DOI:
10.1039/D3RA04850K
(Paper)
RSC Adv., 2023,
13, 34772-34781
A novel graphene/triolein complex-based lubricant for improving high temperature water-based drilling fluid
Received
19th July 2023
, Accepted 22nd November 2023
First published on 29th November 2023
Abstract
Drilling engineering plays a pivotal role in the exploration and extraction of subsurface resources. It heavily depends on drilling fluid, which serves various essential functions including cooling the drill bit, removing drilled cuttings, maintaining formation pressure equilibrium, stabilizing the wellbore, transmitting hydraulic pressure, and safeguarding oil and gas reservoirs. Nonetheless, drilling fluid encounters multiple obstacles such as leakage control, waste fluid management, prevention of wellbore collapse, avoidance of hole enlargement, and environmental preservation. In order to surmount these challenges, the introduction of lubricants into the drilling fluid yields a multitude of advantages, encompassing equipment safeguarding, enhanced drilling efficiency, preservation of wellbore integrity, and bolstered drilling safety. These factors hold crucial significance in ensuring the triumph of drilling operations. This paper presents the introduction of a new lubricant derived from triolein. Following the preparation of graphene and triolein, they were incorporated into the drilling fluid system. A set of tests was subsequently conducted after aging at 240 °C for 16 hours. To assess the impact of the lubricant on the drilling fluid, an examination of rheological and filtration properties was conducted. Additionally, investigations into the friction coefficient, adhesion coefficient, and extreme pressure lubricity were carried out to evaluate the lubricating performance of the drilling fluid. Adding lubricants at a temperature of 240 degrees Celsius has successfully controlled the adhesion coefficient of the drilling fluid to below 0.2, reaching a minimum of 0.055, resulting in a reduction rate of over 70%. This indicates that the lubricant performs well at high temperatures, effectively reducing friction and enhancing drilling speed.
1. Introduction
Petroleum engineering plays a significant role and holds great importance in modern society. It is indispensable for driving social progress and development in various aspects such as energy supply, economic growth, industrial raw materials, technological innovation, and national security.1 Drilling engineering plays a crucial role in the oil and gas industry. It not only directly promotes energy supply and economic development but also involves wellbore control, safety, environmental protection, and technological innovation.2 It has a significant impact on the industry's sustainable development and social prosperity. As global energy consumption continues to rise, traditional oil and gas resources are gradually diminishing, prompting people to explore more complex and challenging deep wells, ultra-deep wells, and high-temperature oil and gas reservoirs. This has led to an increase in the number of high-temperature deep wells.3 As the drilling depth increases, the temperature between the drill string and the wellbore also rises. Unfortunately, commonly used drilling fluid lubricants are prone to detachment, which ultimately leads to a decrease in lubrication performance. Additionally, the pressure between the drill string and the casing or wellbore also increases. This increased pressure causes the oil film formed by common lubricants to rupture, resulting in a loss of lubrication performance.4 In severe cases, this can lead to direct friction between the drill string and the casing or wellbore. To address this issue, it may be necessary to explore alternative lubricants that can withstand higher temperatures and pressures.5 Oil-based drilling fluids are known for their excellent lubricity and inhibition performance.6 However, they are not environmentally friendly and are expensive, limiting their widespread use in the oil and gas industry. Therefore, there has been a growing interest in low-cost and eco-friendly water-based drilling fluids that offer similar or better performance. To improve the lubricity of water-based drilling fluids, high-performance lubricants have become essential.7 Research efforts have focused on developing lubricants that can reduce friction and enhance the lubrication properties of the fluid while being environmentally responsible. Traditional lubricants like hydrocarbons, fatty acids, mineral oil, and asphalt have been found to have insufficient lubricating properties and can produce serious bubbles.8 These lubricants also tend to lose effectiveness at high temperatures, compromising their ability to reduce friction in challenging drilling environments. Some traditional lubricants are also toxic, posing environmental hazards. Recent studies have led to the development of innovative lubricants that are more effective and eco-friendly.9 For instance, vegetable oils, such as canola oil and soybean oil, have been found to have excellent lubricating properties and are biodegradable, making them a preferred choice for use in environmentally sensitive areas.10 In addition to using new lubricants, other techniques have also been developed to enhance the lubrication performance of water-based drilling fluids. Surfactants, for example, can be added to the fluid to reduce interfacial tension between the fluid and rock surfaces, leading to improved lubrication performance and reduced friction.11 The use of high-performance lubricants and other additives in water-based drilling fluids can significantly enhance their performance while minimizing their environmental impact.12 As research into eco-friendly lubricants continues, it is expected that even better solutions will emerge to meet the demands of today's ever-changing oil and gas industry.13
In recent years, oleate esters has gained significant attention among industry professionals as a green diesel lubricity improver due to its excellent lubrication performance, good thermal stability, stable high and low-temperature performance, biodegradability, and low toxicity.14 Among these esters, triolein is particularly effective and has a broader applicability to diesel fuel. Triolein, which is commonly used to improve the lubrication performance of diesel fuel, has very limited research as a lubricant for drilling fluid at present.15 Graphene has become a research hotspot both domestically and internationally due to its unique physical and chemical properties.16 However, the application research of graphene in the field of petroleum engineering is still in its early stages. The limited dispersibility of graphene in water hinders its practical utility as an additive for water-based lubricants. Graphene possesses remarkable self-lubricating properties that hold great potential for enhancing the lubrication performance of drilling fluids. Due to its unique structural and mechanical properties, graphene has inherent lubricity, low friction coefficient, and excellent wear resistance, which make it an ideal candidate for improving the tribological behavior of drilling fluids. Zhao et al. conducted a comparative study on the lubrication and wear properties of PAO4 lubricating oil before and after adding 0.01% graphene using a spherical contact reciprocating motion method.17–19 The results showed that the friction coefficient of PAO4 lubricating oil could be reduced by up to 78% and the wear rate could be reduced by up to 95% after the addition of graphene. However, there are very few reports on the simultaneous use of triolein and graphene as lubricants for drilling fluids. Since both of them have lubricating properties, combining them may result in even better friction reduction effects.20–22
In this study, both graphene and triolein were found to possess lubricating properties. The dispersion of graphene in triolein was found to significantly enhance the lubrication performance of drilling fluids. It was developed as a lubricant with high-temperature resistance. The evaluation of its lubricating performance in water-based drilling fluids focused on two aspects: the lubricity of the drilling fluid itself and the lubricity of the filter cake. Furthermore, an optical microscope was employed to conduct further analysis on the mechanism by which the lubricant reduces friction.
2. Materials and methods
2.1 Materials
Graphene paste was purchased from xfnano, INC, which contains 5 wt% graphene. Triolein (99%) was purchased from Shandong Usolf Chemical Co., Ltd. Hydrolyzed polyacrylonitrile ammonium salt, PFL-L filtrate reducer, anti-high temperature asphalt anti-collapse agent and sulfonated phenolic resin are all provided by the oilfield. All reagents were not further purified.
2.2 Preparation of lubricant
We weighed the appropriate amounts of graphene and triolein at a mass ratio of 1
:
4. Next, we added the graphene to the triolein and stirred the mixture until the graphene was evenly dispersed in the triolein. We then heated the mixture to 60 °C, maintained this temperature while stirring continuously until a homogeneous black solution was formed. This procedure ensured that the graphene was well dispersed within the triolein matrix and provided the necessary conditions for our subsequent experiments.
2.3 Preparation of drilling fluid system
Sodium bentonite and anhydrous sodium carbonate are added into water, stirred for 24 hours, and then hydrated for 24 hours. The composition of drilling fluid system is shown in Table 1.
Table 1 Formulation of drilling fluid
Products |
Content |
Sodium bentonite |
4 wt% |
Anhydrous sodium carbonate |
0.25 wt% |
Hydrolyzed polyacrylonitrile ammonium salt |
2 wt% |
Filtrate reducer |
1.5 wt% |
Asphalt anti-collapse agent |
3 wt% |
Sulfonated phenolic resin |
2 wt% |
2.4 Rheological performance test
The rheological properties of drilling fluids such as apparent viscosity (AV), plastic viscosity (PV) and yield point (YP) were measured before and after hot rolling for 16 h using a rotational viscometer (HTD Model 13145). The measurements consisted of measuring the readings at six different rotational speeds, which ranged from 600 to 3 RPM. AV, PV and YP were calculated by the following equations:where θ600 is the dial reading at 600 RPM and θ300 is the dial reading at 300 RPM.
2.5 Filtration performance test
Drilling fluid filtration loss was measured using a filter tester (SD4, HAITONGDA, China) for 30 min at 0.69 MPa pressure according to American Petroleum Institute (API) standard.
2.6 Lubrication performance test
2.6.1 Adhesive coefficient test. NF-2 adhesion coefficient meter was used to measure the adhesion coefficient of filter cakes. The drilling fluid was poured into a cup and filtered for 30 min at 3.5 MPa, then the filtration loss was recorded. Nitrogen was introduced and pressurized to 3.5 MPa for 5 min, at which time the filter cake and the adhesive disk were fully cemented. The torque wrench indicator was set to zero, then the wrench was put on the adhesion coefficient meter and slowly rotated. When the wrench started to slide and the indicator reached the maximum value, the indicator was recorded. The steps were repeated every 5 min, and the final torque was present when the indicator stopped changing. According to formulas (4) and (5), the adhesion coefficient of filter cake and its reduction rate were calculated. |
Δf = (f0 − f1) × 100%/f0
| (5) |
where f0 is the adhesion coefficient of drilling fluid system without lubricant, and f1 is the adhesion coefficient of drilling fluid system with lubricant.
2.6.2 Extreme pressure lubricator test. The lubrication coefficient of the drilling fluid was evaluated using an extreme pressure lubricator, wherein a friction block was installed and the instrument was powered on. The rotation speed was then adjusted to 60 RPM and allowed to run idle for 5 minutes until it stabilized. Once stable, a sample cup containing distilled water was placed in such a way that the friction block and the friction ring were completely submerged. Subsequently, the torque wrench was adjusted to 150 psi, and once the lubrication coefficient was recorded, the torque was released, and the lubrication coefficient was reset to zero as part of the correction process. To determine the evaluation parameters of the test sample, the distilled water in the sample cup was replaced with the test sample, and the above steps were repeated, recording the lubrication coefficient after the instrument had run for another 5 minutes. The following formulas were utilized to calculate the relevant evaluation parameters |
M = drilling fluid reading/100
| (6) |
|
ΔK = (K0 − K1) × 100%/K0
| (9) |
where K0 is the lubrication coefficient of the drilling fluid system without lubricant, and the K1 is lubrication coefficient of the drilling fluid system with lubricant.
2.6.3 Tribological test. The friction and wear properties of drilling fluid are typically described by the Coefficient of Friction (COF). To precisely measure coefficient of friction, this study utilized an MS-T3001 friction and wear tester. The testing process involved employing a ball-on-plate pattern where a 3 mm radius stationary plate was subjected to a load of 5 N and a given speed of 200 rpm, while an upper ball with a silicon nitride material sliding against it repeatedly. The test was conducted for a duration of 20 minutes altogether, performed at room temperature. Once the test was completed, the ball and plate were thoroughly cleansed using ultrasonic cleaning methods. It's worth noting that the plate was made from 35CrMo steel while the ball was composed of silicon nitride. During the testing process, the researchers recorded the friction coefficient to determine the lubricating properties of the drilling fluid concerning various lubricants and temperatures affected its performance. Ultimately, the results helped to provide essential data for future studies, such as optimizing the formulation of drilling fluids with improved lubricity.
2.7 Characterization of graphene and triolein
2.7.1 Scanning electron microscopy (SEM). SEM can observe the micromorphology and structure of the sample and reveal the fine surface features. The microstructure of graphene and the image of graphene absorbed on bentonite was observed by SEM (JSM7401, Japan).
2.7.2 Fourier infrared spectroscopy (FT-IR). FT-IR can identify the various functional groups present in the sample by the location and intensity of the characteristic peaks. The structural characteristics of triolein and graphene was tested by FT-IR. The scan range was 400 cm−1 to 4000 cm−1.
2.7.3 Particle size analysis. Particle size analysis can give the number proportion and distribution of particles of different sizes in the particle sample, and provide information about the overall size range and dispersion of the particle collection. Triolein, graphene and their mixture at a concentration of 3 wt% were added to the drilling fluid systems respectively, the hybrid treatments were carried out at 80 °C for 16 h, and the aged hybrid treatments were dried and crushed. Then the hybrid treatments were prepared into 3 wt% aqueous solution and diluted by 300 times, and the particle sizes were measured.
2.7.4 Microscope observation. In order to reveal the mechanism of lubricant reducing friction, the roughness and the worn scar of the friction plate was observed by an optical microscope DP73 (Olympus) and a NexView 3D white light interferometer.
3. Results and discussion
3.1 Characterization
Fig. 1a presents the images of triolein (TO) and TO/G. The flake structure of graphene was observed using SEM, as depicted in Fig. 1b. Additionally, Fig. 1c illustrates the absorption of graphene on bentonite. The size of the composite material is distributed between a few microns to a few hundred microns, and graphene can be adsorbed on the bentonite particles to a large extent.
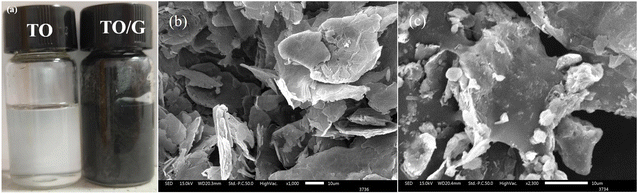 |
| Fig. 1 (a) Photograph of TO and TO/G, (b) SEM image of graphene, (c) SEM image of graphene absorbed on bentonite. | |
The interaction of triolein, graphene, and TO/G was investigated by FTIR (Fig. 1a). In the FTIR spectrum, 1467 cm−1 represents the bending vibration peak of –CH2–, and the –CH2– peak has a significant blue shift (from 1467 cm−1 to 1474 cm−1) after triolein and graphene are combined. At the same time, the peak of –CH2– in triolein also redshifted from 2927 cm−1 to 2923 cm−1, indicating hydrogen bond formation. In addition, the particle size distribution of the composite decreases. According to the information provided, the particle size distribution of drilling fluids with added graphene ranges between 2000 and 4000 nm. This suggests that the graphene particles are relatively large in size, which could impact the performance of the drilling fluids. However, after adding the mixture of triolein and graphene to the drilling fluids, a significant reduction in particle size distribution is observed. The particle size ranges between 800–1000 nm, indicating that the addition of the mixture leads to increased dispersion of the graphene particles within the drilling fluids. Overall, the results suggest that the mixture of triolein and graphene can effectively reduce the particle size of the drilling fluids, which is likely to have a positive impact on their performance in drilling operations (Fig. 2).
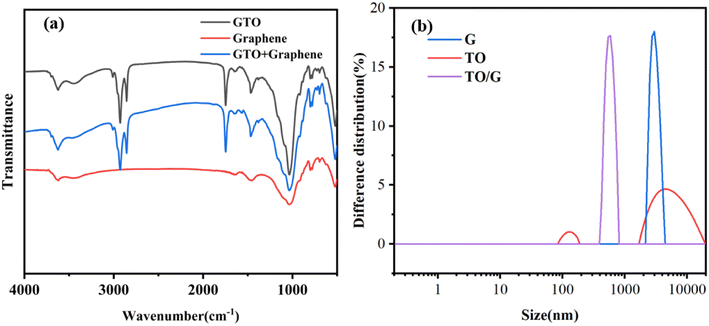 |
| Fig. 2 (a) FT-IR spectra of triolein and graphene, and (b) particle size analysis of triolein and graphene. | |
3.2 Lubricity evaluation
3.2.1 Adhesion coefficient analysis. The formation of a filter cake by the drilling fluid on the borehole wall results in a sticky surface, creating frictional resistance when the drill pipe is in motion. This phenomenon is commonly referred to as the adhesion coefficient. Excessively high adhesion coefficients can cause drilling challenges and accelerate wear on the drilling tools. Hence, it is crucial to minimize the adhesion coefficient to ensure smooth drilling operations. By reducing the adhesion coefficient, the stickiness of the filter cake can be mitigated, resulting in reduced frictional resistance between the drill pipe and the borehole wall. This, in turn, facilitates the movement of the drill pipe and enhances drilling efficiency.As shown in Fig. 3, the overall adhesion coefficient shows a trend of decreasing with the increase in lubricant content. After aging at 240 °C, the adhesion coefficient of drilling fluid without lubricant was 0.232. After adding 1 wt% TO/G, the adhesion coefficient decreased to 0.1774, with a decrease rate of 23%. When adding 3 wt% TO/G, the adhesion coefficient was 0.5915, with a decrease rate of 74.5%. At other temperature gradients, the adhesion coefficient decreases with the increase of lubricant content.
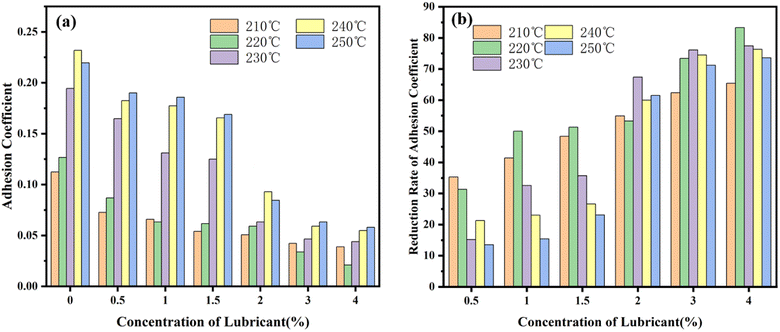 |
| Fig. 3 (a) Adhesion coefficient and (b) reduction of adhesion coefficient of the drilling fluid containing different concentrations of the lubricant. | |
3.2.2 Tribological analysis. Friction and wear testing is a valuable method to simulate the frictional interaction between the drilling fluid and the drill pipe during drilling operations. This testing approach enables us to assess the coefficient of friction (COF) of the drilling fluid. Through friction and wear testing, we can evaluate the performance of different drilling fluid formulations or additives. This helps in identifying fluids that exhibit lower COF values, indicating reduced friction and improved lubrication properties. Lower COF values are beneficial as they contribute to smoother drilling operations, reducing energy consumption and minimizing wear on the drill pipe.Fig. 4 shows the relationship between friction coefficient and lubricant addition after drilling fluid is aged at 220 °C and 240 °C respectively. When the temperature rises from 220 to 240, there is a noticeable increase in the COF, indicating that high temperatures indeed cause some components in the drilling fluid to decompose, leading to a decline in its performance. However, as the lubricant content increases, the COF gradually decreases, indicating that the lubricant can still provide lubricating effects even at high temperatures. Fig. 5 shows the average friction coefficient and its reduction rate of drilling fluid during the 20 minutes test. After aging at 240 °C, the average friction coefficient of drilling fluid without lubricant is 0.2775, and after adding 1 wt% lubricant, the friction coefficient decreases to 0.1828, with a reduction rate of 41.4. When the lubricant content is increased to 3 wt%, the friction coefficient is 0.11, and the reduction rate reaches 60%.
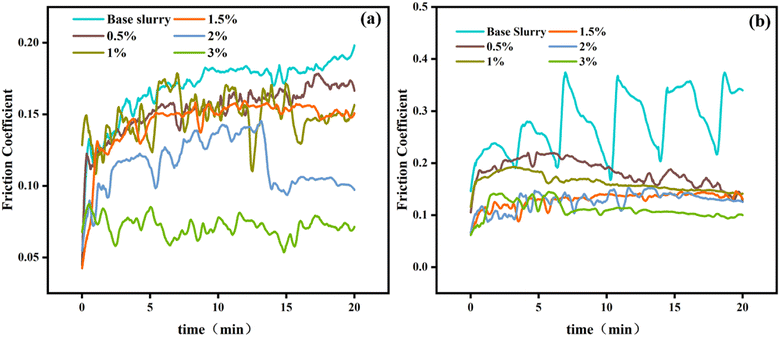 |
| Fig. 4 Friction coefficient of the drilling fluid at (a) 220 °C and (b) 240 °C as a function of time. | |
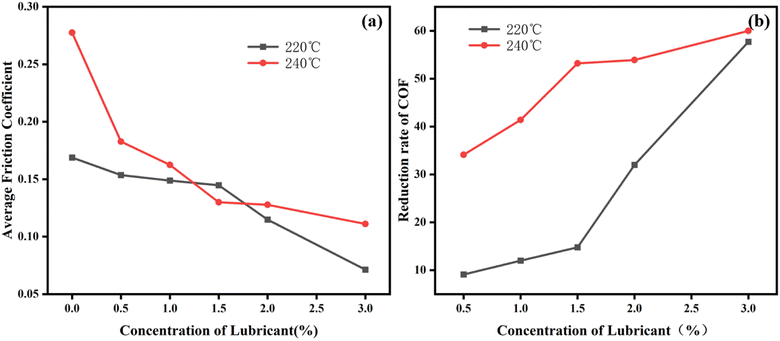 |
| Fig. 5 Average COF (a) and it's reduction rate (b) of the drilling fluid containing different concentrations of the lubricant. | |
3.2.3 Extreme pressure lubricity. The primary purpose of the extreme pressure lubricity tester is to assess the impact of lubricating additives on the lubricity of drilling fluids, such as mud. It also aids in determining the optimal dosage of these lubricating additives. Additionally, the tester is utilized to measure the extreme pressure film strength of lubricants. Both of these technical parameters hold significant importance in various applications, including oil drilling, directional drilling, and trenchless technology. By conducting tests using the extreme pressure lubricity tester, engineers and researchers can evaluate the effectiveness of different lubricating additives in enhancing the lubricity of drilling fluids. It enables them to determine the appropriate concentration or dosage of these additives to achieve optimal lubrication properties. This information is crucial for maintaining efficient and smooth drilling operations while minimizing friction and wear between drilling components.Fig. 6 shows the extreme pressure lubrication coefficient of drilling fluid aged at different temperatures and its reduction rate. It can be seen that lubrication coefficient of the control group is higher 0.1943–0.2237. After 1 wt% lubricant was added, TO/G played a lubricating role in the temperature range of 240 °C, obviously reduced the lubrication coefficient of the drilling fluid system to 0.1739–0.1209, and the reduction rate was 25%–37.8%. The recommended dosage of lubricant was between 1 wt% and 3 wt%. At this time, the drilling fluid had a low lubrication coefficient. At 3 wt%, the lubrication coefficient reached a minimum of 0.1209, and the reduction rate was 37.8%.
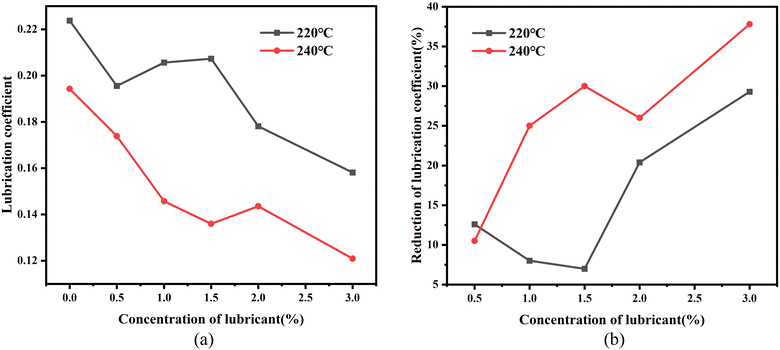 |
| Fig. 6 Lubrication coefficient of the drilling fluid containing different concentrations of the lubricant (a) and its reduction rate (b). | |
3.3 Effect of TO/G on the rheological and filtration of the WBDF
As shown in Fig. 7, the apparent viscosity and plastic viscosity of drilling fluid have increased after adding lubricant. With the increase of temperature, the viscosity of drilling fluid showed a trend of decreasing at first and then increasing. With the increase of the amount of lubricant, the fluid loss increased slightly.
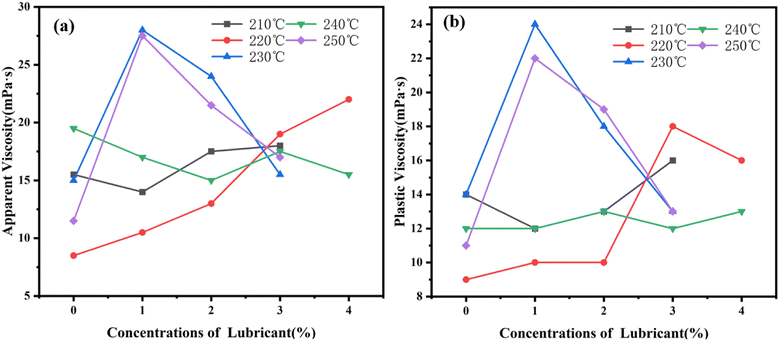 |
| Fig. 7 (a) Apparent viscosity and (b) plastic viscosity of the drilling fluid containing different concentrations of the lubricant. | |
After aging at 240 °C and adding 3 wt% lubricant, the apparent viscosity of drilling fluid is 18 mPa s and the filtration loss is 17 ml. Photos of filter cake is shown in the Fig. 9, it can be seen that all the filter cakes were dense with good toughness, and the thickness were 1–2 mm.
3.4 Observation of the worn scar
After the friction and wear test, the plate was observed by an optical microscope and a white light interferometer. The width and depth of the worn scar can further reflect the effect of lubricity. Fig. 8 shows the surface of worn scar. In the base slurry without any lubricant (Fig. 9a), the width of worn scar was much wider than those samples containing lubricant (Fig. 9b–f). And there was also a tendency that the width of worn scar gradually decreased with the increase of the concentration of lubricant, which is similar to the change of friction coefficient. Subsequently, a white light interferometer was used to observe the 3D topography of worn scars. As is shown in Fig. 10, compared with the base slurry, the width and depth were smaller after adding lubricant.
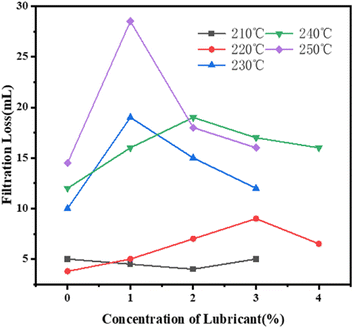 |
| Fig. 8 Filtration loss of the drilling fluid containing different concentrations of the lubricant. | |
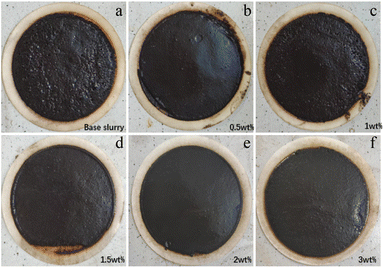 |
| Fig. 9 Photographs of filter cake containing different concentrations of lubricant. (a) base mud, (b) 0.5 wt% TO/G, (c) 1 wt% TO/G, (d) 1.5 wt% TO/G, (e) 2 wt% TO/G, (f) 3 wt% TO/G. | |
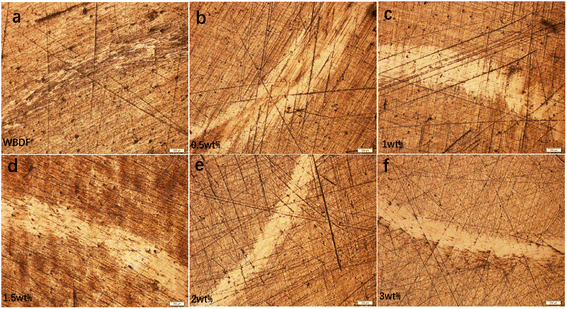 |
| Fig. 10 Surface topography of worn scars under different dosages of lubricant. (a) base mud, (b) 0.5 wt% TO/G, (c) 1 wt% TO/G, (d) 1.5 wt% TO/G, (e) 2 wt% TO/G, (f) 3 wt% TO/G. | |
The 3D topography of the worn scars can be seen and the width and depth of the worn scars can be observed by using the 3D white light interferometer. Without adding lubricant, the wear mark is deep, and the wear mark depth is significantly reduced after adding lubricant, indicating that the addition of lubricant effectively reduces the wear of the friction surface. This is because the hydroxyl and amino groups rich in hydrogen atoms in the chain segment of the lubricant molecule form hydrogen bonds with the oxygen atoms and other groups on the surface of the drilling tool, adsorbed on the surface of the drilling tool, forming a lubricating film, effectively reducing the friction and weakening the friction between the drilling tool and the drilling fluid.
3.5 Possible lubrication mechanism
Drawing upon microscopic observations of worn scars and recent research on surface friction mechanisms, Fig. 11 illustrates the potential lubrication mechanism of TO/G. During the drilling process, a constant generation of cuttings occurs, resulting in direct contact with the drill pipe. As the drill pipe rotates and vibrates, the surface of the pipe experiences continuous wear. Moreover, the presence of a significant amount of bentonite particles exacerbates the damage inflicted upon the drill pipe, consequently reducing its overall service life. To elaborate further, the lubrication mechanism of TO/G can be understood as follows: when TO/G is employed as a lubricating agent, it forms a protective film or coating on the surface of the drill pipe. This film acts as a barrier, preventing direct contact between the cuttings and the surface of the pipe. Consequently, it minimizes the frictional forces that contribute to wear and tear. The use of TO/G as a lubricant also exhibits advantages in terms of its ability to inhibit the detrimental impact of bentonite particles. The lubricating properties of TO/G help to reduce the adhesion and agglomeration of these particles on the surface of the drill pipe, thereby mitigating their abrasive effects and preserving the integrity of the pipe for an extended period. The lubrication mechanism of TO/G involves the formation of a protective film or coating on the drill pipe's surface, which effectively reduces direct contact between the cuttings and the pipe. Furthermore, it provides a means of minimizing the damaging effects of bentonite particles, ultimately extending the service life of the drill pipe and enhancing overall drilling efficiency (Fig. 12).
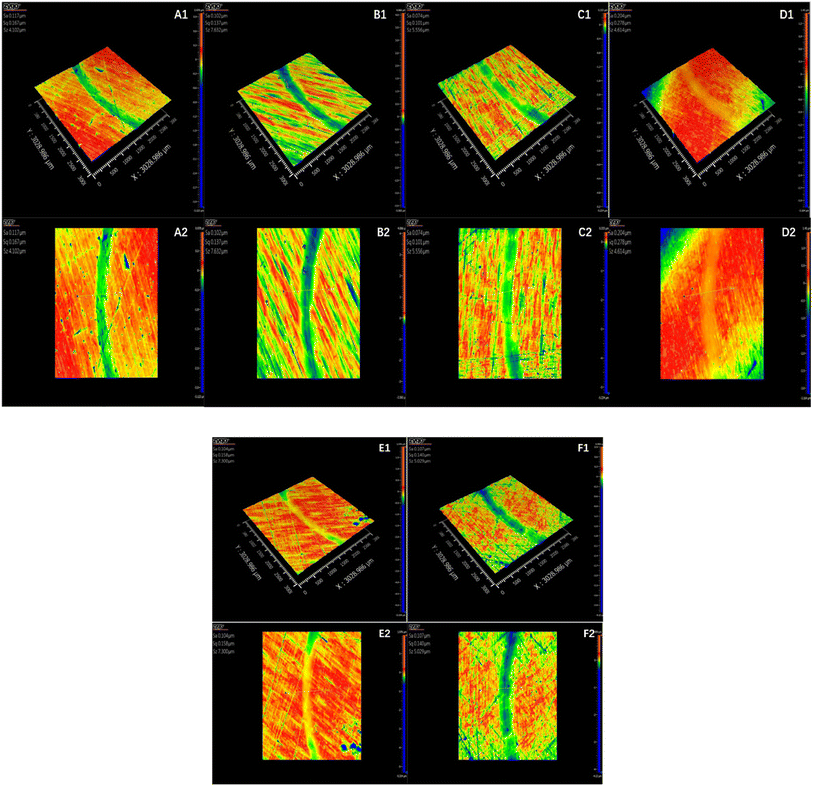 |
| Fig. 11 3D topography of worn scars under different lubricants. (A1 and A2) Base slurry, (B1 and B2) 0.5 wt% TO/G, (C1 and C2) 1 wt% TO/G, (D1 and D2) 1.5 wt% TO/G, (E1 and E2) 2 wt% TO/G, and (F1 and F2) 3 wt% TO/G. | |
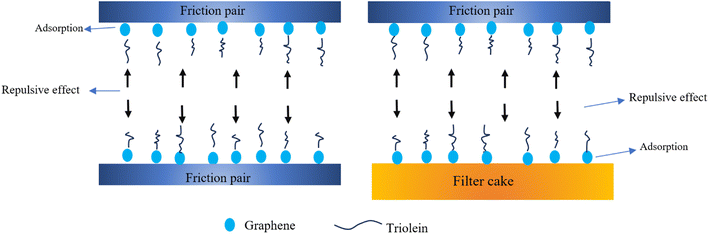 |
| Fig. 12 Possible lubrication mechanism of TO/G. | |
4. Conclusions
A blend of graphene and triolein was prepared as a water-based drilling fluid lubricant. The efficiency of the lubricant was evaluated by conducting friction and wear tests, along with measuring the adhesion coefficient and extreme pressure lubrication coefficient before and after exposure to high temperature aging. Moreover, rheological and filtration properties were also examined in the drilling fluid. To further understand the mechanism of lubrication, FT-IR and SEM photos were used for analysis. It was observed that the TO/G blend improved the mechanical properties of the lubricant at high temperatures and resulted in better lubrication efficiency compared to conventional lubricants.
(1) Adding graphene and glyceryl trioleate into the base slurry can improve the lubrication performance of drilling fluid, and at the same time, due to the synergistic effect between them, the lubricant has better effect, and it still shows good performance after high temperature aging.
(2) The addition of lubricant has little influence on the rheological properties and filtration loss of drilling fluid.
(3) By analyzing the infrared spectrum of the lubricant and the electron microscope pictures of the filter cake, it is found that the sliding friction between the filter cake and the drilling tool is transformed into rolling friction by graphene particles through adsorption, and glyceryl trioleate can also be adsorbed on the metal surface to form a lubricating film, which greatly improves the lubricating performance of the drilling fluid through their combined action.
Conflicts of interest
There are no conflicts to declare.
Acknowledgements
We would like to thanks to the Financial Support of Scientific research and technology development projects of China National Petroleum Corporation Limited (2022ZG06) and the National Natural Science Foundation of China (52274011) and Science and Technology Innovation Special Project of Xiong'an New Area (2022XAGG0500) for this work.
References
- H. Wang, H. Huang, J. Guodong, C. Chen, Z. Lv, W. Chen, W. Bi and L. Liu, Progress and challenges of drilling and completion technologies for deep,ultra-deep and horizontal wells of CNPC, China Pet. Explor., 2023, 28(3), 1–11 Search PubMed.
- S. Lin, H. Wang and J. Guodong, Current situation, challenges and developing trend of CNPC's oil & gas drilling, Nat. Gas Ind., 2013, 33(10), 1–10 Search PubMed.
- Y. Su, B. Lu and Y. Liu, et al., Status and research suggestions on the drilling and completion technologies for onshore deep and ultra deep wells in China, Oil Drill. Prod. Technol., 2020, 42(5), 527–542 Search PubMed.
- M. K. Mohammadi and K. T. Nowtarki, A Case Study on the Successful Application of Solids Lubricants in Directional and Horizontal Drilling Operations to Reduce Torque and Drag and Improve Rop in One of the Carbonate Oil Reservoirs, SPE/IATMI Asia Search PubMed.
- G. L. R. Leal, A. I. C. Garnica, R. R. Silva, L. R. Viana, A. C. Bezerra Júnior, J. C. O. Freitas and F. D. S. Curbelo, Formulation of Novel Ecofriendly Microemulsion-Based Drilling Fluids for Improving Rheological and Filtration Characteristics, J. Pet. Sci. Eng., 2022, 215, 110562 CrossRef CAS.
- A. H. Arain, S. Ridha and I. Ali, Development and Performance Evaluation of Castor Oil Based Biodiesel as an Eco-Friendly Ester-Based Drilling Fluid, Pet. Sci. Technol., 2023, 41(19), 1831–1851 CrossRef CAS.
- A. Fereidounpour and M. J. S. Hosseini, A Field Study, Laboratory Test and Cost Estimation of Solid and Liquid Lubricants in Directional Wells to Reduce Friction Coefficient and Improve Rop, SN Appl. Sci., 2020, 2(9), 1495 CrossRef CAS.
- D. Kania, R. Yunus, R. Omar, S. A. Rashid and B. M. Jan, A Review of Biolubricants in Drilling Fluids: Recent Research, Performance, and Applications, J. Pet. Sci. Eng., 2015, 135, 177–184 CrossRef CAS.
- L. Geng, M. Wang, H. Jiang and X. Guang, The Status of the Development of Graphene Applications in Petroleum Engineering, Pet. Drill. Tech., 2019, 47(5), 80–85 Search PubMed.
- W. Li, X. Zhao, H. Peng, J. Guo, T. Ji, B. Chen, Z. You, and L. Liu, A Novel Environmentally Friendly Lubricant for Water-Based Drilling Fluids as a New Application of Biodiesel, Paper presented at the IADC/SPE Asia Pacific Drilling Technology Conference, 2016 Search PubMed.
- S. K. Naidu, E. E. Klaus and J. Larry Duda, Evaluation of Liquid Phase Oxidation Products of Ester and Mineral Oil Lubricants, Ind. Eng. Chem. Prod. Res. Dev., 1984, 23(4), 613–619 CrossRef CAS.
- A. Aftab, A. R. Ismall and Z. H. Ibupoto, Enhancing the rheological properties and shale inhibition behavior of water-based mud using nanosilica, multi-walled carbon nanotube, and graphene nanoplatelet, Egypt. J. Pet., 2017, 26(2), 291–299 CrossRef.
- K. S. Rong, X. Y. Yao, T. M. Lu, J. Q. Gong, Y. S. Yu and J. G. Li, Development and Performance Evaluation of Environmental Friendly Drilling Fluid Lubricant Based on Amide Reaction, Fresenius Environ. Bull., 2022, 31(8), 7796–7803 CAS.
- X. Luo, W. L. Han, H. Ren and Q. Z. Zhuang, Experimental Study of a Novel Environmental Friendly, High Performance Lubricant for Water Based Drilling Fluid, Fresenius Environ. Bull., 2019, 28(7), 5624–5631 CAS.
- G. Mittal, H. Kesarwani, S. Sharma, A. Saxena and IEEE, Experimental Investigations of Novel Fatty Oil Based Lubricant-Enhanced Water Based Drilling Mud Via Lubricity Coefficient, Filtration Loss and Rheological Characterization, Oceans, 2022, 2022, 1–8 Search PubMed.
- Y. Liu, Z. Qiu, P. Yang, Z. Chen, H. Zhong and X. Zhao, Preparation and Evaluation of a Environment-Friendly and Extreme Pressure Lubricant Used in Drilling Fluid, Appl. Chem. Ind., 2018, 47(12), 2590–2594 Search PubMed.
- L. Zhao, Z. Cai and Z. ZHANG, et al., Tribological properties of graphene as effective lubricant additive in oil on textured bronze surface, Chin. J. Mater. Res., 2016, 30(1), 57–62 CAS.
- L. Zhang, S. Hou, Y. Wu, F. You and J. Zhang, Research Progress and Development Trend of Environmentally Friendly Lubricants for Drilling Fluids, Oilfield Chem., 2022, 39(1), 163–169 CAS.
- W. Zhu and X. Zheng, Biodegradable Lubricant with High-Temperature and Ionic-Contamination Resistance: Deep Eutectic Solvent Chcl-Peg, ACS Omega, 2022, 7(43), 38380–38388 CrossRef CAS PubMed.
- X. Tian, N. Song, G. Yang, C. Zhou, S. Zhang and P. Zhang, Organic-Sulfonate Functionalized Graphene as a High Temperature Lubricant for Efficient Antifriction and Antiwear in Water Based Drilling Fluid, Tribol. Lett., 2022, 70, 32 CrossRef CAS.
- J. Ma, J. Xu, S. Pang, W. Zhou, B. Xia and Y. An, Novel Environmentally Friendly Lubricants for Drilling Fluids Applied in Shale Formation, Energy Fuels, 2021, 35(9), 8153–8162 CrossRef CAS.
- W. Yu, S. Li, H. Yang and J. Luo, Progress in the Functional Modification of Graphene/Graphene Oxide: A Review, RSC Adv., 2020, 10(26), 15328–15345, 10.1039/D0RA01068E.
|
This journal is © The Royal Society of Chemistry 2023 |
Click here to see how this site uses Cookies. View our privacy policy here.