Detoxification of bisphenol A via sulfur-mediated carbon–carbon σ-bond scission†
Received
19th December 2022
, Accepted 10th March 2023
First published on 17th March 2023
Abstract
Environmental contamination with bisphenol A (BPA), produced via degradation of plastic waste, constitutes a major hazard for human health due to the ability of BPA to bind to estrogen receptors and thereby induce hormonal imbalances. Unfortunately, BPA cannot be degraded to a “safe” material without breaking C–C σ-bonds, and existing methods required to break these bonds employ petroleum-derived chemicals and environmentally-harmful metal ions. Therefore, there is an urgent need to develop new “green” methods to break BPA into monoaryl compounds without the use of such reagents and, ideally, convert those monoaryls into valuable materials that can be productively utilized instead of being discarded as chemical waste. Herein we report a new mechanism by which O,O′-dimethyl bisphenol A (DMBPA), obtained from BPA-containing plastic via low-temperature recycling, undergoes C–C σ-bond cleavage via thiocracking, a reaction with elemental sulfur at temperatures lower than those used in many thermal plastic recycling techniques (e.g., <325 °C). Mechanistic analyses and microstructural characterization of the DMBPA-derived materials produced by thiocracking elucidated multiple subunits comprising monoaryl species. Impressively, analyses of recoverable organics revealed that >95% of DMBPA had been broken down into monoaryl components. Furthermore, the DMBPA–sulfur composite produced by thiocracking (BC90) exhibited compressive strength (∼20 MPa) greater than those of typical Portland cements. Consequently, this new thiocracking method creates the ability to destroy the estrogen receptor-binding components of BPA wastes using greener techniques and, simultaneously, to produce a mechanically-robust composite material that represents a sustainable alternative to Portland cements.
Sustainability spotlight
Environmental contamination with bisphenol A (BPA), produced via degradation of plastic wastes, constitutes a major hazard for human health due to the ability of BPA to bind to estrogen receptors and thereby induce hormonal imbalances. Unfortunately, BPA cannot be degraded to a “safe” material without breaking C–C σ-bonds, and existing methods required to break these bonds employ petroleum-derived chemicals and environmentally-harmful metal ions. Therefore, there is an urgent need to develop new “green” methods to break BPA into monoaryl compounds without the use of toxic reagents and, ideally, convert those monoaryls into valuable materials that can be productively utilized instead of being discarded as chemical waste. Herein we report a new mechanism by which O,O′-dimethyl bisphenol A (DMBPA), obtained from BPA-containing plastic via low-temperature recycling, undergoes C–C σ-bond cleavage via thiocracking, a reaction with elemental sulfur at temperatures lower than those used in many thermal plastic recycling techniques. Impressively, analyses of recoverable organics revealed that >95% of DMBPA had been broken down into monoaryl components. The DMBPA–sulfur composite produced by thiocracking (BC90) exhibited compressive strength greater than those of typical Portland cements. Consequently, this new thiocracking method creates the ability to destroy the estrogen receptor-binding components of BPA wastes using greener techniques and, simultaneously, to produce a mechanically-robust composite material that represents a sustainable alternative to Portland cements. This work aligns most directly with UN sustainability goals Good Health and Wellbeing (SDG3), Clean Water and Sanitation (SDG6), Sustainable Cities and Communities (SDG 11), and Responsible Consumption and Production (SDG12), with clear downstream impact on safeguarding Life Below Water (SDG 14) and Life on Land (SDG 15).
|
Introduction
Environmental degradation of polycarbonate and other plastic wastes releases bisphenol A (BPA) and BPA-containing fragments which bind to estrogen receptors in humans and other organisms, thereby disrupting normal hormone signaling and damaging reproductive systems. Entry of BPA into the maternal blood pool, for example, exposes developing embryos to BPA, which increases the probability of miscarriage or premature delivery, and results in abnormally low birth weights.1 New mechanisms to recycle BPA-containing wastes that also cleave BPA subunits into monoaryl species are urgently needed to eliminate the hazards to human and environmental health. Despite some insightful work using nanoparticles to detoxify BPA,2–4 the primary mechanisms for recycling BPA-containing polymers preserve the 4,4-(propane-2,2-diyl)diphenol structure that is responsible for the endocrine-disrupting effects of BPA. We hypothesized that reaction of BPA-containing molecules with elemental sulfur via thiocracking at 310–325 °C would break apart the 4,4′-(propane-2,2-diyl)diphenol core of BPA through C–C σ-bond cleavage and simultaneously produce high sulfur-content materials (HSMs) that could be employed as green alternatives to petroleum-derived plastics and CO2-intensive Portland cement.
Inverse vulcanization, pioneered by Pyun, is the principal method used to prepare HSMs (Scheme 1A and B).5–8 Whereas traditional vulcanization, developed by Goodyear,9 employs <5 wt% of elemental sulfur, Pyun's inverse vulcanization uses sulfur as the majority component. Heating elemental sulfur to temperatures above 159 °C disrupts the cyclo-S8 structure and produces polysulfides with radical termini, [˙S–Sn–S˙] (Scheme 1A). When the temperature is reduced below 159 °C, these radical-terminated polysulfides slowly relax back to the cyclo-S8 structure characteristic of orthorhombic sulfur.10–12 In the presence of olefins, however, the sulfur-centered radicals in these polysulfides can add to the C–C π-bonds to produce composites containing highly-crosslinked networks, which comprise stabilized polymeric sulfur chains. Composites produced in this manner can exhibit exceptional thermomechanical properties, and can be thermally recycled under relatively mild conditions, owing to the thermal reversibility of S–S bond breakage and bond formation.13–18 Fully-sustainable sulfur composites can be prepared when petroleum-derived olefins are replaced with biologically-produced monomers, such as fatty acids,19–21 triglycerides,22–26 terpenoids,25,27–30 amino acid derivatives,31 lignin derivatives,32–35 cellulose derivatives,30,36 and even raw lignocellulosic biomass.37,38 Reaction temperatures for preparing or shaping HSMs can be lowered by using catalysts,39 mechanochemical methods,40 ternary mixtures,41 pre-formation of more reactive sulfur species,42 using nucleophiles to fuse materials together through S–S metathesis,43 or by compression-molding of materials.44 Promising photochemical routes to C–S bond formation towards preparing or healing HSMs also hold potential for lowering the energy requirements of these processes.45
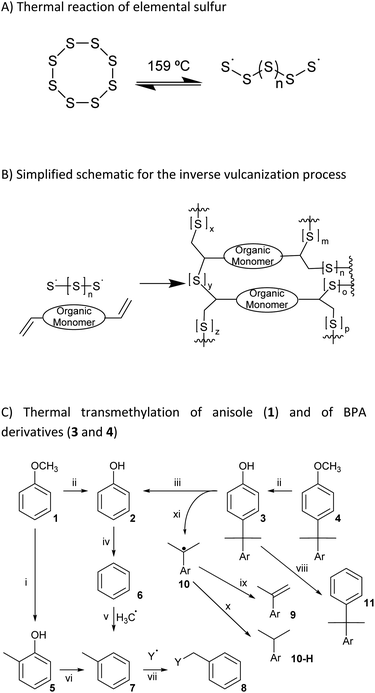 |
| Scheme 1 (A) Established thermal reactions of elemental sulfur to form polymeric sulfur radicals. (B) Crosslinking of olefins with sulfur to form HSMs. (C) Established thermal degradation routes for anisole (1) and bisphenol A derivatives (3 and 4). | |
Although 4,4-(propane-2,2-diyl)diphenol and its derivatives do not contain olefinic subunits, species generated upon heating elemental sulfur can also react with thermal breakdown products of organics to form HSMs comprising a variety of C–S bonds. A process referred to as radical-induced aryl halide–sulfur polymerization (RASP),32,46–48 for example, employs a thermally-generated radical, which then reacts with elemental sulfur to yield HSMs comprising aryl carbon–sulfur bonds. In another example, our group recently reported GS80, a guaiacol–sulfur composite, comprising Caryl–S bonds produced via the reaction of thermally-generated guaiacol-derived aryl radicals with elemental sulfur at 230 °C (Scheme 2A).35 We therefore hypothesized that similar thermal decomposition of other anisole-containing compounds in the presence of elemental sulfur would likewise yield HSMs through the formation of Caryl–S bonds (Scheme 1C).49–60
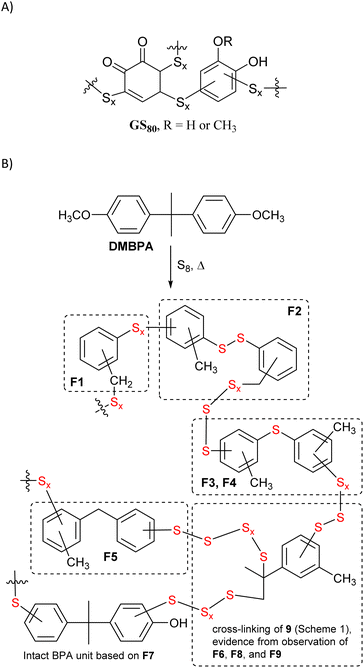 |
| Scheme 2 (A) Microstructures in GS80 (formed by reaction of 80 wt% sulfur with guaiacol). (B) Formation of and microstructures observed in BC90. Substructures are inferred from nine structurally-distinct fragments F1–F9 identified by mass spectrometric analysis of depolymerization products (Chart 1). | |
Thermal recycling of BPA-containing plastics yields the anisole-containing compound O,O′-dimethyl bisphenol A (DMBPA) via photo-induced catalytic C–C bond scission at only 35–40 °C.61 Because DMBPA contains anisole subunits, we hypothesized that the reaction conditions developed by our group for the conversion of guaiacol to GS80 would likewise yield HSMs in which the DMBPA had been broken down into monoaryl species. Herein we report the reaction of DMBPA with elemental sulfur at 310–325 °C to afford the HSM BC90, which comprises monoaryl species derived from C–C σ-bond cleavage in DMBPA.49–60
Results and discussion
The primary objective of the current study was to elucidate a route to chemically disassemble the BPA core structure at a lower temperature than those of current chemical recycling approaches to plastic waste treatment such as carbonization, pyrolysis, combustion, gasification and some applications of hydrocracking.62 The compound O,O′-dimethyl bisphenol A (DMBPA) was selected as the substrate because it can be readily obtained from BPA-containing plastic wastes via low-temperature (35–40 °C) C–C bond scission.61 Thermal decomposition studies of BPA and its derivatives49–60 have revealed that Caryl–Calkyl σ-bond scission becomes significant at 310 °C (Scheme 1C). We therefore combined DMBPA and elemental sulfur in a 1
:
9 mass ratio in a Parr bomb reactor under a nitrogen atmosphere, and then heated the mixture to 310–325 °C for 4 h. Upon cooling to room temperature, the product BC90 was isolated as a black, glassy solid that could be remelted readily (Scheme 2). To determine the relative distribution of aryl-terminated polysulfides vs. entrapped, unreacted cyclo-S8, all unbound cyclo-S8 was extracted from BC90 using carbon disulfide (CS2). Mass-balance analysis of the CS2-soluble and -insoluble fractions revealed that 17.2% of the initial mass of BC90 was unbound cyclo-S8. Elemental microanalysis provided unambiguous evidence that the CS2-soluble fraction contained only elemental sulfur.
One strategy to identify the subunits comprising HSM microstructures is to depolymerize the material by cleaving the labile S–S bonds to afford small organic molecules with improved solubility and greater amenability towards molecular characterization techniques. A sample of BC90 was therefore depolymerized using AlBr3,32,47,63–65 which has been shown to cleave S–S bonds, along with S–C bonds to 1° and 2° alkyl carbons, without affecting S–C bonds to 3° alkyl or aryl carbons. Following AlBr3-mediated depolymerization, these unreacted C–S bonds will be terminated as thiols (i.e., as C–S–H moieties). To quantify the amount of C–S–H moieties, the depolymerization mixture was then treated with the disulfide Ellman's reagent, which undergoes S–S bond scission in the presence of free thiols with a concomitant increase in absorbance at 412 nm (Scheme 3).66,67 Analysis of the depolymerization mixture using this technique indicated a lower limit of 0.7 S atoms per aryl ring in the starting material, but the exact amount could not be determined unambiguously due to the presence of some insoluble material.
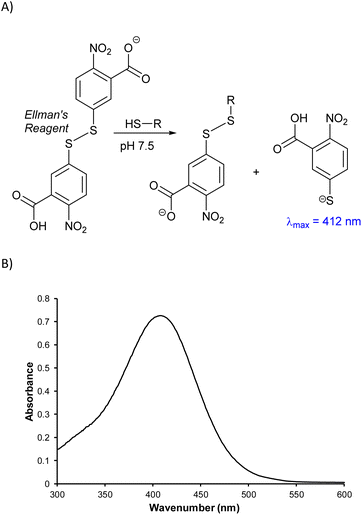 |
| Scheme 3 (A) Mechanism by which Ellman's reagent reacts with thiols to provide a colorimetric response and (B) UV-Vis spectrum resulting from Ellman's analysis of BC90 depolymerization products. | |
The only unambiguous evidence that could be obtained from 1H NMR spectroscopic analysis of this mixture (Fig. S1 and S2 in the ESI†) was quantitative methyl migration, as indicated by the absence of any resonance between 3–3.5 ppm attributable to –OCH3 moieties.
Fortunately, the components of the mixture produced by depolymerization of BC90 could be analyzed by GC-MS, which revealed nine unique fragments (F1–F9, Chart 1 and ESI Fig. S3–S23†). Consistent with 1H NMR spectrometry, none of the fragments comprised –OCH3 moieties. Impressively, fragments F1–F6 do not contain any O-atoms, likely the result of BPA decomposition pathways (iv) and (vi) (Scheme 1), providing unambiguous evidence for the thermal degradation of the bisanisole core of DMBPA. Although the observation of fragment F7 suggested that some intact BPA-like units were present in BC90, GC-MS analysis of the other species confirmed that >95% of the DMBPA bisanisole core structures had fragmented in a manner consistent with known thermal decomposition pathway (ix) (Scheme 1), which proceeds through a tertiary benzylic radical.51 The observation of fragments F8 and F9 indicated that the quaternary carbon bridging anisole rings was not inert under these reaction conditions. These S–Caryl bonds can be formed by reaction of elemental sulfur with tertiary radical 10 or with olefin 9 via traditional inverse vulcanization.
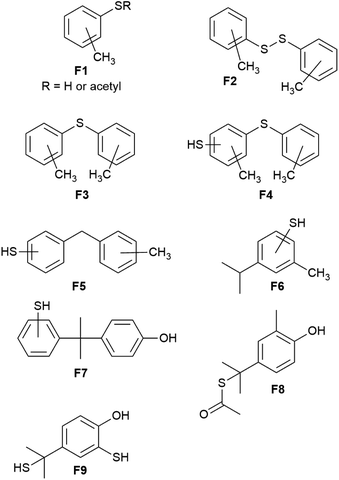 |
| Chart 1 Depolymerization products identified by GC-MS analysis reveal information on the microstructure of BC90. | |
Fragments F1–F7 and F9 comprise S–Caryl bonds that can form only if the anisole subunits of DMBPA react with elemental sulfur in a fashion similar to the anisole derivative guaiacol. Interestingly, fragment F5 contains a new C–C σ-bond formed via methyl group transfer to an aryl ring, which is consistent with previous studies into the thermolysis of anisoles in the absence of other compounds. In the current case, however, their contribution is much lower than observed in thermolysis of pure anisole derivatives due to dilution of the anisole units by the sulfur (90 wt%) that serves as the solvent/comonomer. We therefore concluded that BC90 possessed a highly-complex microstructure, comprising a multitude of subunits corresponding to fragments F1–F9, of which >95% of the aromatic compounds are monoaryls that could only be formed via C–C σ-bond breakage.
Once some general microstructural characteristics had been elucidated and the hypothesized C–S bond-formation was confirmed, it was necessary to determine the extent to which the network could stabilize polymeric sulfur as is possible in HSMs produced by other routes. Differential scanning calorimetry (DSC) confirmed the presence of polymeric sulfur chains in BC90, as evidenced by a characteristic glass transition at −34 °C, along with broad cold crystallization peaks at −5–20 °C and 46–57 °C. Unbound cyclo-S8, in contrast, was identifiable by a melting peak at 116 °C (Fig. S24 in the ESI†). Thermal decomposition onset for BC90 occurred at 235 °C, as judged by the loss of 5% of initial mass. These TGA and DSC features are highly-conserved with the other HSMs. Overall, BC90 possesses 19.4% the crystallinity of elemental sulfur.34,35,46,65
Scanning electron microscopy (SEM) with elemental mapping by energy dispersive X-ray analysis (EDX) performed on samples of BC90 revealed that carbon and sulfur were well-dispersed throughout the material (Fig. S26 in the ESI†), with a minor number of regions in which organic material had agglomerated (Fig. S27 in the ESI†).
Many of the HSMs developed by our group exhibit exceptional thermomechanical properties, and some notable examples have compressive strength values superior to those of traditional cement-like structural materials used in construction.31,34,68–70 Compressive test cylinders of BC90 (photo inset, Fig. 1) could be conveniently prepared by melting a sample of BC90, pouring the liquid sample into a cylindrical mold, and then allowing the material to cure for 5 days at room temperature. Cylindrical samples of BC90 prepared in this manner were subjected to compressional stresses and the strain responses were recorded (Fig. 1). At 22.5 ± 2.1 MPa, the compressional strength of BC90 resides at the high end of compressional strength values measured for other HSMs comprising 90 wt% sulfur (Table 1). Impressively, the compressive strength of BC90 surpasses by 32% the compressive strength requirements for traditional Portland cements employed in residential building foundations.
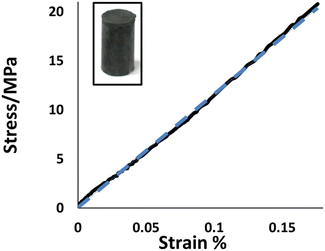 |
| Fig. 1 Stress–strain curve for BC90 (solid line) and linear fit (dashed line). A photo of a compressive test cylinder of BC90 is shown as an inset. | |
Table 1 Compressive strength analysis for HSMsa
Materials (90 wt% sulfur) |
Compressive strength/MPa |
HSMs prepared by the reaction of elemental sulfur (90 wt%) with (a) peanut shell flour, (b) allylated peanut shell flour, (c) octenyl succinate-modified corn starch, (d) citronella oil, (e) geraniol, (f) farnesol, (g) canola oil, (h) sunflower oil. (i) HSM from reaction of S8 (95 wt%) (j) Ordinary Portland cement. ohe compressive strength of OPC can vary, so a value of 17 MPa, the minimum required by ACI 330 for residential building, is used here for comparison.
|
BC90 |
22.5 |
PS90a |
21.3 |
APS90b |
24.1 |
OSS90c |
10.9 |
CitSd |
10.0 |
GerSe |
7.9 |
FarSf |
28.9 |
CanSg |
9.3 |
SunSh |
17.8 |
LinSi |
22.9 |
Portland cementj |
17 |
Conclusions
The compound DMBPA, which is produced by low-temperature recycling of BPA-derived plastics, reacts with elemental sulfur at 310–325 °C such that >95% of DMBPA is converted to monoaryl species. Because the endocrine-disrupting function of a BPA-derived bisphenolic arises from its ability to bind to estrogen receptors, rupturing its bisaryl core into monoaryl species will eliminate these physiologically-harmful effects. Impressively, BC90, the composite material produced by this reaction of DMBPA with elemental sulfur, possesses a compressive strength that surpasses the requirements of traditional Portland cements used in the foundations of residential buildings. Moreover, unlike traditional Portland cements, BC90 is fully thermally-recyclable, with no loss in mechanical strength after multiple cycles. Our findings constitute a mechanism by which the harmful endocrine-disrupting effects of BPA can be eliminated using green chemical methods. In addition, the resulting HSM composites have significant value of their own as sustainable, and recyclable, alternatives to traditional Portland cements. Given the utility of HSMs8,25,39,44,71–81 as components of lithium–sulfur batteries,78,79,82–84 infrared imaging devices,85 water purification adsorbents,86–90 and slow-release fertilizers,91–93 our method will give BPA-derived plastic wastes new life in a wide variety of sustainable endeavors.
Experimental
General considerations and instrumentation
All 1H NMR spectra were recorded on a Bruker Avance spectrometer operating at 300 MHz. TGA was recorded (Mettler Toledo TGA 2 STARe System) over the range 20–800 °C with heating. DSC was acquired (Mettler Toledo DSC 3 STARe System) over the range −60 to 150 °C with a heating rate of 5 °C min−1 under a flow of N2 (200 mL min−1). Each DSC measurement was carried out over three heat–cool cycles. Each measurement was acquired in triplicate to ensure consistent results were obtained. Compressional analysis was performed on a Mark-10 ES30 test stand (Model G1061-1) equipped with a M3-200 force gauge (1000 N maximum force with ±1 N resolution). Compression cylinders were cast from silicone resin molds (Smooth-On Oomoo® 30 tin-cure) with diameters of approximately 6 mm and heights of approximately 9 mm. The data reported are the average of three runs. SEM and EDX were acquired on a Schottky Field Emission Scanning Electron Microscope SU5000 operating in variable pressure mode with an accelerating voltage of 15 keV.
Carbon disulfide extractions were performed by suspending 0.5 g of finely ground material (measured to 0.001 g) in 20 mL of CS2, allowing the solid to settle for 30 minutes, pipetting off the supernatant into a separate vial, and adding another 20 mL of CS2. This process was repeated an additional 3 times so that a total of 5 washes was performed to leave a residue of constant mass. The residual CS2 was evaporated under a flow of N2 and each vial was weighed to determine the fraction that was insoluble.
Materials
Elemental sulfur (99.5%, Alfa Aesar), carbon disulfide (Bean Town Chemicals). Tris(hydroxymethyl)aminomethane hydrochloride and 5,5′-dithio-bis-(2-nitrobenzoic acid) (VWR Analytical). Chemicals were all used as received.
Synthesis
CAUTION: Heating elemental sulfur with organics can result in the formation of H2S gas. H2S is toxic, foul-smelling, and corrosive. Although we did not observe any mass loss attributable to gas generation, the temperature must be carefully controlled to prevent thermal spikes, which contribute to the potential for H2S evolution. Rapid stirring shortened heating times, and very slow addition of reagents can help prevent unforeseen temperature spikes.
Synthesis of BC90.
A 2.0 g sample of DMBPA and 18.0 g of elemental sulfur were weighed out and thoroughly mixed into a stainless-steel reactor vessel of a Parr bomb reactor. The reactor vessel was then sealed in a heating assembly (Parr model 2236HCEB) equipped with a temperature controller (Model 4843) and a mechanically-driven stainless-steel stir rod. The temperature was maintained at 310–325 °C for 4 h under a N2 environment. After the reactor vessel cooled down to room temperature, the hard, black, shiny solid was collected in quantitative yield. The solid so collected was ground into a fine powder and used for all the characterizations described herein. To cast the cylinders for compressive strength analysis, the powder was remelted at 180 °C and poured into silicone resin molds. Elemental analysis and fractionation data are provided in the ESI.†
Depolymerization with AlBr3.
The BC90 sample (30 mg) was crushed to a fine powder and then mixed with 60 mg of AlBr3 in a glovebox under a N2 atmosphere. The solid mixture was suspended in 6 mL of anhydrous toluene for 30 min with continuous stirring. At the end of the reaction time, the solvent was filtered and 5% (v/v) HCl
:
ethanol (5 mL) was added. Following three consecutive washes, the organic layer in toluene was separated and concentrated to give the solid for analysis.
The reaction of depolymerized products with Ellman's reagent.
The procedure was carried out according to a previously reported method with slight changes. The stock solution of DTNB (5,5′-dithio-bis-(2-nitrobenzoic acid)) was prepared by dissolving 40 mg of DTNB in 10 mL of DMSO. The solution was 100-fold diluted into 0.1 mM DTNB solution using Tris HCl (Tris (hydroxymethyl)aminomethane hydrochloride) buffer solution at a pH of 7.4. A 1 mL aliquot of the solution containing depolymerized products and 19 mL of 0.1 mM DTNB were mixed and then let it to sit at room temperature for 2 min. The prepared samples were then analysed using a Cary 50 UV-VIS spectrophotometer. The same procedure was carried out without adding AlBr3 to confirm thiol groups' absence in the initial sample.
Author contributions
The author primarily responsible for particular CRediT roles are provided here. MKL, TT and MSK: data curation, formal analysis, investigation, validation. RCS: writing – original draft, conceptualization, funding acquisition, methodology, resources, supervision. AGT: writing – review and editing, resources, supervision.
Conflicts of interest
There are no conflicts to declare.
Acknowledgements
This research is funded by the National Science Foundation grant number CHE-2203669.
Notes and references
- E. Matuszczak, M. D. Komarowska, W. Debek and A. Hermanowicz, Int. J. Endocrinol., 2019, 2019, 4068717 CrossRef PubMed.
- I. Khan, A. Yuan, S. Khan, A. Khan, S. Khan, S. A. Shah, M. Luo, W. Yaseen, X. Shen and M. Yaseen, ACS Appl. Nano Mater., 2022, 5, 13404–13416 CrossRef CAS.
- I. Khan, M. Luo, S. Khan, H. Asghar, M. Saeed, S. Khan, A. Khan, M. Humayun, L. Guo and B. Shi, Environ. Res., 2022, 207, 112650 CrossRef CAS PubMed.
- I. Khan, S. Khan, J. Chen, S. A. Shah and A. Yuan, J. Cluster Sci., 2022 DOI:10.1007/s10876-022-02317-3.
- W. J. Chung, J. J. Griebel, E. T. Kim, H. Yoon, A. G. Simmonds, H. J. Ji, P. T. Dirlam, R. S. Glass, J. J. Wie, N. A. Nguyen, B. W. Guralnick, J. Park, A. Somogyi, P. Theato, M. E. Mackay, Y.-E. Sung, K. Char and J. Pyun, Nat. Chem., 2013, 5, 518–524 CrossRef CAS PubMed.
- M. Chalker Justin, J. H. Worthington Max, A. Lundquist Nicholas and J. Esdaile Louisa, Top. Curr. Chem., 2019, 377, 16 CrossRef CAS PubMed.
- D. A. Boyd, Angew. Chem., Int. Ed., 2016, 55, 15486–15502 CrossRef CAS PubMed.
- M. J. H. Worthington, R. L. Kucera and J. M. Chalker, Green Chem., 2017, 19, 2748–2761 RSC.
-
C. Goodyear, US Pat., US3633A, 1844 Search PubMed.
- B. Meyer, Chem. Rev., 1964, 64, 429–451 CrossRef CAS.
-
Elemental Sulfur; Chemistry and Physics, ed. B. Meyer, 1965 Search PubMed.
- B. Meyer, Inorg. Sulphur Chem., 1968, 241–258 CAS.
- A. D. Smith, T. Thiounn, E. W. Lyles, E. K. Kibler, R. C. Smith and A. G. Tennyson, J. Polym. Sci., Part A: Polym. Chem., 2019, 57, 1704–1710 CrossRef CAS.
- B. T. Michal, C. A. Jaye, E. J. Spencer and S. J. Rowan, ACS Macro Lett., 2013, 2, 694–699 CrossRef CAS PubMed.
- J. J. Griebel, N. A. Nguyen, S. Namnabat, L. E. Anderson, R. S. Glass, R. A. Norwood, M. E. MacKay, K. Char and J. Pyun, ACS Macro Lett., 2015, 4, 862–866 CrossRef CAS PubMed.
- A. J. R. Amaral and G. Pasparakis, Polym. Chem., 2017, 8, 6464–6484 RSC.
- M. Arslan, B. Kiskan and Y. Yagci, Sci. Rep., 2017, 7, 1–11 CrossRef CAS PubMed.
- A. Takahashi, R. Goseki, K. Ito and H. Otsuka, ACS Macro Lett., 2017, 6, 1280–1284 CrossRef CAS PubMed.
- A. D. Smith, C. D. McMillin, R. C. Smith and A. G. Tennyson, J. Polym. Sci., 2020, 58, 438–445 CrossRef CAS.
- A. D. Smith, R. C. Smith and A. G. Tennyson, Sustainable Chem. Pharm., 2020, 16, 100249 CrossRef.
- A. D. Smith, R. C. Smith and A. G. Tennyson, Sustainable Chem., 2020, 1, 209–237 CrossRef.
- C. V. Lopez, M. S. Karunarathna, M. K. Lauer, C. P. Maladeniya, T. Thiounn, E. D. Ackley and R. C. Smith, J. Polym. Sci., 2020, 58, 2259–2266 CrossRef CAS.
- A. Hoefling, Y. J. Lee and P. Theato, Macromol. Chem. Phys., 2017, 218, 1600303 CrossRef.
- M. J. H. Worthington, R. L. Kucera, I. S. Albuquerque, C. T. Gibson, A. Sibley, A. D. Slattery, J. A. Campbell, S. F. K. Alboaiji, K. A. Muller, J. Young, N. Adamson, J. R. Gascooke, D. Jampaiah, Y. M. Sabri, S. K. Bhargava, S. J. Ippolito, D. A. Lewis, J. S. Quinton, A. V. Ellis, A. Johs, G. J. L. Bernardes and J. M. Chalker, Chem. - Eur. J., 2017, 23, 16219–16230 CrossRef CAS PubMed.
- J. A. Smith, S. J. Green, S. Petcher, D. J. Parker, B. Zhang, M. J. H. Worthington, X. Wu, C. A. Kelly, T. Baker, C. T. Gibson, J. A. Campbell, D. A. Lewis, M. J. Jenkins, H. Willcock, J. M. Chalker and T. Hasell, Chem. - Eur. J., 2019, 25, 10433–10440 CrossRef CAS PubMed.
- A. Gupta, M. J. H. Worthington, H. D. Patel, M. R. Johnston, M. Puri and J. M. Chalker, ACS Sustainable Chem. Eng., 2022, 10, 9022–9028 CrossRef CAS.
- M. P. Crockett, A. M. Evans, M. J. H. Worthington, I. S. Albuquerque, A. D. Slattery, C. T. Gibson, J. A. Campbell, D. A. Lewis, G. J. L. Bernardes and J. M. Chalker, Angew. Chem., Int. Ed., 2016, 55, 1714–1718 CrossRef CAS PubMed.
- S. Oishi, K. Oi, J. Kuwabara, R. Omoda, Y. Aihara, T. Fukuda, T. Takahashi, J.-C. Choi, M. Watanabe and T. Kanbara, ACS Appl. Polym. Mater., 2019, 1, 1195–1202 CrossRef CAS.
- C. P. Maladeniya, M. S. Karunarathna, M. K. Lauer, C. V. Lopez, T. Thiounn and R. C. Smith, Mater. Adv., 2020, 1, 1665–1674 RSC.
- M. K. Lauer, A. G. Tennyson and R. C. Smith, ACS Appl. Polym. Mater., 2020, 2, 3761–3765 CrossRef CAS.
- T. Thiounn, A. G. Tennyson and R. C. Smith, RSC Adv., 2019, 9, 31460–31465 RSC.
- M. S. Karunarathna, A. G. Tennyson and R. C. Smith, J. Mater. Chem. A, 2020, 8, 548–553 RSC.
- M. S. Karunarathna and R. C. Smith, Sustainability, 2020, 12, 734–748 CrossRef CAS.
- M. S. Karunarathna, M. K. Lauer, T. Thiounn, R. C. Smith and A. G. Tennyson, J. Mater. Chem. A, 2019, 7, 15683–15690 RSC.
- M. S. Karunarathna, M. K. Lauer and R. C. Smith, J. Mater. Chem. A, 2020, 8, 20318–20322 RSC.
- M. K. Lauer, T. A. Estrada-Mendoza, C. D. McMillen, G. Chumanov, A. G. Tennyson and R. C. Smith, Adv. Sustainable Syst., 2019, 3, 1900062 CrossRef CAS.
- M. K. Lauer, M. S. Karunarathna, A. G. Tennyson and R. C. Smith, Mater. Adv., 2020, 1, 590–594 RSC.
- M. K. Lauer, M. S. Karunarathna, G. Tennyson Andrew and R. C. Smith, Mater. Adv., 2020, 1, 2271–2278 RSC.
- X. Wu, J. A. Smith, S. Petcher, B. Zhang, D. J. Parker, J. M. Griffin and T. Hasell, Nat. Commun., 2019, 10, 10035–10044 Search PubMed.
- P. Yan, W. Zhao, F. McBride, D. Cai, J. Dale, V. Hanna and T. Hasell, Nat. Commun., 2022, 13, 4824 CrossRef CAS PubMed.
- B. Zhang, S. Petcher and T. Hasell, Chem. Commun., 2019, 55, 10681–10684 RSC.
- S. Sahu and B. Lochab, ACS Sustainable Chem. Eng., 2022, 10, 12355–12364 CrossRef CAS.
- M. Mann, P. J. Pauling, S. J. Tonkin, J. A. Campbell and J. M. Chalker, Macromol. Chem. Phys., 2022, 223, 2100333 CrossRef CAS.
- N. A. Lundquist, A. D. Tikoalu, M. J. H. Worthington, R. Shapter, S. J. Tonkin, F. Stojcevski, M. Mann, C. T. Gibson, J. R. Gascooke, A. Karton, L. C. Henderson, L. J. Esdaile and J. M. Chalker, Chem. - Eur. J., 2020, 26, 10035–10044 CrossRef CAS PubMed.
- J. Jia, J. Liu, Z.-Q. Wang, T. Liu, P. Yan, X.-Q. Gong, C. Zhao, L. Chen, C. Miao, W. Zhao, S. Cai, X.-C. Wang, A. I. Cooper, X. Wu, T. Hasell and Z.-J. Quan, Nat. Chem., 2022, 14, 1249–1257 CrossRef CAS PubMed.
- M. S. Karunarathna, M. K. Lauer, A. G. Tennyson and R. C. Smith, Polym. Chem., 2020, 11, 1621–1628 RSC.
- T. Thiounn, M. S. Karunarathna, L. M. Slann, M. K. Lauer and R. C. Smith, J. Polym. Sci., 2020, 58, 2943–2950 CrossRef CAS.
- J. M. Lee, G. Y. Noh, B. G. Kim, Y. Yoo, W. J. Choi, D.-G. Kim, H. G. Yoon and Y. S. Kim, ACS Macro Lett., 2019, 8, 912–916 CrossRef CAS PubMed.
- J. Zhang, B. Fidalgo, A. Kolios, D. Shen and S. Gu, Sustainable Energy Fuels, 2017, 1, 1788–1794 RSC.
- J. Zhang, B. Fidalgo, D. Shen, R. Xiao and S. Gu, J. Anal. Appl. Pyrolysis, 2016, 122, 323–331 CrossRef CAS.
- C. Puglisi, L. Sturiale and G. Montaudo, Macromolecules, 1999, 32, 2194–2203 CrossRef CAS.
- L.-H. Lee, J. Polym. Sci., Part A: Gen. Pap., 1964, 2, 2859–2873 CrossRef.
- A. Davis and J. Golden, Macromol. Chem. Phys., 2003, 110, 180–184 CrossRef.
- A. Davis and J. H. Golden, Macromol. Chem. Phys., 1964, 78, 16–23 CrossRef CAS.
- A. Davis and J. H. Golden, J. Chem. Soc. B, 1968, 40–45, 10.1039/J29680000040.
- K. B. Abbås, Polymer, 1980, 21, 936–940 CrossRef.
- A. C. Hagenaars, W. J. Goddrie and C. Bailly, Polymer, 2002, 43, 5043–5049 CrossRef CAS.
- B. N. Jang and C. A. Wilkie, Thermochim. Acta, 2005, 426, 73–84 CrossRef CAS.
- B. N. Jang and C. A. Wilkie, Polym. Degrad. Stab., 2004, 86, 419–430 CrossRef CAS.
- E. V. Antonakou and D. S. Achilias, Waste Biomass Valorization, 2013, 4, 9–21 CrossRef CAS.
- S. T. Nguyen, E. A. McLoughlin, J. H. Cox, B. P. Fors and R. R. Knowles, J. Am. Chem. Soc., 2021, 143, 12268–12277 CrossRef CAS PubMed.
- T. Thiounn and R. C. Smith, J. Polym. Sci., 2020, 58, 1347–1364 CrossRef CAS.
- D. S. Tarbell and D. P. Harnish, Chem. Rev. (Washington, DC, U. S.), 1951, 49, 1–90 CrossRef CAS.
- D. P. Harnish and D. S. Tarbell, J. Am. Chem. Soc., 1948, 70, 4123–4127 CrossRef CAS PubMed.
- T. Thiounn, M. K. Lauer, M. S. Karunarathna, A. G. Tennyson and R. C. Smith, Sustainable Chem., 2020, 1, 183–197 CrossRef.
- D. P. Harnish and D. S. Tarbell, J. Am. Chem. Soc., 1948, 70, 4123–4127 CrossRef CAS PubMed.
- P. Eyer, F. Worek, D. Kiderlen, G. Sinko, A. Stuglin, V. Simeon-Rudolf and E. Reiner, Anal. Biochem., 2003, 312, 224–227 CrossRef CAS PubMed.
- M. K. Lauer, T. A. Estrada-Mendoza, C. D. McMillen, G. Chumanov, A. G. Tennyson and R. C. Smith, Adv. Sustainable Syst., 2019, 3, 1900062 CrossRef CAS.
- M. K. Lauer, M. S. Karunarathna, A. G. Tennyson and R. C. Smith, Mater. Adv., 2020, 1, 2271–2278 RSC.
- C. V. Lopez, A. D. Smith and R. C. Smith, RSC Adv., 2022, 12, 1535–1542 RSC.
- B. Zhang, H. Gao, P. Yan, S. Petcher and T. Hasell, Mater. Chem. Front., 2020, 4, 669–675 RSC.
- P. Yan, W. Zhao, B. Zhang, L. Jiang, S. Petcher, J. A. Smith, D. J. Parker, A. I. Cooper, J. Lei and T. Hasell, Angew. Chem., Int. Ed., 2020, 59, 13371–13378 CrossRef CAS PubMed.
- S. J. Tonkin, C. T. Gibson, J. A. Campbell, D. A. Lewis, A. Karton, T. Hasell and J. M. Chalker, Chem. Sci., 2020, 11, 5537–5546 RSC.
- A. D. Tikoalu, N. A. Lundquist and J. M. Chalker, Adv. Sustainable Syst., 2020, 4, 1900111 CrossRef CAS.
- J. M. Chalker, M. J. H. Worthington, N. A. Lundquist and L. J. Esdaile, Top. Curr. Chem., 2019, 377, 1–27 CrossRef CAS PubMed.
- J. M. Scheiger, C. Direksilp, P. Falkenstein, A. Welle, M. Koenig, S. Heissler, J. Matysik, P. A. Levkin and P. Theato, Angew. Chem., Int. Ed., 2020, 59, 18639–18645 CrossRef CAS PubMed.
- M. E. Duarte, B. Huber, P. Theato and H. Mutlu, Polym. Chem., 2020, 11, 241–248 RSC.
- D. T. Nguyen, A. Hoefling, M. Yee, G. T. H. Nguyen, P. Theato, Y. J. Lee and S.-W. Song, ChemSusChem, 2019, 12, 480–486 CrossRef CAS PubMed.
- H. Mutlu, P. Theato, B. Ceper Ezgi, M. Ozmen Mehmet, X. Li, J. Yang, W. Dong, P. Theato and J. Yang, Macromol. Rapid Commun., 2019, 40, e1800650 CrossRef PubMed.
- A. Hoefling, D. T. Nguyen, P. Partovi-Azar, D. Sebastiani, P. Theato, S.-W. Song and Y. J. Lee, Chem. Mater., 2018, 30, 2915–2923 CrossRef CAS.
- A. Hoefling, D. T. Nguyen, Y. J. Lee, S.-W. Song and P. Theato, Mater. Chem. Front., 2017, 1, 1818–1822 RSC.
- Z. Chen, J. Droste, G. Zhai, J. Zhu, J. Yang, M. R. Hansen and X. Zhuang, Chem. Commun., 2019, 55, 9047–9050 RSC.
- F. Zhao, Y. Li and W. Feng, Small Methods, 2018, 2, 1–34 CAS.
- C. V. Lopez, C. P. Maladeniya and R. C. Smith, Electrochem, 2020, 1, 226–259 CrossRef.
- J. J. Griebel, S. Namnabat, E. T. Kim, R. Himmelhuber, D. H. Moronta, W. J. Chung, A. G. Simmonds, K.-J. Kim, J. van der Laan, N. A. Nguyen, E. L. Dereniak, M. E. MacKay, K. Char, R. S. Glass, R. A. Norwood and J. Pyun, Adv. Mater., 2014, 26, 3014–3018 CrossRef CAS PubMed.
- H.-K. Lin, Y.-S. Lai and Y.-L. Liu, ACS Sustainable Chem. Eng., 2019, 7, 4515–4522 CrossRef CAS.
- A. M. Abraham, S. V. Kumar and S. M. Alhassan, Chem. Eng. J., 2018, 332, 1–7 CrossRef CAS.
- D. J. Parker, H. A. Jones, S. Petcher, L. Cervini, J. M. Griffin, R. Akhtar and T. Hasell, J. Mater. Chem. A, 2017, 5, 11682–11692 RSC.
- S. Akay, B. Kayan, D. Kalderis, M. Arslan, Y. Yagci and B. Kiskan, J. Appl. Polym. Sci., 2017, 134, 45306 CrossRef.
- T. Hasell, D. J. Parker, H. A. Jones, T. McAllister and S. M. Howdle, Chem. Commun., 2016, 52, 5383–5386 RSC.
- S. F. do Valle, A. S. Giroto, H. P. G. Reis, G. G. F. Guimarães and C. Ribeiro, J. Agric. Food Chem., 2021, 69, 2392–2402 CrossRef CAS PubMed.
- S. F. Valle, A. S. Giroto, R. Klaic, G. G. F. Guimaraes and C. Ribeiro, Polym. Degrad. Stab., 2019, 162, 102–105 CrossRef CAS.
- M. Mann, J. E. Kruger, F. Andari, J. McErlean, J. R. Gascooke, J. A. Smith, M. J. H. Worthington, C. C. C. McKinley, J. A. Campbell, D. A. Lewis, T. Hasell, M. V. Perkins and J. M. Chalker, Org. Biomol. Chem., 2019, 17, 1929–1936 RSC.
Footnote |
† Electronic supplementary information (ESI) available: Characterization including NMR spectra, GC-MS data, TGA and DSC data, SEM images. See DOI: https://doi.org/10.1039/d2su00138a |
|
This journal is © The Royal Society of Chemistry 2023 |
Click here to see how this site uses Cookies. View our privacy policy here.