DOI:
10.1039/D3RA06395J
(Paper)
RSC Adv., 2023,
13, 31667-31673
Electrospun VO2/carbon fibers for aqueous zinc-ion batteries
Received
20th September 2023
, Accepted 24th October 2023
First published on 30th October 2023
Abstract
Aqueous zinc-ion batteries (AZIBs) have become one of the most potential energy storage devices due to their high safety and low cost. Vanadium oxide is an ideal cathode material for AZIBs because of its unique tunnel structure and multivalent nature. In this work, electrospun VO2/carbon fibers (VO2@CPAN) with a three-dimensional (3D) network are obtained by an electrospinning strategy combining with a controlled heat treatment. As cathode for AZIBs, the 3D network of the carbon fiber significantly improves the conductivity of VO2, avoids the agglomeration of VO2, and increases the stability of VO2. Therefore, VO2@CPAN delivers a specific capacity of 323.2 mA h g−1 at 0.2 A g−1, which is higher than pure VO2. At the same time, excellent capacity retention of 76.6% is obtained at high current density of 10 A g−1 after 3000 cycles.
1. Introduction
Aqueous zinc-ion batteries (AZIBs) have gradually attracted worldwide attention due to their advantages of simple processing, high safety, and environmental friendliness.1–4 At present, a variety of AZIBs cathode materials have been developed, including manganese-based compounds, vanadium-based compounds, Prussian blue analogues, etc.5–9 Among the various cathode materials, vanadium-based materials have great potential for developing high-performance AZIBs due to their multivalence nature and versatile vanadium oxide frameworks.10–13 However, the relatively poor conductivity of VO2 hinders the electron transport, thus limiting its electrochemical performance.14–17 Some strategies have been proposed to improve the conductivity of VO2, among which combining conductive materials, such as polyaniline (PANI), polypyrrole (PPy), and poly(3,4-ethylenedioxythiophene) (PEDOT), is an effective method.18–21 These materials show improved conductivity and stabilized structure by wrapping or embedding VO2. Recently, the oxygen-deficient hydrate vanadium dioxide with polypyrrole coating (Od-HVO@PPy) is developed, in which the conductive polymer coating enhances the electronic transfer and suppresses the cathode dissolution.22 Gu et al. reported nitrogen-doped VO2(B) nanobelts (VO2-N) and carbon-coated VO2 nanobelts (VO2@C), presenting superior electrochemical performances to those of pure VO2(B) in AZIBs.23,24 Liu et al. developed K+ pre-intercalated V2O5, carbon-coated V2O5 microspheres, and V6O13/VO2 electrode materials, which also exhibit improved electrochemical performance for AZIBs.25–27 Although some achievements have been made, improving the ions diffusion and architecture stability of VO2 to achieve high-performance AZIBs is still a much-needed study. For improving the electronic conductivity and structural durability of VO2, carbon fiber is particularly promising due to large specific surface area, great conductivity, and superior stability.
Herein, VO2 was first prepared by hydrothermal method, and then VO2 was embedded in carbon fiber by an electrospinning strategy combining with a controlled heat treatment. The obtained electrospun VO2/carbon fibers (VO2@CPAN) consists of carbon fibers with three-dimensional (3D) network structure and flake-like VO2. The 3D network carbon fibers significantly improve the conductivity of the electrode and the flake-like VO2 provides more active sites for electrochemical reactions. The VO2@CPAN cathode achieves a high specific capacity of 323.2 mA h g−1 at a current density of 0.2 A g−1, which is much higher than the pure VO2 cathode. In addition, an impressive capacity retention rate of 76.6% is obtained after 3000 cycles at a high current density of 10 A g−1.
2. Experimental
2.1. Synthesis of VO2 and VO2@CPAN
For VO2, 2.2 g of Na3VO4 was added to 60 mL of deionized water, accompanied by stirring for 15 min at room temperature, and then 10 mL of ethylene glycol was added and stirred for another 30 min. The pH of the above solution was adjusted to 2 with 2 M HCl. The mixed solution was stirred for 45 minutes at 75 °C, then moved into a 100 mL Teflon-lined stainless steel autoclave and heated to 180 °C for 7 h. VO2 was obtained after washing with deionized water and ethanol, followed by vacuum drying at 60 °C.
For electrospun VO2/carbon fibers (VO2@CPAN), 0.3 g of the obtained VO2 powder was dissolved in to 10 mL of N,N-dimethylformamide (DMF) solution with 10% polyacrylonitrile (PAN), then was stirred at 45 °C for 12 h. The above solution was transferred to a 10 mL of plastic syringe with a 19-gauge blunt tip needle. Electrospinning was carried out in an electrospinning equipment (SS-2535H, Ucalery). The applied voltage is 20 kV, the distance from needle to collector is 15 cm, and the flow rate is 0.05 mm min−1. The as-collected electrospun fibers was first heated to 280 °C in air at a heating rate of 1 °C min−1 and kept for 2 h. After that, it was heated to 500 °C at a heating rate of 5 °C min−1 in a nitrogen atmosphere and kept for 1 h. Finally, it was heated to 700 °C at a heating rate of 5 °C min−1 and kept for 2 h. After natural cooling, electrospun VO2/carbon fibers (VO2@CPAN) are obtained. The pure carbon fibers (CPAN) are prepared by the similar process to VO2@CPAN except no adding VO2 in electrospinning solution.
2.2. Material characterizations
The crystal structures of VO2@CPAN were characterized by an X-ray diffractometer (D8 FOCUS) with a Cu target. The morphology and microstructure of the samples were observed by a field-emission scanning electron microscope (SEM, Quanta 250 FEG, FEI).
2.3. Electrochemical measurements
The electrochemical performance of Zn//VO2@CPAN AZIBs was studied in a CR2032-type coin cells assembled in air. The VO2@CPAN cathode was prepared by mixing VO2@CPAN powder, conductive carbon, and polyvinylidene fluoride (PVDF) with a mass ratio of 7
:
2
:
1 in N-methyl-2-pyrrolidone (NMP), fully grinding in the bowl, coating on the graphite paper and drying at 60 °C for 12 h. The mass of active materials of on current collector was about 2 mg cm−2. The glass fiber membrane was used as the separator, a zinc foil was used as the anode, and 2 M ZnSO4 solution was used as the electrolyte.
Cyclic voltammetry (CV) and electrochemical impedance spectroscopy (EIS) were carried out using a Zahner/Zennium electrochemical workstation. The galvanostatic charge–discharge (GCD) curves and the specific capacity were obtained with a NEWARE battery testing system (CT-4008Tn-5V10mA). CV and GCD were conducted from 0.20 to 1.35 V (vs. Zn2+/Zn).
3. Results and discussion
The preparation process of electrospun VO2/carbon fibers (VO2@CPAN) is shown in Fig. 1. Firstly, the pure VO2 powder was synthesized by simple hydrothermal method. Then, the obtained VO2 powder was dissolved in the solution of N,N-dimethylformamide (DMF) and polyacrylonitrile (PAN) to be electrospun into VO2/PAN fibers, which was converted into VO2/carbon fibers (VO2@CPAN) via a controlled heat treatment.
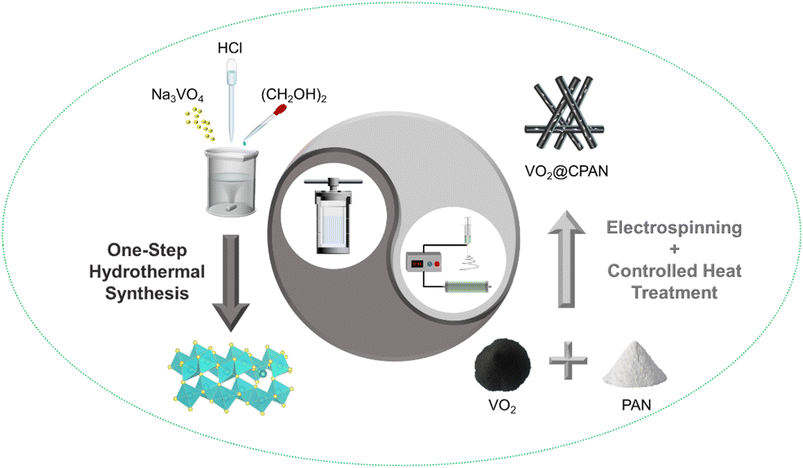 |
| Fig. 1 Schematic illustration of preparation process for VO2@CPAN. | |
Fig. 2 shows the PAN fibers obtained by electrospinning and the CPAN after a controlled heat treatment. It can be seen that both fibers have a uniform diameter of about 200 nm. The VO2 synthesized by simple hydrothermal method presents a disordered flake structure with a width of more than 200 nm, accompanied by severe agglomeration (Fig. 3a and b). The presence of agglomeration could lead to a lack of full contact between the active material and the electrolyte, limiting the complete utilization of the active material. When the VO2 nanosheets were combined with the carbon fibers via an electrospinning strategy combining with a controlled heat treatment, it can be clearly seen that the VO2 nanosheets are uniformly embedded in the carbon fibers and the diameter of the VO2@CPAN composite fibers increase to 1.1 μm (Fig. 3c and d). The 3D network carbon fibers significantly improve the conductivity of the electrode and effectively reduce the agglomeration phenomenon of VO2 nanosheets. Also, this 3D network with abundant porosity can greatly improve ion transfer kinetics during the charge–discharge process.28 The flake-like VO2 provides more active sites for electrochemical reactions, making AZIBs obtain high energy storage.29 The close contact between carbon fibers and VO2 nanosheets establishes an interconnection network with high stability for electrochemical reactions, which effectively improves the cycling life of AZIBs. In order to investigate whether VO2 changes before and after recombination with carbon fiber, the crystal structure of VO2@CPAN was analyzed by X-ray diffraction (XRD). As shown in Fig. 3e, one main peak at 23° in the XRD pattern of VO2@CPAN can be attributed to the carbon fibers, and other peaks are consistent with the monoclinic phase VO2(B) (JSPDS No. 31-1438). For the V 2p XPS spectrum of VO2@CPAN (Fig. 3f), the characteristic peaks at 516.1 (523.3) eV and 517.5 (524.2) eV attributed to V4+/V5+, respectively. The presence of V5+ is due to surface oxidation caused by air atmosphere,30 which is in accord with the less impure peaks appeared in the XRD pattern. This shows that the crystal structure of VO2 after combing with carbon fibers has no obvious change.
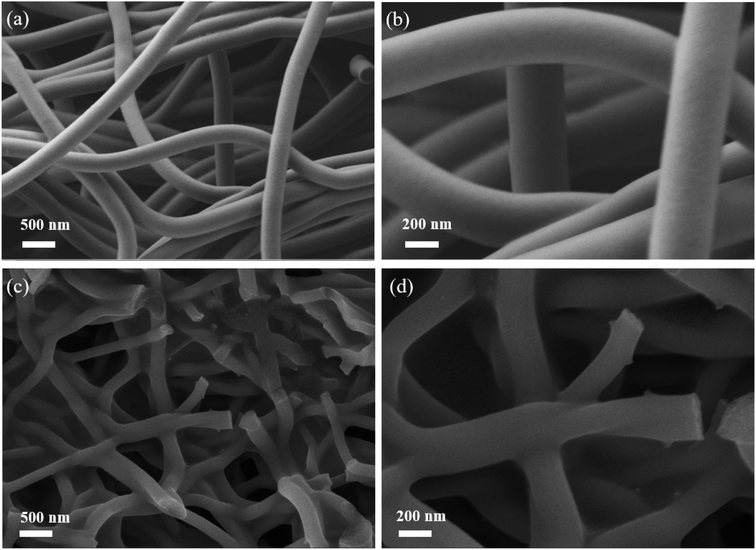 |
| Fig. 2 SEM images of (a and b) PAN fibers and (c and d) CPAN. | |
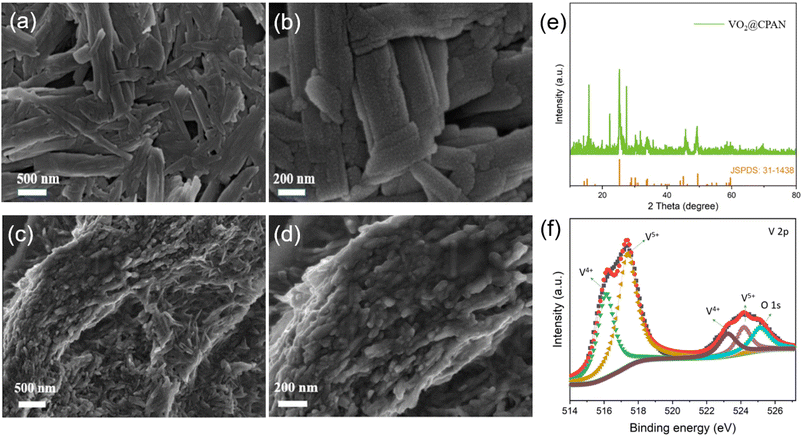 |
| Fig. 3 SEM images of (a and b) VO2 and (c and d) VO2@CPAN; (e) XRD of VO2@CPAN; (f) high-resolution XPS V 2p spectra for VO2@CPAN. | |
In order to evaluate the electrochemical performance of the VO2@CPAN, Zn//VO2@CPAN AZIBs were assembled with VO2@CPAN as cathode, Zn foil as anode, and 2 M ZnSO4 solution as electrolyte. The cyclic voltammetry (CV) curves of Zn//VO2@CPAN and Zn//VO2 AZIBs are shown in Fig. 4a. They have similar redox peaks and Zn//VO2@CPAN batteries exhibit a larger current response, indicating that the 3D network carbon fibers can effectively enhance the electrochemical activity of VO2 nanosheets. Two pairs of redox peaks at around 0.75/0.47 V and 1.15/0.9 V correspond to zinc ion extraction/insertion and V3+/V4+ redox processes, respectively.31 As shown in Fig. 4b, the CV curves of the second and third cycles are basically consistent with the first curve, indicating that the VO2@CPAN electrode has excellent reversibility. In addition, the galvanostatic charge–discharge (GCD) curves (Fig. 4c) of the Zn//VO2@CPAN AZIBs at 0.2 A g−1 show that the second and third discharge/charging curves are highly consistent with the first cycle, which also indicates that VO2@CPAN has superior reversibility and stability as a cathode material. Fig. 4d shows the rate capability of the Zn//VO2@CPAN AZIBs. The specific capacities of Zn//VO2@CPAN AZIBs at 0.2, 0.5, 1.0, 5.0 and 10.0 A g−1 are 326.5, 299.6, 275.4, 244.8 and 217.3 mA h g−1, respectively. When the current density returns to 0.2 A g−1, the capacity can reach 324.1 mA h g−1, which is equivalent to 99.2% of the initial capacity and higher than the Zn//VO2 AZIBs (96.6%). The improvement of rate performance is attributed to 3D network of VO2@CPAN, which provides ample channel for the rapid ion transport.
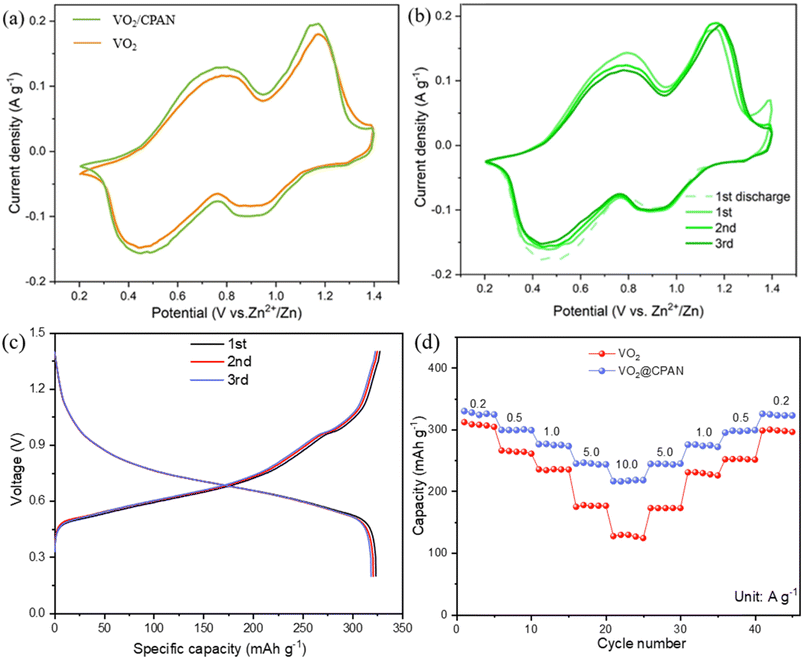 |
| Fig. 4 (a) CV curves of Zn//VO2@CPAN and Zn//VO2 AZIBs at 0.2 mV s−1; (b) CV curves of Zn//VO2@CPAN AZIBs at 0.2 mV s−1; (c) GCD curves of Zn//VO2@CPAN AZIBs at 0.2 A g−1; (d) rate performances of Zn//VO2@CPAN and Zn//VO2 AZIBs. | |
As shown in Fig. 5a, electrochemical impedance spectroscopy (EIS) shows that Zn//VO2@CPAN has a smaller semicircular arc in the high-frequency region, indicating the smaller charge transfer resistance between the VO2@CPAN electrode and the electrolyte.32 This proves that the 3D network carbon fibers provide a direct electron/ion transport pathway, guaranteeing the fast charge transfer and ion exchange in VO2@CPAN. As shown in Fig. 5b, the long-term cycling performance of Zn//VO2@CPAN AZIBs at 0.2 A g−1 was tested. Zn//VO2@CPAN AZIBs exhibited 92.2% capacity retention, whereas Zn//VO2 AZIBs presented a capacity retention rate of only 80.1% after 100 cycles. This shows that the performance of Zn//VO2@CPAN AZIBs has been comprehensively improved. Even at a high current density of 10 A g−1, Zn//VO2@CPAN batteries still achieve a high initial capacity of 217.3 mA h g−1 with a capacity retention of 76.6% after 3000 cycles, much better than Zn//VO2 batteries (Fig. 5c). The 3D network in the VO2@CPAN increases the specific surface area of the active material for the electrolyte access and avoids the agglomeration phenomenon of VO2, which can bring more reaction sites for the electrochemical reaction. Therefore, the electrochemical performance of Zn//VO2@CPAN battery is improved. In addition, at a power density of 375 W kg−1, Zn//VO2@CPAN AZIBs delivered an energy density of 225 W h kg−1. As shown in Ragone plot (Fig. 5d), VO2@CPAN reveals a competitive performance in comparison with other previously reported materials, such as V2O5·4VO2·2.72H2O,33 Nsutite-type VO2 microcrystals,34 HVO,35 Ancient Chinese Coin-shaped VO2,36 LixV2O5·nH2O,37 Na3V2(PO4)2,38 V2O5,39 VS2,40 H2V3O8,41 Zn0.25V2O5·nH2O.42
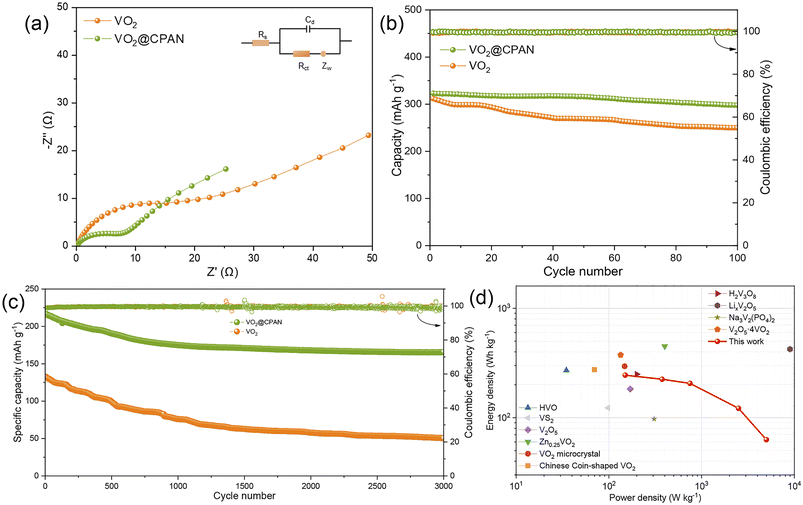 |
| Fig. 5 (a) EIS, cyclic performance and coulombic efficiency at (b) 0.2 A g−1 and (c) 10 A g−1 for Zn//VO2@CPAN and Zn//VO2 AZIBs; (d) Ragone plot of the Zn//VO2 AZIBs and other vanadium-based AZIBs. | |
4. Conclusions
In summary, electrospun VO2/carbon fibers (VO2@CPAN) with a three-dimensional (3D) network were successfully prepared by an electrospinning strategy combining with a controlled heat treatment. The 3D network not only improved the conductivity of VO2, but also avoided the agglomeration of VO2 and provided ample channel for the rapid ion transport. In addition, the flake-like VO2 provides more active sites for electrochemical reactions. Therefore, the VO2@CPAN cathode achieves a high specific capacity of 323.2 mA h g−1 at a current density of 0.2 A g−1, which is much higher than the pure VO2 cathode. At a high current density of 10 A g−1, the Zn//VO2@CPAN battery delivered a high specific capacity of 217.3 mA h g−1 and still maintained 76.6% capacity retention after 3000 cycles. The strategy of designing 3D electrospun VO2/carbon fibers by electrospinning provides a new method for constructing advanced cathode for AZIBs.
Conflicts of interest
There are no conflicts to declare.
Acknowledgements
This work is supported by Shandong Provincial Natural Science Foundation (ZR2022ME181), NSFC (51702123), University of Jinan Science and Technology Planning Project (XKY2034). S. Y. thanks the start-up research funding from University of Jinan.
Notes and references
- M. Liu, D. Zhang, B. Liu, C. Tian, B. Zhao, Y. Wang, Y. Wang, Y. Hu, L. Kong, D. Luo and Z. Chen, Nano Energy, 2022, 103, 107795 CrossRef CAS.
- Y. Zhang, A. Chen and J. Sun, J. Energy Chem., 2021, 54, 655–667 CrossRef CAS.
- S. Yang, Y. Cui, G. Yang, S. Zhao, J. Wang, D. Zhao, C. Yang, X. Wang and B. Cao, J. Power Sources, 2023, 554, 232347 CrossRef CAS.
- J. Zhang, J. Zhao, H. Du, Z. Zhang, S. Wang and G. Cui, Electrochim. Acta, 2018, 280, 108–113 CrossRef CAS.
- H. Wang, W. Yang, H. Xu, M. Li, H. Liu, S. Gong, F. Zhao, C. Li, J. Qi, W. Peng and J. Liu, Small, 2023, 2304504 CrossRef PubMed.
- J. Liu, P. Xu, J. Liang, H. Liu, W. Peng, Y. Li, F. Zhang and X. Fan, Chem. Eng. J., 2020, 389, 124405 CrossRef CAS.
- S. Zuo, J. Liu, W. He, S. Osman, Z. Liu, X. Xu, J. Shen, W. Jiang, J. Liu, Z. Zeng and M. Zhu, J. Phys. Chem. Lett., 2021, 12, 7076–7084 CrossRef CAS PubMed.
- Y. Du, X. Wang and J. Sun, Nano Res., 2020, 14, 754–761 CrossRef.
- Z. Luo, J. Zeng, Z. Liu and H. He, J. Alloys Compd., 2022, 906, 164388 CrossRef CAS.
- Z. Zhang, S. Li, X. Zhang, Y. Du, Z. Wen, S. Ji and J. Sun, Mater. Lett., 2021, 301, 130259 CrossRef CAS.
- Y. Wang, L. Zhou, X. Cao, X. Gao and X. Lu, J. Mater. Chem. A, 2021, 9, 26698–26703 RSC.
- P. Oberholzer, E. Tervoort, A. Bouzid, A. Pasquarello and D. Kundu, ACS Appl. Mater. Interfaces, 2018, 11, 674–682 CrossRef PubMed.
- Z. Chen, J. Hu, T. He, C. Feng, Y. Luo, H. Hou, G. Zou and X. Ji, Energy Storage Mater., 2022, 50, 1–11 CrossRef.
- F. Wu, Y. Jiang, Z. Ye, Y. Huang, Z. Wang, S. Li, Y. Mei, M. Xie, L. Li and R. Chen, J. Mater. Chem. A, 2019, 7, 1315–1322 RSC.
- Z. Wang, K. Yu, Y. Feng, R. Qi, J. Ren and Z. Zhu, ACS Appl. Mater. Interfaces, 2019, 11, 44282–44292 CrossRef CAS PubMed.
- K. Zhu, T. Wu and K. Huang, ACS Nano, 2019, 13, 14447–14458 CrossRef CAS PubMed.
- X. Li, L. Yang, H. Mi, H. Li, M. Zhang, A. Abliz, F. Zhao, S. Wang and H. Li, CrystEngComm, 2021, 23, 8650–8659 RSC.
- J. Wu, W. Xu, Y. Lin, X. Shi, F. Yang and X. Lu, J. Power Sources, 2021, 483, 229114 CrossRef CAS.
- R. Venkatkarthick, N. Rodthongkum, X. Zhang, S. Wang, P. Pattananuwat, Y. Zhao, R. Liu and J. Qin, ACS Appl. Energy Mater., 2020, 3, 4677–4689 CrossRef CAS.
- Y. Liu, Y. Jiang, Z. Hu, J. Peng, W. Lai, D. Wu, S. Zuo, J. Zhang, B. Chen, Z. Dai, Y. Yang, Y. Huang, W. Zhang, W. Zhao, W. Zhang, L. Wang and S. Chou, Adv. Funct. Mater., 2020, 31, 2008033 CrossRef.
- X. Liu, G. Xu, Q. Zhang, S. Huang, L. Li, X. Wei, J. Cao, L. Yang and P. K. Chu, J. Power Sources, 2020, 463, 228223 CrossRef CAS.
- Z. Zhang, B. Xi, X. Wang, X. Ma, W. Chen, J. Feng and S. Xiong, Adv. Funct. Mater., 2021, 31, 2103070 CrossRef CAS.
- X. Gu, J. Wang, X. Zhao, X. Jin, Y. Jiang, P. Dai, N. Wang, Z. Bai, M. Zhang and M. Wu, J. Energy Chem., 2023, 85, 30–38 CrossRef CAS.
- X. Gu, J. Wang, S. Wu, S. Dong, F. Li, A. Cui, M. Zhang, P. Dai and M. Wu, Mater. Adv., 2023 10.1039/D3MA00622K.
- Y. Liu, Y. Liu, X. Wu and Y.-R. Cho, ACS Sustainable Chem. Eng., 2023, 11, 13298–13305 CrossRef CAS.
- Y. Liu, Y. Liu, X. Wu and Y.-R. Cho, J. Colloid Interface Sci., 2022, 628, 33–40 CrossRef CAS PubMed.
- Y. Liu and X. Wu, J. Energy Chem., 2023, 87, 334–341 CrossRef CAS.
- Z.-T. Wang, R.-C. Wang, L.-B. Tang, Y.-J. Li, J. Mao, K.-H. Dai, Z.-J. He and J.-C. Zheng, Solid State Ionics, 2021, 369, 115714 CrossRef CAS.
- S. J. Kim, C. R. Tang, G. Singh, L. M. Housel, S. Yang, K. J. Takeuchi, A. C. Marschilok, E. S. Takeuchi and Y. Zhu, Chem. Mater., 2020, 32, 2053–2060 CrossRef CAS.
- T. Wei, Q. Li, G. Yang and C. Wang, J. Mater. Chem. A, 2018, 6, 8006–8012 RSC.
- X. Dai, F. Wan, L. Zhang, H. Cao and Z. Niu, Energy Storage Mater., 2019, 17, 143–150 CrossRef.
- G. Yang, S. Yang, J. Shen, Y. Cui, J. Sun, G. Duan, B. Cao and Z. Liu, ACS Appl. Energy Mater., 2023, 6, 1871–1876 CrossRef CAS.
- T.-T. Lv, Y.-Y. Liu, H. Wang, S.-Y. Yang, C.-S. Liu and H. Pang, Chem. Eng. J., 2021, 411, 128533 CrossRef CAS.
- Y.-Y. Liu, T.-T. Lv, H. Wang, X.-T. Guo, C.-S. Liu and H. Pang, Chem. Eng. J., 2021, 417, 128408 CrossRef CAS.
- N. Liu, X. Wu, L. Fan, S. Gong, Z. Guo, A. Chen, C. Zhao, Y. Mao, N. Zhang and K. Sun, Adv. Mater., 2020, 32, 1908420 CrossRef CAS PubMed.
- Z. Cao, L. Wang, H. Zhang, X. Zhang, J. Liao, J. Dong, J. Shi, P. Zhuang, Y. Cao, M. Ye, J. Shen and P. M. Ajayan, Adv. Funct. Mater., 2020, 30, 2000472 CrossRef CAS.
- Y. Yang, Y. Tang, G. Fang, L. Shan, J. Guo, W. Zhang, C. Wang, L. Wang, J. Zhou and S. Liang, Energy Environ. Sci., 2018, 11, 3157–3162 RSC.
- G. Lin, R. Ma, Y. Zhou, Q. Liu, X. Dong and J. Wang, Electrochim. Acta, 2018, 261, 49–57 CrossRef CAS.
- P. Hu, M. Yan, T. Zhu, X. Wang, X. Wei, J. Li, L. Zhou, Z. Li, L. Chen and L. Mai, ACS Appl. Mater. Interfaces, 2017, 9, 42717–42722 CrossRef CAS PubMed.
- P. He, M. Yan, G. Zhang, R. Sun, L. Chen, Q. An and L. Mai, Adv. Energy Mater., 2017, 7, 1601920 CrossRef.
- P. He, Y. Quan, X. Xu, M. Yan, W. Yang, Q. An, L. He and L. Mai, Small, 2017, 13, 1702551 CrossRef PubMed.
- D. Kundu, B. D. Adams, V. Duffort, S. H. Vajargah and L. F. Nazar, Nat. Energy, 2016, 1, 16119 CrossRef CAS.
|
This journal is © The Royal Society of Chemistry 2023 |
Click here to see how this site uses Cookies. View our privacy policy here.