DOI:
10.1039/D3RA05580A
(Review Article)
RSC Adv., 2023,
13, 28211-28223
Dielectric barrier discharge plasma catalysis as an alternative approach for the synthesis of ammonia: a review
Received
16th August 2023
, Accepted 14th September 2023
First published on 25th September 2023
Abstract
Numerous researchers have attempted to provide mild reactions and environmentally-friendly methods for NH3 synthesis. Research on non-thermal plasma-assisted ammonia synthesis, notably the atmospheric-pressure nonthermal plasma synthesis of ammonia over catalysts, has recently gained attention in the academic literature. Since non-thermal plasma technology circumvents the existing crises and harsh conditions of the Haber–Bosch process, it can be considered as a promising alternative for clean synthesis of ammonia. Non-thermal dielectric barrier discharge (DBD) plasma has been extensively employed in the synthesis of ammonia due to its particular advantages such as the simple construction of DBD reactors, atmospheric operation at ambient temperature, and low cost. The combination of this plasma and catalytic materials can remarkably affect ammonia formation, energy efficiency, and the generation of by-products. The present article reviews plasma-catalysis ammonia synthesis in a dielectric barrier discharge reactor and the parameters affecting this synthesis system. The proposed mechanisms of ammonia production by this plasma catalysis system are discussed as well.
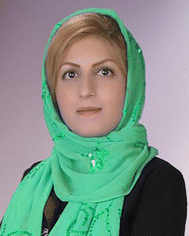 Hamideh Hosseini | Hamideh Hosseini earned her B.Sc. from Imam Khomeini International University in 2004 and M.Sc. from Kharazmi University in 2008. She received her PhD degree in organic chemistry from the Chemistry & Chemical Engineering Research Center of Iran (CCERCI), Tehran, Iran, in 2022. Her major research interest is in the field of the synthesis of chemical compounds using novel methods. |
1. Introduction
1.1. Ammonia: importance and application
Ammonia (NH3), as a nitrogenous valuable source, is used in the manufacture of plastics and fibers, pharmaceuticals, explosives, chemicals, ammonium fertilizers such as carbamide ammonium nitrate and ammonium bicarbonate, etc.1 A number of the applications of ammonia in industries are shown in Fig. 1. Ammonia is also employed as an indirect hydrogen storage material.2 In recent years, the surface functionalization of carbon nanotubes via plasma treatments has been carried out by means of ammonia.3 The formation of organic compounds containing C
N bonds is another achievement of the use of ammonia in the plasma system.4 As compared to other nitrogenous compounds, this compound is produced on a very large molar scale in the industry. The global production of ammonia reported was about 150 million metric tons in 2022.5 Ammonia, in fact, has been known worldwide as a chemical for more than two centuries. Johann Jacob Wepfer was indeed the first researcher to detect ammonia by distillation of putrefied wine yeast in 1679, but Joseph Priestley became known as the discoverer of gaseous ammonia in 1774.1 A few years later, in 1785, ammonia was identified by Claude Louis Berthollet as a compound synthesized from N2 and H2,6 while the preparation of ammonia from its elements was first carried out by Humphry Davy in 1807.7 Until 1900, many scientists and researchers such as William Donkin, Oliver Lodge, Ramsay and Young and others worked on ammonia and obtained remarkable results and achievements.8–10 In line with this research, Fritz Haber synthesized ammonia from hydrogen and nitrogen in desirable amounts in 1909,1 which will be discussed in more detail below.
 |
| Fig. 1 Use of ammonia in different industries. | |
1.2. Ammonia synthesis
Several approaches have been reported in various literatures that were employed to prepare ammonia such as Haber–Bosch process, green Haber–Bosch, electrochemical synthesis, photochemical synthesis, chemical looping process, and plasma-catalysis synthesis which are briefly described in the following sections.
1.3. Haber–Bosch process
In the early 20th century, Fritz Haber and Carl Bosch developed ammonia synthesis using the method of directly synthesizing ammonia from hydrogen and nitrogen with a metal catalyst called Haber–Bosch (HB) process as shown in Fig. 2a. Ammonia synthesis is industrially carried out at high pressure (150–300 bar) and temperature (450–600 °C). Meanwhile, the production of ammonia is reversible and is considered an exothermic reaction. So, by decreasing the temperature according to the Le Chatelier principle, the balance can be shifted towards more ammonia production. On the other hand, lowering the temperature causes the equilibrium and the ammonia production rate to be very low. Therefore, in order to further increase the equilibrium rate and thus the rate of ammonia production, this reaction is performed in the presence of a highly active catalyst. Accordingly, the use of a catalyst in this synthesis is essential to accelerate the reaction.11–13 Also, it has been estimated that this process produces more than 300 million tons of CO2 annually and consumes up to 2% of the world's energy.14 Therefore, it seems logical that the HB process should be replaced by a more environmentally friendly and economically efficient process.
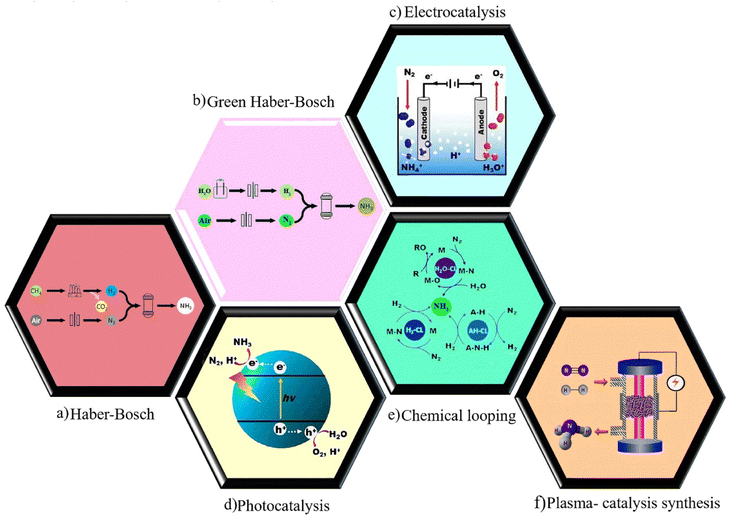 |
| Fig. 2 Schematic illustration of (a) Haber–Bosch process, (b) the green Haber–Bosch process. Reproduced from ref. 103 with permission from Elsevier, copyright 2021. (c) Electrochemical, (d) photochemical, (e) chemical looping. Reproduced from ref. 24 with permission from Elsevier, copyright 2019. (f) Plasma-catalysis synthesis. Reproduced from ref. 87 with permission from Wiley-VCH, copyright 2017. | |
1.4. Green Haber–Bosch
One of the effective alternatives for the production of ammonia in a clean, green, and sustainable way is the electrocatalytic synthesis of ammonia from nitrogen and water under mild reaction conditions using renewable electricity.15 The utilization of water as the hydrogen source in this approach can be a noteworthy advantage compared with HB process as shown in Fig. 2b. Similar to the Haber–Bosch process, ammonia is produced under high pressure and temperature in this approach.
1.5. Electrochemical synthesis
The electrochemical synthesis of ammonia has been introduced as an appealing alternative to the Haber–Bosch process due to its mild operating conditions, lack of carbon dioxide emission, ability to store renewable energies in chemical bonds, and possibility for distributed ammonia production. This synthesis is possible via nitrogen reduction reaction (NRR) or nitrogenous pollutants reduction (Fig. 2c). However, this approach is still in its infant stage and is faced with numerous obstacles.16 Electrochemical synthesis of ammonia has been extensively discussed in some publications.17–21
1.6. Photochemical synthesis
An environmentally-friendly approach to synthesize ammonia from N2 and water driven by solar energy is photocatalytic synthesis of ammonia.22 Despite significant photocatalyst development so far, further advances are required to make practical NH3 production possible.23 In general, photochemical NRR entails the absorption of light to produce photoexcited charge carriers, separation and migration of the electron–hole pairs to the reactive sites of the surface, and reaction of photo-induced electrons with nitrogen to produce ammonia with an uptake of water-derived protons.24 The schematics illustration of this approach is shown in Fig. 2d. Here, no further details will be discussed as the focus of this review is plasma-catalytic synthesis.
1.7. Chemical looping process
Chemical looping for the production of ammonia has received a large amount of interest. In this process, the first step involves the contact of N2 with a solid-state transition metal to generate a nitride (activation) and, in the second step, NH3 is obtained by contacting the nitride with steam or hydrogen. Among the benefits of chemical looping, in addition to the ability to independently control the conditions for N2 activation and product harvest, is the ability to operate at atmospheric pressure for nitrogen activation (Fig. 2e).25
1.8. Plasma-catalysis synthesis
The plasma catalysis process involves integrating plasma and catalysts in order to attain reactant conversions and product selectivities that are not possible with either plasma or catalyst alone. Although plasma-catalytic ammonia production has been known since the early 1900s, the optimization of this reaction is currently the focus of a lot of ongoing research (Fig. 2f).26
Despite the valuable achievements that have been made so far for mild-condition NH3 synthesis by electrochemical, photochemical, chemical looping, and plasma catalysis processes, there are still challenges and limitations in each of the mentioned approaches that researchers are facing. Therefore, more studies need to be carried out to solve the existing challenges in these approaches.
This review aims to further contribute towards the understanding of catalyzed ammonia synthesis in the DBD reactor under mild conditions, which has recently attracted the attention of researchers. The basic concepts of plasma-catalysis and the classification of plasma-assisted catalysis for chemical reactions are discussed in Section 2. The production of ammonia in the plasma catalysis system and the factors affecting this synthetic process are discussed in Section 3.
2. Plasma-catalysis
As mentioned above, the plasma catalysis process is one of the alternative approaches for ammonia production. In order to better understand this process, some fundamental concepts in this field are discussed.
2.1. Plasma
Plasma as the fourth state of matter, comprising 99.9% of the visible universe, contains high-energy electrons, free radicals, active ions, and excited species. This term was first proposed by Langmuir in 1928. Accordingly, plasma is classified into two categories of high and low temperature plasma based on the internal temperature of electrons. There are two types of low temperature plasma: thermal and non-thermal plasma (NTP). NTPs can be divided into atmospheric pressure plasma and low pressure plasma.
As the temperature in non-thermal plasmas is close to ambient temperature, these plasmas are suitable for most chemical reactions. Glow discharge, radiofrequency plasma (RF), dielectric barrier discharge, and atmospheric pressure plasma jet are non-thermal plasmas or cold plasmas that have the most application compared to other plasmas.27,28 Accordingly, NTPs can be considered an alternative approach to the synthesis of chemicals, notably those whose synthesis requires the use of high temperatures and/or pressures or other harsh conditions.4,29
2.2. Dielectric barrier discharge
In 1857, Siemens utilized dielectric barrier discharge (DBD) plasma for the generation of ozone.30 Since that time many types of DBD designs and geometries were made and used for different applications. DBDs, also known as silent discharges, are created using an insulating (dielectric) material to generate self-pulsing plasma between the electrodes.3 Based on the configuration of the setup, there are two main categories for DBDs including volume dielectric barrier discharge (VDBD) and surface dielectric barrier discharge (SDBD) as shown in Fig. 3. In VDBD, plasma is generated in the space between two electrodes which includes a dielectric and discharge gap and whilst in SDBD the space between the electrodes is completely filled by a dielectric and plasma is created on the surface of the dielectric.31 There are various configurations of SDBD and VDBD geometries such as symmetric VDBD with two dielectric barriers, VDBD with a floating dielectric barrier, asymmetric VDBD, symmetric single-sided SDBD, asymmetric SDBD, coplanar SDBD, symmetric double-sided SDBD, cylindrical VDBD, packed-bed DBD which can be found in ref. 31.
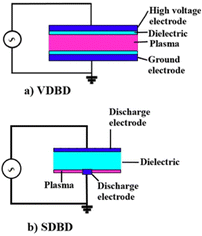 |
| Fig. 3 Two types of dielectric barrier discharges: (a) volume dielectric barrier discharge (b) surface dielectric barrier discharge. Reproduced from ref. 31 with permission from Wiley-VCH, copyright 2020. | |
2.3. Catalyst
Catalysts are substances accelerating the rate of chemical reactions by reducing the activation energy or changing the reaction mechanism without themselves being consumed in the process. In other words, the catalyst and a reactant react to form chemical intermediates and then the reaction of intermediates with each other or with another reactant leads to the formation of the final desired product. Catalysts can be solid, liquid, or gases. Homogeneous and heterogeneous catalysts are two basic types of catalysts. Currently, most chemical reactions are carried out through catalytic processes, especially heterogeneous catalysis. Catalyst synthesis requires specialized facilities and can be a complex process.32
2.4. Plasma catalysis
Plasma-catalysis is a combination of plasma and catalytic materials which are present in the numerous plasma processes. Plasma-catalysis with its various applications such as waste water treatment, material treatment, volatile organic compounds (VOC), indoor air cleaning, methanation, H2 formation, CO2 reduction, and the synthesis of NH3 has attracted a lot of attention among the researchers, especially the chemists.33 As plasma is an environment full of active species, including energetic electrons, ions, radicals, and excited molecules and neutrals, it is difficult to perform chemical reactions with high selectivity. In order to achieve increased selectivity of target products and improved energy efficiency in chemical reactions, it is necessary to use a plasma catalysis system, so the presence of plasma and catalyst together can be effective for performing many chemical reactions. To date, a large number of catalysts have been introduced and used for the plasma-assisted catalytic system in chemical reactions. According to the published articles in this field, oxide supports (TiO2, Al2O3, and SiO2)34–38 and different zeolites,39,40 supported oxides and mixed oxides (intimate mixed oxides and perovskites),41–44 and metal catalysts such as embedded nanoparticles, supported metals, and metal wires are reported more than other catalysts in plasma-assisted catalytic reactions.45,46 Generally, the catalysts applied in plasma reactors are in the form of tablets (pills), granules, extrudates, pellets, and foams.47 These structures affect the performance of catalysts in plasma-assisted catalytic processes.
2.5. The classification of plasma-assisted catalysis for chemical reactions
Four plasma-catalysis systems, single-, two-, multi-stage, as well as cycled system, are considered for the plasma combined with the catalyst, depending on the number of catalyst beds and the position of the catalyst. Single-stage system, also called in-plasma catalysis (IPC), is a configuration where the catalyst is packed in the discharge zone (a). Therefore, the catalyst and plasma are in direct contact with each other. In a two-stage configuration also called post-plasma catalysis (PPC), the catalyst is after the discharge zone (b). In this case, plasma and catalysis cannot interact directly with each other. Additionally, it is possible to combine catalysts with different functions in a multi-stage configuration to obtain the desired and expected plasma treatment (c). This configuration can be an interesting and applicable option in the future notably in industry. Lastly, the cycled system (d) involves two steps: adsorption and plasma decomposition of the contaminants adhering to the surface.48,49 The first two configurations, IPC and PPC which are more common in most reactions, are discussed below.
2.6. In-plasma catalyst (IPC)
Plasma-assisted catalysis uses the energy obtained from the excitation of the plasma to activate species either in the gas phase or on the catalyst surface. As shown in Fig. 4a, in IPC configuration, catalysts are placed in the discharge region.49 So, the catalyst interacts directly with the plasma and with the reaction products, thereby affecting the chemical nature of the process.50 In this configuration, active species such as excited-state atoms and molecules, reactive radicals, photons, and electrons generated by plasma are generally short-lived. The plasma in this one-stage arrangement may be responsible for preparing or modifying the catalyst surface.49
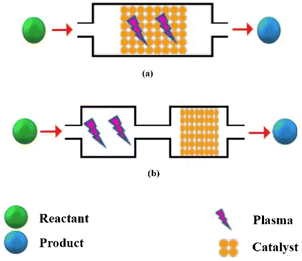 |
| Fig. 4 Two types of plasma-catalysis reactors (a) single-stage system (b) two-stage system. | |
2.7. Post-plasma catalyst (PPC)
In a two-stage arrangement, the catalyst is located downstream of the plasma and is only exposed to species that are released from the plasma (Fig. 4b). Normally, these species are the end-products of the gas phase plasma processing or long-lived intermediates and maybe vibrationally excited species as well.49 Methane partial oxidation to methanol (MPOM) is one of the reactions that is usually performed with the PPC configuration. It seems that the use of the catalyst in PPC configuration in this reaction has some advantages such as its high resistance to carbon deposition and its long-time stability in extended MPOM reactions.51
3. Plasma-catalysis ammonia synthesis in DBD reactors
Researchers have investigated ammonia synthesis using plasma-assisted catalysis in a variety of reactor configurations and operating conditions with a broad range of catalysts.52 Ammonia has been synthesized using different types of discharges including glow discharge,53 RF and microwave discharges,54–59 arc discharge,60 and DBD up to now. Surprisingly, the majority of the studies on the plasma ammonia synthesis from N2 and H2 have been carried out using a DBD plasma at atmospheric pressure and mild temperatures. As a matter of fact, ammonia yield is enhanced when plasma is coupled with a catalyst, but some literature has reported production of ammonia without a catalyst. Accordingly, Kubota et al. synthesized ammonia without the use of a catalyst in a plasma–liquid system in 2010.61 While many attempts have been made to produce ammonia in DBD reactors since the past several decades, plasma-catalytic ammonia synthesis in these reactors has been extensively explored since 2000.62 A brief summary of developments of plasma-catalysis ammonia synthesis in DBD plasma reactors since 2000 is shown in Fig. 5.
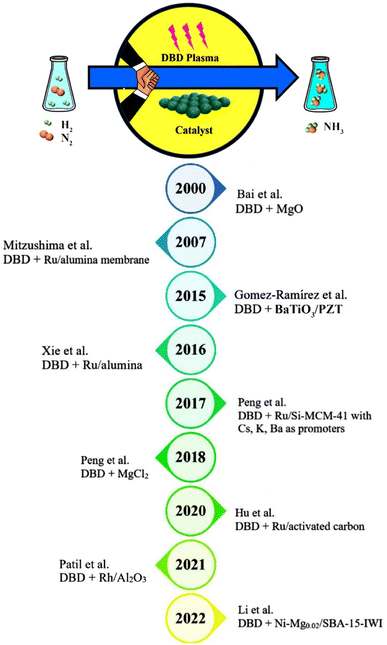 |
| Fig. 5 A summary of developments of plasma-catalysis ammonia synthesis in DBD plasma reactors along with various catalysts since 2000. | |
In order to synthesize ammonia in the plasma-catalysis system, two main factors must be taken into account: the catalyst and the plasma parameters, which will be discussed further in this section.
3.1. Catalyst development
The development of catalysts plays a critical role in improving NTP ammonia synthesis.
In the ammonia synthetic process, several different types of materials as catalysts in connection with plasma have been studied to date, according to literature reports. Among these, oxides and supported oxides,63–65 zeolites,66–68 as well as metals and supported metals69–74 are the most common catalysts.
3.2. Oxides and supported oxides
In addition to TiO2, MgO, CaO, quartz wool, and BaTiO3 as catalyst supports,65 alumina as one of the most frequent catalysts in this group is used in the plasma-catalytic synthesis of ammonia. Xie et al. reported NH3 synthesis process from N2 and H2 over the Al2O3 catalyst in a dielectric barrier discharge plasma reactor.63 They found that ammonia produced using Al2O3 was more than that produced without it. Furthermore, it was stated that the presence of alumina resulted in higher ammonia production in this plasma process due to its certain catalytic activity. In another study, Zhu et al. synthesized ammonia from N2 and H2 by using acidic γ-Al2O3, alkaline γ-Al2O3 and neutral alumina pellets in a dielectric barrier discharge plasma reactor.64 The results demonstrated that the plasma-catalytic synthesis of ammonia increased in the presence of all types of γ-Al2O3 from 15.6% to 44.4%, notably the alkaline γ-Al2O3, in comparison with the plasma reaction without packing materials. This implies that the attendance of a packing material such as oxides can affect both the discharge power required to ignite the plasma and the plasma discharge characteristics.62
3.3. Zeolites
Another group of catalysts in the ammonia synthesis process using plasma-assisted catalysis is zeolites. Gorky et al. examined atmospheric-pressure nonthermal plasma synthesis of ammonia over zeolitic imidazolate frameworks (ZIFs) in a DBD reactor.66 Based on the results obtained from this study, the dipole–dipole interactions between the polar ammonia molecules and the polar walls of the aforementioned ZIFs caused relatively low ammonia uptakes, low storage capacity, and eventually high observed ammonia synthesis rates. Shah et al. also found that the use of zeolite 5A for the plasma-catalytic synthesis of ammonia led to an increased catalytic performance.67 Alternatively, an energy yield of 15.5 g-NH3 per kW per h was obtained with zeolite 5A at an equimolar N2/H2 ratio, which is at least 50 times higher than that without zeolite. Hence, the presence of the zeolites as active catalysts in the DBD reactor can promote the ammonia yield and even energy yield so that ammonia yield of 5.31% was obtained in the presence of zeolite beta.68
3.4. Metals and supported metals
The use of metals and supported metals as catalysts, especially transition metals, for ammonia production in the plasma system has been extensively studied by researchers.69–74 Hu et al. investigated the synthesis of NH3 on activated carbon-supported metal (Ru, Co, Ni, and Fe) catalysts in a coaxial dielectric barrier discharge reactor.71 Based on the reported results, the highest ammonia concentration of 3026.5 ppm and energy efficiency of 0.72 g kW h−1 were obtained with Ru/AC. These results indicate that coupling the dielectric barrier discharge with an activated carbon support increased the NH3 concentration by 11.0–22.5% compared to plasma alone. Moreover, the synthesis of NH3 was increased by up to 37.3% by doping active metal on activated carbon. Li et al. found that the presence of the Ni/LaOF catalyst with dual active centers in a dielectric barrier discharge system can be efficient on the ammonia synthesis rate.72 Accordingly, the ammonia synthesis rate in the presence of Ni/LaOF was about two times higher than when pure LaOF was used and at least 30 times higher than when plasma was used alone. In another study, plasma catalytic synthesis of NH3 on Al2O3 supported transition metals such as Co, Ni, Co–Ni was carried out in a DBD plasma reactor.73 It was found that the highest NH3 synthesis rate in this study was achieved with Co–Ni/Al2O3. In this case, this bimetallic catalyst is not only cheaper, but also reduces the acidity of the catalyst surface and increases the plasma discharge, which benefits the ammonia synthesis. In addition to the catalysts described above, other catalysts for plasma catalytic ammonia synthesis have been proposed by various research groups. For example, Iwamoto et al. tested wool-like electrodes for ammonia synthesis in a DBD reactor.75 Among these catalysts studied, Au showed the highest catalytic activity. Another catalyst reported in NH3 production is a tubular membrane-like catalyst.76,77 The presence of metals such as Ru, Pt, Ni, and Fe on the alumina led to an increase in ammonia synthesis by enhancing the hydrogenation of N(a) species (species adsorbed on an adsorbent are prefixed with “(a)”).77 A number of catalysts used in plasma catalytic ammonia synthesis are listed in Table 1.
Table 1 Summary of literature on the plasma ammonia synthesis using various catalysts in dielectric barrier discharge (DBD) reactors
Entry |
Catalyst |
H2/N2 rate |
Feet flow rate (ml min−1) |
Voltage (kV) |
Power (W) |
NH3 yield (%) |
Energy yield (g kW−1 h−1) |
Energy cost (MJ mol−1) |
Year |
Ref. |
1 |
Pd wound on electrode |
3 |
Batch |
|
12.5 |
3.13 |
|
|
1969 |
78 |
2 |
MgO smeared on electrode |
0.8 |
2266.7 |
0.58 |
|
0.33 |
|
|
2000 |
79 |
3 |
Ru/alumina membrane |
3 |
40 |
4.5 |
127 |
4.36 |
0.37 |
163.9 |
2004 |
76 |
4 |
Ru/alumina membrane |
3 |
30 |
4.5 |
127 |
4.62 |
0.4 |
154.7 |
2007 |
77 |
5 |
BaTio3/PZT |
1 |
38.3 |
3 |
|
2.8 |
0.9 |
136 |
2015 |
80 |
6 |
Alumina and DLC coated alumina |
3 |
60 |
15 |
90.5 |
0.67 |
0.18 |
340 |
2016 |
81 |
7 |
Cs–Ru/MgO |
3 |
4000 |
6 |
|
2.41 |
2.3 |
26.6 |
2016 |
82 |
8 |
Cu wool |
1 |
100 |
5 |
|
3.5 |
3.3 |
18.5 |
2016 |
83 |
9 |
Ru/alumina |
1.5 |
|
|
|
|
6.4 |
95.6 |
2016 |
84 |
10 |
Ni/silica with barium titanate as dielectric |
3 |
25 |
20 |
107 |
12 |
0.75 |
81 |
2017 |
85 |
11 |
Lead zirconium titanate |
3 |
11.5 |
5.5 |
|
0.5 |
0.75 |
81.6 |
2017 |
86 |
12 |
Ru–Mg/alumina |
4 |
2000 |
5.4 |
|
2.55 |
35.7 |
1.7 |
2017 |
87 |
13 |
Ru/alumina |
3 |
1000 |
7.5 |
|
0.05 |
1.9 |
32.2 |
2017 |
65 |
14 |
Ru/Si-MCM-41 with Cs, K, Ba as promoters |
1 |
|
5 |
|
|
1.7 |
3.6 |
2017 |
88 |
15 |
Au wool |
1 |
100 |
|
128.7 |
|
0.58 |
|
2017 |
75 |
16 |
Ni nanoparticles/alumina |
2 |
100 |
|
10 |
2 |
0.89 |
68.9 |
2018 |
89 |
17 |
MgCl2 |
1 |
4000 |
6.4 |
|
|
20.5 |
2.9 |
2018 |
90 |
18 |
Ni/Al2O3 |
2 |
56 |
12 |
25.1 |
|
0.56 |
|
2019 |
91 |
19 |
Ru/α-Al2O3 |
0.5 |
120 |
8 |
38.4 |
1.49 |
1.89 |
32.39 |
2019 |
92 |
20 |
Zeolite 5A |
1 |
25 |
7.5 |
13.3 |
|
15.5 |
3.95 |
2020 |
67 |
21 |
Alkaline γ-Al2O3 |
3 |
100 |
|
24.25 |
|
6.58 |
9.30 |
2020 |
64 |
22 |
Ru/activated carbon |
3 |
100 |
|
13.3 |
|
0.72 |
85 |
2020 |
71 |
23 |
Rh/γ-Al2O3 |
0.5 |
100 |
8 |
24 |
1.43 |
0.94 |
65 |
2021 |
93 |
24 |
Co–Ni/Al2O3 |
1 |
200 |
|
30.81 |
|
0.83 |
|
2022 |
73 |
25 |
Ni–Mg0.02/SBA-15-IWI |
1 |
20 |
9.5 |
|
|
1.05 |
|
2022 |
94 |
3.5. Investigation of the plasma parameters
Apart from the significance of catalysts in plasma-assisted catalysis synthesis of ammonia, the effect of plasma parameters should also be considered, some of which, including the argon addition, the flow rate of reactants, and the feed gas ratio, are discussed below (Fig. 6).
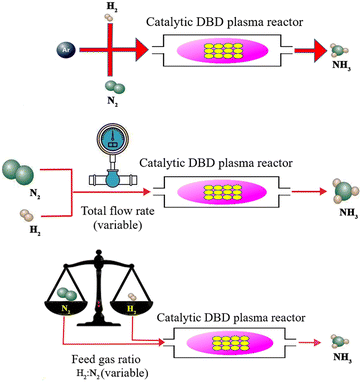 |
| Fig. 6 Some effective plasma parameters in the plasma-catalytic synthesis of ammonia, including the argon addition, the flow rate of reactants, and the feed gas ratio. | |
3.6. Effect of argon addition
Argon can lead to a change in ammonia production during the plasma catalytic synthesis of ammonia from N2 and H2. Indeed, the addition of argon led to an increase in the production of N2+ through charge transfer between Ar+ and N2, enhancing the formation of the NH radical as an intermediate of ammonia, as shown in eqn (1)–(3).95,96
It was realized that when argon was introduced, nitrogen and hydrogen conversion was improved, and this improvement was more pronounced when argon content was higher.92 Although this improvement came at a cost of production rate and energy consumption, the actual value of N2 and H2 was reduced with an increase in the concentration of argon. Accordingly, it was reported that the conversion of reactants improved more than five times in a catalytic DBD reactor with 87% argon dilution, with a 1.5 times rise in energy consumption and a 31% decrease in NH3 generation compared to no dilution condition. In this study, the addition of argon appears to be able to affect the conversion of reactants in a catalytic dielectric barrier discharge reactor more than in a DBD reactor without a catalyst.
3.7. Effect of flow rate
The influence of flowrate of reactants on the plasma-catalytic synthesis of ammonia has been examined by several research groups.69,73,97,98 The increase in the flow rate of gas can lead to a decrease in the residence time of reactive species in the plasma system.69 Additionally, as the gas flow rate increases when the pressure remains constant, more raw reactant gas is added to the system, increasing the chances of reactive particles colliding, which is beneficial to ammonia production.73 Hence, the reaction gas flow rate affects the ammonia production rate. To assess the effect of flow rate on the ammonia production rate, the DBD reactor packed with the Al2O3 supported transition metals such as Co, Ni, and Co–Ni was tested for several gas flow rates. The results indicated that increasing the total gas flow rate as a plasma parameter can improve the synthesis rate of ammonia, although the NH3 production growth rate reduced at a flow rate greater than 120 ml min−1. Ma et al. also investigated the effect of total gas flow rate on NH3 synthesis and energy cost under ambient conditions using the tangled Cu electrode at a constant molar ratio of N2/H2 of 1
:
1 and a discharge power of 20 W.97 It was found that the ammonia concentration decreased with increasing total flow rate as the number of collisions between reactant molecules and energetic electrons and other reactive species decreased. It has also been reported that when the total flow rate increased from 50 to 250 ml min−1, the energy cost of NH3 production reduced from 139.3 to 59.0 MJ mol−1.
As a matter of fact, the higher flow rate, however, enhances the total number of reactants passing through the plasma zone and promotes the conversion of molecules at a constant discharge power.
3.8. Effect of feed gas ratio
H2
:
N2 gas ratios in plasma catalytic NH3 synthesis can affect the concentration and production rate of ammonia as well as the energy consumption of the plasma system.99 To investigate the effect of feed gas ratio on NH3 synthesis, van Raak et al. obtained the ammonia concentrations as well as energy consumption for the different feed gas ratios on Ru/CeO2 and Ru/Ti–CeO2 in a coaxial DBD reactor (Fig. 7).70 As can be seen, the highest concentration for Ru/CeO2 was 2215 ppm at a N2
:
H2 ratio of 1
:
1, while the maximum concentration for Ru/Ti–CeO2 was 2965 ppm at a ratio of 2
:
1. This result illustrated that as N2 increases, the difference between the two catalysts becomes more significant. On the other hand, the lowest energy consumption (ECs), namely 85.4 MJ mol−1, was obtained for Ru/Ti–CeO2 at a ratio of N2
:
H2 = 2
:
1. At the same ratio, the minimum energy consumption for Ru/CeO2 was reported to be 126.5 MJ mol−1. This implies that N2-rich environments combined with Ru-catalysts led to the minimum ECs.
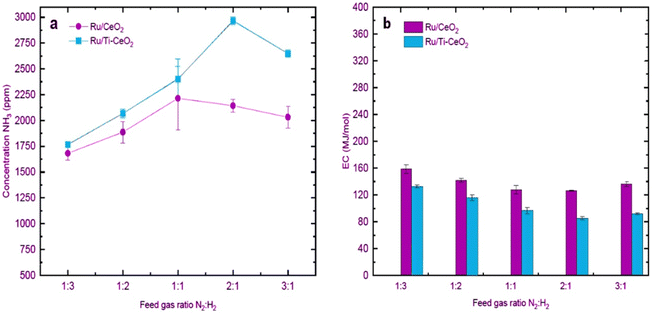 |
| Fig. 7 Effect of different feed gas ratios on (a) NH3 concentrations and (b) ECs. Reproduced from ref. 70 with permission from Elsevier B.V., copyright 2023. | |
3.9. Reaction mechanisms in plasma-catalysis ammonia synthesis
Optical emission spectroscopy (OES) is more commonly utilized than other analytical techniques to determine the plasma species that were obtained from ammonia in a catalytic DBD reactor. Nevertheless, OES is not able to detect all species, including N*.100 The results of optical emission spectroscopy to identify excited species in the N2–H2 plasma reaction using the DBD plasma in the presence of various catalysts have been reported by several research groups, as shown in Table 2.80,91,93,100–102 Although the mechanisms of ammonia synthesis in a non-thermal plasma catalysis system have been reported and described by several groups,103–109 Hong et al. have presented for the first time a detailed kinetic modelling of non-equilibrium N2–H2 atmospheric pressure discharges for catalytic NH3 synthesis.110 As we all know, to form ammonia in the gas phase, the bonds of both molecular hydrogen and molecular nitrogen must be broken.62 This can be achieved via their collision with high-energy electrons in the plasma, as shown in eqn (4) and (5).93 Thus, when N2 molecules collide with high-energy electrons, it is possible for N2 molecules to excite, ionize, and even dissociate. The excited N2 species undergo parallel reactions either by homogeneous reaction with molecules of H2 or by heterogeneous reaction with molecules of H2 adsorbing on the catalyst surface, as shown in eqn (6) and (7). In both cases, the NHx molecules formed are capable of reacting with H2 to produce NH3 molecules, as shown in eqn (8). Catalysts can assist in the adsorption of NH3 onto their surfaces and, if the reaction temperature is above about 250–300 °C, the molecules can thermally decompose, as shown in eqn (9). |
 | (4) |
|
 | (5) |
|
 | (6) |
|
 | (7) |
|
If T > 300 °C: NH3 → N2 + H2
| (9) |
In another study, Mizushima et al. proposed a mechanism for the formation of ammonia in the plasma system.77 In this reaction pathway,
obtained from N2 plasma reaction can form atomic N(a) species. The N(a) atoms react with H atoms or activated
molecules to form NH3. They stated that the presence of metals on alumina can accelerate the hydrogenation of N(a) species, increasing NH3 yields. Based on these results, it is concluded that metals can act as catalysts in the formation of ammonia by N2–H2 plasma.
Table 2 Some species detected by OES under various operating conditions of the dielectric barrier discharge plasma reactor
Entry |
Species |
Electronic transition |
Band |
Wavelength (nm) |
Year |
Ref. |
1 |
N2 (SPS) |
C3Π → B3Π |
0–0 |
357.9 |
2015 |
80 |
2 |
N2+ (FNS) |
B2Σ+u → X2Σ+g |
|
391.4 |
2015 |
80 |
3 |
 |
|
0–0 |
337 |
2015 |
80 |
4 |
NH* |
A3Π → X3∑ |
0–0 |
336 |
2015, 2021, 2022 |
80, 93 and 101 |
5 |
N2+ |
|
|
<250 |
2021 |
93 |
6 |
N |
|
|
742, 818.5, 822, 824, 939, and 1011 |
2022 |
102 |
7 |
Hα |
|
|
656.3 |
2019, 2022, 2022 |
91, 101 and 102 |
8 |
Hβ |
|
|
486.2 |
2022 |
102 |
In addition to OES, the electron impact molecular-beam mass spectrometer (EI-MBMS) as a powerful approach was employed for the detection of gas-phase radicals and molecules in the plasma processes even at atmospheric pressure. Recently, Zhao et al. used an EI-MBMS for in situ identification of gas-phase species in a dielectric barrier discharge plasma-assisted catalytic reactor.111 They succeeded for the first time to identify N2H2, NNH, and NH as the gas-phase species in plasma-assisted NH3 synthesis. Gas-phase NNH can be produced by the following eqn (10) and (11):
|
N(g) + H(g) ⇄ NNH(g)
| (10) |
|
N(v) + H(g) ⇄ NNH(g)
| (11) |
Moreover, according to the following eqn (12) and (13), N2H2 was obtained from the reaction of NNH(g) with H(g) or H2(g).
|
NNH(g) + H(g) ⇄ N2H2(g)
| (12) |
|
NNH(g) + H2(g) ⇄ N2H2(g) + H(g)
| (13) |
Based on the observations made in this study, it was determined that NNH and N2H2 species are important for the production of ammonia in a dielectric barrier discharge reactor because of their interactions. The reaction of N(s) and NH(s) as the surface formed intermediates with H(g) and H(s) can lead to the production of NH2(s) and eventually NH3(s), as shown by the following eqn (14)–(19)
|
N(s) + H(s) ⇄ NH(s) + s
| (15) |
|
NH(s) + H(g) ⇄ NH2(s)
| (16) |
|
NH(s) +H(s) ⇄ NH2(s) + s
| (17) |
|
NH2(s) + H(g) ⇄ NH3(s)
| (18) |
|
NH2(s) +H(s) ⇄ NH3(s) + s
| (19) |
4. Conclusion
Major efforts have been undertaken to develop an alternative and environmentally friendly technology for the production of ammonia under the mild conditions. Plasma catalysis is a promising option for the ammonia production at atmospheric pressures and temperatures close to ambient. In addition to this, the plasma-catalytic has the significant potential to resolve the crises of ammonia synthesis present in the Haber–Bosch process such as the consumption of fossil fuels and environmental pollution. Although currently, ammonia production quantities achievable by plasma reactors are not comparable to those achievable in large Haber–Bosch reactors, by optimizing the catalyst and DBD reactor and studying the kinetics and reactant composition, it is anticipated that plasma technology, particularly DBD plasma, due to its ability to easily create nonequilibrium conditions, will be able to significantly improve the production of NH3. This review focused on the plasma synthesis of NH3 in the DBD reactor packed with different catalysts. In summary, dielectric barrier discharge plasma combined with catalysts can increase not only the ammonia yield but also the synthesis rate. As was mentioned, a wide range of catalysts was used in the plasma-assisted NH3 synthesis process and their effect was examined on ammonia yield and the energy yield. Consequently, reasonably high yields of ammonia in many experiments were reported, but energy efficiencies were not satisfactory. In addition to the effect of the catalyst, other process parameters such as argon addition, the flow rate, and the feed gas ratio would have a pronounced influence on the NH3 synthesis. Recently, the effects of process parameters on NH3 concentration and energy efficiency have been systematically investigated using the central composite design model and response surface methodology (CCD-RSM).69 Based on the analysis of variance (AVONA), the most important variables affecting the NH3 concentration and energy efficiency of the plasma-assisted NH3 synthesis process were the plasma discharge power and the gas flow rate, respectively. Considering the available results of the experiments conducted so far and the proposed mechanisms for ammonia synthesis in the plasma catalyst system, it is concluded that further research is needed to optimize the plasma-catalysis NH3 synthesis process. Therefore, it is expected that the number of experimental and modelling research will increase in the future. However, the selection of efficient catalysts or the innovation of new catalysts as well as the proper design of the DBD reactor in the catalytic plasma system can have a significant impact on ammonia production, energy efficiency and even the production of by-products.
Conflicts of interest
The author declares no known competing interests.
Notes and references
- M. L. Carreon, Plasma catalytic ammonia synthesis: state of the art and future directions, J. Phys. D, 2019, 52, 483001 CrossRef CAS.
- R. Lan, J. T. Irvine and S. Tao, Ammonia and related chemicals as potential indirect hydrogen storage materials, Int. J. Hydrogen Energy, 2012, 37, 1482 CrossRef CAS.
- H. Hosseini and M. Ghaffarzadeh, Surface functionalization of carbon nanotubes via plasma discharge: a review, Inorg. Chem. Commun., 2022, 138, 109276 CrossRef CAS.
- H. Hosseini and M. Ghaffarzadeh, Investigation of Plasma Induced Reactions of Liquid Toluene in Ar/NH3: The Formation of Organic Compounds through Radical Intermediates, Chem. Lett., 2022, 51, 784 CrossRef CAS.
- Statista research department global ammonia production 2010–2022, 2023, https://www.statista.com/statistics/1266378/global-ammonia-production/.
- V. Pattabathula and J. Richardson, Introduction to ammonia production, Chem. Eng. Prog., 2016, 112, 69 Search PubMed.
- H. Davy, I. The Bakerian Lecture, on some chemical agencies of electricity, Philos. Trans. R. Soc. London, 1807, 97, 1 Search PubMed.
- W. F. Donkin, II. On the direct synthesis of ammonia, Proc. R. Soc. London, 1873, 21, 281 CrossRef.
- R. I. O. G. Britain, Proceedings at the Meetings of the Members of the Royal Institution of Great Britain, 1886, vol. 11 Search PubMed.
- W. Ramsay and S. Young, XIV.—The decomposition of ammonia by heat, J. Chem. Soc., Trans., 1884, 45, 88 RSC.
- V. Smil, Enriching the earth: Fritz Haber, Carl Bosch, and the transformation of world food production, MIT Press, Cambridge, MA, USA, 2004 Search PubMed.
- J. Shah, W. Wang, A. Bogaerts and M. L. Carreon, Ammonia synthesis by radio frequency plasma catalysis: revealing the underlying mechanisms, ACS Appl. Energy Mater., 2018, 1, 4824 CrossRef CAS.
- R. R. Schrock, Reduction of dinitrogen, Proc. Natl. Acad. Sci. U.S.A., 2006, 103, 17087 CrossRef CAS PubMed.
- Y. Tanabe and Y. Nishibayashi, Developing more sustainable processes for ammonia synthesis, Coord. Chem. Rev., 2013, 257, 2551 CrossRef CAS.
- G. Duan, Y. Chen, Y. Tang, K. A. Gasem, P. Wan, D. Ding and M. Fan, Advances in electrocatalytic ammonia synthesis under mild conditions, Prog. Energy Combust. Sci., 2020, 81, 100860 CrossRef.
- T. Wu, W. Fan, Y. Zhang and F. Zhang, Electrochemical synthesis of ammonia: progress and challenges, Mater. Today Phys., 2021, 16, 100310 CrossRef CAS.
- S. P. S. B. S. Giddey, S. P. S. Badwal and A. Kulkarni, Review of electrochemical ammonia production technologies and materials, Int. J. Hydrogen Energy, 2013, 38, 14576 CrossRef CAS.
- F. Jiao and B. Xu, Electrochemical ammonia synthesis and ammonia fuel cells, Adv. Mater., 2019, 31, 1805173 CrossRef PubMed.
- G. Soloveichik, Electrochemical synthesis of ammonia as a potential alternative to the Haber–Bosch process, Nat. Catal., 2019, 2, 377 CrossRef CAS.
- G. Hochman, A. S. Goldman, F. A. Felder, J. M. Mayer, A. J. Miller, P. L. Holland, L. A. Goldman, P. Manocha, Z. Song and S. Aleti, Potential economic feasibility of direct electrochemical nitrogen reduction as a route to ammonia, ACS Sustain. Chem. Eng., 2020, 8, 8938 CrossRef CAS.
- B. Wang, T. Li, F. Gong, M. H. D. Othman and R. Xiao, Ammonia as a green energy carrier: electrochemical synthesis and direct ammonia fuel cell-a comprehensive review, Fuel Process. Technol., 2022, 235, 107380 CrossRef CAS.
- Q. Han, H. Jiao, L. Xiong and J. Tang, Progress and challenges in photocatalytic ammonia synthesis, Adv. Mater., 2021, 2, 564 RSC.
- S. Choe, S. M. Kim, Y. Lee, J. Seok, J. Jung, J. S. Lee and Y. J. Jang, Rational design of photocatalysts for ammonia production from water and nitrogen gas, Nano Converg., 2021, 8, 1 CrossRef PubMed.
- Q. Wang, J. Guo and P. Chen, Recent progress towards mild-condition ammonia synthesis, J. Energy Chem., 2019, 36, 25 CrossRef.
- J. G. Chen, R. M. Crooks, L. C. Seefeldt, K. L. Bren, R. M. Bullock, M. Y. Darensbourg, P. L. Holland, B. Hoffman, M. J. Janik, A. K. Jones and M. G. Kanatzidis, Beyond fossil fuel–driven nitrogen transformations, Science, 2018, 360, eaar6611 CrossRef PubMed.
-
(a) C. Yan, C. Waitt, I. Akintola, G. Lee, J. Easa, R. Clarke, F. Geng, D. Poirier, H. O. Otor, G. Rivera-Castro and D. B. Go, Recent advances in plasma catalysis, J. Phys. Chem. C, 2022, 126, 9611 CrossRef CAS;
(b) J. Shah, F. Gorky, P. Psarras, B. Seong, D. A. Gómez-Gualdrón and M. L. Carreon, Enhancement of the yield of ammonia by hydrogen-sink effect during plasma catalysis, ChemCatChem, 2020, 12, 1200 CrossRef CAS.
- R. d'Agostino, P. Favia, C. Oehr and M. R. Wertheimer, Low-temperature plasma processing of materials: past, present, and future, Plasma Processes Polym., 2005, 2, 7 CrossRef.
- C. Tendero, C. Tixier, P. Tristant, J. Desmaison and P. Leprince, Atmospheric pressure plasmas: a review, Spectrochim. Acta, Part B, 2006, 61, 2 CrossRef.
- H. Hosseini, M. Saleem, E. Marotta and C. Paradisi, Nitrogen-containing organic products from the treatment of liquid toluene with plasma-activated N2 gas, Plasma Processes Polym., 2021, 18, 2100012 CrossRef CAS.
- W. Siemens, Ueber die elektrostatische Induction und die Verzögerung des Stroms in Flaschendrähten, Ann. Phys., 1857, 178, 66 CrossRef.
- K. Ollegott, P. Wirth, C. Oberste-Beulmann, P. Awakowicz and M. Muhler, Fundamental Properties and Applications of Dielectric Barrier Discharges in Plasma-Catalytic Processes at Atmospheric Pressure, Chem. Ing. Tech., 2020, 92, 1542 CrossRef CAS.
- J. T. Richardson, Principles of catalyst development, Springer, 2013 Search PubMed.
- G. Chen, L. Wang, T. Godfroid and R. Snyders, Progress in plasma-assisted catalysis for carbon dioxide reduction, in Plasma Chemistry and Gas Conversion, IntechOpen, London, UK, 2018 Search PubMed.
- A. E. Wallis, J. C. Whitehead and K. Zhang, Plasma-assisted catalysis for the destruction of CFC-12 in atmospheric pressure gas streams using TiO2, Catal. Lett., 2007, 113, 29 CrossRef CAS.
- M. A. Malik, Y. Minamitani and K. H. Schoenbach, Comparison of catalytic activity of aluminum oxide and silica gel for decomposition of volatile organic compounds (VOCs) in a plasmacatalytic reactor, IEEE Trans. Plasma Sci., 2005, 33, 50 CAS.
- S. Pekárek, M. Pospíšil and J. Krýsa, Non-Thermal Plasma and TiO2-Assisted n-Heptane Decomposition, Plasma Processes Polym., 2006, 3, 308 CrossRef.
- B. Lu, X. Zhang, X. Yu, T. Feng and S. Yao, Catalytic oxidation of benzene using DBD corona discharges, J. Hazard. Mater., 2006, 137, 633 CrossRef CAS PubMed.
- R. Morent, J. Dewulf, N. Steenhaut, C. Leys and H. Van Langenhove, Hybrid plasma-catalyst system for the removal of trichloroethylene in air, J. Adv. Oxid. Technol., 2006, 9, 53 CAS.
- S. M. Oh, H. H. Kim, A. Ogata, H. Einaga, S. Futamura and D. W. Park, Effect of zeolite in surface discharge plasma on the decomposition of toluene, Catal. Lett., 2005, 99, 101 CrossRef CAS.
- L. Intriago, E. Díaz, S. Ordóñez and A. Vega, Combustion of trichloroethylene and dichloromethane over protonic zeolites: influence of adsorption properties on the catalytic performance, Microporous
Mesoporous Mater., 2006, 91, 161 CrossRef CAS.
- Y. F. Guo, D. Q. Ye, K. F. Chen, J. C. He and W. L. Chen, Toluene decomposition using a wire-plate dielectric barrier discharge reactor with manganese oxide catalyst in situ, J. Mol. Catal. A: Chem., 2006, 245, 93 CrossRef CAS.
- J. O. Chae, V. Demidiouk, M. Yeulash, I. C. Choi and T. G. Jung, Experimental study for indoor air control by plasma-catalyst hybrid system, IEEE Trans. Plasma Sci., 2004, 32, 493 CrossRef CAS.
- S. Delagrange, L. Pinard and J. M. Tatibouët, Combination of a non-thermal plasma and a catalyst for toluene removal from air: manganese based oxide catalysts, Appl. Catal., B, 2006, 68, 92 CrossRef CAS.
- H. Grossmannova, D. Neirynck and C. Leys, Atmospheric discharge combined with Cu-Mn/Al2O3 catalyst unit for the removal of toluene, Czech. J. Phys., 2006, 56, B1156 CrossRef.
- M. Magureanu, N. B. Mandache, J. Hu, R. Richards, M. Florea and V. I. Parvulescu, Plasma-assisted catalysis total oxidation of trichloroethylene over gold nano-particles embedded in SBA-15 catalysts, Appl. Catal., B, 2007, 76, 275 CrossRef CAS.
- H. Uyama, T. Nakamura, S. Tanaka and O. Matsumoto, Catalytic effect of iron wires on the syntheses of ammonia and hydrazine in a radio-frequency discharge, Plasma Chem. Plasma Process., 1993, 13, 117 CrossRef CAS.
- Plasma chemistry and catalysis in gases and liquids, ed. V. I. Pârvulescu, M. Magureanu and P. Lukes, John Wiley & Sons, 2012 Search PubMed.
- H. H. Kim, Y. Teramoto, A. Ogata, H. Takagi and T. Nanba, Plasma catalysis for environmental treatment and energy applications, Plasma Chem. Plasma Process., 2016, 36, 45 CrossRef CAS.
- J. C. Whitehead, Plasma catalysis: a solution for environmental problems, Pure Appl. Chem., 2010, 82, 1329 CAS.
- M. Russo, G. Iervolino, V. Vaiano and V. Palma, Non-thermal plasma coupled with catalyst for the degradation of water pollutants: a review, Catalysts, 2020, 10, 1438 CrossRef CAS.
- L. Chen, X. Zhang, L. Huang and L. Lei, Post-plasma catalysis for methane partial oxidation to methanol: role of the copper-promoted iron oxide catalyst, Chem. Eng. Technol., 2010, 33, 2073 CrossRef CAS.
- P. Mehta, P. Barboun, D. B. Go, J. C. Hicks and W. F. Schneider, Catalysis enabled by plasma activation of strong chemical bonds: a review, ACS Energy Lett., 2019, 4, 1115 CrossRef CAS.
- K. Sugiyama, K. Akazawa, M. Oshima, H. Miura, T. Matsuda and O. Nomura, Ammonia synthesis by means of plasma over MgO catalyst, Plasma Chem. Plasma Process., 1986, 6, 179 CrossRef CAS.
- H. Uyama and O. Matsumoto, Synthesis of ammonia in high-frequency discharges, Plasma Chem. Plasma Process., 1989, 9, 13 CrossRef CAS.
- J. R. Shah, J. M. Harrison and M. L. Carreon, Ammonia plasma-catalytic synthesis using low melting point alloys, Catalysts, 2018, 8, 437 CrossRef.
- J. Shah, T. Wu, J. Lucero, M. A. Carreon and M. L. Carreon, Nonthermal plasma synthesis of ammonia over Ni-MOF-74, ACS Sustain. Chem. Eng., 2018, 7, 377 CrossRef.
- L. G. Siemsen, The synthesis of ammonia from hydrogen and atomic nitrogen on the rhenium (110) surface, Iowa State University, 1990 Search PubMed.
- M. B. Yaala, A. Saeedi, D. F. Scherrer, L. Moser, R. Steiner, M. Zutter, M. Oberkofler, G. De Temmerman, L. Marot and E. Meyer, Plasma-assisted catalytic formation of ammonia in N2–H2 plasma on a tungsten surface, Phys. Chem. Chem. Phys., 2019, 21, 16623 RSC.
- X. Bai, S. Tiwari, B. Robinson, C. Killmer, L. Li and J. Hu, Microwave catalytic synthesis of ammonia from methane and nitrogen, Catal. Sci. Technol., 2018, 8, 6302 RSC.
- A. K. Brewer and R. R. Miller, The synthesis of ammonia in the low voltage arc, J. Am. Chem. Soc., 1931, 53, 2968 CrossRef CAS.
- Y. Kubota, K. Koga, M. Ohno and T. Hara, Synthesis of ammonia through direct chemical reactions between an atmospheric nitrogen plasma jet and a liquid, Plasma Fusion Res., 2010, 5, 042 CrossRef.
- K. H. Rouwenhorst, Y. Engelmann, K. van't Veer, R. S. Postma, A. Bogaerts and L. Lefferts, Plasma-driven catalysis: green ammonia synthesis with intermittent electricity, Green Chem., 2020, 22, 6258 RSC.
- Q. Xie, S. Zhuge, X. Song, M. Lu, R. Ruan, Y. Nie and J. Ji, Hydrogenation of plasma-excited nitrogen over an alumina catalyst for ammonia synthesis, Int. J. Hydrogen Energy, 2018, 43, 14885 CrossRef CAS.
- X. Zhu, X. Hu, X. Wu, Y. Cai, H. Zhang and X. Tu, Ammonia synthesis over γ-Al2O3 pellets in a packed-bed dielectric barrier discharge reactor, J. Phys. D, 2020, 53, 164002 CrossRef CAS.
- B. S. Patil, Plasma (catalyst)-assisted nitrogen fixation: reactor development for nitric oxide and ammonia production, 2017 Search PubMed.
- F. Gorky, J. M. Lucero, J. M. Crawford, B. Blake, M. A. Carreon and M. L. Carreon, Plasma-induced catalytic conversion of nitrogen and hydrogen to ammonia over zeolitic imidazolate frameworks ZIF-8 and ZIF-67, ACS Appl. Mater. Interfaces, 2021, 13, 21338 CrossRef CAS PubMed.
- J. R. Shah, F. Gorky, J. Lucero, M. A. Carreon and M. L. Carreon, Ammonia synthesis via atmospheric plasma catalysis: zeolite 5A, a case of study, Ind. Eng. Chem. Res., 2020, 59, 5167 CrossRef CAS.
- F. Gorky, M. A. Carreon and M. L. Carreon, Experimental strategies to increase ammonia yield in plasma catalysis over LTA and BEA zeolites, IOP SciNotes, 2020, 1, 024801 CrossRef.
- J. Liu, X. Zhu, C. Zhou, J. Du, Y. Gan, G. Chen and X. Tu, Plasma-catalytic ammonia synthesis over BaTiO3 supported metal catalysts: process optimization using response surface methodology, Vacuum, 2022, 203, 111205 CrossRef CAS.
- T. A. B. J. van Raak, S. Li and F. Gallucci, Prevailing surface reactions in the plasma-catalytic ammonia synthesis with Ru/CeO2 and Ru/Ti-CeO2, Chem. Eng. J., 2023, 455, 140691 CrossRef CAS.
- X. Hu, X. Zhu, X. Wu, Y. Cai and X. Tu, Plasma-enhanced NH3 synthesis over activated carbon-based catalysts: effect of active metal phase, Plasma Processes Polym., 2020, 17, 2000072 CrossRef CAS.
- K. Li, S. Chen, H. Wang and F. Wang, Plasma-assisted ammonia synthesis over Ni/LaOF: dual active centers consisting of oxygen vacancies and Ni, Appl. Catal., A, 2023, 650, 118983 CrossRef CAS.
- Y. Liu, C. W. Wang, X. F. Xu, B. W. Liu, G. M. Zhang, Z. W. Liu, Q. Chen and H. B. Zhang, Synergistic effect of Co–Ni bimetal on plasma catalytic ammonia synthesis, Plasma Chem. Plasma Process., 2022, 42, 267 CrossRef CAS.
- F. A. Herrera, G. H. Brown, P. Barboun, N. Turan, P. Mehta, W. F. Schneider, J. C. Hicks and D. B. Go, The impact of transition metal catalysts on macroscopic dielectric barrier discharge (DBD) characteristics in an ammonia synthesis plasma catalysis reactor, J. Phys. D, 2019, 52, 224002 CrossRef CAS.
- M. Iwamoto, M. Akiyama, K. Aihara and T. Deguchi, Ammonia synthesis on wool-like Au, Pt, Pd, Ag, or Cu electrode catalysts in nonthermal atmospheric-pressure plasma of N2 and H2, ACS Catal., 2017, 7, 6924 CrossRef CAS.
- T. Mizushima, K. Matsumoto, J. I. Sugoh, H. Ohkita and N. Kakuta, Tubular membrane-like catalyst for reactor with dielectric-barrier-discharge plasma and its performance in ammonia synthesis, Appl. Catal., A, 2004, 265, 53 CrossRef CAS.
- T. Mizushima, K. Matsumoto, H. Ohkita and N. Kakuta, Catalytic effects of metal-loaded membrane-like alumina tubes on ammonia synthesis in atmospheric pressure plasma by dielectric barrier discharge, Plasma Chem. Plasma Process., 2007, 27, 1 CrossRef CAS.
- E. N. Eremin, A. N. Maltsev and V. M. Belova, Behaviour of a Catalyst in a Glow-discharge Plasma, Russ. J. Phys. Chem., 1969, 43, 443 Search PubMed.
- M. D. Bai, X. Y. Bai, Z. T. Zhang and M. D. Bai, Synthesis of ammonia in a strong electric field discharge at ambient pressure, Plasma Chem. Plasma Process., 2000, 20, 511 CrossRef.
- A. Gómez-Ramírez, J. Cotrino, R. M. Lambert and A. R. González-Elipe, Efficient synthesis of ammonia from N2 and H2 alone in a ferroelectric packed-bed DBD reactor, Plasma Sources Sci. Technol., 2015, 24, 065011 CrossRef.
- J. Hong, M. Aramesh, O. Shimoni, D. H. Seo, S. Yick, A. Greig, C. Charles, S. Prawer and A. B. Murphy, Plasma catalytic synthesis of ammonia using functionalized-carbon coatings in an atmospheric-pressure non-equilibrium discharge, Plasma Chem. Plasma Process., 2016, 36, 917 CrossRef CAS.
- P. Peng, Y. Li, Y. Cheng, S. Deng, P. Chen and R. Ruan, Atmospheric pressure ammonia synthesis using non-thermal plasma assisted catalysis, Plasma Chem. Plasma Process., 2016, 36, 1201 CrossRef CAS.
- K. Aihara, M. Akiyama, T. Deguchi, M. Tanaka, R. Hagiwara and M. Iwamoto, Remarkable catalysis of a wool-like copper electrode for NH3 synthesis from N2 and H2 in non-thermal atmospheric plasma, Chem. Commun., 2016, 52, 13560 RSC.
- D. Xie, Y. Sun, T. Zhu, X. Fan, X. Hong and W. Yang, Ammonia synthesis and by-product formation from H2O, H2 and N2 by dielectric barrier discharge combined with an Ru/Al2O3 catalyst, RSC Adv., 2016, 6, 105338 RSC.
- G. Akay and K. Zhang, Process intensification in ammonia synthesis using novel coassembled supported microporous catalysts promoted by nonthermal plasma, Ind. Eng. Chem. Res., 2017, 56, 457 CrossRef CAS.
- A. Gómez-Ramírez, A. M. Montoro-Damas, J. Cotrino, R. M. Lambert and A. R. González-Elipe, About the enhancement of chemical yield during the atmospheric plasma synthesis of ammonia in a ferroelectric packed bed reactor, Plasma Processes Polym., 2017, 1600081 CrossRef.
- H. H. Kim, Y. Teramoto, A. Ogata, H. Takagi and T. Nanba, Atmospheric-pressure nonthermal plasma synthesis of ammonia over ruthenium catalysts, Plasma Processes Polym., 2017, 14, 1600157 CrossRef.
- P. Peng, Y. Cheng, R. Hatzenbeller, M. Addy, N. Zhou, C. Schiappacasse, D. Chen, Y. Zhang, E. Anderson, Y. Liu, P. Chen and R. Ruan, Ru-based multifunctional mesoporous catalyst for low-pressure and non-thermal plasma synthesis of ammonia, Int. J. Hydrogen Energy, 2017, 42, 19056 CrossRef CAS.
- P. Mehta, P. Barboun, F. A. Herrera, J. Kim, P. Rumbach, D. B. Go, J. C. Hicks and W. F. Schneider, Overcoming ammonia synthesis scaling relations with plasma-enabled catalysis, Nat. Catal., 2018, 1, 269 CrossRef.
- P. Peng, P. Chen, M. Addy, Y. Cheng, E. Anderson, N. Zhou, C. Schiappacasse, Y. Zhang, D. Chen, R. Hatzenbeller and Y. Liu, Atmospheric plasma-assisted ammonia synthesis enhanced via synergistic catalytic absorption, ACS Sustain. Chem. Eng., 2018, 7, 100 CrossRef.
- Y. Wang, M. Craven, X. Yu, J. Ding, P. Bryant, J. Huang and X. Tu, Plasma-enhanced catalytic
synthesis of ammonia over a Ni/Al2O3 catalyst at near-room temperature: insights into the importance of the catalyst surface on the reaction mechanism, ACS Catal., 2019, 9, 10780 CrossRef CAS PubMed.
- S. Li, T. Van Raak and F. Gallucci, Investigating the operation parameters for ammonia synthesis in dielectric barrier discharge reactors, J. Phys. D Appl. Phys., 2019, 53, 014008 CrossRef.
- B. S. Patil, N. Cherkasov, N. V. Srinath, J. Lang, A. O. Ibhadon, Q. Wang and V. Hessel, The role of heterogeneous catalysts in the plasma-catalytic ammonia synthesis, Catal. Today, 2021, 362, 2 CrossRef CAS.
- S. Li, Y. Shao, H. Chen and X. Fan, Nonthermal plasma catalytic ammonia synthesis over a Ni catalyst supported on MgO/SBA-15, Ind. Eng. Chem. Res., 2022, 61, 3292 CrossRef CAS.
- J. Hong, S. Prawer and A. B. Murphy, Production of ammonia by heterogeneous catalysis in a packed-bed dielectric-barrier discharge: influence of argon addition and voltage, IEEE Trans. Plasma Sci., 2014, 42, 2338 Search PubMed.
- J. Hong, S. Prawer and A. B. Murphy, Plasma catalysis as an alternative route for ammonia production: status, mechanisms, and prospects for progress, ACS Sustain. Chem. Eng., 2018, 6, 15 CrossRef CAS.
- Y. Ma, Y. Tian, Y. Zeng and X. Tu, Plasma synthesis of ammonia in a tangled wire dielectric barrier discharge reactor: effect of electrode materials, J. Energy Inst., 2021, 99, 137 CrossRef CAS.
- Q. Xie, S. Zhuge, X. Song, M. Lu, F. Yu, R. Ruan and Y. Nie, Non-thermal atmospheric plasma synthesis of ammonia in a DBD reactor packed with various catalysts, J. Phys. D: Appl. Phys., 2019, 53, 064002 CrossRef.
- Y. Gorbanev, Y. Engelmann, K. van't Veer, E. Vlasov, C. Ndayirinde, Y. Yi, S. Bals and A. Bogaerts, Al2O3-Supported Transition Metals for Plasma-Catalytic NH3 Synthesis in a DBD Plasma: Metal Activity and Insights into Mechanisms, Catalysts, 2021, 11, 1230 CrossRef CAS.
- N. V. D. Long, M. Al-Bared, L. Lin, K. Davey, N. N. Tran, N. Pourali, K. K. Ostrikov, E. Rebrov and V. Hessel, Understanding plasma-assisted ammonia synthesis via crossing discipline borders of literature: a critical review, Chem. Eng. Sci., 2022, 24, 11809 Search PubMed.
- S. Gershman, H. Fetsch, F. Gorky and M. L. Carreon, Identifying regimes during plasma catalytic ammonia synthesis, Plasma Chem. Plasma Process., 2022, 42, 731 CrossRef CAS.
- Z. Chen, S. Jaiswal, A. Diallo, S. Sundaresan and B. E. Koel, Effect of Porous Catalyst Support on Plasma-Assisted Catalysis for Ammonia Synthesis, J. Phys. Chem. A, 2022, 126, 8741 CrossRef CAS PubMed.
- D. Zhou, R. Zhou, R. Zhou, B. Liu, T. Zhang, Y. Xian, P. J. Cullen, X. Lu and K. K. Ostrikov, Sustainable ammonia production by non-thermal plasmas: status, mechanisms, and opportunities, Chem. Eng. J., 2021, 421, 129544 CrossRef CAS.
- T. W. Liu, F. Gorky, M. L. Carreon and D. A. Gómez-Gualdrón, Energetics of reaction pathways enabled by N and H radicals during catalytic, plasma-assisted NH3 synthesis, ACS Sustain. Chem. Eng., 2022, 10, 2034 CrossRef CAS.
- F. Gorky, H. M. Nguyen, J. M. Lucero, S. Guthrie, J. M. Crawford, M. A. Carreon and M. L. Carreon, CC3 porous organic cage crystals and membranes for the non-thermal plasma catalytic ammonia synthesis, Chem. Eng. J. Adv., 2022, 11, 100340 CrossRef CAS.
- Y. Wang, W. Yang, S. Xu, S. Zhao, G. Chen, A. Weidenkaff, C. Hardacre, X. Fan, J. Huang and X. Tu, Shielding protection by mesoporous catalysts for improving plasma-catalytic ambient ammonia synthesis, J. Am. Chem. Soc., 2022, 144, 12020 CrossRef CAS PubMed.
- L. R. Winter, B. Ashford, J. Hong, A. B. Murphy and J. G. Chen, Identifying surface reaction intermediates in plasma catalytic ammonia synthesis, ACS Catal., 2020, 10, 14763 CrossRef CAS.
- K. H. Rouwenhorst, H. G. Burbach, D. W. Vogel, J. N. Paulí, B. Geerdink and L. Lefferts, Plasma-catalytic ammonia synthesis beyond thermal equilibrium on Ru-based catalysts in non-thermal plasma, Catal. Sci. Technol., 2021, 11, 2834 RSC.
- K. van't Veer, Y. Engelmann, F. Reniers and A. Bogaerts, Plasma-catalytic ammonia synthesis in a DBD plasma: role of microdischarges and their afterglows, J. Phys. Chem. C, 2020, 124, 22871 CrossRef.
- J. Hong, S. Pancheshnyi, E. Tam, J. J. Lowke, S. Prawer and A. B. Murphy, Kinetic modelling of NH3 production in N2–H2 non-equilibrium atmospheric-pressure plasma catalysis, J. Phys. D, 2017, 50, 154005 CrossRef.
- H. Zhao, G. Song, Z. Chen, X. Yang, C. Yan, S. Abe, Y. Ju, S. Sundaresan and B. E. Koel, In situ identification of NNH and N2H2 by using molecular-beam mass spectrometry in plasma-assisted catalysis for NH3 synthesis, ACS Energy Lett., 2021, 7, 53 CrossRef.
|
This journal is © The Royal Society of Chemistry 2023 |
Click here to see how this site uses Cookies. View our privacy policy here.