DOI:
10.1039/D3RA04863B
(Review Article)
RSC Adv., 2023,
13, 28975-28983
Research status of soda residue in the field of environmental pollution control
Received
19th July 2023
, Accepted 25th September 2023
First published on 4th October 2023
Abstract
High-quality soda ash (Na2CO3) is mainly produced using the ammonia–alkaline method, generating a significant amount of industrial waste called soda residue. In China, the annual production of soda residue exceeds 10 million tons. The large-scale open-air storage of soda residue not only occupies land but also causes severe pollution to the surrounding environment. Soda residue displays characteristics such as strong alkalinity, high reactivity, and a well-developed pore structure, making it a valuable raw material for producing environmentally functional materials. This article provided an overview and summary of soda residue, including its sources and hazards, basic properties, applications in environmental management (wastewater treatment, flue gas desulfurization, and soil remediation), and associated risks. The limitations of using soda residue in “waste to waste” technologies were also analyzed. Based on this analysis, the article suggests focusing on simultaneous removal of heavy metal ions using soda residue, safely disposing of and acquiring resources from metal-laden sludge, efficiently dechlorinating soda residue, using soda residue for contaminated soil solidification, stabilization, and assisted remediation, controlling pollution via green and circular utilization approaches, and assessing long-term risk.
1 Introduction
Soda ash, also known as sodium carbonate, is an essential basic chemical raw material widely used in various industries, such as construction materials, chemicals, metallurgy, textiles, food, national defense, and pharmaceuticals, contributing significantly to the national economy.1,2 Currently, soda ash is primarily produced via three methods, namely the combined-soda, the ammonia-soda, and the natural soda processes. The ammonia-soda process involves producing ammonium chloride and sodium carbonate, as shown in Fig. 1. It is one of the main methods for soda ash production and requires the consumption of large amounts of industrial salt, limestone (calcium carbonate), and ammonia. The ammonia-soda process offers advantages such as high product quality, low-salt soda ash production, large-scale continuous production suitability, and byproduct ammonia recycling. However, its drawbacks include limited product diversity, low raw material utilization, and substantial waste solution and residue generation, known as soda residue (white mud). Since 2003, China has been the global leader in soda ash production and output. Since 2020, the production capacity has reached 33.17 million tons, with an output of 27.592 million tons, generating an annual soda residue emission of 10 million tons.3–5
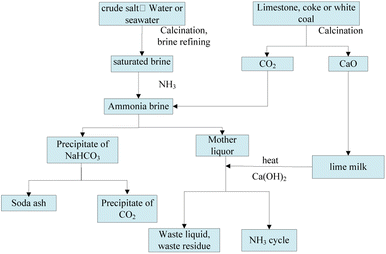 |
| Fig. 1 A schematic diagram of soda ash production via the ammonia-soda method. | |
The increasing discharge of soda residue has raised concerns about its associated hazards. The main risks of soda residue are related to the contamination caused by its filtrate and dust. The primary components of soda residue are CaCO3, CaCl2, and NaCl, with a chloride content exceeding the standard in the filtrate. Due to rapid urban development, the location of soda residue dumps has gradually become the center of urban areas. Soda residue is often left uncovered and exposed to the elements, forming a weathered, dry surface layer due to wind, sunlight, and rain. Soda residue dust typically affects the atmospheric environmental quality in an area of over 200
000 square kilometers. However, during periods of strong winds, the soda residue dust is carried into the atmosphere, severely polluting the environment6,7 Additionally, large amounts of soda residue are piled up or buried in tidal flats, occupying land resources and encroaching into the sea, forming harmful “white seas”.8 Furthermore, the high Ca2+, Mg2+, and Cl− concentrations in soda residue can disrupt soil structure, leading to soil salinization,9 posing a serious threat to the ecological environment.
In recent years, the stringent environmental requirements set by the government have made efficient soda residue treatment a pressing issue for domestic and international experts and companies. Several application strategies have been proposed for the resource utilization of soda residue (Fig. 2), including potential applications for construction engineering (such as road construction and building materials), chemicals (such as rubber, plastics, and papermaking), environmental engineering (such as wastewater treatment, coal combustion desulfurization agents, soil passivators, and amendments), and byproduct development (such as calcium chloride extraction).10–12 However, with a utilization rate below 5%, large-scale soda residue application has not yet been achieved in China. Waste-to-waste treatment technology has become an effective approach for promoting a circular economy. Utilizing soda residue for pollution control has become a new challenge in recent years due to its unique chemical composition, structure, and properties. This article provides an overview of soda residue applications in environmental protection fields such as wastewater treatment, flue gas desulfurization, and soil remediation. The analysis of existing problems and application prospects aims to provide technical references for expanding the soda residue resource utilization.
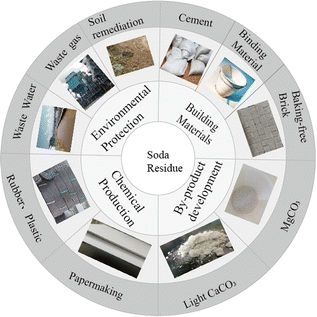 |
| Fig. 2 Soda residue resource utilization. | |
2 Sources and properties of soda residue
2.1 Sources
Soda residue mainly results from the saltwater refining, limestone calcination, and ammonia evaporation processes during soda ash production via the ammonia-soda method.13 (1) Saltwater refining process: crude salt solutions obtained from salt mines contain impurities, such as calcium, magnesium, and sulfate ions, which are removed before the solution enters the chlorine absorption tower by adding a Ca(OH)2 solution and Na2CO3. The specific reactions are shown in eqn (1)–(3). The insoluble or sparingly soluble substances formed during this process represent one of the sources of soda residue. (2) Limestone calcination process: since complete CaCO3 decomposition cannot be achieved during limestone calcination in a lime kiln, some impurities in the resultant lime slurry do not participate in subsequent reactions. The specific reactions are shown in eqn (4) and (5). Excess CaCO3, Ca(OH)2, SiO2, and other substances during this process represent another source of soda residue. (3) Ammonia evaporation process: the reaction between the lime slurry and NH4Cl during circulation soda ash production generates NH3. The remaining NaCl and the CaCl2 by product formed during this process contribute to the soda residue chloride component. The reactions are shown in eqn (6) and (7). |
Mg2+ + 2OH− → Mg(OH)2
| (1) |
|
NaCl + CO2 + NH3 + H2O → NH4Cl + NaHCO3
| (6) |
|
NH4Cl + Ca(OH)2 → CaCl2 + H2O + NH3
| (7) |
2.2 Properties
Soda residue appears as a white granular material with a pH between 10 and 12. It is classified as a strong alkaline waste residue containing elements such as Ca, C, Cl, Mg, Na, Si, and Al.14 The soda residue composition varies slightly between different alkali plants. The primary soda residue chemical components in some Chinese alkali plants are shown in Table 1. Its phase composition primarily comprises calcium salts, such as CaCO3, Ca(OH)2, CaCl2, CaSO4, and various other salts and insoluble materials.15 Studies have shown13,16 that soda residue has a loose structure and well-developed porosity, mainly comprising rod-shaped and spindle-shaped CaCO3 nano-aggregates, porous CaCO3, and rod-shaped CaSO4, with particle sizes ranging between 0.5 μm and 70.0 μm. The particle size distribution was about 60% in the 0.5 μm to 10.0 μm range, about 35% in the 10.0 μm to 35.0 μm, and about 5% in the 35.0 μm to 70.0 μm range.17
Table 1 Composition of soda residue in various domestic regions (mass fraction, %)a
Place of origin |
CaO |
K2O |
Cl− |
SiO2 |
Al2O3 |
Na2O |
Fe2O3 |
MgO |
SO3 |
LOI |
Ref. |
LOI: loss on ignition. |
Tangshan |
43.2 |
5.57 |
23 |
9.87 |
3.25 |
3.93 |
0.91 |
9.77 |
5.57 |
2.86 |
11 |
Guangdong |
39.16 |
0.05 |
4.42 |
2.78 |
2.02 |
1.15 |
0.57 |
7.53 |
4.22 |
36.47 |
18 |
Tangshan |
52.88 |
0.38 |
11.9 |
10.19 |
3.25 |
1.84 |
1.23 |
8.35 |
8.87 |
— |
7 |
Lianyungang |
58.73 |
— |
— |
11.16 |
3.97 |
— |
4.32 |
14.25 |
— |
— |
19 |
Shandong |
51.22 |
0.31 |
8.14 |
8.42 |
2.18 |
8.33 |
1.83 |
10.24 |
3.14 |
— |
20 |
Huai'an |
52.25 |
0.15 |
18.4 |
4.06 |
1.76 |
2.46 |
1.17 |
2.33 |
16.9 |
— |
21 |
Shandong |
62.81 |
0.17 |
0.16 |
10.2 |
9.00 |
0.23 |
1.31 |
12.5 |
0.3 |
— |
22 |
Huai'an |
32.25 |
0.18 |
— |
0.34 |
0.06 |
2.35 |
0.89 |
3.57 |
— |
49.03 |
23 |
3 Soda residue application for environmental protection
3.1 Wastewater treatment
Soda residue has a large pore volume and specific surface area, resulting in a strong adsorption capacity.13 Additionally, its aqueous solution is alkaline and carries a negative charge, exhibiting colloid properties,24 providing a crucial foundation for its application in environmental management. Previous studies have demonstrated that soda residue can purify wastewater by removing heavy metal ions, organic pollutants, and phosphates from the water. Removing impurities using soda residue involves multiple mechanisms, including precipitation, complexation reactions, ion exchange, and adsorption, with a significant focus on adsorption studies. Extensive research has investigated the adsorption characteristics of soda residue via adsorption kinetics and isotherm experiments. The adsorption properties of soda residue are presented in Table 2.
Table 2 The pollutant adsorption properties of soda residue and its modified materials in watera
Adsorbate |
Adsorbent |
T (°C) |
qe (mg g−1) |
C0 (mg L−1) |
pH |
Contact time |
Amount of adsorbent |
Kinetic model |
Isotherm model |
Ref. |
Comment: Fe3O4/SA-AR is a combination of magnetic sodium alginate-soda residue aerogel and Fe3O4, O-HAP refers to the optimization of hydroxyapatite production from soda residue, FeCAR/MnCAR refers to soda residue modification with FeCl3·6H2O (FeCAR) and MnSO4·H2O (MnCAR), and LSWM represents the leaching solution of white mud. |
Cd2+ |
Fe3O4/SA-AR |
— |
38.83 |
325 |
5 |
20 h |
0.3 g L−1 |
Pseudo-second-order |
Langmuir |
25 |
Pb2+ |
O-HAP |
165 |
1429 |
— |
5–7 |
14.5 h |
— |
Pseudo-second-order |
Langmuir |
26 |
As5+ |
FeCAR |
25 |
44.4 |
10 |
>7 |
10 h |
— |
Pseudo-second-order |
Langmuir |
19 |
As5+ |
MnCAR |
25 |
22.6 |
10 |
≤7 |
10 h |
— |
Pseudo-second-order |
Langmuir |
19 |
Fe2+, Mn2+, Cu2+, Zn2+, Cd2+ and Pb2+ |
Natural attapulgite + soda residue |
— |
— |
150 mg L−1 for Fe and 100 mg L−1 for other metals |
— |
— |
— |
Pseudo-second-order |
Freundlich |
27 |
Reactive bright red K-2BP |
LSWM |
20 |
416.7 |
100 |
12 |
90 s |
2 g L−1 |
— |
Freundlich |
28 |
Reactive light yellow K-6G |
LSWM |
20 |
454.5 |
100 |
12 |
90 s |
2 g L−1 |
— |
Freundlich |
28 |
Acid orange II |
LSWM |
20 |
769.2 |
100 |
12 |
90 s |
2 g L−1 |
— |
Freundlich |
28 |
Direct yellow |
LSWM |
20 |
2186.4 |
100 |
12 |
90 s |
2 g L−1 |
— |
Freundlich |
28 |
Acid blue 80 |
Soda residue |
|
440 |
300 |
10.5 |
6 h |
— |
|
— |
29 |
Emulsified oil |
LSWM |
10 |
— |
1500 |
12 |
10 min |
4 g L−1 |
— |
— |
30 |
Petroleum sulfonate |
LSWM |
30 |
3798 |
200 |
12 |
60 s |
— |
Pseudo-second-order |
Langmuir |
31 |
3.1.1 Heavy metal removal. More extensive metal mining and smelting activities in China have increased the severity of surface water contamination by heavy metals, such as Cd, Cu, Zn, Pb, and As.32 Even low doses of Cd, Pb, and As can be toxic to humans.33 The common methods currently used to remove metal ions from water include chemical precipitation, ion exchange, membrane filtration, coagulation, flocculation, flotation, electrochemical treatment, and adsorption. Precipitation and adsorption are combined to remove heavy metals from wastewater using soda residue. On the one hand, heavy metal ions precipitate continuously in alkaline conditions. On the other hand, both the precipitate and soda residue particle surfaces display a certain adsorption capacity for heavy metal ions. Precipitation plays a vital role during the initial removal stage, while surface adsorption dominates during the stable removal stage. The iron-manganese oxide-bound and the carbonate-bound heavy metal ion forms dominated the soda residue surface, with a lesser presence of organic forms.34,35However, one of the main limitations of the precipitation approach is the production of significant amounts of metal-laden sludge.36,37 Continuous scientific and technological progress has promoted research on safe methods for treating and recycling metal-laden sludge. First, hydrometallurgical technology (e.g., acid leaching and solvent extraction) is used for the stepwise recovery of valuable metals in sludge. Second, pyrometallurgical technology is used to simultaneously solidify heavy metals and prepare decorative materials (e.g., glass ceramics). Third, the heavy metal oxides in sludge can be separated and purified to prepare environmentally functional materials (e.g., NiCr2O4/CuCr2O4 catalytic reduction reagents and CuO/Cu2O oxygen carriers for chemical looping combustion). Fourth, it is used as an additive to produce construction materials.
Soda residue modification for utilization as an adsorbent has attracted increasing research attention to enhance its heavy metal adsorption efficiency in water. One approach is combining soda residue with sodium alginate and Fe3O4(Fe3O4/SA-AR) (see Fig. 3 for the preparation process, reactions (8) and (9)) to remove Cd2+ from water. Studies have shown that Cd2+ can be removed via –OH group complexation, Cd2+ and H+ ion exchange in –COOH groups, and electrostatic adsorption. The sodium ions in the long-chain sodium alginate polymer undergo ion exchange reactions with divalent cations, forming a cross-linked network structure and a hydrogel. Fe3O4 addition improves the soda residue dispersibility in the solution, enabling magnetic recovery and reuse. Furthermore, the modified soda residue exhibits random metal ion charge distribution, forming a wide range of multi-ion bonds via inter- and intrachain complexation to enhance the soda residue adsorption capacity.25 Another method involves immersing the soda residue in a (NH4)2HPO4 solution to obtain hydroxyapatite (O-HAP). This increases the number of hydroxyl groups on the soda residue surface and modifies the pore structure, enhancing the adsorption capacity to 12.0- to 45.8-fold higher than activated carbon.26
|
H+ + H2O + AR → Mn+ + Ca2+ + H+
| (8) |
|
Mn+ + Ca2+ + 2NaAlg → Ca(Alg)2 + 2Na+ + M(Alg)n
| (9) |
 |
| Fig. 3 The Fe3O4/SA-AR preparation process. | |
Research has shown38 that the adsorption process for a multi-metal system containing various heavy metals is considerably more complex than single-metal adsorption. This can be ascribed to the synergistic or antagonistic effect between different ions when multiple heavy metals are involved in the adsorption process, influencing the adsorption performance of individual metals. Cao et al.39 investigated the surface adsorption behavior of soda residue in the presence of Cd2+, Cu2+, and Zn2+ as competing ions. The results indicated that the competitive adsorption coefficient between Cd2+ and Zn2+ exhibited an upward trend as the concentration and pH increased, while that of Cu2+ declined. However, the competitive adsorption coefficient between Cd2+ and Zn2+ decreased at a higher temperature, while that of Cu2+ increased.
3.1.2 Organic pollutant removal from wastewater. Organic pollutants in wastewater mainly originate from the processes used in the textile, leather, paper, and printing industries and include oily organic pollutants generated during industrial production. Wastewater containing organic pollutants is characterized by high chemical oxygen demand (COD), low biochemical oxygen demand (BOD), and intense coloration. Many dyes and their degradation products in wastewater pose significant risks to aquatic organisms and human health.40 Traditional methods often do not remove organic pollutants due to their complex aromatic structures, hydrophobic nature, and poor biodegradability.41 However, the high specific surface area and large surface energy of soda residue allow for organic pollutant adsorption.Current research involving organic substance removal using soda residue mainly focuses on removing anionic and cationic dyes and oily organic pollutants. Soda residue has been employed for the adsorption-precipitation removal of reactive bright red K-2BP, reactive light yellow K-6G, acid orange II, direct yellow R,28 and Acid Blue 80 (ref. 29) from wastewater. The mechanism involves the fine-particle precipitation of hydroxides with large surface areas and high surface free energy in highly alkaline solutions, which adsorb anionic dyes.42 However, the soda residue adsorption capacity is significantly influenced by the pH of the solution. At lower initial pH values, only Fe3+ and Al3+ precipitates form, resulting in limited adsorption capacity due to the low Fe3+ and Al3+ content in the residue (Table 1). Conversely, a significant number of Mg(OH)2 and Ca(OH)2 crystals form at higher pH values, while the production of intermediate products during crystal formation increases the positive surface charge, consequently enhancing anionic dye adsorption via charge neutralization (reaction (10)). Furthermore, during precipitation, the newly formed three-dimensional network structure of hydroxides can capture and adsorb dyes, significantly improving dye removal efficiency. Surfactant-modified soda residue can mitigate the pH effect.43,44 For example, sodium dodecyl sulfate surfactant can maintain a negative surface charge within a wide pH range (pH 3–11), consequently exhibiting excellent adsorption performance for cationic dyes when the residue is modified.45 Surface-modified soda residue with surfactants also exhibits hydrophobic properties, displaying strong adsorption affinity for hydrophobic organic pollutants, facilitating their efficient removal from wastewater.
Furthermore, research was also conducted on the removal of oil-containing organic compounds, such as emulsified oil,30 oil emulsions,46 and petroleum sulfonate31 from wastewater, with promising adsorption results (Table 2). Studies have shown that soda residue and hydroxide particles formed in highly alkaline conditions restrict oil droplet migration via electrostatic attraction, hydrogen bonding, and particle surface adhesion, leading to the adsorption and encapsulation of oil droplets or organic components in the hydroxide crystals to effectively remove organic pollutants.47
|
 | (10) |
3.1.3 Application in eutrophication water control. Phosphorus plays a significant role in water body eutrophication.48 Some studies have shown that soda residue can be used to effectively remove phosphorus from water. Yan et al.49 modified soda residue using NaOH and HCl and tested their ability to remove phosphate from water. The maximum adsorption capacity values of the alkali- and acid-modified residues were 211.9 mg g−1 and 2.2 mg g−1, respectively, indicating that alkali modification significantly enhanced the phosphorus removal performance of soda residue, while acid modification exhibited a suppressive effect. The phosphorus removal mechanism of alkali-modified residue involves two main parts: the formation of Ca–P precipitation via the reaction between Ca2+ and H2PO4− and HPO42− in the solution system (reactions (11)–(13)) and the formation of phosphorus-containing precipitate due to the Mg, Al, and Fe ions (leached from the soda residue) reaction with H2PO4− and PO43− (reactions (14)–(16)).50 Wang et al.51 synthesized soda residue-based polymer adsorbents by combining 4
:
1 soda residue with kaolin and sodium silicate activators to remove phosphate from water. The amorphous calcium–aluminum–silicate formed during geopolymerization released hydroxide ions, facilitating insoluble calcium hydrogen phosphate (CaHPO4·2H2O) formation via the reaction between Ca2+ and phosphate ions to remove the phosphorus. The theoretical maximum adsorption capacity was 56.45 mg g−1. |
Ca2+ + HPO42− + 2H2O → CaHPO4·2H2O
| (11) |
|
Ca2+ + 2H2PO4− + H2O → Ca(H2PO5)2·H2O˙
| (12) |
|
5Ca2+ + 3HPO42− + 4OH− → Ca5(PO4)3OH + 3H2O
| (13) |
|
Mg2+ + 2H2PO4− → Mg(H2PO4)2˙
| (14) |
|
Al3+ + PO43− → AlPO4
| (15) |
|
Fe3+ + PO43− → FePO4
| (16) |
3.2 Flue gas desulfurization
China is the largest global coal producer. Approximately 0.014 ton of SO2 is produced as a byproduct for every ton of standard coal burned.52 SO2 stimulates respiratory diseases in humans and contributes to acid rain formation, which can damage the environment. The current desulfurization methods in China mainly include dry, semi-dry, and wet desulfurization.53 The basic principle of desulfurization involves gas–liquid/gas–solid acid–base neutralization. Although limestone/lime wet flue gas desulfurization (FGD) technology is widely used, large-scale limestone mining can lead to ecological destruction and resource depletion. Using soda residue as a substitute for limestone or lime can facilitate the development of new desulfurizing agents. This approach reduces desulfurization costs and improves desulfurization efficiency while producing gypsum as a desulfurization byproduct, which can satisfy solid waste resource utilization requirements. As shown in Fig. 4, the process involves the removal of sand and stone from the soda residue via sedimentation, followed by concentration to obtain soda residue sludge with a settling rate of around 85%. By replacing the chloride ions with wash water, a chlorine-removing desulfurizing agent is obtained for flue gas desulfurization.54
 |
| Fig. 4 The process flow chart of liquid desulfurizer preparation from soda residue. | |
The high alkalinity of soda residue (pH 12.0–12.4) ensures an alkaline environment in the slurry of the desulfurization tower, promoting economical, efficient desulfurization with costs 40–60% lower than when using the limestone/lime method, and a desulfurization efficiency of 99%, resulting in SO2 concentration in flue gas as low as 20 mg m−3.55 Additionally, the physical properties and chemical composition of the soda residue byproducts are similar to those produced via limestone desulfurization, making them suitable for application in construction products and cement retarders. Soda residue can also be combined with other solid waste for desulfurization. For example, mixing soda residue with carbide slag during flue gas desulfurization experiments showed that the particle sizes of the soda residue, the soda residue to carbide slag ratio, organic acid addition, and pH values impacted the soda residue desulfurization efficiency. The highest soda residue desulfurization rate (95%) was achieved at a pH exceeding 5, a particle size below 60 μm, a soda residue to carbide slag ratio of 1
:
1, and an addition of a certain amount of binary organic acid.56 Wet soda residue desulfurization occurs in three stages.57 The first involves the rapid reaction of OH−, Mg2+, and Ca2+ with SO2 in the slurry, leading to CaSO3 and MgSO3 formation, with some of the products oxidizing to sulfates (reactions (17) and (18)). The second stage involves the absorption of SO2 by HCO3− (reaction (19)). The third includes two types of reactions: one is the secondary reaction of Mg2+, Ca2+, and OH− (dissolved and ionized from Mg(OH)2, CaCO3, and CaO) with SO2 (reactions (20) and (21)), while the other involves the secondary reaction of CaSO3 and MgSO3 with SO2 (reaction (22)).
When HCl gas is present in the flue gas, the absorption efficiency of SO2 increases rather than decreases, and the enhancement effect is mainly observed during the later desulfurization stage. This is because HCl first reacts with the CaO in the desulfurizing agent to form calcium chloride hydroxide (CaClOH), which then reacts further with SO2 to achieve desulfurization. This indicates that modified soda residue can be used for simultaneous flue gas desulfurization and dechlorination.58
Therefore, utilizing soda residue as a flue gas desulfurizing agent in coal-fired power plants addresses the issue of soda residue disposal in the soda industry and helps control pollution emissions, facilitating a rational, effective circular economy.
|
Ca2+ + Mg2+ + 4OH− + 2SO2 → CaSO3 + MgSO3 + 2H2O
| (17) |
|
H2O + CO32− + SO2 → HCO3− + HSO3−
| (18) |
|
HCO3− + SO2 → HSO3− + CO2
| (19) |
|
Mg2+ + 2OH− + SO2 → MgSO3 + H2O
| (20) |
|
Ca2+ + 2OH− + SO2 → CaSO3 + H2O
| (21) |
|
CaSO3 + MgSO3 + 2H2O + 2SO2 → Ca(HSO3)2 + Mg(HSO3)2
| (22) |
3.3 Soil remediation
Soil contamination with toxic metals, pesticides, and organic pollutants remains a growing global concern. While the presence of pollutants in the soil is a natural consequence of rock weathering, elevated levels are mainly attributed to human activities.59,60 Many studies have shown that fully utilizing soda residue characteristics can condition the soil and stabilize the heavy metals in contaminated soil. On the one hand, soda residue is alkaline, with a high salt content (13%), and contains a significant amount of activated calcium ions and various trace elements essential for crop growth (such as Ca, Mg, Si, K, and P). Therefore, soda residue can be used to adjust acidic soil, produce compound plant fertilizers, supplement soil with trace elements, and promote organic matter decomposition.61 For example, Li62 et al. used soda residue to improve the acidity of tea plantation soil and alleviate aluminum toxicity. The results showed that adding soda residue increased the soil pH, effectively addressing soil acidification issues. Additionally, soda residue reduces the total soluble aluminum, exchangeable aluminum, and organically bound aluminum by forming and retaining hydroxyl aluminum polymers, increases exchangeable Ca, Mg, K, and Na, and enhances the effective cation exchange capacity to improve soil fertility. Huang63 et al. processed soda residue into calcium–magnesium compound fertilizers using a specific technique for agricultural production. The results indicated that this fertilizer increased crop yields and improved soil quality.
On the other hand, soda residue effectively immobilizes heavy metals in the soil, as shown in Table 3.
Table 3 The effect of ammonia soda residue on soil remediation
Passivation materials |
Pollution |
Type of soil |
Type of experiment |
Effect |
Ref. |
Soda residue |
Pb |
Artificially polluted soil |
Laboratory experiment |
After 28 days of curing, the lead content in the leachate is reduced to about 30% |
22 |
Soda residue |
Pb |
Artificially polluted soil |
Laboratory experiment |
The maximum adsorption amount of the tested specimen is 34 mg g−1, which is significantly higher than those of other clay materials |
67 |
Cement-soda residue |
Zn |
Artificially polluted soil |
Laboratory experiment |
Under freeze–thaw cycles, the initial Zn content increasing from 500 to 10 000 mg kg−1, the cumulative fraction of leached Zn2+ increased more than 5 times |
62 |
Fly ash + soda residue |
Pb |
Artificially polluted soil |
Laboratory experiment |
The soil strength increases significantly and is more suitable for the removal of lead from contaminated soil stains at low concentrations |
68 |
P-containing soda residue |
Pb |
Shooting range soil |
Pot experiment |
More than 60% of soil-Pb was transformed to residual fraction |
61 |
Biochar + soda residues |
Cd, Pb |
Pyrite mining area |
Field experiment |
Decreased the Cd/Pb contents of maize grains by 0.16–0.21 mg kg−1 (Cd) and 0.05–0.51 mg kg−1 (Pb) over the 3 year period |
66 |
Yan et al.64 used soda residue, calcined soda residue, phosphorus-containing soda residue, and calcined phosphorus-containing soda residue to remediate Pb-contaminated soil. The results indicated that phosphorus- and calcined phosphorus-containing soda residues achieved Pb passivation efficiencies exceeding 60% and 90%, respectively. Treatment significantly decreased the bioavailability and bioaccessible fraction of Pb. Moreover, phosphorus-containing soda residue moderately increased phosphorus nutrients in the soil without significantly affecting its physicochemical properties. Liu et al.65 used a soda residue cement composite solidification agent to treat Zn-contaminated soil and discussed the effect of the curing time, binder ratio, and Zn2+ concentration on its unconfined compressive strength. The results showed that a higher Zn2+ concentration led to Zn(OH)2 formation during the solidification process, consequently reducing the unconfined compressive strength of the soil.
In addition, studies have also examined the simultaneous passivation and remediation of heavy metals co-contaminated soils using soda residue. Wei et al.61 employed soda residue-modified biochar for the simultaneous remediation of Cd and Pb co-contaminated soil. The results indicated that the yield of maize grown in the co-contaminated soil increased by approximately 10 tons per hectare over three years, while the Cd and Pb content in the maize grains met the Chinese feed additive standards. Furthermore, soda residue-modified biochar application significantly increased the soil pH and reduced the heavy metal reactivity. Hydration, precipitation, and adsorption represent the main mechanisms for immobilizing soil pollution using soda residue. Hydration refers to the primary reaction that occurs when alkali residue is introduced into the soil and persists throughout the soil remediation process.68 Complex chemical reactions take place between the soil and alkali residue components, such as CaCO3, Ca(OH)2, SiO2, and Al2O3, generating several hydration products,69 as shown in eqn (23)–(28). The formation of various hydration products contributes to soil compaction, improves the leaching characteristics, and enhances the adsorption and encapsulation of the hydration products.
|
CaCO3 + Ca(OH)2 → CaCO3·Ca(OH)2
| (23) |
|
CaCO3 + 2CaO + SiO2 + (n + 1)H2O → CaSiO3·CaCO3·Ca(OH)2·nH2O
| (24) |
|
SiO2 + Ca(OH)2 + nH2O → CaO·SiO2·(n + 1)H2O
| (25) |
|
Al2O3 + Ca(OH)2 + nH2O → CaO·Al2O3·(n + 1)H2O
| (26) |
|
Ca(OH)2 + SiO2 + nH2O → CaO·SiO2·(n + 1)H2O
| (27) |
|
2Ca(OH)2 + CaCO3 + SiO2 + nH2O → CaSiO3·CaCO3·Ca(OH)2·(n + 1)H2O
| (28) |
Furthermore, soda residue provides alkalinity to acidic, contaminated soils and generates insoluble precipitates, which serve as the primary immobilization and stabilization products for heavy metals. Studies have shown that heavy metals in acidic soils exhibit high reactivity.70,71 Soda residue addition significantly increases the soil alkalinity and the number of exchangeable cations.60 For instance, Pb and Zn in soil react with OH− and CO32− to form precipitates.66,72 The reactions are represented by eqn (29)–(32). The forms of the precipitates are influenced by pH, as shown in eqn (33). The Zn precipitate types vary as the pH level increases.73 However, high heavy metal concentrations in the soil can facilitate the rapid formation of substantial precipitates, which, to some extent, hinder the hydration process.74
|
Pb2+ + 2OH− → Pb(OH)2
| (29) |
|
Pb2+ + CO32− → PbCO3
| (30) |
|
2Pb2+ + 2OH− + CO32− → Pb2(OH)2CO3
| (31) |
|
Zn2+ + 2OH− → Zn(OH)2
| (32) |
|
[Zn(OH2)6]2+ → [Zn(OH)]+ → [Zn(OH)2]0 → [Zn(OH)3]− → [Zn(OH)4]2−
| (33) |
In addition, soda residue application increases the soil pH and promotes calcium zeolite formation during the solidification process, consequently enhancing heavy metal adsorption.75 This is because higher alkalinity can neutralize a significant number of H+ ions in acidic soils, providing more heavy metal ion adsorption sites. The generated calcium zeolite presents a larger surface area. The abundant anions on the soda residue surface can adsorb more metal cations to achieve charge balance.61,76
4 The risks and challenges of soda residue in environmental applications
Although soda residue displays considerable potential for environmental protection, the ecological and environmental risks associated with its use should not be overlooked.
(1) A large amount of sludge is generated: during alkaline sludge wastewater treatment, the metal ions or organic substances in the wastewater form sludge or sediment after precipitation, neutralization, and other treatments. The treatment and disposal of alkaline heavy metal-containing sludge remain a global challenge, causing severe water and soil pollution when not treated correctly.77
(2) Dechlorination and desulfurization wastewater generation: to reduce equipment corrosion by chlorine, the soda residue solution requires dechlorination treatment, inevitably producing concentrated and harmful chlorinated wastewater. Moreover, soda residue desulfurization wastewater is characterized by high pH, which is toxic to organisms, disrupting their living environment and physiological functions, and inhibiting gymnosperm growth.78
(3)Application limitations: using soda residue as an adsorbent or precipitant to remove pollutants from water often requires strict control of the operational conditions and certain modifications. This increases adsorbent cost and causes this approach to remain experimental, restricting application for large-scale wastewater treatment.
(4) Enhanced absorption and accumulation of harmful elements in crops: in addition to the main Ca, Na, Si, and Al components, soda residue also contains small amounts of harmful elements, such as Hg, Cd, Cu, F, Cl, As, Pb, and Ni. Using soda residue as a passivating agent for soil amendment during soil pollution remediation poses significant ecological risks.79,80 Wang et al.77 reported that these elements in soda residue were harmful during heavy metal-contaminated soil remediation. For example, adding soda residue to soil planted with Brassica plants can increase cadmium bioavailability and uptake by plant roots. Soda residue application can also significantly increase the water-soluble fluoride in the soil, leading to fluoride accumulation in crops.
(5) Soil salinization and alkalization: soda residues contain about 4% sodium chloride and several soluble salts, of which CaCO3 is a highly viscous inert salt. Therefore, soda residue lead to salt accumulation, soil crusting, plant water uptake inhibition, physiological plant activity interference, and soil chemistry alteration. This initiates and exacerbates soil salinization, further promoting land degradation and reducing arable land productivity.81–83
5 Conclusion and prospects
Due to its small particle size, large specific surface area, high pH, charged nature, and solubility, soda residue exhibits strong adsorption capacity. Furthermore, its surface area can be increased via appropriate modification to enhance its adsorption performance. Although soda residue and its modified forms show considerable potential in various environmental protection applications, such as wastewater treatment, flue gas desulfurization, and soil remediation, several technical and research challenges remain that must be addressed to improve utilization. The following are research challenges in the environmental application of soda residue:
(1) Current research mainly focuses on removing individual heavy metals using soda residue, while surface water pollution often involves the coexistence of multiple heavy metals. Each metal ion has an optimal pH for removal, which varies among different metal ions. Therefore, it is important to examine the appropriate conditions, removal efficiency, and mechanisms to simultaneously remove multiple metal ions using soda residue to efficiently purify wastewater containing multiple metals. Additionally, since current research primarily concentrates on Cd, Cu, Zn, Pb, and As, it is necessary to investigate a broader heavy metal range.
(2) Although a mature methodological approach is available for treating and disposing of ordinary sludge, removing heavy metals from the alkaline sludge produced by soda residue is more challenging. This impedes the industrial application of soda residue, necessitating the development and exploration of new treatment and removal techniques.
(3) The compositions of soda residue generated by different processes vary. Using a large quantity of chlorine- and salt-containing soda residue as a flue gas desulfurization agent can damage equipment. Therefore, research should focus on improving the soda residue dechlorination and desalination processes.
(4) The high alkalinity of soda residue and the presence of trace Hg, Cd, Cu, F, Cl, As, Pb, Ni, and other pollutants can cause soil salinization and groundwater pollution when applied in large quantities. Therefore, a long-term tracking risk evaluation is necessary before using soda residue in soil.
Author contributions
Yonglan Zong: writing – original draft; Jiantao Gong and Yonglin Wu: writing – optimization and modification; Jilai Zhang and Youbo Su: supervision; Tianguo Li and Chenglei Hu: conceptualization; Ming Jiang: writing – review and editing.
Conflicts of interest
There are no conflicts to declare.
Acknowledgements
The authors gratefully acknowledge the Yunnan Agricultural Foundation Research Projects (202101BD070001-113).
References
- R. Jadeja and A. Tewari, J. Hazard. Mater., 2007, 147, 148–154 CrossRef CAS PubMed.
- M. Cichosz, U. Kiełkowska, K. Skowron, Ł. Kiedzik, S. Łazarski, M. Szkudlarek, B. Kowalska and D. Żurawski, Materials, 2022, 15, 4828 CrossRef CAS PubMed.
- D. A. Matthews, Water, Air, Soil Pollut., 2003, 146, 55–73 CrossRef CAS.
- S. Şener, Chem. Eng. J., 2008, 138, 207–214 CrossRef.
- T. Kasikowski, R. Buczkowski and M. Cichosz, Int. J. Prod. Econ., 2008, 112, 971–984 CrossRef.
- Q. Wang, J. Li, G. Yao, X. Zhu, S. Hu, J. Qiu, P. Chen and X. Lyu, Constr. Build. Mater., 2020, 241, 117994 CrossRef CAS.
- D. Xu, W. Ni, Q. Wang, C. Xu and K. Li, J. Cleaner Prod., 2021, 307, 127262 CrossRef CAS.
- Z. Zhang, C. Xie, Z. Sang and D. Li, Sustainability, 2022, 14, 13661 CrossRef CAS.
- T. Kasikowski, R. Buczkowski, B. Dejewska, K. Peszyńska-Białczyk, E. Lemanowska and B. Igliński, J. Cleaner Prod., 2004, 12, 759–769 CrossRef.
- X. Zhao, C. Liu, L. Wang, L. Zuo, Q. Zhu and W. Ma, Cem. Concr. Compos., 2019, 98, 125–136 CrossRef CAS.
- W. Guo, Z. Zhang, Z. Xu, J. Zhang, Y. Bai, Q. Zhao and Y. Qiu, Constr. Build. Mater., 2022, 333, 127352 CrossRef CAS.
- H. Gong, L. Zhao, X. Rui, J. Hu and N. Zhu, J. Hazard. Mater., 2022, 432, 128668 CrossRef CAS PubMed.
- C. Li, Y. Liang, L. Jiang, C. Zhang and Q. Wang, Constr. Build. Mater., 2021, 300, 123981 CrossRef CAS.
- Z. Wang, X. Lyu, G. Yao, P. Wu, J. Wang and J. Wei, J. Cleaner Prod., 2020, 262, 121345 CrossRef CAS.
- H. Wang, X. Zhao, H. Gao, T. Yuan and X. Zhang, Constr. Build. Mater., 2023, 366, 130214 CrossRef CAS.
- W. Qi, Q. Ren, Q. Zhao, Y. Feng, W. Qi, Y. Han and Y. Huang, Constr. Build. Mater., 2022, 348, 128594 CrossRef CAS.
- C. J. Ma, X. R. Zhang, L. Han and Y. W. Gou, Shanxi Architecture, 2019, 45(14), 78–80 Search PubMed.
- S. Zhou, Y. Ling and J. Zhao, J. Civ. Environ. Eng., 2012, 2(1), 1–7 Search PubMed.
- Y. Yan, C. Chen, Q. Li, X. Sun and L. Wang, Desalin. Water Treat., 2016, 57, 20401–20410 CrossRef CAS.
- W. Yin, K. Zhang, S. Ouyang, X. Bai, W. Sun and J. Zhao, Front. Earth Sci., 2021, 9, 747675 CrossRef.
- F. Zha, D. Pan, L. Xu, B. Kang, C. Yang and C. Chu, Adv. Civ. Eng., 2018, 8595419 Search PubMed.
- F. Yan, X. Lina, T. Qi, Z. Junde and J. Bing, IOP Conf. Ser.: Earth Environ. Sci., 2021, 811, 012008 CrossRef.
- J. Zhang and Q. Wang, Int. J. Hydrogen Energy, 2013, 38, 13564–13571 CrossRef CAS.
- Q. Wang, J. Li, J. Zhang, P. Wu, X. Lyu, S. Hu, J. Qiu, X. Liu and H. Yu, J. Cleaner Prod., 2021, 295, 126433 CrossRef CAS.
- S. J. Wang, H. Bu, H. J. Chen, T. Hu, W. Z. Chen, J. H. Wu, H. J. Hu, M. Z. Lin, Y. Li and G. B. Jiang, Chem. Eng. J., 2020, 399, 125760 CrossRef CAS.
- Y. Yan, Y. Wang, X. Sun, J. Li, J. Shen, W. Han, X. Liu and L. Wang, Appl. Surf. Sci., 2014, 317, 946–954 CrossRef CAS.
- H. Chen, Y. Ai, Y. Jia, J. Li, M. Gu and M. Chen, Sci. Total Environ., 2022, 843, 157120 CrossRef CAS PubMed.
- G. Zhang, X. Li, Y. Li, T. Wu, D. Sun and F. Lu, Desalination, 2011, 274, 255–261 CrossRef CAS.
- M. X. Zhu, L. Lee, H. H. Wang and Z. Wang, J. Hazard. Mater., 2007, 149, 735–741 CrossRef CAS PubMed.
- R. Gao, F. Li, Y. Li and T. Wu, Chem. Eng. J., 2017, 309, 513–521 CrossRef CAS.
- L. Cheng, L. Ye, D. Sun, T. Wu and Y. Li, Chem. Eng. J., 2015, 264, 672–680 CrossRef CAS.
- L. Liu, Z. Yang, W. Yang, W. Jiang, Q. Liao, M. Si and F. Zhao, J. Environ. Sci., 2024, 139, 23–33 CrossRef.
- C. V. Mohod and J. D hote, J. Res. Innovation Food Sci. Technol., 2013, 2(7), 2992–2996 Search PubMed.
- F. Fu and Q. Wang, J. Environ. Manage., 2011, 92, 407–418 CrossRef CAS PubMed.
- S. Babel, J. Hazard. Mater., 2003, 97, 219–243 CrossRef CAS PubMed.
- Y. X. Zhang, T. Su, H. Y. Chen, Y. Zhang, Z. Geng, S. Y. Zhu, X. F. Xie, H. Zhang, Y. D. Gao and Y. Huo, Environ. Res., 2023, 216, 114462 CrossRef CAS PubMed.
- Y. Fei and Y. H. Hu, Chemosphere, 2023, 335, 139077 CrossRef CAS PubMed.
- J. He, C. S. Li, X. W. Wang, W. G. Sun and N. Mi, Acta Sedimentol. Sin., 2003,(3), 500–505 Search PubMed.
- X. Cao, J. C. Sun, C. J. Jing, Y. Gao, Y. Liuang and X. H. Long, Shangdong Sci, 2009, 22(6), 17–20 Search PubMed.
- Z. Liu, T. A. Khan, M. A. Islam and U. Tabrez, Bioresour. Technol., 2022, 354, 127168 CrossRef CAS PubMed.
- Y. Tu, G. Shao, W. Zhang, J. Chen, Y. Qu, F. Zhang, S. Tian, Z. Zhou and Z. Ren, Sci. Total Environ., 2022, 828, 154390 CrossRef CAS PubMed.
- S. Netpradit, P. Thiravetyan and S. Towprayoon, Water Res., 2003, 37, 763–772 CrossRef CAS PubMed.
- B. Nandi, A. Goswami and M. Purkait, Appl. Clay Sci., 2009, 42, 583–590 CrossRef CAS.
- X. Pan, M. Zhang, H. Liu, S. Ouyang, N. Ding and P. Zhang, Appl. Surf. Sci., 2020, 522, 146370 CrossRef CAS.
- L. Xu and J. Chen, Pollut. Control Technol., 2015, 28(1), 8 Search PubMed.
- T. Wu, D. J. Sun, Y. J. Li and G. C. Zhang, Adv. Mater. Res., 2011, 356–360, 1570–1574 Search PubMed.
- F. Li, L. Ye, Y. Li and T. Wu, RSC Adv., 2016, 6, 31092–31100 RSC.
- P. Cheng, Y. Liu, L. Yang, Q. Ren, X. Wang, Y. Chi, H. Yuan, S. Wang and Y. X. Ren, J. Environ. Chem. Eng., 2023, 11, 109377 CrossRef CAS.
- Y. Yan, X. Sun, F. Ma, J. Li, J. Shen, W. Han, X. Liu and L. Wang, J. Environ. Sci., 2014, 26, 970–980 CrossRef CAS PubMed.
- Y. Yan, X. Sun, F. Ma, J. Li, J. Shen, W. Han, X. Liu and L. Wang, J. Taiwan Inst. Chem. Eng., 2014, 45, 1709–1716 CrossRef CAS.
- Q. Wang, Y. R. Song, H. Z. Guo, B. F. Zhang, T. Yu and P. Yuan, Non-Met. Mines, 2022, 45(3), 76–81 Search PubMed.
- D. Yue, B. Han, Y. Sun and T. Yang, Waste Manage., 2014, 34, 1041–1044 CrossRef CAS PubMed.
- X. Zhang, L. Zhang, S. Liu, X. Zhu, P. Zhou, X. Cheng, R. Zhang, L. Zhang and L. Chen, J. Hazard. Mater., 2022, 423, 127179 CrossRef CAS PubMed.
- B. J. Wang, X. R. Geng and Z. H. Liu, Soda Ind., 2015,(6), 12–15 Search PubMed.
- X. F. Wang, F. Wang, G. J. Lu, J. Y. Huang, F. Zhang, Y. T. Feng and Y. Y. Liu, Res. Environ. Sci., 2018, 31(9), 6 Search PubMed.
- R. L. Bing, Y. H. Lian and Y. Y. Wang, Environ. Sci. Technol., 2006, 029(7), 21–22 Search PubMed , 25..
- Y. L. Ma and Y. F. Bai, Chin. J. Environ. Eng., 2001, 2(5), 74–80 CAS.
- L. J. Yang, Master degree Thesis, Beijing University of Chemical Technology, 2020 Search PubMed.
- C. Belviso, Processes, 2020, 8, 820 CrossRef CAS.
- S. Khalid, M. Shahid, N. K. Niazi, B. Murtaza, I. Bibi and C. Dumat, J. Geochem. Explor., 2017, 182, 247–268 CrossRef CAS.
- L. Shi and H. Luo, Trans. Nonferrous Met. Soc. China, 2009, 19, 1383–1388 CrossRef CAS.
- J. Y. Li, N. Wang, R. K. Xu and D. Tiwari, Pedosphere, 2010, 20, 645–654 CrossRef CAS.
- Z. H. Huang, Soda Ind., 2009,(1), 1005–8370 Search PubMed.
- Y. Yan, F. Qi, B. Seshadri, Y. Xu, J. Hou, Y. S. Ok, X. Dong, Q. Li, X. Sun, L. Wang and N. Bolan, Chemosphere, 2016, 162, 315–323 CrossRef CAS PubMed.
- J. Liu, F. Zha, L. Xu, B. Kang, C. Yang, Q. Feng, W. Zhang and J. Zhang, Cold Reg. Sci. Technol., 2020, 172, 102992 CrossRef.
- L. Wei, Y. Huang, L. Huang, Q. Huang, Y. Li, X. Li, S. Yang, C. Liu and Z. Liu, Agric., Ecosyst. Environ., 2021, 306, 107198 CrossRef CAS.
- F. Zha, H. Wang, L. Xu, C. Yang, B. Kang, C. Chu, Y. Deng and X. Tan, Environ. Earth Sci., 2020, 79, 230 CrossRef CAS.
- J. Liu, F. Zha, L. Xu, Y. Deng and C. Chu, in Proceedings of GeoShanghai 2018 International Conference: Geoenvironment and Geohazard, ed. A. Farid and H. Chen, Springer Singapore, Singapore, 2018, pp. 442–449 Search PubMed.
- X. An, D. Zuo, F. Wang and C. Liang, Environ. Earth Sci., 2022, 81, 508 CrossRef CAS.
- K. E. Giller, E. Witter and S. P. McGrath, Soil Boil. Biochem., 2009, 41, 2031–2037 CrossRef CAS.
- D. Adamczyk-Szabela, J. Markiewicz and W. M. Wolf, Water, Air, Soil Pollut., 2015, 226, 106 CrossRef PubMed.
- J. Ma, N. Yan, M. Zhang, J. Liu, X. Bai and Y. Wang, Sustainability, 2020, 12, 5852 CrossRef CAS.
- M. Yousuf, A. Mollah, R. K. Vempati, T.-C. Lin and D. L. Cocke, Waste Manage., 1995, 15, 137–148 CrossRef CAS.
- L. Calgaro, S. Contessi, A. Bonetto, E. Badetti, G. Ferrari, G. Artioli and A. Marcomini, J. Soils Sediments, 2021, 21, 1755–1768 CrossRef CAS.
- Y. Chen, C. Zhu, Y. Sun, H. Duan, W. Ye and D. Wu, J. Radioanal. Nucl. Chem., 2012, 292, 1339–1347 CrossRef CAS.
- J. Li, Q. Xue, P. Wang, Z. Li and Y. Du, Environ. Prog. Sustainable Energy, 2015, 34, 957–963 CrossRef CAS.
- X. Wang, X. Yan and X. Li, J. Integr. Agr., 2020, 19, 601–611 CrossRef CAS.
- Y. Sun, X. Chi and X. Yang, in 3rd International Conference on Bioinformatics and Biomedical Engineering, IEEE, Beijing, China, 2009, pp. 1–6 Search PubMed.
- H. Xiang, Z. Yang, X. Min, Y. Liang, C. Peng, X. Liu, R. Yuan, Q. Wang and F. Zhao, Hydrometallurgy, 2023, 221, 106121 CrossRef CAS.
- L. Liu, Z. Yang, F. Zhao, Z. Chai, W. Yang, H. Xiang, Q. Liao, M. Si and Z. Lin, Chem. Eng. J., 2023, 471, 144758 CrossRef CAS.
- J. He, X. Shi, Z. Li, L. Zhang, X. Feng and L. Zhou, Constr. Build. Mater., 2020, 242, 118126 CrossRef CAS.
- R. Machado and R. Serralheiro, Horticulturae, 2017, 3, 30 CrossRef.
- Q. Jiang, Y. He, Y. Wu, B. Dian, J. Zhang, T. Li and M. Jiang, Environ. Pollut., 2022, 312, 120094 CrossRef CAS PubMed.
|
This journal is © The Royal Society of Chemistry 2023 |
Click here to see how this site uses Cookies. View our privacy policy here.