DOI:
10.1039/D3RA05433K
(Paper)
RSC Adv., 2023,
13, 27984-27996
NiFe2O4@SiO2–Cu as a novel and efficient magnetically recoverable nanocatalyst for regioselective synthesis of β-thiol-1,2,3-triazoles under benign conditions†
Received
10th August 2023
, Accepted 13th September 2023
First published on 20th September 2023
Abstract
A green, mild and eco-friendly approach for the three component one-pot regioselective synthesis of 1,2,3-triazoles from thiiranes has been introduced in the presence of NiFe2O4@SiO2–Cu as a new and recoverable nanocatalyst. First, the NiFe2O4 nanoparticles have been produced through a solid-state reaction of hydrated nickel sulfate, hydrated iron(III) nitrate, NaOH and NaCl salts, and then calcined at 700 °C. Next, in order to protect the ferrite particles from oxidation and aggregation, the NiFe2O4 was core-shelled using tetraethyl orthosilicate (TEOS) and converted to NiFe2O4@SiO2. Finally, the novel NiFe2O4@SiO2–Cu nanocomposite was successfully prepared by adding copper(II) chloride solution and solid potassium borohydride. The catalyst has been characterized by FT-IR, SEM, EDX, VSM, ICP-OES, TEM and XRD techniques. The 1,3-dipolar cyclization of 1,2,3-triazoles was performed successfully in water at room temperature in high yields. The recoverability and reusability of the heterogeneous NiFe2O4@SiO2–Cu have also been investigated using VSM, SEM and FT-IR analyses. The catalyst was used four times in consecutive runs without considerable loss of activity. The presented procedure provides significant benefits such as using water as a green solvent, absence of hazardous organic solvents, high yields, benign conditions and recyclability of the magnetic catalyst.
1. Introduction
Multi-component reactions (MCRs), in which three or more reactants react to produce only one product, provide an easy and practical process for generating intricate molecules with structural complexity.1 The eco-friendliness, perfect regioselectivity high product yields, short reaction time and convenience of the method are among the benefits of these types of reactions.
Moreover, one-pot reactions have recently received a lot of attention in various fields such as industrial chemistry, organic synthesis, biomedical, production of bioactive reagents, pharmaceutical investigations and drug discovery.2–5 These reactions provide excellent facilities for versatile preparation of a wide diversity of organic compounds especially biologic active molecules which have benefits such as high atom economy, escape of time-consuming protection-deprotection steps, making them certainly better than classical multi-step synthetic procedures.6–9 These approaches are effective because several synthetic transformations and bond-forming steps can be carried out in a single pot, while circumventing several purification procedures at the same time. A one-pot procedure can thus minimize chemical waste, save time, and simplify practical aspects.10–12 Furthermore, in the growing field of organocatalysis,13 organocatalysts are extremely effective reagents in achieving a one-pot, multi-step synthesis. This is evidenced by a dramatic increase of impressive syntheses over the past decade.14–17
1,2,3-Triazoles have been considered as one of the most prominent and substantial intermediates in pharmaceutical and biological industries. They show unique activities such as antioxidants, analgesic, antimicrobial, anti HIV, anticancer, local anaesthetic, anticonvulsant, antiproliferative, antiallergic, antiviral, antitubercular, antifungal, antibacterial, anti-inflammatory and antimalarial.18–26
Recently, the Huisgen 1,3-dipolar cycloaddition between azides and alkynes has been utilized to manufacture the 1,2,3-triazoles.27 Although, one-pot synthesis of β-hydroxy-1,2,3-triazoles has been reported using click reaction of azides, alkynes and epoxides catalyzed by copper catalysts,28–43 but the use of thiiranes in the mentioned reaction has been investigated only in two cases.44,45
Recently, the diverse synthetic reactions have been improved and facilitated using heterogeneous catalysts.46–48 Moreover, magnetic nanoparticles have received great attention as green heterogeneous catalysts in organic synthesis due to their convenient synthesis, easy separation, high degree of catalytic activity and chemical stability, operational simplicity, eco-friendliness, and recoverability using an external magnetic field without the need for filtration and leaching or loss of the catalyst.49–51
However, the nano-ferrites always suffer from adsorption problems because they have a large surface to volume ratio and can develop strong magnetic attractions that lead to self-aggregation and a decrease in the amount of functional groups on the surface.52
To prevent agglomeration of magnetic nanoparticles and improve their efficiency, their surfaces could be modified using various materials such as silica, metals, polymers, metal oxides, surfactant, etc.53 The coating of nano-ferrites with a functionalized shell, not only reduces the aggregation of the nanoparticles in the solution, but also improves the efficiency of the catalyst by increasing the amount of functional groups on the surface. Furthermore, in recent years, the nanostructures coated with silica, metal and metal oxides have been widely used as selective detector of biochemical substances,54,55 easy separable catalysts in organic transformations, and smart nanomaterials utilized in the biomedical area to develop the role of biosynthesized nanoparticles for ameliorating human health through broad applications in the targeted drug delivery, controlled release drug delivery, wound dressing, tissue scaffolding, and medical implants.56–58
In continuation of our research on the successful synthesis of magnetic nanoparticles,59–64 herein, we would like to introduce the novel recoverable NiFe2O4@SiO2–Cu nanocatalyst for the three-component regioselective procedure for synthesis of β-thiol-1,4-disubstituted-1,2,3 triazoles from sodium azide, thiiranes, and terminal alkynes in water at room temperature (Scheme 1).
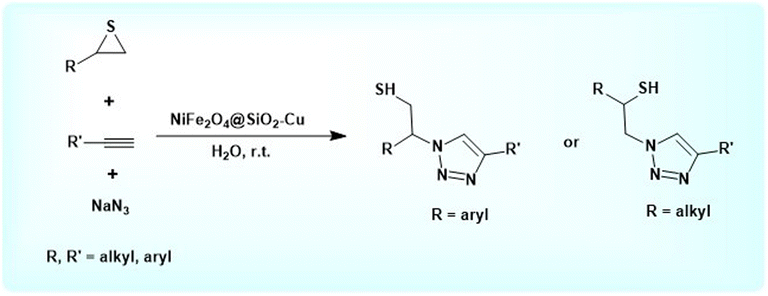 |
| Scheme 1 Synthesis of β-thiol-1,2,3-triazoles from thiiranes catalyzed by NiFe2O4@SiO2–Cu. | |
2. Experimental
2.1. Materials and instruments
All chemical substrates were purchased from the Merck and Aldrich Chemical Companies and were used without further purification. FT-IR spectra were obtained by Thermo Nicolet Nexus 670 FT-IR, and 1H/13C NMR spectra were recorded on 500 MHz Bruker Avance spectrometer. HRMS analyses were also performed in the electron impact mode (EI) at 70 eV. Magnetic properties of nanoparticles were measured by a VSM (Meghnatis Daghigh Kavir Co., Kashan Kavir, Iran) at room temperature. Melting points were measured on an Electrothermal IA9100 microscopic digital melting point apparatus. Morphology and size distribution of the particles were examined by TEM using an EM10C-100 kV series microscope from the Zeiss Company, Germany. FESEM images were obtained using FESEM-TESCAN. The energy dispersive X-ray spectrometer (EDS) analysis was taken on a MIRA3 FE-SEM microscope (TESCAN, Czech Republic) equipped with an EDS detector (Oxford Instruments, UK). The crystalline structure of the catalyst was studied by X-ray diffraction on a Bruker D8-Advanced diffractometer with graphite-monochromatized Cu Kα radiation (λ = 1.54056 Å) at room temperature. The Cu content on the catalyst was determined by PerkinElmer Optima 7300DV ICP-OES analyzer.
2.2. Synthesis of NiFe2O4
NiFe2O4 nanoparticles were synthesized by a solid-state method according to our previously reported procedures.59 Concisely, in an agate mortar, NiSO4·6H2O (0.31 g, 2 mmol), Fe(NO3)3·9H2O (1.61 g, 4 mmol), NaOH (0.64 g, 16 mmol), and NaCl (0.232 g, 4 mmol) were placed in a molar ratio of 1
:
2
:
8
:
2 and ground for 1 hour. After 5 minutes of grinding, the mixture turned into a brown paste. The reaction proceeded with the release of heat. The reaction was completed in one hour. In order to remove the extra salts, the doughy mixture was washed with distilled water several times, and then it was dried at 80 °C for 2 h. The obtained product was calcined at 700 °C for 2 hours to afford the pure NiFe2O4 nanoparticles as a brown powder.
2.3. Preparation of NiFe2O4@SiO2
The surface of nickel ferrite nanoparticles was silica coated through an amended sol–gel procedure.64 First, NiFe2O4 (0.5 g) was added to a solution of ethanol (50 mL), distilled water (10 mL) and ammonium hydroxide (2.5 mL, 25%) and ultrasonicated for 2 h. Then 1.5 mL of tetraethyl orthosilicate (TEOS) was added dropwise to the prepared mixture and sonicated for a further 20 min. After continuous stirring at room temperature for 24 h, the NiFe2O4@SiO2 particles were collected, washed several times with distilled water and dried in an oven at 100 °C for 20 h.
2.4. Preparation of NiFe2O4@SiO2–Cu nanocomposite
First, NiFe2O4@SiO2 (1 g) was added to a solution of CuCl2·2H2O (0.68 g, 4 mmol) in distilled water (50 mL). The mixture was stirred strongly for 30 min and then KBH4 powder (0.1 g) was added gradually to reduce Cu2+ cations and produce the Cu nanoparticles. After continues stirring of the mixture for 1 hour at room temperature, the NiFe2O4@SiO2–Cu nanocomposite was generated and separated using a magnet, washed with distilled water and finally dried under air atmosphere.
2.5. Synthesis of thiiranes from epoxides: a general procedure
The different thiiranes were prepared using a previously reported solvent-free method.65 Briefly, a mixture of epoxide (1 mmol) and alumina supported thiourea (0.752 g, 25% w/w) was placed in a mortar and ground at room temperature. The progress of the reaction was tracked by TLC using n-hexane
:
EtOAc (10
:
4) as an eluent. After completion of the reaction, the mixture was washed with ethylacetate. Next, the washing solvents were evaporated under reduced pressure to obtain the crude thiirane, which was then purified using a short-column chromatography over silica gel.
2.6. Synthesis of β-thiol-1,2,3-triazoles from thiiranes catalyzed by NiFe2O4@SiO2–Cu in water at room temperature: a general procedure
A solution of the thiirane (1 mmol), alkyne (1 mmol) and NaN3 (0.078 g, 1.2 mmol) in H2O (5 mL) was placed in a round-bottomed flask equipped with a magnetic stirrer. After adding the NiFe2O4@SiO2–Cu nanocatalyst (0.02 g) to the solution, the mixture was stirred for an appropriate time at room temperature. The completion of the reaction was evaluated by TLC using n-hexane
:
EtOAc (10
:
2) as an eluent. Then, the nanocatalyst was separated applying an external magnetic field and accumulated for the next cycle. To obtain the product, the reaction mixture was extracted with ethyl acetate and then dried over anhydrous Na2SO4. The organic solvent was evaporated and the crude β-thiol-1,4-disubstituted-1,2,3-triazole was produced. The β-thiol-1,4-disubstituted-1,2,3-triazoles derivatives were purified through recrystallization with EtOH/H2O (1
:
1), and then characterized by HRMS (EI), FT-IR, 1H NMR and 13C NMR spectra. All products are known compounds and were confirmed by comparison of their spectra with those of valid samples;44,45 these data are given in the ESI.†
2.7. Recycling of NiFe2O4@SiO2–Cu nanocatalyst
After completion of the reaction, the magnetic nanoparticles of NiFe2O4@SiO2–Cu were separated using a simple magnet, washed several times with ethyl acetate, and dried under air atmosphere. The collected nanoparticles were reused in the next run without any remarkable loss of magnetic property or catalytic activity.
3. Results and discussion
3.1. Synthesis and characterization of NiFe2O4@SiO2–Cu nanocatalyst
Nickel ferrite nanoparticles with a large surface to volume ratio have high catalytic activity. However, they tend to aggregate and agglomerate, which subsequently leads to minimize the surface energies. The naked ferrite nanoparticles due to their high chemical activity are easily oxidized in air, which usually resulting in loss of magnetic property and the reduction of their dispersity. Therefore, coating of their surface with an inorganic layer such as silica, metal or nonmetal elementary substances is useful. The protecting shells not only prevent the accumulation of the particles in the solution, but also improve the efficiency of the catalyst by providing the more functional groups on its surface.45,64 Easy separation, recyclability, and reusability are among the advantages of nickel magnetic ferrites, which make them suitable supports for the synthesis of nanocomposites.
NiFe2O4@SiO2–Cu was prepared in a three-step process (Scheme 2). The new synthesized NiFe2O4@SiO2–Cu nanocatalyst was characterized by diverse methods such as vibration sample magnetometer (VSM), FT-IR, transmission electron microscopy (TEM), X-ray diffraction (XRD), field emission scanning electron microscope (FESEM), energy dispersive X-ray spectrometer (EDS), and inductively coupled plasma optical emission spectrometry (ICP-OES).
 |
| Scheme 2 Synthesis of NiFe2O4@SiO2–Cu nanocomposite. | |
3.1.1. Vibration sample magnetometer (VSM). Magnetic properties of NiFe2O4, NiFe2O4@SiO2 and NiFe2O4@SiO2–Cu nanoparticles were investigated by the vibrating sample magnetometer (VSM). The narrow cycles with low coercivity indicate the typical ferromagnetic behavior of the soft magnetic materials at room temperature. The saturation magnetization (Ms) value of NiFe2O4, NiFe2O4@SiO2 and NiFe2O4@SiO2–Cu was around 50, 21 and 5 emu g−1, respectively. Hence, the amount of Ms and the magnetic property are reduced by coating one layer on another. This is due to the presence of nonmagnetic layers of silica and copper in the nanocomposite structure (Fig. 1).
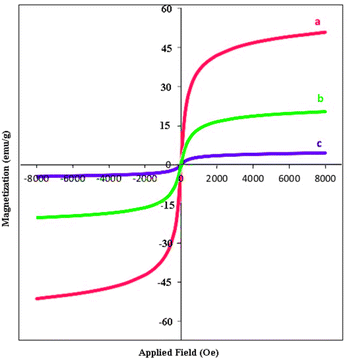 |
| Fig. 1 Magnetization curves of (a) NiFe2O4, (b) NiFe2O4@SiO2 and (c) NiFe2O4@SiO2–Cu. | |
3.1.2. Fourier transform infra-red (FT-IR) spectrum. The functional groups in the magnetic nanoparticles of NiFe2O4, NiFe2O4@SiO2 and NiFe2O4@SiO2–Cu were identified by the FT-IR spectroscopy (Fig. 2). The absorption peak at 590 cm−1 belongs to the vibration of metal oxide bonds (Fe–O and Ni–O) which shows the presence of NiFe2O4 nanoparticles. The absorption bands at 3446 and 1623 cm−1 correspond to the O–H stretching and bending modes in the adsorbed water, respectively.62
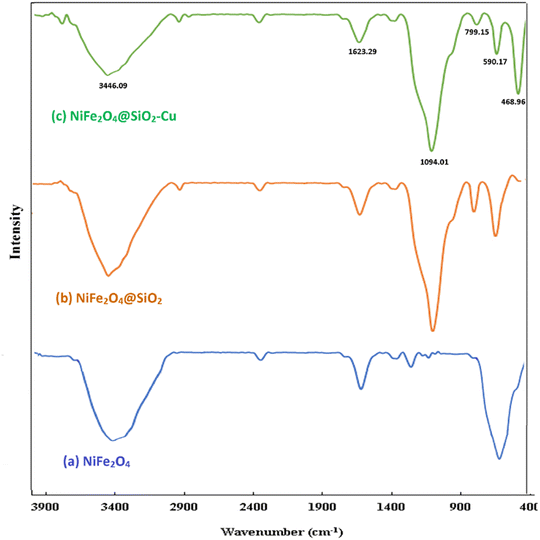 |
| Fig. 2 FT-IR (KBr) spectra of (a) NiFe2O4, (b) NiFe2O4@SiO2 and (c) NiFe2O4@SiO2–Cu. | |
The broad bands at 1094 and 799 cm−1 are related to the asymmetrical and symmetrical stretching vibrations of Si–O–Si, which confirm the presence of silica layers in the composite. An absorption peak appeared at 468 cm−1 is attributed to the bending vibrations of O–Si–O.66 The band corresponding to Cu–O stretching vibrations also appears in this region, which probably overlaps with the absorption band at 468 cm−1 and leads to an increase in its intensity.45
3.1.3. X-ray diffraction (XRD). The X-ray diffraction (XRD) patterns of NiFe2O4, NiFe2O4@SiO2 and NiFe2O4@SiO2–Cu nanoparticles are illustrated in Fig. 3. As shown, all the peaks of NiFe2O4, SiO2 and Cu particles are detectable. The diffraction peaks at 2θ = 18.55, 30.42°, 35.80°, 37.46°, 43.49°, 53.92°, 57.48°, 63.11° and 74.13° correspond to (111), (220), (311), (222), (400), (422), (511), (440) and (622) crystal planes of NiFe2O4, which confirm the synthesis of pure and crystalline NiFe2O4 nanoparticles. These peaks are compatible with the standard data (JCPDS 01-074-2081).43
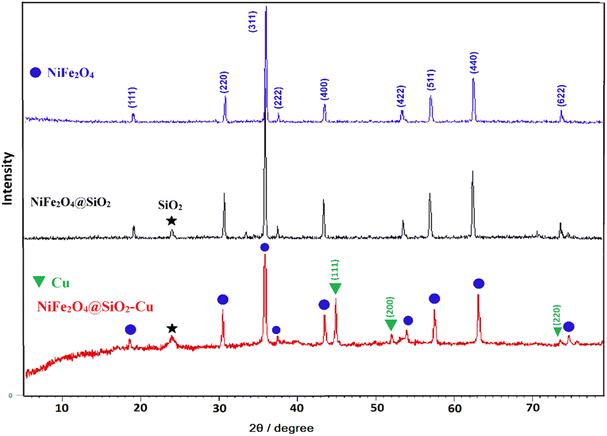 |
| Fig. 3 XRD patterns of NiFe2O4, NiFe2O4@SiO2 and NiFe2O4@SiO2–Cu. | |
The same patterns of characteristic peaks can be seen for NiFe2O4@SiO2, indicating that the embedded magnetite cores keep their crystalline phase after SiO2 covering. The diffraction peaks of Cu situated at 2θ = 43.7°, 50.7°, and 74.3° are related to the (111), (200), and (220) planes of the fcc structure, respectively and they are in agreement with copper standard (JCPDS 04-0836).44 The average crystallite size of nanoparticles is calculated using the Scherrer's formula (36 nm).
3.1.4. TEM and FESEM of NiFe2O4@SiO2–Cu. The morphology and size distribution of the as-prepared nanocomposite were checked by TEM and FESEM methods. TEM images of NiFe2O4@SiO2–Cu show the cores of nickel ferrite surrounded by the black silica layers. The copper nanoparticles are also visible as dark grains immobilized on silica layer (Fig. 4).
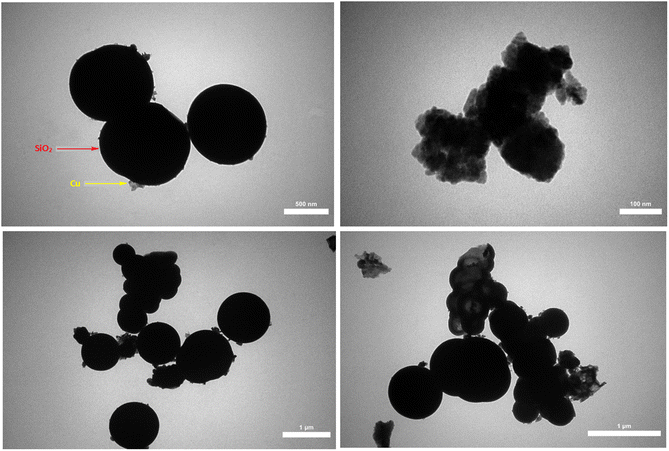 |
| Fig. 4 TEM images of NiFe2O4@SiO2–Cu. | |
FESEM images of NiFe2O4, NiFe2O4@SiO2 and NiFe2O4@SiO2–Cu are shown in Fig. 5. These images provide more detailed information on the morphology of the synthesized magnetic nanocomposite. As can be seen, the surface of the ferrite is completely covered by SiO2, and nickel ferrite particles are camouflaged under silica layers. In addition, the copper nanoparticles immobilized on the monodispersed NiFe2O4@SiO2 spheres are clearly visible in the images. The presence of nanoparticles with diameters ranging from 20 to 44 nm is confirmed through FESEM images. The obtained results are completely consistent with TEM and XRD data.
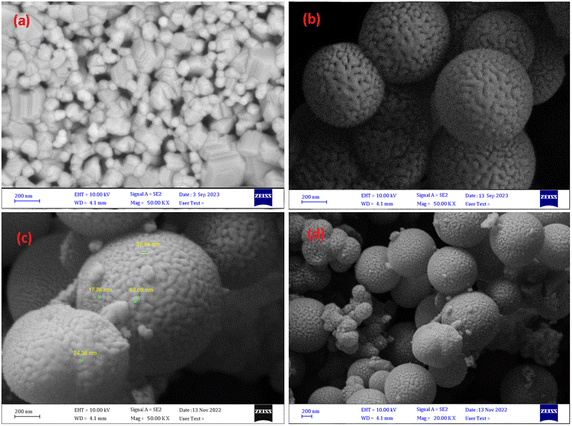 |
| Fig. 5 FESEM images of (a) NiFe2O4, (b) NiFe2O4@SiO2, (c) and (d) NiFe2O4@SiO2–Cu. | |
3.1.5. EDS of NiFe2O4@SiO2–Cu. The chemical composition of NiFe2O4@SiO2–Cu with weight and atomic percentage of the elements were detected using EDS technique and elemental mapping patterns. This analysis confirms the presence of Cu, Ni, Fe, Si and O elements in the structure of nanocomposite (Fig. 6). The higher peak intensity of Si element compared to Fe and Ni peaks indicates that NiFe2O4 nanoparticles are trapped by SiO2 and confirms the synthesized core–shell structure of NiFe2O4@SiO2. The exact concentration of Ni, Fe and Cu was determined by ICP-OES and the resulting amounts were 2.01, 3.38 and 2.35 wt% respectively, which are in high agreement with EDS data.
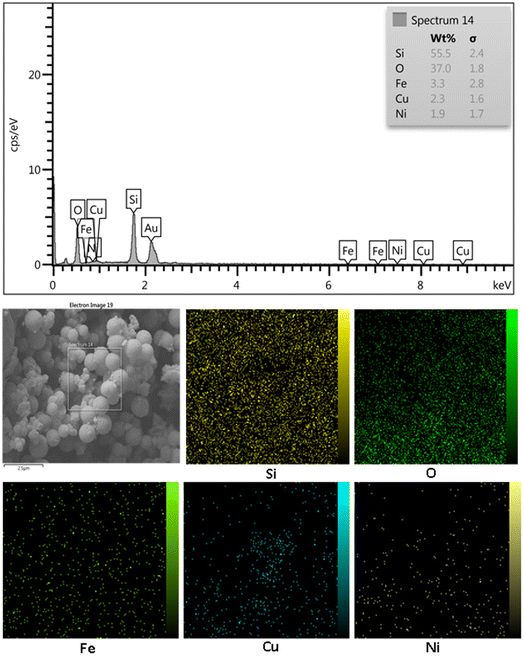 |
| Fig. 6 EDS of NiFe2O4@SiO2–Cu and elemental mapping of Fe, Ni, O, Si, Cu. | |
3.2. Synthesis of β-thiol-1,2,3-triazoles catalyzed by NiFe2O4@SiO2–Cu
The reaction conditions of the one-pot click synthesis of 2-phenyl-2-(4-phenyl-1H-1,2,3-triazol-1-yl)ethane-1-thiol from styrene episulfide, sodium azide and phenyl acetylene was optimized applying different conditions.
The various factors such as solvent, reaction time and quantity of catalyst and reactant were investigated. The results obtained are summarized in Table 1. The most satisfactory outcome was achieved using styrene episulfide (1 mmol), phenylacetylene (1 mmol), sodium azide (1.2 mmol) and NiFe2O4@SiO2–Cu (0.02 g) as catalyst in water at room temperature (Table 1, entry 4).
Table 1 Three-component reaction of styrene episulfide with phenylacetylene and sodium azide catalysed by NiFe2O4@SiO2–Cu under different conditionsa
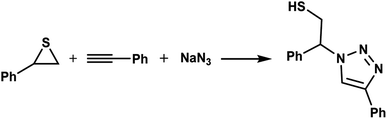
|
Entry |
NiFe2O4@SiO2–Cu (g) |
Solvent |
Time (h) |
Yieldb (%) |
All reactions were carried out with styrene episulfide (1 mmol), phenylacetylene (1 mmol) and sodium azide (1.2 mmol) at room temperature. Isolated yields. Catalysed by NiFe2O4. Catalysed by NiFe2O4@SiO2. Catalysed by Cu nanoparticles. |
1 |
— |
H2O |
20 |
0 |
2 |
0.01 |
H2O |
10 |
50 |
3 |
0.015 |
H2O |
10 |
80 |
4 |
0.02 |
H2O |
8 |
98 |
5 |
0.03 |
H2O |
8 |
98 |
6 |
0.02 |
CCl4 |
24 |
0 |
7 |
0.02 |
THF |
24 |
0 |
8 |
0.02 |
n-Hexane |
24 |
0 |
9 |
0.02 |
EtOAc |
3 |
65 |
10 |
0.02 |
DMF |
3 |
55 |
11 |
0.02 |
CH3CN |
8 |
93 |
12 |
0.02 |
EtOH |
8 |
95 |
13 |
0.02 |
MeOH |
8 |
95 |
14c |
0.02 |
H2O |
8 |
Trace |
15d |
0.02 |
H2O |
8 |
65 |
16e |
0.02 |
H2O |
8 |
95 |
It is important that in the absence of the catalyst, the reaction showed no improvement even after 20 h (entry 1). In order to optimize the catalyst quantity, the model reaction was tested utilizing different amounts of catalyst (0.01, 0.015, 0.02 and 0.03 g), and the desired result was obtained using 0.02 g. Increasing the catalyst quantity from 0.015 to 0.02 g not only decreased the reaction time but also increased the product yield (entries 2–4). Using more amounts of the catalyst did not affect the triazole yield (entry 5).
In order to study the effect of solvent, the model reaction was carried out in various solvents. The results revealed that the polar solvents were practical and useful whereas non-polar solvents were not appropriate to accomplish the reaction (entries 6–13).
Water as an abundant, green and eco-friendly solvent is superior to other solvents, and it was chosen as the favorable option (entry 4).
In order to evaluate the catalytic activity of the catalyst components, the model reaction was investigated separately using NiFe2O4, NiFe2O4@SiO2 and Cu under the optimal conditions (entries 14–16). The results showed that although the presence of NiFe2O4 and SiO2 in the catalyst structure increased the efficiency of the catalyst, copper nanoparticles played the most significant role in this regard. The highest product yield can be achieved in the presence of NiFe2O4@SiO2–Cu because the synergistic effect between components greatly improves the catalytic activity and selectivity.
The usability and generality of this research were investigated by the reaction of structurally diverse thiiranes with either electron-donating or withdrawing substituents and cyclic thiiranes in the presence of phenylacetylene, sodium azide and NiFe2O4@SiO2–Cu nanocatalyst under the optimum conditions (Table 2, entries 1–8). The reaction of some other alkynes such as aliphatic terminal alkynes and 4-methoxyphenyl acetylene with styrene episulfide was also examined under the optimized conditions (entries 9–11). The results show that all reactions were performed successfully within 8–10 h to give the corresponding 1,2,3-triazoles in 81–98% yields.
Table 2 Regioselective one-pot synthesis of β-thiol-1,2,3-triazoles from thiiranes catalysed by NiFe2O4@SiO2–Cua
Entry |
Thiirane (a) |
Alkyne |
Triazole (b) |
Time (h) |
Yieldb (%) |
m.p.45 (°C) |
All reactions were carried out with 1 mmol of thiirane in the presence of alkyne (1 mmol), sodium azide (1.2 mmol) and nano-NiFe2O4@SiO2–Cu (0.02 g) in water at room temperature. Yields refer to isolated pure products. |
1 |
 |
 |
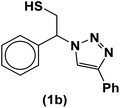 |
8 |
98 |
122–124 |
2 |
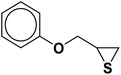 |
 |
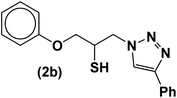 |
9 |
90 |
113–114 |
3 |
 |
 |
 |
8.5 |
82 |
154–157 |
4 |
 |
 |
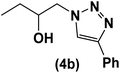 |
10 |
94 |
104–106 |
5 |
 |
 |
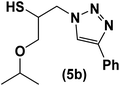 |
9 |
89 |
74–75 |
6 |
 |
 |
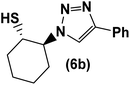 |
8 |
93 |
156–159 |
7 |
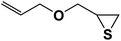 |
 |
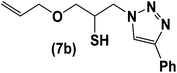 |
8.5 |
90 |
70 |
8 |
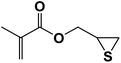 |
 |
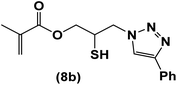 |
8 |
81 |
86–92 |
9 |
 |
 |
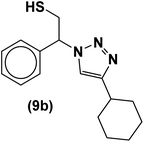 |
10 |
90 |
125–128 |
10 |
 |
 |
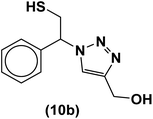 |
9.5 |
92 |
101–105 |
11 |
 |
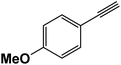 |
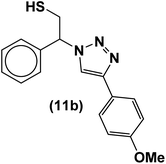 |
8.5 |
96 |
130–132 |
3.3. Recycling of NiFe2O4@SiO2–Cu catalyst
The other green aspect of this method was also investigated by the reusability of NiFe2O4@SiO2–Cu magnetic nanoparticles in one-pot synthesis of 2-phenyl-2(4-phenyl-1H-1,2,3-triazol-1-yl)ethane-1-thiol from styrene episulfide, sodium azide and phenyl acetylene under the optimized reaction conditions (Table 2, entry 1). After completion of the reaction, the nanoparticles were easily separated and collected by an external magnet, washed with ethyl acetate and then dried to use in the next cycles. The catalyst can be reused several times without the considerable loss of catalytic activity (Fig. 7). Furthermore, to study the reusability and persistence of NiFe2O4@SiO2–Cu particles, VSM, FESEM, FT-IR and TEM of the recycled catalyst were studied. The results showed that the structure of nanocatalyst was almost stable even after four runs (Fig. 8).
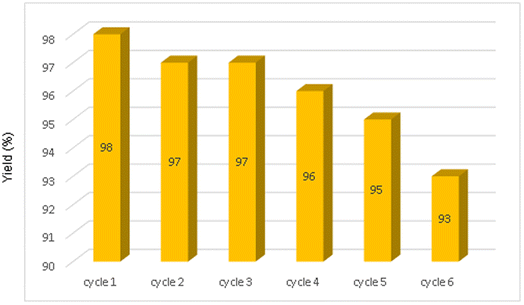 |
| Fig. 7 Recycling of NiFe2O4@SiO2–Cu in the synthesis of 2-phenyl-2-(4-phenyl-1H-1,2,3-triazol-1-yl)ethane-1-thiol. | |
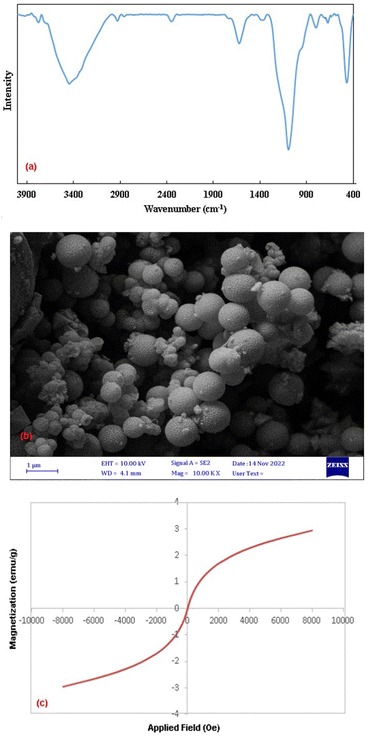 |
| Fig. 8 (a) FT-IR, (b) FESEM and (c) VSM of NiFe2O4@SiO2–Cu after four runs. | |
The extent of Ni, Fe and Cu leaching during catalytic reactions was investigated by ICPOES analysis of the supernatant liquid after removal of the catalyst. The results confirmed the absence of metals in the supernatant liquid.
3.4. Hot filtration test
The heterogeneity of the catalyst was confirmed through the hot filtration test. For this purpose, the catalyst was filtered after 2 hours in the model reaction at 100 °C, and the filtrate was allowed to react for additional 10 hours, but no progress of the reaction was seen in the absence of the catalyst, indicating no leakage of the catalyst into the reaction mixture. Therefore, NiFe2O4@SiO2–Cu is heterogeneous and is essential to perform the cyclization reaction.
3.5. Comparison of NiFe2O4@SiO2–Cu catalytic activity with other catalysts
The click synthesis of 1,2,3-triazole from thiiranes is a new topic and has not been considered so far, except in two recent cases reported by the authors of this paper.44,45 The privileges of the mentioned method were revealed by comparing the 1,3-dioplar reaction of styrene episulfide, phenyl acetylene and sodium azide in the presence of NiFe2O4@SiO2–Cu with the other two previously reported catalysts. In terms of temperature, recyclability and product yield, the present procedure is more favorable. The reaction is carried out in the presence of NiFe2O4@SiO2–Cu at room temperature and the product is obtained with higher yield. The most important advantage of this method is the completion of the reaction at low temperature under mild conditions, which indicates the higher efficiency of the newly synthesized nanocatalyst.
3.6. The proposed mechanism for regioselective synthesis of β-thiol-1,2,3-triazoles catalyzed by NiFe2O4@SiO2–Cu
The possible mechanism for the synthesis of β-thiol-1,2,3-triazole involves two pathways (A) and (B) (Scheme 3). NiFe2O4@SiO2–Cu simultaneously catalyzes both cleavage of the thiirane ring and 1,3-dipolar cycloaddition to produce triazoles.39,45 First, a non-covalent interaction is established between the azide and the metal of catalyst, and then the thiirane ring is activated by the catalyst through its Lewis acid property. Next, the azide is transferred from the catalyst and the ring opening of thiirane occurs to produce 2-azido-2-arylethanethiol (pathway A). In this pathway, the cleavage of thiirane rings is regioselective and thiiranes bearing aryl substituents due to the stability of benzyl carbocation prefer to be opened from the more hindered position via SN1 type of mechanism (α-cleavage); while the thiiranes with alkyl and allyl groups are effectively opened from less hindered place via SN2 type of mechanism (β-cleavage). In this pathway, the catalytic effect of NiFe2O4@SiO2–Cu was examined through the reaction between styrene episulfide and sodium azide in the absence of catalyst, and it was revealed that, only a very small amount of 2-azido-2-arylethanethiol had been produced. Consumption of reactants and also the production of 2-azido-2-phenylethanethiol intermediate were tracked by gas chromatography (GC) method and thin layer chromatography (TLC) runs of the reaction mixture, and it was found that 2-azido-2-arylethanethiol is rapidly formed, therefore, the 1,3-dipolar cycloaddition step is the rate-determining step (RDS).
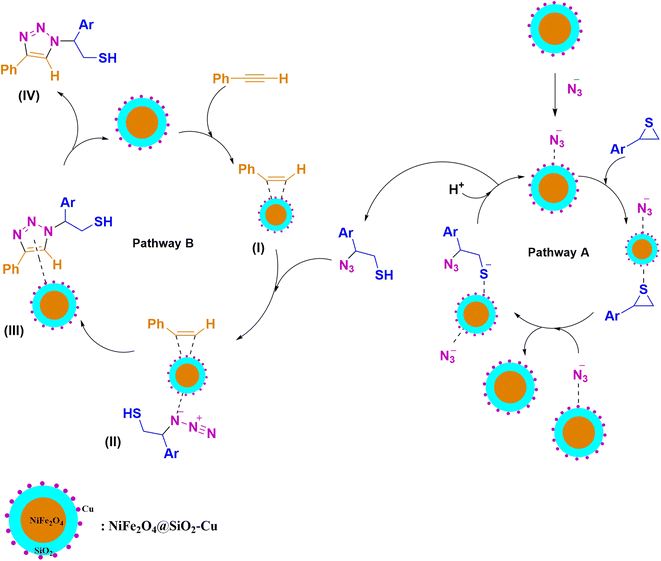 |
| Scheme 3 The mechanism proposed for the regioselective synthesis of β-thiol-1,2,3-triazole catalyzed by NiFe2O4@SiO2–Cu. | |
In pathway B, initially, the terminal alkyne is activated through π-complexation with catalyst to give intermediate (I).67 Then, the reaction of 2-azido-2-phenylethanethiol produced in pathway A with intermediate (I) leads to generate the intermediate (II), and 1,2,3-triazole (III) is subsequently created from the 1,3-dipolar cycloaddition between azide and intermediate (II). The consumption of the alkyne as well as the disappearing of the 2-azido-2-arylethanethiol intermediate, were monitored by the GC and TLC of the reaction mixture. Eventually, the catalyst nanoparticles were separated from intermediate (III), and 1,2,3-triazole (IV) was obtained.
4. Conclusions
In conclusion, the NiFe2O4@SiO2–Cu nanocomposite as a new magnetic nanocatalyst was successfully synthesized and characterized using various analytical techniques such as FT-IR, XRD, FESEM, EDS, ICP-OES, TEM, and VSM. Its unique efficacy in organic synthesis was investigated through a one-pot multi-component reaction for the synthesis of diverse β-thiol-1,4-disubstituted-1,2,3-triazoles, which hold chemical and potential biological significance, via a reaction involving sodium azide, terminal alkyne, and aliphatic/aromatic/cyclic thiiranes. The application of this nanocomposite in the aforementioned reaction resulted in the production of pure products with high yields, and acceptable reaction times. The current method proves highly suitable for obtaining a broad scope of 1,2,3-triazoles, which are considered valuable heterocyclic compounds in the pharmaceutical field. Furthermore, the as-prepared nanocatalyst demonstrated excellent recyclability, as it was easily recovered from the reaction mixture using an external magnet and reused for four consecutive runs. Overall, the notable characteristics of this approach encompass the utilization of the reusable catalytic system, one-pot procedure, mild reaction conditions, perfect regioselectivity, green solvent, readily accessible starting reactants, and effortless product filtration, as well as high yields of the target products. These privileged characteristics make this new approach environmentally attractive and cost effective.
Conflicts of interest
There are no conflicts to declare.
Acknowledgements
The financial support of this work by the Research Council of Payame Noor University is gratefully acknowledged.
References
- S. Saranya, K. R. Rohit, S. Radhika and G. Anilkumar, Org. Biomol. Chem., 2019, 17, 8048 RSC.
- L. M. Ramos, M. O. Rodrigues and B. A. D. Neto, Org. Biomol. Chem., 2019, 17, 7260 RSC.
- K. K. Das, S. Manna and S. Panda, Chem. Commun., 2021, 57, 441 RSC.
- L. Biesen and T. J. J. Müller, Adv. Synth. Catal., 2021, 363, 980 CrossRef CAS.
- D. Insuasty, J. Castillo, D. Becerra, H. Rojas and R. Abonia, Molecules, 2020, 25, 505 CrossRef PubMed.
- A. Ashraf, Z. Shafiq, K. Mahmood, M. Yaqub and W. Rauf, RSC Adv., 2020, 10, 5938 RSC.
- A. Singh, N. A. Mir, S. Choudhary, D. Singh, P. Sharma, R. Kantc and I. Kumar, RSC Adv., 2018, 8, 15448 RSC.
- S. A. R. Mulla, M. Y. Pathan, S. S. Chavan, S. P. Gample and D. Sarkar, RSC Adv., 2014, 4, 7666 RSC.
- J. C. Flores-Reyes, V. C. Cotlame-Salinas, I. A. Ibarra, E. González-Zamora and A. Islas-Jácome, RSC Adv., 2023, 13, 16091 RSC.
- R. Javahershenas and S. Nikzat, RSC Adv., 2023, 13, 16619 RSC.
- M. Rimaz, B. Khalili, G. Khatyal, H. Mousavi and F. Aali, Aust. J. Chem., 2017, 70, 1274 CrossRef CAS.
- C. Wang, Q. Li, S. Wang, G. Zhu, A. Zhu and L. Li, RSC Adv., 2021, 11, 38108 RSC.
- S. Mukherjee, J. W. Yang, S. Hoffmann and B. List, Chem. Rev., 2007, 107, 547 CrossRef PubMed.
- D.-H. Jhuo, B.-C. Hong, C.-W. Chang and G.-H. Lee, Org. Lett., 2014, 16, 2724 CrossRef CAS PubMed.
- Y. Hayashi, H. Gotoh, T. Hayashi and M. Shoji, Angew. Chem., 2005, 117, 4284 CrossRef.
- M. Marigo, T. C. Wabnitz, D. Fielenbach and K. A. Jørgensen, Angew. Chem., 2005, 117, 804 CrossRef.
- D. Enders, M. R. M. Huttl, C. Grondal and G. Raabe, Nature, 2006, 441, 861 CrossRef CAS PubMed.
- M. F. Mady, G. E. A. Awad and K. B. Jørgensen, Eur. J. Med. Chem., 2014, 84, 433 CrossRef CAS PubMed.
- H. N. Hafez, H. A. Abbas and A. R. El-Gazzar, Acta Pharm., 2008, 58, 359 CAS.
- M. D. Chen, S. J. Lu, G. P. Yuag, S. Y. Yang and X. L. Du, Heterocycl. Commun., 2000, 6, 421 CAS.
- F. C. Silva, M. C. B. V. de Souza, I. I. P. Frugulhetti, H. C. Castro, S. L. d. O. Souza, T. M. L. de Souza, D. Q. Rodrigues, A. M. T. Souza, P. A. Abreu, F. Passamani, C. R. Rodrigues and V. F. Ferreira, Eur. J. Med. Chem., 2009, 44, 373 CrossRef PubMed.
- A. Kamal, S. Prabhakar, M. J. Ramaiah, P. V. Reddy, C. R. Reddy, A. Mallareddy, N. Shankaraiah, T. L. N. Reddy, S. N. C. V. L. Pushpavalli and M. Pal-Bhadra, Eur. J. Med. Chem., 2011, 46, 3820 CrossRef CAS PubMed.
- K. M. Banu, A. Dinaker and C. Ananthnarayan, Indian J. Pharm. Sci., 1999, 61, 202 CAS.
- G. Ravi, A. R. Nath, A. Nagaraj, S. Damodhar and G. N. Rao, Der Pharma Chemica, 2014, 6, 223 Search PubMed.
- T. W. Kim, Y. Yong, S. Y. Shin, H. Jung, K. H. Park, Y. H. Lee, Y. Lim and K. Y. Jung, Bioorg. Chem., 2015, 59, 1 CrossRef PubMed.
- R. Raj, P. Singh, P. Singh, J. Gut, P. J. Rosenthal and V. Kumar, Eur. J. Med. Chem., 2013, 62, 590 CrossRef CAS PubMed.
- R. Eisavi and A. Karimi, RSC Adv., 2019, 9, 29873 RSC.
- F. Alonso, Y. Moglie, G. Radivoy and M. Yus, J. Org. Chem., 2011, 76, 8394 CrossRef CAS PubMed.
- F. Alonso, Y. Moglie, G. Radivoy and M. Yus, Adv. Synth. Catal., 2010, 352, 3208 CrossRef CAS.
- H. Sharghi, M. H. Beyzavi, A. Safavi, M. M. Doroodmand and R. Khalifeh, Adv. Synth. Catal., 2009, 351, 2391 CrossRef CAS.
- J. S. Yadav, B. V. S. Reddy, G. M. Reddy and D. N. Chary, Tetrahedron Lett., 2007, 48, 8773 CrossRef CAS.
- T. Boningari, A. Olmos, B. M. Reddy, J. Sommer and P. Pale, Eur. J. Org Chem., 2010, 2010, 6338 CrossRef.
- H. Sharghi, M. Hosseini-Sarvari, F. Moeini, R. Khalifeh and A. S. Beni, Helv. Chim. Acta, 2010, 93, 435 CrossRef CAS.
- B. S. P. Anil Kumar, K. Harsha Vardhan Reddy, G. Satish, R. Uday Kumar and Y. V. D. Nageswar, RSC Adv., 2014, 4, 60652 RSC.
- H. Naeimi and V. Nejadshafiee, New J. Chem., 2014, 38, 5429 RSC.
- K. Rajender Reddy, C. Uma Maheswari, K. Rajgopal and M. Lakshmi Kantam, Synth. Commun., 2008, 38, 2158 CrossRef.
- H. Esmaeili-Shahri, H. Eshghi, J. Lari and S. A. Rounaghi, Appl. Organomet. Chem., 2018, 32, e3947 CrossRef.
- N. Noshiranzadeh, M. Emami, R. Bikas and A. Kozakiewicz, New J. Chem., 2017, 41, 2658 RSC.
- H. Sharghi and I. Ghaderi, Org. Chem. Res., 2017, 3, 162 Search PubMed.
- H. Sharghi, A. Khoshnood, M. M. Doroodmand and R. Khalifeh, J. Iran. Chem. Soc., 2012, 9, 231 CrossRef CAS.
- H. Sharghi, S. Ebrahimpourmoghaddam, M. M. Doroodmand and A. Purkhosrow, Asian J. Org. Chem., 2012, 1, 377 CrossRef CAS.
- G. Kumaraswamy, K. Ankamma and A. Pitchaiah, J. Org. Chem., 2007, 72, 9822 CrossRef CAS PubMed.
- J. Lu, E. Q. Ma, Y. H. Liu, Y. M. Li, L. P. Mo and Z. H. Zhang, RSC Adv., 2015, 5, 59167 RSC.
- R. Eisavi and K. Naseri, RSC Adv., 2021, 11, 13061 RSC.
- R. Eisavi and F. Ahmadi, Sci. Rep., 2022, 12, 11939 CrossRef CAS PubMed.
- M. Boudart, Chem. Rev., 1995, 95, 661 CrossRef CAS.
- H. Hattori, Chem. Rev., 1995, 95, 537 CrossRef CAS.
- M. R. Othman, Z. Helwani, Martunus and W. J. N. Fernando, Appl. Organomet. Chem., 2009, 23, 335 CrossRef CAS.
- E. J. Ras and G. Rothenberg, RSC Adv., 2014, 4, 5963 RSC.
- M. Gilanizadeh and B. Zeynizadeh, Res. Chem. Intermed., 2020, 46, 2962 Search PubMed.
- V. Polshettiwar, R. Luque, A. Fihri, H. Zhu, M. Bouhrara and J. M. Basset, Chem. Rev., 2011, 111, 3036 CrossRef CAS PubMed.
- T. Wang, L. Zhang, H. Wang, W. Yang, Y. Fu, W. Zhou, W. Yu, K. Xiang, Z. Su, S. Dai and L. Chai, ACS Appl. Mater. Interfaces, 2013, 5, 12449 CrossRef CAS PubMed.
- M. Kumar, H. S. Dosanjh, Sonika, J. Singh, K. Monira and H. Singh, Environ. Sci.: Water Res. Technol., 2020, 6, 491 RSC.
- R. Verma, K. R. B. Singh, R. Verma and J. Singh, Luminescence, 2023, 38, 1393 CrossRef CAS PubMed.
- J. Singh, K. R. B. Singh, M. Kumar, R. Verma, R. Verma, P. Malik, S. Srivastava, R. P. Singh and D. Kumar, Mater. Adv., 2021, 2, 6665 RSC.
- K. R. B. Singh, V. Nayak, J. Singh, A. K. Singh and R. P. Singh, RSC Adv., 2021, 11, 24722 RSC.
- R. G. Kerry, K. R. B. Singh, S. Mahari, A. Bihari Jena, B. Panigrahi, K. C. Pradhan, S. Pal, B. Kisan, J. Dandapat, J. Singh, S. S. Pandey, R. P. Singh and S. Majhi, OpenNano, 2023, 10, 100126 CrossRef.
- J. Patel, K. R. B. Singh, A. K. Singh, J. Singh and A. K. Singh, Environ. Res., 2023, 235, 116674 CrossRef CAS PubMed.
- S. Hassanzadeh, R. Eisavi and M. Abbasian, Appl. Organomet. Chem., 2018, 32, e4520 CrossRef.
- R. Eisavi and S. Alifam, Phosphorus, Sulfur Silicon Relat. Elem., 2017, 193, 211 CrossRef.
- R. Eisavi, S. Ghadernejad, B. Zeynizadeh and F. M. Aminzadeh, J. Sulfur Chem., 2016, 37, 537 CrossRef CAS.
- R. Eisavi, F. Ahmadi, B. Ebadzade and S. Ghadernejad, J. Sulfur Chem., 2017, 38, 614 CrossRef CAS.
- S. Hassanzadeh, R. Eisavi and M. Abbasian, J. Sulfur Chem., 2019, 40, 240 CrossRef CAS.
- M. Mahmoudzadeh, E. Mehdipour and R. Eisavi, J. Coord. Chem., 2019, 72, 841 CrossRef CAS.
- R. Eisavi and B. Zeynizadeh, Phosphorus, Sulfur Silicon Relat. Elem., 2016, 191, 65 CrossRef CAS.
- F. Rubio, J. Rubio and J. L. Oteo, Spectrosc. Lett., 1998, 31, 199 CrossRef CAS.
- Y. Fang, K. Bao, P. Zhang, H. Sheng, Y. Yun, S. X. Hu, D. Astruc and M. Zhu, J. Am. Chem. Soc., 2021, 143, 1768 CrossRef CAS PubMed.
Footnote |
† Electronic supplementary information (ESI) available: FT-IR, 1H NMR and 13C NMR spectral information of β-thiol-1,4-disubstituted-1,2,3-triazoles. See DOI: https://doi.org/10.1039/d3ra05433k |
|
This journal is © The Royal Society of Chemistry 2023 |
Click here to see how this site uses Cookies. View our privacy policy here.