Insights into the catalytic potential of a rationally designed magnetic boron nitride nanosheet supported nickel catalyst for the efficient synthesis of 1,4-dihydropyridines†
Received
20th June 2022
, Accepted 23rd September 2022
First published on 14th October 2022
Abstract
Considering the unprecedented attributes of two-dimensional nanomaterials, the present report discloses the fabrication of a novel magnetic boron nitride nanosheet based nickel nanocatalyst (h-BN@Fe3O4@APTES@TPC@Ni) through a covalent bonding approach. In order to certify the successful synthesis of the catalyst, various advanced microscopic and spectroscopic techniques, including TEM, SEM, FT-IR, XRD, EDS, ED-XRF and VSM, were employed. The developed h-BN@Fe3O4@APTES@TPC@Ni catalytic agent acts as a promising candidate to deliver various pharmaceutically relevant 1,4-dihydropyridine scaffolds using aryl aldehydes, dimedone, ethyl acetoacetate and ammonium acetate as reacting species. The devised methodology is accompanied with noteworthy benefits, including mild reaction conditions, wide substrate scope, excellent products yield and short reaction time. Besides this, facile magnetic retrievability and remarkable reusability of the catalyst for six successive runs without any appreciable loss in catalytic efficacy are the additional factors that make this protocol worthwhile.
Introduction
With the rapid advancements in modern materials science, substantial efforts by researchers have been devoted towards the rational design of highly tunable nanomaterials and their applicability in the realm of catalysis. In consideration of the dynamic aspects of heterogeneous catalytic systems, two-dimensional nanomaterials, especially hexagonal boron nitride (h-BN) layered nanostructures, have garnered extensive interest as solid supports owing to their exceptional attributes, such as high surface area to volume ratio; excellent thermal, chemical and mechanical strength; nanometer size; high oxidative resistance; coordinatively unsaturated active sites; and capability of dissipating substantial heat in exothermic reactions.1–11 Further, the catalytic characteristics of boron nitride nanosheets can be enhanced via immobilizing numerous active sites with organic–inorganic functionalities on them through a covalent approach. In addition, integration of h-BN nanosheets with magnetite nanoparticles further enhances their separation from the reaction media using a readily available external magnet, which represents a better separating technique than its energy consuming counterparts.12–17 Taking into account the salient attributes offered by atomically thin 2D h-BN, we herein designed a magnetically responsive h-BN nanostructured based nickel nanocatalyst and examined its catalytic performance in the one-pot multicomponent synthesis of highly privileged heterocyclic compounds, namely 1,4 dihydropyrimidines. These Hantzsch derived synthons exhibit various pharmacological activities, such as anti-inflammatory, antimicrobial, antihypertensive, anti-tumor, anti-diabetic, and cyclooxygenase-2 inhibitor properties.18–21 For instance, nifedipine, amlodipine and nicardipine exhibit calcium channel blocking properties that are used to treat hypertension by relaxing cardiac muscle contraction.22 In relevance to aforementioned activities, some of the biologically active molecules bearing 1,4-dihydropyridine moieties are displayed in Fig. 1. To date, several synthetic approaches for the synthesis of polyhydroquinolines have been reported but due to considerable shortcomings manifested by these protocols, such as prolonged reaction times, acidic or basic conditions, tedious experimental procedures, use of expensive metal salts, etc.,23–32 we focused our research towards the development of an alternative milder strategy via designing a magnetically incorporated h-BN nanosheet based catalytic system that surpasses the aforesaid issues remarkably. Impressed by the immense benefits governed by surface engineered h-BN nanocomposites and our on-going laboratory work,33–41 we herein demonstrate the fabrication of a novel h-BN@Fe3O4@APTES@TPC@Ni catalyst and its utility in the multicomponent coupling of aldehydes, dimedone, ethyl acetoacetate and ammonium acetate to access the respective 1,4-dihydropyridines of biological importance. Such recyclable heterogeneous supported nanocatalysts have been grabbing the attention of the scientific community for years to deliver diverse heterocyclic organic products at the industrial scale.42–49 However, to the best of our knowledge, this is the first report that presents the catalytic significance of a h-BN@Fe3O4@APTES@TPC@Ni nanomaterial in accomplishing the concerned reactions.
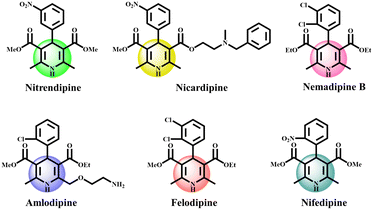 |
| Fig. 1 Structures of bioactive 1,4-dihydropyridines. | |
Experimental
Materials and reagents
Boron nitride micropowder and 3-methylthiophene-2-carboxaldehyde were purchased from Alfa Aesar. (3-Aminopropyl) triethoxysilane was purchased from Sigma-Aldrich. Anhydrous sodium sulphate, ethyl acetate and ethanol were procured from Merck. All other reagents including nickel chloride were of high purity and purchased from Spectrochem Pvt. Ltd.
Instrumentation
Fourier-transform infrared (FT-IR) spectroscopy was employed to confirm the rationally designed organic–inorganic hybrid nanocomposites via determining various functionalities. The spectra were recorded on a Bruker Alpha spectrometer using the KBr pellet method in the range of 4000–400 cm−1. The crystallographic structure of the synthesized nanocomposites was investigated by conducting powder X-ray diffraction (PXRD) measurements using a Rigaku XRD Miniflex 600/600-C diffractometer over a 2θ range of 20–80° (λ = 0.15405 nm, 40 kV, 40 mA) at a scan rate of 5° min−1. To gain insight into the structure and morphology of the nanocomposites, scanning electron microscopy (SEM) images were captured using a Jeol scanning electron microscope. The elemental composition of the catalyst was determined via an SEM coupled EDS technique. The size of the developed nanocomposites was recorded on a Thermo Scientific Talos instrument. Energy-dispersive X-ray fluorescence (ED-XRF) spectroscopy was conducted using a Fischerscope X-ray XAN-FAD BC spectrometer to elucidate the presence of metal in the catalyst. The magnetic properties of pristine as well as surface engineered nanocomposites were analyzed using vibrating sample magnetometry (VSM, EV-9, Microsense, ADE) by magnetic field sweeping between −10
000 and +10
000 Oe. To quantify the nickel content present in the catalyst, flame atomic absorption spectroscopy (model no. N3180021 PinAAcle 500) was used. The one-pot synthesis of a library of 1,4-dihydropyridines was confirmed through analyzing 1H and 13C nuclear magnetic resonance (NMR) spectra in CDCl3, which were recorded using a JEOL JNM-EXCP-400 spectrophotometer.
Preparation of h-BN nanosheets.
Hydroxyl incorporated boron nitride nanosheets were fabricated through an ion-assisted liquid exfoliation approach.50 In a typical procedure, a finely ground homogeneous mixture of sodium hydroxide (2.84 g), potassium hydroxide (2.16 g) and h-BN micropowder (1.0 g) was prepared with subsequent transfer into a Teflon-lined stainless steel autoclave and heated at 180 °C for 2 h. Thereafter, the resultant mixture was allowed to cool to room temperature and was dispersed in deionized water under sonication for an appropriate time period. The nanosheets were then separated via centrifugation, washed thoroughly with deionized water and dried under vacuum.
Preparation of the magnetic h-BN nanosheets (h-BN@Fe3O4).
Prior to the preparation of h-BN@Fe3O4, the synthesized h-BN nanosheets (0.1 g) were well dispersed in ethylene glycol (30 mL) under sonication. Subsequently, ferric chloride (0.5 g) was added into the solution and stirred at 50 °C followed by the addition of sodium acetate (2.0 g) and polyethylene glycol-6000 (1.0 g). The reaction was continued for half an hour so as to prepare a homogeneous mixture. Thereafter, the mixture was transferred into an autoclave and heated at 200 °C for 16 h.51 After completion of the reaction, the resultant h-BN@Fe3O4 nanocomposite was collected using an external magnet and washed thoroughly in ethanol. The obtained material was then dried well in an oven.
Preparation of amine functionalized magnetic h-BN nanosheets (h-BN@Fe3O4@APTES).
The preparation of h-BN@Fe3O4@APTES was accomplished with the addition of 3-aminopropyltriethoxysilane (1 mmol) to a solution of ethanol (50 mL) under sonication. The APTES incorporated solution was then subjected to reflux conditions for 6 h. The nanoparticles so obtained were magnetically separated from the reaction media, washed with ethanol and kept under vacuum for drying purposes.
Preparation of the magnetic h-BN nanosheet supported nickel catalyst (h-BN@Fe3O4@APTES@TPC@Ni).
Initially, the ligand immobilized magnetic nanosheets (h-BN@Fe3O4@APTES@TPC) were developed by introducing 3-methylthiophene-2-carboxaldehyde into an ethanolic solution of h-BN@Fe3O4@APTES under reflux conditions for 6 h. Once the reaction was completed, the nanomaterial was recovered via external magnetic force followed by being washed several times with ethanol and drying overnight. Finally, the desired h-BN@Fe3O4@APTES@TPC@Ni catalyst was synthesized when an ethanolic solution of h-BN@Fe3O4@APTES@TPC and NiCl2·6H2O were allowed to react under constant stirring at room temperature for a time period of 12 h. Afterwards, the catalyst was magnetically separated, with successive washings in ethanol, before being dried in an oven.
General procedure involved in the synthesis of 1,4-dihydropyridine using the h-BN@Fe3O4@APTES@TPC@Ni catalyst.
In order to accomplish the one-pot multicomponent condensation reaction, a mixture of benzaldehyde (1 mmol), dimedone (1 mmol), ethylacetoacetate (1 mmol), ammonium acetate (2 mmol) and h-BN@Fe3O4@APTES@TPC@Ni in DMF was stirred at 60 °C for 45 min. Once the reaction completed, the resulting mixture was allowed to cool to room temperature, with subsequent removal of the catalyst magnetically. Thereafter, the crude mixture was extracted using ethyl acetate followed by separation of the combined organic layer. The product was then dried over anhydrous sodium sulphate and recrystallized with ethanol. The obtained product was analyzed using NMR spectroscopy.
Results and discussion
The h-BN@Fe3O4@APTES@TPC@Ni catalyst was synthesized in a stepwise manner, as shown in Scheme 1. Initially, h-BN@OH nanosheets were fabricated via an ion-assisted liquid exfoliation approach, wherein a mixture of h-BN, NaOH and KOH was heated in a muffle furnace followed by ultrasonication in deionized water. Further, the ethylene glycol mediated synthesis of magnetite decorated nanosheets was accomplished via a solvothermal approach, where a homogeneous mixture of h-BN nanosheets, FeCl3, NaOAc, PEG-6000 and EG was transferred into an autoclave. In the successive step, ferrite coated h-BN nanosheets were functionalized with 3-aminopropyl triethoxysilane to provide an amine terminated nanostructure. The synthesized h-BN@Fe3O4@APTES nanocomposite was then covalently linked to the ligand through imine bond formation to deliver h-BN@Fe3O4@APTES@TPC followed by metalation to produce the desired h-BN@Fe3O4@APTES@TPC@Ni nanocatalyst. The fabricated catalyst thus obtained was analyzed using various reliable physicochemical techniques, including SEM, TEM, EDS, ED-XRF, FT-IR, XRD and VSM.
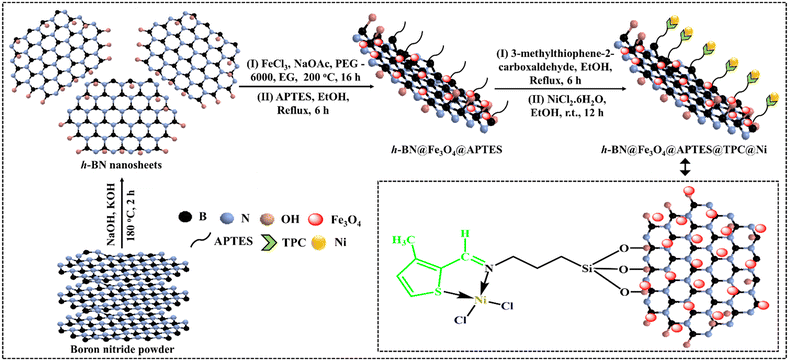 |
| Scheme 1 Schematic representation of the synthesis of the h-BN@Fe3O4@APTES@TPC@Ni catalytic system. | |
Catalyst characterization
Shape, size, and morphology analysis.
To study the morphological and structural characteristics of the designed h-BN, h-BN@Fe3O4 and h-BN@Fe3O4@APTES@TPC@Ni nanostructures, SEM and TEM analysis were carried out, as shown in Fig. 2. The SEM micrograph of exfoliated h-BN shows a laminated morphology with folded edges and a smooth surface. Moving to the h-BN@Fe3O4 nanocomposites shown in Fig. 2b, spherical ferrite nanoparticles were uniformly dispersed on the h-BN surface. In the case of h-BN@Fe3O4@APTES@TPC@Ni, no noticeable morphological changes were observed aside from surface roughening of the h-BN nanosheets and slight agglomeration of the ferrite nanoparticles. Besides this, the TEM image of h-BN reveals ultrathin sheets of 4–7 nm in thickness on average. Fig. 2e shows additional information about the size of the magnetite nanoparticles, which was found to be 200 nm. Furthermore, an increase in the size of Fe3O4 to 253 nm in the h-BN@Fe3O4@APTES@TPC@Ni catalytic system strongly justifies the fact that organic functionalities along with the linker and metallic moieties were immobilized onto its surface.
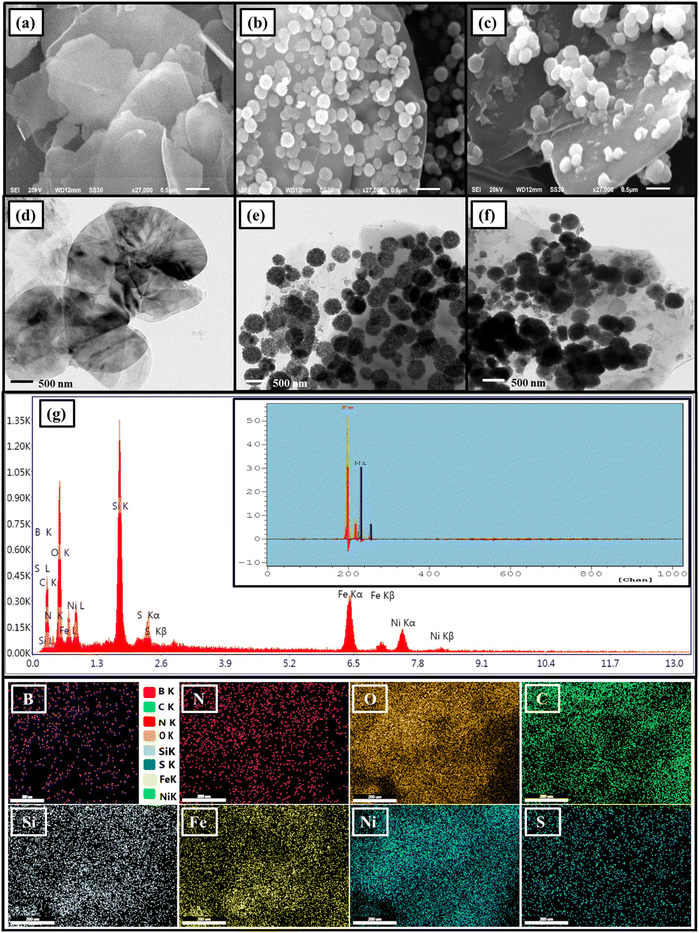 |
| Fig. 2 SEM of (a) h-BN, (b) h-BN@Fe3O4 and (c) h-BN@Fe3O4@APTES@TPC@Ni, TEM of (d) h-BN, (e) h-BN@Fe3O4 and (f) h-BN@Fe3O4@APTES@TPC@Ni, (g) EDS, inset: Corresponding ED-XRF spectra and elemental mapping analysis of h-BN@Fe3O4@APTES@TPC@Ni showing B, N, O, C, Si, Fe, Ni and S elements. | |
Compositional analysis.
The semi-quantitative estimation of the prepared h-BN@Fe3O4@APTES@TPC@Ni catalyst was carried out using SEM equipped EDS technique, as shown in Fig. 2g. The EDS spectrum of h-BN@Fe3O4@APTES@TPC@Ni reveals the existence of B, N, O, Fe, Si, C, S and Ni elements, which authenticates the successful synthesis of a catalytic entity via the covalent grafting of a nickel complex onto a magnetite decorated amine functionalized h-BN nanostructure. To further corroborate the presence of nickel as well as iron in the catalyst, ED-XRF analysis was employed, as can be seen in the inset in Fig. 2g. Additionally, mapping images also endorsed the homogeneous distribution of the respective elements. Furthermore, quantitation of nickel in h-BN@Fe3O4@APTES@TPC@Ni was determined by atomic absorption spectroscopy (AAS) and found to be 0.1021 mmol g−1.
Surface analysis.
The specific surface area of the h-BN@Fe3O4@APTES@TPC@Ni catalyst was determined through BET analysis involving the physical adsorption of nitrogen gas at a temperature of 77 K. Fig. 3a delineates a hysteresis loop, which elucidates that h-BN exists in a layered structure. The specific surface area and pore volume of the catalyst were found to be 21.76 m2 g−1 and 0.0585 cc g−1, respectively. Besides this, NH3-temperature programmed desorption (NH3-TPD) was also conducted to determine the acidic strength of the catalyst. Fig. 4 shows a peak centered at 309 °C, which could be ascribed to the desorption of NH3 by medium acidic sites. Such high temperature desorption represents strong bonding of NH3 with B–O acidic sites in the BN supported catalyst.
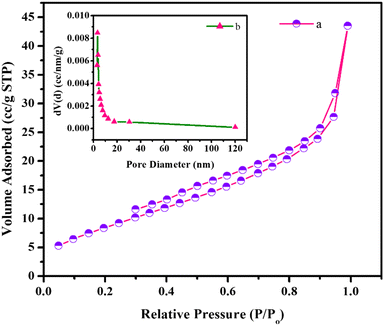 |
| Fig. 3 (a) Nitrogen adsorption–desorption isotherm and (b) corresponding pore size distribution (inset) curve of h-BN@Fe3O4@APTES@TPC@Ni. | |
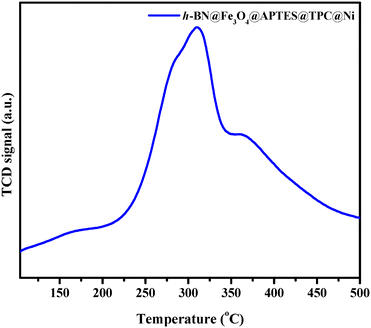 |
| Fig. 4 NH3-TPD pattern of h-BN@Fe3O4@APTES@TPC@Ni. | |
Phase and structural determination.
The crystallographic structure of the stepwise synthesized h-BN, h-BN@Fe3O4, h-BN@Fe3O4@APTES, h-BN@Fe3O4@APTES@TPC and h-BN@Fe3O4@APTES@TPC@Ni nanocomposites were analysed by PXRD, as shown in Fig. 5. The PXRD pattern of the h-BN nanosheets exhibiting hydroxyl groups at the edges reveals five Bragg's diffraction peaks centered at 2θ = 26.9°, 41.6°, 43.8°, 50.0° and 55.1° corresponding to the (002), (100), (101), (102) and (004) crystal planes, respectively (JCPDS card no. 34-0421).52 However, the peaks positioned at (100), (101), (102) and (004) planes are of lower intensity compared to the (002) plane. The detailed pattern of h-BN@Fe3O4 shows four additional peaks at 2θ = 30.20°, 35.53°, 57.31° and 62.87°, attributed to the (220), (311), (511) and (440) planes, respectively, which are in good agreement with the cubic inverse spinel structure of magnetite nanoparticles (JCPDS card no. 19-0629).53 In the case of the h-BN@Fe3O4@APTES, h-BN@Fe3O4@APTES@TPC and h-BN@Fe3O4@APTES@TPC@Ni pattern, similar peaks to those of the h-BN@Fe3O4 pattern are attained, which indicates that the structural integrity remains unaltered even after surface engineering and metalation.
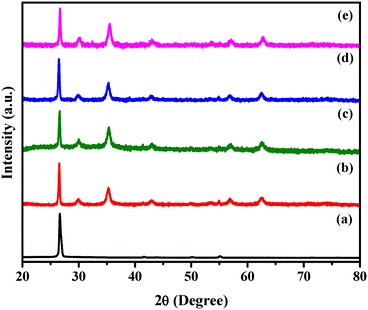 |
| Fig. 5 XRD patterns of (a) h-BN, (b) h-BN@Fe3O4, (c) h-BN@Fe3O4@APTES, (d) h-BN@Fe3O4@APTES@TPC and (e) h-BN@Fe3O4@APTES@TPC@Ni. | |
Functional group analysis.
The presence of covalently linked functionalities onto the ferrite decorated h-BN surface was confirmed by FT-IR spectroscopy analysis, as displayed in Fig. 6. The appearance of two sharp peaks at 1377 and 822 cm−1 in the case of bare h-BN corroborates the existence of B–N stretching and B–N–B bending vibrations, respectively.54 In addition, an additional broad band at 3622 cm−1 authenticates the essence of hydroxyl groups at the smooth edges of h-BN nanosheets. The spectrum of h-BN@Fe3O4 shows a new peak at 588 cm−1 which can be attributed to the stretching vibration of Fe–O bonds.55 Further, in the spectrum of h-BN@Fe3O4@APTES the occurrence of two more characteristic peaks at 1144 and 1033 cm−1 corresponds to the Si–O asymmetric and symmetric mode of the vibrations of organosilane moieties, respectively.56,57 In addition, the emergence of a peak at 2911 cm−1 can be assigned to the –CH2 groups and the peak at 1588 cm−1 is attributed to the –NH2 species, which further affirms the synthesis of the h-BN@Fe3O4@APTES nanocomposite. However, in the case of ligand grafting (h-BN@Fe3O4@APTES@TPC) and metalation (h-BN@Fe3O4@APTES@TPC@Ni), the peak for imine bond formation due to Schiff's condensation is not visible as the peak is concealed under broad B–N bands.58
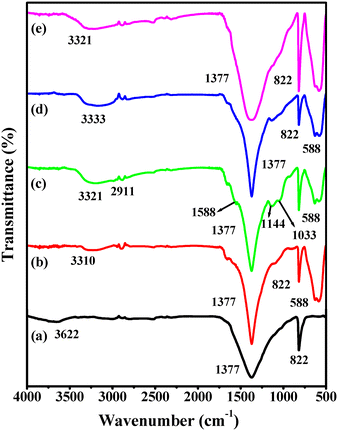 |
| Fig. 6 FT-IR spectra of (a) h-BN, (b) h-BN@Fe3O4, (c) h-BN@Fe3O4@APTES, (d) h-BN@Fe3O4@APTES@TPC and (e) h-BN@Fe3O4@APTES@TPC@Ni. | |
Magnetic properties analysis.
To gain insight into the magnetic properties of the fabricated h-BN, h-BN@Fe3O4, h-BN@Fe3O4@APTES, h-BN@Fe3O4@APTES@TPC and h-BN@Fe3O4@APTES@TPC@Ni nanocomposites, vibrating sample magnetometry analysis was employed with magnetic field sweeping between −10
000 and +10
000 Oe. The well exfoliated h-BN nanosheets show non-magnetic properties, as is evident from the linear curve exhibiting no saturation magnetization (Ms) (Fig. 7). Upon integration with ferrite nanoparticles (h-BN@Fe3O4), superparamagnetic behavior with Ms 46.1 emu g−1 is observed that further dropped to 38.4 emu g−1 upon the covalent anchoring of organosilane motifs (h-BN@Fe3O4@APTES). The Ms value further decreased to 32.7 and 25.6 emu g−1 in the case of h-BN@Fe3O4@APTES@TPC and h-BN@Fe3O4@APTES@TPC@Ni, respectively. However, it is interesting to note that despite the low Ms value of the catalyst, the net magnetization was sufficient to facilitate its easy recovery from the reaction media via conventional external magnetic force. Besides this, the magnetization curves exhibit no remanence (Mr, emu g−1) and coercivity (Hc, Oe), thus highly favouring the superparamagnetic characteristics of the synthesized nanocomposites.
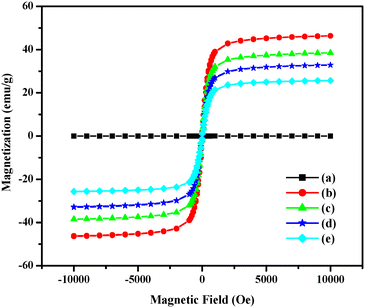 |
| Fig. 7 Magnetization curves of (a) h-BN, (b) h-BN@Fe3O4, (c) h-BN@Fe3O4@APTES, (d) h-BN@Fe3O4@APTES@TPC and (e) h-BN@Fe3O4@APTES@TPC@Ni. | |
TGA and DSC analysis.
To determine the thermal stability behaviour of h-BN@Fe3O4, h-BN@Fe3O4@APTES, h-BN@Fe3O4@APTES@TPC and h-BN@Fe3O4@APTES@TPC@Ni, TGA was conducted under a N2 atmosphere at a heating rate of 10 °C min−1 and the results are outlined in Fig. 8a. The thermogram curve of h-BN@Fe3O4 shows a gradual decrease in weight up to 175 °C, which is attributed to the removal of the surface hydroxyl groups of ferrite nanoparticles. Furthermore, the weight loss from 200 to 300 °C corresponds to the degradation of organic moieties present in h-BN@Fe3O4@APTES and h-BN@Fe3O4@APTES@TPC, respectively. Moreover, continuous weight loss is observed for h-BN@Fe3O4@APTES@TPC@Ni, which represents its complete decomposition. Besides this, differential scanning calorimetry (DSC) measurements were also conducted in a N2 flow (50 mL min−1) to study the heat flow as a function of temperature, which arises due to physical or chemical procedures. Fig. 8b illustrates a peak shift from 56 °C towards higher temperature after the surface modification of h-BN, which further confirms its strong adhesion with the organic–inorganic hybrid functionalities.
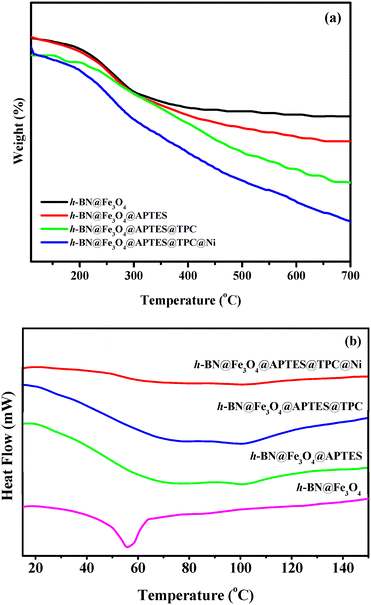 |
| Fig. 8 (a) TGA and (b) DSC curves of h-BN@Fe3O4, h-BN@Fe3O4@APTES, h-BN@Fe3O4@APTES@TPC and h-BN@Fe3O4@APTES@TPC@Ni. | |
Catalytic evaluation.
The catalytic performance of a newly designed h-BN@Fe3O4@APTES@TPC@Ni catalyst was investigated in the one-pot multicomponent condensation reaction to access 1,4-dihydropyridines. To facilitate the reaction, control experiments were performed using dimedone (1 mmol), benzaldehyde (1 mmol), ethyl acetoacetate (1 mmol) and ammonium acetate (2 mmol) as the reacting species. Initially, a catalyst free approach was studied which resulted in a trace yield of the product (entry 1, Table 1) and thus it is worth mentioning that the use of catalyst is highly important to accelerate the reaction. Maximum product yield was attained when the amount of catalyst was increased up to 15 mg (entry 3, Table 1). In order to further refine the reaction parameters, the effect of different solvents such as DMF, water, ethanol and acetonitrile on the product yield was studied and the best results were obtained in the case of DMF (entries 2, 3, 8 and 11, Table 1). However, the reaction was also carried out under a solvent free approach, but a trace product yield was obtained (entry 7, Table 1). Furthermore, temperature played a prominent role in promoting the reaction, as can be seen from the results summarized in Table 1 (entries 3, 8 and 9). Lowering of temperature to 50 °C and 30 °C slowed down the rate of formation of the targeted product as the product yields were not satisfactory (entries 8 and 9, Table 1). In addition, variation in product yields was achieved by varying the time interval from 30–60 min (entries 3, 10 and 11, Table 1) and it was observed that 45 min is the optimum time for carrying out the reaction towards maximum yield. Taking into consideration the optimized reaction profile, we went further to evaluate the performance of precursors obtained during h-BN@Fe3O4@APTES@TPC@Ni synthesis and it was found that no noticeable yield was acquired in any of the cases (entries 12–15, Table 1).
Table 1 Optimization of the reaction parameters of the synthesis of 1,4-dihydropyridinea
S. no |
Catalyst (mg) |
Solvent (mL) |
Temp. (°C) |
Time (min) |
Yield (%) |
Reaction conditions: benzaldehyde (1 mmol), dimedone (1 mmol), ethyl acetoacetate (1 mmol), ammonium acetate (2 mmol), catalyst (x mg), solvent (2 mL).
|
1. |
— |
DMF |
60 |
45 |
Trace |
2. |
h-BN@Fe3O4@APTES@TPC@Ni (10 mg) |
DMF |
60 |
45 |
88 |
3. |
h-BN@Fe3O4@APTES@TPC@Ni (15 mg) |
DMF |
60 |
45 |
97 |
4. |
h-BN@Fe3O4@APTES@TPC@Ni (15 mg) |
H2O |
60 |
45 |
Trace |
5. |
h-BN@Fe3O4@APTES@TPC@Ni (15 mg) |
EtOH |
60 |
45 |
72 |
6. |
h-BN@Fe3O4@APTES@TPC@Ni (15 mg) |
CH3CN |
60 |
45 |
48 |
7. |
h-BN@Fe3O4@APTES@TPC@Ni (15 mg) |
Solvent-free |
60 |
45 |
Trace |
8. |
h-BN@Fe3O4@APTES@TPC@Ni (15 mg) |
DMF |
50 |
45 |
83 |
9. |
h-BN@Fe3O4@APTES@TPC@Ni (15 mg) |
DMF |
30 |
45 |
Trace |
10. |
h-BN@Fe3O4@APTES@TPC@Ni (15 mg) |
DMF |
60 |
30 |
64 |
11. |
h-BN@Fe3O4@APTES@TPC@Ni (15 mg) |
DMF |
60 |
60 |
97 |
12. |
h-BN@Fe3O4@APTES@TPC (15 mg) |
DMF |
60 |
45 |
Trace |
13. |
h-BN@Fe3O4@APTES (15 mg) |
DMF |
60 |
45 |
Trace |
14. |
h-BN@Fe3O4 (15 mg) |
DMF |
60 |
45 |
Trace |
15. |
h-BN (15 mg) |
DMF |
60 |
45 |
Trace |
Scope and generality of the protocol
After investigating the optimum reaction conditions, a series of 1,4-dihydropyridines were synthesized using aryl aldehydes, dimedone, ethyl acetoacetate and ammonium acetate as reactants, with the results outlined in Fig. 9.
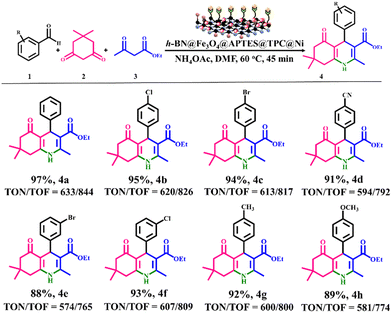 |
| Fig. 9 Catalytic efficacy of h-BN@Fe3O4@APTES@TPC@Ni in the synthesis of a variety of 1,4-dihydropyridines. Reaction conditions: arylaldehyde (1 mmol), dimedone (1 mmol), ethyl acetoacetate (1 mmol), ammonium acetate (2 mmol), catalyst (15 mg), DMF (2 mL), 60 °C, 45 min. | |
It was observed that the reactions occurred smoothly and delivered the desired products in good to excellent yields in both the cases of benzaldehydes possessing electron-withdrawing and electron-donating substituents. The formation of all the corresponding products was evidenced through 1H and 13C NMR analysis.
Mechanistic approach
A sequential mechanistic pathway attributed to the formation of 1,4-dihydropyridines is outlined in Scheme 2. The reaction occurs with the activation of both aryl aldehyde and dimedone to generate an electrophile and nucleophile, which further react together to form Knoevenagel intermediate A. Thereafter, intermediate A undergoes Michael addition with a β-dicarbonyl ester enolate to produce intermediate B, which on subsequent addition of ammonium acetate gives intermediate C. Further, the intramolecular cyclization of intermediate C provides the desired 1,4-DHP with loss of a water molecule and regeneration of the catalytic moiety.
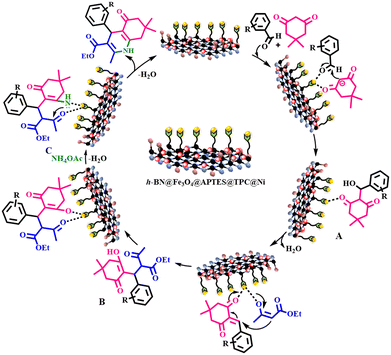 |
| Scheme 2 Illustration of a plausible mechanistic pathway catalyzed by h-BN@Fe3O4@APTES@TPC@Ni for the synthesis of 1,4-dihydropyridines. | |
A comparative study of h-BN@Fe3O4@APTES@TPC@Ni activity with the literature reports
Various competitive homogeneous and heterogeneous catalytic systems for the one-pot multicomponent synthesis of 1,4-dihydropyridines have been reported to date. However, some of the protocols face crucial challenges that need to be addressed. In this regard, the present study shows remarkable advantages over previously published reports, as presented in Table 2. High product yield, short reaction time, magnetic separability and recyclability up to six consecutive runs are the fascinating attributes of this strategy that make the protocol economically viable and operationally facile. To the best of our knowledge, this is the first ever report that discloses the synthetic route to a h-BN@Fe3O4@APTES@TPC@Ni catalyst and details its utility in promoting the concerned reaction.
Table 2 Comparison of the catalytic activity of the h-BN@Fe3O4@APTES@TPC@Ni nanocatalyst with literature precedents for the synthesis of 1,4-dihydropyridines
S. no |
Catalyst and catalyst amount |
Conditions |
Yield (%) |
Ref. |
1. |
Yb(OTf)3, 5 mol% |
EtOH, r.t., 5 h |
90 |
23
|
2. |
Sc(OTf)3, 5 mol% |
EtOH, r.t., 4 h |
93 |
24
|
3. |
ZnO, 10 mol% |
EtOH, 80 °C, 1 h |
92 |
25
|
4. |
La2O3, 10 mol% |
TFE, r.t., 1–1.5 h |
89 |
26
|
5. |
BiBr3, 2 mol% |
EtOH, r.t., 1.5 h |
86 |
27
|
6. |
h-BN@Fe3O4@APTES@TPC@Ni, 15 mg |
DMF, 60 °C, 45 min |
97 |
This study |
Heterogeneity tests
A leaching experiment was conducted to determine the stability of the synthesized magnetic h-BN nanosheet supported nickel catalyst. Keeping the reaction parameters the same, the model reaction was catalyzed by h-BN@Fe3O4@APTES@TPC@Ni. After 30 min of the reaction, the catalyst was removed from the reaction mixture using an external magnet and the yield of the product was found to be 64%. Thereafter, the reaction was continued for an additional 30 min and the results revealed no significant increase in yield, thus justifying that leaching of the active metallic species was prevented during the course of the reaction.
Recyclability tests
To commence the recyclability tests, a model reaction was monitored under the optimal reaction profile. After completion of the reaction, the catalyst was simply retrieved by means of an external magnet, washed with ethanol, dried in an oven and further reused for successive runs. It was observed that h-BN@Fe3O4@APTES@TPC@Ni exhibited remarkable catalytic potential for up to six subsequent runs with no appreciable loss in its activity, as displayed in Fig. 10.
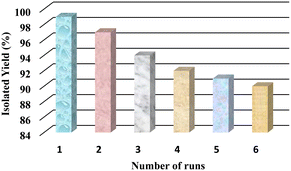 |
| Fig. 10 Recyclability experiment for the synthesis of 1,4-dihydropyridine [reaction conditions: benzaldehyde (1 mmol), dimedone (1 mmol), ethyl acetoacetate (1 mmol), ammonium acetate (2 mmol), h-BN@Fe3O4@APTES@TPC@Ni (15 mg), DMF (2 mL), 60 °C, 45 min]. | |
In addition, SEM, XRD and VSM spectra of the recovered catalyst were compared with the data of the fresh sample, which showed no morphological, crystalline and magnetization changes, respectively (Fig. S1 and S2†), thus providing strong evidence of the excellent durability and stability of the catalyst.
Conclusions
In summary, a novel and highly robust magnetically integrated ultrathin h-BN nanosheet based nickel nanocatalyst was fabricated and further exploited in the multicomponent reaction of arylaldehydes, dimedone, ethyl acetoacetate and ammonium acetate to access 1,4-dihydropyridines of biological interest. The developed h-BN@Fe3O4@APTES@TPC@Ni catalyst allied with mild reaction conditions manifests a sustainable approach towards successfully transforming the substrates to desired products in good to excellent yields. Besides this, short reaction times, facile recovery and good recyclability of the catalyst are the additional merits that make the protocol highly desirable. Moreover, the anchoring of ferrite nanoparticles onto the surface of atomically thin h-BN nanosheets not only facilitates magnetic separation of the catalyst but also enhances the active centres for immobilizing organic–inorganic functionalities. Hence, the present work demonstrates the inevitable benefits of the magnetic h-BN@Fe3O4@APTES@TPC@Ni nanocatalyst and will hopefully enlighten forthcoming generations to formulate such sustainable catalysts that would be highly beneficial to furnish massive organic motifs of industrial significance.
Conflicts of interest
There are no conflicts to declare.
Acknowledgements
The authors, Pooja Rana, Sneha Yadav, Bhavya Arora and Priyanka acknowledge CSIR and UGC New Delhi, India for the award of research fellowship. Authors also thank USIC-CLF, DU for XRD, SEM, FTIR analysis and AIIMS for TEM analysis.
References
- A. P. Farkas, Á. Szitás, D. Jurdi, K. Palotás, J. Kiss and Z. Kónya, Appl. Catal., A, 2020, 592, 117440 CrossRef CAS.
- A. Takagaki, S. Nakamura, M. Watanabe, Y. Kim, J. T. Song, K. Jimura and T. Ishihara, Appl. Catal., A, 2020, 608, 117843 CrossRef CAS.
- G. Bharath, K. Rambabu, A. Hai, F. Banat, S. Rajendran, D. D. Dionysiou and P. L. Show, Fuel, 2021, 290, 119826 CrossRef CAS.
- R. Sang, X. Cheng, W. Li, P. Luo, Y. Zhang, R. Nie and Y. Wu, Chem. Res. Chin. Univ., 2017, 33, 811–815 CrossRef CAS.
- Q. Weng, X. Wang, X. Wang, Y. Bando and D. Golberg, Chem. Soc. Rev., 2016, 45, 3989–4012 RSC.
- L. Wang, Y. Wang, C. W. Zhang, J. Wen, X. Weng and L. Shi, Catal. Sci. Technol., 2020, 10, 1248–1255 RSC.
- Z. Cao, J. Bu, Z. Zhong, C. Sun, Q. Zhang, J. Wang and X. Xie, Appl. Catal., A, 2019, 578, 105–115 CrossRef CAS.
- B. Liu, S. Yan, A. Zhang, Z. Song, Q. Sun, B. Huo and J. Liu, ChemNanoMat, 2019, 5, 784–791 CrossRef CAS.
- A. K. Roy, S. Y. Park and I. In, Nanotechnol., 2015, 26, 105601 CrossRef PubMed.
- R. Nie, R. Sang, X. Ma, Y. Zheng, X. Cheng, W. Li and Y. Wu, J. Catal., 2016, 344, 286–292 CrossRef CAS.
- N. Lv, L. Sun, L. Chen, Y. Li, J. Zhang, P. Wu and H. Li, Phys. Chem. Chem. Phys., 2019, 21, 21867–21874 RSC.
- A. S. Konopatsky, K. L. Firestein, N. D. Evdokimenko, A. L. Kustov, V. S. Baidyshev, V. C. Il'ya and D. V. Shtansky, J. Catal., 2021, 402, 130–142 CrossRef CAS.
- J. Zhao, G. Chen, Y. He, S. Li, Z. Duan, Y. Li and J. Luo, RSC Adv., 2019, 9, 6583–6588 RSC.
- H. Liu, Z. Jia, S. Ji, Y. Zheng, M. Li and H. Yang, Catal. Today, 2011, 175, 293–298 CrossRef CAS.
- K. Mori, Y. Kondo, S. Morimoto and H. Yamashita, Chem. Lett., 2007, 36, 1068–1069 CrossRef CAS.
- K. H. Choi, J. E. Park and D. H. Suh, Phys. Chem. Chem. Phys., 2017, 19, 4048–4055 RSC.
- A. Maleki and M. Kamalzare, Catal. Commun., 2014, 53, 67–71 CrossRef CAS.
- H. Niaz, H. Kashtoh, J. A. Khan, A. Khan, M. T. Alam, K. M. Khan and M. I. Choudhary, Eur. J. Med. Chem., 2015, 95, 199–209 CrossRef CAS.
- V. K. Sharma and S. K. Singh, RSC Adv., 2017, 7, 2682–2732 RSC.
- A. S. Davari, K. Abnous, S. Mehri, M. Ghandadi and F. Hadizadeh, Bioorg. Chem., 2014, 57, 83–89 CrossRef CAS PubMed.
- R. Bansal, G. Narang, C. Calle, R. Carron, K. Pemberton and A. L. Harvey, Drug Dev. Res., 2013, 74, 50–61 CrossRef CAS.
- F. Bossert, H. Meyer and E. Wehinger, Angew. Chem., Int. Ed. Engl., 1981, 20, 762–769 CrossRef.
- L. M. Wang, J. Sheng, L. Zhang, J. W. Han, Z. Y. Fan, H. Tian and C. T. Qian, Tetrahedron, 2005, 61, 1539–1543 CrossRef CAS.
- J. L. Donelson, R. A. Gibbs and S. K. De, J. Mol. Catal. A: Chem., 2006, 256, 309–311 CrossRef CAS.
- F. M. Moghaddam, H. Saeidian, Z. Mirjafary and A. Sadeghi, J. Iran. Chem. Soc., 2009, 6, 317–324 CrossRef CAS.
- S. U. Tekale, V. P. Pagore, S. S. Kauthale and R. P. Pawar, Chin. Chem. Lett., 2014, 25, 1149–1152 CrossRef CAS.
- J. S. Yoo, T. J. Laughlin, J. J. Krob and R. S. Mohan, Tetrahedron Lett., 2015, 56, 4060–4062 CrossRef CAS.
- G. Sabitha, G. K. K. Reddy, C. S. Reddy and J. S. Yadav, Tetrahedron Lett., 2003, 44, 4129–4131 CrossRef CAS.
- J. G. Breitenbucher and G. Figliozzi, Tetrahedron Lett., 2000, 41, 4311–4315 CrossRef CAS.
- M. A. Chari and K. Yamasundar, Catal. Commun., 2005, 6, 624–626 CrossRef.
- M. M. Heravi, K. Bakhtiari, N. M. Javadi, F. F. Bamoharram, M. Saeedi and H. A. Oskooie, J. Mol. Catal. A: Chem., 2007, 264, 50–52 CrossRef CAS.
- M. F. Gordeev, D. V. Patel and E. M. Gordon, J. Org. Chem., 1996, 61, 924–928 CrossRef CAS.
- R. K. Sharma, S. Yadav, S. Sharma, S. Dutta and A. Sharma, ACS Omega, 2018, 3, 15100–15111 CrossRef CAS PubMed.
- R. K. Sharma, A. Sharma, S. Sharma, S. Dutta, S. Yadav and B. Arora, ACS Omega, 2019, 4, 3146–3158 CrossRef CAS PubMed.
- S. Yadav, S. Sharma, S. Dutta, A. Sharma, A. Adholeya and R. K. Sharma, Inorg. Chem., 2020, 59, 8334–8344 CrossRef CAS.
- R. K. Sharma, B. Arora, S. Sharma, S. Dutta, A. Sharma, S. Yadav and K. Solanki, Mater. Chem. Front., 2020, 4, 605–620 RSC.
- S. Yadav, R. Dixit, S. Sharma, S. Dutta, B. Arora, P. Rana, B. Kaushik, P. Rana, A. Adholeya, M. B. Gawande and R. K. Sharma, Mater. Chem. Front., 2021, 5, 7343–7355 RSC.
- S. Yadav, R. Dixit, S. Sharma, S. Dutta, K. Solanki and R. K. Sharma, Mater. Adv., 2021, 2, 2153–2187 RSC.
- P. Rana, R. Dixit, S. Sharma, S. Dutta, S. Yadav, A. Sharma, B. Kaushik, A. Adholeya and R. K. Sharma, Sci. Rep., 2021, 11, 24429 CrossRef CAS PubMed.
- S. Yadav, R. Dixit, S. Sharma, S. Dutta, B. Arora, P. Rana, B. Kaushik, K. Solanki and R. K. Sharma, New J. Chem., 2022, 46, 10829–10843 RSC.
- P. Rana, R. Dixit, S. Sharma, S. Dutta, S. Yadav, B. Arora, B. Kaushik and R. K. Sharma, ACS Appl. Nano Mater., 2022, 5, 4875–4886 CrossRef CAS.
- F. Ghobakhloo, D. Azarifar, M. Mohammadi, H. Keypour and H. Zeynali, Inorg. Chem., 2022, 61, 4825–4841 CrossRef CAS PubMed.
- M. Mohammadi, M. Khodamorady, B. Tahmasbi, K. Bahrami and A. Ghorbani-Choghamarani, J. Ind. Eng. Chem., 2021, 97, 1–78 CrossRef CAS.
- M. Mohammadi and A. Ghorbani-Choghamarani, Res. Chem. Intermed., 2022, 48, 2641–2663 CrossRef CAS.
- M. Kazemi and M. Mohammadi, Appl. Organomet. Chem., 2020, 34, 1–31 CrossRef.
- M. Mohammadi and A. Ghorbani-Choghamarani, RSC Adv., 2022, 12, 2770–2787 RSC.
- A. Ghorbani-Choghamarani, M. Mohammadi, L. Shiri and Z. Taherinia, Res. Chem. Intermed., 2019, 45, 5705–5723 CrossRef CAS.
- T. Tamoradi, S. M. Mousavi and M. Mohammadi, New J. Chem., 2020, 44, 3012–3020 RSC.
- N. Hussain-Khil, A. Ghorbani-Choghamarani and M. Mohammadi, Sci. Rep., 2021, 11, 1–15 CrossRef PubMed.
- T. Wang, M. Wang, L. Fu, Z. Duan, Y. Chen, X. Hou and J. Yu, Sci. Rep., 2018, 8, 1–8 Search PubMed.
- Y. Ma, B. Mu, X. Zhang, H. Xu, Z. Qu, L. Gao and J. Tian, Fuel, 2019, 239, 579–586 CrossRef CAS.
- W. Sun, Y. Meng, Q. Fu, F. Wang, G. Wang, W. Gao and F. Lu, ACS Appl. Mater. Interfaces, 2016, 8, 9881–9888 CrossRef CAS PubMed.
- F. Yuan, W. Jiao, F. Yang, W. Liu, Z. Xu and R. Wang, RSC Adv., 2017, 7, 43380–43389 RSC.
- X. Cheng, W. Li, R. Nie, X. Ma, R. Sang, L. Guo and Y. Wu, Adv. Synth. Catal., 2017, 359, 454–466 CrossRef CAS.
- C. Garkoti, J. Shabir and S. Mozumdar, New J. Chem., 2017, 41, 9291–9298 RSC.
- J. Hou, G. Li, N. Yang, L. Qin, M. E. Grami, Q. Zhang and X. Qu, RSC Adv., 2014, 4, 44282–44290 RSC.
- L. Weng, H. Wang, X. Zhang, L. Liu and H. Zhang, J. Mater. Sci.: Mater. Electron., 2018, 29, 14267–14276 CrossRef CAS.
- W. Li, G. Lv, X. Cheng, R. Sang, X. Ma, Y. Zhang and Y. Wu, Tetrahedron, 2016, 72, 8557–8564 CrossRef CAS.
|
This journal is © The Royal Society of Chemistry 2023 |
Click here to see how this site uses Cookies. View our privacy policy here.