Layer-by-layer anodes with an orientation-arranged structure induced by magnetic field for high-performance lithium ion batteries†
Received
20th September 2022
, Accepted 21st November 2022
First published on 21st November 2022
Abstract
Fe3O4/carbon fibers (CFs) in a novel layer-by-layer (LBL) alignment as anodes for lithium ion batteries (LIBs) were successfully prepared through the assistance of a magnetic field. In this approach, Fe3O4 nanoparticles were deposited on carbon fibers by the sol–gel approach. Induced by a magnetic field, the alignment of Fe3O4/CFs was formed, and the LBL structure was fabricated by alternately dropping the hydrous and organic slurries of active materials. Due to the change in the orientation of the magnetic field, each subsequent prepared Fe3O4/CF alignment layer was vertical to the last one, and the electrical conductivity of Fe3O4/CFs, spaces for Li+ storage and channels for the diffusion of Li+ all sharply increased. Thus, a high electrochemical performance was achieved: specific capacities of 1671.3 and 504.6 mA h g−1 at current densities of 0.1 A g−1 and 3 A g−1, respectively; capacity retention of 83.8% and specific capacity > 420 mA h g−1 at 3 A g−1 after 2000 cycles for LIBs.
1 Introduction
With the rapid promotion and popularization of portable electronics, the development of high-performance Li ion batteries (LIBs) is inevitable.1–5 One strategy is the design of novel electrodes for the batteries by improving the specific capacity of active materials or modifying the structure of electrodes.5–10 Transition metal oxides and sulfides are promising anode materials for LIBs and sodium ion batteries (SIBs) due to their high theoretical specific capacity (e.g., 926 mA h g−1 for Fe3O4).11–14 However, some challenges must be overcome before the commercial applications of transition metal oxide or sulfide-based electrodes can be achieved; for example, excessive volume effect, suffered a lot by the electrode materials, is caused by the active material layer and current collector in the repeated extraction-insertion of Li+/Na+.13,14 Moreover, the poor intrinsic conductivity of transition metal oxides or sulfides also limits the performance of anodes.15,16 In recent years, many studies have investigated methods to overcome the above defects: one strategy is loading these active materials on a conductive framework (such as graphene, porous carbon, amorphous carbon) to enhance the transfer of electrodes;17–21 the preparation of an active materials@shell structure is another strategy to buffer the excessive volume effect as the strong skeleton of shells limits the volume change of active materials in charge/discharge processes.8,22–27 Additionally, modifying the structure of electrodes is also an efficient strategy to conquer the above challenges.28–32 Fe3O4/Cu nanorod anodes were fabricated by a two-step approach: Cu nanorods were grown using a electrochemically assisted template method and then Fe3O4 nanoparticles were electrodeposited.33 A carbon cloth was also employed as general scaffolds to develop novel electrodes without the usage of binders.34,35 Notably, the electrodes were also modified by the assistance of a magnetic field that served as the driving force for the self-assembly of materials.36–39 For example, graphitic anodes were modified by ferromagnetic nanoparticles, and the current collector could be vertically distributed so as to reduce the tortuosity under the induction of the magnetic field.36,37 Single layer orientation-arranged electrodes were also induced by a magnetic field because they were made from Fe3O4 composites. Such a layered electrode structure built an efficient conductive network and reduced the electrode resistance, further enhancing the rate capacity and cycle performance of LIBs.38,39
In the present work, Fe3O4/carbon fibers (CFs) in a novel layer-by-layer (LBL) alignment have been successfully prepared through the assistance of a magnetic field as anodes for LIBs. In this approach, Fe3O4 nanoparticles were deposited on carbon fibers by the sol–gel approach. Induced by a magnetic field, the alignment of the Fe3O4/CFs was formed and the LBL structure was fabricated by alternately dropping the hydrous and organic slurries of active materials. Due to the change in the orientation of the magnetic field, the prepared Fe3O4/CF alignment layer was vertical to the last one. These LBL Fe3O4/CF alignments might be superb anode materials for LIBs and SIBs, exhibiting superior electrochemical properties.
2 Experiment
2.1 Preparation of Fe3O4/CFs
To synthesize a Fe3O4/CF composite, in N2 atmosphere, 0.01 mol Fe2+ and 0.02 mol Fe3+ ions were dissolved into 100 mL deionized water and then 2.52 g carbon fibers were dispersed in deionized water stirred at 60 °C; Fe3O4 nanoparticles were deposited on carbon fibers by adding NaOH into the solution to maintain pH > 10. Finally, Fe3O4/CFs was obtained after filtering and drying.
2.2 Preparation of the layer-by-layer Fe3O4/CF alignment-anode
In this work, arboxyl methylated cellulose (CMC) and N-methyl pyrrolidinone (NMP) were employed as binders. Fe3O4/CFs, super-p and PVDF were dispersed in N-methyl pyrrolidinone (NMP) to get a slurry with a mass ratio of 8
:
1
:
1. The organic slurry was dropped on the copper foil, and then the Fe3O4/CF coating was placed in the magnetic field for 1 h to form the first Fe3O4/CF alignment-layer. To form the second layer, Fe3O4/CF, super-p and CMC were dispersed in distilled water at a weight ratio of 8
:
1
:
1. The hydrous slurry was dropped on the first Fe3O4/CF alignment layer and then was placed in the magnetic field for 1 h, which was vertical to the alignment of the first layer. Thus, the layer-by-layer Fe3O4/CF alignment-anode was formed by alternately dropping the hydrous and organic mixing slurries in the magnetic field (Fig. 1). For comparison, 2-layer, 4-layer and 6-layer anodes were assembled. Unfortunately, the 6-layer anode was too thick and cracked. The 2-LBL and 4-LBL Fe3O4/CF alignment anodes were marked by 2L and 4L Fe3O4/CFs, respectively. Fe3O4/CF-based anode prepared by traditional methods without the LBL alignment was marked by R-Fe3O4/CFs. To observe the cross-section of the layer-by-layer Fe3O4/CF alignment structure, a 5-LBL structure was prepared on the glass slide, which was easier broken than the structure prepared on the copper foil.
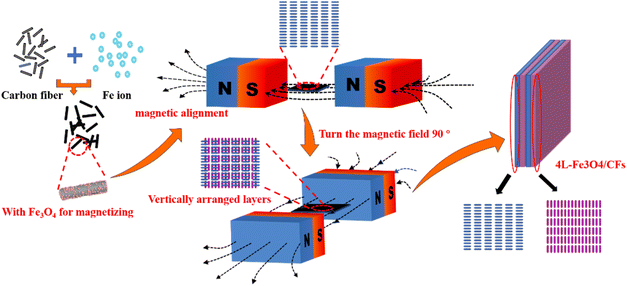 |
| Fig. 1 Scheme of the pathway for the synthesis of an LBL Fe3O4/CF alignment-anode. | |
2.3 Characterization
Samples were characterized and analyzed by a X-ray diffractometer (XRD, Bruker AXS), vibrating sample magnetometer (VSM, MLVSM9 MagLab 9 T, Oxford Instrument), high resolution transmission electron microscopy (TEM: JEOL, JEM-2100F) and field emitted scanning electron microscopy (FESEM, JEOL: JSM-6700F).
2.4 Electrochemical measurements
Coin cells (2016-type) were assembled by using the as-prepared LBL alignment structure as a working electrode and a lithium metal disk as the counter. Porous polypropylene film (Celgard 2400) and 1 M LiPF6 dissolved in a solution with 1
:
1
:
1 (volume ratio) ethylene carbonate (EC), diethyl carbonate (DEC) and dimethyl carbonate (DMC) were used as the separator and electrolyte, respectively. After assembly, the cyclic voltammetry (CV) profiles were scanned at a rate of 0.1 mV s−1 in the voltage range of 0.01–3 V (electrochemical workstation: CHI 760E). The cycling stability and galvanostatic charge–discharge (GCD) measurements of the cells were carried out at between 0.001 and 3 V (vs. Li+/Li, for LIBs) with a battery test system (LAND CT-2001A tester). An electrochemical workstation (Autolab Pgstat302n) was employed to measure the impedance spectrum and simulate the circuit of batteries. The frequency range was 0.01 Hz to 100 kHz, with a 5 mV amplitude.
3 Results and discussion
The XRD pattern of Fe3O4/CFs prepared by the sol–gel approach is shown in Fig. 2a and the peaks are consistent with the XRD patterns of Fe3O4 (JCPDS: 19-0629), of which 2θ = 30.07°, 35.42°, 43.05°, 53.41°, 56.93° and 63.48° correspond to the (220), (311), (400), (422), (511) and (440) crystal planes of Fe3O4, respectively; and no characteristic peaks of impurities (e.g., Fe2O3 and other ferrous oxides) have been found in the XRD pattern of Fe3O4/CFs. The diffraction peak (2θ = 26.6°) is in the (002) crystal plane of the carbon fiber, which is very strong, indicating that the carbon fiber has superior crystallinity. When being dispersed in an aqueous solution, all prepared Fe3O4/CF composites can respond to the added magnetic field (Fig. S1 in ESI†). According to the results of the VSM, the saturation magnetization (Ms) and coercivity values (Hc) of Fe3O4/CFs are 62 emu g−1 and 135 Oe, respectively (Fig. 2b). Thus, the magnetic property of the prepared Fe3O4/CFs can be aligned by being induced with magnets.
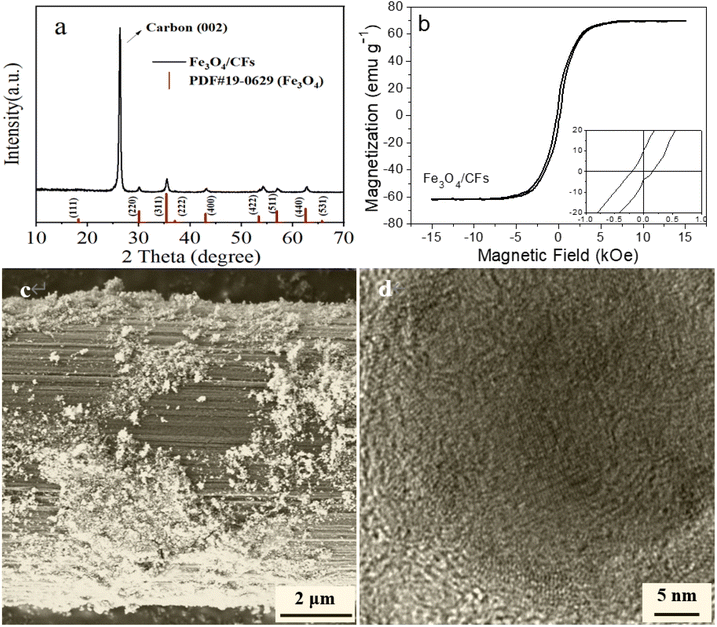 |
| Fig. 2 (a) XRD pattern, (b) VSM hysteresis loops (the central part of the loop was inserted) and (c) SEM image of Fe3O4/CFs, and (d) high resolution TEM images of Fe3O4 nanoparticles. | |
The morphology and microstructure of the Fe3O4/CF sample and the 4L-Fe3O4/CF anode are shown in Fig. 2 and 3. The SEM image of Fe3O4/CFs is shown in Fig. 2c and Fe3O4 nanoparticles are distributed on the surface of carbon fiber (their average diameter is ∼6.5 μm). The average size of the prepared Fe3O4 nanoparticles is ∼20 nm and the (220) lattice of Fe3O4 nanoparticles can be easily found in the HRTEM image (Fig. 2d). Because of magnetic Fe3O4 nanoparticles, the majority of Fe3O4/CFs is moved to form the alignment; as shown in Fig. 3a, the nanofibers are regularly interleaved and form the support skeleton network of the anode. Due to the alignment layer being very thin, the next Fe3O4/CF layer is exposed, which causes the orientation-arranged structure to look ambiguous (Fig. 3a). Thus, an optical microscope is employed to further observe the orientation-arranged anodes (Fig. S2†), suggesting the orientation of the Fe3O4/CFs is well arranged. Alternately dropping the hydrous and organic mixing slurries causes the LBL Fe3O4/CFs alignment anode and the Fe3O4/CFs alignment layer to be vertical to the next layer due to the changing orientation of the magnetic field (Fig. 3b and c). The fibers are overlapped regularly to form a continuous electronic conductive network in the anode. It is worth mentioning that the interleaving gap formed by the regular alignment of fibers in the anode structure may provide sufficient space for the volume change of Fe3O4 particles during charge and discharge and higher Li+ storage space, which might enhance the stability and specific capacity accordingly. Additionally, there are such interleaving gaps in the longitudinal distribution of the whole anode and these form a layered continuous conductive network, which further optimizes the anode. Therefore, under the same anode load, the layered alignment anode has more advantages than the traditionally assembled anode (R-Fe3O4/CFs).
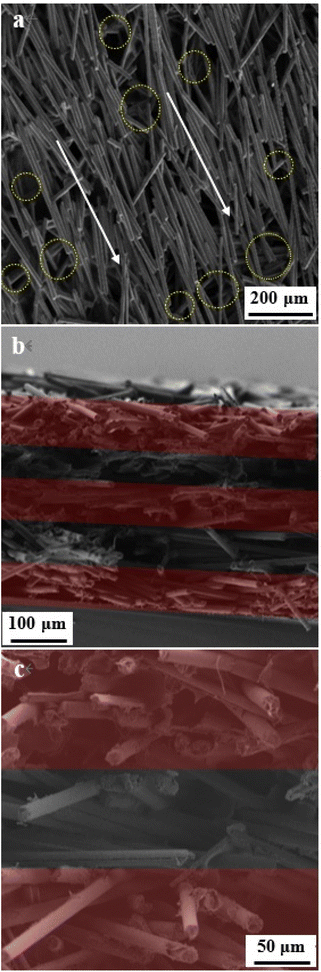 |
| Fig. 3 SEM images of (a) Fe3O4/CF alignment (because the alignment layer is very thin, the next Fe3O4/CFs layer is exposed, which is marked by yellow circles) and (b) and (c) cross section of layer-by-layer structure. | |
Fig. 4a shows the cyclic voltammetry curve of the prepared Fe3O4/CF anodes measured at room temperature at a scanning rate of 0.1 mV s−1 and voltage of 0.01–3 V (vs. Li/Li+). In the first cycle, the reduction peak at 0.55 V is caused by the reduction of Fe3+ and Fe2+ to Fe0 and the irreversible reaction of the electrolyte to form a solid electrolyte interface (SEI) layer.40–45 The reduction peak at 0.902 V can be attributed to the insertion of Li+ to form the LixFe3O4 intermediate.21 During charging, the wide peak at 1.73 V is mainly due to the oxidation of Fe0 to Fe2+ and Fe3+. Furthermore, the anodic peak at about 0.25 V represents the intercalation processes of lithium in the carbon phase (C + xLi+ + xe− → LixC).40 After the first cycle, the redox peaks shift to a higher potential. The redox peaks in the second and third cycles correspond to the mutual transformation between Fe0 and Fe3O4, and the reaction is 3Fe + 4Li2O ↔ Fe3O4 + 8Li+ + 8e−.21,41,42 The two reduction peaks at 0.6 V and 0.905 V merge into one reduction peak in the second and third cycles, and the peak intensity is weakened, indicating that there is an irreversible capacity loss in the initial intercalation process.
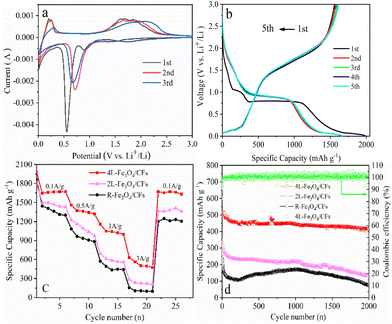 |
| Fig. 4 Electrochemical performance of the prepared anodes for LIBs: CV profile (a) at a scan rate of 0.1 mV s−1 between 0.01 and 3 V vs. Li+/Li for the 1st–3rd charge/discharge cycles of 4L-Fe3O4/CFs; (b) the galvanostatic charge–discharge profiles of 4L-Fe3O4/CFs; (c) charge–discharge cycling performance of 4L-Fe3O4/CFs and 2L-Fe3O4/CFs, and R-Fe3O4/CFs at different current densities from 0.1 to 3 A g−1; (d) specific capacity retention rate of 4L-Fe3O4/CFs at 3 A g−1. | |
Fig. 4b shows the discharge–charge profiles of the 4L-Fe3O4/CF anode at a current density of 0.1 A g−1. It can be observed that the specific discharge/charge capacity of the first cycle is 1983.3 mA h g−1 and 1558.4 mA h g−1, respectively, with initial coulombic efficiency (ICE) is 78.6%. The irreversible capacity mainly comes from the formation of the SEI membrane. The discharge voltage platforms of the first cycle are located at ∼1 and ∼0.75 V (Fig. 4b), which correspond to the two reduction peaks in Fig. 4a.
The curves of the second and third cycles basically coincide, indicating that the formation of the SEI film has been basically completed in the first cycle, and the anodic active material tends to be stable. In the period of 2–5 cycles, CE is significantly increased to nearly 100%, and the curves overlap, demonstrating significant stability.
All Fe3O4/CF anodes' rate performances have been tested at gradually increased current densities ranging from 0.1 to 3 A g−1 (Fig. 4c). The reversible specific capacities of the 4L-Fe3O4/CF anode are 1671.3, 1360.1, 1022.5 and 504.6 mA h g−1 at current densities of 0.1, 0.5, 1 and 3 A g−1, respectively. In contrast, 2L-Fe3O4/CFs (1428.6, 1091.7, 584.1 and 220.2 mA h g−1, respectively) and R-Fe3O4/CFs (1299.3, 908.7, 448.1 and 106.7 mA h g−1, respectively) exhibit poor rate performance. When the current density is returned to 0.1 A g−1, the capacity is 1670.6 mA h g−1, which is equivalent to 99.96% of the first reversible specific capacity. It is worth noting that the high discharge capacity of the 4L-Fe3O4/CF anode should be attributed to the orientation-arranged and layered structure of the anode.
In order to further examine the superior electrochemical performance of the 4L-Fe3O4/CF anode, the cyclic performance of the 4L-Fe3O4/CF anode was investigated (Fig. 4d). At a high current density of 3 A g−1, the capacity of the 4L-Fe3O4/CF anode decays slowly in the first 100 cycles, and it is still able to maintain the reversible capacity of 421.1 mA h g−1. The stablity of the 4L-Fe3O4/CFs is one time more than that of the 2L-Fe3O4/CFs and the R-Fe3O4/CFs, after 2000 cycles. After 20 cycles, CEs of all Fe3O4/CF anodes reach 100%. The cycle stability and capacity are greatly enhanced compared with 2L-Fe3O4/CFs and R-Fe3O4/CFs, and the coulomb efficiency is close to 100%. It shows that the 4L-Fe3O4/CF anode has superior cycle stability, and the reversibility of specific capacity is still very good under high current charge and discharge. This outstanding high-rate stability performance is due to the alignment and layered structure of the anode that prevent the crushing and loss of active substances in the process of circulation.
To gain a comprehensive understanding of the lithium ion storage mechanism of the 4L-Fe3O4/CF anode, a series of CV measurements were conducted at various scanning rates. The type of Li+ storage can be qualitatively distinguished based on the CV curve at various scan rates (Fig. 5a). The peak current (i) and scan rate (v) have a relationship shown in the following equations:
| log(i) = log(a) + b log(v) | (2) |
where
a and
b are constants; the value of
b can be determined by the slope of formula
(2). When
b is 0.5, diffusion control contributes to the peak current; when
b is 1, capacitance contributes to the peak current.
41 According to the data presented in
Fig. 5b, the two representative peak
b values of the CV curve are 0.78 and 0.88, with an average of 0.83, indicating that capacitance cannot be ignored and plays a leading role.
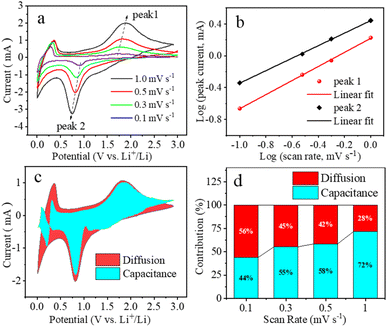 |
| Fig. 5 (a) CV curves of 4L-Fe3O4/CFs at scan rates from 0.1 to 1 mV s−1; (b) relationship between log(peak current) and log(scan rate) plots for anodic and cathodic sweeps of CV; (c) fitted pseudo capacitance contribution of 4L-Fe3O4/CFs at 0.5 mV s−1 and (d) contribution ratio of capacitance-controlled and diffusion-controlled capacities at various scan rates for LIBs. | |
The peak current value consists of the capacitive contribution (k1v) and the diffusion control contribution (k2v1/2). In order to distinguish quantitatively between two types of Li+ storage, eqn (2) can be transformed into eqn (3):
k1 and
k2 have different values at different voltage positions.
40 Therefore, the percentage of lithium storage capacity can be determined by calculating
k1 and
k2. For instance, when the scan rate is 0.5 mV s
−1, the capacitive contribution in
Fig. 5c corresponds to the blue region, while the diffusive contribution corresponds to the red one. At various scan rates, the percentage of diffusion control and capacitance to total capacity is shown in
Fig. 5d. As the sweep speed increases, the proportion of capacitive contribution increases proportionally: when the sweep speed is 0.1, 0.3, 0.5, and 1.0 mV s
−1, the proportion of capacitive contribution is 44%, 55%, 58%, and 72%, respectively. Such a high capacitance explains further why the Fe
3O
4/CFs anode's specific capacity exceeds the theoretical capacity. The capacitance is a result of the novel alignment structure between the layers of anode, which enables faster lithium ion and electron transfer and transmission.
The electrochemical impedance spectroscopy (EIS) of 4L-Fe3O4/CFs and R-Fe3O4/CFs has been tested (Fig. 6a) to better examine the mechanism of the superior electrochemical performance of 4L-Fe3O4/CFs. The equivalent circuit diagram obtained by simulation has been inserted, as shown in Fig. 6a. The semicircle in the high frequency region represents charge transfer, whereas the linearity in the low frequency region represents diffusion. The charge transfer resistance (Rct) of 4L-Fe3O4/CFs is much lower (158 Ω) than that of R-Fe3O4/CFs (583 Ω), indicating that the LBL structure of 4L-Fe3O4/CFs sharply improves the electrical conductivity of Fe3O4/CFs. CNT/fibers have come under the spotlight because of the possibility that they can be arranged in a controlled way.43 Therefore, it is necessary to construct orientation-arranged composite structures for improving the properties of composites. For example, in research investigating the effect of aligning CNTs in composite material structures, a remarkable improvement in the electrical properties of CNT composites was observed, as compared to their random placements.44 In recent research reported by Lee et al., two factors, the CNT length and their arrangement, were introduced as important characteristics affecting electron transport properties in the matrix of composite materials.45 Additionally, the linear fitting of Z′–ω−1/2 in the low-frequency region is showed in Fig. 6b, from which a slope of σ can be obtained. The lithium-ion diffusion coefficient can be computed from the formulae as follows:
| D = R2T2/(2A2n4F4C2σ2) | (4) |
| Z′ = Rs + Rct + σ2ω−1/2 | (5) |
where
R and
T represent gas constant and room temperature, respectively.
A,
n,
F and
C correspond to the surface area of the anode, the number of electrons per molecule participating in the electron transfer reaction, the Faraday constant, and the concentration of lithium ions in the anode, respectively. In addition,
σ is the slope of the line
Z′–
ω−1/2, which can be obtained from the line of
Z′–
ω−1/2 (shown in
Fig. 6b). The only variable that influences the calculation result in this formula is
σ. The lithium ion diffusion coefficient
DLi+ (cm
2 s
−1) of the 4L-Fe
3O
4/CF anode is 5.195 × 10
−15 cm
2 s
−1, which is a bit greater than that of R-Fe
3O
4/CFs (3.448 × 10
−15 cm
2 s
−1), according to the calculations, which suggests the LBL structure enhances Fe
3O
4/CFs mainly by improving their electrical conductivity.
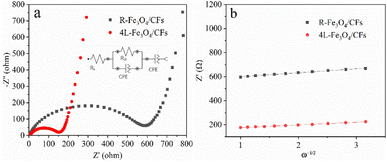 |
| Fig. 6 (a) Nyquist plots and Randles equivalent circuit of the prepared 4L-Fe3O4/CFs, R-Fe3O4/CFs anodes and the common equivalent circuit, and (b) the relationship between Z′ and ω−1/2 of 4L-Fe3O4/CFs and R-Fe3O4/CFs anodes (vs. Li/Li+). | |
It should be noted that the layer-by-layer structure of the anode improves the electrochemical performance of Fe3O4/CFs due to the novelty of the structure. The present LBL structure of the anodes sharply improves the electrical conductivity of Fe3O4/CFs. In the 4L-Fe3O4/CF anode, each alignment layer is vertical to the next layer, which increases the contact between two layers. Thus, a regular and continuous conductive network has been built, which gives 4L-Fe3O4/CFs higher conductivity, significantly reduces the Rct (Fig. 6a), leading to its superior rate performance (Fig. 4c). Additionally, the ordered structure could create many nanopores in the LBL anode, which provides more spaces for Li+ storage (Fig. 4c) or channels for the diffusion of Li+ (Fig. 6b). Finally, the novel structure can preserve the mechanical integrity of the anode by buffering the volume change, and further preventing the pulverization of Fe3O4 during the charge–discharge process; with the same loading of Fe3O4/CFs, 4L-Fe3O4/CFs has higher retention of specific capacity than 2L-Fe3O4/CFs in the cycle performance test (Fig. 4d). The 4L-Fe3O4/CF anode performs better (1671.3 mA h g−1 at a current density of 0.1 A g−1; 504.6 mA h g−1 at 3 A g−1) than many reported Fe3O4-based anodes for LIBs (at 0.1 A g−1): ∼600 (Fe3O4/Fe3C/CF),16 ∼732 (C/Fe3O4/rGO),20 <772 (Fe3O4/rGO),19 973 (Fe3O4/rGO),42 1084 (porous Fe3O4/carbon microspheres (PFCMs)),46 1101.4 (Fe3O4@C2e),47 1334 (Fe3O4@C/rGO),17 1411.8 (Fe3O4/C),48 ∼1500 (hollow Fe3O4/graphene),49 903 (at 0.2C, magnetic field-induced orientation-arranged Fe3O4/graphene nanocomposites)38 and 1140 (at 0.2C, magnetic field assisted orientation-arranged Fe3O4 nanocrystal/rGO paper)39 mA h g−1; at 3 A g−1: <250 (α-Fe2O3@Fe3O4 heterostructure (CFH)),21 335.8 (Fe3O4/rGO),19 <400 (Fe3O4/Fe3C/CF),16 <400 (N-doped carbon nanofibers (Fe3O4/NCNFs)),50 240 (at 5C, magnetic field-induced orientation-arranged Fe3O4/graphene nanocomposites),38 <500 (Fe3O4@C/rGO)51 and ∼500 (porous Fe3O4/carbon microspheres (PFCMs)46 mA h g−1). Hence, such a layer-by-layer Fe3O4/CF alignment provides a novel method for advanced electrodes, which might be widely used in areas as supercapacitors, catalysis, adsorbents and fuel cells.52–60
4 Conclusions
In summary, Fe3O4/carbon fibers in a layer-by-layer alignment have been successfully prepared through a facile approach as anodes for LIBs. Each alignment layer is vertical to the one before it, which increases contact between two layers, leading to the sharp increase of the electrical conductivity of Fe3O4/CFs, as well as more spaces for Li+ storage and channels for the diffusion of Li+. Thus, a high electrochemical performance is achieved, with specific capacities of 1671.3 and 504.6 mA h g−1 at current densities of 0.1 A g−1 and 3 A g−1, respectively; capacity retention of 83.8% and specific capacity >420 mA h g−1 at 3 A g−1 after 2000 cycles for LIBs.
Conflicts of interest
The authors declare no conflicts of interest.
Acknowledgements
This research was supported by funds from Shanghai Institute of Technology (YJ2010-50-1), Pujiang Talent Project (13PJ1407400) and funds (14520503100, 15520503400) from science and technology commission of Shanghai municipality, and research fund (project #21306113) from the National Natural Science Foundation of China.
Notes and references
- Y. Q. Wang, N. An, L. Wen, L. Wang, X. T. Jiang, F. Hou, Y. X. Yin and J. Liang, J. Energy Chem., 2021, 55, 391–419 CrossRef CAS.
- W. L. Cai, Y. X. Yao, G. L. Zhu, C. Yan, L. L. Jiang, C. X. He, J. Q. Huang and Q. Zhang, Chem. Soc. Rev., 2020, 49, 3806–3833 RSC.
- L. J. Xie, C. Tang, Z. H. Bi, M. X. Song, Y. F. Fan, C. Yan, X. M. Li, F. Y. Su, Q. Zhang and C. M. Chen, Adv. Energy Mater., 2021, 11, 2101650 CrossRef CAS.
- H. W. Wang, J. Z. Fu, C. Wang, J. Y. Wang, A. K. Yang, C. C. Li, Q. F. Sun, Y. Cui and H. Q. Li, Energy Environ. Sci., 2020, 1, 848–858 RSC.
- K. W. Mu, K. X. Liu, Z. Y. Wang, S. Zanman, Y. H. Yin, X. B. Liu, Y. S. Li, B. Y. Xia and Z. P. Wu, J. Mater. Chem. A, 2020, 8, 19444–19453 RSC.
- P. Li, J. Y. Hwang and Y. K. Sun, ACS Nano, 2019, 13, 2624–2633 CAS.
- A. Tolosa, M. Widmaier, B. Kruner, J. M. Griffin and V. Presser, Sustainable Energy Fuels, 2018, 2, 215–228 RSC.
- Z. M. Zheng, P. Li, J. S. Huang, H. D. Liu, Y. Zao, Z. L. Hu, L. Zhang, H. X. Chen, M. S. Wang, D. L. Peng and Q. B. Zhang, J. Energy Chem., 2020, 41, 126–134 CrossRef.
- X. Li, X. H. Sun, X. D. Hu, F. R. Fan, S. Cai, C. M. Zheng and G. D. Stucky, Nano Energy, 2020, 77, 105143 CrossRef CAS.
- S. L. Gao, F. Y. Sun, A. Brady, Y. Y. Pan, A. Erwin, D. D. Yang, V. Tsukruk, A. G. Stack, T. Saito, H. B. Yang and P. F. Cao, Nano Energy, 2020, 73, 104804 CrossRef CAS.
- B. Y. Sun, W. Zheng, X. C. Yin, X. Chen, F. P. Kong, S. F. Lou, C. Y. Du, P. J. Zuo, J. Y. Xie, J. J. Wang and G. P. Yin, J. Phys. Chem. C, 2021, 125, 22435–22445 CrossRef CAS.
- Q. Li, H. S. Li, Q. T. Xia, Z. Q. Hu, Y. Zhu, S. S. Yan, C. Ge, Q. H. Zhang, X. X. Wang, X. T. Shang, S. T. Fan, Y. Z. Long, L. Gu, G. X. Miao, G. H. Yu and J. S. Moodera, Nat. Mater., 2021, 20, 76–83 CrossRef CAS PubMed.
- Y. Yang, W. Yuan, X. Q. Zhang, C. Wang, Y. H. Yuan, Y. Huang, Y. T. Ye, Z. Q. Qiu and Y. Tang, Renewable Sustainable Energy Rev., 2020, 127, 109884 CrossRef CAS.
- X. L. Wang, Y. G. Liu, H. Y. Han, Y. Y. Zhao, W. M. Ma and H. Y. Sun, Sustainable Energy Fuels, 2017, 1, 915–922 RSC.
- Q. Q. Peng, C. Guo, S. Qi, W. W. Sun, L. P. Lv, F. H. Du, B. F. Wang, S. Q. Chen and Y. Wang, RSC Adv., 2021, 11, 1261–1270 RSC.
- W. J. Wang, D. M. Chen, H. Xu, G. X. Yu, S. Q. Sun, W. Zhang and J. Chen, Sustainable Energy Fuels, 2020, 4, 3519–3527 RSC.
- X. Y. Li, L. Z. Chen, Y. Q. Qu and Y. Y. Ma, Sustainable Energy Fuels, 2018, 2, 1124–1140 RSC.
- L. L. Ma, B. X. Hou, N. Z. Shang, S. H. Zhang, C. Wang, L. B. Zong, J. J. Song, J. Y. Wang and X. X. Zhao, Mater. Chem. Front., 2021, 5, 4579–4588 RSC.
- C. R. Hao, T. G. Gao, A. B. Yuan and J. Q. Xu, Chin. Chem. Lett., 2021, 32, 113–118 CrossRef CAS.
- Q. C. Wu, R. L. Jiang and H. W. Liu, Ceram. Int., 2020, 46, 12732–12739 CrossRef CAS.
- Q. Y. Yi, M. M. Du, B. Shen, J. H. Ji, C. C. Dong, M. Y. Xing and J. L. Zhang, Sci. Bull., 2020, 65, 233–242 CrossRef CAS.
- N. N. Li, Z. M. Sheng, H. L. Tian, C. K. Chang, R. P. Jia and S. Han, RSC Adv., 2018, 8, 33030–33034 RSC.
- Z. M. Sheng, N. N. Li, Q. M. Xu, C. Y. Hong, S. Y. Wu, C. K. Chang, S. Han and C. M. Li, Sustainable Energy Fuels, 2021, 5, 4080–4086 RSC.
- N. N. Li, Z. M. Sheng, H. Huang, Z. Z. Gan, C. K. Chang, R. P. Jia and S. Han, J. Alloys Compd., 2019, 792, 25–31 CrossRef CAS.
- Z. K. Liu, J. M. Kang, Z. H. Zhao, Y. H. Zheng, Y. Liu, C. X. Xiong, S. Wang and Q. L. Yang, Carbon, 2021, 171, 36–44 CrossRef CAS.
- C. Y. Hong, Z. M. Sheng, M. H. Hu, X. Y. Dai, C. K. Chang, Q. Z. Chen and D. Y. Zhang, RSC Adv., 2016, 6, 59896–59899 RSC.
- Z. M. Sheng, X. J. Chang, Y. H. Chen, C. Y. Hong, N. N. Li, C. K. Chang, R. P. Jia and S. Han, RSC Adv., 2017, 7, 42083–42087 RSC.
- X. K. Lu, A. Bertei, D. P. Finegan, C. Tan, S. R. Daemi, J. S. Weaving, K. B. O'Regan, T. M. M. Heenan, G. Hinds, E. Kendrick, D. J. L. Brett and P. R. Shearing, Nat. Commun., 2020, 11, 2079 CrossRef CAS.
- M. Z. Ge, C. Y. Cao, G. M. Biesold, C. D. Sewell, S. M. Hao, J. Y. Huang, W. Zhang, Y. K. Lai and Z. Q. Lin, Adv. Mater., 2021, 33, 2004577 CrossRef CAS PubMed.
- C. Heubner, A. Nickol, J. Seeba, S. Reuber, N. Junker, M. Wolter, M. Schneider and A. Michaelis, J. Power Sources, 2019, 419, 119–126 CrossRef CAS.
- X. Zhang, Z. Y. Ju, Y. Zhu, K. J. Takeuchi, E. S. Takeuchi, A. C. Marschilok and G. H. Yu, Adv. Energy Mater., 2021, 11, 2000808 CrossRef CAS.
- G. Li, T. Ouyang, T. Z. Xiong, Z. Jiang, D. Adekoya, Y. Wu, Y. C. Huang and M. S. Balogun, Carbon, 2021, 174, 1–9 CrossRef CAS.
- P. L. Taberna, S. Mitra, P. Poizot, P. Simon and J. M. Tarascon, Nat. Mater., 2006, 5, 567–573 CrossRef CAS.
- M. L. Mao, F. L. Yan, C. Y. Cui, J. M. Ma, M. Zhang, T. H. Wang and C. S. Wang, Nano Lett., 2017, 17, 3830–3836 CrossRef CAS PubMed.
- J. Xia, L. Liu, S. Jamil, J. J. Xie, H. X. Yan, Y. T. Yuan, Y. Zhang, S. Nie, J. Pan, X. Y. Wang and G. Z. Cao, Energy Storage Mater., 2019, 17, 1–11 CrossRef.
- J. Billaud, F. Bouville, T. Magrini, C. Villevieille and A. R. Studart, Nat. Energy, 2016, 1, 16097 CrossRef CAS.
- L. Zhang, M. Zeng, D. Wu and X. Yan, ACS Sustainable Chem. Eng., 2019, 7, 6152–6160 CrossRef CAS.
- H. Wang, J. Xie, M. Follette, T. C. Back and P. B. Amama, RSC Adv., 2016, 6, 83117–83125 RSC.
- K. Zhang, W. Zhao, J. T. Lee, G. Jang, X. Shi and J. H. Park, J. Mater. Chem. A, 2014, 2, 9636 RSC.
- W. Feng, H. Rong, M. Daobin, W. Borong and C. Shi, ACS Appl. Mater. Interfaces, 2014, 6, 19254–19264 CrossRef PubMed.
- B. Xu, L. Yu, X. Zhao, H. Wang, C. Wang, L. Y. Zhang and G. Wu, J. Colloid Interface Sci., 2021, 584, 827–837 CrossRef CAS.
- L. J. Wan, D. Yan, X. T. Xu, J. B. Li, T. Lu, Y. Gao, Y. F. Yao and L. K. Pan, J. Mater. Chem. A, 2018, 6, 24940–24948 RSC.
- H. Yue, V. Reguero, E. Senokos, A. Monreal-Bernal, B. Mas, J. P. Fernández-Blázquez, R. Marcilla and J. J. Vilatela, Carbon, 2017, 122, 47–53 CrossRef CAS.
- M. Mecklenburg, D. Mizushima, N. Ohtake, W. Bauhofer, B. Fiedler and K. Schulte, Carbon, 2015, 91, 275–290 CrossRef CAS.
- J. Lee, I. Y. Stein, M. E. Devoe, D. J. Lewis, N. Lachman, S. S. Kessler, S. T. Buschhorn and B. L. Wardle, Appl. Phys. Lett., 2015, 106, 053110 CrossRef.
- H. Liu, S. h. Luo, D. b. Hu, X. Liu, Q. Wang, Z. y. Wang, Y. l. Wang, L. j. Chang, Y. g. Liu, T. F. Yi, Y. h. Zhang and A. m. Hao, Appl. Surf. Sci., 2019, 495, 2004577 CrossRef.
- W. Han, X. Qin, J. Wu, Q. Li, M. Liu, Y. Xia, H. Du, B. Li and F. Kang, Nano Res., 2017, 11, 892–904 CrossRef.
- Q. S. Zhao, J. L. Liu, Y. X. Wang, W. Tian, J. Y. Liu, J. Z. Zang, H. Ning, C. H. Yang and M. B. Wu, Electrochim. Acta, 2018, 262, 233–240 CrossRef CAS.
- T. T. Li, B. W. Wang, J. Ning, W. Li, G. N. Guo, D. D. Han, B. Xue, J. X. Zou, G. H. Wu, Y. C. Yang, A. G. Dong and D. Y. Zhao, Multiscale Lithiation Evolution, Matter, 2019, 1, 976–987 CrossRef.
- L. Guo, H. Sun, C. Qin, W. Li, F. Wang, W. Song, J. Du, F. Zhong and Y. Ding, Appl. Surf. Sci., 2018, 459, 263–270 CrossRef CAS.
- J. L. Xu, X. Zhang, Y. X. Miao, M. X. Wen, W. J. Yan, P. Lu, Z. R. Wang and Q. Sun, Appl. Surf. Sci., 2021, 546, 149163 CrossRef CAS.
- Z. Z. Gan, Z. M. Sheng, H. Huang, X. Y. Dai, R. L. Niu and R. P. Jia, Sustainable Energy Fuels, 2019, 3, 3335–3343 RSC.
- Z. M. Sheng, C. Y. Hong, N. N. Li, Q. Z. Chen, R. P. Jia, D. Y. Zhang and S. Han, Electrochim. Acta, 2018, 259, 1104–1109 CrossRef CAS.
- Z. M. Sheng, Z. Z. Gan, H. Huang, R. L. Niu, Z. W. Han and R. P. Jia, Sens. Actuators, B, 2020, 305, 127550 CrossRef CAS.
- H. Huang, Z. M. Sheng, R. L. Niu, C. M. Li and S. Han, Catal. Sci. Technol., 2021, 11, 1323–1329 RSC.
- Z. M. Sheng, M. H. Hu, X. Y. Dai, C. Y. Hong, C. C. Cheng, Q. Z. Chen and X. J. Chang, Microporous Mesoporous Mater., 2016, 234, 224–229 CrossRef CAS.
- R. P. Jia, Z. Z. Gan, H. Huang and Z. M. Sheng, Electrochim. Acta, 2021, 368, 137617 CrossRef CAS.
- B. Xue, T. T. Li, B. W. Wang, L. Ji, D. Yang and A. G. Dong, Sustainable Energy Fuels, 2018, 2, 616–625 RSC.
- Y. T. Zhu, K. H. Yue, C. F. Xia, S. Zaman, H. Yang, X. Y. Wang, Y. Yan and B. Y. Xia, Nano-Micro Lett., 2021, 13, 137 CrossRef CAS.
- T. Yue, A. I. Douka, K. Qi, Y. B. Qiu, X. P. Guo and B. Y. Xia, J. Mater. Chem. A, 2021, 9, 21799–21806 RSC.
|
This journal is © The Royal Society of Chemistry 2023 |
Click here to see how this site uses Cookies. View our privacy policy here.