DOI:
10.1039/D2SU00105E
(Critical Review)
RSC Sustainability, 2023,
1, 404-417
A critical review of the production of hydroxyaromatic carboxylic acids as a sustainable method for chemical utilisation and fixation of CO2
Received
19th November 2022
, Accepted 11th March 2023
First published on 13th March 2023
Abstract
Hydroxyaromatic carboxylic acids (HACAs) such as salicylic acids, hydroxynaphthoic acids and their halogenated derivatives are essential feedstocks for the pharmaceutical, dye, fragrance, cosmetic and food industries. Large-scale production of HACAs is currently based on the Kolbe–Schmitt reaction between CO2 and petroleum-based phenolic compounds. This batch reaction is carried out at ∼125 °C, ∼85 bar and reaction times of up to 18 hours to achieve high conversions (≈99%). The long reaction times and dependence on fossil-derived phenols have negative sustainability implications. However, as a CO2-based process, HACA production has the potential for large-volume anthropogenic CO2 sequestration and contributes to net zero. A big challenge is that the current global production capacity of HACAs uses only about 41
450 tonnes per year of CO2 which is just ≈0.00012% of the annual anthropogenic emissions. Therefore, significant efforts are needed to increase both the sustainable production and demand for such CO2-based products to enhance their economic and environmental sustainability. This review covers the basic kinetic and thermodynamic stability of CO2. Thereafter, a comprehensive coverage of early and current developments to improve the carboxylation of phenols to make HACAs is given, while discussing their industrial potential. Moreover, it covers new propositions to use biomass-derived phenolic compounds for sustainable production of HACAs. There is also a need to expand the uses and applications of HACAs and recent reports on the production of HACA-based recyclable vinyl polymers point in the right direction.
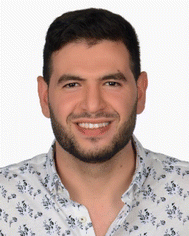 Omar Mohammad | Omar Mohammad received his B.Eng. (2020) in Chemical Engineering from Aston University, Birmingham (UK) with a placement year in Munich. During his placement at the Technical University of Munich, Omar worked on developing heterogeneous catalysts for dehydrogenation of light alkanes. After graduation, Omar worked as a R&D assistant at Stoli Chem (2020). He participated in designing a continuous reactor technology and managed feasibility projects on catalytic hydrogenation. He is currently a PhD candidate at the Energy & Bioproducts Research Institute (EBRI) working on the production of hydroxyaromatic carboxylic acids from waste lignin under the supervision of Dr Jude Onwudili and Dr Qingchun Yuan. |
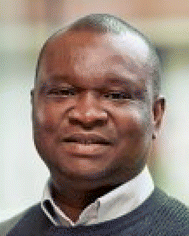 Jude A. Onwudili | Dr Jude Onwudili is a Senior Lecturer in Chemical Engineering at Aston University, Birmingham (UK) and a Fellow of the Royal Society of Chemistry. He obtained his PhD in Chemical and Process Engineering in 2015 at the University of Leeds (UK), where he held several research and teaching positions before joining Aston. He is an expert in advanced thermo-catalytic processing of biomass and wastes and currently leads a Sustainable Fuels and Chemicals (SFC) Group within Aston's Energy and Bioproducts Research Institute. He has published over 100 academic papers, with more than 4700 citations and an h-index of 39. |
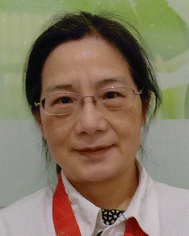 Qingchun Yuan | Dr Qingchun Yuan is a Lecturer in Chemical Engineering at Aston University and an IChemE Chartered Chemical Engineer. She received her first degree in Chemical Engineering from Dalian University of Technology in 1986 and her PhD in Polymer Science and Engineering from Nottingham Trent University in 2005. Her research expertise lies in the multidisciplinary area of surface/interface science and engineering, catalyst development, membranes and nanotechnology. Her current research interest is in developing negative emission technologies for GHG removal and sustainable processing. Dr Yuan has published more than 40 peer-reviewed journal papers with an h-index of 22. |
Sustainability spotlight
Carbon capture, utilisation and storage (CCUS), through chemical fixation of anthropogenic CO2 in organic chemicals such as hydroxyaromatic carboxylic acids (HACAs), has the potential to contribute to a circular economy and net zero. At present, commercial production of HACAs via the Kolbe–Schmitt reaction involves the use of unsustainable fossil-derived phenols and long reaction times in batch reactors. This present work critically reviews the historical and current research efforts to find various pathways to promote sustainable production of HACAs as well as expand their uses and applications. Industrial-scale production of HACAs from CO2 and sustainable biomass-derived phenols aligns with the following UNSDGs; SDG9 ‘Industry, Innovation and Infrastructure’; SDG12 ‘Responsible Consumption and Production’; and SDG13 ‘Climate Action’.
|
1 Introduction
The concentration of carbon dioxide (CO2) in the atmosphere has increased since the beginning of the industrial era, from approximately 277 parts per million (ppm) to nearly 410 ppm in 2019 due to anthropogenic emissions.1,2 Scientific evidence indicates that the increase in atmospheric CO2 concentration has been primarily caused by fossil fuel burning, cement production, deforestation and other land-use activities, in particular, large-scale farming and agriculture.3 Presently, global anthropogenic CO2 emissions are about 34 billion tonnes per year and it is anticipated to continuously increase in the coming years.1
The most obvious way of reducing the concentration of CO2 in the atmosphere is to stop its release through burning of carbon-based fuels (both fossil and non-fossil). Atmospheric CO2 concentrations can also be reduced through industrial-scale fixation of CO2 through carbon capture, utilisation and storage (CCUS) technologies. Presently around 230 million tonnes of CO2 are used every year as raw material, ingredient and chemical feedstock across various sectors.4 North America accounts for 33% of the current global demand for CO2, followed by China with 21% and Europe at 16%. These three regions, therefore, account for more than two-thirds of global CO2 demand, with the market for existing uses expected to grow in the coming years.4 There are two possible approaches to using CO2 as a chemical, namely the direct approach,4,5 and the chemical conversion approach.6 Unfortunately, most of these uses are short-lived, meaning that they release CO2 back into the atmosphere within a short period of time. These short-lived uses include urea production, which consumes around 130 million tonnes of CO2 annually,4 through the Snamprogetti urea process. In addition, enhanced oil recovery (EOR) consumed between 70 and 80 million tonnes of CO2 per annum. Other sectors that use CO2 without long-term storage include metal fabrication, healthcare, fire extinguishers, dry cleaning and production of food and beverages. Indeed, urea production and EOR consume nearly 90% of all annual CO2 being currently used. However, for chemical fixation to contribute to CO2 emission reduction, its use in the production of durable chemical products must be encouraged. There are other chemical fixation processes being developed for CO2 utilisation including the production of inorganic materials such as limestone and aggregates7 as well as the production of organic compounds such as methanol,8 cyclic carbonates,9 hydroxy aromatic carboxylic acids (HACAs)10 and polycarbonates.11 Although the current global demand for CO2-based organic chemicals lacks the potential to valorise enough CO2 emissions to make a major contribution to meeting the global reduction objectives, it can play a major role to meet global goals as part of an “all technologies” approach.4,12 For instance, every year around 100 million tonnes of methanol are produced, with a yield of 728 kg per tonne of CO2 consumed.13 Hence, global methanol production via CO2 hydrogenation would require around 140 million tonnes of CO2 each year. While this is only 0.4% of current anthropogenic CO2 emissions, it sounds promising as future increases in the demand for methanol and other CO2-based organic chemical are possible.
One group of CO2-based chemicals with potential high future demands is HACAs, due to the versatility of their possible uses and applications. Notable HACAs include salicylic acids, hydroxynaphthoic acids and various halogenated derivatives that may be employed as intermediates or starting materials in the pharmaceutical,14–16 dye,17,18 fragrance,19 cosmetic,20,21 food21,22 and bioplastic industries.23–25 Currently, commercial quantities of HACAs are produced via the Kolbe–Schmitt reaction between phenolic compounds and CO2. Thus, increasing the production, uses and applications of HACAs can contribute to increased CO2 utilisation and long-term CO2 sequestration.
Even though CO2 is being consumed in the Kolbe–Schmitt reaction, reducing the energy demand and using renewable energy from low-carbon or carbon-free sources are hugely important that can also contribute to the CCUS strategy.26 In addition, the production of durable solid materials from HACAs can offer long-term carbon storage capability and, therefore, can be considered as a method of CO2 sequestration.12 In contrast, the manners of usage of urea and methanol mean they can only store CO2 for limited periods of time. For instance, using CO2-derived methanol as fuel means realising it back to the environment arguably before the benefits of CCUS are realised.26 Instead, producing engineering and construction plastics from HACAs27 can give much longer sequestration and sustainability advantages, whether they are biodegradable or non-biodegradable.28 However, there is a stronger case for CO2-derived non-biodegradable plastics with a longer lifespan to contribute to the CCUS strategy by being incorporated into long-term products.29
There are established methods for production of aromatic carboxylic acids such as the oxidation of alkyl benzenes (Scheme 1),30,31 or through hydrolysis of aromatic amides (Scheme 2).32 Yet, the Kolbe–Schmitt reaction still remains the most straightforward method for accessing many HACAs.33,34
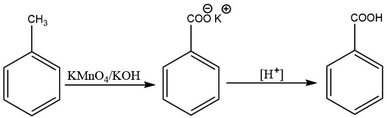 |
| Scheme 1 Model for oxidation of alkylarenes to aromatic carboxylic acids. | |
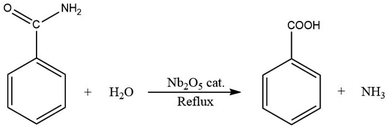 |
| Scheme 2 Hydrolysis of aromatic amides to aromatic carboxylic acids. | |
Production of HACAs generally involves a two-stage reaction. First, production of dry alkali metal salt of hydroxy aromatics or phenolic compounds e.g., sodium phenoxide followed by carboxylation at moderate temperatures and high pressures (125 °C and 85 bar) in batch mode. Hence, many research efforts have focused on improving the current carboxylation method since the original report in 1884.10,35 However, most of the developed methods have not been industrially adopted due to their limitations at scale, safety concerns and high costs. There is also the chemical barrier of the difficulty of inducing enough nucleophilicity to a level that promotes the addition of CO2 to monohydric aromatic compounds, which accounts for most industrial HACA production.
This review, therefore, critically analyses each of the developed carboxylation methods by using phenol as a model compound. This review also discusses (i) possible conversion routes via the Kolbe–Schmitt reaction, (ii) background on how the Kolbe–Schmitt reaction has been developed, (iii) the proposed mechanisms of the carboxylation reaction, (iv) critical analysis of each of the developed carboxylation methods and their setbacks and finally, (vi) identify gaps in the research area as well as proposing a new synthetic procedure that has the potential to move from the reliance of HACAs from crude oil to biomass-derived-HACAs.
2 Thermodynamic and kinetic stability of CO2
CO2 is a highly stable molecule due to its linear structure, strong covalent bonds and low energy state. It is weakly acidic which makes it able to readily react with inorganic basic oxides. Hence, the most extensive natural reactions of CO2 are the formation of metal carbonates (e.g., limestone) and hydrogen carbonates due to its weakly acidic nature.36 However, chemical fixation of CO2 into organic compounds requires high temperatures and pressures to overcome these energy barriers.37 Since most emissions arise from human activities relating to the use of organic carbons in fossil fuels, the most efficient utilisation of captured CO2 should be to make new organic molecules. This will help to establish a sustainable anthropogenic carbon cycle38 and thereby promote a circular economy. Presently, only a few industrial processes utilise CO2 as a raw material to make organic chemicals due to its thermodynamic and kinetic stability. In other words, CO2 has a strong covalent bond, which means it requires a lot of energy to undergo a chemical transformation.39 Most CO2 conversions are catalytically promoted.38 Thus, only a few specific reactions of CO2 are well known and commercially useful.
In its ground state, the CO2 molecule is a linear triatomic molecule belonging to the D∞h point group. The central carbon atom possesses sp hybridisation, meaning both C
O bonds have equivalent orbitals with a C–O distance of 116 pm. Each of the C–O bonds has a dipole moment with the same magnitude but in opposite directions. Because of its linearity, the dipoles associated with each C–O bond cancel each other out, see Fig. 1. Such a facet makes the CO2 molecule non-polar and exhibit remarkable kinetic and thermodynamic stability.37
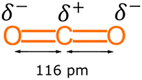 |
| Fig. 1 Chemical structure of the CO2 molecule. | |
The strong electronegativity differences between carbon and oxygen enable CO2 to exhibit amphoteric character, having both Lewis basic character at oxygen and Lewis acidic character at the carbon. These characteristics influence CO2 binding to transition metals. In this case, metals with high oxidation states predominantly interact with the oxygen atoms whereas metals with low oxidation states mainly interact with the carbon atom.37,40 However, CO2 is a stronger acceptor of electron density than a donor; therefore, the molecule's reactivity is driven by the electrophilic character of carbon rather than the weak nucleophilic characteristics of the oxygen atoms.37 In other words, due to the electron deficiency of the carbonyl carbon of the CO2 molecule, it has stronger affinity towards electron-donating species and nucleophiles which is observed in the Kolbe–Schmitt reaction.39
3 Historical developments of the Kolbe-type carboxylation reactions
Kolbe developed one of the few industrially relevant CO2-based methods in 1860.41 This was achieved through heating a mixture of phenol and sodium in the presence of CO2 at atmospheric pressure. The reaction proceeded via the formation of sodium salicylate which was consequently dissolved in water and precipitated into salicylic acid upon acidification (Scheme 3).33
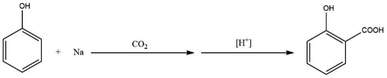 |
| Scheme 3 Kolbe's first developed carboxylation reaction in the 1860s. | |
Kolbe needed to prepare a considerable amount of salicylic acid a few years later. However, the initial work was not easily scalable, as salicylic acid yields varied significantly under seemingly similar reaction conditions. In order to correct this variation in yield, Kolbe discovered that one-half of the initial amount of phenol was volatilized from the reaction mixture. He also discovered that not only was sodium salicylate produced in the reaction, but also sodium phenoxide and sodium carbonate. From this observation, Kolbe recommended a new procedure for the preparation of salicylic acid starting from sodium phenoxide (Scheme 4). This was achieved by evaporating to dryness an equimolar solution of phenol and sodium hydroxide.
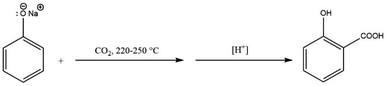 |
| Scheme 4 Kolbe's developed carboxylation method by starting with sodium phenoxide. | |
Dried sodium phenoxide was heated to 180 °C in an iron retort and CO2 passed slowly over the heated salt. The final temperature was raised to 220–250 °C and the reaction was considered complete when no more phenol could be distilled. Since half of the starting phenol was lost by volatilisation, the yield of salicylic acid never exceeded 50%.33
Schmitt enhanced Kolbe's method by carrying out the reaction under pressure in 1884, which improved the overall yield significantly.10 In a closed vessel, dry sodium phenoxide was heated with carbon dioxide at 120–130 °C for several hours at a pressure of 80 to 94 bar, see Scheme 5. No phenol was lost under these conditions, and a nearly quantitative yield of salicylic acid was produced. This procedure is now known as the Kolbe–Schmitt reaction, and it is still the standard method for manufacturing a wide range of salicylic acids.
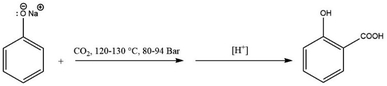 |
| Scheme 5 The industrially applied Kolbe–Schmitt reaction conducted under high pressures (80–94 bar). | |
A further variant of the Kolbe–Schmitt reaction was introduced by Marasse in 1894, see Scheme 6.42 This method involves the carbonation of a mixture of free phenol and excess anhydrous potassium carbonate under pressure and elevated temperatures to produce salicylic acid potassium salt which is followed by acidification. In many cases, the Marrase modification provides better yields as well as avoids the time-consuming preparation of hygroscopic phenoxides.33 However, industrially, the Marrase variant is economically more expensive due to the costs of the carbonates compared to metal hydroxides. In order to make the process cheaper, Marrase proposed to adjust the molar reaction, instead of excess potassium carbonate to one mole of potassium carbonate to two moles of phenol in the presence of CO2.33,42
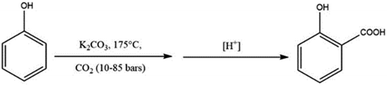 |
| Scheme 6 The Marasse modification of the Kolbe–Schmitt reaction uses an excess of anhydrous potassium carbonate. | |
Despite the efforts conducted by Marasse, the Kolbe–Schmitt reaction remains the standard method for preparation of many salicylic acids. It is important to highlight that the described method is not limited to phenols but can be applied for preparation of other aromatic carboxylic acids through carboxylation of naphthols and halogenated benzenes.
3.1 Reaction mechanisms of Kolbe–Schmitt type carboxylation reactions
Phenols contain hydroxyl (–OH) group bonded to an sp2-hybridised carbon atom of an aromatic ring. As a result, the phenoxide ion is highly stable due to the negative charge being fully delocalised over the benzene ring (Scheme 7).43
 |
| Scheme 7 Delocalisation of the alkoxide ion over the benzene ring. | |
Also, the lone pairs on the –OH oxygen atom are equally delocalised into the aromatic ring, making phenols more acidic than cyclohexanol and acyclic alcohols. Scheme 7 also shows that carboxylation is via electrophilic attack on the aromatic ring at the ortho and meta positions, which become enriched with electrons following delocalisation.
Several experimental and theoretical investigations have been conducted to elucidate the mechanism of the Kolbe–Schmitt reaction and the structure of the intermediate NaOPh–CO2 complex. As a plausible intermediate, Schmitt and Hentschel proposed that the reaction proceeded via the formation of alkali metal phenyl carbonate (PhO–CO2Na).10,33,44 Johnson proposed that ortho-substitution in an allylic system occurs due to intra-molecular chelation according to Scheme 8 (alkali-metal-induced electrophilic replacement of nuclear hydrogen by carboxyl with migration of the alkali metal to the carboxyl group).45,46
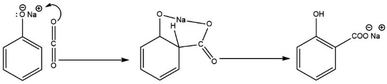 |
| Scheme 8 Johnson's proposed intramolecular chelation mechanism. | |
Hales agreed with Johnson regarding the formation of metal carboxylate as the final product. However, through an infrared absorption spectra study, he proposed a mechanism based on the preliminary association of sodium phenoxide with CO2 to form a complex followed by an intramolecular reaction with the displacement of the ortho-hydrogen by an electrophilic attack, based on Scheme 9.33,46
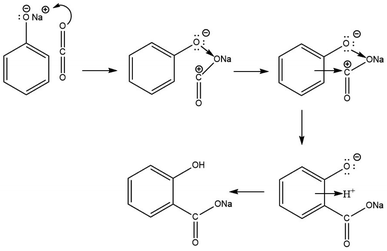 |
| Scheme 9 Hale's proposed carboxylation mechanism. | |
In 2002, Marković disclosed more precise information regarding the mechanisms of the Kolbe–Schmitt reaction when the density functional theory (DFT) was evaluated as a more accurate approach for quantum chemistry calculations.47 The DFT method revealed that the reaction between sodium phenoxide and carbon dioxide proceeds via the formation of three transition states and three intermediates. In the first step, the carbon dioxide molecule attacks a polarised O–Na bond of sodium phenoxide, forming the intermediate NaPh–CO2 complex. In the following stage, the electrophilic carbon atom attacks the ring predominantly at the ortho position, creating two new intermediates. A 1,3-proton shift from the C to the O atom produces sodium salicylate as the final product (Scheme 10).47
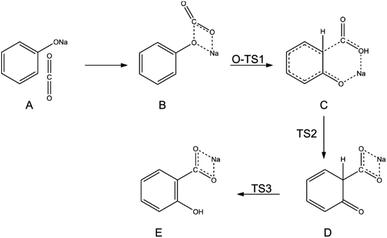 |
| Scheme 10 TS1, TS2, TS3 are the transitions states, and B, C and D are the proposed intermediates. | |
For a long time, the alkali metal phenoxide–CO2 complex had been widely accepted as an intermediate in the first stage of the reaction of phenoxide. Further studies using C-13 nuclear magnetic resonance (NMR), the general-purpose semi-empirical molecular orbital package (MOPAC) and parametric method 3 (PM3) for the study of chemical structures and reactions have revealed further details. For instance, through C-13 NMR and MOPAC/PM3 calculations,56 Kosugi et al. proved that the CO2 complex is not an intermediate that gives carboxylic acids. Contrasting previous notions, the authors proposed a competitor that decomposes thermally (<100 °C) to phenoxide, which then undergoes further competitive reactions. On this basis, a carbonate-like complex (PhOK–CO2) that undergoes direct carboxylation was proposed as the intermediate of the Kolbe–Schmitt reaction.57 In accordance with experimental results obtained by the NMR and infra-red (IR) measurements, Marković et al. later vaguely supported the idea of the existence of the PhOK–CO2 complex and, however, negated the mechanism of direct carboxylation of the benzene ring. It suggested that under reduced pressure of carbon dioxide, the complex is not solvated with the CO2 molecules – hence no reaction occurs. In contrast, at high pressure and temperature, carbon dioxide behaves as a solvent, and the KOPh–CO2 complex becomes solvated with one or two CO2 molecules. One of the added CO2 moieties performs an electrophilic attack on the benzene ring, whereas the old CO2 moiety becomes a molecule of solvent.58
4 Recent carboxylation methods
Since the Kolbe–Schmitt reaction was first reported in 1884,10 numerous investigations have focused on overcoming either the two-pot, high pressure or batch mode nature of the industrially applied carboxylation process. This has led to the development of various carboxylation methodologies, categorised by the use of novel activation/carboxylation agents,53,55 heterogeneous catalysts48–52 and homogeneous stoichiometric reagents35,53,54 as shown in Table 1. These new developments attempt to reduce the long reaction times and high CO2 pressures that characterise the conventional Kolbe–Schmitt reaction.
Table 1 Recently developed carboxylation methodologies since the Kolbe–Schmitt reaction
Phenol feedstock |
Catalyst type |
Catalyst/reagent |
Solvent |
Reactor |
Yield |
Reference |
Phenol-3-methoxy |
— |
NaH |
— |
Balloon and vial |
80% |
48
|
Phenol |
Heterogeneous |
C@Fe–Al2O3 |
H2O |
250 ml three-necked round-bottom flask |
<5% |
49
|
Phenol |
Heterogeneous |
Ag@ZIF |
— |
Gas flow cell |
— |
50
|
Phenol |
Heterogeneous |
AlBr3 |
scCO2 |
50 ml autoclave |
55.9% |
51
|
Phenol |
— |
Sodium ethyl carbonate |
— |
100 ml glass placed in a stainless steel autoclave |
87.4% |
52
|
Resorcinol |
— |
1,8-Diazabicyclo[5.4.0]undec-7-ene (DBU) |
Dimethylformamide (DMF) |
Pressure tube inside a stirred autoclave |
>99% |
35
|
Resorcinol |
— |
KHCO3 |
H2O |
Micro-reactors |
37% |
53 and 54 |
Resorcinol |
Ionic liquids |
1-Ethyl-3-methylimidazolium hydrogen carbonate |
MeOH/H2O (2 : 3) |
Microwave-assisted 80 ml quartz reactor |
62% |
55
|
Resorcinol |
1-Ethyl-3-methylimidazolium hydrogen carbonate |
MeOH/H2O (2 : 3) |
1/16-Inch capillary reactor |
57% |
53
|
4.1 Novel activation/carboxylation agents
4.1.1 Alkali metal hydrides.
The use of alkali metal hydrides as activating reagents to promote the carboxylation of phenol has been reported. It is regarded as an efficient method to produce aromatic hydroxycarboxylic acids at high yields. This new method involves a one-pot reaction of NaH with a phenolic compound at atmospheric CO2 pressures (Scheme 11).
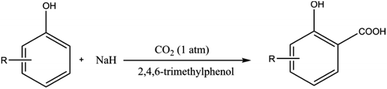 |
| Scheme 11 Carboxylation reaction using alkali-metal-hydrides at atmospheric pressure. | |
Using NaH instead of NaOH prevents the formation of water during the deprotonation of the phenolic compound, thereby providing direct access to salicylic acid derivatives without the need of preparing and drying sodium phenoxide. It is important to highlight that 2,4,6-trimethylphenol as a recyclable additive significantly increased the initial reaction rate as well as improved the final yield of the carboxylation. It was suggested that the additive 2,4,6-trimethylphenol acts as an aid for CO2 capture.48 However, sodium hydride (NaH), when used with certain solvents, can undergo exothermic decomposition at relatively low temperatures generating heat and incondensable gases, leading to a runaway reaction or even an explosion.59
4.1.2 Carboxylation with alkyl carbonates.
In 1983, Marasse invented the first carboxylation of phenols utilising alkali metal carbonates as a modification on the industrially applied Kolbe–Schmitt reaction, with the aim of avoiding the time-consuming procedure of preparing the hygroscopic phenoxide.42 Later, Suerbaev illustrated an alternative carboxylating reagent for phenols by utilising alkali metal salts of ethylcarbonic acid (Scheme 12).52
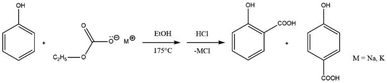 |
| Scheme 12 Carboxylation reaction using metal ethyl carbonates. | |
The two-step synthetic procedure of the alkali metal salts of ethylcarbonic acid was performed by reacting ethanol with NaOH/KOH to produce sodium or potassium ethoxide. Subsequently, this was carboxylated to synthesise sodium and potassium ethyl carbonates. The experimental procedure was carried out by loading a 100 ml glass reactor with dry powdered sodium/potassium ethyl carbonate and phenol in solvent-free mode. After the reaction, the unreacted phenols were recovered using toluene, and the conversion was calculated based on the unreacted phenols. It was reported that the optimal conditions (T = 200 °C and τ = 6 h) for the carboxylation reaction of phenol with sodium ethylcarbonate yielded 87.4% of hydroxybenzoic acid whereas the yield under optimal conditions was 63.7% using potassium ethylcarbonate.52
Since making sodium/potassium ethylcarbonate is time consuming and requires a lot of energy, starting with sodium hydroxide to make the hygroscopic sodium phenoxide remains the optimum method.
4.1.3 Ionic liquids.
Ionic liquids (ILs) are defined as compounds composed of ions with melting point below 100 °C. Despite the first ionic liquid (ethylammonium nitrate) being reported by Paul Walden in 1914,60 ionic liquids have received wider attention only in the past two decades.61 ILs exhibit a number of unique properties that make them suitable solvents for various industrial applications. High polarity, thermal stability, ionic conductivity and low volatility and melting point are some of the physiochemical properties of ILs.62 In order to investigate the applicability of ILs in the Kolbe–Schmitt reaction, hydrogencarbonate-based ILs, particularly, 1-ethyl-3-methylimidazolium hydrogencarbonate, [C2MIM][HCO3], has been investigated as an exemplary reactive solvent (Fig. 2).55
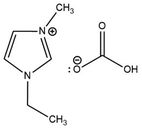 |
| Fig. 2 Chemical structure of 1-ethyl-3-methylimidazolium hydrogencarbonate. | |
Selective conversion of resorcinol to 2,4-hydroxybenzoic acid using [C2MIM][HCO3] was found to produce maximum yields of 60% at temperatures between 100 and 160 °C within 10–60 minutes in a microwave-assisted autoclave operating between 6 and 8 bars.55 Although little difference at ambient pressure was found for the carboxylating reagents [K][HCO3] and [C2MIM][HCO3],55 the production process of ILs is process-intensive. ILs as heat transfer fluids currently have significant cost disadvantages due to the lack of large-scale synthesis and the high cost of reagents.63
4.2 Heterogenous catalysts
4.2.1 Carbon coated γ-alumina pellets.
The first Kolbe–Schmitt type reaction using a heterogeneous catalyst was recently reported.49 Carbon-coated γ-alumina pellets (C@Fe–Al2O3), a new hybrid material catalyst, were synthesised to give both catalytic and hydrophobic characteristics for the phenol reaction in aqueous solutions under atmospheric pressure and mild temperature conditions, using CO2 as a feedstock.49 The Kolbe–Schmitt reaction is inhibited by the presence of water since anhydrous phenoxide is considered as the intermediate for carboxylation of the aromatic ring.10 The novel catalyst provided a gateway for the reaction to occur by allowing the phenol and CO2 to diffuse to the active sites in the carbon-coated alumina hybrid, while the aqueous solution remains outside the spheres due to their hydrophobic characteristics created by the coated carbonaceous material. The participation of Fe was not resolved; hence it was not possible for the researcher to elucidate a mechanism. The yield of salicylic acid was relatively low, <5% which was measured using HPLC.49 The poor yields can be attributed to the synergistic impact of internal and exterior mass transfer limitations of diffusion which is the porous catalyst structure and gas–liquid–solid interphase between the reactants and catalyst particles.
4.2.2 Metal–organic frameworks (MOFs).
Due to their well-defined 3D architectures, permanent porosity, and diverse chemical functionalities, metal–organic framework nanoparticles (MOF NPs) are emerging as potentially promising matrices for catalytic reactions. Advancements in methods for producing modular MOF NPs have allowed precise control over particle size, shape, and surface chemistry, hence maximising their catalytic capabilities unnnder unconventional conditions.64 A recent study has been conducted using the Kolbe–Schmitt type reaction as a model for direct C–H carboxylation of mercaptophenol (MP) using CO2 gas on active Ag nanoparticles and a zeolitic imidazolate framework (ZIF) layer (Ag@ZIF) under ambient conditions. The reaction was monitored in situ using Surface-Enhanced Raman Spectroscopy (SERS). The SERS-active Ag nanoparticle and ZIF layer exhibited unprecedented CO2meta-carboxylation that was previously deemed impossible, see Scheme 13.50 NP@MOFs are therefore a promising strategy to achieve high performance and selective CO2 valorisation without the need of elevated temperature or pressure, thus more energy efficient for an environmentally and economically sustainable gas process.
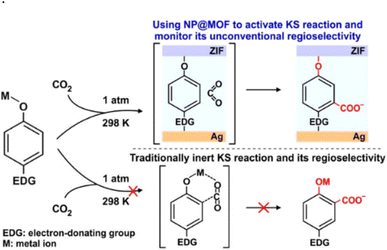 |
| Scheme 13 Carboxylation reaction in an unconventional region using MOFs and an electron donating group (Ag@ZIF). “Reprinted with permission from copyright 2020 American Chemical Society”.50 | |
Although MOFs exhibit numerous advantageous properties, the practical use of these novel materials has been restricted due to high production costs, low capacity and difficulties in regeneration. This type of Kolbe–Schmitt reaction is only a proof-of-concept at this point, and further study is necessary before it can be scaled up for commercial application.
4.2.3 Lewis acid catalyst.
The first Lewis-acid mediated carboxylation was discovered by Friedel and Crafts when CO2 was bubbled through a mixture of aluminium chloride (Al2Cl6) and benzene heated to its boiling point; a little quantity of benzoic acid was formed, along with the production of a small amount of hydrogen chloride.65 Owing to CO2's low electrophilicity and the side reactions caused by the high Lewis-acidity of aluminium-based compounds, carboxylic acids are obtained in low yields.66 The acid strength of the halogen atom is a function of the nature of the groups covalently bonded to it.67 The Lewis acid strength is enhanced by electron-withdrawing groups. For instance, AlBr3 combines the highest Lewis acidity and good solubility in non-polar solvents.51 The empty 2p orbital on the boron makes trivalent boron compounds act as Lewis acids.67 In 2008, Iijima reported an efficient regioselective carboxylation of phenol to salicylic acid with supercritical CO2 in the presence of aluminium bromide.51 Among the Lewis acid halides investigated, aluminium bromide (AlBr3) was found to be the most active. AlBr3 as the catalyst yielded 55.9% of salicylic acid at moderate temperatures (80 °C) and under supercritical CO2 conditions.
According to the original report,51 the reaction is initiated with the formation of the phenoxyaluminium dibromide intermediate. This intermediate then attacks the CO2 at its ∂+ carbon through the electron-rich carbon at the ortho position to form the aluminium salt of salicylate. However, the insertion of CO2 into the O–Al bond to form a carbonate is more likely to occur as suggested in other reports.68,69 Following the insertion of CO2 into the Al–O bond, the double bond at the ortho-position attacks the carbonate carbon, with the subsequent cleavage of the PhO–C bond to form the phenoxide ion and ortho-positioned aluminium dibromide salicylate group. This is followed by re-aromatisation through proton shift to the phenoxide oxygen to form the phenolic group as seen in Scheme 14. In the last stage, the salt is protonated by HBr to yield salicylic acid and regenerates the AlBr3 catalyst.
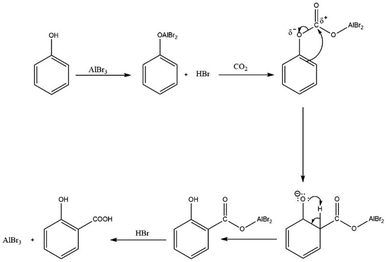 |
| Scheme 14 Proposed mechanism of carboxylation of phenols using a Lewis acid catalyst with improvement from the original report.51 | |
The results of this work provide a promising opportunity to investigate other Lewis-based catalysts. Yet, it does not solve the issues associated with batch mode operation. Moreover, using NaOH is ten times more cost-effective than using AlBr3 from the perspective of process viability.
4.3 Homogeneous stoichiometric reagents
4.3.1 Organic base.
As previously reported, forming the phenoxide ion via treatment with a basic hydroxide metal e.g., KOH and NaOH or other basic reagents e.g., KHCO3, NaHCO3 and K2CO3 is the popular route for the carboxylation of phenols.33,52,70,71 The aim of utilising a base is to increase the nucleophilicity of the benzene ring to a level that promotes CO2 addition. Unlike monohydroxylbenzenes, activated phenols such as dihydroxylbenzenes are more readily reactive and can react even in aqueous solutions.55 Therefore, a recent study anticipated that introducing dianion species using an organic base would induce enough nucleophilicity to promote the addition of CO2. This type of Kolbe–Schmitt reaction proceeded under ambient conditions through treating dihydroxybenzenes (resorcinols) with a strong organic base to synthesise the corresponding salicylic acid (Scheme 15).35
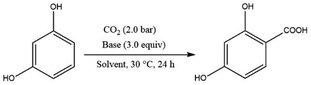 |
| Scheme 15 Carboxylation of di-hydroxy aromatic compounds mediated by an organic base under ambient conditions. | |
The Kolbe–Schmitt type reaction of resorcinol using 1,8-diazabicyclo[5.4.0]undec-7-ene (DBU) as an organic base under 2.0 MPa of CO2 at 30 °C was found to be the optimal condition in terms of yield and cost. It is important to note that the solvents had a synergistic effect in facilitating the reaction. For example, CH3CN and dimethylformamide (DMF) yielded 99% of the corresponding resorcylic acid, however, the yield was significantly reduced using toluene as a solvent.35
Aqueous solutions of organic amines including DBU are highly irritating and prolonged exposure may lead to injury to the eyes, skin and respiratory system.72 Moreover, inorganic bases such as NaOH and KOH are 10 times cheaper than organic bases. Thus, from an economic and chemistry point of view,73 the conventional Kolbe–Schmitt reaction is more favourable. Despite the flaws of this research, it provides a gateway for further research in testing immobilised organic base catalysts as a novel route for the Kolbe–Schmitt reaction which has not been conducted before.
5 Attempts on continuous carboxylation systems
Most industrial and laboratory-scale attempts to produce HACAs have relied on batch processing due to the prolonged reaction times required for the chemical transformation. However, there are several reports in the literature on attempts to use continuous processing for HACA production. For example, to test and validate the implementation of continuous flow in the Kolbe–Schmitt reaction, Hessel carried out the first aqueous Kolbe–Schmitt synthesis using resorcinol to yield 2,4-dihydroxybenzoic acid in a microreactor rig.70 Resorcinol was reacted with aqueous KHCO3 at high temperatures (up to 200 °C) and pressures (up to 74 bar) which shortened the reaction time from 2 hours to less than a minute. The maximum yield of resorcylic acids at optimised protocol settings was 48%; however, due to short reaction times, the microreactor increased the space-time yields by a factor of 440 compared to a batch process.70
Ionic liquids were also investigated in a continuous 1/16-inch capillary reactor using reactive imidazolium-based ionic liquids with a hydrogen carbonate anion. 1-Ethyl-3-methylimidazolium hydrogen carbonate (EMIM-HC, C7H12N2O3, 172.18 g mol−1) exhibited maximum yields of 57% for 220 °C and a residence time of 32 s or for only 6.5 s at 200 °C, which exceeded the best results obtained for the aqueous KHCO3-based Kolbe–Schmitt synthesis by 13%.53
Later, in 2008 as part of the German Federal Environmental Foundation's financing cluster “Novel Process Windows”, the potential of continuous processing with the aim to intensify the Kolbe–Schmitt synthesis using the example of the 2,4-dihydroxybenzoic acid from resorcinol was experimented. Krtschil and his co-workers revealed that the micro-structured reactor resulted in tenfold higher productivity (0.75 tonnes per annum) with the ability of further scalability compared to the capillary reactor of different scales (1/8 inch and 1/18 inch).53 It is worth noting that the CO2-donating salt, KHCO3, produced higher yields (58%) and activity, indicating that hydrogen carbonates are preferable to carbonates. The results obtained from the laboratory scale were scaled up to the pilot scale. This was achieved through a set of tailor-made electrically heated micro-structured reactors comprising 40 microchannels. This enabled space–time yields up to 28
800 kg m−3 h−1 at a product yield of 32%. Despite low yields, the space–time yields were significantly improved due to reduced reaction times from hours to a few seconds.54
Using continuous processing for the Kolbe–Schmitt type reaction means that time and energy can be saved by avoiding frequent loading, unloading, and heating up and cooling down cycles. Furthermore, the high surface area of the reactor wall increases heat transfer, allowing efficient heat management – saving both energy and costs. In any case, the drawbacks of continuous flow chemistry are inevitable; small reactor diameters increase the chances of cloggages and blockages leading to unstable plant operation. Micro-reactors used as a green route are limited to large-scale productions.74 Mixing in narrow diameters is static and arises from fluid velocity and pressure, which influences important process parameters including reaction kinetics, fluid mechanics and thermodynamics. Therefore, many continuous flow technologies have not been implemented at a commercial scale. If this CCUS option is to play a role at a commercial scale, continuous flow reactor technology that is easily scalable needs to be developed.
6 Trends and future perspectives on HACA production
While new carboxylation methods are gaining attention, none of them has been tested at an industrial scale due to several reasons. Some of the limitations are high production costs, low yields and saturation of the HACA’s low market volumes, due to limited uses and applications.
6.1 Expanding the HACA market
Salicylic acid is the best-known HACA for its use in anti-acne treatments.19 It is also an important intermediate for the production of pain relief drugs such as aspirin and rubefacients for acute and chronic musculoskeletal pain.75,76 Moreover, aminosalicylic acid, starting from 3-nitro salicylic acid can be used in the synthesis of azo dyes. Azo-dyes can then be employed as colourants in a variety of consumer products, including textiles, agriculture, pharmaceuticals, and cosmetics.77
Although HACAs can be used directly or as an intermediate for the production of various commercial end products, there is currently insufficient worldwide demand to fully valorise CO2 to offset anthropogenic CO2 emissions.78 The annual production of HACAs such as salicylic acid and hydroxynaphthoic acid is 13
000 metric tonnes per year,79,80 and if it is assumed that the production process consumes 1
:
1 molar ratio of CO2, the total CO2 consumption would be 41
450 tonnes per year of CO2. This is only 0.00012% of the global anthropogenic CO2 emissions. It is important to highlight that this case does not take into account other HACAs such as alkylated HACAs, halogenated HACAs, protocatechuic acid, resorcylic acid, vanillic acid and so on. Therefore, the total annual CO2 consumption via HACA production should be even higher.
Recent fundamental research hinted at the development of recyclable vinyl polymers from HACAs, providing a gateway for a partial replacement of polymer vinyl chloride (PVC) whose annual global production is estimated to be 44.3 million tonnes.25 Further research effort is therefore required to expand on current application of HACAs and their potential use in production of vinyl polymers and others. In addition, HACAs can be used for the production of azo dyes. Therefore, the present and potential uses of HACAs could potentially be increased through innovation. With the growing interest in CCUS, more research efforts can be focused on more cost-effective and safer HACA production processes. This can enhance the competitiveness of using HACAs in a variety of organic chemical products and by extension, increase CO2 utilisation and make significant contributions to net-zero targets.
6.2 Sustainability through biomass-derived phenolic compounds
Petroleum-based aromatic chemicals are the primary source of industrial raw materials for the manufacturing of many HACAs.81 However, a range of phenolics can be obtained from biomass which can be used as green raw materials for the production of HACAs. For instance, the pulp and paper industry generates 70 million tonnes of lignin annually and generally, this is used as a green source of thermal energy through direct combustion.82 The thermochemical conversion of lignin to high-value chemicals such as phenolic compounds is more feasible and economically advantageous than its use as an energy source or through any existing bioconversion routes.83 Bio-oil yield from fast pyrolysis can reach up to 70% (wet basis)84 and yield up to 94% of phenolic compounds using lignin from the pulping process.85 Vast quantities of lignin are available for conversion into useful aromatic compounds which then can be converted into HACAs but at the moment, lignin is still exploited as a low-value bio-energy source.86
Other ways of utilising lignin have been proposed by researchers such as funnelling and functionalisation of a mixture of lignin-derived monomers into a singular high-value chemical. Some of these methods include catalytic demethoxylation and transalkylation of a mixture of phenolic compounds using Au/TiO2 and HZSM-5 zeolite in a mixed-bed configuration to phenols,87 the use of activated carbon (AC)-supported MoWBO to convert vanillic acid and syringic acid into terephthalic acid (TPA),88 and depolymerisation of lignin with H2 in methanol over a Ru/C catalyst to obtain phenolic monomers in the first step. The obtained monomers were then demethoxylated with MoOx/AC. The generated 4-alkylphenols were then carbonylated with CO into 4-alkylbenzoic acid. In the final stage, the various alkyl chains were then oxidised with the Co–Mn–Br catalyst into carboxy groups, transforming the 4-alkylbenzoic acid mixture into TPA.89 An example of funnelling and functionalisation of a mixture of lignin-derived phenolic monomers into phenol is depicted in Fig. 3.
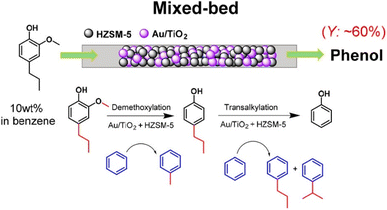 |
| Fig. 3 One step process for demethoxylation and dealkylation over a mixed bed of Au/TiO2 and HZSM-5 catalysts in benzene using a fixed-bed reactor. Reprinted from (ref. 87). | |
Despite the optimistic efforts conducted by researchers, it is important to understand the bottleneck of valorisation of the “lignin-to-chemicals” strategy before phenolics from lignin can be used industrially. For instance, funnelling and functionalisation of a mixture of lignin-derived monomers into a single high-value chemical require additional steps – not feasible from a step-economy point of view. Furthermore, the valorisation of one or two phenolic compounds is concerning due to combined yields typically below 5 wt%.89 Therefore, narrowing the product distribution to target industrially relevant phenolics that can be converted to HACAs is necessary. Obtaining the right technology and separation technique will ultimately allow commercialisation since it is economically advantageous to produce HACAs from lignin than a direct energy source. If successful, obtaining HACAs from biomass will help to meet the twin goals of reducing CO2 and the overwhelming dependence on fossil-derived chemicals for a more sustainable future.
6.3 Sustainability through continuous carboxylation
The first continuous Kolbe–Schmitt type reaction was carried out in 2005. This was achieved through carboxylation of a dihydric-phenol (resorcinol) in an aqueous solution to 2,4-dihydroxybenzoic acid (β-resorcylic acid) using a microreactor rig.70 As previously stated, this case is only valid for di- or tri-hydric aromatic compounds. However, due to the popularity of HACAs from monohydric phenols, this potential has been largely overlooked. Therefore, new uses can be found for the HACAs obtained from polyhydric phenols in order to accelerate the development of the feasible continuous processing that can lead to large consumption of CO2.
For example, the β-isomer of resorcylic acid (β-resorcylic acid) is currently being produced by carboxylation of resorcinol, in which the global production capacity stood at 44
800 tonnes in 2000.90 β-Resorcylic acid has been reported to be useful in the production of moisture-proof materials for direct adhesion to a floor panel for transportation vehicles and building structures,91 synthesis of methylphenidate pro-drugs,92 flavouring agents,93 and synthesis of various active pharmaceutical ingredients such as etamivan, modecainide, brovanexine and vanitiolide93 and polymer aerogels.94 Therefore, the prospect for continuous production of certain HACAs is bright, given that several polyhydric phenols can easily be obtained from sustainable biomass.
6.4 Sustainability through renewable energy and electrocarboxylation
Renewable and carbon-free energy sources, such as solar, hydroelectric, wind, geothermal and nuclear, provide energy with zero or almost zero emissions.95–97 Hence, synthesis methods that utilise CO2 and do not rely on a petrochemical energy source to further reduce the carbon footprint are attractive options to explore. One promising process is electrocarboxylation, which involves the electrochemical fixation of CO2 in organic chemicals including alkenes, organic halides, aldehydes, ketones and imines.98 The electrochemical carboxylation can either be conducted with a sacrificial anode, like magnesium or aluminium, or with an inert anode, like platinum or carbon. Sacrificial anodes have larger oxidation potential than other reaction species, thereby making this setup compatible with a straightforward undivided electrolysis cell between the catholyte and anolyte. The metal cations (Mg2+, Al3+) produced by the counter electrode rapidly coordinate with the carboxylate anions formed at the cathode. The corresponding metal carboxylates are easily isolated from the organic solvents. The cathodic reduction in the synthesis of carboxylic acids can be categorised into two possible routes (Fig. 4).99
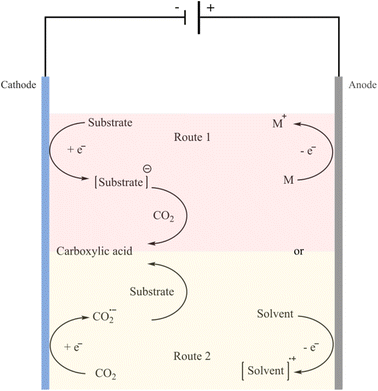 |
| Fig. 4 The two general routes for electrochemical carboxylation reactions using CO2 to synthesize carboxylic acids. Reprinted from (ref. 99). Route 1: reduction of the substrate at the cathode to generate the radical anion or carbanion intermediate which then reacts with CO2; route 2: prior reduction of CO2 at the cathode which then reacts with the substrate. | |
In the case of the Kolbe–Schmitt type reaction, carboxylation of phenols is most likely to take place via the first route. Hence, electrocarboxylation using CO2 can be a worthy alternative to overcome the limitations associated with the Kolbe–Schmitt reaction.98
Although electrochemical carboxylation might be a potent substitute for the traditional chemical approach, this method inevitably has its limits. The metal cations (Mg2+, Al3+) generated from the sacrificial anodes contaminate the reaction mixture, which is a major drawback.100 Additionally, the inability to reduce phenols with sufficient nucleophilicity has prevented electrocarboxylation of phenolics from being achieved to this date.
7 Conclusion
In this study, several historical and recent research efforts on the carboxylation of phenolic compounds for the production of HACAs have been reviewed. Starting from the well-known Kolbe–Schmitt reaction, the review covers some of the recent research efforts to enhance the carboxylation of phenolic compounds utilising CO2. While the industrial production scale of HACAs still relies on the historical two-pot Kolbe–Schmitt reaction, many recent developments have focused on the modification of this reaction to reduce, CO2 pressures, reaction times, high energy demand and dependence on fossil-derived feedstock. These developments include the synthesis and use of intermediate compounds (e.g., ionic liquids), heterogeneous catalysts (e.g., C@Fe–Al2O3) and homogeneous stoichiometric reagents (e.g., DBU). Currently, this process consumes only 0.00012% of global anthropogenic emissions which is not enough to valorise enough CO2 to cope with the anthropogenic emissions. Therefore, research efforts have also focused to expand the use of the final HACAs in the chemical industry for the manufacture of plastics such as vinyl polymers and other household goods as well as obtaining phenolic compounds from biomass for a more sustainable HACA production. Increased utilisation of CO2 in chemical production has the potential to promote net zero and scale back the effects of climate change.
Conflicts of interest
There are no conflicts of interest to declare.
Notes and references
-
E. Dlugokencky and P. Tans, Trends in Atmospheric Carbon Dioxide, National Oceanic and Atmospheric Administration, Earth System Research Laboratory (NOAA/ESRL), 2020, https://www.esrl.noaa.gov/gmd/ccgg/trends/global.html, accessed October 25, 2021 Search PubMed.
- F. Joos and R. Spahni, Rates of change in natural and anthropogenic radiative forcing over the past 20,000 years, Proc. Natl. Acad. Sci. U. S. A., 2008, 105, 1425–1430, DOI:10.1073/PNAS.0707386105.
-
P. Ciais, C. Sabine, G. Bala, L. Bopp, V. Brovkin, J. Canadell, A. Chhabra, R. DeFries, J. Galloway, M. Heimann, C. Jones, C. Le Quéré, R. B. Myneni, S. Piao and P. Thornton, Carbon and Other Biogeochemical Cycles, in: Climate Change 2013: The Physical Science Basis, Contribution of Working Group I to the Fifth Assessment Report of the Intergovernmental Panel on Climate Change, ed. T. F. Stocker, D. Qin, G.-K. Plattner, M. Tignor, S. K. Allen, J. Boschung, A. Nauels, Y. Xia, V. Bex and P. M. Midgley, Cambridge, United Kingdom, 2013 Search PubMed.
- International Energy Agency, Putting CO 2 to Use, Energy Rep., 2019, 86 Search PubMed.
- E. C. Ra, K. Y. Kim, E. H. Kim, H. Lee, K. An and J. S. Lee, Recycling Carbon Dioxide through Catalytic Hydrogenation: Recent Key Developments and Perspectives, ACS Catal., 2020, 10, 11318–11345, DOI:10.1021/ACSCATAL.0C02930/ASSET/IMAGES/LARGE/CS0C02930_0015.JPEG.
- X. Zhang, A. Zhang, X. Jiang, J. Zhu, J. Liu and J. Li,
et al., Utilization of CO2 for aromatics production over ZnO/ZrO2-ZSM-5 tandem catalyst, J. CO2 Util., 2019, 29, 140–145, DOI:10.1016/j.jcou.2018.12.002.
- B. Liu, J. Qin, J. Shi, J. Jiang, X. Wu and Z. He, New perspectives on utilization of CO2 sequestration technologies in cement-based materials, Constr. Build. Mater., 2021, 272, 121660, DOI:10.1016/j.conbuildmat.2020.121660.
- R. P. Ye, J. Ding, W. Gong, M. D. Argyle, Q. Zhong and Y. Wang,
et al., CO2 hydrogenation to high-value products via heterogeneous catalysis, Nat. Commun., 2019, 10, 1–15, DOI:10.1038/s41467-019-13638-9.
- M. North and R. Pasquale, Mechanism of cyclic carbonate synthesis from epoxides and CO2, Angew. Chem., Int. Ed., 2009, 48, 2946–2948, DOI:10.1002/anie.200805451.
- R. Schmitt, Beitrag zur Kenntniss der Kolbe’schen Salicylsäure Synthese, J. Prakt. Chem., 1885, 31, 397–411, DOI:10.1002/prac.18850310130.
- Y. Gu, K. Matsuda, A. Nakayama, M. Tamura, Y. Nakagawa and K. Tomishige, Direct Synthesis of Alternating Polycarbonates from CO2 and Diols by Using a Catalyst System of CeO2 and 2-Furonitrile, ACS Sustainable Chem. Eng., 2019, 7, 6304–6315, DOI:10.1021/acssuschemeng.8b06870.
- R. M. Cuéllar-Franca and A. Azapagic, Carbon capture, storage and utilisation technologies: A critical analysis and comparison of their life cycle environmental impacts, J. CO2 Util., 2015, 9, 82–102, DOI:10.1016/j.jcou.2014.12.001.
- S. Sarp, S. Gonzalez Hernandez, C. Chen and S. W. Sheehan, Alcohol Production from Carbon Dioxide: Methanol as a Fuel and Chemical Feedstock, Joule, 2021, 5, 59–76, DOI:10.1016/j.joule.2020.11.005.
- M. S. Satpute, V. D. Gangan and I. Shastri, Methyl Vanillate Ether Derivatives as Future Potential Drug, International Journal of Scientific Research in Science and Technology, 2019, 129–134, DOI:10.32628/ijsrst19616.
-
W. Lei, S. Yuexin, D. Yunmei and Z. Yaping, Ornidazole pharmaceutical co-crystal and preparation method thereof, CN113234021A, 2021.
- X. B. Zhang, Y. X. Liu and Z. H. Luo, Kinetic study of the aqueous Kolbe-Schmitt synthesis of 2,4- and 2,6-dihydroxybenzoic acids, Chem. Eng. Sci., 2019, 195, 107–119, DOI:10.1016/j.ces.2018.11.045.
-
K. M. Brinkman, D. R. Hanley and J. L. Sullivan, Alkyl salicylate resin for carbonless copy paper and imaging use, European Patent, EP0338808A2, European Patent Office, 1989.
-
S. Hahn and Organization WH, Resorcinol, 2006, p. 72 Search PubMed.
- D. Ekinci and M. Şentürk, Kfrevioǧlu ÖI. Salicylic acid derivatives: Synthesis, features and usage as therapeutic tools, Expert Opin. Ther. Pat., 2011, 21, 1831–1841, DOI:10.1517/13543776.2011.636354.
- T. Arif, Salicylic acid as a peeling agent: a comprehensive review, Clin., Cosmet. Invest. Dermatol., 2015, 8, 455, DOI:10.2147/CCID.S84765.
- S. Wang, M. Bilal, H. Hu, W. Wang and X. Zhang, 4-Hydroxybenzoic acid—a versatile platform intermediate for value-added compounds, Appl. Microbiol. Biotechnol., 2018, 102, 3561–3571, DOI:10.1007/s00253-018-8815-x.
-
H. D. Preston, R. F. van Croonenborgh, W. J. N. Marsden, G. Matheis, D. Gerard, K. Quirin, Raw Materials for Flavourings: Non-flavouring Ingredients, Flavourings, Wiley, 2007, pp. 314–389, DOI:10.1002/9783527611454.ch3c.
- J. D. Tibbetts, D. Russo, A. A. Lapkin and S. D. Bull, Efficient Syntheses of Biobased Terephthalic Acid, p-Toluic Acid, and p-Methylacetophenone via One-Pot Catalytic Aerobic Oxidation of Monoterpene Derived Bio- p-cymene, ACS Sustainable Chem. Eng., 2021, 9(25), 8642–8652, DOI:10.1021/acssuschemeng.1c02605.
- R. C. Schmeltzer, K. E. Schmalenberg and K. E. Uhrich, Synthesis and Cytotoxicity of Salicylate-Based Poly(anhydride esters) Synthesis and Cytotoxicity of Salicylate-Based Poly(anhydride esters), Biomacromolecules, 2005, 6, 359–367, DOI:10.1021/bm049544.
- A. Kazama and Y. Kohsaka, Radical polymerization of “dehydroaspirin” with the formation of a hemiacetal ester skeleton: A hint for recyclable vinyl polymers, Polym. Chem., 2019, 10, 2764–2768, 10.1039/c9py00474b.
-
Advice S, Academies E, Novel carbon capture and utilisation technologies capture and. SAPEA Evidence Review Report, 2018 Search PubMed.
- H. J. Kim, Y. Reddi, C. J. Cramer, M. A. Hillmyer and C. J. Ellison, Readily Degradable Aromatic Polyesters from Salicylic Acid, ACS Macro Lett., 2020, 9, 96–102, DOI:10.1021/acsmacrolett.9b00890.
- S. M. Emadian, T. T. Onay and B. Demirel, Biodegradation of bioplastics in natural environments, Waste Manag., 2017, 59, 526–536, DOI:10.1016/j.wasman.2016.10.006.
- H. Karan, C. Funk, M. Grabert, M. Oey and B. Hankamer, Green Bioplastics as Part of a Circular Bioeconomy, Trends Plant Sci., 2019, 24, 237–249, DOI:10.1016/j.tplants.2018.11.010.
-
G. V. Ambulgekar, S. D. Samant and A. B. Pandit, Oxidation of alkylarenes to the corresponding acids using aqueous potassium permanganate by hydrodynamic cavitation, Ultrason. Sonochem., Elsevier, 2004, vol. 11, pp. 191–6, DOI:10.1016/j.ultsonch.2004.01.027.
- J. Miki, Y. Osada, T. Konoshi, Y. Tachibana and T. Shikada, Selective oxidation of toluene to benzoic acid catalyzed by modified vanadium oxides, Appl. Catal., A, 1996, 137, 93–104, DOI:10.1016/0926-860X(95)00304-5.
- S. M. A. H. Siddiki, M. N. Rashed, A. S. Touchy, M. A. R. Jamil, Y. Jing and T. Toyao,
et al., Hydrolysis of amides to carboxylic acids catalyzed by Nb2O5, Catal. Sci. Technol., 2021, 11, 1949–1960, 10.1039/d0cy02230f.
- A. S. Lindsey and H. Jeskey, The Kolbe-Schmitt Reaction, Chem. Rev., 1957, 57, 583–620, DOI:10.1021/cr50016a001.
- X. Wu and F. Zheng, Chemical Transformations of Carbon Dioxide, Top. Curr. Chem., 2018, 1–60, DOI:10.1007/978-3-319-77757-3.
- Y. Sadamitsu, A. Okumura, K. Saito and T. Yamada, Kolbe–Schmitt type reaction under ambient conditions mediated by an organic base, Chem. Commun., 2019, 55, 9837–9840, 10.1039/C9CC04550C.
-
G. H. Rau, Electrochemical CO2 capture and storage
with hydrogen generation, Energy Procedia, Elsevier, 2009, vol. 1, pp. 823–8, DOI:10.1016/j.egypro.2009.01.109.
-
M. Aresta, A. Dibenedetto and E. Quaranta, Reaction Mechanisms in Carbon Dioxide Conversion, Springer Berlin Heidelberg, Berlin, Heidelberg, 2015, DOI:10.1007/978-3-662-46831-9.
- Y. Li, S. H. Chan and Q. Sun, Heterogeneous catalytic conversion of CO2: A comprehensive theoretical review, Nanoscale, 2015, 7, 8663–8683, 10.1039/c5nr00092k.
- T. Sakakura, J. C. Choi and H. Yasuda, Transformation of carbon dioxide, Chem. Rev., 2007, 107, 2365–2387, DOI:10.1021/cr068357u.
- A. Tortajada, F. Juliá-Hernández, M. Börjesson, T. Moragas and R. Martin, Transition-Metal-Catalyzed Carboxylation Reactions with Carbon Dioxide, Angew. Chem., Int. Ed., 2018, 57, 15948–15982, DOI:10.1002/ANIE.201803186.
- H. Kolbe, Ueber Synthese der Salicylsäure, Justus Liebigs Ann. Chem., 1860, 113, 125–127, DOI:10.1002/jlac.18601130120.
-
S. Marasse, Process of making salicylic acid, US Pat., US529182A, 1894 Search PubMed.
- R. J. Ouellette and J. D. Rawn, Alcohols and Phenols, Principles of Organic Chemistry, 2015, 209–238, DOI:10.1016/b978-0-12-802444-7.00008-2.
- W. Hentschel and J. Prakt, Ueber phenylirte Kohlensiiureather und deren Ueberfu hriing in Salicylsanre, J. Prakt. Chem., 1882, 39 Search PubMed.
- J. R. Johnson, Abnormal Reactions of Benzylmagnesium Chloride. II. The Mechanism of the o-Tolyl Rearrangement, J. Am. Chem. Soc., 1933, 55, 3029–3032, DOI:10.1021/ja01334a073.
- J. L. Hales, J. I. Jones and A. S. Lindsey, Mechanism of the Kolbe–Schmitt reaction. Part I. Infra-red studies, J. Chem. Soc., 1954, 23, 3145–3151, 10.1039/JR9540003145.
- Z. Marković, J. P. Engelbrecht and S. Marković, Theoretical study of the Kolbe-Schmitt reaction mechanism, Zeitschrift fur Naturforschung - Section A Journal of Physical Sciences, 2002, 57, 812–818 Search PubMed.
- J. Luo, S. Preciado, P. Xie and I. Larrosa, Carboxylation of Phenols with CO 2 at Atmospheric Pressure, Chem.–Eur. J., 2016, 22, 6798–6802, DOI:10.1002/chem.201601114.
- F. Calvo-Castañera, J. Álvarez-Rodríguez and N. Candela, Maroto-Valiente Á. First Phenol Carboxylation with CO2 on Carbon Nanostructured C@Fe-Al2O3 Hybrids in Aqueous Media under Mild Conditions, Nanomaterials, 2021, 11, 190, DOI:10.3390/nano11010190.
- H. K. Lee, C. S. Koh, W.-S. Lo, Y. Liu, I. Y. Phang and H. Y. Sim,
et al., Applying a Nanoparticle@MOF Interface To Activate an Unconventional Regioselectivity of an Inert Reaction at Ambient Conditions, J. Am. Chem. Soc., 2020, 142, 11521–11527, DOI:10.1021/jacs.0c04144.
- T. Iijima and T. Yamaguchi, Efficient regioselective carboxylation of phenol to salicylic acid with supercritical CO2 in the presence of aluminium bromide, J. Mol. Catal. A: Chem., 2008, 295, 52–56, DOI:10.1016/j.molcata.2008.07.017.
- K. A. Suerbaev, M. K. Aldabergenov and N. Z. Kudaibergenov, Carboxylation of hydroxyarens with metal alkyl carbonates, Green Process. Synth., 2015, 4, 91–96, DOI:10.1515/GPS-2014-0098.
- U. Krtschil, V. Hessel, D. Reinhard and A. Stark, Flow Chemistry of the Kolbe-Schmitt Synthesis from Resorcinol: Process Intensification by Alternative Solvents, New Reagents and Advanced Reactor Engineering, Chem. Eng. Technol., 2009, 32, 1774–1789, DOI:10.1002/ceat.200900450.
- U. Krtschil, V. Hessel, H. J. Kost and D. Reinhard, Kolbe-Schmitt Flow Synthesis in Aqueous Solution - From Lab Capillary Reactor to Pilot Plant, Chem. Eng. Technol., 2013, 36, 1010–1016, DOI:10.1002/ceat.201200633.
- A. Stark, S. Huebschmann, M. Sellin, D. Kralisch, R. Trotzki and B. Ondruschka, Microwave-Assisted Kolbe-Schmitt Synthesis Using Ionic Liquids or Dimcarb as Reactive Solvents, Chem. Eng. Technol., 2009, 32, 1730–1738, DOI:10.1002/ceat.200900331.
-
T. Hirano, MOPAC Manual (Seventh Edition). MOPAC Man, 1993 Search PubMed.
- Y. Kosugi, Y. Imaoka, F. Gotoh, M. A. Rahim, Y. Matsui and K. Sakanishi, Carboxylations of alkali metal phenoxides with carbon dioxide, Org. Biomol. Chem., 2003, 1, 817–821, 10.1039/b210793g.
- Z. Marković, S. Marković, N. Manojlović and J. Predojević-Simović, Mechanism of the kolbe-schmitt reaction. structure of the intermediate potassium phenoxide-CO2 complex, J. Chem. Inf. Model., 2007, 47, 1520–1525, DOI:10.1021/ci700068b.
- Q. Yang, M. Sheng, J. J. Henkelis, S. Tu, E. Wiensch and H. Zhang,
et al., Explosion Hazards of Sodium Hydride in Dimethyl Sulfoxide, N, N-Dimethylformamide, and N, N-Dimethylacetamide, Org. Process Res. Dev., 2019, 23, 2210–2217, DOI:10.1021/acs.oprd.9b00276.
-
P. Walden, On the molecular quantity and electrical conductivity of some molten salts, Izvstiya Imperial Academy of Sciences, VI series, 1914, 8, 6, pp. 405–422 Search PubMed.
- Z. Lei, B. Chen, Y. M. Koo and D. R. Macfarlane, Introduction: Ionic Liquids, Chem. Rev., 2017, 117, 6633–6635, DOI:10.1021/acs.chemrev.7b00246.
- F. U. Shah, O. I. Gnezdilov and A. Filippov, Ion dynamics in halogen-free phosphonium bis(salicylato)borate ionic liquid electrolytes for lithium-ion batteries, Phys. Chem. Chem. Phys., 2017, 19, 16721–16730, 10.1039/C7CP02722B.
- E. A. Chernikova, L. M. Glukhov, V. G. Krasovskiy, L. M. Kustov, M. G. Vorobyeva and A. A. Koroteev, Ionic liquids as heat transfer fluids: comparison with known systems, possible applications, advantages and disadvantages, Russ. Chem. Rev., 2015, 84, 875–890, DOI:10.1070/RCR4510.
- S. Wang, C. M. McGuirk, A. D’Aquino, J. A. Mason and C. A. Mirkin, Metal–Organic Framework Nanoparticles, Adv. Mater., 2018, 30, 1800202, DOI:10.1002/adma.201800202.
- C. Friedel and J. M. Crafts, Ann. Chim. Phys., 1888, 14, 441 Search PubMed.
- J. Luo and I. Larrosa, C−H Carboxylation of Aromatic Compounds through CO2 Fixation, ChemSusChem, 2017, 10, 3317–3332, DOI:10.1002/cssc.201701058.
- A. Corma and H. García, Lewis acids: From conventional homogeneous to green homogeneous and heterogeneous catalysis, Chem. Rev., 2003, 103, 4307–4365, DOI:10.1021/cr030680z.
- N. Hazari and J. E. Heimann, Carbon Dioxide Insertion into Group 9 and 10 Metal-Element σ Bonds, Inorg. Chem., 2017, 56, 13655–13678, DOI:10.1021/acs.inorgchem.7b02315.
- F. Castro-Gómez, G. Salassa, A. W. Kleij and C. Bo, A DFT study on the mechanism of the cycloaddition reaction of CO 2 to epoxides catalyzed by Zn(Salphen) complexes, Chem.–Eur. J., 2013, 19, 6289–6298, DOI:10.1002/chem.201203985.
- V. Hessel, C. Hofmann, P. Löb, J. Löhndorf, H. Löwe and A. Ziogas, Aqueous Kolbe−Schmitt Synthesis Using Resorcinol in a Microreactor Laboratory Rig under High-p, T Conditions, Org. Process Res. Dev., 2005, 9, 479–489, DOI:10.1021/op050045q.
- M. A. Rahim, Y. Matsui, T. Matsuyama and Y. Kosugi, Regioselective Carboxylation of Phenols with Carbon Dioxide, Bull. Chem. Soc. Jpn., 2003, 76, 2191–2195, DOI:10.1246/bcsj.76.2191.
- H.-W. Leung and D. J. Paustenbach, Organic acids and bases: Review of toxicological studies, Am. J. Ind. Med., 1990, 18, 717–735, DOI:10.1002/ajim.4700180610.
-
P. T. Anastas and J. C. Warner, Green Chemistry: Theory and Practice: Paperback: Paul Anastas - Oxford University Press, Oxford University Press, 1998 Search PubMed.
- F. M. Akwi and P. Watts, Continuous flow chemistry: where are we now? Recent applications, challenges and limitations, Chem. Commun., 2018, 54, 13894–13928, 10.1039/c8cc07427e.
- S. Derry, P. J. Wiffen, E. A. Kalso, R. F. Bell, D. Aldington, T. Phillips, H. Gaskell and R. A. Moore, Topical analgesics for acute and chronic pain in adults - an overview of Cochrane Reviews, Cochrane Database Syst. Rev., 2017, CD008609, DOI:10.1002/14651858.CD008609.pub2.
- J. Park, M. A. Kelly, J. X. Kang, S. S. Seemakurti, J. L. Ramirez and M. C. Hatzell,
et al., Production of active pharmaceutical ingredients (APIs) from lignin-derived phenol and catechol, Green Chem., 2021, 23, 7488–7498, 10.1039/d1gc02158c.
- K. R. Raghavendra and K. Ajay Kumar, Synthesis of some novel azo dyes and their dyeing, redox and antifungal properties, Int. J. ChemTech Res., 2013, 5, 1756–1760 CAS.
- R. M. Cuéllar-Franca and A. Azapagic, Carbon capture, storage and utilisation technologies: A critical analysis and comparison of their life cycle environmental impacts, J. CO2 Util., 2015, 9, 82–102, DOI:10.1016/j.jcou.2014.12.001.
-
CEIC, China Market Price: Monthly Avg: Organic Chemical Material: Methanol, Methyl Alcohol | Economic Indicators, 2021, https://www.ceicdata.com/en/china/china-petroleum–chemical-industry-association-petrochemical-price-organic-chemical-material/cn-market-price-monthly-avg-organic-chemical-material-salicylic-acid-technical-grade, accessed November 23, 2021 Search PubMed.
-
M. Y. Kawamura and M. H. Maruyama, SIDS Initial Assessment Report For SIAM 19, 2004 Search PubMed.
-
S. T. Yang, H. Huang, A. Tay, W. Qin, L. D. Guzman and E. C. San Nicolas, Extractive Fermentation for the Production of Carboxylic Acids, Bioprocess Value-Added Prod from Renew Resour, 2007, pp. 421–446, DOI:10.1016/B978-044452114-9/50017-7.
- D. S. Bajwa, G. Pourhashem, A. H. Ullah and S. G. Bajwa, A concise review of current lignin production, applications, products and their environmental impact, Ind. Crops Prod., 2019, 139, 111526, DOI:10.1016/j.indcrop.2019.111526.
- S. Feng, S. Cheng, Z. Yuan, M. Leitch and C. Xu, Valorization of bark for chemicals and materials: A review, Renewable Sustainable Energy Rev., 2013, 26, 560–578, DOI:10.1016/j.rser.2013.06.024.
- A. V. Bridgwater, D. Meier and D. Radlein, An overview of fast pyrolysis of biomass, Org. Geochem., 1999, 30, 1479–1493, DOI:10.1016/S0146-6380(99)00120-5.
- V. B. F. Custodis, C. Bährle, F. Vogel and J. A. Van Bokhoven, Phenols and aromatics from fast pyrolysis of variously prepared lignins from hard- and softwoods, J. Anal. Appl. Pyrolysis, 2015, 115, 214–223, DOI:10.1016/j.jaap.2015.07.018.
- L. Dessbesell, M. Paleologou, M. Leitch, R. Pulkki and C. Xu, Global lignin supply overview and kraft lignin potential as an alternative for petroleum-based polymers, Renewable Sustainable Energy Rev., 2020, 123, 109768, DOI:10.1016/j.rser.2020.109768.
- X. Huang, J. M. Ludenhoff, M. Dirks, X. Ouyang, M. D. Boot and E. J. M. Hensen, Selective Production of Biobased Phenol from Lignocellulose-Derived Alkylmethoxyphenols, ACS Catal., 2018, 8, 11184–11190, DOI:10.1021/acscatal.8b03430.
- Z. Bai, W. C. Phuan, J. Ding, T. H. Heng, J. Luo and Y. Zhu, Production of Terephthalic Acid from Lignin-Based Phenolic Acids by a Cascade Fixed-Bed Process, ACS Catal., 2016, 6, 6141–6145, DOI:10.1021/acscatal.6b02052.
- S. Song, J. Zhang, G. Gözaydın and N. Yan, Production of Terephthalic Acid from Corn Stover Lignin, Angew. Chem., 2019, 131, 4988–4991, DOI:10.1002/ange.201814284.
- S. Hahn, J. Kielhorn, J. Koppenhöfer, A. Wibbertmann and I. Mangelsdorf, Concise international chemical assessment document 71, IPCS Concise Int. Chem. Assess. Doc., 2006, 1–46 Search PubMed.
-
O. Shigeki Muta and O. Masatoshi Suzuki, Moisture-proof material, US Pat., US9546303B2, 2017 Search PubMed.
-
G. Sven, C. Guochen, B. Bindu, M. Travis and B. Sanjib, Methylphenidate-prodrugs, processes of making and using the same, US Pat., US9453037B2, 2016 Search PubMed.
- M. S. Satpute, V. D. Gangan and I. Shastri, Synthesis and antibacterial activity of novel 3-hydroxy benzoic acid hybrid derivatives [Part II], Rasayan J. Chem., 2019, 12, 1077–1084, DOI:10.31788/RJC.2019.1235167.
- P. J. M. Carrott, L. M. Marques and M. M. L. Ribeiro Carrott, Core-shell polymer aerogels prepared by co-polymerisation of 2,4-dihydroxybenzoic acid, resorcinol and formaldehyde, Microporous Mesoporous Mater., 2012, 158, 170–174, DOI:10.1016/j.micromeso.2012.03.040.
- N. L. Panwar, S. C. Kaushik and S. Kothari, Role of renewable energy sources in environmental protection: A review, Renewable Sustainable Energy Rev., 2011, 15, 1513–1524, DOI:10.1016/j.rser.2010.11.037.
- K. Dong, R. Sun and G. Hochman, Do natural gas and renewable energy consumption lead to less CO2 emission? Empirical evidence from a panel of BRICS countries, Energy, 2017, 141, 1466–1478, DOI:10.1016/j.energy.2017.11.092.
- Q. Schiermeier, J. Tollefson, T. Scully, A. Witze and O. Morton, Energy alternatives: Electricity without carbon, Nature, 2008, 454, 816–823, DOI:10.1038/454816a.
- R. Matthessen, J. Fransaer, K. Binnemans and D. E. De Vos, Electrocarboxylation: Towards sustainable and efficient synthesis of valuable carboxylic acids, Beilstein J. Org. Chem., 2014, 10, 2484–2500, DOI:10.3762/bjoc.10.260.
- X. F. Liu, K. Zhang, L. Tao, X. B. Lu and W. Z. Zhang, Recent advances in electrochemical carboxylation reactions using carbon dioxide, Green Chemical Engineering, 2022, 3, 125–137, DOI:10.1016/j.gce.2021.12.001.
- H Tateno, Y Matsumura, K Nakabayashi, H Senboku and M Atobe, Development of a novel electrochemical carboxylation system using a microreactor, RSC Adv., 2015, 5, 98721–98723, 10.1039/c5ra19289g.
|
This journal is © The Royal Society of Chemistry 2023 |
Click here to see how this site uses Cookies. View our privacy policy here.