Sustainable and efficient production of furoic acid from furfural through amine assisted oxidation with hydrogen peroxide and its implementation for the synthesis of alkyl furoate†
Received
17th November 2022
, Accepted 4th January 2023
First published on 10th January 2023
Abstract
Aromatic functionality is an important feature for the design of new molecules with specific properties. Today fossil fuel feedstocks provide aryl building blocks with well-known chemistry, which can be implemented in different products for different applications. Furan building blocks are biobased chemicals derived from biomass, which have the potential to be implemented in different end products such as polymers and surfactants, substituting petrochemicals. The success in implementing furan-based compounds is strongly dependent on an efficient chemical pathway, which can give low operating costs and high yields. In this paper, we study the production of furoic acid starting from furfural through a base assisted oxidation with hydrogen peroxide. Specifically, we report a strategy to efficiently produce furoic acid and integrate this with the production of the intermediate alkyl furoate for surfactant production. Further evaluation was done on the recovery and valorisation of the co-products (sodium sulfate and amine oxide) showing that the economics of the process can be further improved. This approach can provide high reaction yield (99%) and an efficient separation of the final product, providing a valuable competitive building block for surfactant synthesis.
Sustainability spotlight
Currently, most commodity chemicals are strongly dependent on fossil fuels. The implementation of cost-effective and green technologies is strongly required but face multiple challenges from lack of research and high cost. Environmental policies and regulations which force the chemical industry to adopt such sustainable practices have resulted in the delocalization of industry towards areas where regulations are less stringent. This work introduces a new concept combining a novel green manufacturing technology to develop a new competitive commodity chemical, promoting circular economy and self-sufficiency. This, in turn, reduces the need for the transportation of the feedstock and final product, decreases CO2 emissions and valorises waste products, thus decreasing our reliance on fossil fuels. These concepts align with the UN SDG 12.
|
Background
The production of biobased platform chemicals for the synthesis of new sustainable materials that can replace petrochemicals is a topic of much scientific interest.1–4 Furfural and 5-HMF are viewed as the main candidates for the replacement of aromatic building blocks, which currently are derived from benzene, toluene and xylene.5–8 One of the main uses of these aromatic building blocks is in the surfactant industry, to produce linear alkyl benzene sulfonate (LAS), which finds many applications in cleaning products.9,10 In the last 5 years, research has been conducted to find alternative green solutions to LAS, which can deliver the same performance in cleaning formulations.11,12 Different studies have shown that furan-based surfactants show similar emulsifying properties compared with LAS and better basic properties in terms of CMC, resistance to hard water and Krafft point.13 However, while different studies have shown the benefits of using furan head groups in place of aryl ones,14 a critical discussion on the source and economic competitiveness in using furan instead of benzene still needs to be addressed more in depth. Few studies focused on establishing a catalytic route, not focusing on the overall feasibility of the process.15,16 Indeed, extensive studies have been done in the last 20 years on the feasible production of HMF, but despite high yields achieved through intensive R&D in catalyst development, separation remains an issue, which limits the economic viability of this molecule.17,18 In one of our recent publications, we addressed this issue showing that the isolation of HMF is viable only when fructose is used as a feedstock and barely competitive even in a highly optimized process, strongly hindering its application as a commodity chemical.19 Therefore, the application of HMF as a surfactant building block to replace LAS is unlikely to succeed at present. On the other hand, furfural, derived from the pentosan fraction of biomass, can deliver a cheaper building block since it can be obtained directly from biomass through acid treatment in high yield and it can be easily purified due to its high vapour pressure, which allows distillation.20 For this reason, furfural is readily available in the market at a low price (<2 $ per kg) with high marginality, representing a potential feedstock to be used in the production of different commodity chemicals.21 Several studies have reported the successful use of furfural derivatives as building blocks for the synthesis of new surfactants but these always pass through intermediate steps involving the transformation of furfural into its derivative. For example, Dauenhauer and co-workers used furan, which involved the decarboxylation of furfural, while Hoffman and co-workers used 5-alkoxy-2[5H]-furanones derived from the photooxygenation of furfural.11,22 The feasibility in using furan based feedstock in this application is limited by the transformation of furfural into these intermediates, which needs to be carefully assessed. We recently reported a new biobased surfactant, sulfonated alkyl furoate, based on the simple esterification of furoic acid and fatty alcohol, called SAF.23 In our study, we showed that this surfactant can be economically competitive if the oxidation of furfural to furoic acid is carried out efficiently. At present, traditional techniques for aerobic aldehyde oxidation based on Ag2O in conjunction with a base are adopted on a large scale.24 The process consists of bubbling air in an aqueous furfural solution (between 6 and 10%) in a slurry reactor. The solution is then acidified and furoic acid precipitates as a solid. However, this process is limited by the low recyclability of the catalyst because furfural undergoes decomposition under basic conditions leading to humin byproducts, which are deleterious to catalyst activity.25,26 Moreover, furoic acid has high solubility in water (3%), which reduces the efficiency of the separation. Different research studies have focused on catalyst development for the oxidation of furfural using water as solvent through the usage of different metal active centres. The main challenge in this approach is establishing a catalytic system which can carry out the conversion at a high furfural loading to allow good separation efficiency. Due the enhanced solubility of metals during the catalytic activity under acidic conditions, the formation of the acid at high concentration will favour leaching accompanied by particle size agglomeration, which will result in the loss of catalytic activity over multiple runs.27 This would require an optimum support, which can minimize the leaching and stabilize the noble metal particles in the support.28,29 In this matter, different catalysts which showed stability in batch operation proved to deactivate when they are used continuously since the catalysts are exposed to higher flow rates.30 Different studies have reported robust catalytic systems which can carry out this conversion efficiently through non-noble metal-based approaches, but further considerations are needed for what concern the initial concentration of furfural used and the stability of the catalyst over continuous operation.31,32 Polyoxometalates proved to be able to carry out such transformation at a relatively high concentration of furfural (10%) but recyclability was not tested for furan based substrates, which is an important aspect since humin side products can be deleterious to the catalytic activity.33 Noble metals suffer from this type of deactivation, and therefore low concentration below 2% is needed.34 Homogeneous catalysis has also been investigated in different studies, showing that it can carry out oxidation efficiently especially when carbene is used as the ligand or in its pure form, but difficulties are encountered in recovering efficiently the catalyst, since the downstream process for the purification of furoic acid requires acidification.35–38 In this matter, an approach with a good trade-off between high yield of reaction and separation is still lacking in the current literature. To overcome these limitations, we have developed a new system to produce furoic acid under concentrated conditions using the stoichiometric oxidant H2O2 assisted by a base (Fig. 1). Since furfural is not stable towards strong bases such as NaOH and KOH, we selected amines as weak bases to perform this oxidation. We selected tributylamine in particular since it guarantees a stable reaction environment, limiting side reactions. The separation efficiency of the process has been studied, showing that both amine and furoic acid can be efficiently separated. By exploiting the hydrophobicity of tributyl amine, we implemented a basification step where the amine is separated in a second liquid phase and furoic acid is separated through acidification of the aqueous layer. This approach allows the water usage to be minimized, which represents a problem for most aerobic oxidations since they are carried out at a low concentration of furfural. We then studied the esterification of the produced furoic acid with dodecanol to produce alkyl furoate, which can be used as a surfactant intermediate for SAF. We believe that this approach can solve the aforementioned issues regarding the viable production of furoic acid, leading to a cheaper and more sustainable process.
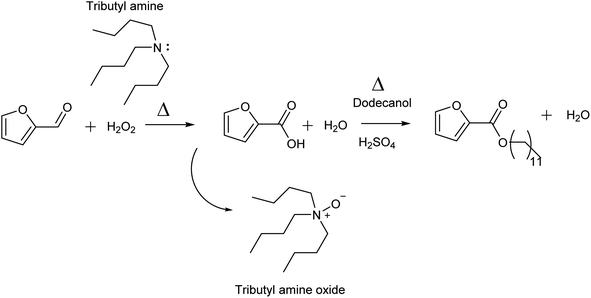 |
| Fig. 1 Reaction scheme to produce furoic acid and alkyl furoate passing through an amine assisted oxidation with hydrogen peroxide. | |
Results and discussion
Oxidation of furfural under different process parameters
The selection of the base was done by analysing the stability of furfural. A stability test was conducted through the addition of NaOH and amine in two different batches and the results were analysed by HPLC. It was observed that when NaOH was added the colour of the solution changed within 5 min to brown and to dark black upon heating at 55 °C for 10 min. The HPLC analysis confirmed the degradation of furfural (about 52%) accompanied by the formation of furoic acid (27%) formed through the Cannizzaro reaction. On the other hand, furfural proved to be stable upon addition of amine and only 5% degradation was observed upon heating. For these reasons, the usage of NaOH was discarded.
Our initial trials (Table 1) revealed that the reaction proceeds only when amine and furfural are mixed together with hydrogen peroxide and no conversion is observed when furfural or amine separately is mixed with the oxidant (1), indicating that there is an activation mechanism which makes the oxidation possible. The oxidation mechanism is not completely clear. The literature mentions that peracetic acid is a better oxidant for the amine than hydrogen peroxide, indicating that furan carboxyperoxy acid may be formed, leading to disproportionation with the amine, forming amine oxide and carboxylic acid.39,40 Our first study aimed to find the optimum conditions to form carboxylic acid with minimum conversion of amine. Then we could establish a process to isolate both products, developing an efficient and sustainable process.
Table 1 Oxidation performed on a 5 g scale of furfural at different temperatures, amine contents, hydrogen peroxide quantities and times. Experiments were performed upon gradual addition of H2O2 ensuring that the temperature remained within 15 °C of the starting temperature. Tributylamine was used as the amine. Yields were calculated through HPLC
Entry |
T (°C) |
Amine content (eq.) |
H2O2 concentration (%) |
H2O2 equivalent (eq.) |
Time (h) |
Yield (%) |
1 |
55 |
None |
30 |
1 |
1 |
0.03 |
2 |
55 |
1 |
30 |
1 |
1 |
68.9 |
3 |
55 |
0.7 |
30 |
1 |
1 |
62.9 |
4 |
55 |
0.5 |
30 |
1 |
1 |
35 |
5 |
70 |
0.7 |
30 |
1 |
1 |
61.9 |
6 |
70 |
1 |
30 |
1 |
1 |
62.6 |
7 |
55 |
1 |
30 |
2 |
1 |
95.2 |
8 |
55 |
1 |
50 |
1 |
2 |
88.4 |
We began by analysing the effect of different hydrogen peroxide concentrations, temperatures, amine molar ratios and times on the yield of reaction upon slow addition of hydrogen peroxide. It is important to mention that our screening experiments were designed to avoid a temperature increase of more than 15 °C as isothermal conditions were difficult to achieve due to the exothermicity of reaction. It required about 2 h to inject all of the hydrogen peroxide and the temperature increase was minor up to 70% of the total addition. A preliminary set of experiments was performed to analyse the effect of the base on the reaction yield (entries 1–4 in Table 1), revealing that stoichiometric amounts of amine are the optimum, with yields close to 70%. Although this is a step toward a viable process, these conditions prevent the separation of the final product since furfural is unstable at either low or high pH, which is required during the separation, leading to humin formation which deposits on the furoic acid crystals. In the ESI† we report two different isolations of furoic acids carried out with and without residual furfural. Increasing the temperature to 70 °C did not lead to any remarkable improvements in the final results (entries 5 and 6). A further increase in the yield could be achieved by increasing the equivalents of hydrogen peroxide (7) or using 50% hydrogen peroxide instead of 30% (8). The fact that higher yields are achieved with the same equivalent of H2O2 using 50% instead of 30% (entries 2 and 8) indicates an inhibitory effect of water on the kinetics of the reaction, and therefor it needs to be minimized to obtain high yield.
All results reported in Table 1 led to over 70% amine oxide formation, limiting the availability of amine for recycling and indicating that part of the hydrogen peroxide is not used for the oxidation of the aldehyde.
Larger scale trials
In order to have better temperature control, the scale of the reaction was increased to 20 grams, allowing the system to absorb the heat more efficiently, limiting the temperature overshoot which proved deleterious to the reaction. We cooled the reaction at 5 °C and exploited the exothermicity of the reaction to reach the desired temperature set-point. Once the addition of hydrogen peroxide was completed, the reaction flask was heated to the operating temperature. In Fig. 2 we report the results using tributylamine as the base since this is less volatile than triethylamine, minimizing amine losses through evaporation during the heating. Kinetic analysis over different temperatures revealed that most of the reaction occurs within the first hour of the addition of hydrogen peroxide. Different trends were observed at different temperatures. At 55 °C, the furoic acid yield reached 64% and a further 0.4 eq. were required to reach a yield of over 96%. At 70 °C, the oxidation was even more efficient, reaching 75% yield under stoichiometric conditions and 30% excess of hydrogen peroxide to enable us to reach 98% yield. At 90 °C, there was a decrease in yield and an increase in decomposition of hydrogen peroxide under basic conditions, decreasing the availability of the oxidant. Moreover, higher temperatures favour the formation of the amine oxide, decreasing further the substrate specificity of the oxidant.
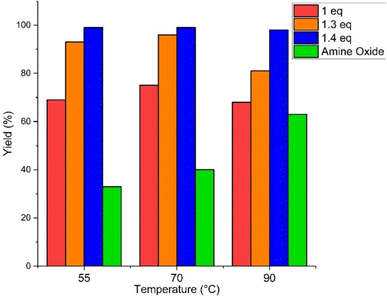 |
| Fig. 2 Oxidation of furfural at different temperatures and hydrogen peroxide equivalents. Amine oxide yield evaluated at the end of the H2O2 addition. | |
At all temperatures, full conversion of furfural was not achieved with 1 eq. of hydrogen peroxide since part of H2O2 still oxidizes the amine instead of the furfural and a small fraction decomposes under basic conditions into water and oxygen. By adding a further 0.3 eq. the conversion reached values over 96% at 70 °C, while at 55 and 90 °C, 0.4 eq. were needed.
Mode of addition
According to the previous experiments, temperature is the main parameter influencing the conversion of amine into amine oxide and this rises over the first equivalent of hydrogen peroxide added. A previous report on base assisted oxidation of aldehydes has shown that a strong excess of H2O2 (more than 2 eq.) is needed to achieve complete conversion of the substrate, probably due to the instability of the peroxide in a basic environment.41,42 In order to further understand the reaction parameters which influence this transformation, we studied four different peroxide addition methodologies. In order to analyse the selectivity and determine if the effect of excess amine and furfural over hydrogen peroxide can lead to the oxidation of amine oxide, we performed a gradual addition of amine and H2O2 into furfural and furfural and H2O2 into amine over 10 additions. The results in Fig. 3 demonstrated that there is not a significant difference in the final amine oxide content.
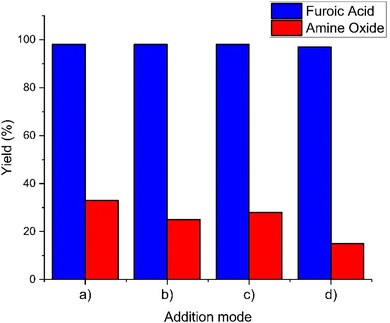 |
| Fig. 3 Effect of the addition mode of hydrogen peroxide on the yield of furoic acid and amine oxide. (a) Addition of hydrogen peroxide into a premixed mixture of furfural and amine at 55 °C, (b) addition of hydrogen peroxide (1.3 eq.) and amine into furfural at 55 °C through 10 additions, (c) addition of hydrogen peroxide (1.3 eq.) and furfural into amine at 55 °C through 10 additions, and (d) addition of hydrogen peroxide into a premixed amine-furfural mixture at 55 °C (addition of the first 0.5 eq. over 10 h). | |
Following our observation that most of the amine oxide is formed during the addition of the first 0.5 eq. of H2O2, we performed a very slow addition of this amount over 10 h and the amine oxide formation was reduced, increasing the amount of recoverable amine to 85%. This indicates that the addition of H2O2 has a strong influence over the selectivity of the reaction, improving the process when the addition is carried out slowly in the initial stage of the reaction when most of the furfural is not yet converted.
Separation of furoic acid and esterification
The purpose of the separation is to obtain furoic acid that can be esterified successfully with a fatty alcohol and implemented in the production of biobased furan surfactant. Our approach for the separation involved solubilizing the furoic acid into an aqueous phase through the addition of a strong base such as sodium hydroxide. The concentration of sodium hydroxide had to be carefully chosen since the water content has a dual effect. A high water content would compromise the separation of the furoic acid since the residual solubility is about 3%, and on the other hand at a low water content the sodium furoate precipitates out of the mixture, forming a very viscous slurry. We identified 20% NaOH as the ideal concentration to minimize the loss of furoic acid and avoid the precipitation of the salt. After the addition of NaOH, the hydrophobic amine separated into a different phase. According to NMR, the amine phase didn't show the presence of any degradation products and it could be re-used in a subsequent cycle. The aqueous layer was washed with 3 volumes of ethyl acetate to recover the amine oxide which can then be isolated through evaporation and finally furoic acid was precipitated through the addition of H2SO4, which leads to furoic acid upon filtration. The isolated yield (81%) didn't match the calculated one reported in the previous paragraph (96%) due to the residual product left in the water phase due to slow crystallization kinetics and saturation limits. However, the crude acid proved unsuitable for esterification with dodecanol, leading to conversions less than 20% in 2 h, whereas in our previous studies the furoic acid had to be completely converted. Upon our observation that residual solids were still present in the esterification reaction mixture, we identified the presence of sodium sulfate that coprecipitates with furoic acid during the acidification. In order to validate this hypothesis, we dissolved the solid in acetonitrile and filtered the residue. After the evaporation of the solvent, the furoic acid was esterified successfully with the same results as we reported in our previous publication. While this approach is successful on a small scale, the introduction of an organic solvent can be deleterious to the environmental and economic credentials of the process. On a large scale, however, this problem can be solved by dissolving the furoic acid in dodecanol and performing hot filtration since Na2SO4 is not soluble in dodecanol. This approach could not be tested on a small scale since the mixture in contact with the filter cools down rapidly, causing reprecipitation of the furoic acid.
Techno-economic assessment
The economic and environmental viability for the proposed process depends on the treatment of wastewater which contains sodium sulphate derived from the basification and acidification steps and recovery of the amine oxide from the oxidation. Since the wastewater contains about 20% salt, it has to be pre-treated before being treated in the wastewater treatment (WWT) to reach a level of total salinity less than 1% (general limit for WWT disposal). Moreover, part of the furoic acid cannot be recovered due to the saturation limit in water and will have to be disposed in the WWT. This will decrease the profitability of the plant but will not represent an environmental concern since furoic acid has been reported to be readily biodegradable. For optimum plant operation, we decided to consider as a base case scenario the recovery of both sodium sulfate and amine oxide since they are both highly concentrated in the respective stream. Indeed, treatment by reverse osmosis or ion exchange would lead to many operational problems due to precipitation on the membrane or bed saturation. This would lead to high operating costs with no added value. For this reason, we integrated the recovery of sodium sulfate to be valorised as a side product of the process through a multi-effect evaporation process, which allows the concentration and precipitation of the salt. We report the results as the minimum selling price (MSP), which includes the price to have zero net profit which includes the capital and operating costs in implementing the units to recover the compound. As per definition, this can be regarded as the cost to implement the section in the plant or a representative waste treatment cost to be disposed before treating the stream in the WWT.
Five different sections in the plant design can be identified and process conditions were chosen according to the experimental results reported in the previous section. In the oxidation and work-up sections, furfural is transformed into furoic acid in a batch reactor with a yield over 99% and separated through basification and acidification with recycling of the amine. 81% isolated yield is considered according to the saturation limit of this compound in water and our experimental results. In the esterification, the furoic acid is converted into dodecyl furoate through the addition of sulfuric acid as a catalyst and water is removed through evaporation. In amine oxide recovery, the water phase of the furoic acid section is washed with ethyl acetate in a ratio of 3
:
1 and the solvent is removed through a 3 stage evaporation process with working pressures of 0.4, 0.1 and 0.05 bar, which concentrates the oxides to 52% (the remaining is ethyl acetate). 99% of ethyl acetate is recovered while 1% is flared since final drying of amine oxide will be carried out through continuous nitrogen assisted evaporation (CO2 emissions are accounted). In the production of sodium sulfate, the stream of concentrated sodium sulfate (20%) with residual furoic acid (3%) is treated. This section consists of a 2-stage evaporation package at (0.6 and 0.2 bar), which removes water until achieving 12% water content in the solid, which is over the saturation point of sodium sulfate, allowing the sodium sulfate to precipitate. In the final stage, a concentrated solution of furoic acid is obtained, which can be further recovered by simple cooling and integrated into the final product. The process scheme with mass flow rates is reported in Fig. 4 and detailed mass balance is reported in the ESI.†
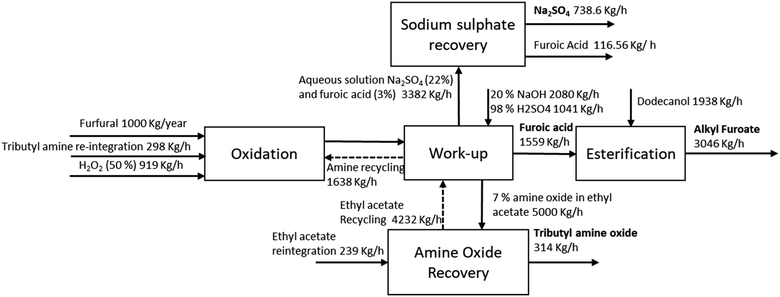 |
| Fig. 4 Process scheme showing different sections of the process with mass balance. | |
In Table 2 we report the contributions of each section towards the CO2 emissions and minimum selling price of each product to compensate for the operating and annualized capital costs. This includes operating costs for feedstocks, chemical auxiliaries, annualized equipment cost, labour and other annual costs (maintenance, laboratories, supervision, plant overheads, depreciation, insurance, local tax and royalties) with detailed values reported in the ESI.† The Total CAPEX which includes direct field cost, direct field labour cost, indirect cost and home-office cost has been estimated to be 24 m$ (details of the calculations in the ESI†).
Table 2 Results on the CO2 emissions and minimum selling price (MSP) for each section of the process
|
CO2 emissions (kg kg−1 product) |
MSP ($ per kg) |
Furoic acid |
0 |
2.06 |
Alkyl furoate |
0.06 |
2.44 |
Sodium sulphate |
0.345 |
0.56 |
Amine oxide |
0.505 |
2.19 |
It can be deduced that the main CO2 contribution derives from the recovery of the side products due to the use of evaporators, which require high energy inputs, while the oxidation and esterification sections have minimal emissions thanks to the possibility of heat recovery and high exothermicity of the oxidation. The process produces furoic acid and alkyl furoate at a low cost (market price of furoic acid: 11–15 $ per kg) while higher prices are required for sodium sulfate and amine oxide. Indeed, Na2SO4 has a market price of 0.116 $ per kg against the 0.56 $ per kg from our process, making its recovery non-competitive. This can therefore be regarded as a disposal cost for the concentrated water stream. Amine oxide also proved to require high capital costs for its recovery, and therefore its application needs to be found ideally in speciality chemical processes, which can afford higher selling prices. If long alkyl chain amines are used, the corresponding amine oxides can find applications as amphoteric surfactants used in personal care. For short chain amines, the amine oxide recovery section can be removed and the stream is treated for disposal along with sodium sulfate if no market is found. The amine oxide will remain in the water phase and treated in the WWT due its high reported biodegradability.
The process we present resulted in an overall environmentally friendly and economically viable process for the production of multiple valuable components. However, different considerations need to be taken into consideration for the environmental credentials of the process. Indeed, H2O2, even if its cost is negligible, has an environmental impact, which can be deleterious since its current production is heavily dependent on the usage of toxic and cancerogenic substances such as anthraquinone. Moreover, tributylamine and the corresponding oxides remain petroleum-based, which increases remarkably the carbon impact of the process for the production of the amine and the use of the oxide for a specific application. A full life cycle analysis would give a more detailed assessment of the sustainability of such a process.
Conclusions
We optimized a process for the production of furoic acid starting from furfural through an oxidation approach using a base and hydrogen peroxide as a stoichiometric oxidant with the final aim to produce the surfactant intermediate dodecyl furoate. The process proved to be highly efficient and selective, oxidizing more than 96% of the initial furfural into the final product. The process has different drawbacks due to product separation, which results in the loss of furoic acid through water saturation, partial loss of amine to oxidation to amine oxide and treatment of a highly concentrated sodium sulfate waste product. We countered these problems by studying a base case scenario where each product is valorised, implementing a separation technique for each of these streams. Amine oxide was removed through organic solvent washing and sodium sulfate through evaporation and precipitation, allowing the reconcentration of the residual furoic acid and re-precipitation in a separate stream. Technoeconomic analysis showed positive preliminary data in terms of the minimum selling price and CO2 emissions, establishing this process as a promising, scalable, efficient technology to be integrated in a biorefinery.
Conflicts of interest
The authors have no conflicts of interest to report.
Acknowledgements
AAG and James M. Perry wish to thank Mark Richardson for funding related to his postdoctoral research and PhD.
References
- A. Corma Canos, S. Iborra and A. Velty, Chem. Rev., 2007, 107, 2411–2502 CrossRef PubMed.
- F. Cherubini and A. H. Strómman, Energy Fuels, 2010, 24, 2657–2666 CrossRef CAS.
-
E4tech, Re-Cord and Wur, From the Sugar Platform to Biofuels and Biochemicals, 2015 Search PubMed.
- Ó. Ögmundarson, M. J. Herrgård, J. Forster, M. Z. Hauschild and P. Fantke, Nat. Sustain., 2020, 3, 167–174 CrossRef.
- M. G. Davidson, S. Elgie, S. Parsons and T. J. Young, Green Chem., 2021, 23, 3154–3171 RSC.
- J. Slak, B. Pomeroy, A. Kostyniuk, M. Grilc and B. Likozar, Chem. Eng. J., 2022, 429, 132325 CrossRef CAS.
- A. Al Ghatta and J. P. Hallett, Green Chem., 2022, 24, 3309–3313 RSC.
- X. Li, P. Jia and T. Wang, ACS Catal., 2016, 6, 7621–7640 CrossRef CAS.
- A. K. Mungray and P. Kumar, Int. Biodeterior. Biodegrad., 2009, 63, 981–987 CrossRef CAS.
- I. Dolganova, I. Dolganov, E. Ivanchina and E. Ivashkina, J. Surfactants Deterg., 2018, 21, 175–184 CrossRef CAS.
- D. S. Park, K. E. Joseph, M. Koehle, C. Krumm, L. Ren, J. N. Damen, M. H. Shete, H. S. Lee, X. Zuo, B. Lee, W. Fan, D. G. Vlachos, R. F. Lobo, M. Tsapatsis and P. J. Dauenhauer, ACS Cent. Sci., 2016, 2, 820–824 CrossRef CAS PubMed.
- P. Siwayanan, R. Aziz, N. A. Bakar, H. Ya, R. Jokiman and S. Chelliapan, J. Surfactants Deterg., 2014, 17, 871–880 CrossRef CAS.
- X. Yue and Y. Queneau, ChemSusChem, 2022, 2022, e202102660 Search PubMed.
- G. A. Kraus and J. J. Lee, J. Surfactants Deterg., 2013, 16, 317–320 CrossRef CAS.
- H. Nguyen, Y. Wang, D. Moglia, J. Fu, W. Zheng, M. Orazov and D. G. Vlachos, Catal. Sci. Technol., 2021, 11, 2762–2769 RSC.
- K. S. Arias, M. J. Climent, A. Corma and S. Iborra, ChemSusChem, 2014, 7, 210–220 CrossRef CAS PubMed.
- A. Al Ghatta, J. D. E. T. Wilton-Ely and J. P. Hallett, ChemSusChem, 2019, 12, 4452–4460 CrossRef PubMed.
- A. Al Ghatta, J. D. E. T. Wilton-Ely and J. P. Hallett, ACS Sustainable Chem. Eng., 2019, 7, 16483–16492 CrossRef.
- A. Al Ghatta, J. D. E. T. Wilton-Ely and J. P. Hallett, Green Chem., 2021, 23, 1716–1733 RSC.
- A. Wang, N. P. Balsara and A. T. Bell, Green Chem., 2018, 20, 2903–2912 RSC.
- G. Zang, A. Shah and C. Wan, J. Cleaner Prod., 2020, 260, 120837 CrossRef CAS.
- A. Gassama, C. Ernenwein, A. Youssef, M. Agach, E. Riguet, S. Marinković, B. Estrine and N. Hoffmann, Green Chem., 2013, 15, 1558–1566 RSC.
- A. Al Ghatta, R. C. Aravenas, Y. Wu, J. M. Perry, J. Lemus and J. P. Hallett, ACS Sustainable Chem. Eng., 2022, 10, 8846–8855 CrossRef CAS PubMed.
- Q. Tian, D. Shi and Y. Sha, Molecules, 2008, 13, 948–957 CrossRef CAS PubMed.
- D. Zhao, D. Zhao, D. Rodriguez-Padron, D. Rodriguez-Padron, R. Luque, R. Luque, C. Len and C. Len, ACS Sustainable Chem. Eng., 2020, 8, 8486–8495 CrossRef CAS.
- A. Al Ghatta, X. Zhou, G. Casarano, J. D. E. T. Wilton-Ely and J. P. Hallett, ACS Sustainable Chem. Eng., 2021, 9, 2212–2223 CrossRef CAS.
- B. Sang, J. Li, X. Tian, F. Yuan and Y. Zhu, Mol. Catal., 2019, 470, 67–74 CrossRef.
- N. K. Gupta, S. Nishimura, A. Takagaki and K. Ebitani, Green Chem., 2011, 13, 824 RSC.
- M. Douthwaite, X. Huang, S. Iqbal, P. J. Miedziak, G. L. Brett, S. A. Kondrat, J. K. Edwards, M. Sankar, D. W. Knight, D. Bethell and G. J. Hutchings, Catal. Sci. Technol., 2017, 7, 5284–5293 RSC.
- A. Roselli, Y. Carvalho, F. Dumeignil, F. Cavani, S. Paul and R. Wojcieszak, Catalysts, 2020, 10, 73 CrossRef CAS.
- X. Yu, Z. Miao, H. Wang, W. Jia, Q. Wang, Y. Sun, X. Tang, X. Zeng, S. Yang, Z. Li, Z. J. Wei, F. Xu and L. Lin, Fuel, 2022, 317, 123579 CrossRef CAS.
- Y. Zhang, Y. Cheng, H. Cai, S. He, Q. Shan, H. Zhao, Y. Chen and B. Wang, Green Chem., 2017, 19, 5708–5713 RSC.
- G. Yi, S. P. Teong and Y. Zhang, Green Chem., 2016, 18, 979–983 RSC.
- C. P. Ferraz, M. Zieliński, M. Pietrowski, S. Heyte, F. Dumeignil, L. M. Rossi and R. Wojcieszak, ACS Sustainable Chem. Eng., 2018, 6, 16332–16340 CrossRef CAS.
- A. Brandolese, D. Ragno, G. Di Carmine, T. Bernardi, O. Bortolini, P. P. Giovannini, O. G. Pandoli, A. Altomare and A. Massi, Org. Biomol. Chem., 2018, 16, 8955–8964 RSC.
- S. Kar, Q. Q. Zhou, Y. Ben-David and D. Milstein, J. Am. Chem. Soc., 2022, 144, 1288–1295 CrossRef CAS PubMed.
- S. Xu, X. Zhang, W. Xiong, P. Li, W. Ma, X. Hu and Y. Wu, Chem. Commun., 2022, 58, 2132–2135 RSC.
- M. Liu and C.-J. Li, Angew. Chem., 2016, 128, 10964–10968 CrossRef.
- W. D. Emmons, J. Am. Chem. Soc., 1957, 79, 5528–5530 CrossRef CAS.
- K. Ibne-Rasa and J. Edwards, J. Am. Chem. Soc., 1962, 84, 763–768 CrossRef CAS.
- Z.-Q. Cong, C.-I. Wang, T. Chen and B.-Z. Yin, Synth. Commun., 2006, 679–683 CrossRef CAS.
- M. J. da Silva and A. A. Rodrigues, Mol. Catal., 2020, 493, 111104 CrossRef CAS.
|
This journal is © The Royal Society of Chemistry 2023 |
Click here to see how this site uses Cookies. View our privacy policy here.