DOI:
10.1039/D3SC05283D
(Review Article)
Chem. Sci., 2023,
14, 13346-13366
Recent advances in electrospinning nanofiber materials for aqueous zinc ion batteries
Received
6th October 2023
, Accepted 2nd November 2023
First published on 3rd November 2023
Abstract
Aqueous zinc ion batteries (AZIBs) are regarded as one of the most promising large-scale energy storage systems because of their considerable energy density and intrinsic safety. Nonetheless, the severe dendrite growth of the Zn anode, the serious degradation of the cathode, and the boundedness of separators restrict the application of AZIBs. Fortunately, electrospinning nanofibers demonstrate huge potential and bright prospects in constructing AZIBs with excellent electrochemical performance due to their controllable nanostructure, high conductivity, and large specific surface area (SSA). In this review, we first briefly introduce the principles and processing of the electrospinning technique and the structure design of electrospun fibers in AZIBs. Then, we summarize the recent advances of electrospinning nanofibers in AZIBs, including the cathodes, anodes, and separators, highlighting the nanofibers' working mechanism and the correlations between electrode structure and performance. Finally, based on insightful understanding, the prospects of electrospun fibers for high-performance AZIBs are also presented.
1 Introduction
With the rapid consumption of fossil resources and increasing demand for highly efficient utilization of new energy, the search and study of energy storage devices with high earth abundance, good safety, and long cycle life are urgently required.1–4 As a promising candidate for large-scale energy storage systems, AZIBs have attracted wide attention due to their rapid reaction kinetics, environmental benignity, and affordability.5–7 Generally, AZIBs are composed of a Zn anode, mild or weakly acidic electrolyte, separator, and cathode. Zn metal with a high theoretical capacity (820 mA h g−1) and low redox potential (−0.76 V vs. the standard hydrogen electrode) is considered an ideal anode for AZIBs.8,9 In addition, the cathode plays a crucial role in the performance of AZIBs, as it serves as a host framework to accommodate Zn2+.10,11 So far, cathode materials for AZIBs include manganese, vanadium, Prussian blue analogs, organic compounds, etc.12 These cathode materials are related to the operation voltage, cycle stability and rate performance of AZIBs.13,14 Herein, the application of suitable cathode materials can improve the performance of AZIBs.
Despite the many advantages of AZIBs, however, many challenges seriously hinder their further application. Firstly, in contrast to lithium/sodium ion batteries, the reaction mechanisms of AZIBs are complicated and immature,15 and can be categorized into three main types, including Zn2+ insertion/extraction,16,17 H+/Zn2+ co-insertion/extraction,18 and chemical conversion reactions.19 Among them, the Zn2+ insertion/extraction reaction mechanism is the most commonly acknowledged in AZIBs.20 Secondly, the non-uniform Zn2+ deposition and the decomposition of active H2O molecules belonging to the solvation layer of Zn2+ will result in uncontrolled growth of Zn dendrites and the formation of by-products on the surface of the Zn anode, ultimately causing battery failure.21 Thirdly, due to the Jahn–Teller effect, the active materials of the manganese-based materials will dissolve in weakly acidic aqueous electrolyte, resulting in material collapse and the rapid degradation of capacity.22,23 In addition, vanadium-based compounds and organic compounds also face the challenge of dissolution.24 Fourthly, as the crucial component of AZIBs, the separator can prevent direct contact between the electrodes and provide the channel for ion migration.25 However, traditional separators (such as glass fiber, filter paper, and non-woven fabrics) cannot meet the requirements for AZIBs of excellent mechanical properties, high wettability, high ionic conductivity, and electrical insulation.26,27 To alleviate these limitations, some novel material preparation technologies and many functional materials have been adopted and fabricated. Among them, the electrospinning nanofibers have advantages such as large surface area to volume ratio, high aspect ratio, directional transportation, and short ionic transport lengths, which are desirable in energy storage applications.28 In the previously reported literature, there is no uniform definition of one-dimensional (1D) nanofibers.29 Thereby, in this review, single electrospinning nanofibers are defined as 1D nanofibers. During electrospinning, 1D nanofibers deposited and disorderly arranged on the collector can form the two-dimensional (2D) nano-film. Different from the conventional 2D nano-film, the preparation of three-dimensional (3D) fibrous structures is complicated. In general, the fabrication strategies of 3D structures include increasing the electrospinning, self-assembly, assembly by post-processing of 2D nano-film (such as layer-by-layer electrospinning), and direct assembly by an auxiliary factor (like a 3D template).30 These 2D and 3D architecture materials with high flexibility and high surface area-to-mass ratio are assembled by 1D fibers exhibit faster intercalation kinetics in AZIBs. Besides, some unique structures (such as core/shell structures and hierarchical pores), defects, and functional groups can be created and introduced on the electrospinning nanofibers, which is beneficial for AZIBs.31
For example, Tang et al. fabricated N-doped carbon fibers to improve the electronic conductivity of cathode materials.32 Liang et al. synthesized zincophilic carbon nanofiber interlayers by an electrospinning method to uniformize the deposition of Zn2+.33 Meanwhile, Fang et al. fabricated a polyacrylonitrile (PAN) nanofiber separator with high porosity and excellent flexibility.34 A brief timeline of the representative works of electrospinning nanofibers on AZIBs is summarized in Fig. 1.35–42 Although electrospinning nanofibers are widely applied in AZIBs, there is still no specific review focus on electrospinning nanomaterials' application in AZIBs. Thus, it is necessary to summarize the research progress of AZIBs based on the electrospinning nanomaterials.
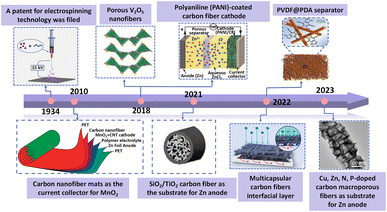 |
| Fig. 1 Timeline of the progress of the electrospinning nanofibers in AZIBs. Adapted from ref. 36, copyright 2022, American Chemical Society. Adapted from ref. 37, copyright 2010, American Chemical Society. Adapted from ref. 38, copyright 2019, Elsevier B.V. Adapted from ref. 39, copyright 2018, American Chemical Society. Adapted from ref. 35, copyright 2021, Wiley-VCH. Adapted from ref. 40, copyright 2022, the Author(s). Adapted from ref. 41, copyright 2022, the Author(s). Adapted from ref. 42, copyright 2023, American Chemical Society. | |
Herein, in this review, we first introduce the principle and processing of the electrospinning technique. Then, the different structures of electrospinning nanofibers in AZIBs are summarized. Thirdly, we highlight the development of electrospinning materials in AZIBs, such as cathodes,39,43,44 anodes,45–47 and separators.34,48 Finally, we propose the challenges, development prospects, and future research directions of the electrospinning materials in AZIBs.
2 Principle and processing of the electrospinning technique
The electrospinning technique is a novel patented technology invented in 1934 that enables the direct and continuous preparation of polymer nanofibers,49,50 including not only synthetic polymeric compounds such as poly(vinyl pyrrolidone) (PVP), poly(vinylidene fluoride) (PVDF), and polyacrylonitrile (PAN),51 but also natural macromolecules and their derivatives like chitosan and silk protein.30 A common electrospinning apparatus usually comprises a high-voltage power supply, a metallic or plastic syringe, and a collector.31 A “Taylor cone” at the end of the nozzle will form a jet of electrically conductive polymeric precursor solution (or polymer melt) in a classic electrospinning process when the voltage between the collector and needle exceeds a critical value.50 After a short distance of stable motion, these jets will go into an unstable movement stage. Experiencing a series of stretching and solvent evaporation, the polymer solution jets will solidify and finally be deposited on the collector, forming polymer fibers.52
The structure and morphology of electrospinning nanofibers are affected by numerous factors such as the properties of polymer solutions, processing parameters, and ambient parameters.53 The molecular weight of the polymer is a significant parameter affecting electrospinning nanofibers, which directly affects the properties of the precursor solution, such as viscosity, conductivity, and surface tension.54 At the same mass fraction, polymer solutions with higher molecular weight exhibit higher viscosity than those with lower molecular weight. In general, high viscosity usually results in the formation of large diameter nanofibers, while low viscosity solutions facilitate the preparation of small diameter nanofibers.50 Voltage and feed rate are other important factors affecting the diameter of the nanofibers. It is well known that the critical voltage is required to form electrospinning nanofibers.55 With the increase of voltage, the diameter of nanofibers will decrease at an appropriate concentration of polymer solution.52 In contrast, increasing the feed rate will lead to an increase in fiber diameter.56 Besides, the diameter of nanofibers is also influenced by environmental parameters (such as humidity and temperature). A moderately high temperature and a low relative humidity will promote the evaporation of solvent and the solidification of jets, which is favorable for decreasing the diameter of nanofibers. These factors are not independent and have a significant influence on each other. Therefore, before preparing the nanofibers with specific morphology and diameter, the interaction between these parameters needs to be considered.
3 Electrospinning nanofibers design for zinc ion batteries
Generally speaking, the structure of materials significantly impacts the electrochemical performance of batteries. For instance, constructing a porous structure cathode material can increase the SSA of the material and facilitate the intimate electrolyte penetration and rapid transfer of Zn2+.57 Furthermore, the hollow structure has the ability to accommodate the volume changes of the electrodes.58 Different structures of nanofibers (e.g., core/shell, porous, hollow, and so on) can be fabricated by the electrospinning method. Thus, the design of different structure nanofibers by electrospinning in AZIBs will be discussed and summarized in this section.
3.1 Core/shell structure
In the year 2003, nanofibers with core/shell structures were prepared by coaxial electrospinning for the first time.59 Since then, the core/shell-structured electrospinning nanofibers have been extensively utilized in energy storage due to their unique features. Compared with normal electrospinning fibers, the advantage of core/shell nanofibers is to allow many non-spinnable polymers to be used as electrospinnable materials,60 such as polyaniline and polyvinyl alcohol.61 In the process of electrospinning, two kinds of immiscible solutions were added to two syringes, respectively. Then, under a high voltage electrostatic field, the shell solution will converge with the core solution at the nozzle, finally forming the core/shell structured fibers.62 In AZIBs, the core/shell nanostructure fibers are usually used as the electrode material due to the large SSA and excellent charge storage. For example, Long et al. fabricated Mn3O4 nanoparticles (Mn3O4 NPs)/polyacrylonitrile (PAN) composite nanofibers by coaxial electrospinning.63 During annealing, the Mn3O4/PAN fibers were carbonized to Mn3O4@HCFs nanofibers with core/shell structure.
3.2 Porous structure
Porous structure electrospinning nanofibers have the advantages of large SSA, short ion diffusion length, and fast electrolyte access, and have been widely used in AZIBs.64 Besides, the abundant porosity can accommodate the volume changes caused by ion insertion/extraction, thus mitigating structural distortion during cycling.65 In electrospinning, phase separation and sacrificial template methods are usually used to produce porous structures in nanofibers. The mechanism of the phase separation method can be categorized into vapor-induced phase separation (VIPS), non-solvent-induced phase separation (NIPS), and thermally induced phase separation (TIPS).66 Usually, the fabrication of porous nanofibers involves one or more phase separation methods, while suitable polymers and solvents are also required. Sacrificial templates include polymers, metals, metal oxides, and inorganic salts.67 For instance, Liu's group used block copolymer poly(methyl methacrylate)-block-polyacrylonitrile (PMMA-b-PAN) as a raw material to fabricate polymer mats.68 In this polymer mat, the incompatibility between the PMMA block and PAN will result in microphase separation, which will further release and generate abundant micro-/mesopores at high temperatures. This porous structure can shorten the ion diffusion path and facilitate the migration of electrolytes in the electrode.
3.3 Hollow structure
The principle of coaxial electrospinning to prepare hollow structure nanofibers involves generally soluble or volatile substances (such as oil) as the core layer, and polymer solution as the shell layer, through the coaxial electrospinning process and removal of the core layer to obtain hollow fibers.69,70 The construction of hollow structures can significantly increase the number of active sites, improve the high aspect ratio of nanofibers, and enable accommodating massive deposition at a high current density without a distinct volume change. Additionally, it can be prepared by the Kirkendall effect.71 For example, Xue et al. proposed a hollow TiO2 and SiO2 carbon fiber. During the carbonization process, hollow porous fibers were formed due to the different decomposition and diffusion rates of different molecular weight PVP.35
3.4 Bead-like structure
In recent years, the bead-like structure of electrospinning nanofibers has attracted extensive attention on account of its unique geometric shape and chemical performance. Usually, bead-like structure fibers are considered the by-products of the electrospinning process. Their formation can be devoted to the axisymmetric instability of the fluid jet under an external electric field.72,73 According to the literature, decreasing the viscosity of the polymer solution (or net charge density of the jets) will facilitate the formation of beads.74 However, the lower surface tension of the precursor polymer solution favors the production of bead-like fibers during the process of electrospinning. For instance, the manganese-based metal–organic framework (Mn-MOF) spheres can be wrapped in PAN through the electrospinning technique.36 After carbonization in N2, the bead-like cathode materials for AZIBs can be achieved by stringing MnOx with carbon fiber ropes.
3.5 Hierarchical structure
Hierarchically structured fibers consist of multiple nanostructures, which can be fabricated by electrospinning and post-treatment technologies.50 Compared to primary structures, the hierarchical structure improves the electrical conductivity of metal oxides and the storage of Zn2+.75 For instance, Zhang et al. produced vanadium nitride embedded nitrogen-doped carbon nanofiber (VN/N-CNFs) composite hierarchical structures by the electrospinning method.76 Additionally, nano-whiskers can be observed in the branches of VN/N-CNFs.
4 Applications of electrospinning nanofibers in zinc ion batteries
Owing to their versatility and applicability, electrospinning nanofibers have been extensively applied in AZIBs. Firstly, electrospinning nanofibers possess high mechanical flexibility to meet the trend of flexible AZIBs. Secondly, the nanofiber structure can shorten the Zn2+ diffusion pathway and reduce reaction impedance in cycling. Thirdly, electrospinning nanofibers with electrical conductivity and stability can be used as a collector to uniformize the deposition of Zn2+, achieving a “dendrite-free” metal Zn anode. Last but not least, the nanofiber separator with appropriate thickness, high mechanical strength, and controllable pore size can be fabricated by the electrospinning technique, which can facilitate the transfer of Zn2+, improve the wettability between the separator and electrolyte, and resist the piercing of the Zn dendrites. Therefore, this section will summarize the application of electrospinning nanofibers in the cathodes, anodes, and separators of AZIBs.
4.1 Cathodes
In particular, as an important component of AZIBs, the cathode material largely determines the electrochemical behaviors of the battery.77 Therefore, high-performance cathode materials have been the focus of research in the last decade.78 However, cathode materials still face challenges such as poor conductivity, dissolution issues, and volume variation.23,79 Electrospinning carbon nanofibers can provide carbonaceous frameworks with high conductivity to improve the conductivity and reaction kinetics of materials.55,80 Besides, the active materials can be embedded in carbon nanofibers with a porous structure and large SSA, which greatly prevents the dissolution and volume variation of materials.81,82 For clarity, the application of electrospinning nanofibers in cathode materials is described in the following aspects: vanadium-based materials, manganese-based materials, and other cathode materials.
4.1.1 Vanadium-based cathodes.
Vanadium oxides have become one of the most promising cathode materials because of their various oxidation states, high theoretical specific capacity, and abundant crystal structure.83,84 However, vanadium-based cathodes will dissolve in mild acidic aqueous electrolytes because of the strong polarity of water molecules and anions, resulting in capacity fading. In addition, dissolved substances will deposit on the surface of the Zn anode, reducing the reactivity and utilization of the Zn metal.85 Usually, vanadium-based materials are semiconductors that possess poor electronic conductivity, so highly conductive substances are often used in the preparation of the cathode electrodes to improve the conductivity of the materials.86
To alleviate these limitations, numerous approaches have been proposed to enhance the electrochemical performance of vanadium-based materials. Among them is preparing VxOy nanofibers by the electrospinning technique with excellent ion diffusion pathways, high conductivity, and nanostructures, which promote electron/ion transport and improve the cycling ability of the cathode. For example, to address the problems of dissolution and poor conductivity of VO2, Liu et al. prepared self-supported VOC-NF composites by the electrospinning method followed by steam treatment, in which VO2 nanodots were embedded in carbon nanowires.87 In VOC-NF, the carbon shell with good electrical conductivity not only prevented the dissolution of the vanadium element but also avoided the use of binder and conductive species, resulting in high discharge specific capacity and energy density.88 Therefore, the vanadium-based cathode exhibited a satisfactory electrochemical performance due to the rapid Zn2+ diffusion and electron transfer. Generally speaking, the component distribution of the polymer solution determines the content and distribution of active materials in electrospun nanofibers.89 The concentration distribution of precursors during the electrospinning process could therefore be adjusted to produce nanofibers with a continuous concentration gradient. Niu's group combined a dynamic concentration adjustment technique and electrospinning method to develop continuous gradient composite films (GCFs) (Fig. 2a).90 The polymer solution was continuously added to the precursor solution to form a continuously diluted resultant precursor solution. In VO-GCFs, VO nanoparticles were gradient distributed throughout the carbon fiber matrix after the electrospinning and annealing process. In particular, the electronic conductivity of VO-GCFs gradually increased with the gradient distribution of VO nanoparticles, which facilitated the rapid transfer of electrons and improved the reaction kinetics and electrochemical performance. Compared with homogeneous or down-graded VO-GCFs, the up-graded cathode exhibited an excellent cycling and rate ability. Hence, at a current density of 5.0 A g−1, the discharge capacity of the Zn//VO-GCFs battery was nearly unchanged after 1000 cycles (Fig. 2b). In the rate performance test, the average discharge capacity of the up-graded cathode was 477.1 mA h g−1 at 5 A g−1. As the current density became 0.3 A g−1, the capacity retention of the up-graded cathode reached 81.2% (Fig. 2c).
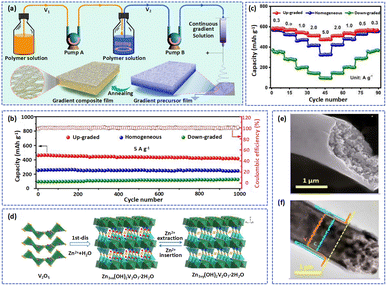 |
| Fig. 2 (a) Schematic illustration of fabricating gradient composite films. (b) Cycling performances and (c) rate capabilities of the up-graded cathode. Adapted from ref. 90, copyright 2022, Elsevier B.V. (d) Schematic illustration of the reaction mechanism of the V2O5 electrode. Adapted from ref. 38, copyright 2019, Elsevier B.V. (e) SEM and (f) TEM images of the hierarchical hybrid fibers with V2O5. Adapted from ref. 91, copyright 2019, American Chemical Society. | |
Constructing a microstructure can efficiently improve the transport kinetics of cathode materials.12 For instance, a hierarchical structure could shorten ion transport pathways,92,93 a porous structure with a large SSA can provide abundant transfer channels for Zn2+,85 a hollow structure can act as a host to load active materials,94etc. Some researchers have prepared many vanadium-based nanofibers with special structures to improve the cycling ability of electrodes. For example, Chen et al. successfully produced porous V2O5 nanofibers via the electrospinning method followed by calcination.38 This abundant mesoporous structure is conducive to electrolyte permeation and Zn2+ insertion. In the first charging process, the V2O5 transformed into Zn pyrovanadate with a highly stable open framework, which greatly favors the reversible Zn2+ insertion/extraction (Fig. 2d). Therefore, after 500 cycles, the battery with a V2O5 nanofiber cathode showed a high capacity of 166 mA h g−1 and an impressive capacity retention of 81% at 2C. Furthermore, Wang et al. fabricated novel hybrid fibers with core/shell hybrid fibers (Fig. 2e and f), which promoted rapid electron/ion transmission and high mass loading, thus gaining a better energy storage capability and rate performance ability.91
Heteroatom doping is an effective method to modify the intrinsic electronic/ionic properties of electrode materials for AZIBs.95 Doped heteroatoms can widen the interlamellar spacing and redistribute the charge of the surface atoms, increasing ion storage and facilitating electron transport.96,97 During the process of electrospinning, N-containing polymers (such as PVP and PAN) were often used. These polymers were transformed into N-doped carbon nanofibers after carbonization, which contributed to an increase in the electronic conductivity of materials and provided more active sites for Zn2+ insertion/extraction. For instance, Zhang et al. fabricated an N-doped VN-encapsulated carbon nanofiber (VN/N-CNFs) compound by carbonizing H2BDC and VCl3/PAN fibers.76 The 3D self-supported hierarchical structure of the VN/N-CNFs process was thus directly applicable as an electrode for AZIBs and exhibited ultra-long cycle lifetimes and super-high rates. As shown in Fig. 3a and b, Zhang et al. prepared N-doped C/V2O3 (N@C/V2O3) microfibers by the electrospinning method.98 The graphitic N atoms in the composites could promote charge transfer and improve the electrical conductivity and stable cycling ability of N@C/V2O3. Thus, the battery based on the N@C/V2O3 electrode delivered a specific capacity of 322.3 mA h g−1 and superhigh capacity retention of 91.7% after 4000 cycles at 10 A g−1 (Fig. 3c). Besides, Yoo et al. produced Fe-doped V2O5 nanorods by immersing the PAN fiber templates in sol solutions with vanadium salt and iron salt followed by calcination (Fig. 3d).99 As an outstanding cathode for AZIBs, the Fe-V2O5 not only shortened the diffusion distance of Zn2+ but also provided extra active sites for Zn2+ storage.
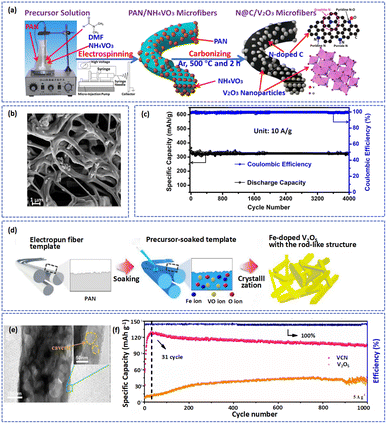 |
| Fig. 3 (a) A diagrammatic representation of the synthetic procedure and structure of N@C/V2O3 composites. (b) SEM image of samples. (c) The cycling ability and coulombic efficiency of the N@C/V2O3 cathode at 10 A g−1. Adapted from ref. 98, copyright 2020, Elsevier B.V. (d) An illustration of the synthetic process for Fe-doped V2O5. Adapted from ref. 99, copyright 2021, Elsevier B.V. (e) TEM image of VCN fibers. (f) Long-term cycling performance of VCN at 5 A g−1. Adapted from ref. 75, copyright 2020, Elsevier B.V. | |
Under thermal treatment, carbon will consume the lattice of materials or surface O atoms to form defects.24 For example, at high temperatures, vanadium oxide nanofibers (VCN) were generated with physical and chemical defects by decomposing VO(acac)2/PAN precursor fibers.75 The physical defects such as pore pathways and caverns can provide more storage sites for Zn2+ and abundant chemical defects benefit the Zn2+ insertion/extraction during cycling (Fig. 3e). As shown in Fig. 3f, compared with V2O5, the Zn//VCN cell produced higher capacity retention of about 83% and stabler coulombic efficiency (almost 100%) at 5 A g−1 after cycling over 1000 cycles, which was attributed to the synergistic effect of dual defects. Table 1 summarizes the electrochemical performances of vanadium-based materials with electrospinning fibers.
Table 1 A summary of electrospinning vanadium-based nanofiber materials for AZIBs
Materials |
Electrospinning solution (precursor/polymer/solvent) |
Structure |
Long cycle performance |
Rate performance |
Ref. |
VOC-NF |
C10H14O5V/PAN/DMF |
— |
120 mA h g−1 at 20 A g−1 after 18 000 cycles (63% capacity retention) |
215 mA h g−1 at 20 A g−1 |
87
|
VO-GCFs |
VOC2O4/PAN/DMF |
Porous |
The capacity is nearly unchanged after 1000 cycles at 5 A g−1 |
477.1 mA h g−1 at 5.0 A g−1 |
90
|
V2O5-CFC |
V2O5/PAN/DMF |
— |
154 mA h g−1 at 0.5 A g−1 after 1000 cycles |
91 mA h g−1 at 4 A g−1 |
100
|
V2O5 |
VO2/PVP/H2O2 |
— |
The capacity is 36% of the maximum value after 500 cycles at 2 A g−1 |
179 mA h g−1 at 2 A g−1 |
101
|
V2O5 |
NH4VO3, H2C2O4·2H2O/PVP/DMF |
Porous |
166 mA h g−1 at 2C after 500 cycles (81% capacity retention) |
104 mA h g−1 at 10C |
38
|
V2O5/Zn2V2O7 |
C15H21O6V, C2H4O2, PMMA/PAN/DMF (NH4VO3, Zn(NO3)2, H2O, PMMA/PAN/DMF) |
Hierarchical |
High capacity retention (for V2O5 it is 95.8% and for Zn2V2O7 it is 93.1%) after 8000 cycles at 8 A g−1 |
— |
91
|
VN/N-CNFs |
H2BDC, VCl3/PAN/DMF |
Hierarchical |
482 mA h g−1 at 50 A g−1 after 30 000 cycles |
297 mA h g−1 at 100 A g−1 |
76
|
N@C/V2O3 |
NH4VO3/PAN/DMF |
— |
322.3 mA h g−1 at 10 A g−1 after 4000 cycles (91.7% capacity retention) |
242.2 mA h g−1 at 30 A g−1 |
98
|
Al2O3@VSe2 NSs@N-CNFs |
VO(acac)2/PAN, PVP/DMF |
Core/shell |
502.2 mA h g−1 at 0.05 A g−1 after 500 cycles (91.6% capacity retention) |
— |
43
|
V2O3@C NFs |
C15H21O6V/PAN/DMF |
— |
65 mA h g−1 at 2 A g−1 after 1000 cycles |
100 mA h g−1 at 2 A g−1 |
102
|
Fe-doped V2O5 |
PAN/DMF |
— |
The capacity retention is 85% after 160 cycles at 1.3 A g−1 |
256 mA h g−1 at 2 A g−1 |
99
|
VCN |
VO(acac)2/PAN/DMF |
Hierarchical |
1000 cycles (83% capacity retention) |
73 mA h g−1 at 10 A g−1 |
75
|
V2O5 |
PAN/DMF |
— |
The capacity retention is 74.6% after 300 cycles at 1.3 A g−1 |
— |
103
|
4.1.2 Manganese-based cathodes.
Manganese-based materials, including MnO, MnO2, Mn2O3, Mn3O4, ZnMn2O4, MnS, and so on, have been widely studied in AZIBs because of their numerous merits such as high operating voltage, cheapness, abundant resources, and nonpoisonous nature.104 Unfortunately, some challenges prevent its practical application.105 Manganese-based electrodes are usually constructed of active powder, conductivity agents, binders, and collectors. However, the poor electrical conductivity and random aggregation of manganese-based composites cannot realize fast charging at high current densities.23
Carbon nanofibers with large SSA and high electrical conductivity can be used as conductive substrates for cathode materials loading, which not only facilitates fast electron transfer but also simply the preparation of electrodes without binders and conductive additives.44 For example, Guo et al. used porous carbon fibers (PCF) to support MnO2 to form a free-standing PFC@MnO2 electrode.68 Specifically, the graphitic PCF fabricated by the electrospinning technique and high-temperature treatment with high electrical conductivity and uniform pores (Fig. 4a) favors the mass loading of MnO2 (59.1%) and fast charging. As a result, owing to the fast ion/electron transport ability of PFC@MnO2, the Zn//PFC@MnO2 displayed impressive structural stability at various current densities. Besides, Yang et al. prepared high-flexibility nitrogen-doped carbon films through an electrospinning technique and calcination with PAN, PVP, 2-methylimidazole, and zinc acetate as raw materials (Fig. 4b).106 During carbonization, the evaporation of Zn endowed the CNFs with a porous structure, which not only provided abundant reaction sites for the growth of δ-MnO2 but also had a strong electrostatic attraction for Mn2+. As displayed in Fig. 4c, the lamellar-like K+-intercalated δ-MnO2 (KMO) was loaded on the surface of CNFs via the hydrothermal method of KMnO4, and the resulting KMO/CNFs presented a large surface area to enable expansion of the contact area between KMO and the electrolyte and promote ion transfer. Therefore, even after 1000 cycles at 3 A g−1, the KMO/CNFs still exhibited a reversible capacity of 190 mA h g−1 (Fig. 4d). What's more, compared with KMO, KMO/CNF showed lower charge-transfer and ion-diffusion kinetics, which was attributed to the existence of CNFs. Hiralal et al. explored the relationship between the capacity of the battery and the diameter of carbon fibers when carbon fibers were used as the substrate for the cathode.37 The results showed that decreasing the diameter will enhance the surface area, charge collection area, and conductivity of carbon fibers, which will promote electrolyte diffusion in the electrode, resulting in a higher capacity battery.
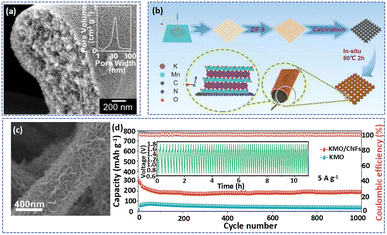 |
| Fig. 4 (a) Cross-sectional SEM image of a porous carbon fiber. Adapted from ref. 68, copyright 2022, Wiley-VCH. (b) The fabrication of KMO/CNFs is illustrated schematically. (c) SEM image of KMO/CNFs. (d) Long-term cycling performance of KMO/CNFs at 3.0 A g−1. Adapted from ref. 106, copyright 2022, Wiley-VCH. | |
There is no doubt that using carbon nanofibers as a substrate is an effective way to improve the electrical conductivity of manganese-based compounds. However, the construction of a firm and tight interface between active materials and carbon fibers is still a great challenge that needs to be addressed in the future.
Embedding active substances in carbon nanofiber matrixes could inhibit the dissolution of manganese-based materials and construct highways for electrons.32,107,108 For instance, Ding et al. prepared CNF coated bead-like manganese oxide (MnOx-CNFs) via the electrospinning method (Fig. 5a).36 As shown in Fig. 5b, the MnOx particles were tightly encapsulated in the amorphous carbon layer, which effectively relieved its dissolution. Moreover, Wu's group embedded MnS/MnO with the heterostructures in N-doped carbon fibers to form MnS/MnO@N-CF with high ion and electron conductivity (Fig. 5c).32 As shown in Fig. 5d and e, the MnS/MnS nanoparticles were uniformly dispersed in carbon matrixes, and the edges of active materials were connected by a large amount of amorphous carbon, which was conducive to the storage of electrolyte and the enhancement of the conductivity of the materials. Benefiting from the protection of the carbon layer, the structure of active materials remained stable without collapse and pulverization after cycling, indicating an excellent stable cycling ability of the electrode.
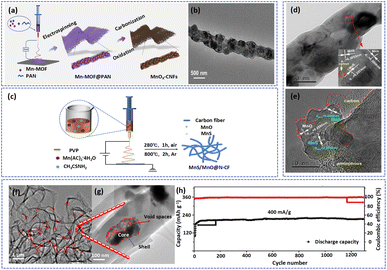 |
| Fig. 5 (a) Schematic illustration of the synthesis process and (b) TEM image of MnOx-CNFs. Adapted from ref. 31, copyright 2022, American Chemical Society. (c) An illustration of the MnS/MnO@N-CF synthesis process. (d) SEM and (e) TEM images of MnS/MnO@N-CF. Adapted from ref. 27, copyright 2022, Elsevier B.V. (f and g) TEM images of Mn3O4@HCFs. (h) Long cycling performance and coulombic efficiency of the Mn3O4@HCF electrode at 0.4 A g−1. Adapted from ref. 59, copyright 2020, Elsevier Ltd. | |
However, this strategy will partly reduce the ion transport efficiency and active substance utilization of active materials. As a result, the precise control of the structure of nanofibers is essential to achieve a cathode with excellent electrochemical performance. As a typical example, Long et al. fabricated Mn3O4@HCFs with core/shell structure by a coaxial electrospinning method and subsequent high temperature treatment.63 This fiber consisted of a carbon shell with a thickness of about 70 nm (content of 12.7 wt%) and Mn3O4 nanoparticles (Fig. 5f and g). The amorphous carbon layer not only served as a protective layer between Mn3O4 and the electrolyte, preventing the dissolution of the active substance, but also mitigated the volume expansion of the electrode during cycling. In addition, the void spaces between the carbon shell and the Mn3O4 core can accommodate a large amount of electrolyte, providing space for electrochemical reactions. Therefore, the battery based on the Mn3O4@HCFs cathode material displayed ultra-stable cycling capability with 96.9% capacity retention and high coulombic efficiency of around 100% after 1300 cycles at 0.4 A g−1 (Fig. 5h). The precise control of nano- and microstructures can also be achieved by template methods.109 For example, the manganese dioxide precursor was wrapped on the surface of a CNF matrix using a hydrothermal method and then calcining to obtain tunnel-structured α-K0.19MnO2 nanotubes.110 It is worth noting that the CNF as the template will be consumed during the calcining process. Owing to the stability of the structure of α-K0.19MnO2, the cathode possessed excellent rate and cycling performance. Table 2 summarizes the electrochemical performances of manganese-based materials with electrospinning fibers.
Table 2 A summary of electrospinning manganese-based nanofiber materials for AZIBs
Materials |
Electrospinning solution (precursor/polymer/solvent) |
Structure |
Long cycle performance |
Rate performance |
Ref. |
PFC@MnO2 |
PMMA-b-PAN/DMF |
Porous |
A high capacity of 184 mA h g−1 at 1 A g−1 |
— |
68
|
KMO/CNFs |
Zn(AC)2/PVP, PAN/DMF |
Porous |
190 mA h g−1 at 3 A g−1 after 1000 cycles |
236 mA h g−1 at 3 A g−1 |
106
|
δ-MnO2-CNFs |
BTDA, BZD/PVP, PAA/DMF |
— |
120.9 mA h g−1 at 1 A g−1 after 500 cycles |
127.3 mA h g−1 at 2 A g−1 |
111
|
VO-MnO2@CNFs |
PAN/DMF |
— |
135 mA h g−1 at 1 A g−1 after 740 cycles |
148 mA h g−1 at 1 A g−1 |
44
|
MnS/MnO@N-CF |
Mn(Ac)2, C2H5NS/PVP/ethanol |
— |
151 mA h g−1 at 0.5 A g−1 after 400 cycles |
128.7 mA h g−1 at 2 A g−1 |
32
|
MnO@N-C |
Mn(Ac)2/PVP/ethanol |
— |
176.3 mA h g−1 at 0.5 A g−1 after 200 cycles |
66.3 mA h g−1 at 2 A g−1 |
107
|
MnO1−x@CNF |
Mn(Ac)2/PAN/DMF |
— |
96 mA h g−1 at 2 A g−1 after 2500 cycles (90% capacity retention) |
158 mA h g−1 at 1 A g−1 |
108
|
MnOx-CNFs |
Mn-MOF/PAN/DMF |
Bead-like |
The capacity retention is 71% after 5000 cycles at 3 A g−1 |
131.4 mA h g−1 at 5 A g−1 |
36
|
Mn3O4@HCFs |
Mn3O4/PAN/DMF |
Core/shell |
The capacity retention is 96.9% after 1300 cycles at 0.4 A g−1 |
115.7 mA h g−1 at 2 A g−1 |
63
|
α-K0.19MnO2 |
PAN/DMF |
— |
211 mA h g−1 at 1C after 2500 cycles (78% capacity retention) |
113 mA h g−1 at 20C |
110
|
Mn3O4 |
Mn(Ac)2/PVP/H2O, ethanol |
— |
104 mA h g−1 at 2 A g−1 after 1000 cycles |
153 mA h g−1 at 5 A g−1 |
112
|
4.1.3 Other cathode materials.
In addition to vanadium-based and manganese-based materials, many other cathode materials were prepared by the electrospinning method. Kim et al. fabricated a freestanding carbon fiber (CF) as a current collector to support polyaniline (PANI) via electrospinning and carbonization (Fig. 6a).39 Especially, the CF with high conductivity (resistance about 20 Ω sq−1) was firstly activated by HNO3 treatment to increase the number of active sites (some groups such as C
O, C–O, and O–C
O), which can promote the in situ polymerization of aniline monomers on the CF surface to achieve a PANI/CF cathode. Due to the high conductivity of the 3D CF, the PANI/CF showed a small electron resistance of about 400 Ω sq−1, allowing the fast transfer of electrons. Benefiting from the high conductivity and free-standing structure of composites, the PANI/CF can be used as an electrode directly without binder and conductive additives to assemble batteries in arbitrary geometries (Fig. 6b). As displayed in Fig. 6c, the battery with the PANI/CF electrode delivered excellent rate performance at 600C.
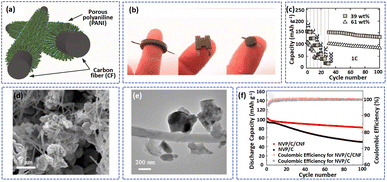 |
| Fig. 6 (a) A schematic diagram showing the in situ polymerization of aniline in an aqueous solution to synthesize a PANI/CF cathode. (b) Optical images of ring-, H-, and cylindrical shapes of Zn-PANI batteries. (c) Cycling ability of the cells with different PANI loading. Adapted from ref. 34, copyright 2018, American Chemical Society. (d) SEM and (e) TEM images of NVP/C/CNF. (f) Cycle performance of NVP/C/CNF and NVP/C at 0.1 A g−1. Adapted from ref. 109, copyright 2021, American Chemical Society. | |
Xu et al. synthesized a composite in which hybrid carbon coated Na3V2(PO4)3 was interconnected with carbon nanofibers (NVP/C/CNF) by electrospinning and sol–gel methods.113 As displayed in Fig. 6d and e, the NVP nanoparticles were randomly wrapped tightly in CNF to form a 3D conductive network to improve the electron conductivity and stable structure ability of the composite. Compared to NVP/C, the NVP/C/CNF electrode exhibited a more stable cycling ability. The battery based on NVP/C/CNF displayed a high capacity retention of 82.5% after 100 cycles at 0.1 A g−1, which is much higher than that of the battery based on NVP/C (52.7%) (Fig. 6f). A comparison of the performance of other cathode materials is presented in Table 3.
Table 3 A summary of electrospinning nanofibers for other cathode materials of AZIBs
Materials |
Electrospinning solution (precursor/polymer/solvent) |
Structure |
Long cycle performance |
Rate performance |
Ref. |
PANI/CF |
PAN/DMF |
— |
— |
The capacity fade was about 20% |
39
|
NVP/C/CNF |
— |
— |
The capacity retention is 82.5% after 100 cycles at 0.1 A g−1 |
65.0 mA h g−1 at 1.0 A g−1 |
113
|
4.2 Anodes
In aqueous electrolytes, the thermodynamic and electrochemical instability of the Zn metal anode dramatically shortens the service life of AZIBs and limits their practical applications.114,115 Among them, thermodynamic instability is manifested by serious corrosion reactions on the surface of Zn during cycling, which consumes the active Zn and decreases the coulombic efficiency of the Zn anode. The electrochemical instability is presented by uncontrollable dendrite growth, where the formed Zn dendrites will penetrate the separator, ultimately leading to the failure of the cell.116 As a result, various approaches have been proposed to address these above issues, including (1) optimizing the composition and concentration of electrolytes to stabilize the Zn anode;117,118 (2) protecting the Zn anode surface from direct contact with the electrolyte by forming an interfacial layer and reducing the occurrence of corrosion side reactions;119,120 and (3) constructing a 3D substrate that can help reduce local current densities and promote the uniform distribution of Zn2+, which is advantageous for the homogeneous deposition of Zn and inhibits the growth of dendrites.78,121 Among them, interfacial layer modification and 3D substrate construction are effective and direct strategies to protect the Zn anode. Carbon and polymer fibers fabricated by the electrospinning method with high flexibility adjustable structures are considered to be an ideal material for use as the protective layer and substrate for the Zn anode. Therefore, we will summarize and discuss the application of electrospinning fibers for protective layers and substrates of the Zn anode.
4.2.1 Pure carbon fibers.
The unique advantages of carbon materials as a substrate or protective layer for the Zn anode can be summarized in the following aspects: (1) the carbon materials with large SSA and porous structure can lower the local current density and accommodate the volume variation of the Zn anode during cycling. (2) A carbon substrate-based anode with high flexibility and processibility can be used to assemble flexible batteries. (3) A carbon protecting layer can provide abundant ion channels to promote the transfer of Zn2+ and inhibit the formation of Zn dendrites. As a typical carbon material, carbon fibers exhibit high axial strength, low density, good expansion, anisotropy, and excellent corrosion resistance.122,123 In particular, the diameter and porosity of carbon fibers can be controlled by the electrospinning method, which has more practical applications in anodes.124 For example, carbon nanofiber frameworks were prepared by electrospinning and calcination treatments, where the diameter (about 200 nm) and porosity of the nanofibers could be adjusted by electrospinning parameters.45 Interestingly, the plasma treatment improved the surface hydrophilicity of the carbon fibers, which was conducive to promoting the uniform deposition of Zn2+. Thus, benefiting from the coordination of the 3D framework, conductivity, and hydrophilicity of the carbon fibers, Zn was homogeneously deposited on the carbon fibers without severe aggregation at a current density of 0.5 mA cm−2 with an areal capacity of 5 mA h cm−2 (Fig. 7a). Most importantly, at a 40% depth of discharge (DOD) (an areal capacity of 2 mA h cm−2), the Zn@CNF‖Zn@CNF symmetric cell was stably cycled over 193 h at a current density of 2 mA cm−2 (Fig. 7b). As demonstrated in Fig. 7c, compared with Zn@Ti//V2O5, the battery of Zn@CNF//V2O5 displayed a better cycling ability.
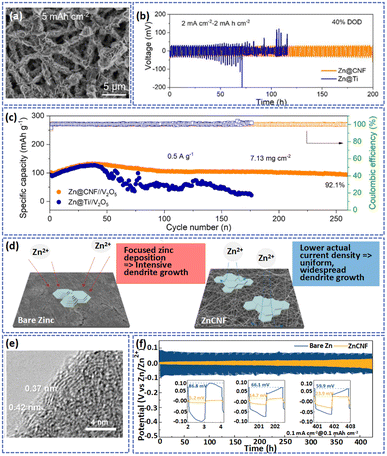 |
| Fig. 7 (a) SEM image of CNFs after being electrodeposited with an amount of Zn at a current density of 0.5 mA cm−2 with a capacity of 5.0 mA h cm−2. (b) Cycling performance of symmetric cells with different electrodes at 2 mA cm−2. (c) Cycling ability of full cells at the current density of 0.5 A g−1. Adapted from ref. 45, copyright 2022, American Chemical Society. (d) The deposition behaviors of Zn2+ on the different substrates. (e) HRTEM pattern of CNF. (f) Long cycling performance of bare Zn and ZnCNF symmetric cells. Adapted from ref. 124, copyright 2022, John Wiley & Sons Ltd. | |
In their study, Baek et al. produced a ZnCNF anode through the electro-deposition of Zn on the surface of electrospun carbon nanofibers.124 The 3D porous network of carbon with large SSA (53.04 m2 g−1) and high conductivity (830 S m−1) can decrease the local current density during the cycling process and provide more nucleation sites, thus reducing the nucleation overpotential of Zn in the initial stage. Meanwhile, the graphitic carbon with a low lattice mismatch interfacial layer to the Zn (002) plane can promote the preferred orientation of Zn to the (002) plane. Consequently, compared with bare Zn, the ZnCNF showed a smooth and compact anode surface after cycles (Fig. 7d and e). As shown in Fig. 7f, the symmetric cell demonstrated a stabler plating/stripping behavior with a small voltage hysteresis of 23.9 mV after 400 cycles at the current density of 0.1 mA cm−2 with an areal capacity of 0.1 mA h cm−2.
4.2.2 Carbon fibers with zincophilic materials.
Although the pure carbon fibers with large SSA can contribute to the homogeneous distribution of the electric field and confine the Zn in 3D pores to avoid its accumulation during the stripping/plating processes, the hydrophobic and zincophobic carbon matrixes lead to a high energy barrier of Zn nucleation, which is unfavorable for the uniform growth of Zn.125 The nucleation behavior of Zn is greatly affected by the surface properties of the substrate. Herein, zincophilic materials (such as functional groups and metal nanoparticles) are introduced on the surface of carbon matrixes to reduce nucleation polarization, achieving a highly reversible Zn cycling process and inhibiting the formation of Zn dendrites.
The functional groups including N,125,126 C
O,127 F,128 and –NH2 (ref. 129) with high electronegativity serve as zincophilic sites to capture the positively charged Zn2+, guiding the homogeneous nucleation and plating of Zn. Chen's group fabricated a 3D N-doped carbon nanofiber film@Zn (3DN-C@Zn) anode to assemble a 3DN-C@Zn//AlVO-DMF battery. The N doping can improve the hydrophilicity of carbon fibers, decreasing the diffusion energy barrier of Zn2+.130 Therefore, the 3DN-C@Zn//AlVO-DMF battery was stably cycled over 200 cycles at 1 A g−1 without obvious capacity decay, which is better than that of bare Zn which suffered a short circuit after three cycles at the same current density. Besides, Zhang's group reported a novel N,O co-doped carbon nanofiber interlayer of a Zn anode via the electrospinning method combined with carbonization treatment.33 At high temperatures, the PAN fibrous membrane transformed into a freestanding carbon fiber interlayer doped with abundant O and N atoms. As the result of theoretical calculation, compared with other sites, the C
O/NPd (−1.11 eV) and C
O/NPr dual doping sites (−1.64 eV) showed higher binding energy with the Zn atom, indicating a higher ability to absorb Zn2+ (Fig. 8a). Therefore, owing to the porous structure of carbon fibers and high Zn affinity of N and O heteroatoms, a compact and flat Zn deposition layer on the carbon fiber interlayer can be observed after cycling for 400 h at 5 mA cm−2 (Fig. 8b). As exhibited in Fig. 8c and d, at the current density of 5 mA cm−2 and areal capacity of 1 mA h cm−2, the modified symmetric cell displayed a lower nucleation potential of about 59.5 mV, and a stabler cycling ability (over 1200 h).
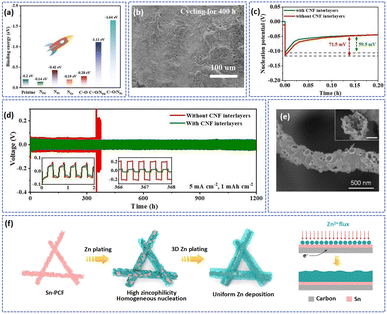 |
| Fig. 8 (a) A comparison of the binding energy between Zn atoms and different adsorption sites. The morphology (b), charge/discharge curves (d), and Zn nucleation overpotential (c) at 5 mA cm−2 with a capacity of 1 mA h cm−2. Adapted from ref. 33, copyright 2021, Elsevier B.V. (e) The SEM image and (f) Zn plating and nucleation diagrams on Sn-PCF. Adapted from ref. 134, copyright 2022, Elsevier B.V. | |
In addition, the introduction of zincophilic metal nanoparticles such as Ag,131 Sn,121 Co,132 and In133 on the substrate can also enhance the zincophilicity of the carbon nanofiber matrix. These zincophilic metal nanoparticles can be coupled with the carbon fibers to stabilize the Zn anode by lowering the nucleation potential of Zn and uniformizing the current density. Yang et al. prepared an Sn modified porous carbon fiber (Sn-PCF) framework with a hollow structure to uniformize the deposition of Zn2+ (Fig. 8e).134 At a high current density of 10 mA cm−2 with an areal capacity of 5 mA h cm−2, the Sn-PCF@Zn‖Sn-PCF@Zn symmetric cell exhibited a small voltage hysteresis of 47 mV and a long cycle life (over 500 h), which was almost 10 times that of PCF@Zn. In addition, at a current density of 10 A g−1, Sn-PCF@Zn//Na2V6O16·1.63H2O demonstrated a high capacity retention of 73.5% after 2500 cycles. The reason for the high stable cycle performance of Sn-PCF can be described as the metal Sn possessing a high adsorption ability, which is favorable for regulating the nucleation and deposition of Zn. Besides, the metal Sn can increase the hydrogen evolution energy barrier of the electrode, inhibiting the occurrence of hydrogen evolution reactions. Therefore, owing to the synergetic effect of multifunctional Sn metal and 3D porous carbon, the Zn can be uniformly deposited on the surface of the Sn-PCF (Fig. 8f), and the Sn-PCF@Zn anode had an excellent cycling ability during the test.
Moreover, introducing Cu nanoparticles on the surface of carbon not only improves the conductivity of carbon fibers but also promotes the deposition of Zn. Yang et al. reported Cu nanoparticle modified carbon fibers (Cu@CNFs) as the protective layer to stabilize the anode.135 Benefiting from the large SSA of carbon fibers and the zincophilicity of Cu nanoparticles, the Cu@CNFs-Zn exhibited low polarization and high deposition/dissolution efficiency in cycling.
In addition to doping metal nanoparticles on carbon fibers to homogenize Zn2+ deposition, many researchers have added metal oxides to electrode materials to achieve stable cycling of the Zn anode. For instance, defective ZnOx nanoparticles also demonstrated good affinity for Zn, which can be used to enhance the zincophilicity of electrospun carbon fibers.136 Xue et al. fabricated a 3D porous fiber with TiO2 and SiO2 uniformly distributed in the interior of hollow HSTF.35 Directed by the uniform TiO2, the Zn preferred to deposit at the zincophilic TiO2 seeds inside the fibers and was further accommodated in the porous carbon fiber matrixes without the growth of Zn dendrites. As shown in Fig. 9a, with the increase in plating capacity, the Zn tended to form a uniform and dense deposition layer in the porous pores rather than the surface of carbon fibers. Besides, the inert material of SiO2 can significantly reduce the desolvation active energy during cycling and improve the deposition efficiency of Zn. Consequently, at a high current of 20 mA cm−2, the Zn@HSTF anode demonstrated a highly stable plating/stripping behavior over 2000 cycles (Fig. 9b). Furthermore, the Zn@HSTF//MnO2 full battery delivered impressive cyclability with 85% capacity retention after 1000 cycles at 1 A g−1.
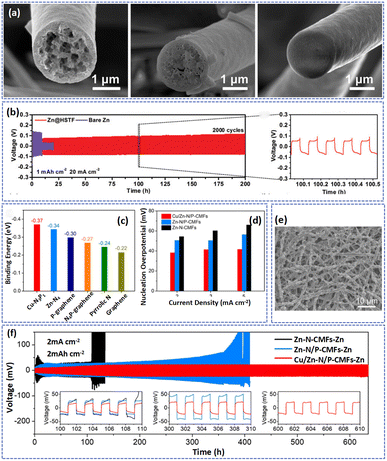 |
| Fig. 9 (a) SEM images showing the top view and cross-sections of the HSTF host after plating with various deposition capacities. (b) Voltage profiles of symmetrical cells at current densities of 20 mA cm−2 and 1 mA h cm−2. Adapted from ref. 35, copyright 2021, Wiley-VCH. (c) A comparison of the binding energy between Zn atoms and different adsorption sites. (d) Nucleation overpotential of Zn on different substrates at current densities of 2, 3, and 5 mA cm−2. (e) FESEM image of the Cu/Zn-N/P-CMF framework after Zn plating with capacities of 2 mA h cm−2. (f) Cycling performance at 2 mA cm−2 and 2 mA h cm−2 for symmetric cells using different composite Zn electrodes. Adapted from ref. 42, copyright 2023, American Chemical Society. | |
3D carbon fibers with functional groups and metal-based nanoparticles could combine the synergistic effects of two zincophilic materials to homogenize the deposition of Zn2+. Yu et al. fabricated a 3D conductive fiber network (Sn@NHCF) consisting of N-doped hollow carbon and Sn nanoparticles.58 The Sn nanoparticles and doped N element possess high zincophilicity and can reduce the nucleation barrier in cycling. Therefore, even after 100 cycles, the Sn@NHCF-Zn electrode exhibited a high coulombic efficiency of 99.7% at a current density of 5 mA cm−2 with 5 mA h cm−2. Typically, Zeng et al. prepared N,P-codoped carbon macroporous fibers embedded with atomically dispersed Cu and Zn atoms (Cu/Zn-N/P-CMFs) as the host for the deposition of Zn.42 It is worth noting that the introduction of N and P atoms not only enhanced the hydrophilicity of carbon fibers but also facilitated the dispersion of Cu and Zn atoms. Besides, they produced Cu-p/Zn-N-CMFs by substituting tannic acid for phytic acid, highlighting the crucial function of P. The results showed that in the absence of PA, Cu aggregated from nanoparticles, which will decrease the reversibility of Zn plating/stripping. The results of theoretical calculation further revealed the zincophilicity of Cu, Zn, N, and P atoms, which can decrease the nucleation overpotential of Zn and favor the oriented deposition of the Zn(002) plane to achieve a dendrite-free anode (Fig. 9c and d). As displayed in Fig. 9e, at a plating capacity of 2 mA h cm−2, the Zn was uniformly deposited on the surface of the substrate with parallel nanoflakes. As a result, the Cu/Zn-N/P-CMFs-Zn‖Cu/Zn-N/P-CMFs-Zn cell displayed a small voltage hysteresis (44.9 mV) and a long cycle life (630 h) at a current density of 2 mA cm−2 with 2 mA h cm−2 (Fig. 9f). In contrast, the battery based on the Zn-N-CMFs-Zn electrode suffered a short-circuit after 110 h due to the serious Zn dendrite growth. Moreover, the Cu/Zn-N/P-CMFs-Zn//MnO2 exhibited ultralong life up to 2500 cycles with a capacity retention of 88.8% at 1 A g−1.
4.2.3 Polymer fibers.
Although the excellent conductivity of carbon fibers can reduce charge accumulation and facilitate electric field distribution, the metal Zn tends to deposit inside the layer, easily resulting in a non-uniform plating behavior.128 In addition to carbon fibers, the electrospun polymer fibers also play an essential role in Zn anode protection. Compared with carbon, the polymer nanofiber protective layer can be formed in situ by the electrospinning method which avoids the utilization of the binder.137 More importantly, the thickness of the polymer fiber layer can be controlled by modulating the electrospinning time. Moreover, the polymer layer has a high flexibility and porous structure, and most of the polymer layer is ionically conductive but electronically insulating, which is beneficial for transporting Zn2+ across the interface layer and the uniform deposition of Zn2+.138,139 In fact, the polymer possesses numerous polar groups that serve as adsorption sites for Zn2+ transfer along the polymer chain to the reaction interface.140 Additionally, these groups facilitate the homogeneous distribution of Zn2+ at the molecular scale by enabling fast ion transport rates. Liu et al. reported an artificial interface (TPZA) with high ionic conductivity (19.8 mS cm−1) by permeating Zn-alginate (ZA) into porous thermoplastic polyurethane (TPU) fibers (Fig. 10a).141 As shown in Fig. 10b and c, owing to the protection of TPZA, the anode sustained the pristine morphology without the formation of by-products. For comparison, after 30 days, the Zn anode which was immersed in the electrolyte was randomly covered by the oriented hexagonal Zn4SO4(OH)6·3H2O. In addition to the property of anti-corrosion, the Zn2+ can transfer along the polymer chains of Zn-Alg, improving the transfer kinetics of Zn2+. Therefore, the Zn@TPZA//Zn@TPZA can be stably cycled over 1200 h at a current density of 5 mA cm−2 with a capacity of 5 mA h cm−2 (Fig. 10d).
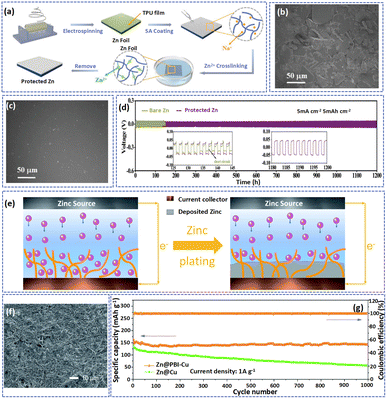 |
| Fig. 10 (a) A description of the fabrication process of Zn@TPZA. SEM images of (b) bare Zn and (c) Zn@TPZA after immersion in 2 M ZnSO4 electrolyte for 30 days. (d) Cycling performance of bare Zn and Zn@TPZA anodes at 5 mA cm−2/5 mA h cm−2. Adapted from ref. 133, copyright 2022, Wiley-VCH. (e) Schematic illustration of Zn deposition on a PBI nanofiber framework modified Cu electrode. (f) SEM image of Zn@PBI-Cu after 100 cycles at 10 mA cm−2. (g) Long-term cycling performance of the battery at 1 A g−1. Adapted from ref. 42, copyright 2020, Royal Society of Chemistry. | |
A polybenzimidazole (PBI) nanofiber with abundant N-containing functional groups can promote the uniform deposition of Zn. Jian et al. constructed a PBI framework on the surface of Cu foil by an electrospinning method to serve as the substrate for Zn deposition, promoting uniform nucleation of Zn and achieving a dendrite-free Zn anode.47 The PBI nanofiber host with polar amine groups and porous structure can promote the permeation of electrolytes in the electrode. As illustrated in Fig. 10e, during the plating of Zn, the amine groups can act as nucleation seeds to guide the Zn to evenly deposit on the pores of the PBI nanofiber substrate to inhibit the formation of Zn dendrites. Consequently, at a current density of 10 mA cm−2, the Zn@PBI-Cu anode showed a compact surface without the vertical growth of zinc dendrites after 100 cycles (Fig. 10f). Besides, at a current density of 1 A g−1, the Zn@PBI-Cu//MnO2 displayed high capacity retention (close to 100%) and a high coulombic efficiency of about 100% after 100 cycles (Fig. 10g). Although this polymer fiber shows outstanding ability to suppress the growth of Zn dendrites, these nonconductive layers exhibit a huge impedance of interfaces which is not conducive to the rate capability of AZIBs.142 The reported electrospun fibers in the anode and their corresponding electrochemical performance are summarized in Table 4.
Table 4 A summary of electrospinning nanofibers for the Zn anode of AZIBs
Anode |
Role of fibers |
Electrospinning solution (precursor/polymer/solvent) |
Structure |
Voltage hysteresis |
Life span |
Coulombic efficiency |
Cycling stability |
Ref. |
Zn@CNF |
Substrate |
PAN/DMF |
Porous |
Less than 20 mV |
488 h at 0.5 mA cm−2 |
98.3% at 0.5 mA cm−2 (126 cycles) |
92.1% at 0.5 A g−1 after 260 cycles |
45
|
ZnCNF |
PAN/DMF |
— |
23.9 mV |
400 h at 0.1 mA cm−2 |
— |
89.4% at 1C after 300 cycles |
124
|
3DN-C@Zn |
CO(NH2)2, Si(OC2H5)4/PAN, PMMA/DMF |
— |
34 mV |
1000 h at 1 mA cm−2 |
99% after 300 cycles |
∼100% at 1 A g−1 after 200 cycles |
130
|
Sn-PCF@Zn |
SiO2/PAN/DMF |
Hollow |
47 mV |
500 h at 10 mA cm−2 |
99.8% at 10 mA cm−2 after 1000 cycles |
73.5% at 10 A g−1 after 2500 cycles |
134
|
Zn@CoCC |
— |
Hierarchical |
— |
800 h at 20 mA cm−2 |
— |
— |
132
|
Zn@Ni@AgNFs |
PVA/H2O |
Core/shell |
— |
— |
— |
90% at 0.13 mA cm−2 after 500 cycles |
143
|
ZnOx@PCNF/Zn |
ZIF-8/PAN/DMF |
— |
34 mV |
250 h at 1 mA cm−2 |
99.3% at 1 mA cm−2 after 150 cycles |
75% at 1C after 100 cycles |
136
|
Zn@HSTF |
C16H36O4Ti, C8H20O4Si/PVP/ethanol, acetic acid |
Hollow |
154 mV |
200 h at 20 mA cm−2 |
99.54% at 20 mA cm−2 after 100 cycles |
85% at 1 A g−1 after 1000 cycles |
35
|
Sn@NHCF-Zn |
SSR/PAN/DMF |
Hollow |
21 mV |
370 h at 1 mA cm−2 |
99.7% at 5 mA cm−2 after 100 cycles |
— |
58
|
Cu/Zn-N/P-CMFs-Zn |
PA-ZnCu NBs/PAN/DMF |
Hollow |
44.9 mV |
630 h at 2 mA cm−2 |
98.2% at 10 mA cm−2 (900 cycles) |
88.8% at 1 A g−1 after 2500 cycles |
42
|
Cu NBs@NCFs-Zn |
CuS NBs/PAN/DMF |
Hollow |
34.6 mV |
450 h at 2 mA cm−2 |
98.8% at 5 mA cm−2 (1000 cycles) |
67.6% at 1 A g−1 after 2000 cycles |
46
|
Zn@PBI-Cu |
PBI/DMAc |
— |
35 mV |
Over 300 h at 10 mA cm−2 |
— |
∼100% at 1 A g−1 after 1000 cycles |
47
|
Zn@PAN-Cu |
PAN/DMF |
— |
— |
∼270 h at 2 mA cm−2 |
∼100% at 2 mA cm−2 |
— |
144
|
Zn@PNF-Cu |
P(VDF-TrFE), pyridine formate buffer/DMF |
— |
— |
250 h at 10 mA cm−2 |
99.2% at 1 mA cm−2 (after 300 cycles) |
— |
145
|
Zn anode with a CNF interlayer |
Protective layer |
PAN/DMF |
— |
— |
1200 h at 5 mA cm−2 |
99% at 1 mA cm−2 (60 cycles) |
108.3% at 1 A g−1 after 420 cycles |
33
|
Cu@CNFs-Zn |
Cu(CH3COO)2·H2O/PAN/DMF |
— |
58 mV |
2200 h at 1 mA cm−2 |
99.9% at 5 mA cm−2 (600 cycles) |
— |
135
|
Zn@MCFs |
ZIF-8/PMMA, PAN/DMF |
Hollow capsule-like |
— |
2500 h at 1 mA cm−2 |
99.67% at 2 mA cm−2 (1000 cycles) |
82.8% at 1 A g−1 after 600 cycles |
40
|
Zn@TPZA |
TPU/DMF |
— |
— |
1200 h at 5 mA cm−2 |
99.05% at 5 mA cm−2 (300 cycles) |
— |
141
|
β-PVDF-Zn |
PVDF/DMF, acetone |
Porous |
40 mV |
850 h at 0.5 mA cm−2 |
— |
— |
146
|
4.3 Separators
High-performance AZIBs depend on the synergy of all components. The separator acts as a carrier for the electrolyte, controlling the transport of ions, which determines the performance of the battery. Glass fiber separators are widely applied in AZIBs due to their high wettability, high ionic conductivity (about 17.3 mS cm−1 after absorbing electrolyte), and abundant porous structure. However, the metal Zn deposit in these pores of the glass fiber separator cannot be entirely converted to Zn2+ in the stripping process, ultimately resulting in the formation of “dead Zn”.27 Moreover, the glass fiber separator that absorbs excess electrolytes increases the total mass of the battery resulting in a low energy density.26 Although filter paper and non-woven fabric separators possess excellent mechanical properties and high porosity, their further application is prevented by the poor transport regulation ability.147 An ideal separator for AZIBs should not only have excellent ionic conductivity after taking in the electrolyte but should also regulate the transport of Zn2+ during the cycling process and prevent the growth of Zn dendrites. Compared to conventional separators, electrospun polymer fiber separators have attracted extensive attention because of their thermal stability, mechanical merit, electronic insulation, high mechanical flexibility, and controllable structure.148 In addition, the functional groups in the polymer fiber can promote the formation of coordination bonds with Zn2+, homogenizing the deposition of Zn2+ and suppressing the formation of Zn dendrites.41
4.3.1 Pure polymer separators.
Owing to its excellent electrochemical stability, PAN has often been used to fabricate electrospun fiber separators.149,150 To stabilize the Zn anode, Liang's team synthesized a 3D long-range ordered PAN separator.34 Compared to the glass fiber separator (640.8%), the lower electrolyte uptake value (430.3%) of PAN film is advantageous for improving the energy density of the battery. Furthermore, the abundant –CN functional groups in the fibers not only promoted the electric field uniform distribution but also combined with Zn2+ to guide the uniform deposition of Zn2+ and effectively inhibit the growth of Zn dendrites. Benefiting from the mechanical flexibility, the PAN film was used as the separator and the current collector to prepare novel “paper-like” AZIBs with an all-in-one structure.151 As displayed in Fig. 11a and b, the Zn and MnO2 nanosheets were closely deposited on both sides of PAN which was modified by carbon nanotubes to form a cell with a thickness of about 97 μm, accelerating the transfer of electrons and achieving rapid kinetics. Therefore, the full cell exhibited a high capacity retention of about 98.7% after 500 cycles at 1 mA cm−2. In addition, at a bending angle of 180°, the battery also showed a high discharge capacity after being cycled at various current densities, indicating an excellent rate performance and outstanding flexibility (Fig. 11c).
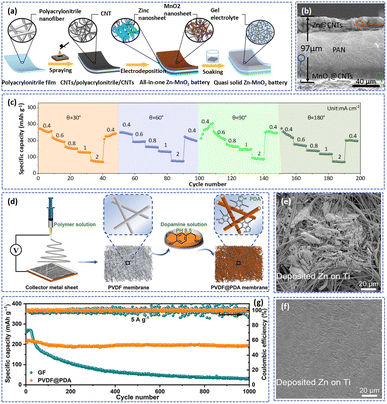 |
| Fig. 11 (a) Diagrammatic sketch showing the fabrication procedure of the AZIB. (b) SEM image of the cross-sectional view of the individual AZIB. (c) Rate performance of the AZIB cell at variational bending angles of 30, 60, 90, and 180°. Adapted from ref. 151, copyright 2021, American Chemical Society. (d) Schematic illustration of the fabrication process of the PVDF@PDA separator. SEM images of the Ti foils after Zn deposition at 2 mA cm−2 and 5 mA h cm−2 in Zn/Ti asymmetric cells with (e) a GF separator and (f) PVDF@PDA separator. (g) Long cycling performance of batteries with different separators at 5 A g−1. Adapted from ref. 41, copyright 2022, The Authors. | |
4.3.2 Hybrid polymer separators.
Although a pure polymer film with high porosity and large SSA can be prepared by the electrospinning method, the poor mechanical strength has limited its application in flexible devices. Compared with pure polymer separators, hybrid polymer separators are prepared by mixing different types of substances by the electrospinning method (or pure polymer separators are modified by functional materials) which can promote the uniform deposition of Zn2+ and improve the mechanical strength of separators due to the multi-functional role and synergistic effect of the newly formed hybrids. For example, Saisangtham et al. used highly flexible polyurethane (PU) as the raw material to prepare PAN/bio-based PU separators by the electrospinning method.152 Besides, they investigated the effects of electrospinning solution concentration and parameters on the separators. The results revealed that the PAN separator modified by PU had a tensile strength of 44.16 MPa, which is much higher than that of the pure PAN membrane.
Moreover, some functional materials including graphene oxide (GO),48 sulfonated polysulfone (SPSF),155 and MXene154 have been added to regulate the flux of Zn2+. Among them is the strong interaction between the functional groups in polydopamine (PDA) and Zn2+, which promotes the transport of Zn2+ on the surface between the separator and electrolyte. Zhou's group developed a PDA functionalized PVDF (PVDF@PDA) to uniformize the homogeneous distribution of Zn2+ and suppress the formation of Zn dendrites (Fig. 11d).41 These abundant polar functional groups (–OH and –NH–) in the PDA improved the hydrophilicity of PVDF@PDA as well as favoring the formation of Zn–O and Zn–N coordination bonds with Zn2+. According to density functional theory calculations, the Zn–O and Zn–N can function as nucleation seeds to decrease the nucleation barrier of Zn and guide the ordered deposition of Zn2+. Herein, compared with the glass fiber separator (Fig. 11e), the surface of Ti foil with the functional separator was even without agglomeration and cracks at 2 mA cm−2 and 5 mA h cm−2 (Fig. 11f). Besides, the PVDF@PDA hybrid separator can effectively prevent the shuttling of V-species by formation of the V–O coordination bond during cycling. Therefore, as demonstrated in Fig. 11g, the Zn//NH4V4O10 full cell with the PVDF@PDA separator exhibited a high capacity retention of 92.3% after 1000 cycles at 5 A g−1.
Poly(m-phenylenedicarboxamide) (PMIA) with abundant amide groups, electrolyte affinity, and outstanding mechanical strength has been used as the separator for Li metal batteries.156 Inspired by this, Hu et al. fabricated a hybrid SPSF@PMIA (SP) nanofiber separator to stabilize the Zn anode.155 The abundant hydrophilic –SO3− in SPSF and the N atom in PMIA with electronegativity will repel anions, which limit the migration of anions and enable the fast transfer of Zn2+. Therefore, compared with the batteries with PMIA (glass fiber or SPSF), the Zn/SP/Zn showed a higher Zn2+ transfer number (tZn2+) of 0.74, which benefits the fast ion diffusion and fast charge transfer processes. Besides, owing to the strong ability of –CO–NH– in PMIA to absorb Zn2+ and the zincophilicity of –SO3− in SPSF, the battery with the SP separator demonstrated a stable cycling ability and rate performance. Table 5 summarizes the polymer nanofiber separator performance.
Table 5 A summary of electrospinning nanofibers for separators of AZIBs
Separator |
Electrospinning solution (precursor/polymer/solvent) |
Electrolyte uptake |
Ionic conductivity |
Tensile strength |
Life span |
Cycling stability |
Ref. |
PAN |
PAN/DMF |
430.3% |
0.45 × 10−2 S cm−1 |
— |
800 h at 0.283 mA cm−2 |
84.3% at 5 A g−1 after 1000 cycles |
34
|
PAN |
PAN/DMF |
— |
— |
— |
— |
98.7% at 1 mA cm−2 after 500 cycles |
151
|
PVA-PAA |
PVA, PAA/H2O |
— |
— |
— |
— |
80% at 1 A g−1 after 2000 cycles |
153
|
PAN/bio-based PU |
PAN, bio-based PU/DMF |
1971% |
3.11 mS cm−1 |
44.16 MPa |
250 h at 1 mA cm−2 |
— |
152
|
PVDF@PDA |
PVDF/DMF and DMAC (1 : 1 by vol) |
403% |
13.9 mS cm−1 |
9.7 MPa |
Over 200 h at 2 mA cm−2 |
92.3% at 5 A g−1 after 1000 cycles |
41
|
PG |
GO/PAN/DMF |
2267% |
7.69 mS cm−1 |
7.1 MPa |
13 000 h at 1 mA cm−2 |
71.5% at 2 A g−1 after 2800 cycles |
48
|
PAN/bio-based PU/Ti3C2Tx MXene |
Ti3C2Tx MXene/PAN, bio-based PU/DMF |
2214 ± 49% |
3.35 mS cm−1 |
1.68 MPa |
— |
— |
154
|
SP |
SPSF, PMIA/DMF, DMAc |
810% |
19.9 mS cm−1 |
2.9 MPa |
Over 1000 h at 1 mA cm−2 |
80.8% at 0.5 A g−1 after 1000 cycles |
155
|
5 Summary and perspectives
In conclusion, the reasons for the outstanding properties of the electrospun nanofibers are as follows. First, electrospun carbon fibers with large SSA and high conductivity can improve the electronic conductivity of materials and promote the diffusion of electrolyte in electrodes, which improve the rate performance and cycling ability of the battery. Second, these materials play a momentous role in maintaining the structural stability of electrodes. The porous (or hollow) structure can accommodate the Zn deposition and prevent the volume variation of the anode. In addition, the dissolution of active materials can be suppressed by forming a physical protective layer. Third, electrospun fibers with high porosity and flexibility can be used as binder-free and bendable electrodes, promising for bendable and wearable devices.
In this review, we summarized the recent progress of electrospinning nanofibers in AZIBs, focusing on vanadium-based materials, manganese-based materials, other cathode materials, carbon fiber-based and polymer fiber substrates, Zn anode protective layer, and polymer separators. In addition, we briefly introduced the principle and processing of the electrospinning technique and structural design of the electrospun fibers. Despite electrospinning fibers having made some research progress in AZIBs, several challenges still remain to be addressed. Therefore, to broaden the application of electrospun nanofibers, the following suggestions should be considered.
5.1 Precise preparation of functional fibers
The microstructure and properties of the electrospun fibers are related to the precursor solution, electrospinning parameters, and subsequent electrospinning process. However, very few studies have investigated the relationship between various parameters and the performance of fibers in AZIBs. Besides, various zincophilic units (such as functional groups, metal nanoparticles, metal oxides, and heteroatoms) have been reported to improve the zincophilicity and hydrophilicity of fibers to facilitate the homogeneous deposition of Zn. Sometimes, excessive zincophilic materials tend to accumulate together, which not only does not homogenize the Zn deposition but also changes the Zn deposition behavior, resulting in a severe growth of Zn dendrites. Thus, the preparation parameters of electrospun fibers should be systematically investigated and optimized.
5.2 In-depth investigation of the mechanisms
The working mechanism of the fiber material cannot be explained simply as the uniform distribution of the electric field on the surface of the Zn anode, the regulation of the flux of zinc ions, and the zincophilicity of the modified material. Specific experimental evidence should be provided. Moreover, some advanced characterization techniques including in situ optical microscopy (OM), in situ electron microscopy (EM) and in situ neutron depth profiling (NDP) and imaging can be used to elucidate the Zn growth mechanism. Analysis of the Zn metal is crucial to understanding the failure mechanism of AZIBs. Considering that the dynamics of electrochemical processes are difficult to observe during cycling, theoretical calculation can be used to further understand the mass transfer process of Zn2+.
5.3 Establishing the test standards
Although electrospun nanofiber electrodes show an impressive long cycle life at a small current density, it is difficult to meet the requirements of commercial applications. Moreover, different standards were used to test the batteries in previous studies, making it difficult to objectively evaluate various modification strategies. Therefore, it is important to establish unified test standards, which will facilitate the application of AZIBs. Besides, the electrochemical performance of the battery over a wide range of temperatures should be provided to promote the practical application of AZIBs in all climates.
5.4 Promoting large-scale commercial application of electrospinning technology
Electrospinning technology provides new insights into improving the performance of batteries. However, it is difficult to apply in industrial production on a large scale due to the use of toxic and corrosive solvents, expensive precursors, and lower production efficiency. Therefore, improving production efficiency, developing low-toxicity and environmentally friendly solvents, and exploring new types of and inexpensive polymer precursors are the main development directions for the future.
Author contributions
All authors contributed to the writing of the manuscript and approved the final version of the manuscript.
Conflicts of interest
The authors declare no conflict of interest.
Acknowledgements
This work was supported financially by the National Natural Science Foundation of China (52171198, 51922099), Fundamental Research Funds for the Central Universities (buctrc202104), and the SINOPEC Technology Development Program (SINOPEC-BUCT Joint project of Molecular Chemistry Center, no. 222230).
Notes and references
- W. Ma, S. Wan, X. Cui, G. Hou, Y. Xiao, J. Rong and S. Chen, Exploration and application of self-healing strategies in lithium batteries, Adv. Funct. Mater., 2023, 33, 2212821 CrossRef CAS.
- L. Feng, Y. Liu, L. Wu, W. Qin, Z. Yang and J. Liu, Surface modification with oxygen vacancy in LiNi0.5Co0.2Mn0.3O2 for lithium-ion batteries, J. Alloys Compd., 2021, 881, 160626 CrossRef CAS.
- L. Feng, Y. Liu, W. Qin, Z. Yang and J. Liu, A novel double modification to enhance electrochemical performance of LiNi0.5Co0.2Mn0.3O2 by substituting Ce for Co site, Electrochim. Acta, 2021, 391, 138904 CrossRef CAS.
- Z. Yao, Y. Wang, S. Wan, W. Ma, J. Rong, Y. Xiao, G. Hou and S. Chen, Recent advances in designing solid-state electrolytes to reduce the working temperature of lithium batteries, Mater. Chem. Front., 2023 10.1039/D3QM00662J.
- M. Zhao, Y. Lv, S. Zhao, Y. Xiao, J. Niu, Q. Yang, J. Qiu, F. Wang and S. Chen, Simultaneously stabilizing both electrodes and electrolytes by a self-separating organometallics interface for high-performance zinc-ion batteries at wide temperatures, Adv. Mater., 2022, 34, 2206239 CrossRef CAS PubMed.
- L. Ma, S. Chen, N. Li, Z. Liu, Z. Tang, J. A. Zapien, S. Chen, J. Fan and C. Zhi, Hydrogen-free and dendrite-free all-solid-state Zn-ion batteries, Adv. Mater., 2020, 32, 1908121 CrossRef CAS PubMed.
- Y. Lv, M. Zhao, Y. Du, Y. Kang, Y. Xiao and S. Chen, Engineering a self-adaptive electric double layer on both electrodes for high-performance zinc metal batteries, Energy Environ. Sci., 2022, 15, 4748–4760 RSC.
- S. Zhao, C. Li, X. Zhang, N. Li, T. Wang, X. Li, C. Wang, G. Qu and X. Xu, An advanced Ca/Zn hybrid battery enabled by the dendrite-free zinc anode and a reversible calcification/decalcification NASICON cathode, Sci. Bull., 2023, 68, 56–64 CrossRef CAS PubMed.
- M. Zhao, J. Rong, F. Huo, Y. Lv, B. Yue, Y. Xiao, Y. Chen, G. Hou, J. Qiu and S. Chen, Semi-immobilized ionic liquid regulator with fast kinetics toward highly stable zinc anode under -35°C to 60°C, Adv. Mater., 2022, 34, 2203153 CrossRef CAS PubMed.
- Y. Yuan, S. Wu, X. Song, J. Y. Lee and B. Kang, Recent progress and regulation strategies of layered materials as cathode of aqueous zinc-ion batteries, Energy Environ. Mater., 2023, e12632, DOI:10.1002/eem2.12632.
- N. Liu, B. Li, Z. He, L. Dai, H. Wang and L. Wang, Recent advances and perspectives on vanadium-and manganese-based cathode materials for aqueous zinc ion batteries, J. Energy Chem., 2021, 59, 134–159 CrossRef CAS.
- X. Jia, C. Liu, Z. G. Neale, J. Yang and G. Cao, Active materials for aqueous zinc ion batteries: synthesis, crystal structure, morphology, and electrochemistry, Chem. Rev., 2020, 120, 7795–7866 CrossRef CAS PubMed.
- S. Zuo, X. Xu, S. Ji, Z. Wang, Z. Liu and J. Liu, Cathodes for aqueous Zn-ion batteries: materials, mechanisms, and kinetics, Chemistry, 2021, 27, 830–860 CrossRef CAS PubMed.
- M. Zhang, R. Liang, T. Or, Y.-P. Deng, A. Yu and Z. Chen, Recent progress on high-performance cathode materials for zinc-ion batteries, Small Struct., 2020, 2, 2000064 CrossRef.
- G. Fang, J. Zhou, A. Pan and S. Liang, Recent advances in aqueous zinc-ion batteries, ACS Energy Lett., 2018, 3, 2480–2501 CrossRef CAS.
- C. Xu, B. Li, H. Du and F. Kang, Energetic zinc ion chemistry: the rechargeable zinc ion battery, Angew. Chem., Int. Ed., 2012, 51, 933–935 CrossRef CAS.
- N. Zhang, F. Cheng, J. Liu, L. Wang, X. Long, X. Liu, F. Li and J. Chen, Rechargeable aqueous zinc-manganese dioxide batteries with high energy and power densities, Nat. Commun., 2017, 8, 405–413 CrossRef PubMed.
- K. Zhu, T. Wu and K. Huang, A high capacity bilayer cathode for aqueous Zn-ion batteries, ACS Nano, 2019, 13, 14447–14458 CrossRef CAS PubMed.
- H. Pan, Y. Shao, P. Yan, Y. Cheng, K. S. Han, Z. Nie, C. Wang, J. Yang, X. Li, P. Bhattacharya, K. T. Mueller and J. Liu, Reversible aqueous zinc/manganese oxide energy storage from conversion reactions, Nat. Energy, 2016, 1, 16039 CrossRef CAS.
- J. R. Loh, J. Xue and W. S. V. Lee, Challenges and strategies in the development of zinc-ion batteries, Small Methods, 2023, 7, 2300101 CrossRef CAS PubMed.
- P. Sun, L. Ma, W. Zhou, M. Qiu, Z. Wang, D. Chao and W. Mai, Simultaneous regulation on solvation shell and electrode interface for dendrite-free Zn ion batteries achieved by a low-cost glucose additive, Angew. Chem., Int. Ed., 2021, 60, 18247–18255 CrossRef CAS PubMed.
- Y. Lv, Y. Xiao, L. Ma, C. Zhi and S. Chen, Recent advances in electrolytes for “beyond aqueous” zinc-ion batteries, Adv. Mater., 2022, 34, 2106409 CrossRef CAS PubMed.
- L. Wu and Y. Dong, Recent progress of carbon nanomaterials for high-performance cathodes and anodes in aqueous zinc ion batteries, Energy Storage Mater., 2021, 41, 715–737 CrossRef.
- C. Guo, S. Yi, R. Si, B. Xi, X. An, J. Liu, J. Li and S. Xiong, Advances on defect engineering of vanadium-based compounds for high-energy aqueous zinc-ion batteries, Adv. Energy Mater., 2022, 12, 2202039 CrossRef CAS.
- Y. Zong, H. He, Y. Wang, M. Wu, X. Ren, Z. Bai, N. Wang, X. Ning and S. X. Dou, Functionalized separator strategies toward advanced aqueous zinc-ion batteries, Adv. Energy Mater., 2023, 13, 2300403 CrossRef CAS.
- L. Li, S. Jia, Z. Cheng and C. Zhang, Improved strategies for separators in zinc-ion Batteries, ChemSusChem, 2023, 16, e202202330 CrossRef CAS.
- Q. Ni, B. Kim, C. Wu and K. Kang, Non-electrode components for rechargeable aqueous zinc batteries: electrolytes, solid-electrolyte-interphase, current collectors, binders, and separators, Adv. Mater., 2022, 34, 2108206 CrossRef CAS PubMed.
- H. Jia, K. Liu, Y. Lam, B. Tawiah, J. H. Xin, W. Nie and S.-x. Jiang, Fiber-based materials for aqueous zinc ion batteries, Adv. Fiber Mater., 2022, 5, 36–58 CrossRef.
- H. Zhong, J. Huang, J. Wu and J. Du, Electrospinning nanofibers to 1D, 2D, and 3D scaffolds and their biomedical applications, Nano Res., 2021, 15, 787–804 CrossRef.
- B. Sun, Y. Z. Long, H. D. Zhang, M. M. Li, J. L. Duvail, X. Y. Jiang and H. L. Yin, Advances in three-dimensional nanofibrous macrostructures via electrospinning, Prog. Polym. Sci., 2014, 39, 862–890 CrossRef CAS.
- Q. Liu, J. Zhu, L. Zhang and Y. Qiu, Recent
advances in energy materials by electrospinning, Renewable Sustainable Energy Rev., 2018, 81, 1825–1858 CrossRef CAS.
- F. Tang, X. Wu, Y. Shen, Y. Xiang, X. Wu, L. Xiong and X. Wu, The intercalation cathode materials of heterostructure MnS/MnO with dual ions defect embedded in N-doped carbon fibers for aqueous zinc ion batteries, Energy Storage Mater., 2022, 52, 180–188 CrossRef.
- Y. Liang, Y. Wang, H. Mi, L. Sun, D. Ma, H. Li, C. He and P. Zhang, Functionalized carbon nanofiber interlayer towards dendrite-free, Zn-ion batteries, Chem. Eng. J., 2021, 425, 131862 CrossRef CAS.
- Y. Fang, X. Xie, B. Zhang, Y. Chai, B. Lu, M. Liu, J. Zhou and S. Liang, Regulating zinc deposition behaviors by the conditioner of PAN separator for zinc-ion batteries, Adv. Funct. Mater., 2021, 32, 2109671 CrossRef.
- P. Xue, C. Guo, N. Wang, K. Zhu, S. Jing, S. Kong, X. Zhang, L. Li, H. Li, Y. Feng, W. Gong and Q. Li, Synergistic manipulation of Zn2+ ion flux and nucleation induction effect enabled by 3D hollow SiO2/TiO2/carbon fiber for long-lifespan and dendrite-free Zn-metal composite anodes, Adv. Funct. Mater., 2021, 31, 2106417 CrossRef CAS.
- L. Ding, J. Gao, T. Yan, C. Cheng, L.-Y. Chang, N. Zhang, X. Feng and L. Zhang, Boosting the cycling stability of aqueous zinc-ion batteries through nanofibrous coating of a bead-like MnOx cathode, ACS Appl. Mater. Interfaces, 2022, 14, 17570–17577 CrossRef CAS.
- P. Hiralal, S. Imaizumi, H. E. Unalan, H. Matsumoto, M. Minagawa, M. Rouvala, A. Tanioka and G. A. J. Amaratunga, Nanomaterial-enhanced all-solid flexible zinc-carbon batteries, ACS Nano, 2010, 4, 2730–2734 CrossRef CAS.
- X. Chen, L. Wang, H. Li, F. Cheng and J. Chen, Porous V2O5 nanofibers as cathode materials for rechargeable aqueous zinc-ion batteries, J. Energy Chem., 2019, 38, 20–25 CrossRef.
- C. Kim, B. Y. Ahn, T.-S. Wei, Y. Jo, S. Jeong, Y. Choi, I.-D. Kim and J. A. Lewis, High-power aqueous zinc-ion batteries for customized electronic devices, ACS Nano, 2018, 12, 11838–11846 CrossRef CAS.
- H. Ying, P. Huang, Z. Zhang, S. Zhang, Q. Han, Z. Zhang, J. Wang and W. Q. Han, Freestanding and flexible interfacial layer enables bottom-up Zn deposition toward dendrite-free aqueous Zn-ion batteries, Nano-Micro Lett., 2022, 14, 180 CrossRef CAS.
- Y. Liu, S. Liu, X. Xie, Z. Li, P. Wang, B. Lu, S. Liang, Y. Tang and J. Zhou, A functionalized separator enables dendrite-free Zn anode via metal-polydopamine coordination chemistry, InfoMat, 2022, 5, e12374 CrossRef.
- Y. Zeng, Z. Pei, D. Luan and X. W. D. Lou, Atomically dispersed zincophilic sites in N,P-codoped carbon macroporous fibers enable efficient Zn metal anodes, J. Am. Chem. Soc., 2023, 145, 12333–12341 CrossRef CAS PubMed.
- J. Yang, H. Yang, C. Ye, T. Li, G. Chen and Y. Qiu, Conformal surface-nanocoating strategy to boost high-performance film cathodes for flexible zinc-ion batteries as an amphibious soft robot, Energy Storage Mater., 2022, 46, 472–481 CrossRef.
- W. Liu, Q. Su, R. Zhu, W. Shi, F. Zhang, G. Du, W. Zhao, M. Zhang and B. Xu, Chemical lithiation-induced oxygen vacancies in MnO2 at room temperature
for aqueous zinc-ion batteries, ACS Appl. Energy Mater., 2023, 6, 6689–6699 CrossRef CAS.
- J. Li, Q. Lin, Z. Zheng, L. Cao, W. Lv and Y. Chen, How is cycle life of three-dimensional zinc metal anodes with carbon fiber backbones affected by depth of dscharge and current density in zinc-ion batteries?, ACS Appl. Mater. Interfaces, 2022, 14, 12323–12330 CrossRef CAS.
- Y. Zeng, P. X. Sun, Z. Pei, Q. Jin, X. Zhang, L. Yu and X. W. David Lou, Nitrogen-doped carbon fibers embedded with zincophilic Cu nanoboxes for stable Zn metal anodes, Adv. Mater., 2022, 34, 2200342 CrossRef CAS.
- Q. Jian, Y. Wan, J. Sun, M. Wu and T. Zhao, A dendrite-free zinc anode for rechargeable aqueous batteries, J. Mater. Chem. A, 2020, 8, 20175–20184 RSC.
- L. Yao, C. Hou, M. Liu, H. Chen, Q. Zhao, Y. Zhao, Y. Wang, L. Liu, Z. W. Yin, J. Qiu, S. Li, R. Qin and F. Pan, Ultra-stable Zn anode enabled by fiber-directed ion migration using mass-producible separator, Adv. Funct. Mater., 2022, 33, 2209301 CrossRef.
- M. Liu, N. Deng, J. Ju, L. Fan, L. Wang, Z. Li, H. Zhao, G. Yang, W. Kang, J. Yan and B. Cheng, A review: electrospun nanofiber materials for lithium-sulfur batteries, Adv. Funct. Mater., 2019, 29, 1905467 CrossRef CAS.
- C. Li, M. Qiu, R. Li, X. Li, M. Wang, J. He, G. Lin, L. Xiao, Q. Qian, Q. Chen, J. Wu, X. Li, Y.-W. Mai and Y. Chen, Electrospinning engineering enables high-performance sodium-ion batteries, Adv. Fiber Mater., 2021, 4, 43–65 CrossRef.
- Y. Hao, F. Hu, Y. Chen, Y. Wang, J. Xue, S. Yang and S. Peng, Recent progress of electrospun nanofibers for zinc-air batteries, Adv. Fiber Mater., 2021, 4, 185–202 CrossRef.
- H. Chen, M. Li, C. Li, X. Li, Y. Wu, X. Chen, J. Wu, X. Li and Y. Chen, Electrospun carbon nanofibers for lithium metal anodes: progress and perspectives, Chin. Chem. Lett., 2022, 33, 141–152 CrossRef CAS.
- C.-L. Zhang and S.-H. Yu, Nanoparticles meet electrospinning: recent advances and future prospects, Chem. Soc. Rev., 2014, 43, 4423–4448 RSC.
- F. Shi, C. Chen and Z.-L. Xu, Recent advances on electrospun nanofiber materials for post-lithium ion batteries, Adv. Fiber Mater., 2021, 3, 275–301 CrossRef CAS.
- B. Zhang, F. Kang, J.-M. Tarascon and J.-K. Kim, Recent advances in electrospun carbon nanofibers and their application in electrochemical energy storage, Prog. Mater. Sci., 2016, 76, 319–380 CrossRef CAS.
- S. Shi, Y. Si, Y. Han, T. Wu, M. I. Iqbal, B. Fei, R. K. Y. Li, J. Hu and J. Qu, Recent progress in protective membranes fabricated via electrospinning: advanced materials, biomimetic structures, and functional applications, Adv. Mater., 2022, 34, 2107938 CrossRef CAS.
- Y. Fu, Q. Wei, G. Zhang, X. Wang, J. Zhang, Y. Hu, D. Wang, L. Zuin, T. Zhou, Y. Wu and S. Sun, High-performance reversible aqueous Zn-ion battery based on porous MnOx nanorods coated by MOF-derived N-doped carbon, Adv. Energy Mater., 2018, 8, 1801445 CrossRef.
- H. Yu, Y. Zeng, N. W. Li, D. Luan, L. Yu and X. W. Lou, Confining Sn nanoparticles in interconnected N-doped hollow carbon spheres as hierarchical zincophilic fibers for dendrite-free Zn metal anodes, Sci. Adv., 2022, 8, eabm5766 CrossRef CAS PubMed.
- Z. Sun, E. Zussman, A. L. Yarin, J. H. Wendorff and A. Greiner, Compound core-shell polymer nanofibers by Co-electrospinning, Adv. Mater., 2003, 15, 1929–1932 CrossRef CAS.
- X. Yang, J. Wang, H. Guo, L. Liu, W. Xu and G. Duan, Structural design toward functional materials by electrospinning: A review, e-Polym., 2020, 20, 682–712 CrossRef CAS.
- J. H. Yu, S. V. Fridrikh and G. C. Rutledge, Production of submicrometer diameter fibers by two-fluid electrospinning, Adv. Mater., 2004, 16, 1562–1566 CrossRef CAS.
- J. Yoon, H.-S. Yang, B.-S. Lee and W.-R. Yu, Recent progress in coaxial electrospinning: new parameters, various structures, and wide applications, Adv. Mater., 2018, 30, 1704765 CrossRef PubMed.
- J. Long, Z. Yang, F. Yang, J. Cuan and J. Wu, Electrospun core-shell Mn3O4/carbon fibers as high-performance cathode materials for aqueous zinc-ion batteries, Electrochim. Acta, 2020, 344, 136155 CrossRef CAS.
- Q. Wei, F. Xiong, S. Tan, L. Huang, E. H. Lan, B. Dunn and L. Mai, Porous one-dimensional nanomaterials: design, fabrication and applications in electrochemical energy storage, Adv. Mater., 2017, 29, 1602300 CrossRef PubMed.
- K. Yu, X. Pan, G. Zhang, X. Liao, X. Zhou, M. Yan, L. Xu and L. Mai, Nanowires in energy storage devices: structures, synthesis, and applications, Adv. Energy Mater., 2018, 8, 1802369 CrossRef.
- X. Cao, W. Chen, P. Zhao, Y. Yang and D.-G. Yu, Electrospun porous nanofibers: pore-forming mechanisms and applications for photocatalytic degradation of organic pollutants in wastewater, Polymers, 2022, 14, 3990 CrossRef CAS PubMed.
- P. Wang, H. Lv, X. Cao, Y. Liu and D.-G. Yu, Recent progress of the preparation and application of electrospun porous nanofibers, Polymers, 2023, 15, 921 CrossRef CAS PubMed.
- D. Guo, W. Zhao, F. Pan and G. Liu, Block copolymer-derived porous carbon fibers enable high MnO2 loading and fast charging in aqueous zinc-ion battery, Batteries Supercaps, 2022, 5, e202100380 CrossRef CAS.
- L. Li, S. Peng, J. K. Y. Lee, D. Ji, M. Srinivasan and S. Ramakrishna, Electrospun hollow nanofibers for advanced secondary batteries, Nano Energy, 2017, 39, 111–139 CrossRef CAS.
- A. K. Moghe and B. S. Gupta, Co-axial electrospinning for nanofiber structures: preparation and applications, Polym. Rev., 2008, 48, 353–377 CrossRef CAS.
- D. Ji, L. Fan, L. Tao, Y. Sun, M. Li, G. Yang, T. Q. Tran, S. Ramakrishna and S. Guo, The Kirkendall effect for engineering oxygen vacancy of hollow Co3O4 nanoparticles toward high-performance portable zinc-air batteries, Angew. Chem., Int. Ed., 2019, 58, 13840–13844 CrossRef CAS PubMed.
- G. Yang, X. Li, Y. He, J. Ma, G. Ni and S. Zhou, From nano to micro to macro: Electrospun hierarchically structured polymeric fibers for biomedical applications, Prog. Polym. Sci., 2018, 81, 80–113 CrossRef CAS.
- M. M. Hohman, M. Shin, G. Rutledge and M. P. Brenner, Electrospinning and electrically forced jets. I. Stability theory, Phys. Fluids, 2001, 13, 2201–2220 CrossRef CAS.
- H. Fong, I. Chun and D. H. Reneker, Beaded nanofibers formed during electrospinning, Polymer, 1999, 40, 4585–4592 CrossRef CAS.
- Z. Chen, J. Hu, S. Liu, H. Hou, G. Zou, W. Deng and X. Ji, Dual defects boosting zinc ion storage of hierarchical vanadium oxide fibers, Chem. Eng. J., 2021, 404, 126536 CrossRef CAS.
- Y. Zhang, S. Jiang, Y. Li, X. Ren, P. Zhang, L. Sun and H. Y. Yang, In situ grown hierarchical electrospun nanofiber skeletons with embedded vanadium nitride nanograins for ultra-fast and super-long cycle life aqueous Zn-ion batteries, Adv. Energy Mater., 2022, 13, 2202826 CrossRef.
- Y. Zhou, F. Chen, H. Arandiyan, P. Guan, Y. Liu, Y. Wang, C. Zhao, D. Wang and D. Chu, Oxide-based cathode materials for rechargeable zinc ion batteries: progresses and challenges, J. Energy Chem., 2021, 57, 516–542 CrossRef CAS.
- S. Yang, H. Du, Y. Li, X. Wu, B. Xiao, Z. He, Q. Zhang and X. Wu, Advances in the structure design of substrate materials for zinc anode of aqueous zinc ion batteries, Green Energy Environ., 2023, 8, 1531–1552 CrossRef CAS.
- V. Mathew, B. Sambandam, S. Kim, S. Kim, S. Park, S. Lee, M. H. Alfaruqi, V. Soundharrajan, S. Islam, D. Y. Putro, J.-Y. Hwang, Y.-K. Sun and J. Kim, Manganese and vanadium oxide cathodes for aqueous rechargeable zinc-ion batteries: a focused view on performance, mechanism, and developments, ACS Energy Lett., 2020, 5, 2376–2400 CrossRef CAS.
- J. Xia, L. Liu, S. Jamil, J. Xie, H. Yan, Y. Yuan, Y. Zhang, S. Nie, J. Pan, X. Wang and G. Cao, Free-standing SnS/C nanofiber anodes for ultralong cycle-life lithium-ion batteries and sodium-ion batteries, Energy Storage Mater., 2019, 17, 1–11 CrossRef.
- J. Li, L. Zhang, W. Xin, M. Yang, H. Peng, Y. Geng, L. Yang, Z. Yan and Z. Zhu, Rationally designed ZnTe@C nanowires with superior zinc storage performance for aqueous Zn batteries, Small, 2023, 2304916, DOI:10.1002/smll.202304916.
- S. Islam, M. H. Alfaruqi, J. Song, S. Kim, D. T. Pham, J. Jo, S. Kim, V. Mathew, J. P. Baboo, Z. Xiu and J. Kim, Carbon-coated manganese dioxide nanoparticles and their enhanced electrochemical properties for zinc-ion battery applications, J. Energy Chem., 2017, 26, 815–819 CrossRef.
- Y. Chen, D. Ma, S. Shen, P. Deng, Z. zhao, M. Yang, Y. Wang, H. Mi and P. Zhang, New insights into high-rate and super-stable aqueous zinc-ion batteries via the design concept of voltage and solvation environment coordinated control, Energy Storage Mater., 2023, 56, 600–610 CrossRef.
- Y. Chen, D. Ma, K. Ouyang, M. Yang, S. Shen, Y. Wang, H. Mi, L. Sun, C. He and P. Zhang, A multifunctional anti-proton electrolyte for high-rate and super-stable aqueous Zn-Vanadium oxide battery, Nano-Micro Lett., 2022, 14, 154 CrossRef CAS PubMed.
- G. Li, L. Sun, S. Zhang, C. Zhang, H. Jin, K. Davey, G. Liang, S. Liu, J. Mao and Z. Guo, Developing cathode materials for aqueous zinc ion batteries: challenges and practical prospects, Adv. Funct. Mater., 2023 DOI:10.1002/adfm.202301291.
- Y. Guo, H. Jiang, B. Liu, X. Wang, Y. Zhang, J. Sun and J. Wang, Better engineering layered vanadium oxides for aqueous zinc-ion batteries: going beyond widening the interlayer spacing, SmartMat, 2023 DOI:10.1002/smm2.1231.
- J. Liu, L. Zhan, K. Sun, K. Huang, T. Wei and C. Wang, Electrospinning preparation of a high-rate self-supported cathode for rechargeable aqueous zinc-ion batteries, Energy Fuels, 2022, 36, 13278–13285 CrossRef CAS.
- L. Zhang, X. Qin, S. Zhao, A. Wang, J. Luo, Z. L. Wang, F. Kang, Z. Lin and B. Li, Advanced matrixes for binder-free nanostructured electrodes in lithium-ion batteries, Adv. Mater., 2020, 32, 1908445 CrossRef CAS PubMed.
- W. Ma, Y. Zhang, S. Pan, Y. Cheng, Z. Shao, H. Xiang, G. Chen, L. Zhu, W. Weng, H. Bai and M. Zhu, Smart fibers for energy conversion and storage, Chem. Soc. Rev., 2021, 50, 7009–7061 RSC.
- Y. Hu, Y. Zhang, J. Zhu and Z. Niu, Rational design of continuous gradient composite films for high-performance zinc-ion batteries, Energy Storage Mater., 2022, 51, 382–390 CrossRef.
- H. Wang, S. Zhang and C. Deng, In situ encapsulating metal oxides into core-shell hierarchical hybrid fibers for flexible zinc-ion batteries toward high durability and ultrafast capability for wearable applications, ACS Appl. Mater. Interfaces, 2019, 11, 35796–35808 CrossRef CAS PubMed.
- C. Deng, S. Zhang, H. Wang and G. Zhang, “Bubble-in-nanorod” hierarchical hybrid fiber: A highly-efficient design for pyrophosphate-based freestanding cathodes towards fast sodium/lithium intercalation, Nano Energy, 2018, 49, 419–433 CrossRef CAS.
- S. Luo, L. Xie, F. Han, W. Wei, Y. Huang, H. Zhang, M. Zhu, O. G. Schmidt and L. Wang, Nanoscale parallel circuitry based on interpenetrating conductive assembly for flexible and high-power zinc ion battery, Adv. Funct. Mater., 2019, 29, 1901336 CrossRef.
- Z. Li, J. Zhang and X. W. Lou, Hollow carbon nanofibers filled with MnO2 nanosheets as efficient sulfur hosts for lithium-sulfur batteries, Angew. Chem., Int. Ed., 2015, 54, 12886–12890 CrossRef CAS PubMed.
- Y. Li, M. Chen, B. Liu, Y. Zhang, X. Liang and X. Xia, Heteroatom doping: an effective way to boost sodium ion storage, Adv. Energy Mater., 2020, 10, 2000927 CrossRef CAS.
- S. Liu, Z. Cai, J. Zhou, A. Pan and S. Liang, Nitrogen-doped TiO2 nanospheres for advanced sodium-ion battery and sodium-ion capacitor applications, J. Mater. Chem. A, 2016, 4, 18278–18283 RSC.
- X. Wu, C. Yin, M. Zhang, Y. Xie, J. Hu, R. Long, X. Wu and X. Wu, The intercalation cathode of MOFs-driven vanadium-based composite embedded in N-doped carbon for aqueous zinc ion batteries, Chem. Eng. J., 2023, 452, 139573 CrossRef CAS.
- H. Zhang, Z. Yao, D. Lan, Y. Liu, L. Ma and J. Cui, N-doped carbon/V2O3 microfibers as high-rate and ultralong-life cathode for rechargeable aqueous zinc-ion batteries, J. Alloys Compd., 2021, 861, 158560 CrossRef CAS.
- G. Yoo, B.-R. Koo, H.-R. An, C. Huang and G.-H. An, Enhanced and stabilized charge transport boosting by Fe-doping effect of V2O5 nanorod for rechargeable Zn-ion battery, J. Ind. Eng. Chem., 2021, 99, 344–351 CrossRef CAS.
- N. Xu, C. Yan, W. He, L. Xu, Z. Jiang, A. Zheng, H. Wu, M. Chen and G. Diao, Flexible electrode material of V2O5 carbon fiber cloth for enhanced zinc ion storage performance in flexible zinc-ion battery, J. Power Sources, 2022, 533, 231358 CrossRef CAS.
- A. I. Volkov, A. S. Sharlaev, O. Ya. Berezina, E. G. Tolstopjatova, L. Fu and V. V. Kondratiev, Electrospun V2O5 nanofibers as high-capacity cathode materials for zinc-ion batteries, Mater. Lett., 2022, 308, 131212 CrossRef CAS.
- X. Liu, Z. Wang, Y. Niu, C. Liu, H. Chen, X. Ren, Z. Liu, W.-M. Lau and D. Zhou, Electrospun V2O3@carbon nanofibers as a flexible and binder-free cathode for highly stable aqueous Zn-ion full batteries, ACS Appl. Energy Mater., 2022, 5, 3525–3535 CrossRef CAS.
- G. Yoo, G. H. Ryu, B.-R. Koo and G.-H. An, Interfacial defect engineering via combusted graphene in V2O5 nanochips to develop high-rate and stable zinc-ion batteries, Ceram. Int., 2021, 47, 31817–31825 CrossRef CAS.
- Y. Zhao, Y. Zhu and X. Zhang, Challenges and perspectives for manganese-based oxides for advanced aqueous zinc-ion batteries, InfoMat, 2019, 2, 237–260 CrossRef.
- Z. Zhang, W. Li, Y. Shen, R. Wang, H. Li, M. Zhou, W. Wang, K. Wang and K. Jiang, Issues and opportunities of manganese-based materials for enhanced Zn-ion storage performances, J. Energy Storage, 2022, 45, 103729 CrossRef.
- J. Yang, G. Yao, Z. Li, Y. Zhang, L. Wei, H. Niu, Q. Chen and F. Zheng, Highly flexible K-intercalated MnO2/carbon membrane for high-performance aqueous zinc-ion battery cathode, Small, 2023, 19, 2205544 CrossRef CAS PubMed.
- F. Tang, T. He, H. Zhang, X. Wu, Y. Li, F. Long, Y. Xiang, L. Zhu, J. Wu and X. Wu, The MnO@N-doped carbon composite derived from electrospinning as cathode material for aqueous zinc ion battery, J. Electroanal. Chem., 2020, 873, 114368 CrossRef CAS.
- M. Chen, S. Xie, X. Zhao, L. Peng, Y. Li, J. Zhang, M. Han, X. Liang, Q. Liu, Y. Zhang, Z. Chen and Q. Chen, Oxygen vacancies enhance H+ diffusion kinetics for a flexible and lightweight aqueous zinc/manganese monoxide battery, ACS Sustain. Chem. Eng., 2022, 10, 12188–12196 CrossRef CAS.
- M. E. Lamm, K. Li, J. Qian, L. Wang, N. Lavoine, R. Newman, D. J. Gardner, T. Li, L. Hu, A. J. Ragauskas, H. Tekinalp, V. Kunc and S. Ozcan, Recent advances in functional materials through cellulose nanofiber templating, Adv. Mater., 2021, 33, 2005538 CrossRef CAS PubMed.
- G. Liu, H. Huang, R. Bi, X. Xiao, T. Ma and L. Zhang, K+ pre-intercalated manganese dioxide with enhanced Zn2+ diffusion for high rate and durable aqueous zinc-ion batteries, J. Mater. Chem. A, 2019, 7, 20806–20812 RSC.
- L. Fang, X. Wang, W. Shi, Z. Le, H. Wang, P. Nie, T. Xu and L. Chang, Carbon nanofibers enabling manganese oxide cathode superior low temperature performance for aqueous zinc-ion batteries, J. Electroanal. Chem., 2023, 940, 117488 CrossRef CAS.
- L. Cheng, Y. Wu, S. Guo, Y. Liu, W. Li, Q. Liu, F. Mo, S. Yu, Y. Huang and J. Wei, Electrospun manganese sesquioxide as cathode for aqueous zinc ion battery with high-rate performance and long cycle life, Mater. Lett., 2022, 327, 132920 CrossRef CAS.
- T. Xu, M. Zhao, Z. Su, Z. Li, V. G. Pol and C.-T. Lo, Investigating architectured Na3V2(PO4)3/C/CNF hybrid cathode in aqueous zinc ion battery, Energy Fuels, 2021, 35, 16194–16201 CrossRef CAS.
- A. Naveed, T. Rasheed, B. Raza, J. Chen, J. Yang, N. Yanna and J. Wang, Addressing thermodynamic instability of Zn anode: classical and recent advancements, Energy Storage Mater., 2022, 44, 206–230 CrossRef.
- C. Li, X. Xie, S. Liang and J. Zhou, Issues and future perspective on zinc metal anode for rechargeable aqueous zinc-ion batteries, Energy Environ. Mater., 2020, 3, 146–159 CrossRef CAS.
- X. Zhou, R. Chen, E. Cui, Q. Liu, H. Zhang, J. Deng, N. Zhang, C. Xie, L. Xu and L. Mai, A novel hydrophobic-zincophilic bifunctional layer for stable Zn metal anodes, Energy Storage Mater., 2023, 55, 538–545 CrossRef.
- Y. Geng, L. Pan, Z. Peng, Z. Sun, H. Lin, C. Mao, L. Wang, L. Dai, H. Liu, K. Pan, X. Wu, Q. Zhang and Z. He, Electrolyte additive engineering for aqueous Zn ion batteries, Energy Storage Mater., 2022, 51, 733–755 CrossRef.
- A. Bayaguud, Y. Fu and C. Zhu, Interfacial parasitic reactions of zinc anodes in zinc ion batteries: Underestimated corrosion and hydrogen evolution reactions and their suppression strategies, J. Energy Chem., 2022, 64, 246–262 CrossRef CAS.
- Y. Yang, C. Liu, Z. Lv, H. Yang, X. Cheng, S. Zhang, M. Ye, Y. Zhang, L. Chen, J. Zhao and C. C. Li, Redistributing Zn-ion flux by interlayer ion channels in Mg-Al layered double hydroxide-based artificial solid electrolyte interface for ultra-stable and dendrite-free Zn metal anodes, Energy Storage Mater., 2021, 41, 230–239 CrossRef.
- Z. Wang, H. Chen, H. Wang, W. Huang, H. Li and F. Pan, In situ growth of a metal-organic framework-based solid electrolyte interphase for highly reversible Zn anodes, ACS Energy Lett., 2022, 7, 4168–4176 CrossRef CAS.
- Y. Yin, S. Wang, Q. Zhang, Y. Song, N. Chang, Y. Pan, H. Zhang and X. Li, Dendrite-free zinc depositioninduced by Tin-modified multifunctional 3D host for stable zinc-based flow battery, Adv. Mater., 2020, 32, 1906803 CrossRef CAS PubMed.
- C. Mao, Y. Chang, X. Zhao, X. Dong, Y. Geng, N. Zhang, L. Dai, X. Wu, L. Wang and Z. He, Functional carbon materials for high-performance Zn metal anodes, J. Energy Chem., 2022, 75, 135–153 CrossRef CAS.
- S. Yang, Y. Cheng, X. Xiao and H. Pang, Development and application of carbon fiber in batteries, Chem. Eng. J., 2020, 384, 123294 CrossRef CAS.
- S. H. Baek, Y. J. Cho, J. M. Park, P. Xiong, J. S. Yeon, H. H. Rana, J. H. Park, G. Jang, S. J. Lee and H. S. Park, Electrospun conductive carbon nanofiber hosts for stable zinc metal anode, Int. J. Energy Res., 2022, 46, 7201–7214 CrossRef CAS.
- Q. Cao, H. Gao, Y. Gao, J. Yang, C. Li, J. Pu, J. Du, J. Yang, D. Cai, Z. Pan, C. Guan and W. Huang, Regulating dendrite-free zinc deposition by 3D zincopilic nitrogen-doped vertical graphene for high-performance flexible Zn-ion batteries, Adv. Funct. Mater., 2021, 31, 2103922 CrossRef CAS.
- L. Wang, G. Fan, J. Liu, L. Zhang, M. Yu, Z. Yan and F. Cheng, Selective nitrogen doping on carbon cloth to enhance the performance of zinc anode, Chin. Chem. Lett., 2021, 32, 1095–1100 CrossRef CAS.
- B. Jiang, W. Liu, Z. Ren, R. Guo, Y. Huang, C. Xu and F. Kang, Oxygen plasma modified carbon cloth with C=O zincophilic sites as a stable host for zinc metal anodes, Front. Chem., 2022, 10, 899810 CrossRef CAS PubMed.
- H. Wang, Y. Chen, H. Yu, W. Liu, G. Kuang, L. Mei, Z. Wu, W. Wei, X. Ji, B. Qu and L. Chen, A multifunctional artificial interphase with fluorine-doped amorphous carbon layer for ultra-stable Zn anode, Adv. Funct. Mater., 2022, 32, 2205600 CrossRef CAS.
- Y. Li, Z. Tan, Y. Liang, Y. Xiao, D. Cen, Y. Liu and Y. Liang, Amine-functionalized carbon cloth host for dendrite-free Zn metal anodes, ACS Appl. Energy Mater., 2021, 4, 4482–4488 CrossRef CAS.
- F. Wan, Z. Hao, S. Wang, Y. Ni, J. Zhu, Z. Tie, S. Bi, Z. Niu and J. Chen, A universal compensation strategy to anchor polar organic molecules in bilayered hydrated vanadates for promoting aqueous zinc-ion storage, Adv. Mater., 2021, 33, 2102701 CrossRef CAS PubMed.
- T. Chen, Y. Wang, Y. Yang, F. Huang, M. Zhu, B. T. W. Ang and J. M. Xue, Heterometallic seed-mediated zinc deposition on inkjet printed silver nanoparticles toward foldable and heat-resistant zinc batteries, Adv. Funct. Mater., 2021, 31, 2101607 CrossRef CAS.
- H. Li, C. Guo, T. Zhang, P. Xue, R. Zhao, W. Zhou, W. Li, A. Elzatahry, D. Zhao and D. Chao, Hierarchical confinement effect with zincophilic and spatial traps stabilized Zn-based aqueous battery, Nano Lett., 2022, 22, 4223–4231 CrossRef CAS PubMed.
- J. Yin, Y. Wang, Y. Zhu, J. Jin, C. Chen, Y. Yuan, Z. Bayhan, N. Salah, N. A. Alhebshi, W. Zhang, U. Schwingenschlögl and H. N. Alshareef, Regulating the redox reversibility of zinc anode toward stable aqueous zinc batteries, Nano Energy, 2022, 99, 107331 CrossRef CAS.
- J.-L. Yang, P. Yang, W. Yan, J.-W. Zhao and H. J. Fan, 3D zincophilic micro-scaffold enables stable Zn deposition, Energy Storage Mater., 2022, 51, 259–265 CrossRef.
- S. Yang, Y. Li, H. Du, Y. Liu, Y. Xiang, L. Xiong, X. Wu and X. Wu, Copper nanoparticle-modified carbon nanofiber for seeded zinc deposition enables stable Zn metal anode, ACS Sustain. Chem. Eng., 2022, 10, 12630–12641 CrossRef CAS.
- Y. Song, Y. Chen, Z. Wang, W. Zhao, C. Qin, H. Yu, X. Wang, Z. Bakenov and Y. Zhang, Defective ZnOx@porous carbon nanofiber network inducing dendrite-free zinc plating as zinc metal anode for high-performance aqueous rechargeable Zn/Na4Mn9O18 battery based on hybrid electrolyte, J. Power Sources, 2022, 518, 230761 CrossRef CAS.
- J. Zheng, Z. Huang, F. Ming, Y. Zeng, B. Wei, Q. Jiang, Z. Qi, Z. Wang and H. Liang, Surface and interface engineering of Zn anodes in aqueous rechargeable Zn-ion batteries, Small, 2022, 18, 2200006 CrossRef CAS PubMed.
- F. Tao, Y. Liu, X. Ren, J. Wang, Y. Zhou, Y. Miao, F. Ren, S. Wei and J. Ma, Different surface modification methods and coating materials of zinc metal anode, J. Energy Chem., 2022, 66, 397–412 CrossRef CAS.
- L. Yuan, J. Hao, C. Kao, C. Wu, H. Liu, S. Dou and S. Qiao, Regulation methods for the Zn/electrolyte interphase and the effectiveness evaluation in aqueous Zn-ion batteries, Energy Environ. Sci., 2021, 14, 5669–5689 RSC.
- H. He, H. Qin, J. Wu, X. Chen, R. Huang, F. Shen, Z. Wu, G. Chen, S. Yin and J. Liu, Engineering interfacial layers to enable Zn metal anodes for aqueous zinc-ion batteries, Energy Storage Mater., 2021, 43, 317–336 CrossRef.
- Q. Liu, Y. Wang, X. Hong, R. Zhou, Z. Hou and B. Zhang, Elastomer-alginate interface for high-power and high-energy Zn metal anodes, Adv. Energy Mater., 2022, 12, 2200318 CrossRef CAS.
- S. Xie, Y. Li, X. Li, Y. Zhou, Z. Dang, J. Rong and L. Dong, Stable zinc anodes enabled by zincophilic Cu nanowire networks, Nano-Micro Lett., 2021, 14, 39 CrossRef PubMed.
- S. B. Singh, D. T. Tran, K. U. Jeong, N. H. Kim and J. H. Lee, A flexible and transparent zinc-nanofiber network electrode for wearable electrochromic, rechargeable Zn-ion battery, Small, 2021, 18, 2104462 CrossRef PubMed.
- S. Kumar, H. Yoon, H. Park, G. Park, S. Suh and H.-J. Kim, A dendrite-free anode for stable aqueous rechargeable zinc-ion batteries, J. Ind. Eng. Chem., 2022, 108, 321–327 CrossRef CAS.
- G. Park, H. Park, W. Seol, S. Suh, J. Y. Jo, S. Kumar and H.-J. Kim, Inhibition of zinc dendrites realized by a β-P(VDF-TrFE) nanofiber layer in aqueous Zn-ion batteries, Membranes, 2022, 12, 1014 CrossRef CAS PubMed.
- J. W. Han, B. K. Park, S. Y. Yang, J. Lee, J. Mun, J. W. Choi and K. J. Kim, Hierarchically porous ferroelectric layer with the aligned dipole moment for a high-performance aqueous Zn metal battery, ACS Appl. Mater. Interfaces, 2022, 14, 48570–48581 CrossRef CAS PubMed.
- Z. Hao, Y. Dai, X. Xu, X. Zhao, Y. Cong, X. Wu and W. Zhou, Strategies for addressing the challenges of aqueous zinc batteries enabled by functional separators, J. Mater. Chem. A, 2023, 11, 11031–11047 RSC.
- X. Li, W. Chen, Q. Qian, H. Huang, Y. Chen, Z. Wang, Q. Chen, J. Yang, J. Li and Y. W. Mai, Electrospinning-based strategies for battery materials, Adv. Energy Mater., 2020, 11, 2000845 CrossRef.
- Y. Ding, H. Hou, Y. Zhao, Z. Zhu and H. Fong, Electrospun polyimide nanofibers and their applications, Prog. Polym. Sci., 2016, 61, 67–103 CrossRef CAS.
- Y. Li, Q. Li and Z. Tan, A review of electrospun nanofiber-based separators for rechargeable lithium-ion batteries, J. Power Sources, 2019, 443, 227262 CrossRef CAS.
- Z. Shao, S. Cheng, Y. Zhang, H. Guo, X. Cui, Z. Sun, Y. Liu, Y. Wu, P. Cui, J. Fu, Q. Su and E. Xie, Wearable and fully biocompatible all-in-one structured “paper-like” zinc ion battery, ACS Appl. Mater. Interfaces, 2021, 13, 34349–34356 CrossRef CAS PubMed.
- S. Saisangtham, C. Likitaporn, P. Kasemsiri, J. Qin, M. Okhawilai, P. Potiyaraj and H. Uyama, Polyacrylonitrile/bio-based polyurethane electrospun fiber mats as advanced separators for high-performance Zn-ion batteries, eXPRESS Polym. Lett., 2022, 16, 827–845 CrossRef CAS.
- X. Wang, F. Wang, L. Wang, M. Li, Y. Wang, B. Chen, Y. Zhu, L. Fu, L. Zha, L. Zhang, Y. Wu and W. Huang, An aqueous rechargeable Zn//Co3O4 battery with high energy density and good cycling behavior, Adv. Mater., 2016, 28, 4904–4911 CrossRef CAS PubMed.
- C. Likitaporn, M. Okhawilai, P. Kasemsiri, J. Qin, P. Potiyaraj and H. Uyama, High electrolyte uptake of MXene integrated membrane separators for Zn-ion batteries, Sci. Rep., 2022, 12, 19915 CrossRef CAS PubMed.
- W. Hu, J. Ju, Y. Zhang, W. Tan, N. Deng, W. Liu, W. Kang and B. Cheng, Deposition behavior regulated by an SPSF@PMIA nanofiber separator for high-performance zinc ion batteries, J. Mater. Chem. A, 2022, 10, 24761–24771 RSC.
- H. Zhao, N. Deng, G. Wang, H. Ren, W. Kang and B. Cheng, A core@sheath nanofiber separator with combined hardness and softness for lithium-metal batteries, Chem. Eng. J., 2021, 404, 126542 CrossRef CAS.
|
This journal is © The Royal Society of Chemistry 2023 |
Click here to see how this site uses Cookies. View our privacy policy here.