, K. D. M. Harris, G. Hyett, W. Jones, A. Krebs, J. Mack, L. Maini, A. G. Orpen, I. P. Parkin, W. C. Shearouse, J. W. Steed and D. C. Waddell, Chem. Soc. Rev., 2012, 41, 413–447 RSC.
- B. Szczęśniak, S. Borysiuk, J. Choma and M. Jaroniec, Mater. Horiz., 2020, 7, 1457–1473 RSC.
- M. Leonardi, M. Villacampa and J. C. Menéndez, Chem. Sci., 2018, 9, 2042–2064 RSC.
- L. S. Germann, M. Arhangelskis, M. Etter, R. E. Dinnebier and T. Friščić, Chem. Sci., 2020, 11, 10092–10100 RSC.
- K.-Y. Baek, W. Lee, J. Lee, J. Kim, H. Ahn, J. I. Kim, J. Kim, H. Lim, J. Shin, Y.-J. Ko, H.-D. Lee, R. H. Friend, T.-W. Lee, J. Lee, K. Kang and T. Lee, Nat. Commun., 2022, 13, 4263 CrossRef CAS PubMed.
-
Y. Nakajima, M. Hamaya, Y. Suzuki, T. Hawai, F. von Drigalski, K. Tanaka, Y. Ushiku and K. Ono, 2022 IEEE/RSJ International Conference on Intelligent Robots and Systems (IROS), 2022, pp. 2320–2326 Search PubMed.
-
Y. Nakajima, M. Hamaya, K. Tanaka, T. Hawai, F. von Drigalski, Y. Takeichi, Y. Ushiku and K. Ono, 2023 IEEE/RSJ International Conference on Intelligent Robots and Systems (IROS), 2023, pp. 8283–8290 Search PubMed.
- T. R. Musgrave and C. E. Mattson, Inorg. Chem., 1968, 7, 1433–1436 CrossRef CAS.
- D. Tan and F. García, Chem. Soc. Rev., 2019, 48, 2274–2292 RSC.
- V. A. Hintermayr, A. F. Richter, F. Ehrat, M. Döblinger, W. Vanderlinden, J. A. Sichert, Y. Tong, L. Polavarapu, J. Feldmann and A. S. Urban, Adv. Mater., 2016, 28, 9478–9485 CrossRef CAS PubMed.
- C. C. Stoumpos, C. D. Malliakas and M. G. Kanatzidis, Inorg. Chem., 2013, 52, 9019–9038 CrossRef CAS PubMed.
- D. Prochowicz, M. Franckevičius, A. M. Cieślak, S. M. Zakeeruddin, M. Grätzel and J. Lewiński, J. Mater. Chem. A, 2015, 3, 20772–20777 RSC.
- T. Seo, K. Kubota and H. Ito, J. Am. Chem. Soc., 2023, 145, 6823–6837 CrossRef CAS PubMed.
- D. Chen, J. Li, X. Chen, J. Chen and J. Zhong, ACS Appl. Mater. Interfaces, 2019, 11, 10059–10067 CrossRef CAS PubMed.
- P. Pal, S. Saha, A. Banik, A. Sarkar and K. Biswas, Chem.–Eur. J., 2018, 24, 1811–1815 CrossRef CAS PubMed.
- E. Gil-González, M. d. R. Rodríguez-Laguna, P. E. Sánchez-Jiménez, A. Perejón and L. A. Pérez-Maqueda, J. Alloys Compd., 2021, 866, 158925 CrossRef.
- E. Gil-González, L. A. Pérez-Maqueda, P. E. Sánchez-Jiménez and A. Perejón, J. Phys. Chem. Lett., 2021, 12, 5540–5546 CrossRef PubMed.
- K. Linberg, P. Szymoniak, A. Schönhals, F. Emmerling and A. A. L. Michalchuk, Chem.–Eur. J., 2023, 29, e202302150 CrossRef CAS PubMed.
- Y. S. Zholdassov, L. Yuan, S. R. Garcia, R. W. Kwok, A. Boscoboinik, D. J. Valles, M. Marianski, A. Martini, R. W. Carpick and A. B. Braunschweig, Science, 2023, 380, 1053–1058 CrossRef CAS PubMed.
- F. H. Bhuiyan, Y.-S. Li, S. H. Kim and A. Martini, Sci. Rep., 2024, 14, 2992 CrossRef CAS PubMed.
- E. Nwoye, S. Raghuraman, M. Costales, J. Batteas and J. R. Felts, Phys. Chem. Chem. Phys., 2023, 25, 29088–29097 RSC.
- V. V. Boldyrev and K. Tkáčová, J. Mater. Synth. Process., 2000, 8, 121–132 CrossRef CAS.
- P. A. Julien and T. Friščić, Cryst. Growth Des., 2022, 22, 5726–5754 CrossRef CAS.
- A. A. L. Michalchuk and F. Emmerling, Angew. Chem., Int. Ed., 2022, 61, e202117270 CrossRef CAS PubMed.
- S. Lukin, L. S. Germann, T. Friščić and I. Halasz, Acc. Chem. Res., 2022, 55, 1262–1277 CrossRef CAS PubMed.
- P. F. M. de Oliveira, A. A. L. Michalchuk, A. G. Buzanich, R. Bienert, R. M. Torresi, P. H. C. Camargo and F. Emmerling, Chem. Commun., 2020, 56, 10329–10332 RSC.
- G. I. Lampronti, A. A. L. Michalchuk, P. P. Mazzeo, A. M. Belenguer, J. K. M. Sanders, A. Bacchi and F. Emmerling, Nat. Commun., 2021, 12, 6134 CrossRef CAS PubMed.
- M. Alrbaihat, F. Khalil Al-Zeidaneen and Q. Abu-Afifeh, Mater. Today: Proc., 2022, 65, 3651–3656 CAS.
- E. Colacino, M. Carta, G. Pia, A. Porcheddu, P. C. Ricci and F. Delogu, ACS Omega, 2018, 3, 9196–9209 CrossRef CAS PubMed.
- S. Li, I. Huskić, N. Novendra, H. M. Titi, A. Navrotsky and T. Friščić, ACS Omega, 2019, 4, 5486–5495 CrossRef CAS PubMed.
- Y. Ozaki, Y. Suzuki, T. Hawai, K. Saito, M. Onishi and K. Ono, npj Comput. Mater., 2020, 6, 1–7 CrossRef.
-
P. Balaz, Mechanochemistry in Nanoscience and Minerals Engineering, Springer, Berlin, Germany, 2008 Search PubMed.
- G. A. Bowmaker, Chem. Commun., 2013, 49, 334–348 RSC.
|
This journal is © The Royal Society of Chemistry 2024 |
Click here to see how this site uses Cookies. View our privacy policy here.