Mechanosynthesis of urea–hydroxybenzoic acid cocrystals as sustained-release nitrogen fertilizer†
Received
16th January 2023
, Accepted 14th June 2023
First published on 16th June 2023
Abstract
Nitrogen is a key nutrient source in agriculture, which has a crucial impact on crop productivity. Out of available nitrogen fertilizers, urea is identified as the major nitrogen source, accounting for ∼60% of global use. However, due to the low nutrient usage efficiency of urea, it has become unsustainable, as 50–70% nitrogen applied is lost due to leaching, volatilization and nitrification, causing a series of environmental hazards and economic losses. Moreover, the recent global pandemic as well as war disrupt the food supply chain and fertilizer market. Here we used mechanochemistry to prepare a series of novel urea cocrystals that showed sustained-release behavior with significant improvement (∼4 times), lower volatilization, and improved hydration stability compared to commercial urea. Therefore, the proposed urea cocrystal based fertilizer system demonstrates a potential sustained-release nitrogen source in agriculture where excessive use of fertilizer and nutrient loss can be minimised.
Sustainability spotlight
Increased population, the recent global pandemic as well as war situations disrupt the food supply chain and fertilizer market. Rapid industrialization and shrinkage in cultivated land necessitate an increase in crop production while maintaining the minimal use of fertilizer. To maintain a balance between the current demands of food supply and population growth, sustainable agricultural practices have been identified as a vital solution. This current study aligns with point 2 of the UN's Sustainable Development Goals “Zero Hunger”. Here we have extended the concept of cocrystallisation to prepare a series of novel urea cocrystals that showed sustained-release behavior, lower volatilization, and improved hydration stability compared to commercial urea, which will help with minimal use of fertilizer with improved agriculture productivity.
|
Introduction
Urea CO(NH2)2 is one of the most widely used nitrogen fertilizers, making up ∼60% of global nitrogen fertilizer requirements.1–3 However, almost 40% of the total nitrogen fertilizer applied to plants is lost to the environment as unreactive atmospheric dinitrogen, affecting the global nitrogen cycle.4 This inherent mismatch between plant demand and nitrogen supply leads to nutrient loss through leaching that affects plant growth. Urea has very high solubility in water (ca. 110–170 g/100 mL, in the 20–40 °C range)5 and its high hygroscopicity also results in mobility and runoff.6 It negatively impacts the environment and human health via groundwater contamination, eutrophication of fresh water, and estuarine ecosystems.7 As a result, excessive amounts of urea are used so that sufficient quantities are available for plants and crops. In order to overcome these problems, slow-release fertilizer technologies have been developed in recent years, but they are not cost efficient;8–13 moreover, there is a possibility of irregular nutrient release. Furthermore, decomposition of urea by soil microbes also contributes to tropospheric pollution related to emissions of nitrogen oxides, ammonia gas, as well as accumulation of nitrous oxide (N2O), a potent greenhouse gas that depletes stratospheric ozone.14 In order to reduce enzymatic urease hydrolysis in soil, exogenous inorganic or organic molecules are often introduced that may inhibit urease activity. It has been established that even naturally occurring humic materials (various organic compounds with phenolic rings) also show urease inhibition activity.15 Because of the special hydrogen-bond donor and acceptor abilities of urea, a large number of cocrystals have been reported, with amides,16 carboxylic acids,17–20 phenols,21,22etc.23,24 In recent years, a few research groups, namely those of Baltrusaitis,25–34 Friščić,31 Užarević,26 Thakuria and Adassooriya,35,36 Aakeröy and coworkers37 introduced the concept of crystal engineering in order to prepare cocrystals (ionic/neutral) of urea with various inorganic and organic coformers to decrease its solubility as well as to improve its hydration behaviour along with inhibition of urease activity.25–27,29–33,38 The selection of a neutral coformer (catechol, salicylic acid, adipic acid, 4-nitrophenol, pimelic acid, citric acid etc.) to prepare a urea cocrystal in order to improve fertilizer activity is a recent trend and only a handful reports are available.28,34,36,37 In a recent highlight, we have emphasised this topic and discussed the importance of mechanochemistry in order to develop sustained-release urea cocrystals as a potential nitrogen source.35 As an extension to our recent report on a 2
:
1 urea·adipic acid polymorphic cocrystal that exhibited lower solubility and sustained-release behaviour compared to commercially available urea36 we have selected a few hydroxybenzoic acids (Scheme 1a) to prepare urea cocrystals using mechanochemistry. The reason for selecting hydroxybenzoic acid coformers is their low solubility as well as the fact they can be considered non-toxic model humic materials.
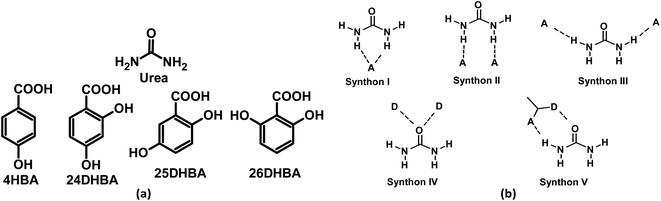 |
| Scheme 1 (a) Molecular structures of urea and substituted hydroxybenzoic acid coformers used in this study. (b) Plausible supramolecular synthons in cocrystals of urea. D and A represents hydrogen-bond donor and acceptor groups. | |
Results and discussion
Urea cocrystals are one of the most widely studied systems that form various plausible supramolecular synthons. Along with organic cocrystals, several organometallic complexes of urea are reported in the literature.39 Based on the hydrogen-bond donor and acceptor groups present in the coformers, urea can form five different supramolecular synthons shown in Scheme 1b. The powder materials of all the multicomponent solids of urea with hydroxybenzoic acids were prepared by taking stoichiometric amounts of urea (60 mg, 1.0 mmol) and respective coformers in a mortar and pestle in the presence of 100 μL of acetonitrile as an added liquid (liquid assisted grinding, LAG) for 30 min. Single crystals suitable for X-ray diffraction were grown from most laboratory solvents, such as acetonitrile, ethanol, methanol, and nitromethane. Single crystal X-ray diffraction (SCXRD) analysis confirms the urea·4HBA and urea·24DHBA cocrystals to be of 0.5
:
1 stoichiometry, whereas urea·25DHBA and urea·26DHBA resulted in 1
:
1 molecular adducts. Urea·4HBA and urea·24DHBA contain 0.5 molecule of urea and one molecule of the respective coformers in the asymmetric unit and solved in the monoclinic (P2/n) and orthorhombic (Pnma) space group, respectively. Both cocrystals contain a usual infinite urea chain connecting the p-hydroxy group of 4HBA/24DHBA acting both as hydrogen-bond donor and acceptor using synthons II and IV, as shown in Fig. 1a and b. The urea·25DHBA cocrystal contains one molecule each of urea and 25DHBA in the asymmetric unit and solved in a chiral monoclinic P21 space group. The crystal structure analysis shows the cocrystal contains all possible supramolecular synthons, viz. III, IV and V, between the urea and 25DHBA molecules. The 5-OH and COOH groups of 25DHBA connect the urea through O–H⋯O and N–H⋯O hydrogen bonds, as shown in Fig. 1c. Surprisingly, urea·26DHBA forms a salt structure with a positional disorder of protonated urea molecules having s.o.f. of 0.495/0.505 for N2A/O1B over two positions. The crystal structure was solved in the monoclinic P21/c space group with one molecule each of protonated urea and 26DHBA anion in the asymmetric unit. The crystallographic parameters of all the urea hydroxybenzoic acid molecular adducts are summarised in Table S1.† The most interesting urea·26DHBA salt structure forms a peculiar cyclic hexameric motif with alternating urea and 26DHBA molecules connected via synthons II and III (Fig. 1d). In 3D these two independent sheets of the hexagonal network intertwined, resulting in a 2-fold honeycomb network structure, as shown in Fig. 1e. This is the first report on the molecular salts of urea with organic acid, although a few salt structures of urea with phosphoric acid and nitric acid were reported in earlier literature.40–44 The reason behind the formation of molecular salt with 26DHBA is the cooperative effect of two intramolecular hydrogen bonds resulting from the 2- and 6-hydroxyl groups of 26DHBA with the carboxylic acid functional. The carboxylic acid C–O bond distances (–C
O and –C–O) of the hydroxybenzoic acids of all molecular adducts of urea are represented in Table S2.† From the table it is evident that C–O bond distances (–C
O and –C–O) of the 26DHBA coformer in urea·26DHBA are nearly identical (1.2577(1) and 1.2613(1) Å), which indicates a resonating carboxylate anion; i.e. the formation of a molecular salt. On the other hand, in all other crystal structures, the carboxylic acid C–O bond distances (–C
O and –C–O) of the hydroxybenzoic acids are different, supporting the formation of cocrystals for the rest.
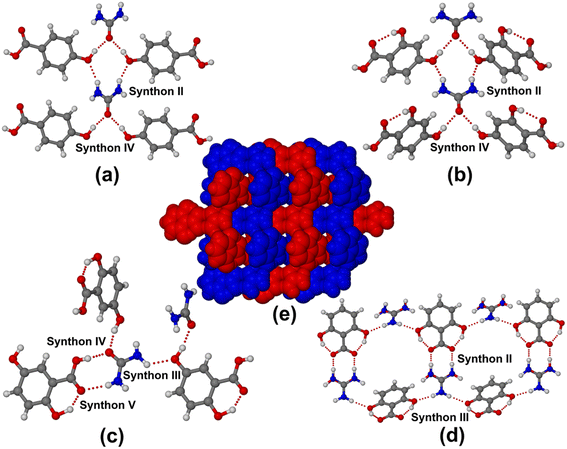 |
| Fig. 1 Various hydrogen-bond synthons present in (a) urea·4HBA, (b) urea·24DHBA, (c) urea·25DHBA, and (d) urea·26DHBA and (e) 2-fold interpenetration of urea·26DHBA salt structure. | |
In order to perform solubility, stability and leaching studies we had to ensure the phase purity of the materials; hence mechanochemical grinding was carried out, and the bulk purity of the urea cocrystals/salt was verified using PXRD analysis without the presence of any possible polymorphic phase (Fig. 2 and see ESI Fig. S1†).
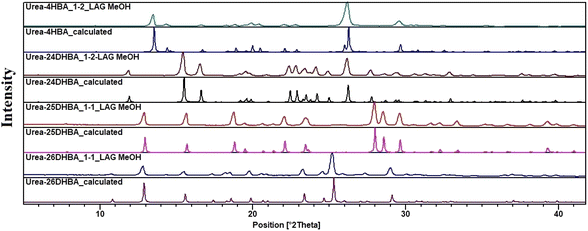 |
| Fig. 2 Comparison of the experimental and calculated powder patterns of urea·4HBA, urea·24DHBA, urea·25DHBA cocrystals and urea·26DHBA molecular salt prepared using LAG (MeOH as liquid) shows an exact match with the respective calculated powder patterns obtained from SCXRD, confirming the phase purity of the bulk solids. | |
Thermal stability of the urea multicomponent solids
Thermogravimetric analysis (TGA) measurements were performed using powder samples of urea cocrystals/salt prepared using LAG, in the 30–450 °C range with a heating rate of 10 °C min−1. The phase purity of the materials was confirmed using PXRD analysis prior to thermal measurements. No weight loss was observed prior to decomposition of all the multicomponent solids, confirming their guest-free nature. TGA measurements also show the materials to be stable up to ca. 180 °C, and they decompose immediately after melting (see ESI Fig. S2†).
Solubility measurement
The solubility of urea is very high (≈110–170 g per 100 mL at 20–40 °C). Based on the reported procedure,28,36 solubility measurement of all the urea hydroxybenzoic acid multicomponent solids was conducted in a controlled manner. 1 g of urea was taken in a vial and dissolved in 1 mL of distilled water; in a second vial, 1 g equivalent of urea cocrystals/salt (for details see ESI, Experimental procedure and Table S3†) were taken and 1 mL of distilled water was added. The material was observed to be almost insoluble (Fig. 3-left). Therefore, in a separate vial in 1 mL of distilled water, a definite amount of the respective cocrystals/salt was added slowly until it precipitated. Based on our observation, the approximate solubility of the urea adducts was calculated (Table 1). From Table 1, it was obvious that the lower solubility of the coformers resulted in a significant decrease in the approximate solubility of the urea cocrystals/salt. BFDH morphology calculation shows (see ESI Fig. S3†) that urea has a block-shaped crystal morphology with a larger number of crystal facets (isotropic morphology) exposed to the solvent medium. Moreover, two amino groups (H-bond donor) and the carbonyl group (H-bond acceptor) of urea are exposed to the crystal surface that facilitates better solvation. On the other hand, for all the urea–hydroxybenzoic acid multicomponent solids, in addition to the H-bond donor/acceptor groups, exposure of the hydrophobic benzene C–H groups of coformers to the crystal surface diminishes solvation energies. Moreover, although all the urea cocrystals/salt are block in shape, one of the crystal facets is larger in size (anisotropic morphology) resulting a relatively smaller number of crystal facets exposed to the solvent medium. In addition, stronger intermolecular hydrogen-bond interactions between urea and coformers, and the presence of intramolecular hydrogen bonds in all the dihydroxybenzoic acids might also contribute to the lower solvation energies of the urea–hydroxybenzoic acid cocrystals/salt.
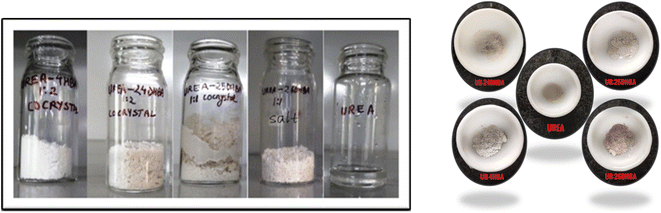 |
| Fig. 3 (Left) Comparison of solubilities for urea·4HBA, urea·24DHBA, urea·25DHBA, urea·26DHBA with pure urea under controlled experiments; (Right) powder samples of urea and respective hydroxybenzoic acid cocrystals/salt stored under 75% RH and ambient temperature. All the multicomponent solids remain as powders without showing deliquescence behaviour even after a period of 2 months, whereas urea deliquesces after a period of ∼1.5 months. | |
Table 1 Approximate solubility of the urea–hydroxybenzoic acid cocrystals/salt compared with commercial urea
Compound |
Approximate solubility (mg mL−1) |
Coformer solubility (mg mL−1) |
Extent of decrease in solubility of urea (%) |
Urea |
1000 |
|
|
Urea·4HBA cocrystal |
9.2 |
5.0 |
99 |
Urea·24DHBA cocrystal |
11.4 |
5.8 |
99 |
Urea·25DHBA cocrystal |
37.4 |
5.0 |
95 |
Urea·26DHBA salt |
15.5 |
7.49 |
98 |
Hydration stability study
Urea absorbs atmospheric moisture and as a result it undergoes deliquescence and is difficult to store or transport. To investigate the hydration stabilities of the synthesised multicomponent adducts of urea, powder materials of the respective samples were stored in a bell jar under 75% relative humidity (RH) and ambient temperature (saturated aqueous sodium chloride (NaCl) solution resulting in an RH of 75%) and PXRDs were recorded after a regular interval of time based on a reported procedure.45 PXRD data were collected in the 2θ range between 5° and 50° at ambient temperature and compared with freshly prepared powder samples. PXRDs of the powder materials and the outcomes of the humidity study of urea multicomponent solids are summarised in ESI Fig. S4 and Table S4,† respectively. From the PXRD analysis it was observed that all the multicomponent solids of urea are stable at 75% RH and ambient temperature. There is no change in the relative intensity or peak position of any of the powder materials, which suggests better stability of the powder materials. On the other hand, under identical conditions, commercial urea absorbs moisture and deliquesces after a period of ∼1.5 months, as observed from the image shown in Fig. 3-right.
Nitrogen release behaviour
The urea concentration of the eluted samples was determined using FT-IR spectroscopy, based on a previously published method.9 The linear relationship between the concentration of urea and the peak area of N–C–N stretching of urea at around 1465 cm−1 (normalized) is used to determine unknown concentrations of urea present in eluted samples (see ESI Fig. S5–S7 and Table S5†). The urea release profile shows that more than 60% of commercial urea has been leached out within two days, whereas urea·hydroxybenzoic acid molecular adducts showed only around 15–20% release. Due to the intense release of urea, crops do not have sufficient time to take up an appropriate amount of its nitrogen and the majority is wasted. This is a great loss not only from the agricultural point of view but also economically and environmentally, which makes commercial urea unsustainable. Out of urea·hydroxybenzoic acid cocrystals/salt, urea·4HBA shows a relatively higher urea release rate in the first couple of days and by the 10th day it has released almost 60% of its urea, while the other cocrystals are found to release around 55% of urea. After the 26th day it reaches a plateau with a maximum of 85% release following the same trend as pure urea. This continuous release over 26 days can be considered as sustainable release, since the process is slow and there is sufficient time for crops to uptake nitrogen. The 15% loss of urea can be attributed to its degradation into ammonium by-products. The controlled released behaviour and lower volatilisation resulted from the presence of strong hydrogen-bond interactions between hydroxybenzoic acid coformer functionals and urea molecules (see ESI Table S6†). 4HBA possesses only one OH group and it possesses a lower number of hydrogen-bonding interactions in urea·4HBA cocrystal compared to the rest of the dihydroxy benzoic acid derivatives. 25DHBA and 26DHBA have the same number of OH groups and they have similar numbers of interactions with urea in their respective crystal structures, leading to a similar trend in urea release profile (maximum around 90% by the 26th day). In the case of urea·24DHBA, its release profile closely resembles that of urea·26DHBA up to the 10th day. However after the 10th day it deviates and shows a more sustained release, achieving up to 94% maximum urea release, which is significantly high compared to our previous report on the urea·adipic acid cocrystal.36 This may be due to the combined effect of stronger intramolecular hydrogen bonds and the presence of more intermolecular hydrogen-bond interactions between urea and coformer, as well as the urease inhibition activity of hydroxybenzoic acid (model humic materials) coformers. The urea release profile of all the synthesised adducts with respect to commercial urea is shown in Fig. 4.
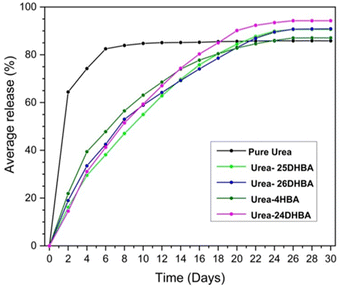 |
| Fig. 4 Urea release profile of urea·hydroxybenzoic acid multicomponent adducts compared with commercial urea for a period of 30 days. | |
In order to support the sustainability of the synthesized cocrystals compared to commercial urea as an alternative fertilizer, we calculated the approximate preparation cost of the materials based on nitrogen release data. We considered 26 days as the reference, according to the urea release profile study for cocrystals as well as urea. As the time taken for maximum urea release is ∼8 days, in order to compare the value with urea cocrystals, we multiplied the cost factor by 26/8 = 3.25 times; i.e. 3.25 times more urea is required to release the equivalent amount of N (∼85%) compared to the respective cocrystals (85–95%). Table 2 shows a reasonably lower cost of production as well as leaching rate for urea cocrystals compared to urea, that supports urea cocrystals being a better alternative.
Table 2 Approximate cost of urea, coformers and urea–hydroxybenzoic acid cocrystals/salt calculated considering the prices of the reagents taken from the same supplier, TCI Chemicals
Compounds used for the current study |
Price for 25 g of compound in INR |
1 mol. equiv. of N in urea cocrystal w.r.t. commercial urea |
Price for 1 mol. equiv. of urea cocrystal w.r.t. commercial urea available for 26 days in INR |
Price of equiv. amount of urea cocrystal leached out compared to commercial urea in INR |
Price of urea cocrystal absorbed by plant in 26 days compared to commercial urea in INR |
Urea |
4400 |
Urea |
4400 × 3.25 = 14 300 |
14 300 × 15% = 2145 |
14 300 × 85% = 12 155 |
4HBA |
2000 |
(Urea)(4HBA)2 |
4400 + 2 × 2000 = 8400 |
8400 × 15% = 1260 |
8400 × 85% = 7140 |
24DHBA |
3100 |
(Urea)(24HBA)2 |
4400 + 2 × 3100 = 10 600 |
10 600 × 6% = 636 |
10 600 × 94% = 9964 |
25DHBA |
4100 |
(Urea)(25HBA) |
4400 + 4100 = 8500 |
8500 × 10% = 850 |
8500 × 90% = 7650 |
26DHBA |
6000 |
(Urea)(26HBA) |
4400 + 6000 = 10 400 |
10 400 × 10% = 1040 |
10 400 × 90% = 9360 |
Conclusions
The mechanochemical syntheses of a few urea cocrystals/salt with substituted hydroxybenzoic acids as model humic materials with improved physicochemical properties have been investigated. The lower solubility of the urea cocrystals/salt indicates the high potential of their use as sustained-release nitrogenous fertilizers. The results prove that considerable changes to the solid forms of urea can be promptly made through a systematic cocrystallisation technique by selecting suitable coformers. Furthermore, these cocrystals/salt with drastically improved hydration stability suggest easy transport and storage of the material compared to commercial urea. Moreover, the urea release profile showed significant improvement in nitrogen absorption by soil with the sustained-release behaviour of the synthesised cocrystals/salt that will help the plant body to absorb nitrogen for a longer period of time compared to commercial urea. The release profiles showed that the novel urea·hydroxybenzoic acid based cocrystal fertilizer system takes 26 days to release ∼90% urea, whereas pure urea reaches a plateau within 8 days with ∼85% urea release, confirming the sustained-release behaviour of the hydroxybenzoic acid based cocrystal fertilizer. Currently we are working on field trials (pot trials) in order to investigate any possible toxicity with some selected crops. To conclude, if the fertilizer industry can adopt the cocrystallisation technique to prepare sustained-release urea cocrystals as alternate fertilizer, the excessive use of fertilizer and nutrient loss can be minimised.
Author contributions
T. R. synthesized and characterized the urea cocrystals/salt. D. G. and P. D. carried out the solubility and hydration stability study. S. P. carried out the nitrogen release study of the synthesized cocrystals/salt. N. M. A. and R. T. designed the project and all authors together finalized the manuscript.
Conflicts of interest
There are no conflicts to declare.
Acknowledgements
This work was funded by Science and Engineering Research Board under the Teachers Associateship for Research Excellence (TARE) grant (Project No. TAR/2021/000251). P. D. thanks the UGC for the Junior Research Fellowship (PhD scholar). R. T. thankfully acknowledges the Sophisticated Analytical Instrumentation Facility (SAIF), GU for the provision of the single crystal X-ray diffractometer and the Department of Chemistry, GU for the Rigaku powder X-ray diffractometer, basic instrumentation facility, and infrastructure. NMA is thankful to National Research Council, Sri Lanka (Grant No. 22-114) and Department of Chemical & Process Engineering, UoP for laboratory facilities.
Notes and references
- X. Zhang, E. A. Davidson, D. L. Mauzerall, T. D. Searchinger, P. Dumas and Y. Shen, Nature, 2015, 528, 51–59 CrossRef CAS PubMed.
- D. Coskun, D. T. Britto, W. Shi and H. J. Kronzucker, Nat. Plants, 2017, 3, 1–10 Search PubMed.
- A. M. Dave, M. H. Mehta, T. M. Aminabhavi, A. R. Kulkarni and K. S. Soppimath, Polym.-Plast. Technol. Eng., 1999, 38, 675–711 CrossRef CAS.
- J. N. Galloway, F. J. Dentener, D. G. Capone, E. W. Boyer, R. W. Howarth, S. P. Seitzinger, G. P. Asner, C. C. Cleveland, P. Green and E. A. Holland, Biogeochemistry, 2004, 70, 153–226 CrossRef CAS.
- F.-M. Lee and L. E. Lahti, J. Chem. Eng. Data, 1972, 17, 304–306 CrossRef CAS.
- C. W. Whittaker, F. O. Lundstrom and S. B. Hendricks, Ind. Eng. Chem., 1933, 25, 1280–1282 CrossRef CAS.
- K. Goulding, S. Jarvis and A. Whitmore, Philos. Trans. R. Soc., B, 2008, 363, 667–680 CrossRef CAS PubMed.
- J. Shi, J. Li, W. Zhou and D. Zhang, Front. For., 2007, 2, 104–109 Search PubMed.
- N. Kottegoda, C. Sandaruwan, G. Priyadarshana, A. Siriwardhana, U. A. Rathnayake, D. M. Berugoda Arachchige, A. R. Kumarasinghe, D. Dahanayake, V. Karunaratne and G. A. J. Amaratunga, ACS Nano, 2017, 11, 1214–1221 CrossRef CAS PubMed.
- N. Kottegoda, I. Munaweera, N. Madusanka and V. Karunaratne, Curr. Sci., 2011, 73–78 CAS.
- N. Madusanka, C. Sandaruwan, N. Kottegoda, D. Sirisena, I. Munaweera, A. De Alwis, V. Karunaratne and G. A. J. Amaratunga, Appl. Clay Sci., 2017, 150, 303–308 CrossRef CAS.
- A. S. Giroto, G. G. F. Guimarães, M. Foschini and C. Ribeiro, Sci. Rep., 2017, 7, 46032 CrossRef CAS PubMed.
- C. Wang, J. Lv, J. Xie, J. Yu, J. Li, J. Zhang, C. Tang, T. Niu and B. E. Patience, Sci. Rep., 2021, 11, 8070 CrossRef CAS PubMed.
- M. Zaman, S. Saggar, J. D. Blennerhassett and J. Singh, Soil Biol. Biochem., 2009, 41, 1270–1280 CrossRef CAS.
- L. Dong, A. L. Córdova-Kreylos, J. Yang, H. Yuan and K. M. Scow, Soil Biol. Biochem., 2009, 41, 1612–1621 CrossRef CAS PubMed.
- K. Moribe, M. Tsuchiya, Y. Tozuka, K. Yamaguchi, T. Oguchi and K. Yamamoto, J. Inclusion Phenom. Macrocyclic Chem., 2006, 54, 9–16 CrossRef CAS.
- S. Aitipamula, L. K. Mapp, A. B. H. Wong, P. S. Chow and R. B. H. Tan, CrystEngComm, 2015, 17, 9323–9335 RSC.
- A. Alhalaweh, S. George, D. Boström and S. P. Velaga, Cryst. Growth Des., 2010, 10, 4847–4855 CrossRef CAS.
- S. Bolton, J. Pharm. Sci., 1963, 52, 1071–1074 CrossRef CAS PubMed.
- D. M. Altwein, J. N. Delgado and F. P. Cosgrove, J. Pharm. Sci., 1965, 54, 603–606 CrossRef CAS PubMed.
- M. Pickering and R. Small, Acta Crystallogr., Sect. B: Struct. Crystallogr. Cryst. Chem., 1982, 38, 3161–3163 CrossRef.
- R. B. Hammond, C. Ma, K. J. Roberts, P. Y. Ghi and R. K. Harris, J. Phys. Chem. B, 2003, 107, 11820–11826 CrossRef CAS.
- R. Lee, S. A. Mason, E. Mossou, G. Lamming, M. R. Probert and J. W. Steed, Cryst. Growth Des., 2016, 16, 7175–7185 CrossRef CAS.
- Y. Zhou, F. Guo, C. E. Hughes, D. L. Browne, T. R. Peskett and K. D. M. Harris, Cryst. Growth Des., 2015, 15, 2901–2907 CrossRef CAS.
- K. Barčauskaitė, Z. Brazienė, D. Avižienytė, M. Silva, D. Drapanauskaite, K. Honer, K. Gvildienė, R. Slinksiene, K. Jancaitiene, R. Mazeika, G. Staugaitis, T. Dambrauskas, K. Baltakys and J. Baltrusaitis, J. Environ. Chem. Eng., 2020, 8, 103965 CrossRef.
- I. Brekalo, V. Martinez, B. Karadeniz, P. Orešković, D. Drapanauskaite, H. Vriesema, R. Stenekes, M. Etter, I. Dejanović, J. Baltrusaitis and K. Užarević, ACS Sustainable Chem. Eng., 2022, 10, 6743–6754 CrossRef CAS.
- L. Casali, L. Mazzei, O. Shemchuk, K. Honer, F. Grepioni, S. Ciurli, D. Braga and J. Baltrusaitis, Chem. Commun., 2018, 54, 7637–7640 RSC.
- L. Casali, L. Mazzei, O. Shemchuk, L. Sharma, K. Honer, F. Grepioni, S. Ciurli, D. Braga and J. Baltrusaitis, ACS Sustainable Chem. Eng., 2019, 7, 2852–2859 CrossRef CAS.
- K. Honer, E. Kalfaoglu, C. Pico, J. McCann and J. Baltrusaitis, ACS Sustainable Chem. Eng., 2017, 5, 8546–8550 CrossRef CAS.
- K. Honer, C. Pico and J. Baltrusaitis, ACS Sustainable Chem. Eng., 2018, 6, 4680–4687 CrossRef CAS.
- P. A. Julien, L. S. Germann, H. M. Titi, M. Etter, R. E. Dinnebier, L. Sharma, J. Baltrusaitis and T. Friščić, Chem. Sci., 2020, 11, 2350–2355 RSC.
- L. Mazzei, V. Broll, L. Casali, M. Silva, D. Braga, F. Grepioni, J. Baltrusaitis and S. Ciurli, ACS Sustainable Chem. Eng., 2019, 7, 13369–13378 CrossRef CAS.
- C. Navizaga, J. Boecker, A. M. Sviklas, J. Galeckiene and J. Baltrusaitis, ACS Sustainable Chem. Eng., 2017, 5, 1747–1754 CrossRef CAS.
- M. Silva, K. Barcauskaite, D. Drapanauskaite, H. Tian, T. Bučko and J. Baltrusaitis, ACS Earth Space Chem., 2020, 4, 1018–1028 CrossRef CAS.
- N. M. Adassooriya, S. P. Mahanta and R. Thakuria, CrystEngComm, 2022, 24, 1679–1689 RSC.
- S. Parakatawella, D. Gogoi, P. Deka, Y. Xu, C. Sandaruwan, A. C. A. Jayasundera, M. Arhangelskis, R. Thakuria and N. M. Adassooriya, ChemSusChem, 2022, 15, e202102445 CrossRef CAS PubMed.
- B. Sandhu, A. S. Sinha, J. Desper and C. B. Aakeröy, Chem. Commun., 2018, 54, 4657–4660 RSC.
- S. G. Davey, Nat. Rev. Chem., 2022, 1 CAS.
- S. K. Chandran, R. Thakuria and A. Nangia, CrystEngComm, 2008, 10, 1891–1898 RSC.
- S. Harkema and D. Feil, Acta Crystallogr., Sect. B: Struct. Sci., 1969, 25, 589–591 CrossRef CAS.
- Y. V. Nelyubina, K. A. Lyssenko, D. G. Golovanov and M. Y. Antipin, CrystEngComm, 2007, 9, 991–996 RSC.
- Y.-L. Liu and W. Zhang, Dalton Trans., 2018, 47, 45–48 RSC.
- C. Wilson, Acta Crystallogr., Sect. B: Struct. Sci., 2001, 57, 435–439 CrossRef CAS PubMed.
- A. Parkin, S. M. Harte, A. E. Goeta and C. C. Wilson, New J. Chem., 2004, 28, 718–721 RSC.
- K. K. Sarmah, P. Sarma, D. R. Rao, P. Gupta, N. K. Nath, M. Arhangelskis and R. Thakuria, Cryst. Growth Des., 2018, 18, 2138–2150 CrossRef CAS.
Footnote |
† Electronic supplementary information (ESI) available: Crystallographic data (CCDC deposition numbers 2190718–2190721) and details of synthesis, measurements for urea adducts; crystallographic parameters of all urea adduct; experimental details of urea release study and solubility study; thermogravimetric traces of urea adduct; powder X-ray diffraction patterns of various LAG and hydration stability study and hydrogen bond parameters of urea adducts. For ESI and crystallographic data in CIF or other electronic format see DOI: https://doi.org/10.1039/d3su00021d |
|
This journal is © The Royal Society of Chemistry 2023 |
Click here to see how this site uses Cookies. View our privacy policy here.